sensor SUZUKI SX4 2006 1.G Service Workshop Manual
[x] Cancel search | Manufacturer: SUZUKI, Model Year: 2006, Model line: SX4, Model: SUZUKI SX4 2006 1.GPages: 1556, PDF Size: 37.31 MB
Page 393 of 1556
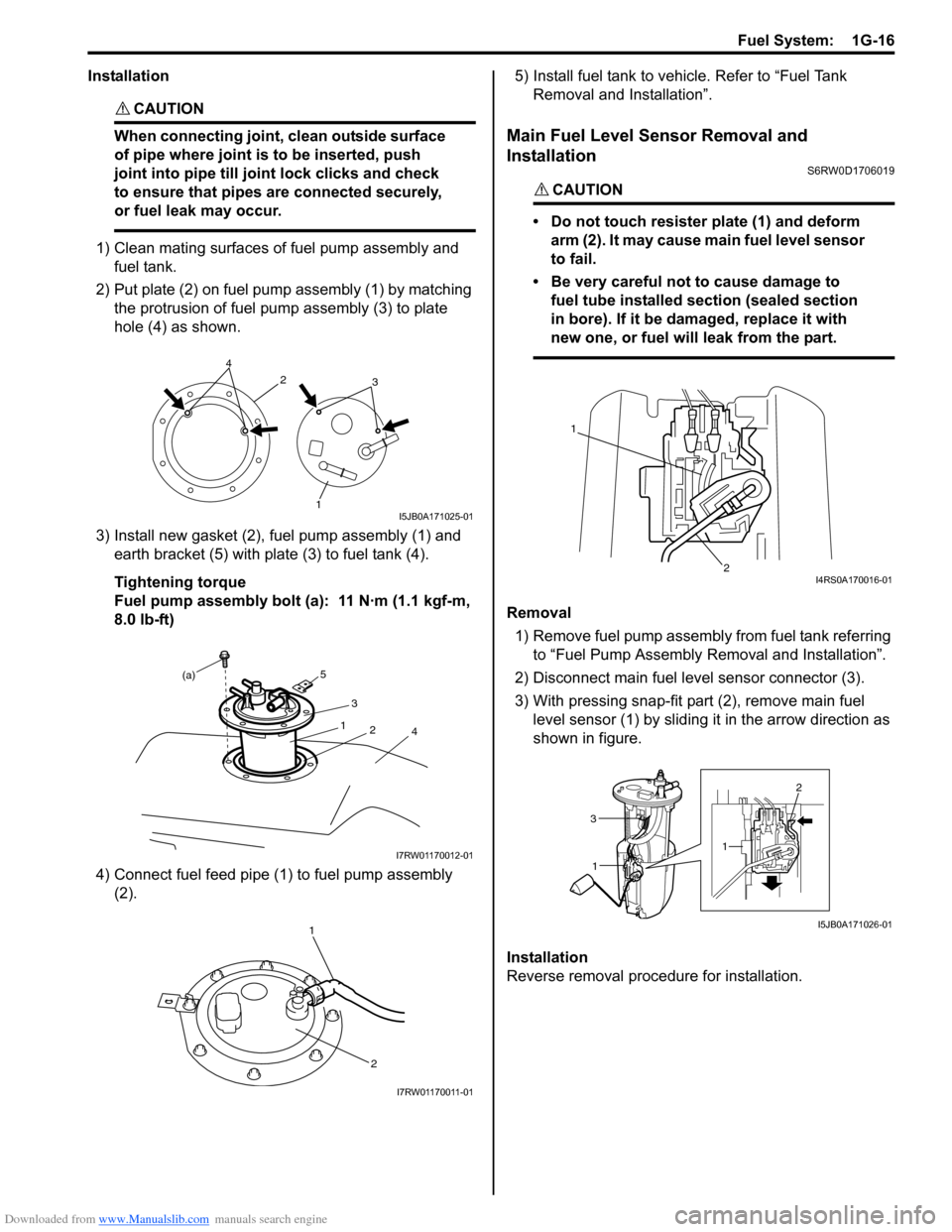
Downloaded from www.Manualslib.com manuals search engine Fuel System: 1G-16
Installation
CAUTION!
When connecting joint, clean outside surface
of pipe where joint is to be inserted, push
joint into pipe till joint lock clicks and check
to ensure that pipes are connected securely,
or fuel leak may occur.
1) Clean mating surfaces of fuel pump assembly and
fuel tank.
2) Put plate (2) on fuel pump assembly (1) by matching
the protrusion of fuel pump assembly (3) to plate
hole (4) as shown.
3) Install new gasket (2), fuel pump assembly (1) and
earth bracket (5) with plate (3) to fuel tank (4).
Tightening torque
Fuel pump assembly bolt (a): 11 N·m (1.1 kgf-m,
8.0 lb-ft)
4) Connect fuel feed pipe (1) to fuel pump assembly
(2).5) Install fuel tank to vehicle. Refer to “Fuel Tank
Removal and Installation”.
Main Fuel Level Sensor Removal and
Installation
S6RW0D1706019
CAUTION!
• Do not touch resister plate (1) and deform
arm (2). It may cause main fuel level sensor
to fail.
• Be very careful not to cause damage to
fuel tube installed section (sealed section
in bore). If it be damaged, replace it with
new one, or fuel will leak from the part.
Removal
1) Remove fuel pump assembly from fuel tank referring
to “Fuel Pump Assembly Removal and Installation”.
2) Disconnect main fuel level sensor connector (3).
3) With pressing snap-fit part (2), remove main fuel
level sensor (1) by sliding it in the arrow direction as
shown in figure.
Installation
Reverse removal procedure for installation.
