engine TOYOTA CAMRY V20 1986 Service Information
[x] Cancel search | Manufacturer: TOYOTA, Model Year: 1986, Model line: CAMRY V20, Model: TOYOTA CAMRY V20 1986Pages: 2389, PDF Size: 84.44 MB
Page 206 of 2389
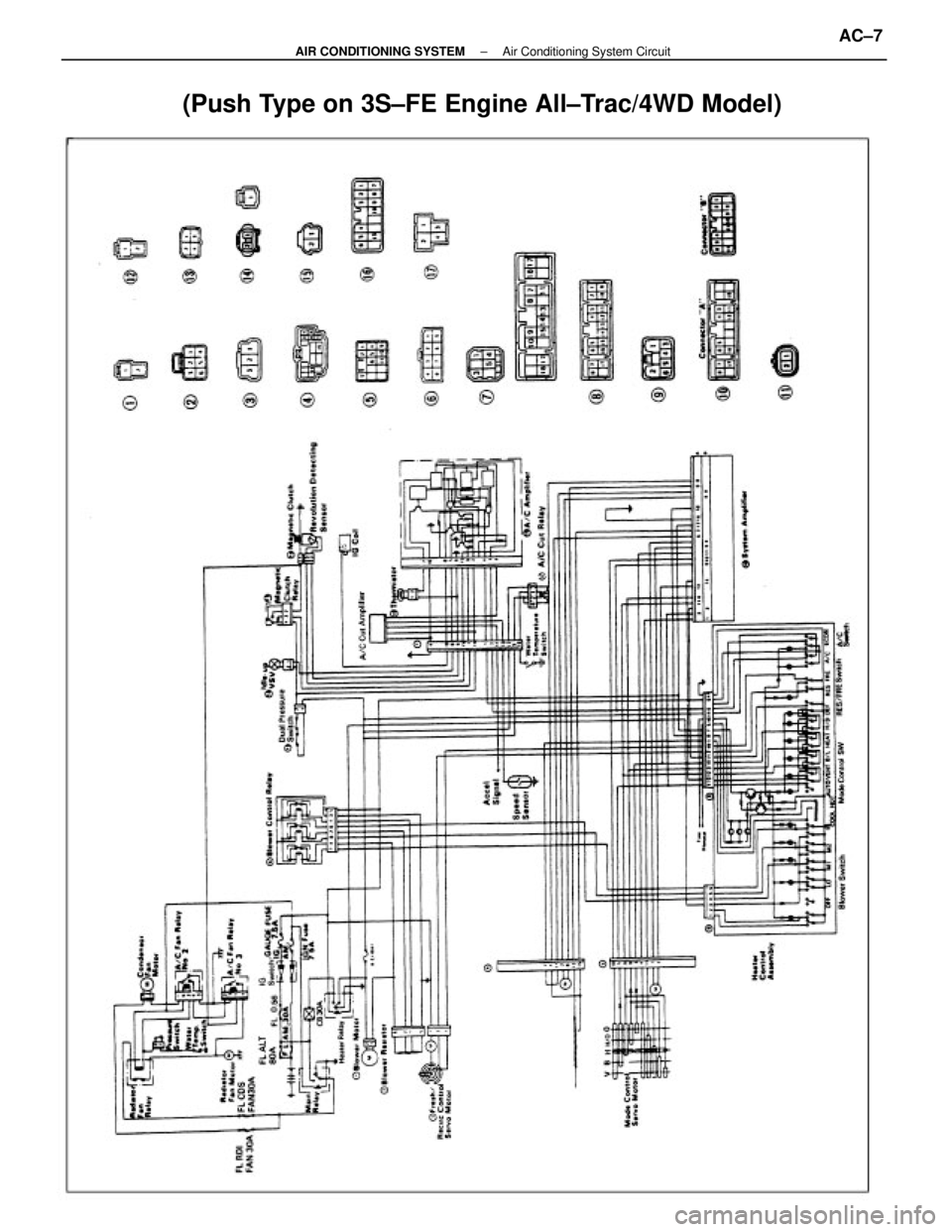
(Push Type on 3S±FE Engine All±Trac/4WD Model)
± AIR CONDITIONING SYSTEMAir Conditioning System CircuitAC±7
Page 207 of 2389
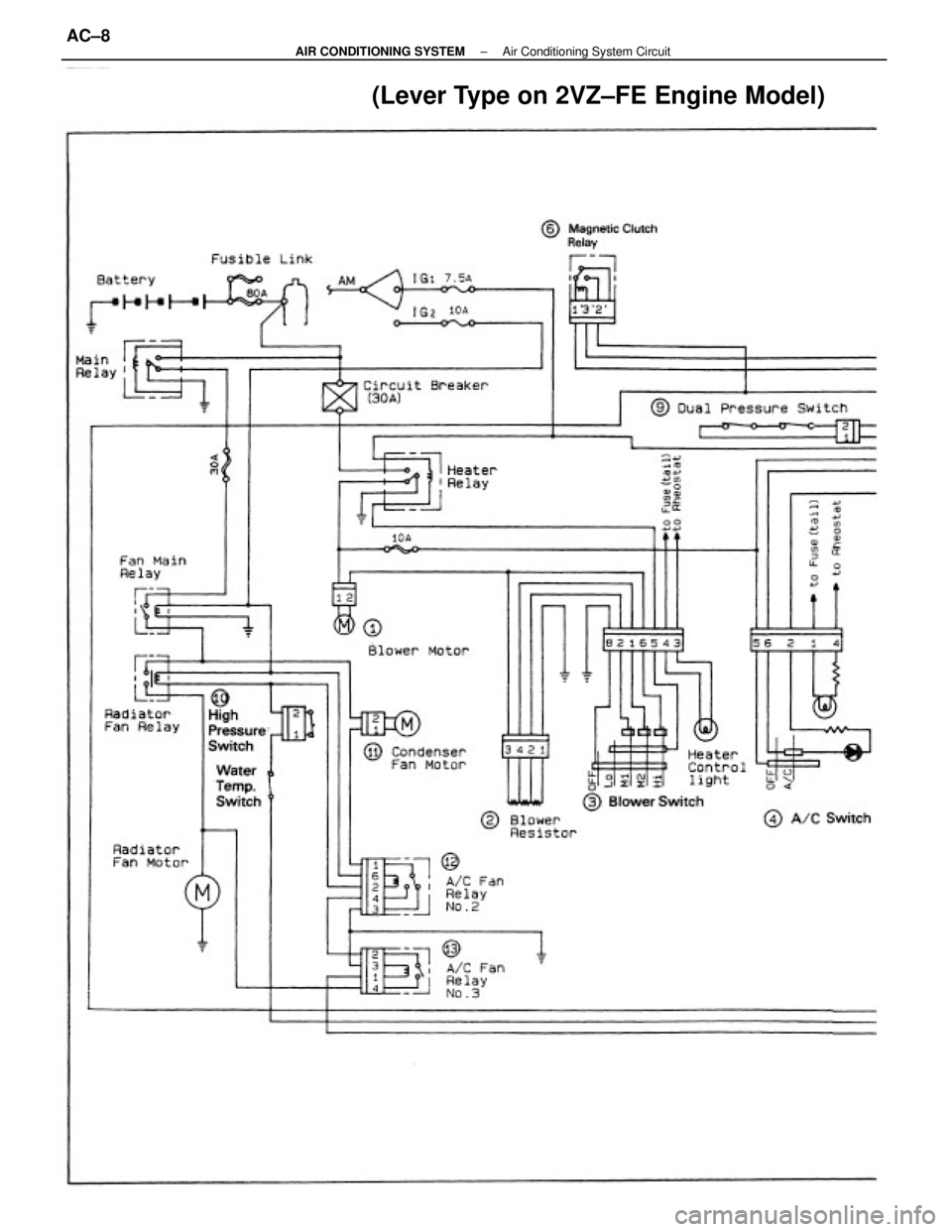
