engine SUZUKI SWIFT 2000 1.G SF310 Service Workshop Manual
[x] Cancel search | Manufacturer: SUZUKI, Model Year: 2000, Model line: SWIFT, Model: SUZUKI SWIFT 2000 1.GPages: 557, PDF Size: 14.35 MB
Page 459 of 557
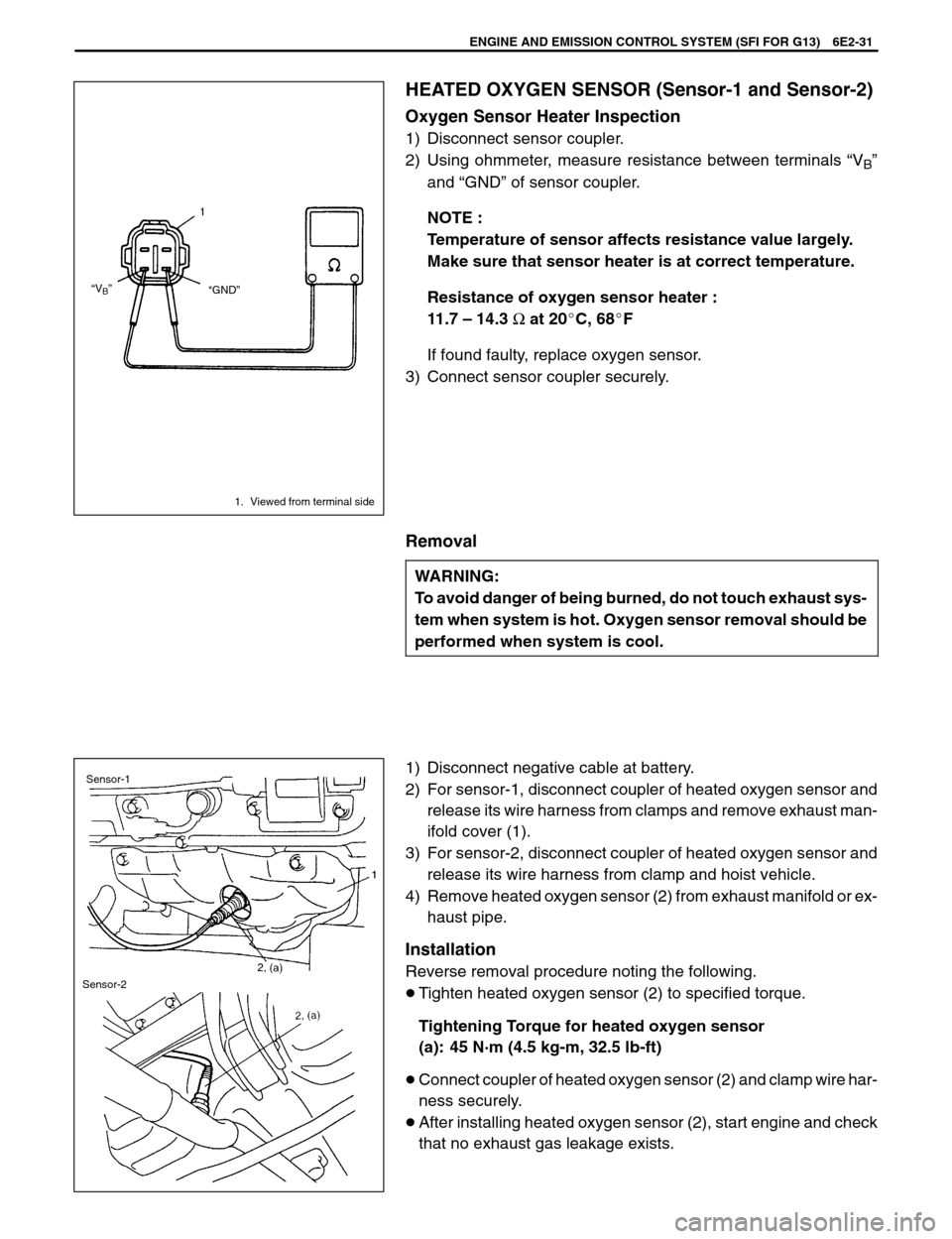
ENGINE AND EMISSION CONTROL SYSTEM (SFI FOR G13) 6E2-31
1. Viewed from terminal side
Sensor-1
Sensor-2
“VB”
“GND”
HEATED OXYGEN SENSOR (Sensor-1 and Sensor-2)
Oxygen Sensor Heater Inspection
1) Disconnect sensor coupler.
2) Using ohmmeter, measure resistance between terminals “V
B”
and “GND” of sensor coupler.
NOTE :
Temperature of sensor affects resistance value largely.
Make sure that sensor heater is at correct temperature.
Resistance of oxygen sensor heater :
11.7 – 14.3 Ω at 20C, 68F
If found faulty, replace oxygen sensor.
3) Connect sensor coupler securely.
Removal
WARNING:
To avoid danger of being burned, do not touch exhaust sys-
tem when system is hot. Oxygen sensor removal should be
performed when system is cool.
1) Disconnect negative cable at battery.
2) For sensor-1, disconnect coupler of heated oxygen sensor and
release its wire harness from clamps and remove exhaust man-
ifold cover (1).
3) For sensor-2, disconnect coupler of heated oxygen sensor and
release its wire harness from clamp and hoist vehicle.
4) Remove heated oxygen sensor (2) from exhaust manifold or ex-
haust pipe.
Installation
Reverse removal procedure noting the following.
Tighten heated oxygen sensor (2) to specified torque.
Tightening Torque for heated oxygen sensor
(a): 45 N·m (4.5 kg-m, 32.5 lb-ft)
Connect coupler of heated oxygen sensor (2) and clamp wire har-
ness securely.
After installing heated oxygen sensor (2), start engine and check
that no exhaust gas leakage exists.
