SUZUKI SX4 2006 1.G Service Workshop Manual
Manufacturer: SUZUKI, Model Year: 2006, Model line: SX4, Model: SUZUKI SX4 2006 1.GPages: 1556, PDF Size: 37.31 MB
Page 371 of 1556
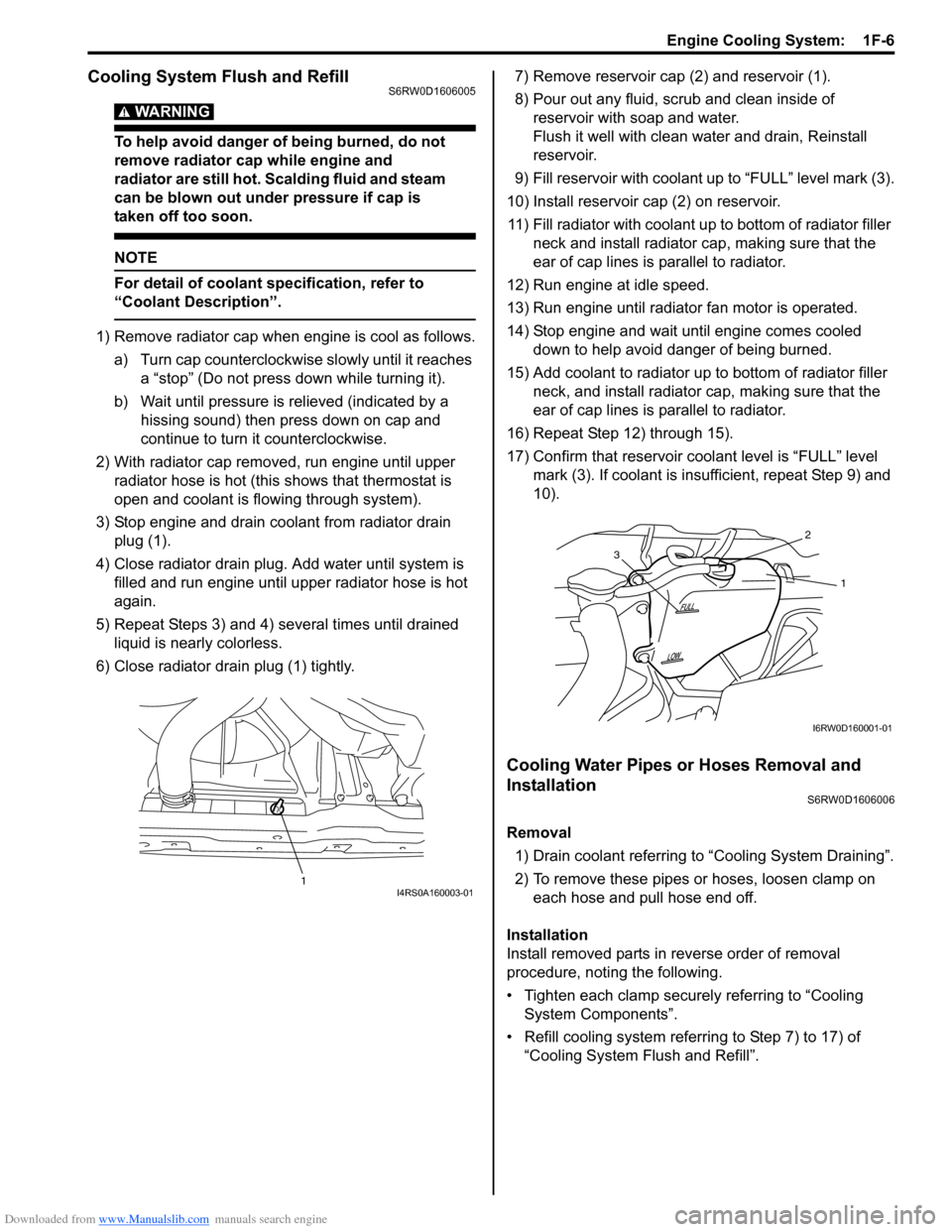
Downloaded from www.Manualslib.com manuals search engine Engine Cooling System: 1F-6
Cooling System Flush and RefillS6RW0D1606005
WARNING!
To help avoid danger of being burned, do not
remove radiator cap while engine and
radiator are still hot. Scalding fluid and steam
can be blown out under pressure if cap is
taken off too soon.
NOTE
For detail of coolant specification, refer to
“Coolant Description”.
1) Remove radiator cap when engine is cool as follows.
a) Turn cap counterclockwise slowly until it reaches
a “stop” (Do not press down while turning it).
b) Wait until pressure is relieved (indicated by a
hissing sound) then press down on cap and
continue to turn it counterclockwise.
2) With radiator cap removed, run engine until upper
radiator hose is hot (this shows that thermostat is
open and coolant is flowing through system).
3) Stop engine and drain coolant from radiator drain
plug (1).
4) Close radiator drain plug. Add water until system is
filled and run engine until upper radiator hose is hot
again.
5) Repeat Steps 3) and 4) several times until drained
liquid is nearly colorless.
6) Close radiator drain plug (1) tightly.7) Remove reservoir cap (2) and reservoir (1).
8) Pour out any fluid, scrub and clean inside of
reservoir with soap and water.
Flush it well with clean water and drain, Reinstall
reservoir.
9) Fill reservoir with coolant up to “FULL” level mark (3).
10) Install reservoir cap (2) on reservoir.
11) Fill radiator with coolant up to bottom of radiator filler
neck and install radiator cap, making sure that the
ear of cap lines is parallel to radiator.
12) Run engine at idle speed.
13) Run engine until radiator fan motor is operated.
14) Stop engine and wait until engine comes cooled
down to help avoid danger of being burned.
15) Add coolant to radiator up to bottom of radiator filler
neck, and install radiator cap, making sure that the
ear of cap lines is parallel to radiator.
16) Repeat Step 12) through 15).
17) Confirm that reservoir coolant level is “FULL” level
mark (3). If coolant is insufficient, repeat Step 9) and
10).
Cooling Water Pipes or Hoses Removal and
Installation
S6RW0D1606006
Removal
1) Drain coolant referring to “Cooling System Draining”.
2) To remove these pipes or hoses, loosen clamp on
each hose and pull hose end off.
Installation
Install removed parts in reverse order of removal
procedure, noting the following.
• Tighten each clamp securely referring to “Cooling
System Components”.
• Refill cooling system referring to Step 7) to 17) of
“Cooling System Flush and Refill”.
