SUZUKI SWIFT 2000 1.G RG413 Service Workshop Manual
[x] Cancel search | Manufacturer: SUZUKI, Model Year: 2000, Model line: SWIFT, Model: SUZUKI SWIFT 2000 1.GPages: 698, PDF Size: 16.01 MB
Page 121 of 698
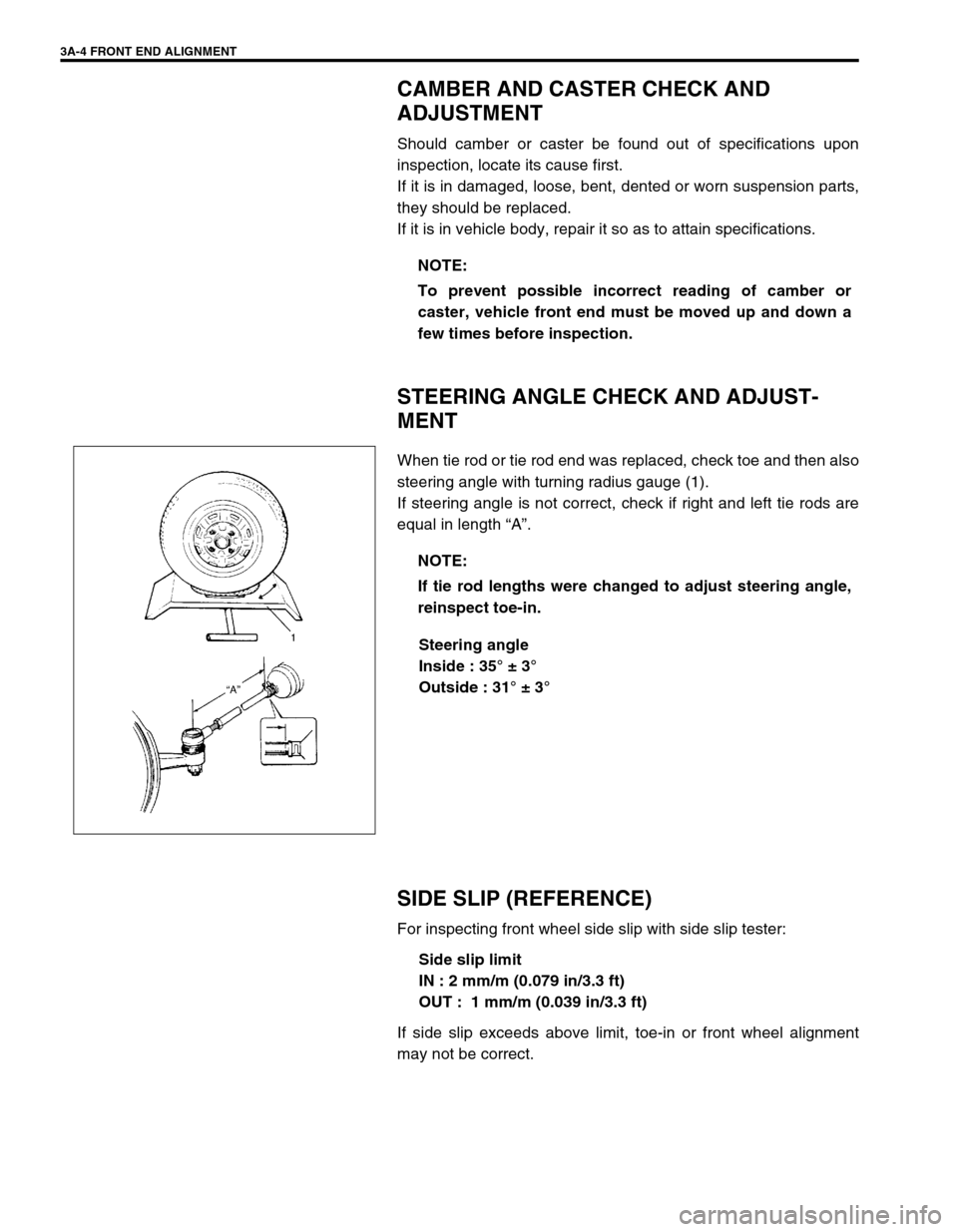
3A-4 FRONT END ALIGNMENT
CAMBER AND CASTER CHECK AND
ADJUSTMENT
Should camber or caster be found out of specifications upon
inspection, locate its cause first.
If it is in damaged, loose, bent, dented or worn suspension parts,
they should be replaced.
If it is in vehicle body, repair it so as to attain specifications.
STEERING ANGLE CHECK AND ADJUST-
MENT
When tie rod or tie rod end was replaced, check toe and then also
steering angle with turning radius gauge (1).
If steering angle is not correct, check if right and left tie rods are
equal in length “A”.
Steering angle
Inside : 35° ± 3°
Outside : 31° ± 3°
SIDE SLIP (REFERENCE)
For inspecting front wheel side slip with side slip tester:
Side slip limit
IN : 2 mm/m (0.079 in/3.3 ft)
OUT : 1 mm/m (0.039 in/3.3 ft)
If side slip exceeds above limit, toe-in or front wheel alignment
may not be correct.NOTE:
To prevent possible incorrect reading of camber or
caster, vehicle front end must be moved up and down a
few times before inspection.
NOTE:
If tie rod lengths were changed to adjust steering angle,
reinspect toe-in.