3
1 2 4
I5JB0A171025-01
3
1
2
(a)
4
5
I7RW01170012-01
1
2
I7RW01170011-01
1
2I4RS0A170016-01
1 3
12
I5JB0A171026-01
Page 394 of 1556
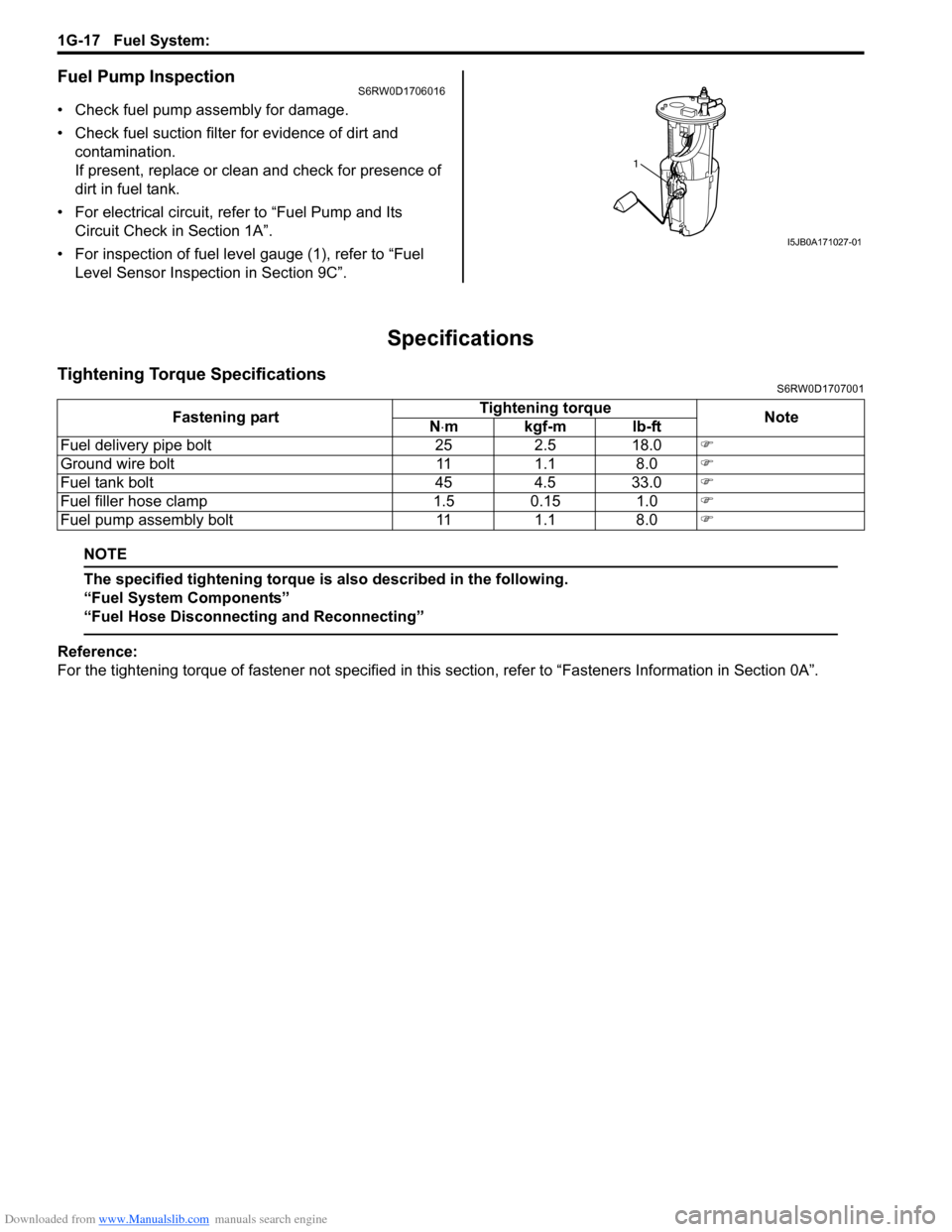
Downloaded from www.Manualslib.com manuals search engine 1G-17 Fuel System:
Fuel Pump InspectionS6RW0D1706016
• Check fuel pump assembly for damage.
• Check fuel suction filter for evidence of dirt and
contamination.
If present, replace or clean and check for presence of
dirt in fuel tank.
• For electrical circuit, refer to “Fuel Pump and Its
Circuit Check in Section 1A”.
• For inspection of fuel level gauge (1), refer to “Fuel
Level Sensor Inspection in Section 9C”.
Specifications
Tightening Torque SpecificationsS6RW0D1707001
NOTE
The specified tightening torque is also described in the following.
“Fuel System Components”
“Fuel Hose Disconnecting and Reconnecting”
Reference:
For the tightening torque of fastener not specified in this section, refer to “Fasteners Information in Section 0A”.
1
I5JB0A171027-01
Fastening partTightening torque
Note
N⋅mkgf-mlb-ft
Fuel delivery pipe bolt 25 2.5 18.0 )
Ground wire bolt 11 1.1 8.0 )
Fuel tank bolt 45 4.5 33.0 )
Fuel filler hose clamp 1.5 0.15 1.0 )
Fuel pump assembly bolt 11 1.1 8.0 )
Page 396 of 1556
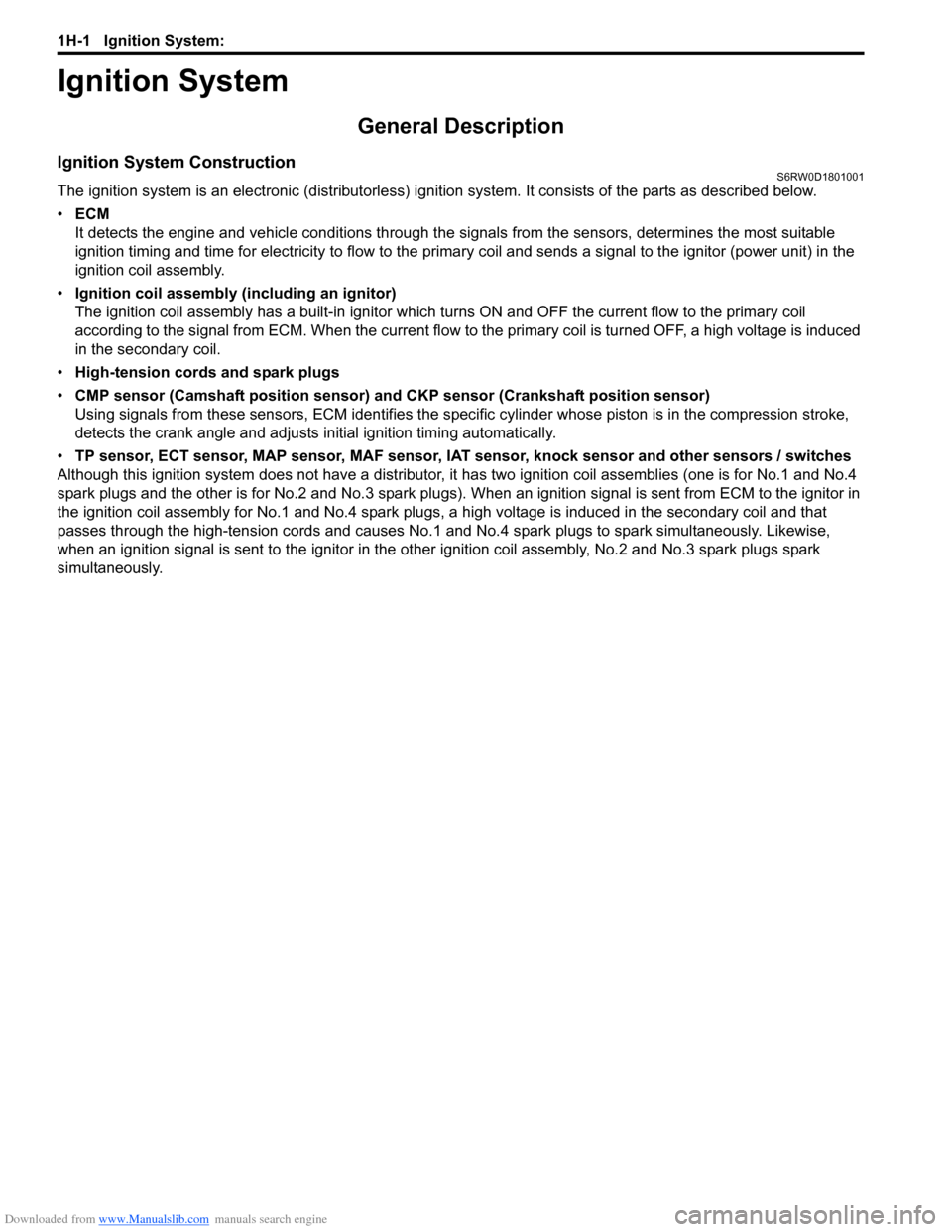
Downloaded from www.Manualslib.com manuals search engine 1H-1 Ignition System:
Engine
Ignition System
General Description
Ignition System ConstructionS6RW0D1801001
The ignition system is an electronic (distributorless) ignition system. It consists of the parts as described below.