1I4RS0A160003-01
2
1
3
I6RW0D160001-01
Page 372 of 1556
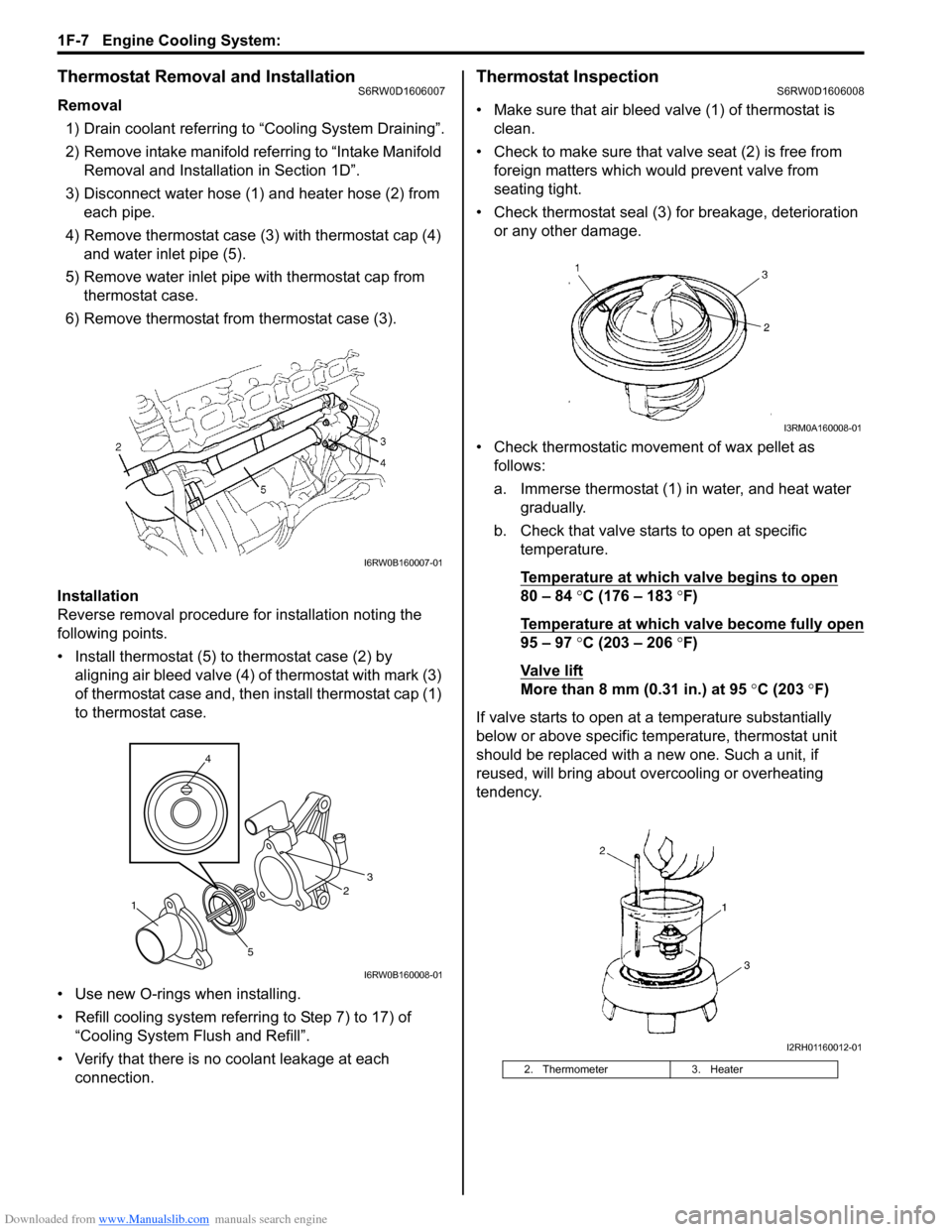
Downloaded from www.Manualslib.com manuals search engine 1F-7 Engine Cooling System:
Thermostat Removal and InstallationS6RW0D1606007
Removal
1) Drain coolant referring to “Cooling System Draining”.
2) Remove intake manifold referring to “Intake Manifold
Removal and Installation in Section 1D”.
3) Disconnect water hose (1) and heater hose (2) from
each pipe.
4) Remove thermostat case (3) with thermostat cap (4)
and water inlet pipe (5).
5) Remove water inlet pipe with thermostat cap from
thermostat case.
6) Remove thermostat from thermostat case (3).
Installation
Reverse removal procedure for installation noting the
following points.
• Install thermostat (5) to thermostat case (2) by
aligning air bleed valve (4) of thermostat with mark (3)
of thermostat case and, then install thermostat cap (1)
to thermostat case.
• Use new O-rings when installing.
• Refill cooling system referring to Step 7) to 17) of
“Cooling System Flush and Refill”.
• Verify that there is no coolant leakage at each
connection.
Thermostat InspectionS6RW0D1606008
• Make sure that air bleed valve (1) of thermostat is
clean.
• Check to make sure that valve seat (2) is free from
foreign matters which would prevent valve from
seating tight.
• Check thermostat seal (3) for breakage, deterioration
or any other damage.
• Check thermostatic movement of wax pellet as
follows:
a. Immerse thermostat (1) in water, and heat water
gradually.
b. Check that valve starts to open at specific
temperature.
Temperature at which valve begins to open
80 – 84 °C (176 – 183 °F)
Temperature at which valve become fully open
95 – 97 °C (203 – 206 °F)
Va l v e l i ft
More than 8 mm (0.31 in.) at 95 °C (203 °F)
If valve starts to open at a temperature substantially
below or above specific temperature, thermostat unit
should be replaced with a new one. Such a unit, if
reused, will bring about overcooling or overheating
tendency.
