ESP SSANGYONG MUSSO 1998 Workshop Repair Manual
[x] Cancel search | Manufacturer: SSANGYONG, Model Year: 1998, Model line: MUSSO, Model: SSANGYONG MUSSO 1998Pages: 1463, PDF Size: 19.88 MB
Page 122 of 1463
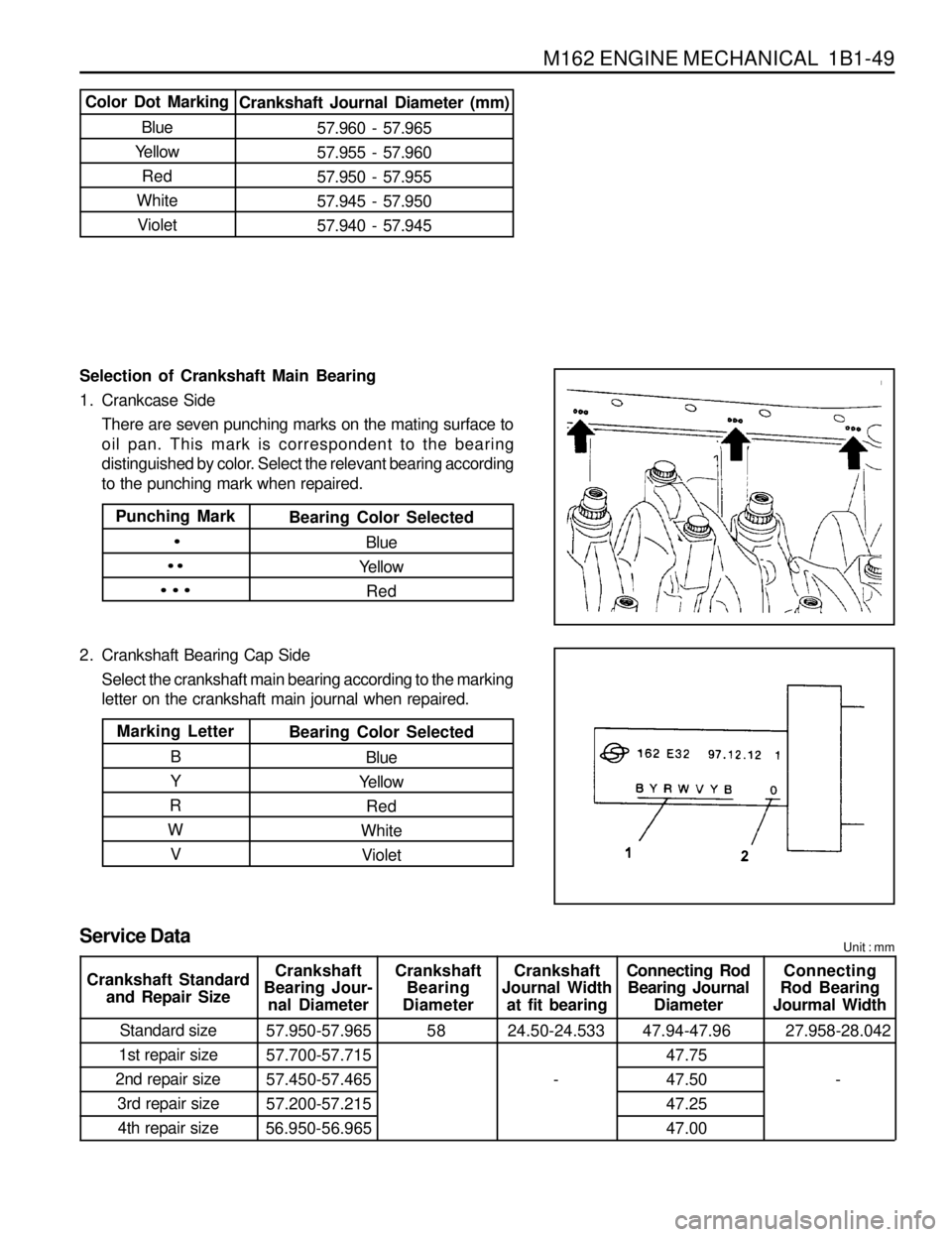
M162 ENGINE MECHANICAL 1B1-49
Selection of Crankshaft Main Bearing
1. Crankcase Side
There are seven punching marks on the mating surface to
oil pan. This mark is correspondent to the bearing
distinguished by color. Select the relevant bearing according
to the punching mark when repaired.
2. Crankshaft Bearing Cap Side
Select the crankshaft main bearing according to the marking
letter on the crankshaft main journal when repaired.
Color Dot Marking
Blue
Yellow
Red
White
VioletCrankshaft Journal Diameter (mm)
57.960 - 57.965
57.955 - 57.960
57.950 - 57.955
57.945 - 57.950
57.940 - 57.945
Punching Mark
·
··
···
Bearing Color Selected
Blue
Yellow
Red
Marking Letter
B
Y
R
W
VBearing Color Selected
Blue
Yellow
Red
White
Violet
Service DataUnit : mm
Crankshaft
Bearing Jour-
nal DiameterCrankshaft
Bearing
DiameterCrankshaft
Journal Width
at fit bearingConnecting Rod
Bearing Journal
DiameterConnecting
Rod Bearing
Jourmal Width
Standard size
1st repair size
2nd repair size
3rd repair size
4th repair size57.950-57.965
57.700-57.715
57.450-57.465
57.200-57.215
56.950-56.96558 24.50-24.533
-47.94-47.96
47.75
47.50
47.25
47.0027.958-28.042
- Crankshaft Standard
and Repair Size
Page 138 of 1463
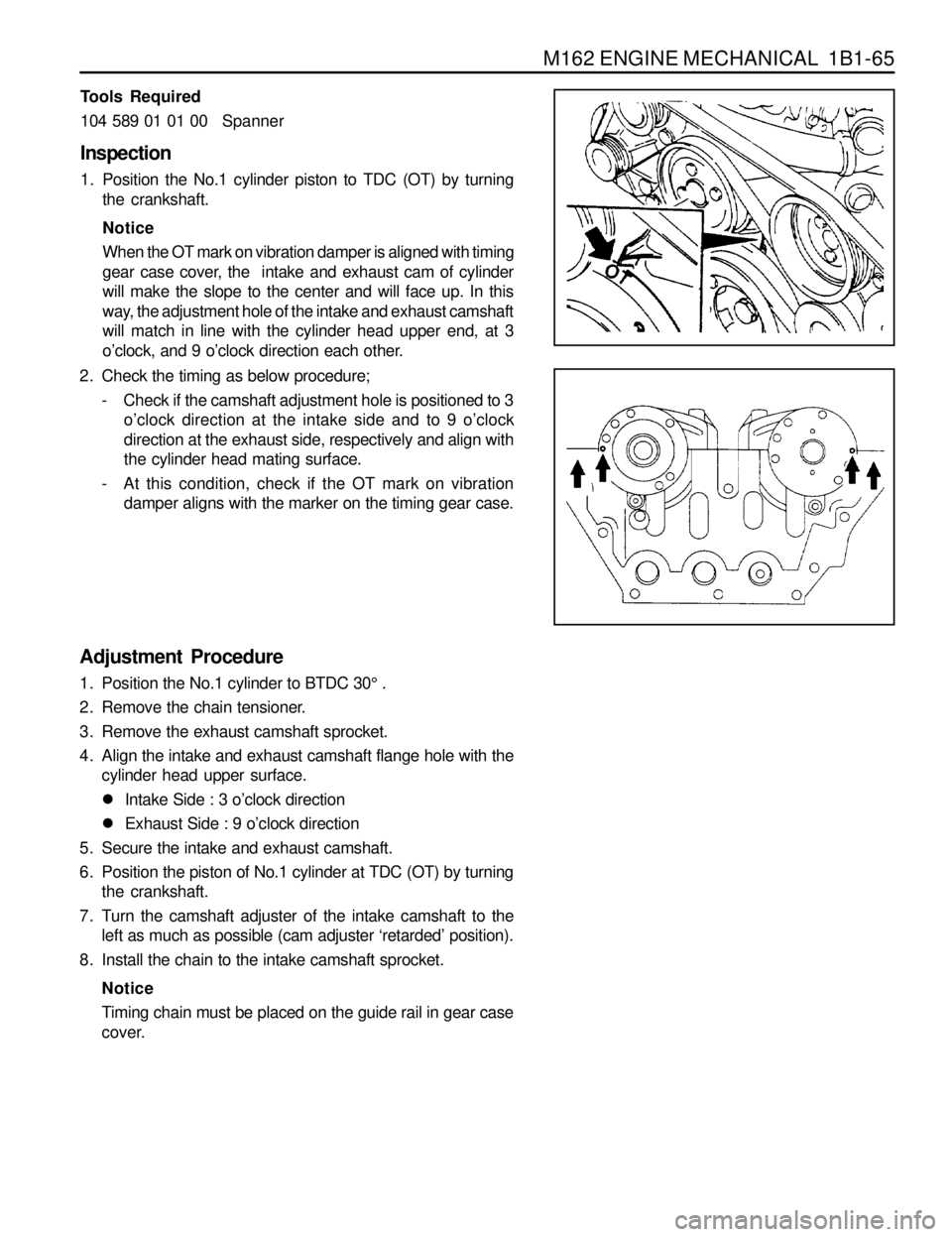
M162 ENGINE MECHANICAL 1B1-65
Adjustment Procedure
1. Position the No.1 cylinder to BTDC 30° .
2. Remove the chain tensioner.
3. Remove the exhaust camshaft sprocket.
