TOYOTA AVENSIS 2005 Service Repair Manual
Manufacturer: TOYOTA, Model Year: 2005, Model line: AVENSIS, Model: TOYOTA AVENSIS 2005Pages: 5135, PDF Size: 95.28 MB
Page 4611 of 5135
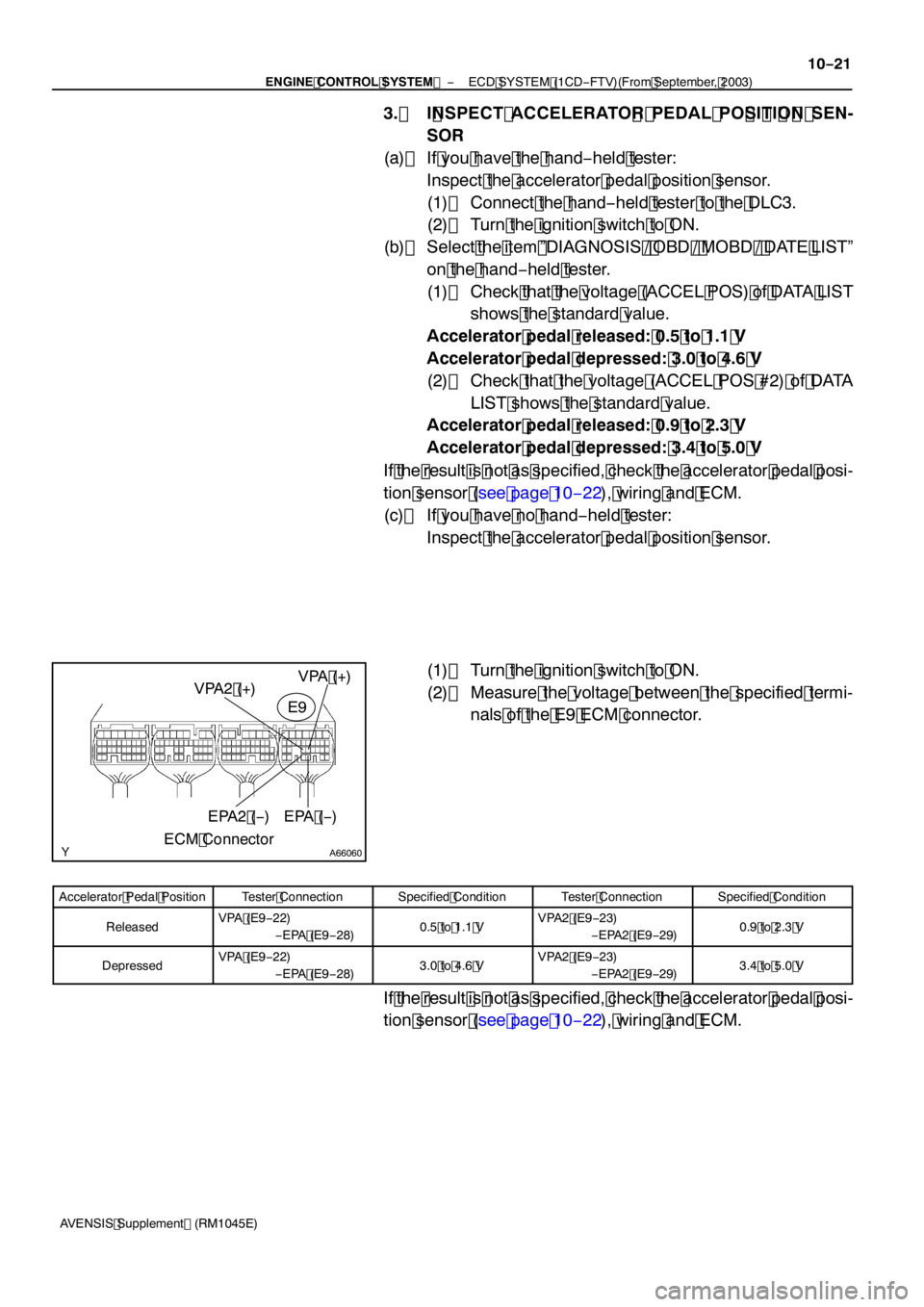
A66060ECM ConnectorEPA2 (
−) VPA (+)
VPA2 (+)
EPA (−)
E9
−
ENGINE CONTROL SYSTEM ECD SYSTEM (1CD−FTV)(From September, 2003)
10 −21
AVENSIS Supplement (RM1045E)
3. I NSPECT ACCELERATO R PEDAL PO SI TI O N SEN-
SOR
(a) If you have the hand −held tester:
Inspect the accelerator pedal position sensor.
(1) Connect the hand −held tester to the DLC3.
(2) Turn the ignition switch to ON.
(b) Select the item ”DIAGNOSIS / OBD / MOBD / DATE LIST” on the hand −held tester.
(1) Check that the voltage (ACCEL POS) of DATA LIST shows the standard value.
Accelerator pedal released: 0.5 to 1.1 V
Accelerator pedal depressed: 3.0 to 4.6 V
(2) Check that the voltage (ACCEL POS #2) of DATA LIST shows the standard value.
Accelerator pedal released: 0.9 to 2.3 V
Accelerator pedal depressed: 3.4 to 5.0 V
If the result is not as specified, check the accelerator pedal posi-
tion sensor (see page 10 −22), wiring and ECM.
(c) If you have no hand −held tester:
Inspect the accelerator pedal position sensor.
(1) Turn the ignition switch to ON.
(2) Measure the voltage between the specified termi- nals of the E9 ECM connector.
Accelerator Pedal PositionTester ConnectionSpecified ConditionTester ConnectionSpecified Condition
ReleasedVPA (E9 −22)
− EPA (E9 −28)0.5 to 1.1 VVPA2 (E9 −23)
− EPA2 (E9 −29)0.9 to 2.3 V
DepressedVPA (E9 −22)
− EPA (E9 −28)3.0 to 4.6 VVPA2 (E9 −23)
− EPA2 (E9 −29)3.4 to 5.0 V
If the result is not as specified, check the accelerator pedal posi-
tion sensor (see page 10 −22), wiring and ECM.