•ECM
It detects the engine and vehicle conditions through the signals from the sensors, determines the most suitable
ignition timing and time for electricity to flow to the primary coil and sends a signal to the ignitor (power unit) in the
ignition coil assembly.
•Ignition coil assembly (including an ignitor)
The ignition coil assembly has a built-in ignitor which turns ON and OFF the current flow to the primary coil
according to the signal from ECM. When the current flow to the primary coil is turned OFF, a high voltage is induced
in the secondary coil.
•High-tension cords and spark plugs
•CMP sensor (Camshaft position sensor) and CKP sensor (Crankshaft position sensor)
Using signals from these sensors, ECM identifies the specific cylinder whose piston is in the compression stroke,
detects the crank angle and adjusts initial ignition timing automatically.
•TP sensor, ECT sensor, MAP sensor, MAF sensor, IAT sensor, knock sensor and other sensors / switches
Although this ignition system does not have a distributor, it has two ignition coil assemblies (one is for No.1 and No.4
spark plugs and the other is for No.2 and No.3 spark plugs). When an ignition signal is sent from ECM to the ignitor in
the ignition coil assembly for No.1 and No.4 spark plugs, a high voltage is induced in the secondary coil and that
passes through the high-tension cords and causes No.1 and No.4 spark plugs to spark simultaneously. Likewise,
when an ignition signal is sent to the ignitor in the other ignition coil assembly, No.2 and No.3 spark plugs spark
simultaneously.
Page 397 of 1556
