SSANGYONG NEW ACTYON SPORTS 2013 Service Manual
NEW ACTYON SPORTS 2013
SSANGYONG
SSANGYONG
https://www.carmanualsonline.info/img/67/57512/w960_57512-0.png
SSANGYONG NEW ACTYON SPORTS 2013 Service Manual
Trending: cooling, Cylinder head bolt, air condition, key, check engine light, flat tire, window
Page 251 of 751
15-510000-00
3) Input/Output for CAN communication
Page 252 of 751
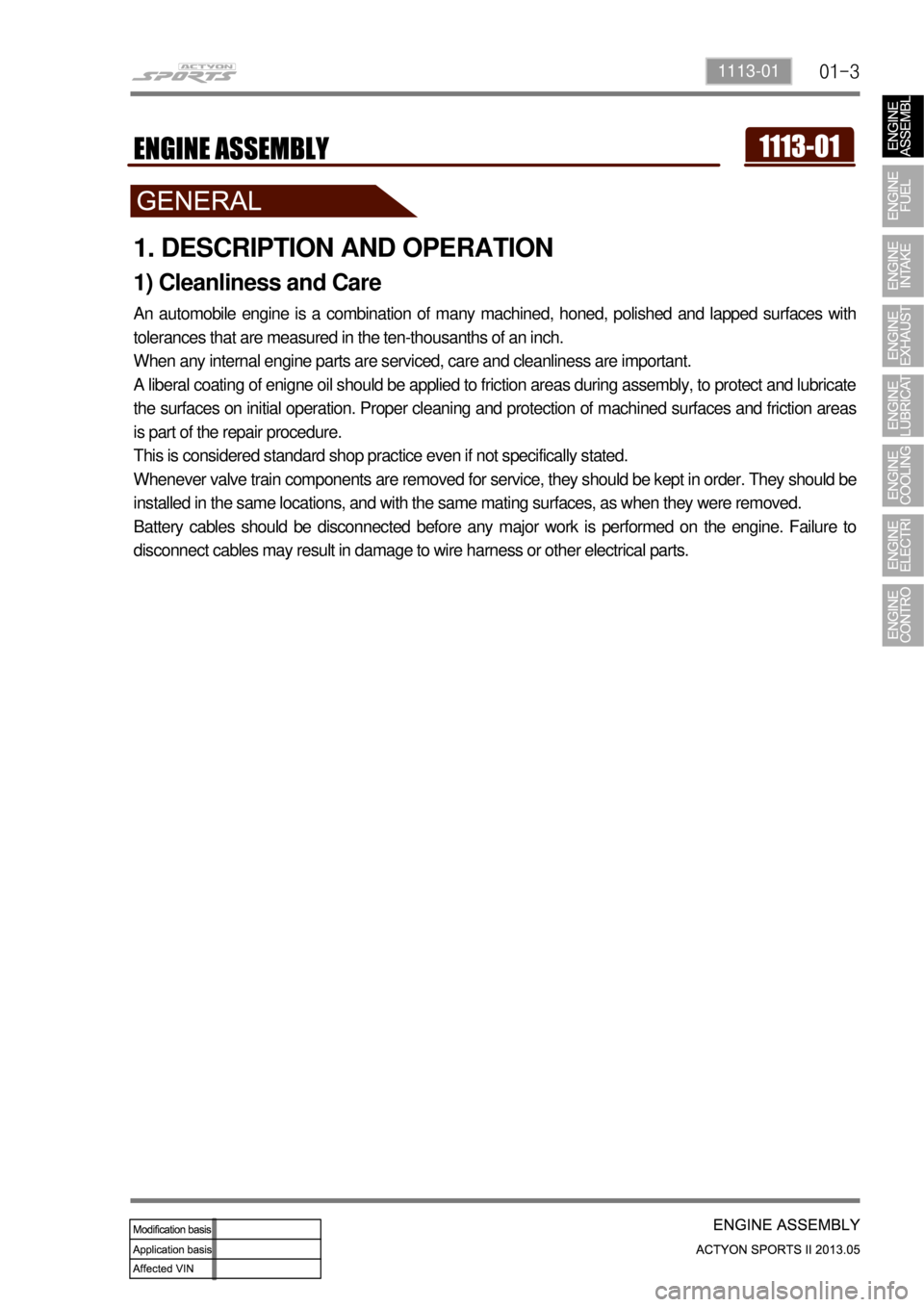
01-31113-01
1. DESCRIPTION AND OPERATION
1) Cleanliness and Care
An automobile engine is a combination of many machined, honed, polished and lapped surfaces with
tolerances that are measured in the ten-thousanths of an inch.
