engine YAMAHA VX110 2005 Owner's Guide
[x] Cancel search | Manufacturer: YAMAHA, Model Year: 2005, Model line: VX110, Model: YAMAHA VX110 2005Pages: 347, PDF Size: 14.17 MB
Page 91 of 347
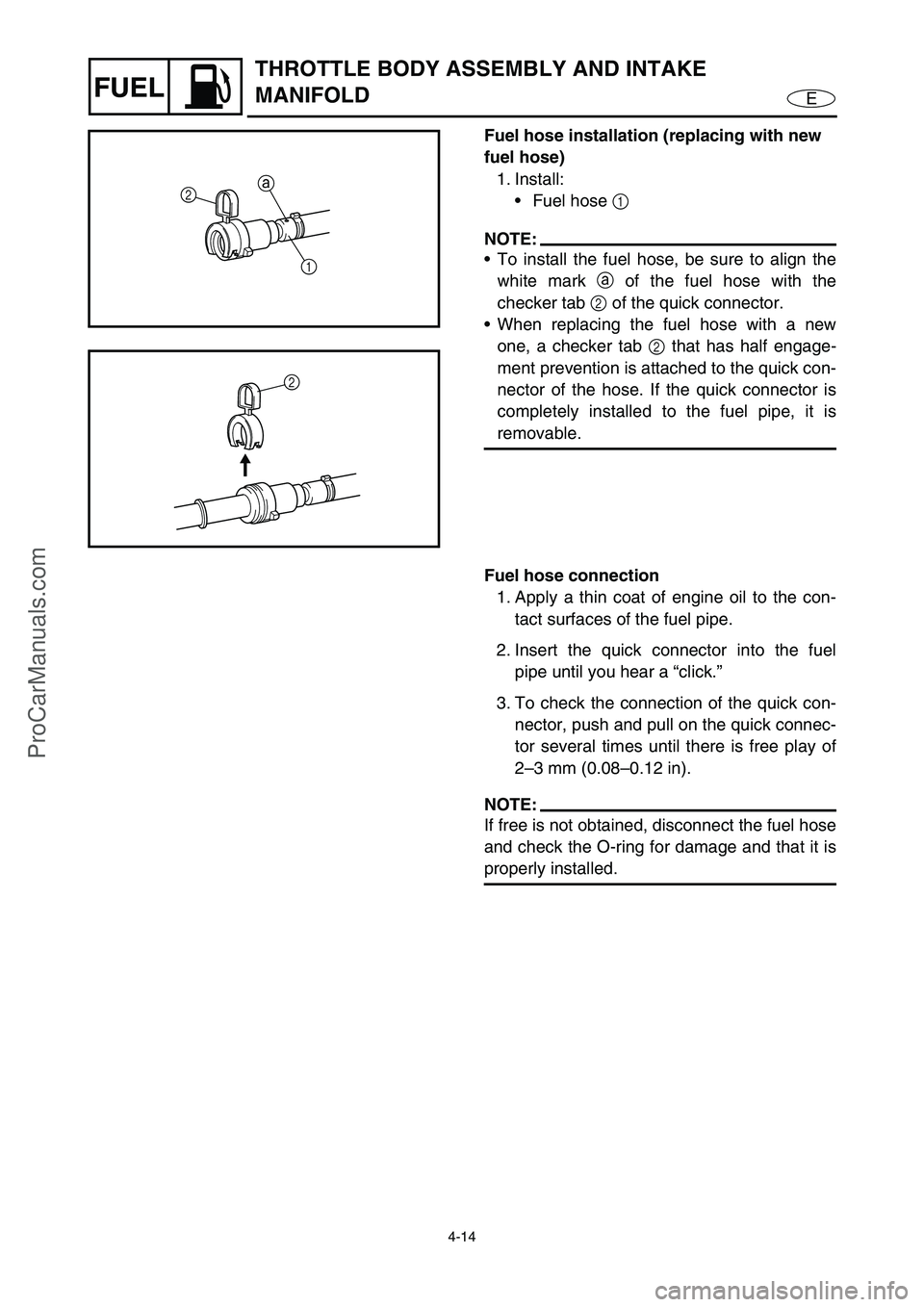
4-14
EFUEL
THROTTLE BODY ASSEMBLY AND INTAKE
MANIFOLD
Fuel hose installation (replacing with new
fuel hose)
1. Install:
Fuel hose 1
NOTE:
To install the fuel hose, be sure to align the
white mark a
of the fuel hose with the
checker tab 2
of the quick connector.