Page 122 of 698
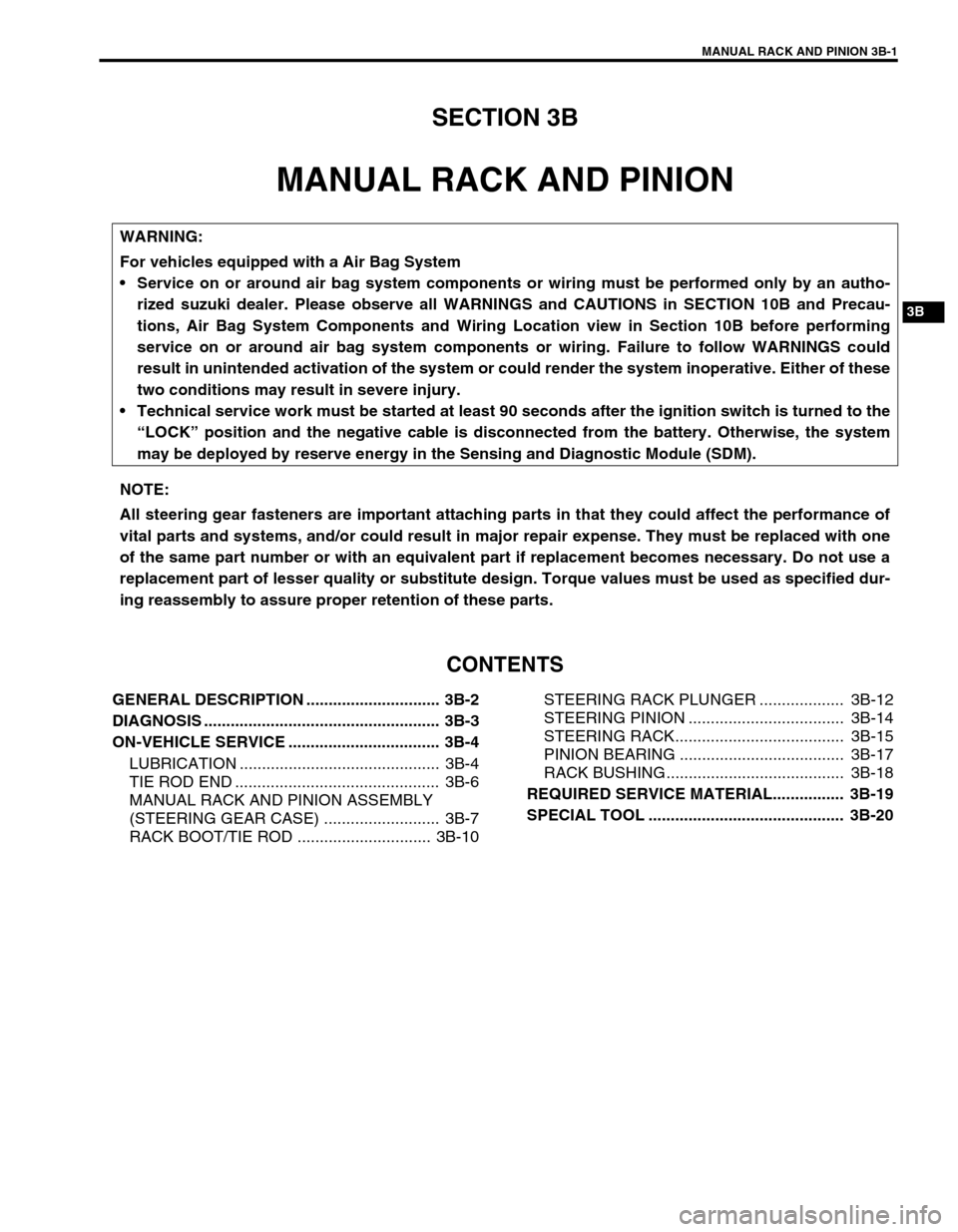
MANUAL RACK AND PINION 3B-1
6F1
6F2
6G
6H
7A
3B
7C1
7D
7E
7F
8A
8B
8C
8D
8E
9
10
10A
10B
SECTION 3B
MANUAL RACK AND PINION
CONTENTS
GENERAL DESCRIPTION .............................. 3B-2
DIAGNOSIS ..................................................... 3B-3
ON-VEHICLE SERVICE .................................. 3B-4
LUBRICATION ............................................. 3B-4
TIE ROD END .............................................. 3B-6
MANUAL RACK AND PINION ASSEMBLY
(STEERING GEAR CASE) .......................... 3B-7
RACK BOOT/TIE ROD .............................. 3B-10STEERING RACK PLUNGER ................... 3B-12
STEERING PINION ................................... 3B-14
STEERING RACK...................................... 3B-15
PINION BEARING ..................................... 3B-17
RACK BUSHING ........................................ 3B-18
REQUIRED SERVICE MATERIAL................ 3B-19
SPECIAL TOOL ............................................ 3B-20
WARNING:
For vehicles equipped with a Air Bag System
Service on or around air bag system components or wiring must be performed only by an autho-
rized suzuki dealer. Please observe all WARNINGS and CAUTIONS in SECTION 10B and Precau-
tions, Air Bag System Components and Wiring Location view in Section 10B before performing
service on or around air bag system components or wiring. Failure to follow WARNINGS could
result in unintended activation of the system or could render the system inoperative. Either of these
two conditions may result in severe injury.
Technical service work must be started at least 90 seconds after the ignition switch is turned to the
“LOCK” position and the negative cable is disconnected from the battery. Otherwise, the system
may be deployed by reserve energy in the Sensing and Diagnostic Module (SDM).
NOTE:
All steering gear fasteners are important attaching parts in that they could affect the performance of
vital parts and systems, and/or could result in major repair expense. They must be replaced with one
of the same part number or with an equivalent part if replacement becomes necessary. Do not use a
replacement part of lesser quality or substitute design. Torque values must be used as specified dur-
ing reassembly to assure proper retention of these parts.
