TOYOTA RAV4 1996 Service Repair Manual
Manufacturer: TOYOTA, Model Year: 1996, Model line: RAV4, Model: TOYOTA RAV4 1996Pages: 1354, PDF Size: 30.43 MB
Page 211 of 1354
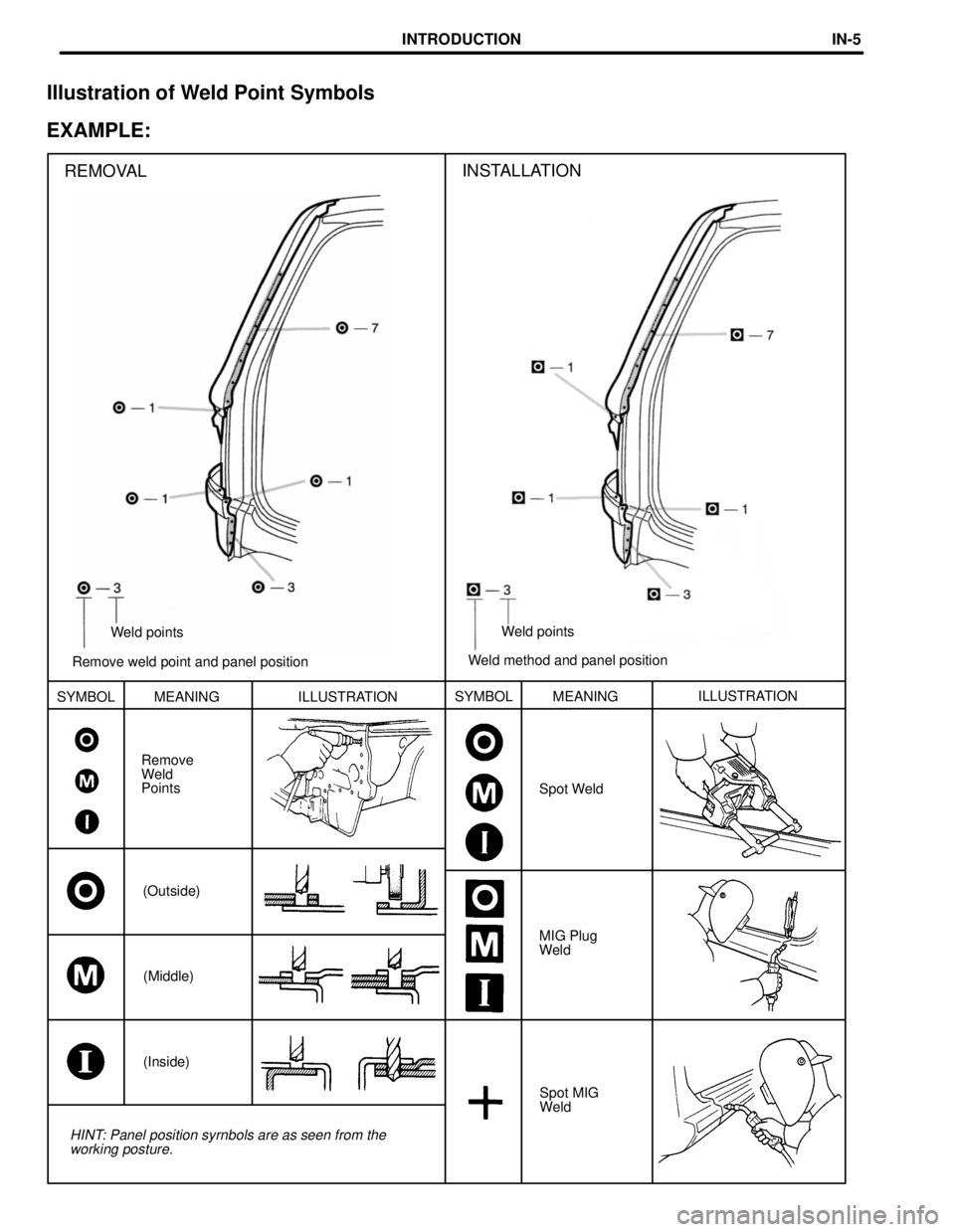
Remove weld point and panel positionWeld points
REMOVAL
Weld method and panel positionWeld points
INSTALLATION
SYMBOL MEANING ILLUSTRATIONSYMBOL
Spot WeldMEANINGILLUSTRATION
Remove
Weld
Points
(Outside)
MIG Plug
Weld
(Middle)
(Inside)
Spot MIG
Weld
HINT: Panel position syrnbols are as seen from the
working posture.
