sensor RENAULT SCENIC 2014 J95 / 3.G Petrol Injection - Sagem3000 Repair Manual
[x] Cancel search | Manufacturer: RENAULT, Model Year: 2014, Model line: SCENIC, Model: RENAULT SCENIC 2014 J95 / 3.GPages: 181
Page 123 of 181
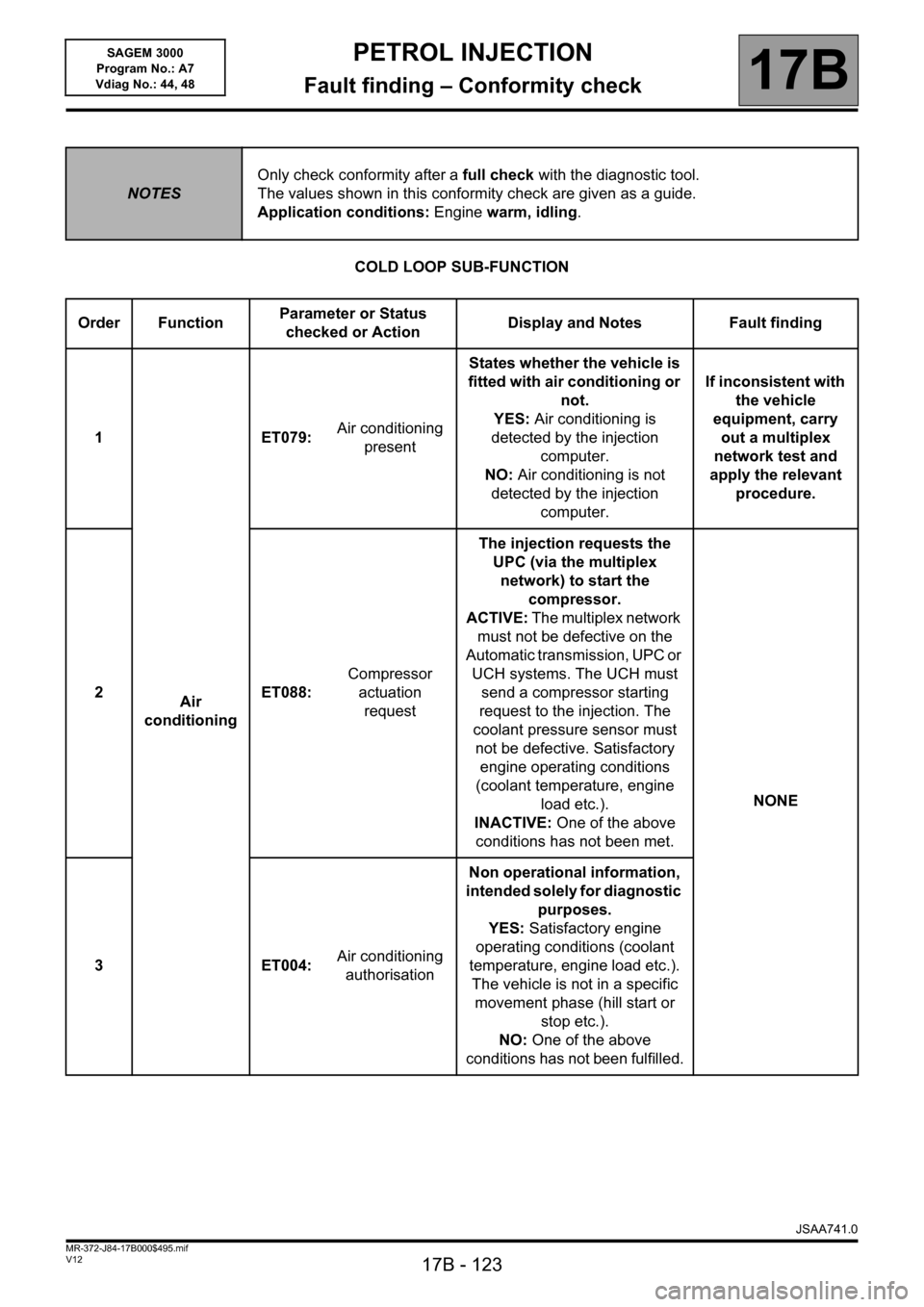
PETROL INJECTION
Fault finding – Conformity check17B
17B - 123V12 MR-372-J84-17B000$495.mif
SAGEM 3000
Program No.: A7
Vdiag No.: 44, 48
COLD LOOP SUB-FUNCTION
NOTESOnly check conformity after a full check with the diagnostic tool.
The values shown in this conformity check are given as a guide.
Application conditions: Engine warm, idling.
Order FunctionParameter or Status
checked or ActionDisplay and Notes Fault finding
1
Air
conditioningET079: Air conditioning
presentStates whether the vehicle is
fitted with air conditioning or
not.
YES: Air conditioning is
detected by the injection
computer.
NO: Air conditioning is not
detected by the injection
computer.If inconsistent with
the vehicle
equipment, carry
out a multiplex
network test and
apply the relevant
procedure.
2ET088: Compressor
actuation
requestThe injection requests the
UPC (via the multiplex
network) to start the
compressor.
ACTIVE: The multiplex network
must not be defective on the
Automatic transmission, UPC or
UCH systems. The UCH must
send a compressor starting
request to the injection. The
coolant pressure sensor must
not be defective. Satisfactory
engine operating conditions
(coolant temperature, engine
load etc.).
INACTIVE: One of the above
conditions has not been met.NONE
3ET004: Air conditioning
authorisationNon operational information,
intended solely for diagnostic
purposes.
YES: Satisfactory engine
operating conditions (coolant
temperature, engine load etc.).
The vehicle is not in a specific
movement phase (hill start or
stop etc.).
NO: One of the above
conditions has not been fulfilled.