I6RW0B160007-01
4
53
12
I6RW0B160008-01
2. Thermometer 3. Heater
I3RM0A160008-01
I2RH01160012-01
Page 373 of 1556
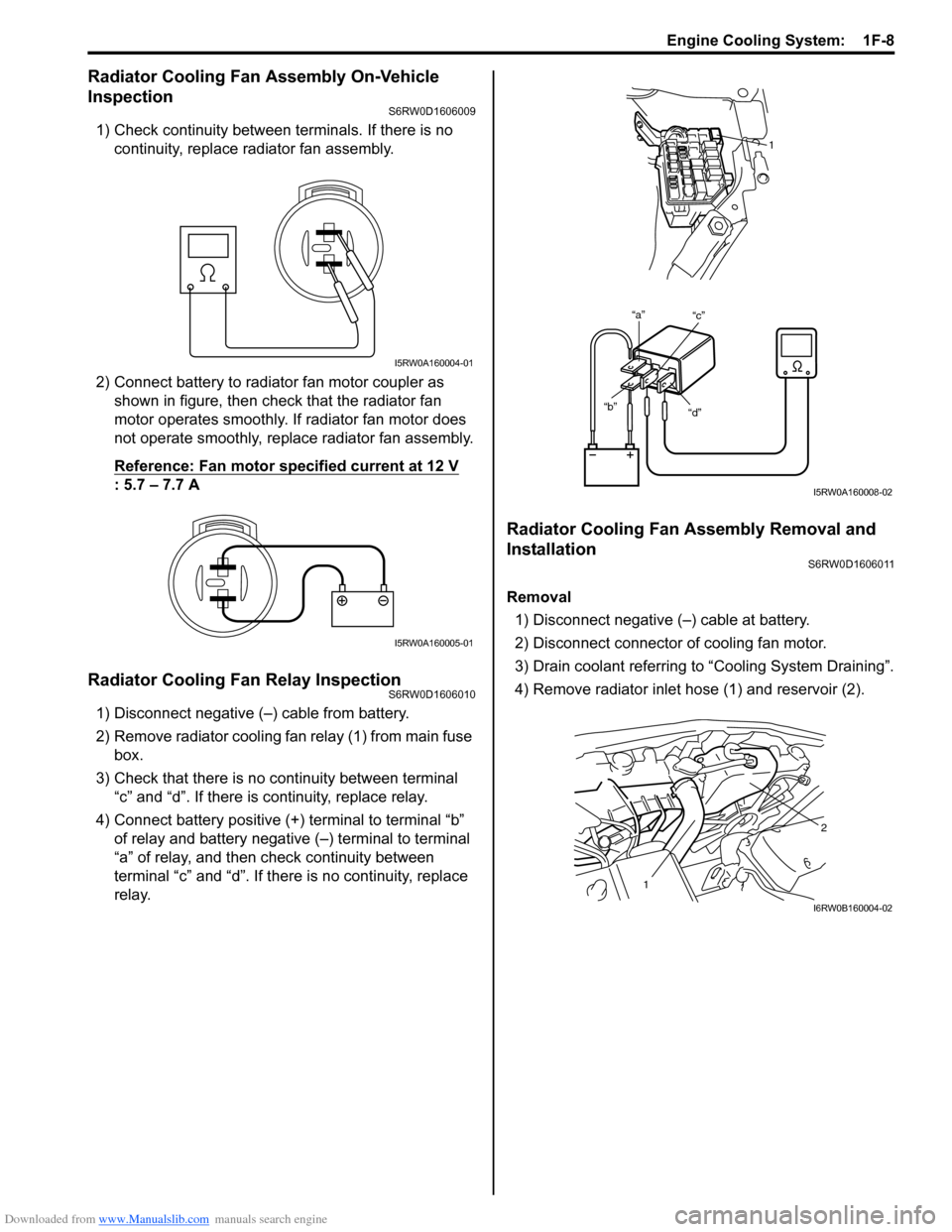
Downloaded from www.Manualslib.com manuals search engine Engine Cooling System: 1F-8
Radiator Cooling Fan Assembly On-Vehicle
Inspection
S6RW0D1606009
1) Check continuity between terminals. If there is no
continuity, replace radiator fan assembly.
2) Connect battery to radiator fan motor coupler as
shown in figure, then check that the radiator fan
motor operates smoothly. If radiator fan motor does
not operate smoothly, replace radiator fan assembly.
Reference: Fan motor specified current at 12 V
: 5.7 – 7.7 A
Radiator Cooling Fan Relay InspectionS6RW0D1606010
1) Disconnect negative (–) cable from battery.
2) Remove radiator cooling fan relay (1) from main fuse
box.
3) Check that there is no continuity between terminal
“c” and “d”. If there is continuity, replace relay.
4) Connect battery positive (+) terminal to terminal “b”
of relay and battery negative (–) terminal to terminal
“a” of relay, and then check continuity between
terminal “c” and “d”. If there is no continuity, replace
relay.
Radiator Cooling Fan Assembly Removal and
Installation
S6RW0D1606011
Removal
1) Disconnect negative (–) cable at battery.
2) Disconnect connector of cooling fan motor.
3) Drain coolant referring to “Cooling System Draining”.
4) Remove radiator inlet hose (1) and reservoir (2).
I5RW0A160004-01
I5RW0A160005-01
“d” “b”“
a”
“c”
1
I5RW0A160008-02
1
2
I6RW0B160004-02
Page 374 of 1556
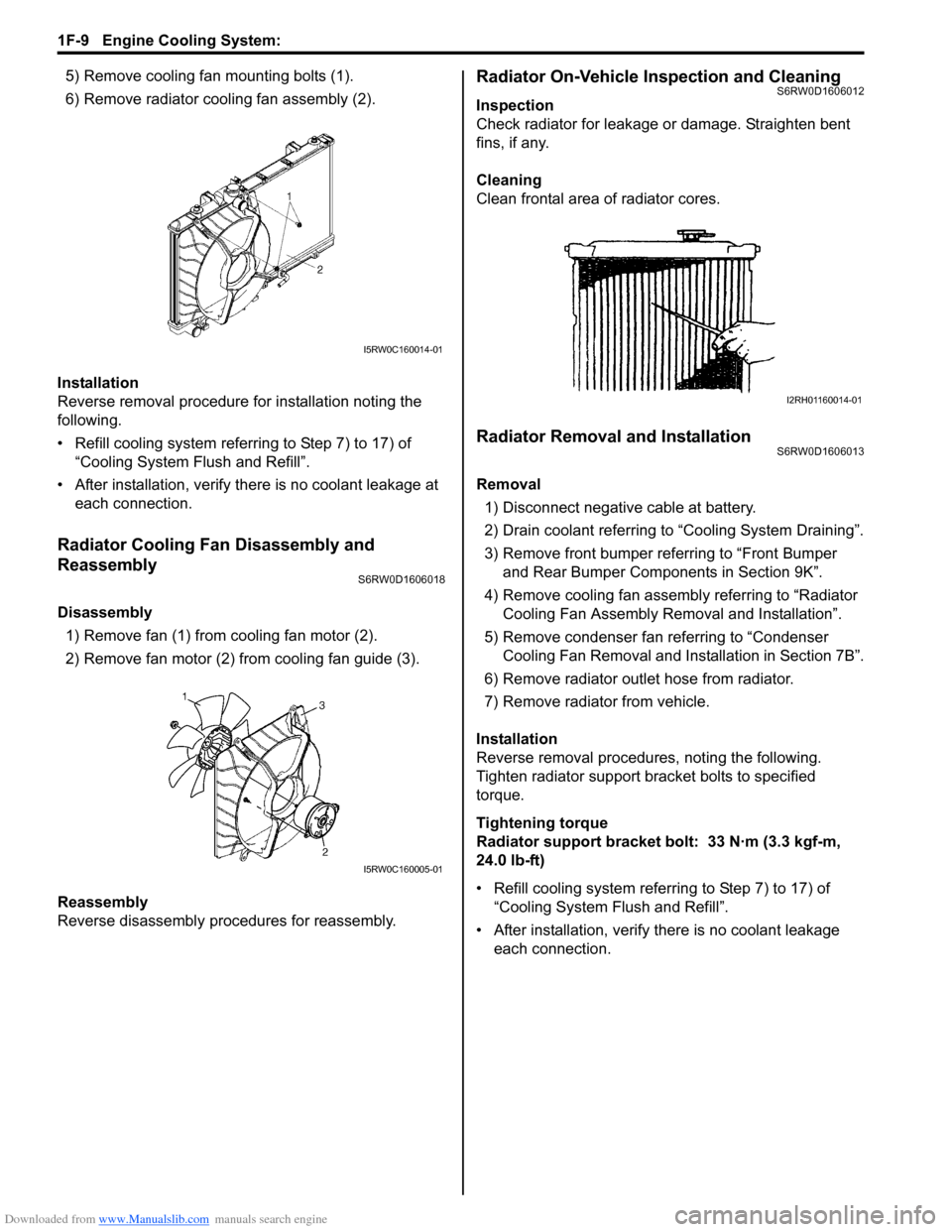
Downloaded from www.Manualslib.com manuals search engine 1F-9 Engine Cooling System:
5) Remove cooling fan mounting bolts (1).