Illustration of Weld Point Symbols
EXAMPLE:
INTRODUCTIONINœ5
Page 212 of 1354
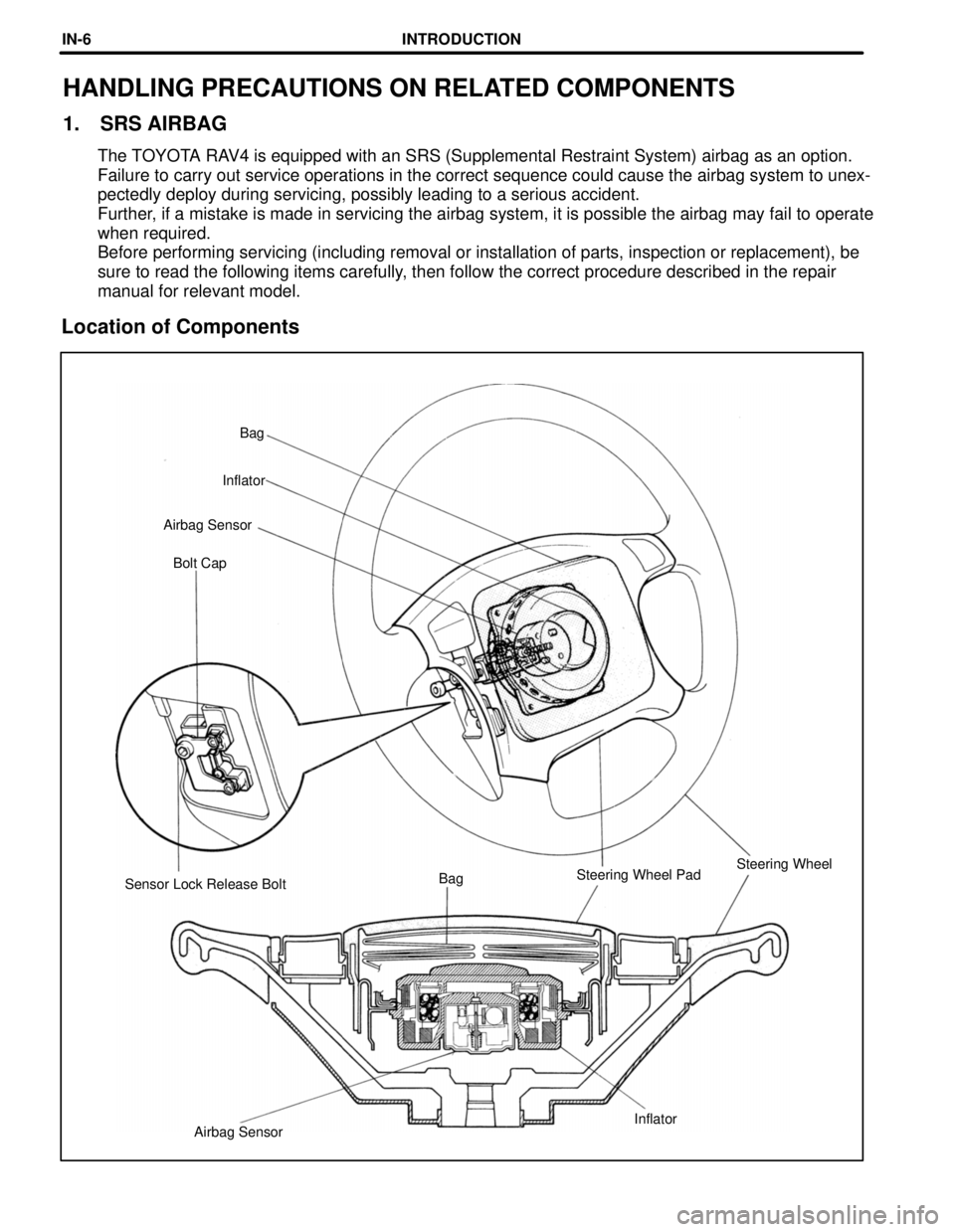
Airbag SensorInflator Sensor Lock Release BoltBagSteering Wheel PadSteering Wheel Bolt Cap Airbag SensorInflatorBag
HANDLING PRECAUTIONS ON RELATED COMPONENTS
1. SRS AIRBAG
The TOYOTA RAV4 is equipped with an SRS (Supplemental Restraint System) airbag as an option.
Failure to carry out service operations in the correct sequence could cause the airbag system to unexœ
pectedly deploy during servicing, possibly leading to a serious accident.
Further, if a mistake is made in servicing the airbag system, it is possible the airbag may fail to operate
when required.
Before performing servicing (including removal or installation of parts, inspection or replacement), be
sure to read the following items carefully, then follow the correct procedure described in the repair
manual for relevant model.