Page 460 of 557
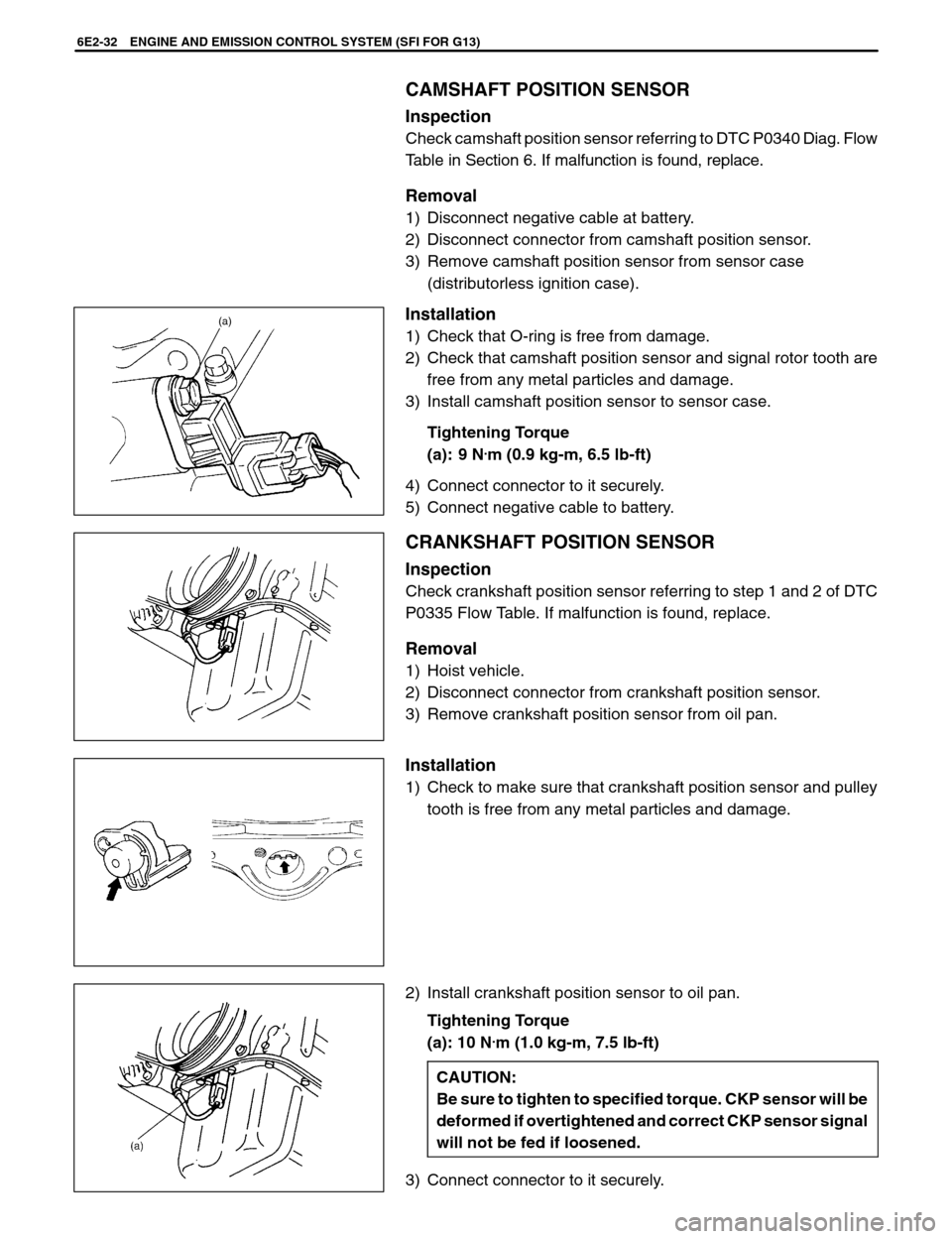
(a)
6E2-32 ENGINE AND EMISSION CONTROL SYSTEM (SFI FOR G13)
CAMSHAFT POSITION SENSOR
Inspection
Check camshaft position sensor referring to DTC P0340 Diag. Flow
Table in Section 6. If malfunction is found, replace.
Removal
1) Disconnect negative cable at battery.
2) Disconnect connector from camshaft position sensor.
3) Remove camshaft position sensor from sensor case
(distributorless ignition case).
Installation
1) Check that O-ring is free from damage.
2) Check that camshaft position sensor and signal rotor tooth are
free from any metal particles and damage.
3) Install camshaft position sensor to sensor case.
Tightening Torque
(a): 9 N
.m (0.9 kg-m, 6.5 lb-ft)
4) Connect connector to it securely.
5) Connect negative cable to battery.
CRANKSHAFT POSITION SENSOR
Inspection
Check crankshaft position sensor referring to step 1 and 2 of DTC
P0335 Flow Table. If malfunction is found, replace.
Removal
1) Hoist vehicle.
2) Disconnect connector from crankshaft position sensor.
3) Remove crankshaft position sensor from oil pan.
Installation
1) Check to make sure that crankshaft position sensor and pulley
tooth is free from any metal particles and damage.
2) Install crankshaft position sensor to oil pan.
Tightening Torque
(a): 10 N
.m (1.0 kg-m, 7.5 lb-ft)
CAUTION:
Be sure to tighten to specified torque. CKP sensor will be
deformed if overtightened and correct CKP sensor signal
will not be fed if loosened.
3) Connect connector to it securely.
