gas type SSANGYONG KORANDO 1997 Service Repair Manual
[x] Cancel search | Manufacturer: SSANGYONG, Model Year: 1997, Model line: KORANDO, Model: SSANGYONG KORANDO 1997Pages: 2053, PDF Size: 88.33 MB
Page 2 of 2053
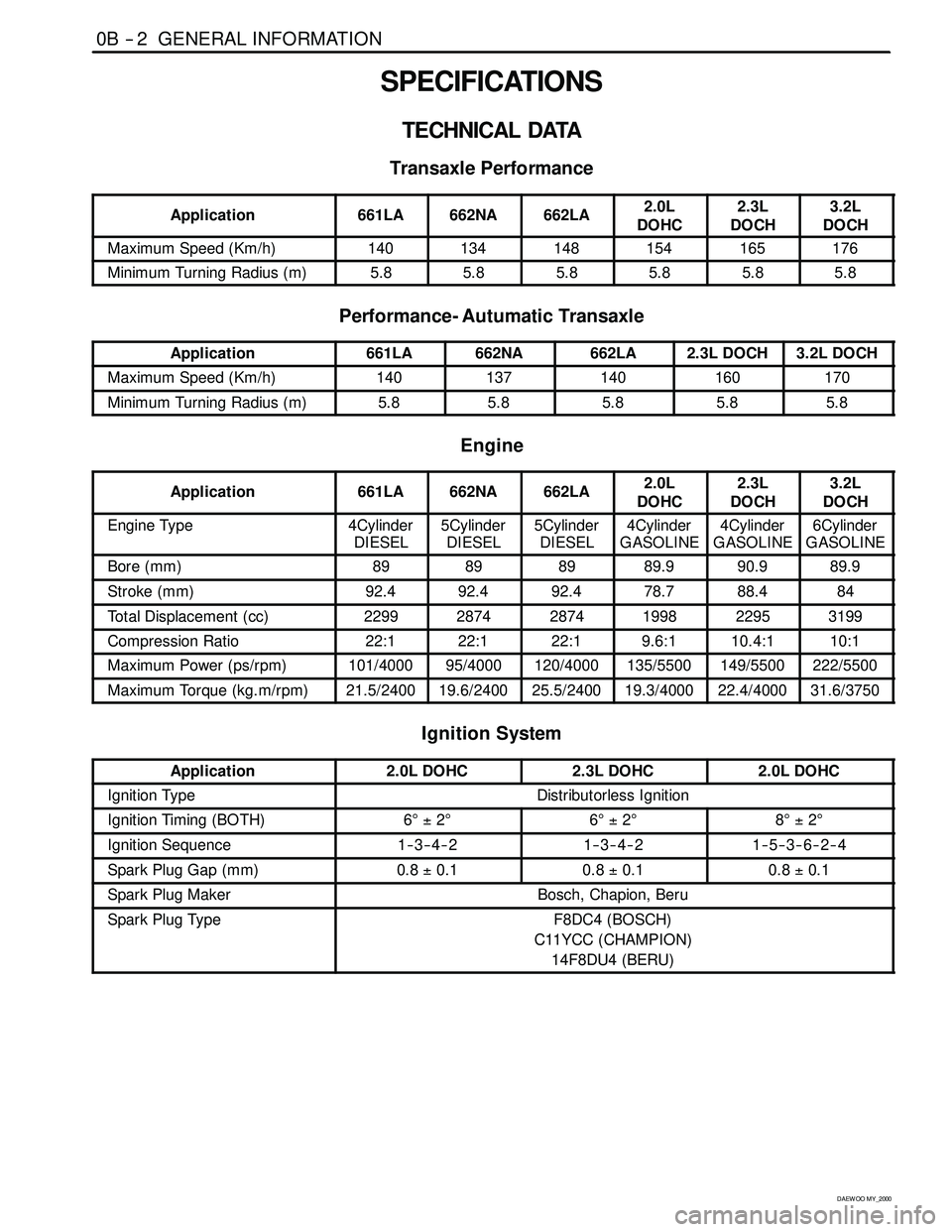
0B -- 2 GENERAL INFORMATION
D AEW OO M Y_2000
SPECIFICATIONS
TECHNICAL DATA
Transaxle Performance
Application661LA662NA662LA2.0L
DOHC2.3L
DOCH3.2L
DOCH
Maximum Speed (Km/h)140134148154165176
Minimum Turning Radius (m)5.85.85.85.85.85.8
Performance- Autumatic Transaxle
Application661LA662NA662LA2.3L DOCH3.2L DOCH
Maximum Speed (Km/h)140137140160170
Minimum Turning Radius (m)5.85.85.85.85.8
Engine
Application661LA662NA662LA2.0L
DOHC2.3L
DOCH3.2L
DOCH
Engine Type4Cylinder
DIESEL5Cylinder
DIESEL5Cylinder
DIESEL4Cylinder
GASOLINE4Cylinder
GASOLINE6Cylinder
GASOLINE
Bore (mm)89898989.990.989.9
Stroke (mm)92.492.492.478.788.484
Total Displacement (cc)229928742874199822953199
Compression Ratio22:122:122:19.6:110.4:110:1
Maximum Power (ps/rpm)101/400095/4000120/4000135/5500149/5500222/5500
Maximum Torque (kg.m/rpm)21.5/240019.6/240025.5/240019.3/400022.4/400031.6/3750
Ignition System
Application2.0L DOHC2.3L DOHC2.0L DOHC
Ignition TypeDistributorless Ignition
Ignition Timing (BOTH)6°±2°6°±2°8°±2°
Ignition Sequence1--3--4--21--3--4--21--5--3--6--2--4
Spark Plug Gap (mm)0.8±0.10.8±0.10.8±0.1
Spark Plug MakerBosch, Chapion, Beru
Spark Plug TypeF8DC4 (BOSCH)
C11YCC (CHAMPION)
14F8DU4 (BERU)
Page 8 of 2053
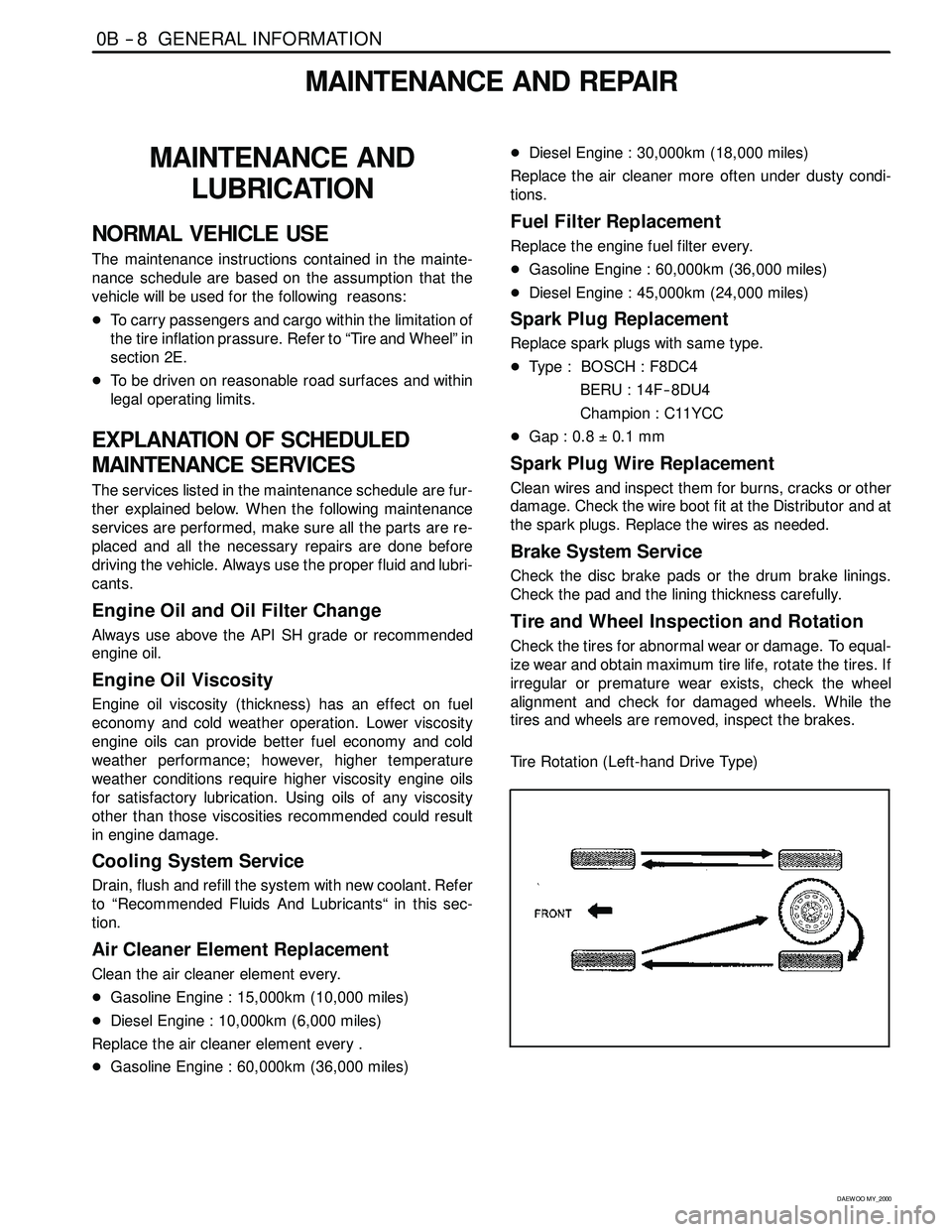
0B -- 8 GENERAL INFORMATION
D AEW OO M Y_2000
MAINTENANCE AND REPAIR
MAINTENANCE AND
LUBRICATION
NORMAL VEHICLE USE
The maintenance instructions contained in the mainte-
nance schedule are based on the assumption that the
vehicle will be used for the following reasons:
DTo carry passengers and cargo within the limitation of
the tire inflation prassure. Refer to “Tire and Wheel” in
section 2E.
DTo be driven on reasonable road surfaces and within
legal operating limits.
EXPLANATION OF SCHEDULED
MAINTENANCE SERVICES
The services listed in the maintenance schedule are fur-
ther explained below. When the following maintenance