Page 123 of 698
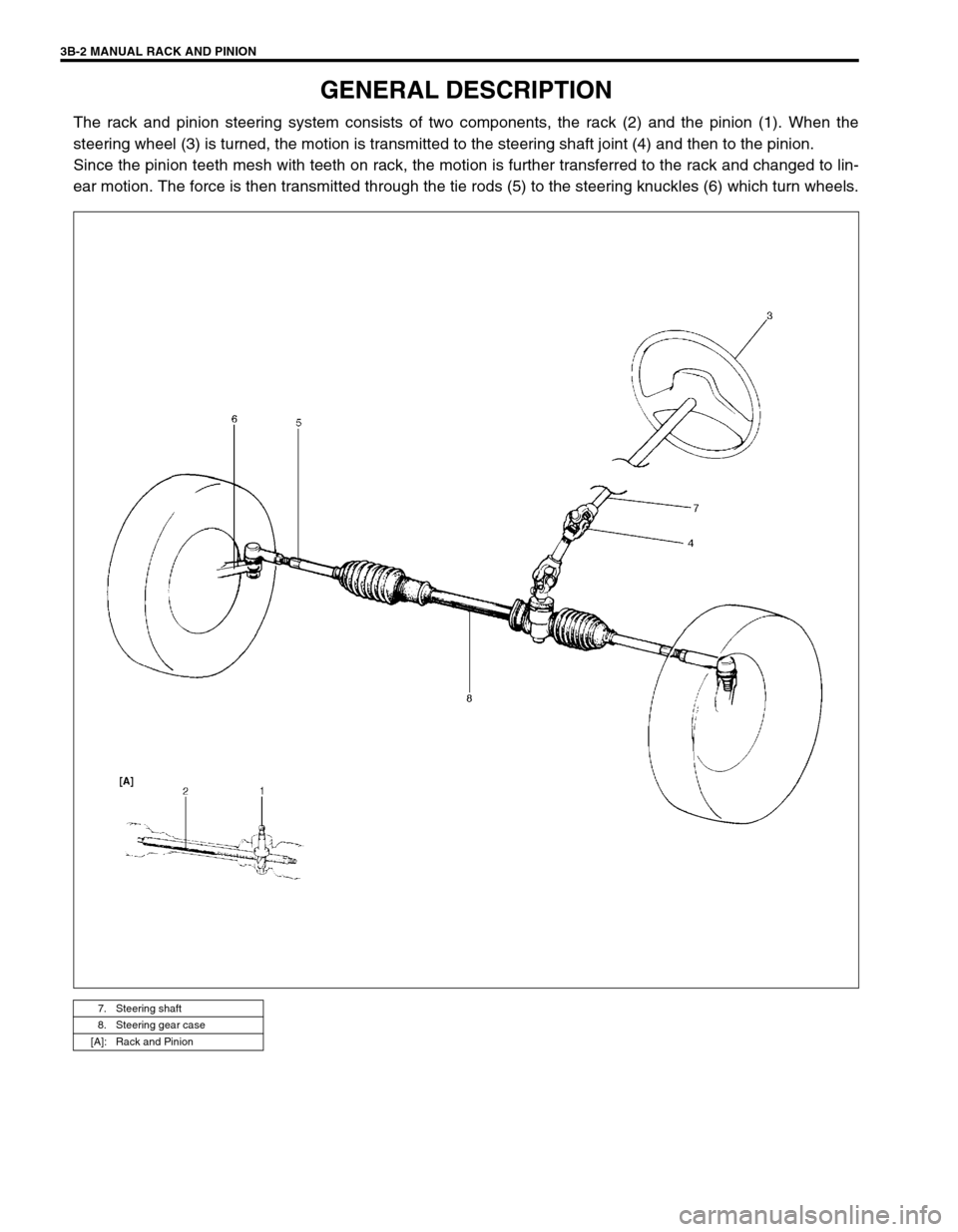
3B-2 MANUAL RACK AND PINION
GENERAL DESCRIPTION
The rack and pinion steering system consists of two components, the rack (2) and the pinion (1). When the
steering wheel (3) is turned, the motion is transmitted to the steering shaft joint (4) and then to the pinion.
Since the pinion teeth mesh with teeth on rack, the motion is further transferred to the rack and changed to lin-
ear motion. The force is then transmitted through the tie rods (5) to the steering knuckles (6) which turn wheels.
7. Steering shaft
8. Steering gear case
[A]: Rack and Pinion
Page 124 of 698
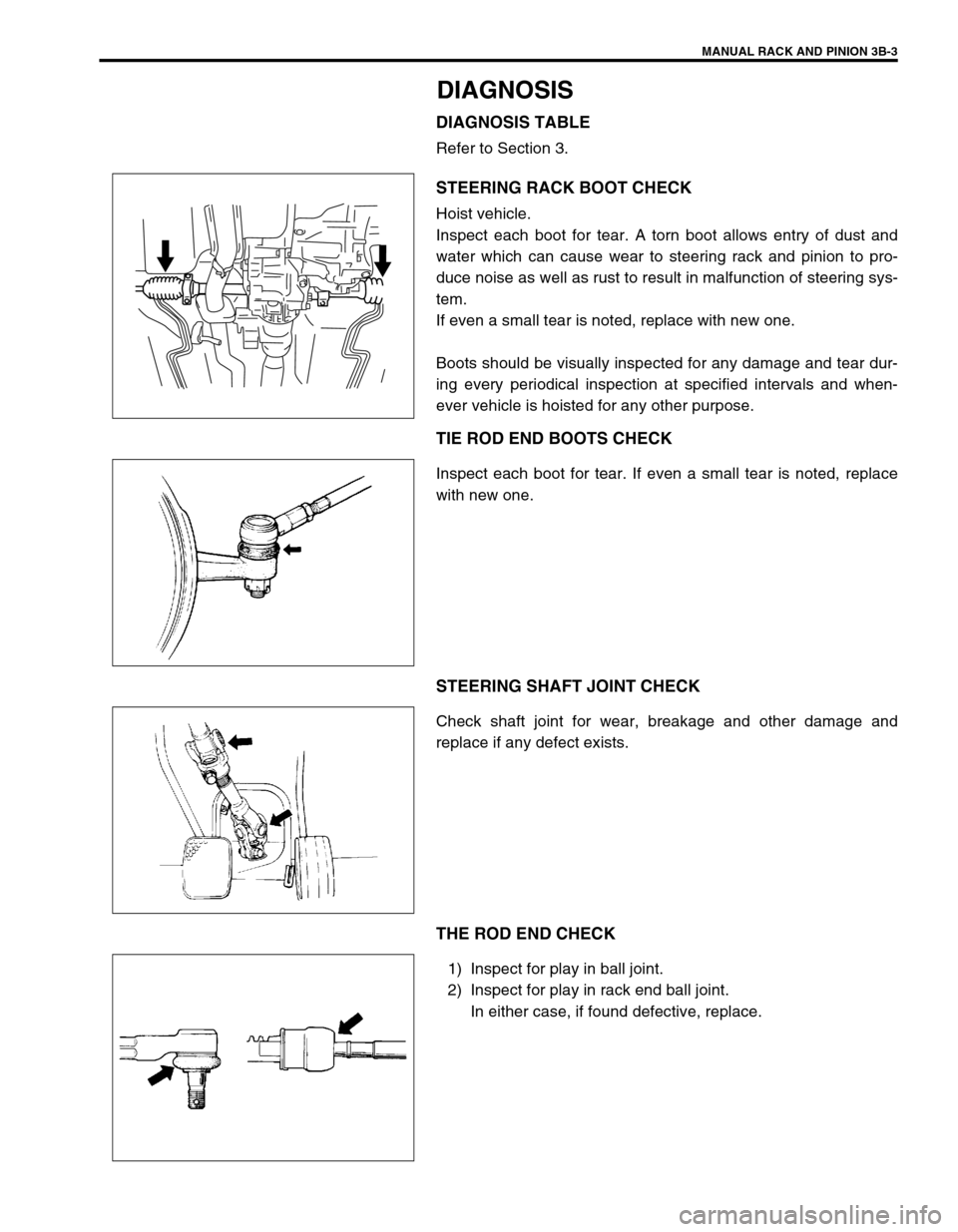
MANUAL RACK AND PINION 3B-3
DIAGNOSIS
DIAGNOSIS TABLE
Refer to Section 3.
