air condition SSANGYONG RODIUS 2012 User Guide
[x] Cancel search | Manufacturer: SSANGYONG, Model Year: 2012, Model line: RODIUS, Model: SSANGYONG RODIUS 2012Pages: 715, PDF Size: 79.36 MB
Page 312 of 715
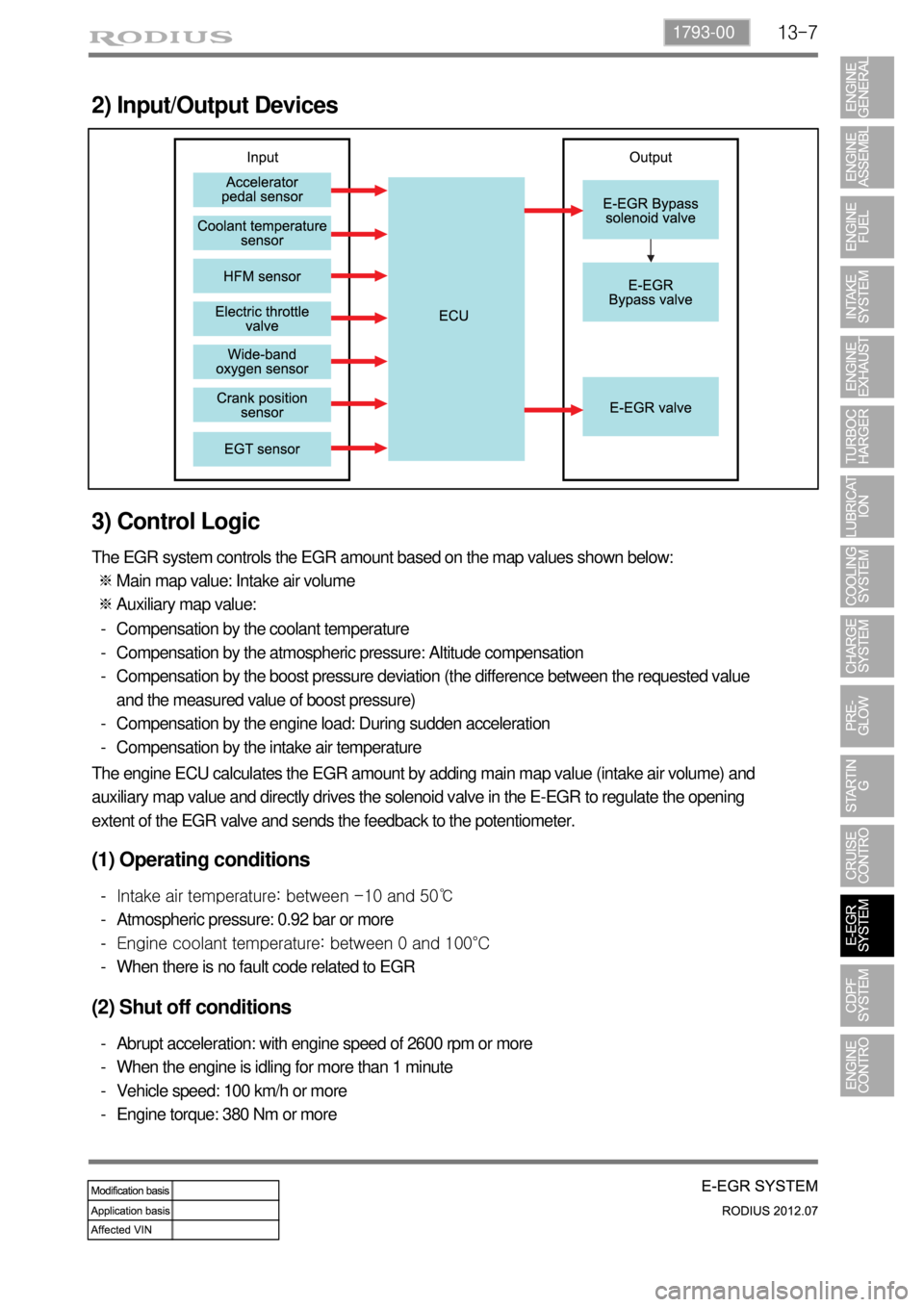
13-71793-00
2) Input/Output Devices
3) Control Logic
The EGR system controls the EGR amount based on the map values shown below:
Main map value: Intake air volume
Auxiliary map value: ※
※
Compensation by the coolant temperature
Compensation by the atmospheric pressure: Altitude compensation
Compensation by the boost pressure deviation (the difference between the requested value
and the measured value of boost pressure)
Compensation by the engine load: During sudden acceleration
Compensation by the intake air temperature -
-
-
-
-
The engine ECU calculates the EGR amount by adding main map value (intake air volume) and
auxiliary map value and directly drives the solenoid valve in the E-EGR to regulate the opening
extent of the EGR valve and sends the feedback to the potentiometer.