When replacing the fuel hose with a new
one, a checker tab 2
that has half engage-
ment prevention is attached to the quick con-
nector of the hose. If the quick connector is
completely installed to the fuel pipe, it is
removable.
2
1a
2
Fuel hose connection
1. Apply a thin coat of engine oil to the con-
tact surfaces of the fuel pipe.
2. Insert the quick connector into the fuel
pipe until you hear a “click.”
3. To check the connection of the quick con-
nector, push and pull on the quick connec-
tor several times until there is free play of
2–3 mm (0.08–0.12 in).
NOTE:
If free is not obtained, disconnect the fuel hose
and check the O-ring for damage and that it is
properly installed.
ProCarManuals.com
Page 94 of 347
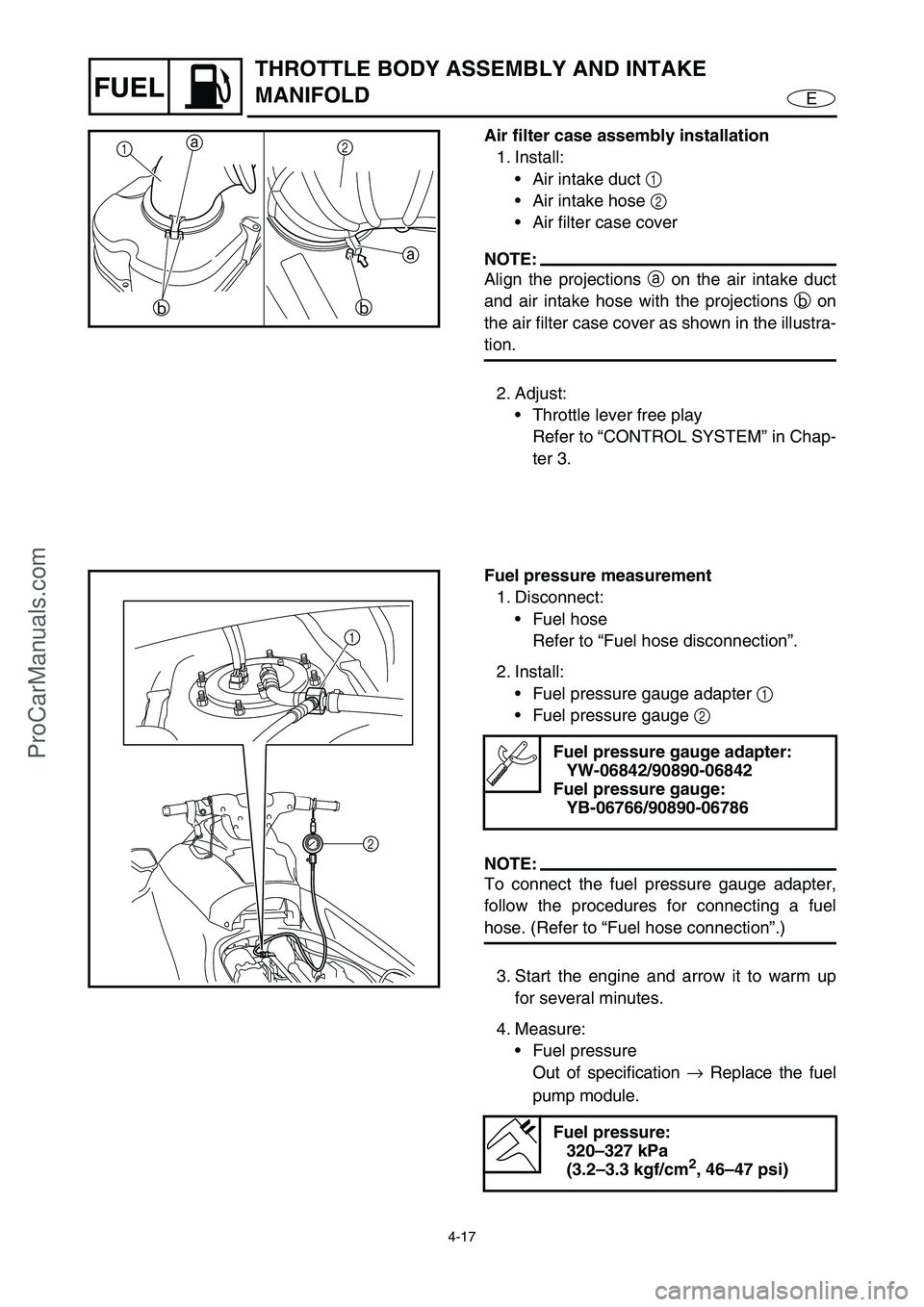
4-17
EFUEL
THROTTLE BODY ASSEMBLY AND INTAKE
MANIFOLD
Air filter case assembly installation
1. Install:
Air intake duct 1
Air intake hose 2
Air filter case cover
NOTE:
Align the projections a
on the air intake duct
and air intake hose with the projections b
on
the air filter case cover as shown in the illustra-
tion.