STEERING RACK BOOT CHECK
Hoist vehicle.
Inspect each boot for tear. A torn boot allows entry of dust and
water which can cause wear to steering rack and pinion to pro-
duce noise as well as rust to result in malfunction of steering sys-
tem.
If even a small tear is noted, replace with new one.
Boots should be visually inspected for any damage and tear dur-
ing every periodical inspection at specified intervals and when-
ever vehicle is hoisted for any other purpose.
TIE ROD END BOOTS CHECK
Inspect each boot for tear. If even a small tear is noted, replace
with new one.
STEERING SHAFT JOINT CHECK
Check shaft joint for wear, breakage and other damage and
replace if any defect exists.
THE ROD END CHECK
1) Inspect for play in ball joint.
2) Inspect for play in rack end ball joint.
In either case, if found defective, replace.
Page 125 of 698
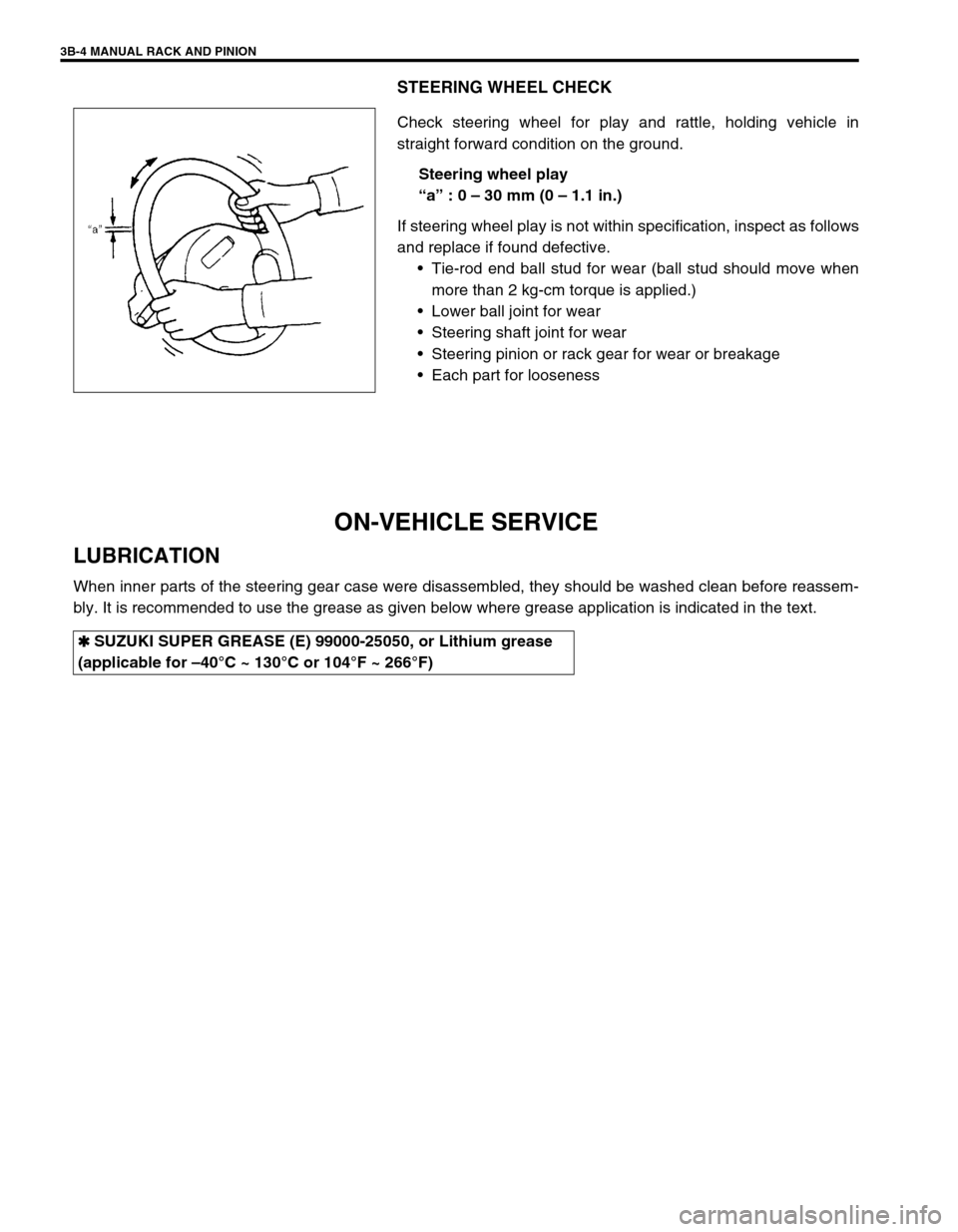
3B-4 MANUAL RACK AND PINION
STEERING WHEEL CHECK
Check steering wheel for play and rattle, holding vehicle in
straight forward condition on the ground.
Steering wheel play
“a” : 0 – 30 mm (0 – 1.1 in.)
If steering wheel play is not within specification, inspect as follows
and replace if found defective.
Tie-rod end ball stud for wear (ball stud should move when
more than 2 kg-cm torque is applied.)
Lower ball joint for wear
Steering shaft joint for wear
Steering pinion or rack gear for wear or breakage
Each part for looseness
ON-VEHICLE SERVICE
LUBRICATION
When inner parts of the steering gear case were disassembled, they should be washed clean before reassem-
bly. It is recommended to use the grease as given below where grease application is indicated in the text.