(1) Operating conditions
Intake air temperature: between -10 and 50℃
Atmospheric pressure: 0.92 bar or more
Engine coolant temperature: between 0 and 100°C
When there is no fault code related to EGR -
-
-
-
(2) Shut off conditions
Abrupt acceleration: with engine speed of 2600 rpm or more
When the engine is idling for more than 1 minute
Vehicle speed: 100 km/h or more
Engine torque: 380 Nm or more -
-
-
-
Page 314 of 715
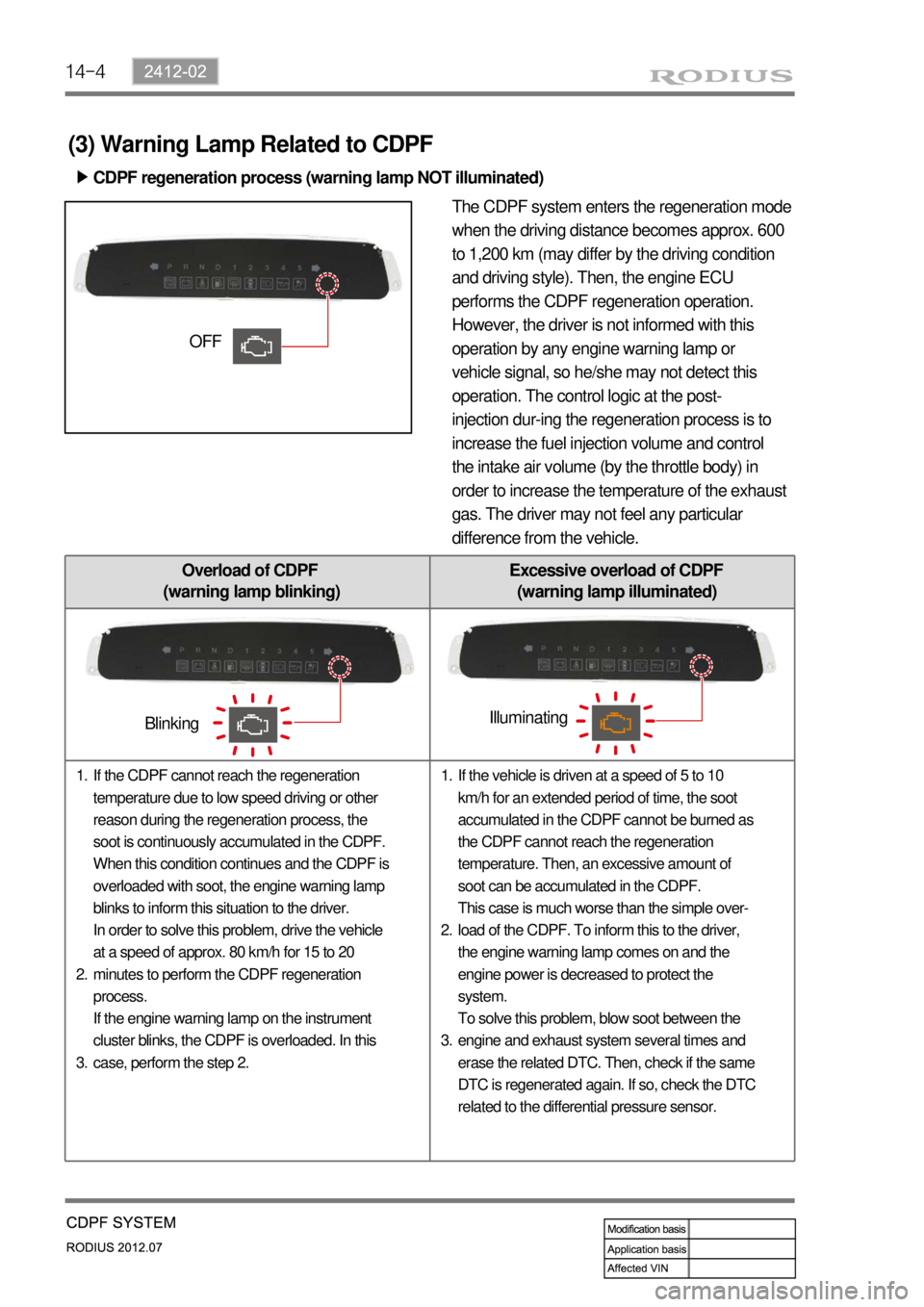
14-4
Overload of CDPF
(warning lamp blinking)Excessive overload of CDPF
(warning lamp illuminated)
(3) Warning Lamp Related to CDPF
CDPF regeneration process (warning lamp NOT illuminated) ▶
The CDPF system enters the regeneration mode
when the driving distance becomes approx. 600
to 1,200 km (may differ by the driving condition
and driving style). Then, the engine ECU
performs the CDPF regeneration operation.
However, the driver is not informed with this
operation by any engine warning lamp or
vehicle signal, so he/she may not detect this
operation. The control logic at the post-
injection dur-ing the regeneration process is to
increase the fuel injection volume and control
the intake air volume (by the throttle body) in
order to increase the temperature of the exhaust
gas. The driver may not feel any particular
difference from the vehicle.
If the CDPF cannot reach the regeneration
temperature due to low speed driving or other
reason during the regeneration process, the
soot is continuously accumulated in the CDPF.
When this condition continues and the CDPF is
overloaded with soot, the engine warning lamp
blinks to inform this situation to the driver.
In order to solve this problem, drive the vehicle
at a speed of approx. 80 km/h for 15 to 20
minutes to perform the CDPF regeneration
process.
If the engine warning lamp on the instrument
cluster blinks, the CDPF is overloaded. In this
case, perform the step 2. 1.
2.
3.If the vehicle is driven at a speed of 5 to 10