(Lever Type on 2VZ±FE Engine Model)
± AIR CONDITIONING SYSTEMAir Conditioning System CircuitAC±8
Page 209 of 2389
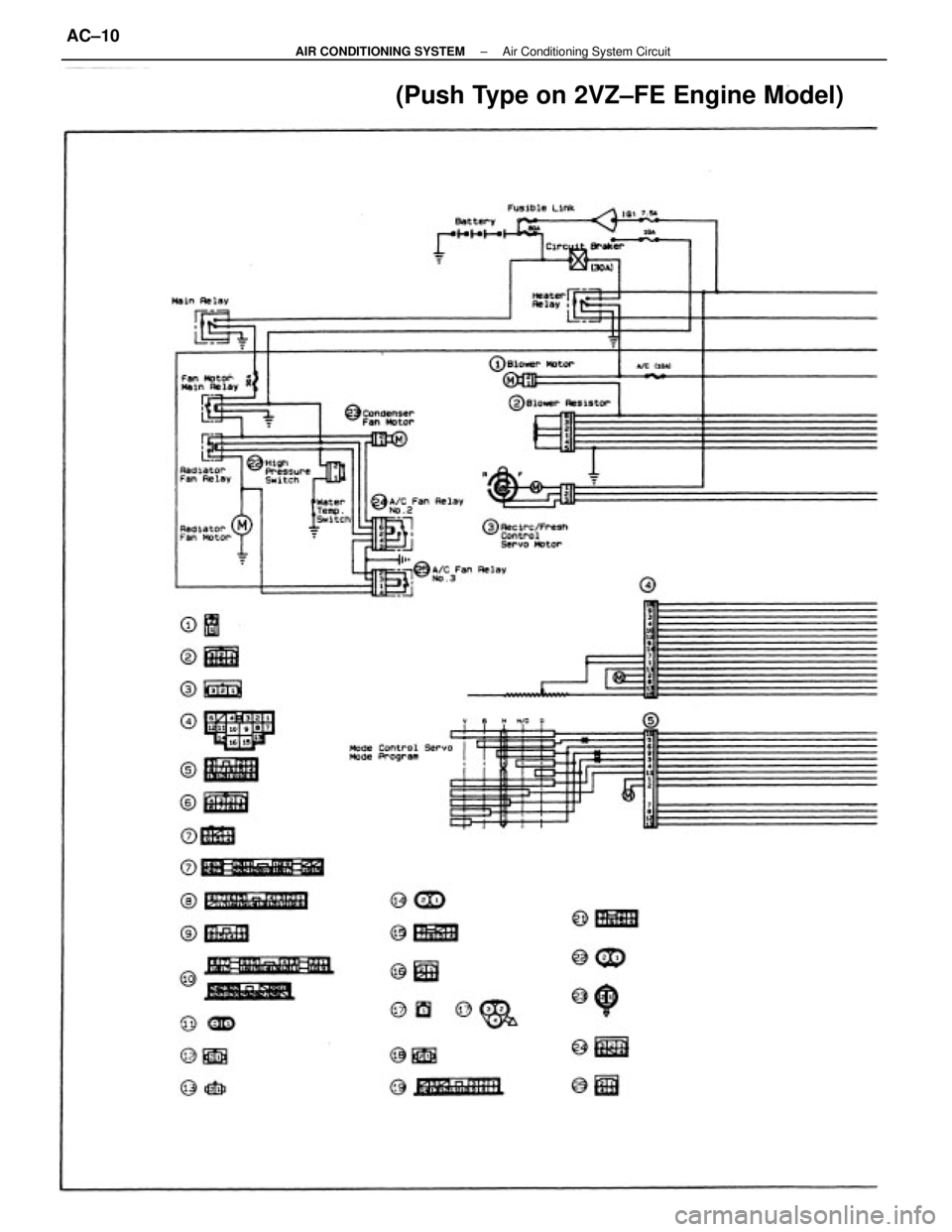
(Push Type on 2VZ±FE Engine Model)
± AIR CONDITIONING SYSTEMAir Conditioning System CircuitAC±10
Page 218 of 2389
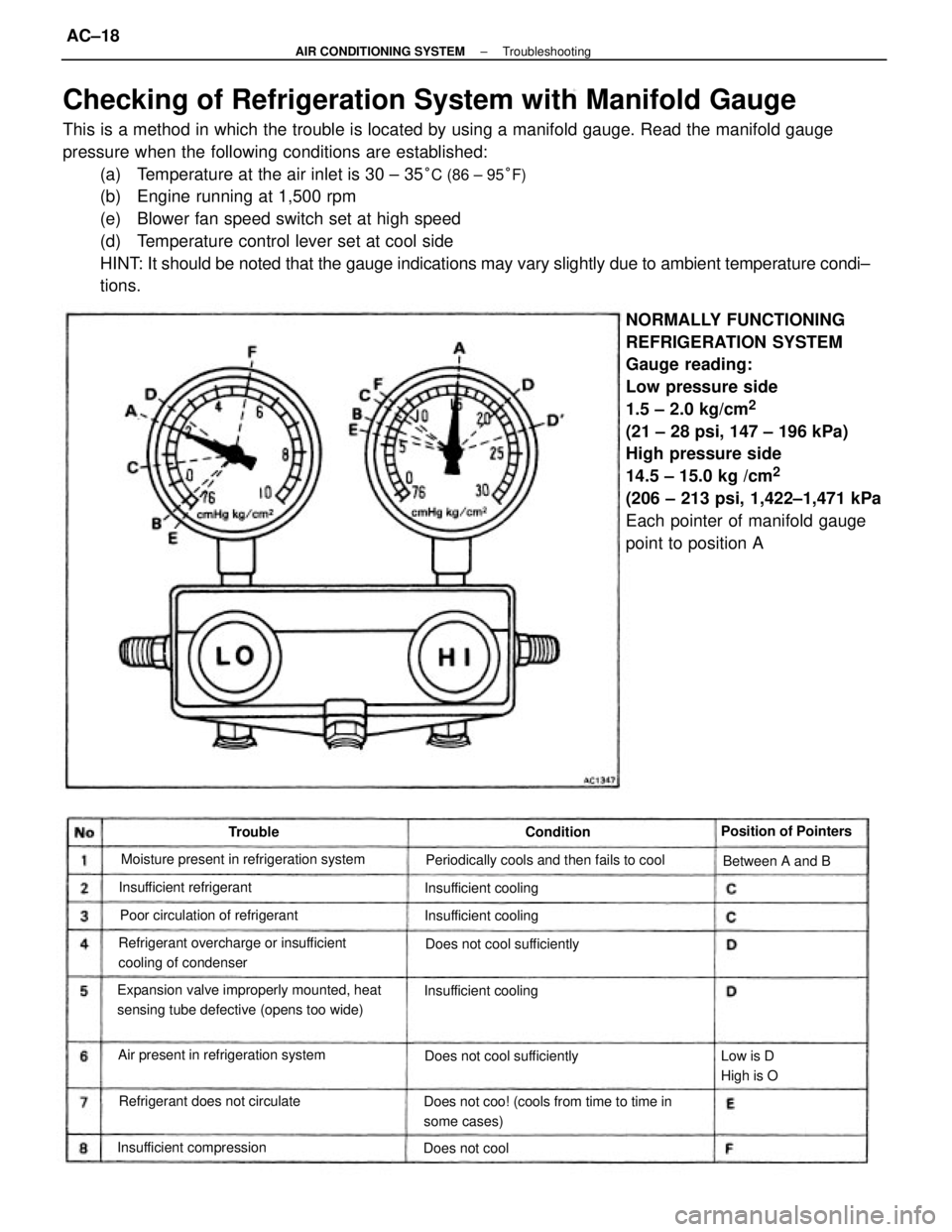
Checking of Refrigeration System with Manifold Gauge
This is a method in which the trouble is located by using a manifold gauge. Read the manifold gauge
pressure when the following conditions are established:
(a) Temperature at the air inlet is 30 ± 35
°C (86 ± 95°F)
(b) Engine running at 1,500 rpm
(e) Blower fan speed switch set at high speed
(d) Temperature control lever set at cool side
HINT: It should be noted that the gauge indications may vary slightly due to ambient temperature condi±
tions.
