coolant RENAULT SCENIC 2009 J84 / 2.G Engine And Peripherals EDC16 Repair Manual
[x] Cancel search | Manufacturer: RENAULT, Model Year: 2009, Model line: SCENIC, Model: RENAULT SCENIC 2009 J84 / 2.GPages: 273
Page 231 of 273
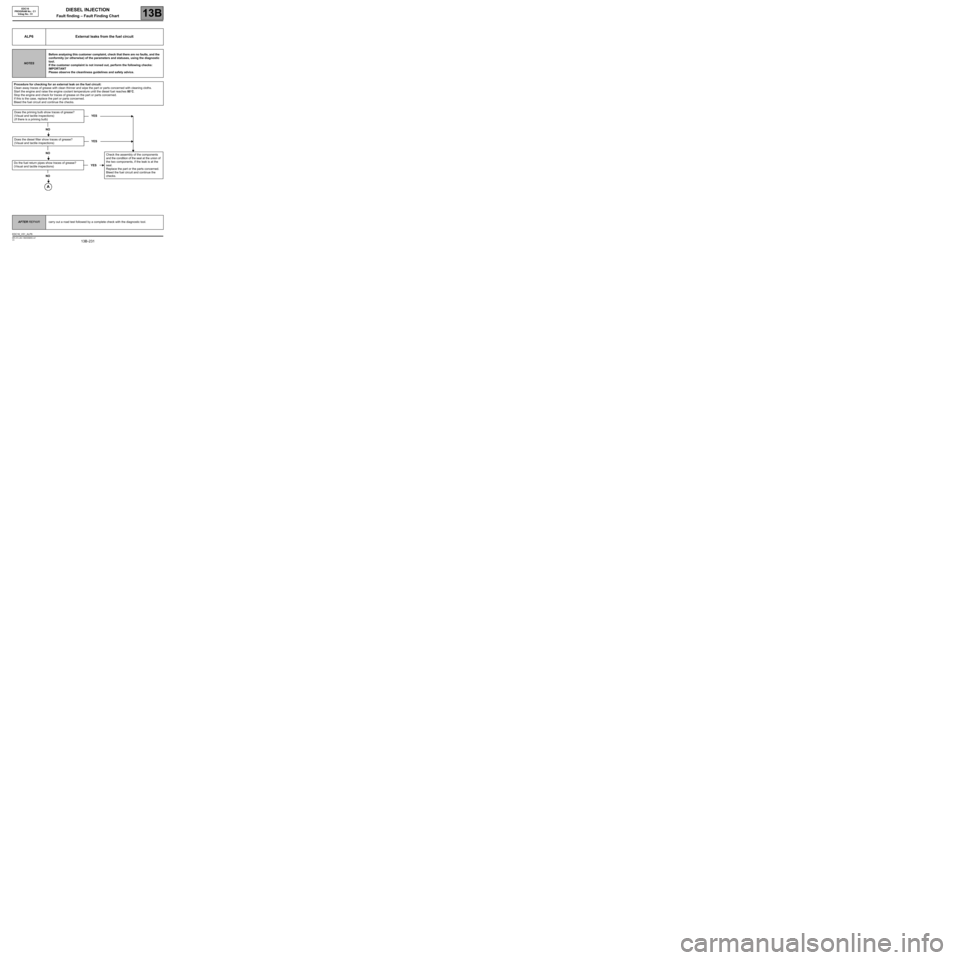
DIESEL INJECTION
Fault finding – Fault Finding Chart13B
13B -231V3 MR-372-J84-13B250$855.mif
EDC16
PROGRAM No.: C1
Vdiag No.: 51
ALP6 External leaks from the fuel circuit
NOTESBefore analysing this customer complaint, check that there are no faults, and the
conformity (or otherwise) of the parameters and statuses, using the diagnostic
tool.
If the customer complaint is not ironed out, perform the following checks:
IMPORTANT
Please observe the cleanliness guidelines and safety advice.
Procedure for checking for an external leak on the fuel circuit:
Clean away traces of grease with clean thinner and wipe the part or parts concerned with cleaning cloths.
