air condition SUZUKI SWIFT 2000 1.G RG413 Service Workshop Manual
[x] Cancel search | Manufacturer: SUZUKI, Model Year: 2000, Model line: SWIFT, Model: SUZUKI SWIFT 2000 1.GPages: 698, PDF Size: 16.01 MB
Page 429 of 698
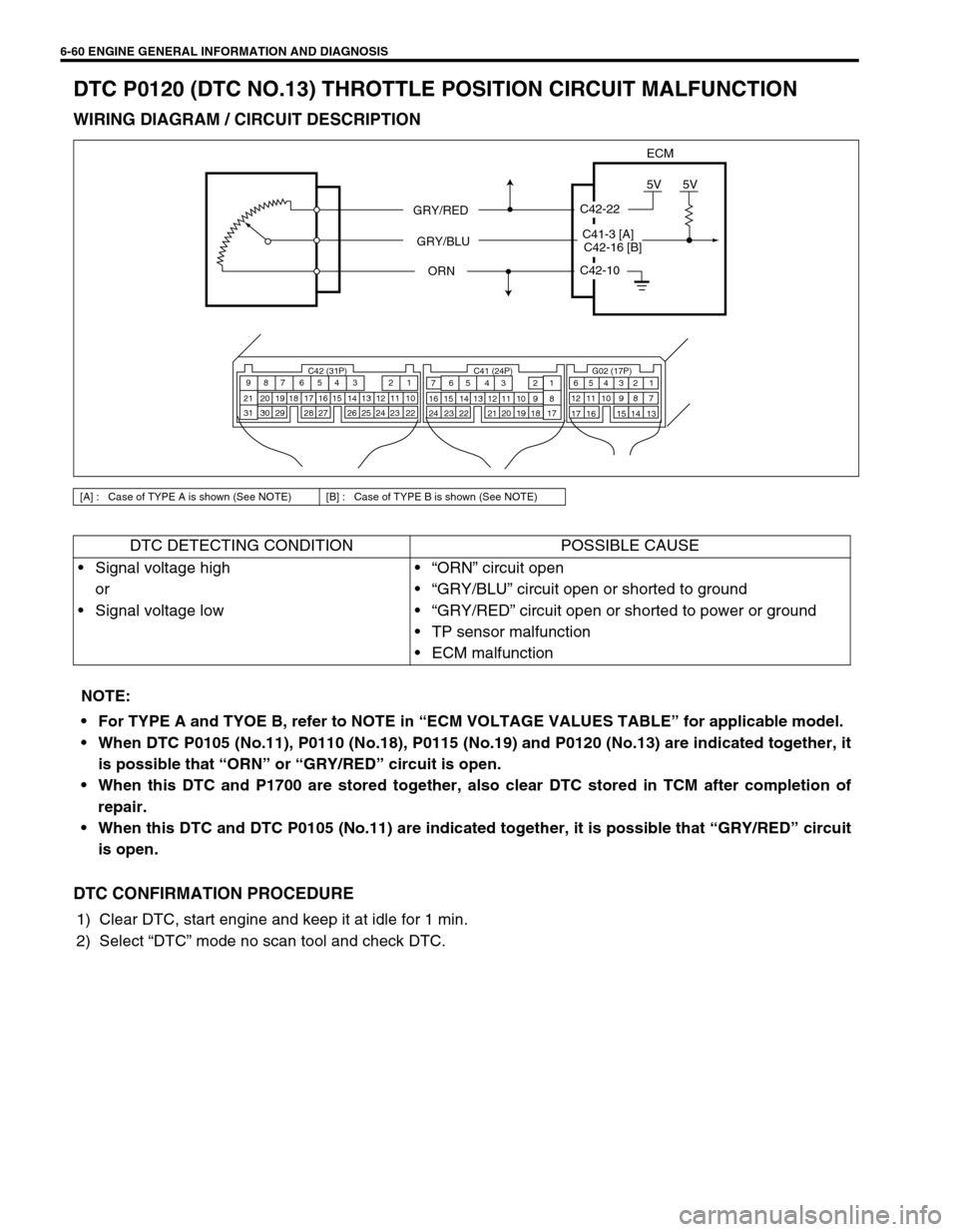
6-60 ENGINE GENERAL INFORMATION AND DIAGNOSIS
DTC P0120 (DTC NO.13) THROTTLE POSITION CIRCUIT MALFUNCTION
WIRING DIAGRAM / CIRCUIT DESCRIPTION
DTC CONFIRMATION PROCEDURE
1) Clear DTC, start engine and keep it at idle for 1 min.
2) Select “DTC” mode no scan tool and check DTC.
[A] : Case of TYPE A is shown (See NOTE) [B] : Case of TYPE B is shown (See NOTE)
DTC DETECTING CONDITION POSSIBLE CAUSE
Signal voltage high
or
Signal voltage low“ORN” circuit open
“GRY/BLU” circuit open or shorted to ground
“GRY/RED” circuit open or shorted to power or ground
TP sensor malfunction
ECM malfunction
C42-10
C42-22
5V5V
ECM
GRY/RED
GRY/BLU
ORN
C42 (31P) C41 (24P) G02 (17P)1 2 3 4 5 6 7 8 9
10 11 12 13 14 15 16 17 18 19 20 21
22 23 24 25 26 28 27 29 30 315 6
1 2 3 4 5 6 7
11 12
9 10 11 13 12 14 15 16
16 171 2
7 8
13 14 3 4
9 10
15 17 188
19 20 21 22 23 24
C42-16 [B] C41-3 [A]
NOTE:
For TYPE A and TYOE B, refer to NOTE in “ECM VOLTAGE VALUES TABLE” for applicable model.
When DTC P0105 (No.11), P0110 (No.18), P0115 (No.19) and P0120 (No.13) are indicated together, it
is possible that “ORN” or “GRY/RED” circuit is open.
When this DTC and P1700 are stored together, also clear DTC stored in TCM after completion of
repair.
When this DTC and DTC P0105 (No.11) are indicated together, it is possible that “GRY/RED” circuit
is open.
