ESP SSANGYONG MUSSO 1998 Workshop User Guide
[x] Cancel search | Manufacturer: SSANGYONG, Model Year: 1998, Model line: MUSSO, Model: SSANGYONG MUSSO 1998Pages: 1463, PDF Size: 19.88 MB
Page 1045 of 1463
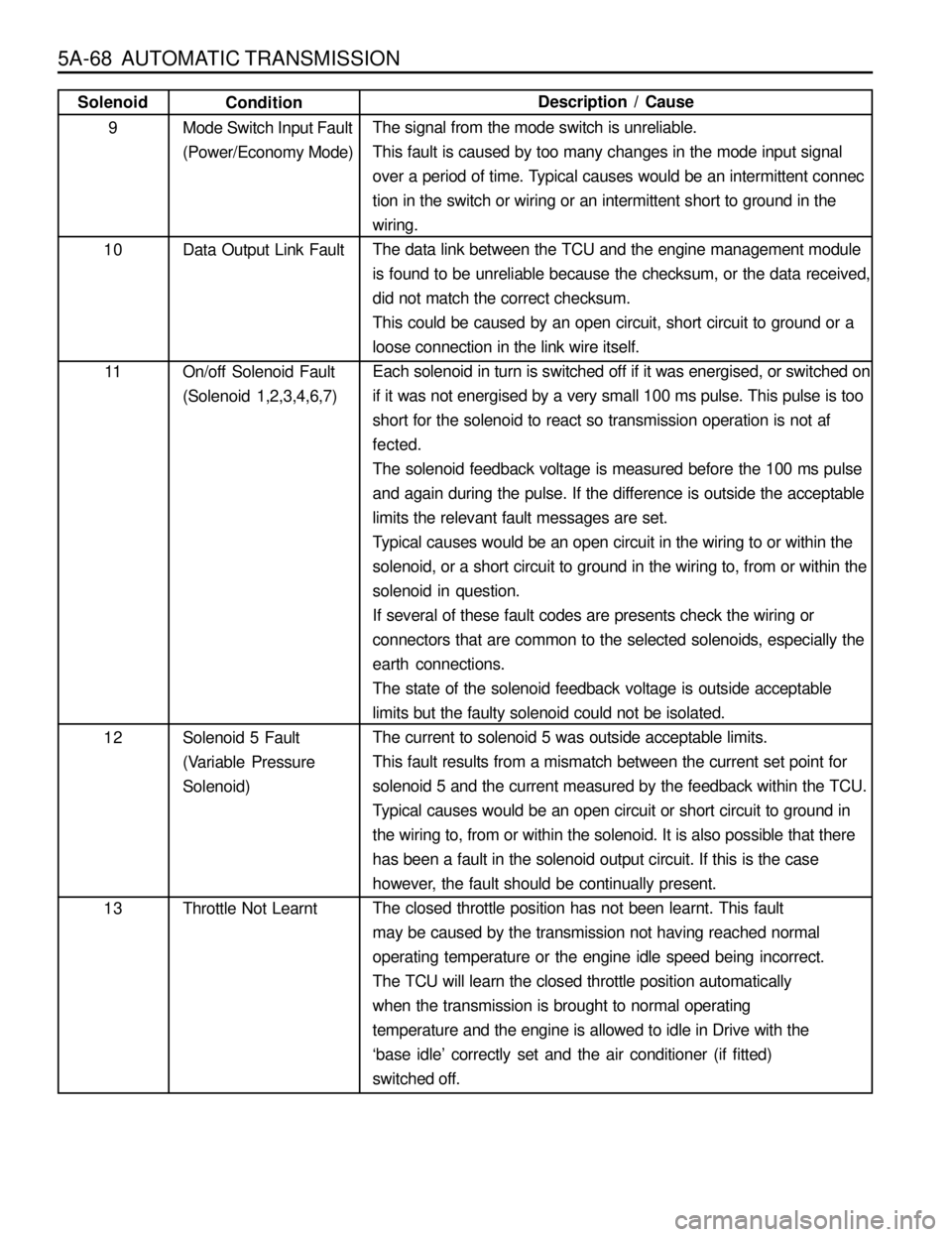
5A-68 AUTOMATIC TRANSMISSION
Description / Cause
The signal from the mode switch is unreliable.
This fault is caused by too many changes in the mode input signal
over a period of time. Typical causes would be an intermittent connec
tion in the switch or wiring or an intermittent short to ground in the
wiring.
The data link between the TCU and the engine management module
is found to be unreliable because the checksum, or the data received,
did not match the correct checksum.
This could be caused by an open circuit, short circuit to ground or a
loose connection in the link wire itself.
Each solenoid in turn is switched off if it was energised, or switched on
if it was not energised by a very small 100 ms pulse. This pulse is too
short for the solenoid to react so transmission operation is not af
fected.
The solenoid feedback voltage is measured before the 100 ms pulse
and again during the pulse. If the difference is outside the acceptable
limits the relevant fault messages are set.
Typical causes would be an open circuit in the wiring to or within the
solenoid, or a short circuit to ground in the wiring to, from or within the
solenoid in question.
If several of these fault codes are presents check the wiring or
connectors that are common to the selected solenoids, especially the
earth connections.
The state of the solenoid feedback voltage is outside acceptable
limits but the faulty solenoid could not be isolated.
The current to solenoid 5 was outside acceptable limits.
This fault results from a mismatch between the current set point for
solenoid 5 and the current measured by the feedback within the TCU.
Typical causes would be an open circuit or short circuit to ground in
the wiring to, from or within the solenoid. It is also possible that there
has been a fault in the solenoid output circuit. If this is the case
however, the fault should be continually present.
The closed throttle position has not been learnt. This fault
may be caused by the transmission not having reached normal
operating temperature or the engine idle speed being incorrect.