km/h for an extended period of time, the soot
accumulated in the CDPF cannot be burned as
the CDPF cannot reach the regeneration
temperature. Then, an excessive amount of
soot can be accumulated in the CDPF.
This case is much worse than the simple over-
load of the CDPF. To inform this to the driver,
the engine warning lamp comes on and the
engine power is decreased to protect the
system.
To solve this problem, blow soot between the
engine and exhaust system several times and
erase the related DTC. Then, check if the same
DTC is regenerated again. If so, check the DTC
related to the differential pressure sensor. 1.
2.
3.
OFF
BlinkingIlluminating
Page 328 of 715
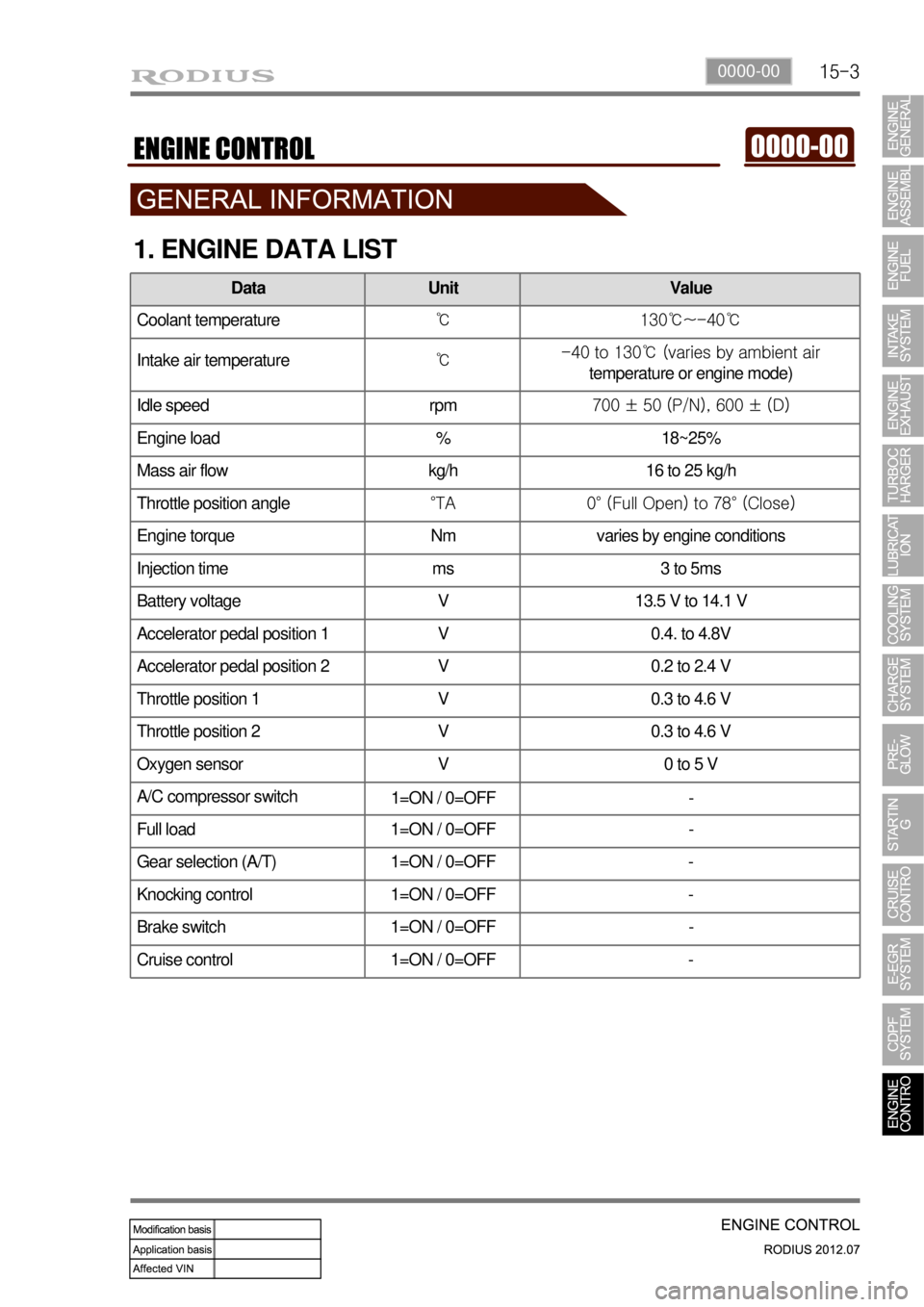
15-30000-00
1. ENGINE DATA LIST
Data Unit Value
Coolant temperature℃ 130℃~-40℃
Intake air temperature℃ -40 to 130℃ (varies by ambient air
temperature or engine mode)
Idle speed rpm 700 ± 50 (P/N), 600 ± (D)
Engine load % 18~25%
Mass air flow kg/h 16 to 25 kg/h
Throttle position angle°TA 0° (Full Open) to 78° (Close)
Engine torque Nm varies by engine conditions
Injection time ms 3 to 5ms
Battery voltage V 13.5 V to 14.1 V
Accelerator pedal position 1 V 0.4. to 4.8V
Accelerator pedal position 2 V 0.2 to 2.4 V
Throttle position 1 V 0.3 to 4.6 V
Throttle position 2 V 0.3 to 4.6 V
Oxygen sensor V 0 to 5 V
A/C compressor switch
1=ON / 0=OFF -
Full load 1=ON / 0=OFF -
Gear selection (A/T) 1=ON / 0=OFF -
Knocking control 1=ON / 0=OFF -
Brake switch 1=ON / 0=OFF -
Cruise control 1=ON / 0=OFF -
Page 338 of 715
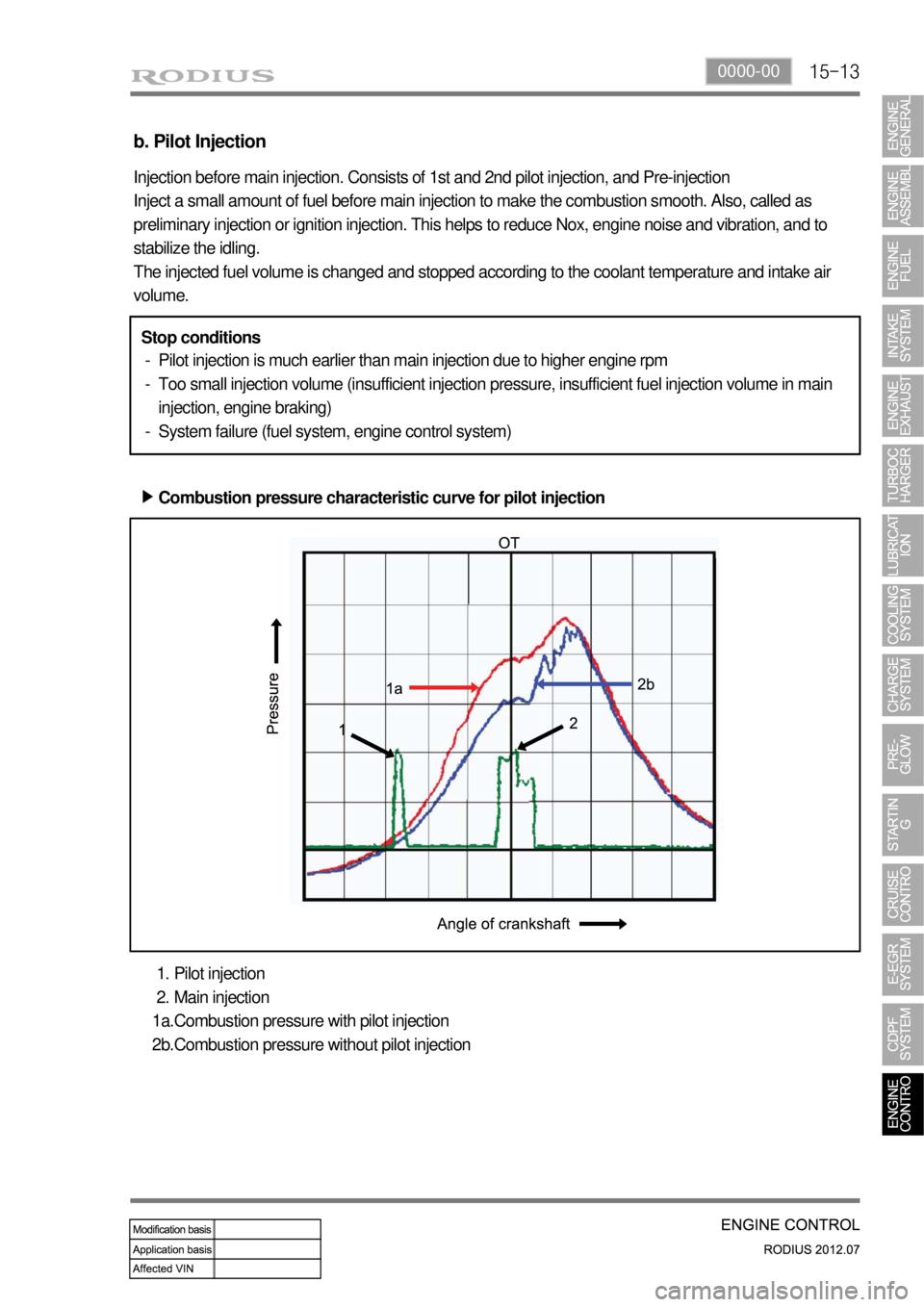
15-130000-00
b. Pilot Injection
Injection before main injection. Consists of 1st and 2nd pilot injection, and Pre-injection
Inject a small amount of fuel before main injection to make the combustion smooth. Also, called as
preliminary injection or ignition injection. This helps to reduce Nox, engine noise and vibration, and to
stabilize the idling.