NORMALLY FUNCTIONING
REFRIGERATION SYSTEM
Gauge reading:
Low pressure side
1.5 ± 2.0 kg/cm
2
(21 ± 28 psi, 147 ± 196 kPa)
High pressure side
14.5 ± 15.0 kg /cm
2
(206 ± 213 psi, 1,422±1,471 kPa
Each pointer of manifold gauge
point to position A
Expansion valve improperly mounted, heat
sensing tube defective (opens too wide)
Does not coo! (cools from time to time in
some cases) Refrigerant overcharge or insufficient
cooling of condenserMoisture present in refrigeration system
Periodically cools and then fails to cool
Air present in refrigeration systemPoor circulation of refrigerant
Refrigerant does not circulateDoes not cool sufficiently
Does not cool sufficiently
Insufficient compressionInsufficient refrigerantPosition of Pointers
Insufficient cooling Insufficient cooling
Insufficient cooling
Low is D
High is OBetween A and B
Does not coolCondition Trouble
± AIR CONDITIONING SYSTEMTroubleshootingAC±18
Page 221 of 2389
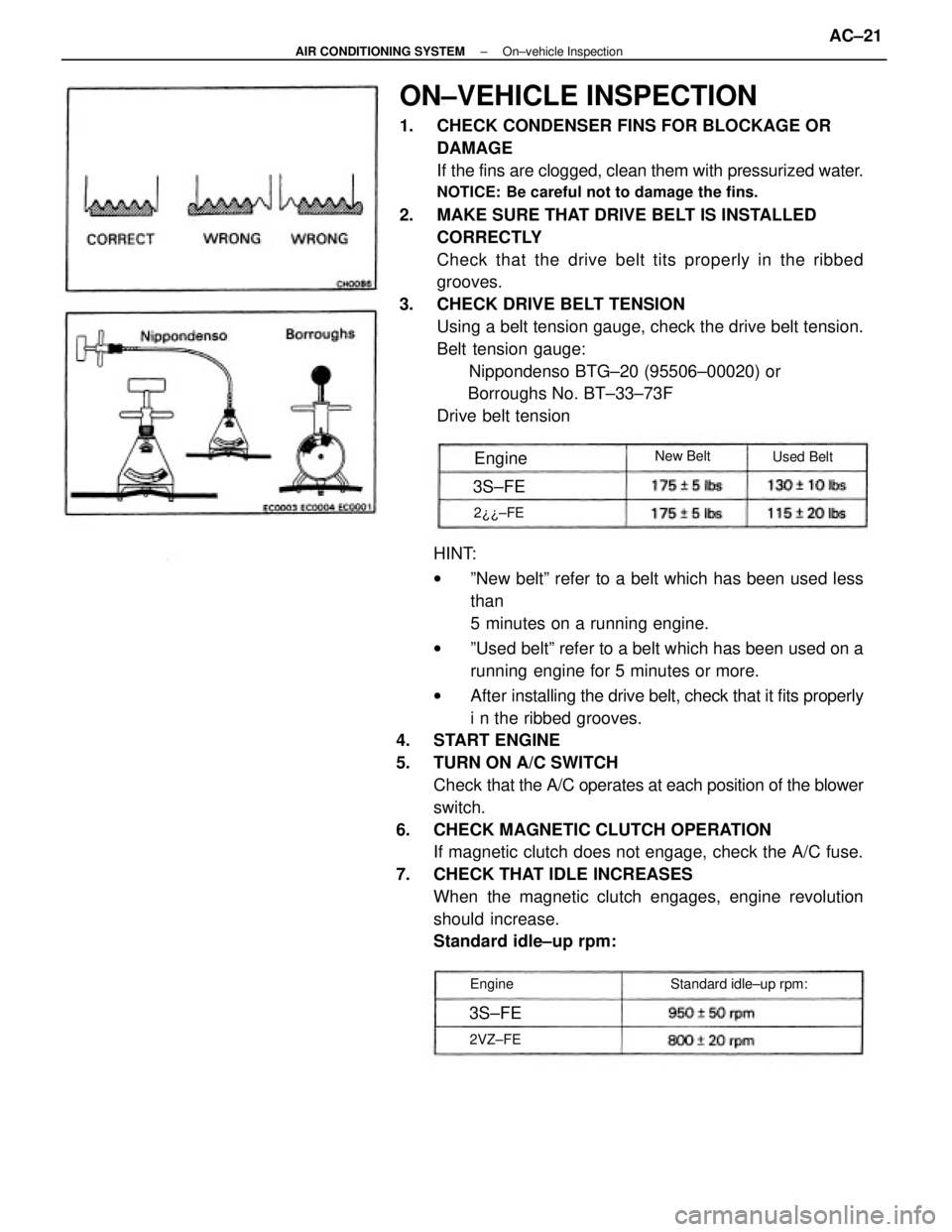
HINT:
wºNew beltº refer to a belt which has been used less
than
5 minutes on a running engine.
wºUsed beltº refer to a belt which has been used on a
running engine for 5 minutes or more.
wAfter installing the drive belt, check that it fits properly
i n the ribbed grooves.
4. START ENGINE
5. TURN ON A/C SWITCH
Check that the A/C operates at each position of the blower
switch.
6. CHECK MAGNETIC CLUTCH OPERATION
If magnetic clutch does not engage, check the A/C fuse.
7. CHECK THAT IDLE INCREASES
When the magnetic clutch engages, engine revolution
should increase.
Standard idle±up rpm:
ON±VEHICLE INSPECTION
1. CHECK CONDENSER FINS FOR BLOCKAGE OR
DAMAGE
If the fins are clogged, clean them with pressurized water.
NOTICE: Be careful not to damage the fins.
2. MAKE SURE THAT DRIVE BELT IS INSTALLED
CORRECTLY
Check that the drive belt tits properly in the ribbed
grooves.
3. CHECK DRIVE BELT TENSION
Using a belt tension gauge, check the drive belt tension.
