sensor RENAULT SCENIC 2009 J84 / 2.G Engine And Peripherals EDC16 Workshop Manual
[x] Cancel search | Manufacturer: RENAULT, Model Year: 2009, Model line: SCENIC, Model: RENAULT SCENIC 2009 J84 / 2.GPages: 273
Page 2 of 273
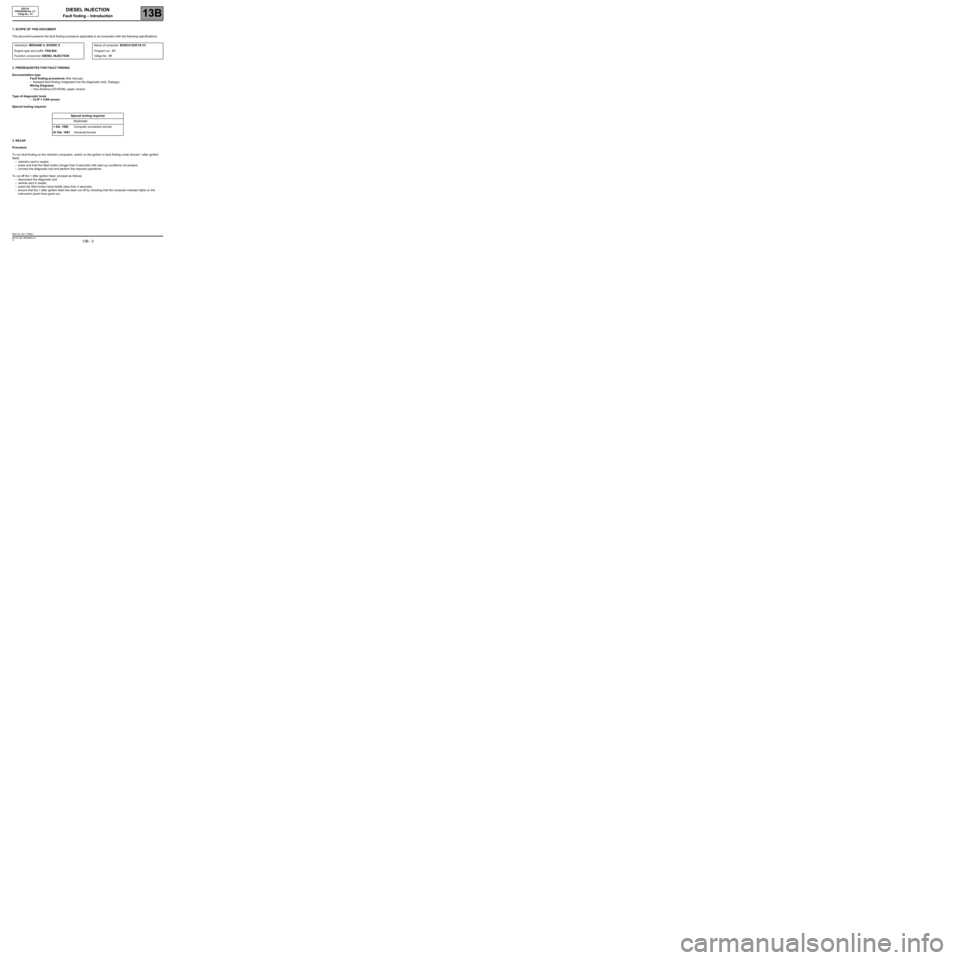
DIESEL INJECTION
Fault finding – Introduction13B
13B - 2V3 MR-372-J84-13B250$045.mif
113B
EDC16
PROGRAM No: C1
Vdiag No.: 51DIESEL INJECTION
Fault finding – Introduction
1. SCOPE OF THIS DOCUMENT
This document presents the fault finding procedure applicable to all computers with the following specifications:
2. PREREQUISITES FOR FAULT FINDING
Documentation type
Fault finding procedures (this manual):
–Assisted fault finding (integrated into the diagnostic tool), Dialogys.
Wiring Diagrams:
–Visu-Schéma (CD-ROM), paper version.
Type of diagnostic tools
–CLIP + CAN sensor
Special tooling required
3. RECAP
Procedure
To run fault finding on the vehicle's computers, switch on the ignition in fault finding mode (forced + after ignition
feed).
–vehicle's card in reader;
–press and hold the Start button (longer than 5 seconds) with start-up conditions not present,
–connect the diagnostic tool and perform the required operations.
