check engine SSANGYONG MUSSO 2003 Manual PDF
[x] Cancel search | Manufacturer: SSANGYONG, Model Year: 2003, Model line: MUSSO, Model: SSANGYONG MUSSO 2003Pages: 1574, PDF Size: 26.41 MB
Page 356 of 1574
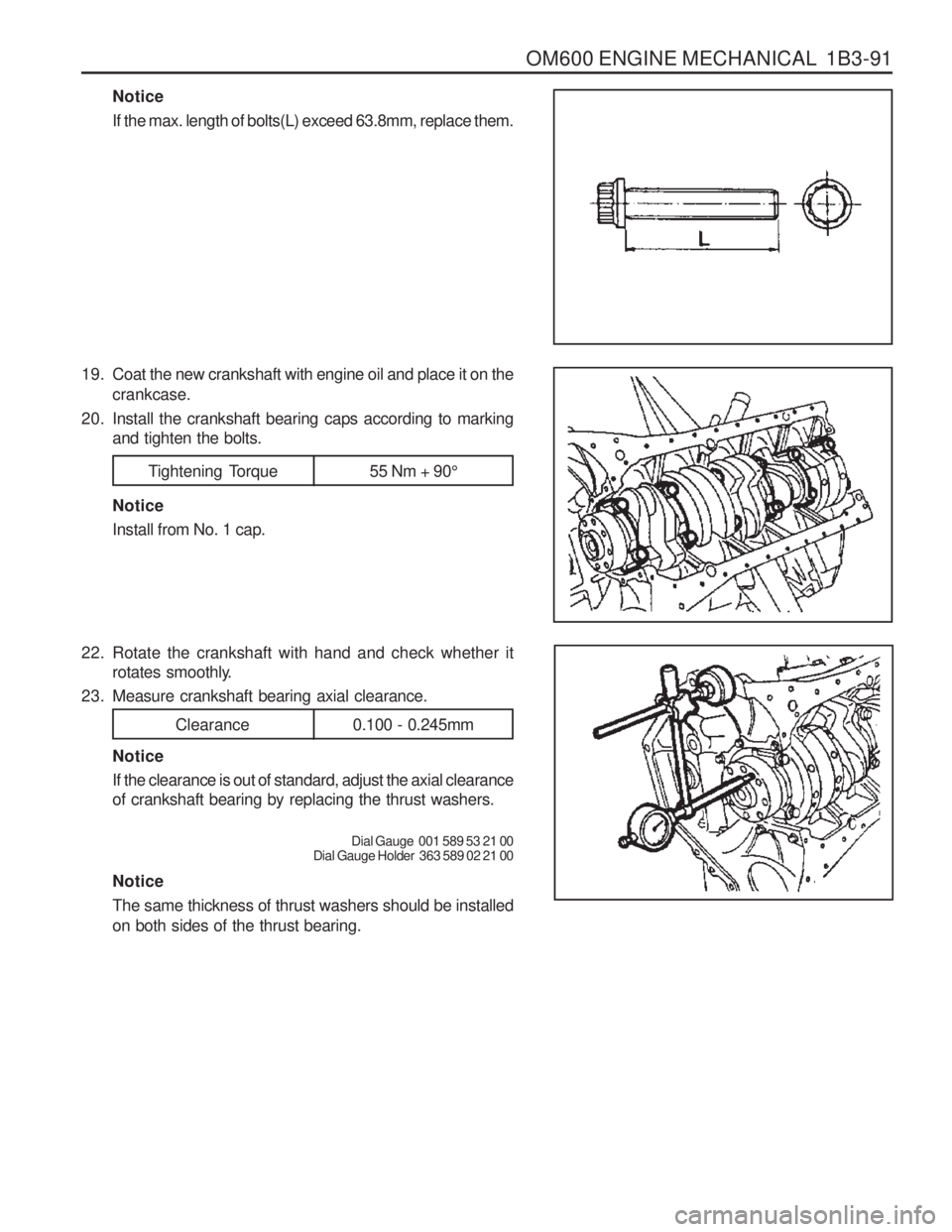
OM600 ENGINE MECHANICAL 1B3-91
Notice If the max. length of bolts(L) exceed 63.8mm, replace them.
19. Coat the new crankshaft with engine oil and place it on the crankcase.
20. Install the crankshaft bearing caps according to marking and tighten the bolts.
Tightening Torque 55 Nm + 90 °
Notice Install from No. 1 cap.
22. Rotate the crankshaft with hand and check whether it rotates smoothly.
23. Measure crankshaft bearing axial clearance.
Clearance 0.100 - 0.245mm
Notice If the clearance is out of standard, adjust the axial clearance of crankshaft bearing by replacing the thrust washers.
Dial Gauge 001 589 53 21 00
Dial Gauge Holder 363 589 02 21 00
Notice The same thickness of thrust washers should be installed on both sides of the thrust bearing.