Belt tension gauge:
Nippondenso BTG±20 (95506±00020) or
Borroughs No. BT±33±73F
Drive belt tension
Standard idle±up rpm:Used Belt New Belt
Engine
Engine2¿¿±FE
2VZ±FE
3S±FE3S±FE
± AIR CONDITIONING SYSTEMOn±vehicle InspectionAC±21
Page 222 of 2389
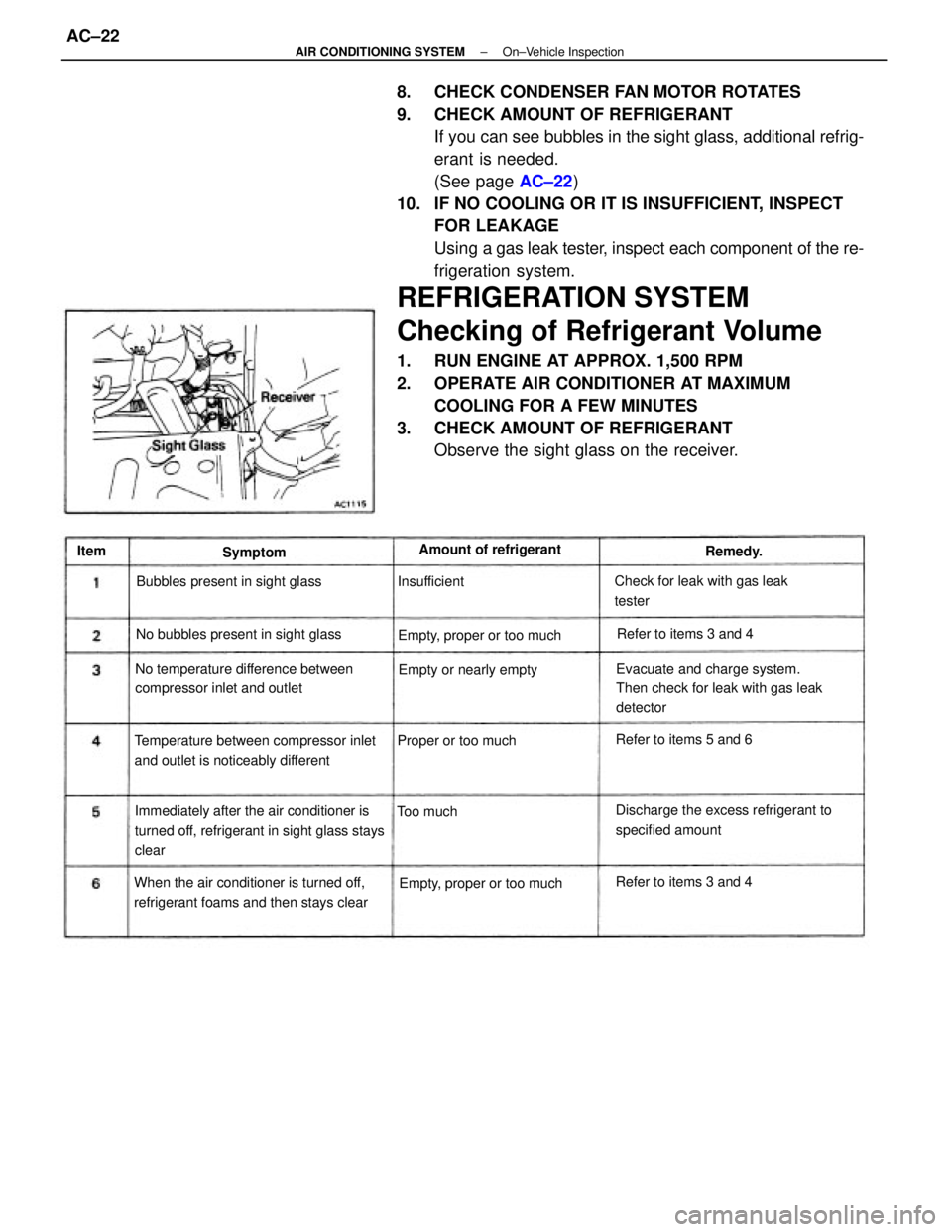
8. CHECK CONDENSER FAN MOTOR ROTATES
9. CHECK AMOUNT OF REFRIGERANT
If you can see bubbles in the sight glass, additional refrig-
erant is needed.
(See page AC±22)
10. IF NO COOLING OR IT IS INSUFFICIENT, INSPECT
FOR LEAKAGE
Using a gas leak tester, inspect each component of the re-
frigeration system.
REFRIGERATION SYSTEM
Checking of Refrigerant Volume
1. RUN ENGINE AT APPROX. 1,500 RPM
2. OPERATE AIR CONDITIONER AT MAXIMUM
COOLING FOR A FEW MINUTES
3. CHECK AMOUNT OF REFRIGERANT
Observe the sight glass on the receiver.
Immediately after the air conditioner is
turned off, refrigerant in sight glass stays
clear
When the air conditioner is turned off,
refrigerant foams and then stays clearEvacuate and charge system.
Then check for leak with gas leak
detector
Temperature between compressor inlet
and outlet is noticeably different
Discharge the excess refrigerant to
specified amount No temperature difference between
compressor inlet and outletCheck for leak with gas leak
tester
No bubbles present in sight glassBubbles present in sight glass
Empty, proper or too much Empty, proper or too muchAmount of refrigerant
Empty or nearly empty
Refer to items 5 and 6
Refer to items 3 and 4Refer to items 3 and 4
Proper or too muchInsufficient Symptom
Too muchRemedy. Item
± AIR CONDITIONING SYSTEMOn±Vehicle InspectionAC±22
Page 223 of 2389
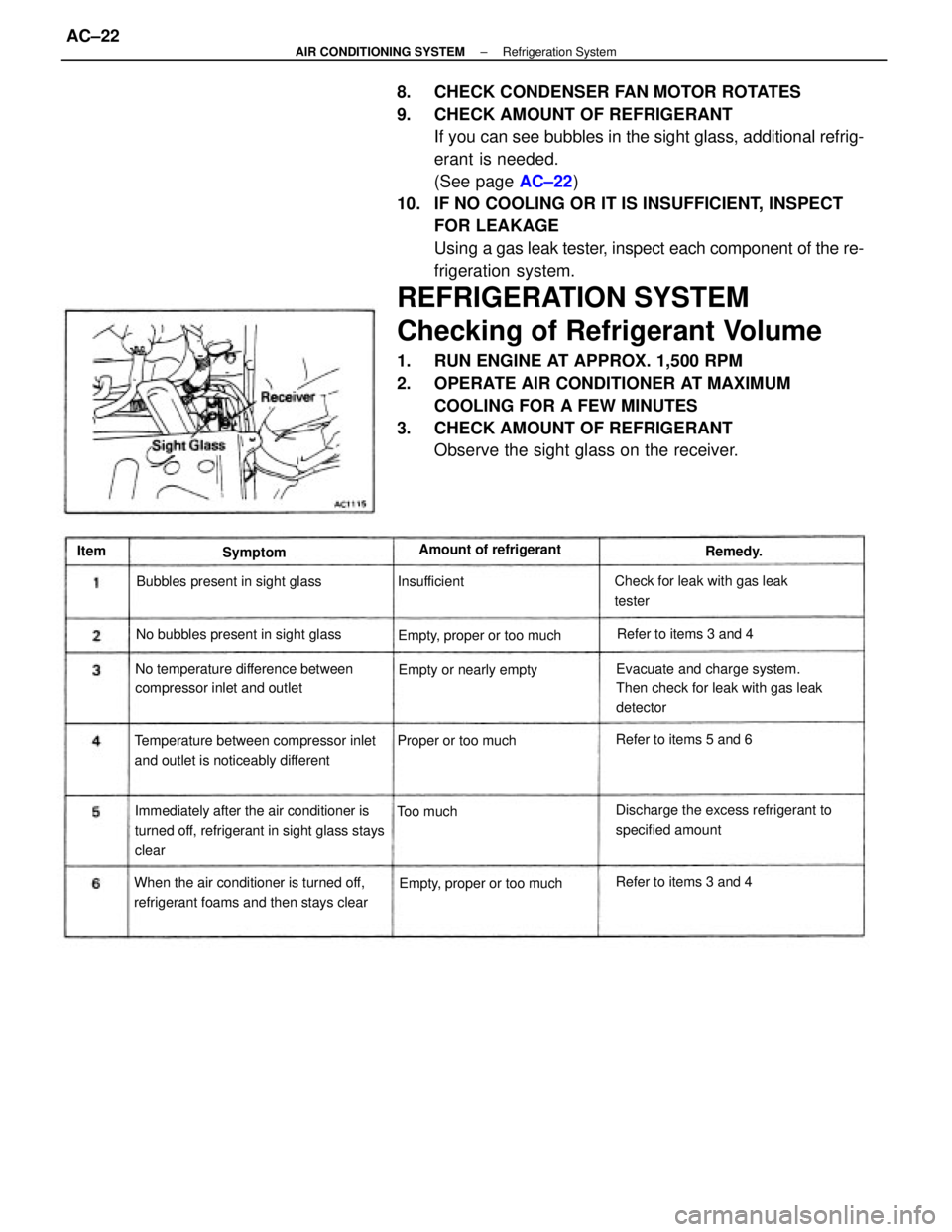