Page 461 of 557
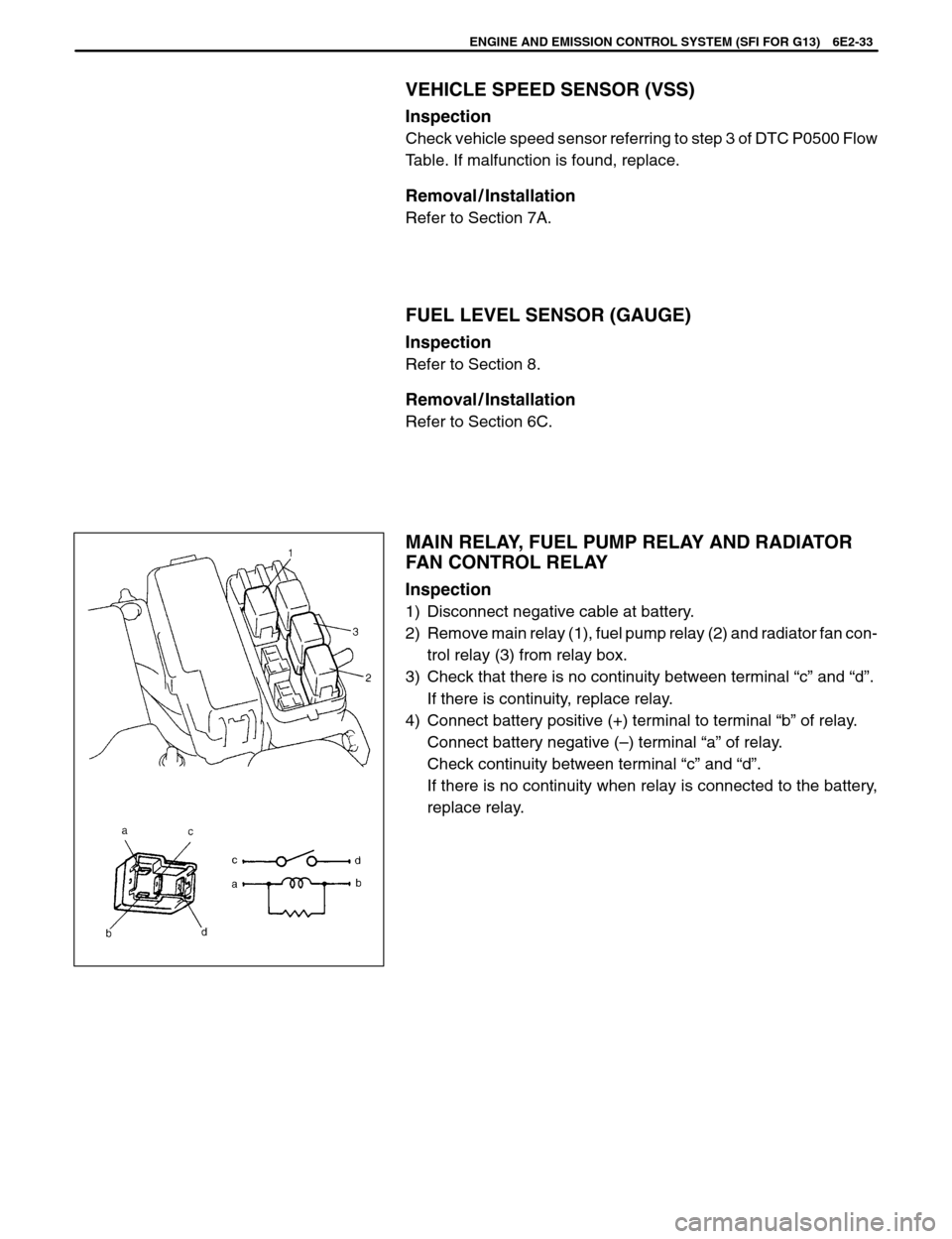
ENGINE AND EMISSION CONTROL SYSTEM (SFI FOR G13) 6E2-33
VEHICLE SPEED SENSOR (VSS)
Inspection
Check vehicle speed sensor referring to step 3 of DTC P0500 Flow
Table. If malfunction is found, replace.
Removal / Installation
Refer to Section 7A.
FUEL LEVEL SENSOR (GAUGE)
Inspection
Refer to Section 8.
Removal / Installation
Refer to Section 6C.
MAIN RELAY, FUEL PUMP RELAY AND RADIATOR
FAN CONTROL RELAY
Inspection
1) Disconnect negative cable at battery.
2) Remove main relay (1), fuel pump relay (2) and radiator fan con-
trol relay (3) from relay box.
3) Check that there is no continuity between terminal “c” and “d”.
If there is continuity, replace relay.
4) Connect battery positive (+) terminal to terminal “b” of relay.
Connect battery negative (–) terminal “a” of relay.
Check continuity between terminal “c” and “d”.
If there is no continuity when relay is connected to the battery,
replace relay.
Page 462 of 557

6E2-34 ENGINE AND EMISSION CONTROL SYSTEM (SFI FOR G13)
FUEL CUT OPERATION
Inspection
NOTE:
Before inspection, check to make sure that gear shift lever is
in neutral position (with A / T model, selector lever in “P”
range), A / C is OFF and that parking brake lever is pulled all the
way up.
1) Warm up engine to normal operating temperature.
2) While listening to sound of injector (1) by using sound scope (2)
or such, increase engine speed to higher than 3,000 r / min.
3) Check to make sure that sound to indicate operation of injector
stops when throttle valve is closed instantly and it is heard again
when engine speed is reduced to less than about 2,000 r / min.
RADIATOR FAN CONTROL SYSTEM
System Inspection
WARNING:
Keep hands, tools, and clothing away from engine cooling
fan to help prevent personal injury. This fan is electric and
can come on whether or not the engine is running. The fan
can start automatically in response to the ECT sensor with
the ignition switch in the ON position.
Check system for operation referring to Flow Table B-8 in Section
6.
If radiator fan fails to operate properly, check relay, radiator fan and
electrical circuit.
Radiator Fan
Inspection
1) Check continuity between each two terminals.
If there is no continuity, replace radiator fan motor.