4. Align the intake and exhaust camshaft flange hole with the
cylinder head upper surface.
lIntake Side : 3 o’clock direction
lExhaust Side : 9 o’clock direction
5. Secure the intake and exhaust camshaft.
6. Position the piston of No.1 cylinder at TDC (OT) by turning
the crankshaft.
7. Turn the camshaft adjuster of the intake camshaft to the
left as much as possible (cam adjuster ‘retarded’ position).
8. Install the chain to the intake camshaft sprocket.
Notice
Timing chain must be placed on the guide rail in gear case
cover. Tools Required
104 589 01 01 00Spanner
Inspection
1. Position the No.1 cylinder piston to TDC (OT) by turning
the crankshaft.
Notice
When the OT mark on vibration damper is aligned with timing
gear case cover, the intake and exhaust cam of cylinder
will make the slope to the center and will face up. In this
way, the adjustment hole of the intake and exhaust camshaft
will match in line with the cylinder head upper end, at 3
o’clock, and 9 o’clock direction each other.
2. Check the timing as below procedure;
- Check if the camshaft adjustment hole is positioned to 3
o’clock direction at the intake side and to 9 o’clock
direction at the exhaust side, respectively and align with
the cylinder head mating surface.
- At this condition, check if the OT mark on vibration
damper aligns with the marker on the timing gear case.
Page 245 of 1463
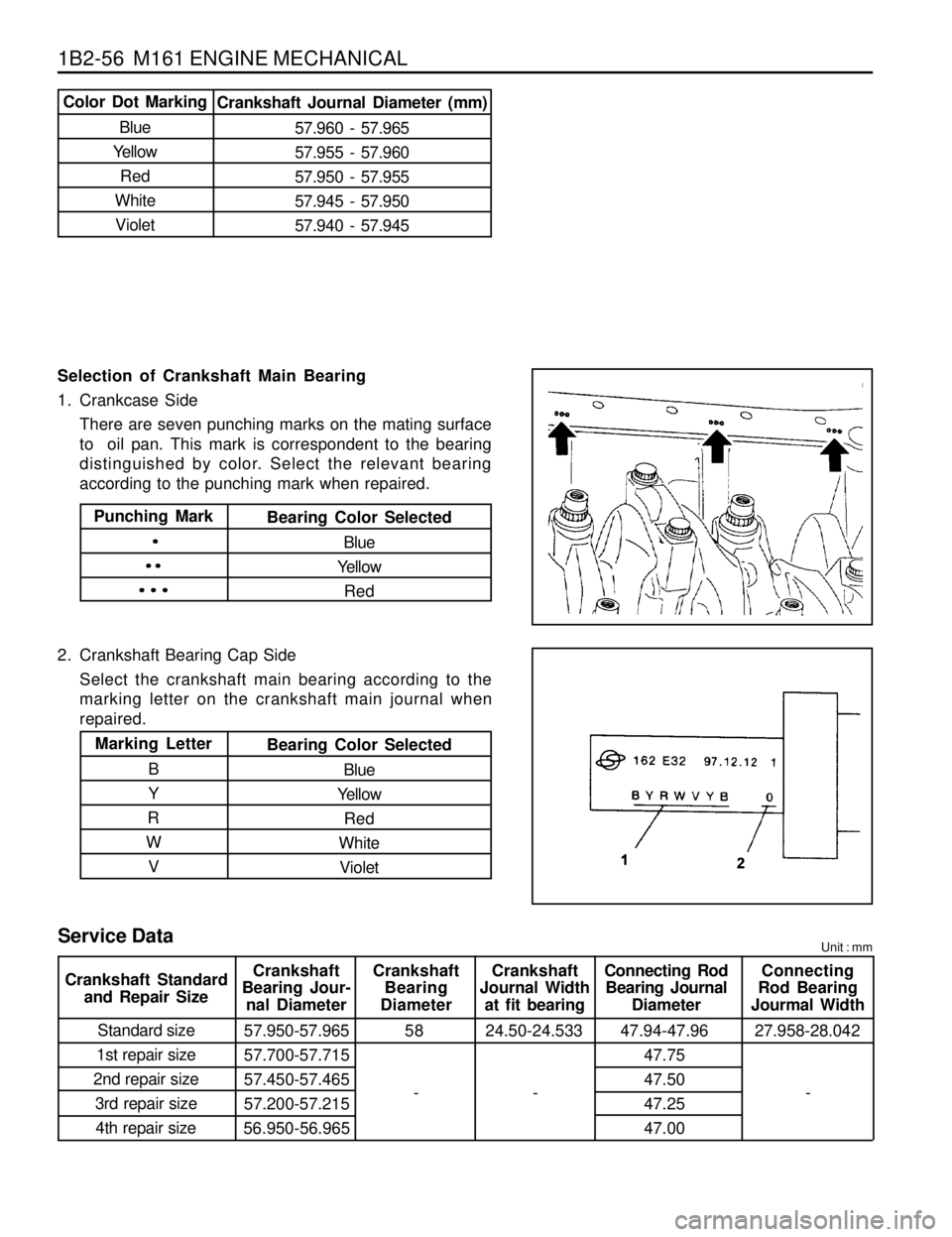
1B2-56 M161 ENGINE MECHANICAL
Selection of Crankshaft Main Bearing
1. Crankcase Side
There are seven punching marks on the mating surface
to oil pan. This mark is correspondent to the bearing
distinguished by color. Select the relevant bearing
according to the punching mark when repaired.
