air condition SUZUKI SWIFT 2000 1.G RG413 Service Manual Online
[x] Cancel search | Manufacturer: SUZUKI, Model Year: 2000, Model line: SWIFT, Model: SUZUKI SWIFT 2000 1.GPages: 698, PDF Size: 16.01 MB
Page 284 of 698
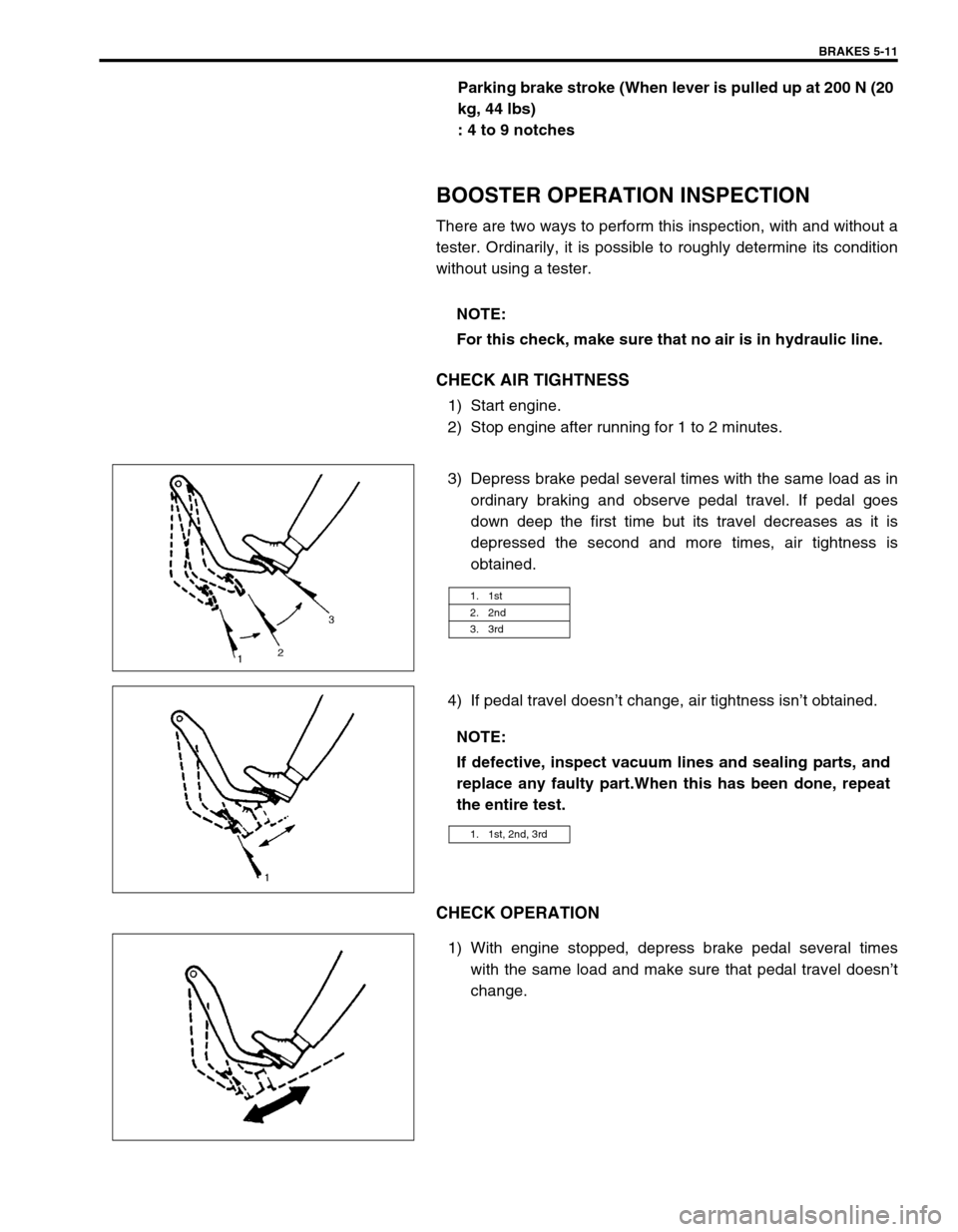
BRAKES 5-11
Parking brake stroke (When lever is pulled up at 200 N (20
kg, 44 lbs)
: 4 to 9 notches
BOOSTER OPERATION INSPECTION
There are two ways to perform this inspection, with and without a
tester. Ordinarily, it is possible to roughly determine its condition
without using a tester.
CHECK AIR TIGHTNESS
1) Start engine.
2) Stop engine after running for 1 to 2 minutes.
3) Depress brake pedal several times with the same load as in
ordinary braking and observe pedal travel. If pedal goes
down deep the first time but its travel decreases as it is
depressed the second and more times, air tightness is
obtained.
4) If pedal travel doesn’t change, air tightness isn’t obtained.
CHECK OPERATION
1) With engine stopped, depress brake pedal several times
with the same load and make sure that pedal travel doesn’t
change. NOTE:
For this check, make sure that no air is in hydraulic line.
1. 1st
2. 2nd
3. 3rd
NOTE:
If defective, inspect vacuum lines and sealing parts, and
replace any faulty part.When this has been done, repeat
the entire test.