services are performed, make sure all the parts are re-
placed and all the necessary repairs are done before
driving the vehicle. Always use the proper fluid and lubri-
cants.
Engine Oil and Oil Filter Change
Always use above the API SH grade or recommended
engine oil.
Engine Oil Viscosity
Engine oil viscosity (thickness) has an effect on fuel
economy and cold weather operation. Lower viscosity
engine oils can provide better fuel economy and cold
weather performance; however, higher temperature
weather conditions require higher viscosity engine oils
for satisfactory lubrication. Using oils of any viscosity
other than those viscosities recommended could result
in engine damage.
Cooling System Service
Drain, flush and refill the system with new coolant. Refer
to “Recommended Fluids And Lubricants“ in this sec-
tion.
Air Cleaner Element Replacement
Clean the air cleaner element every.
DGasoline Engine : 15,000km (10,000 miles)
DDiesel Engine : 10,000km (6,000 miles)
Replace the air cleaner element every .
DGasoline Engine : 60,000km (36,000 miles)DDiesel Engine : 30,000km (18,000 miles)
Replace the air cleaner more often under dusty condi-
tions.
Fuel Filter Replacement
Replace the engine fuel filter every.
DGasoline Engine : 60,000km (36,000 miles)
DDiesel Engine : 45,000km (24,000 miles)
Spark Plug Replacement
Replace spark plugs with same type.
DType : BOSCH : F8DC4
BERU : 14F-- 8DU4
Champion : C11YCC
DGap : 0.8±0.1 mm
Spark Plug Wire Replacement
Clean wires and inspect them for burns, cracks or other
damage. Check the wire boot fit at the Distributor and at
the spark plugs. Replace the wires as needed.
Brake System Service
Check the disc brake pads or the drum brake linings.
Check the pad and the lining thickness carefully.
Tire and Wheel Inspection and Rotation
Check the tires for abnormal wear or damage. To equal-
ize wear and obtain maximum tire life, rotate the tires. If
irregular or premature wear exists, check the wheel
alignment and check for damaged wheels. While the
tires and wheels are removed, inspect the brakes.
Tire Rotation (Left-hand Drive Type)