JSAA741.0
Page 124 of 181
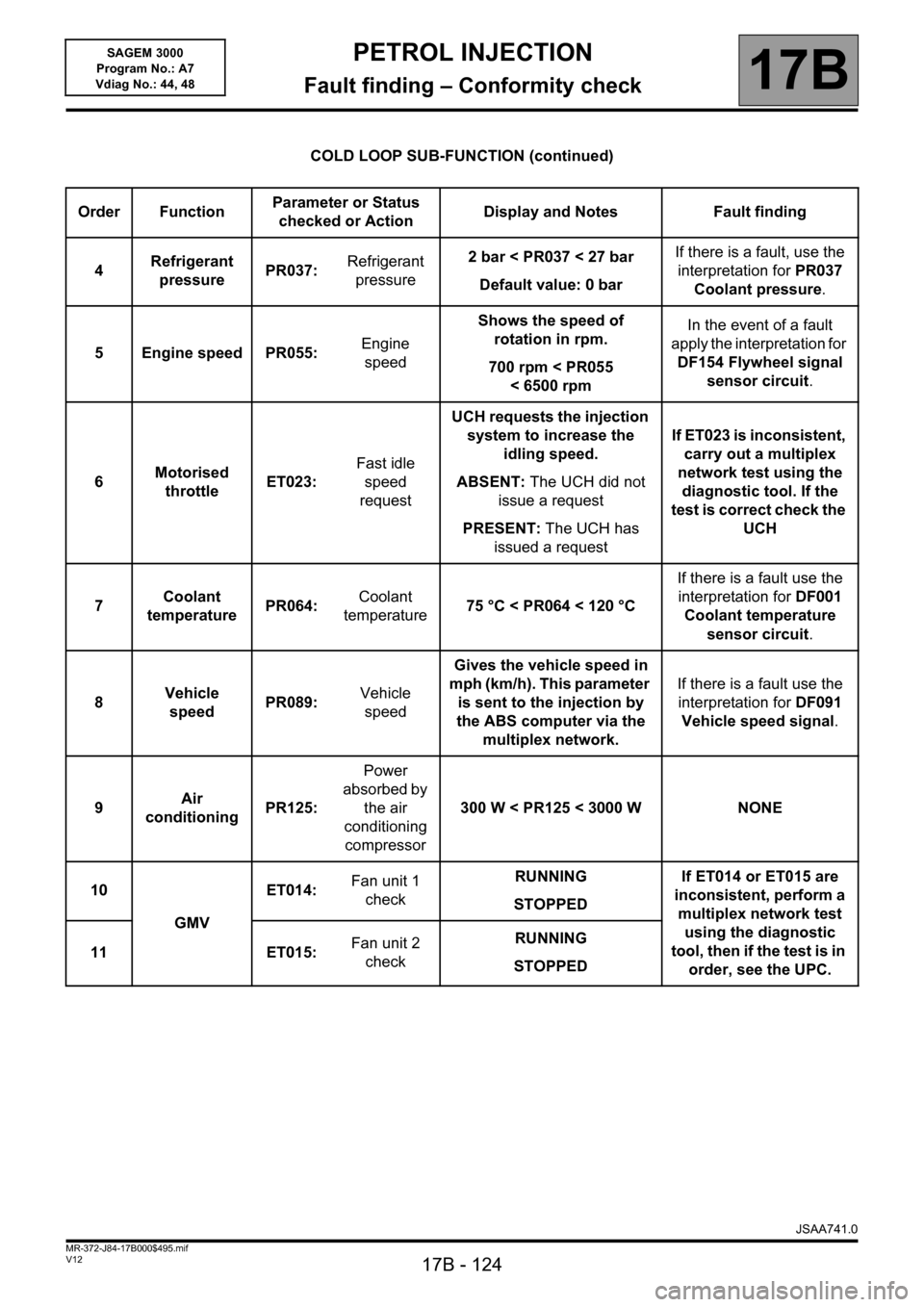
PETROL INJECTION
Fault finding – Conformity check17B
17B - 124V12 MR-372-J84-17B000$495.mif
SAGEM 3000
Program No.: A7
Vdiag No.: 44, 48
COLD LOOP SUB-FUNCTION (continued)
Order FunctionParameter or Status
checked or ActionDisplay and Notes Fault finding
4Refrigerant
pressurePR037: Refrigerant
pressure2 bar < PR037 < 27 bar
Default value: 0 barIf there is a fault, use the
interpretation for PR037
Coolant pressure.
5 Engine speed PR055: Engine
speedShows the speed of
rotation in rpm.
700 rpm < PR055
< 6500 rpmIn the event of a fault
apply the interpretation for
DF154 Flywheel signal
sensor circuit.
6Motorised
throttleET023: Fast idle
speed
requestUCH requests the injection
system to increase the
idling speed.
ABSENT: The UCH did not
issue a request
PRESENT: The UCH has
issued a requestIf ET023 is inconsistent,
carry out a multiplex
network test using the
diagnostic tool. If the
test is correct check the
UCH
7Coolant
temperaturePR064: Coolant
temperature75 °C < PR064 < 120 °CIf there is a fault use the
interpretation for DF001
Coolant temperature
sensor circuit.
8Vehicle
speedPR089: Vehicle
speedGives the vehicle speed in
mph (km/h). This parameter
is sent to the injection by
the ABS computer via the
multiplex network.If there is a fault use the
interpretation for DF091
Vehicle speed signal.
9Air
conditioningPR125: Power
absorbed by
the air
conditioning
compressor300 W < PR125 < 3000 W NONE
10
GMVET014: Fan unit 1
checkRUNNING
STOPPEDIf ET014 or ET015 are
inconsistent, perform a
multiplex network test
using the diagnostic
tool, then if the test is in
order, see the UPC. 11 ET015: Fan unit 2
checkRUNNING
STOPPED
JSAA741.0
Page 125 of 181
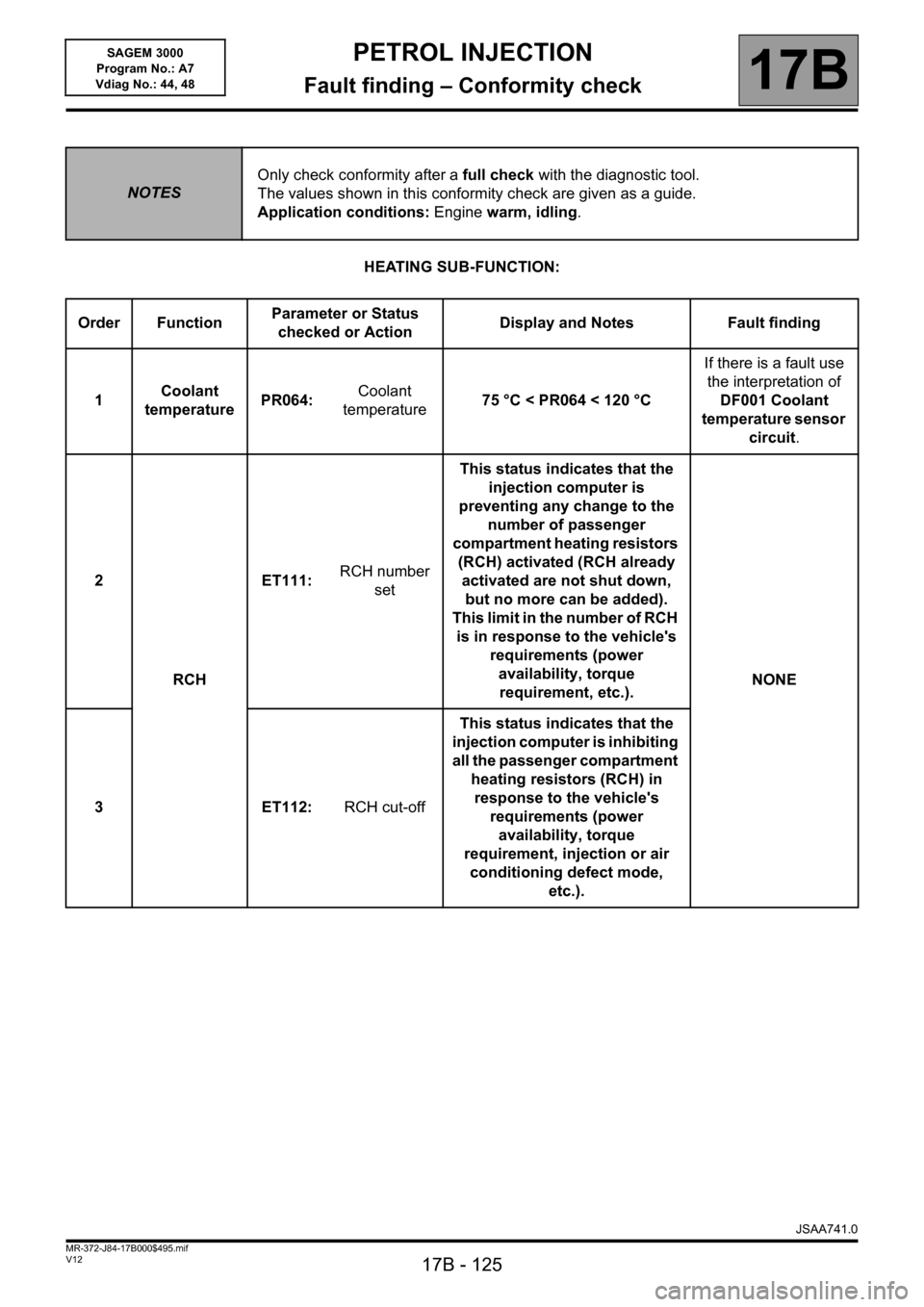
PETROL INJECTION
Fault finding – Conformity check17B
17B - 125V12 MR-372-J84-17B000$495.mif
SAGEM 3000