1. 1st, 2nd, 3rd
Page 285 of 698
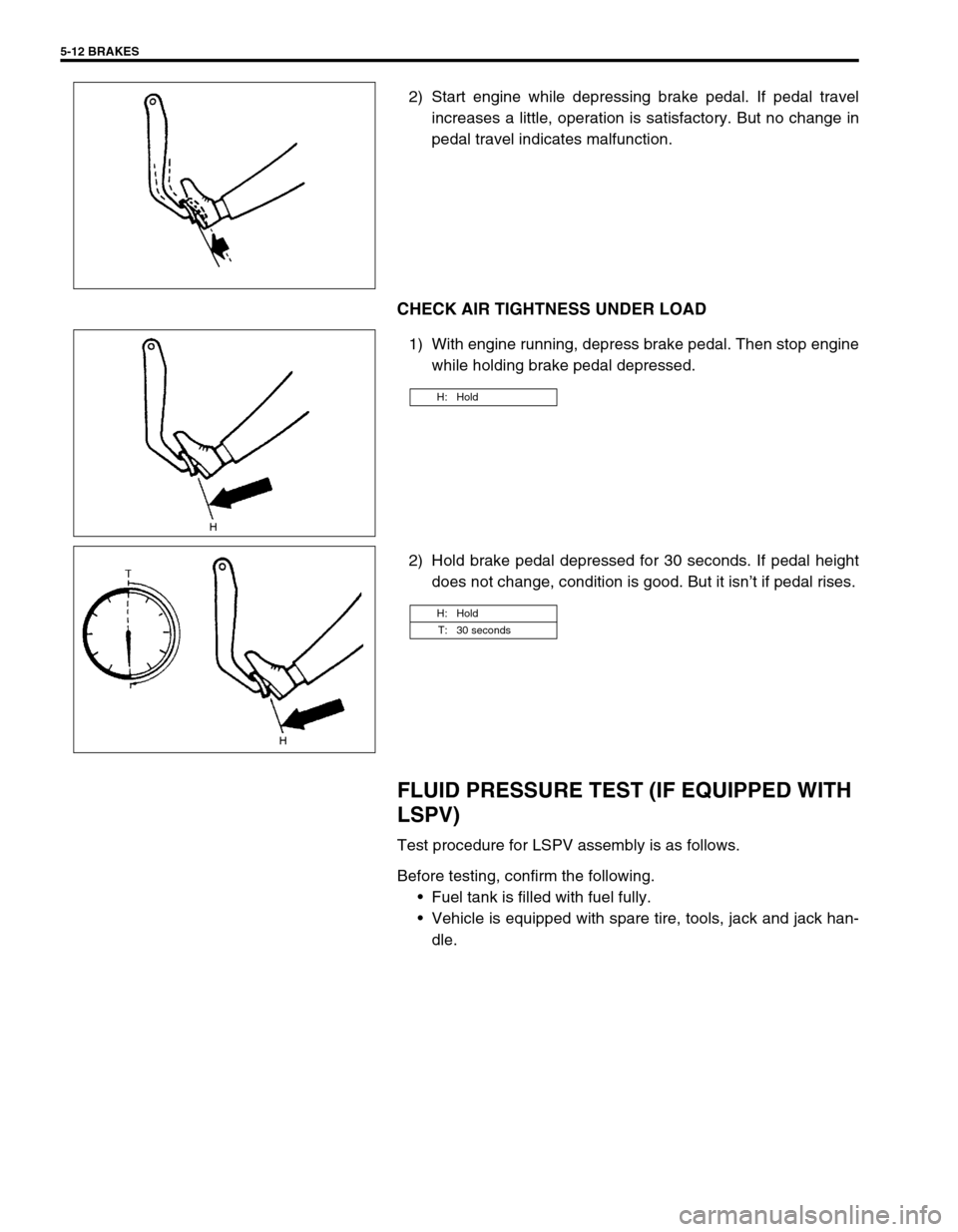
5-12 BRAKES
2) Start engine while depressing brake pedal. If pedal travel
increases a little, operation is satisfactory. But no change in
pedal travel indicates malfunction.
CHECK AIR TIGHTNESS UNDER LOAD
1) With engine running, depress brake pedal. Then stop engine
while holding brake pedal depressed.
2) Hold brake pedal depressed for 30 seconds. If pedal height
does not change, condition is good. But it isn’t if pedal rises.
FLUID PRESSURE TEST (IF EQUIPPED WITH
LSPV)
Test procedure for LSPV assembly is as follows.
Before testing, confirm the following.
Fuel tank is filled with fuel fully.
Vehicle is equipped with spare tire, tools, jack and jack han-
dle.
H: Hold
H: Hold
T: 30 seconds
Page 288 of 698
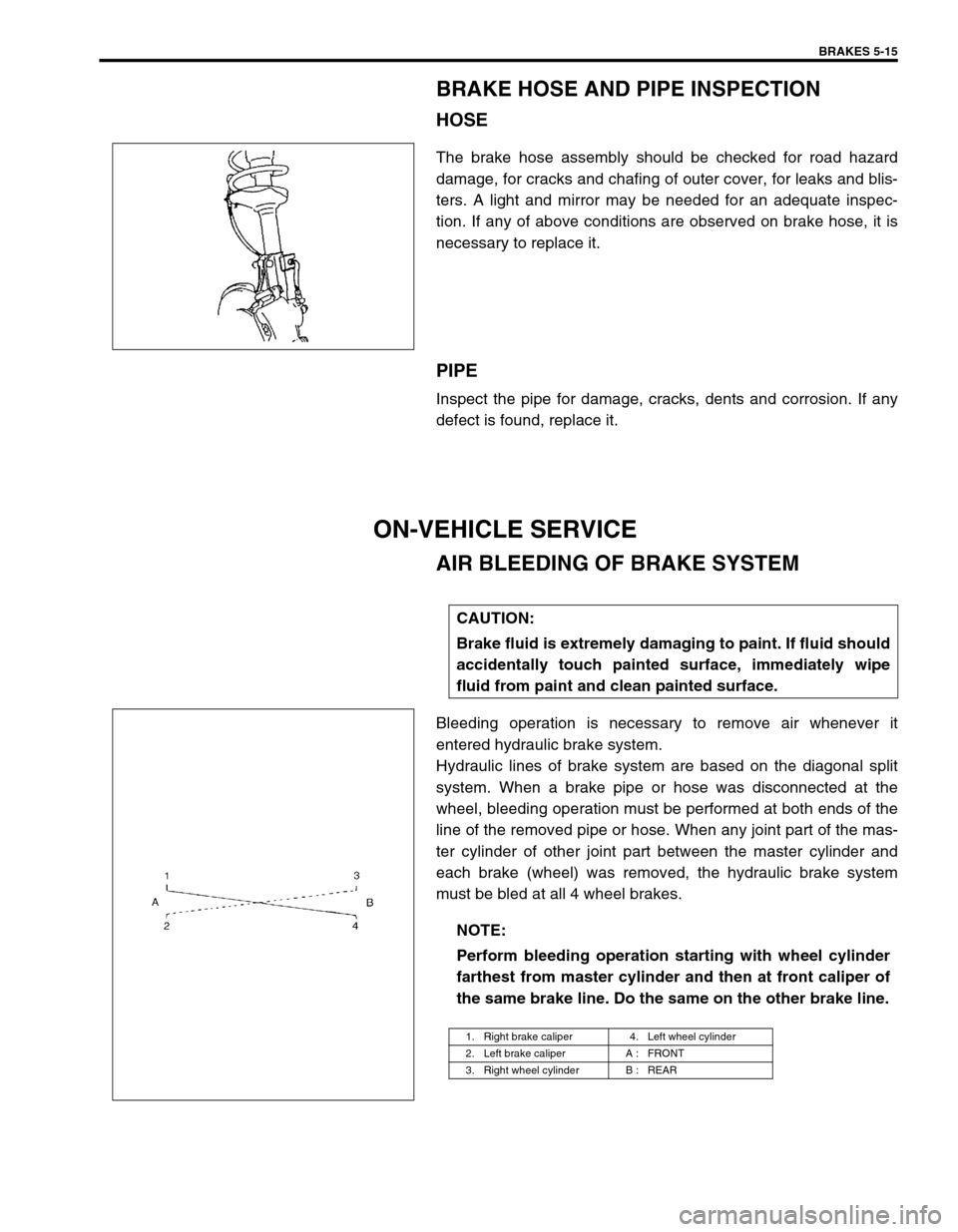
BRAKES 5-15
BRAKE HOSE AND PIPE INSPECTION
HOSE
The brake hose assembly should be checked for road hazard
damage, for cracks and chafing of outer cover, for leaks and blis-
ters. A light and mirror may be needed for an adequate inspec-
tion. If any of above conditions are observed on brake hose, it is
necessary to replace it.