The injected fuel volume is changed and stopped according to the coolant temperature and intake air
volume.
Pilot injection is much earlier than main injection due to higher engine rpm
Too small injection volume (insufficient injection pressure, insufficient fuel injection volume in main
injection, engine braking)
System failure (fuel system, engine control system) -
-
-
Pilot injection
Main injection
Combustion pressure with pilot injection
Combustion pressure without pilot injection 1.
2.
1a.
2b. Stop conditions
Combustion pressure characteristic curve for pilot injection ▶
Page 341 of 715
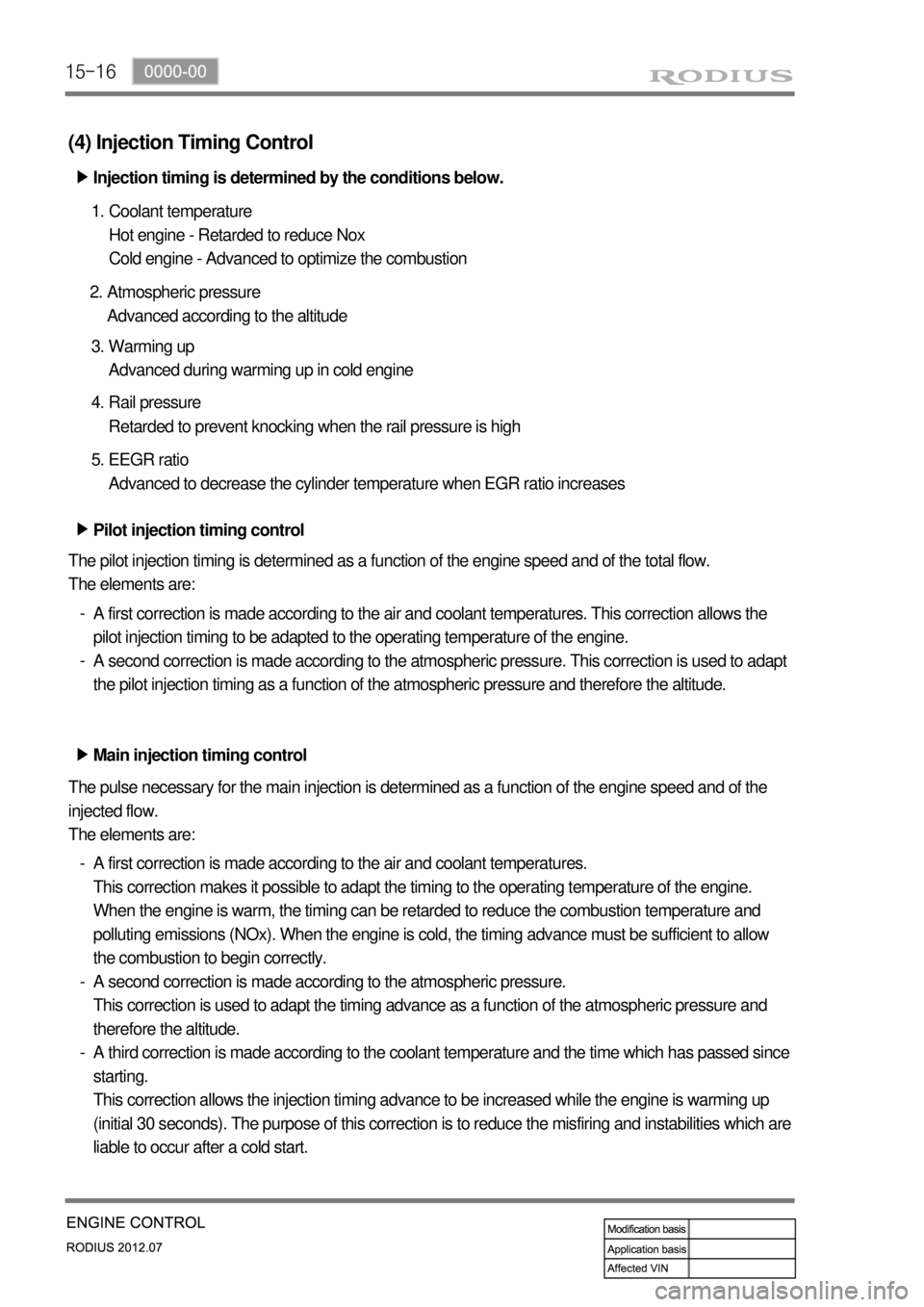
15-16
Pilot injection timing control ▶
The pilot injection timing is determined as a function of the engine speed and of the total flow.
The elements are:
A first correction is made according to the air and coolant temperatures. This correction allows the
pilot injection timing to be adapted to the operating temperature of the engine.
A second correction is made according to the atmospheric pressure. This correction is used to adapt
the pilot injection timing as a function of the atmospheric pressure and therefore the altitude. -
-
(4) Injection Timing Control
Injection timing is determined by the conditions below. ▶
Coolant temperature
Hot engine - Retarded to reduce Nox
Cold engine - Advanced to optimize the combustion 1.
Atmospheric pressure
Advanced according to the altitude 2.
Warming up
Advanced during warming up in cold engine 3.
Rail pressure
Retarded to prevent knocking when the rail pressure is high 4.
EEGR ratio
Advanced to decrease the cylinder temperature when EGR ratio increases 5.
Main injection timing control ▶
The pulse necessary for the main injection is determined as a function of the engine speed and of the
injected flow.
The elements are:
A first correction is made according to the air and coolant temperatures.
This correction makes it possible to adapt the timing to the operating temperature of the engine.
When the engine is warm, the timing can be retarded to reduce the combustion temperature and
polluting emissions (NOx). When the engine is cold, the timing advance must be sufficient to allow
the combustion to begin correctly.
A second correction is made according to the atmospheric pressure.
This correction is used to adapt the timing advance as a function of the atmospheric pressure and
therefore the altitude.
A third correction is made according to the coolant temperature and the time which has passed since
starting.