2. Adjust:
Throttle lever free play
Refer to “CONTROL SYSTEM” in Chap-
ter 3.
a
b a
b
2
1
Fuel pressure measurement
1. Disconnect:
Fuel hose
Refer to “Fuel hose disconnection”.
2. Install:
Fuel pressure gauge adapter 1
Fuel pressure gauge 2
NOTE:
To connect the fuel pressure gauge adapter,
follow the procedures for connecting a fuel
hose. (Refer to “Fuel hose connection”.)
3. Start the engine and arrow it to warm up
for several minutes.
4. Measure:
Fuel pressure
Out of specification →
Replace the fuel
pump module.
Fuel pressure gauge adapter:
YW-06842/90890-06842
Fuel pressure gauge:
YB-06766/90890-06786
Fuel pressure:
320–327 kPa
(3.2–3.3 kgf/cm
2, 46–47 psi)
2
1
ProCarManuals.com
Page 97 of 347
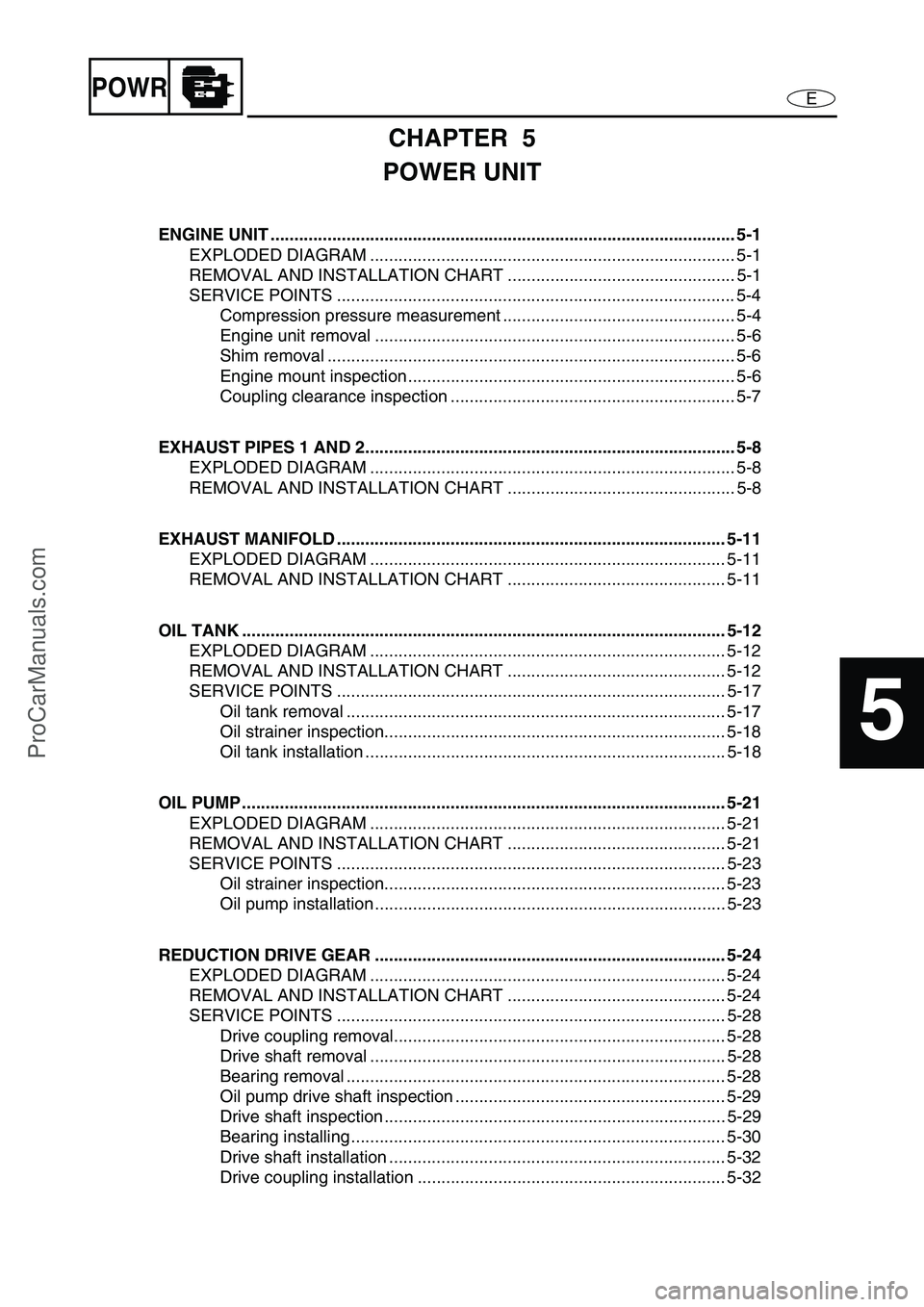
EPOWR
1
2
3
4
5
6
7
8
9
CHAPTER 5
POWER UNIT
ENGINE UNIT .................................................................................................. 5-1
EXPLODED DIAGRAM ............................................................................. 5-1
REMOVAL AND INSTALLATION CHART ................................................ 5-1
SERVICE POINTS .................................................................................... 5-4
Compression pressure measurement ................................................. 5-4
Engine unit removal ............................................................................ 5-6
Shim removal ...................................................................................... 5-6
Engine mount inspection ..................................................................... 5-6
Coupling clearance inspection ............................................................ 5-7
EXHAUST PIPES 1 AND 2.............................................................................. 5-8
EXPLODED DIAGRAM ............................................................................. 5-8