PIPE
Inspect the pipe for damage, cracks, dents and corrosion. If any
defect is found, replace it.
ON-VEHICLE SERVICE
AIR BLEEDING OF BRAKE SYSTEM
Bleeding operation is necessary to remove air whenever it
entered hydraulic brake system.
Hydraulic lines of brake system are based on the diagonal split
system. When a brake pipe or hose was disconnected at the
wheel, bleeding operation must be performed at both ends of the
line of the removed pipe or hose. When any joint part of the mas-
ter cylinder of other joint part between the master cylinder and
each brake (wheel) was removed, the hydraulic brake system
must be bled at all 4 wheel brakes.
CAUTION:
Brake fluid is extremely damaging to paint. If fluid should
accidentally touch painted surface, immediately wipe
fluid from paint and clean painted surface.
NOTE:
Perform bleeding operation starting with wheel cylinder
farthest from master cylinder and then at front caliper of
the same brake line. Do the same on the other brake line.
1. Right brake caliper 4. Left wheel cylinder
2. Left brake caliper A : FRONT
3. Right wheel cylinder B : REAR
Page 311 of 698
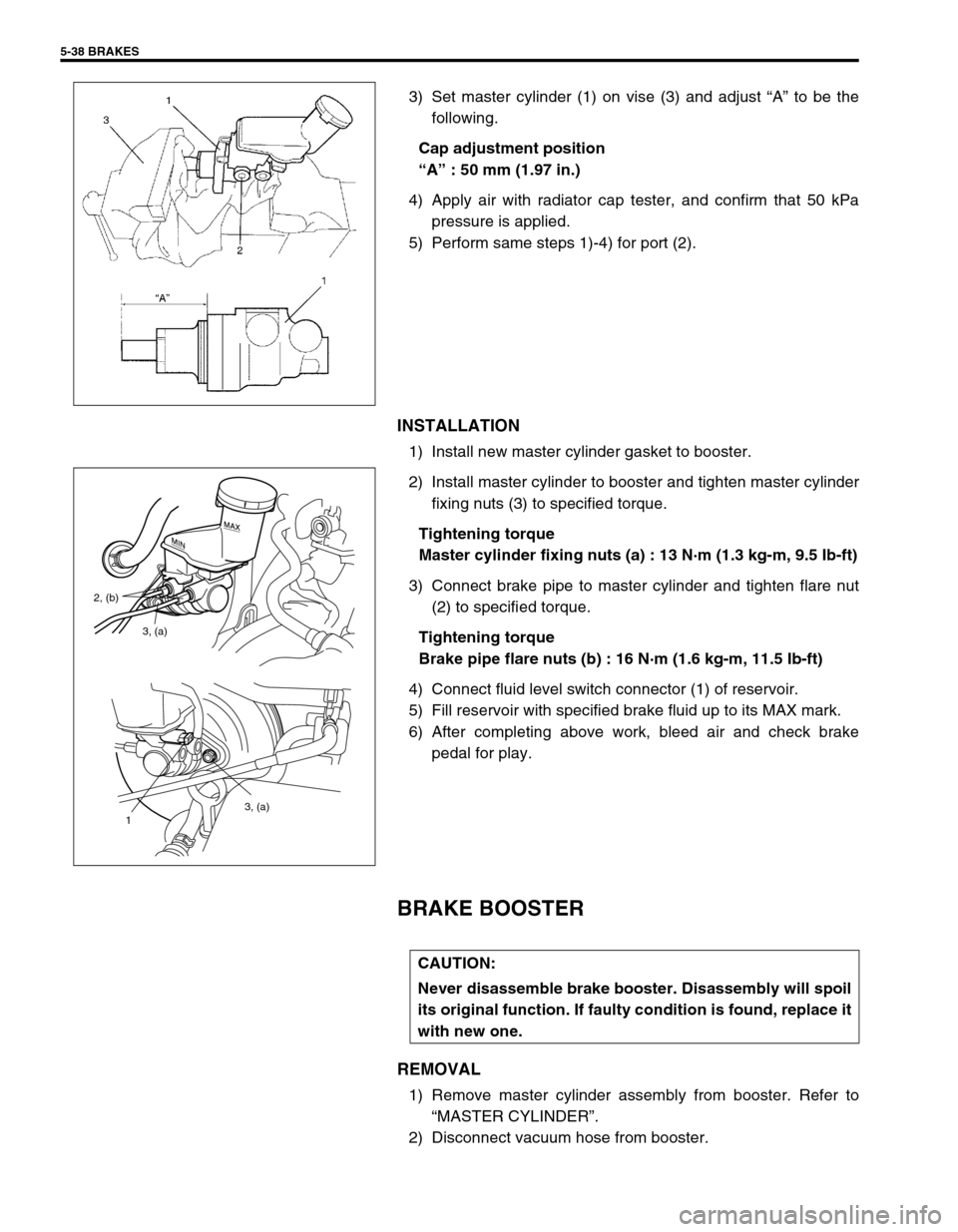
5-38 BRAKES
3) Set master cylinder (1) on vise (3) and adjust “A” to be the
following.
Cap adjustment position
“A” : 50 mm (1.97 in.)
4) Apply air with radiator cap tester, and confirm that 50 kPa
pressure is applied.
5) Perform same steps 1)-4) for port (2).
INSTALLATION
1) Install new master cylinder gasket to booster.
2) Install master cylinder to booster and tighten master cylinder
fixing nuts (3) to specified torque.