Page 463 of 557
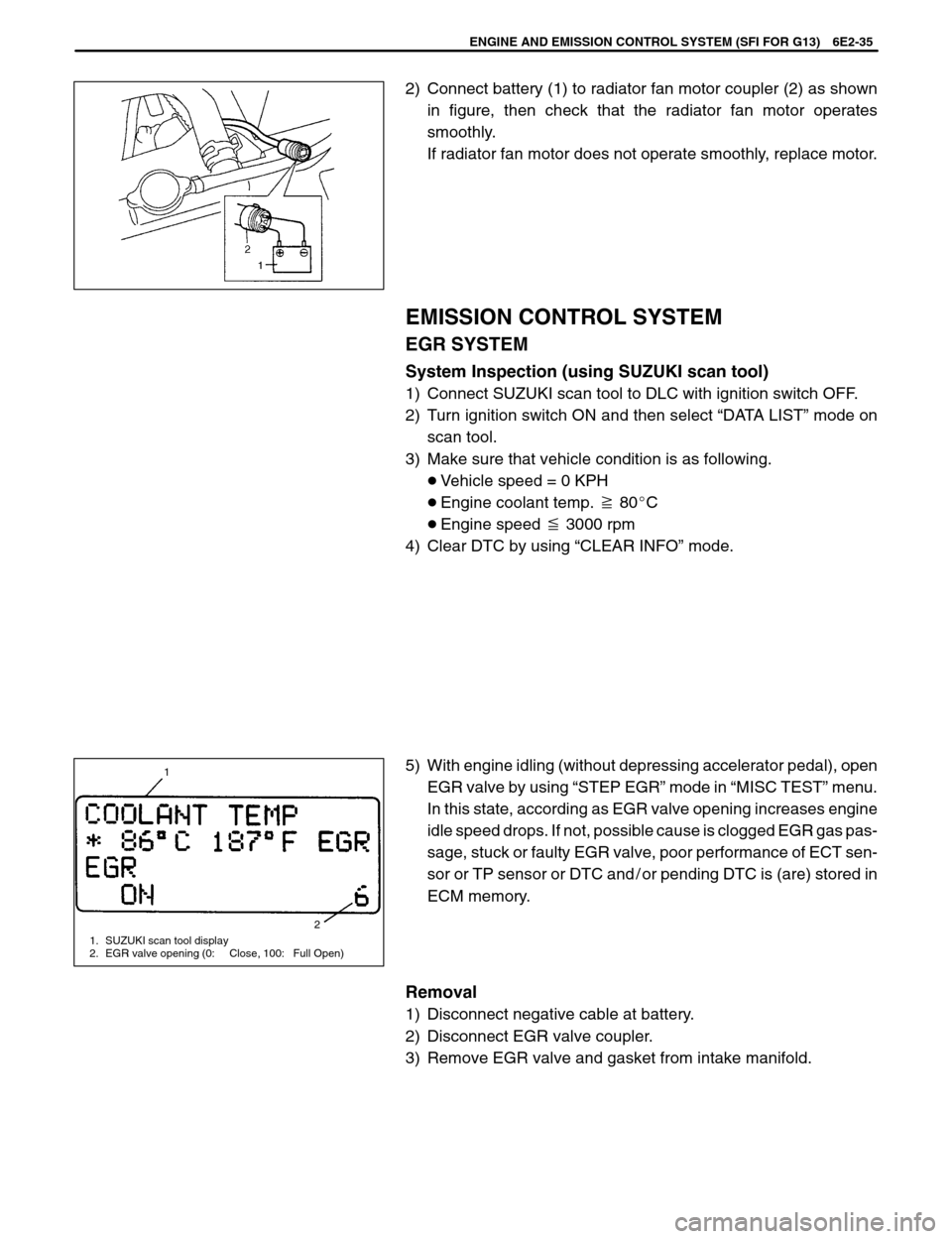
1
2
1. SUZUKI scan tool display
2. EGR valve opening (0: Close, 100: Full Open)
ENGINE AND EMISSION CONTROL SYSTEM (SFI FOR G13) 6E2-35
2) Connect battery (1) to radiator fan motor coupler (2) as shown
in figure, then check that the radiator fan motor operates
smoothly.
If radiator fan motor does not operate smoothly, replace motor.
EMISSION CONTROL SYSTEM
EGR SYSTEM
System Inspection (using SUZUKI scan tool)
1) Connect SUZUKI scan tool to DLC with ignition switch OFF.
2) Turn ignition switch ON and then select “DATA LIST” mode on
scan tool.
3) Make sure that vehicle condition is as following.
Vehicle speed = 0 KPH
Engine coolant temp. 80C
Engine speed 3000 rpm
4) Clear DTC by using “CLEAR INFO” mode.
5) With engine idling (without depressing accelerator pedal), open
EGR valve by using “STEP EGR” mode in “MISC TEST” menu.
In this state, according as EGR valve opening increases engine
idle speed drops. If not, possible cause is clogged EGR gas pas-
sage, stuck or faulty EGR valve, poor performance of ECT sen-
sor or TP sensor or DTC and / or pending DTC is (are) stored in
ECM memory.
Removal
1) Disconnect negative cable at battery.
2) Disconnect EGR valve coupler.
3) Remove EGR valve and gasket from intake manifold.
Page 464 of 557
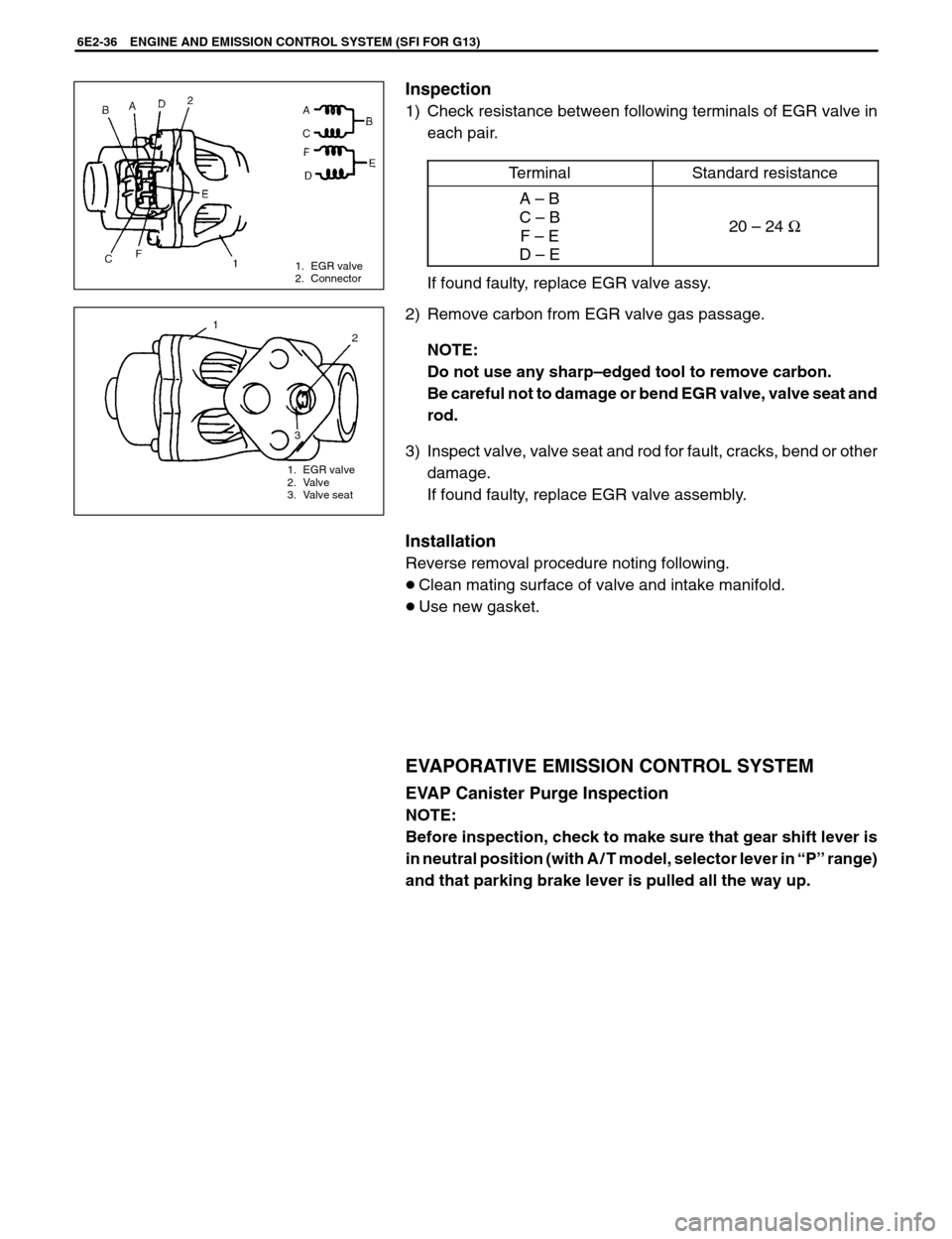
6E2-36 ENGINE AND EMISSION CONTROL SYSTEM (SFI FOR G13)
1. EGR valve
2. Connector
1
2
1. EGR valve
2. Valve
3. Valve seat3
Inspection
1) Check resistance between following terminals of EGR valve in
each pair.