Program No.: A7
Vdiag No.: 44, 48
HEATING SUB-FUNCTION:
NOTESOnly check conformity after a full check with the diagnostic tool.
The values shown in this conformity check are given as a guide.
Application conditions: Engine warm, idling.
Order FunctionParameter or Status
checked or ActionDisplay and Notes Fault finding
1Coolant
temperaturePR064: Coolant
temperature75 °C < PR064 < 120 °CIf there is a fault use
the interpretation of
DF001 Coolant
temperature sensor
circuit.
2
RCHET111: RCH number
setThis status indicates that the
injection computer is
preventing any change to the
number of passenger
compartment heating resistors
(RCH) activated (RCH already
activated are not shut down,
but no more can be added).
This limit in the number of RCH
is in response to the vehicle's
requirements (power
availability, torque
requirement, etc.).NONE
3 ET112: RCH cut-offThis status indicates that the
injection computer is inhibiting
all the passenger compartment
heating resistors (RCH) in
response to the vehicle's
requirements (power
availability, torque
requirement, injection or air
conditioning defect mode,
etc.).
JSAA741.0
Page 132 of 181
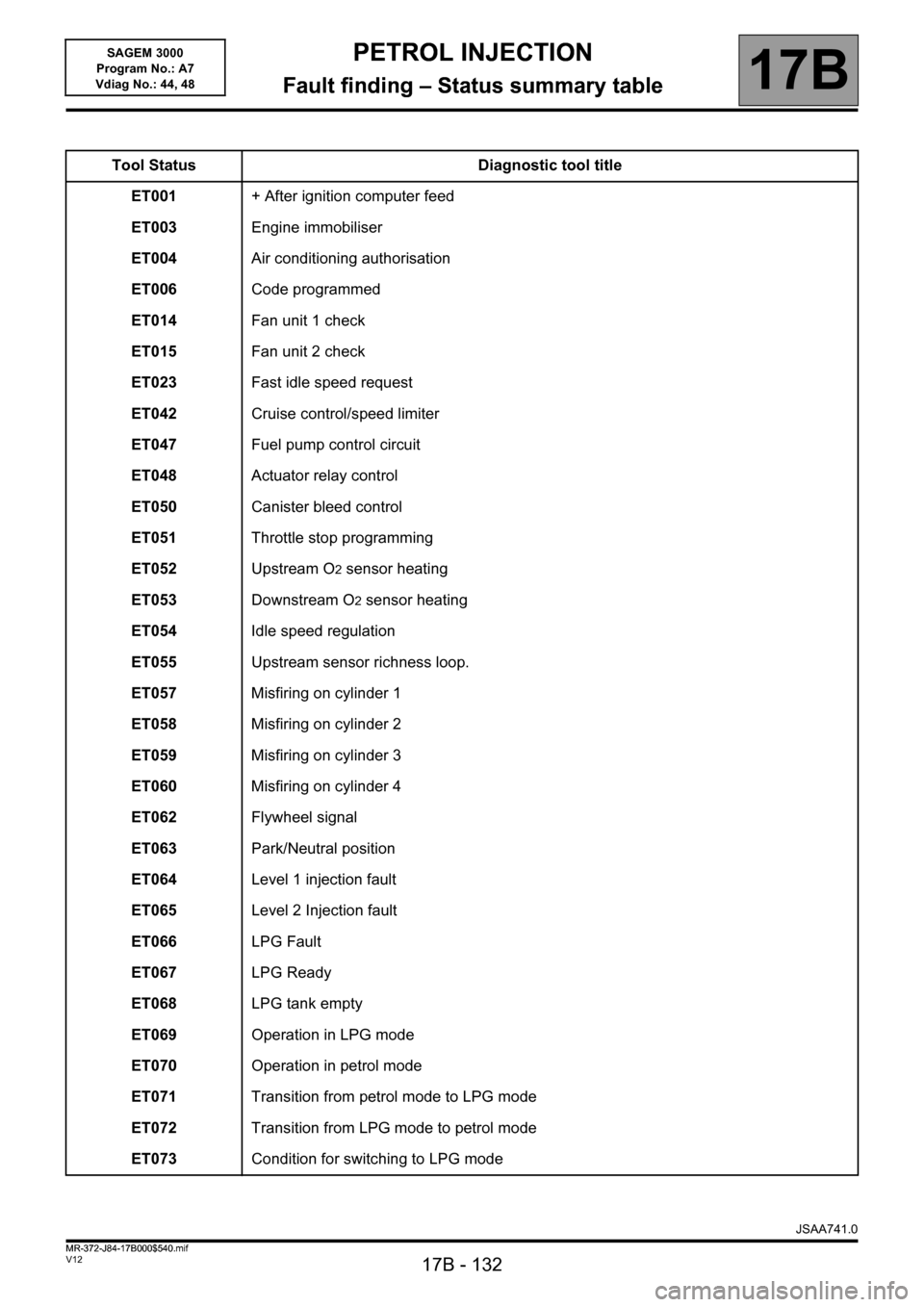
PETROL INJECTION
Fault finding – Status summary table17B
17B - 132V12 MR-372-J84-17B000$540.mif
SAGEM 3000
Program No.: A7
Vdiag No.: 44, 48PETROL INJECTION
Fault finding – Status summary table
Tool Status Diagnostic tool title
ET001+ After ignition computer feed
ET003Engine immobiliser
ET004Air conditioning authorisation
ET006Code programmed
ET014Fan unit 1 check
ET015Fan unit 2 check
ET023Fast idle speed request
ET042Cruise control/speed limiter
ET047Fuel pump control circuit
ET048Actuator relay control
ET050Canister bleed control
ET051Throttle stop programming
ET052Upstream O
2 sensor heating
ET053Downstream O
2 sensor heating
ET054Idle speed regulation
ET055Upstream sensor richness loop.