Page 18 of 2053
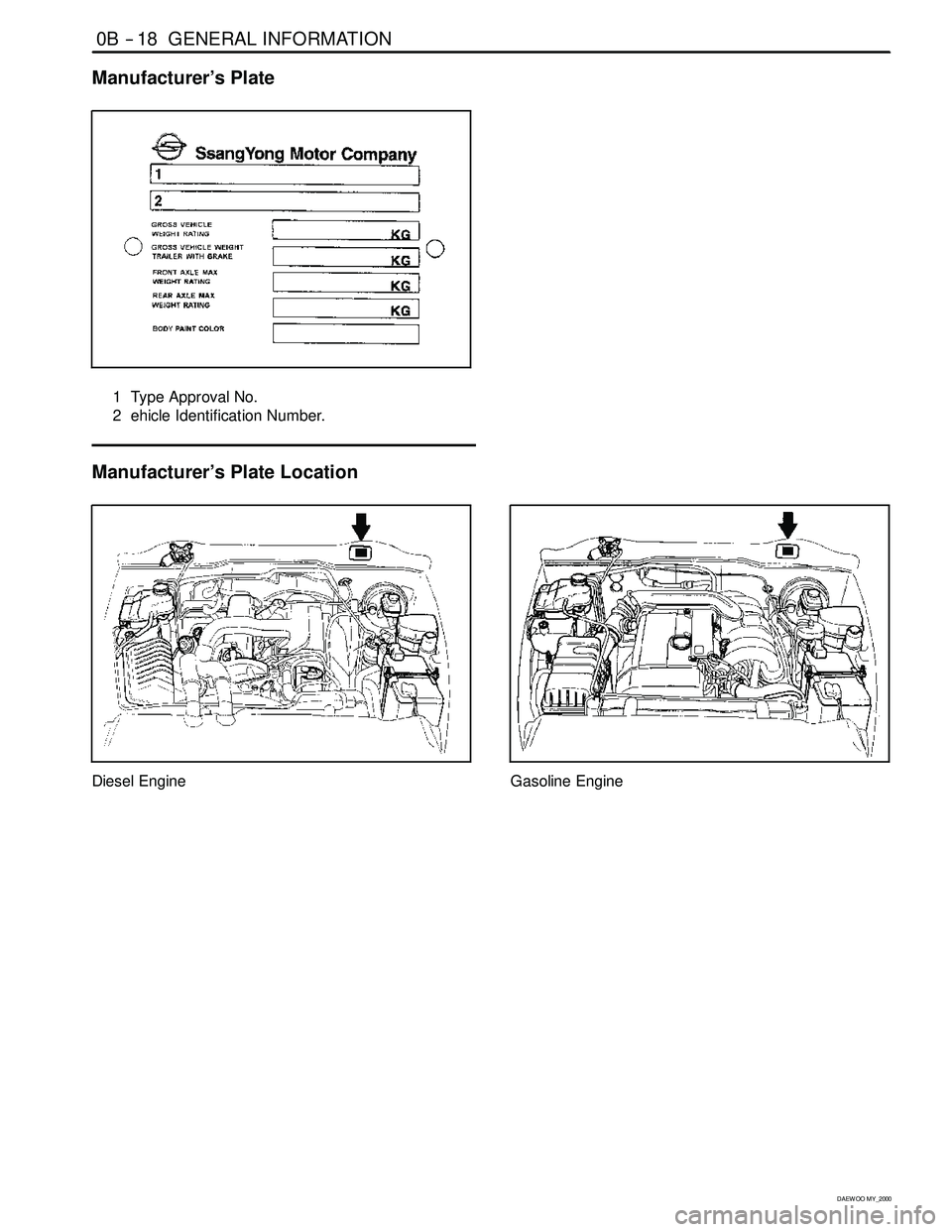
0B -- 18 GENERAL INFORMATION
D AEW OO M Y_2000
Manufacturer’s Plate
1 Type Approval No.
2 ehicle Identification Number.
Manufacturer’s Plate Location
Diesel EngineGasoline Engine
Page 22 of 2053
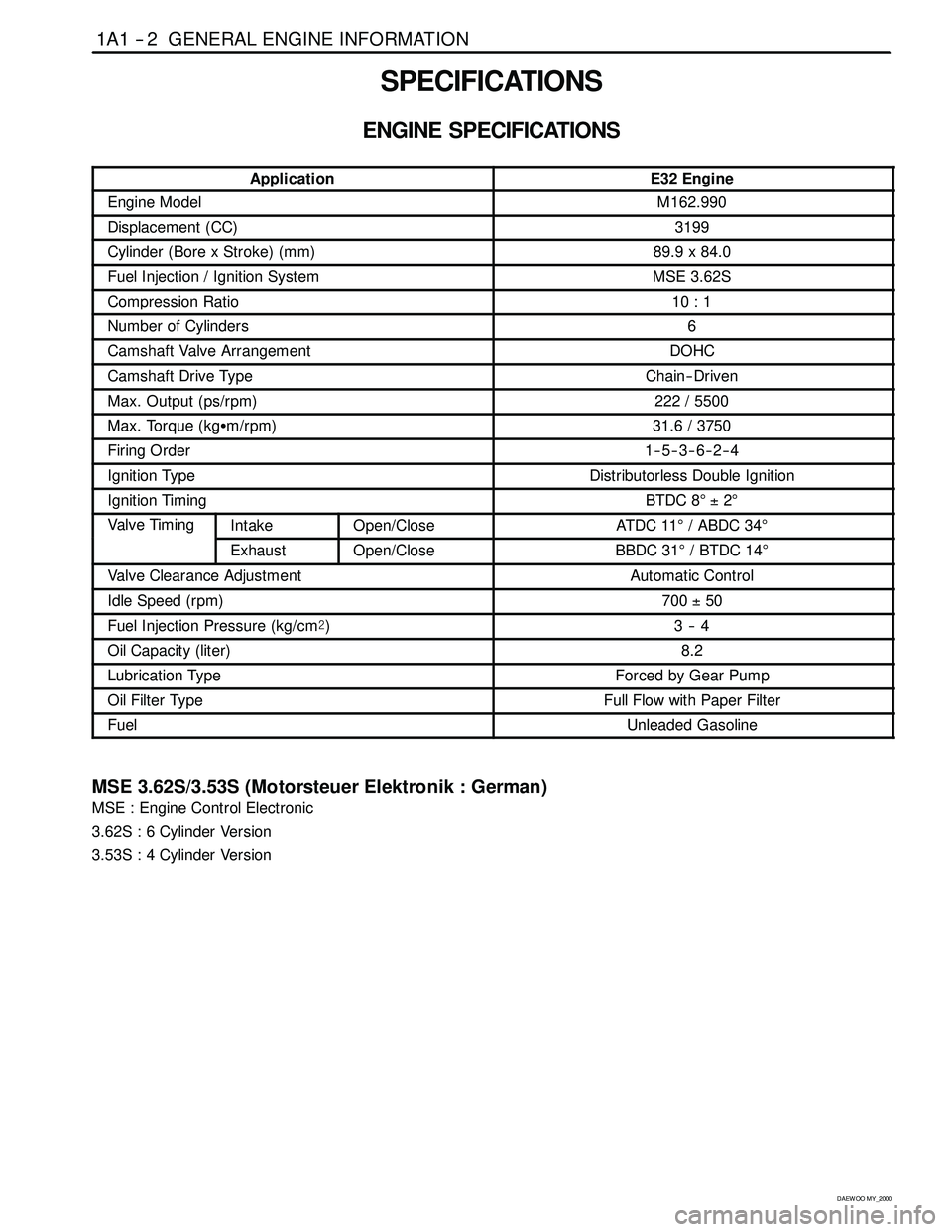
1A1 -- 2 GENERAL ENGINE INFORMATION
D AEW OO M Y_2000
SPECIFICATIONS
ENGINE SPECIFICATIONS
ApplicationE32 Engine
Engine ModelM162.990
Displacement (CC)3199
Cylinder (Bore x Stroke)(mm)89.9 x 84.0
Fuel Injection / Ignition SystemMSE 3.62S
Compression Ratio10 : 1
Number of Cylinders6
Camshaft Valve ArrangementDOHC
Camshaft Drive TypeChain-- Driven
Max. Output (ps/rpm)222 / 5500
Max. Torque (kgSm/rpm)31.6 / 3750
Firing Order1--5--3--6--2--4
Ignition TypeDistributorless Double Ignition
Ignition TimingBTDC 8°±2°
Valve TimingIntakeOpen/CloseAT DC 11°/ ABDC 34°g
ExhaustOpen/CloseBBDC 31°/BTDC14°
Valve Clearance AdjustmentAutomatic Control
Idle Speed (rpm)700±50
Fuel Injection Pressure (kg/cm@)3--4
Oil Capacity (liter)8.2
Lubrication TypeForced by Gear Pump
Oil Filter TypeFull Flow with Paper Filter
FuelUnleaded Gasoline
MSE 3.62S/3.53S (Motorsteuer Elektronik : German)
MSE : Engine Control Electronic
3.62S : 6 Cylinder Version
3.53S : 4 Cylinder Version
Page 26 of 2053
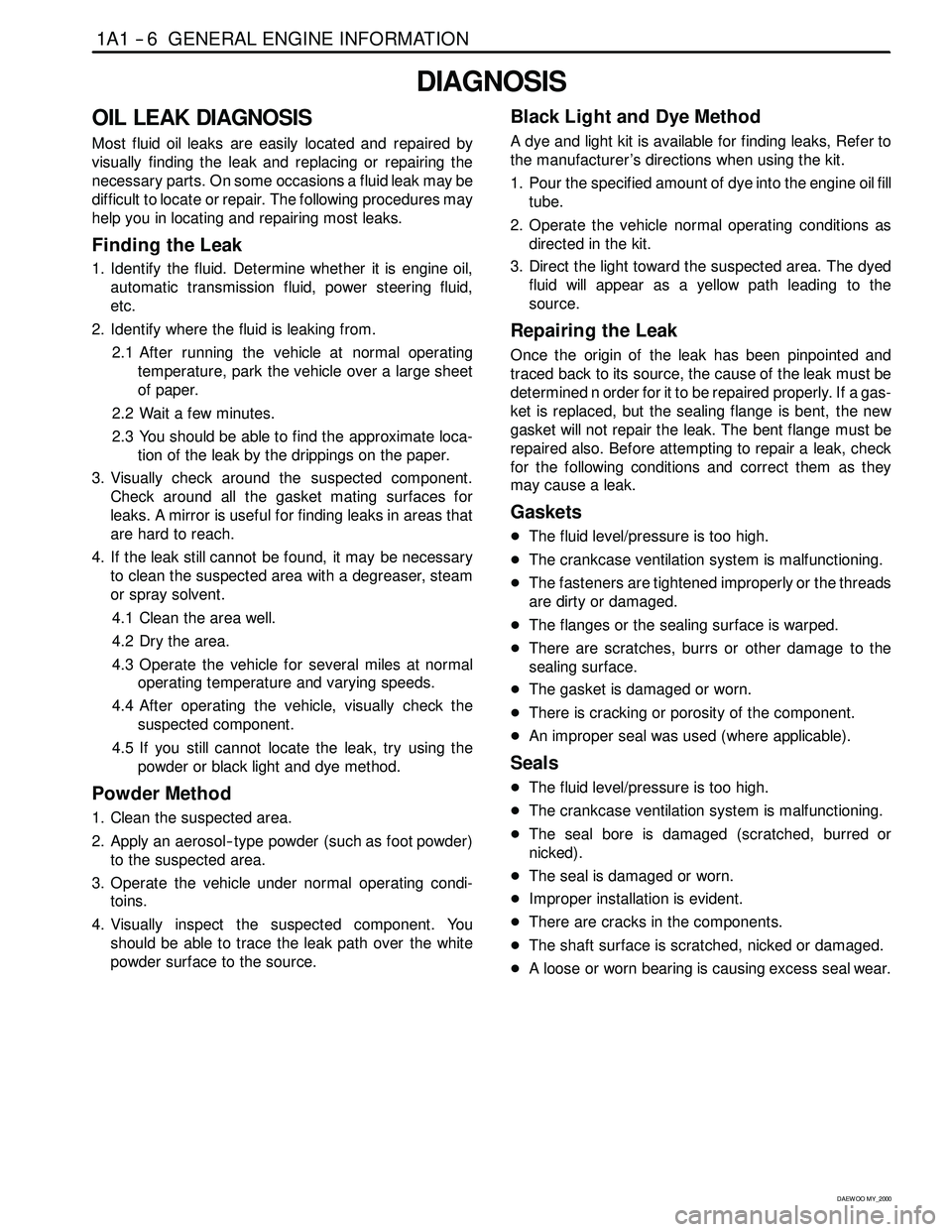
1A1 -- 6 GENERAL ENGINE INFORMATION
D AEW OO M Y_2000
DIAGNOSIS
OIL LEAK DIAGNOSIS
Most fluid oil leaks are easily located and repaired by
visually finding the leak and replacing or repairing the
necessary parts. On some occasions a fluid leak may be
difficult to locate or repair. The following procedures may
help you in locating and repairing most leaks.
Finding the Leak
1. Identify the fluid. Determine whether it is engine oil,
automatic transmission fluid, power steering fluid,
etc.
2. Identify where the fluid is leaking from.
2.1 After running the vehicle at normal operating
temperature, park the vehicle over a large sheet
of paper.
2.2 Wait a few minutes.
2.3 You should be able to find the approximate loca-
tion of the leak by the drippings on the paper.
3. Visually check around the suspected component.
Check around all the gasket mating surfaces for
leaks. A mirror is useful for finding leaks in areas that
are hard to reach.
4. If the leak still cannot be found, it may be necessary
