filter RENAULT SCENIC 2011 J95 / 3.G Engine And Peripherals EDC16C36 Workshop Manual
[x] Cancel search | Manufacturer: RENAULT, Model Year: 2011, Model line: SCENIC, Model: RENAULT SCENIC 2011 J95 / 3.GPages: 431, PDF Size: 2.03 MB
Page 8 of 431
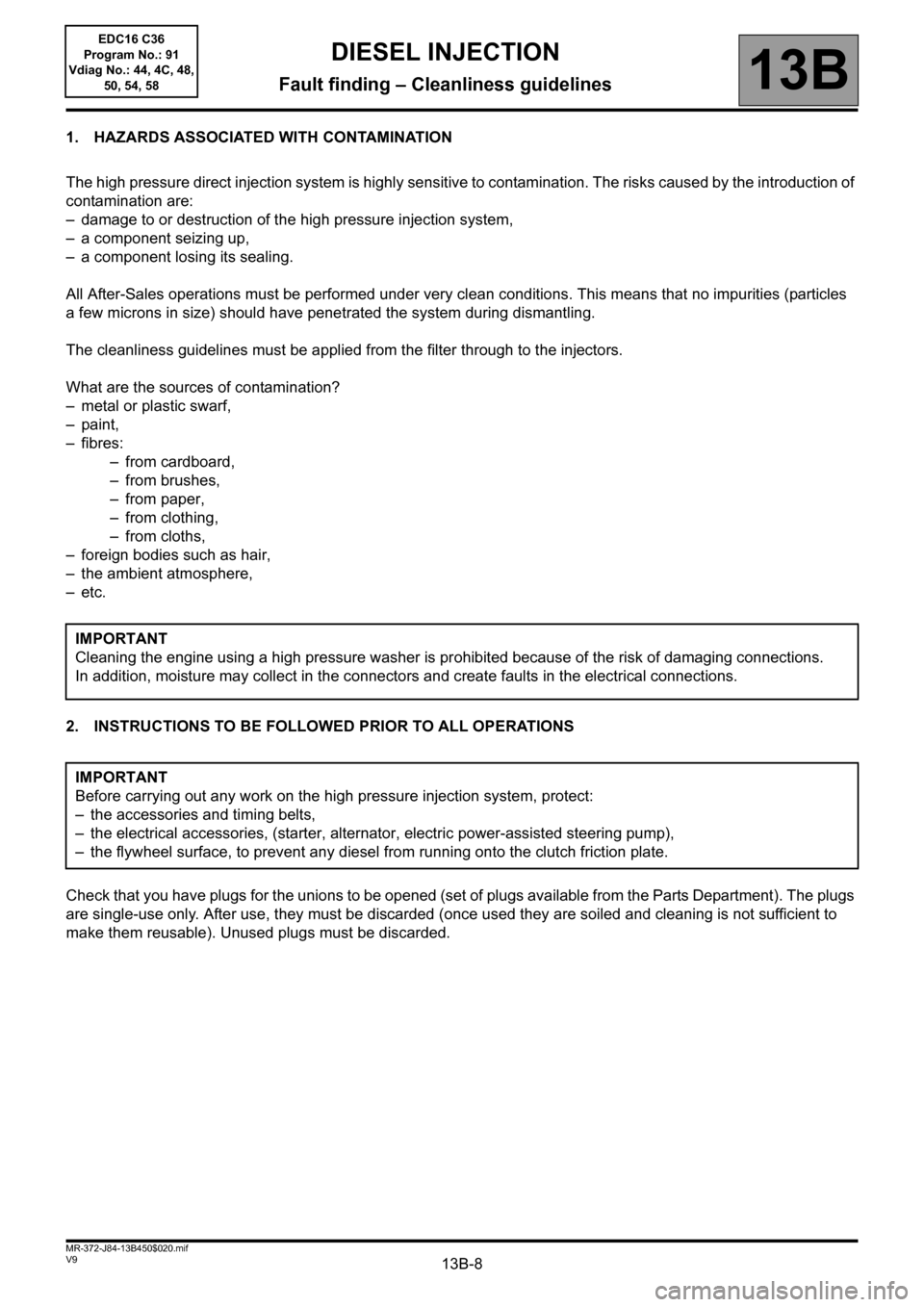
13B-8V9 MR-372-J84-13B450$020.mif
13B
EDC16 C36
Program No.: 91
Vdiag No.: 44, 4C, 48,
50, 54, 58
1. HAZARDS ASSOCIATED WITH CONTAMINATION
The high pressure direct injection system is highly sensitive to contamination. The risks caused by the introduction of
contamination are:
– damage to or destruction of the high pressure injection system,
– a component seizing up,
– a component losing its sealing.
All After-Sales operations must be performed under very clean conditions. This means that no impurities (particles
a few microns in size) should have penetrated the system during dismantling.
The cleanliness guidelines must be applied from the filter through to the injectors.
What are the sources of contamination?
– metal or plastic swarf,
– paint,
–fibres:
– from cardboard,
– from brushes,
– from paper,
– from clothing,
– from cloths,
– foreign bodies such as hair,
– the ambient atmosphere,
–etc.
2. INSTRUCTIONS TO BE FOLLOWED PRIOR TO ALL OPERATIONS
Check that you have plugs for the unions to be opened (set of plugs available from the Parts Department). The plugs
are single-use only. After use, they must be discarded (once used they are soiled and cleaning is not sufficient to
make them reusable). Unused plugs must be discarded.IMPORTANT
Cleaning the engine using a high pressure washer is prohibited because of the risk of damaging connections.
In addition, moisture may collect in the connectors and create faults in the electrical connections.
IMPORTANT
Before carrying out any work on the high pressure injection system, protect:
– the accessories and timing belts,
– the electrical accessories, (starter, alternator, electric power-assisted steering pump),
– the flywheel surface, to prevent any diesel from running onto the clutch friction plate.