The TCU will learn the closed throttle position automatically
when the transmission is brought to normal operating
temperature and the engine is allowed to idle in Drive with the
‘base idle’ correctly set and the air conditioner (if fitted)
switched off. Condition
Mode Switch Input Fault
(Power/Economy Mode)
Data Output Link Fault
On/off Solenoid Fault
(Solenoid 1,2,3,4,6,7)
Solenoid 5 Fault
(Variable Pressure
Solenoid)
Throttle Not LearntSolenoid
9
10
11
12
13
Page 1080 of 1463
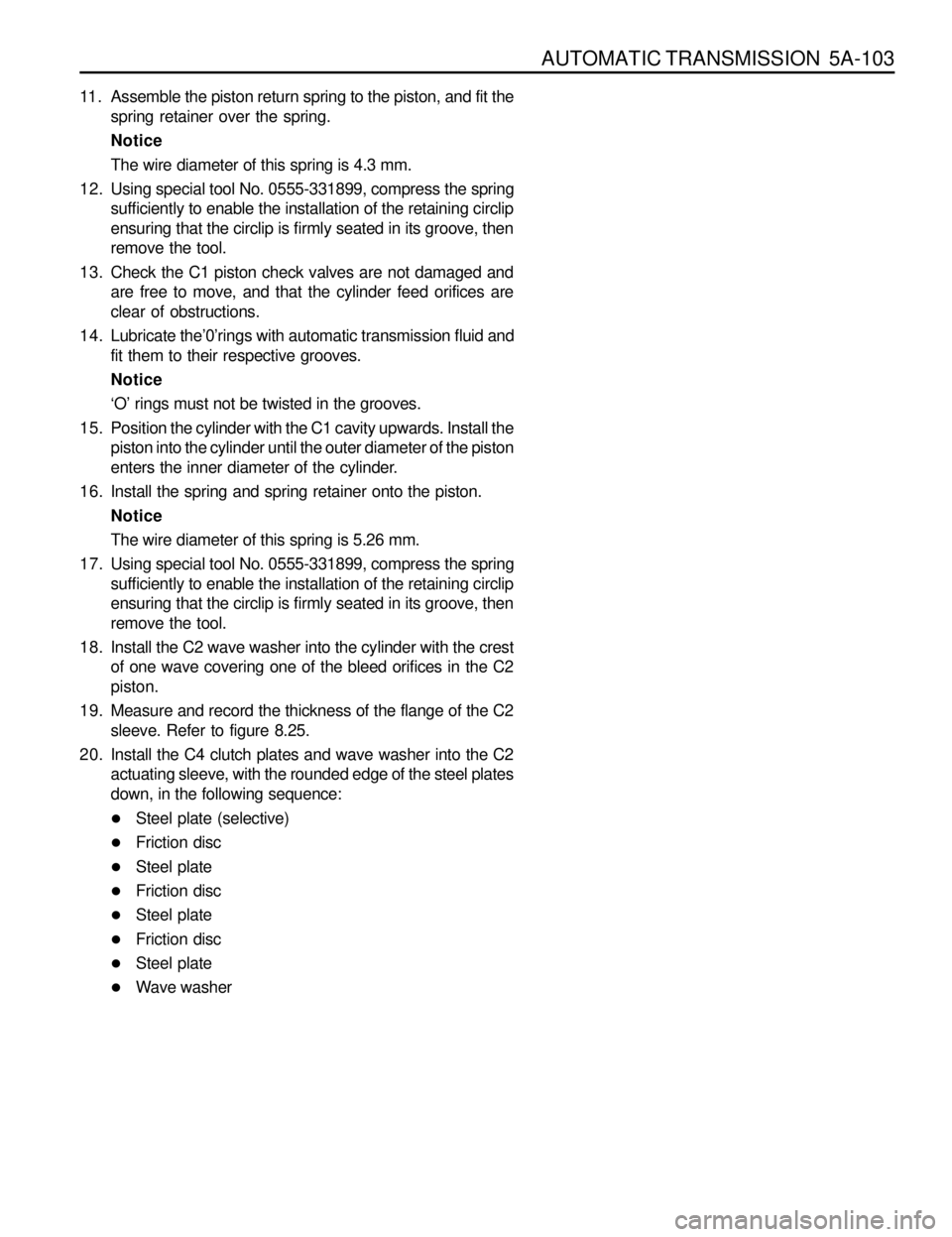
AUTOMATIC TRANSMISSION 5A-103
11. Assemble the piston return spring to the piston, and fit the
spring retainer over the spring.
Notice
The wire diameter of this spring is 4.3 mm.
12. Using special tool No. 0555-331899, compress the spring
sufficiently to enable the installation of the retaining circlip
ensuring that the circlip is firmly seated in its groove, then
remove the tool.
13. Check the C1 piston check valves are not damaged and
are free to move, and that the cylinder feed orifices are
clear of obstructions.
14. Lubricate the’0’rings with automatic transmission fluid and
fit them to their respective grooves.
Notice
‘O’ rings must not be twisted in the grooves.
15. Position the cylinder with the C1 cavity upwards. Install the
piston into the cylinder until the outer diameter of the piston
enters the inner diameter of the cylinder.
16. Install the spring and spring retainer onto the piston.
Notice
The wire diameter of this spring is 5.26 mm.
17. Using special tool No. 0555-331899, compress the spring
sufficiently to enable the installation of the retaining circlip
ensuring that the circlip is firmly seated in its groove, then
remove the tool.
18. Install the C2 wave washer into the cylinder with the crest
of one wave covering one of the bleed orifices in the C2
piston.
19. Measure and record the thickness of the flange of the C2
sleeve. Refer to figure 8.25.
20. Install the C4 clutch plates and wave washer into the C2
actuating sleeve, with the rounded edge of the steel plates
down, in the following sequence:
lSteel plate (selective)