to clean the suspected area with a degreaser, steam
or spray solvent.
4.1 Clean the area well.
4.2 Dry the area.
4.3 Operate the vehicle for several miles at normal
operating temperature and varying speeds.
4.4 After operating the vehicle, visually check the
suspected component.
4.5 If you still cannot locate the leak, try using the
powder or black light and dye method.
Powder Method
1. Clean the suspected area.
2. Apply an aerosol-- type powder (such as foot powder)
to the suspected area.
3. Operate the vehicle under normal operating condi-
toins.
4. Visually inspect the suspected component. You
should be able to trace the leak path over the white
powder surface to the source.
Black Light and Dye Method
A dye and light kit is available for finding leaks, Refer to
the manufacturer ’s directions when using the kit.
1. Pour the specified amount of dye into the engine oil fill
tube.
2. Operate the vehicle normal operating conditions as
directed in the kit.
3. Direct the light toward the suspected area. The dyed
fluid willappear as a yellow path leading to the
source.
Repairing the Leak
Once the origin of the leak has been pinpointed and
traced back to its source, the cause of the leak must be
determined n order for it to be repaired properly. If a gas-
ket is replaced, but the sealing flange is bent, the new
gasket will not repair the leak. Thebent flange must be
repaired also. Before attempting to repair a leak, check
for the following conditions and correct them as they
may cause a leak.
Gaskets
DThe fluid level/pressure is too high.
DThe crankcase ventilation system is malfunctioning.
DThe fasteners are tightened improperly or the threads
are dirty or damaged.
DThe flanges or the sealing surface is warped.
DThere are scratches, burrs or other damage to the
sealing surface.
DThe gasket is damaged or worn.
DThere is cracking or porosity of the component.
DAn improper seal was used (where applicable).
Seals
DThe fluid level/pressure is too high.
DThe crankcase ventilation system is malfunctioning.
DThe seal bore is damaged (scratched, burred or
nicked).
DThe seal is damaged or worn.
DImproper installation is evident.
DThere are cracks in the components.
DThe shaft surface is scratched, nicked or damaged.
DA loose or worn bearing is causing excess seal wear.