Page 4612 of 5135
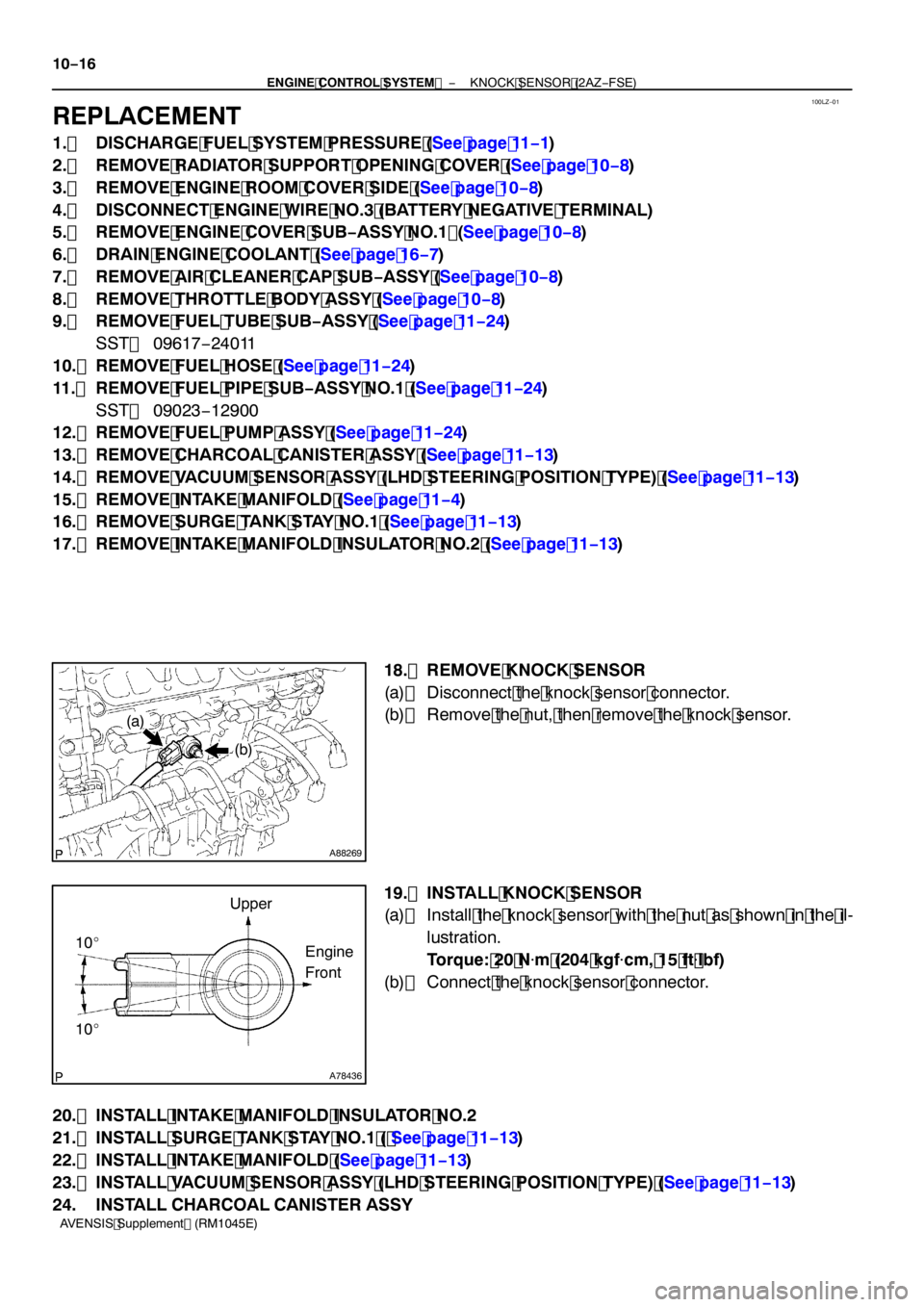
100LZ−01
A88269
(a)
(b)
A78436
10 _
10 _ Upper
Engine
Front
10
−16
−
ENGINE CONTROL SYSTEM KNOCK SENSOR (2AZ−FSE)
AVENSIS Supplement (RM1045E)
REPLACEMENT
1. DISCHARGE FUEL SYSTEM PRESSURE (See page 11 −1)
2. REMOVE RADIATOR SUPPORT OPENING COVER (See page 10 −8)
3. REMOVE ENGINE ROOM COVER SIDE (See page 10 −8)
4. DISCONNECT ENGINE WIRE NO.3 (BATTERY NEGATIVE TERMINAL)
5. REMOVE ENGINE COVER SUB −ASSY NO.1 (See page 10 −8)
6. DRAIN ENGINE COOLANT (See page 16 −7)
7. REMOVE AIR CLEANER CAP SUB −ASSY (See page 10 −8)
8. REMOVE THROTTLE BODY ASSY (See page 10 −8)
9. REMOVE FUEL TUBE SUB −ASSY (See page 11 −24)
SST 09617 −24011
10. REMOVE FUEL HOSE (See page 11 −24)
11. REMOVE FUEL PIPE SUB −ASSY NO.1 (See page 11 −24)
SST 09023 −12900
12. REMOVE FUEL PUMP ASSY (See page 11 −24)
13. REMOVE CHARCOAL CANISTER ASSY (See page 11 −13)
14. REMOVE VACUUM SENSOR ASSY (LHD STEERING POSITION TYPE) (See page 11 −13)
15. REMOVE INTAKE MANIFOLD (See page 11 −4)
16. REMOVE SURGE TANK STAY NO.1 (See page 11 −13)
17. REMOVE INTAKE MANIFOLD INSULATOR NO.2 (See page 11 −13)
18. REMOVE KNOCK SENSOR
(a) Disconnect the knock sensor connector.
(b) Remove the nut, then remove the knock sensor.
19. INSTALL KNOCK SENSOR
(a) Install the knock sensor with the nut as shown in the il- lustration.
Torque: 20 N m (204 kgf cm, 15 ft lbf)
(b) Connect the knock sensor connector.
20. INSTALL INTAKE MANIFOLD INSULATOR NO.2
21. INSTALL SURGE TANK STAY NO.1 ( See page 11 −13)
22. INSTALL INTAKE MANIFOLD (See page 11 −13)
23. INSTALL VACUUM SENSOR ASSY (LHD STEERING POSITION TYPE) (See page 11 −13)
24. INSTALL CHARCOAL CANISTER ASSY
Page 4613 of 5135
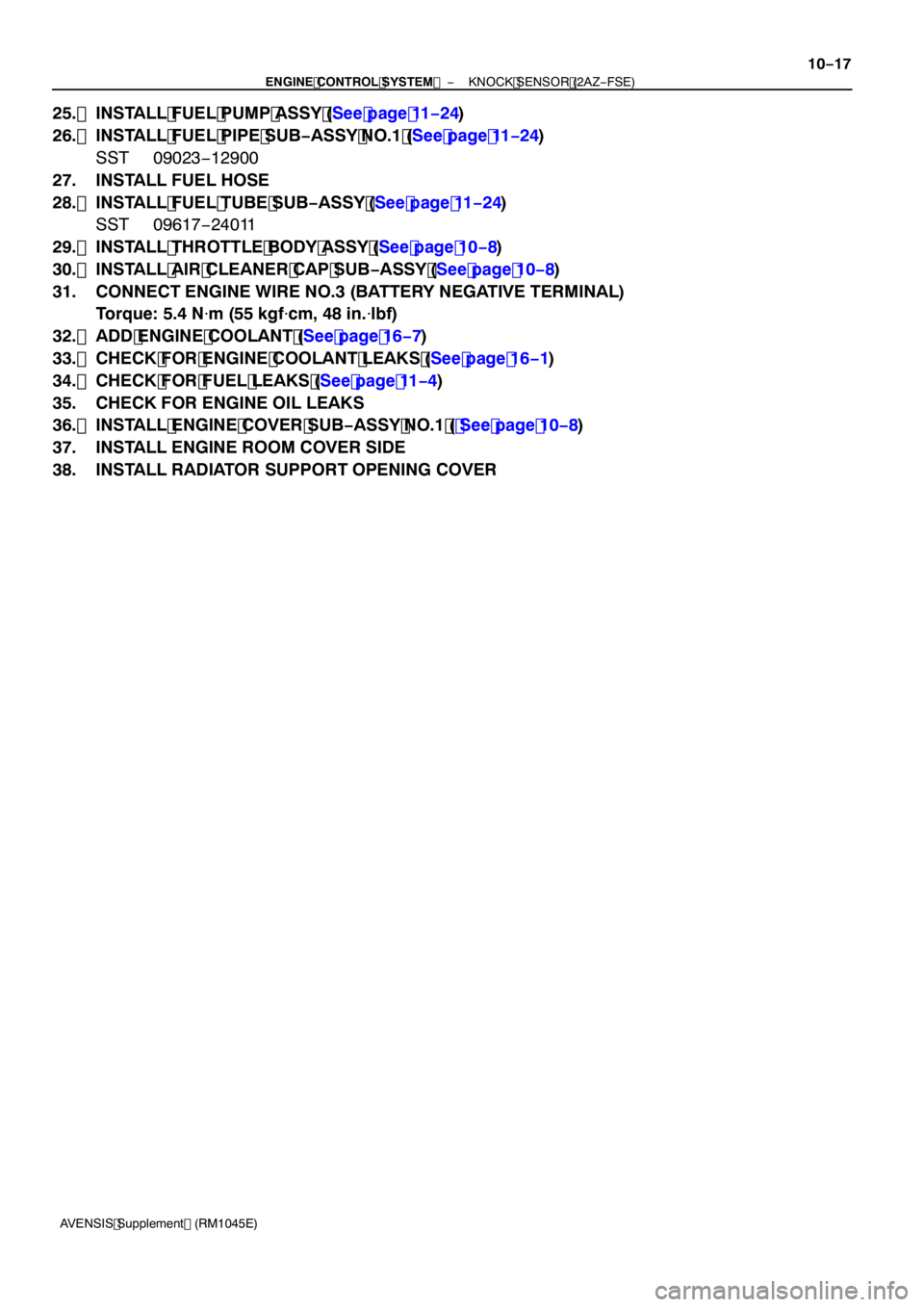
−
ENGINE CONTROL SYSTEM KNOCK SENSOR (2AZ−FSE)
10 −17
AVENSIS Supplement (RM1045E)
25. INSTALL FUEL PUMP ASSY (See page 11 −24)
26. INSTALL FUEL PIPE SUB −ASSY NO.1 (See page 11 −24)
SST 09023 −12900
27. INSTALL FUEL HOSE
28. INSTALL FUEL TUBE SUB −ASSY (See page 11 −24)
SST 09617 −24011
29. INSTALL THROTTLE BODY ASSY (See page 10 −8)
30. INSTALL AIR CLEANER CAP SUB −ASSY (See page 10 −8)
31. CONNECT ENGINE WIRE NO.3 (BATTERY NEGATIVE TERMINAL) Torque: 5.4 N m (55 kgf cm, 48 in. lbf)
32. ADD ENGINE COOLANT (See page 16 −7)