2. Crankshaft Bearing Cap Side
Select the crankshaft main bearing according to the
marking letter on the crankshaft main journal when
repaired.
Color Dot Marking
Blue
Yellow
Red
White
VioletCrankshaft Journal Diameter (mm)
57.960 - 57.965
57.955 - 57.960
57.950 - 57.955
57.945 - 57.950
57.940 - 57.945
Punching Mark
·
··
···
Bearing Color Selected
Blue
Yellow
Red
Marking Letter
B
Y
R
W
VBearing Color Selected
Blue
Yellow
Red
White
Violet
Service DataUnit : mm
Crankshaft
Bearing Jour-
nal DiameterCrankshaft
Bearing
DiameterCrankshaft
Journal Width
at fit bearingConnecting Rod
Bearing Journal
DiameterConnecting
Rod Bearing
Jourmal Width
Standard size
1st repair size
2nd repair size
3rd repair size
4th repair size57.950-57.965
57.700-57.715
57.450-57.465
57.200-57.215
56.950-56.96558 24.50-24.533 47.94-47.96
47.75
47.50
47.25
47.0027.958-28.042 Crankshaft Standard
and Repair Size
- --
Page 404 of 1463
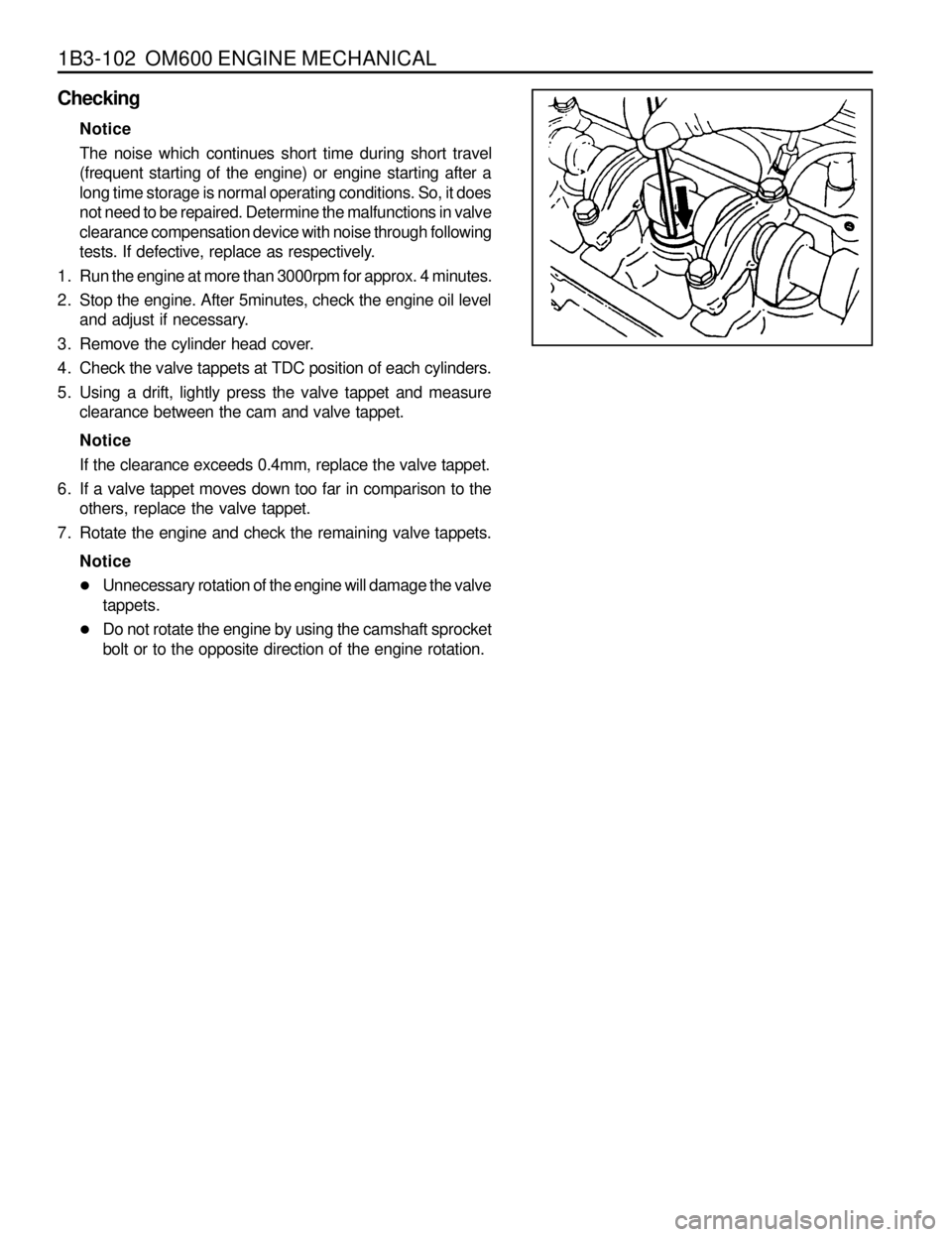
1B3-102 OM600 ENGINE MECHANICAL
Checking
Notice
The noise which continues short time during short travel
(frequent starting of the engine) or engine starting after a
long time storage is normal operating conditions. So, it does
not need to be repaired. Determine the malfunctions in valve
clearance compensation device with noise through following
tests. If defective, replace as respectively.
1. Run the engine at more than 3000rpm for approx. 4 minutes.
2. Stop the engine. After 5minutes, check the engine oil level
and adjust if necessary.
3. Remove the cylinder head cover.
4. Check the valve tappets at TDC position of each cylinders.
5. Using a drift, lightly press the valve tappet and measure
clearance between the cam and valve tappet.
Notice
If the clearance exceeds 0.4mm, replace the valve tappet.
6. If a valve tappet moves down too far in comparison to the
others, replace the valve tappet.
7. Rotate the engine and check the remaining valve tappets.
Notice
lUnnecessary rotation of the engine will damage the valve
tappets.
lDo not rotate the engine by using the camshaft sprocket
bolt or to the opposite direction of the engine rotation.