Page 357 of 1574
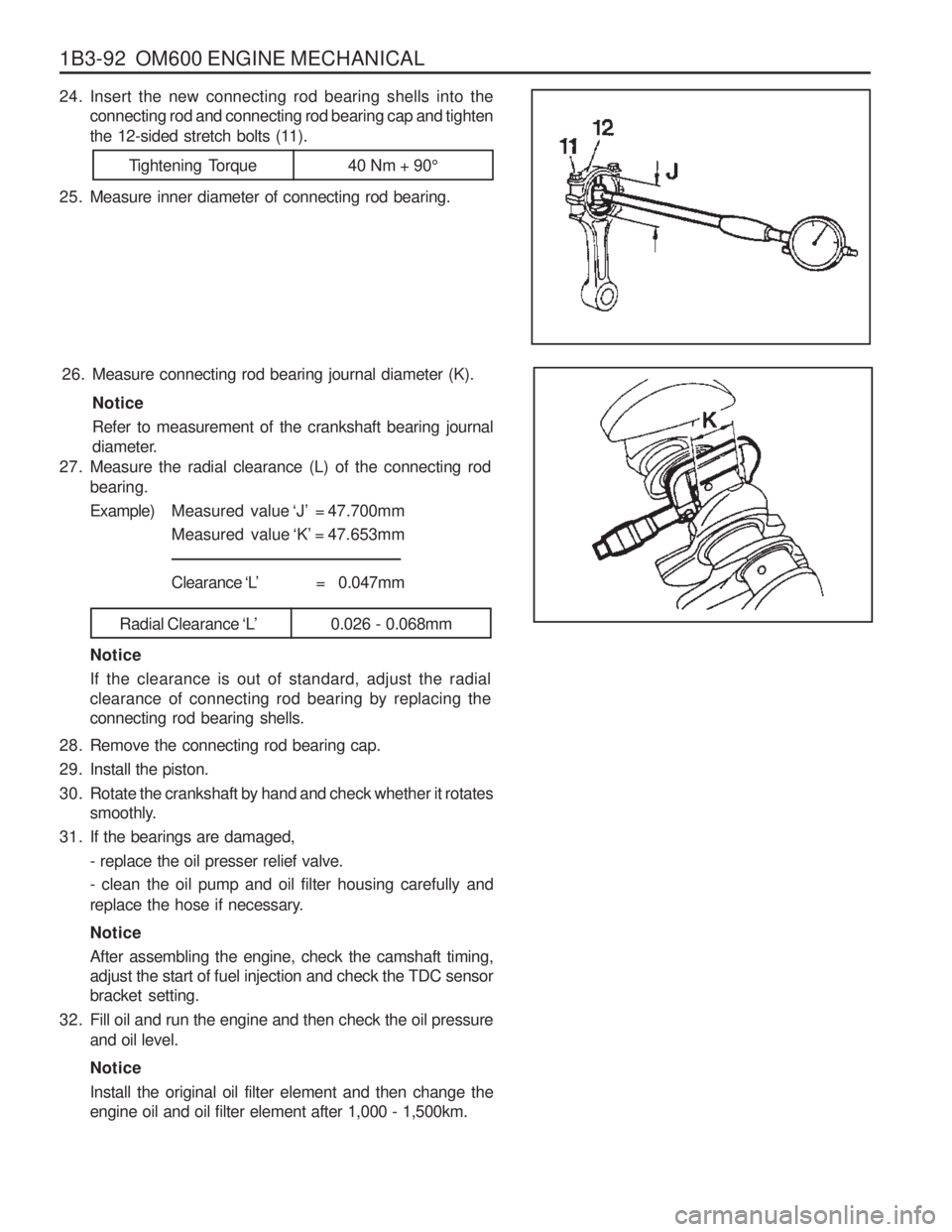
1B3-92 OM600 ENGINE MECHANICAL
28. Remove the connecting rod bearing cap.
29. Install the piston.
30. Rotate the crankshaft by hand and check whether it rotatessmoothly.
31. If the bearings are damaged,
- replace the oil presser relief valve. - clean the oil pump and oil filter housing carefully and
replace the hose if necessary. Notice After assembling the engine, check the camshaft timing, adjust the start of fuel injection and check the TDC sensorbracket setting.
32. Fill oil and run the engine and then check the oil pressure and oil level. Notice Install the original oil filter element and then change the engine oil and oil filter element after 1,000 - 1,500km.
27. Measure the radial clearance (L) of the connecting rod
bearing. Example) Measured value ‘J’ = 47.700mm
Measured value ‘K’ = 47.653mm
Clearance ‘L’ = 0.047mm
Radial Clearance ‘L’0.026 - 0.068mm
Notice If the clearance is out of standard, adjust the radial clearance of connecting rod bearing by replacing theconnecting rod bearing shells.
26. Measure connecting rod bearing journal diameter (K).
Notice Refer to measurement of the crankshaft bearing journal
diameter.
24. Insert the new connecting rod bearing shells into theconnecting rod and connecting rod bearing cap and tighten
the 12-sided stretch bolts (11).