Page 432 of 698
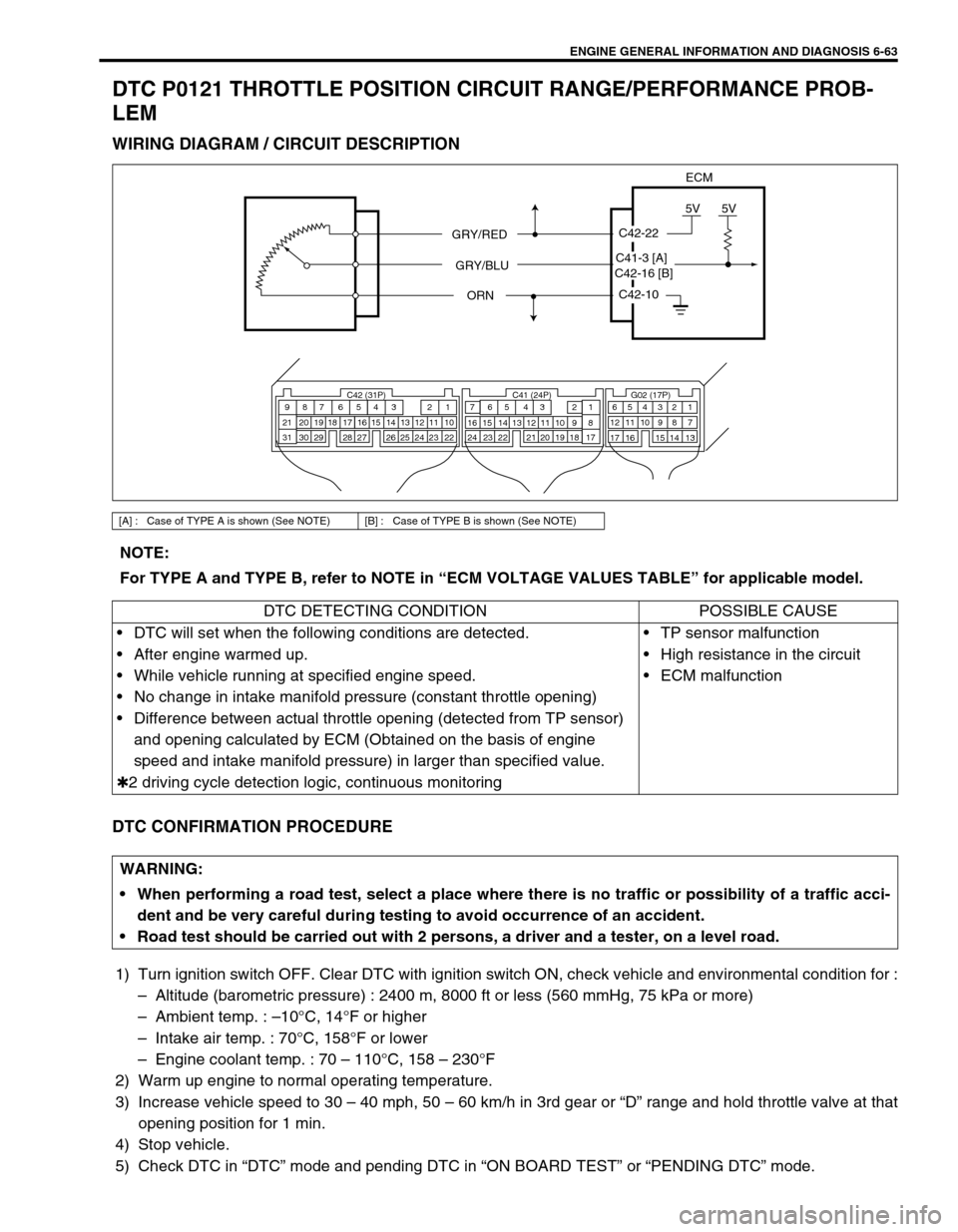
ENGINE GENERAL INFORMATION AND DIAGNOSIS 6-63
DTC P0121 THROTTLE POSITION CIRCUIT RANGE/PERFORMANCE PROB-
LEM
WIRING DIAGRAM / CIRCUIT DESCRIPTION
DTC CONFIRMATION PROCEDURE
1) Turn ignition switch OFF. Clear DTC with ignition switch ON, check vehicle and environmental condition for :
–Altitude (barometric pressure) : 2400 m, 8000 ft or less (560 mmHg, 75 kPa or more)
–Ambient temp. : –10°C, 14°F or higher
–Intake air temp. : 70°C, 158°F or lower
–Engine coolant temp. : 70 – 110°C, 158 – 230°F
2) Warm up engine to normal operating temperature.
3) Increase vehicle speed to 30 – 40 mph, 50 – 60 km/h in 3rd gear or “D” range and hold throttle valve at that
opening position for 1 min.
4) Stop vehicle.
5) Check DTC in “DTC” mode and pending DTC in “ON BOARD TEST” or “PENDING DTC” mode.
[A] : Case of TYPE A is shown (See NOTE) [B] : Case of TYPE B is shown (See NOTE)
C42-10
C42-22
5V5V
ECM
GRY/RED
GRY/BLU
ORN
C42 (31P) C41 (24P) G02 (17P)1 2 3 4 5 6 7 8 9
10 11 12 13 14 15 16 17 18 19 20 21
22 23 24 25 26 28 27 29 30 315 6
1 2 3 4 5 6 7
11 12
9 10 11 13 12 14 15 16
16 171 2
7 8
13 14 3 4
9 10
15 17 188
19 20 21 22 23 24
C42-16 [B]C41-3 [A]
NOTE:
For TYPE A and TYPE B, refer to NOTE in “ECM VOLTAGE VALUES TABLE” for applicable model.
DTC DETECTING CONDITION POSSIBLE CAUSE
DTC will set when the following conditions are detected.
After engine warmed up.
While vehicle running at specified engine speed.
No change in intake manifold pressure (constant throttle opening)
Difference between actual throttle opening (detected from TP sensor)
and opening calculated by ECM (Obtained on the basis of engine
speed and intake manifold pressure) in larger than specified value.
✱2 driving cycle detection logic, continuous monitoringTP sensor malfunction
High resistance in the circuit
ECM malfunction
WARNING:
When performing a road test, select a place where there is no traffic or possibility of a traffic acci-