Start the engine and raise the engine coolant temperature until the diesel fuel reaches 80˚C.
Stop the engine and check for traces of grease on the part or parts concerned.
If this is the case, replace the part or parts concerned.
Bleed the fuel circuit and continue the checks.
Does the priming bulb show traces of grease?
(Visual and tactile inspections)
(If there is a priming bulb)YES
NO
Does the diesel filter show traces of grease?
(Visual and tactile inspections)YES
NO
Do the fuel return pipes show traces of grease?
(Visual and tactile inspections)
NO
YESCheck the assembly of the components
and the condition of the seal at the union of
the two components, if the leak is at the
seal.
Replace the part or the parts concerned.
Bleed the fuel circuit and continue the
checks.
AFTER REPAIRcarry out a road test followed by a complete check with the diagnostic tool.
EDC16_V51_ALP6
Page 246 of 273
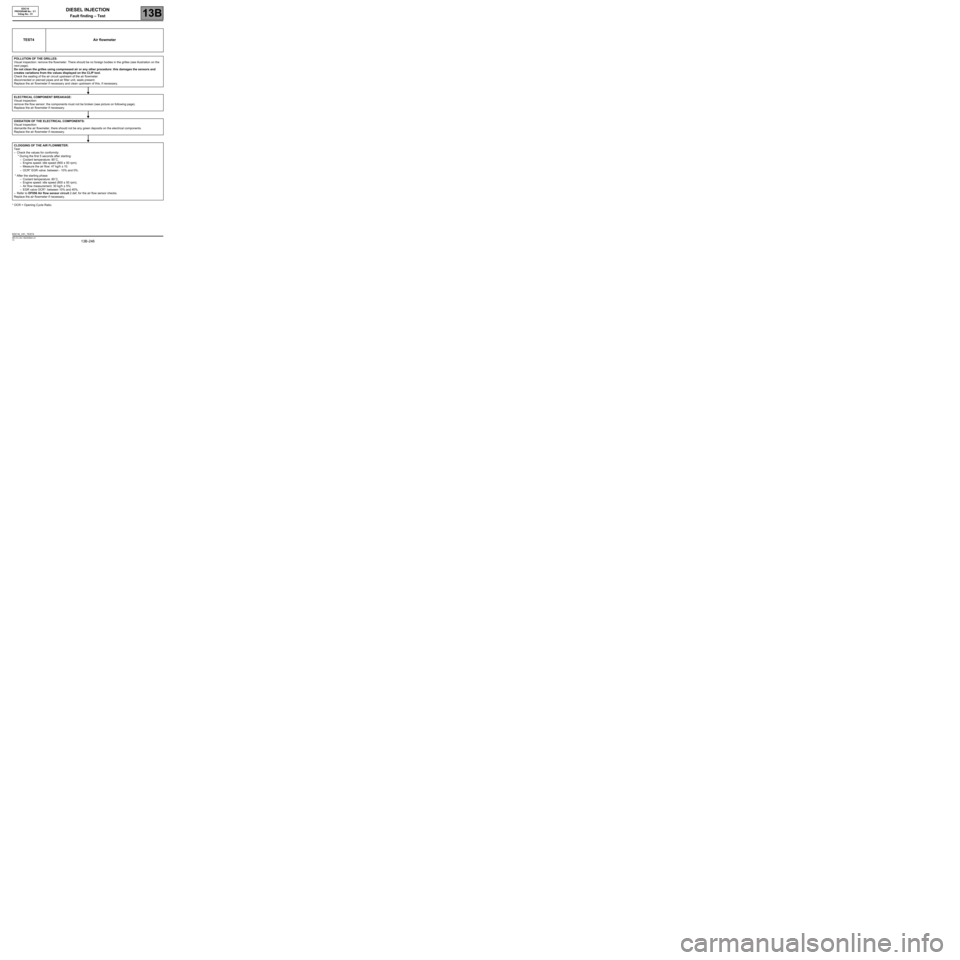
DIESEL INJECTION
Fault finding – Test13B
13B -246V3 MR-372-J84-13B250$900.mif
EDC16
PROGRAM No.: C1
Vdiag No.: 51
* OCR = Opening Cycle Ratio.