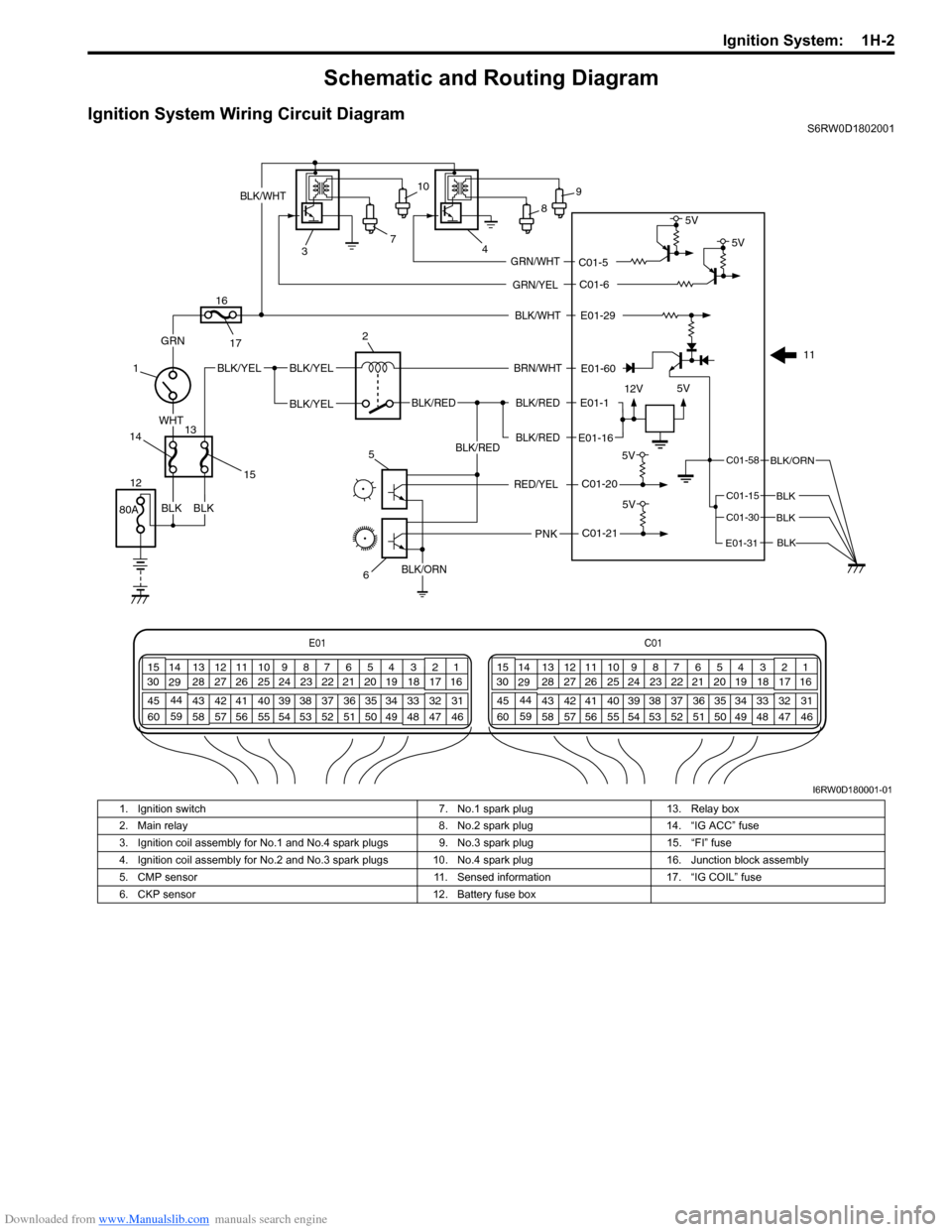
Downloaded from www.Manualslib.com manuals search engine Ignition System: 1H-2
Schematic and Routing Diagram
Ignition System Wiring Circuit DiagramS6RW0D1802001
E01-60
E01-29
12V5V
5V
E01-1
E01-16
BLK/WHT
BLK/RED
BLK/RED
BLK/RED
80A
BLK/YELBLK/YEL
BLK/YEL
GRN
BLK
WHT
BRN/WHT
BLK/ORN
BLK
BLK
BLK
C01-20
BLK/RED
PNK
BLK/ORN
5V
C01-21
BLK/WHT
7
34
1
125
6 2
11 89 10
GRN/YEL
GRN/WHT
C01-6
C01-55V
5V
RED/YEL
C01-58
C01-15
C01-30
E01-31
E01C01
3 4
18 19 5 6 7 10 11
17 20
47 46 49 50 51 21 22
5216 259
24 14
29
55 57 54 53 59
60 582
26 27 28 15
30
56 4832 31 34 35 36 37 40 42 39 38 44
45 43 41 331 12 13
238 3 4
18 19 5 6 7 10 11
17 20
47 46 49 50 51 21 22
5216 259
24 14
29
55 57 54 53 59
60 582
26 27 28 15
30
56 4832 31 34 35 36 37 40 42 39 38 44
45 43 41 331 12 13
238
13
14
15
16
17
BLK
I6RW0D180001-01
1. Ignition switch 7. No.1 spark plug 13. Relay box
2. Main relay 8. No.2 spark plug 14. “IG ACC” fuse
3. Ignition coil assembly for No.1 and No.4 spark plugs 9. No.3 spark plug 15. “FI” fuse
4. Ignition coil assembly for No.2 and No.3 spark plugs 10. No.4 spark plug 16. Junction block assembly
5. CMP sensor 11. Sensed information 17. “IG COIL” fuse
6. CKP sensor 12. Battery fuse box
Page 398 of 1556
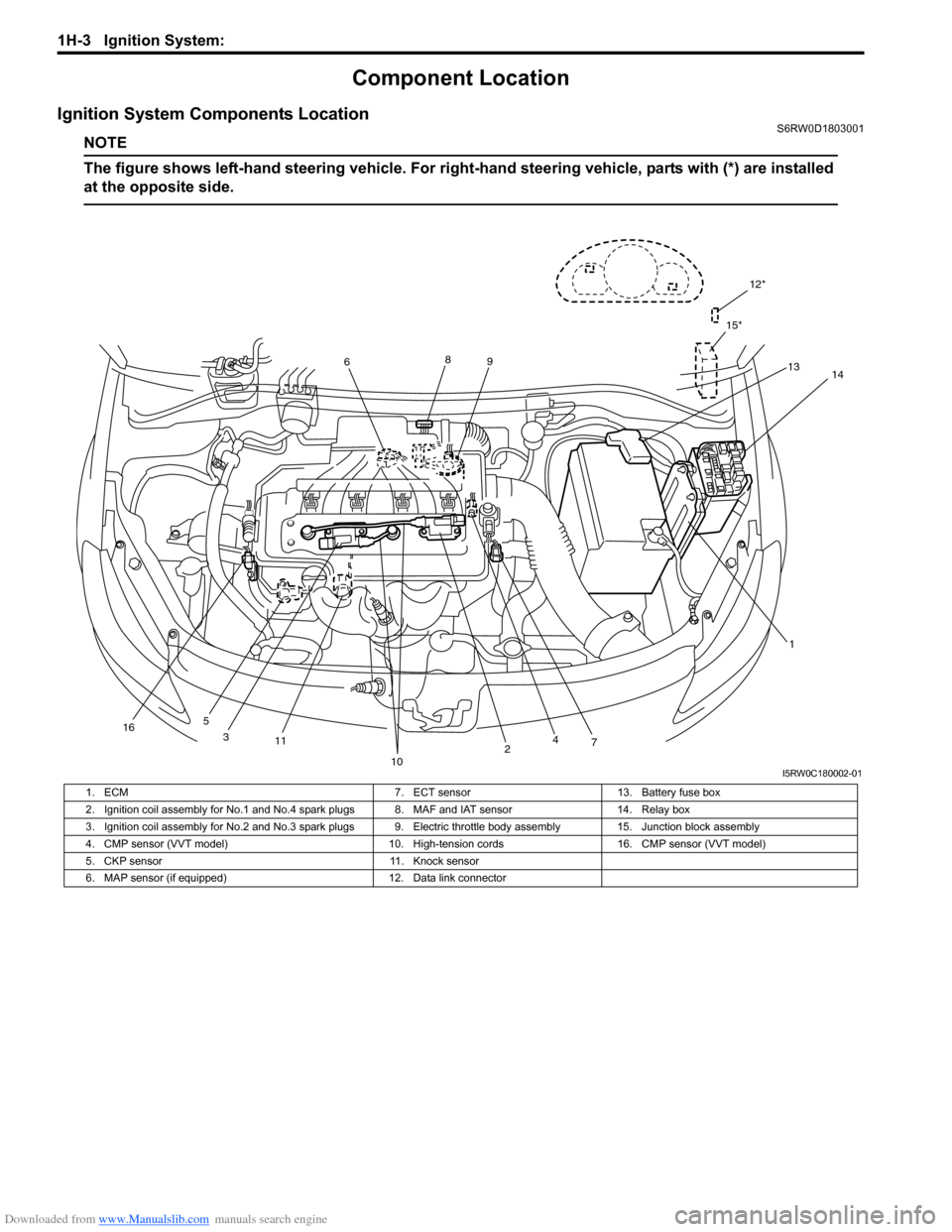
Downloaded from www.Manualslib.com manuals search engine 1H-3 Ignition System:
Component Location
Ignition System Components LocationS6RW0D1803001
NOTE
The figure shows left-hand steering vehicle. For right-hand steering vehicle, parts with (*) are installed
at the opposite side.