ET057Misfiring on cylinder 1
ET058Misfiring on cylinder 2
ET059Misfiring on cylinder 3
ET060Misfiring on cylinder 4
ET062Flywheel signal
ET063Park/Neutral position
ET064Level 1 injection fault
ET065Level 2 Injection fault
ET066LPG Fault
ET067LPG Ready
ET068LPG tank empty
ET069Operation in LPG mode
ET070Operation in petrol mode
ET071Transition from petrol mode to LPG mode
ET072Transition from LPG mode to petrol mode
ET073Condition for switching to LPG mode
JSAA741.0
MR-372-J84-17B000$540.mif
Page 138 of 181
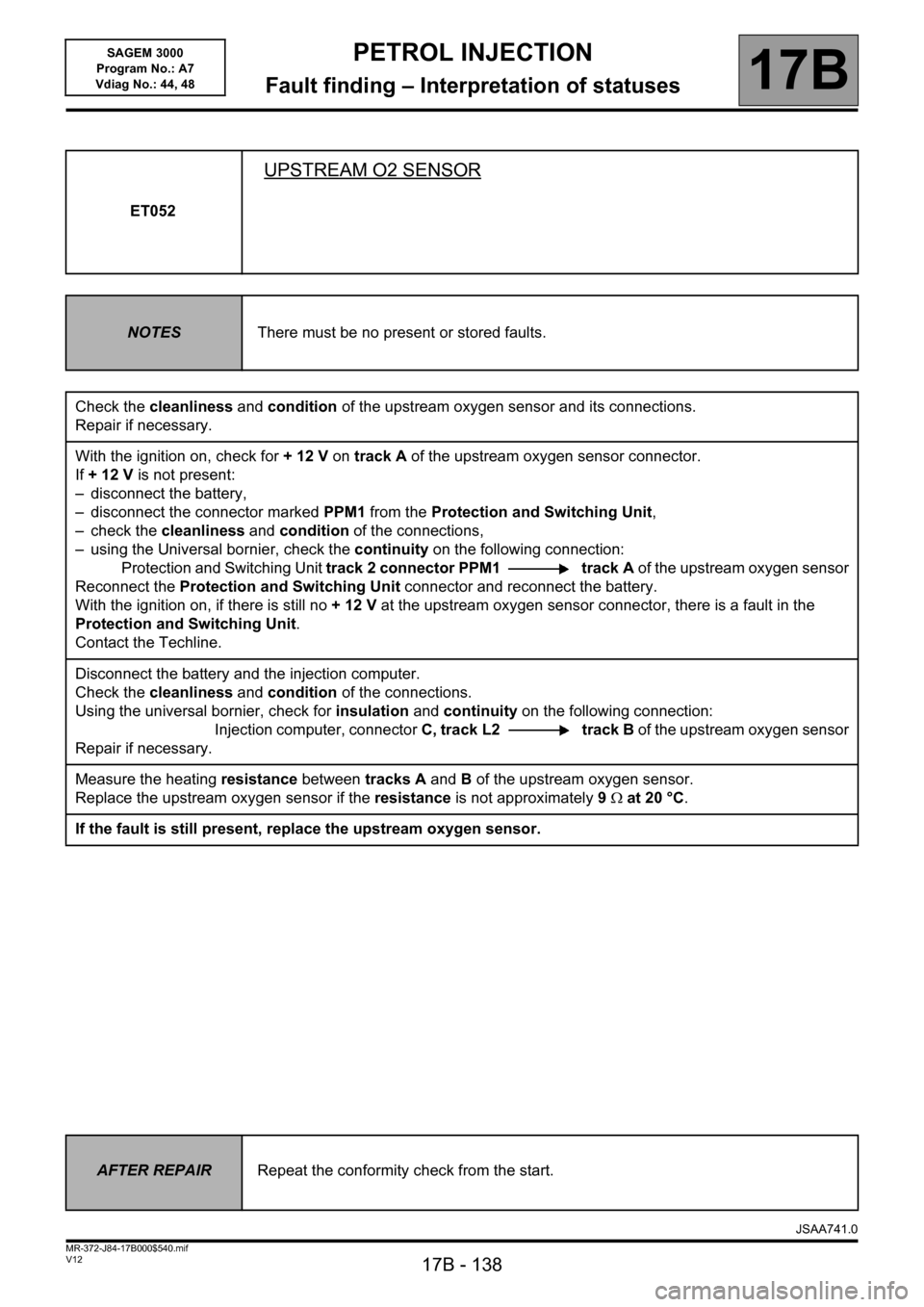
PETROL INJECTION
Fault finding – Interpretation of statuses17B
17B - 138V12 MR-372-J84-17B000$540.mif
SAGEM 3000
Program No.: A7
Vdiag No.: 44, 48
ET052
UPSTREAM O2 SENSOR
NOTESThere must be no present or stored faults.
Check the cleanliness and condition of the upstream oxygen sensor and its connections.
Repair if necessary.
With the ignition on, check for + 12 V on track A of the upstream oxygen sensor connector.
If +12V is not present:
– disconnect the battery,
– disconnect the connector marked PPM1 from the Protection and Switching Unit,
– check the cleanliness and condition of the connections,
– using the Universal bornier, check the continuity on the following connection:
Protection and Switching Unit track 2 connector PPM1 track A of the upstream oxygen sensor
Reconnect the Protection and Switching Unit connector and reconnect the battery.
With the ignition on, if there is still no +12V at the upstream oxygen sensor connector, there is a fault in the
Protection and Switching Unit.
Contact the Techline.
Disconnect the battery and the injection computer.
Check the cleanliness and condition of the connections.