When any internal engine parts are serviced, care and cleanliness are important.
A liberal coating of enigne oil should be applied to friction areas during assembly, to protect and lubricate
the surfaces on initial operation. Proper cleaning and protection of machined surfaces and friction areas
is part of the repair procedure.
This is considered standard shop practice even if not specifically stated.
Whenever valve train components are removed for service, they should be kept in order. They should be
installed in the same locations, and with the same mating surfaces, as when they were removed.
Battery cables should be disconnected before any major work is performed on the engine. Failure to
disconnect cables may result in damage to wire harness or other electrical parts.
Page 253 of 751
01-4
2) On-engine Service
Disconnect the negative battery cable before removing or installing any electrical unit, or when a
tool or equipment could easily come in contact with exposed electrical terminals.
Disconnecting this cable will help prevent personal injury and damage to the vehicle. The ignition
must also be in LOCK unless otherwise noted. -
Any time the air cleaner is removed, the intake opening should be covered. This will protect
against accidental entrance of foreign material, which could follow the intake passage into the
cylinder and cause extensive damage when the engine is started. -
Page 254 of 751
01-51113-01
Front View
Rear View
2. G23D ENGINE ASSEMBLY
Page 255 of 751
01-6
LH Side View
RH Side View
Page 256 of 751
01-71113-01
3. G23D ENGINE STRUCTURE
Front View
Side View
Page 257 of 751
01-8
Front View ▶
NO. FUNCTION NO. FUNCTION
1 HFM Sensor 12 Intake Manifold
2 Intake Air Duct 13 Cylinder Head
3 Cylinder Head Cover 14 Exhaust Manifold
4 Ignition Coi 15 Dipstick Guide Tube and Gauge
5 Spark Plug Connector 16 Connecting Rod
6 Fuel Distributor 17 Crankshaft
7 Injector 18 Engine Mounting Bracket
8 Exhaust Camshaft 19 Starter
9 Intake Camshaft 20 Crankcase
10 Valve Tappet 21 Oil Pump Sprocket
11 Intake Valve 22 Oil Pan
NO. FUNCTION NO. FUNCTION
23 Camshaft Adjuster 29 Oil Pump Drive Chain