This correction allows the injection timing advance to be increased while the engine is warming up
(initial 30 seconds). The purpose of this correction is to reduce the misfiring and instabilities which are
liable to occur after a cold start. -
-
-
Page 343 of 715
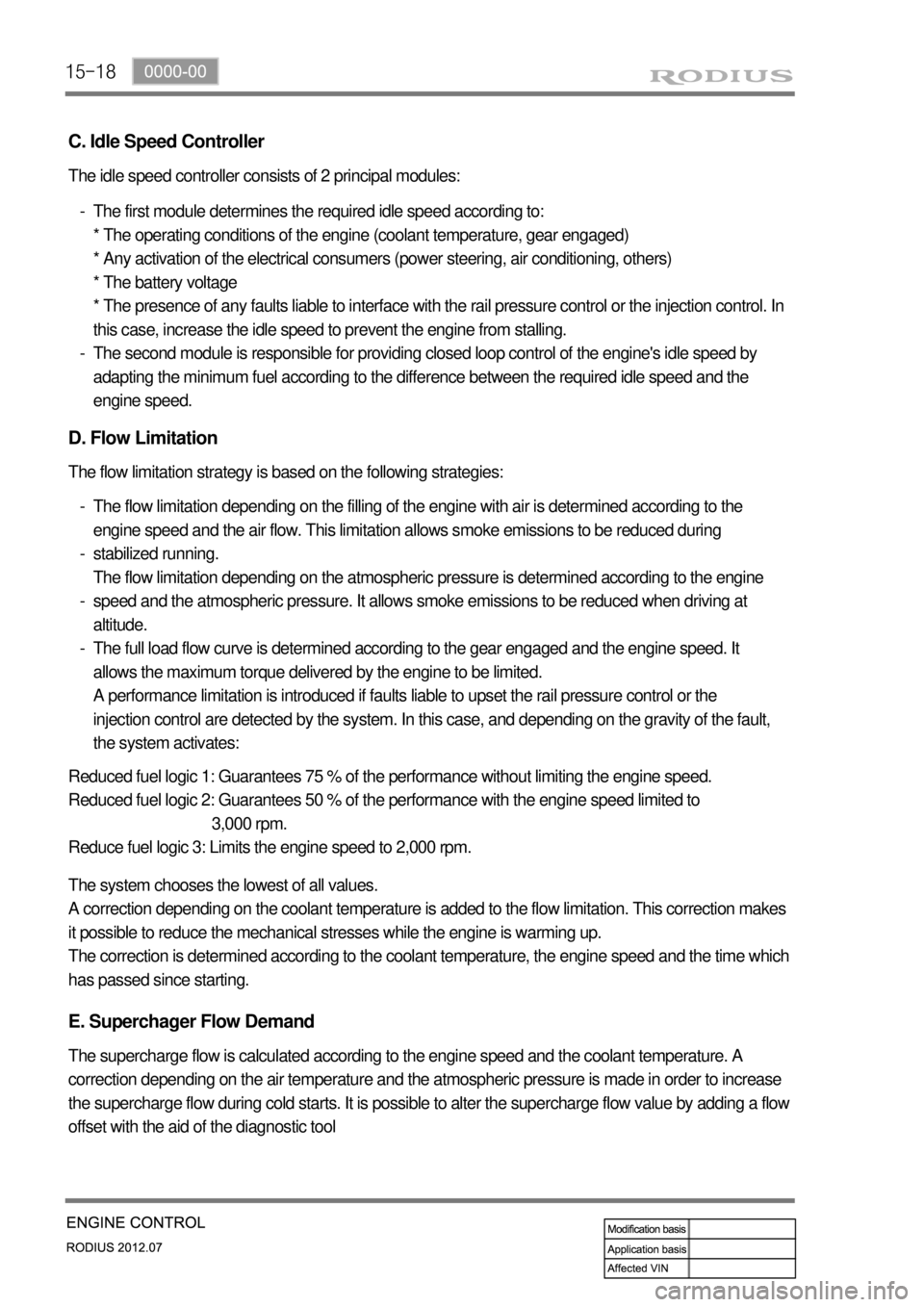
15-18
C. Idle Speed Controller
The idle speed controller consists of 2 principal modules:
The first module determines the required idle speed according to:
* The operating conditions of the engine (coolant temperature, gear engaged)
* Any activation of the electrical consumers (power steering, air conditioning, others)
* The battery voltage
* The presence of any faults liable to interface with the rail pressure control or the injection control. In
this case, increase the idle speed to prevent the engine from stalling.
The second module is responsible for providing closed loop control of the engine's idle speed by
adapting the minimum fuel according to the difference between the required idle speed and the
engine speed. -
-
D. Flow Limitation
The flow limitation strategy is based on the following strategies:
The flow limitation depending on the filling of the engine with air is determined according to the
engine speed and the air flow. This limitation allows smoke emissions to be reduced during
stabilized running.
The flow limitation depending on the atmospheric pressure is determined according to the engine
speed and the atmospheric pressure. It allows smoke emissions to be reduced when driving at
altitude.
The full load flow curve is determined according to the gear engaged and the engine speed. It
allows the maximum torque delivered by the engine to be limited.
A performance limitation is introduced if faults liable to upset the rail pressure control or the
injection control are detected by the system. In this case, and depending on the gravity of the fault,
the system activates: -
-
-
-
Reduced fuel logic 1: Guarantees 75 % of the performance without limiting the engine speed.
Reduced fuel logic 2: Guarantees 50 % of the performance with the engine speed limited to
3,000 rpm.
Reduce fuel logic 3: Limits the engine speed to 2,000 rpm.
The system chooses the lowest of all values.
A correction depending on the coolant temperature is added to the flow limitation. This correction makes
it possible to reduce the mechanical stresses while the engine is warming up.
The correction is determined according to the coolant temperature, the engine speed and the time which
has passed since starting.