Tightening torque
Master cylinder fixing nuts (a) : 13 N·m (1.3 kg-m, 9.5 Ib-ft)
3) Connect brake pipe to master cylinder and tighten flare nut
(2) to specified torque.
Tightening torque
Brake pipe flare nuts (b) : 16 N·m (1.6 kg-m, 11.5 Ib-ft)
4) Connect fluid level switch connector (1) of reservoir.
5) Fill reservoir with specified brake fluid up to its MAX mark.
6) After completing above work, bleed air and check brake
pedal for play.
BRAKE BOOSTER
REMOVAL
1) Remove master cylinder assembly from booster. Refer to
“MASTER CYLINDER”.
2) Disconnect vacuum hose from booster.
3, (a)
1
3, (a) 2, (b)
CAUTION:
Never disassemble brake booster. Disassembly will spoil
its original function. If faulty condition is found, replace it
with new one.
Page 314 of 698
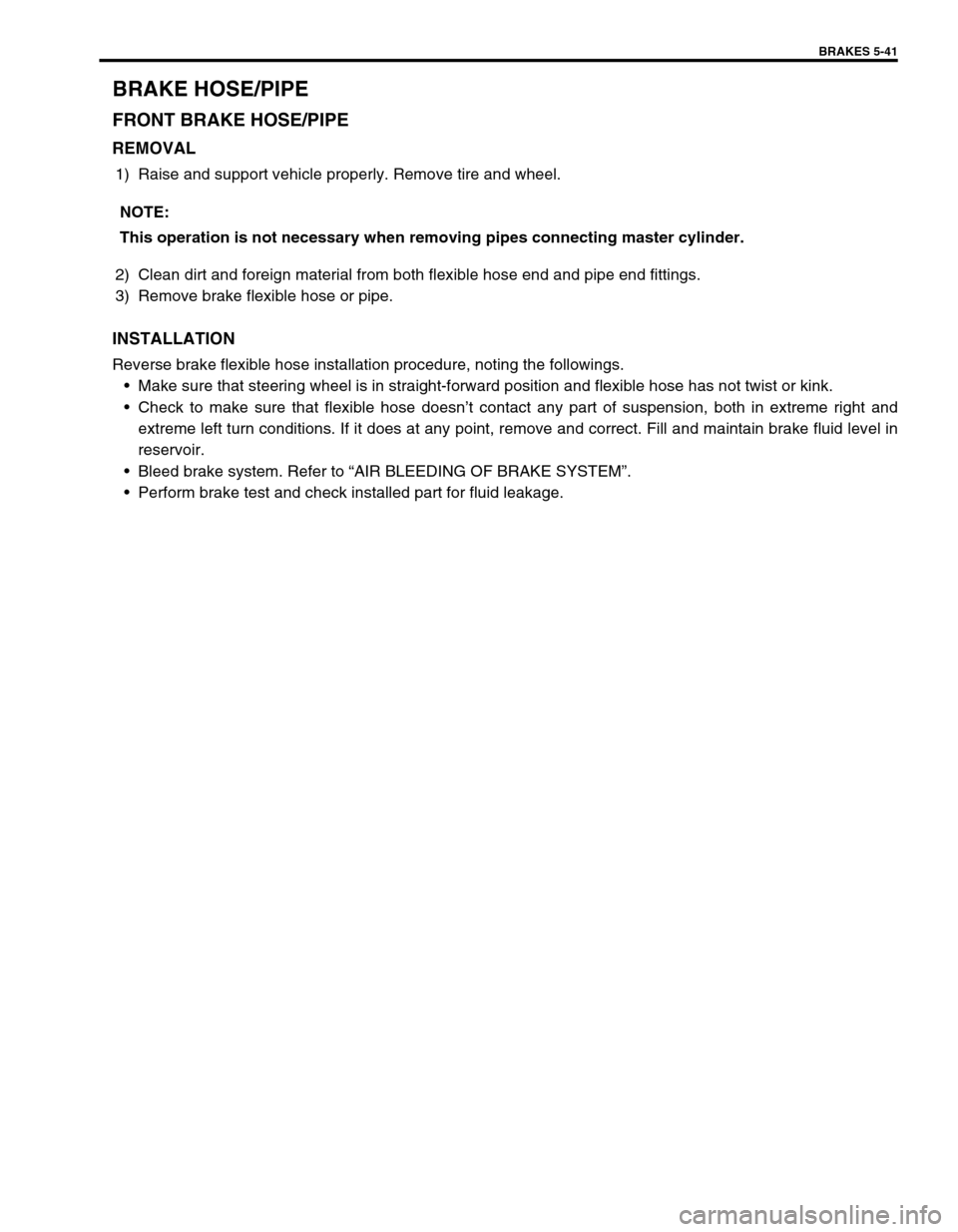
BRAKES 5-41
BRAKE HOSE/PIPE
FRONT BRAKE HOSE/PIPE
REMOVAL
1) Raise and support vehicle properly. Remove tire and wheel.
2) Clean dirt and foreign material from both flexible hose end and pipe end fittings.
3) Remove brake flexible hose or pipe.
INSTALLATION
Reverse brake flexible hose installation procedure, noting the followings.
Make sure that steering wheel is in straight-forward position and flexible hose has not twist or kink.
Check to make sure that flexible hose doesn’t contact any part of suspension, both in extreme right and
extreme left turn conditions. If it does at any point, remove and correct. Fill and maintain brake fluid level in
reservoir.
Bleed brake system. Refer to “AIR BLEEDING OF BRAKE SYSTEM”.
Perform brake test and check installed part for fluid leakage. NOTE:
This operation is not necessary when removing pipes connecting master cylinder.
