alternator RENAULT SCENIC 2011 J95 / 3.G Engine And Peripherals Siemens Injection Workshop Manual
[x] Cancel search | Manufacturer: RENAULT, Model Year: 2011, Model line: SCENIC, Model: RENAULT SCENIC 2011 J95 / 3.GPages: 329, PDF Size: 1.71 MB
Page 7 of 329
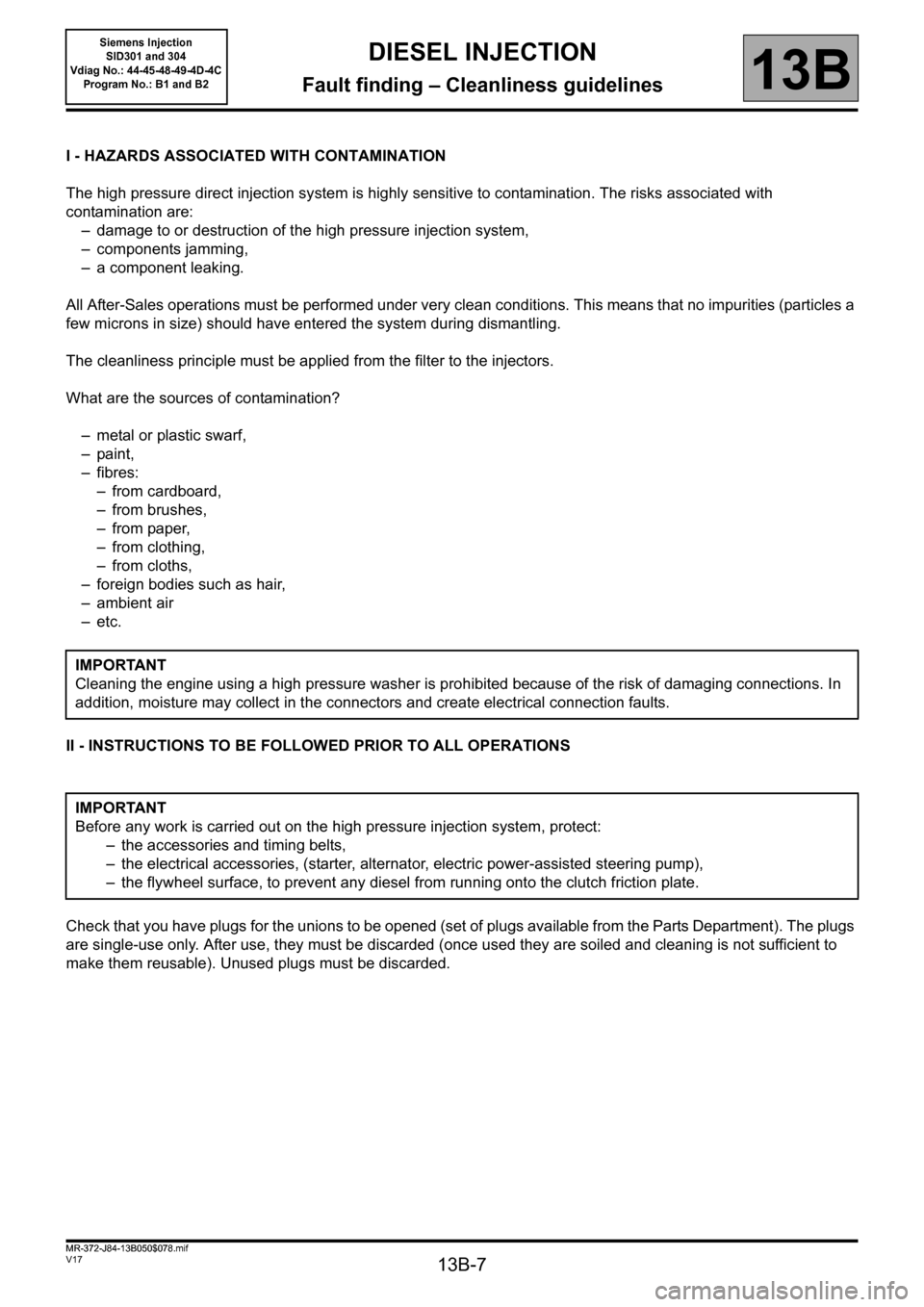
13B-7
MR-372-J84-13B050$078.mif
V17
13B
DIESEL INJECTION
Fault finding – Cleanliness guidelines
I - HAZARDS ASSOCIATED WITH CONTAMINATION
The high pressure direct injection system is highly sensitive to contamination. The risks associated with
contamination are:
– damage to or destruction of the high pressure injection system,
– components jamming,
– a component leaking.