6) Remove radiator cooling fan assembly (2).
Installation
Reverse removal procedure for installation noting the
following.
• Refill cooling system referring to Step 7) to 17) of
“Cooling System Flush and Refill”.
• After installation, verify there is no coolant leakage at
each connection.
Radiator Cooling Fan Disassembly and
Reassembly
S6RW0D1606018
Disassembly
1) Remove fan (1) from cooling fan motor (2).
2) Remove fan motor (2) from cooling fan guide (3).
Reassembly
Reverse disassembly procedures for reassembly.
Radiator On-Vehicle Inspection and CleaningS6RW0D1606012
Inspection
Check radiator for leakage or damage. Straighten bent
fins, if any.
Cleaning
Clean frontal area of radiator cores.
Radiator Removal and InstallationS6RW0D1606013
Removal
1) Disconnect negative cable at battery.
2) Drain coolant referring to “Cooling System Draining”.
3) Remove front bumper referring to “Front Bumper
and Rear Bumper Components in Section 9K”.
4) Remove cooling fan assembly referring to “Radiator
Cooling Fan Assembly Removal and Installation”.
5) Remove condenser fan referring to “Condenser
Cooling Fan Removal and Installation in Section 7B”.
6) Remove radiator outlet hose from radiator.
7) Remove radiator from vehicle.
Installation
Reverse removal procedures, noting the following.
Tighten radiator support bracket bolts to specified
torque.
Tightening torque
Radiator support bracket bolt: 33 N·m (3.3 kgf-m,
24.0 lb-ft)
• Refill cooling system referring to Step 7) to 17) of
“Cooling System Flush and Refill”.
• After installation, verify there is no coolant leakage
each connection.
I5RW0C160014-01
I5RW0C160005-01
I2RH01160014-01
Page 375 of 1556
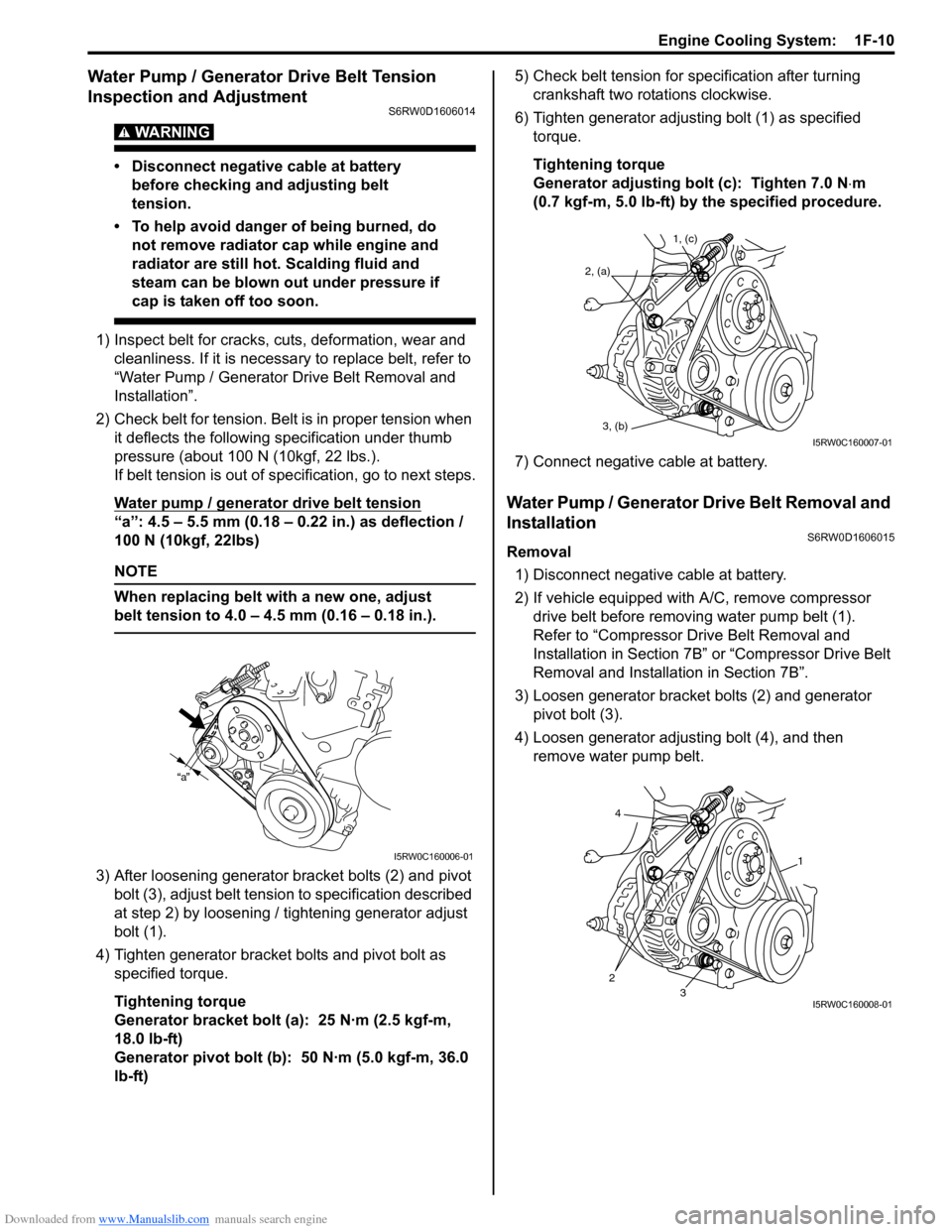
Downloaded from www.Manualslib.com manuals search engine Engine Cooling System: 1F-10
Water Pump / Generator Drive Belt Tension
Inspection and Adjustment
S6RW0D1606014
WARNING!