To cut off the + after ignition feed, proceed as follows:
–disconnect the diagnostic tool,
–vehicle card in reader,
–press the Start button twice briefly (less than 3 seconds),
–ensure that the + after ignition feed has been cut off by checking that the computer indicator lights on the
instrument panel have gone out. Vehicle(s): MEGANE II, SCENIC II
Engine type and suffix: F9Q 804
Function concerned: DIESEL INJECTIONName of computer: BOSCH EDC16 C3
Program no.: C1
Vdiag No.: 51
Special tooling required
Multimeter
+ Elé. 1590Computer connection bornier
Or Elé. 1681Universal bornier
EDC16_V51_PRELI
MR-372-J84-13B250$045.mif
Page 9 of 273
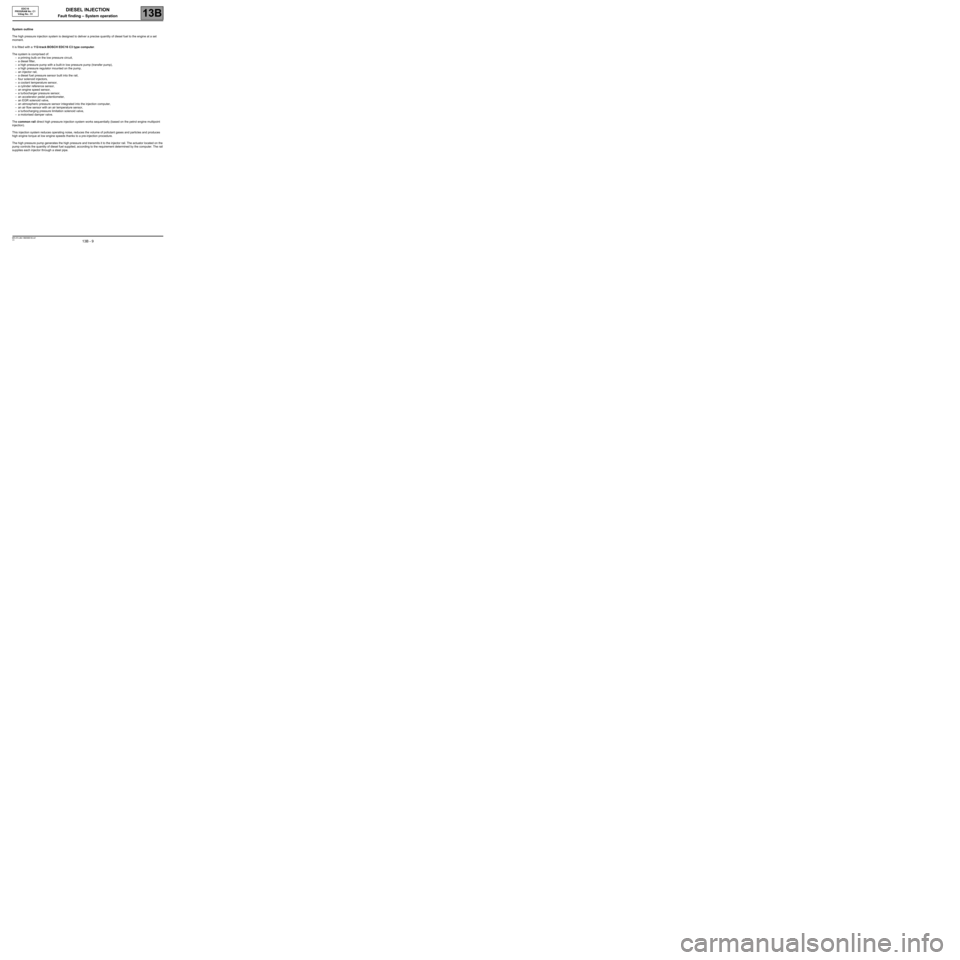
DIESEL INJECTION
Fault finding – System operation13B
13B - 9V3 MR-372-J84-13B250$135.mif
EDC16
PROGRAM No: C1
Vdiag No.: 51DIESEL INJECTION
Fault finding – System operation
System outline
The high pressure injection system is designed to deliver a precise quantity of diesel fuel to the engine at a set
moment.
It is fitted with a 112-track BOSCH EDC16 C3 type computer.
The system is comprised of:
–a priming bulb on the low pressure circuit,
–a diesel filter,
–a high pressure pump with a built-in low pressure pump (transfer pump),
–a high pressure regulator mounted on the pump,
–an injector rail,
–a diesel fuel pressure sensor built into the rail,
–four solenoid injectors,
–a coolant temperature sensor,
–a cylinder reference sensor,
–an engine speed sensor,
–a turbocharger pressure sensor,
–an accelerator pedal potentiometer,
–an EGR solenoid valve,
–an atmospheric pressure sensor integrated into the injection computer,
–an air flow sensor with an air temperature sensor,
–a turbocharging pressure limitation solenoid valve,
–a motorised damper valve.
The common rail direct high pressure injection system works sequentially (based on the petrol engine multipoint
injection).
This injection system reduces operating noise, reduces the volume of pollutant gases and particles and produces
high engine torque at low engine speeds thanks to a pre-injection procedure.
The high pressure pump generates the high pressure and transmits it to the injector rail. The actuator located on the
pump controls the quantity of diesel fuel supplied, according to the requirement determined by the computer. The rail
supplies each injector through a steel pipe.