All After-Sales operations must be performed under very clean conditions. This means that no impurities (particles a
few microns in size) should have entered the system during dismantling.
The cleanliness principle must be applied from the filter to the injectors.
What are the sources of contamination?
– metal or plastic swarf,
– paint,
–fibres:
– from cardboard,
– from brushes,
– from paper,
– from clothing,
– from cloths,
– foreign bodies such as hair,
–ambient air
–etc.
II - INSTRUCTIONS TO BE FOLLOWED PRIOR TO ALL OPERATIONS
Check that you have plugs for the unions to be opened (set of plugs available from the Parts Department). The plugs
are single-use only. After use, they must be discarded (once used they are soiled and cleaning is not sufficient to
make them reusable). Unused plugs must be discarded.IMPORTANT
Cleaning the engine using a high pressure washer is prohibited because of the risk of damaging connections. In
addition, moisture may collect in the connectors and create electrical connection faults.
IMPORTANT
Before any work is carried out on the high pressure injection system, protect:
– the accessories and timing belts,
– the electrical accessories, (starter, alternator, electric power-assisted steering pump),
– the flywheel surface, to prevent any diesel from running onto the clutch friction plate.
MR-372-J84-13B050$078.mif
Siemens Injection
SID301 and 304
Vdiag No.: 44-45-48-49-4D-4C
Program No.: B1 and B2
Page 19 of 329
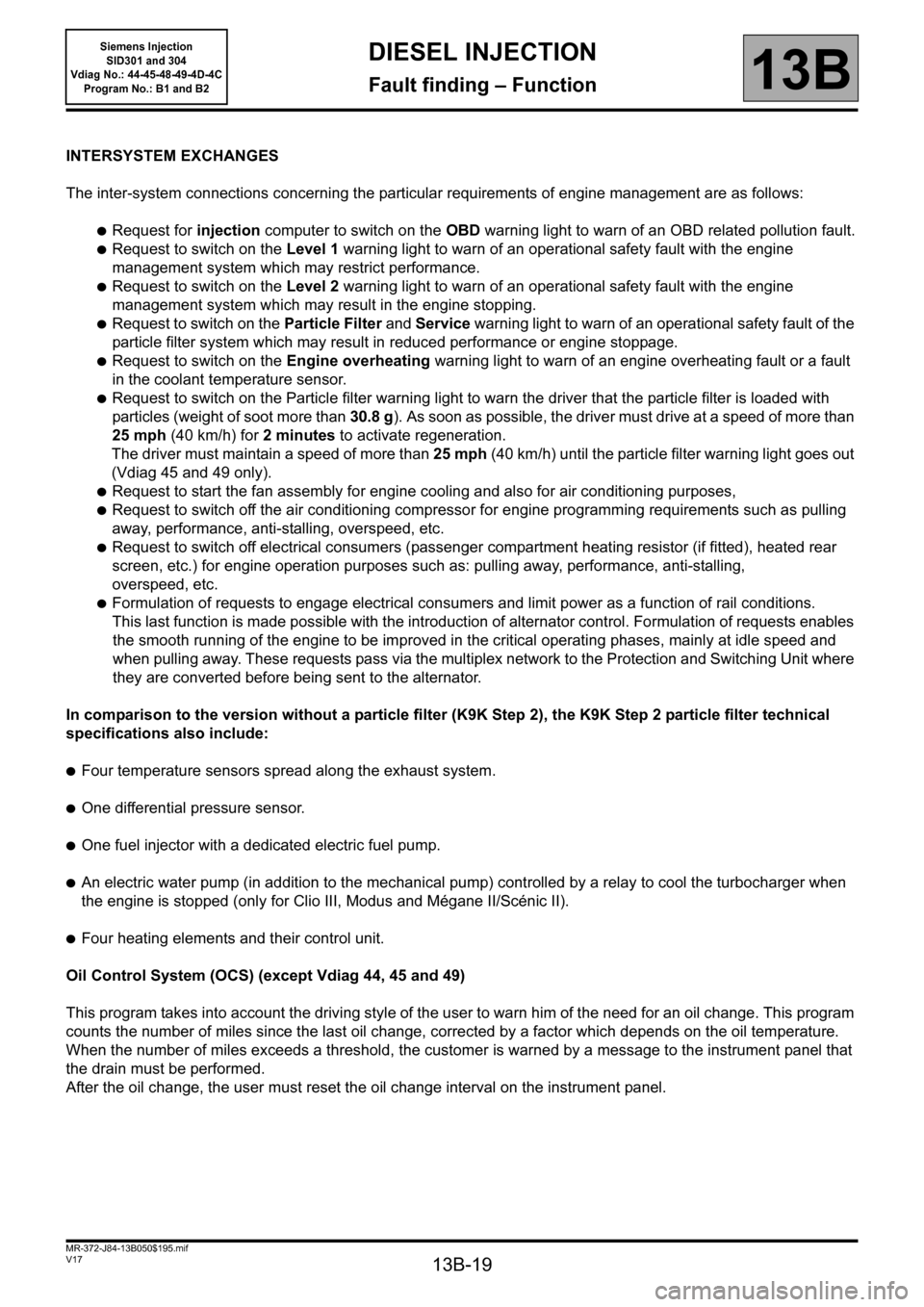
13B-19
MR-372-J84-13B050$195.mif
V17
Siemens Injection
SID301 and 304
Vdiag No.: 44-45-48-49-4D-4C
Program No.: B1 and B2DIESEL INJECTION
Fault finding – Function13B
INTERSYSTEM EXCHANGES
The inter-system connections concerning the particular requirements of engine management are as follows:
●Request for injection computer to switch on the OBD warning light to warn of an OBD related pollution fault.
●Request to switch on the Level 1 warning light to warn of an operational safety fault with the engine
management system which may restrict performance.
●Request to switch on the Level 2 warning light to warn of an operational safety fault with the engine
management system which may result in the engine stopping.
●Request to switch on the Particle Filter and Service warning light to warn of an operational safety fault of the
particle filter system which may result in reduced performance or engine stoppage.
●Request to switch on the Engine overheating warning light to warn of an engine overheating fault or a fault