dent and be very careful during testing to avoid occurrence of an accident.
Road test should be carried out with 2 persons, a driver and a tester, on a level road.
Page 435 of 698
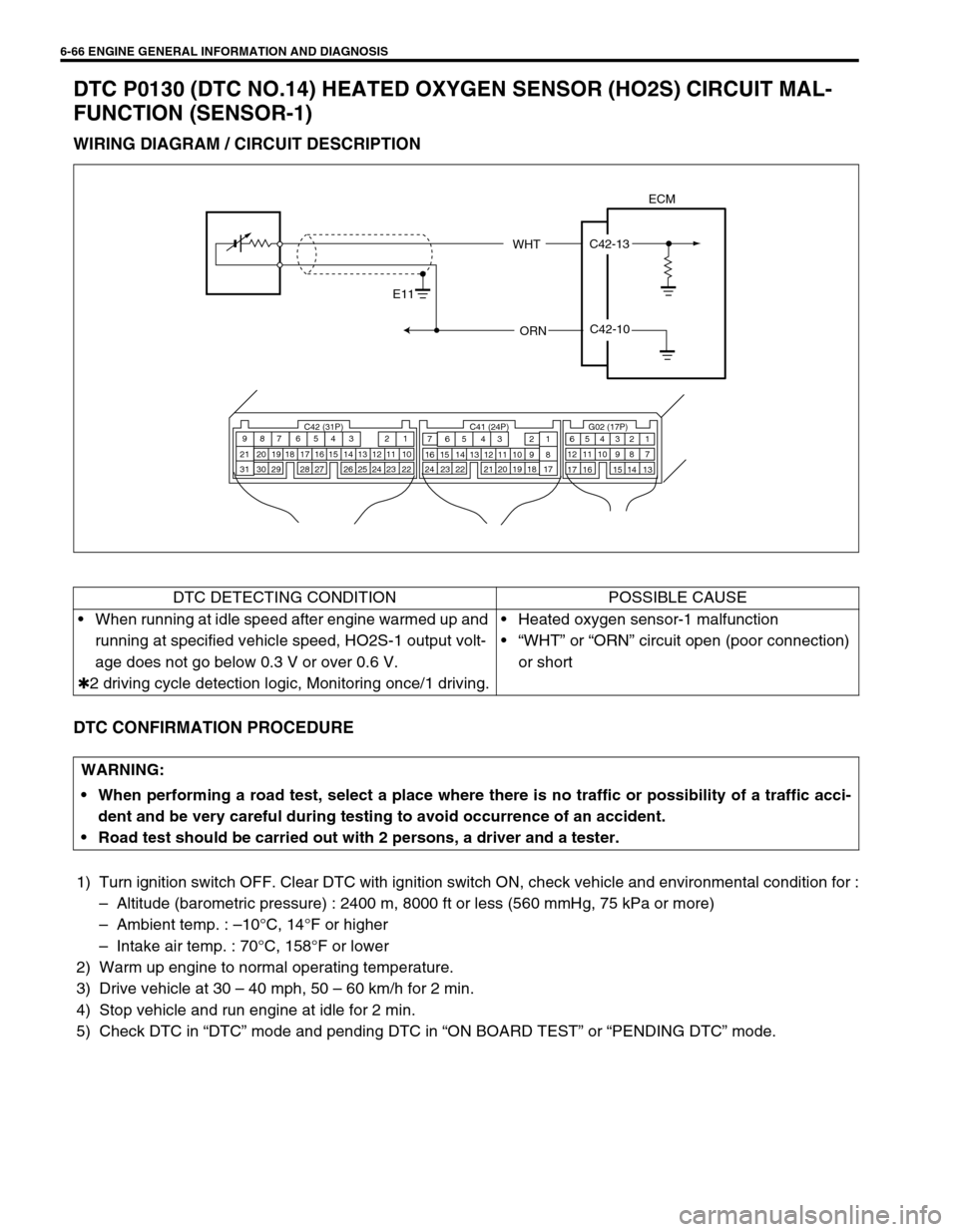
6-66 ENGINE GENERAL INFORMATION AND DIAGNOSIS
DTC P0130 (DTC NO.14) HEATED OXYGEN SENSOR (HO2S) CIRCUIT MAL-
FUNCTION (SENSOR-1)
WIRING DIAGRAM / CIRCUIT DESCRIPTION
DTC CONFIRMATION PROCEDURE
1) Turn ignition switch OFF. Clear DTC with ignition switch ON, check vehicle and environmental condition for :
–Altitude (barometric pressure) : 2400 m, 8000 ft or less (560 mmHg, 75 kPa or more)
–Ambient temp. : –10°C, 14°F or higher
–Intake air temp. : 70°C, 158°F or lower
2) Warm up engine to normal operating temperature.
3) Drive vehicle at 30 – 40 mph, 50 – 60 km/h for 2 min.
4) Stop vehicle and run engine at idle for 2 min.
5) Check DTC in “DTC” mode and pending DTC in “ON BOARD TEST” or “PENDING DTC” mode.
ECM
WHT
ORNC42-10 C42-13
E11
C42 (31P) C41 (24P) G02 (17P)1 2 3 4 5 6 7 8 9
10 11 12 13 14 15 16 17 18 19 20 21
22 23 24 25 26 28 27 29 30 315 6
1 2 3 4 5 6 7
11 12
9 10 11 13 12 14 15 16
16 171 2
7 8
13 14 3 4
9 10
15 17 188
19 20 21 22 23 24
DTC DETECTING CONDITION POSSIBLE CAUSE
When running at idle speed after engine warmed up and
running at specified vehicle speed, HO2S-1 output volt-
age does not go below 0.3 V or over 0.6 V.
✱2 driving cycle detection logic, Monitoring once/1 driving.Heated oxygen sensor-1 malfunction
“WHT” or “ORN” circuit open (poor connection)
or short
WARNING:
When performing a road test, select a place where there is no traffic or possibility of a traffic acci-
dent and be very careful during testing to avoid occurrence of an accident.
Road test should be carried out with 2 persons, a driver and a tester.
Page 441 of 698
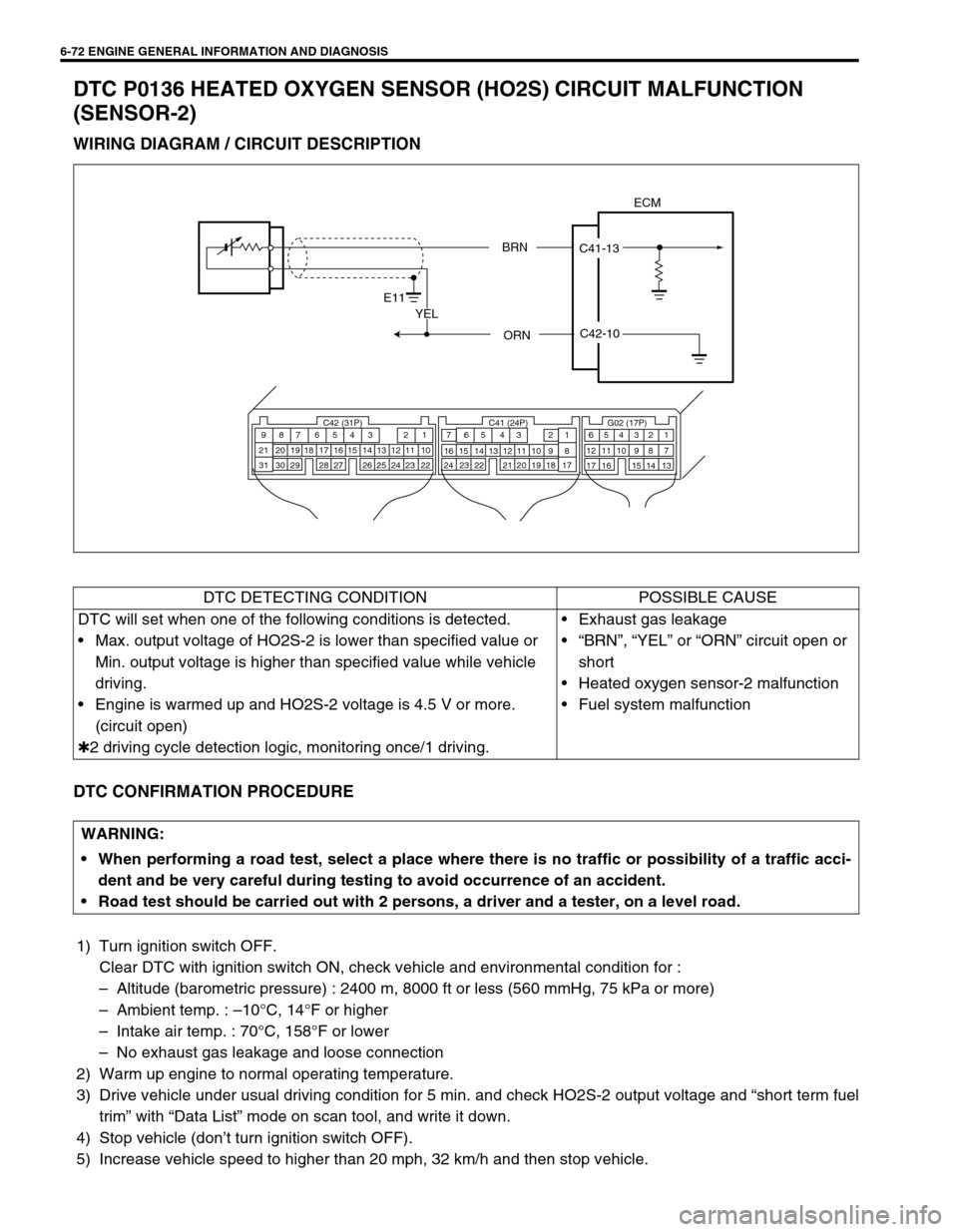
6-72 ENGINE GENERAL INFORMATION AND DIAGNOSIS
DTC P0136 HEATED OXYGEN SENSOR (HO2S) CIRCUIT MALFUNCTION
(SENSOR-2)
WIRING DIAGRAM / CIRCUIT DESCRIPTION
DTC CONFIRMATION PROCEDURE
1) Turn ignition switch OFF.