✱
✱✱ ✱ SUZUKI SUPER GREASE (E) 99000-25050, or Lithium grease
(applicable for –40°C ~ 130°C or 104°F ~ 266°F)
Page 126 of 698
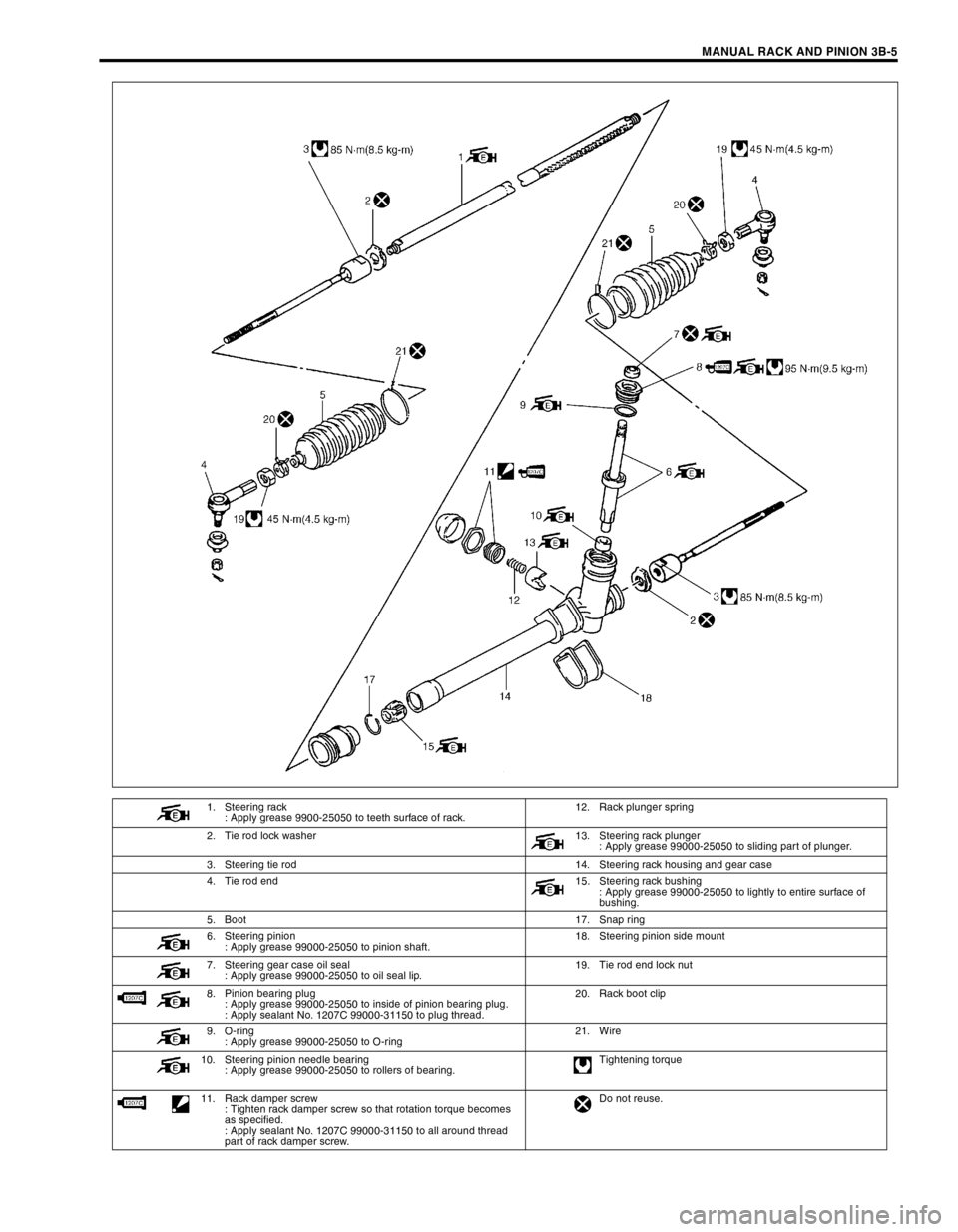
!"#$"%&'"()&"#*&+,#,-#&./01
!" #$%%&'()*&+,-
.*/0012*)&%+3%*4455678585*$9*$%%$:*3;&<+,%*9<*&+,-"!7" =+,-*01;()%&*30&'()
7" >'%*&9?*19,-*@+3:%& !A" #$%%&'()*&+,-*01;()%&
.*/0012*)&%+3%*44555678585*$9*31'?'()*0+&$*9<*01;()%&"
A" #$%%&'()*$'%*&9? !B" #$%%&'()*&+,-*:9;3'()*+(?*)%+&*,+3%
B" >'%*&9?*%(? !8" #$%%&'()*&+,-*C;3:'()
.*/0012*)&%+3%*44555678585*$9*1'):$12*$9*%($'&%*3;&<+,%*9<*
C;3:'()"
8" D99$ !E" #(+0*&'()
F" #$%%&'()*0'('9(
.*/0012*)&%+3%*44555678585*$9*0'('9(*3:+<$"!G" #$%%&'()*0'('9(*3'?%*H9;($
E" #$%%&'()*)%+&*,+3%*9'1*3%+1
.*/0012*)&%+3%*44555678585*$9*9'1*3%+1*1'0"!4" >'%*&9?*%(?*19,-*(;$
G" I'('9(*C%+&'()*01;)
.*/0012*)&%+3%*44555678585*$9*'(3'?%*9<*0'('9(*C%+&'()*01;)"
.*/0012*3%+1+($*J9"*!75EK*445556A!!85*$9*01;)*$:&%+?"75" =+,-*C99$*,1'0
4" L6&'()
.*/0012*)&%+3%*44555678585*$9*L6&'()7!" M'&%
!5" #$%%&'()*0'('9(*(%%?1%*C%+&'()
.*/0012*)&%+3%*44555678585*$9*&911%&3*9<*C%+&'()">'):$%('()*$9&N;%
!!" =+,-*?+H0%&*3,&%@
.*>'):$%(*&+,-*?+H0%&*3,&%@*39*$:+$*&9$+$'9(*$9&N;%*C%,9H%3*
+3*30%,'<'%?"