Location of Components
INTRODUCTIONINœ6
Page 213 of 1354
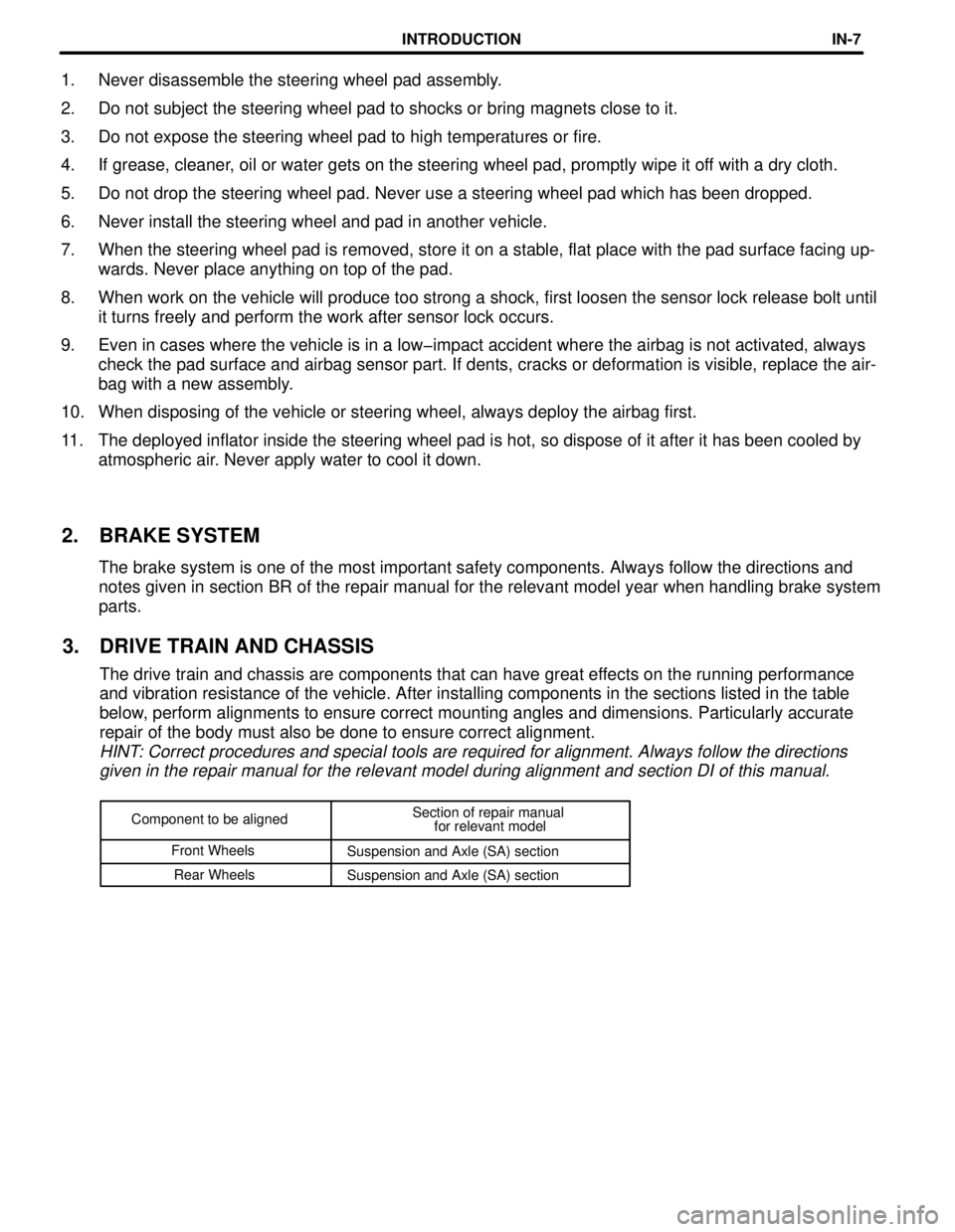
Component to be alignedSection of repair manual
for relevant model
Front Wheels
Suspension and Axle (SA) section
Rear Wheels
Suspension and Axle (SA) section
1. Never disassemble the steering wheel pad assembly.
2. Do not subject the steering wheel pad to shocks or bring magnets close to it.
3. Do not expose the steering wheel pad to high temperatures or fire.
4. If grease, cleaner, oil or water gets on the steering wheel pad, promptly wipe it off with a dry cloth.
5. Do not drop the steering wheel pad. Never use a steering wheel pad which has been dropped.
6. Never install the steering wheel and pad in another vehicle.
7. When the steering wheel pad is removed, store it on a stable, flat place with the pad surface facing upœ
wards. Never place anything on top of the pad.
8. When work on the vehicle will produce too strong a shock, first loosen the sensor lock release bolt until
it turns freely and perform the work after sensor lock occurs.
9. Even in cases where the vehicle is in a low-impact accident where the airbag is not activated, always
check the pad surface and airbag sensor part. If dents, cracks or deformation is visible, replace the airœ
bag with a new assembly.
10. When disposing of the vehicle or steering wheel, always deploy the airbag first.
11. The deployed inflator inside the steering wheel pad is hot, so dispose of it after it has been cooled by
atmospheric air. Never apply water to cool it down.
2. BRAKE SYSTEM
The brake system is one of the most important safety components. Always follow the directions and
notes given in section BR of the repair manual for the relevant model year when handling brake system
parts.
3. DRIVE TRAIN AND CHASSIS
The drive train and chassis are components that can have great effects on the running performance
and vibration resistance of the vehicle. After installing components in the sections listed in the table
below, perform alignments to ensure correct mounting angles and dimensions. Particularly accurate
repair of the body must also be done to ensure correct alignment.
HINT: Correct procedures and special tools are required for alignment. Always follow the directions
given in the repair manual for the relevant model during alignment and section DI of this manual.
INTRODUCTIONINœ7
Page 214 of 1354
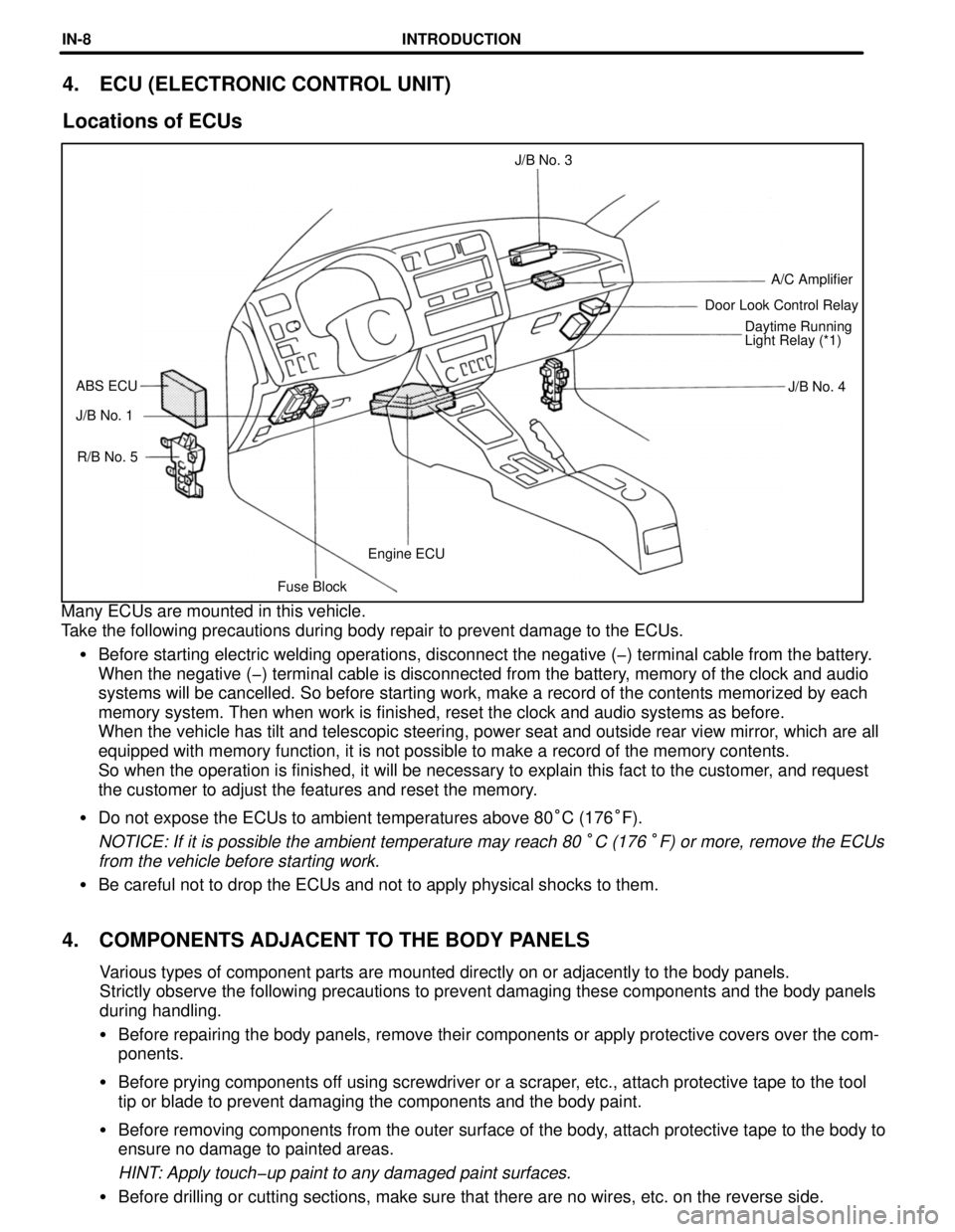
Fuse BlockEngine ECU R/B No. 5 J/B No. 1J/B No. 4 ABS ECUDaytime Running
Light Relay (*1) Door Look Control RelayA/C Amplifier J/B No. 3
4. ECU (ELECTRONIC CONTROL UNIT)
Locations of ECUs
Many ECUs are mounted in this vehicle.