in the coolant temperature sensor.
●Request to switch on the Particle filter warning light to warn the driver that the particle filter is loaded with
particles (weight of soot more than 30.8 g). As soon as possible, the driver must drive at a speed of more than
25 mph (40 km/h) for 2 minutes to activate regeneration.
The driver must maintain a speed of more than 25 mph (40 km/h) until the particle filter warning light goes out
(Vdiag 45 and 49 only).
●Request to start the fan assembly for engine cooling and also for air conditioning purposes,
●Request to switch off the air conditioning compressor for engine programming requirements such as pulling
away, performance, anti-stalling, overspeed, etc.
●Request to switch off electrical consumers (passenger compartment heating resistor (if fitted), heated rear
screen, etc.) for engine operation purposes such as: pulling away, performance, anti-stalling,
overspeed, etc.
●Formulation of requests to engage electrical consumers and limit power as a function of rail conditions.
This last function is made possible with the introduction of alternator control. Formulation of requests enables
the smooth running of the engine to be improved in the critical operating phases, mainly at idle speed and
when pulling away. These requests pass via the multiplex network to the Protection and Switching Unit where
they are converted before being sent to the alternator.
In comparison to the version without a particle filter (K9K Step 2), the K9K Step 2 particle filter technical
specifications also include:
●Four temperature sensors spread along the exhaust system.
●One differential pressure sensor.
●One fuel injector with a dedicated electric fuel pump.
●An electric water pump (in addition to the mechanical pump) controlled by a relay to cool the turbocharger when
the engine is stopped (only for Clio III, Modus and Mégane II/Scénic II).
●Four heating elements and their control unit.
Oil Control System (OCS) (except Vdiag 44, 45 and 49)
This program takes into account the driving style of the user to warn him of the need for an oil change. This program
counts the number of miles since the last oil change, corrected by a factor which depends on the oil temperature.
When the number of miles exceeds a threshold, the customer is warned by a message to the instrument panel that
the drain must be performed.
After the oil change, the user must reset the oil change interval on the instrument panel.