.*/0012*3%+1+($*J9"*!75EK*445556A!!85*$9*+11*+&9;(?*$:&%+?*
0+&$*9<*&+,-*?+H0%&*3,&%@"O9*(9$*&%;3%"
Page 127 of 698
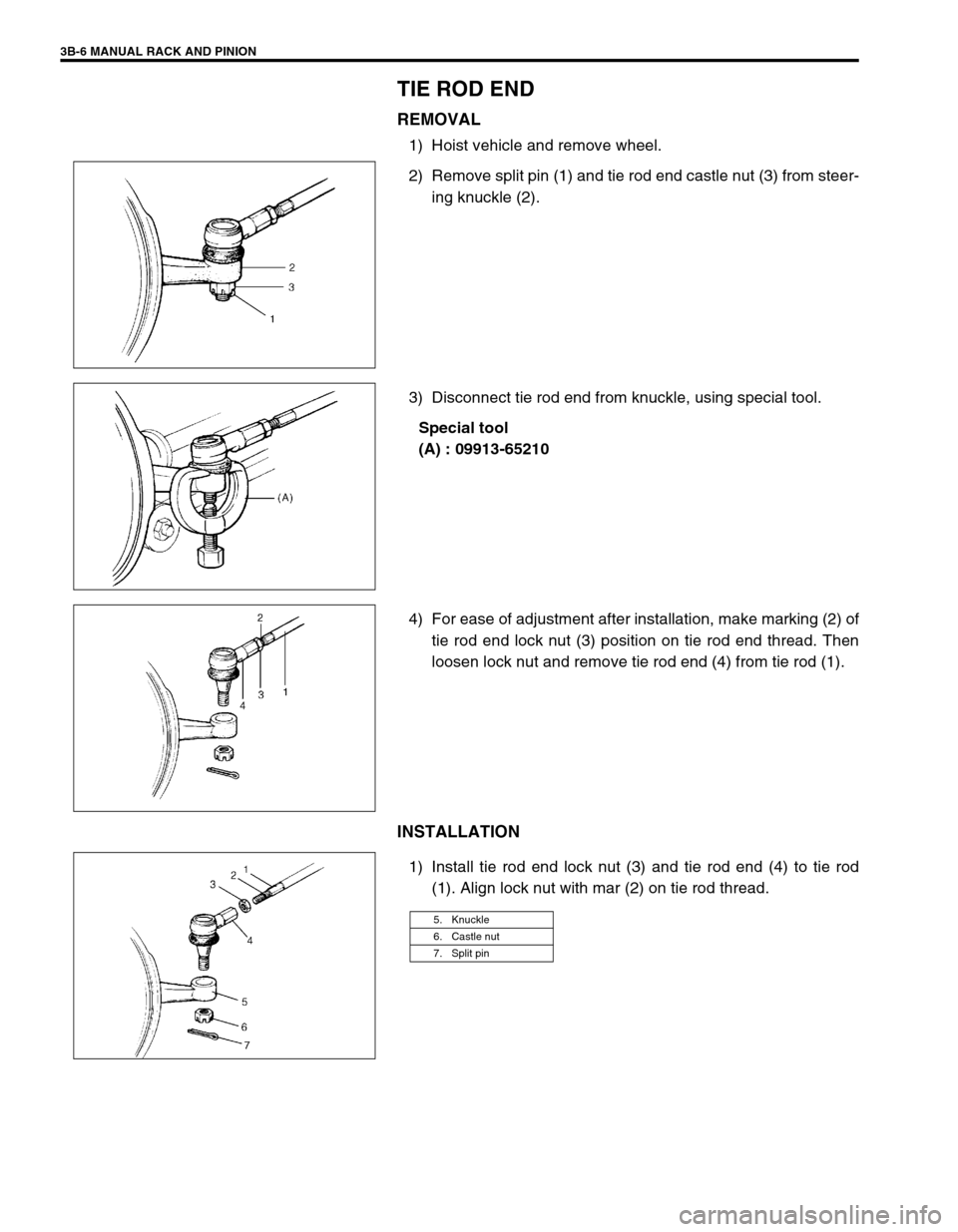
3B-6 MANUAL RACK AND PINION
TIE ROD END
REMOVAL
1) Hoist vehicle and remove wheel.
2) Remove split pin (1) and tie rod end castle nut (3) from steer-
ing knuckle (2).
3) Disconnect tie rod end from knuckle, using special tool.
Special tool
(A) : 09913-65210
4) For ease of adjustment after installation, make marking (2) of
tie rod end lock nut (3) position on tie rod end thread. Then
loosen lock nut and remove tie rod end (4) from tie rod (1).
INSTALLATION
1) Install tie rod end lock nut (3) and tie rod end (4) to tie rod
(1). Align lock nut with mar (2) on tie rod thread.
5. Knuckle
6. Castle nut
7. Split pin
Page 128 of 698
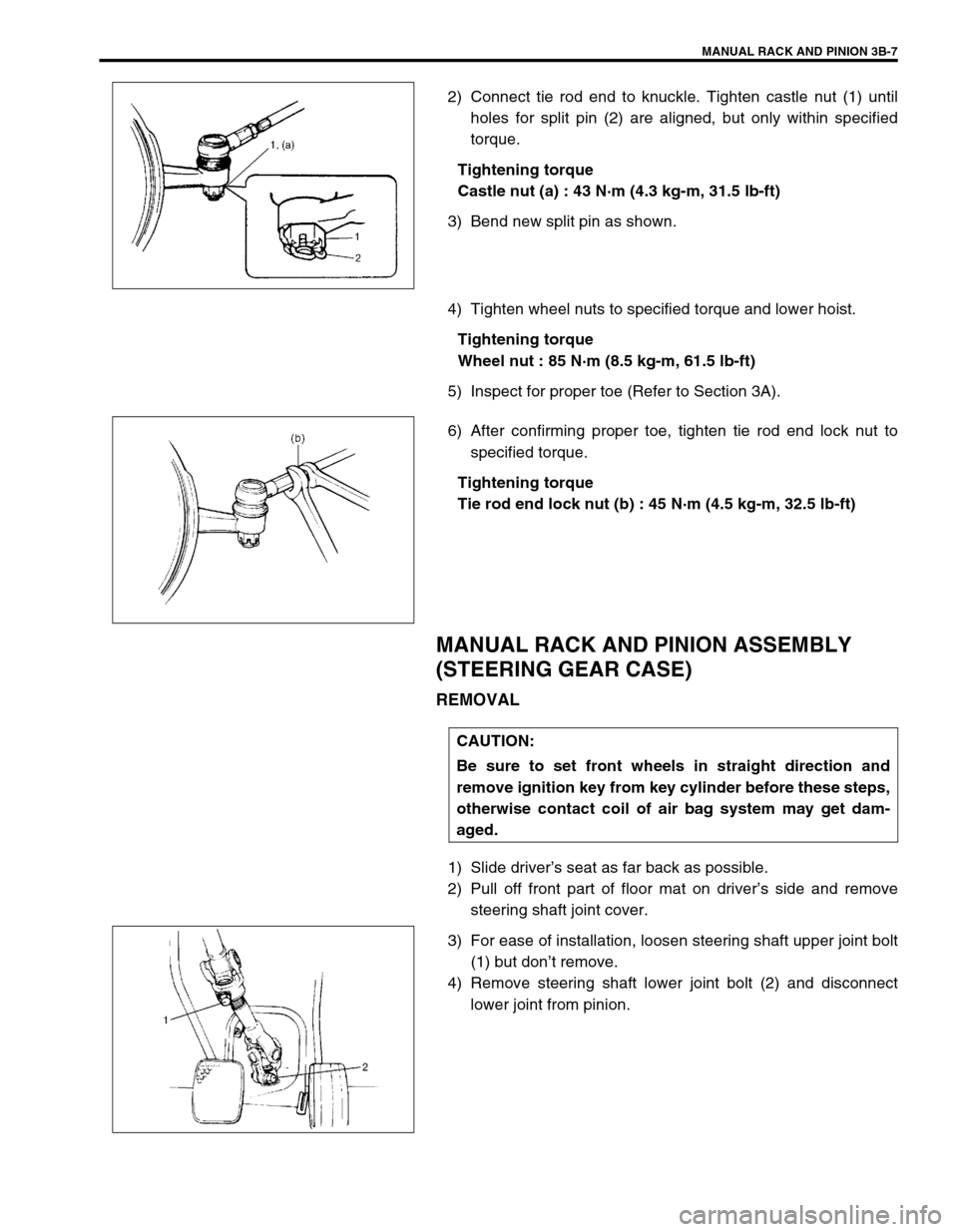
MANUAL RACK AND PINION 3B-7
2) Connect tie rod end to knuckle. Tighten castle nut (1) until
holes for split pin (2) are aligned, but only within specified
torque.
Tightening torque
Castle nut (a) : 43 N·m (4.3 kg-m, 31.5 lb-ft)