Terminal
Standard resistance
A – B
C – B
F – E
D – E
20 – 24 Ω
If found faulty, replace EGR valve assy.
2) Remove carbon from EGR valve gas passage.
NOTE:
Do not use any sharp–edged tool to remove carbon.
Be careful not to damage or bend EGR valve, valve seat and
rod.
3) Inspect valve, valve seat and rod for fault, cracks, bend or other
damage.
If found faulty, replace EGR valve assembly.
Installation
Reverse removal procedure noting following.
Clean mating surface of valve and intake manifold.
Use new gasket.
EVAPORATIVE EMISSION CONTROL SYSTEM
EVAP Canister Purge Inspection
NOTE:
Before inspection, check to make sure that gear shift lever is
in neutral position (with A / T model, selector lever in “P” range)
and that parking brake lever is pulled all the way up.
Page 465 of 557
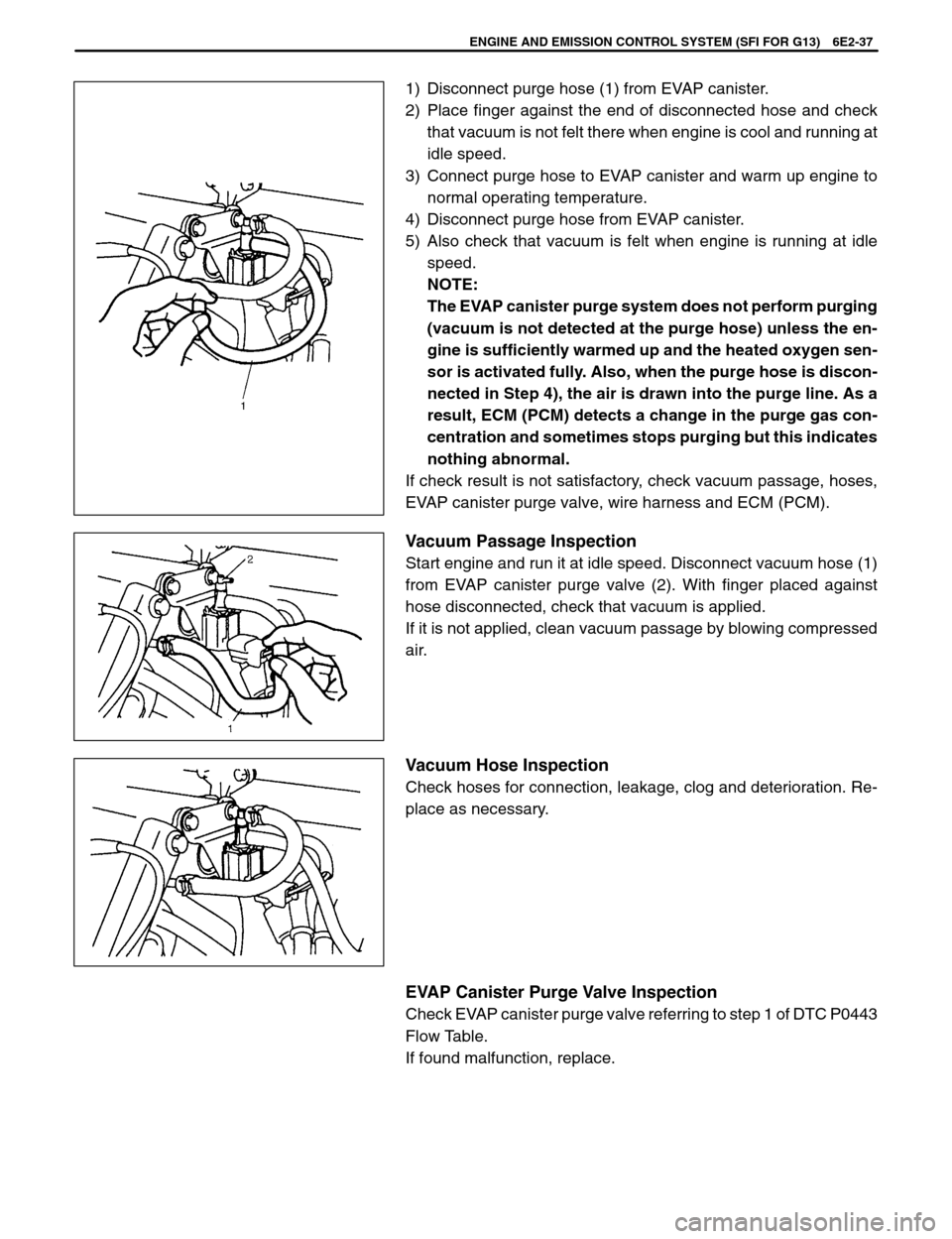
ENGINE AND EMISSION CONTROL SYSTEM (SFI FOR G13) 6E2-37
1) Disconnect purge hose (1) from EVAP canister.