Page 286 of 2053
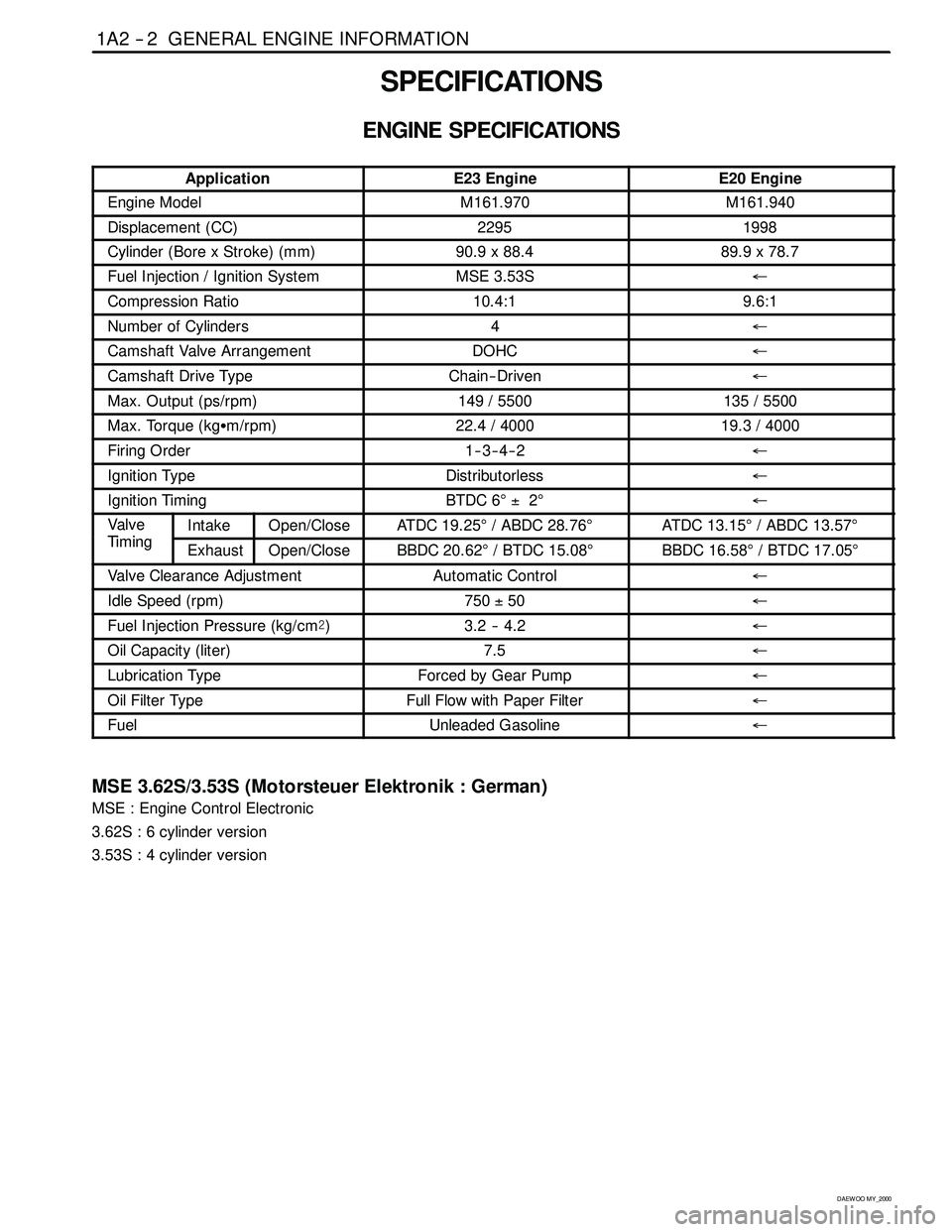
1A2 -- 2 GENERAL ENGINE INFORMATION
D AEW OO M Y_2000
SPECIFICATIONS
ENGINE SPECIFICATIONS
ApplicationE23 EngineE20 Engine
Engine ModelM161.970M161.940
Displacement (CC)22951998
Cylinder (Bore x Stroke)(mm)90.9 x 88.489.9 x 78.7
Fuel Injection / Ignition SystemMSE 3.53S←
Compression Ratio10.4:19.6:1
Number of Cylinders4←
Camshaft Valve ArrangementDOHC←
Camshaft Drive TypeChain-- Driven←
Max. Output (ps/rpm)149 / 5500135 / 5500
Max. Torque (kgSm/rpm)22.4 / 400019.3 / 4000
Firing Order1--3--4--2←
Ignition TypeDistributorless←
Ignition TimingBTDC 6°±2°←
Va lv e
Tii
IntakeOpen/CloseATDC 19.25°/ ABDC 28.76°ATDC 13.15°/ ABDC 13.57°
Tim in gExhaustOpen/CloseBBDC 20.62°/ BTDC 15.08°BBDC 16.58°/ BTDC 17.05°
Valve Clearance AdjustmentAutomatic Control←
Idle Speed (rpm)750±50←
Fuel Injection Pressure (kg/cm@)3.2 -- 4.2←
Oil Capacity (liter)7.5←
Lubrication TypeForced by Gear Pump←
Oil Filter TypeFull Flow with Paper Filter←
FuelUnleaded Gasoline←
MSE 3.62S/3.53S (Motorsteuer Elektronik : German)
MSE : Engine Control Electronic
3.62S : 6 cylinder version
3.53S : 4 cylinder version
Page 291 of 2053
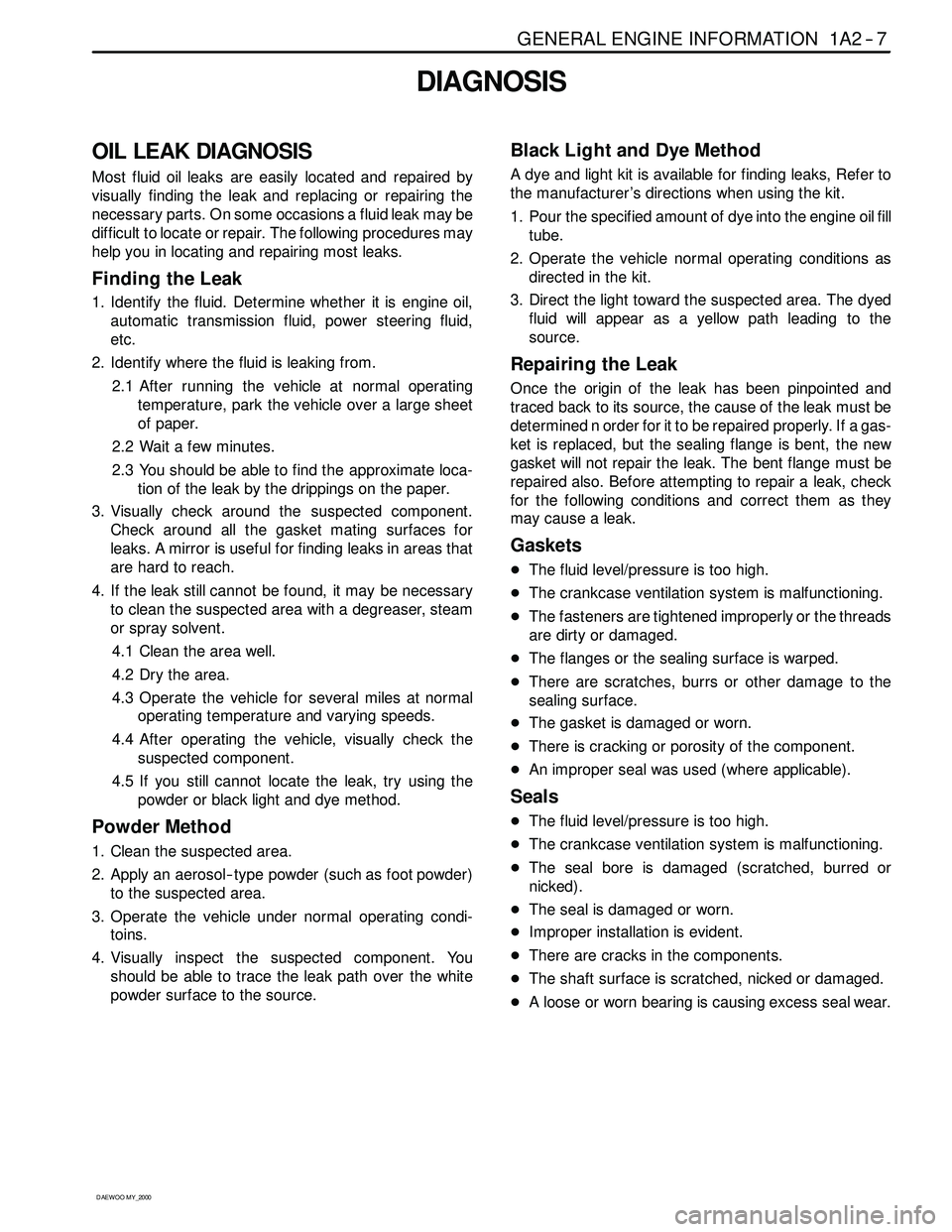
GENERAL ENGINE INFORMATION 1A2 -- 7
D AEW OO M Y_2000
DIAGNOSIS
OIL LEAK DIAGNOSIS
Most fluid oil leaks are easily located and repaired by
visually finding the leak and replacing or repairing the
necessary parts. On some occasions a fluid leak may be
difficult to locate or repair. The following procedures may
help you in locating and repairing most leaks.