3) Bend new split pin as shown.
4) Tighten wheel nuts to specified torque and lower hoist.
Tightening torque
Wheel nut : 85 N·m (8.5 kg-m, 61.5 lb-ft)
5) Inspect for proper toe (Refer to Section 3A).
6) After confirming proper toe, tighten tie rod end lock nut to
specified torque.
Tightening torque
Tie rod end lock nut (b) : 45 N·m (4.5 kg-m, 32.5 lb-ft)
MANUAL RACK AND PINION ASSEMBLY
(STEERING GEAR CASE)
REMOVAL
1) Slide driver’s seat as far back as possible.
2) Pull off front part of floor mat on driver’s side and remove
steering shaft joint cover.
3) For ease of installation, loosen steering shaft upper joint bolt
(1) but don’t remove.
4) Remove steering shaft lower joint bolt (2) and disconnect
lower joint from pinion.
CAUTION:
Be sure to set front wheels in straight direction and
remove ignition key from key cylinder before these steps,
otherwise contact coil of air bag system may get dam-
aged.
Page 129 of 698
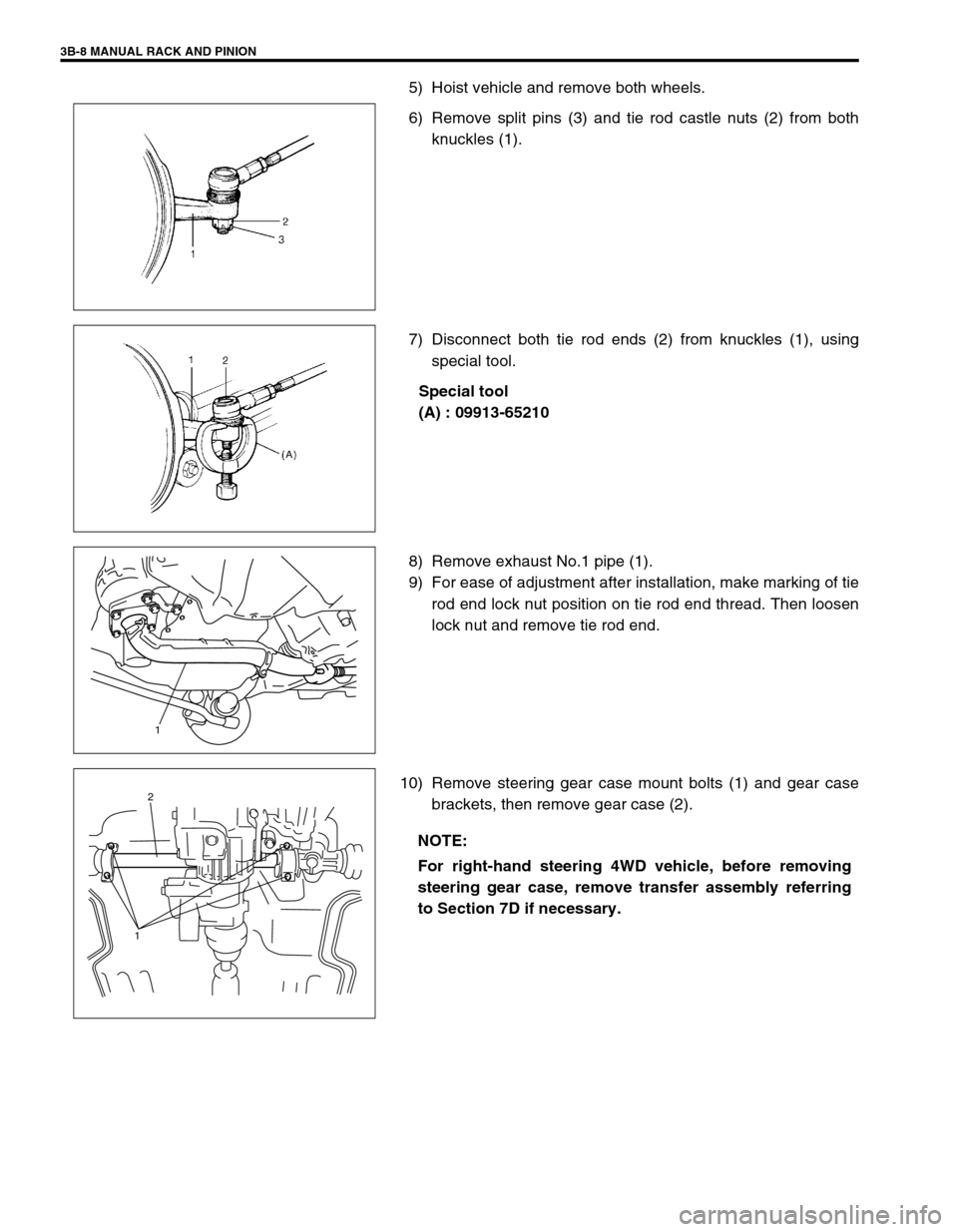
3B-8 MANUAL RACK AND PINION
5) Hoist vehicle and remove both wheels.