8. CHECK CONDENSER FAN MOTOR ROTATES
9. CHECK AMOUNT OF REFRIGERANT
If you can see bubbles in the sight glass, additional refrig-
erant is needed.
(See page AC±22)
10. IF NO COOLING OR IT IS INSUFFICIENT, INSPECT
FOR LEAKAGE
Using a gas leak tester, inspect each component of the re-
frigeration system.
REFRIGERATION SYSTEM
Checking of Refrigerant Volume
1. RUN ENGINE AT APPROX. 1,500 RPM
2. OPERATE AIR CONDITIONER AT MAXIMUM
COOLING FOR A FEW MINUTES
3. CHECK AMOUNT OF REFRIGERANT
Observe the sight glass on the receiver.
Immediately after the air conditioner is
turned off, refrigerant in sight glass stays
clear
When the air conditioner is turned off,
refrigerant foams and then stays clearEvacuate and charge system.
Then check for leak with gas leak
detector
Temperature between compressor inlet
and outlet is noticeably different
Discharge the excess refrigerant to
specified amount No temperature difference between
compressor inlet and outletCheck for leak with gas leak
tester
No bubbles present in sight glassBubbles present in sight glass
Empty, proper or too much Empty, proper or too muchAmount of refrigerant
Empty or nearly empty
Refer to items 5 and 6
Refer to items 3 and 4Refer to items 3 and 4
Proper or too muchInsufficient Symptom
Too muchRemedy. Item
± AIR CONDITIONING SYSTEMRefrigeration SystemAC±22
Page 224 of 2389
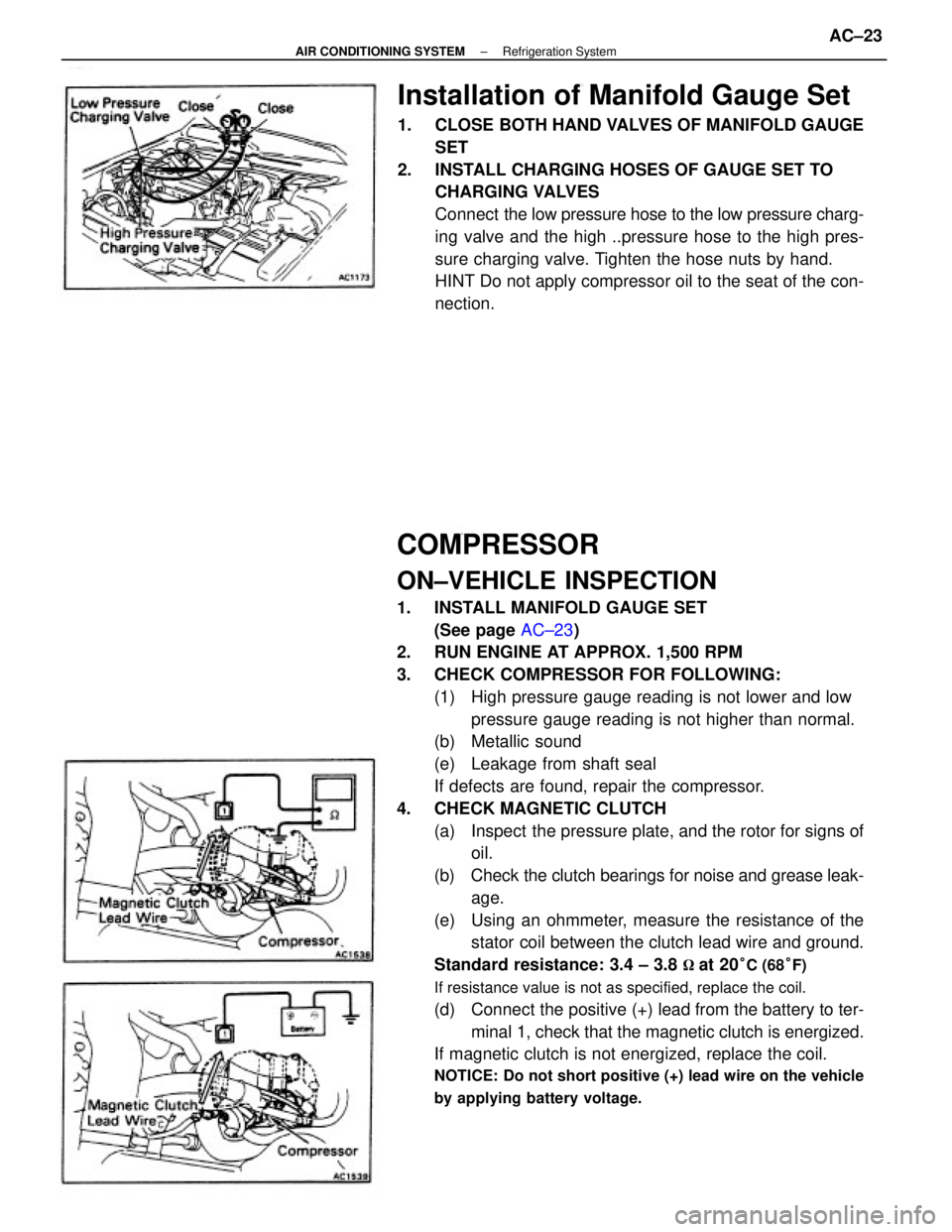
COMPRESSOR
ON±VEHICLE INSPECTION
1. INSTALL MANIFOLD GAUGE SET
(See page AC±23)
2. RUN ENGINE AT APPROX. 1,500 RPM
3. CHECK COMPRESSOR FOR FOLLOWING:
(1) High pressure gauge reading is not lower and low
pressure gauge reading is not higher than normal.