lFriction disc
lSteel plate
lFriction disc
lSteel plate
lFriction disc
lSteel plate
lWave washer
Page 1087 of 1463
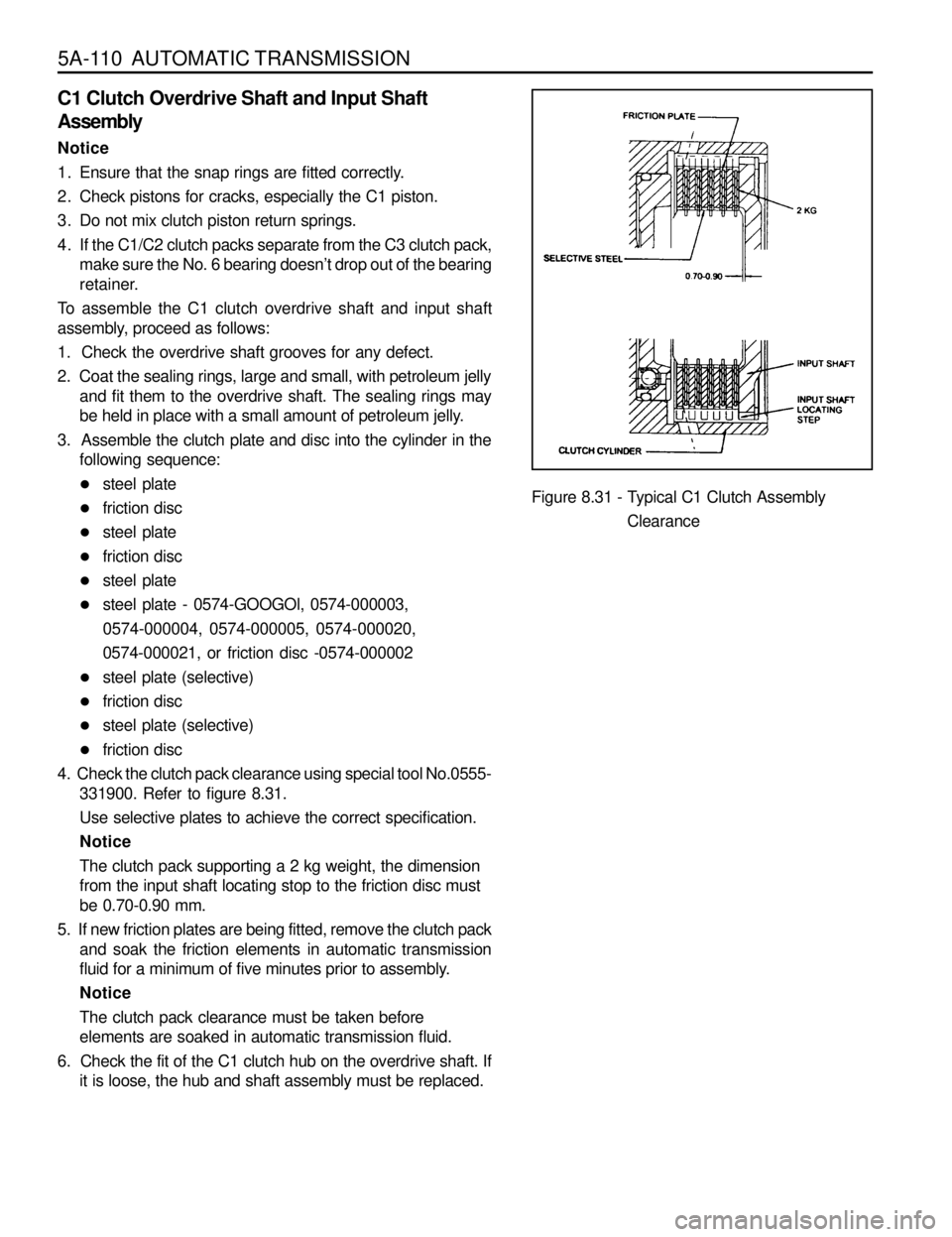
5A-110 AUTOMATIC TRANSMISSION
C1 Clutch Overdrive Shaft and Input Shaft
Assembly
Notice
1. Ensure that the snap rings are fitted correctly.
2. Check pistons for cracks, especially the C1 piston.
3. Do not mix clutch piston return springs.
4. If the C1/C2 clutch packs separate from the C3 clutch pack,
make sure the No. 6 bearing doesn’t drop out of the bearing
retainer.
To assemble the C1 clutch overdrive shaft and input shaft
assembly, proceed as follows:
1. Check the overdrive shaft grooves for any defect.
2. Coat the sealing rings, large and small, with petroleum jelly
and fit them to the overdrive shaft. The sealing rings may
be held in place with a small amount of petroleum jelly.
3. Assemble the clutch plate and disc into the cylinder in the
following sequence:
lsteel plate
lfriction disc
lsteel plate
lfriction disc
lsteel plate
lsteel plate - 0574-GOOGOl, 0574-000003,
0574-000004, 0574-000005, 0574-000020,
0574-000021, or friction disc -0574-000002
lsteel plate (selective)
lfriction disc
lsteel plate (selective)
lfriction disc
4. Check the clutch pack clearance using special tool No.0555-
331900. Refer to figure 8.31.
Use selective plates to achieve the correct specification.
Notice
The clutch pack supporting a 2 kg weight, the dimension
from the input shaft locating stop to the friction disc must
be 0.70-0.90 mm.
5. If new friction plates are being fitted, remove the clutch pack
and soak the friction elements in automatic transmission
fluid for a minimum of five minutes prior to assembly.
Notice
The clutch pack clearance must be taken before
elements are soaked in automatic transmission fluid.
6. Check the fit of the C1 clutch hub on the overdrive shaft. If
it is loose, the hub and shaft assembly must be replaced.Figure 8.31 - Typical C1 Clutch Assembly
Clearance
Page 1211 of 1463
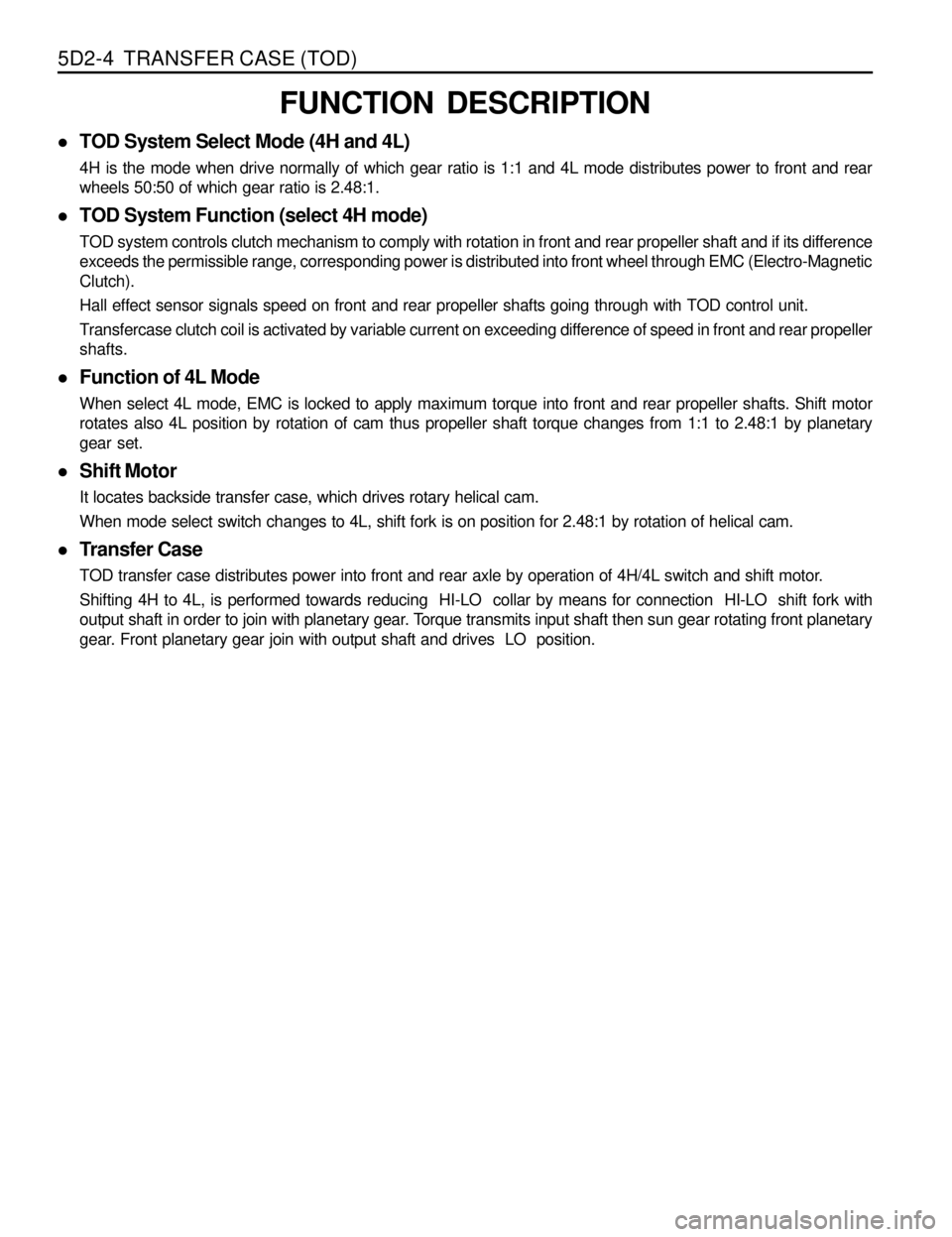
5D2-4 TRANSFER CASE (TOD)
FUNCTION DESCRIPTION
lTOD System Select Mode (4H and 4L)
4H is the mode when drive normally of which gear ratio is 1:1 and 4L mode distributes power to front and rear
wheels 50:50 of which gear ratio is 2.48:1.
lTOD System Function (select 4H mode)
TOD system controls clutch mechanism to comply with rotation in front and rear propeller shaft and if its difference
exceeds the permissible range, corresponding power is distributed into front wheel through EMC (Electro-Magnetic
Clutch).
Hall effect sensor signals speed on front and rear propeller shafts going through with TOD control unit.