12*
15*
13
1 689
11
10
74
5
14
2 3
16
I5RW0C180002-01
1. ECM 7. ECT sensor 13. Battery fuse box
2. Ignition coil assembly for No.1 and No.4 spark plugs 8. MAF and IAT sensor 14. Relay box
3. Ignition coil assembly for No.2 and No.3 spark plugs 9. Electric throttle body assembly 15. Junction block assembly
4. CMP sensor (VVT model) 10. High-tension cords 16. CMP sensor (VVT model)
5. CKP sensor 11. Knock sensor
6. MAP sensor (if equipped) 12. Data link connector
Page 399 of 1556
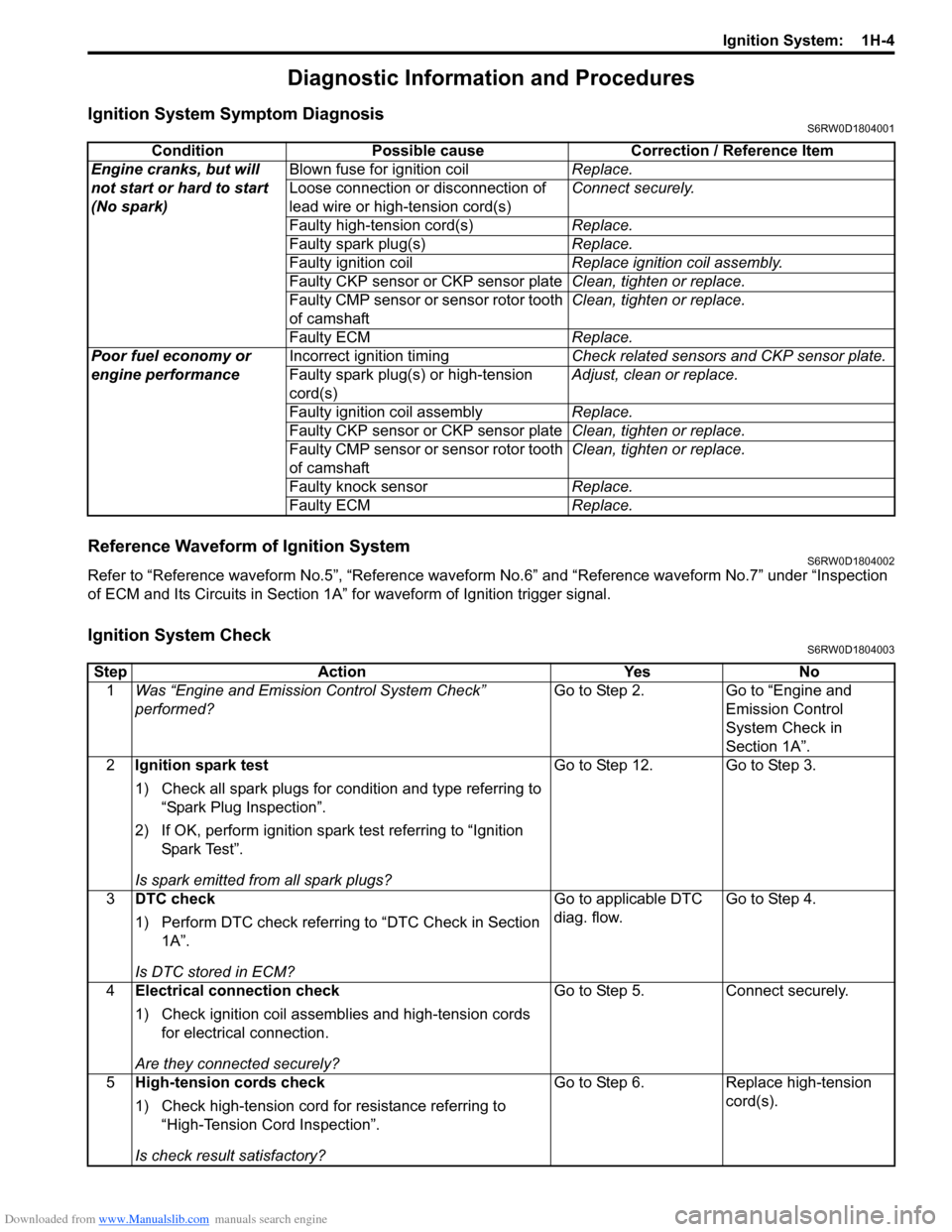
Downloaded from www.Manualslib.com manuals search engine Ignition System: 1H-4
Diagnostic Information and Procedures
Ignition System Symptom DiagnosisS6RW0D1804001
Reference Waveform of Ignition SystemS6RW0D1804002
Refer to “Reference waveform No.5”, “Reference waveform No.6” and “Reference waveform No.7” under “Inspection
of ECM and Its Circuits in Section 1A” for waveform of Ignition trigger signal.
Ignition System CheckS6RW0D1804003
Condition Possible cause Correction / Reference Item
Engine cranks, but will
not start or hard to start
(No spark)Blown fuse for ignition coilReplace.
Loose connection or disconnection of
lead wire or high-tension cord(s)Connect securely.
Faulty high-tension cord(s)Replace.
Faulty spark plug(s)Replace.
Faulty ignition coilReplace ignition coil assembly.
Faulty CKP sensor or CKP sensor plateClean, tighten or replace.
Faulty CMP sensor or sensor rotor tooth
of camshaftClean, tighten or replace.
Faulty ECMReplace.
Poor fuel economy or
engine performanceIncorrect ignition timingCheck related sensors and CKP sensor plate.
Faulty spark plug(s) or high-tension
cord(s)Adjust, clean or replace.
Faulty ignition coil assemblyReplace.
Faulty CKP sensor or CKP sensor plateClean, tighten or replace.
Faulty CMP sensor or sensor rotor tooth
of camshaftClean, tighten or replace.
Faulty knock sensorReplace.
Faulty ECMReplace.
Step Action Yes No
1Was “Engine and Emission Control System Check”
performed?Go to Step 2. Go to “Engine and
Emission Control
System Check in
Section 1A”.
2Ignition spark test
1) Check all spark plugs for condition and type referring to
“Spark Plug Inspection”.
2) If OK, perform ignition spark test referring to “Ignition
Spar k Tes t”.
Is spark emitted from all spark plugs?Go to Step 12. Go to Step 3.
3DTC check
1) Perform DTC check referring to “DTC Check in Section
1A”.
Is DTC stored in ECM?Go to applicable DTC
diag. flow.Go to Step 4.
4Electrical connection check
1) Check ignition coil assemblies and high-tension cords
for electrical connection.
Are they connected securely?Go to Step 5. Connect securely.
5High-tension cords check
1) Check high-tension cord for resistance referring to
“High-Tension Cord Inspection”.
Is check result satisfactory?Go to Step 6. Replace high-tension
cord(s).