Page 33 of 329
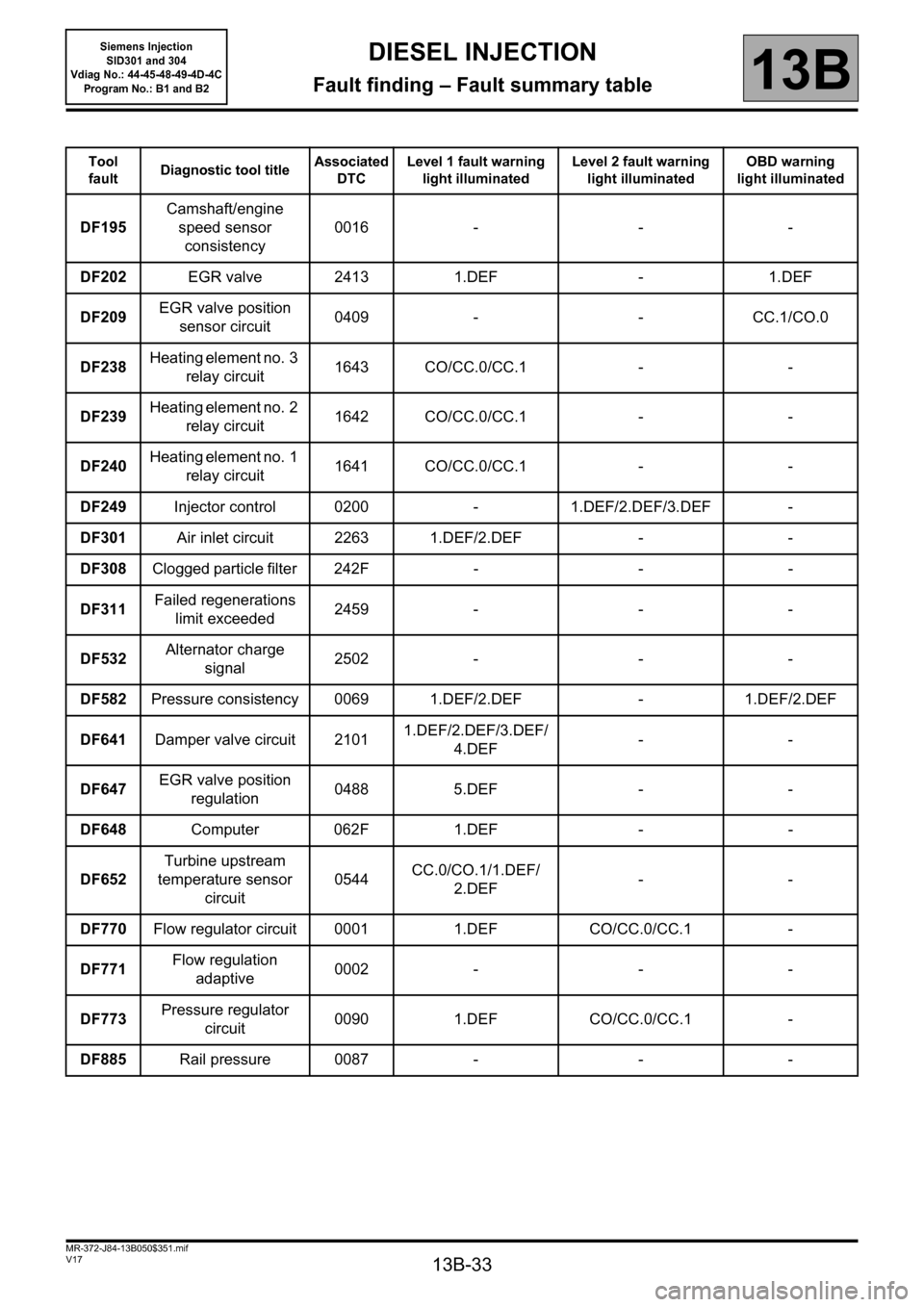
13B-33
MR-372-J84-13B050$351.mif
V17
Siemens Injection
SID301 and 304
Vdiag No.: 44-45-48-49-4D-4C
Program No.: B1 and B2DIESEL INJECTION
Fault finding – Fault summary table13B
Tool
faultDiagnostic tool titleAssociated
DTCLevel 1 fault warning
light illuminatedLevel 2 fault warning
light illuminatedOBD warning
light illuminated
DF195Camshaft/engine
speed sensor
consistency0016 - - -
DF202EGR valve 2413 1.DEF - 1.DEF
DF209EGR valve position
sensor circuit0409 - - CC.1/CO.0
DF238Heating element no. 3
relay circuit 1643 CO/CC.0/CC.1 - -
DF239Heating element no. 2
relay circuit 1642 CO/CC.0/CC.1 - -
DF240Heating element no. 1
relay circuit 1641 CO/CC.0/CC.1 - -
DF249Injector control 0200 - 1.DEF/2.DEF/3.DEF -
DF301Air inlet circuit 2263 1.DEF/2.DEF - -
DF308Clogged particle filter 242F - - -
DF311Failed regenerations
limit exceeded 2459 - - -
DF532Alternator charge
signal2502 - - -