MR-372-J84-13B250$135.mif
Page 10 of 273
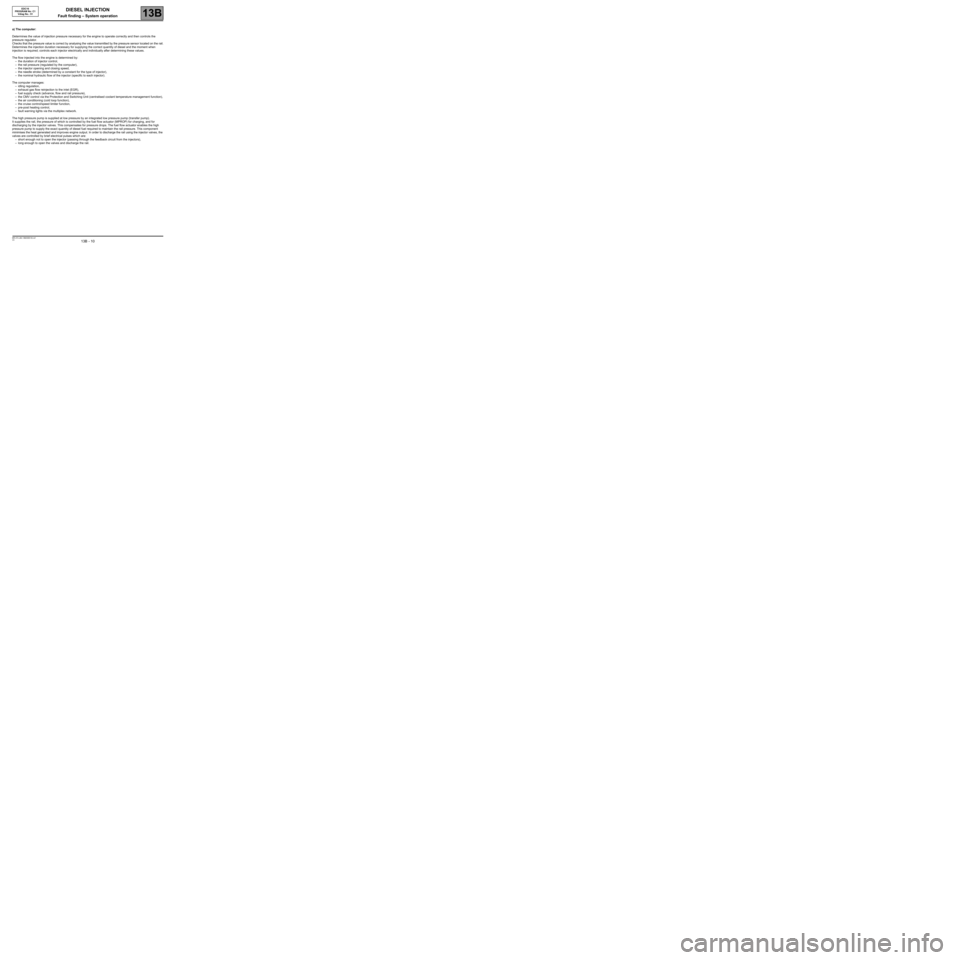
DIESEL INJECTION
Fault finding – System operation13B
13B - 10V3 MR-372-J84-13B250$135.mif
EDC16
PROGRAM No: C1
Vdiag No.: 51
a) The computer:
Determines the value of injection pressure necessary for the engine to operate correctly and then controls the
pressure regulator.
Checks that the pressure value is correct by analysing the value transmitted by the pressure sensor located on the rail.
Determines the injection duration necessary for supplying the correct quantity of diesel and the moment when
injection is required; controls each injector electrically and individually after determining these values.
The flow injected into the engine is determined by:
–the duration of injector control,
–the rail pressure (regulated by the computer),
–the injector opening and closing speed,
–the needle stroke (determined by a constant for the type of injector),
–the nominal hydraulic flow of the injector (specific to each injector).
The computer manages:
–idling regulation,
–exhaust gas flow reinjection to the inlet (EGR),
–fuel supply check (advance, flow and rail pressure),
–the CMV control via the Protection and Switching Unit (centralised coolant temperature management function),
–the air conditioning (cold loop function),
–the cruise control/speed limiter function,
–pre-post heating control,
–fault warning lights via the multiplex network.
The high pressure pump is supplied at low pressure by an integrated low pressure pump (transfer pump).
It supplies the rail, the pressure of which is controlled by the fuel flow actuator (MPROP) for charging, and for
discharging by the injector valves. This compensates for pressure drops. The fuel flow actuator enables the high
pressure pump to supply the exact quantity of diesel fuel required to maintain the rail pressure. This component
minimises the heat generated and improves engine output. In order to discharge the rail using the injector valves, the
valves are controlled by brief electrical pulses which are:
–short enough not to open the injector (passing through the feedback circuit from the injectors),
–long enough to open the valves and discharge the rail.
Page 11 of 273

DIESEL INJECTION
Fault finding – System operation13B
13B - 11V3 MR-372-J84-13B250$135.mif
EDC16
PROGRAM No: C1
Vdiag No.: 51
b) Multiplex connection between the different vehicle computers.
The electronic system fitted in this vehicle is multiplexed.
This enables dialogue between the various vehicle computers. As a result:
–the activation of the fault warning lights on the instrument panel is performed by the multiplex network, with the
vehicle speed sensor on the gearbox deactivated,
–vehicle faults are displayed by the multiplex network,
–the vehicle speed sensor on the gearbox is not needed.
The vehicle speed signal on the instrument panel is transmitted by the ABS computer via a wire connection, then
sent out on the multiplex network by the instrument panel. The vehicle speed signal is used mainly by the injection
computer and the airbag computer.
Some vehicles have adopted a sensor for detecting water in the diesel fuel, located in the filter. If there is water in the
diesel fuel, the orange "Injection and pre-post heating" warning light will come on.
The system can inject diesel fuel into the engine at a pressure of up to 1600 bar. Before each operation, check that
the injector rail is depressurised and that the fuel temperature is not too high.
You must respect the cleanliness guidelines and safety advice specified in this document for any work on the high
pressure injection system.
Removal of the internal parts of the pump and injectors is prohibited. Only the fuel flow actuator, the diesel fuel
temperature sensor and the venturi can be replaced.
For safety reasons, it is strictly prohibited to undo a high pressure pipe union when the engine is running.
It is not possible to remove the pressure sensor from the fuel rail because this may cause circuit contamination
faults. If the pressure sensor fails, the pressure sensor, the rail and the five high pressure pipes must be replaced.
It is forbidden to remove any injection pump pulley bearing the number 070 575. If the pump needs to be replaced,
replace the pulley.
Supplying + 12 V directly to any component in the system is prohibited.
Ultrasonic decoking and cleaning are prohibited.
Never start the engine unless the battery is connected correctly.
Disconnect the injection computer when carrying out any welding work on the vehicle.WARNING
The engine must not operate with:
–Diesel fuel containing more than 10 % diester,
–petrol, even in tiny quantities.