DIESEL INJECTION
Fault finding – Cleanliness guidelines
Page 10 of 431
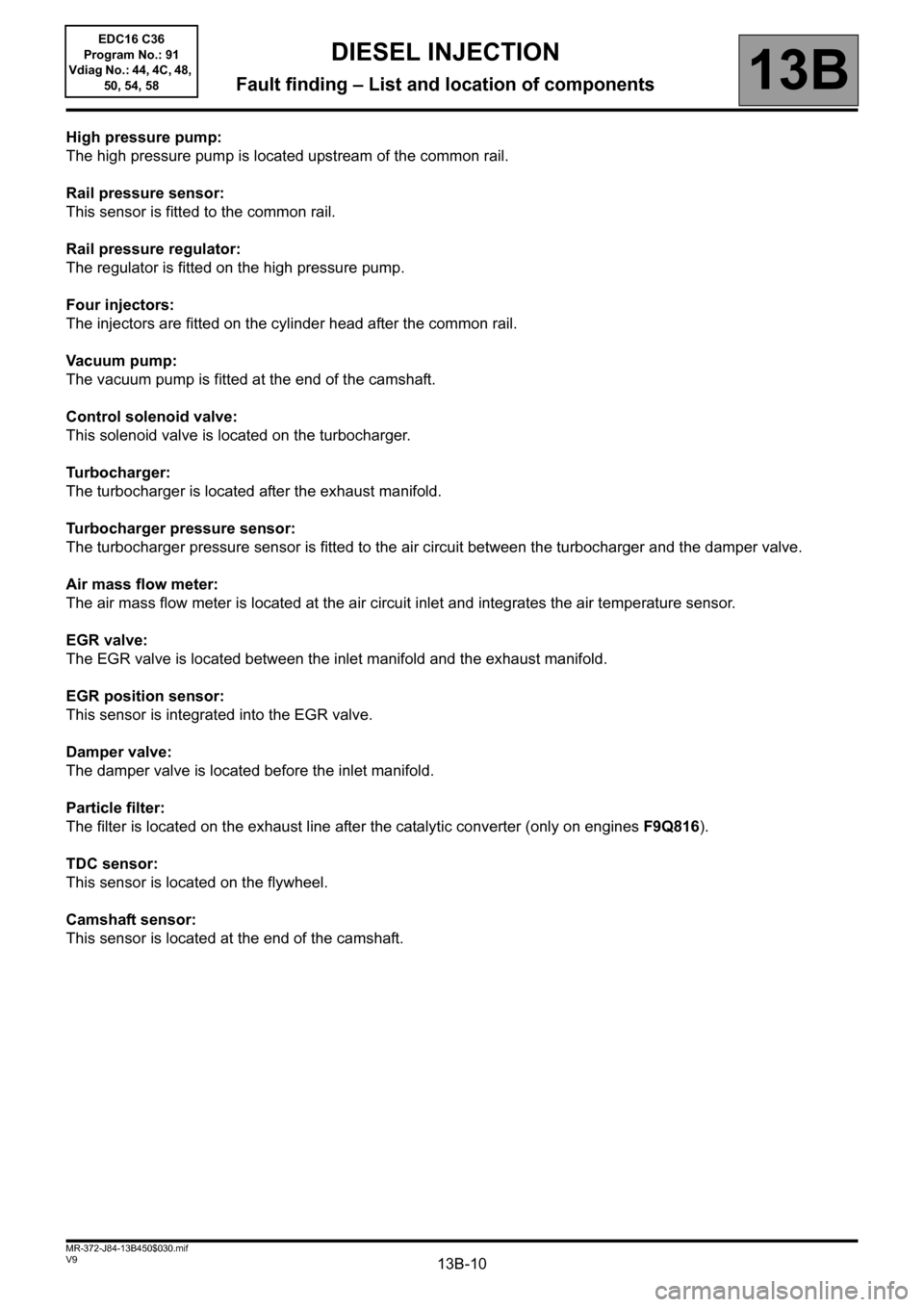
13B-10V9 MR-372-J84-13B450$030.mif
13B
EDC16 C36
Program No.: 91
Vdiag No.: 44, 4C, 48,
50, 54, 58
High pressure pump:
The high pressure pump is located upstream of the common rail.
Rail pressure sensor:
This sensor is fitted to the common rail.
Rail pressure regulator:
The regulator is fitted on the high pressure pump.
Four injectors:
The injectors are fitted on the cylinder head after the common rail.
Vacuum pump:
The vacuum pump is fitted at the end of the camshaft.
Control solenoid valve:
This solenoid valve is located on the turbocharger.
Turbocharger:
The turbocharger is located after the exhaust manifold.
Turbocharger pressure sensor:
The turbocharger pressure sensor is fitted to the air circuit between the turbocharger and the damper valve.
Air mass flow meter:
The air mass flow meter is located at the air circuit inlet and integrates the air temperature sensor.
EGR valve:
The EGR valve is located between the inlet manifold and the exhaust manifold.
EGR position sensor:
This sensor is integrated into the EGR valve.
Damper valve:
The damper valve is located before the inlet manifold.
Particle filter:
The filter is located on the exhaust line after the catalytic converter (only on engines F9Q816).
TDC sensor:
This sensor is located on the flywheel.
Camshaft sensor:
This sensor is located at the end of the camshaft.
DIESEL INJECTION
Fault finding – List and location of components
Page 11 of 431
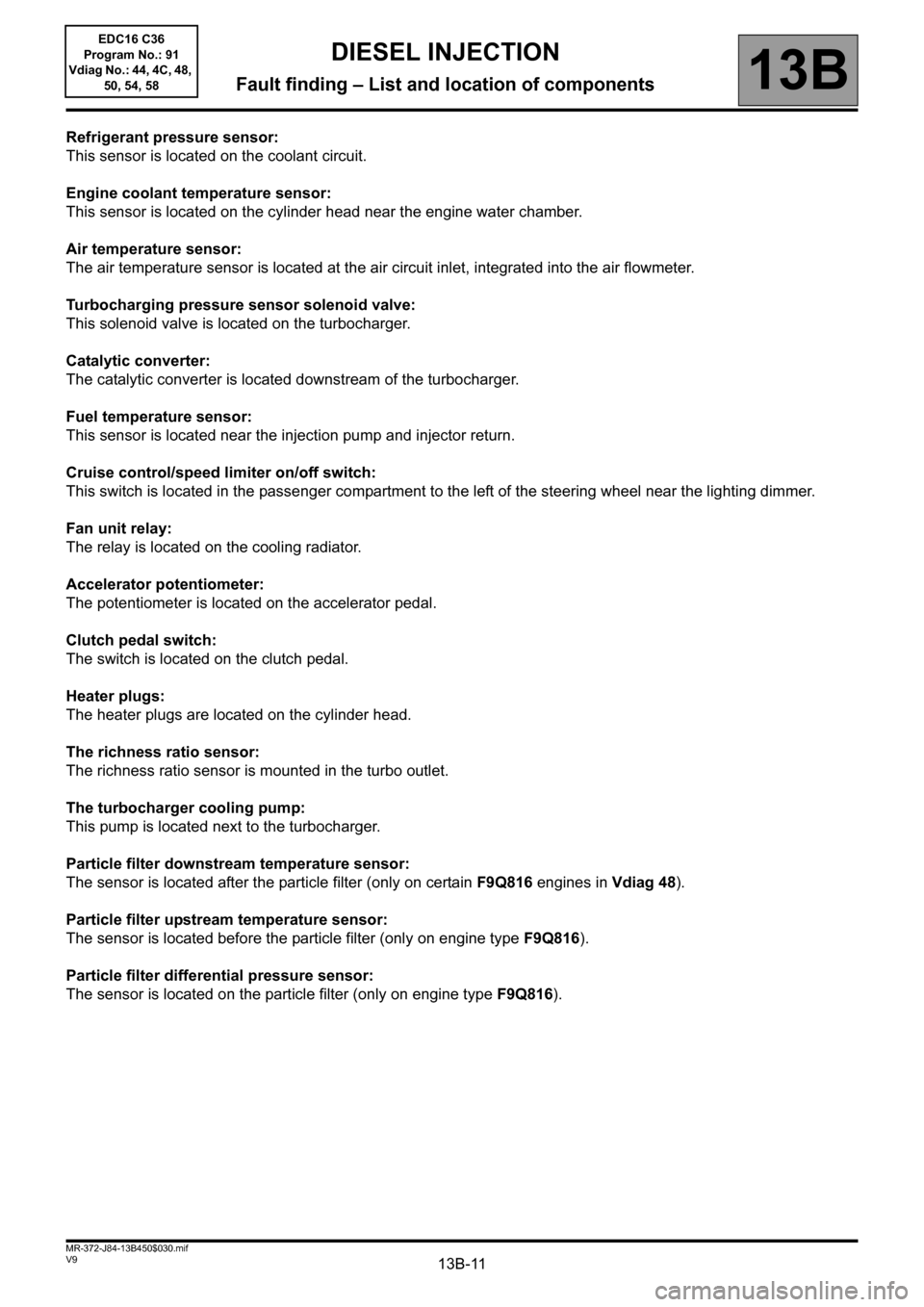
13B-11V9 MR-372-J84-13B450$030.mif
DIESEL INJECTION
Fault finding – List and location of components13B
EDC16 C36
Program No.: 91
Vdiag No.: 44, 4C, 48,
50, 54, 58
Refrigerant pressure sensor:
This sensor is located on the coolant circuit.