33. CHECK FOR ENGINE COOLANT LEAKS (See page 16 −1)
34. CHECK FOR FUEL LEAKS (See page 11 −4)
35. CHECK FOR ENGINE OIL LEAKS
36. INSTALL ENGINE COVER SUB −ASSY NO.1 ( See page 10 −8)
37. INSTALL ENGINE ROOM COVER SIDE
38. INSTALL RADIATOR SUPPORT OPENING COVER
Page 4614 of 5135
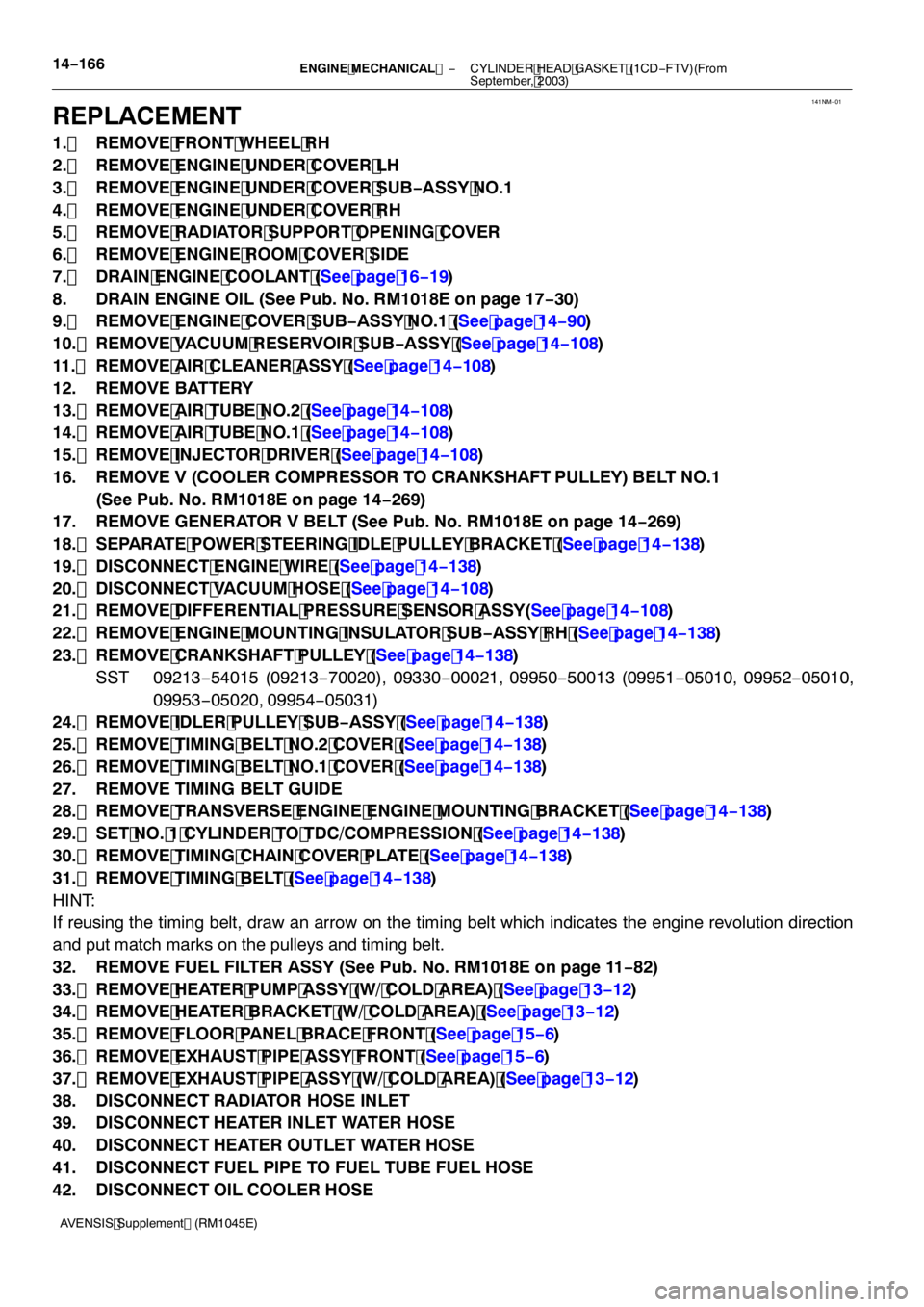
141NM−01
14 −166−
ENGINE MECHANICAL CYLINDER HEAD GASKET (1CD −FTV)(From
September, 2003)
AVENSIS Supplement (RM1045E)
REPLACEMENT
1. REMOVE FRONT WHEEL RH
2. REMOVE ENGINE UNDER COVER LH
3. REMOVE ENGINE UNDER COVER SUB −ASSY NO.1
4. REMOVE ENGINE UNDER COVER RH
5. REMOVE RADIATOR SUPPORT OPENING COVER
6. REMOVE ENGINE ROOM COVER SIDE
7. DRAIN ENGINE COOLANT (See page 16 −19)
8. DRAIN ENGINE OIL (See Pub. No. RM1018E on page 17 −30)
9. REMOVE ENGINE COVER SUB −ASSY NO.1 (See page 14 −90)
10. REMOVE VACUUM RESERVOIR SUB −ASSY (See page 14 −108)
11. REMOVE AIR CLEANER ASSY (See page 14 −108)
12. REMOVE BATTERY
13. REMOVE AIR TUBE NO.2 (See page 14 −108)
14. REMOVE AIR TUBE NO.1 (See page 14 −108)
15. REMOVE INJECTOR DRIVER (See page 14 −108)
16. REMOVE V (COOLER COMPRESSOR TO CRANKSHAFT PULLEY) BELT NO.1
(See Pub. No. RM1018E on page 14 −269)
17. REMOVE GENERATOR V BELT (See Pub. No. RM1018E on page 14 −269)
18. SEPARATE POWER STEERING IDLE PULLEY BRACKET (See page 14 −138)
19. DISCONNECT ENGINE WIRE (See page 14 −138)
20. DISCONNECT VACUUM HOSE (See page 14 −108)
21. REMOVE DIFFERENTIAL PRESSURE SENSOR ASSY(See page 14 −108)
22. REMOVE ENGINE MOUNTING INSULATOR SUB −ASSY RH (See page 14 −138)
23. REMOVE CRANKSHAFT PULLEY (See page 14 −138)
SST 09213 −54015 (09213 −70020), 09330 −00021, 09950 −50013 (09951 −05010, 09952 −05010,
09953 −05020, 09954 −05031)
24. REMOVE IDLER PULLEY SUB −ASSY (See page 14 −138)
25. REMOVE TIMING BELT NO.2 COVER (See page 14 −138)
26. REMOVE TIMING BELT NO.1 COVER (See page 14 −138)
27. REMOVE TIMING BELT GUIDE
28. REMOVE TRANSVERSE ENGINE ENGINE MOUNTING BRACKET (See page 14 −138)
29. SET NO. 1 CYLINDER TO TDC/COMPRESSION (See page 14 −138)
30. REMOVE TIMING CHAIN COVER PLATE (See page 14 −138)
31. REMOVE TIMING BELT (See page 14 −138)
HINT:
If reusing the timing belt, draw an arrow on the timing belt which indicates the engine revolution direction
and put match marks on the pulleys and timing belt.