Page 14 of 273
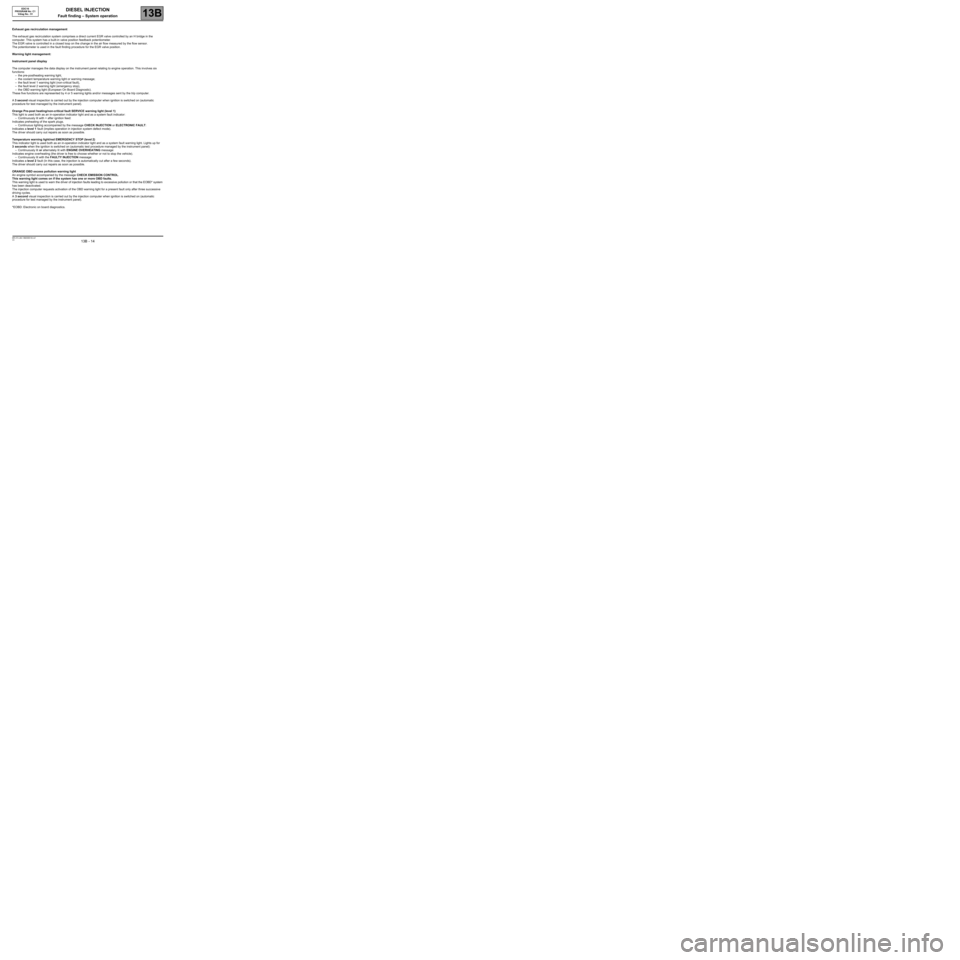
DIESEL INJECTION
Fault finding – System operation13B
13B - 14V3 MR-372-J84-13B250$135.mif
EDC16
PROGRAM No: C1
Vdiag No.: 51
Exhaust gas recirculation management
The exhaust gas recirculation system comprises a direct current EGR valve controlled by an H bridge in the
computer. This system has a built-in valve position feedback potentiometer.
The EGR valve is controlled in a closed loop on the change in the air flow measured by the flow sensor.
The potentiometer is used in the fault finding procedure for the EGR valve position.
Warning light management:
Instrument panel display
The computer manages the data display on the instrument panel relating to engine operation. This involves six
functions:
–the pre-postheating warning light,
–the coolant temperature warning light or warning message;
–the fault level 1 warning light (non-critical fault),
–the fault level 2 warning light (emergency stop),
–the OBD warning light (European On Board Diagnostic).
These five functions are represented by 4 or 5 warning lights and/or messages sent by the trip computer.
A 3 second visual inspection is carried out by the injection computer when ignition is switched on (automatic
procedure for test managed by the instrument panel).
Orange Pre-post heating/non-critical fault SERVICE warning light (level 1)
This light is used both as an in-operation indicator light and as a system fault indicator:
–Continuously lit with + after ignition feed:
Indicates preheating of the spark plugs.
–Continuous lighting accompanied by the message CHECK INJECTION or ELECTRONIC FAULT:
Indicates a level 1 fault (implies operation in injection system defect mode).
The driver should carry out repairs as soon as possible.
Temperature warning light/red EMERGENCY STOP (level 2)
This indicator light is used both as an in-operation indicator light and as a system fault warning light. Lights up for
3 seconds when the ignition is switched on (automatic test procedure managed by the instrument panel):
–Continuously lit or alternately lit with ENGINE OVERHEATING message:
Indicates engine overheating (the driver is free to choose whether or not to stop the vehicle).
–Continuously lit with the FAULTY INJECTION message:
Indicates a level 2 fault (In this case, the injection is automatically cut after a few seconds).
The driver should carry out repairs as soon as possible.
ORANGE OBD excess pollution warning light
An engine symbol accompanied by the message CHECK EMISSION CONTROL.
This warning light comes on if the system has one or more OBD faults.
This warning light is used to warn the driver of injection faults leading to excessive pollution or that the EOBD* system
has been deactivated.
The injection computer requests activation of the OBD warning light for a present fault only after three successive
driving cycles.
A 3 second visual inspection is carried out by the injection computer when ignition is switched on (automatic
procedure for test managed by the instrument panel).
*EOBD: Electronic on board diagnostics.