• Disconnect negative cable at battery
before checking and adjusting belt
tension.
• To help avoid danger of being burned, do
not remove radiator cap while engine and
radiator are still hot. Scalding fluid and
steam can be blown out under pressure if
cap is taken off too soon.
1) Inspect belt for cracks, cuts, deformation, wear and
cleanliness. If it is necessary to replace belt, refer to
“Water Pump / Generator Drive Belt Removal and
Installation”.
2) Check belt for tension. Belt is in proper tension when
it deflects the following specification under thumb
pressure (about 100 N (10kgf, 22 lbs.).
If belt tension is out of specification, go to next steps.
Water pump / generator drive belt tension
“a”: 4.5 – 5.5 mm (0.18 – 0.22 in.) as deflection /
100 N (10kgf, 22lbs)
NOTE
When replacing belt with a new one, adjust
belt tension to 4.0 – 4.5 mm (0.16 – 0.18 in.).
3) After loosening generator bracket bolts (2) and pivot
bolt (3), adjust belt tension to specification described
at step 2) by loosening / tightening generator adjust
bolt (1).
4) Tighten generator bracket bolts and pivot bolt as
specified torque.
Tightening torque
Generator bracket bolt (a): 25 N·m (2.5 kgf-m,
18.0 lb-ft)
Generator pivot bolt (b): 50 N·m (5.0 kgf-m, 36.0
lb-ft)5) Check belt tension for specification after turning
crankshaft two rotations clockwise.
6) Tighten generator adjusting bolt (1) as specified
torque.
Tightening torque
Generator adjusting bolt (c): Tighten 7.0 N⋅m
(0.7 kgf-m, 5.0 lb-ft) by the specified procedure.
7) Connect negative cable at battery.
Water Pump / Generator Drive Belt Removal and
Installation
S6RW0D1606015
Removal
1) Disconnect negative cable at battery.
2) If vehicle equipped with A/C, remove compressor
drive belt before removing water pump belt (1).
Refer to “Compressor Drive Belt Removal and
Installation in Section 7B” or “Compressor Drive Belt
Removal and Installation in Section 7B”.
3) Loosen generator bracket bolts (2) and generator
pivot bolt (3).
4) Loosen generator adjusting bolt (4), and then
remove water pump belt.
a
I5RW0C160006-01
1, (c)
2, (a)
3, (b)
I5RW0C160007-01
4
23
1
I5RW0C160008-01
Page 376 of 1556
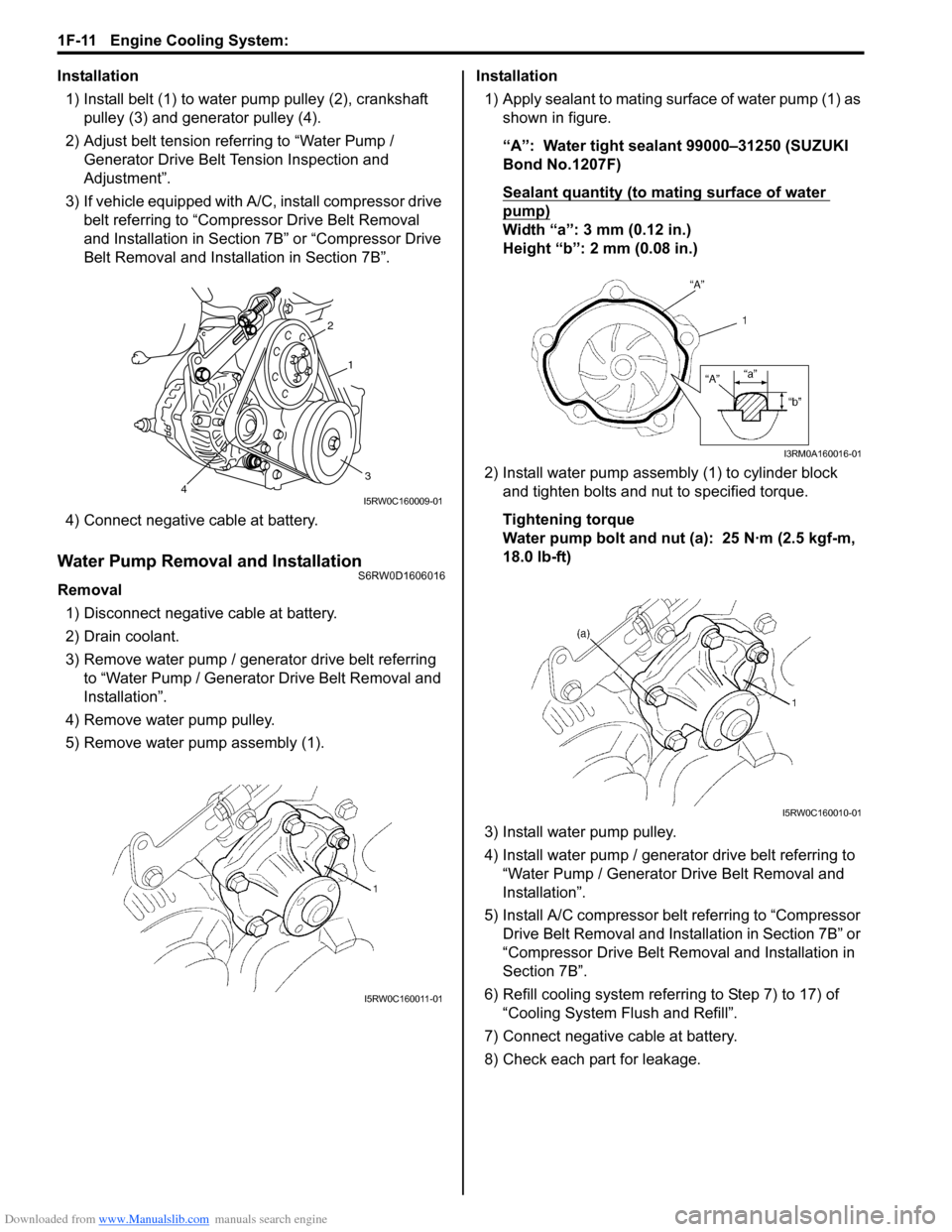
Downloaded from www.Manualslib.com manuals search engine 1F-11 Engine Cooling System:
Installation
1) Install belt (1) to water pump pulley (2), crankshaft
pulley (3) and generator pulley (4).