Finding the Leak
1. Identify the fluid. Determine whether it is engine oil,
automatic transmission fluid, power steering fluid,
etc.
2. Identify where the fluid is leaking from.
2.1 After running the vehicle at normal operating
temperature, park the vehicle over a large sheet
of paper.
2.2 Wait a few minutes.
2.3 You should be able to find the approximate loca-
tion of the leak by the drippings on the paper.
3. Visually check around the suspected component.
Check around all the gasket mating surfaces for
leaks. A mirror is useful for finding leaks in areas that
are hard to reach.
4. If the leak still cannot be found, it may be necessary
to clean the suspected area with a degreaser, steam
or spray solvent.
4.1 Clean the area well.
4.2 Dry the area.
4.3 Operate the vehicle for several miles at normal
operating temperature and varying speeds.
4.4 After operating the vehicle, visually check the
suspected component.
4.5 If you still cannot locate the leak, try using the
powder or black light and dye method.
Powder Method
1. Clean the suspected area.
2. Apply an aerosol-- type powder (such as foot powder)
to the suspected area.
3. Operate the vehicle under normal operating condi-
toins.
4. Visually inspect the suspected component. You
should be able to trace the leak path over the white
powder surface to the source.
Black Light and Dye Method
A dye and light kit is available for finding leaks, Refer to
the manufacturer ’s directions when using the kit.
1. Pour the specified amount of dye into the engine oil fill
tube.
2. Operate the vehicle normal operating conditions as
directed in the kit.
3. Direct the light toward the suspected area. The dyed
fluid willappear as a yellow path leading to the
source.
Repairing the Leak
Once the origin of the leak has been pinpointed and
traced back to its source, the cause of the leak must be
determined n order for it to be repaired properly. If a gas-
ket is replaced, but the sealing flange is bent, the new
gasket will not repair the leak. Thebent flange must be
repaired also. Before attempting to repair a leak, check
for the following conditions and correct them as they
may cause a leak.
Gaskets
DThe fluid level/pressure is too high.
DThe crankcase ventilation system is malfunctioning.
DThe fasteners are tightened improperly or the threads
are dirty or damaged.
DThe flanges or the sealing surface is warped.
DThere are scratches, burrs or other damage to the
sealing surface.
DThe gasket is damaged or worn.
DThere is cracking or porosity of the component.
DAn improper seal was used (where applicable).
Seals
DThe fluid level/pressure is too high.
DThe crankcase ventilation system is malfunctioning.
DThe seal bore is damaged (scratched, burred or
nicked).
DThe seal is damaged or worn.
DImproper installation is evident.
DThere are cracks in the components.
DThe shaft surface is scratched, nicked or damaged.
DA loose or worn bearing is causing excess seal wear.
Page 545 of 2053
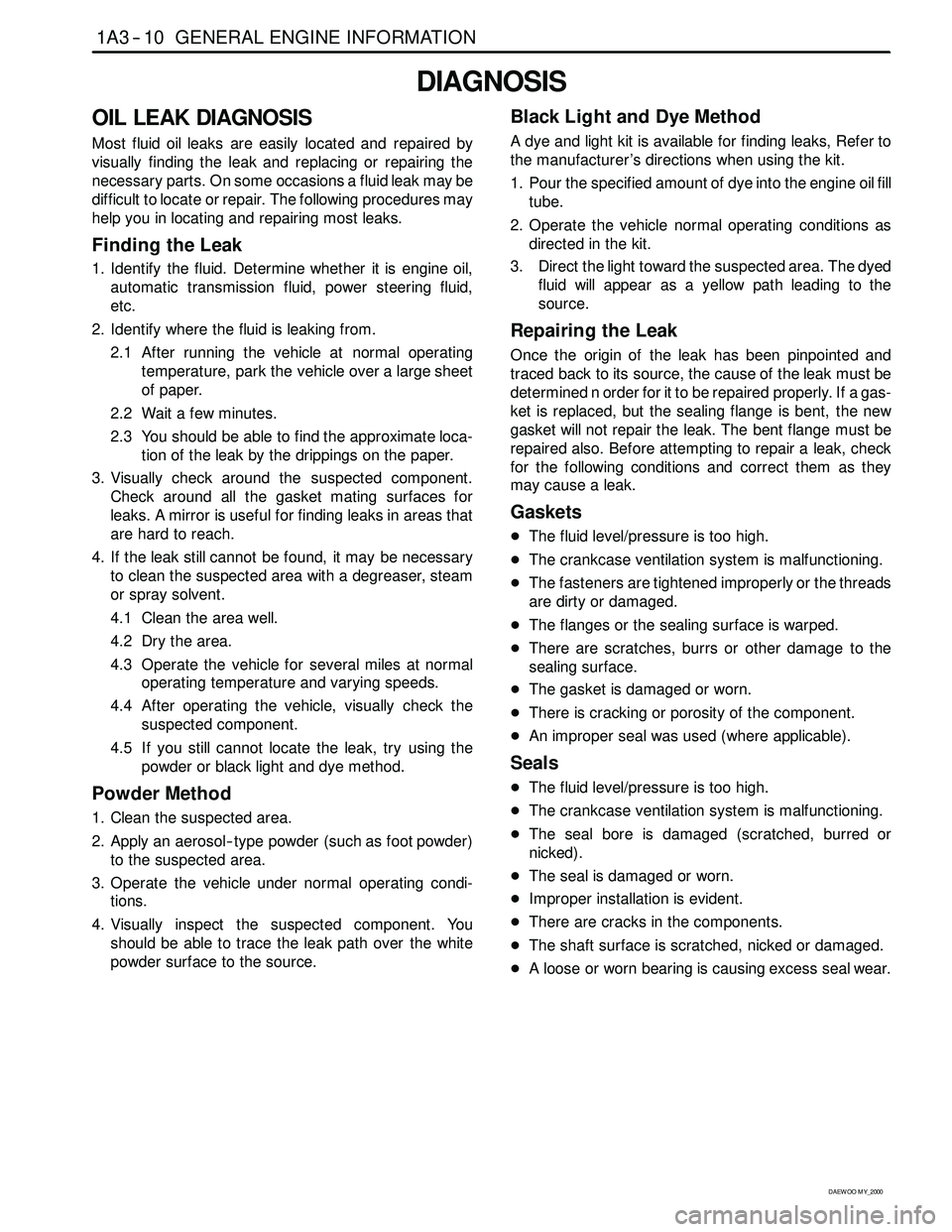
1A3 -- 10 GENERAL ENGINE INFORMATION
D AEW OO M Y_2000
DIAGNOSIS
OIL LEAK DIAGNOSIS
Most fluid oil leaks are easily located and repaired by
visually finding the leak and replacing or repairing the
necessary parts. On some occasions a fluid leak may be
difficult to locate or repair. The following procedures may
help you in locating and repairing most leaks.
