lug pattern SSANGYONG MUSSO 1998 Workshop Repair Manual
[x] Cancel search | Manufacturer: SSANGYONG, Model Year: 1998, Model line: MUSSO, Model: SSANGYONG MUSSO 1998Pages: 1463, PDF Size: 19.88 MB
Page 625 of 1463
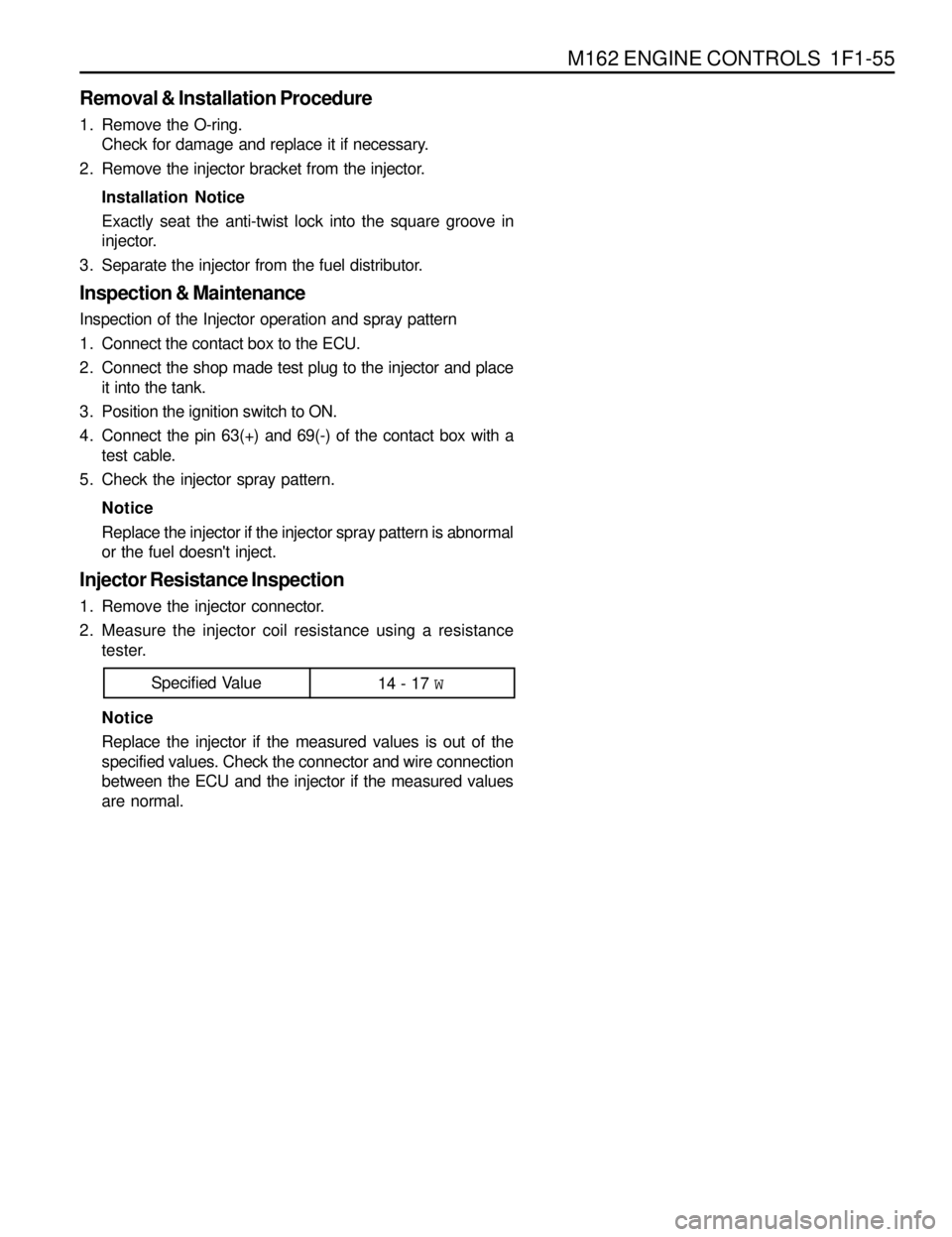
M162 ENGINE CONTROLS 1F1-55
Removal & Installation Procedure
1. Remove the O-ring.
Check for damage and replace it if necessary.