Transfercase clutch coil is activated by variable current on exceeding difference of speed in front and rear propeller
shafts.
lFunction of 4L Mode
When select 4L mode, EMC is locked to apply maximum torque into front and rear propeller shafts. Shift motor
rotates also 4L position by rotation of cam thus propeller shaft torque changes from 1:1 to 2.48:1 by planetary
gear set.
lShift Motor
It locates backside transfer case, which drives rotary helical cam.
When mode select switch changes to 4L, shift fork is on position for 2.48:1 by rotation of helical cam.
lTransfer Case
TOD transfer case distributes power into front and rear axle by operation of 4H/4L switch and shift motor.
Shifting 4H to 4L, is performed towards reducing HI-LO collar by means for connection HI-LO shift fork with
output shaft in order to join with planetary gear. Torque transmits input shaft then sun gear rotating front planetary
gear. Front planetary gear join with output shaft and drives LO position.
Page 1212 of 1463
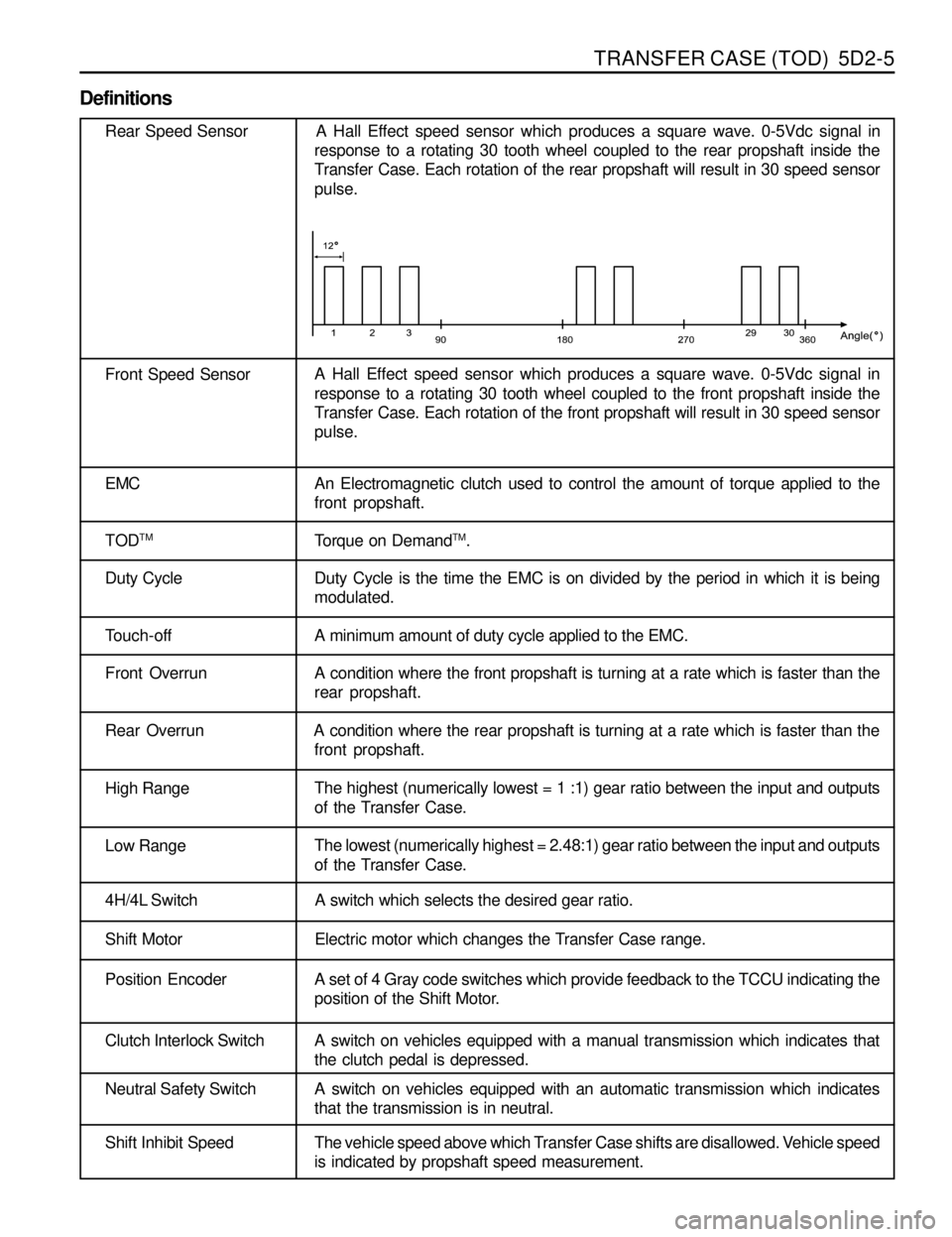
TRANSFER CASE (TOD) 5D2-5
Definitions
Rear Speed Sensor A Hall Effect speed sensor which produces a square wave. 0-5Vdc signal in
response to a rotating 30 tooth wheel coupled to the rear propshaft inside the
Transfer Case. Each rotation of the rear propshaft will result in 30 speed sensor
pulse.
Front Speed SensorA Hall Effect speed sensor which produces a square wave. 0-5Vdc signal in
response to a rotating 30 tooth wheel coupled to the front propshaft inside the
Transfer Case. Each rotation of the front propshaft will result in 30 speed sensor
pulse.
EMC An Electromagnetic clutch used to control the amount of torque applied to the
front propshaft.
TOD
TMTorque on DemandTM.
Duty Cycle Duty Cycle is the time the EMC is on divided by the period in which it is being
modulated.
Touch-off A minimum amount of duty cycle applied to the EMC.
Front OverrunA condition where the front propshaft is turning at a rate which is faster than the
rear propshaft.
Rear Overrun A condition where the rear propshaft is turning at a rate which is faster than the
front propshaft.
High RangeThe highest (numerically lowest = 1 :1) gear ratio between the input and outputs
of the Transfer Case.
Low RangeThe lowest (numerically highest = 2.48:1) gear ratio between the input and outputs
of the Transfer Case.
4H/4L Switch A switch which selects the desired gear ratio.
Shift Motor Electric motor which changes the Transfer Case range.
Position Encoder A set of 4 Gray code switches which provide feedback to the TCCU indicating the
position of the Shift Motor.
Clutch Interlock Switch A switch on vehicles equipped with a manual transmission which indicates that
the clutch pedal is depressed.
Neutral Safety Switch A switch on vehicles equipped with an automatic transmission which indicates
that the transmission is in neutral.
Shift Inhibit Speed The vehicle speed above which Transfer Case shifts are disallowed. Vehicle speed
is indicated by propshaft speed measurement.