Finding the Leak
1. Identify the fluid. Determine whether it is engine oil,
automatic transmission fluid, power steering fluid,
etc.
2. Identify where the fluid is leaking from.
2.1 After running the vehicle at normal operating
temperature, park the vehicle over a large sheet
of paper.
2.2 Wait a few minutes.
2.3 You should be able to find the approximate loca-
tion of the leak by the drippings on the paper.
3. Visually check around the suspected component.
Check around all the gasket mating surfaces for
leaks. A mirror is useful for finding leaks in areas that
are hard to reach.
4. If the leak still cannot be found, it may be necessary
to clean the suspected area with a degreaser, steam
or spray solvent.
4.1 Clean the area well.
4.2 Dry the area.
4.3 Operate the vehicle for several miles at normal
operating temperature and varying speeds.
4.4 After operating the vehicle, visually check the
suspected component.
4.5 If you still cannot locate the leak, try using the
powder or black light and dye method.
Powder Method
1. Clean the suspected area.
2. Apply an aerosol-- type powder (such as foot powder)
to the suspected area.
3. Operate the vehicle under normal operating condi-
tions.
4. Visually inspect the suspected component. You
should be able to trace the leak path over the white
powder surface to the source.
Black Light and Dye Method
A dye and light kit is available for finding leaks, Refer to
the manufacturer ’s directions when using the kit.
1. Pour the specified amount of dye into the engine oil fill
tube.
2. Operate the vehicle normal operating conditions as
directed in the kit.
3. Direct the light toward the suspected area. The dyed
fluid willappear as a yellow path leading to the
source.
Repairing the Leak
Once the origin of the leak has been pinpointed and
traced back to its source, the cause of the leak must be
determined n order for it to be repaired properly. If a gas-
ket is replaced, but the sealing flange is bent, the new
gasket will not repair the leak. Thebent flange must be
repaired also. Before attempting to repair a leak, check
for the following conditions and correct them as they
may cause a leak.
Gaskets
DThe fluid level/pressure is too high.
DThe crankcase ventilation system is malfunctioning.
DThe fasteners are tightened improperly or the threads
are dirty or damaged.
DThe flanges or the sealing surface is warped.
DThere are scratches, burrs or other damage to the
sealing surface.
DThe gasket is damaged or worn.
DThere is cracking or porosity of the component.
DAn improper seal was used (where applicable).
Seals
DThe fluid level/pressure is too high.
DThe crankcase ventilation system is malfunctioning.
DThe seal bore is damaged (scratched, burred or
nicked).
DThe seal is damaged or worn.
DImproper installation is evident.
DThere are cracks in the components.
DThe shaft surface is scratched, nicked or damaged.
DA loose or worn bearing is causing excess seal wear.
Page 896 of 2053
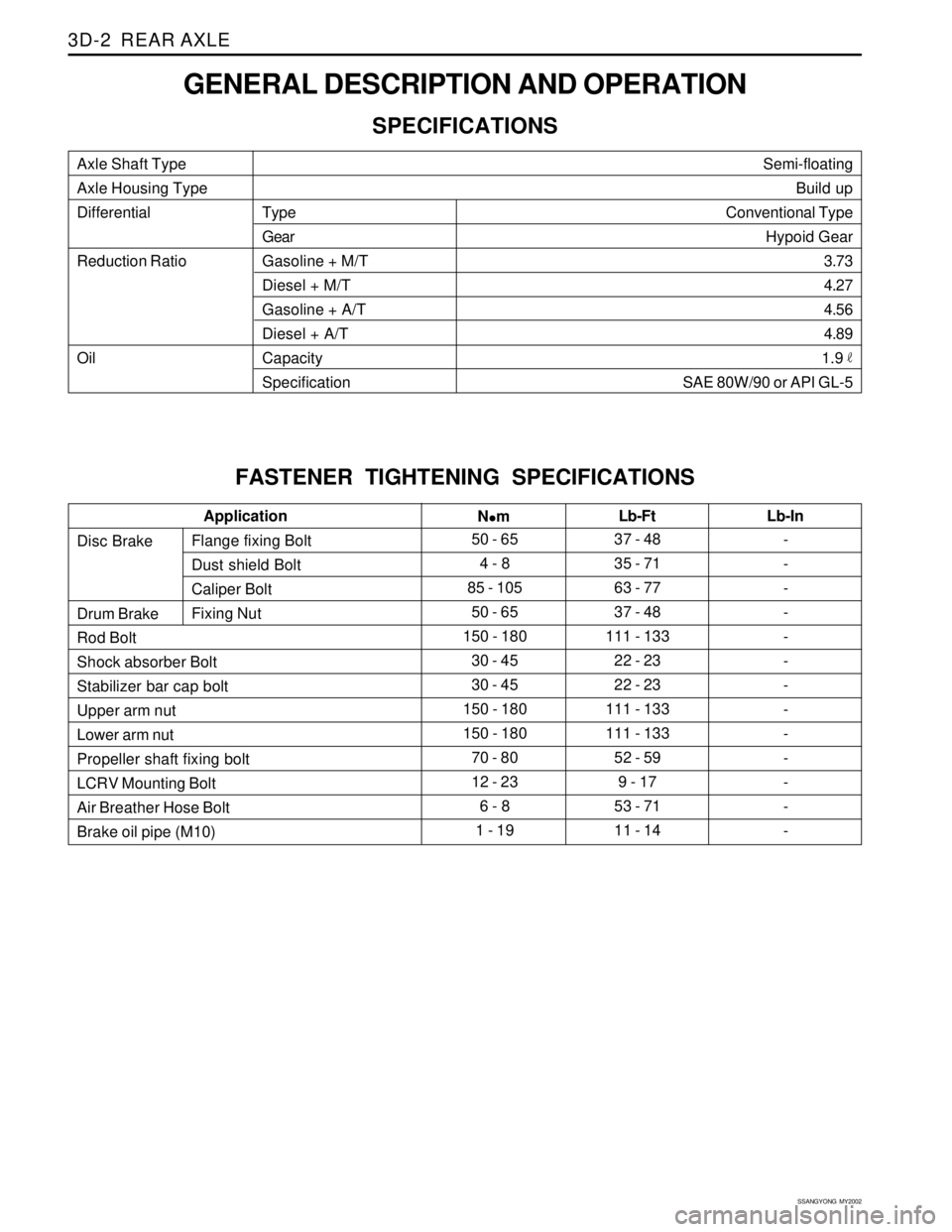
SSANGYONG MY2002
3D-2 REAR AXLE
Disc Brake
Drum Brake50 - 65
4 - 8
85 - 105
50 - 65
150 - 180
30 - 45
30 - 45
150 - 180
150 - 180
70 - 80
12 - 23
6 - 8
1 - 19Lb-Ft Axle Shaft Type
Axle Housing Type
Differential