Clear DTC with ignition switch ON, check vehicle and environmental condition for :
–Altitude (barometric pressure) : 2400 m, 8000 ft or less (560 mmHg, 75 kPa or more)
–Ambient temp. : –10°C, 14°F or higher
–Intake air temp. : 70°C, 158°F or lower
–No exhaust gas leakage and loose connection
2) Warm up engine to normal operating temperature.
3) Drive vehicle under usual driving condition for 5 min. and check HO2S-2 output voltage and “short term fuel
trim” with “Data List” mode on scan tool, and write it down.
4) Stop vehicle (don’t turn ignition switch OFF).
5) Increase vehicle speed to higher than 20 mph, 32 km/h and then stop vehicle.
ECM
E11BRN
ORNC42-10 C41-13
C42 (31P) C41 (24P) G02 (17P)1 2 3 4 5 6 7 8 9
10 11 12 13 14 15 16 17 18 19 20 21
22 23 24 25 26 28 27 29 30 315 6
1 2 3 4 5 6 7
11 12
9 10 11 13 12 14 15 16
16 171 2
7 8
13 14 3 4
9 10
15 17 188
19 20 21 22 23 24
YEL
DTC DETECTING CONDITION POSSIBLE CAUSE
DTC will set when one of the following conditions is detected.
Max. output voltage of HO2S-2 is lower than specified value or
Min. output voltage is higher than specified value while vehicle
driving.
Engine is warmed up and HO2S-2 voltage is 4.5 V or more.
(circuit open)
✱2 driving cycle detection logic, monitoring once/1 driving.Exhaust gas leakage
“BRN”, “YEL” or “ORN” circuit open or
short
Heated oxygen sensor-2 malfunction
Fuel system malfunction
WARNING:
When performing a road test, select a place where there is no traffic or possibility of a traffic acci-
dent and be very careful during testing to avoid occurrence of an accident.
Road test should be carried out with 2 persons, a driver and a tester, on a level road.
Page 442 of 698
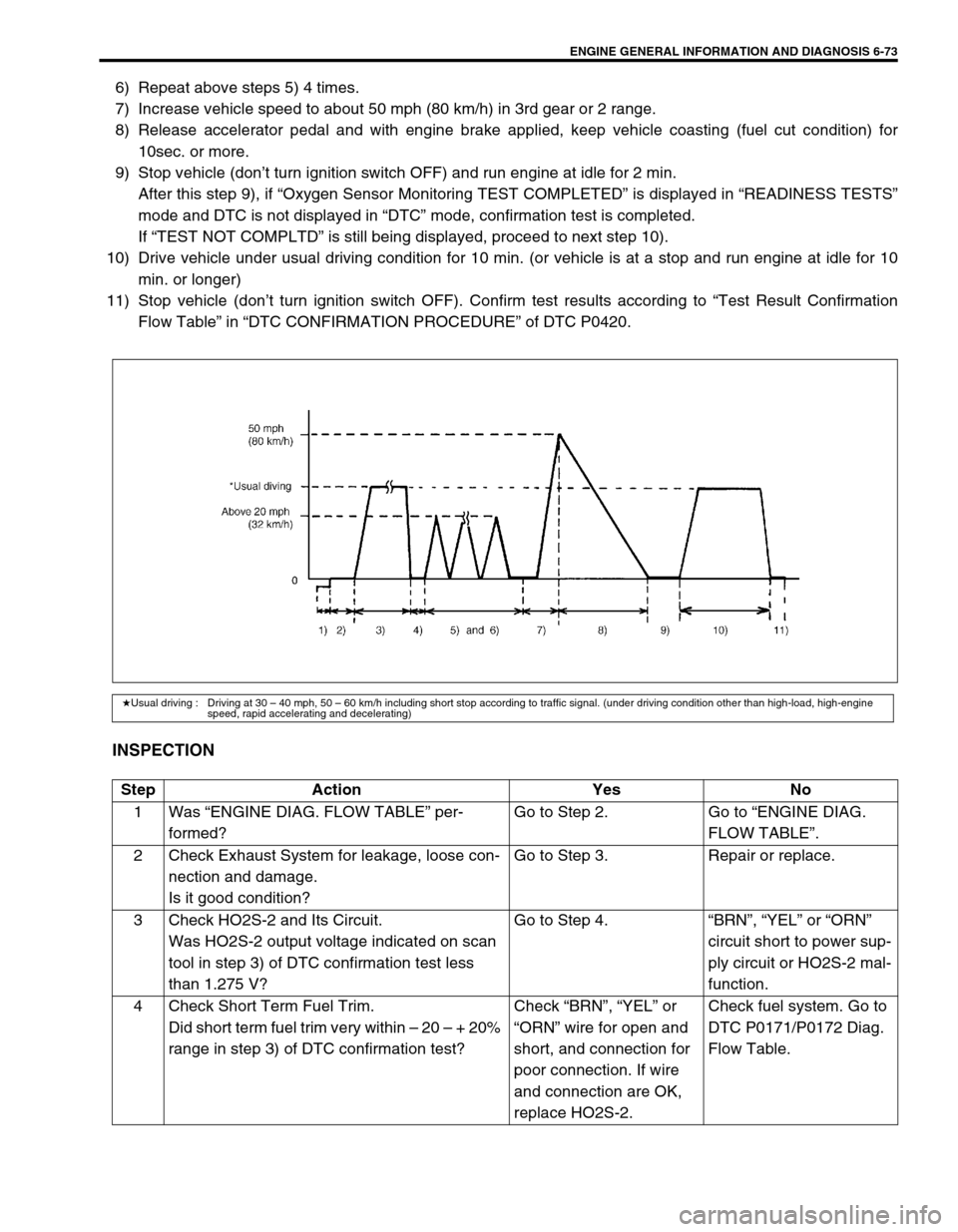
ENGINE GENERAL INFORMATION AND DIAGNOSIS 6-73
6) Repeat above steps 5) 4 times.
7) Increase vehicle speed to about 50 mph (80 km/h) in 3rd gear or 2 range.
8) Release accelerator pedal and with engine brake applied, keep vehicle coasting (fuel cut condition) for
10sec. or more.
9) Stop vehicle (don’t turn ignition switch OFF) and run engine at idle for 2 min.
After this step 9), if “Oxygen Sensor Monitoring TEST COMPLETED” is displayed in “READINESS TESTS”
mode and DTC is not displayed in “DTC” mode, confirmation test is completed.
If “TEST NOT COMPLTD” is still being displayed, proceed to next step 10).
10) Drive vehicle under usual driving condition for 10 min. (or vehicle is at a stop and run engine at idle for 10
min. or longer)
11) Stop vehicle (don’t turn ignition switch OFF). Confirm test results according to “Test Result Confirmation
Flow Table” in “DTC CONFIRMATION PROCEDURE” of DTC P0420.