2. Remove the injector bracket from the injector.
Installation Notice
Exactly seat the anti-twist lock into the square groove in
injector.
3. Separate the injector from the fuel distributor.
Inspection & Maintenance
Inspection of the Injector operation and spray pattern
1. Connect the contact box to the ECU.
2. Connect the shop made test plug to the injector and place
it into the tank.
3. Position the ignition switch to ON.
4. Connect the pin 63(+) and 69(-) of the contact box with a
test cable.
5. Check the injector spray pattern.
Notice
Replace the injector if the injector spray pattern is abnormal
or the fuel doesn't inject.
Injector Resistance Inspection
1. Remove the injector connector.
2. Measure the injector coil resistance using a resistance
tester.
Notice
Replace the injector if the measured values is out of the
specified values. Check the connector and wire connection
between the ECU and the injector if the measured values
are normal.
Specified Value
14 - 17 W
Page 704 of 1463
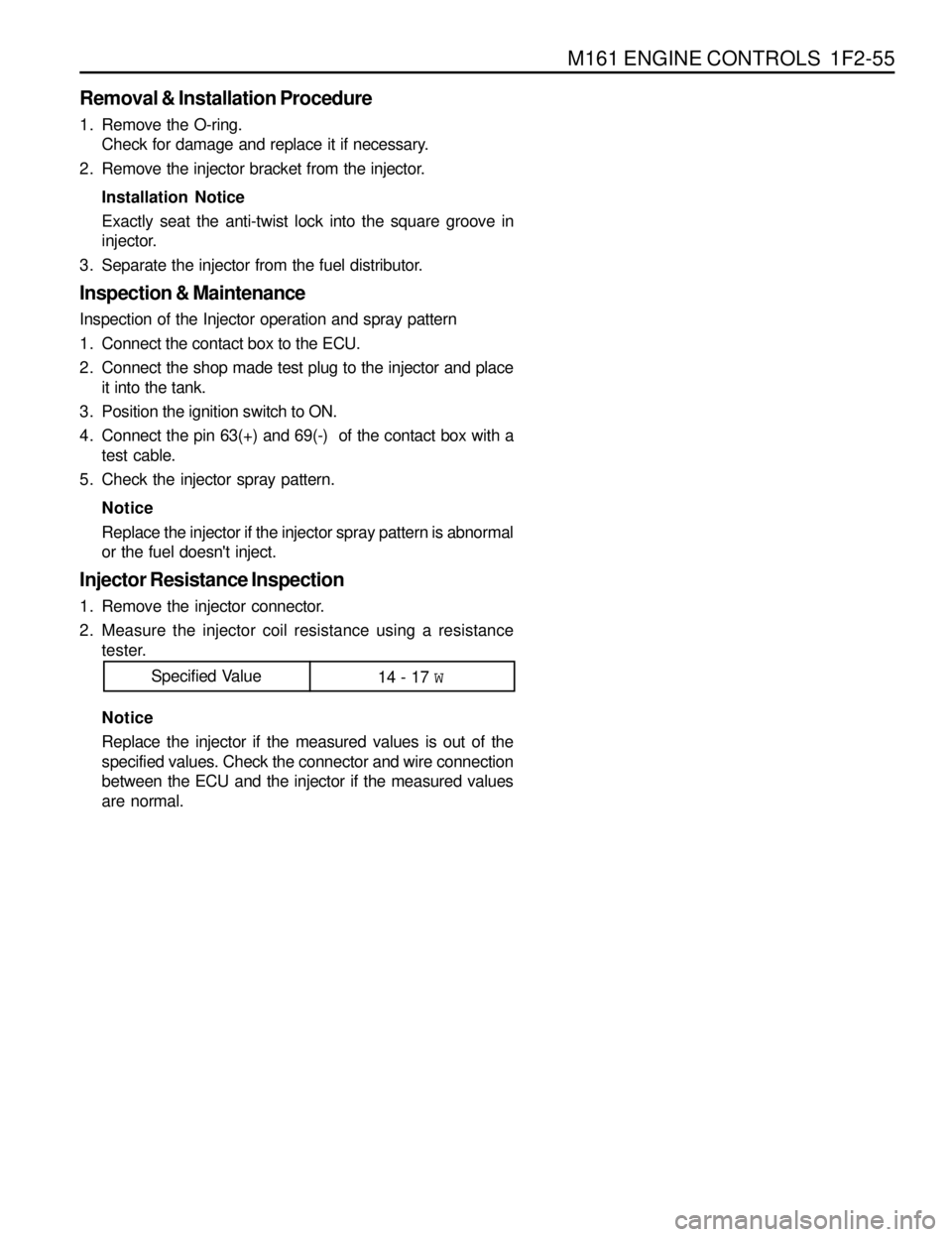
M161 ENGINE CONTROLS 1F2-55
Removal & Installation Procedure
1. Remove the O-ring.
Check for damage and replace it if necessary.
2. Remove the injector bracket from the injector.
Installation Notice
Exactly seat the anti-twist lock into the square groove in
injector.
3. Separate the injector from the fuel distributor.
Inspection & Maintenance
Inspection of the Injector operation and spray pattern
1. Connect the contact box to the ECU.
2. Connect the shop made test plug to the injector and place
it into the tank.