Page 326 of 698
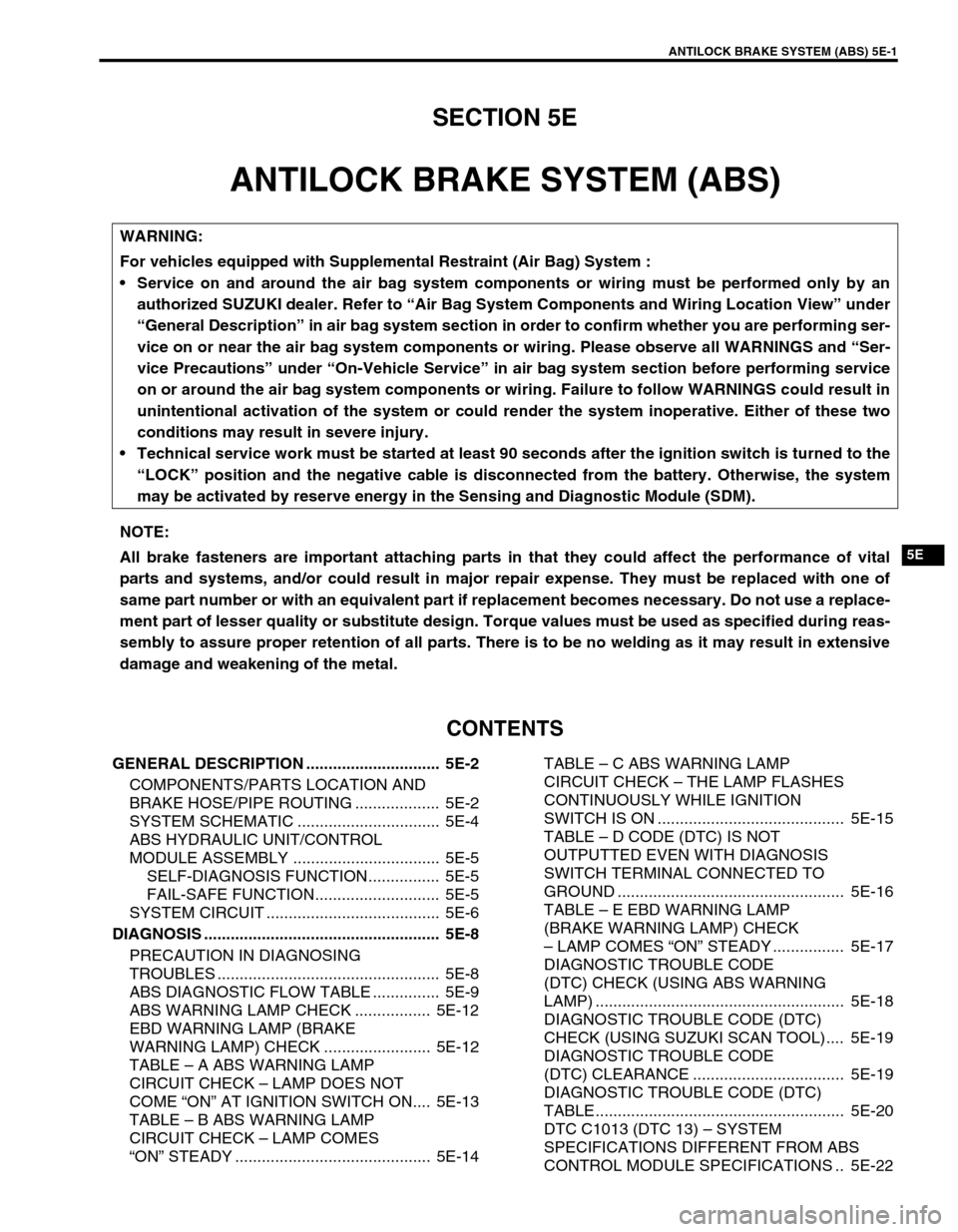
ANTILOCK BRAKE SYSTEM (ABS) 5E-1
6F1
6F2
6G
6H
6K
7A
7A1
7B1
7C1
7D
7E
7F
8A
8B
8C
8D
8E
5E
9
10
10A
10B
SECTION 5E
ANTILOCK BRAKE SYSTEM (ABS)
CONTENTS
GENERAL DESCRIPTION .............................. 5E-2
COMPONENTS/PARTS LOCATION AND
BRAKE HOSE/PIPE ROUTING ................... 5E-2
SYSTEM SCHEMATIC ................................ 5E-4
ABS HYDRAULIC UNIT/CONTROL
MODULE ASSEMBLY ................................. 5E-5
SELF-DIAGNOSIS FUNCTION................ 5E-5
FAIL-SAFE FUNCTION............................ 5E-5
SYSTEM CIRCUIT ....................................... 5E-6
DIAGNOSIS ..................................................... 5E-8
PRECAUTION IN DIAGNOSING
TROUBLES .................................................. 5E-8
ABS DIAGNOSTIC FLOW TABLE ............... 5E-9
ABS WARNING LAMP CHECK ................. 5E-12
EBD WARNING LAMP (BRAKE
WARNING LAMP) CHECK ........................ 5E-12
TABLE – A ABS WARNING LAMP
CIRCUIT CHECK – LAMP DOES NOT
COME “ON” AT IGNITION SWITCH ON.... 5E-13
TABLE – B ABS WARNING LAMP
CIRCUIT CHECK – LAMP COMES
“ON” STEADY ............................................ 5E-14TABLE – C ABS WARNING LAMP
CIRCUIT CHECK – THE LAMP FLASHES
CONTINUOUSLY WHILE IGNITION
SWITCH IS ON .......................................... 5E-15
TABLE – D CODE (DTC) IS NOT
OUTPUTTED EVEN WITH DIAGNOSIS
SWITCH TERMINAL CONNECTED TO
GROUND ................................................... 5E-16
TABLE – E EBD WARNING LAMP
(BRAKE WARNING LAMP) CHECK
– LAMP COMES “ON” STEADY ................ 5E-17
DIAGNOSTIC TROUBLE CODE
(DTC) CHECK (USING ABS WARNING
LAMP) ........................................................ 5E-18
DIAGNOSTIC TROUBLE CODE (DTC)
CHECK (USING SUZUKI SCAN TOOL).... 5E-19
DIAGNOSTIC TROUBLE CODE
(DTC) CLEARANCE .................................. 5E-19
DIAGNOSTIC TROUBLE CODE (DTC)
TABLE........................................................ 5E-20
DTC C1013 (DTC 13) – SYSTEM
SPECIFICATIONS DIFFERENT FROM ABS
CONTROL MODULE SPECIFICATIONS .. 5E-22 WARNING:
For vehicles equipped with Supplemental Restraint (Air Bag) System :
Service on and around the air bag system components or wiring must be performed only by an
authorized SUZUKI dealer. Refer to “Air Bag System Components and Wiring Location View” under
“General Description” in air bag system section in order to confirm whether you are performing ser-
vice on or near the air bag system components or wiring. Please observe all WARNINGS and “Ser-
vice Precautions” under “On-Vehicle Service” in air bag system section before performing service
on or around the air bag system components or wiring. Failure to follow WARNINGS could result in
unintentional activation of the system or could render the system inoperative. Either of these two
conditions may result in severe injury.
Technical service work must be started at least 90 seconds after the ignition switch is turned to the
“LOCK” position and the negative cable is disconnected from the battery. Otherwise, the system
may be activated by reserve energy in the Sensing and Diagnostic Module (SDM).