Using the universal bornier, check for insulation and continuity on the following connection:
Injection computer, connectorC, track L2 track B of the upstream oxygen sensor
Repair if necessary.
Measure the heating resistance between tracks A and B of the upstream oxygen sensor.
Replace the upstream oxygen sensor if the resistance is not approximately 9 at 20 °C.
If the fault is still present, replace the upstream oxygen sensor.
AFTER REPAIRRepeat the conformity check from the start.
JSAA741.0
Page 139 of 181
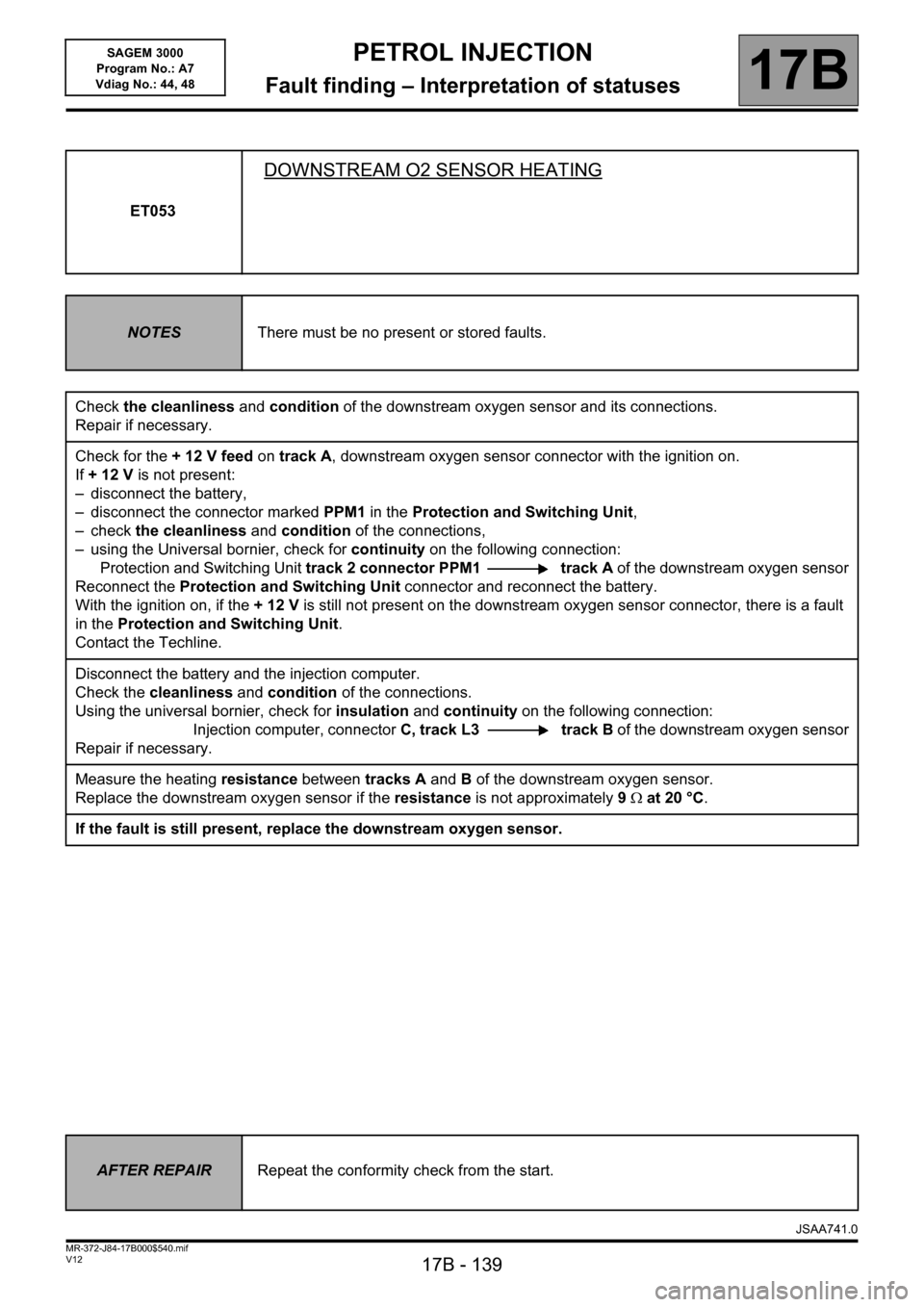
PETROL INJECTION
Fault finding – Interpretation of statuses17B
17B - 139V12 MR-372-J84-17B000$540.mif
SAGEM 3000
Program No.: A7
Vdiag No.: 44, 48
ET053
DOWNSTREAM O2 SENSOR HEATING
NOTESThere must be no present or stored faults.
Check the cleanliness and condition of the downstream oxygen sensor and its connections.
Repair if necessary.
Check for the + 12 V feed on track A, downstream oxygen sensor connector with the ignition on.
If +12V is not present:
– disconnect the battery,
– disconnect the connector marked PPM1 in the Protection and Switching Unit,
–check the cleanliness and condition of the connections,
– using the Universal bornier, check for continuity on the following connection:
Protection and Switching Unit track 2 connector PPM1 track A of the downstream oxygen sensor
Reconnect the Protection and Switching Unit connector and reconnect the battery.
With the ignition on, if the +12V is still not present on the downstream oxygen sensor connector, there is a fault
in the Protection and Switching Unit.
Contact the Techline.
Disconnect the battery and the injection computer.
Check the cleanliness and condition of the connections.
Using the universal bornier, check for insulation and continuity on the following connection:
Injection computer, connectorC, track L3 track B of the downstream oxygen sensor
Repair if necessary.
Measure the heating resistance between tracks A and B of the downstream oxygen sensor.
Replace the downstream oxygen sensor if the resistance is not approximately 9 at 20 °C.
If the fault is still present, replace the downstream oxygen sensor.
AFTER REPAIRRepeat the conformity check from the start.