INSPECTION
Usual driving : Driving at 30 – 40 mph, 50 – 60 km/h including short stop according to traffic signal. (under driving condition other than high-load, high-engine
speed, rapid accelerating and decelerating)
Step Action Yes No
1Was “ENGINE DIAG. FLOW TABLE” per-
formed?Go to Step 2. Go to “ENGINE DIAG.
FLOW TABLE”.
2 Check Exhaust System for leakage, loose con-
nection and damage.
Is it good condition?Go to Step 3. Repair or replace.
3 Check HO2S-2 and Its Circuit.
Was HO2S-2 output voltage indicated on scan
tool in step 3) of DTC confirmation test less
than 1.275 V?Go to Step 4.“BRN”, “YEL” or “ORN”
circuit short to power sup-
ply circuit or HO2S-2 mal-
function.
4 Check Short Term Fuel Trim.
Did short term fuel trim very within – 20 – + 20%
range in step 3) of DTC confirmation test?Check “BRN”, “YEL” or
“ORN” wire for open and
short, and connection for
poor connection. If wire
and connection are OK,
replace HO2S-2.Check fuel system. Go to
DTC P0171/P0172 Diag.
Flow Table.
Page 445 of 698
![SUZUKI SWIFT 2000 1.G RG413 Service Workshop Manual 6-76 ENGINE GENERAL INFORMATION AND DIAGNOSIS
DTC P0171 FUEL SYSTEM TOO LEAN
DTC P0172 FUEL SYSTEM TOO RICH
WIRING DIAGRAM / CIRCUIT DESCRIPTION
1. Injector [a] : Signal to decrease amount of fuel inj SUZUKI SWIFT 2000 1.G RG413 Service Workshop Manual 6-76 ENGINE GENERAL INFORMATION AND DIAGNOSIS
DTC P0171 FUEL SYSTEM TOO LEAN
DTC P0172 FUEL SYSTEM TOO RICH
WIRING DIAGRAM / CIRCUIT DESCRIPTION
1. Injector [a] : Signal to decrease amount of fuel inj](/img/20/7606/w960_7606-444.png)
6-76 ENGINE GENERAL INFORMATION AND DIAGNOSIS
DTC P0171 FUEL SYSTEM TOO LEAN
DTC P0172 FUEL SYSTEM TOO RICH
WIRING DIAGRAM / CIRCUIT DESCRIPTION
1. Injector [a] : Signal to decrease amount of fuel injection [f] : A/F mixture becomes leaner
2. HO2S-1 [b] : Signal to increase amount of fuel injection [g] : Oxygen concentration decreases
3. WU-TWC (Warm up-three way catalytic convec-
tor)[c] : High voltage [h] : Oxygen concentration increases
4. Sensed information [d] : Low voltage
5. ECM [e] : A/F mixture becomes richer
[a]
[b]
[f] [e] [g][d]
[h][c]
1
2 5
1
2
2
3
54
+BECM
C42-9
C42-21
C42-8 C42-31
C42-1
BLU/YEL
BLU/WHT
BLU/RED
BLK/ORN
C42-3
BLK/ORN BLU/ORN
WHT
ORNC42-10C42-13
E111
DTC DETECTING CONDITION POSSIBLE CAUSE
When one of the following conditions occurs while
engine running under closed loop condition.
Air/fuel ratio too lean
(Total fuel trim (short and long terms added) is more
than 30%)
Air/fuel ratio too rich
(Total fuel trim is less than – 30%)
✱2 driving cycle detection logic, continuous monitoring.Vacuum leaks (air drawn in).
Exhaust gas leakage.
Heated oxygen sensor-1 circuit malfunction.
Fuel pressure out of specification.
Fuel injector malfunction (clogged or leakage).
MAP sensor poor performance.
ECT sensor poor performance.
IAT sensor poor performance.
TP sensor poor performance.
EVAP control system malfunction.
PCV valve malfunction.
Page 446 of 698
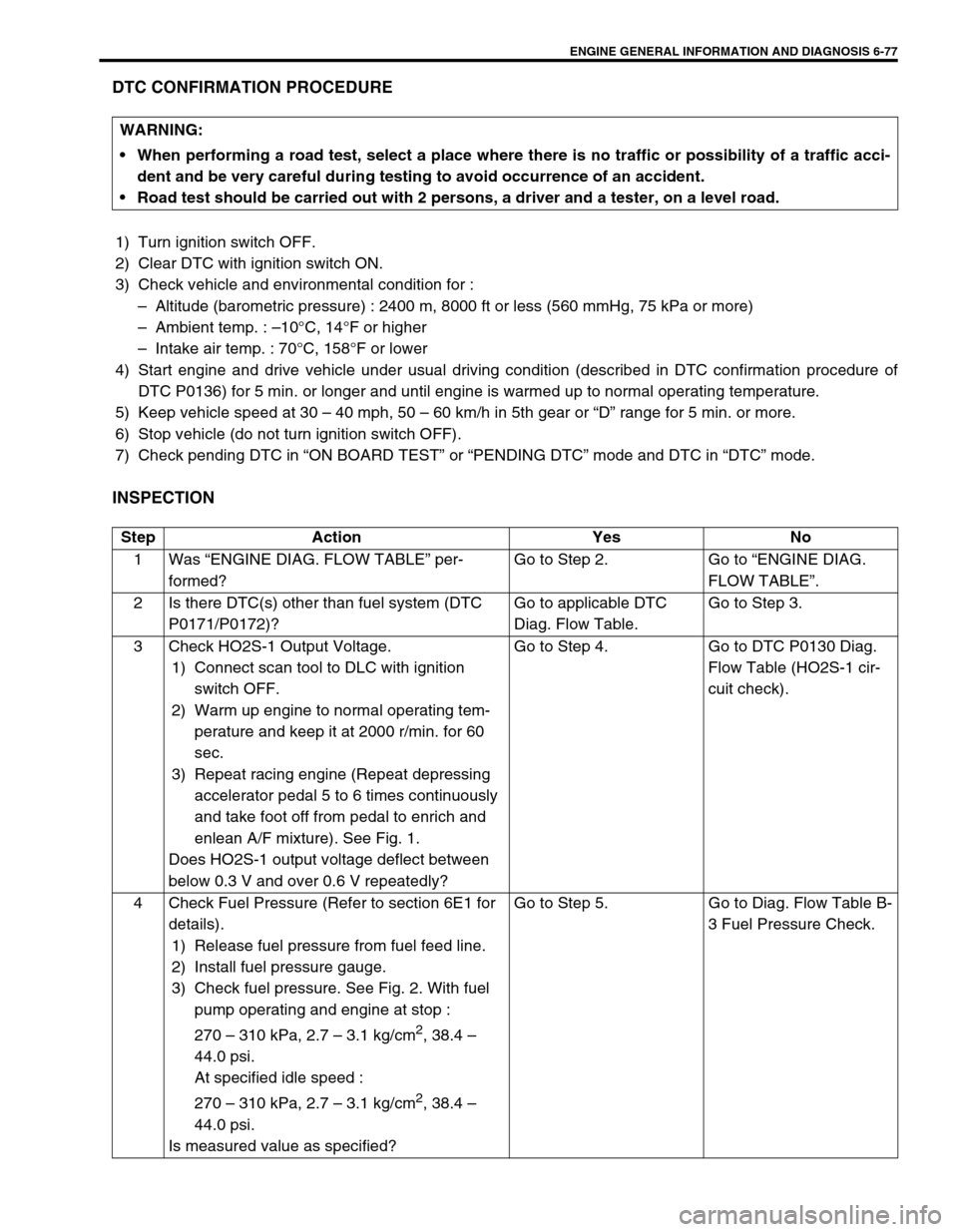
ENGINE GENERAL INFORMATION AND DIAGNOSIS 6-77
DTC CONFIRMATION PROCEDURE
1) Turn ignition switch OFF.