6) Remove split pins (3) and tie rod castle nuts (2) from both
knuckles (1).
7) Disconnect both tie rod ends (2) from knuckles (1), using
special tool.
Special tool
(A) : 09913-65210
8) Remove exhaust No.1 pipe (1).
9) For ease of adjustment after installation, make marking of tie
rod end lock nut position on tie rod end thread. Then loosen
lock nut and remove tie rod end.
10) Remove steering gear case mount bolts (1) and gear case
brackets, then remove gear case (2).
1
NOTE:
For right-hand steering 4WD vehicle, before removing
steering gear case, remove transfer assembly referring
to Section 7D if necessary.
2
1
Page 130 of 698
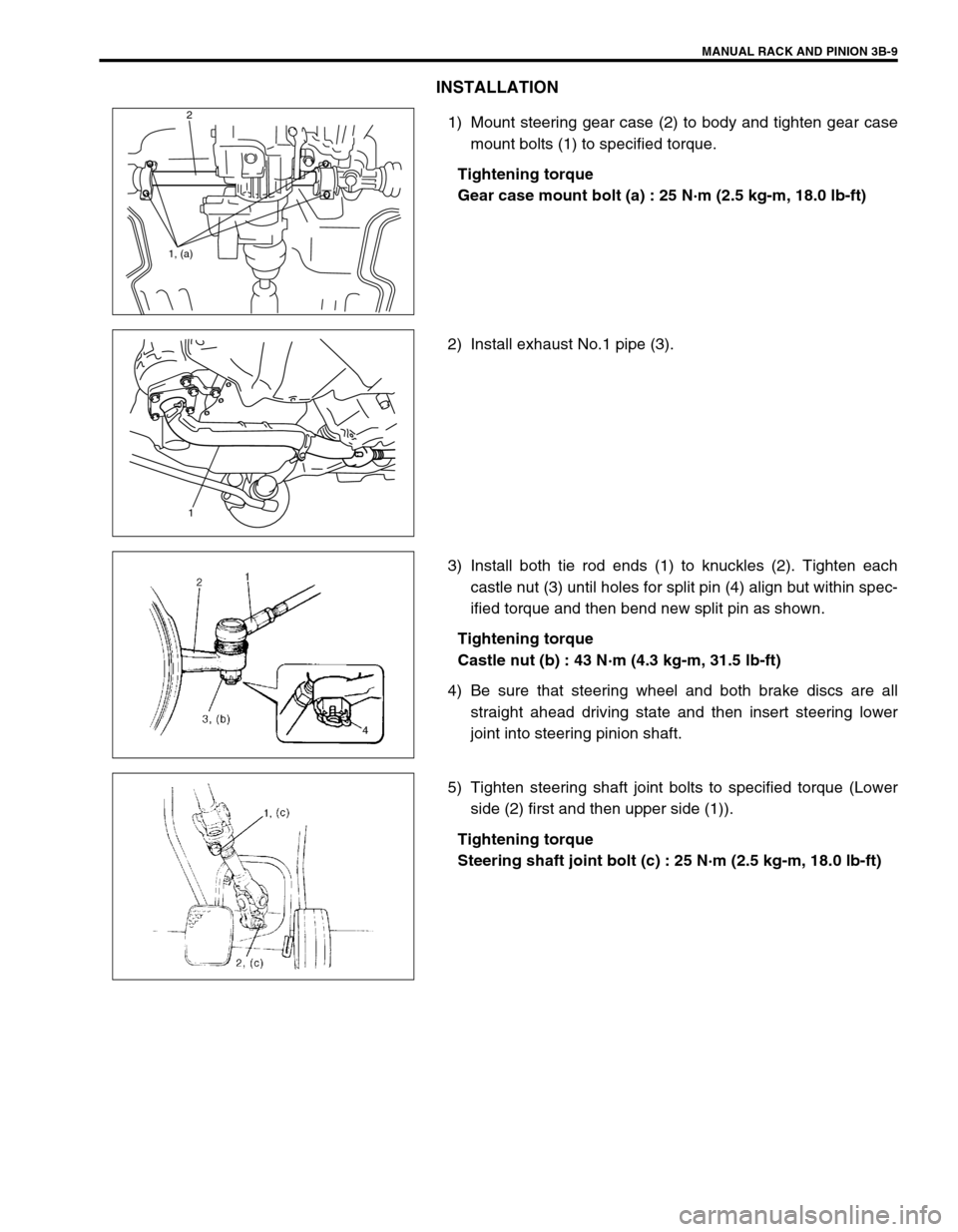
MANUAL RACK AND PINION 3B-9
INSTALLATION
1) Mount steering gear case (2) to body and tighten gear case
mount bolts (1) to specified torque.
Tightening torque
Gear case mount bolt (a) : 25 N·m (2.5 kg-m, 18.0 lb-ft)
2) Install exhaust No.1 pipe (3).
3) Install both tie rod ends (1) to knuckles (2). Tighten each
castle nut (3) until holes for split pin (4) align but within spec-
ified torque and then bend new split pin as shown.
Tightening torque
Castle nut (b) : 43 N·m (4.3 kg-m, 31.5 lb-ft)
4) Be sure that steering wheel and both brake discs are all
straight ahead driving state and then insert steering lower
joint into steering pinion shaft.
5) Tighten steering shaft joint bolts to specified torque (Lower
side (2) first and then upper side (1)).
Tightening torque
Steering shaft joint bolt (c) : 25 N·m (2.5 kg-m, 18.0 lb-ft)2
1, (a)
1