Page 15 of 273
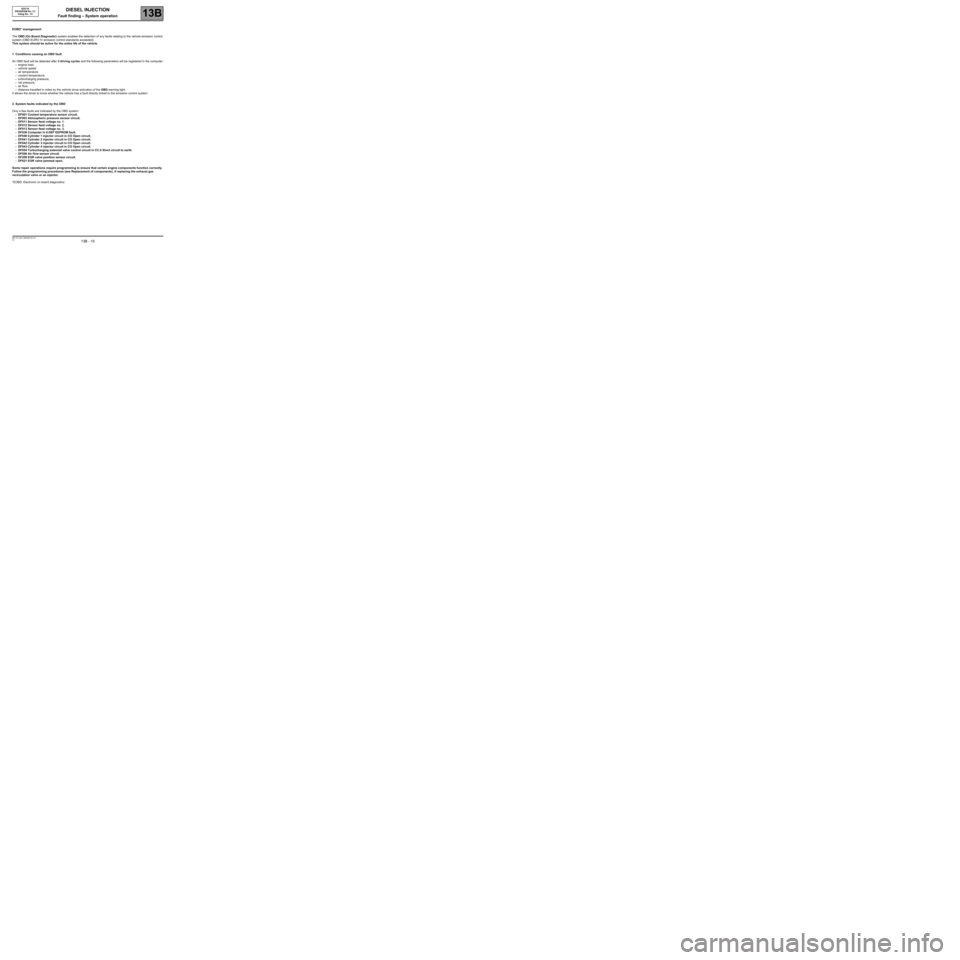
DIESEL INJECTION
Fault finding – System operation13B
13B - 15V3 MR-372-J84-13B250$135.mif
EDC16
PROGRAM No: C1
Vdiag No.: 51
EOBD* management:
The OBD (On Board Diagnostic) system enables the detection of any faults relating to the vehicle emission control
system (OBD EURO IV emission control standards exceeded).
This system should be active for the entire life of the vehicle.
1. Conditions causing an OBD fault
An OBD fault will be detected after 3 driving cycles and the following parameters will be registered in the computer:
–engine load,
–vehicle speed
–air temperature
–coolant temperature,
–turbocharging pressure,
–rail pressure,
–air flow,
–distance travelled in miles by the vehicle since activation of the OBD warning light.
It allows the driver to know whether the vehicle has a fault directly linked to the emission control system.
2. System faults indicated by the OBD
Only a few faults are indicated by the OBD system:
–DF001 Coolant temperature sensor circuit.
–DF003 Atmospheric pressure sensor circuit.
–DF011 Sensor feed voltage no. 1.
–DF012 Sensor feed voltage no. 2.
–DF013 Sensor feed voltage no. 3.
–DF038 Computer in 6.DEF EEPROM fault.
–DF040 Cylinder 1 injector circuit in CO Open circuit.
–DF041 Cylinder 2 injector circuit in CO Open circuit.
–DF042 Cylinder 3 injector circuit in CO Open circuit.
–DF043 Cylinder 4 injector circuit in CO Open circuit.
–DF054 Turbocharging solenoid valve control circuit in CC.0 Short circuit to earth.
–DF056 Air flow sensor circuit.
–DF209 EGR valve position sensor circuit.
–DF621 EGR valve jammed open.
Some repair operations require programming to ensure that certain engine components function correctly.
Follow the programming procedures (see Replacement of components), if replacing the exhaust gas
recirculation valve or an injector.