2) Clear DTC with ignition switch ON.
3) Check vehicle and environmental condition for :
–Altitude (barometric pressure) : 2400 m, 8000 ft or less (560 mmHg, 75 kPa or more)
–Ambient temp. : –10°C, 14°F or higher
–Intake air temp. : 70°C, 158°F or lower
4) Start engine and drive vehicle under usual driving condition (described in DTC confirmation procedure of
DTC P0136) for 5 min. or longer and until engine is warmed up to normal operating temperature.
5) Keep vehicle speed at 30 – 40 mph, 50 – 60 km/h in 5th gear or “D” range for 5 min. or more.
6) Stop vehicle (do not turn ignition switch OFF).
7) Check pending DTC in “ON BOARD TEST” or “PENDING DTC” mode and DTC in “DTC” mode.
INSPECTION
WARNING:
When performing a road test, select a place where there is no traffic or possibility of a traffic acci-
dent and be very careful during testing to avoid occurrence of an accident.
Road test should be carried out with 2 persons, a driver and a tester, on a level road.
Step Action Yes No
1Was “ENGINE DIAG. FLOW TABLE” per-
formed?Go to Step 2. Go to “ENGINE DIAG.
FLOW TABLE”.
2 Is there DTC(s) other than fuel system (DTC
P0171/P0172)?Go to applicable DTC
Diag. Flow Table.Go to Step 3.
3 Check HO2S-1 Output Voltage.
1) Connect scan tool to DLC with ignition
switch OFF.
2) Warm up engine to normal operating tem-
perature and keep it at 2000 r/min. for 60
sec.
3) Repeat racing engine (Repeat depressing
accelerator pedal 5 to 6 times continuously
and take foot off from pedal to enrich and
enlean A/F mixture). See Fig. 1.
Does HO2S-1 output voltage deflect between
below 0.3 V and over 0.6 V repeatedly?Go to Step 4. Go to DTC P0130 Diag.
Flow Table (HO2S-1 cir-
cuit check).
4 Check Fuel Pressure (Refer to section 6E1 for
details).
1) Release fuel pressure from fuel feed line.
2) Install fuel pressure gauge.
3) Check fuel pressure. See Fig. 2. With fuel
pump operating and engine at stop :
270 – 310 kPa, 2.7 – 3.1 kg/cm
2, 38.4 –
44.0 psi.
At specified idle speed :
270 – 310 kPa, 2.7 – 3.1 kg/cm
2, 38.4 –
44.0 psi.
Is measured value as specified?Go to Step 5. Go to Diag. Flow Table B-
3 Fuel Pressure Check.
Page 447 of 698
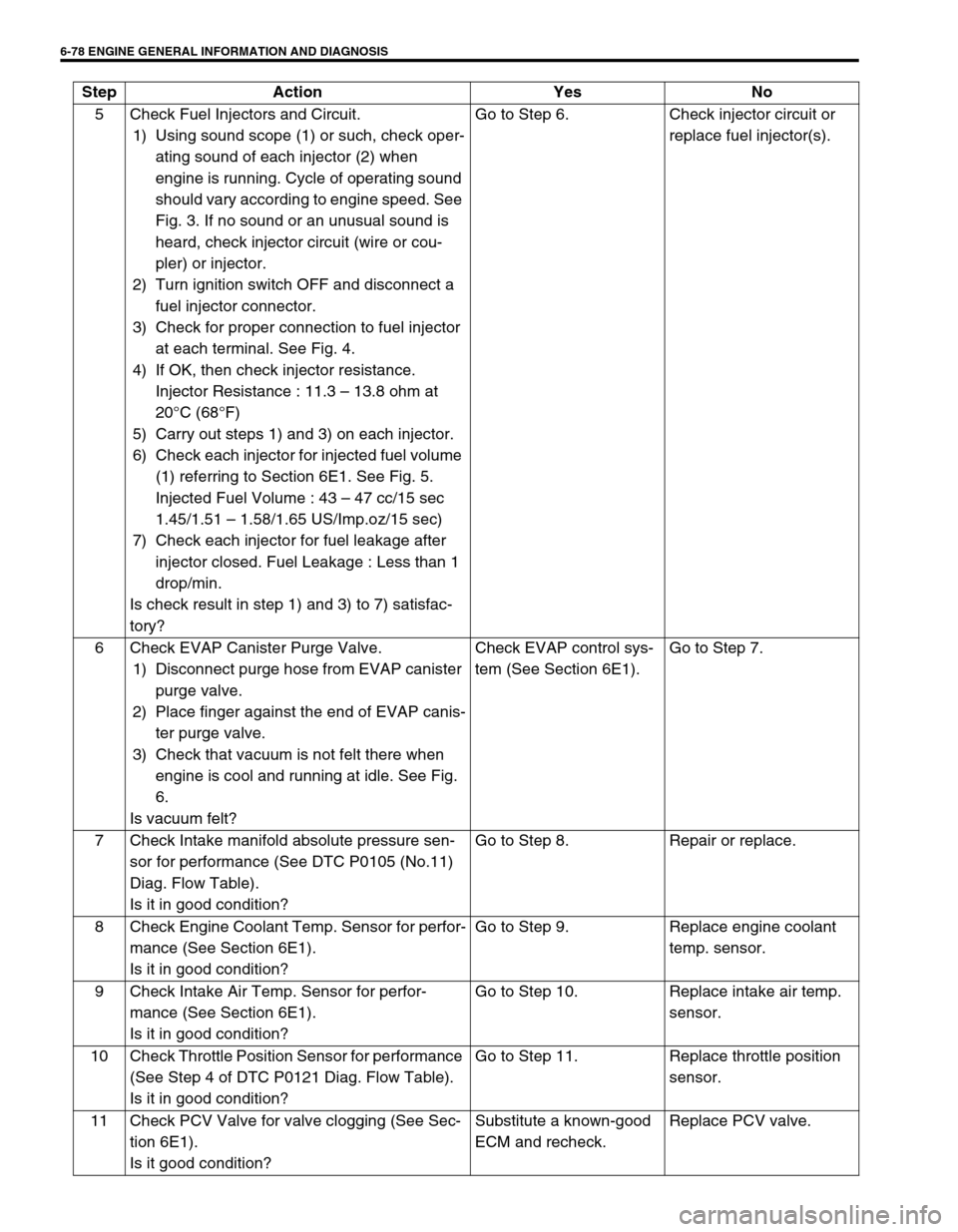
6-78 ENGINE GENERAL INFORMATION AND DIAGNOSIS
5 Check Fuel Injectors and Circuit.
1) Using sound scope (1) or such, check oper-
ating sound of each injector (2) when
engine is running. Cycle of operating sound
should vary according to engine speed. See
Fig. 3. If no sound or an unusual sound is
heard, check injector circuit (wire or cou-
pler) or injector.
2) Turn ignition switch OFF and disconnect a
fuel injector connector.
3) Check for proper connection to fuel injector
at each terminal. See Fig. 4.
4) If OK, then check injector resistance.