JSAA741.0
Page 141 of 181
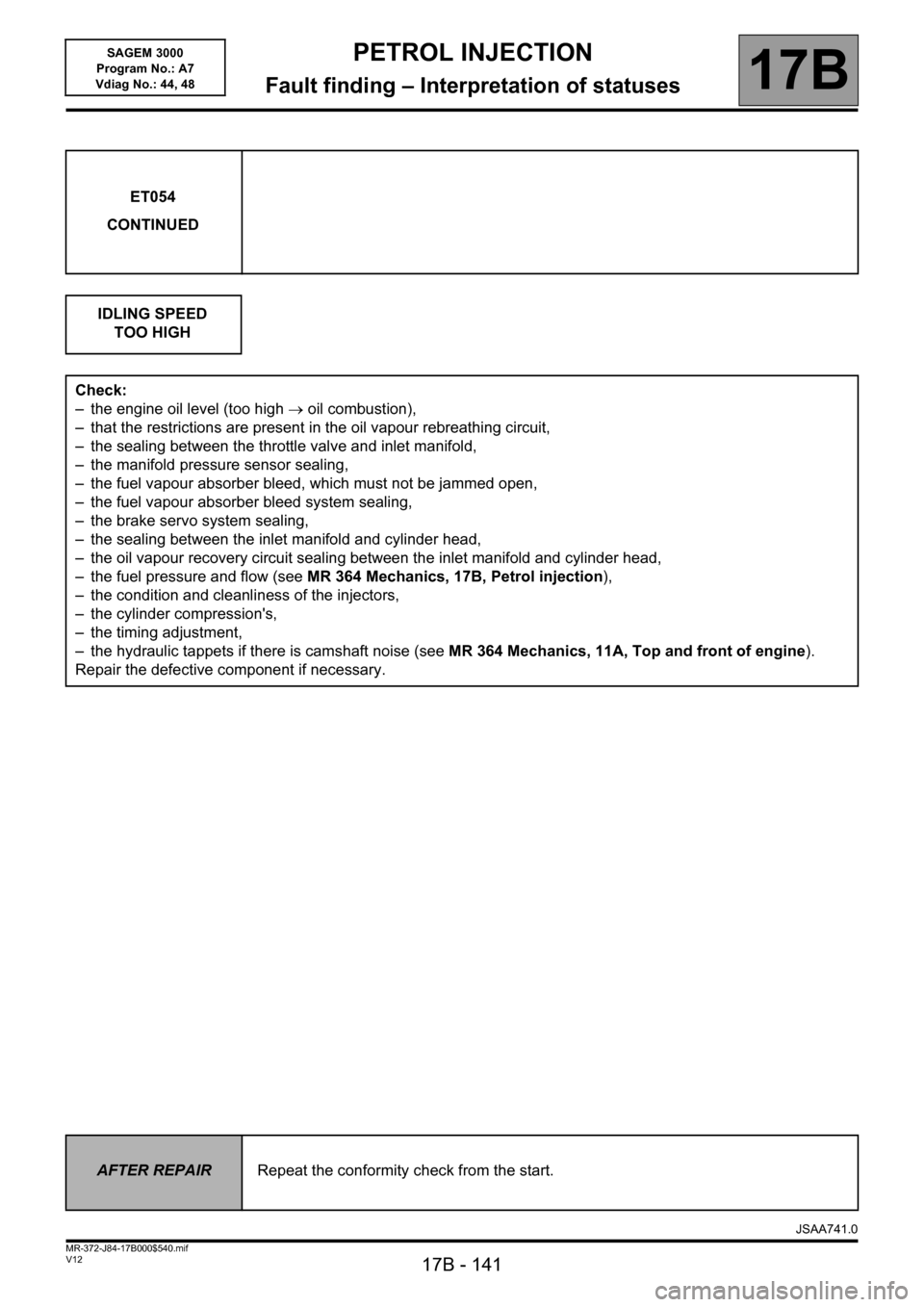
PETROL INJECTION
Fault finding – Interpretation of statuses17B
17B - 141V12 MR-372-J84-17B000$540.mif
SAGEM 3000
Program No.: A7
Vdiag No.: 44, 48
ET054
CONTINUED
IDLING SPEED
TOO HIGH
Check:
– the engine oil level (too high oil combustion),
– that the restrictions are present in the oil vapour rebreathing circuit,
– the sealing between the throttle valve and inlet manifold,
– the manifold pressure sensor sealing,
– the fuel vapour absorber bleed, which must not be jammed open,
– the fuel vapour absorber bleed system sealing,
– the brake servo system sealing,
– the sealing between the inlet manifold and cylinder head,
– the oil vapour recovery circuit sealing between the inlet manifold and cylinder head,
– the fuel pressure and flow (see MR 364 Mechanics, 17B, Petrol injection),
– the condition and cleanliness of the injectors,
– the cylinder compression's,
– the timing adjustment,
– the hydraulic tappets if there is camshaft noise (see MR 364 Mechanics, 11A, Top and front of engine).
Repair the defective component if necessary.
AFTER REPAIRRepeat the conformity check from the start.
JSAA741.0
Page 142 of 181
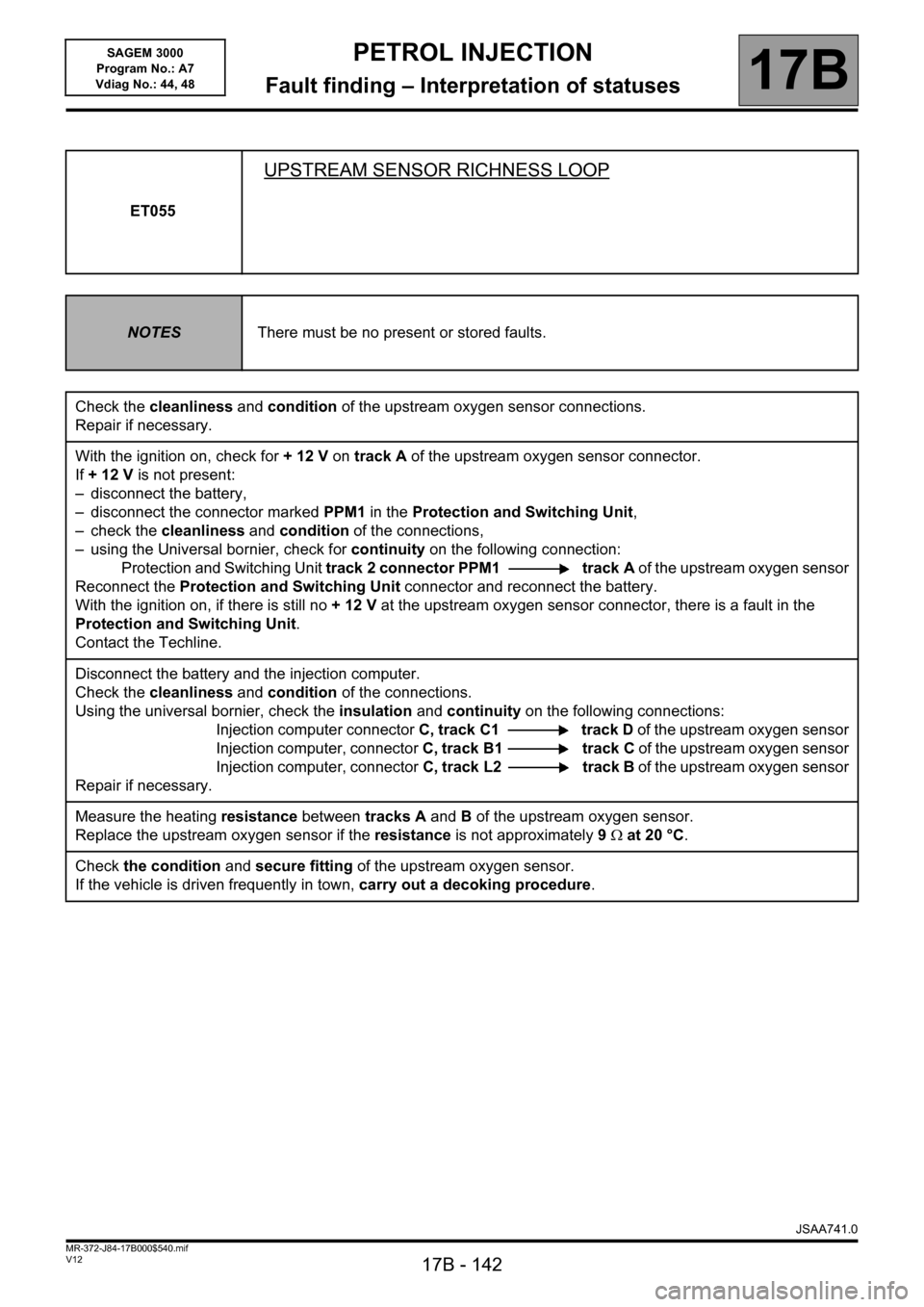
PETROL INJECTION
Fault finding – Interpretation of statuses17B
17B - 142V12 MR-372-J84-17B000$540.mif
SAGEM 3000
Program No.: A7
Vdiag No.: 44, 48
ET055
UPSTREAM SENSOR RICHNESS LOOP
NOTESThere must be no present or stored faults.