Page 1216 of 1463
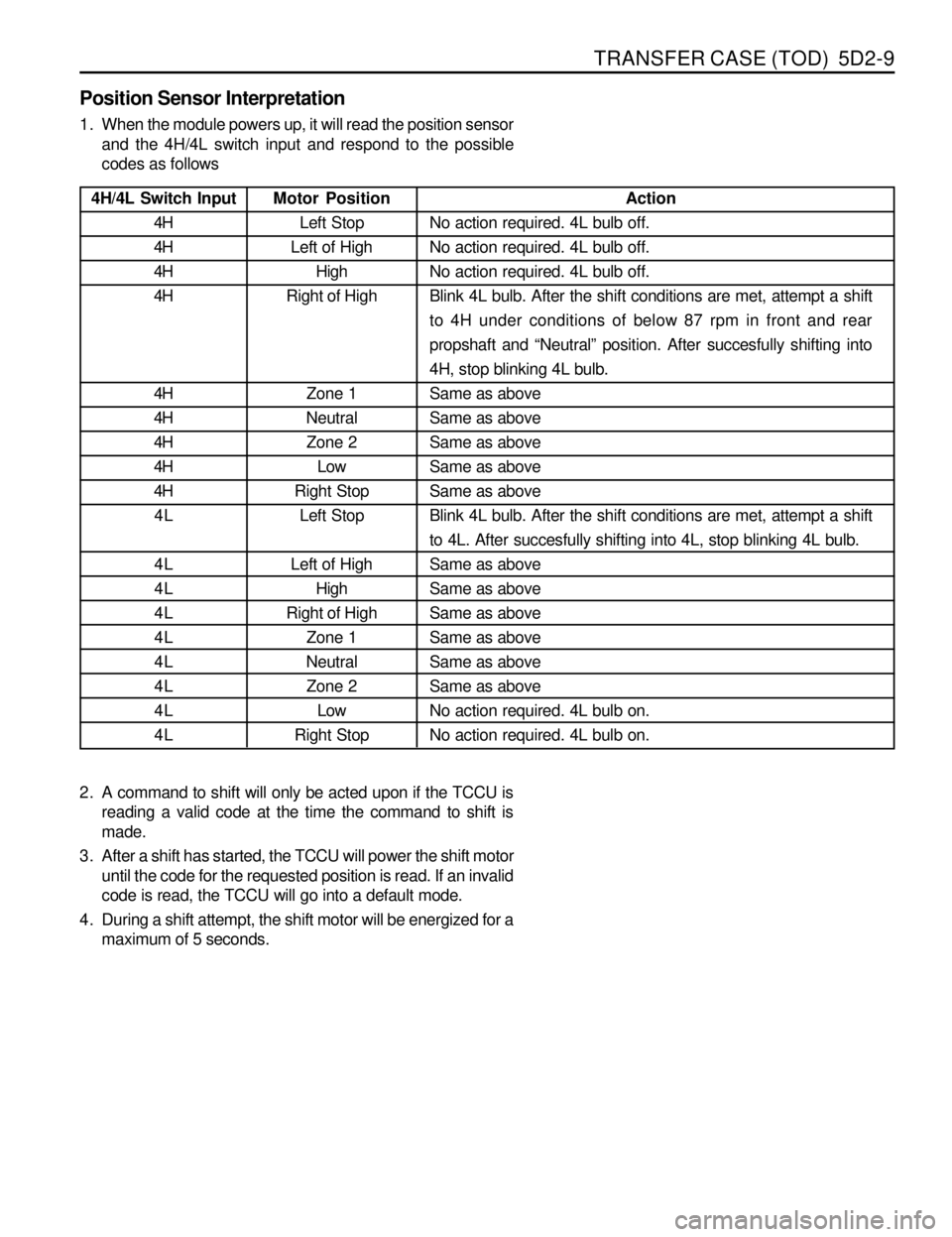
TRANSFER CASE (TOD) 5D2-9
4H/4L Switch Input
4H
4H
4H
4H
4H
4H
4H
4H
4H
4L
4L
4L
4L
4L
4L
4L
4L
4L
Position Sensor Interpretation
1. When the module powers up, it will read the position sensor
and the 4H/4L switch input and respond to the possible
codes as follows
2. A command to shift will only be acted upon if the TCCU is
reading a valid code at the time the command to shift is
made.
3. After a shift has started, the TCCU will power the shift motor
until the code for the requested position is read. If an invalid
code is read, the TCCU will go into a default mode.
4. During a shift attempt, the shift motor will be energized for a
maximum of 5 seconds.Motor Position
Left Stop
Left of High
High
Right of High
Zone 1
Neutral
Zone 2
Low
Right Stop
Left Stop
Left of High
High
Right of High
Zone 1
Neutral
Zone 2
Low
Right StopAction
No action required. 4L bulb off.
No action required. 4L bulb off.
No action required. 4L bulb off.
Blink 4L bulb. After the shift conditions are met, attempt a shift
to 4H under conditions of below 87 rpm in front and rear
propshaft and “Neutral” position. After succesfully shifting into
4H, stop blinking 4L bulb.
Same as above
Same as above
Same as above
Same as above
Same as above
Blink 4L bulb. After the shift conditions are met, attempt a shift
to 4L. After succesfully shifting into 4L, stop blinking 4L bulb.
Same as above
Same as above
Same as above
Same as above
Same as above
Same as above
No action required. 4L bulb on.
No action required. 4L bulb on.
Page 1217 of 1463
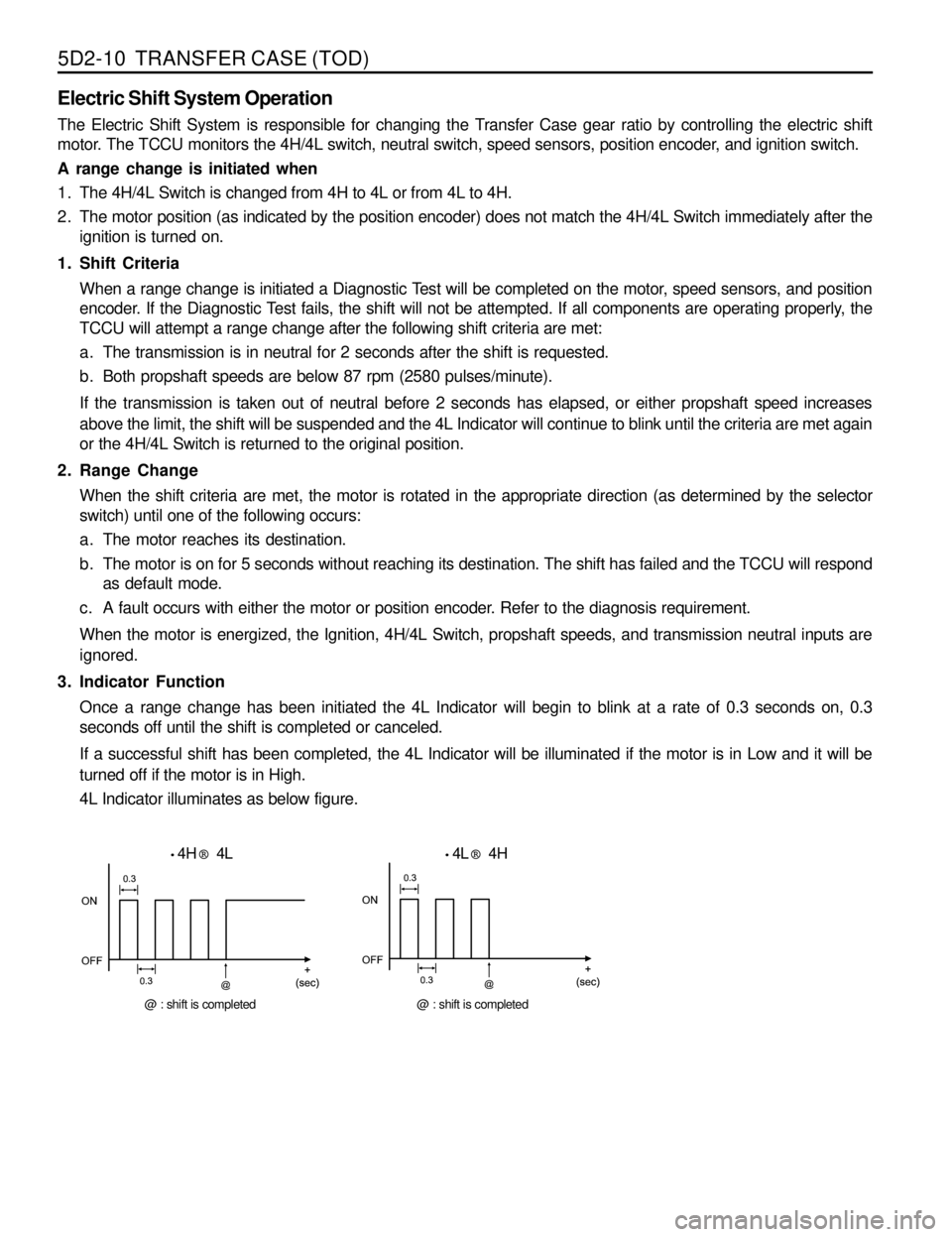
5D2-10 TRANSFER CASE (TOD)
Electric Shift System Operation
The Electric Shift System is responsible for changing the Transfer Case gear ratio by controlling the electric shift
motor. The TCCU monitors the 4H/4L switch, neutral switch, speed sensors, position encoder, and ignition switch.