(b) Metallic sound
(e) Leakage from shaft seal
If defects are found, repair the compressor.
4. CHECK MAGNETIC CLUTCH
(a) Inspect the pressure plate, and the rotor for signs of
oil.
(b) Check the clutch bearings for noise and grease leak-
age.
(e) Using an ohmmeter, measure the resistance of the
stator coil between the clutch lead wire and ground.
Standard resistance: 3.4 ± 3.8
at 20°C (68°F)
If resistance value is not as specified, replace the coil.
(d) Connect the positive (+) lead from the battery to ter-
minal 1, check that the magnetic clutch is energized.
If magnetic clutch is not energized, replace the coil.
NOTICE: Do not short positive (+) lead wire on the vehicle
by applying battery voltage.
Installation of Manifold Gauge Set
1. CLOSE BOTH HAND VALVES OF MANIFOLD GAUGE
SET
2. INSTALL CHARGING HOSES OF GAUGE SET TO
CHARGING VALVES
Connect the low pressure hose to the low pressure charg-
ing valve and the high ..pressure hose to the high pres-
sure charging valve. Tighten the hose nuts by hand.
HINT Do not apply compressor oil to the seat of the con-
nection.
± AIR CONDITIONING SYSTEMRefrigeration SystemAC±23
Page 225 of 2389
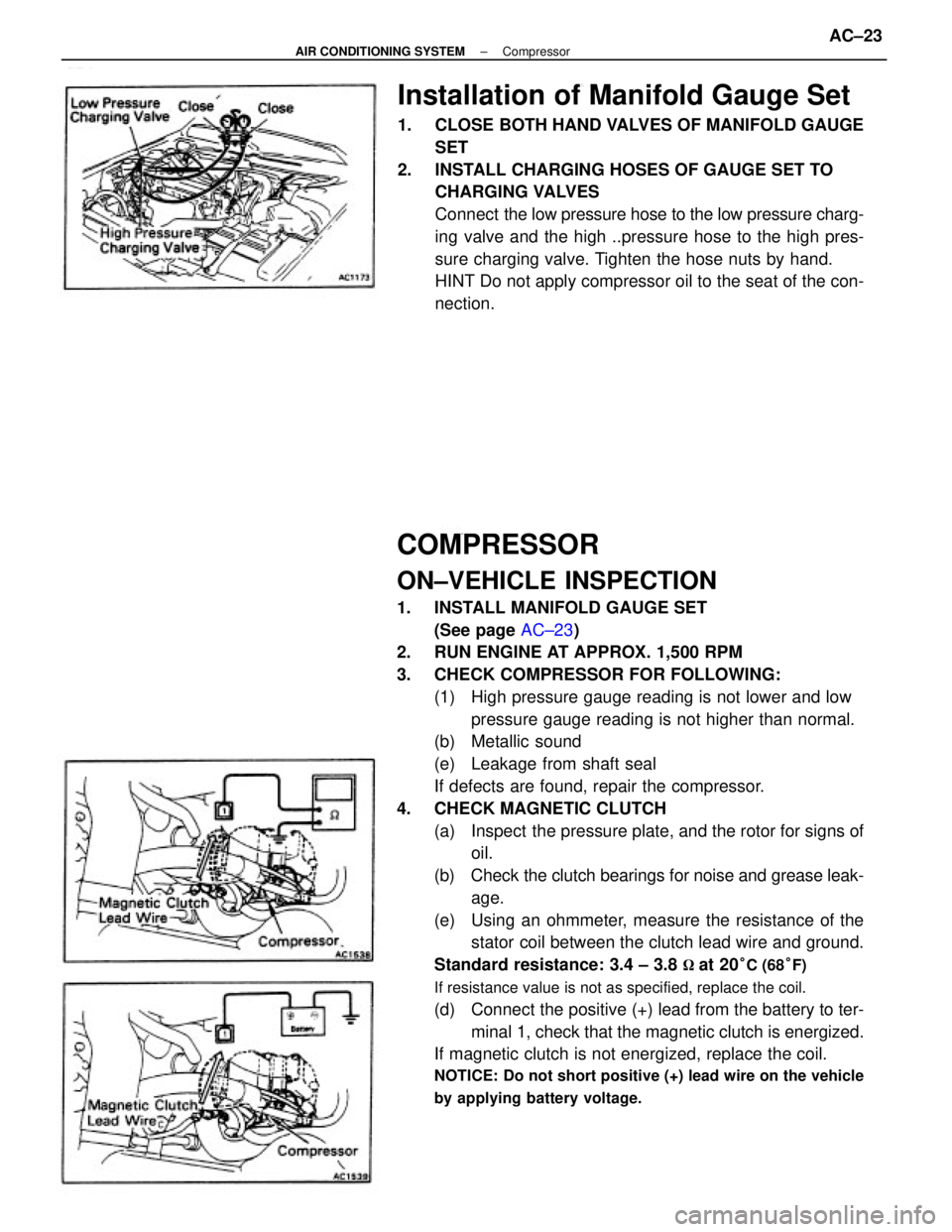
COMPRESSOR
ON±VEHICLE INSPECTION
1. INSTALL MANIFOLD GAUGE SET
(See page AC±23)
2. RUN ENGINE AT APPROX. 1,500 RPM
3. CHECK COMPRESSOR FOR FOLLOWING:
(1) High pressure gauge reading is not lower and low
pressure gauge reading is not higher than normal.