DF582Pressure consistency 0069 1.DEF/2.DEF - 1.DEF/2.DEF
DF641Damper valve circuit 21011.DEF/2.DEF/3.DEF/
4.DEF--
DF647EGR valve position
regulation0488 5.DEF - -
DF648Computer 062F 1.DEF - -
DF652Turbine upstream
temperature sensor
circuit 0544CC.0/CO.1/1.DEF/
2.DEF--
DF770Flow regulator circuit 0001 1.DEF CO/CC.0/CC.1 -
DF771Flow regulation
adaptive0002 - - -
DF773Pressure regulator
circuit0090 1.DEF CO/CC.0/CC.1 -
DF885Rail pressure 0087 - - -
Page 59 of 329
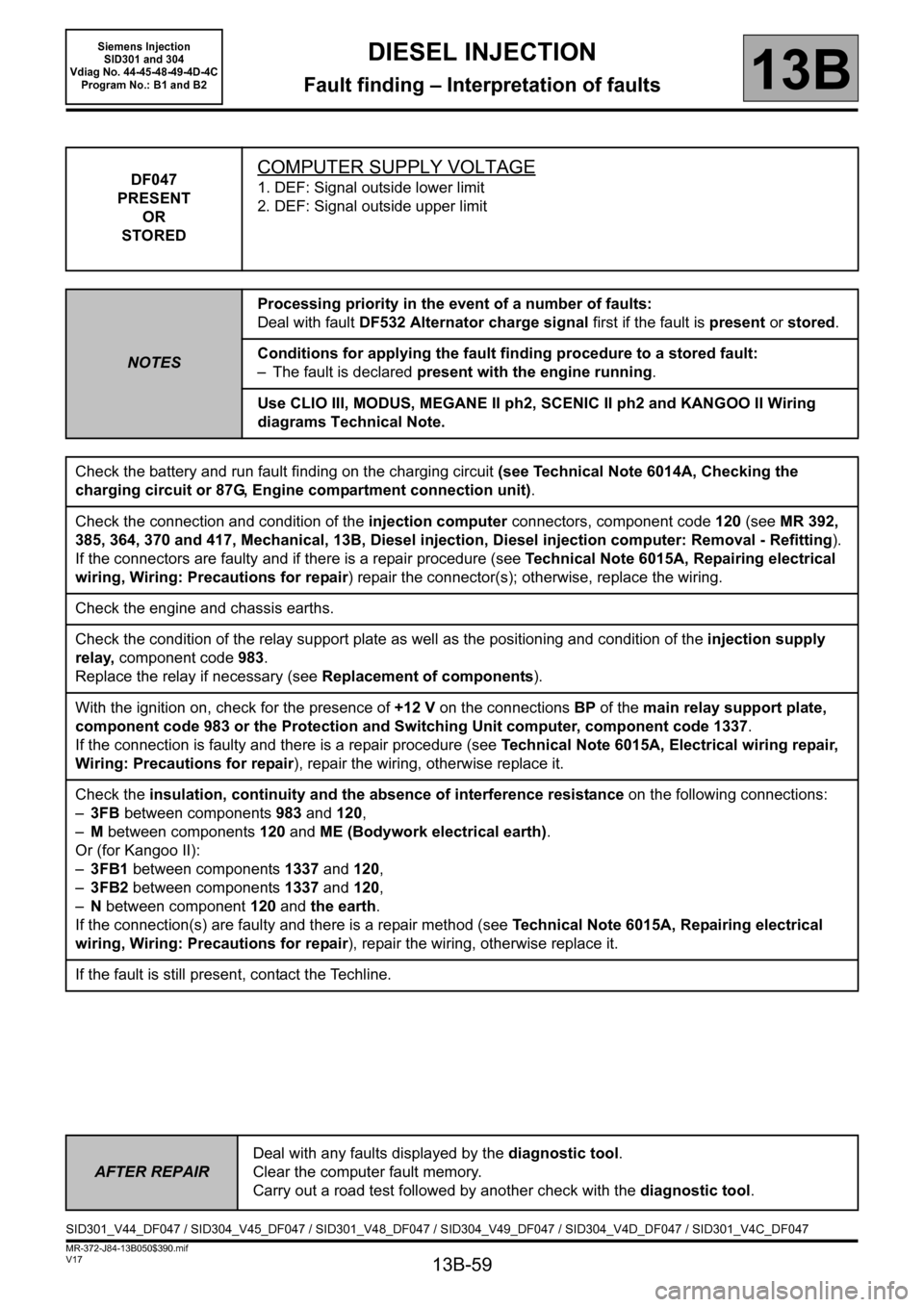
13B-59
MR-372-J84-13B050$390.mif
V17
DIESEL INJECTION
Fault finding – Interpretation of faults
Siemens Injection
SID301 and 304
Vdiag No. 44-45-48-49-4D-4C
Program No.: B1 and B2
13B
DF047
PRESENT
OR
STOREDCOMPUTER SUPPLY VOLTAGE
1. DEF: Signal outside lower limit
2. DEF: Signal outside upper limit
NOTESProcessing priority in the event of a number of faults:
Deal with fault DF532 Alternator charge signal first if the fault is present or stored.