A range change is initiated when
1. The 4H/4L Switch is changed from 4H to 4L or from 4L to 4H.
2. The motor position (as indicated by the position encoder) does not match the 4H/4L Switch immediately after the
ignition is turned on.
1. Shift Criteria
When a range change is initiated a Diagnostic Test will be completed on the motor, speed sensors, and position
encoder. If the Diagnostic Test fails, the shift will not be attempted. If all components are operating properly, the
TCCU will attempt a range change after the following shift criteria are met:
a. The transmission is in neutral for 2 seconds after the shift is requested.
b. Both propshaft speeds are below 87 rpm (2580 pulses/minute).
If the transmission is taken out of neutral before 2 seconds has elapsed, or either propshaft speed increases
above the limit, the shift will be suspended and the 4L Indicator will continue to blink until the criteria are met again
or the 4H/4L Switch is returned to the original position.
2. Range Change
When the shift criteria are met, the motor is rotated in the appropriate direction (as determined by the selector
switch) until one of the following occurs:
a. The motor reaches its destination.
b. The motor is on for 5 seconds without reaching its destination. The shift has failed and the TCCU will respond
as default mode.
c. A fault occurs with either the motor or position encoder. Refer to the diagnosis requirement.
When the motor is energized, the Ignition, 4H/4L Switch, propshaft speeds, and transmission neutral inputs are
ignored.
3. Indicator Function
Once a range change has been initiated the 4L Indicator will begin to blink at a rate of 0.3 seconds on, 0.3
seconds off until the shift is completed or canceled.
If a successful shift has been completed, the 4L Indicator will be illuminated if the motor is in Low and it will be
turned off if the motor is in High.
4L Indicator illuminates as below figure.
· 4H ® 4L
@ : shift is completed
· 4L ® 4H
@ : shift is completed
Page 1218 of 1463
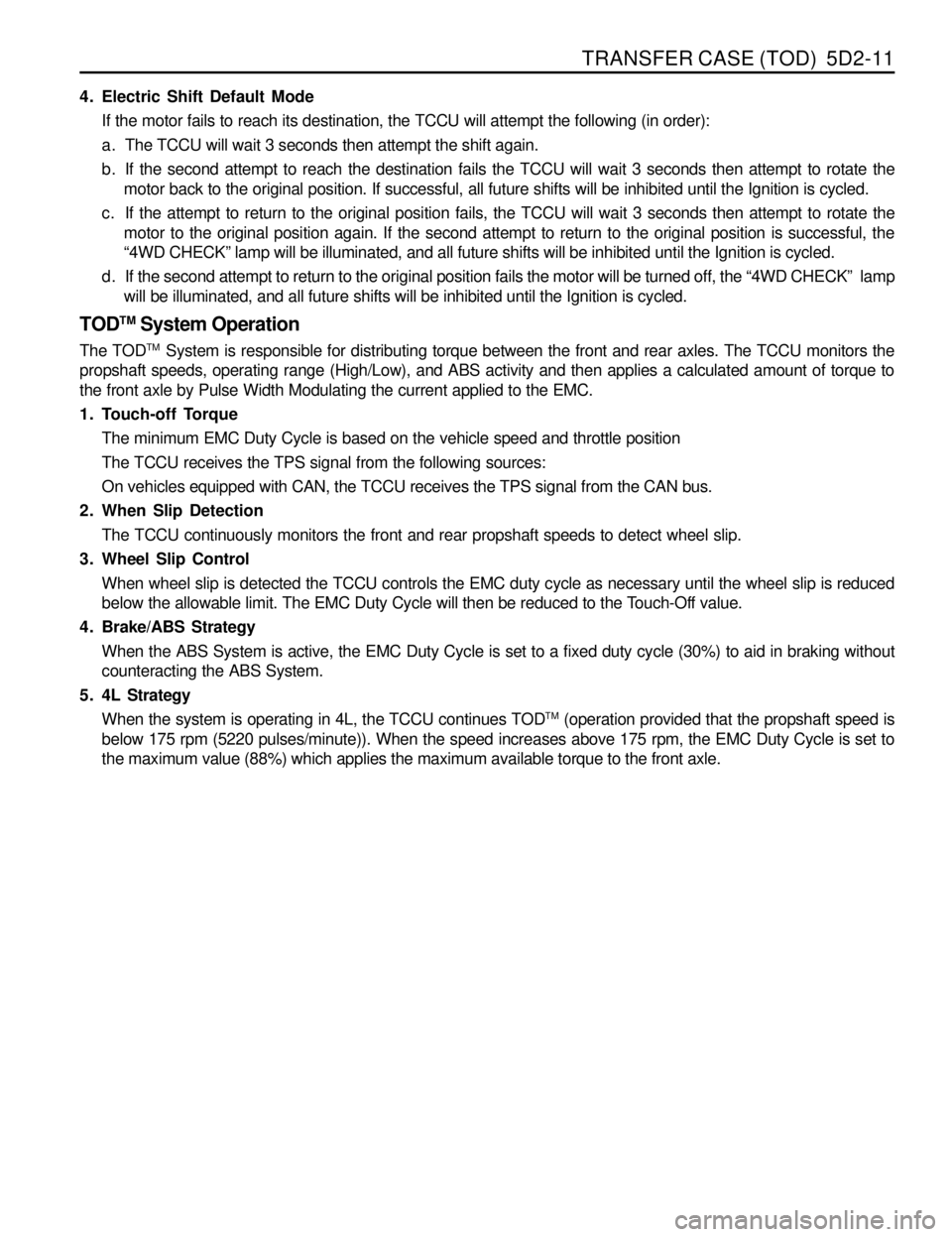
TRANSFER CASE (TOD) 5D2-11
4. Electric Shift Default Mode
If the motor fails to reach its destination, the TCCU will attempt the following (in order):
a. The TCCU will wait 3 seconds then attempt the shift again.
b. If the second attempt to reach the destination fails the TCCU will wait 3 seconds then attempt to rotate the
motor back to the original position. If successful, all future shifts will be inhibited until the Ignition is cycled.
c. If the attempt to return to the original position fails, the TCCU will wait 3 seconds then attempt to rotate the
motor to the original position again. If the second attempt to return to the original position is successful, the
“4WD CHECK” lamp will be illuminated, and all future shifts will be inhibited until the Ignition is cycled.
d. If the second attempt to return to the original position fails the motor will be turned off, the “4WD CHECK” lamp
will be illuminated, and all future shifts will be inhibited until the Ignition is cycled.