Engine coolant temperature sensor:
This sensor is located on the cylinder head near the engine water chamber.
Air temperature sensor:
The air temperature sensor is located at the air circuit inlet, integrated into the air flowmeter.
Turbocharging pressure sensor solenoid valve:
This solenoid valve is located on the turbocharger.
Catalytic converter:
The catalytic converter is located downstream of the turbocharger.
Fuel temperature sensor:
This sensor is located near the injection pump and injector return.
Cruise control/speed limiter on/off switch:
This switch is located in the passenger compartment to the left of the steering wheel near the lighting dimmer.
Fan unit relay:
The relay is located on the cooling radiator.
Accelerator potentiometer:
The potentiometer is located on the accelerator pedal.
Clutch pedal switch:
The switch is located on the clutch pedal.
Heater plugs:
The heater plugs are located on the cylinder head.
The richness ratio sensor:
The richness ratio sensor is mounted in the turbo outlet.
The turbocharger cooling pump:
This pump is located next to the turbocharger.
Particle filter downstream temperature sensor:
The sensor is located after the particle filter (only on certain F9Q816 engines in Vdiag 48).
Particle filter upstream temperature sensor:
The sensor is located before the particle filter (only on engine type F9Q816).
Particle filter differential pressure sensor:
The sensor is located on the particle filter (only on engine type F9Q816).
Page 12 of 431
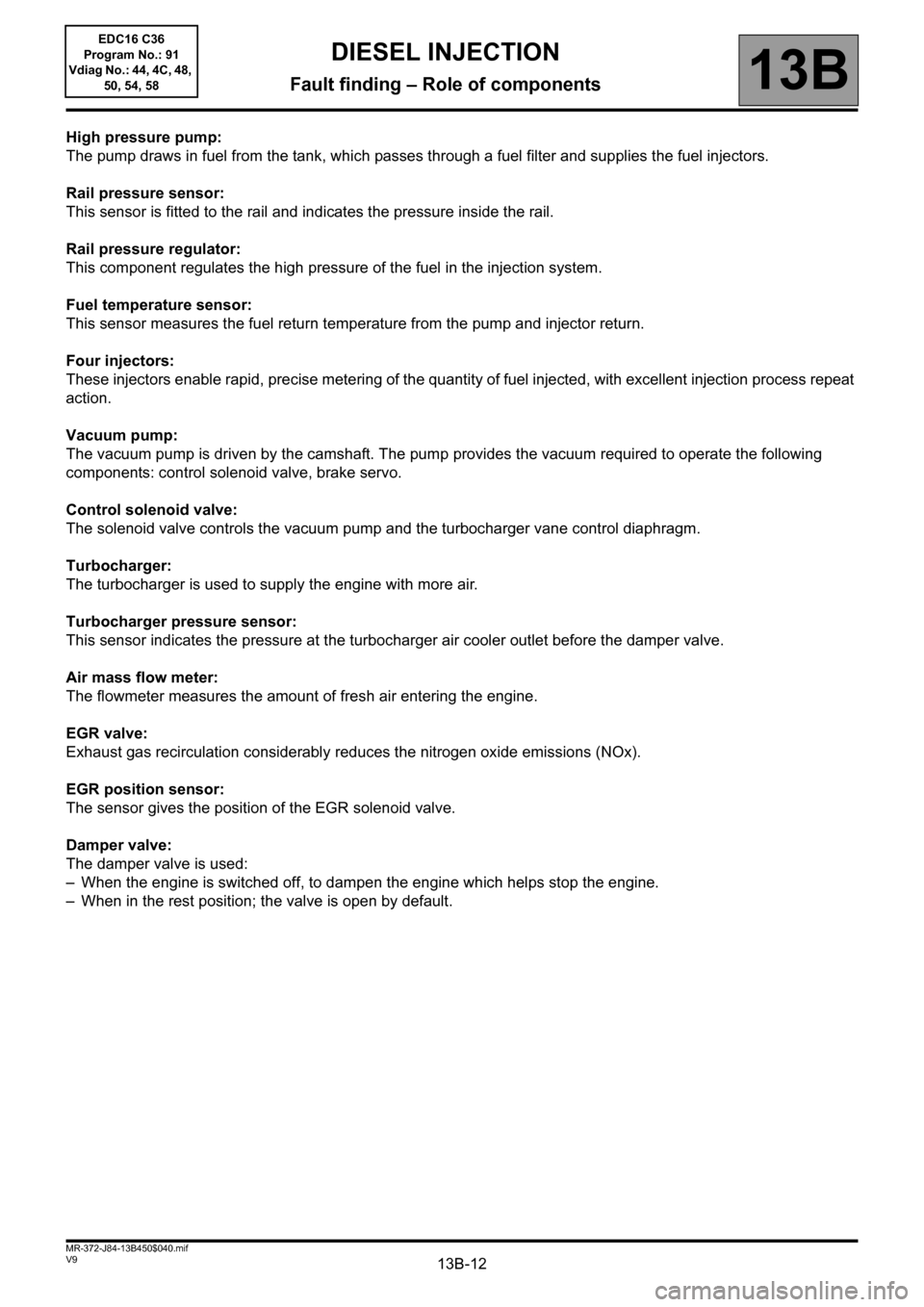
13B-12V9 MR-372-J84-13B450$040.mif
13B
EDC16 C36
Program No.: 91
Vdiag No.: 44, 4C, 48,
50, 54, 58
High pressure pump:
The pump draws in fuel from the tank, which passes through a fuel filter and supplies the fuel injectors.
Rail pressure sensor:
This sensor is fitted to the rail and indicates the pressure inside the rail.
Rail pressure regulator:
This component regulates the high pressure of the fuel in the injection system.
Fuel temperature sensor:
This sensor measures the fuel return temperature from the pump and injector return.