32. REMOVE FUEL FILTER ASSY (See Pub. No. RM1018E on page 11 −82)
33. REMOVE HEATER PUMP ASSY (W/ COLD AREA) (See page 13 −12)
34. REMOVE HEATER BRACKET (W/ COLD AREA) (See page 13 −12)
35. REMOVE FLOOR PANEL BRACE FRONT (See page 15 −6)
36. REMOVE EXHAUST PIPE ASSY FRONT (See page 15 −6)
37. REMOVE EXHAUST PIPE ASSY (W/ COLD AREA) (See page 13 −12)
38. DISCONNECT RADIATOR HOSE INLET
39. DISCONNECT HEATER INLET WATER HOSE
40. DISCONNECT HEATER OUTLET WATER HOSE
41. DISCONNECT FUEL PIPE TO FUEL TUBE FUEL HOSE
42. DISCONNECT OIL COOLER HOSE
Page 4615 of 5135
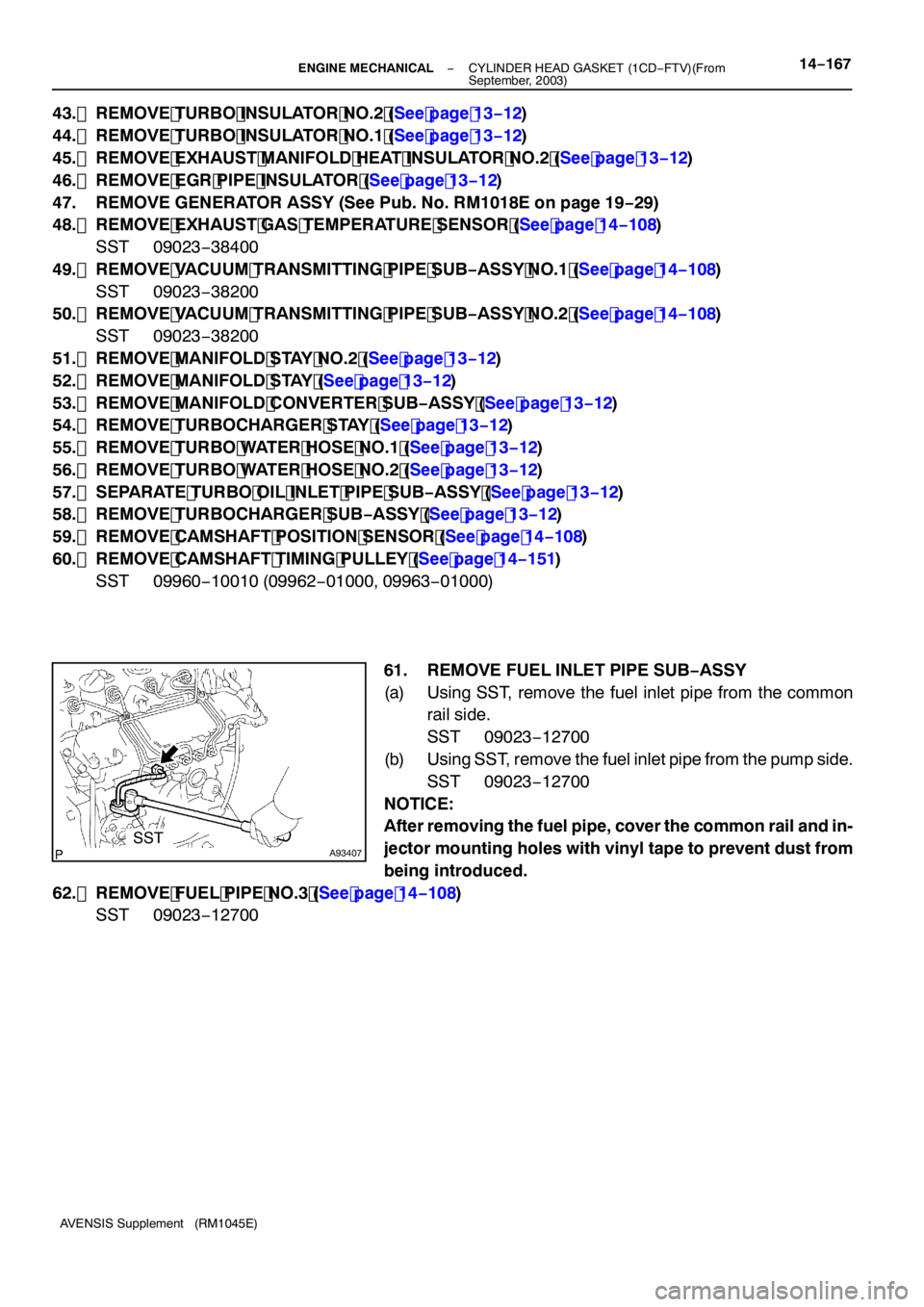
A93407SST
−
ENGINE MECHANICAL CYLINDER HEAD GASKET (1CD −FTV)(From
September, 2003)14 −167
AVENSIS Supplement (RM1045E)
43. REMOVE TURBO INSULATOR NO.2 (See page 13 −12)
44. REMOVE TURBO INSULATOR NO.1 (See page 13 −12)
45. REMOVE EXHAUST MANIFOLD HEAT INSULATOR NO.2 (See page 13 −12)
46. REMOVE EGR PIPE INSULATOR (See page 13 −12)
47. REMOVE GENERATOR ASSY (See Pub. No. RM1018E on page 19 −29)
48. REMOVE EXHAUST GAS TEMPERATURE SENSOR (See page 14 −108)
SST 09023 −38400
49. REMOVE VACUUM TRANSMITTING PIPE SUB −ASSY NO.1 (See page 14 −108)
SST 09023 −38200
50. REMOVE VACUUM TRANSMITTING PIPE SUB −ASSY NO.2 (See page 14 −108)
SST 09023 −38200
51. REMOVE MANIFOLD STAY NO.2 (See page 13 −12)
52. REMOVE MANIFOLD STAY (See page 13 −12)
53. REMOVE MANIFOLD CONVERTER SUB −ASSY (See page 13 −12)
54. REMOVE TURBOCHARGER STAY (See page 13 −12)
55. REMOVE TURBO WATER HOSE NO.1 (See page 13 −12)
56. REMOVE TURBO WATER HOSE NO.2 (See page 13 −12)
57. SEPARATE TURBO OIL INLET PIPE SUB −ASSY (See page 13 −12)
58. REMOVE TURBOCHARGER SUB −ASSY (See page 13 −12)
59. REMOVE CAMSHAFT POSITION SENSOR (See page 14 −108)
60. REMOVE CAMSHAFT TIMING PULLEY (See page 14 −151)
SST 09960 −10010 (09962 −01000, 09963 −01000)
61. REMOVE FUEL INLET PIPE SUB −ASSY
(a) Using SST, remove the fuel inlet pipe from the common rail side.