TODTM System Operation
The TODTM System is responsible for distributing torque between the front and rear axles. The TCCU monitors the
propshaft speeds, operating range (High/Low), and ABS activity and then applies a calculated amount of torque to
the front axle by Pulse Width Modulating the current applied to the EMC.
1. Touch-off Torque
The minimum EMC Duty Cycle is based on the vehicle speed and throttle position
The TCCU receives the TPS signal from the following sources:
On vehicles equipped with CAN, the TCCU receives the TPS signal from the CAN bus.
2. When Slip Detection
The TCCU continuously monitors the front and rear propshaft speeds to detect wheel slip.
3. Wheel Slip Control
When wheel slip is detected the TCCU controls the EMC duty cycle as necessary until the wheel slip is reduced
below the allowable limit. The EMC Duty Cycle will then be reduced to the Touch-Off value.
4. Brake/ABS Strategy
When the ABS System is active, the EMC Duty Cycle is set to a fixed duty cycle (30%) to aid in braking without
counteracting the ABS System.
5. 4L Strategy
When the system is operating in 4L, the TCCU continues TOD
TM (operation provided that the propshaft speed is
below 175 rpm (5220 pulses/minute)). When the speed increases above 175 rpm, the EMC Duty Cycle is set to
the maximum value (88%) which applies the maximum available torque to the front axle.
Page 1222 of 1463
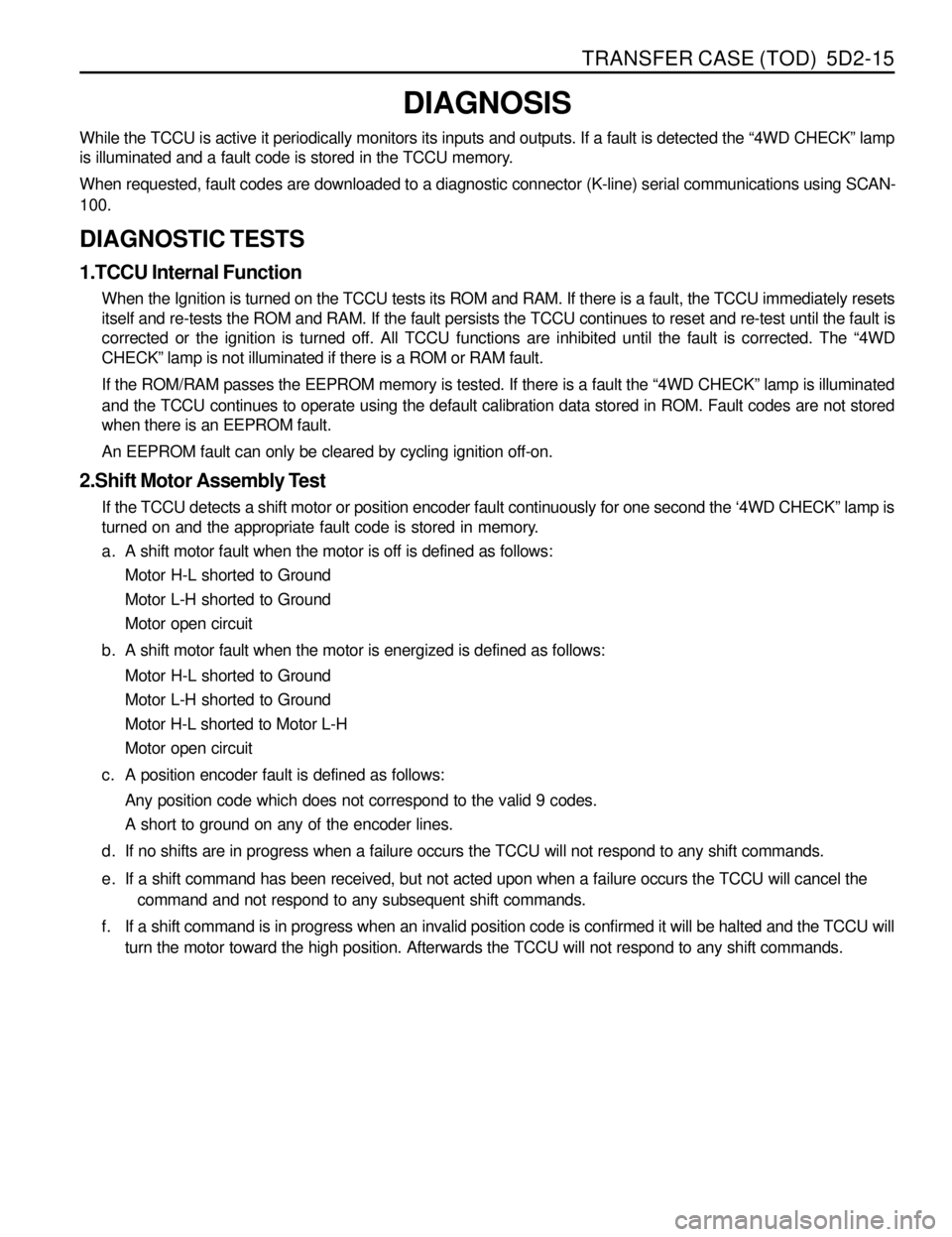
TRANSFER CASE (TOD) 5D2-15
DIAGNOSIS
While the TCCU is active it periodically monitors its inputs and outputs. If a fault is detected the “4WD CHECK” lamp
is illuminated and a fault code is stored in the TCCU memory.
When requested, fault codes are downloaded to a diagnostic connector (K-line) serial communications using SCAN-
100.
DIAGNOSTIC TESTS
1.TCCU Internal Function
When the Ignition is turned on the TCCU tests its ROM and RAM. If there is a fault, the TCCU immediately resets
itself and re-tests the ROM and RAM. If the fault persists the TCCU continues to reset and re-test until the fault is
corrected or the ignition is turned off. All TCCU functions are inhibited until the fault is corrected. The “4WD
CHECK” lamp is not illuminated if there is a ROM or RAM fault.
If the ROM/RAM passes the EEPROM memory is tested. If there is a fault the “4WD CHECK” lamp is illuminated
and the TCCU continues to operate using the default calibration data stored in ROM. Fault codes are not stored
when there is an EEPROM fault.
An EEPROM fault can only be cleared by cycling ignition off-on.
2.Shift Motor Assembly Test
If the TCCU detects a shift motor or position encoder fault continuously for one second the ‘4WD CHECK” lamp is
turned on and the appropriate fault code is stored in memory.
a. A shift motor fault when the motor is off is defined as follows:
Motor H-L shorted to Ground
Motor L-H shorted to Ground
Motor open circuit
b. A shift motor fault when the motor is energized is defined as follows:
Motor H-L shorted to Ground
Motor L-H shorted to Ground
Motor H-L shorted to Motor L-H
Motor open circuit
c. A position encoder fault is defined as follows:
Any position code which does not correspond to the valid 9 codes.