2) Adjust belt tension referring to “Water Pump /
Generator Drive Belt Tension Inspection and
Adjustment”.
3) If vehicle equipped with A/C, install compressor drive
belt referring to “Compressor Drive Belt Removal
and Installation in Section 7B” or “Compressor Drive
Belt Removal and Installation in Section 7B”.
4) Connect negative cable at battery.
Water Pump Removal and InstallationS6RW0D1606016
Removal
1) Disconnect negative cable at battery.
2) Drain coolant.
3) Remove water pump / generator drive belt referring
to “Water Pump / Generator Drive Belt Removal and
Installation”.
4) Remove water pump pulley.
5) Remove water pump assembly (1).Installation
1) Apply sealant to mating surface of water pump (1) as
shown in figure.
“A”: Water tight sealant 99000–31250 (SUZUKI
Bond No.1207F)
Sealant quantity (to mating surface of water
pump)
Width “a”: 3 mm (0.12 in.)
Height “b”: 2 mm (0.08 in.)
2) Install water pump assembly (1) to cylinder block
and tighten bolts and nut to specified torque.
Tightening torque
Water pump bolt and nut (a): 25 N·m (2.5 kgf-m,
18.0 lb-ft)
3) Install water pump pulley.
4) Install water pump / generator drive belt referring to
“Water Pump / Generator Drive Belt Removal and
Installation”.
5) Install A/C compressor belt referring to “Compressor
Drive Belt Removal and Installation in Section 7B” or
“Compressor Drive Belt Removal and Installation in
Section 7B”.
6) Refill cooling system referring to Step 7) to 17) of
“Cooling System Flush and Refill”.
7) Connect negative cable at battery.
8) Check each part for leakage.
2
1
34I5RW0C160009-01
I5RW0C160011-01
I3RM0A160016-01
I5RW0C160010-01
Page 377 of 1556

Downloaded from www.Manualslib.com manuals search engine Engine Cooling System: 1F-12
Water Pump InspectionS6RW0D1606017
CAUTION!
Do not disassemble water pump.
If any repair is required on pump, replace it
as assembly.
Rotate water pump by hand to check for smooth
operation. If pump does not rotate smoothly or makes
abnormal noise, replace it.
Specifications
Tightening Torque SpecificationsS6RW0D1607001
NOTE
The specified tightening torque is also described in the following.
“Cooling System Components”
Reference:
For the tightening torque of fastener not specified in this section, refer to “Fasteners Information in Section 0A”.
Special Tools and Equipment
Recommended Service MaterialS6RW0D1608001
I2RH0B160019-01
Fastening partTightening torque
Note
N⋅mkgf-mlb-ft
Radiator support bracket bolt 33 3.3 24.0 )
Generator bracket bolt 25 2.5 18.0 )
Generator pivot bolt 50 5.0 36.0 )
Generator adjusting bolt Tighten 7.0 N⋅m (0.7 kgf-m, 5.0 lb-ft) by the
specified procedure. )
Water pump bolt and nut 25 2.5 18.0 )
Material SUZUKI recommended product or Specification Note
Water tight sealant SUZUKI Bond No.1207F P/No.: 99000–31250 )
Page 378 of 1556
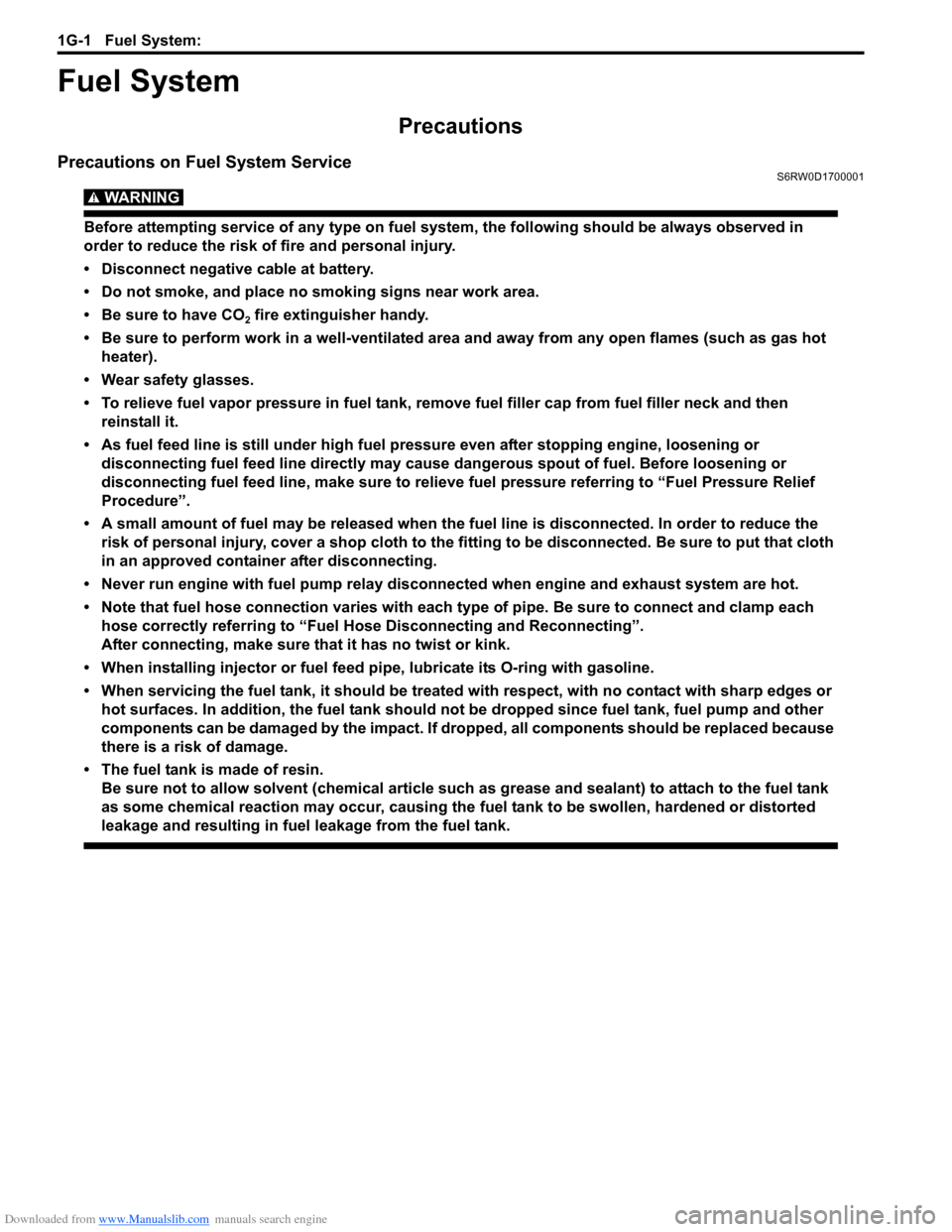
Downloaded from www.Manualslib.com manuals search engine 1G-1 Fuel System:
Engine
Fuel System
Precautions
Precautions on Fuel System ServiceS6RW0D1700001
WARNING!