3. Position the ignition switch to ON.
4. Connect the pin 63(+) and 69(-) of the contact box with a
test cable.
5. Check the injector spray pattern.
Notice
Replace the injector if the injector spray pattern is abnormal
or the fuel doesn't inject.
Injector Resistance Inspection
1. Remove the injector connector.
2. Measure the injector coil resistance using a resistance
tester.
Notice
Replace the injector if the measured values is out of the
specified values. Check the connector and wire connection
between the ECU and the injector if the measured values
are normal.
Specified Value
14 - 17 W
Page 1046 of 1463
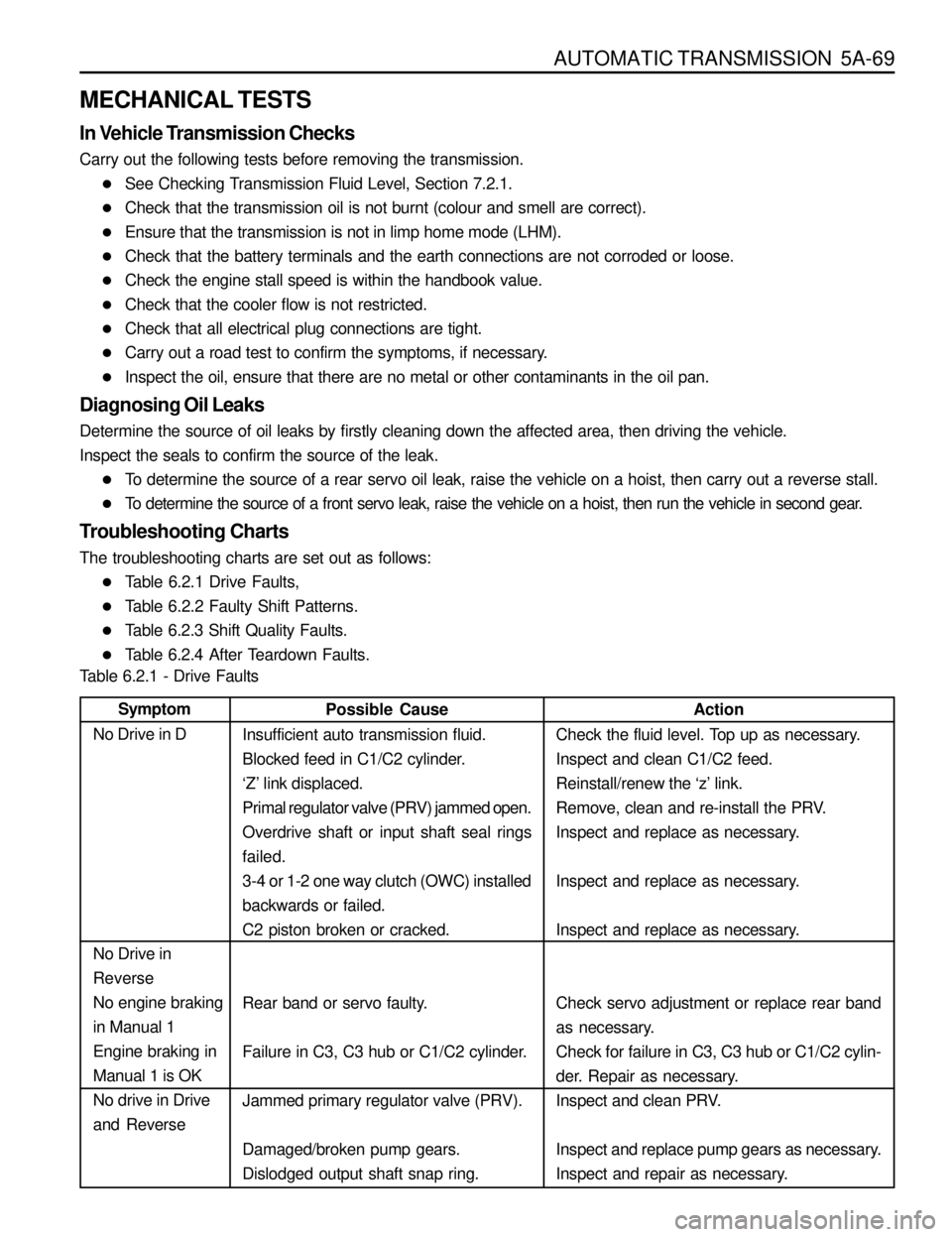
AUTOMATIC TRANSMISSION 5A-69
MECHANICAL TESTS
In Vehicle Transmission Checks
Carry out the following tests before removing the transmission.
lSee Checking Transmission Fluid Level, Section 7.2.1.
lCheck that the transmission oil is not burnt (colour and smell are correct).
lEnsure that the transmission is not in limp home mode (LHM).
lCheck that the battery terminals and the earth connections are not corroded or loose.
lCheck the engine stall speed is within the handbook value.
lCheck that the cooler flow is not restricted.
lCheck that all electrical plug connections are tight.
lCarry out a road test to confirm the symptoms, if necessary.
lInspect the oil, ensure that there are no metal or other contaminants in the oil pan.
Diagnosing Oil Leaks
Determine the source of oil leaks by firstly cleaning down the affected area, then driving the vehicle.
Inspect the seals to confirm the source of the leak.