25. Measure inner diameter of connecting rod bearing.
Tightening Torque 40 Nm + 90 °
Page 358 of 1574
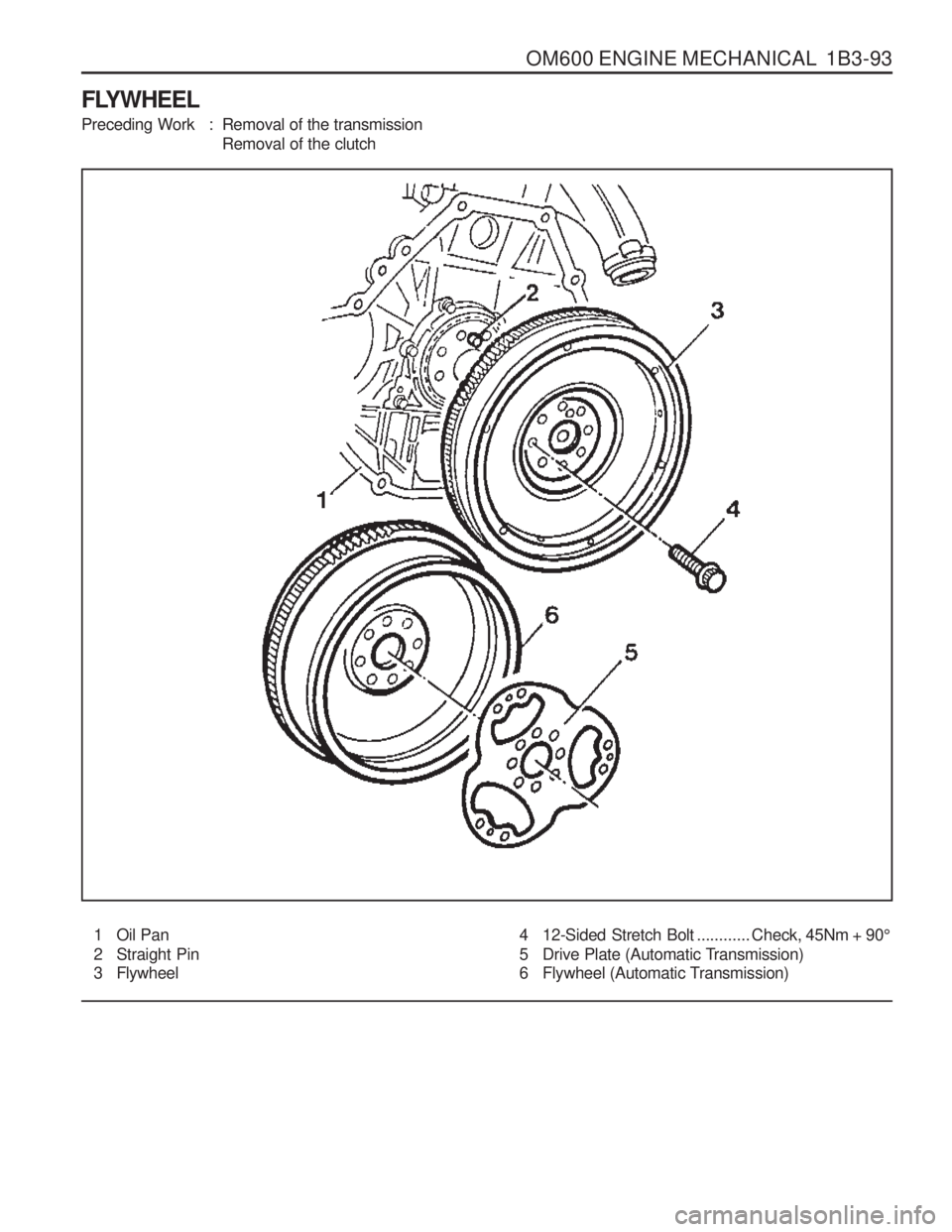
OM600 ENGINE MECHANICAL 1B3-93
FLYWHEEL
Preceding Work : Removal of the transmissionRemoval of the clutch
1 Oil Pan
2 Straight Pin
3 Flywheel 4 12-Sided Stretch Bolt
............ Check, 45Nm + 90 °
5 Drive Plate (Automatic Transmission)
6 Flywheel (Automatic Transmission)
Page 366 of 1574
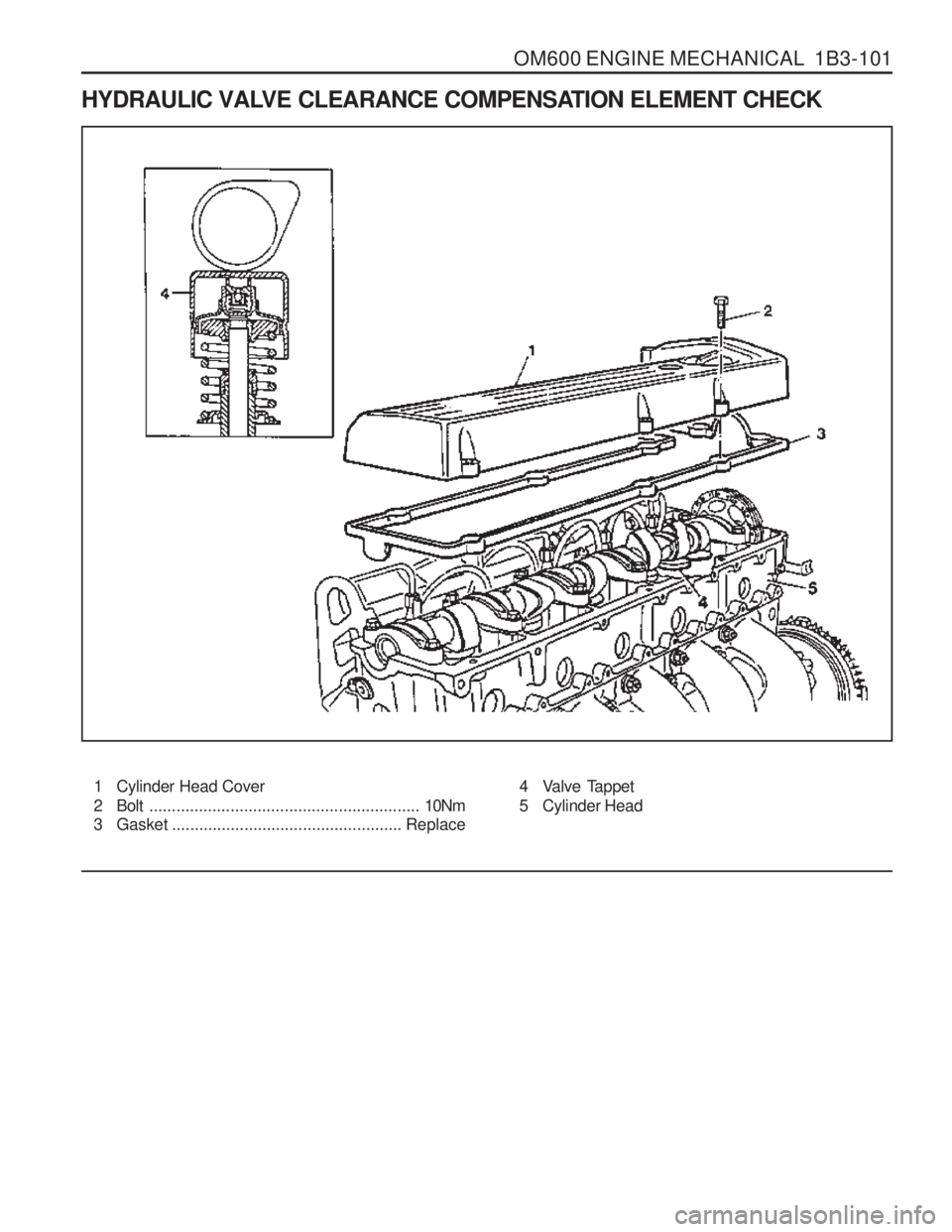
OM600 ENGINE MECHANICAL 1B3-101
HYDRAULIC VALVE CLEARANCE COMPENSATION ELEMENT CHECK
1 Cylinder Head Cover
