wheel SSANGYONG MUSSO 2003 Workshop Manual
[x] Cancel search | Manufacturer: SSANGYONG, Model Year: 2003, Model line: MUSSO, Model: SSANGYONG MUSSO 2003Pages: 1574, PDF Size: 26.41 MB
Page 378 of 1574
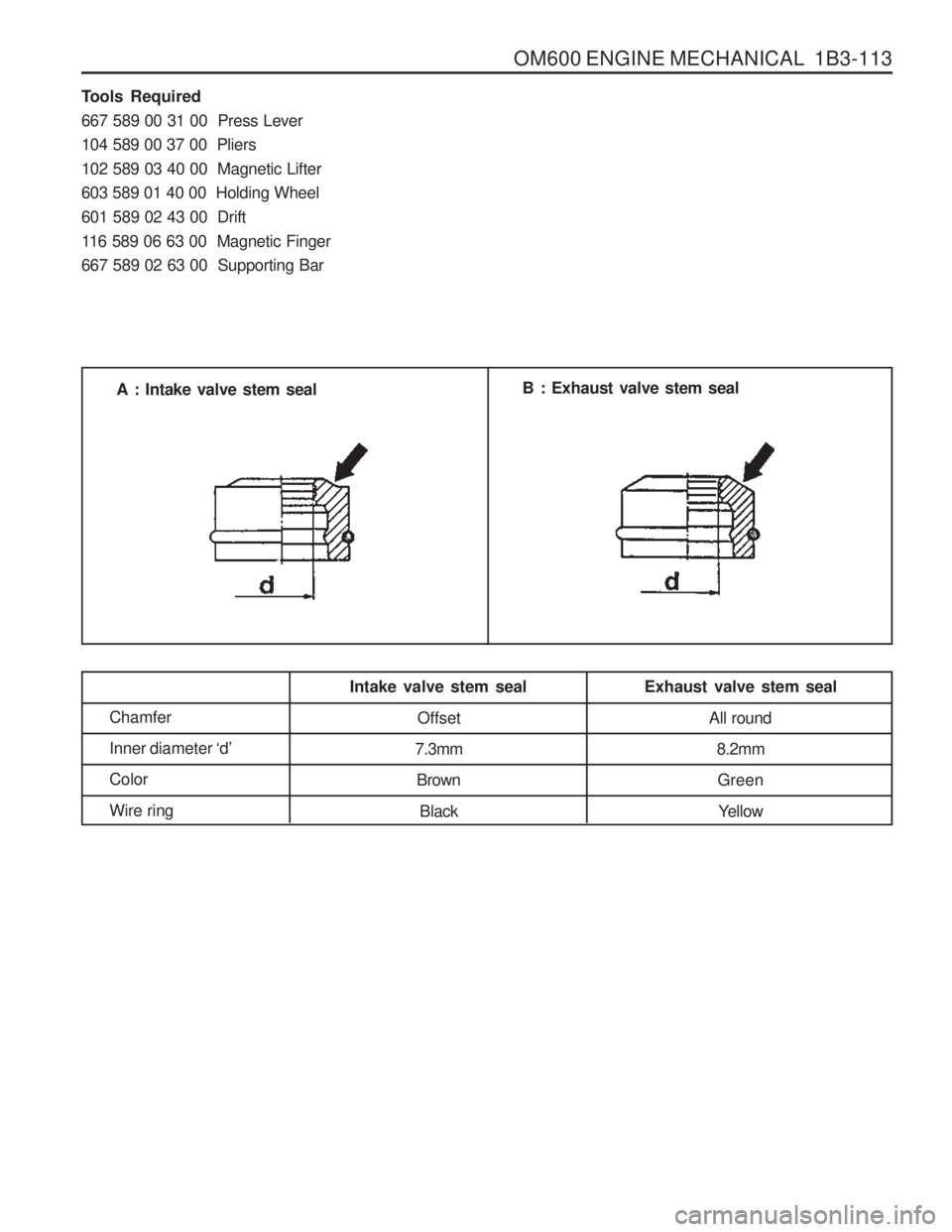
OM600 ENGINE MECHANICAL 1B3-113
Tools Required 667 589 00 31 00 Press Lever104 589 00 37 00 Pliers102 589 03 40 00 Magnetic Lifter603 589 01 40 00 Holding Wheel601 589 02 43 00 Drift
116 589 06 63 00 Magnetic Finger667 589 02 63 00 Supporting BarA : Intake valve stem seal
B : Exhaust valve stem seal
Chamfer Inner diameter ‘d’
ColorWire ring Intake valve stem seal
Offset
7.3mm Brown Black Exhaust valve stem seal
All round8.2mmGreen Yellow
Page 379 of 1574
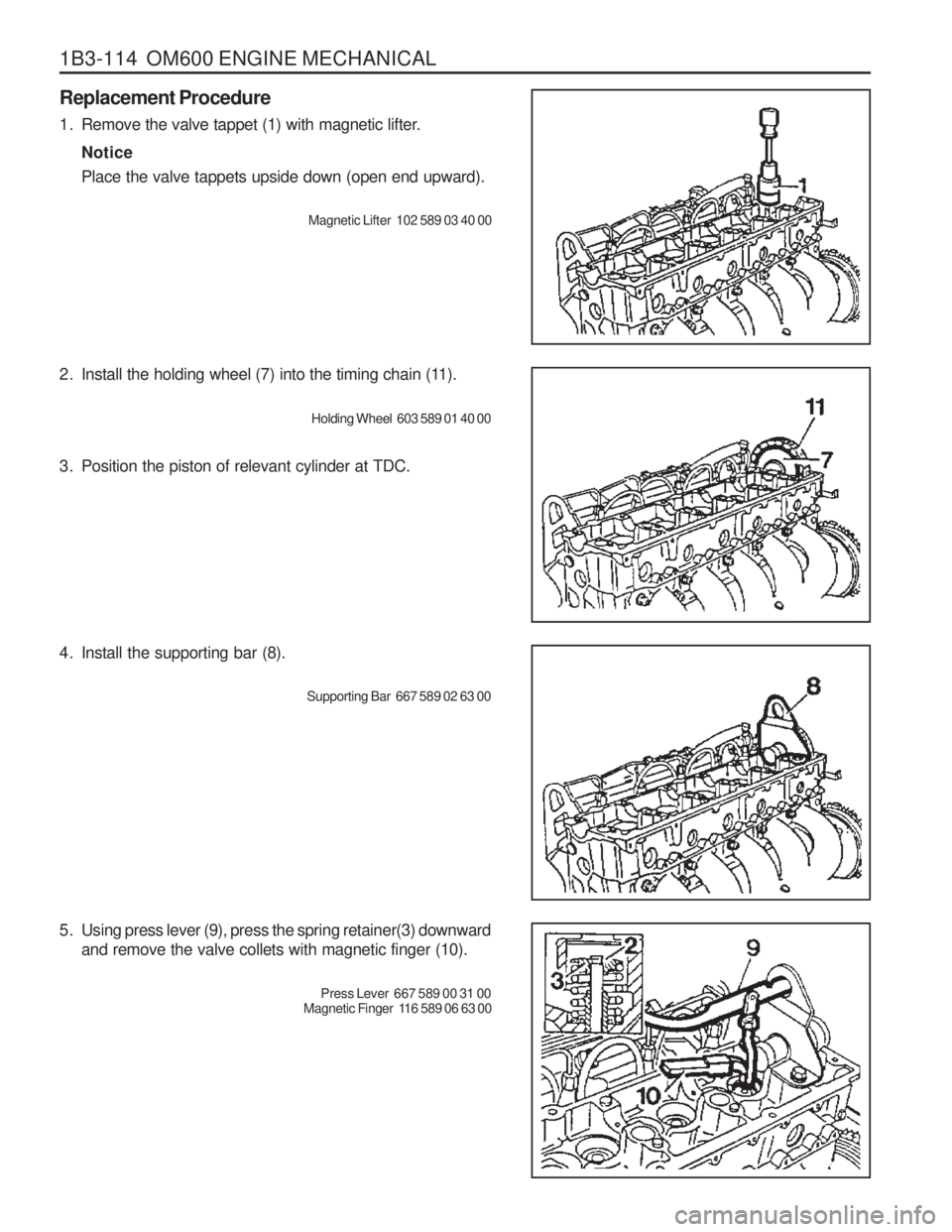
1B3-114 OM600 ENGINE MECHANICAL Replacement Procedure
1. Remove the valve tappet (1) with magnetic lifter.Notice Place the valve tappets upside down (open end upward).