NOTE:
All brake fasteners are important attaching parts in that they could affect the performance of vital
parts and systems, and/or could result in major repair expense. They must be replaced with one of
same part number or with an equivalent part if replacement becomes necessary. Do not use a replace-
ment part of lesser quality or substitute design. Torque values must be used as specified during reas-
sembly to assure proper retention of all parts. There is to be no welding as it may result in extensive
damage and weakening of the metal.
Page 336 of 698
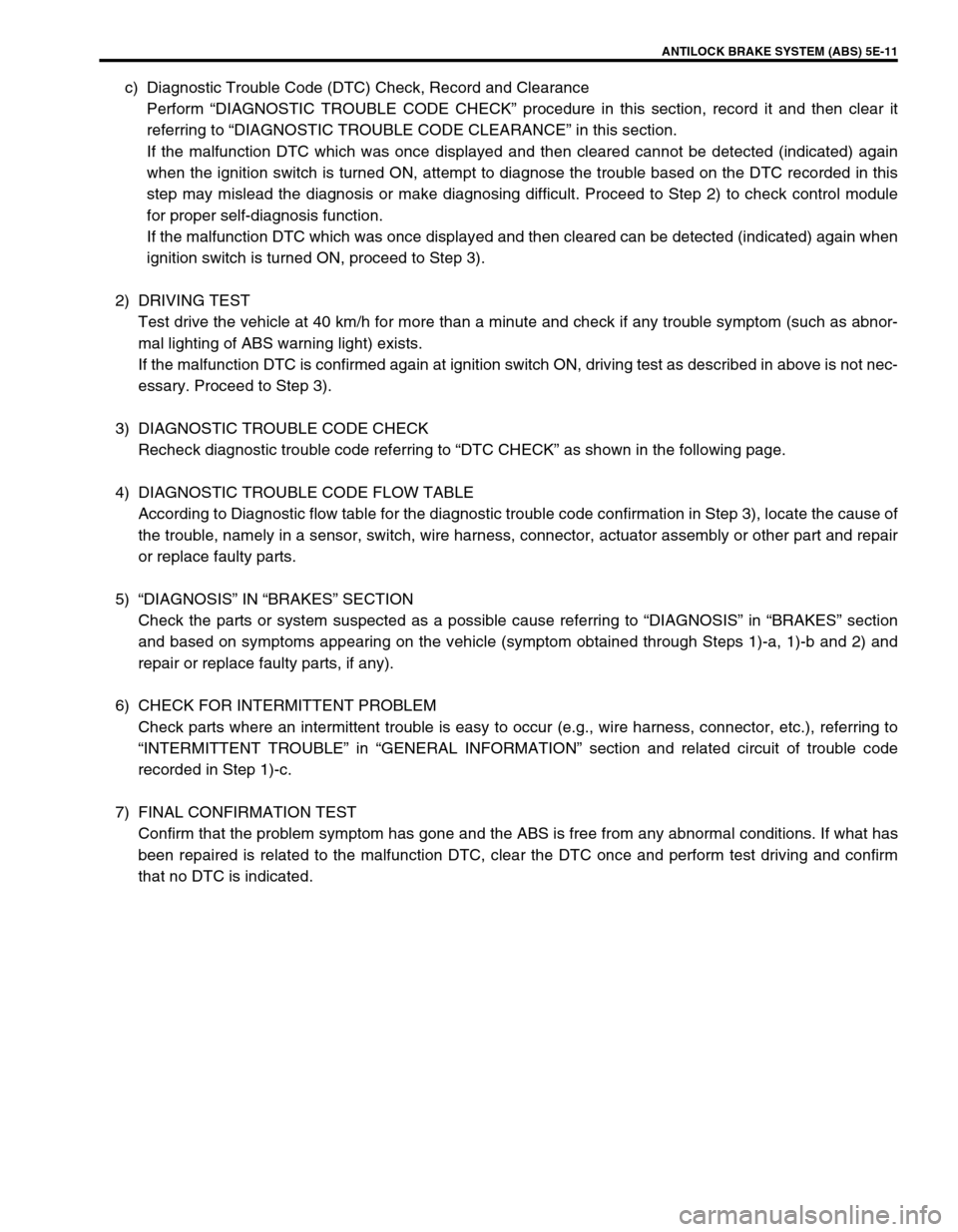
ANTILOCK BRAKE SYSTEM (ABS) 5E-11
c) Diagnostic Trouble Code (DTC) Check, Record and Clearance
Perform “DIAGNOSTIC TROUBLE CODE CHECK” procedure in this section, record it and then clear it
referring to “DIAGNOSTIC TROUBLE CODE CLEARANCE” in this section.
If the malfunction DTC which was once displayed and then cleared cannot be detected (indicated) again
when the ignition switch is turned ON, attempt to diagnose the trouble based on the DTC recorded in this
step may mislead the diagnosis or make diagnosing difficult. Proceed to Step 2) to check control module
for proper self-diagnosis function.
If the malfunction DTC which was once displayed and then cleared can be detected (indicated) again when
ignition switch is turned ON, proceed to Step 3).
2) DRIVING TEST
Test drive the vehicle at 40 km/h for more than a minute and check if any trouble symptom (such as abnor-
mal lighting of ABS warning light) exists.
If the malfunction DTC is confirmed again at ignition switch ON, driving test as described in above is not nec-
essary. Proceed to Step 3).
3) DIAGNOSTIC TROUBLE CODE CHECK
Recheck diagnostic trouble code referring to “DTC CHECK” as shown in the following page.
4) DIAGNOSTIC TROUBLE CODE FLOW TABLE
According to Diagnostic flow table for the diagnostic trouble code confirmation in Step 3), locate the cause of
the trouble, namely in a sensor, switch, wire harness, connector, actuator assembly or other part and repair
or replace faulty parts.
5)“DIAGNOSIS” IN “BRAKES” SECTION
Check the parts or system suspected as a possible cause referring to “DIAGNOSIS” in “BRAKES” section
and based on symptoms appearing on the vehicle (symptom obtained through Steps 1)-a, 1)-b and 2) and
repair or replace faulty parts, if any).
6) CHECK FOR INTERMITTENT PROBLEM
Check parts where an intermittent trouble is easy to occur (e.g., wire harness, connector, etc.), referring to
“INTERMITTENT TROUBLE” in “GENERAL INFORMATION” section and related circuit of trouble code
recorded in Step 1)-c.
7) FINAL CONFIRMATION TEST
Confirm that the problem symptom has gone and the ABS is free from any abnormal conditions. If what has
been repaired is related to the malfunction DTC, clear the DTC once and perform test driving and confirm
that no DTC is indicated.