2) Place finger against the end of disconnected hose and check
that vacuum is not felt there when engine is cool and running at
idle speed.
3) Connect purge hose to EVAP canister and warm up engine to
normal operating temperature.
4) Disconnect purge hose from EVAP canister.
5) Also check that vacuum is felt when engine is running at idle
speed.
NOTE:
The EVAP canister purge system does not perform purging
(vacuum is not detected at the purge hose) unless the en-
gine is sufficiently warmed up and the heated oxygen sen-
sor is activated fully. Also, when the purge hose is discon-
nected in Step 4), the air is drawn into the purge line. As a
result, ECM (PCM) detects a change in the purge gas con-
centration and sometimes stops purging but this indicates
nothing abnormal.
If check result is not satisfactory, check vacuum passage, hoses,
EVAP canister purge valve, wire harness and ECM (PCM).
Vacuum Passage Inspection
Start engine and run it at idle speed. Disconnect vacuum hose (1)
from EVAP canister purge valve (2). With finger placed against
hose disconnected, check that vacuum is applied.
If it is not applied, clean vacuum passage by blowing compressed
air.
Vacuum Hose Inspection
Check hoses for connection, leakage, clog and deterioration. Re-
place as necessary.
EVAP Canister Purge Valve Inspection
Check EVAP canister purge valve referring to step 1 of DTC P0443
Flow Table.
If found malfunction, replace.
Page 466 of 557
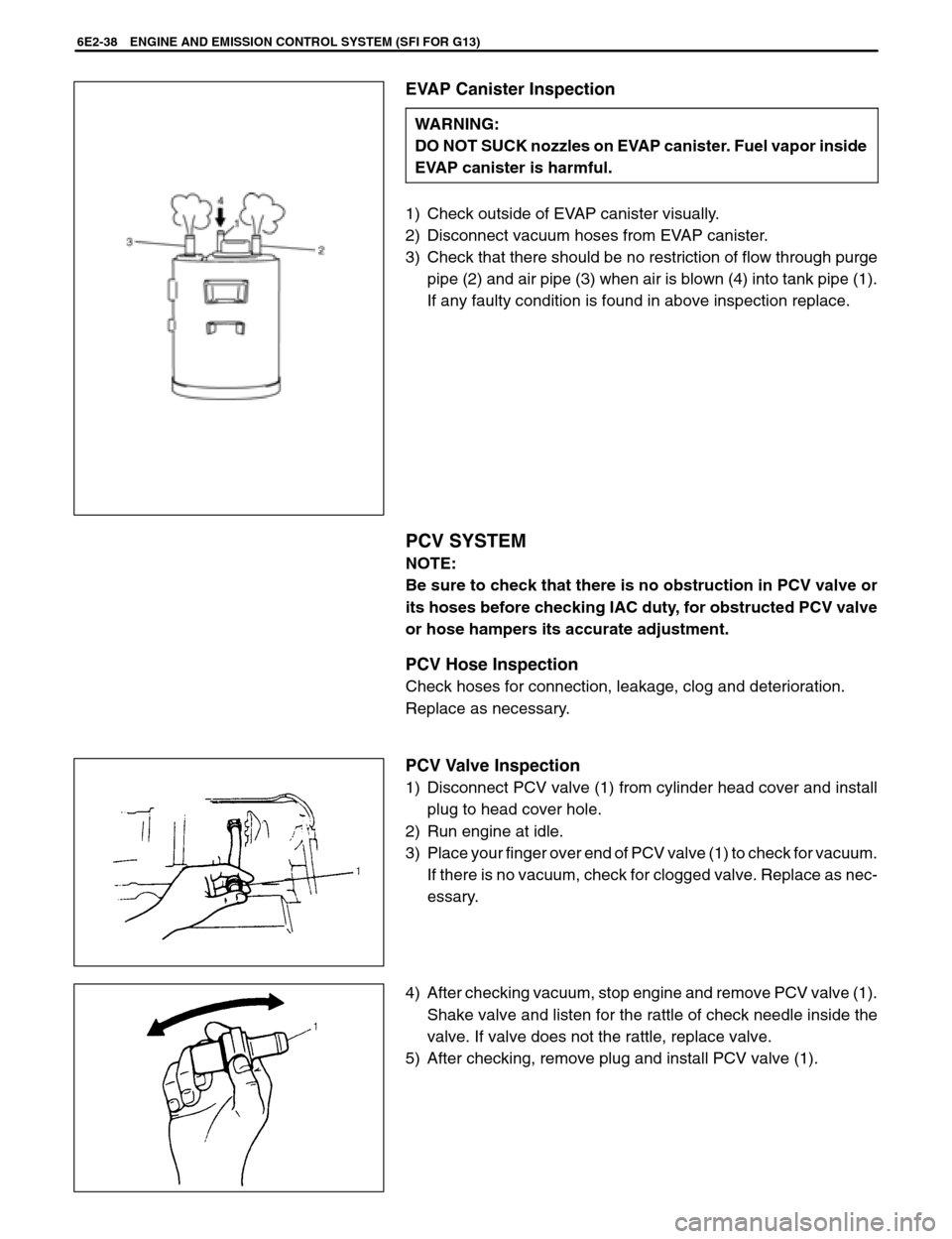
6E2-38 ENGINE AND EMISSION CONTROL SYSTEM (SFI FOR G13)
EVAP Canister Inspection
WARNING:
DO NOT SUCK nozzles on EVAP canister. Fuel vapor inside
EVAP canister is harmful.
1) Check outside of EVAP canister visually.
2) Disconnect vacuum hoses from EVAP canister.
3) Check that there should be no restriction of flow through purge
pipe (2) and air pipe (3) when air is blown (4) into tank pipe (1).
If any faulty condition is found in above inspection replace.
PCV SYSTEM
NOTE:
Be sure to check that there is no obstruction in PCV valve or
its hoses before checking IAC duty, for obstructed PCV valve
or hose hampers its accurate adjustment.
PCV Hose Inspection
Check hoses for connection, leakage, clog and deterioration.
Replace as necessary.
PCV Valve Inspection
1) Disconnect PCV valve (1) from cylinder head cover and install
plug to head cover hole.
2) Run engine at idle.
3) Place your finger over end of PCV valve (1) to check for vacuum.