Take the following precautions during body repair to prevent damage to the ECUs.
Before starting electric welding operations, disconnect the negative (-) terminal cable from the battery.
When the negative (-) terminal cable is disconnected from the battery, memory of the clock and audio
systems will be cancelled. So before starting work, make a record of the contents memorized by each
memory system. Then when work is finished, reset the clock and audio systems as before.
When the vehicle has tilt and telescopic steering, power seat and outside rear view mirror, which are all
equipped with memory function, it is not possible to make a record of the memory contents.
So when the operation is finished, it will be necessary to explain this fact to the customer, and request
the customer to adjust the features and reset the memory.
Do not expose the ECUs to ambient temperatures above 80°C (176°F).
NOTICE: If it is possible the ambient temperature may reach 80 °C (176 °F) or more, remove the ECUs
from the vehicle before starting work.
Be careful not to drop the ECUs and not to apply physical shocks to them.
4. COMPONENTS ADJACENT TO THE BODY PANELS
Various types of component parts are mounted directly on or adjacently to the body panels.
Strictly observe the following precautions to prevent damaging these components and the body panels
during handling.
Before repairing the body panels, remove their components or apply protective covers over the comœ
ponents.
Before prying components off using screwdriver or a scraper, etc., attach protective tape to the tool
tip or blade to prevent damaging the components and the body paint.
Before removing components from the outer surface of the body, attach protective tape to the body to
ensure no damage to painted areas.
HINT: Apply touch-up paint to any damaged paint surfaces.
Before drilling or cutting sections, make sure that there are no wires, etc. on the reverse side.
INTRODUCTIONINœ8
Page 215 of 1354
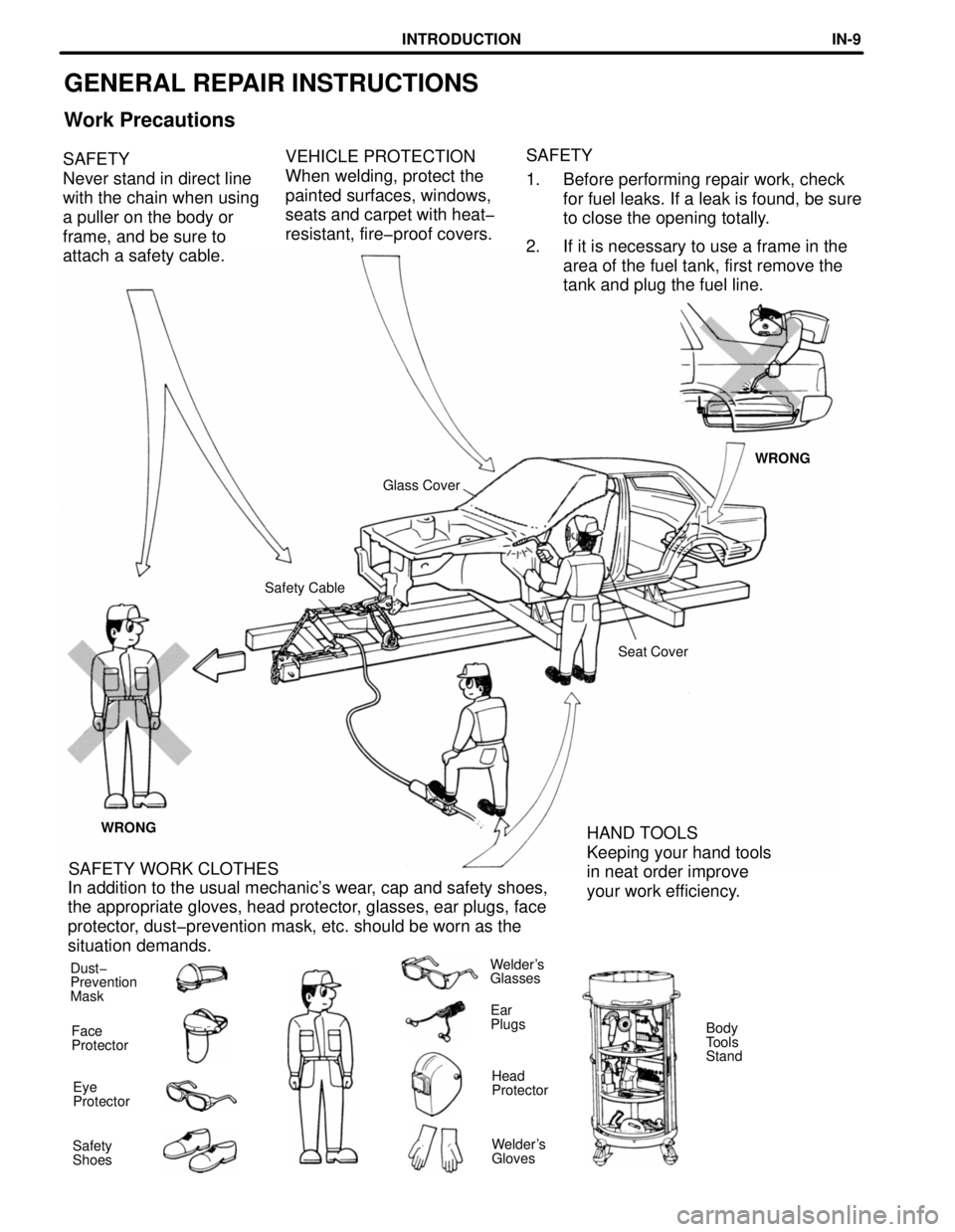
GENERAL REPAIR INSTRUCTIONS
Work Precautions
VEHICLE PROTECTION
When welding, protect the
painted surfaces, windows,
seats and carpet with heat-
resistant, fire-proof covers. SAFETY
Never stand in direct line
with the chain when using
a puller on the body or
frame, and be sure to
attach a safety cable.SAFETY
1. Before performing repair work, check
for fuel leaks. If a leak is found, be sure
to close the opening totally.