Page 338 of 698
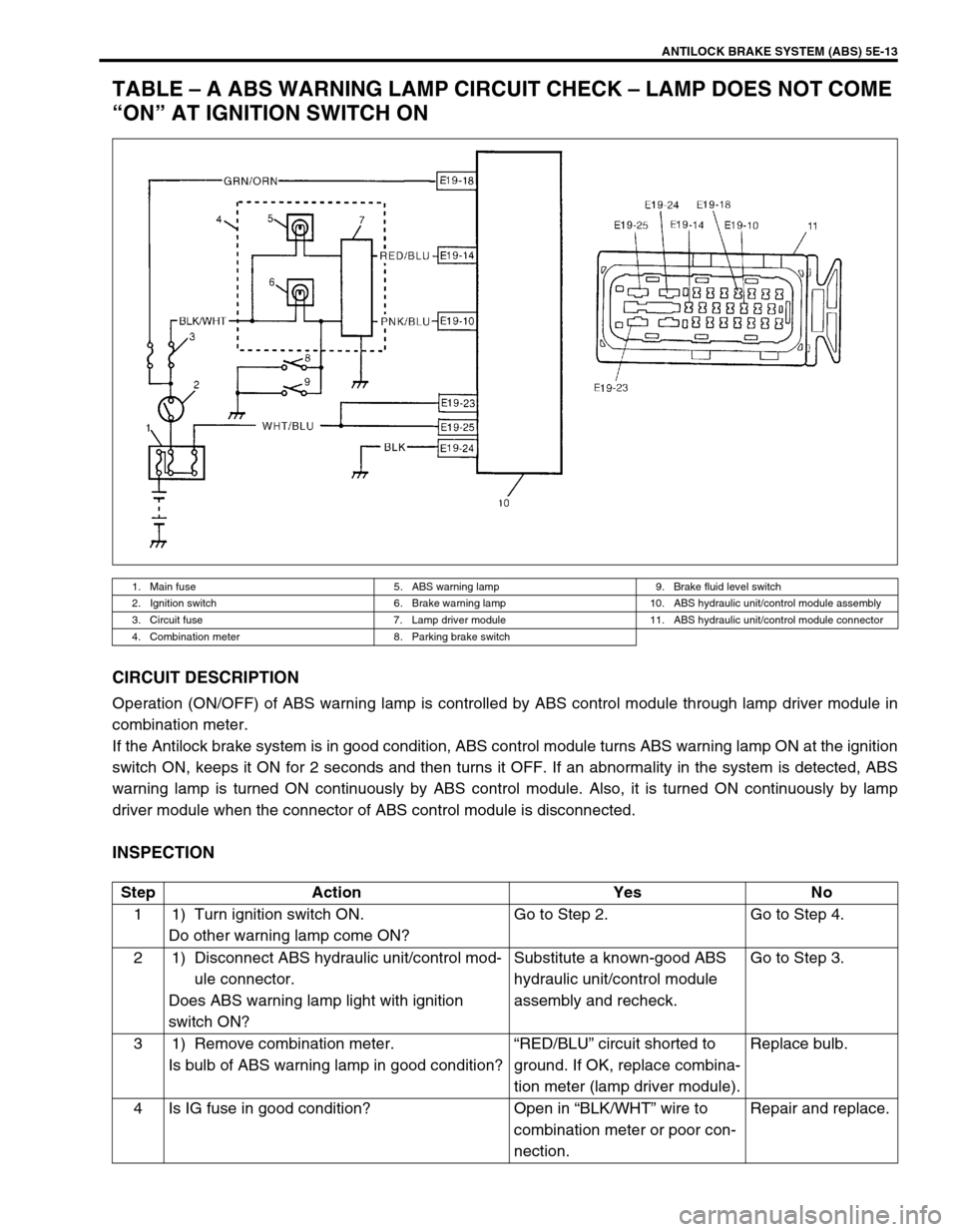
ANTILOCK BRAKE SYSTEM (ABS) 5E-13
TABLE – A ABS WARNING LAMP CIRCUIT CHECK – LAMP DOES NOT COME
“ON” AT IGNITION SWITCH ON
CIRCUIT DESCRIPTION
Operation (ON/OFF) of ABS warning lamp is controlled by ABS control module through lamp driver module in
combination meter.
If the Antilock brake system is in good condition, ABS control module turns ABS warning lamp ON at the ignition
switch ON, keeps it ON for 2 seconds and then turns it OFF. If an abnormality in the system is detected, ABS
warning lamp is turned ON continuously by ABS control module. Also, it is turned ON continuously by lamp
driver module when the connector of ABS control module is disconnected.
INSPECTION
1. Main fuse 5. ABS warning lamp 9. Brake fluid level switch
2. Ignition switch 6. Brake warning lamp 10. ABS hydraulic unit/control module assembly
3. Circuit fuse 7. Lamp driver module 11. ABS hydraulic unit/control module connector
4. Combination meter 8. Parking brake switch
Step Action Yes No
1 1) Turn ignition switch ON.
Do other warning lamp come ON?Go to Step 2. Go to Step 4.
2 1) Disconnect ABS hydraulic unit/control mod-
ule connector.
Does ABS warning lamp light with ignition
switch ON?Substitute a known-good ABS
hydraulic unit/control module
assembly and recheck.Go to Step 3.
3 1) Remove combination meter.
Is bulb of ABS warning lamp in good condition?“RED/BLU” circuit shorted to
ground. If OK, replace combina-
tion meter (lamp driver module).Replace bulb.
4 Is IG fuse in good condition? Open in “BLK/WHT” wire to
combination meter or poor con-
nection.Repair and replace.
Page 341 of 698

5E-16 ANTILOCK BRAKE SYSTEM (ABS)
TABLE – D CODE (DTC) IS NOT OUTPUTTED EVEN WITH DIAGNOSIS
SWITCH TERMINAL CONNECTED TO GROUND
CIRCUIT DESCRIPTION
When diagnosis switch terminal is connected to ground with ignition switch turned ON, the ABS control module
outputs diagnostic trouble code by flashing ABS warning lamp.
INSPECTION
1. ABS warning lamp in combination meter 3. Diagnosis monitor coupler 3-2. Diagnosis ground terminal
2. ABS hydraulic unit/control module assembly 3-1. Diagnosis switch terminal 4. ABS hydraulic unit/control module connector
Step Action Yes No
1 Is it shorted diagnosis switch terminal and
ground terminal by service wire properly?Go to Step 2. Connect service wire
securely.