Conditions for applying the fault finding procedure to a stored fault:
– The fault is declared present with the engine running.
Use CLIO III, MODUS, MEGANE II ph2, SCENIC II ph2 and KANGOO II Wiring
diagrams Technical Note.
Check the battery and run fault finding on the charging circuit (see Technical Note 6014A, Checking the
charging circuit or 87G, Engine compartment connection unit).
Check the connection and condition of the injection computer connectors, component code 120 (see MR 392,
385, 364, 370 and 417, Mechanical, 13B, Diesel injection, Diesel injection computer: Removal - Refitting).
If the connectors are faulty and if there is a repair procedure (see Technical Note 6015A, Repairing electrical
wiring, Wiring: Precautions for repair) repair the connector(s); otherwise, replace the wiring.
Check the engine and chassis earths.
Check the condition of the relay support plate as well as the positioning and condition of the injection supply
relay, component code 983.
Replace the relay if necessary (see Replacement of components).
With the ignition on, check for the presence of +12 V on the connectionsBP of the main relay support plate,
component code 983 or the Protection and Switching Unit computer, component code 1337.
If the connection is faulty and there is a repair procedure (see Technical Note 6015A, Electrical wiring repair,
Wiring: Precautions for repair), repair the wiring, otherwise replace it.
Check the insulation, continuity and the absence of interference resistance on the following connections:
–3FB between components983 and 120,
–M between components120 and ME (Bodywork electrical earth).
Or (for Kangoo II):
–3FB1 between components 1337 and 120,
–3FB2 between components 1337 and 120,
–N between component 120 and the earth.
If the connection(s) are faulty and there is a repair method (see Technical Note 6015A, Repairing electrical
wiring, Wiring: Precautions for repair), repair the wiring, otherwise replace it.
If the fault is still present, contact the Techline.
AFTER REPAIRDeal with any faults displayed by the diagnostic tool.
Clear the computer fault memory.
Carry out a road test followed by another check with the diagnostic tool.