2. If it is necessary to use a frame in the
area of the fuel tank, first remove the
tank and plug the fuel line.
WRONG
Glass Cover
Safety Cable
Seat Cover
WRONG
HAND TOOLS
Keeping your hand tools
in neat order improve
your work efficiency. SAFETY WORK CLOTHES
In addition to the usual mechanic's wear, cap and safety shoes,
the appropriate gloves, head protector, glasses, ear plugs, face
protector, dust-prevention mask, etc. should be worn as the
situation demands.
Dust-
Prevention
MaskWelder's
Glasses
Ear
Plugs
Face
ProtectorBody
Tools
Stand
Head
Protector Eye
Protector
Welder's
Gloves Safety
Shoes
INTRODUCTIONINœ9
Page 216 of 1354
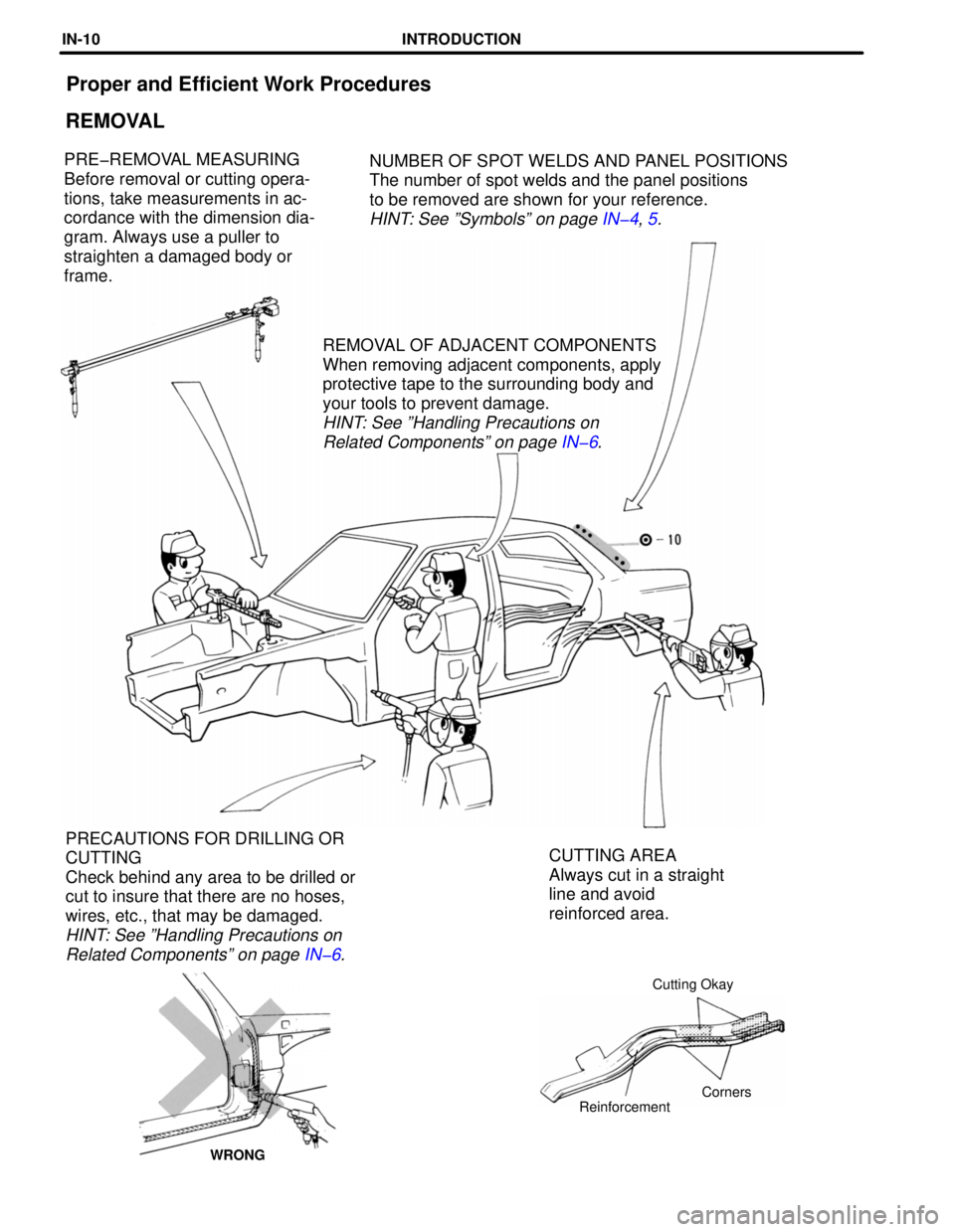
Proper and Efficient Work Procedures
REMOVAL
NUMBER OF SPOT WELDS AND PANEL POSITIONS
The number of spot welds and the panel positions
to be removed are shown for your reference.
HINT: See ºSymbolsº on page IN-4, 5.
PRE-REMOVAL MEASURING
Before removal or cutting operaœ
tions, take measurements in acœ
cordance with the dimension diaœ
gram. Always use a puller to
straighten a damaged body or
frame.
REMOVAL OF ADJACENT COMPONENTS
When removing adjacent components, apply
protective tape to the surrounding body and
your tools to prevent damage.
HINT: See ºHandling Precautions on
Related Componentsº on page IN-6.
CUTTING AREA
Always cut in a straight
line and avoid
reinforced area. PRECAUTIONS FOR DRILLING OR
CUTTING
Check behind any area to be drilled or
cut to insure that there are no hoses,
wires, etc., that may be damaged.
HINT: See ºHandling Precautions on
Related Componentsº on page IN-6.