Reduction Ratio
OilType
Gear
Gasoline + M/T
Diesel + M/T
Gasoline + A/T
Diesel + A/T
Capacity
SpecificationSemi-floating
Build up
Conventional Type
Hypoid Gear
3.73
4.27
4.56
4.89
1.9
SAE 80W/90 or API GL-5
GENERAL DESCRIPTION AND OPERATION
SPECIFICATIONS
37 - 48
35 - 71
63 - 77
37 - 48
111 - 133
22 - 23
22 - 23
111 - 133
111 - 133
52 - 59
9 - 17
53 - 71
11 - 14 Flange fixing Bolt
Dust shield Bolt
Caliper Bolt
Fixing NutN
z z z z
zm ApplicationLb-In
-
-
-
-
-
-
-
-
-
-
-
-
-
FASTENER TIGHTENING SPECIFICATIONS
Rod Bolt
Shock absorber Bolt
Stabilizer bar cap bolt
Upper arm nut
Lower arm nut
Propeller shaft fixing bolt
LCRV Mounting Bolt
Air Breather Hose Bolt
Brake oil pipe (M10)
Page 1143 of 2053
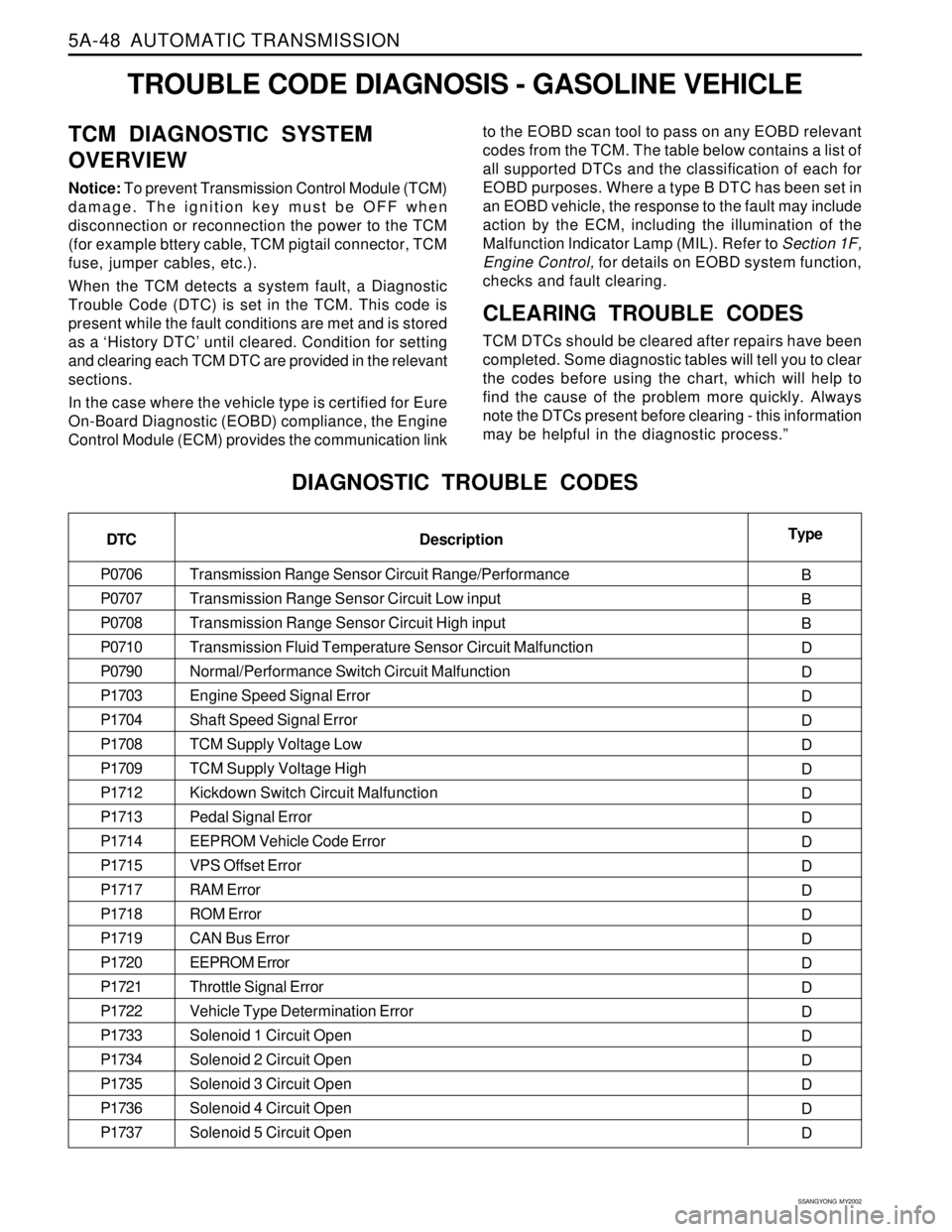
5A-48 AUTOMATIC TRANSMISSION
SSANGYONG MY2002
TROUBLE CODE DIAGNOSIS - GASOLINE VEHICLE
TCM DIAGNOSTIC SYSTEM
OVERVIEW
Notice: To prevent Transmission Control Module (TCM)
damage. The ignition key must be OFF when
disconnection or reconnection the power to the TCM
(for example bttery cable, TCM pigtail connector, TCM
fuse, jumper cables, etc.).
When the TCM detects a system fault, a Diagnostic
Trouble Code (DTC) is set in the TCM. This code is
present while the fault conditions are met and is stored
as a ‘History DTC’ until cleared. Condition for setting
and clearing each TCM DTC are provided in the relevant
sections.
In the case where the vehicle type is certified for Eure
On-Board Diagnostic (EOBD) compliance, the Engine
Control Module (ECM) provides the communication linkto the EOBD scan tool to pass on any EOBD relevant
codes from the TCM. The table below contains a list of
all supported DTCs and the classification of each for
EOBD purposes. Where a type B DTC has been set in
an EOBD vehicle, the response to the fault may include
action by the ECM, including the illumination of the
Malfunction lndicator Lamp (MIL). Refer to Section 1F,
Engine Control, for details on EOBD system function,
checks and fault clearing.
CLEARING TROUBLE CODES
TCM DTCs should be cleared after repairs have been
completed. Some diagnostic tables will tell you to clear
the codes before using the chart, which will help to
find the cause of the problem more quickly. Always
note the DTCs present before clearing - this information
may be helpful in the diagnostic process.”
DIAGNOSTIC TROUBLE CODES
DTC
P0706
P0707
P0708
P0710
P0790
P1703
P1704
P1708
P1709
P1712
P1713
P1714
P1715
P1717
P1718
P1719
P1720
P1721
P1722
P1733
P1734
P1735
P1736
P1737Type
B
B
B
D
D
D
D
D
D
D
D
D
D
D
D
D
D
D
D
D
D
D
D
D Description
Transmission Range Sensor Circuit Range/Performance
Transmission Range Sensor Circuit Low input
Transmission Range Sensor Circuit High input
Transmission Fluid Temperature Sensor Circuit Malfunction
Normal/Performance Switch Circuit Malfunction
Engine Speed Signal Error
Shaft Speed Signal Error
TCM Supply Voltage Low
TCM Supply Voltage High
Kickdown Switch Circuit Malfunction
Pedal Signal Error
EEPROM Vehicle Code Error
VPS Offset Error
RAM Error
ROM Error
CAN Bus Error
EEPROM Error
Throttle Signal Error
Vehicle Type Determination Error
Solenoid 1 Circuit Open
Solenoid 2 Circuit Open
Solenoid 3 Circuit Open
Solenoid 4 Circuit Open
Solenoid 5 Circuit Open