Magnetic Lifter 102 589 03 40 00
2. Install the holding wheel (7) into the timing chain (11). Holding Wheel 603 589 01 40 00
3. Position the piston of relevant cylinder at TDC.
4. Install the supporting bar (8). Supporting Bar 667 589 02 63 00
5. Using press lever (9), press the spring retainer(3) downward and remove the valve collets with magnetic finger (10).
Press Lever 667 589 00 31 00
Magnetic Finger 116 589 06 63 00
Page 447 of 1574
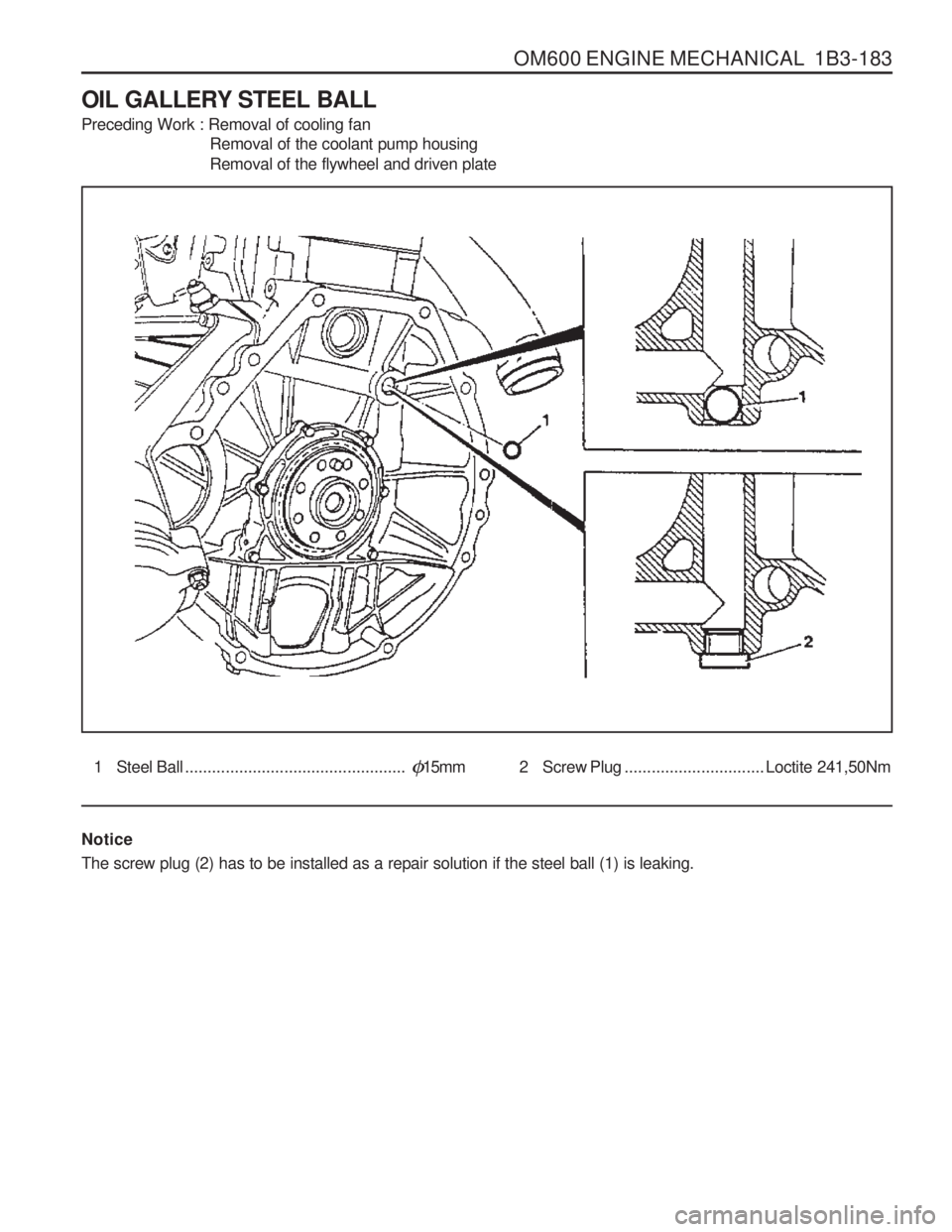
OM600 ENGINE MECHANICAL 1B3-183
OIL GALLERY STEEL BALL Preceding Work : Removal of cooling fan Removal of the coolant pump housing Removal of the flywheel and driven plate
1 Steel Ball................................................. 15mm 2 Screw Plug ............................... Loctite 241,50Nm
Notice The screw plug (2) has to be installed as a repair solution if the steel ball (1) is leaking.