Page 566 of 1463
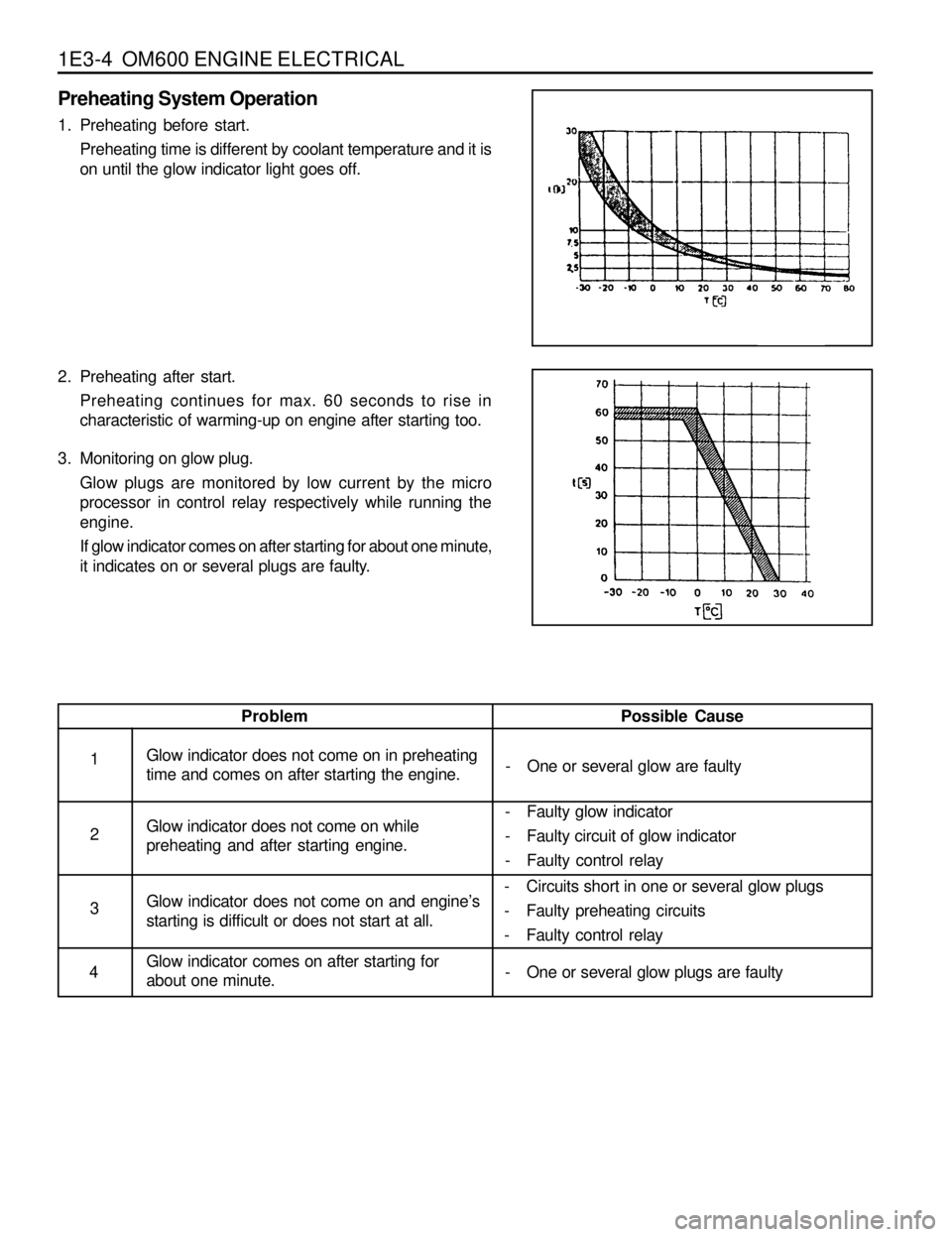
1E3-4 OM600 ENGINE ELECTRICAL
Preheating System Operation
1. Preheating before start.
Preheating time is different by coolant temperature and it is
on until the glow indicator light goes off.
2. Preheating after start.
Preheating continues for max. 60 seconds to rise in
characteristic of warming-up on engine after starting too.
3. Monitoring on glow plug.
Glow plugs are monitored by low current by the micro
processor in control relay respectively while running the
engine.
If glow indicator comes on after starting for about one minute,
it indicates on or several plugs are faulty.
Possible Cause
- One or several glow are faulty Problem
Glow indicator does not come on in preheating
time and comes on after starting the engine.
Glow indicator does not come on while
preheating and after starting engine.
Glow indicator does not come on and engine’s
starting is difficult or does not start at all.
Glow indicator comes on after starting for
about one minute.1
2
3
4- Faulty glow indicator
- Faulty circuit of glow indicator
- Faulty control relay
- Circuits short in one or several glow plugs
- Faulty preheating circuits
- Faulty control relay
- One or several glow plugs are faulty
Page 837 of 1463
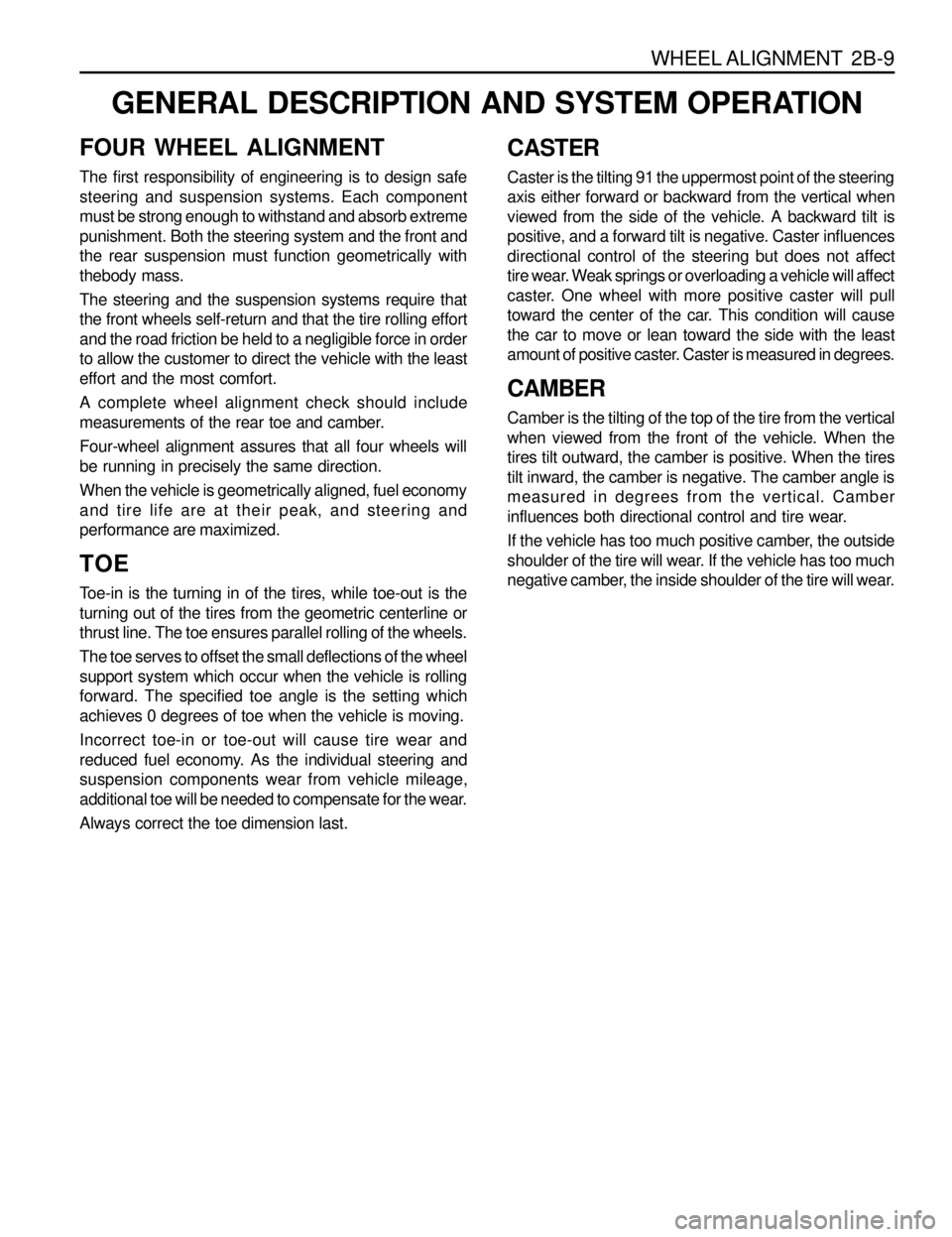
WHEEL ALIGNMENT 2B-9
GENERAL DESCRIPTION AND SYSTEM OPERATION
FOUR WHEEL ALIGNMENT
CASTER
Caster is the tilting 91 the uppermost point of the steering
axis either forward or backward from the vertical when
viewed from the side of the vehicle. A backward tilt is
positive, and a forward tilt is negative. Caster influences
directional control of the steering but does not affect
tire wear. Weak springs or overloading a vehicle will affect
caster. One wheel with more positive caster will pull
toward the center of the car. This condition will cause
the car to move or lean toward the side with the least
amount of positive caster. Caster is measured in degrees.