2 Bolt............................................................ 10Nm
3 Gasket ................................................... Replace4 Valve Tappet
5 Cylinder Head
Page 367 of 1574
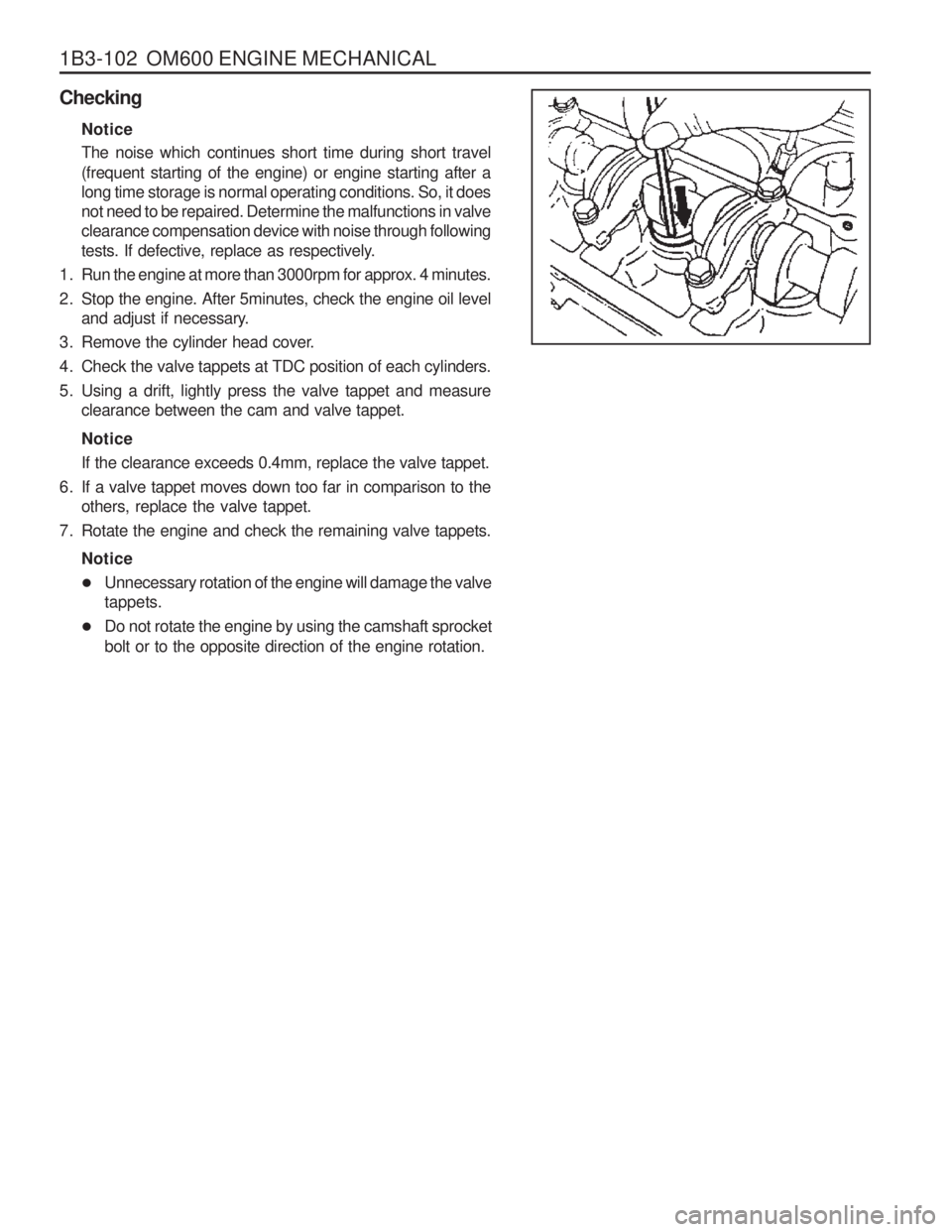
1B3-102 OM600 ENGINE MECHANICAL
CheckingNotice The noise which continues short time during short travel (frequent starting of the engine) or engine starting after a long time storage is normal operating conditions. So, it doesnot need to be repaired. Determine the malfunctions in valveclearance compensation device with noise through following
tests. If defective, replace as respectively.