TEST4 Air flowmeter
POLLUTION OF THE GRILLES:
Visual inspection: remove the flowmeter. There should be no foreign bodies in the grilles (see illustration on the
next page).
Do not clean the grilles using compressed air or any other procedure: this damages the sensors and
creates variations from the values displayed on the CLIP tool.
Check the sealing of the air circuit upstream of the air flowmeter:
disconnected or pierced pipes and air filter unit, seals present.
Replace the air flowmeter if necessary and clean upstream of this, if necessary.
ELECTRICAL COMPONENT BREAKAGE:
Visual inspection:
remove the flow sensor: the components must not be broken (see picture on following page).
Replace the air flowmeter if necessary.
OXIDATION OF THE ELECTRICAL COMPONENTS:
Visual inspection:
dismantle the air flowmeter, there should not be any green deposits on the electrical components.
Replace the air flowmeter if necessary.
CLOGGING OF THE AIR FLOWMETER:
Test:
–Check the values for conformity:
* During the first 5 seconds after starting:
–Coolant temperature: 80˚C,
–Engine speed: idle speed (800 ± 50 rpm);
–Measure the air flow: 47 kg/h ± 10.
–OCR* EGR valve: between - 10% and 0%.
* After the starting phase:
–Coolant temperature: 80˚C,
–Engine speed: idle speed (800 ± 50 rpm);
–Air flow measurement: 30 kg/h ± 5%;
–EGR valve OCR*: between 10% and 40%.
–Refer to DF056 Air flow sensor circuit 2.def, for the air flow sensor checks.
Replace the air flowmeter if necessary.
EDC16_V51_TEST4
Page 248 of 273
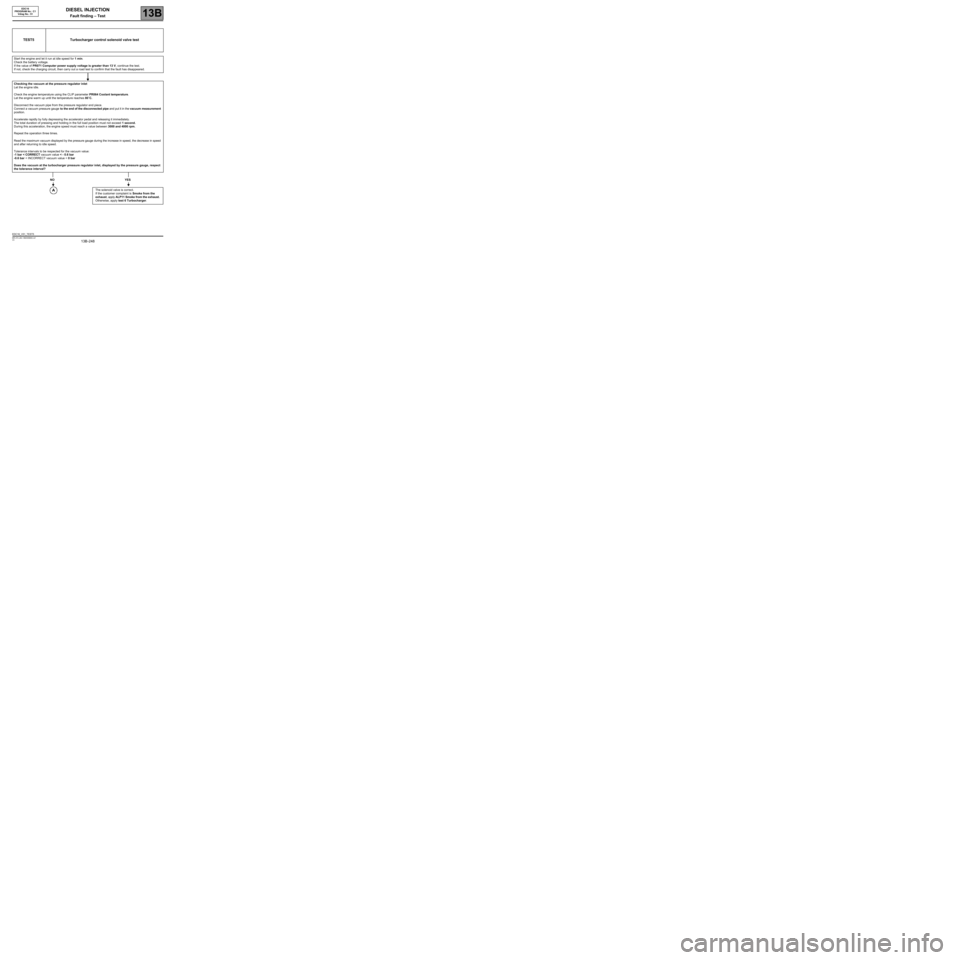
DIESEL INJECTION
Fault finding – Test13B
13B -248V3 MR-372-J84-13B250$900.mif
EDC16
PROGRAM No.: C1
Vdiag No.: 51
TEST5 Turbocharger control solenoid valve test
Start the engine and let it run at idle speed for 1 min.