CAMBER
Camber is the tilting of the top of the tire from the vertical
when viewed from the front of the vehicle. When the
tires tilt outward, the camber is positive. When the tires
tilt inward, the camber is negative. The camber angle is
measured in degrees from the vertical. Camber
influences both directional control and tire wear.
If the vehicle has too much positive camber, the outside
shoulder of the tire will wear. If the vehicle has too much
negative camber, the inside shoulder of the tire will wear. The first responsibility of engineering is to design safe
steering and suspension systems. Each component
must be strong enough to withstand and absorb extreme
punishment. Both the steering system and the front and
the rear suspension must function geometrically with
thebody mass.
The steering and the suspension systems require that
the front wheels self-return and that the tire rolling effort
and the road friction be held to a negligible force in order
to allow the customer to direct the vehicle with the least
effort and the most comfort.
A complete wheel alignment check should include
measurements of the rear toe and camber.
Four-wheel alignment assures that all four wheels will
be running in precisely the same direction.
When the vehicle is geometrically aligned, fuel economy
and tire life are at their peak, and steering and
performance are maximized.
TOE
Toe-in is the turning in of the tires, while toe-out is the
turning out of the tires from the geometric centerline or
thrust line. The toe ensures parallel rolling of the wheels.
The toe serves to offset the small deflections of the wheel
support system which occur when the vehicle is rolling
forward. The specified toe angle is the setting which
achieves 0 degrees of toe when the vehicle is moving.
Incorrect toe-in or toe-out will cause tire wear and
reduced fuel economy. As the individual steering and
suspension components wear from vehicle mileage,
additional toe will be needed to compensate for the wear.
Always correct the toe dimension last.
Page 963 of 1463
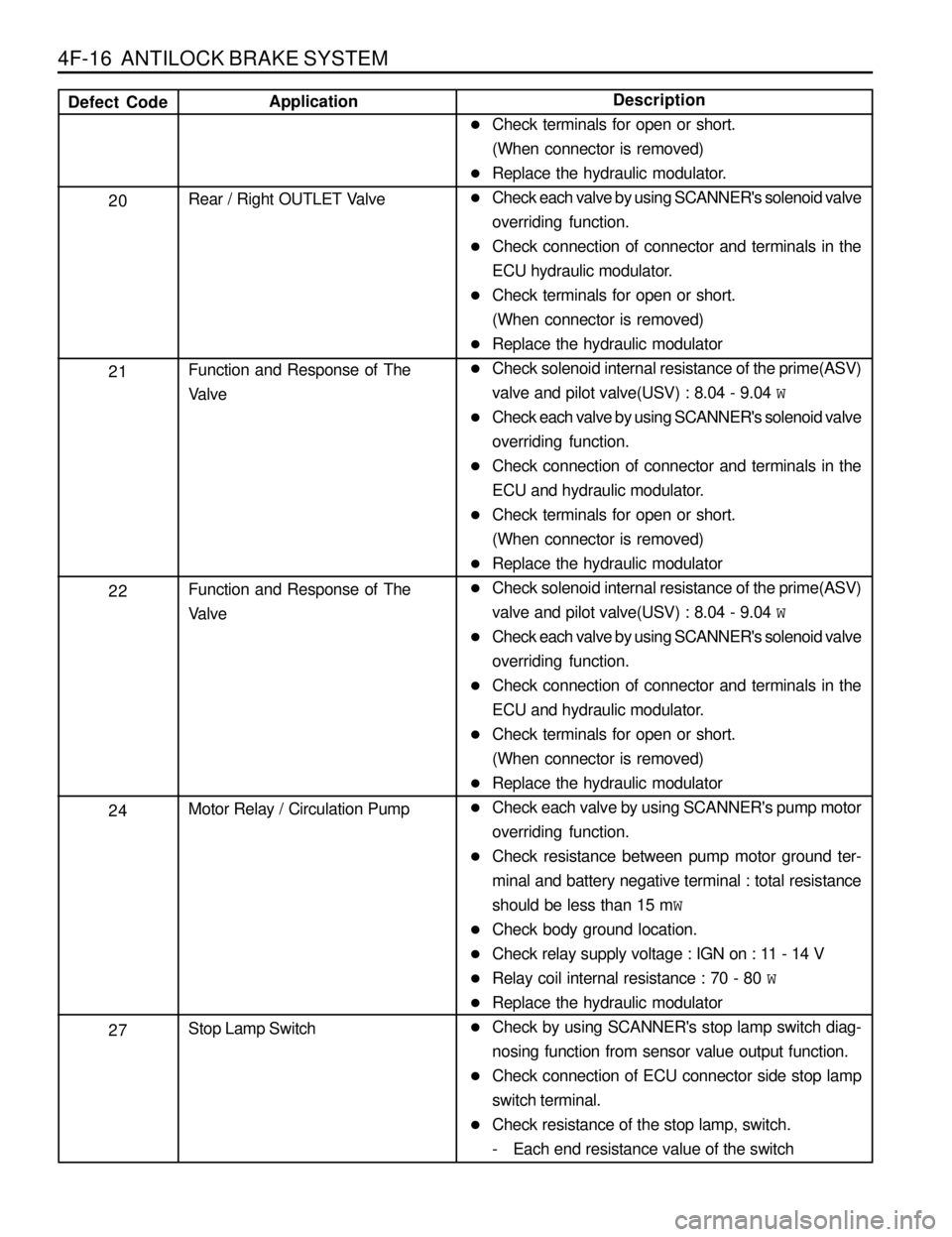
4F-16 ANTILOCK BRAKE SYSTEM
Description
lCheck terminals for open or short.