*EOBD: Electronic on board diagnostics
Page 18 of 273
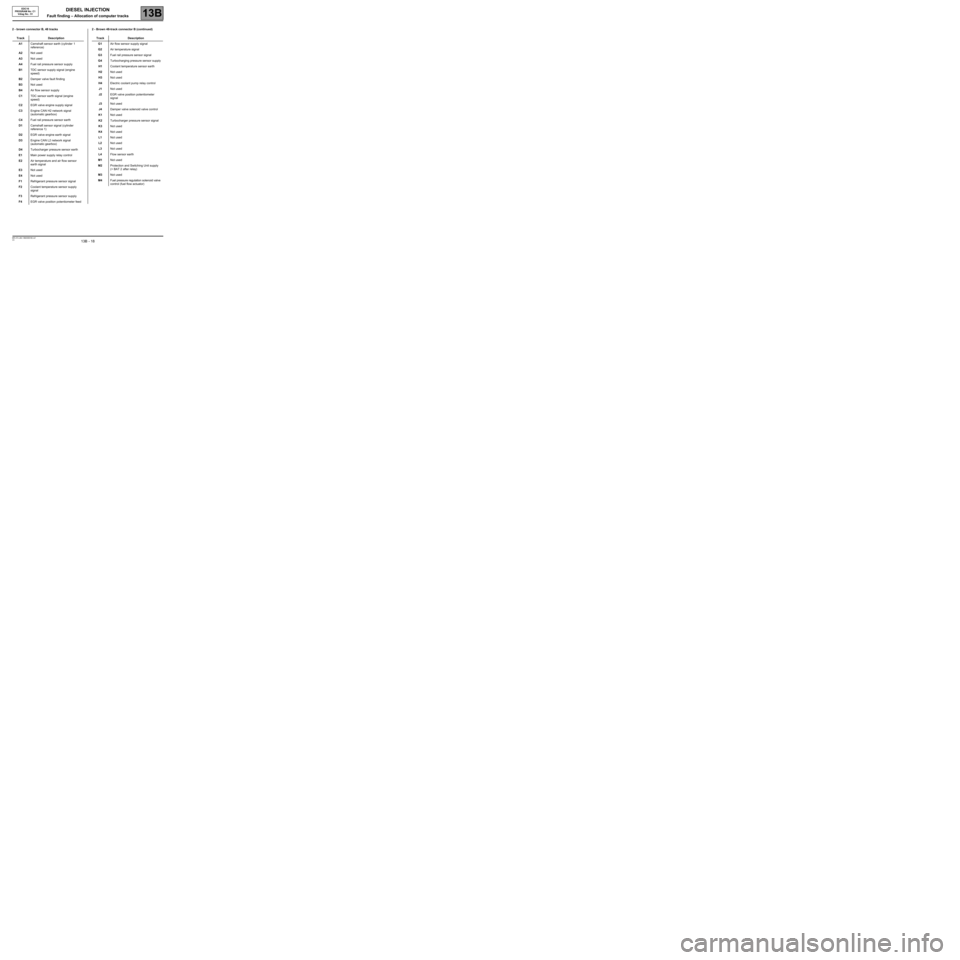
DIESEL INJECTION
Fault finding – Allocation of computer tracks13B
13B - 18V3 MR-372-J84-13B250$180.mif
EDC16
PROGRAM No: C1
Vdiag No.: 51
2 - brown connector B, 48 tracks 2 - Brown 48-track connector B (continued)
Track Description
A1Camshaft sensor earth (cylinder 1
reference)
A2Not used
A3Not used
A4Fuel rail pressure sensor supply
B1TDC sensor supply signal (engine
speed)
B2Damper valve fault finding
B3Not used
B4Air flow sensor supply
C1TDC sensor earth signal (engine
speed)
C2EGR valve engine supply signal
C3Engine CAN H2 network signal
(automatic gearbox)
C4Fuel rail pressure sensor earth
D1Camshaft sensor signal (cylinder
reference 1)
D2EGR valve engine earth signal
D3Engine CAN L2 network signal
(automatic gearbox)
D4Turbocharger pressure sensor earth
E1Main power supply relay control
E2Air temperature and air flow sensor
earth signal
E3Not used
E4Not used
F1Refrigerant pressure sensor signal
F2Coolant temperature sensor supply
signal
F3Refrigerant pressure sensor supply
F4EGR valve position potentiometer feed
Track Description
G1Air flow sensor supply signal
G2Air temperature signal
G3Fuel rail pressure sensor signal
G4Turbocharging pressure sensor supply
H1Coolant temperature sensor earth
H2Not used
H3Not used
H4Electric coolant pump relay control
J1Not used
J2EGR valve position potentiometer
signal
J3Not used