SST 09023 −12700
(b) Using SST, remove the fuel inlet pipe from the pump side.
SST 09023 −12700
NOTICE:
After removing the fuel pipe, cover the common rail and in-
jector mounting holes with vinyl tape to prevent dust from
being introduced.
62. REMOVE FUEL PIPE NO.3 (See page 14 −108)
SST 09023 −12700
Page 4616 of 5135
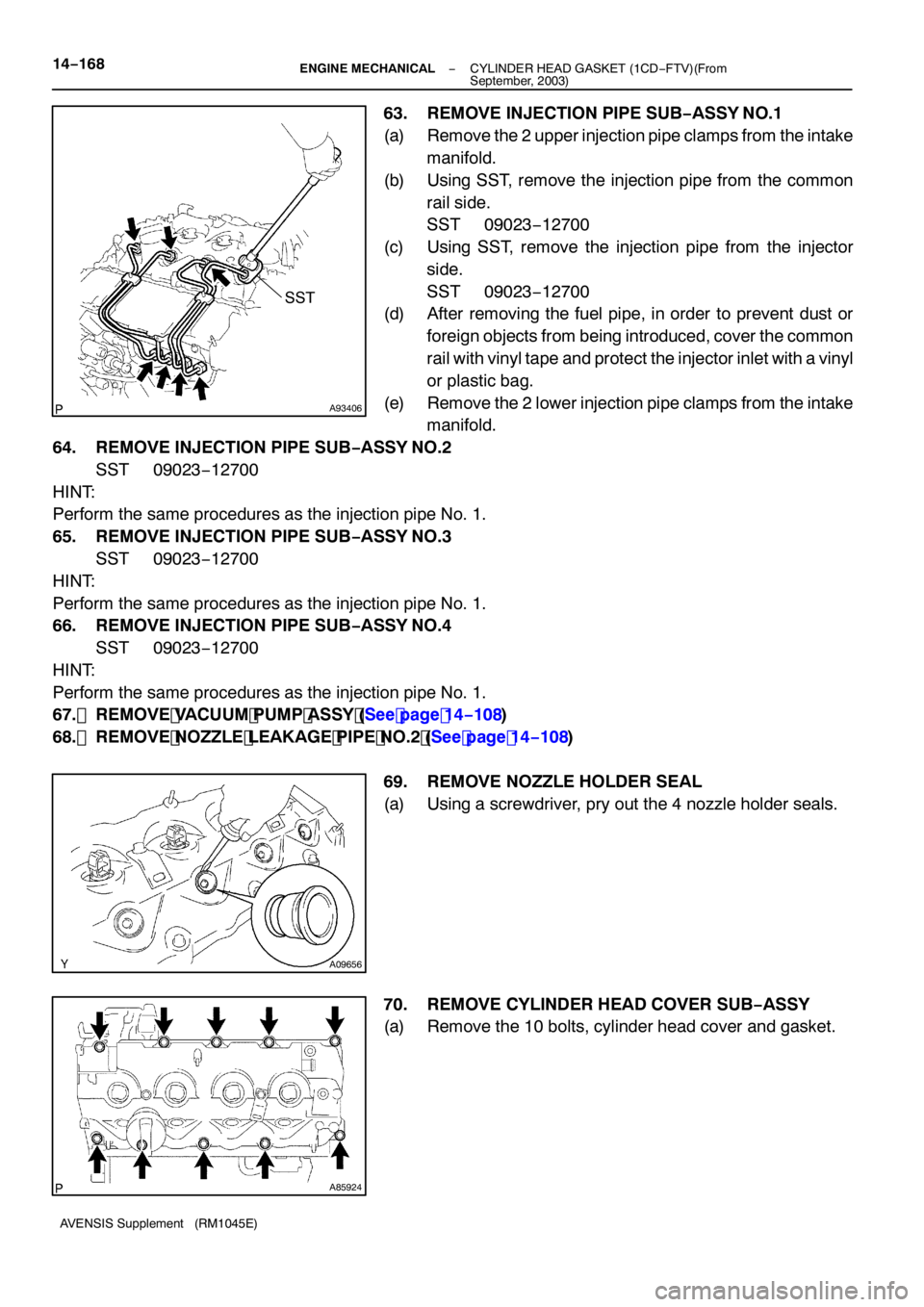
A93406
SST
A09656
A85924
14−168−
ENGINE MECHANICAL CYLINDER HEAD GASKET (1CD −FTV)(From
September, 2003)
AVENSIS Supplement (RM1045E)
63. REMOVE INJECTION PIPE SUB −ASSY NO.1
(a) Remove the 2 upper injection pipe clamps from the intake manifold.
(b) Using SST, remove the injection pipe from the common
rail side.
SST 09023 −12700
(c) Using SST, remove the injection pipe from the injector side.
SST 09023 −12700
(d) After removing the fuel pipe, in order to prevent dust or
foreign objects from being introduced, cover the common
rail with vinyl tape and protect the injector inlet with a vinyl
or plastic bag.
(e) Remove the 2 lower injection pipe clamps from the intake manifold.
64. REMOVE INJECTION PIPE SUB −ASSY NO.2
SST 09023 −12700
HINT:
Perform the same procedures as the injection pipe No. 1.
65. REMOVE INJECTION PIPE SUB −ASSY NO.3
SST 09023 −12700
HINT:
Perform the same procedures as the injection pipe No. 1.
66. REMOVE INJECTION PIPE SUB −ASSY NO.4
SST 09023 −12700
HINT:
Perform the same procedures as the injection pipe No. 1.
67. REMOVE VACUUM PUMP ASSY (See page 14 −108)
68. REMOVE NOZZLE LEAKAGE PIPE NO.2 (See page 14 −108)
69. REMOVE NOZZLE HOLDER SEAL
(a) Using a screwdriver, pry out the 4 nozzle holder seals.
70. REMOVE CYLINDER HEAD COVER SUB −ASSY
(a) Remove the 10 bolts, cylinder head cover and gasket.