Injector Resistance : 11.3 – 13.8 ohm at
20°C (68°F)
5) Carry out steps 1) and 3) on each injector.
6) Check each injector for injected fuel volume
(1) referring to Section 6E1. See Fig. 5.
Injected Fuel Volume : 43 – 47 cc/15 sec
1.45/1.51 – 1.58/1.65 US/Imp.oz/15 sec)
7) Check each injector for fuel leakage after
injector closed. Fuel Leakage : Less than 1
drop/min.
Is check result in step 1) and 3) to 7) satisfac-
tory?Go to Step 6. Check injector circuit or
replace fuel injector(s).
6 Check EVAP Canister Purge Valve.
1) Disconnect purge hose from EVAP canister
purge valve.
2) Place finger against the end of EVAP canis-
ter purge valve.
3) Check that vacuum is not felt there when
engine is cool and running at idle. See Fig.
6.
Is vacuum felt?Check EVAP control sys-
tem (See Section 6E1).Go to Step 7.
7 Check Intake manifold absolute pressure sen-
sor for performance (See DTC P0105 (No.11)
Diag. Flow Table).
Is it in good condition?Go to Step 8. Repair or replace.
8 Check Engine Coolant Temp. Sensor for perfor-
mance (See Section 6E1).
Is it in good condition?Go to Step 9. Replace engine coolant
temp. sensor.
9 Check Intake Air Temp. Sensor for perfor-
mance (See Section 6E1).
Is it in good condition?Go to Step 10. Replace intake air temp.
sensor.
10 Check Throttle Position Sensor for performance
(See Step 4 of DTC P0121 Diag. Flow Table).
Is it in good condition?Go to Step 11. Replace throttle position
sensor.
11 Check PCV Valve for valve clogging (See Sec-
tion 6E1).
Is it good condition?Substitute a known-good
ECM and recheck.Replace PCV valve. Step Action Yes No
Page 451 of 698
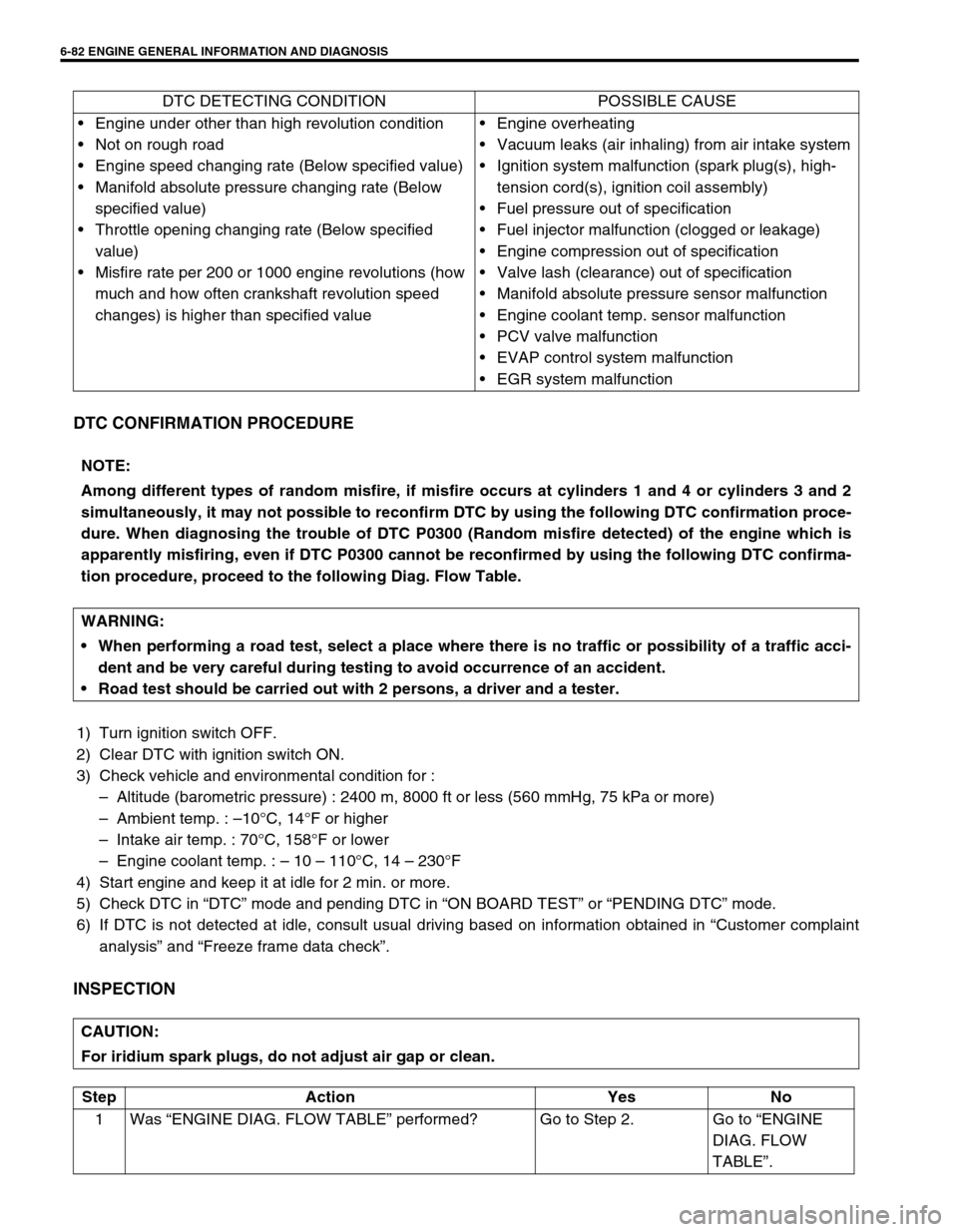
6-82 ENGINE GENERAL INFORMATION AND DIAGNOSIS
DTC CONFIRMATION PROCEDURE
1) Turn ignition switch OFF.
2) Clear DTC with ignition switch ON.
3) Check vehicle and environmental condition for :
–Altitude (barometric pressure) : 2400 m, 8000 ft or less (560 mmHg, 75 kPa or more)
–Ambient temp. : –10°C, 14°F or higher
–Intake air temp. : 70°C, 158°F or lower
–Engine coolant temp. : – 10 – 110°C, 14 – 230°F
4) Start engine and keep it at idle for 2 min. or more.
5) Check DTC in “DTC” mode and pending DTC in “ON BOARD TEST” or “PENDING DTC” mode.
6) If DTC is not detected at idle, consult usual driving based on information obtained in “Customer complaint
analysis” and “Freeze frame data check”.
INSPECTION
DTC DETECTING CONDITION POSSIBLE CAUSE
Engine under other than high revolution condition
Not on rough road
Engine speed changing rate (Below specified value)
Manifold absolute pressure changing rate (Below
specified value)
Throttle opening changing rate (Below specified
value)
Misfire rate per 200 or 1000 engine revolutions (how
much and how often crankshaft revolution speed
changes) is higher than specified valueEngine overheating
Vacuum leaks (air inhaling) from air intake system
Ignition system malfunction (spark plug(s), high-
tension cord(s), ignition coil assembly)
Fuel pressure out of specification
Fuel injector malfunction (clogged or leakage)
Engine compression out of specification
Valve lash (clearance) out of specification
Manifold absolute pressure sensor malfunction
Engine coolant temp. sensor malfunction
PCV valve malfunction
EVAP control system malfunction
EGR system malfunction
NOTE:
Among different types of random misfire, if misfire occurs at cylinders 1 and 4 or cylinders 3 and 2
simultaneously, it may not possible to reconfirm DTC by using the following DTC confirmation proce-
dure. When diagnosing the trouble of DTC P0300 (Random misfire detected) of the engine which is
apparently misfiring, even if DTC P0300 cannot be reconfirmed by using the following DTC confirma-
tion procedure, proceed to the following Diag. Flow Table.