Page 400 of 1556
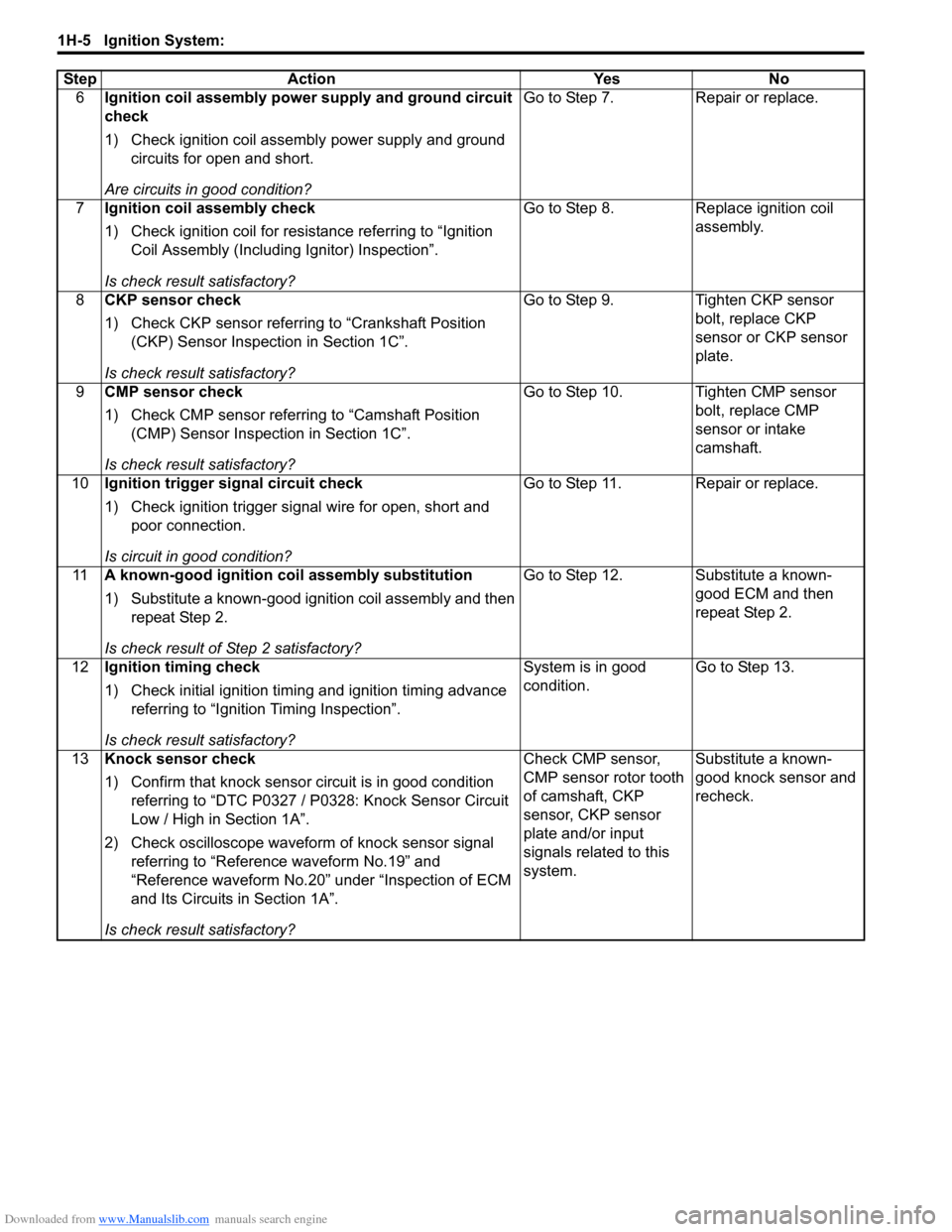
Downloaded from www.Manualslib.com manuals search engine 1H-5 Ignition System:
6Ignition coil assembly power supply and ground circuit
check
1) Check ignition coil assembly power supply and ground
circuits for open and short.
Are circuits in good condition?Go to Step 7. Repair or replace.
7Ignition coil assembly check
1) Check ignition coil for resistance referring to “Ignition
Coil Assembly (Including Ignitor) Inspection”.
Is check result satisfactory?Go to Step 8. Replace ignition coil
assembly.
8CKP sensor check
1) Check CKP sensor referring to “Crankshaft Position
(CKP) Sensor Inspection in Section 1C”.
Is check result satisfactory?Go to Step 9. Tighten CKP sensor
bolt, replace CKP
sensor or CKP sensor
plate.
9CMP sensor check
1) Check CMP sensor referring to “Camshaft Position
(CMP) Sensor Inspection in Section 1C”.
Is check result satisfactory?Go to Step 10. Tighten CMP sensor
bolt, replace CMP
sensor or intake
camshaft.
10Ignition trigger signal circuit check
1) Check ignition trigger signal wire for open, short and
poor connection.
Is circuit in good condition?Go to Step 11. Repair or replace.
11A known-good ignition coil assembly substitution
1) Substitute a known-good ignition coil assembly and then
repeat Step 2.
Is check result of Step 2 satisfactory?Go to Step 12. Substitute a known-
good ECM and then
repeat Step 2.
12Ignition timing check
1) Check initial ignition timing and ignition timing advance
referring to “Ignition Timing Inspection”.
Is check result satisfactory?System is in good
condition.Go to Step 13.
13Knock sensor check
1) Confirm that knock sensor circuit is in good condition
referring to “DTC P0327 / P0328: Knock Sensor Circuit
Low / High in Section 1A”.
2) Check oscilloscope waveform of knock sensor signal
referring to “Reference waveform No.19” and
“Reference waveform No.20” under “Inspection of ECM
and Its Circuits in Section 1A”.
Is check result satisfactory?Check CMP sensor,
CMP sensor rotor tooth
of camshaft, CKP
sensor, CKP sensor
plate and/or input
signals related to this
system.Substitute a known-
good knock sensor and
recheck. Step Action Yes No
Page 404 of 1556
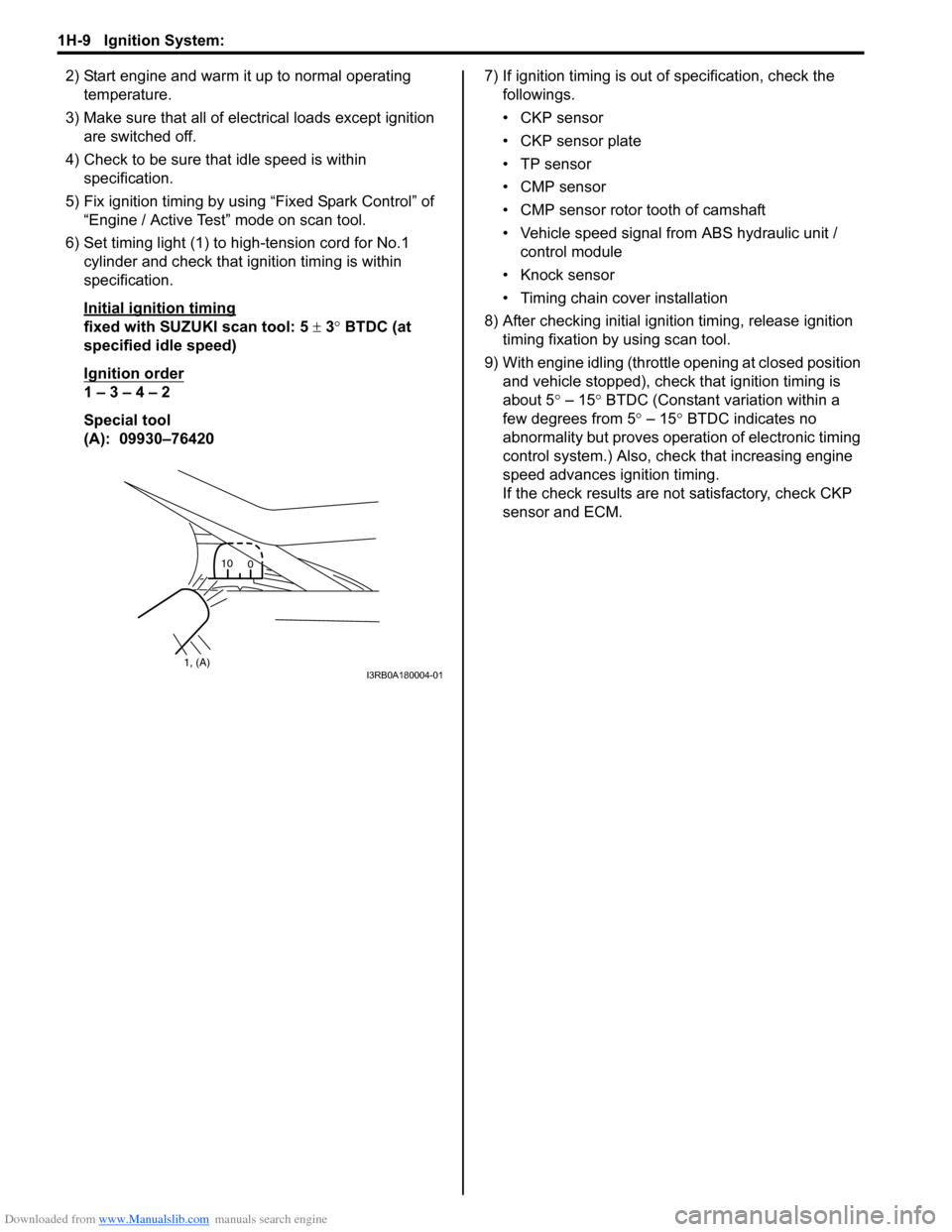
Downloaded from www.Manualslib.com manuals search engine 1H-9 Ignition System:
2) Start engine and warm it up to normal operating
temperature.