Four injectors:
These injectors enable rapid, precise metering of the quantity of fuel injected, with excellent injection process repeat
action.
Vacuum pump:
The vacuum pump is driven by the camshaft. The pump provides the vacuum required to operate the following
components: control solenoid valve, brake servo.
Control solenoid valve:
The solenoid valve controls the vacuum pump and the turbocharger vane control diaphragm.
Turbocharger:
The turbocharger is used to supply the engine with more air.
Turbocharger pressure sensor:
This sensor indicates the pressure at the turbocharger air cooler outlet before the damper valve.
Air mass flow meter:
The flowmeter measures the amount of fresh air entering the engine.
EGR valve:
Exhaust gas recirculation considerably reduces the nitrogen oxide emissions (NOx).
EGR position sensor:
The sensor gives the position of the EGR solenoid valve.
Damper valve:
The damper valve is used:
– When the engine is switched off, to dampen the engine which helps stop the engine.
– When in the rest position; the valve is open by default.
DIESEL INJECTION
Fault finding – Role of components
Page 13 of 431
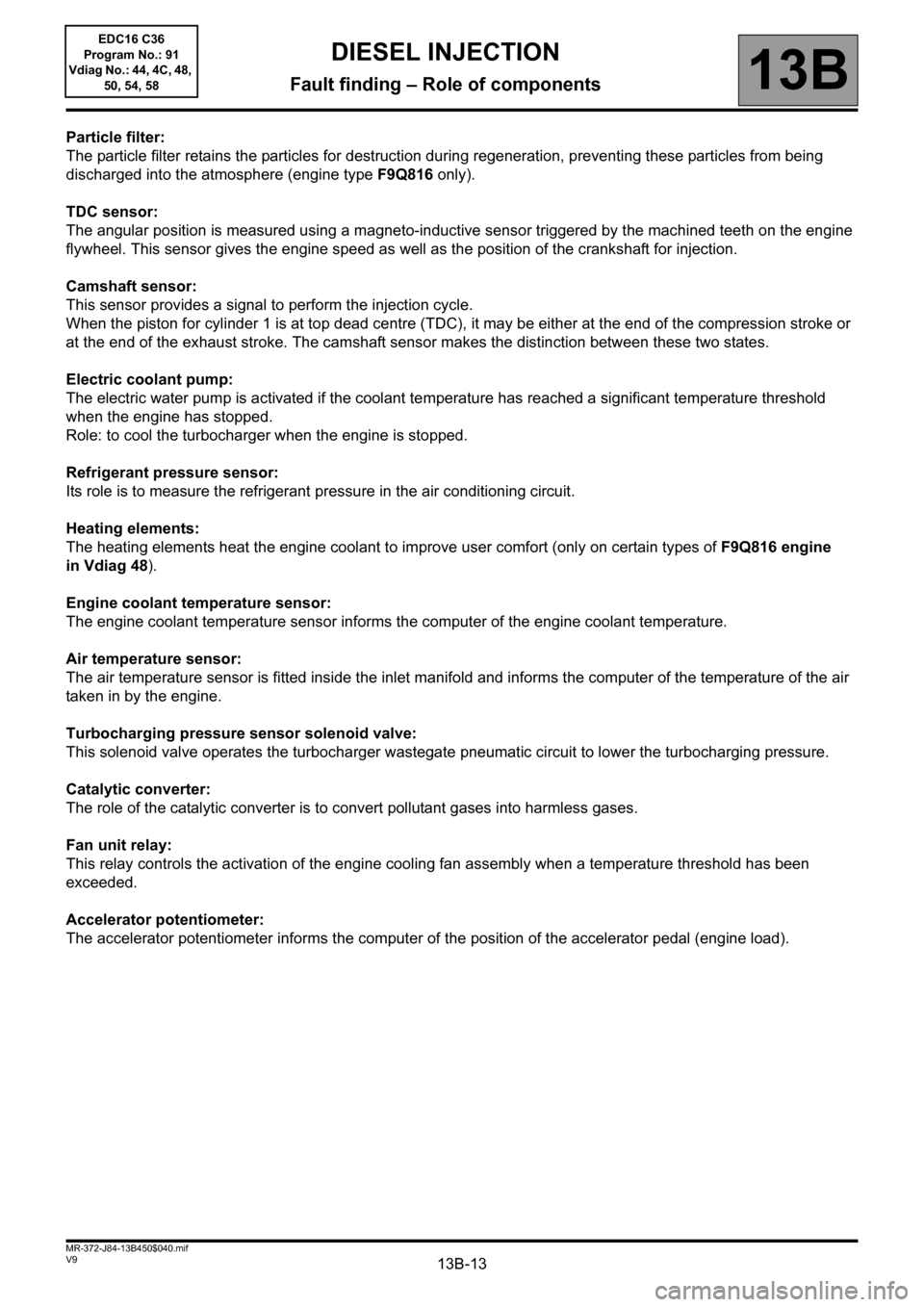
13B-13V9 MR-372-J84-13B450$040.mif
DIESEL INJECTION
Fault finding – Role of components13B
EDC16 C36
Program No.: 91
Vdiag No.: 44, 4C, 48,
50, 54, 58
Particle filter:
The particle filter retains the particles for destruction during regeneration, preventing these particles from being
discharged into the atmosphere (engine type F9Q816 only).
TDC sensor:
The angular position is measured using a magneto-inductive sensor triggered by the machined teeth on the engine
flywheel. This sensor gives the engine speed as well as the position of the crankshaft for injection.
Camshaft sensor:
This sensor provides a signal to perform the injection cycle.
When the piston for cylinder 1 is at top dead centre (TDC), it may be either at the end of the compression stroke or
at the end of the exhaust stroke. The camshaft sensor makes the distinction between these two states.
Electric coolant pump:
The electric water pump is activated if the coolant temperature has reached a significant temperature threshold
when the engine has stopped.
Role: to cool the turbocharger when the engine is stopped.
Refrigerant pressure sensor:
Its role is to measure the refrigerant pressure in the air conditioning circuit.
Heating elements:
The heating elements heat the engine coolant to improve user comfort (only on certain types of F9Q816 engine
in Vdiag 48).
Engine coolant temperature sensor:
The engine coolant temperature sensor informs the computer of the engine coolant temperature.
Air temperature sensor:
The air temperature sensor is fitted inside the inlet manifold and informs the computer of the temperature of the air
taken in by the engine.
Turbocharging pressure sensor solenoid valve:
This solenoid valve operates the turbocharger wastegate pneumatic circuit to lower the turbocharging pressure.
Catalytic converter:
The role of the catalytic converter is to convert pollutant gases into harmless gases.
Fan unit relay:
This relay controls the activation of the engine cooling fan assembly when a temperature threshold has been
exceeded.
Accelerator potentiometer:
The accelerator potentiometer informs the computer of the position of the accelerator pedal (engine load).