1. Run the engine at more than 3000rpm for approx. 4 minutes.
2. Stop the engine. After 5minutes, check the engine oil level and adjust if necessary.
3. Remove the cylinder head cover.
4. Check the valve tappets at TDC position of each cylinders.
5. Using a drift, lightly press the valve tappet and measure clearance between the cam and valve tappet. Notice If the clearance exceeds 0.4mm, replace the valve tappet.
6. If a valve tappet moves down too far in comparison to the others, replace the valve tappet.
7. Rotate the engine and check the remaining valve tappets.
Notice
Unnecessary rotation of the engine will damage the valve tappets.
Do not rotate the engine by using the camshaft sprocket bolt or to the opposite direction of the engine rotation.
Page 369 of 1574
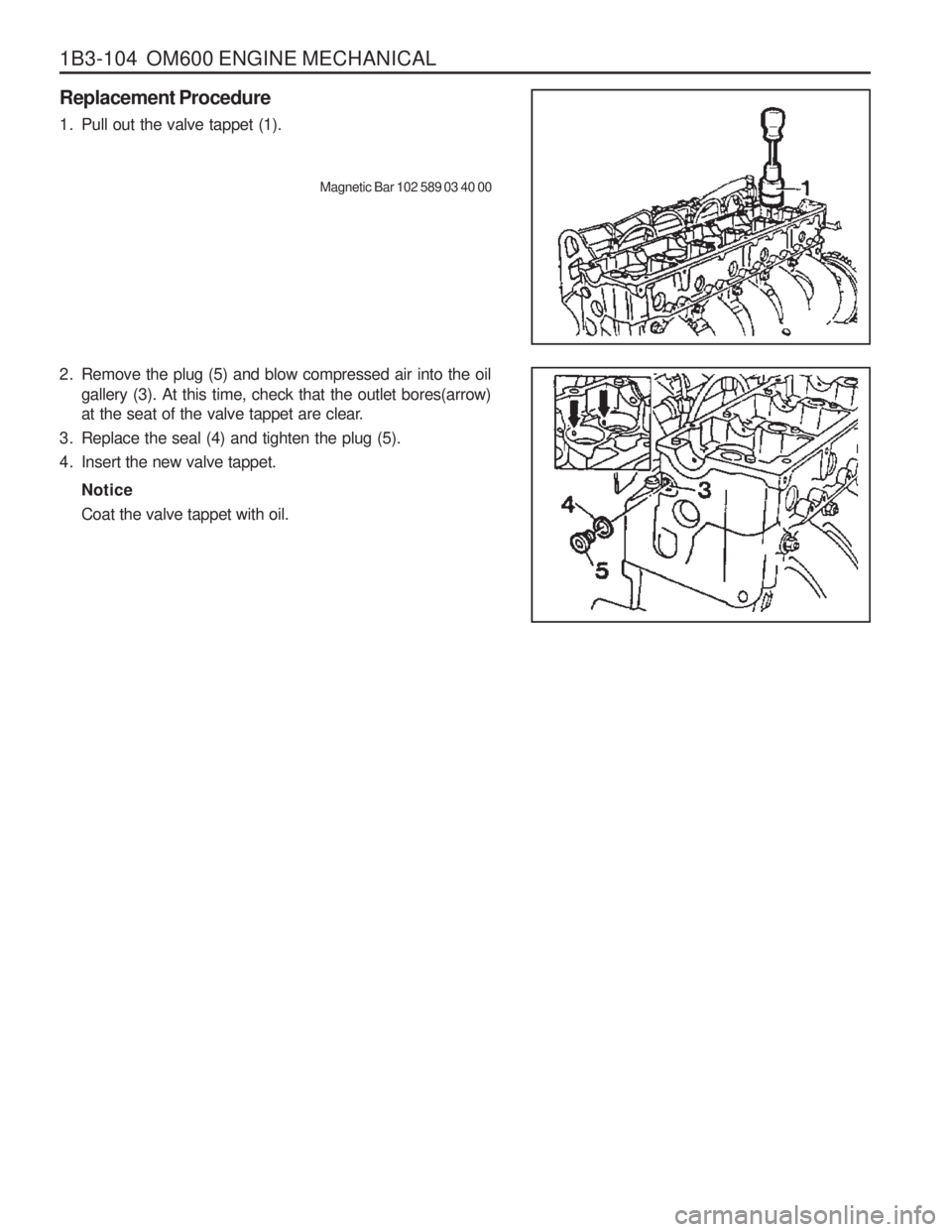
1B3-104 OM600 ENGINE MECHANICAL
Replacement Procedure
1. Pull out the valve tappet (1).Magnetic Bar 102 589 03 40 00
2. Remove the plug (5) and blow compressed air into the oil gallery (3). At this time, check that the outlet bores(arrow)
at the seat of the valve tappet are clear.
3. Replace the seal (4) and tighten the plug (5).
4. Insert the new valve tappet.
NoticeCoat the valve tappet with oil.