2 1) Disconnect service wire.
2) Disconnect ABS hydraulic unit/control mod-
ule connector.
3) Measure resistance between diagnosis
switch terminal and connector terminal
“E19-12”.
Is it infinite (∞)?“PNK” circuit open. Go to Step 3.
3 1) Measure resistance between ground termi-
nal of monitor coupler and body ground.
Is continuity indicated?Go to Step 4.“BLK” circuit open or poor
connection.
4 1) Check for proper connection to ABS
hydraulic unit/control module at terminal
“E19-12”.
2) If OK, then check ABS warning lamp circuit
referring to TABLE A, B and C.
Is it in good condition?Substitute a known-good
ABS hydraulic with/control
module assembly and
recheck.Repair “ABS” warning
lamp circuit.
Page 349 of 698
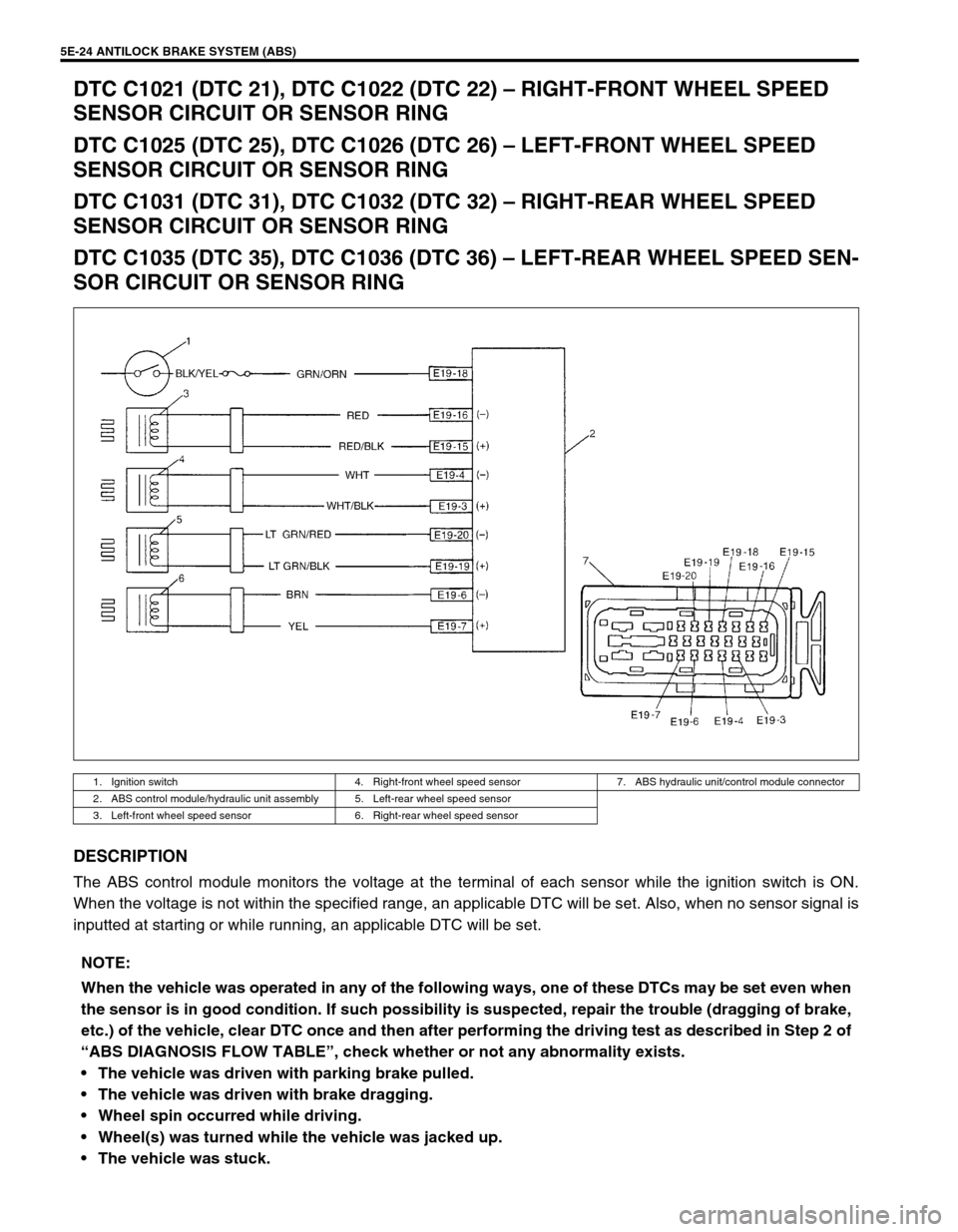
5E-24 ANTILOCK BRAKE SYSTEM (ABS)
DTC C1021 (DTC 21), DTC C1022 (DTC 22) – RIGHT-FRONT WHEEL SPEED
SENSOR CIRCUIT OR SENSOR RING
DTC C1025 (DTC 25), DTC C1026 (DTC 26) – LEFT-FRONT WHEEL SPEED
SENSOR CIRCUIT OR SENSOR RING
DTC C1031 (DTC 31), DTC C1032 (DTC 32) – RIGHT-REAR WHEEL SPEED
SENSOR CIRCUIT OR SENSOR RING
DTC C1035 (DTC 35), DTC C1036 (DTC 36) – LEFT-REAR WHEEL SPEED SEN-
SOR CIRCUIT OR SENSOR RING
DESCRIPTION
The ABS control module monitors the voltage at the terminal of each sensor while the ignition switch is ON.
When the voltage is not within the specified range, an applicable DTC will be set. Also, when no sensor signal is
inputted at starting or while running, an applicable DTC will be set.
1. Ignition switch 4. Right-front wheel speed sensor 7. ABS hydraulic unit/control module connector
2. ABS control module/hydraulic unit assembly 5. Left-rear wheel speed sensor
3. Left-front wheel speed sensor 6. Right-rear wheel speed sensor
NOTE:
When the vehicle was operated in any of the following ways, one of these DTCs may be set even when
the sensor is in good condition. If such possibility is suspected, repair the trouble (dragging of brake,
etc.) of the vehicle, clear DTC once and then after performing the driving test as described in Step 2 of
“ABS DIAGNOSIS FLOW TABLE”, check whether or not any abnormality exists.
The vehicle was driven with parking brake pulled.
The vehicle was driven with brake dragging.
Wheel spin occurred while driving.
Wheel(s) was turned while the vehicle was jacked up.
The vehicle was stuck.