(When connector is removed)
lReplace the hydraulic modulator.
lCheck each valve by using SCANNER's solenoid valve
overriding function.
lCheck connection of connector and terminals in the
ECU hydraulic modulator.
lCheck terminals for open or short.
(When connector is removed)
lReplace the hydraulic modulator
lCheck solenoid internal resistance of the prime(ASV)
valve and pilot valve(USV) : 8.04 - 9.04 W
lCheck each valve by using SCANNER's solenoid valve
overriding function.
lCheck connection of connector and terminals in the
ECU and hydraulic modulator.
lCheck terminals for open or short.
(When connector is removed)
lReplace the hydraulic modulator
lCheck solenoid internal resistance of the prime(ASV)
valve and pilot valve(USV) : 8.04 - 9.04 W
lCheck each valve by using SCANNER's solenoid valve
overriding function.
lCheck connection of connector and terminals in the
ECU and hydraulic modulator.
lCheck terminals for open or short.
(When connector is removed)
lReplace the hydraulic modulator
lCheck each valve by using SCANNER's pump motor
overriding function.
lCheck resistance between pump motor ground ter-
minal and battery negative terminal : total resistance
should be less than 15 mW
lCheck body ground location.
lCheck relay supply voltage : IGN on : 11 - 14 V
lRelay coil internal resistance : 70 - 80 W
lReplace the hydraulic modulator
lCheck by using SCANNER's stop lamp switch diag-
nosing function from sensor value output function.
lCheck connection of ECU connector side stop lamp
switch terminal.
lCheck resistance of the stop lamp, switch.
- Each end resistance value of the switch Application
Rear / Right OUTLET Valve
Function and Response of The
Valve
Function and Response of The
Valve
Motor Relay / Circulation Pump
Stop Lamp Switch
Defect Code
20
21
22
24
27
Page 1041 of 1463
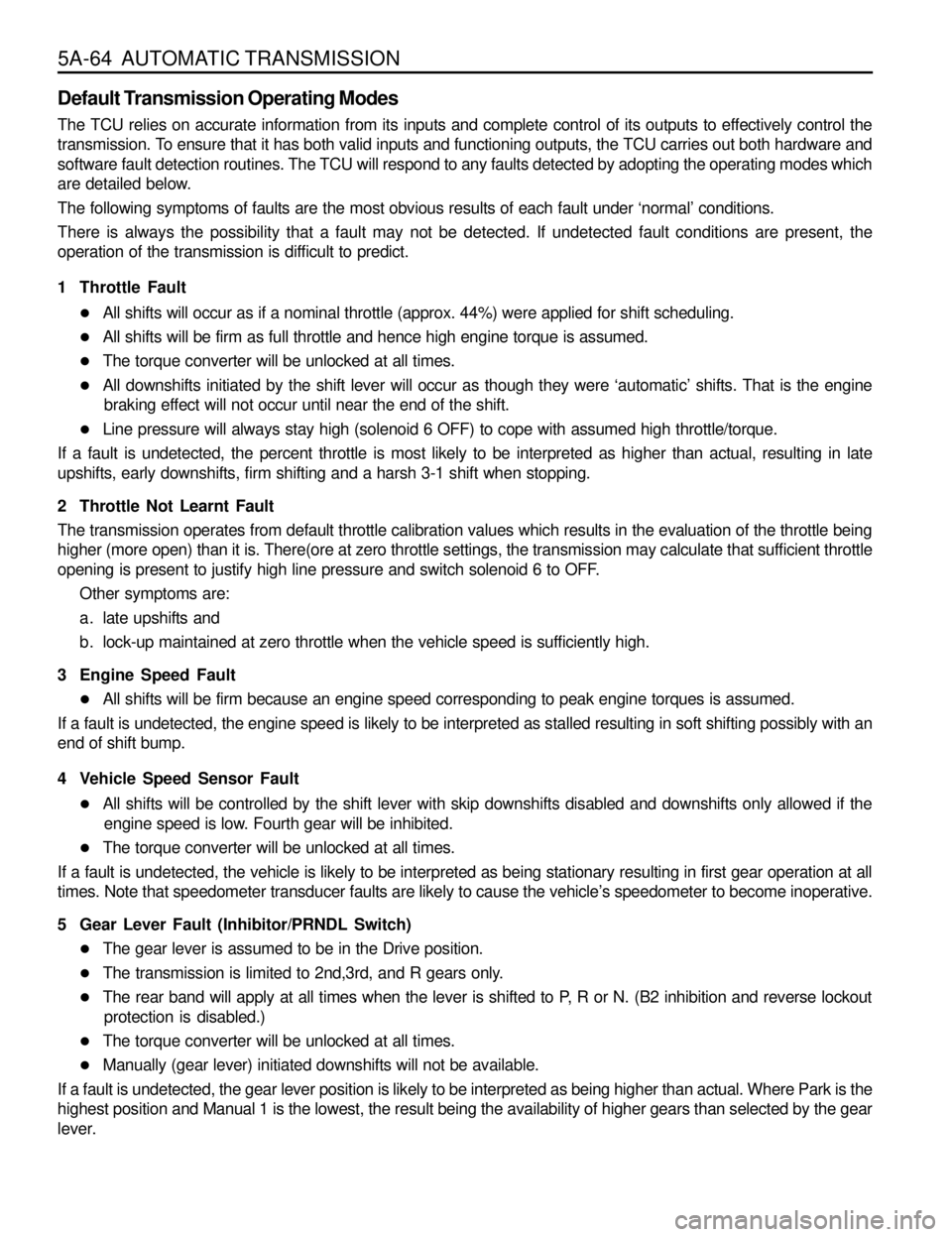
5A-64 AUTOMATIC TRANSMISSION
Default Transmission Operating Modes
The TCU relies on accurate information from its inputs and complete control of its outputs to effectively control the
transmission. To ensure that it has both valid inputs and functioning outputs, the TCU carries out both hardware and
software fault detection routines. The TCU will respond to any faults detected by adopting the operating modes which
are detailed below.
The following symptoms of faults are the most obvious results of each fault under ‘normal’ conditions.
There is always the possibility that a fault may not be detected. If undetected fault conditions are present, the
operation of the transmission is difficult to predict.
1 Throttle Fault
lAll shifts will occur as if a nominal throttle (approx. 44%) were applied for shift scheduling.
lAll shifts will be firm as full throttle and hence high engine torque is assumed.
lThe torque converter will be unlocked at all times.
lAll downshifts initiated by the shift lever will occur as though they were ‘automatic’ shifts. That is the engine
braking effect will not occur until near the end of the shift.
lLine pressure will always stay high (solenoid 6 OFF) to cope with assumed high throttle/torque.
If a fault is undetected, the percent throttle is most likely to be interpreted as higher than actual, resulting in late
upshifts, early downshifts, firm shifting and a harsh 3-1 shift when stopping.
2 Throttle Not Learnt Fault
The transmission operates from default throttle calibration values which results in the evaluation of the throttle being
higher (more open) than it is. There(ore at zero throttle settings, the transmission may calculate that sufficient throttle
opening is present to justify high line pressure and switch solenoid 6 to OFF.
Other symptoms are:
a. late upshifts and
b. lock-up maintained at zero throttle when the vehicle speed is sufficiently high.