Page 370 of 1574
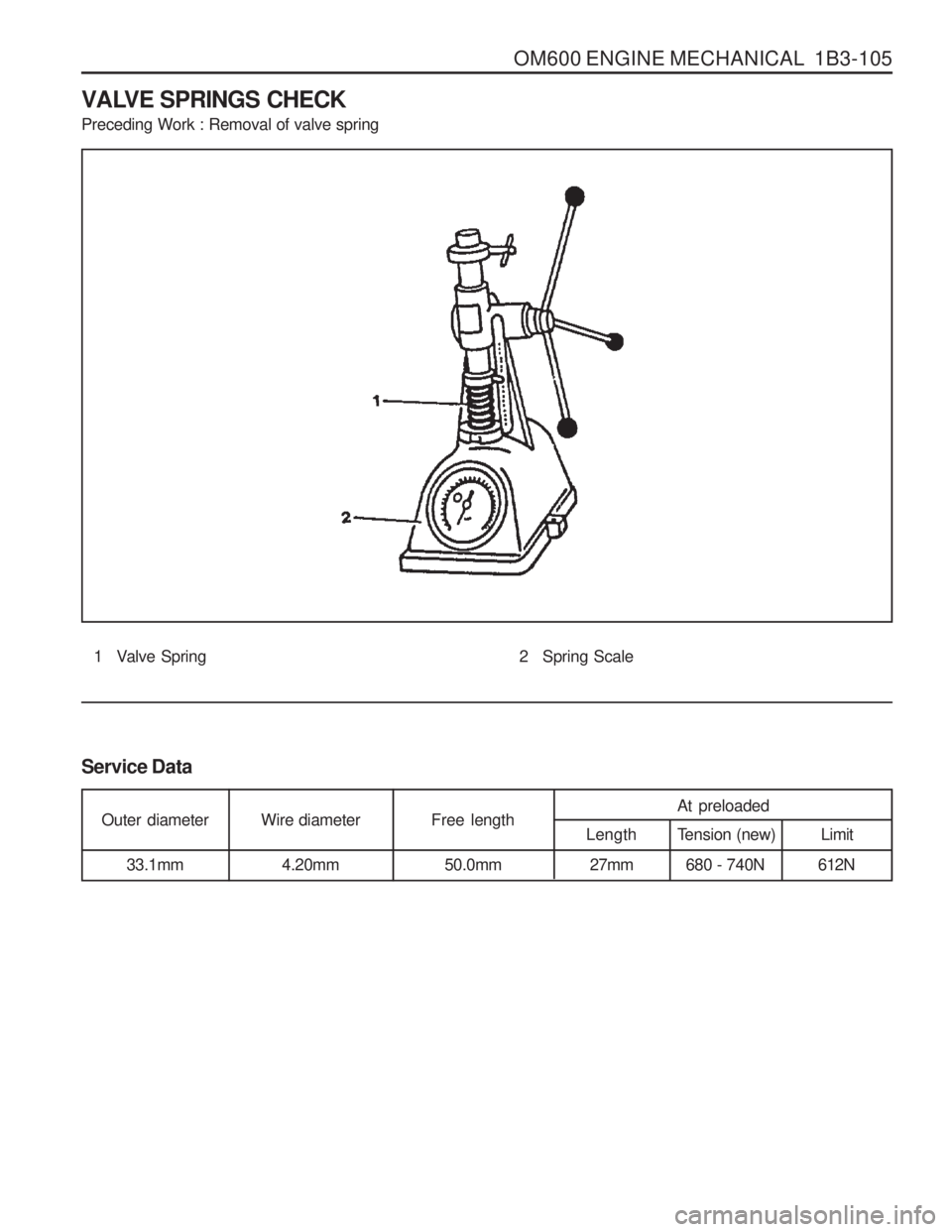
OM600 ENGINE MECHANICAL 1B3-105
VALVE SPRINGS CHECK Preceding Work : Removal of valve spring
1 Valve Spring
Service Data
Outer diameter33.1mm Wire diameter
4.20mm Free length
50.0mm At preloaded
Length Tension (new)
680 - 740N
27mm Limit
612N
2 Spring Scale
Page 371 of 1574
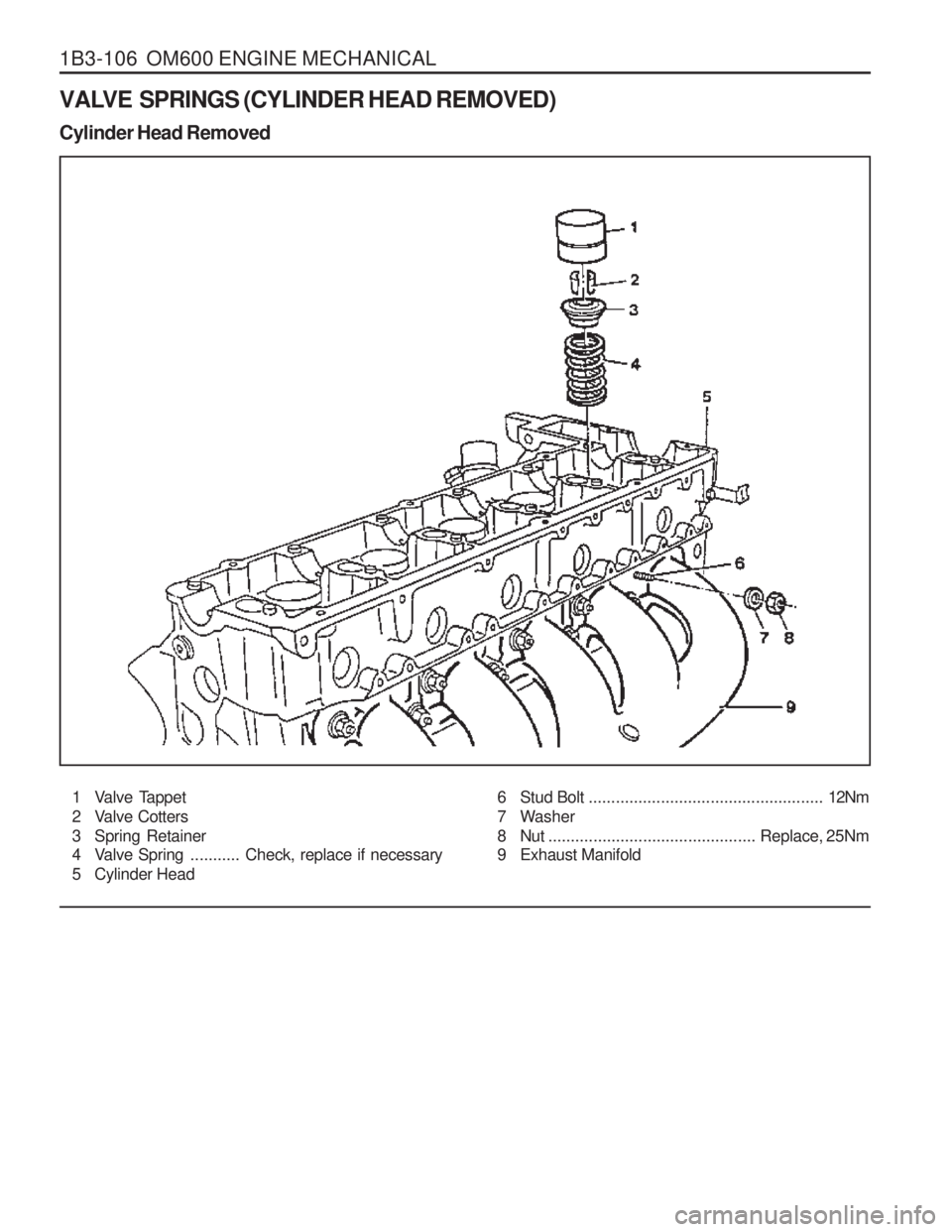
1B3-106 OM600 ENGINE MECHANICAL
VALVE SPRINGS (CYLINDER HEAD REMOVED) Cylinder Head Removed1 Valve Tappet
2 Valve Cotters
3 Spring Retainer