Page 14 of 431
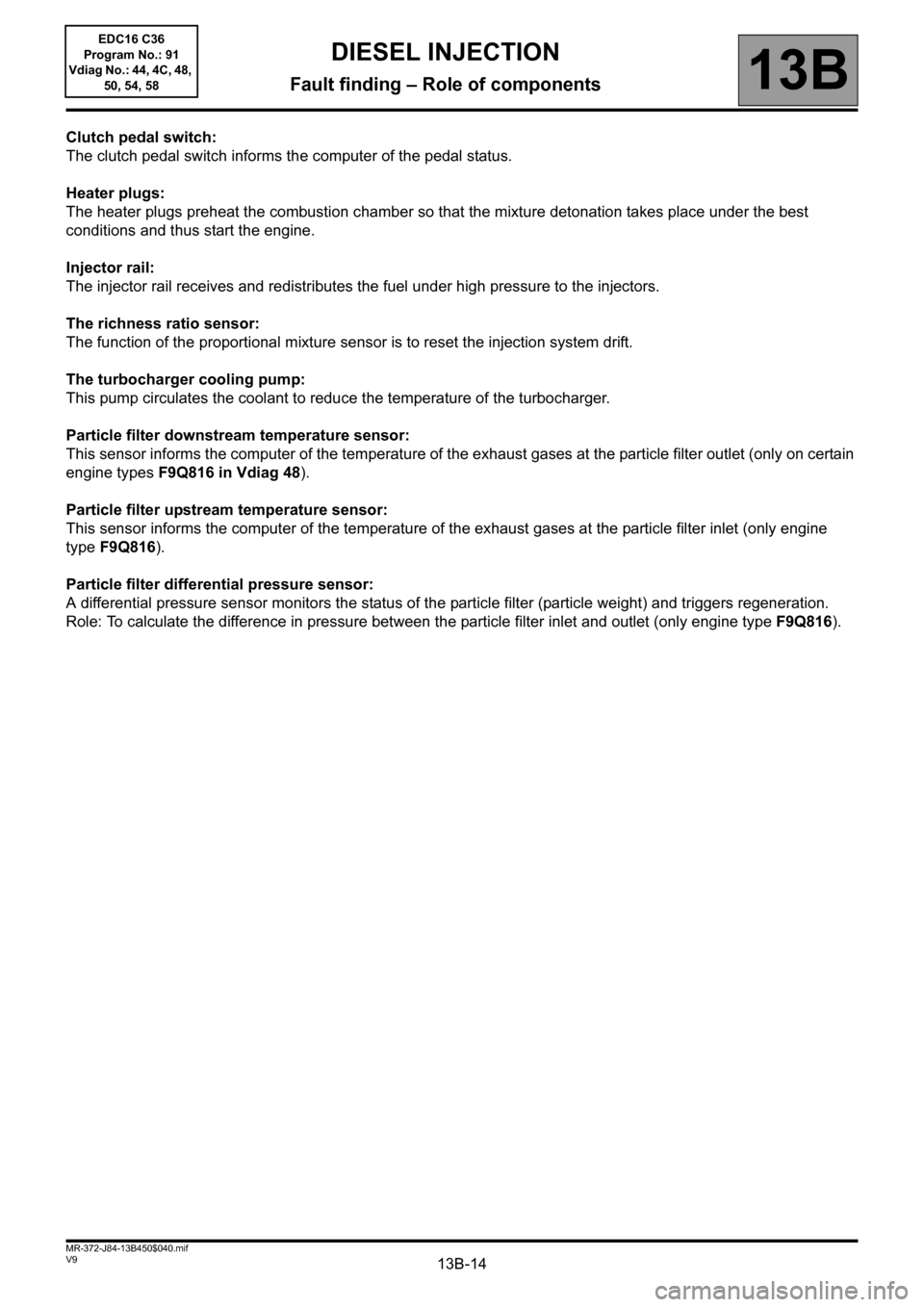
13B-14V9 MR-372-J84-13B450$040.mif
DIESEL INJECTION
Fault finding – Role of components13B
EDC16 C36
Program No.: 91
Vdiag No.: 44, 4C, 48,
50, 54, 58
Clutch pedal switch:
The clutch pedal switch informs the computer of the pedal status.
Heater plugs:
The heater plugs preheat the combustion chamber so that the mixture detonation takes place under the best
conditions and thus start the engine.
Injector rail:
The injector rail receives and redistributes the fuel under high pressure to the injectors.
The richness ratio sensor:
The function of the proportional mixture sensor is to reset the injection system drift.
The turbocharger cooling pump:
This pump circulates the coolant to reduce the temperature of the turbocharger.
Particle filter downstream temperature sensor:
This sensor informs the computer of the temperature of the exhaust gases at the particle filter outlet (only on certain
engine types F9Q816 in Vdiag 48).
Particle filter upstream temperature sensor:
This sensor informs the computer of the temperature of the exhaust gases at the particle filter inlet (only engine
typeF9Q816).
Particle filter differential pressure sensor:
A differential pressure sensor monitors the status of the particle filter (particle weight) and triggers regeneration.
Role: To calculate the difference in pressure between the particle filter inlet and outlet (only engine type F9Q816).
Page 15 of 431
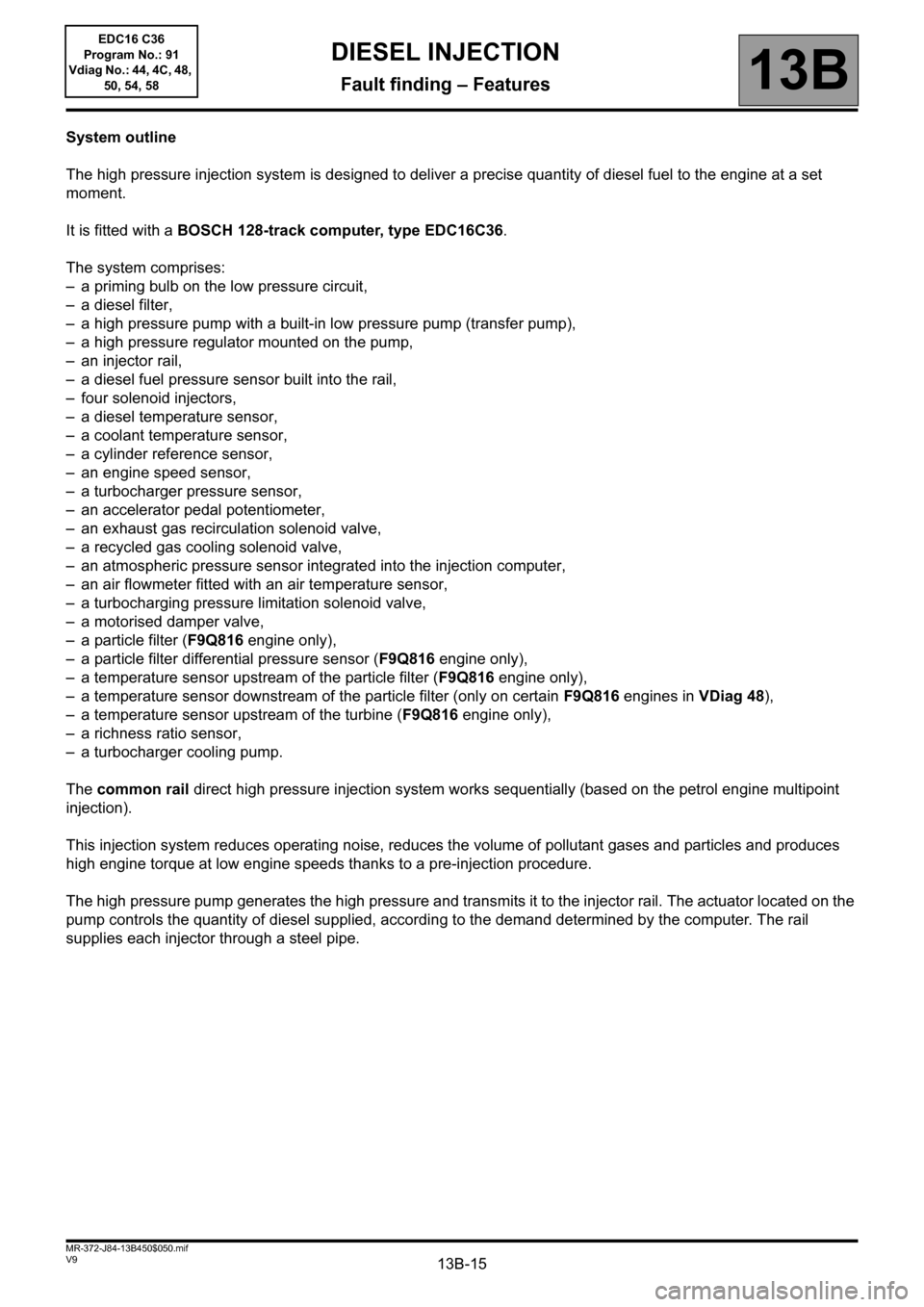
13B-15V9 MR-372-J84-13B450$050.mif
13B
EDC16 C36
Program No.: 91
Vdiag No.: 44, 4C, 48,
50, 54, 58
System outline
The high pressure injection system is designed to deliver a precise quantity of diesel fuel to the engine at a set
moment.