Page 4617 of 5135
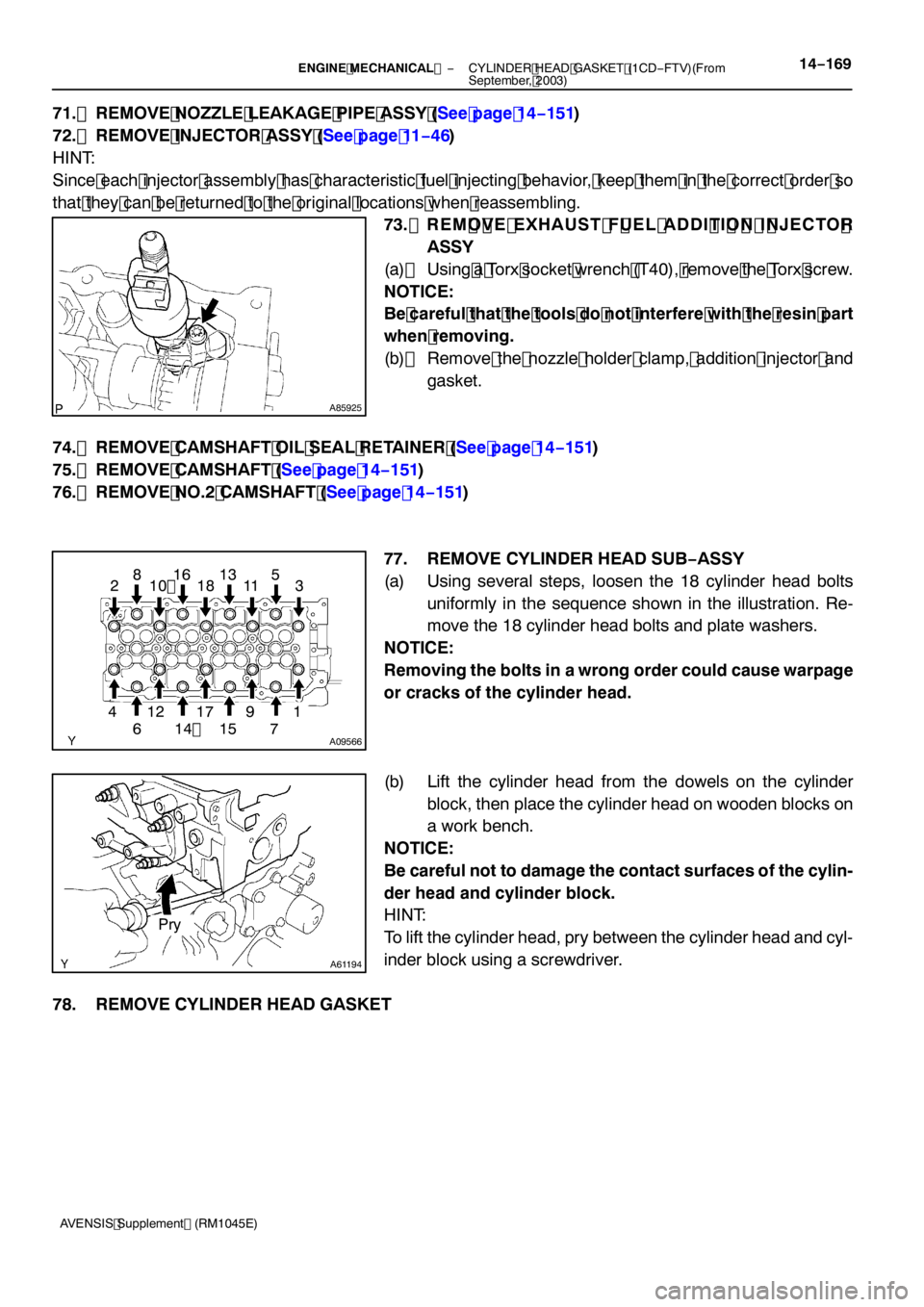
A85925
A09566
1
234 5
67 89
10 11
12 13
14 15
16
1718
A61194
Pry
−
ENGINE MECHANICAL CYLINDER HEAD GASKET (1CD −FTV)(From
September, 2003)14 −169
AVENSIS Supplement (RM1045E)
71. REMOVE NOZZLE LEAKAGE PIPE ASSY (See page 14 −151)
72. REMOVE INJECTOR ASSY (See page 11 −46)
HINT:
Since each injector assembly has characteristic fuel injecting behavior, keep them in the correct order so
that they can be returned to the original locations when reassembling. 73. REM O VE EXHAUST F UEL ADDI TI O N I NJECTO R
ASSY
(a) Using a Torx socket wrench (T40), remove the Torx screw.
NOTICE:
Be careful that the tools do not interfere with the resin part
when removing.
(b) Remove the nozzle holder clamp, addition injector and gasket.
74. REMOVE CAMSHAFT OIL SEAL RETAINER (See page 14 −151)
75. REMOVE CAMSHAFT (See page 14 −151)
76. REMOVE NO.2 CAMSHAFT (See page 14 −151)
77. REMOVE CYLINDER HEAD SUB −ASSY
(a) Using several steps, loosen the 18 cylinder head bolts
uniformly in the sequence shown in the illustration. Re-
move the 18 cylinder head bolts and plate washers.
NOTICE:
Removing the bolts in a wrong order could cause warpage
or cracks of the cylinder head.
(b) Lift the cylinder head from the dowels on the cylinder block, then place the cylinder head on wooden blocks on
a work bench.
NOTICE:
Be careful not to damage the contact surfaces of the cylin-
der head and cylinder block.
HINT:
To lift the cylinder head, pry between the cylinder head and cyl-
inder block using a screwdriver.
78. REMOVE CYLINDER HEAD GASKET
Page 4618 of 5135
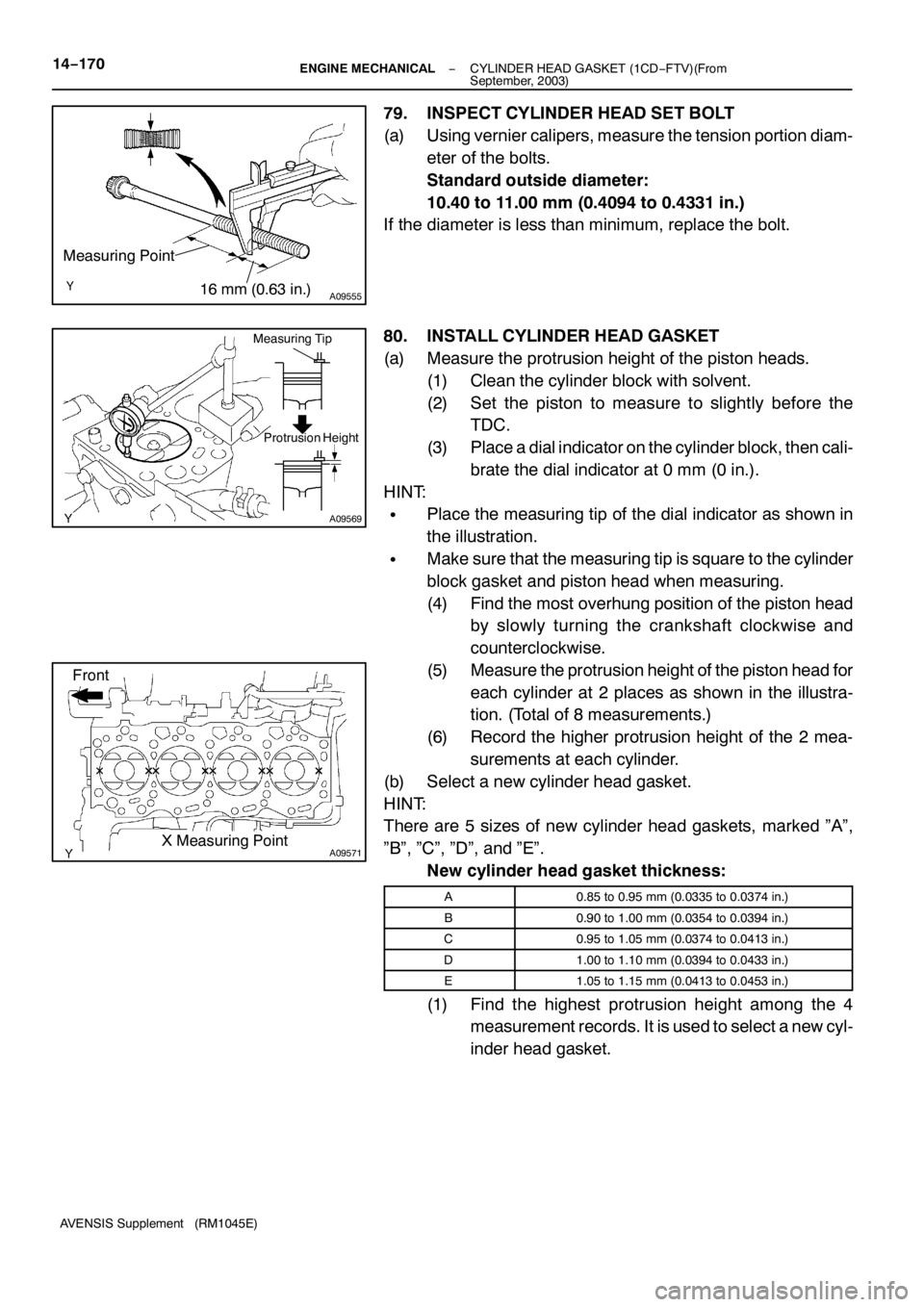
A09555
Measuring Point
16 mm (0.63 in.)