Check the cleanliness and condition of the upstream oxygen sensor connections.
Repair if necessary.
With the ignition on, check for + 12 V on track A of the upstream oxygen sensor connector.
If +12V is not present:
– disconnect the battery,
– disconnect the connector marked PPM1 in the Protection and Switching Unit,
– check the cleanliness and condition of the connections,
– using the Universal bornier, check for continuity on the following connection:
Protection and Switching Unit track 2 connector PPM1 track A of the upstream oxygen sensor
Reconnect the Protection and Switching Unit connector and reconnect the battery.
With the ignition on, if there is still no +12V at the upstream oxygen sensor connector, there is a fault in the
Protection and Switching Unit.
Contact the Techline.
Disconnect the battery and the injection computer.
Check the cleanliness and condition of the connections.
Using the universal bornier, check the insulation and continuity on the following connections:
Injection computer connectorC, track C1 track D of the upstream oxygen sensor
Injection computer, connectorC, track B1 track C of the upstream oxygen sensor
Injection computer, connectorC, track L2 track B of the upstream oxygen sensor
Repair if necessary.
Measure the heating resistance between tracks A and B of the upstream oxygen sensor.
Replace the upstream oxygen sensor if the resistance is not approximately 9 at 20 °C.
Check the condition and secure fitting of the upstream oxygen sensor.
If the vehicle is driven frequently in town, carry out a decoking procedure.
JSAA741.0
Page 143 of 181
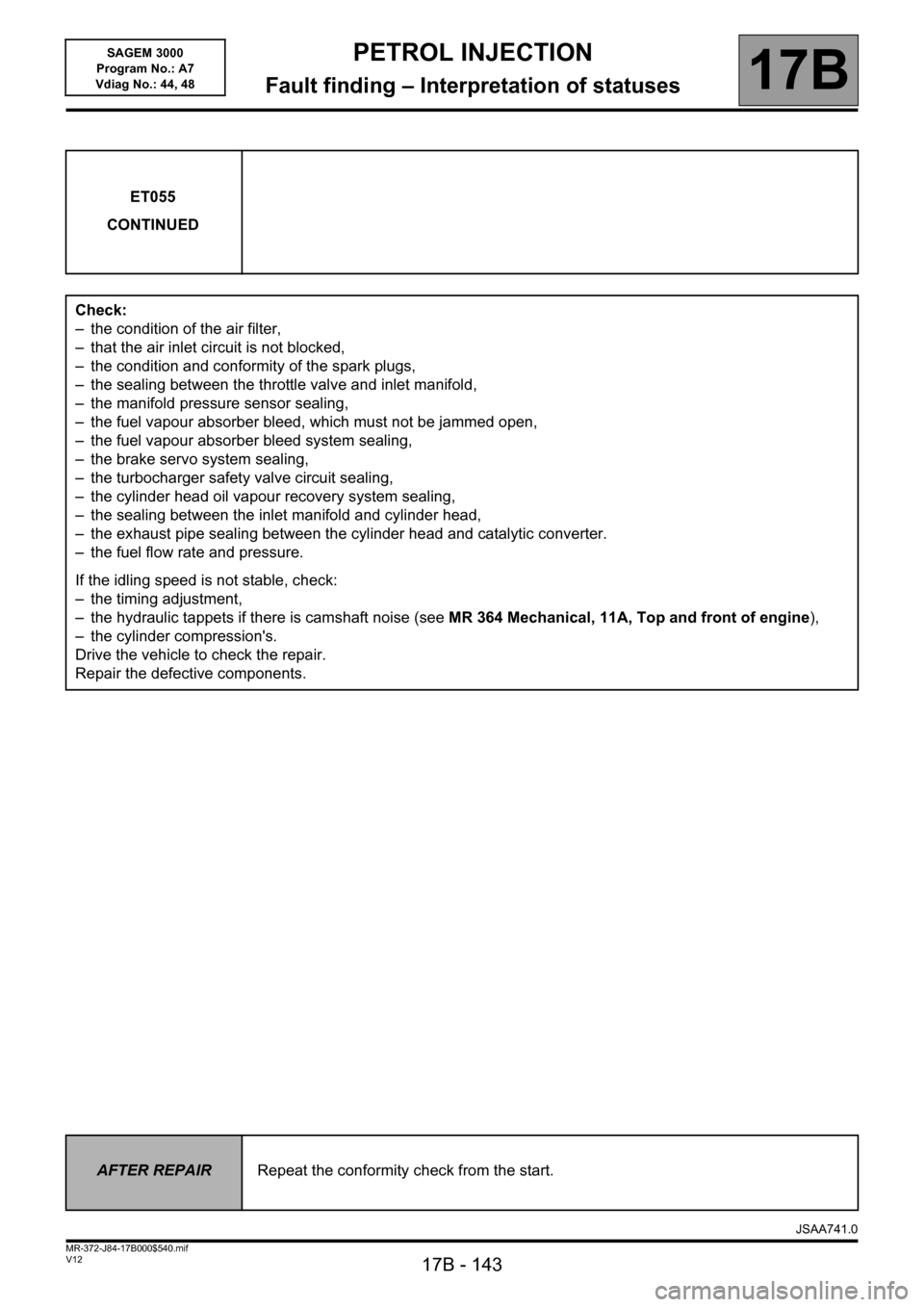
PETROL INJECTION
Fault finding – Interpretation of statuses17B
17B - 143V12 MR-372-J84-17B000$540.mif
SAGEM 3000
Program No.: A7
Vdiag No.: 44, 48
ET055
CONTINUED
Check:
– the condition of the air filter,
– that the air inlet circuit is not blocked,
– the condition and conformity of the spark plugs,
– the sealing between the throttle valve and inlet manifold,
– the manifold pressure sensor sealing,
– the fuel vapour absorber bleed, which must not be jammed open,
– the fuel vapour absorber bleed system sealing,
– the brake servo system sealing,
– the turbocharger safety valve circuit sealing,
– the cylinder head oil vapour recovery system sealing,
– the sealing between the inlet manifold and cylinder head,
– the exhaust pipe sealing between the cylinder head and catalytic converter.