A short to ground on any of the encoder lines.
d. If no shifts are in progress when a failure occurs the TCCU will not respond to any shift commands.
e. If a shift command has been received, but not acted upon when a failure occurs the TCCU will cancel the
command and not respond to any subsequent shift commands.
f. If a shift command is in progress when an invalid position code is confirmed it will be halted and the TCCU will
turn the motor toward the high position. Afterwards the TCCU will not respond to any shift commands.
Page 1223 of 1463
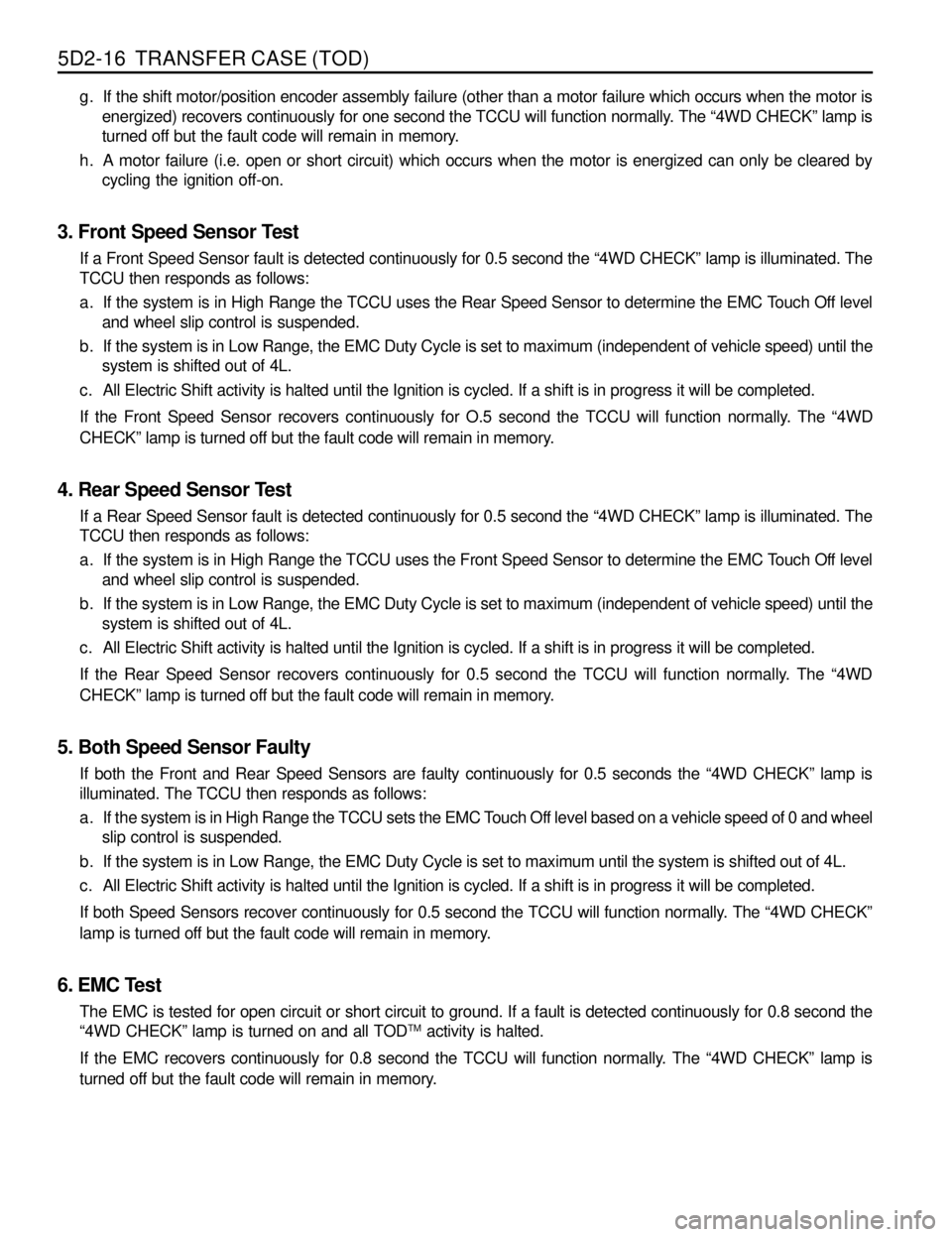
5D2-16 TRANSFER CASE (TOD)
g. If the shift motor/position encoder assembly failure (other than a motor failure which occurs when the motor is
energized) recovers continuously for one second the TCCU will function normally. The “4WD CHECK” lamp is
turned off but the fault code will remain in memory.
h. A motor failure (i.e. open or short circuit) which occurs when the motor is energized can only be cleared by
cycling the ignition off-on.
3. Front Speed Sensor Test
If a Front Speed Sensor fault is detected continuously for 0.5 second the “4WD CHECK” lamp is illuminated. The
TCCU then responds as follows:
a. If the system is in High Range the TCCU uses the Rear Speed Sensor to determine the EMC Touch Off level
and wheel slip control is suspended.
b. If the system is in Low Range, the EMC Duty Cycle is set to maximum (independent of vehicle speed) until the
system is shifted out of 4L.
c. All Electric Shift activity is halted until the Ignition is cycled. If a shift is in progress it will be completed.
If the Front Speed Sensor recovers continuously for O.5 second the TCCU will function normally. The “4WD
CHECK” lamp is turned off but the fault code will remain in memory.
4. Rear Speed Sensor Test
If a Rear Speed Sensor fault is detected continuously for 0.5 second the “4WD CHECK” lamp is illuminated. The
TCCU then responds as follows:
a. If the system is in High Range the TCCU uses the Front Speed Sensor to determine the EMC Touch Off level
and wheel slip control is suspended.
b. If the system is in Low Range, the EMC Duty Cycle is set to maximum (independent of vehicle speed) until the
system is shifted out of 4L.
c. All Electric Shift activity is halted until the Ignition is cycled. If a shift is in progress it will be completed.
If the Rear Speed Sensor recovers continuously for 0.5 second the TCCU will function normally. The “4WD
CHECK” lamp is turned off but the fault code will remain in memory.
5. Both Speed Sensor Faulty
If both the Front and Rear Speed Sensors are faulty continuously for 0.5 seconds the “4WD CHECK” lamp is
illuminated. The TCCU then responds as follows:
a. If the system is in High Range the TCCU sets the EMC Touch Off level based on a vehicle speed of 0 and wheel
slip control is suspended.
b. If the system is in Low Range, the EMC Duty Cycle is set to maximum until the system is shifted out of 4L.
c. All Electric Shift activity is halted until the Ignition is cycled. If a shift is in progress it will be completed.
If both Speed Sensors recover continuously for 0.5 second the TCCU will function normally. The “4WD CHECK”
lamp is turned off but the fault code will remain in memory.
6. EMC Test
The EMC is tested for open circuit or short circuit to ground. If a fault is detected continuously for 0.8 second the
“4WD CHECK” lamp is turned on and all TODTM activity is halted.
If the EMC recovers continuously for 0.8 second the TCCU will function normally. The “4WD CHECK” lamp is
turned off but the fault code will remain in memory.