Before attempting service of any type on fuel system, the following should be always observed in
order to reduce the risk of fire and personal injury.
• Disconnect negative cable at battery.
• Do not smoke, and place no smoking signs near work area.
• Be sure to have CO
2 fire extinguisher handy.
• Be sure to perform work in a well-ventilated area and away from any open flames (such as gas hot
heater).
• Wear safety glasses.
• To relieve fuel vapor pressure in fuel tank, remove fuel filler cap from fuel filler neck and then
reinstall it.
• As fuel feed line is still under high fuel pressure even after stopping engine, loosening or
disconnecting fuel feed line directly may cause dangerous spout of fuel. Before loosening or
disconnecting fuel feed line, make sure to relieve fuel pressure referring to “Fuel Pressure Relief
Procedure”.
• A small amount of fuel may be released when the fuel line is disconnected. In order to reduce the
risk of personal injury, cover a shop cloth to the fitting to be disconnected. Be sure to put that cloth
in an approved container after disconnecting.
• Never run engine with fuel pump relay disconnected when engine and exhaust system are hot.
• Note that fuel hose connection varies with each type of pipe. Be sure to connect and clamp each
hose correctly referring to “Fuel Hose Disconnecting and Reconnecting”.
After connecting, make sure that it has no twist or kink.
• When installing injector or fuel feed pipe, lubricate its O-ring with gasoline.
• When servicing the fuel tank, it should be treated with respect, with no contact with sharp edges or
hot surfaces. In addition, the fuel tank should not be dropped since fuel tank, fuel pump and other
components can be damaged by the impact. If dropped, all components should be replaced because
there is a risk of damage.
• The fuel tank is made of resin.
Be sure not to allow solvent (chemical article such as grease and sealant) to attach to the fuel tank
as some chemical reaction may occur, causing the fuel tank to be swollen, hardened or distorted
leakage and resulting in fuel leakage from the fuel tank.
Page 379 of 1556
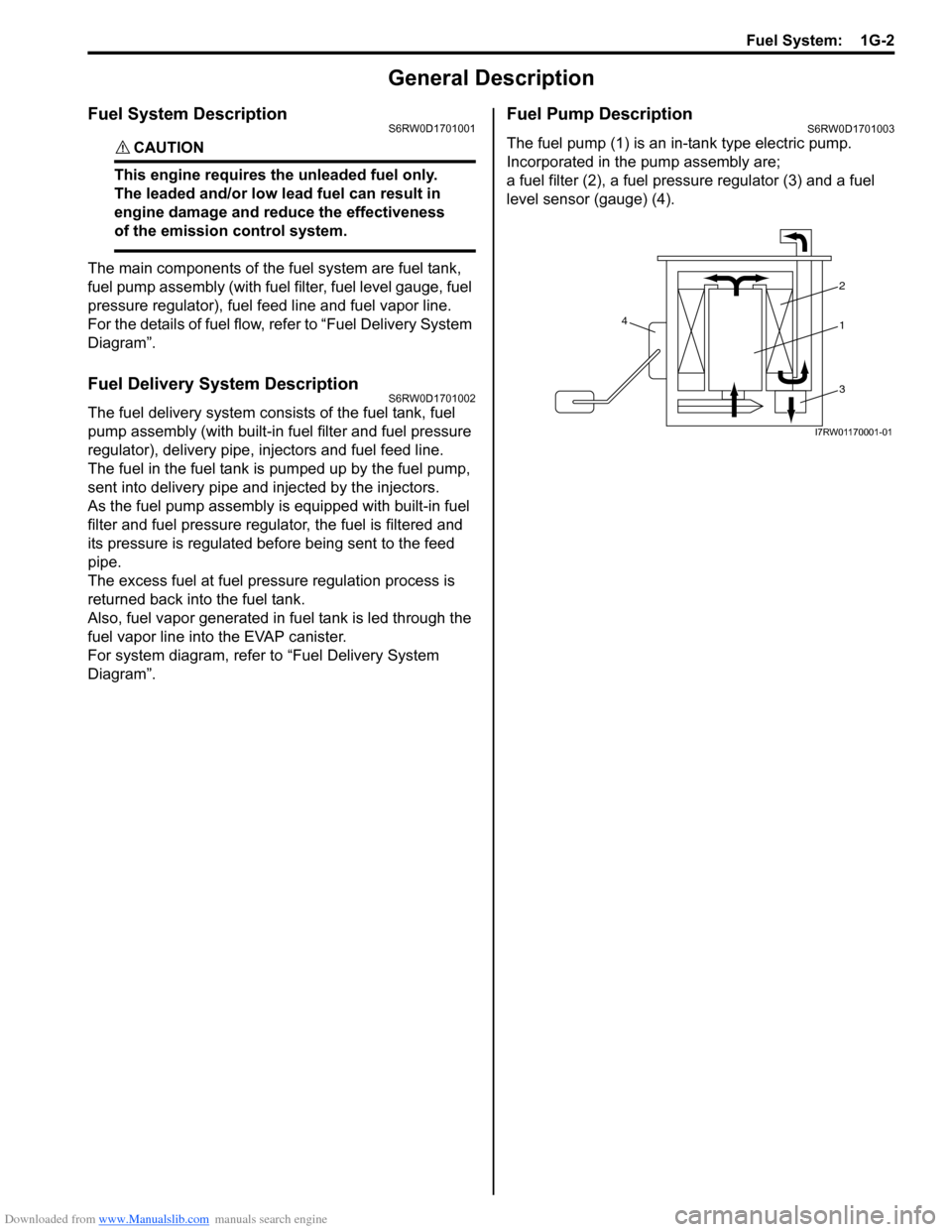
Downloaded from www.Manualslib.com manuals search engine Fuel System: 1G-2
General Description
Fuel System DescriptionS6RW0D1701001
CAUTION!