– the fuel flow rate and pressure.
If the idling speed is not stable, check:
– the timing adjustment,
– the hydraulic tappets if there is camshaft noise (seeMR 364 Mechanical, 11A, Top and front of engine),
– the cylinder compression's.
Drive the vehicle to check the repair.
Repair the defective components.
AFTER REPAIRRepeat the conformity check from the start.
JSAA741.0
Page 144 of 181
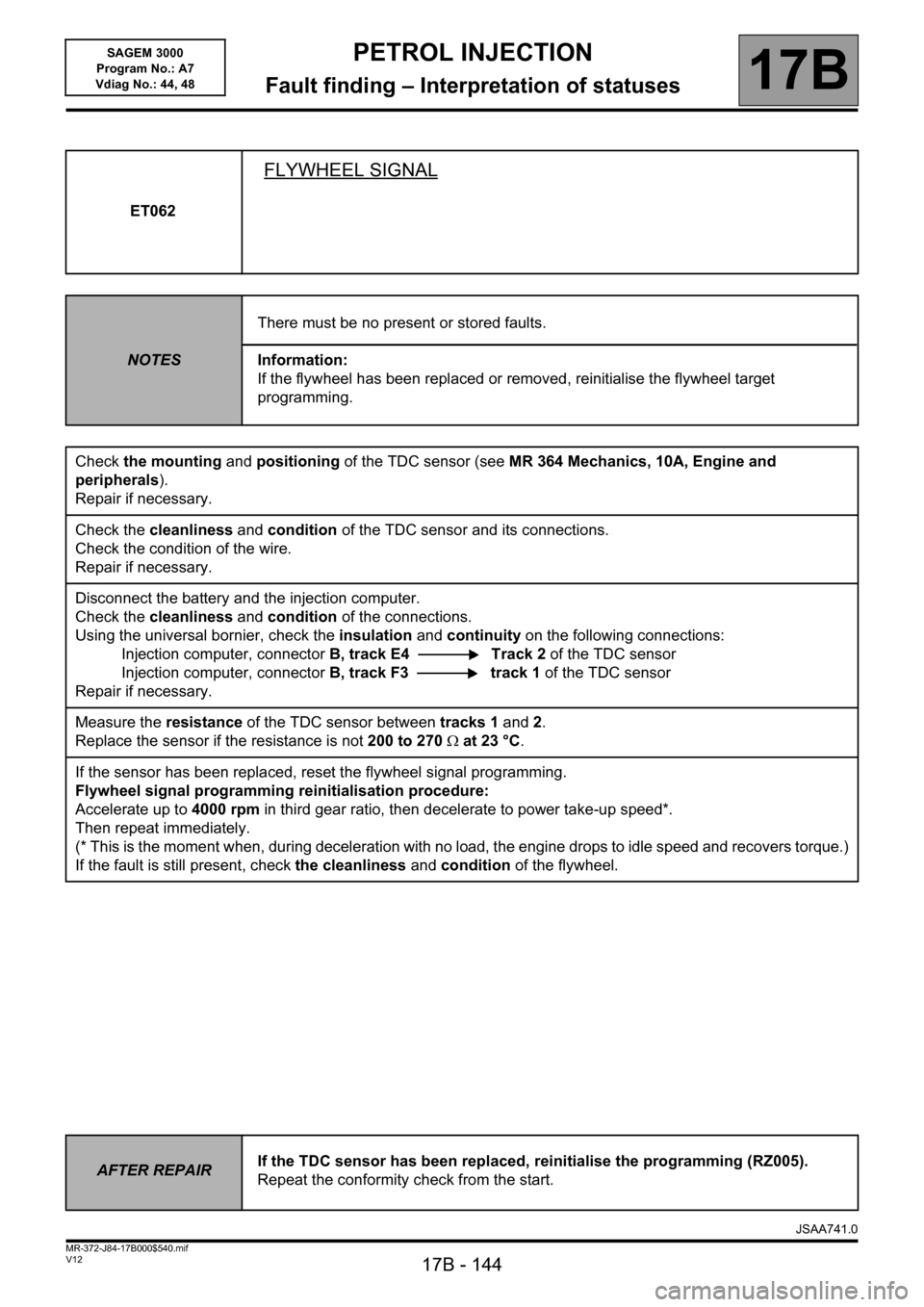
PETROL INJECTION
Fault finding – Interpretation of statuses17B
17B - 144V12 MR-372-J84-17B000$540.mif
SAGEM 3000
Program No.: A7
Vdiag No.: 44, 48
ET062
FLYWHEEL SIGNAL
NOTESThere must be no present or stored faults.
Information:
If the flywheel has been replaced or removed, reinitialise the flywheel target
programming.
Check the mounting and positioning of the TDC sensor (see MR 364 Mechanics, 10A, Engine and
peripherals).
Repair if necessary.
Check the cleanliness and condition of the TDC sensor and its connections.
Check the condition of the wire.
Repair if necessary.
Disconnect the battery and the injection computer.
Check the cleanliness and condition of the connections.
Using the universal bornier, check the insulation and continuity on the following connections:
Injection computer, connectorB, track E4 Track 2 of the TDC sensor
Injection computer, connectorB, track F3 track 1 of the TDC sensor
Repair if necessary.
Measure the resistance of the TDC sensor between tracks 1 and 2.
Replace the sensor if the resistance is not 200 to 270 at 23 °C.
If the sensor has been replaced, reset the flywheel signal programming.
Flywheel signal programming reinitialisation procedure:
Accelerate up to 4000 rpm in third gear ratio, then decelerate to power take-up speed*.
Then repeat immediately.
(* This is the moment when, during deceleration with no load, the engine drops to idle speed and recovers torque.)
If the fault is still present, check the cleanliness and condition of the flywheel.
AFTER REPAIRIf the TDC sensor has been replaced, reinitialise the programming (RZ005).
Repeat the conformity check from the start.
JSAA741.0