Page 597 of 1574
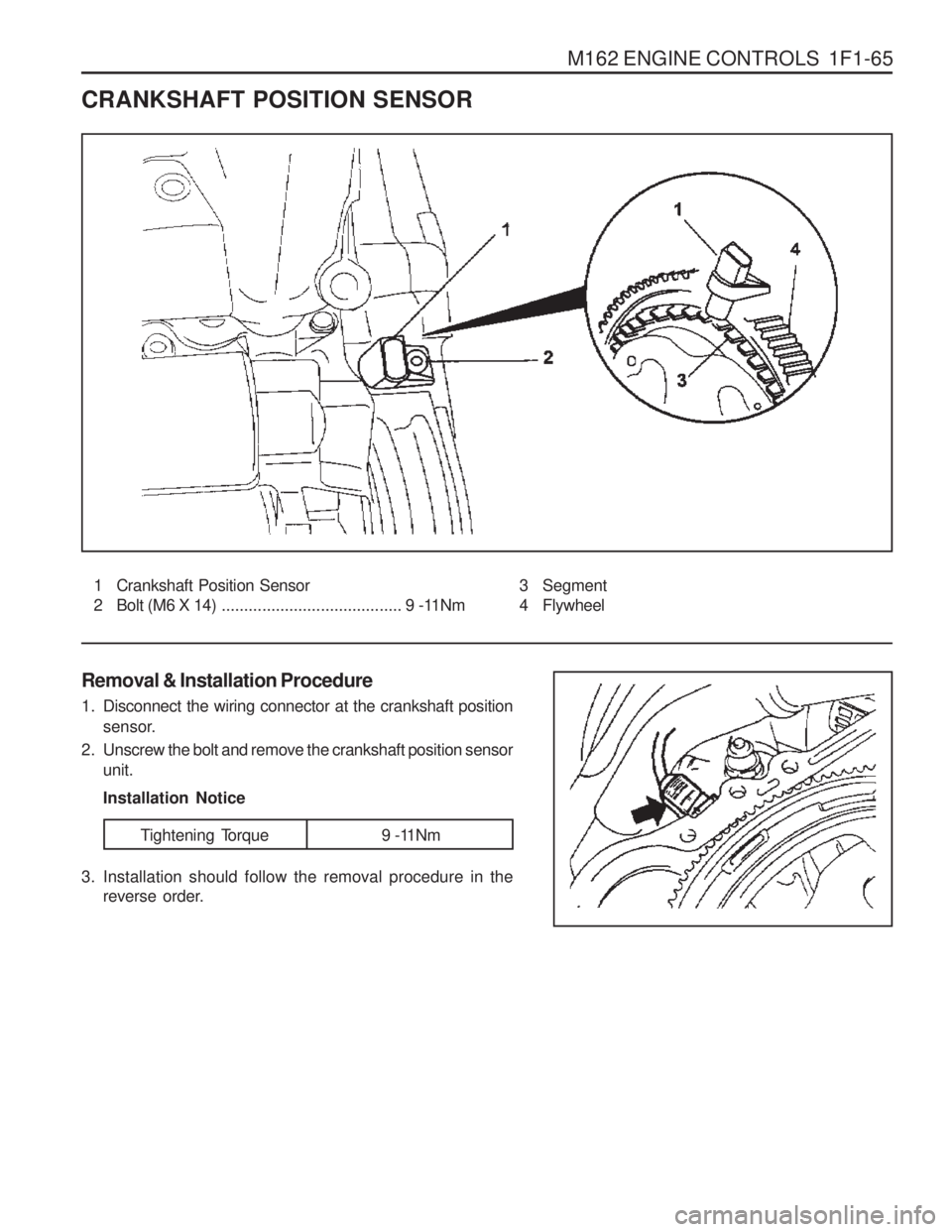
M162 ENGINE CONTROLS 1F1-65
1 Crankshaft Position Sensor
2 Bolt (M6 X 14)........................................ 9 -11Nm
CRANKSHAFT POSITION SENSOR
Removal & Installation Procedure
1. Disconnect the wiring connector at the crankshaft position
sensor.