Check the battery voltage.
If the value of PR071 Computer power supply voltage is greater than 13 V, continue the test.
If not, check the charging circuit, then carry out a road test to confirm that the fault has disappeared.
Checking the vacuum at the pressure regulator inlet
Let the engine idle.
Check the engine temperature using the CLIP parameter PR064 Coolant temperature.
Let the engine warm up until the temperature reaches 80˚C.
Disconnect the vacuum pipe from the pressure regulator end piece.
Connect a vacuum pressure gauge to the end of the disconnected pipe and put it in the vacuum measurement
position.
Accelerate rapidly by fully depressing the accelerator pedal and releasing it immediately.
The total duration of pressing and holding in the full load position must not exceed 1 second.
During this acceleration, the engine speed must reach a value between 3000 and 4000 rpm.
Repeat the operation three times.
Read the maximum vacuum displayed by the pressure gauge during the increase in speed, the decrease in speed
and after returning to idle speed.
Tolerance intervals to be respected for the vacuum value:
-1 bar < CORRECT vacuum value < - 0.6 bar
-0.6 bar < INCORRECT vacuum value < 0 bar
Does the vacuum at the turbocharger pressure regulator inlet, displayed by the pressure gauge, respect
the tolerance interval?
NO YES
The solenoid valve is correct.
If the customer complaint is Smoke from the
exhaust, apply ALP11 Smoke from the exhaust.
Otherwise, apply test 6 Turbocharger.
1
EDC16_V51_TEST5
Page 273 of 273
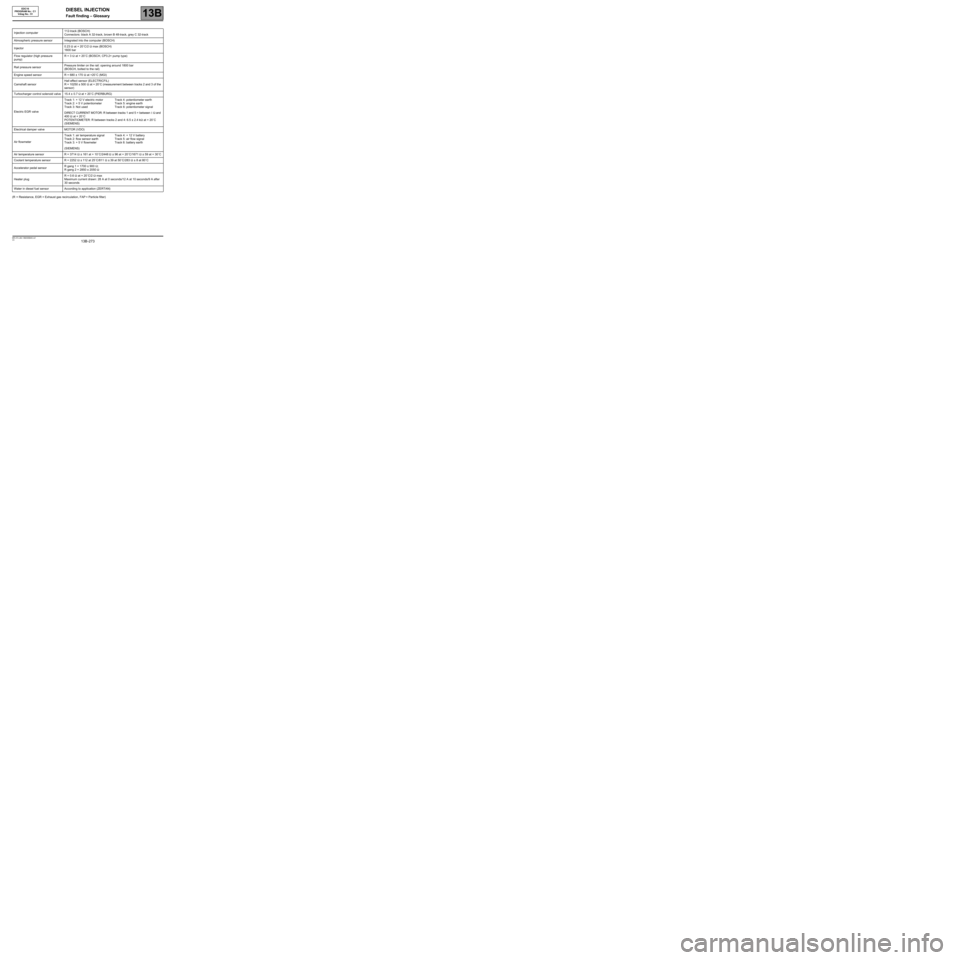
DIESEL INJECTION
Fault finding – Glossary13B
13B -273V3 MR-372-J84-13B250$945.mif
EDC16
PROGRAM No.: C1
Vdiag No.: 51DIESEL INJECTION