(b) Metallic sound
(e) Leakage from shaft seal
If defects are found, repair the compressor.
4. CHECK MAGNETIC CLUTCH
(a) Inspect the pressure plate, and the rotor for signs of
oil.
(b) Check the clutch bearings for noise and grease leak-
age.
(e) Using an ohmmeter, measure the resistance of the
stator coil between the clutch lead wire and ground.
Standard resistance: 3.4 ± 3.8
at 20°C (68°F)
If resistance value is not as specified, replace the coil.
(d) Connect the positive (+) lead from the battery to ter-
minal 1, check that the magnetic clutch is energized.
If magnetic clutch is not energized, replace the coil.
NOTICE: Do not short positive (+) lead wire on the vehicle
by applying battery voltage.
Installation of Manifold Gauge Set
1. CLOSE BOTH HAND VALVES OF MANIFOLD GAUGE
SET
2. INSTALL CHARGING HOSES OF GAUGE SET TO
CHARGING VALVES
Connect the low pressure hose to the low pressure charg-
ing valve and the high ..pressure hose to the high pres-
sure charging valve. Tighten the hose nuts by hand.
HINT Do not apply compressor oil to the seat of the con-
nection.
± AIR CONDITIONING SYSTEMCompressorAC±23
Page 227 of 2389
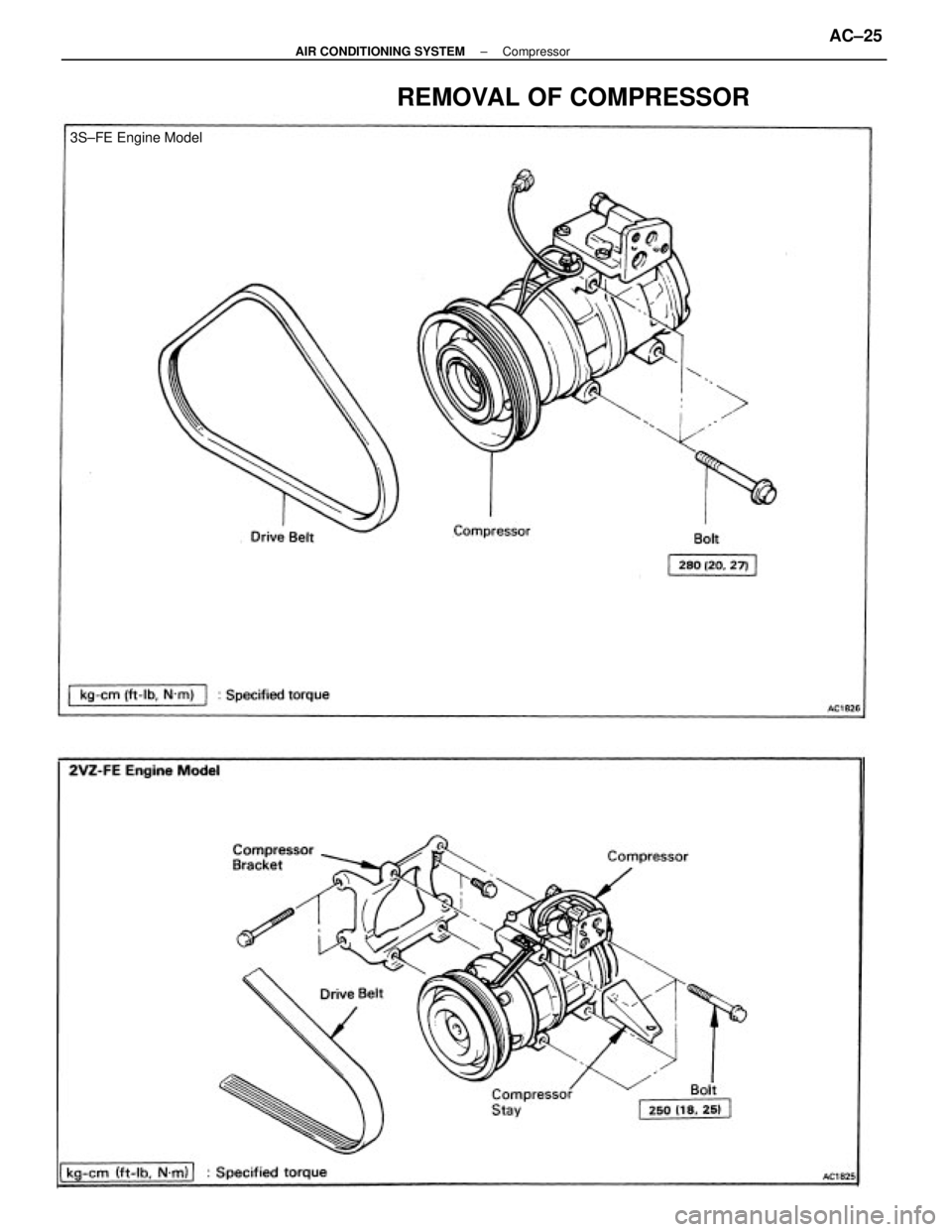
REMOVAL OF COMPRESSOR
3S±FE Engine Model
± AIR CONDITIONING SYSTEMCompressorAC±25