3 Engine Speed Fault
lAll shifts will be firm because an engine speed corresponding to peak engine torques is assumed.
If a fault is undetected, the engine speed is likely to be interpreted as stalled resulting in soft shifting possibly with an
end of shift bump.
4 Vehicle Speed Sensor Fault
lAll shifts will be controlled by the shift lever with skip downshifts disabled and downshifts only allowed if the
engine speed is low. Fourth gear will be inhibited.
lThe torque converter will be unlocked at all times.
If a fault is undetected, the vehicle is likely to be interpreted as being stationary resulting in first gear operation at all
times. Note that speedometer transducer faults are likely to cause the vehicle’s speedometer to become inoperative.
5 Gear Lever Fault (Inhibitor/PRNDL Switch)
lThe gear lever is assumed to be in the Drive position.
lThe transmission is limited to 2nd,3rd, and R gears only.
lThe rear band will apply at all times when the lever is shifted to P, R or N. (B2 inhibition and reverse lockout
protection is disabled.)
lThe torque converter will be unlocked at all times.
lManually (gear lever) initiated downshifts will not be available.
If a fault is undetected, the gear lever position is likely to be interpreted as being higher than actual. Where Park is the
highest position and Manual 1 is the lowest, the result being the availability of higher gears than selected by the gear
lever.
Page 1042 of 1463
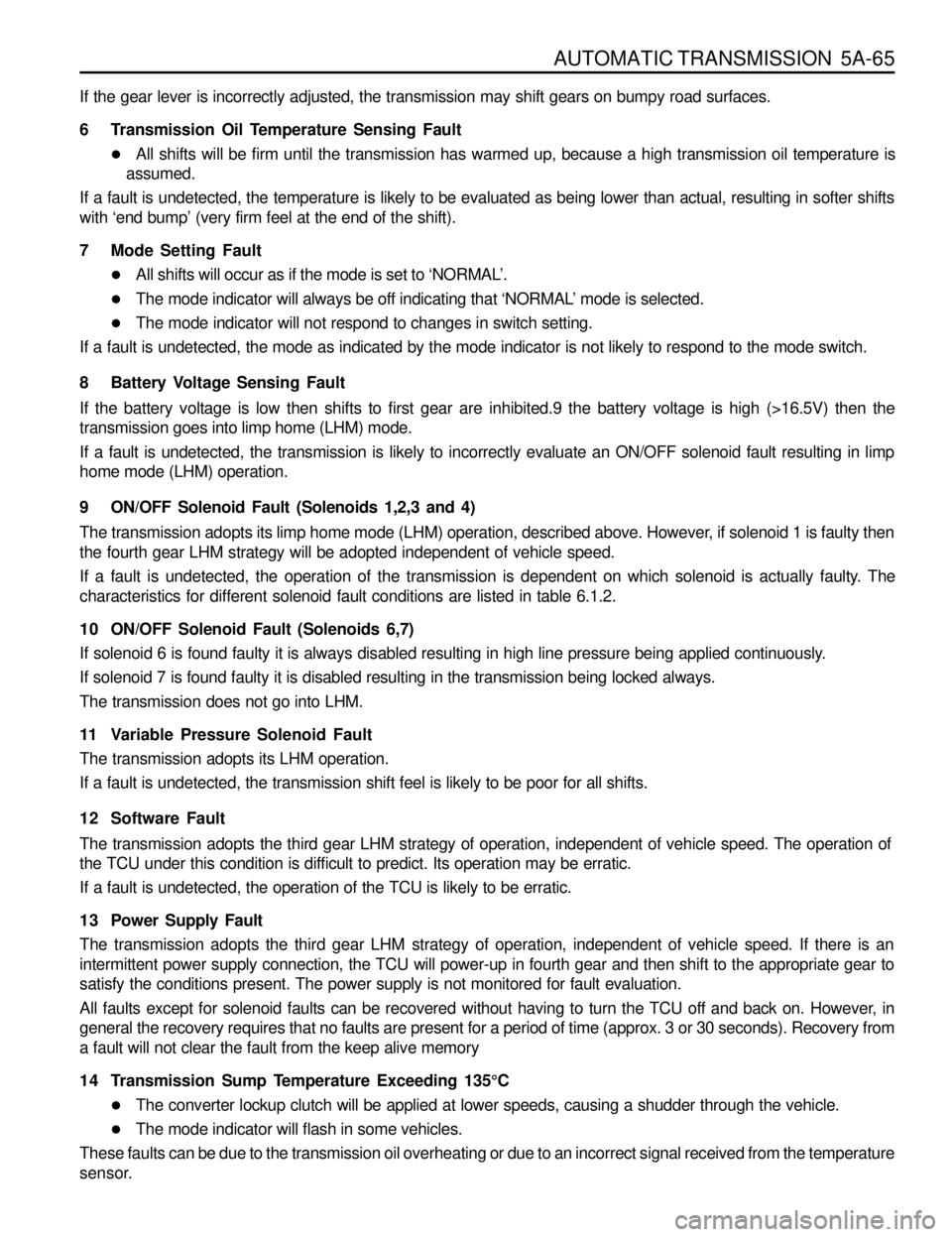
AUTOMATIC TRANSMISSION 5A-65
If the gear lever is incorrectly adjusted, the transmission may shift gears on bumpy road surfaces.
6 Transmission Oil Temperature Sensing Fault
lAll shifts will be firm until the transmission has warmed up, because a high transmission oil temperature is
assumed.
If a fault is undetected, the temperature is likely to be evaluated as being lower than actual, resulting in softer shifts
with ‘end bump’ (very firm feel at the end of the shift).
7 Mode Setting Fault
lAll shifts will occur as if the mode is set to ‘NORMAL’.
lThe mode indicator will always be off indicating that ‘NORMAL’ mode is selected.
lThe mode indicator will not respond to changes in switch setting.
If a fault is undetected, the mode as indicated by the mode indicator is not likely to respond to the mode switch.
8 Battery Voltage Sensing Fault
If the battery voltage is low then shifts to first gear are inhibited.9 the battery voltage is high (>16.5V) then the
transmission goes into limp home (LHM) mode.
If a fault is undetected, the transmission is likely to incorrectly evaluate an ON/OFF solenoid fault resulting in limp
home mode (LHM) operation.
9 ON/OFF Solenoid Fault (Solenoids 1,2,3 and 4)
The transmission adopts its limp home mode (LHM) operation, described above. However, if solenoid 1 is faulty then
the fourth gear LHM strategy will be adopted independent of vehicle speed.
If a fault is undetected, the operation of the transmission is dependent on which solenoid is actually faulty. The
characteristics for different solenoid fault conditions are listed in table 6.1.2.
10 ON/OFF Solenoid Fault (Solenoids 6,7)
If solenoid 6 is found faulty it is always disabled resulting in high line pressure being applied continuously.
If solenoid 7 is found faulty it is disabled resulting in the transmission being locked always.
The transmission does not go into LHM.
11 Variable Pressure Solenoid Fault
The transmission adopts its LHM operation.
If a fault is undetected, the transmission shift feel is likely to be poor for all shifts.
12 Software Fault
The transmission adopts the third gear LHM strategy of operation, independent of vehicle speed. The operation of
the TCU under this condition is difficult to predict. Its operation may be erratic.