2. Unscrew the bolt and remove the crankshaft position sensor unit. Installation Notice
3. Installation should follow the removal procedure in the reverse order. 3 Segment
4 Flywheel
Tightening Torque 9 -11Nm
Page 692 of 1574
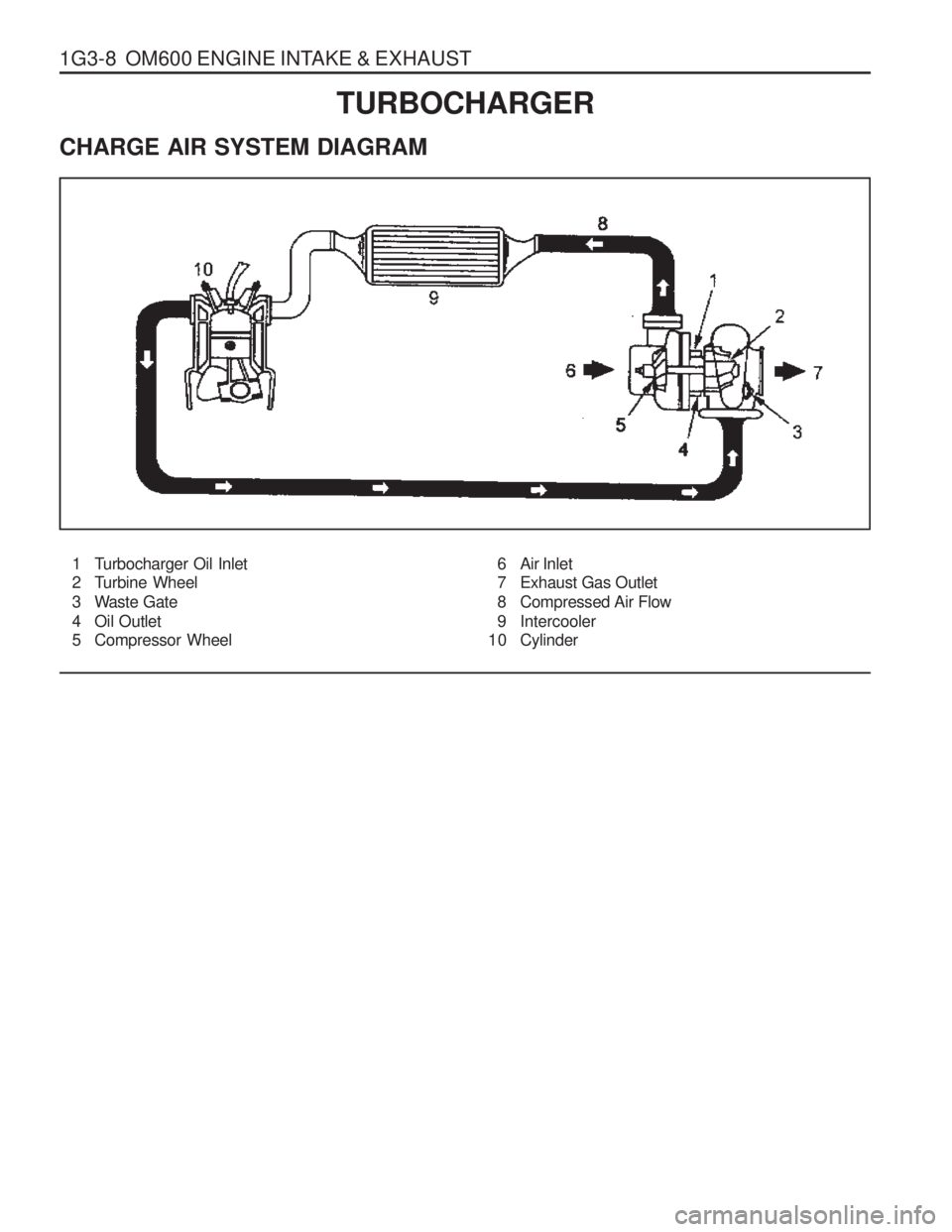
1G3-8 OM600 ENGINE INTAKE & EXHAUST
1 Turbocharger Oil Inlet
2 Turbine Wheel
3 Waste Gate
4 Oil Outlet
5 Compressor Wheel6 Air Inlet
7 Exhaust Gas Outlet
8 Compressed Air Flow
9 Intercooler
10 Cylinder
TURBOCHARGER
CHARGE AIR SYSTEM DIAGRAM
Page 699 of 1574
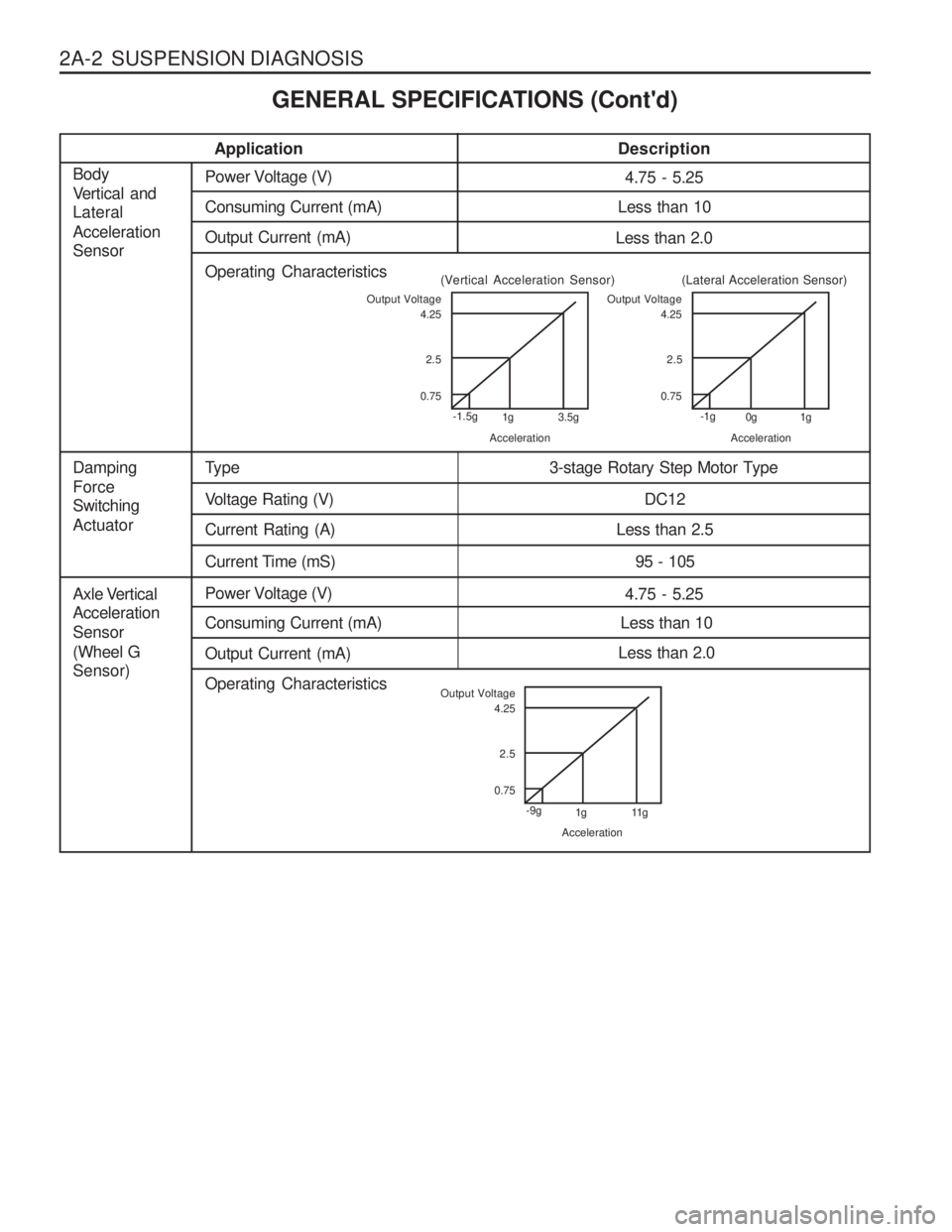
2A-2 SUSPENSION DIAGNOSISApplication
Description
4.75 - 5.25Power Voltage (V)
Axle Vertical Acceleration Sensor(Wheel G Sensor) Less than 10
Consuming Current (mA)
Less than 2.0
Output Current (mA)
Operating Characteristics
Type
Damping Force Switching Actuator3-stage Rotary Step Motor Type