A09569
Measuring Tip
Protrusion Height
A09571
Front
X Measuring Point 14−170
− ENGINE MECHANICALCYLINDER HEAD GASKET (1CD−FTV)(From
September, 2003)
AVENSIS Supplement (RM1045E)
79. INSPECT CYLINDER HEAD SET BOLT
(a) Using vernier calipers, measure the tension portion diam-
eter of the bolts.
Standard outside diameter:
10.40 to 11.00 mm (0.4094 to 0.4331 in.)
If the diameter is less than minimum, replace the bolt.
80. INSTALL CYLINDER HEAD GASKET
(a) Measure the protrusion height of the piston heads.
(1) Clean the cylinder block with solvent.
(2) Set the piston to measure to slightly before the
TDC.
(3) Place a dial indicator on the cylinder block, then cali-
brate the dial indicator at 0 mm (0 in.).
HINT:
SPlace the measuring tip of the dial indicator as shown in
the illustration.
SMake sure that the measuring tip is square to the cylinder
block gasket and piston head when measuring.
(4) Find the most overhung position of the piston head
by slowly turning the crankshaft clockwise and
counterclockwise.
(5) Measure the protrusion height of the piston head for
each cylinder at 2 places as shown in the illustra-
tion. (Total of 8 measurements.)
(6) Record the higher protrusion height of the 2 mea-
surements at each cylinder.
(b) Select a new cylinder head gasket.
HINT:
There are 5 sizes of new cylinder head gaskets, marked ”A”,
”B”, ”C”, ”D”, and ”E”.
New cylinder head gasket thickness:
A0.85 to 0.95 mm (0.0335 to 0.0374 in.)
B0.90 to 1.00 mm (0.0354 to 0.0394 in.)
C0.95 to 1.05 mm (0.0374 to 0.0413 in.)
D1.00 to 1.10 mm (0.0394 to 0.0433 in.)
E1.05 to 1.15 mm (0.0413 to 0.0453 in.)
(1) Find the highest protrusion height among the 4
measurement records. It is used to select a new cyl-
inder head gasket.
Page 4619 of 5135
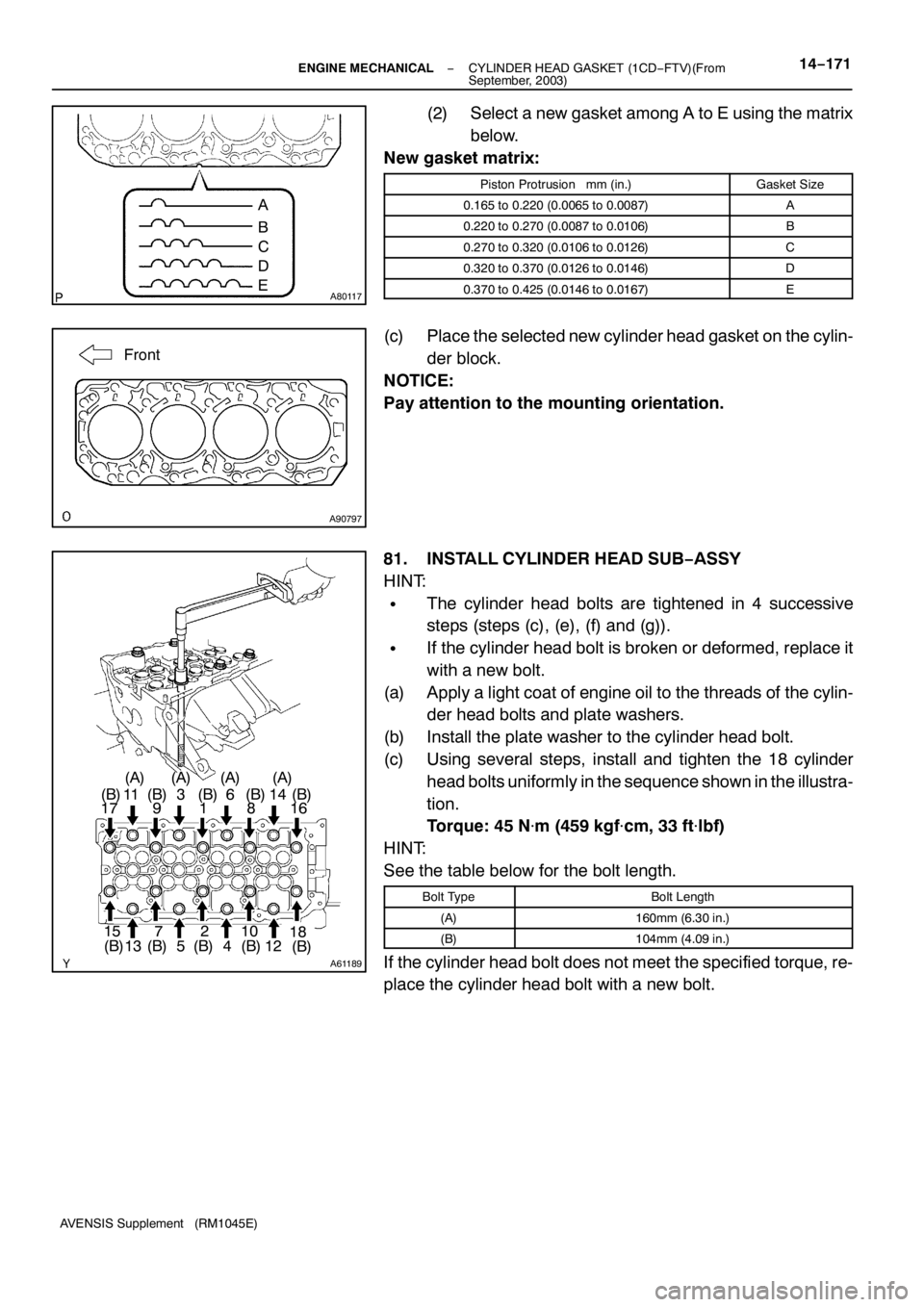
A80117
A
B
C
D
E
A90797
Front
A61189
10 11
12 1314
1516 1718 2 1
4 56 3
78 9(A) (A) (A)
(B) (B) (B) (B)
(B) (B) (B)(B) (B) (B)(A)
− ENGINE MECHANICALCYLINDER HEAD GASKET (1CD−FTV)(From
September, 2003)14−171
AVENSIS Supplement (RM1045E)
(2) Select a new gasket among A to E using the matrix
below.