24 Oil Filler Cap 30 Oil Strainer
25 Engine Hanger Bracket 31 Oil Pump
26 Cooling Fan and Viscous Clutch 32 Ring Gear and Flywheel of Drive Plate
27 Oil Filter 33 Piston
28 Timing Chain
Side View ▶
Page 258 of 751
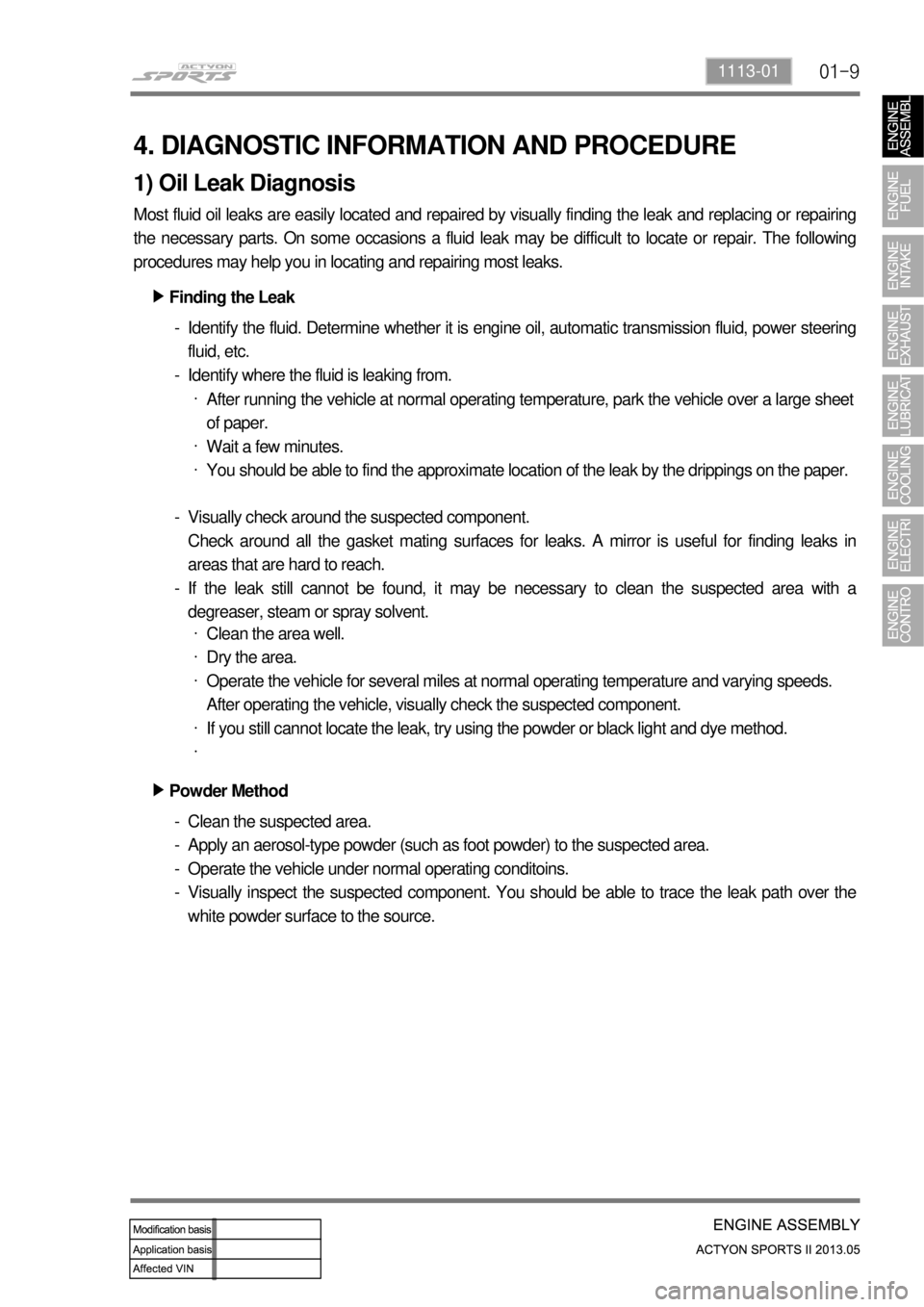
01-91113-01
4. DIAGNOSTIC INFORMATION AND PROCEDURE
1) Oil Leak Diagnosis
Most fluid oil leaks are easily located and repaired by visually finding the leak and replacing or repairing
the necessary parts. On some occasions a fluid leak may be difficult to locate or repair. The following
procedures may help you in locating and repairing most leaks.
Finding the Leak ▶
Identify the fluid. Determine whether it is engine oil, automatic transmission fluid, power steering
fluid, etc.
Identify where the fluid is leaking from. -
-
After running the vehicle at normal operating temperature, park the vehicle over a large sheet
of paper.
Wait a few minutes.
You should be able to find the approximate location of the leak by the drippings on the paper. ·
·
·
Visually check around the suspected component.
Check around all the gasket mating surfaces for leaks. A mirror is useful for finding leaks in
areas that are hard to reach.
If the leak still cannot be found, it may be necessary to clean the suspected area with a
degreaser, steam or spray solvent. -
-
Clean the area well.
Dry the area.
Operate the vehicle for several miles at normal operating temperature and varying speeds.
After operating the vehicle, visually check the suspected component.
If you still cannot locate the leak, try using the powder or black light and dye method. ·
·
·
·
·
Clean the suspected area.
Apply an aerosol-type powder (such as foot powder) to the suspected area.
Operate the vehicle under normal operating conditoins.
Visually inspect the suspected component. You should be able to trace the leak path over the
white powder surface to the source. -
-
-
- Powder Method ▶
Page 259 of 751
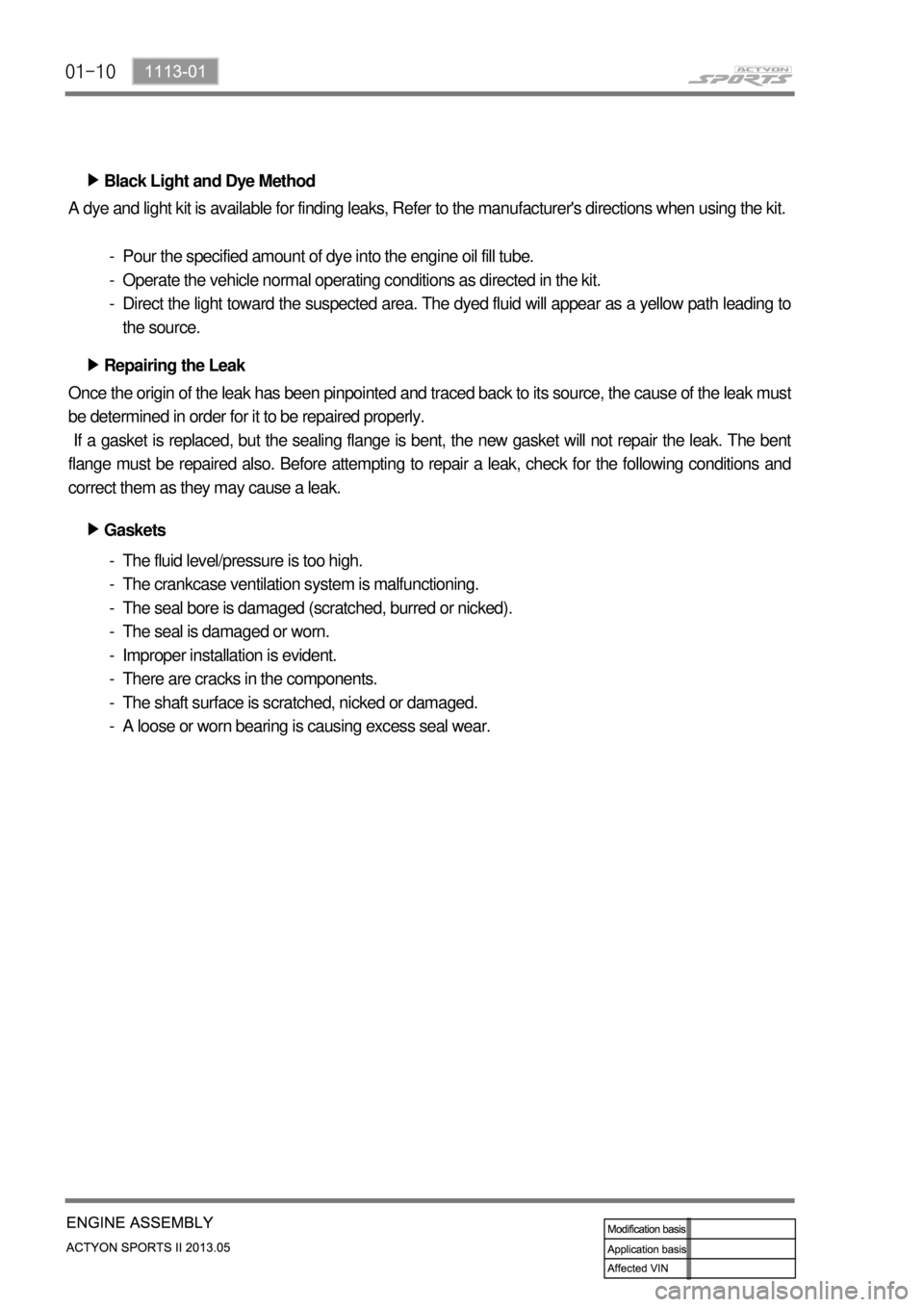
01-10
Black Light and Dye Method ▶
A dye and light kit is available for finding leaks, Refer to the manufacturer's directions when using the kit.