Voltage Rating (V)
DC12
Current Rating (A)
Less than 2.5
Current Time (mS) 95 - 105
4.75 - 5.25Power Voltage (V)
Body
Vertical and Lateral Acceleration Sensor
Less than 10
Consuming Current (mA)
Less than 2.0
Output Current (mA)
Operating Characteristics
Output Voltage
0.752.5
4.25
-1.5g 1g 3.5g
Acceleration
(Vertical Acceleration Sensor)Output Voltage
0.752.5
4.25
-1g 0g 1g
Acceleration
(Lateral Acceleration Sensor)
Output Voltage
0.752.5
4.25
-9g 1g 11g
Acceleration
GENERAL SPECIFICATIONS (Cont'd)
Page 700 of 1574
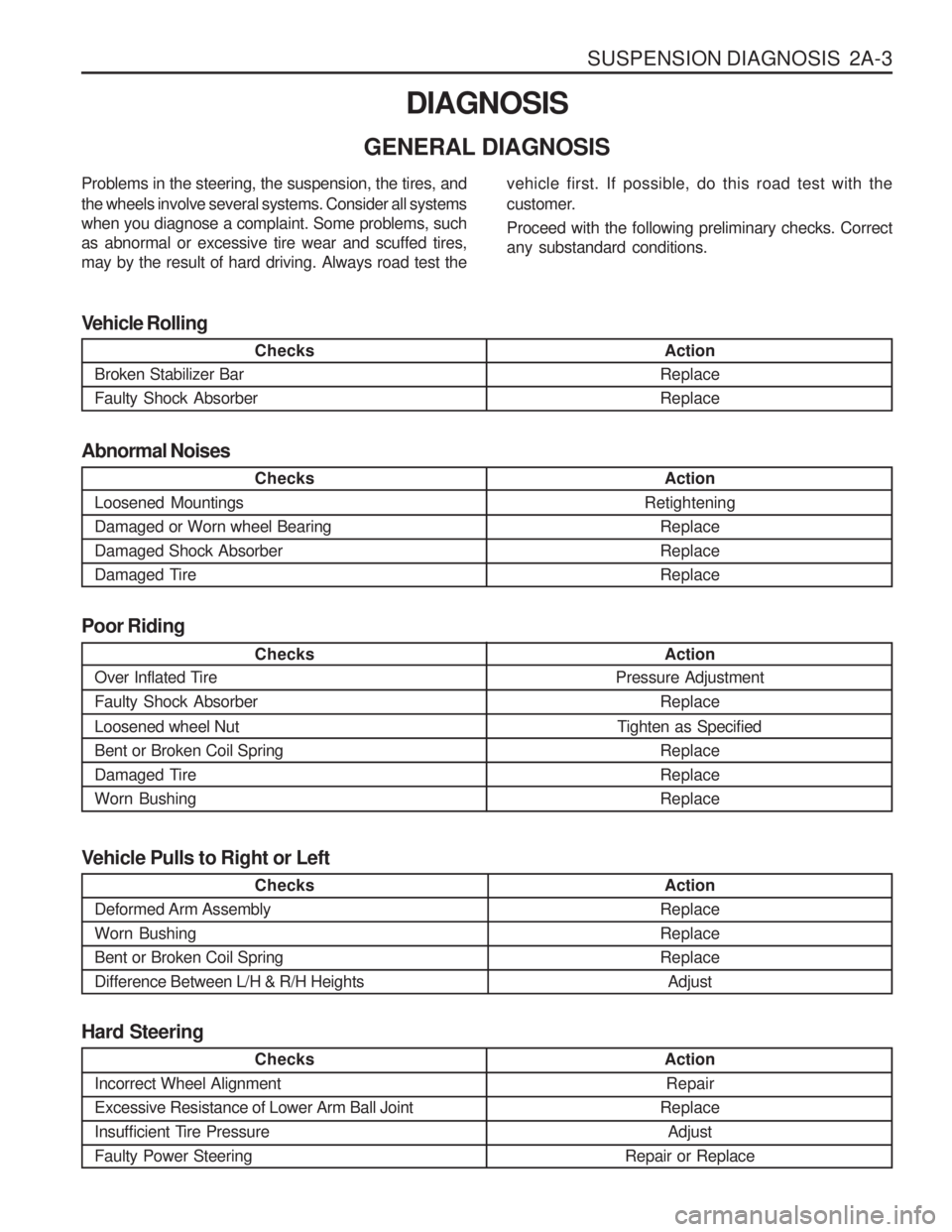
SUSPENSION DIAGNOSIS 2A-3
DIAGNOSIS
GENERAL DIAGNOSIS
Checks
Loosened Mountings Damaged or Worn wheel BearingDamaged Shock Absorber
Damaged Tire Action
Retightening ReplaceReplaceReplace
Abnormal Noises
Checks
Broken Stabilizer Bar Faulty Shock Absorber Action
ReplaceReplace
Vehicle Rolling
Checks