It is fitted with a BOSCH 128-track computer, type EDC16C36.
The system comprises:
– a priming bulb on the low pressure circuit,
– a diesel filter,
– a high pressure pump with a built-in low pressure pump (transfer pump),
– a high pressure regulator mounted on the pump,
– an injector rail,
– a diesel fuel pressure sensor built into the rail,
– four solenoid injectors,
– a diesel temperature sensor,
– a coolant temperature sensor,
– a cylinder reference sensor,
– an engine speed sensor,
– a turbocharger pressure sensor,
– an accelerator pedal potentiometer,
– an exhaust gas recirculation solenoid valve,
– a recycled gas cooling solenoid valve,
– an atmospheric pressure sensor integrated into the injection computer,
– an air flowmeter fitted with an air temperature sensor,
– a turbocharging pressure limitation solenoid valve,
– a motorised damper valve,
– a particle filter (F9Q816 engine only),
– a particle filter differential pressure sensor (F9Q816 engine only),
– a temperature sensor upstream of the particle filter (F9Q816 engine only),
– a temperature sensor downstream of the particle filter (only on certain F9Q816 engines in VDiag 48),
– a temperature sensor upstream of the turbine (F9Q816 engine only),
– a richness ratio sensor,
– a turbocharger cooling pump.
The common rail direct high pressure injection system works sequentially (based on the petrol engine multipoint
injection).
This injection system reduces operating noise, reduces the volume of pollutant gases and particles and produces
high engine torque at low engine speeds thanks to a pre-injection procedure.
The high pressure pump generates the high pressure and transmits it to the injector rail. The actuator located on the
pump controls the quantity of diesel supplied, according to the demand determined by the computer. The rail
supplies each injector through a steel pipe.
DIESEL INJECTION
Fault finding – Features
Page 16 of 431
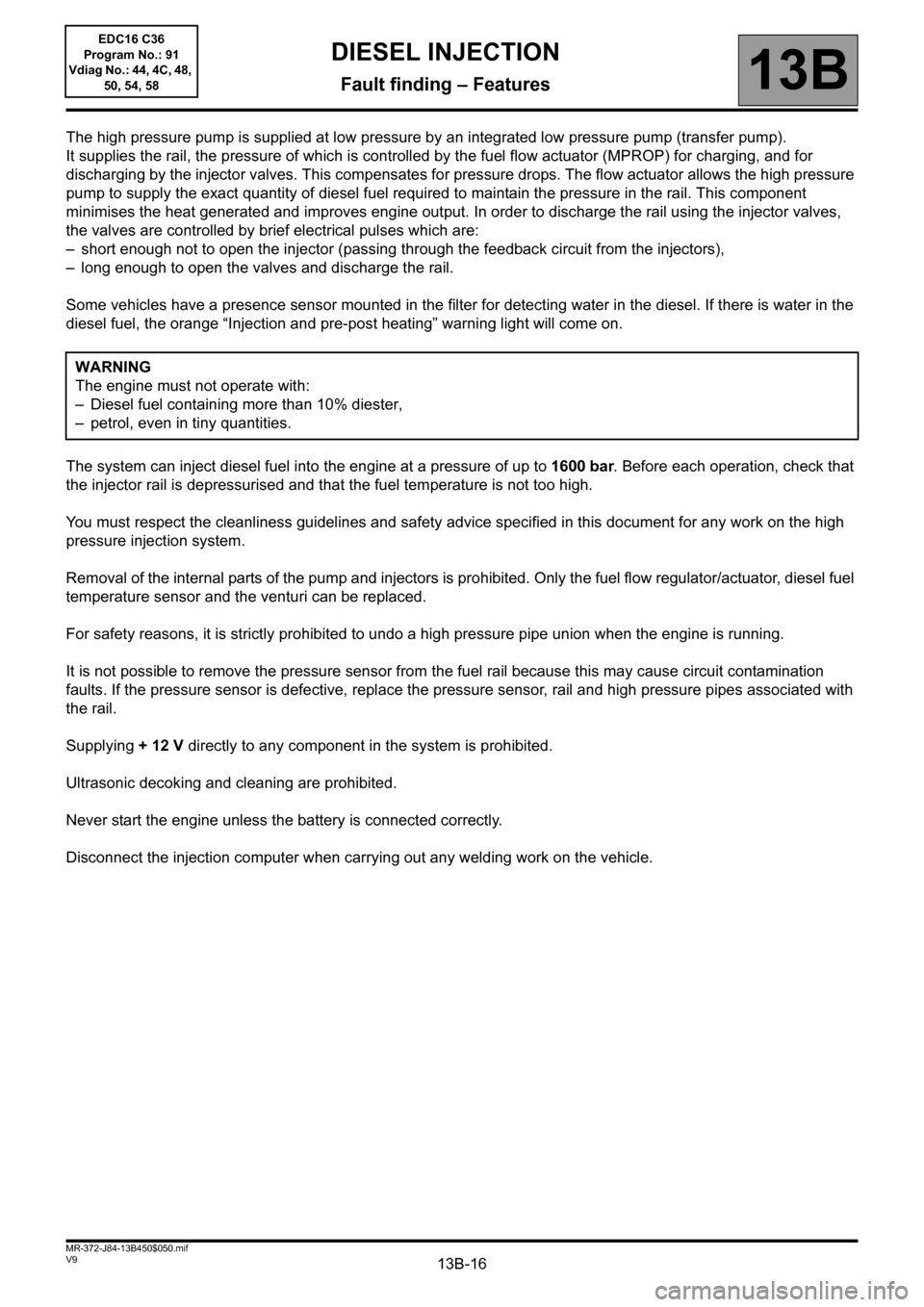
13B-16V9 MR-372-J84-13B450$050.mif
DIESEL INJECTION
Fault finding – Features13B
EDC16 C36
Program No.: 91
Vdiag No.: 44, 4C, 48,
50, 54, 58
The high pressure pump is supplied at low pressure by an integrated low pressure pump (transfer pump).