Cutting Okay
Corners
Reinforcement
WRONG
INTRODUCTIONINœ10
Page 217 of 1354
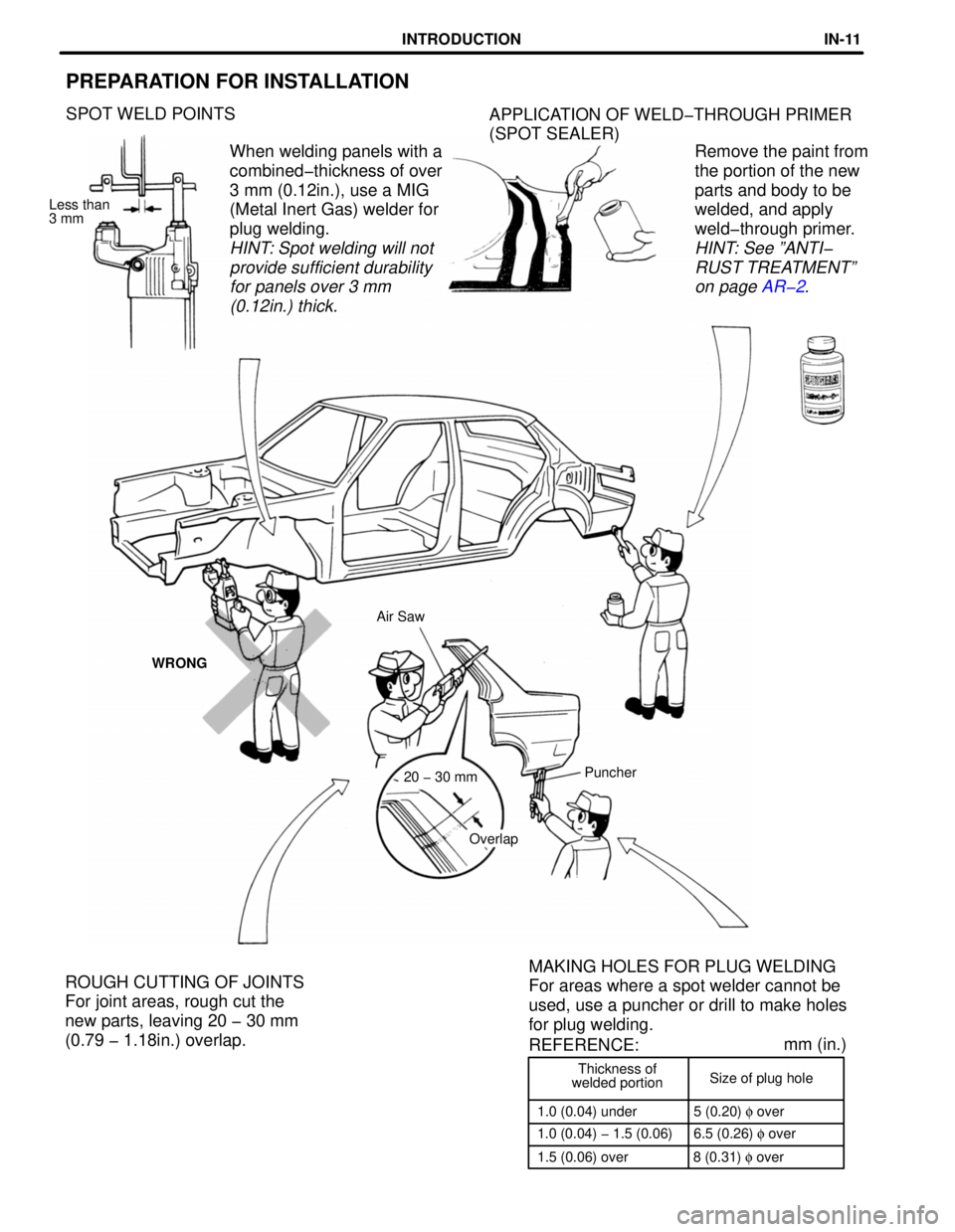
Thickness of
welded portionSize of plug hole
1.0 (0.04) under 5 (0.20) f over
1.0 (0.04) - 1.5 (0.06) 6.5 (0.26) f over
1.5 (0.06) over 8 (0.31) f over
REFERENCE:mm (in.)
PREPARATION FOR INSTALLATION
SPOT WELD POINTS
APPLICATION OF WELD-THROUGH PRIMER
(SPOT SEALER)
When welding panels with a
combined-thickness of over
3 mm (0.12in.), use a MIG
(Metal Inert Gas) welder for
plug welding.
HINT: Spot welding will not
provide sufficient durability
for panels over 3 mm
(0.12in.) thick.
Less than
3 mm
Remove the paint from
the portion of the new
parts and body to be
welded, and apply
weld-through primer.
HINT: See ºANTI-
RUST TREATMENTº
on page AR-2.
Air Saw
WRONG
Puncher
20 - 30 mm
Overlap
ROUGH CUTTING OF JOINTS
For joint areas, rough cut the
new parts, leaving 20 - 30 mm
(0.79 - 1.18in.) overlap.MAKING HOLES FOR PLUG WELDING
For areas where a spot welder cannot be
used, use a puncher or drill to make holes
for plug welding.