Over Inflated Tire Faulty Shock Absorber Loosened wheel Nut Bent or Broken Coil Spring
Damaged TireWorn Bushing Action
Pressure Adjustment
Replace
Tighten as Specified ReplaceReplaceReplace
Poor Riding
Problems in the steering, the suspension, the tires, and the wheels involve several systems. Consider all systems when you diagnose a complaint. Some problems, suchas abnormal or excessive tire wear and scuffed tires,may by the result of hard driving. Always road test the
vehicle first. If possible, do this road test with the
customer. Proceed with the following preliminary checks. Correct any substandard conditions.
Checks
Incorrect Wheel Alignment Excessive Resistance of Lower Arm Ball Joint
Insufficient Tire PressureFaulty Power Steering
Action Repair
Replace Adjust
Repair or Replace
Hard Steering
Checks
Deformed Arm Assembly Worn BushingBent or Broken Coil SpringDifference Between L/H & R/H Heights Action
ReplaceReplaceReplace Adjust
Vehicle Pulls to Right or Left
Page 701 of 1574
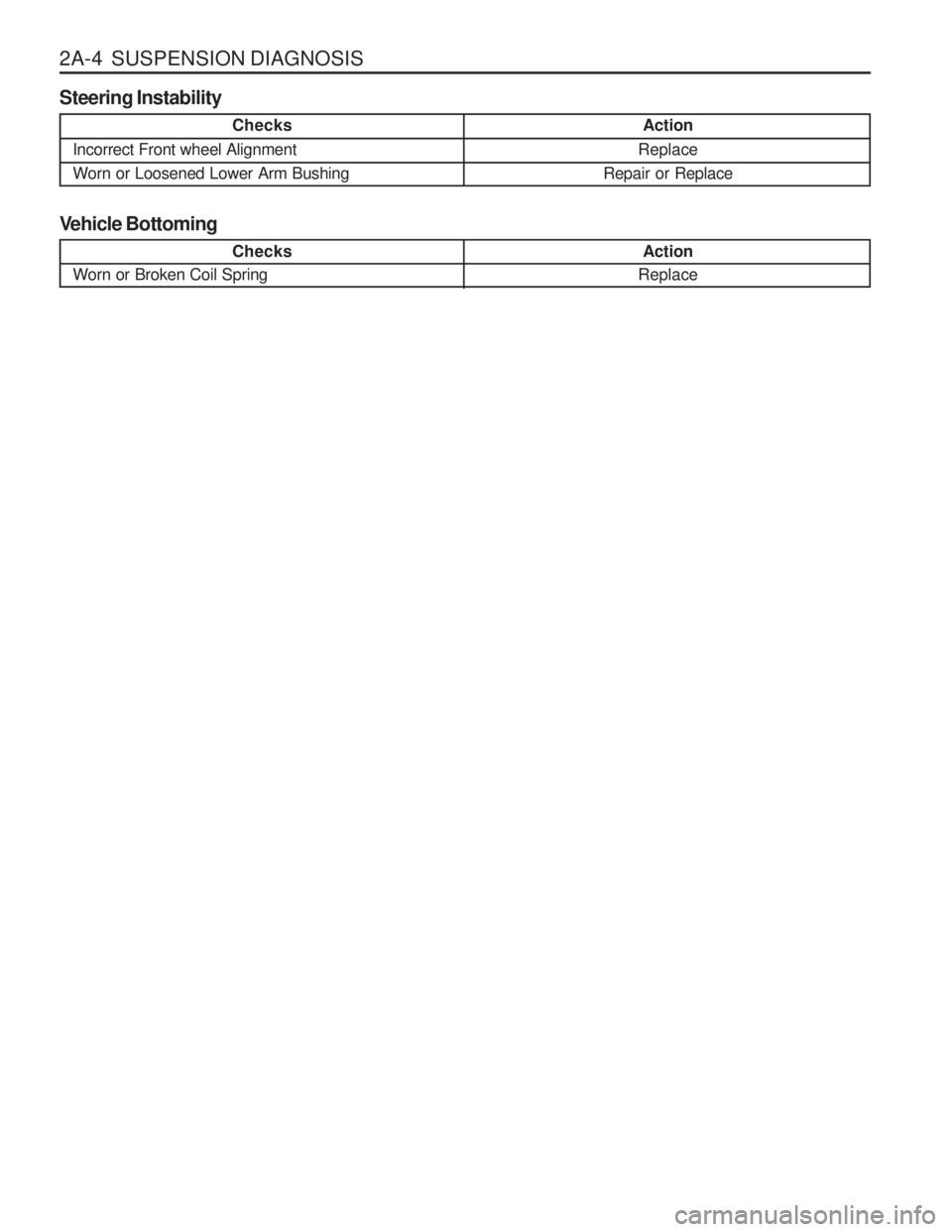
2A-4 SUSPENSION DIAGNOSISChecks
Worn or Broken Coil Spring Checks
Incorrect Front wheel Alignment Worn or Loosened Lower Arm Bushing
Action
Replace
Repair or Replace
Steering Instability
Action
Replace
Vehicle Bottoming
Page 702 of 1574
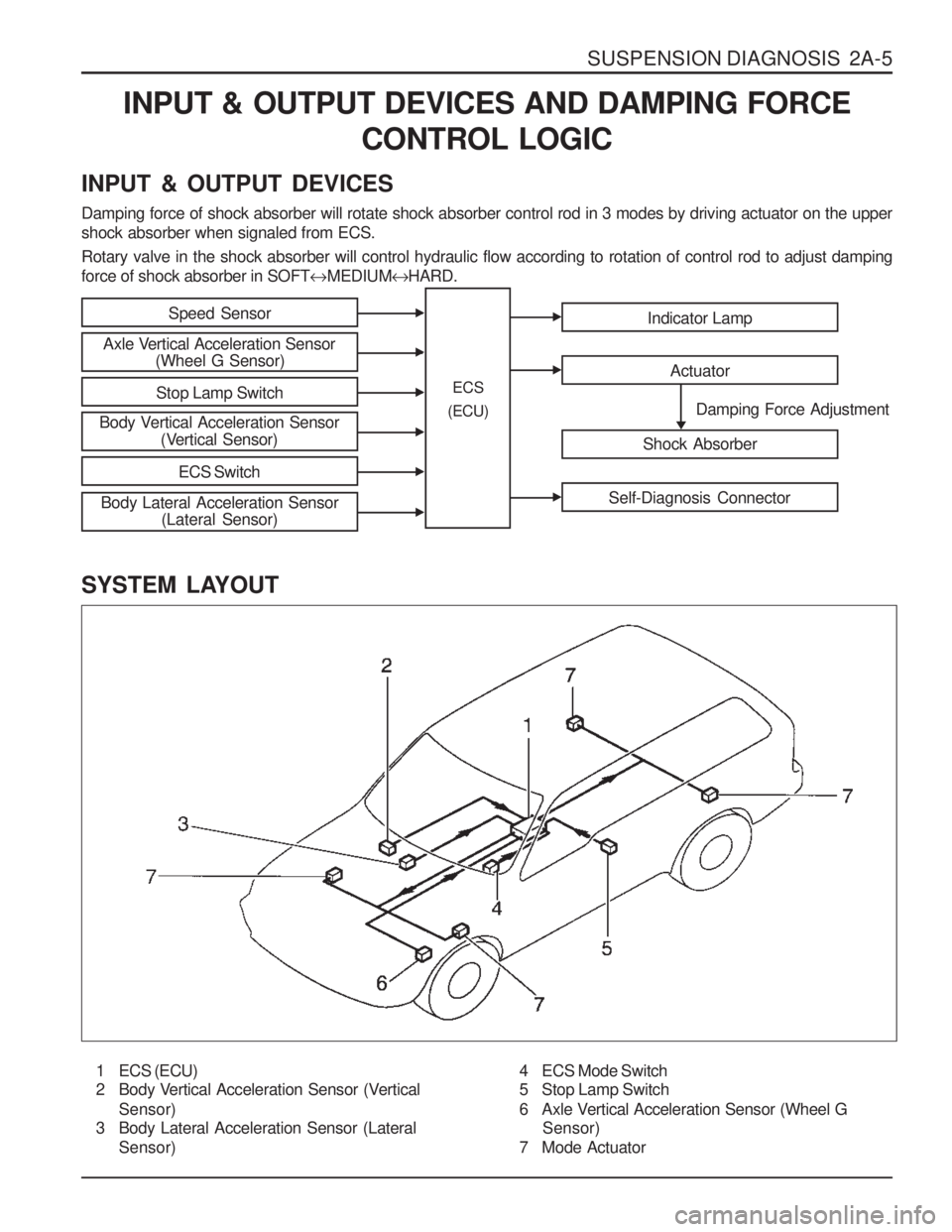
SUSPENSION DIAGNOSIS 2A-5
INPUT & OUTPUT DEVICES AND DAMPING FORCECONTROL LOGIC
INPUT & OUTPUT DEVICES Damping force of shock absorber will rotate shock absorber control rod in 3 modes by driving actuator on the upper shock absorber when signaled from ECS. Rotary valve in the shock absorber will control hydraulic flow according to rotation of control rod to adjust damping force of shock absorber in SOFT MEDIUM HARD.