J4Damper valve solenoid valve control
K1Not used
K2Turbocharger pressure sensor signal
K3Not used
K4Not used
L1Not used
L2Not used
L3Not used
L4Flow sensor earth
M1Not used
M2Protection and Switching Unit supply
(+ BAT 2 after relay)
M3Not used
M4Fuel pressure regulation solenoid valve
control (fuel flow actuator)
Page 19 of 273
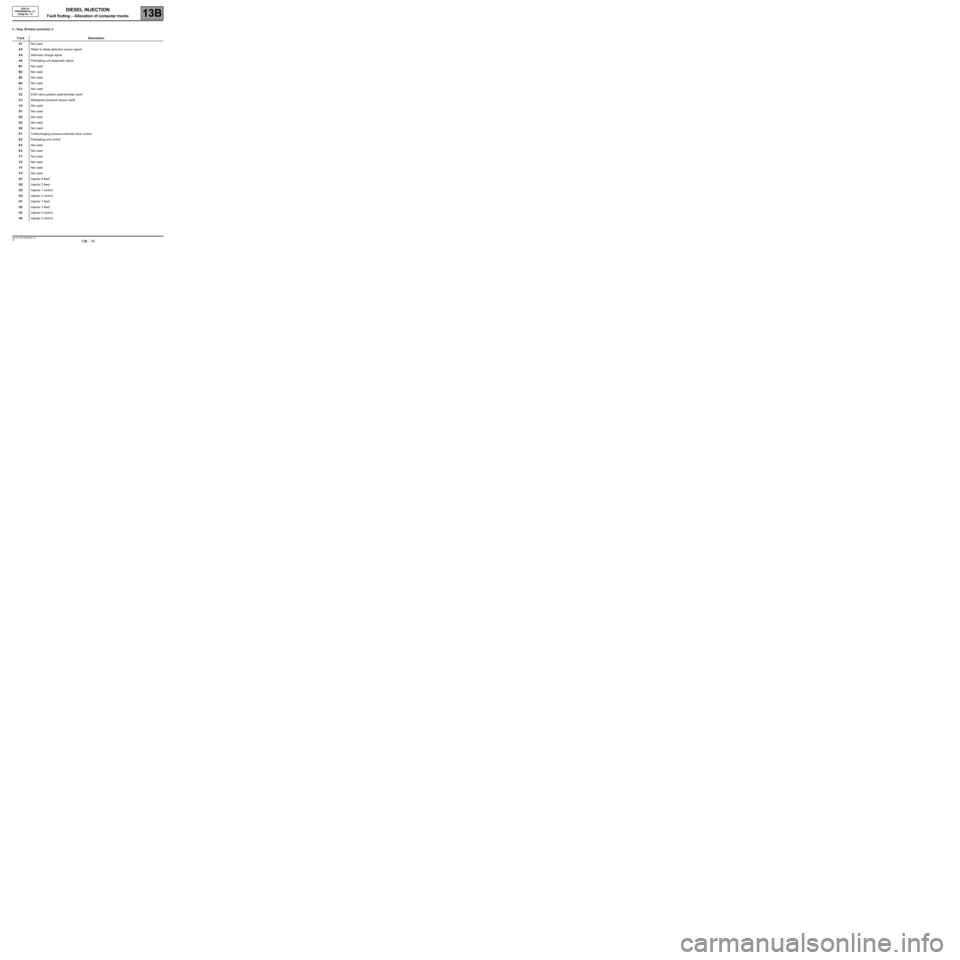
DIESEL INJECTION
Fault finding – Allocation of computer tracks13B
13B - 19V3 MR-372-J84-13B250$180.mif
EDC16
PROGRAM No: C1
Vdiag No.: 51
3 - Grey 32-track connector C
Track Description
A1Not used
A2Water in diesel detection sensor signal
A3Alternator charge signal
A4Preheating unit diagnostic signal
B1Not used
B2Not used
B3Not used
B4Not used
C1Not used
C2EGR valve position potentiometer earth
C3Refrigerant pressure sensor earth
C4Not used
D1Not used
D2Not used
D3Not used
D4Not used
E1Turbocharging pressure solenoid valve control
E2Preheating unit control
E3Not used
E4Not used
F1Not used
F2Not used
F3Not used
F4Not used
G1Injector 4 feed
G2Injector 2 feed
G3Injector 1 control
G4Injector 2 control
H1Injector 1 feed
H2Injector 3 feed
H3Injector 4 control
H4Injector 3 control
Page 25 of 273
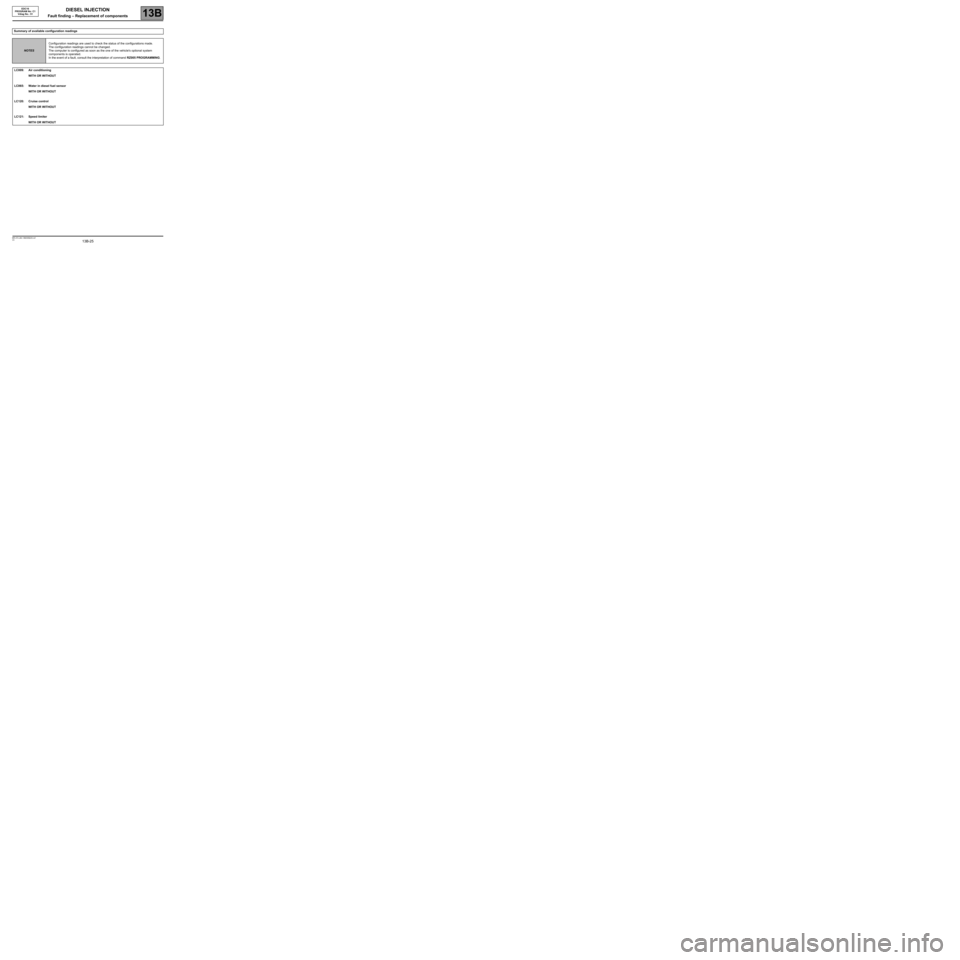
DIESEL INJECTION
Fault finding – Replacement of components13B
13B-25V3 MR-372-J84-13B250$225.mif
EDC16
PROGRAM No: C1
Vdiag No.: 51
Summary of available configuration readings
NOTESConfiguration readings are used to check the status of the configurations made.