lTo determine the source of a rear servo oil leak, raise the vehicle on a hoist, then carry out a reverse stall.
lTo determine the source of a front servo leak, raise the vehicle on a hoist, then run the vehicle in second gear.
Troubleshooting Charts
The troubleshooting charts are set out as follows:
lTable 6.2.1 Drive Faults,
lTable 6.2.2 Faulty Shift Patterns.
lTable 6.2.3 Shift Quality Faults.
lTable 6.2.4 After Teardown Faults.
Table 6.2.1 - Drive Faults
Action
Check the fluid level. Top up as necessary.
Inspect and clean C1/C2 feed.
Reinstall/renew the āzā link.
Remove, clean and re-install the PRV.
Inspect and replace as necessary.
Inspect and replace as necessary.
Inspect and replace as necessary.
Check servo adjustment or replace rear band
as necessary.
Check for failure in C3, C3 hub or C1/C2 cylin-
der. Repair as necessary.
Inspect and clean PRV.
Inspect and replace pump gears as necessary.
Inspect and repair as necessary. Possible Cause
Insufficient auto transmission fluid.
Blocked feed in C1/C2 cylinder.
āZā link displaced.
Primal regulator valve (PRV) jammed open.
Overdrive shaft or input shaft seal rings
failed.
3-4 or 1-2 one way clutch (OWC) installed
backwards or failed.
C2 piston broken or cracked.
Rear band or servo faulty.
Failure in C3, C3 hub or C1/C2 cylinder.
Jammed primary regulator valve (PRV).
Damaged/broken pump gears.
Dislodged output shaft snap ring.Symptom
No Drive in D
No Drive in
Reverse
No engine braking
in Manual 1
Engine braking in
Manual 1 is OK
No drive in Drive
and Reverse