If a fault is undetected, the operation of the TCU is likely to be erratic.
13 Power Supply Fault
The transmission adopts the third gear LHM strategy of operation, independent of vehicle speed. If there is an
intermittent power supply connection, the TCU will power-up in fourth gear and then shift to the appropriate gear to
satisfy the conditions present. The power supply is not monitored for fault evaluation.
All faults except for solenoid faults can be recovered without having to turn the TCU off and back on. However, in
general the recovery requires that no faults are present for a period of time (approx. 3 or 30 seconds). Recovery from
a fault will not clear the fault from the keep alive memory
14 Transmission Sump Temperature Exceeding 135°C
lThe converter lockup clutch will be applied at lower speeds, causing a shudder through the vehicle.
lThe mode indicator will flash in some vehicles.
These faults can be due to the transmission oil overheating or due to an incorrect signal received from the temperature
sensor.
Page 1044 of 1463
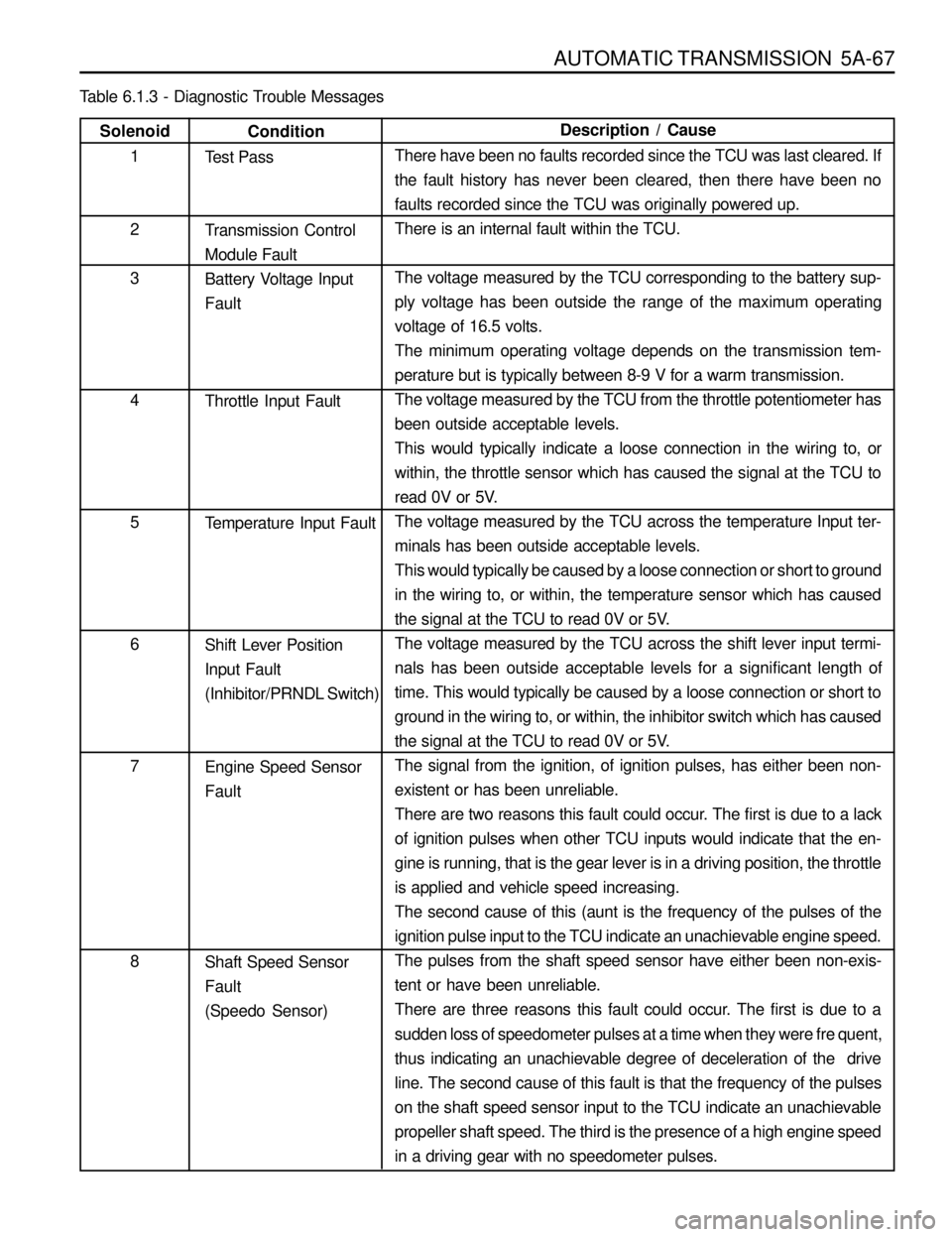
AUTOMATIC TRANSMISSION 5A-67
Table 6.1.3 - Diagnostic Trouble Messages
Description / Cause
There have been no faults recorded since the TCU was last cleared. If
the fault history has never been cleared, then there have been no
faults recorded since the TCU was originally powered up.
There is an internal fault within the TCU.
The voltage measured by the TCU corresponding to the battery sup-
ply voltage has been outside the range of the maximum operating
voltage of 16.5 volts.
The minimum operating voltage depends on the transmission tem-
perature but is typically between 8-9 V for a warm transmission.
The voltage measured by the TCU from the throttle potentiometer has
been outside acceptable levels.
This would typically indicate a loose connection in the wiring to, or
within, the throttle sensor which has caused the signal at the TCU to
read 0V or 5V.
The voltage measured by the TCU across the temperature Input ter-
minals has been outside acceptable levels.
This would typically be caused by a loose connection or short to ground
in the wiring to, or within, the temperature sensor which has caused
the signal at the TCU to read 0V or 5V.
The voltage measured by the TCU across the shift lever input termi-
nals has been outside acceptable levels for a significant length of
time. This would typically be caused by a loose connection or short to
ground in the wiring to, or within, the inhibitor switch which has caused
the signal at the TCU to read 0V or 5V.
The signal from the ignition, of ignition pulses, has either been non-
existent or has been unreliable.
There are two reasons this fault could occur. The first is due to a lack
of ignition pulses when other TCU inputs would indicate that the en-
gine is running, that is the gear lever is in a driving position, the throttle
is applied and vehicle speed increasing.
The second cause of this (aunt is the frequency of the pulses of the
ignition pulse input to the TCU indicate an unachievable engine speed.
The pulses from the shaft speed sensor have either been non-exis-
tent or have been unreliable.
There are three reasons this fault could occur. The first is due to a
sudden loss of speedometer pulses at a time when they were fre quent,
thus indicating an unachievable degree of deceleration of the drive
line. The second cause of this fault is that the frequency of the pulses
on the shaft speed sensor input to the TCU indicate an unachievable
propeller shaft speed. The third is the presence of a high engine speed
in a driving gear with no speedometer pulses. Condition
Test Pass
Transmission Control
Module Fault
Battery Voltage Input
Fault
Throttle Input Fault
Temperature Input Fault
Shift Lever Position
Input Fault
(Inhibitor/PRNDL Switch)
Engine Speed Sensor
Fault
Shaft Speed Sensor
Fault
(Speedo Sensor)Solenoid
1
2
3
4
5
6
7
8