If there is no vacuum, check for clogged valve. Replace as nec-
essary.
4) After checking vacuum, stop engine and remove PCV valve (1).
Shake valve and listen for the rattle of check needle inside the
valve. If valve does not the rattle, replace valve.
5) After checking, remove plug and install PCV valve (1).
Page 467 of 557
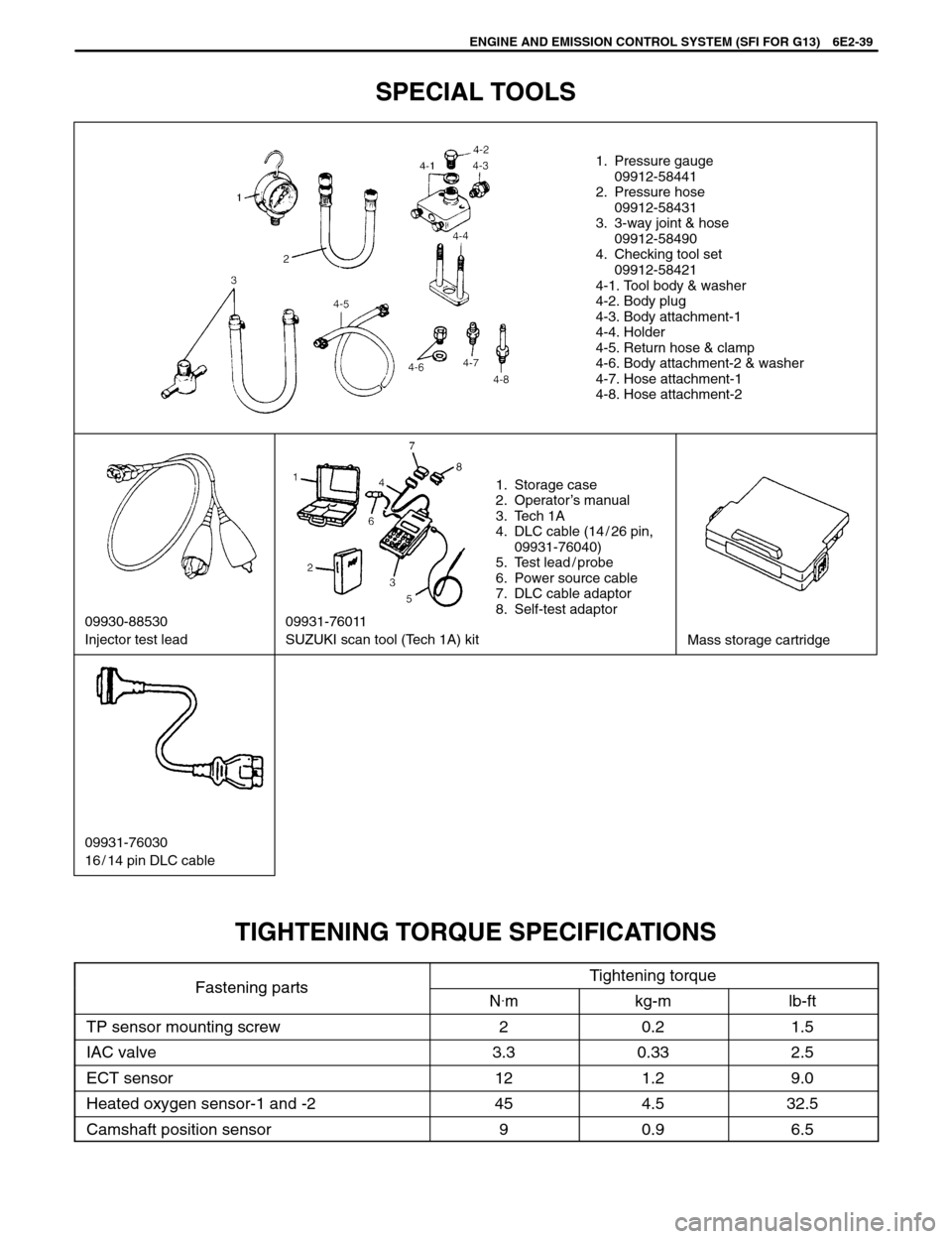
ENGINE AND EMISSION CONTROL SYSTEM (SFI FOR G13) 6E2-39
09930-88530
Injector test lead09931-76011
SUZUKI scan tool (Tech 1A) kit
Mass storage cartridge
09931-76030
16 / 14 pin DLC cable1. Pressure gauge
09912-58441
2. Pressure hose
09912-58431
3. 3-way joint & hose
09912-58490
4. Checking tool set
09912-58421
4-1. Tool body & washer
4-2. Body plug
4-3. Body attachment-1
4-4. Holder
4-5. Return hose & clamp
4-6. Body attachment-2 & washer
4-7. Hose attachment-1
4-8. Hose attachment-2
1. Storage case
2. Operator’s manual
3. Tech 1A
4. DLC cable (14 / 26 pin,
09931-76040)
5. Test lead / probe
6. Power source cable
7. DLC cable adaptor
8. Self-test adaptor
SPECIAL TOOLS
TIGHTENING TORQUE SPECIFICATIONS
FasteningpartsTightening torqueFastening artsN.mkg-mlb-ft
TP sensor mounting screw20.21.5
IAC valve3.30.332.5
ECT sensor121.29.0
Heated oxygen sensor-1 and -2454.532.5
Camshaft position sensor90.96.5
Page 468 of 557
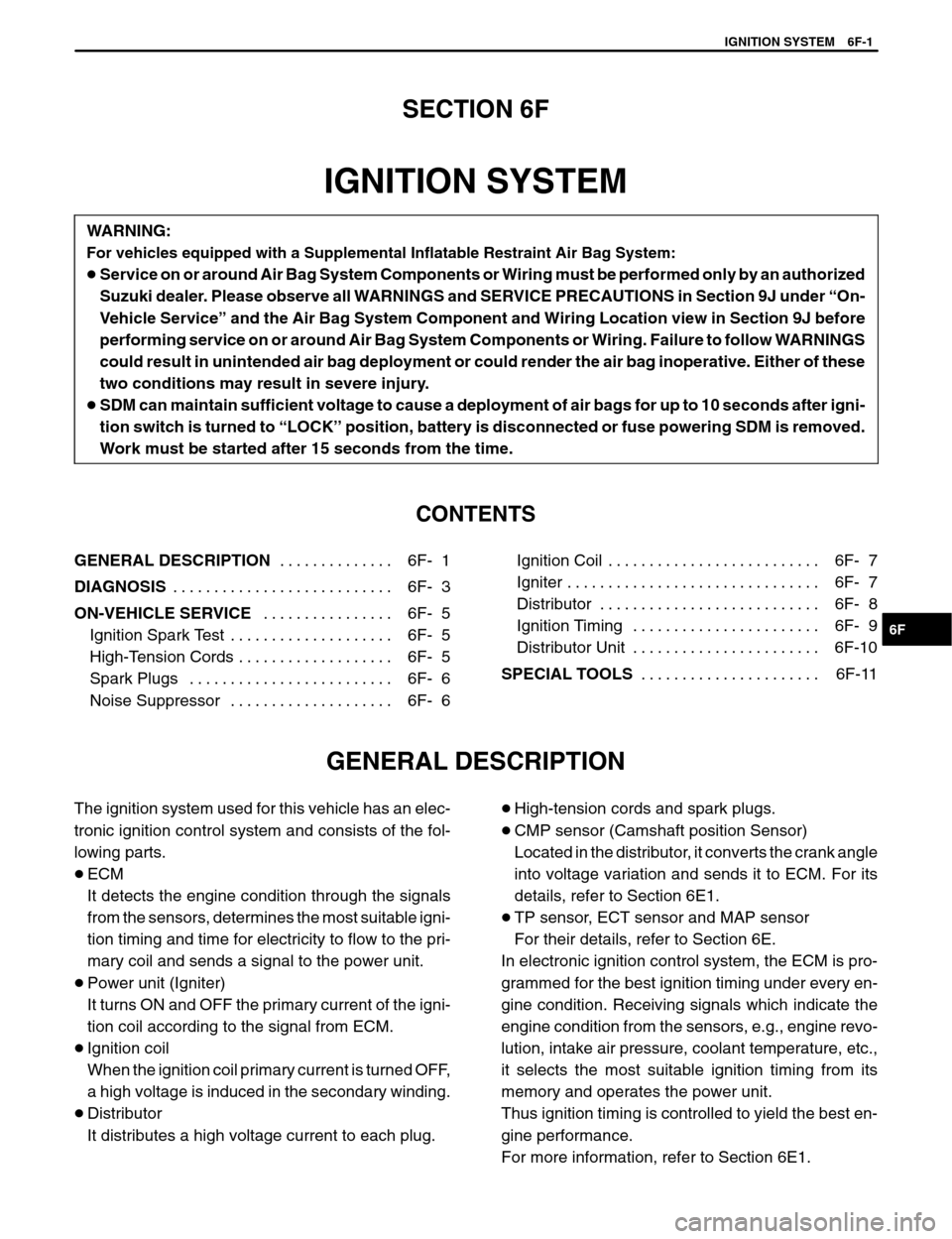
6F
IGNITION SYSTEM 6F-1
GENERAL DESCRIPTION6F- 1 . . . . . . . . . . . . . .
DIAGNOSIS6F- 3 . . . . . . . . . . . . . . . . . . . . . . . . . . .
ON-VEHICLE SERVICE6F- 5 . . . . . . . . . . . . . . . .
Ignition Spark Test 6F- 5. . . . . . . . . . . . . . . . . . . .
High-Tension Cords 6F- 5. . . . . . . . . . . . . . . . . . .
Spark Plugs 6F- 6. . . . . . . . . . . . . . . . . . . . . . . . .
Noise Suppressor 6F- 6. . . . . . . . . . . . . . . . . . . . Ignition Coil 6F- 7. . . . . . . . . . . . . . . . . . . . . . . . . .
Igniter 6F- 7. . . . . . . . . . . . . . . . . . . . . . . . . . . . . . .
Distributor 6F- 8. . . . . . . . . . . . . . . . . . . . . . . . . . .
Ignition Timing 6F- 9. . . . . . . . . . . . . . . . . . . . . . .
Distributor Unit 6F-10. . . . . . . . . . . . . . . . . . . . . . .
SPECIAL TOOLS6F-11 . . . . . . . . . . . . . . . . . . . . . .
The ignition system used for this vehicle has an elec-