WARNING:
When performing a road test, select a place where there is no traffic or possibility of a traffic acci-
dent and be very careful during testing to avoid occurrence of an accident.
Road test should be carried out with 2 persons, a driver and a tester.
CAUTION:
For iridium spark plugs, do not adjust air gap or clean.
Step Action Yes No
1Was “ENGINE DIAG. FLOW TABLE” performed? Go to Step 2. Go to “ENGINE
DIAG. FLOW
TABLE”.
Page 452 of 698
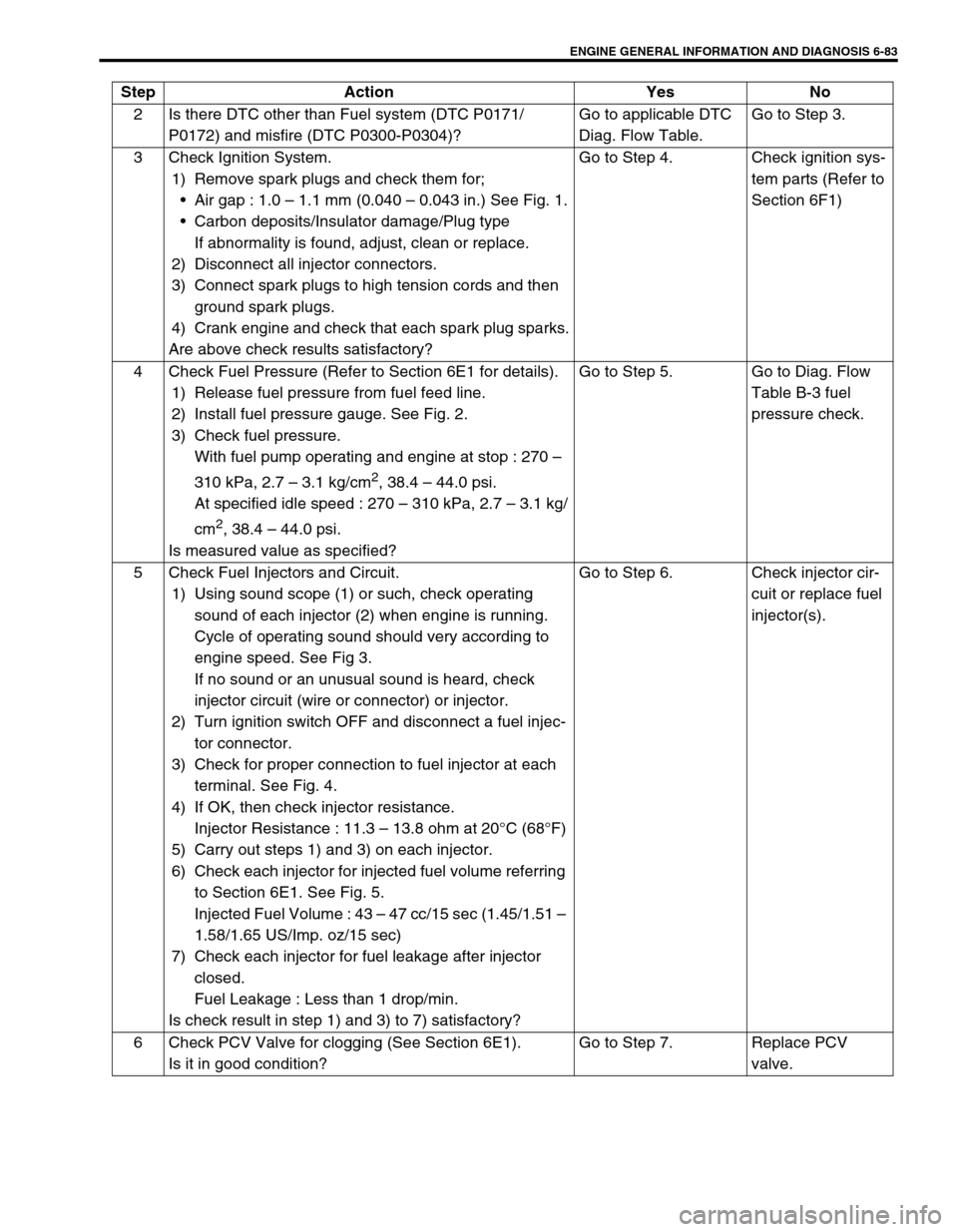
ENGINE GENERAL INFORMATION AND DIAGNOSIS 6-83
2 Is there DTC other than Fuel system (DTC P0171/
P0172) and misfire (DTC P0300-P0304)?Go to applicable DTC
Diag. Flow Table.Go to Step 3.
3 Check Ignition System.
1) Remove spark plugs and check them for;
Air gap : 1.0 – 1.1 mm (0.040 – 0.043 in.) See Fig. 1.
Carbon deposits/Insulator damage/Plug type
If abnormality is found, adjust, clean or replace.
2) Disconnect all injector connectors.
3) Connect spark plugs to high tension cords and then
ground spark plugs.
4) Crank engine and check that each spark plug sparks.
Are above check results satisfactory?Go to Step 4. Check ignition sys-
tem parts (Refer to
Section 6F1)
4 Check Fuel Pressure (Refer to Section 6E1 for details).
1) Release fuel pressure from fuel feed line.
2) Install fuel pressure gauge. See Fig. 2.
3) Check fuel pressure.
With fuel pump operating and engine at stop : 270 –
310 kPa, 2.7 – 3.1 kg/cm
2, 38.4 – 44.0 psi.
At specified idle speed : 270 – 310 kPa, 2.7 – 3.1 kg/
cm
2, 38.4 – 44.0 psi.
Is measured value as specified?Go to Step 5. Go to Diag. Flow
Table B-3 fuel
pressure check.
5 Check Fuel Injectors and Circuit.
1) Using sound scope (1) or such, check operating
sound of each injector (2) when engine is running.
Cycle of operating sound should very according to
engine speed. See Fig 3.
If no sound or an unusual sound is heard, check
injector circuit (wire or connector) or injector.
2) Turn ignition switch OFF and disconnect a fuel injec-
tor connector.
3) Check for proper connection to fuel injector at each
terminal. See Fig. 4.
4) If OK, then check injector resistance.
Injector Resistance : 11.3 – 13.8 ohm at 20°C (68°F)
5) Carry out steps 1) and 3) on each injector.
6) Check each injector for injected fuel volume referring
to Section 6E1. See Fig. 5.
Injected Fuel Volume : 43 – 47 cc/15 sec (1.45/1.51 –
1.58/1.65 US/Imp. oz/15 sec)
7) Check each injector for fuel leakage after injector
closed.
Fuel Leakage : Less than 1 drop/min.
Is check result in step 1) and 3) to 7) satisfactory?Go to Step 6. Check injector cir-
cuit or replace fuel
injector(s).
6 Check PCV Valve for clogging (See Section 6E1).
Is it in good condition?Go to Step 7. Replace PCV
valve. Step Action Yes No