Fault finding – Glossary
(R = Resistance, EGR = Exhaust gas recirculation, FAP = Particle filter)Injection computer112-track (BOSCH)
Connectors: black A 32-track, brown B 48-track, grey C 32-track
Atmospheric pressure sensor Integrated into the computer (BOSCH)
Injector0.23 Ω at + 20˚C/2 Ω max (BOSCH)
1600 bar
Flow regulator (high pressure
pump)R = 3 Ω at + 20˚C (BOSCH, CP3.2+ pump type)
Rail pressure sensorPressure limiter on the rail: opening around 1800 bar
(BOSCH, bolted to the rail)
Engine speed sensor R = 680 ± 170 Ω at +20˚C (MGI)
Camshaft sensorHall effect sensor (ELECTRICFIL)
R = 10250 ± 500 Ω at + 20˚C (measurement between tracks 2 and 3 of the
sensor)
Turbocharger control solenoid valve 15.4 ± 0.7 Ω at + 20˚C (PIERBURG)
Electric EGR valveTrack 1: + 12 V electric motor
Track 2: + 5 V potentiometer
Track 3: Not usedTrack 4: potentiometer earth
Track 5: engine earth
Track 6: potentiometer signal
DIRECT CURRENT MOTOR: R between tracks 1 and 5 = between 1 Ω and
400 Ω at + 20˚C
POTENTIOMETER: R between tracks 2 and 4: 6.5 ± 2.4 kΩ at + 20˚C
(SIEMENS)
Electrical damper valve MOTOR (VDO)
Air flowmeterTrack 1: air temperature signal
Track 2: flow sensor earth
Track 3: + 5 V flowmeterTrack 4: + 12 V battery
Track 5: air flow signal
Track 6: battery earth
(SIEMENS)
Air temperature sensor R = 3714 Ω ± 161 at + 10˚C/2448 Ω ± 96 at + 20˚C/1671 Ω ± 59 at + 30˚C
Coolant temperature sensor R = 2252 Ω ± 112 at 25˚C/811 Ω ± 39 at 50˚C/283 Ω ± 8 at 80˚C
Accelerator pedal sensorR gang 1 = 1700 ± 900 Ω;
R gang 2 = 2850 ± 2050 Ω
Heater plugR = 0.6 Ω at + 20˚C/2 Ω max
Maximum current drawn: 28 A at 0 seconds/12 A at 10 seconds/9 A after
30 seconds
Water in diesel fuel sensor According to application (ZERTAN)