It supplies the rail, the pressure of which is controlled by the fuel flow actuator (MPROP) for charging, and for
discharging by the injector valves. This compensates for pressure drops. The flow actuator allows the high pressure
pump to supply the exact quantity of diesel fuel required to maintain the pressure in the rail. This component
minimises the heat generated and improves engine output. In order to discharge the rail using the injector valves,
the valves are controlled by brief electrical pulses which are:
– short enough not to open the injector (passing through the feedback circuit from the injectors),
– long enough to open the valves and discharge the rail.
Some vehicles have a presence sensor mounted in the filter for detecting water in the diesel. If there is water in the
diesel fuel, the orange “Injection and pre-post heating” warning light will come on.
The system can inject diesel fuel into the engine at a pressure of up to 1600 bar. Before each operation, check that
the injector rail is depressurised and that the fuel temperature is not too high.
You must respect the cleanliness guidelines and safety advice specified in this document for any work on the high
pressure injection system.
Removal of the internal parts of the pump and injectors is prohibited. Only the fuel flow regulator/actuator, diesel fuel
temperature sensor and the venturi can be replaced.
For safety reasons, it is strictly prohibited to undo a high pressure pipe union when the engine is running.
It is not possible to remove the pressure sensor from the fuel rail because this may cause circuit contamination
faults. If the pressure sensor is defective, replace the pressure sensor, rail and high pressure pipes associated with
the rail.
Supplying + 12 V directly to any component in the system is prohibited.
Ultrasonic decoking and cleaning are prohibited.
Never start the engine unless the battery is connected correctly.
Disconnect the injection computer when carrying out any welding work on the vehicle. WARNING
The engine must not operate with:
– Diesel fuel containing more than 10% diester,
– petrol, even in tiny quantities.
Page 17 of 431
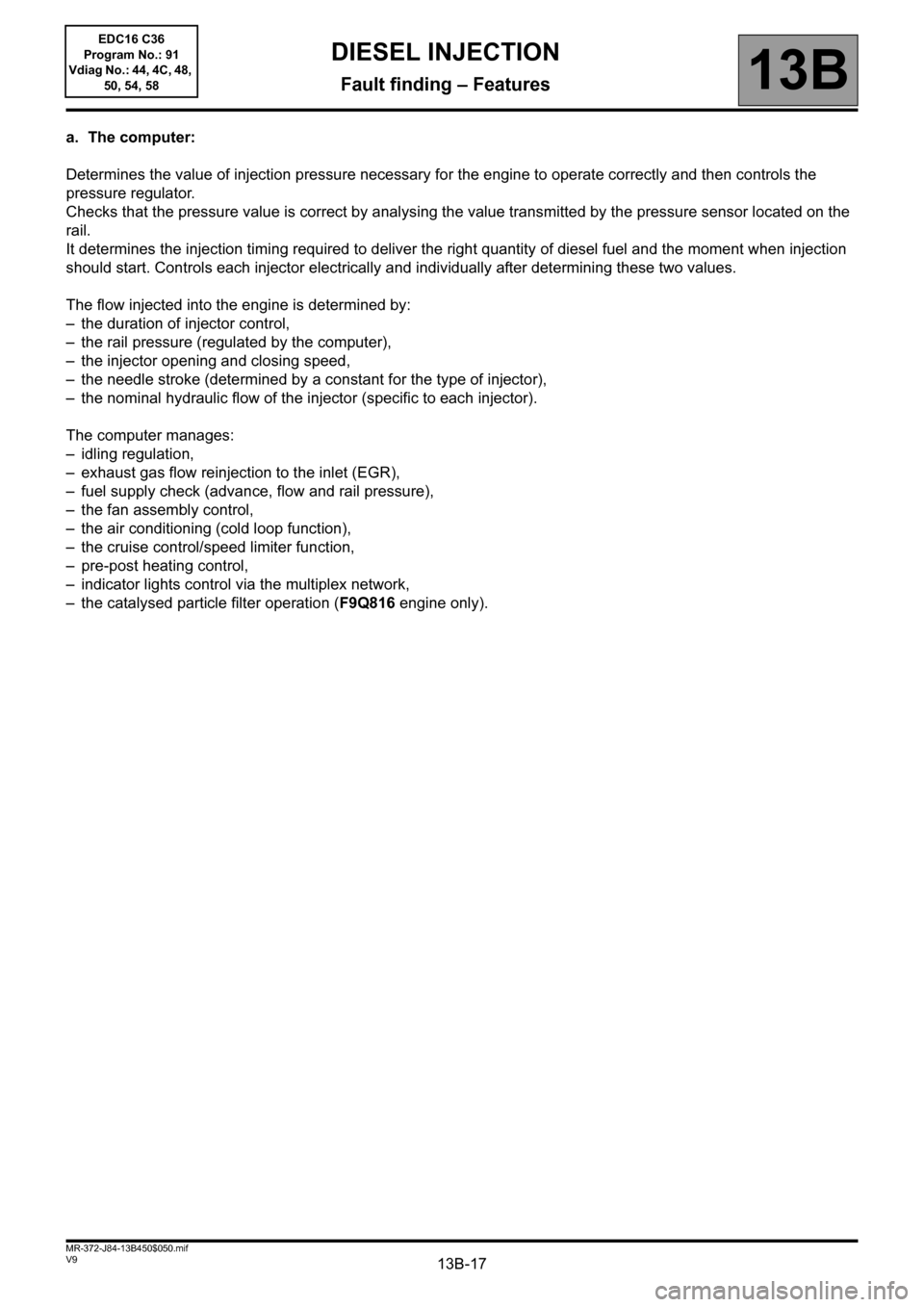
13B-17V9 MR-372-J84-13B450$050.mif
DIESEL INJECTION
Fault finding – Features13B
EDC16 C36
Program No.: 91
Vdiag No.: 44, 4C, 48,
50, 54, 58
a. The computer:
Determines the value of injection pressure necessary for the engine to operate correctly and then controls the
pressure regulator.
Checks that the pressure value is correct by analysing the value transmitted by the pressure sensor located on the
rail.