The configuration readings cannot be changed.
The computer is configured as soon as the one of the vehicle's optional system
components is operated.
In the event of a fault, consult the interpretation of command RZ005 PROGRAMMING.
LC009: Air conditioning
WITH OR WITHOUT
LC065: Water in diesel fuel sensor
WITH OR WITHOUT
LC120: Cruise control
WITH OR WITHOUT
LC121: Speed limiter
WITH OR WITHOUT
Page 26 of 273
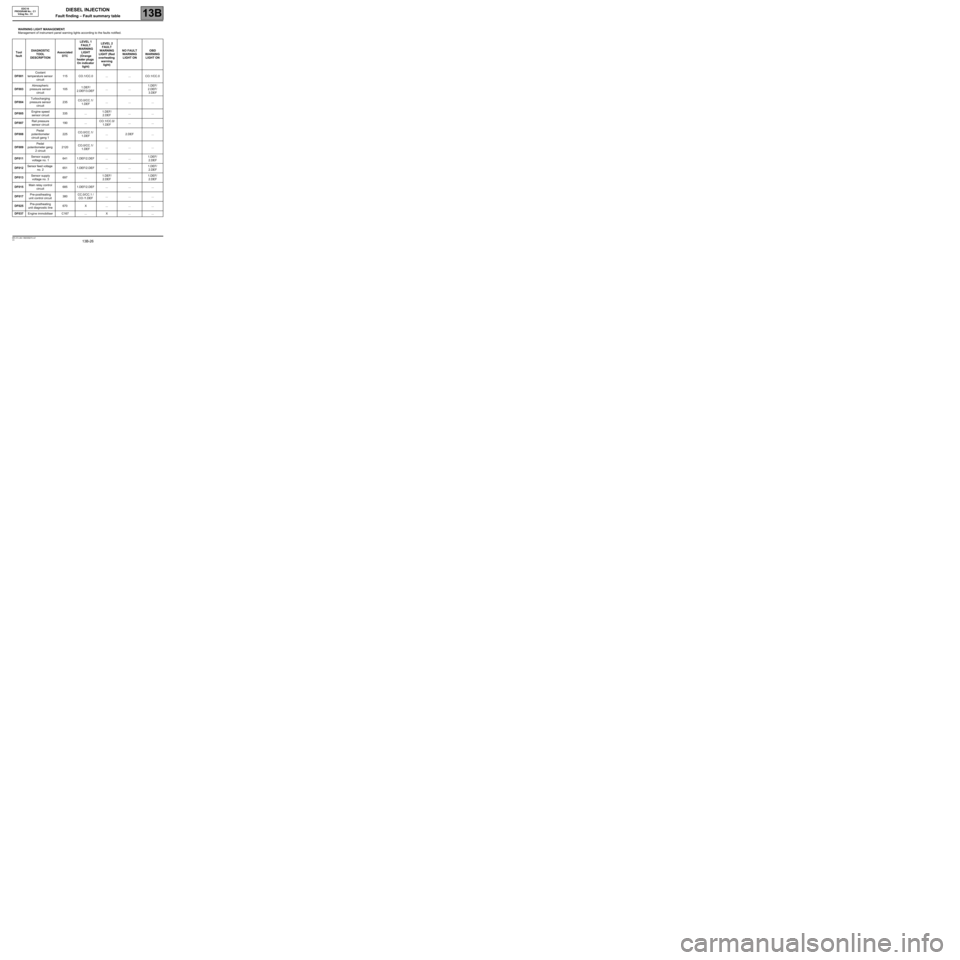
DIESEL INJECTION
Fault finding – Fault summary table13B
13B-26V3 MR-372-J84-13B250$270.mif
EDC16
PROGRAM No.: C1
Vdiag No.: 51DIESEL INJECTION
Fault finding – Fault summary table
WARNING LIGHT MANAGEMENT:
Management of instrument panel warning lights according to the faults notified.
Tool
faultDIAGNOSTIC
TOOL
DESCRIPTIONAssociated
DTCLEVEL 1
FAULT
WARNING
LIGHT
(Orange
heater plugs
On indicator
light)LEVEL 2
FAULT
WARNING
LIGHT (Red
overheating
warning
light)NO FAULT
WARNING
LIGHT ONOBD
WARNING
LIGHT ON
DF001Coolant
temperature sensor
circuit115 CO.1/CC.0 ... ... CO.1/CC.0
DF003Atmospheric
pressure sensor
circuit1051.DEF/
2.DEF/3.DEF... ...1.DEF/
2.DEF/
3.DEF
DF004Turbocharging
pressure sensor
circuit235CO.0/CC.1/
1.DEF... ... ...
DF005Engine speed
sensor circuit335 ...1.DEF/
2.DEF... ...
DF007Rail pressure
sensor circuit190 ...CO.1/CC.0/
1.DEF... ...
DF008Pedal
potentiometer
circuit gang 1225CO.0/CC.1/
1.DEF... 2.DEF ...
DF009Pedal
potentiometer gang
2 circuit2120CO.0/CC.1/
1.DEF... ... ...
DF011Sensor supply
voltage no. 1641 1.DEF/2.DEF ... ...1.DEF/
2.DEF
DF012Sensor feed voltage
no. 2651 1.DEF/2.DEF ... ...1.DEF/
2.DEF
DF013Sensor supply
voltage no. 3697 ...1.DEF/
2.DEF...1.DEF/
2.DEF
DF015Main relay control
circuit685 1.DEF/2.DEF ... ... ...
DF017Pre-postheating
unit control circuit380CC.0/CC.1 /
CO /1.DEF... ... ...
DF025Pre-postheating
unit diagnostic line670 X ... ... ...
DF037Engine immobiliser C167 ... X ... ...