tronic ignition control system and consists of the fol-
lowing parts.
ECM
It detects the engine condition through the signals
from the sensors, determines the most suitable igni-
tion timing and time for electricity to flow to the pri-
mary coil and sends a signal to the power unit.
Power unit (Igniter)
It turns ON and OFF the primary current of the igni-
tion coil according to the signal from ECM.
Ignition coil
When the ignition coil primary current is turned OFF,
a high voltage is induced in the secondary winding.
Distributor
It distributes a high voltage current to each plug.High-tension cords and spark plugs.
CMP sensor (Camshaft position Sensor)
Located in the distributor, it converts the crank angle
into voltage variation and sends it to ECM. For its
details, refer to Section 6E1.
TP sensor, ECT sensor and MAP sensor
For their details, refer to Section 6E.
In electronic ignition control system, the ECM is pro-
grammed for the best ignition timing under every en-
gine condition. Receiving signals which indicate the
engine condition from the sensors, e.g., engine revo-
lution, intake air pressure, coolant temperature, etc.,
it selects the most suitable ignition timing from its
memory and operates the power unit.
Thus ignition timing is controlled to yield the best en-
gine performance.
For more information, refer to Section 6E1.
SECTION 6F
IGNITION SYSTEM
WARNING:
For vehicles equipped with a Supplemental Inflatable Restraint Air Bag System:
Service on or around Air Bag System Components or Wiring must be performed only by an authorized
Suzuki dealer. Please observe all WARNINGS and SERVICE PRECAUTIONS in Section 9J under “On-
Vehicle Service” and the Air Bag System Component and Wiring Location view in Section 9J before
performing service on or around Air Bag System Components or Wiring. Failure to follow WARNINGS
could result in unintended air bag deployment or could render the air bag inoperative. Either of these
two conditions may result in severe injury.
SDM can maintain sufficient voltage to cause a deployment of air bags for up to 10 seconds after igni-
tion switch is turned to “LOCK” position, battery is disconnected or fuse powering SDM is removed.
Work must be started after 15 seconds from the time.
CONTENTS
GENERAL DESCRIPTION