E. Superchager Flow Demand
The supercharge flow is calculated according to the engine speed and the coolant temperature. A
correction depending on the air temperature and the atmospheric pressure is made in order to increase
the supercharge flow during cold starts. It is possible to alter the supercharge flow value by adding a flow
offset with the aid of the diagnostic tool
Page 349 of 715
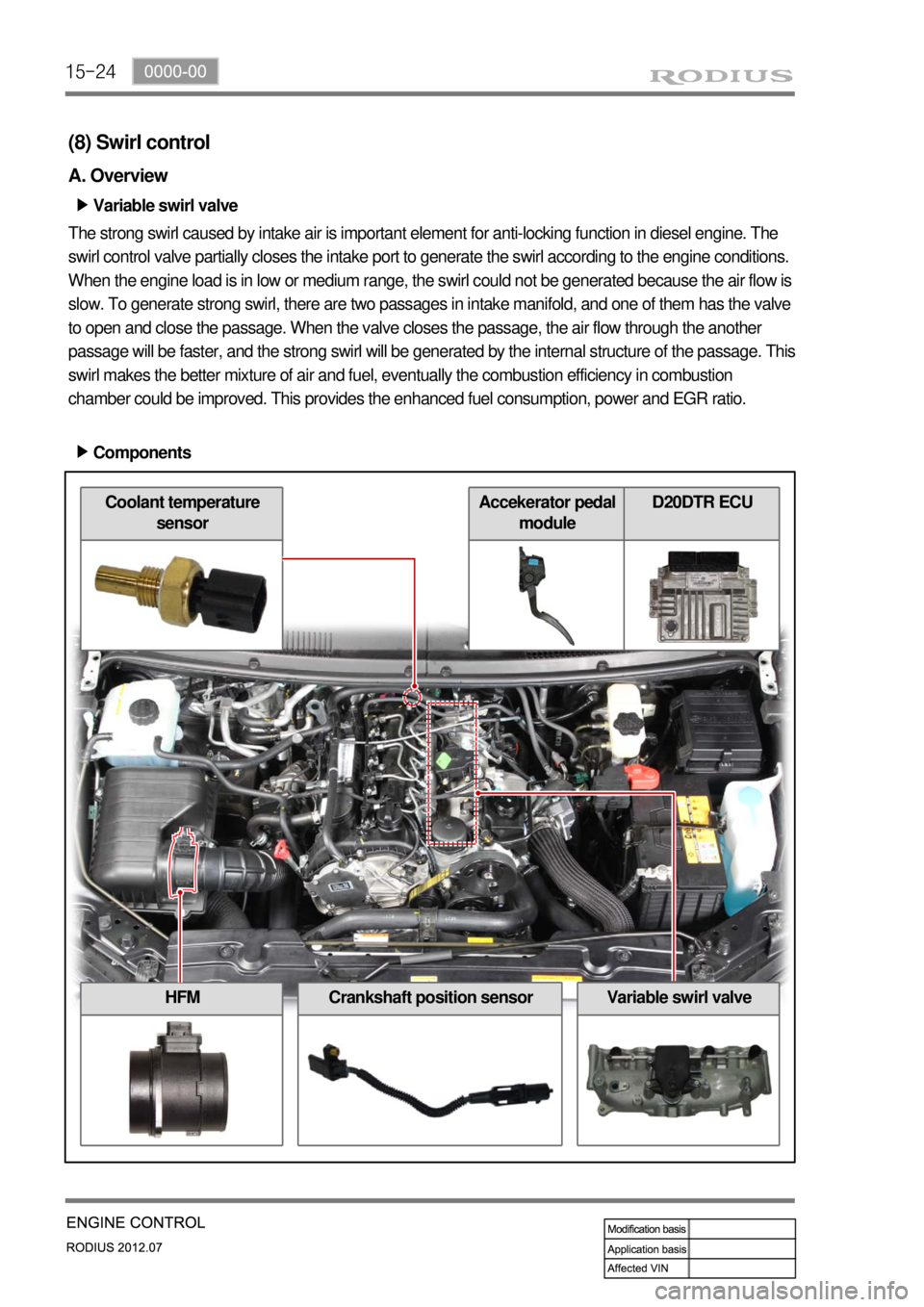
15-24
(8) Swirl control
A. Overview
Variable swirl valve ▶
The strong swirl caused by intake air is important element for anti-locking function in diesel engine. The
swirl control valve partially closes the intake port to generate the swirl according to the engine conditions.
When the engine load is in low or medium range, the swirl could not be generated because the air flow is
slow. To generate strong swirl, there are two passages in intake manifold, and one of them has the valve
to open and close the passage. When the valve closes the passage, the air flow through the another
passage will be faster, and the strong swirl will be generated by the internal structure of the passage. This
swirl makes the better mixture of air and fuel, eventually the combustion efficiency in combustion
chamber could be improved. This provides the enhanced fuel consumption, power and EGR ratio.
Components ▶
HFMCrankshaft position sensorVariable swirl valve
Coolant temperature
sensorAccekerator pedal
moduleD20DTR ECU
Page 352 of 715
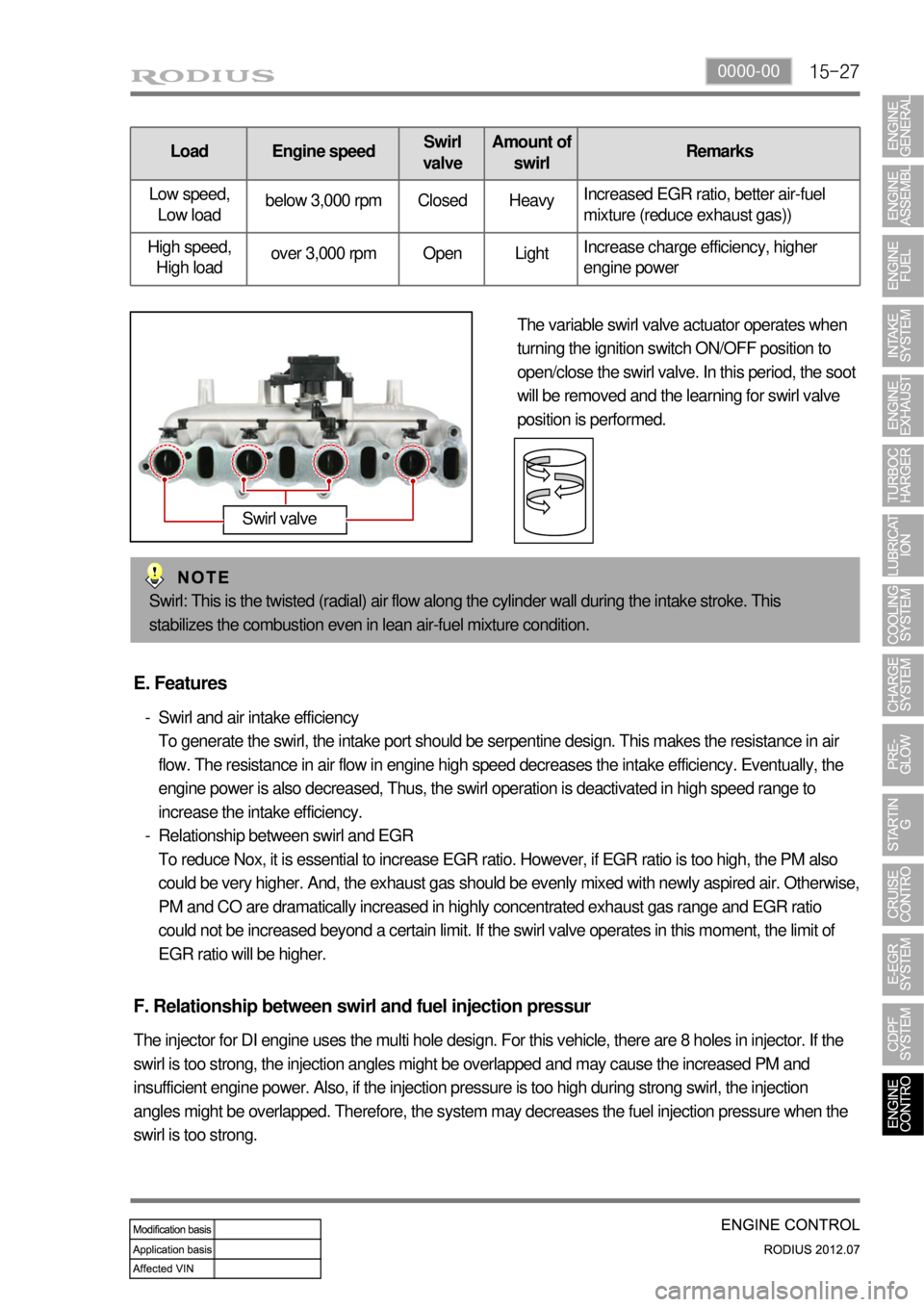
15-270000-00
Load Engine speedSwirl
valveAmount of
swirlRemarks
Low speed,
Low loadbelow 3,000 rpm Closed HeavyIncreased EGR ratio, better air-fuel
mixture (reduce exhaust gas))
High speed,
High loadover 3,000 rpm Open LightIncrease charge efficiency, higher
engine power
The variable swirl valve actuator operates when
turning the ignition switch ON/OFF position to
open/close the swirl valve. In this period, the soot
will be removed and the learning for swirl valve
position is performed.