This engine requires the unleaded fuel only.
The leaded and/or low lead fuel can result in
engine damage and reduce the effectiveness
of the emission control system.
The main components of the fuel system are fuel tank,
fuel pump assembly (with fuel filter, fuel level gauge, fuel
pressure regulator), fuel feed line and fuel vapor line.
For the details of fuel flow, refer to “Fuel Delivery System
Diagram”.
Fuel Delivery System DescriptionS6RW0D1701002
The fuel delivery system consists of the fuel tank, fuel
pump assembly (with built-in fuel filter and fuel pressure
regulator), delivery pipe, injectors and fuel feed line.
The fuel in the fuel tank is pumped up by the fuel pump,
sent into delivery pipe and injected by the injectors.
As the fuel pump assembly is equipped with built-in fuel
filter and fuel pressure regulator, the fuel is filtered and
its pressure is regulated before being sent to the feed
pipe.
The excess fuel at fuel pressure regulation process is
returned back into the fuel tank.
Also, fuel vapor generated in fuel tank is led through the
fuel vapor line into the EVAP canister.
For system diagram, refer to “Fuel Delivery System
Diagram”.
Fuel Pump DescriptionS6RW0D1701003
The fuel pump (1) is an in-tank type electric pump.
Incorporated in the pump assembly are;
a fuel filter (2), a fuel pressure regulator (3) and a fuel
level sensor (gauge) (4).
2
41
3
I7RW01170001-01
Page 380 of 1556
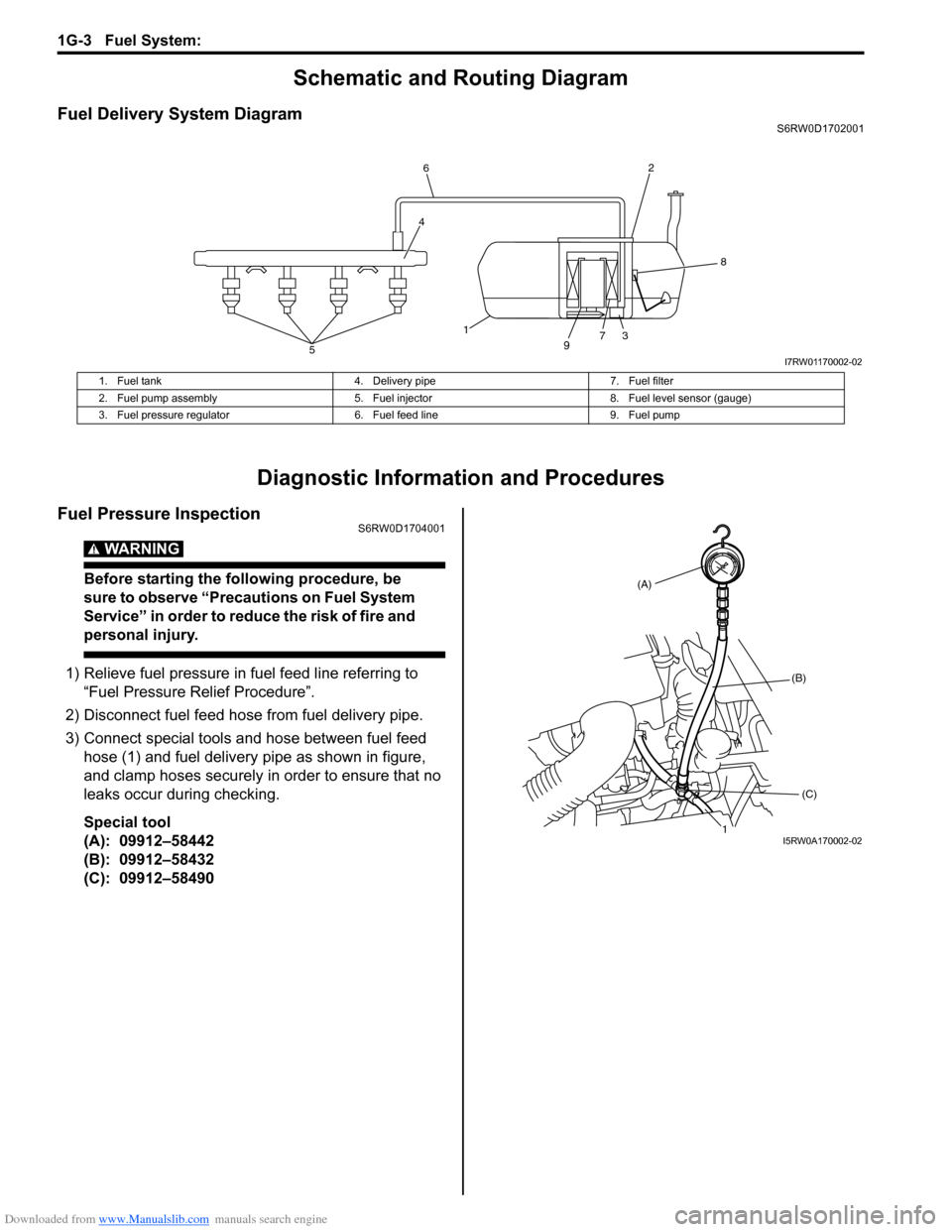
Downloaded from www.Manualslib.com manuals search engine 1G-3 Fuel System:
Schematic and Routing Diagram
Fuel Delivery System DiagramS6RW0D1702001
Diagnostic Information and Procedures
Fuel Pressure InspectionS6RW0D1704001
WARNING!
Before starting the following procedure, be
sure to observe “Precautions on Fuel System
Service” in order to reduce the risk of fire and
personal injury.
1) Relieve fuel pressure in fuel feed line referring to
“Fuel Pressure Relief Procedure”.
2) Disconnect fuel feed hose from fuel delivery pipe.
3) Connect special tools and hose between fuel feed
hose (1) and fuel delivery pipe as shown in figure,
and clamp hoses securely in order to ensure that no
leaks occur during checking.
Special tool
(A): 09912–58442
(B): 09912–58432
(C): 09912–58490
73 6
1 4
5
8
9
2
I7RW01170002-02
1. Fuel tank 4. Delivery pipe 7. Fuel filter
2. Fuel pump assembly 5. Fuel injector 8. Fuel level sensor (gauge)
3. Fuel pressure regulator 6. Fuel feed line 9. Fuel pump
(C) (B)
(A)
1I5RW0A170002-02