4 Valve Spring ...........Check, replace if necessary
5 Cylinder Head
6 Stud Bolt .................................................... 12Nm
7 Washer
8 Nut .............................................. Replace, 25Nm
9 Exhaust Manifold
Page 372 of 1574
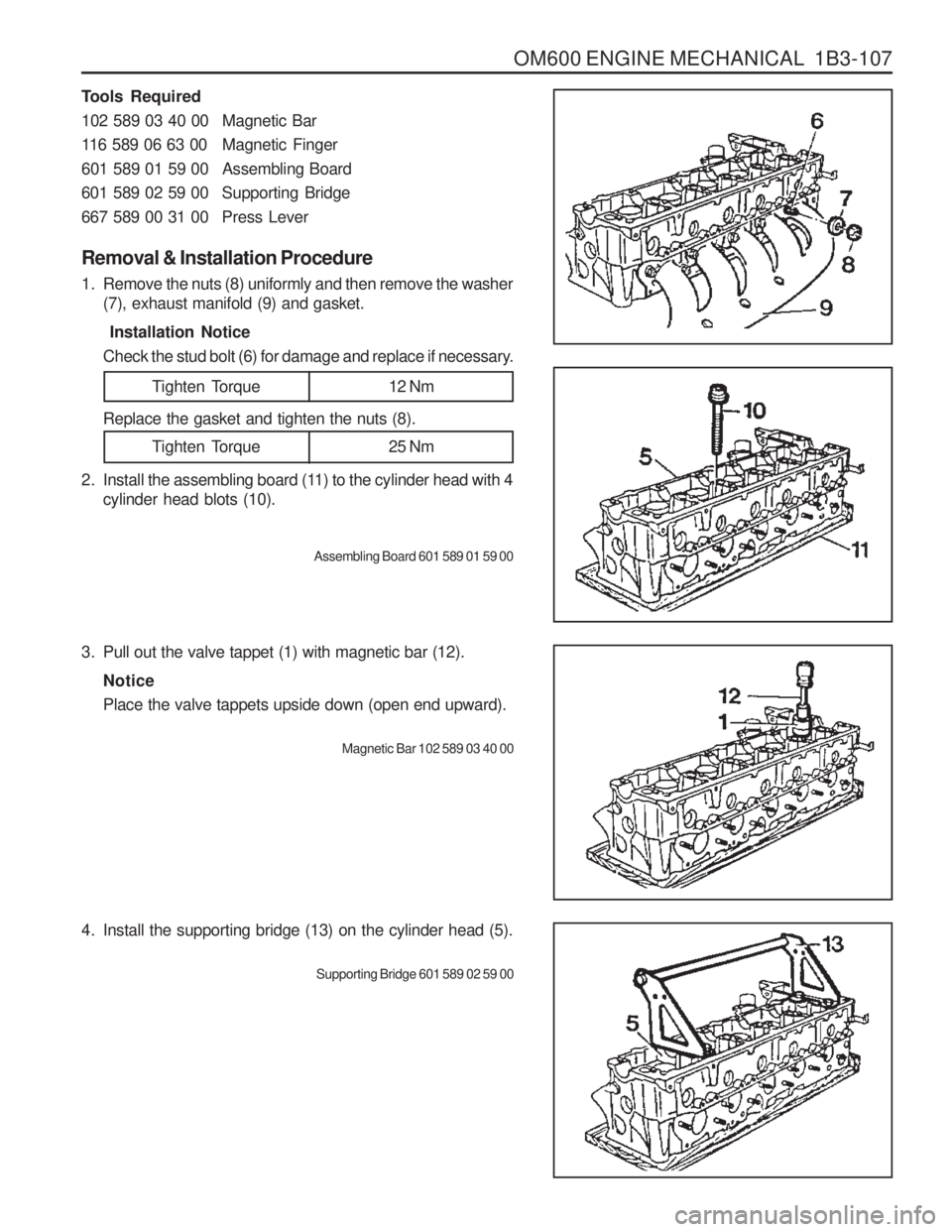
OM600 ENGINE MECHANICAL 1B3-107
Removal & Installation Procedure
1. Remove the nuts (8) uniformly and then remove the washer(7), exhaust manifold (9) and gasket. Installation Notice
Check the stud bolt (6) for damage and replace if necessary.