It determines the injection timing required to deliver the right quantity of diesel fuel and the moment when injection
should start. Controls each injector electrically and individually after determining these two values.
The flow injected into the engine is determined by:
– the duration of injector control,
– the rail pressure (regulated by the computer),
– the injector opening and closing speed,
– the needle stroke (determined by a constant for the type of injector),
– the nominal hydraulic flow of the injector (specific to each injector).
The computer manages:
– idling regulation,
– exhaust gas flow reinjection to the inlet (EGR),
– fuel supply check (advance, flow and rail pressure),
– the fan assembly control,
– the air conditioning (cold loop function),
– the cruise control/speed limiter function,
– pre-post heating control,
– indicator lights control via the multiplex network,
– the catalysed particle filter operation (F9Q816 engine only).
Page 18 of 431
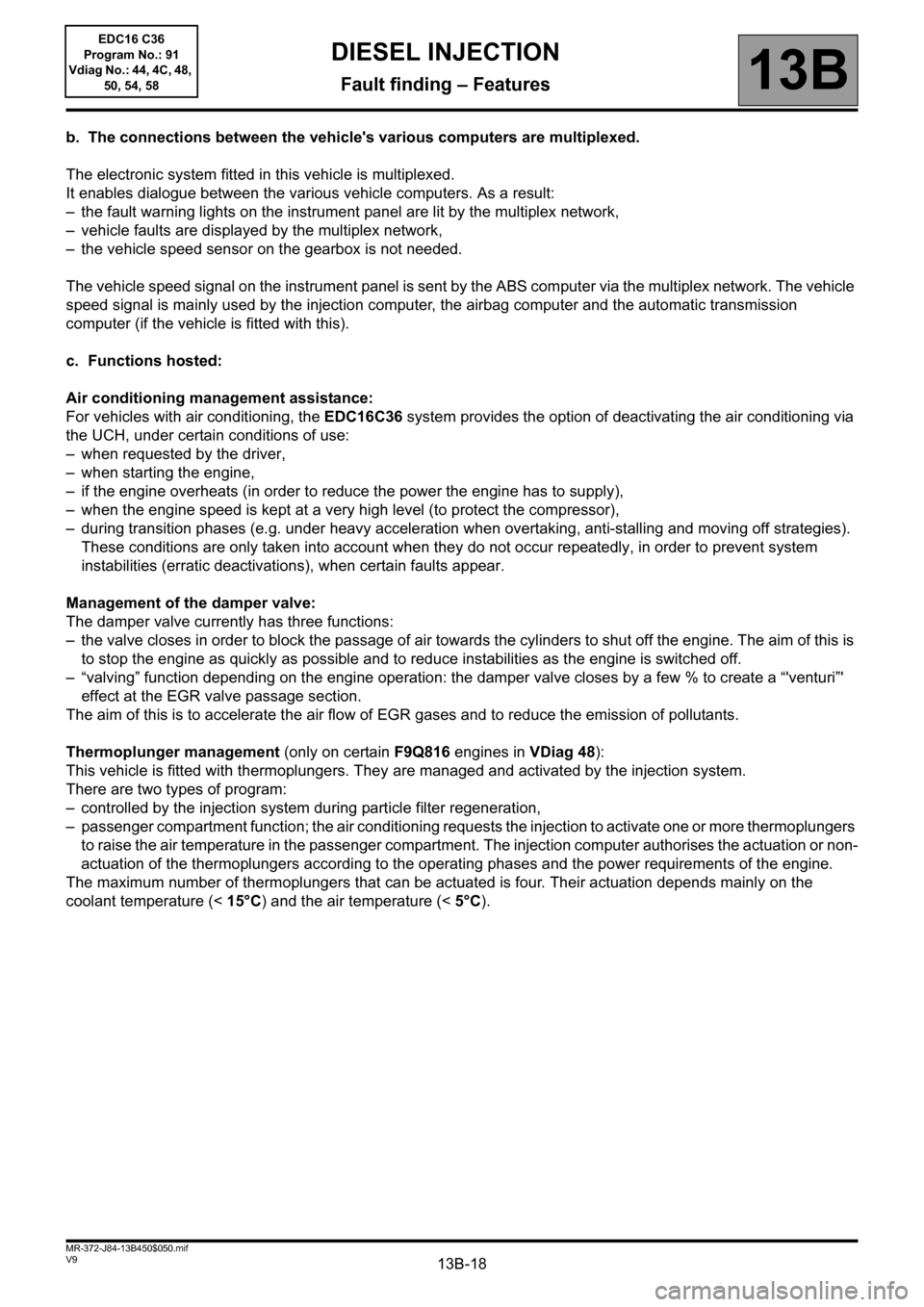
13B-18V9 MR-372-J84-13B450$050.mif
DIESEL INJECTION
Fault finding – Features13B
EDC16 C36
Program No.: 91
Vdiag No.: 44, 4C, 48,
50, 54, 58
b. The connections between the vehicle's various computers are multiplexed.
The electronic system fitted in this vehicle is multiplexed.
It enables dialogue between the various vehicle computers. As a result:
– the fault warning lights on the instrument panel are lit by the multiplex network,
– vehicle faults are displayed by the multiplex network,
– the vehicle speed sensor on the gearbox is not needed.
The vehicle speed signal on the instrument panel is sent by the ABS computer via the multiplex network. The vehicle
speed signal is mainly used by the injection computer, the airbag computer and the automatic transmission
computer (if the vehicle is fitted with this).
c. Functions hosted:
Air conditioning management assistance:
For vehicles with air conditioning, the EDC16C36 system provides the option of deactivating the air conditioning via
the UCH, under certain conditions of use:
– when requested by the driver,
– when starting the engine,
– if the engine overheats (in order to reduce the power the engine has to supply),
– when the engine speed is kept at a very high level (to protect the compressor),
– during transition phases (e.g. under heavy acceleration when overtaking, anti-stalling and moving off strategies).
These conditions are only taken into account when they do not occur repeatedly, in order to prevent system
instabilities (erratic deactivations), when certain faults appear.
Management of the damper valve:
The damper valve currently has three functions:
– the valve closes in order to block the passage of air towards the cylinders to shut off the engine. The aim of this is
to stop the engine as quickly as possible and to reduce instabilities as the engine is switched off.
– “valving” function depending on the engine operation: the damper valve closes by a few % to create a “'venturi”'
effect at the EGR valve passage section.
The aim of this is to accelerate the air flow of EGR gases and to reduce the emission of pollutants.
Thermoplunger management (only on certain F9Q816 engines in VDiag 48):
This vehicle is fitted with thermoplungers. They are managed and activated by the injection system.
There are two types of program:
– controlled by the injection system during particle filter regeneration,
– passenger compartment function; the air conditioning requests the injection to activate one or more thermoplungers
to raise the air temperature in the passenger compartment. The injection computer authorises the actuation or non-
actuation of the thermoplungers according to the operating phases and the power requirements of the engine.
The maximum number of thermoplungers that can be actuated is four. Their actuation depends mainly on the
coolant temperature (< 15°C) and the air temperature (< 5°C).