3) Make sure that all of electrical loads except ignition
are switched off.
4) Check to be sure that idle speed is within
specification.
5) Fix ignition timing by using “Fixed Spark Control” of
“Engine / Active Test” mode on scan tool.
6) Set timing light (1) to high-tension cord for No.1
cylinder and check that ignition timing is within
specification.
Initial ignition timing
fixed with SUZUKI scan tool: 5 ± 3° BTDC (at
specified idle speed)
Ignition order
1 – 3 – 4 – 2
Special tool
(A): 09930–764207) If ignition timing is out of specification, check the
followings.
• CKP sensor
• CKP sensor plate
• TP sensor
• CMP sensor
• CMP sensor rotor tooth of camshaft
• Vehicle speed signal from ABS hydraulic unit /
control module
• Knock sensor
• Timing chain cover installation
8) After checking initial ignition timing, release ignition
timing fixation by using scan tool.
9) With engine idling (throttle opening at closed position
and vehicle stopped), check that ignition timing is
about 5° – 15° BTDC (Constant variation within a
few degrees from 5° – 15° BTDC indicates no
abnormality but proves operation of electronic timing
control system.) Also, check that increasing engine
speed advances ignition timing.
If the check results are not satisfactory, check CKP
sensor and ECM.
1, (A)10
0I3RB0A180004-01
Page 406 of 1556
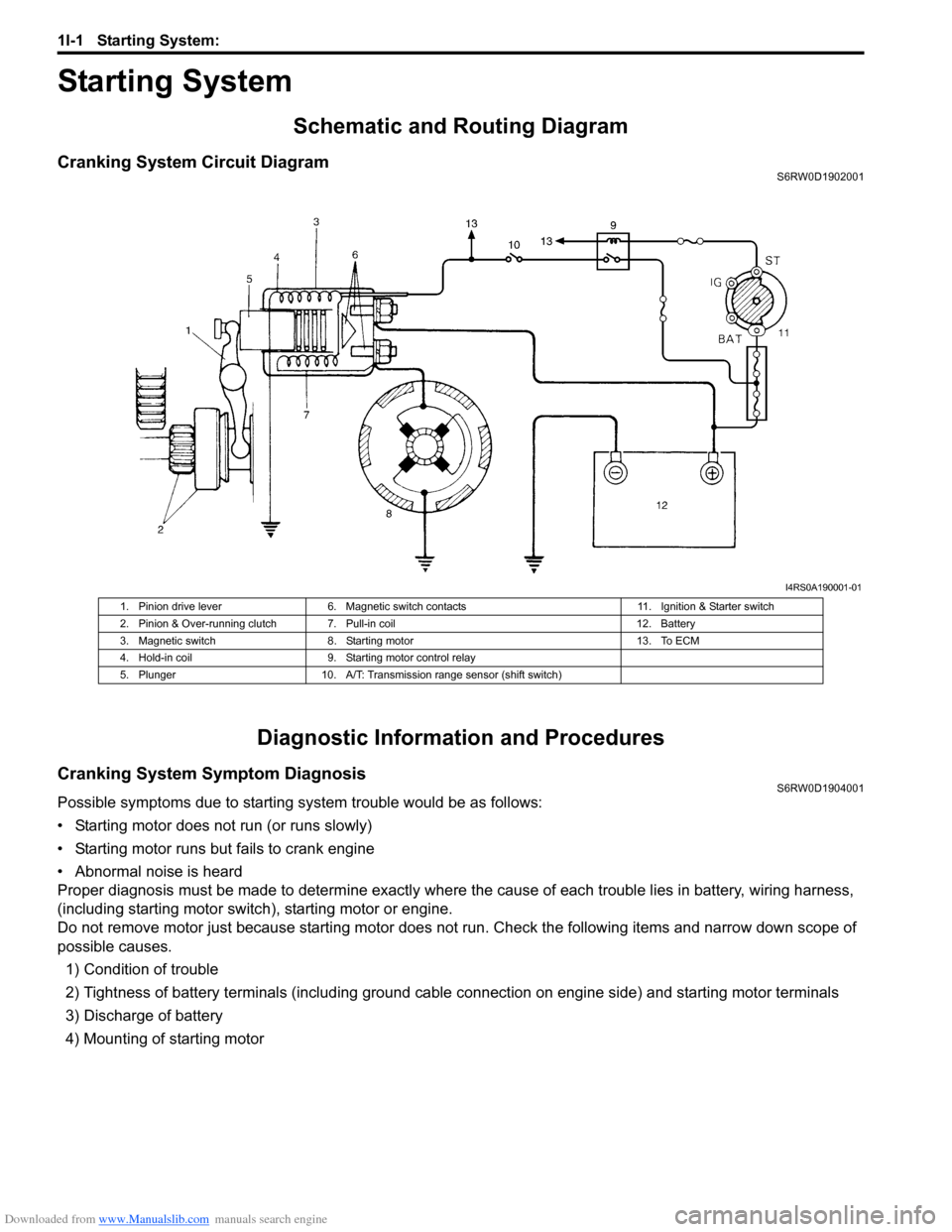
Downloaded from www.Manualslib.com manuals search engine 1I-1 Starting System:
Engine
Starting System
Schematic and Routing Diagram
Cranking System Circuit DiagramS6RW0D1902001
Diagnostic Information and Procedures
Cranking System Symptom DiagnosisS6RW0D1904001
Possible symptoms due to starting system trouble would be as follows:
• Starting motor does not run (or runs slowly)
• Starting motor runs but fails to crank engine
• Abnormal noise is heard
Proper diagnosis must be made to determine exactly where the cause of each trouble lies in battery, wiring harness,
(including starting motor switch), starting motor or engine.
Do not remove motor just because starting motor does not run. Check the following items and narrow down scope of
possible causes.