Tighten Torque 12 Nm
Tighten Torque 25 Nm
Tools Required
102 589 03 40 00 Magnetic Bar
116 589 06 63 00 Magnetic Finger
601 589 01 59 00 Assembling Board
601 589 02 59 00 Supporting Bridge
667 589 00 31 00 Press Lever
Replace the gasket and tighten the nuts (8).
2. Install the assembling board (11) to the cylinder head with 4 cylinder head blots (10).
Assembling Board 601 589 01 59 00
3. Pull out the valve tappet (1) with magnetic bar (12). NoticePlace the valve tappets upside down (open end upward).
Magnetic Bar 102 589 03 40 00
4. Install the supporting bridge (13) on the cylinder head (5).Supporting Bridge 601 589 02 59 00
Page 373 of 1574
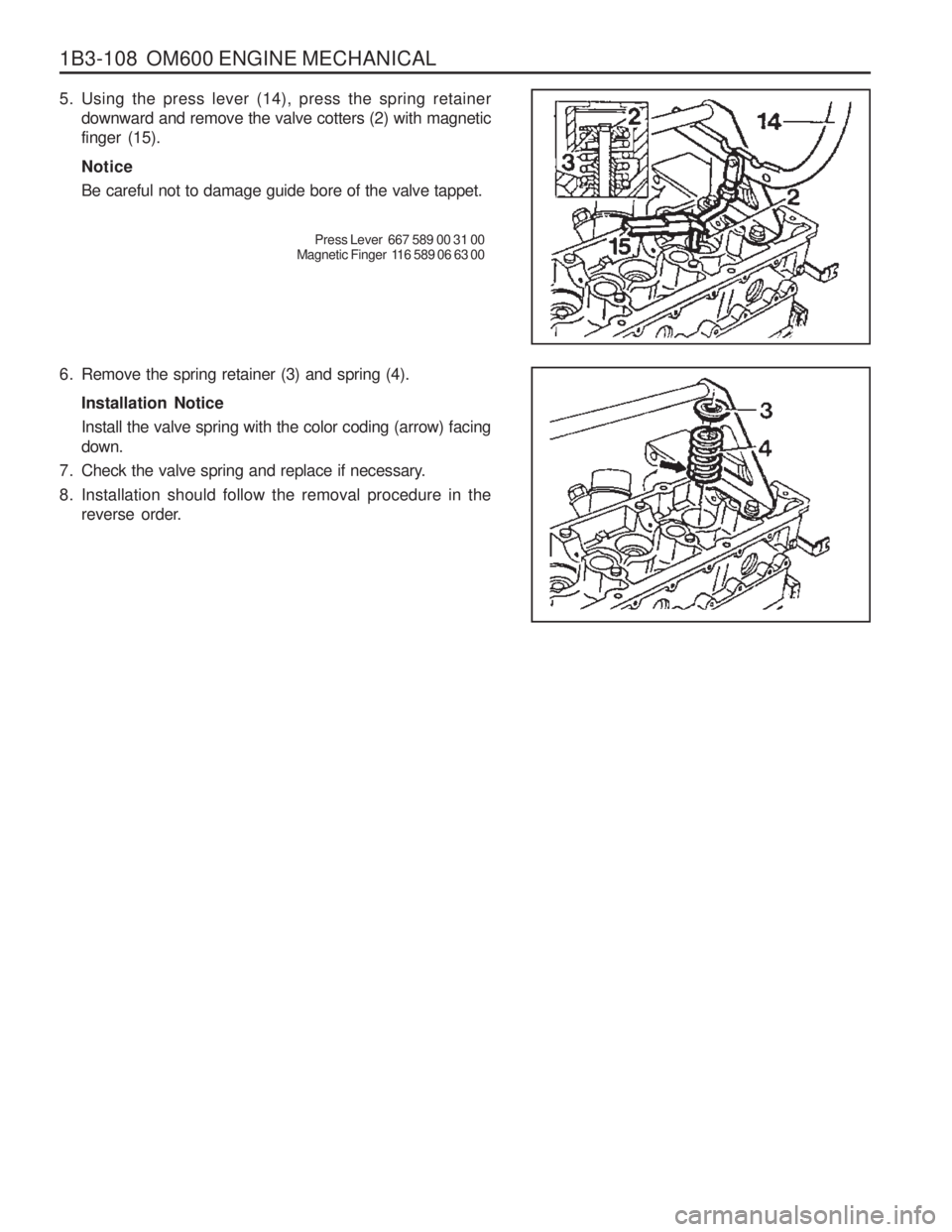
1B3-108 OM600 ENGINE MECHANICAL
5. Using the press lever (14), press the spring retainerdownward and remove the valve cotters (2) with magnetic finger (15). Notice Be careful not to damage guide bore of the valve tappet.
Press Lever 667 589 00 31 00
Magnetic Finger 116 589 06 63 00
6. Remove the spring retainer (3) and spring (4). Installation NoticeInstall the valve spring with the color coding (arrow) facing down.
7. Check the valve spring and replace if necessary.
8. Installation should follow the removal procedure in the reverse order.