New gasket matrix:
Piston Protrusion mm (in.)Gasket Size
0.165 to 0.220 (0.0065 to 0.0087)A
0.220 to 0.270 (0.0087 to 0.0106)B
0.270 to 0.320 (0.0106 to 0.0126)C
0.320 to 0.370 (0.0126 to 0.0146)D
0.370 to 0.425 (0.0146 to 0.0167)E
(c) Place the selected new cylinder head gasket on the cylin-
der block.
NOTICE:
Pay attention to the mounting orientation.
81. INSTALL CYLINDER HEAD SUB−ASSY
HINT:
SThe cylinder head bolts are tightened in 4 successive
steps (steps (c), (e), (f) and (g)).
SIf the cylinder head bolt is broken or deformed, replace it
with a new bolt.
(a) Apply a light coat of engine oil to the threads of the cylin-
der head bolts and plate washers.
(b) Install the plate washer to the cylinder head bolt.
(c) Using several steps, install and tighten the 18 cylinder
head bolts uniformly in the sequence shown in the illustra-
tion.
Torque: 45 Nm (459 kgfcm, 33 ftlbf)
HINT:
See the table below for the bolt length.
Bolt TypeBolt Length
(A)160mm (6.30 in.)
(B)104mm (4.09 in.)
If the cylinder head bolt does not meet the specified torque, re-
place the cylinder head bolt with a new bolt.
Page 4620 of 5135
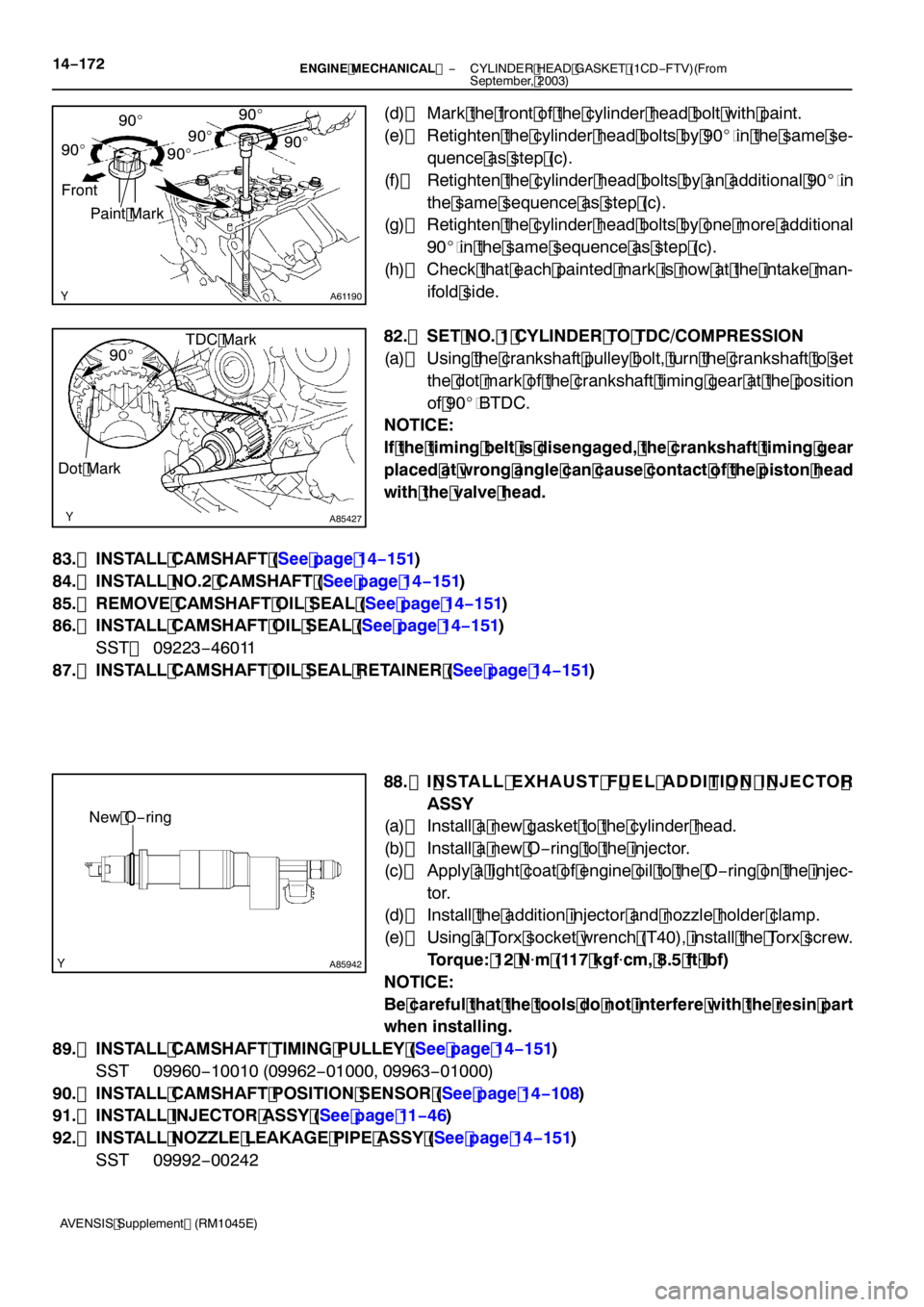
A61190
90_ 90
_
90_90
_ 90
_
90_
Paint Mark
Front
A85427
TDC Mark
Dot Mark
90 _
A85942
New O −ring
14 −172−
ENGINE MECHANICAL CYLINDER HEAD GASKET (1CD −FTV)(From
September, 2003)
AVENSIS Supplement (RM1045E)
(d) Mark the front of the cylinder head bolt with paint.
(e) Retighten the cylinder head bolts by 90 _ in the same se-
quence as step (c).
(f) Retighten the cylinder head bolts by an additional 90 _ in
the same sequence as step (c).
(g) Retighten the cylinder head bolts by one more additional
90_ in the same sequence as step (c).
(h) Check that each painted mark is now at the intake man-
ifold side.
82. SET NO. 1 CYLINDER TO TDC/COMPRESSION
(a) Using the crankshaft pulley bolt, turn the crankshaft to set the dot mark of the crankshaft timing gear at the position
of 90_ BTDC.
NOTICE:
If the timing belt is disengaged, the crankshaft timing gear
placed at wrong angle can cause contact of the piston head
with the valve head.
83. INSTALL CAMSHAFT (See page 14 −151)
84. INSTALL NO.2 CAMSHAFT (See page 14 −151)
85. REMOVE CAMSHAFT OIL SEAL (See page 14 −151)
86. INSTALL CAMSHAFT OIL SEAL (See page 14 −151)
SST 09223 −46011
87. INSTALL CAMSHAFT OIL SEAL RETAINER (See page 14 −151)
88. I NSTALL EXHAUST F UEL ADDI TI O N I NJECTO R ASSY
(a) Install a new gasket to the cylinder head.
(b) Install a new O −ring to the injector.
(c) Apply a light coat of engine oil to the O −ring on the injec-
tor.
(d) Install the addition injector and nozzle holder clamp.
(e) Using a Torx socket wrench (T40), install the Torx screw. Torque: 12 N m (117 kgf cm, 8.5 ft lbf)
NOTICE:
Be careful that the tools do not interfere with the resin part
when installing.
89. INSTALL CAMSHAFT TIMING PULLEY (See page 14 −151)
SST 09960 −10010 (09962 −01000, 09963 −01000)
90. INSTALL CAMSHAFT POSITION SENSOR (See page 14 −108)
91. INSTALL INJECTOR ASSY (See page 11 −46)
92. INSTALL NOZZLE LEAKAGE PIPE ASSY (See page 14 −151)
SST 09992 −00242