1) Condition of trouble
2) Tightness of battery terminals (including ground cable connection on engine side) and starting motor terminals
3) Discharge of battery
4) Mounting of starting motor
I4RS0A190001-01
1. Pinion drive lever 6. Magnetic switch contacts 11. Ignition & Starter switch
2. Pinion & Over-running clutch 7. Pull-in coil 12. Battery
3. Magnetic switch 8. Starting motor 13. To ECM
4. Hold-in coil 9. Starting motor control relay
5. Plunger 10. A/T: Transmission range sensor (shift switch)
Page 407 of 1556
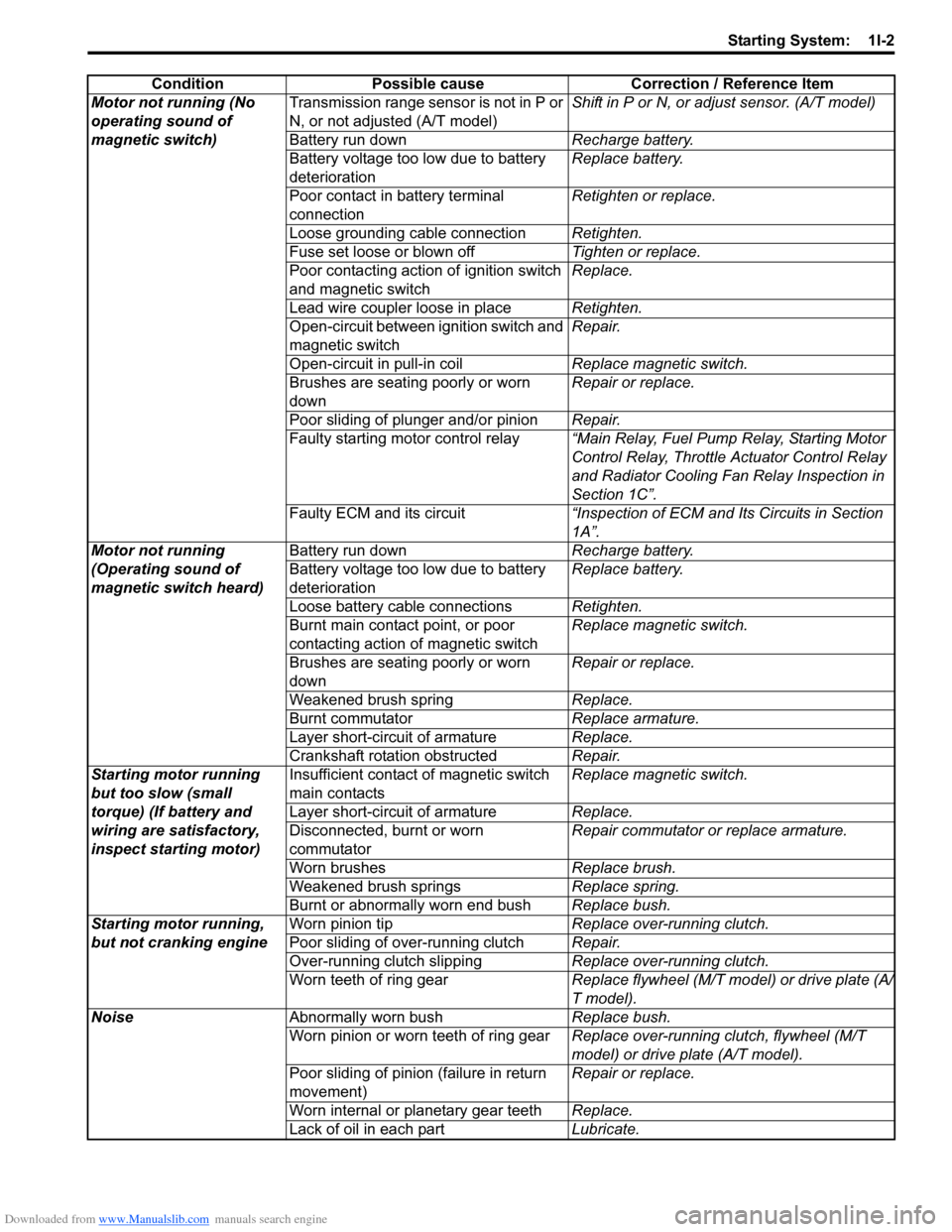
Downloaded from www.Manualslib.com manuals search engine Starting System: 1I-2
Condition Possible cause Correction / Reference Item
Motor not running (No
operating sound of
magnetic switch)Transmission range sensor is not in P or
N, or not adjusted (A/T model)Shift in P or N, or adjust sensor. (A/T model)
Battery run downRecharge battery.
Battery voltage too low due to battery
deteriorationReplace battery.
Poor contact in battery terminal
connectionRetighten or replace.
Loose grounding cable connectionRetighten.
Fuse set loose or blown offTighten or replace.
Poor contacting action of ignition switch
and magnetic switchReplace.
Lead wire coupler loose in placeRetighten.
Open-circuit between ignition switch and
magnetic switchRepair.
Open-circuit in pull-in coilReplace magnetic switch.
Brushes are seating poorly or worn
downRepair or replace.
Poor sliding of plunger and/or pinionRepair.
Faulty starting motor control relay“Main Relay, Fuel Pump Relay, Starting Motor
Control Relay, Throttle Actuator Control Relay
and Radiator Cooling Fan Relay Inspection in
Section 1C”.
Faulty ECM and its circuit“Inspection of ECM and Its Circuits in Section
1A”.
Motor not running
(Operating sound of
magnetic switch heard)Battery run downRecharge battery.
Battery voltage too low due to battery
deteriorationReplace battery.
Loose battery cable connectionsRetighten.
Burnt main contact point, or poor
contacting action of magnetic switchReplace magnetic switch.
Brushes are seating poorly or worn
downRepair or replace.
Weakened brush springReplace.
Burnt commutatorReplace armature.
Layer short-circuit of armatureReplace.
Crankshaft rotation obstructedRepair.
Starting motor running
but too slow (small
torque) (If battery and
wiring are satisfactory,
inspect starting motor)Insufficient contact of magnetic switch
main contactsReplace magnetic switch.
Layer short-circuit of armatureReplace.
Disconnected, burnt or worn
commutatorRepair commutator or replace armature.
Worn brushesReplace brush.
Weakened brush springsReplace spring.
Burnt or abnormally worn end bushReplace bush.
Starting motor running,
but not cranking engineWorn pinion tipReplace over-running clutch.
Poor sliding of over-running clutchRepair.
Over-running clutch slippingReplace over-running clutch.
Worn teeth of ring gearReplace flywheel (M/T model) or drive plate (A/
T model).
NoiseAbnormally worn bushReplace bush.
Worn pinion or worn teeth of ring gearReplace over-running clutch, flywheel (M/T
model) or drive plate (A/T model).
Poor sliding of pinion (failure in return
movement)Repair or replace.
Worn internal or planetary gear teethReplace.
Lack of oil in each partLubricate.