INTRODUCTIONINœ11
Page 218 of 1354
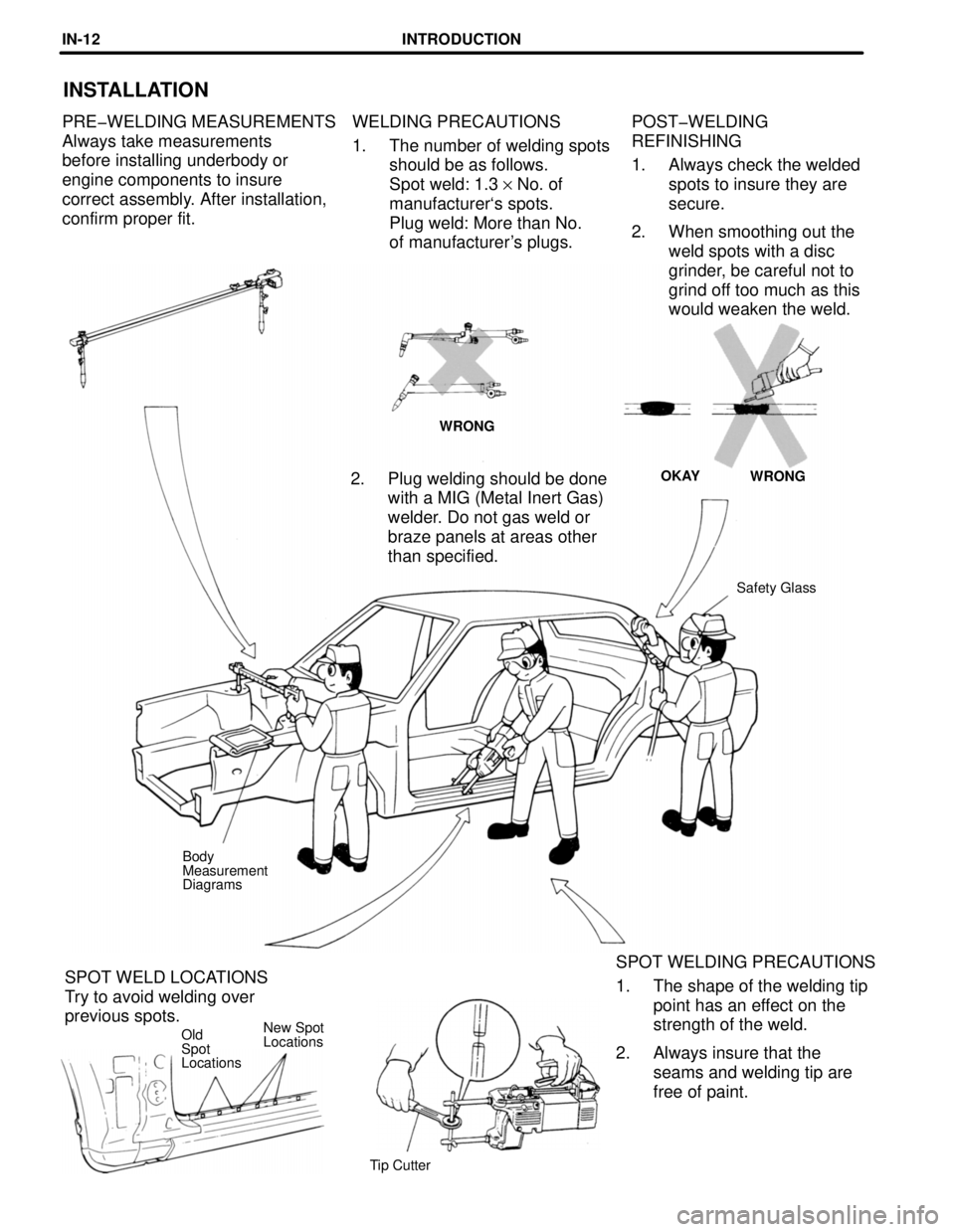
New Spot
Locations
POST-WELDING
REFINISHING
1. Always check the welded
spots to insure they are
secure.
2. When smoothing out the
weld spots with a disc
grinder, be careful not to
grind off too much as this
would weaken the weld.
INSTALLATION
PRE-WELDING MEASUREMENTS
Always take measurements
before installing underbody or
engine components to insure
correct assembly. After installation,
confirm proper fit.WELDING PRECAUTIONS
1. The number of welding spots
should be as follows.
Spot weld: 1.3 y No. of
manufacturer`s spots.
Plug weld: More than No.
of manufacturer's plugs.
WRONG
WRONG OKAY
2. Plug welding should be done
with a MIG (Metal Inert Gas)
welder. Do not gas weld or
braze panels at areas other
than specified.
Safety Glass
Body
Measurement
Diagrams
SPOT WELDING PRECAUTIONS
1. The shape of the welding tip
point has an effect on the
strength of the weld.
2. Always insure that the
seams and welding tip are
free of paint. SPOT WELD LOCATIONS
Try to avoid welding over
previous spots.
Old
Spot
Locations
Tip Cutter
INTRODUCTIONINœ12
Page 219 of 1354
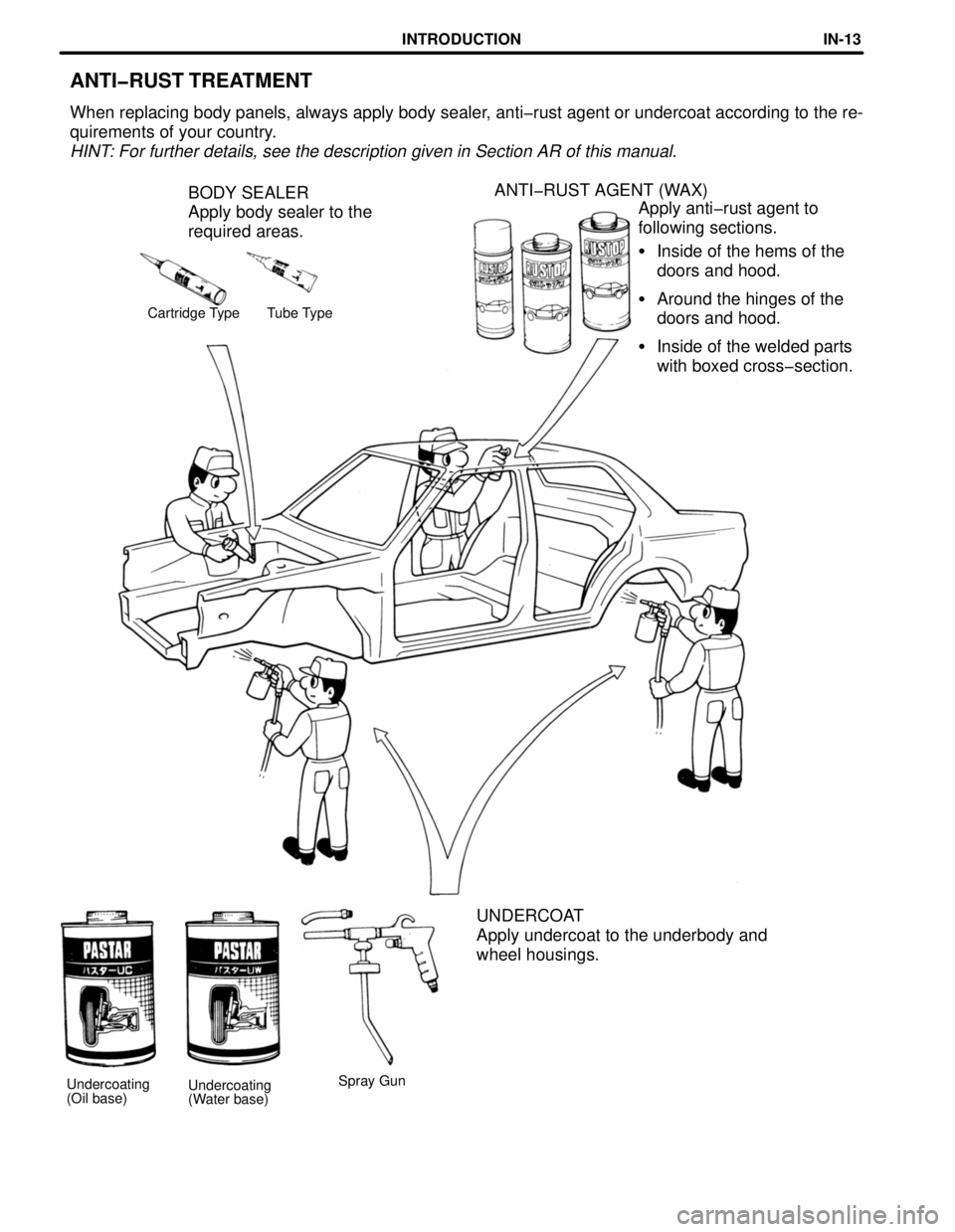
ANTI-RUST TREATMENT
When replacing body panels, always apply body sealer, anti-rust agent or undercoat according to the reœ
quirements of your country.