Swirl: This is the twisted (radial) air flow along the cylinder wall during the intake stroke. This
stabilizes the combustion even in lean air-fuel mixture condition.
Swirl valve
E. Features
Swirl and air intake efficiency
To generate the swirl, the intake port should be serpentine design. This makes the resistance in air
flow. The resistance in air flow in engine high speed decreases the intake efficiency. Eventually, the
engine power is also decreased, Thus, the swirl operation is deactivated in high speed range to
increase the intake efficiency.
Relationship between swirl and EGR
To reduce Nox, it is essential to increase EGR ratio. However, if EGR ratio is too high, the PM also
could be very higher. And, the exhaust gas should be evenly mixed with newly aspired air. Otherwise,
PM and CO are dramatically increased in highly concentrated exhaust gas range and EGR ratio
could not be increased beyond a certain limit. If the swirl valve operates in this moment, the limit of
EGR ratio will be higher. -
-
F. Relationship between swirl and fuel injection pressur
The injector for DI engine uses the multi hole design. For this vehicle, there are 8 holes in injector. If the
swirl is too strong, the injection angles might be overlapped and may cause the increased PM and
insufficient engine power. Also, if the injection pressure is too high during strong swirl, the injection
angles might be overlapped. Therefore, the system may decreases the fuel injection pressure when the
swirl is too strong.
Page 363 of 715
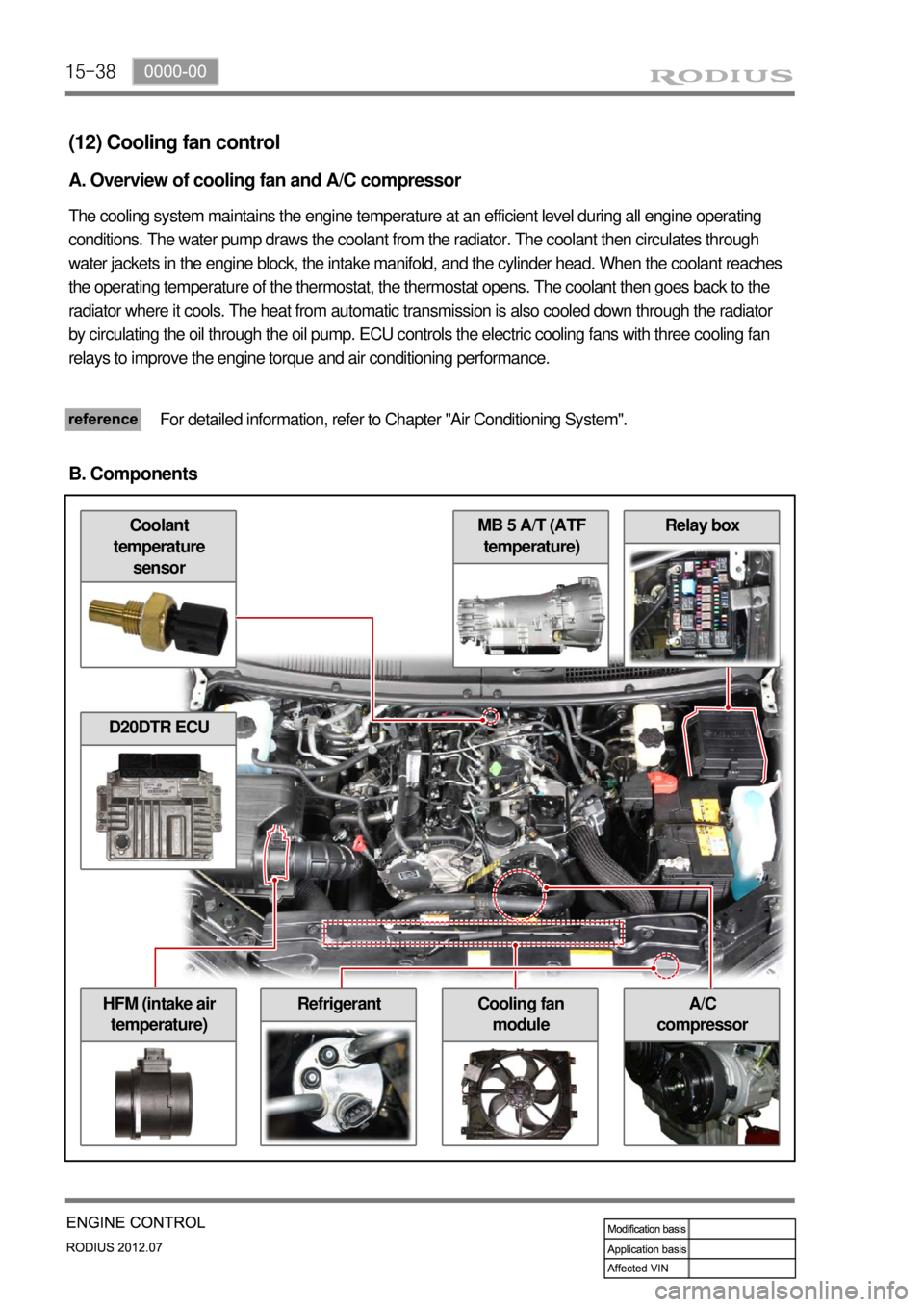
15-38
Relay box
A/C
compressorHFM (intake air
temperature)Cooling fan
module
MB 5 A/T (ATF
temperature)Coolant
temperature
sensor
(12) Cooling fan control
A. Overview of cooling fan and A/C compressor
The cooling system maintains the engine temperature at an efficient level during all engine operating
conditions. The water pump draws the coolant from the radiator. The coolant then circulates through
water jackets in the engine block, the intake manifold, and the cylinder head. When the coolant reaches
the operating temperature of the thermostat, the thermostat opens. The coolant then goes back to the
radiator where it cools. The heat from automatic transmission is also cooled down through the radiator
by circulating the oil through the oil pump. ECU controls the electric cooling fans with three cooling fan
relays to improve the engine torque and air conditioning performance.