SID301_V44_DF047 / SID304_V45_DF047 / SID301_V48_DF047 / SID304_V49_DF047 / SID304_V4D_DF047 / SID301_V4C_DF047
Page 88 of 329
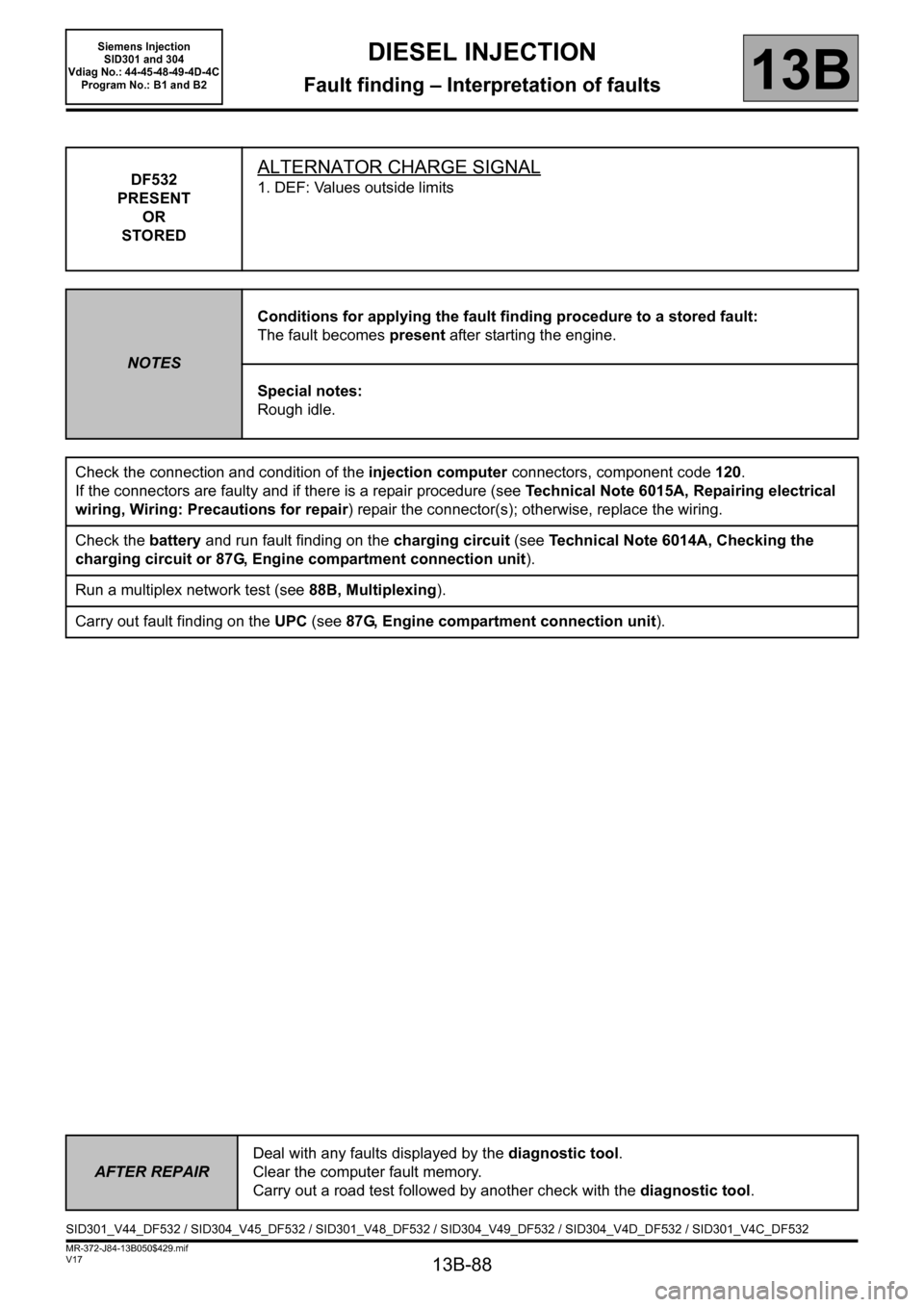
13B-88
MR-372-J84-13B050$429.mif
V17
DIESEL INJECTION
Fault finding – Interpretation of faults
Siemens Injection
SID301 and 304
Vdiag No.: 44-45-48-49-4D-4C
Program No.: B1 and B2
13B
DF532
PRESENT
OR
STOREDALTERNATOR CHARGE SIGNAL
1. DEF: Values outside limits
NOTESConditions for applying the fault finding procedure to a stored fault:
The fault becomes present after starting the engine.
Special notes:
Rough idle.
Check the connection and condition of the injection computer connectors, component code 120.
If the connectors are faulty and if there is a repair procedure (see Technical Note 6015A, Repairing electrical
wiring, Wiring: Precautions for repair) repair the connector(s); otherwise, replace the wiring.
Check the battery and run fault finding on the charging circuit (see Technical Note 6014A, Checking the
charging circuit or 87G, Engine compartment connection unit).
Run a multiplex network test (see88B, Multiplexing).
Carry out fault finding on the UPC (see 87G, Engine compartment connection unit).
AFTER REPAIRDeal with any faults displayed by the diagnostic tool.
Clear the computer fault memory.
Carry out a road test followed by another check with the diagnostic tool.
SID301_V44_DF532 / SID304_V45_DF532 / SID301_V48_DF532 / SID304_V49_DF532 / SID304_V4D_DF532 / SID301_V4C_DF532