Pour the specified amount of dye into the engine oil fill tube.
Operate the vehicle normal operating conditions as directed in the kit.
Direct the light toward the suspected area. The dyed fluid will appear as a yellow path leading to
the source. -
-
-
Once the origin of the leak has been pinpointed and traced back to its source, the cause of the leak must
be determined in order for it to be repaired properly.
If a gasket is replaced, but the sealing flange is bent, the new gasket will not repair the leak. The bent
flange must be repaired also. Before attempting to repair a leak, check for the following conditions and
correct them as they may cause a leak.Repairing the Leak ▶
Gaskets ▶
The fluid level/pressure is too high.
The crankcase ventilation system is malfunctioning.
The seal bore is damaged (scratched, burred or nicked).
The seal is damaged or worn.
Improper installation is evident.
There are cracks in the components.
The shaft surface is scratched, nicked or damaged.
A loose or worn bearing is causing excess seal wear. -
-
-
-
-
-
-
-
Page 260 of 751
01-111113-01
2) Compression Pressure Test
Standard Service Data ▶
A9912 0012B (001 589 76 21 00) Compression Pressure Tester -
Measuring Procedure ▶
Warm the engine up to normal operating temperature.
Remove the spark plugs using the spark plug wrench.
Place the diagram sheet to compression pressure tester A9912 0012B (001 589 76 21 00).
Connect the adaptor to compression pressure tester A9912 0012B (001 589 76 21 00) and
install it into the spark plug hole.
Crank the engine approx. eight revolutions by using the start motor.
Compare the measurements of compression pressure tester A9912 0012B (001 589 76 21 00)
with the specifications.
Measure the compression pressure of the other cylinders in the same way.
If measured value is not within the specifications, perform the cylinder pressure leakage test. -
-
-
-
-
-
-
-
Discharge the combustion residues in the cylinders before testing the compression pressure.
Apply the parking brake before cranking the engine. -
-
Trending: key battery, coolant temperature, fuses, air suspension, wheel size, warning, trailer