HINT: For further details, see the description given in Section AR of this manual.
BODY SEALER
Apply body sealer to the
required areas.ANTI-RUST AGENT (WAX)
Apply anti-rust agent to
following sections.
Inside of the hems of the
doors and hood.
Around the hinges of the
doors and hood.
Inside of the welded parts
with boxed cross-section.
Cartridge Type Tube Type
UNDERCOAT
Apply undercoat to the underbody and
wheel housings.
Spray Gun
Undercoating
(Oil base)Undercoating
(Water base)
INTRODUCTIONINœ13
Page 220 of 1354
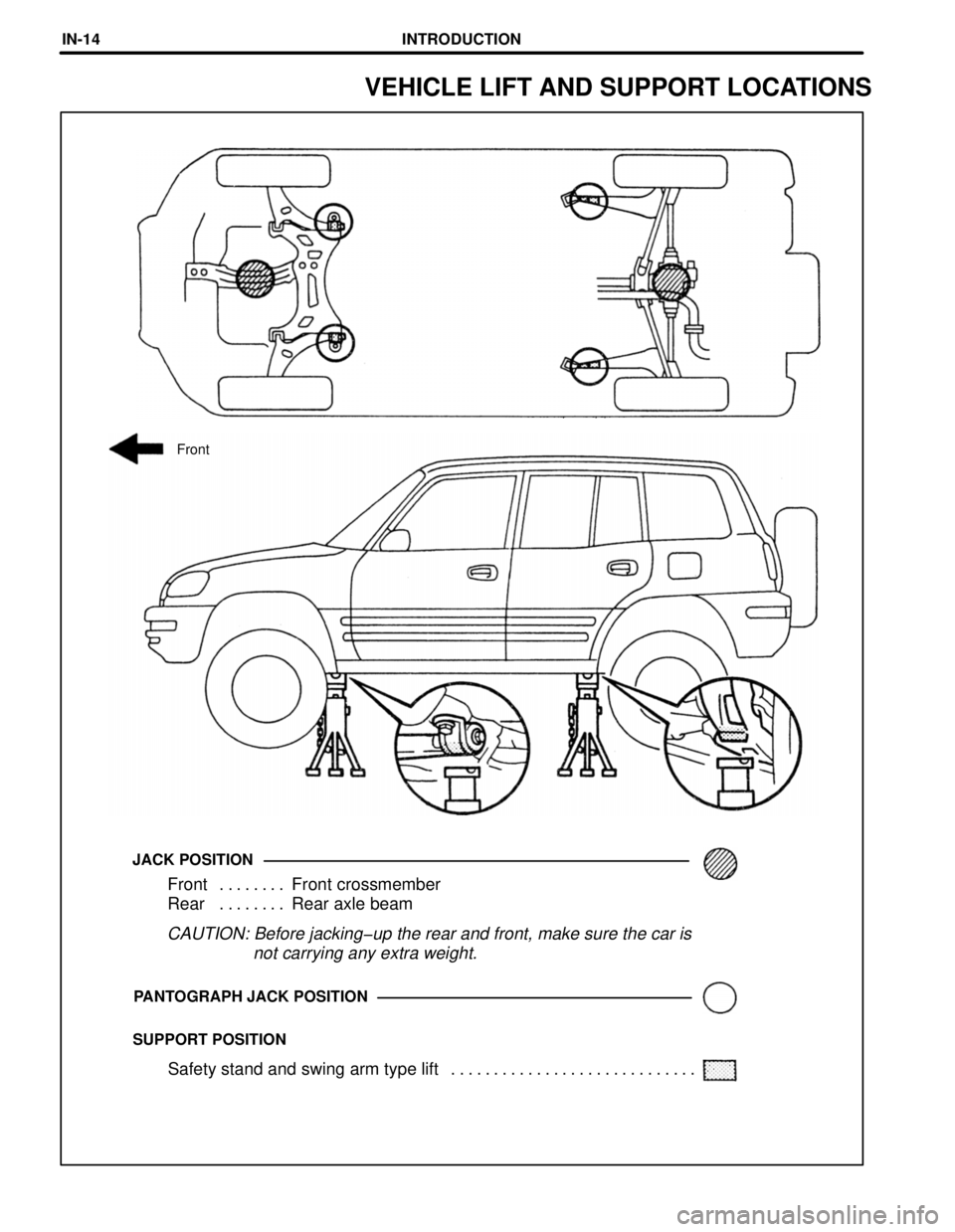
SUPPORT POSITIONPANTOGRAPH JACK POSITION
CAUTION: Before jacking-up the rear and front, make sure the car is
not carrying any extra weight.
Front Front crossmember. . . . . . . .
Rear Rear axle beam. . . . . . . .
JACK POSITION
Front
VEHICLE LIFT AND SUPPORT LOCATIONS
Safety stand and swing arm type lift . . . . . . . . . . . . . . . . . . . . . . . . . . . . .
INTRODUCTIONINœ14