SYSTEM LAYOUT
1 ECS (ECU)
2 Body Vertical Acceleration Sensor (Vertical Sensor)
3 Body Lateral Acceleration Sensor (Lateral
Sensor)
Speed Sensor
Axle Vertical Acceleration Sensor (Wheel G Sensor)
Stop Lamp Switch
Body Vertical Acceleration Sensor (Vertical Sensor)
ECS Switch
Indicator Lamp
Actuator
Shock Absorber
Self-Diagnosis Connector
Damping Force Adjustment
ECS
(ECU)
Body Lateral Acceleration Sensor (Lateral Sensor)
4 ECS Mode Switch
5 Stop Lamp Switch
6 Axle Vertical Acceleration Sensor (Wheel G
Sensor)
7 Mode Actuator
Page 704 of 1574
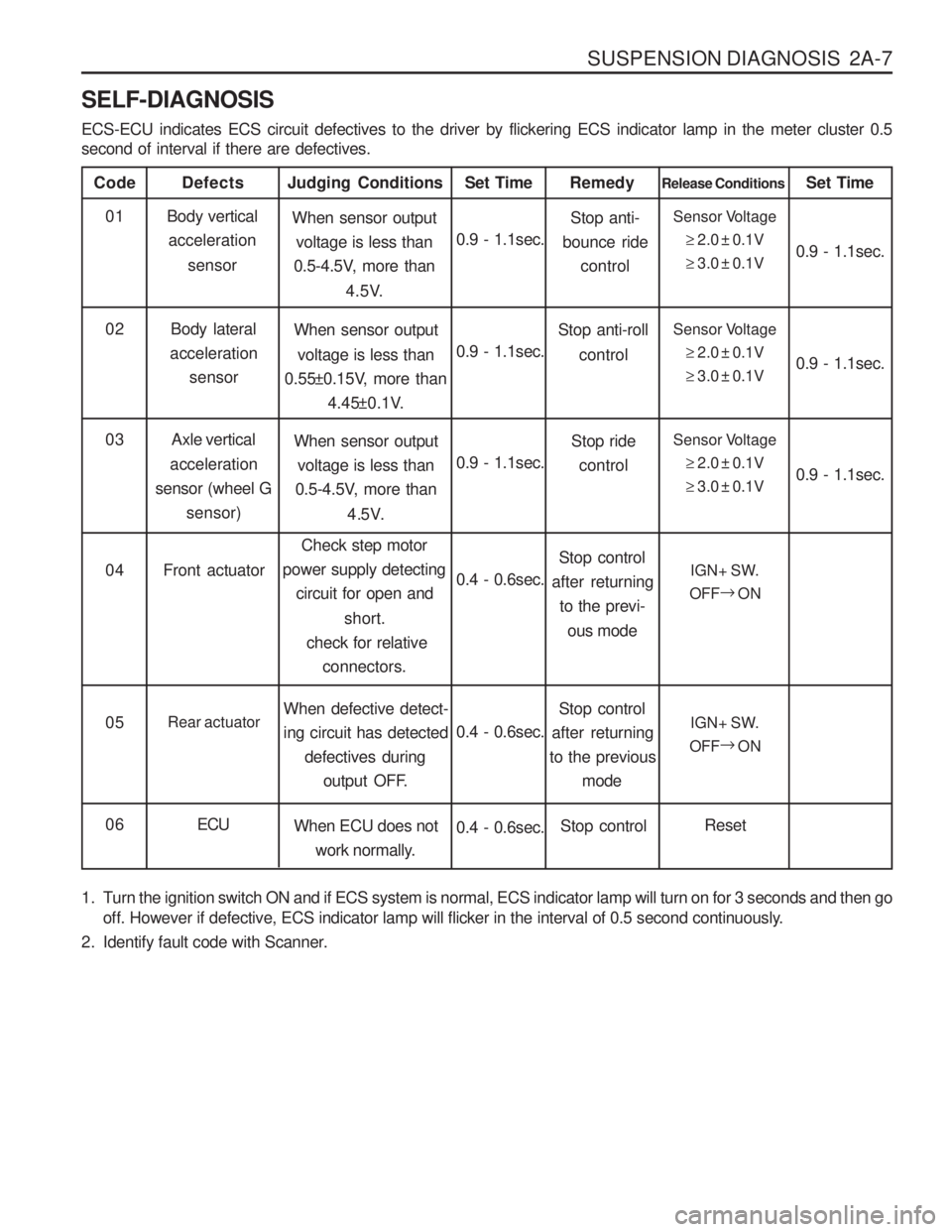
SUSPENSION DIAGNOSIS 2A-7
SELF-DIAGNOSIS ECS-ECU indicates ECS circuit defectives to the driver by flickering ECS indicator lamp in the meter cluster 0.5 second of interval if there are defectives.
Code
Body verticalacceleration
sensor
Defects
When sensor outputvoltage is less than
0.5-4.5V, more than
4.5V.
Judging Conditions01
0.9 - 1.1sec.Set TimeSensor Voltage
2.0 ± 0.1V
3.0 ± 0.1V
Release Conditions
0.9 - 1.1sec.
Set Time
Body lateral
acceleration sensor When sensor output
voltage is less than
0.55±0.15V, more than
4.45±0.1V.
02
0.9 - 1.1sec.Sensor Voltage
2.0 ± 0.1V
3.0 ± 0.1V 0.9 - 1.1sec.
Stop anti-
bounce ride
control
Remedy
Stop anti-roll control
Axle vertical
acceleration
sensor (wheel G sensor) When sensor output
voltage is less than
0.5-4.5V, more than
4.5V.
03
0.9 - 1.1sec.Sensor Voltage
2.0 ± 0.1V
3.0 ± 0.1V 0.9 - 1.1sec.
Stop ride
control
Front actuator Check step motor
power supply detecting
circuit for open and
short.
check for relative connectors.
04
0.4 - 0.6sec.IGN+ SW.
OFF
ON
Stop control
after returning to the previ-
ous mode
Rear actuator When defective detect- ing circuit has detected
defectives during
output OFF.
05
0.4 - 0.6sec.IGN+ SW.
OFF
ON
Stop control
after returning
to the previous
mode
ECU When ECU does not
work normally.
06
0.4 - 0.6sec.Reset
Stop control
1. Turn the ignition switch ON and if ECS system is normal, ECS indicator lamp will turn on for 3 seconds and then go off. However if defective, ECS indicator lamp will flicker in the interval of 0.5 second continuously.
2. Identify fault code with Scanner.