For detailed information, refer to Chapter "Air Conditioning System".
B. Components
D20DTR ECU
Refrigerant
Page 368 of 715
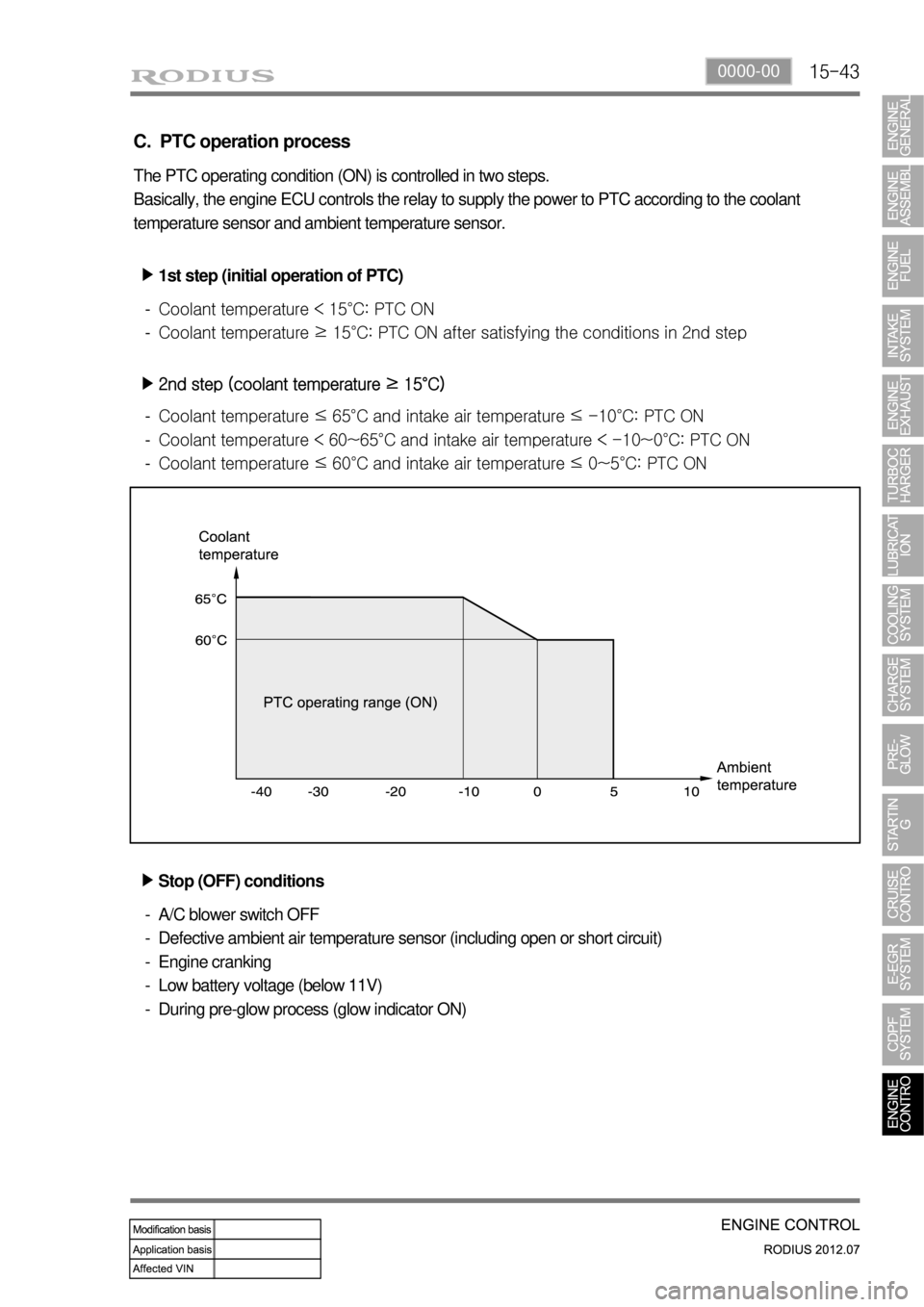
15-430000-00
C. PTC operation process
The PTC operating condition (ON) is controlled in two steps.
Basically, the engine ECU controls the relay to supply the power to PTC according to the coolant
temperature sensor and ambient temperature sensor.
1st step (initial operation of PTC) ▶
Coolant temperature < 15°C: PTC ON
<006a00960096009300880095009b0047009b008c00940097008c00990088009b009c0099008c004702fb00470058005c00b6006a006100470077007b006a00470076007500470088008d009b008c00990047009a0088009b0090009a008d00a00090009500
8e0047009b008f008c0047008a00960095008b0090009b0090>ons in 2nd step -
-
2nd step (coolant temperature ≥ 15°C) ▶
<006a00960096009300880095009b0047009b008c00940097008c00990088009b009c0099008c004702fa0047005d005c00b6006a004700880095008b004700900095009b00880092008c00470088009000990047009b008c00940097008c00990088009b00
9c0099008c004702fa004700540058005700b6006a00610047>PTC ON
<006a00960096009300880095009b0047009b008c00940097008c00990088009b009c0099008c004700630047005d005700a5005d005c00b6006a004700880095008b004700900095009b00880092008c00470088009000990047009b008c00940097008c00
990088009b009c0099008c00470063004700540058005700a5>0°C: PTC ON
<006a00960096009300880095009b0047009b008c00940097008c00990088009b009c0099008c004702fa0047005d005700b6006a004700880095008b004700900095009b00880092008c00470088009000990047009b008c00940097008c00990088009b00
9c0099008c004702fa0047005700a5005c00b6006a00610047>PTC ON -
-
-
Stop (OFF) conditions ▶
A/C blower switch OFF
Defective ambient air temperature sensor (including open or short circuit)
Engine cranking
Low battery voltage (below 11V)
During pre-glow process (glow indicator ON) -
-
-
-
-