REMOVAL AND INSTALLATION CHART ................................................ 5-8
EXHAUST MANIFOLD .................................................................................. 5-11
EXPLODED DIAGRAM ........................................................................... 5-11
REMOVAL AND INSTALLATION CHART .............................................. 5-11
OIL TANK ...................................................................................................... 5-12
EXPLODED DIAGRAM ........................................................................... 5-12
REMOVAL AND INSTALLATION CHART .............................................. 5-12
SERVICE POINTS .................................................................................. 5-17
Oil tank removal ................................................................................ 5-17
Oil strainer inspection........................................................................ 5-18
Oil tank installation ............................................................................ 5-18
OIL PUMP ...................................................................................................... 5-21
EXPLODED DIAGRAM ........................................................................... 5-21
REMOVAL AND INSTALLATION CHART .............................................. 5-21
SERVICE POINTS .................................................................................. 5-23
Oil strainer inspection........................................................................ 5-23
Oil pump installation .......................................................................... 5-23
REDUCTION DRIVE GEAR .......................................................................... 5-24
EXPLODED DIAGRAM ........................................................................... 5-24
REMOVAL AND INSTALLATION CHART .............................................. 5-24
SERVICE POINTS .................................................................................. 5-28
Drive coupling removal...................................................................... 5-28
Drive shaft removal ........................................................................... 5-28
Bearing removal ................................................................................ 5-28
Oil pump drive shaft inspection ......................................................... 5-29
Drive shaft inspection ........................................................................ 5-29
Bearing installing ............................................................................... 5-30
Drive shaft installation ....................................................................... 5-32
Drive coupling installation ................................................................. 5-32
ProCarManuals.com
Page 100 of 347
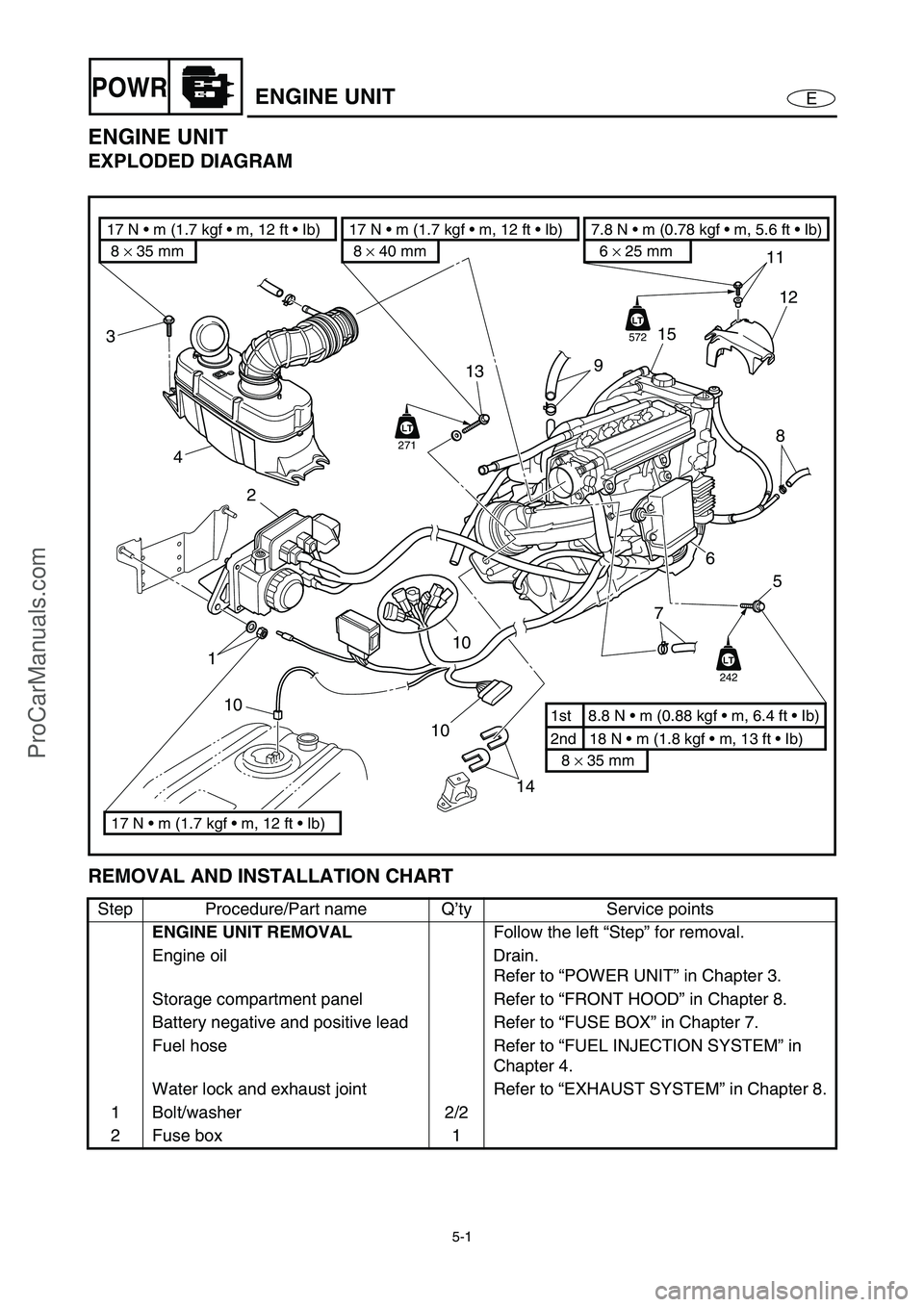
5-1
EPOWRENGINE UNIT
ENGINE UNIT
EXPLODED DIAGRAM
REMOVAL AND INSTALLATION CHART
Step Procedure/Part name Q’ty Service points
ENGINE UNIT REMOVAL
Follow the left “Step” for removal.
Engine oil Drain.
Refer to “POWER UNIT” in Chapter 3.
Storage compartment panel Refer to “FRONT HOOD” in Chapter 8.
Battery negative and positive lead Refer to “FUSE BOX” in Chapter 7.
Fuel hose Refer to “FUEL INJECTION SYSTEM” in
Chapter 4.
Water lock and exhaust joint Refer to “EXHAUST SYSTEM” in Chapter 8.
1 Bolt/washer 2/2
2 Fuse box 1
14 10
10
2
113
3
4
11
15
12
8
7
9
6
5
2nd 18 N m (1.8 kgf m, 13 ft Ib) 1st 8.8 N m (0.88 kgf m, 6.4 ft Ib)
8 × 35 mm
6 × 25 mm
7.8 N m (0.78 kgf m, 5.6 ft Ib)
8 × 35 mm 17 N m (1.7 kgf m, 12 ft Ib)
17 N m (1.7 kgf m, 12 ft Ib)8 × 40 mm
17 N m (1.7 kgf m, 12 ft Ib)
10LT
242
LT
LT
572
LT
LT
271
ProCarManuals.com
Page 101 of 347
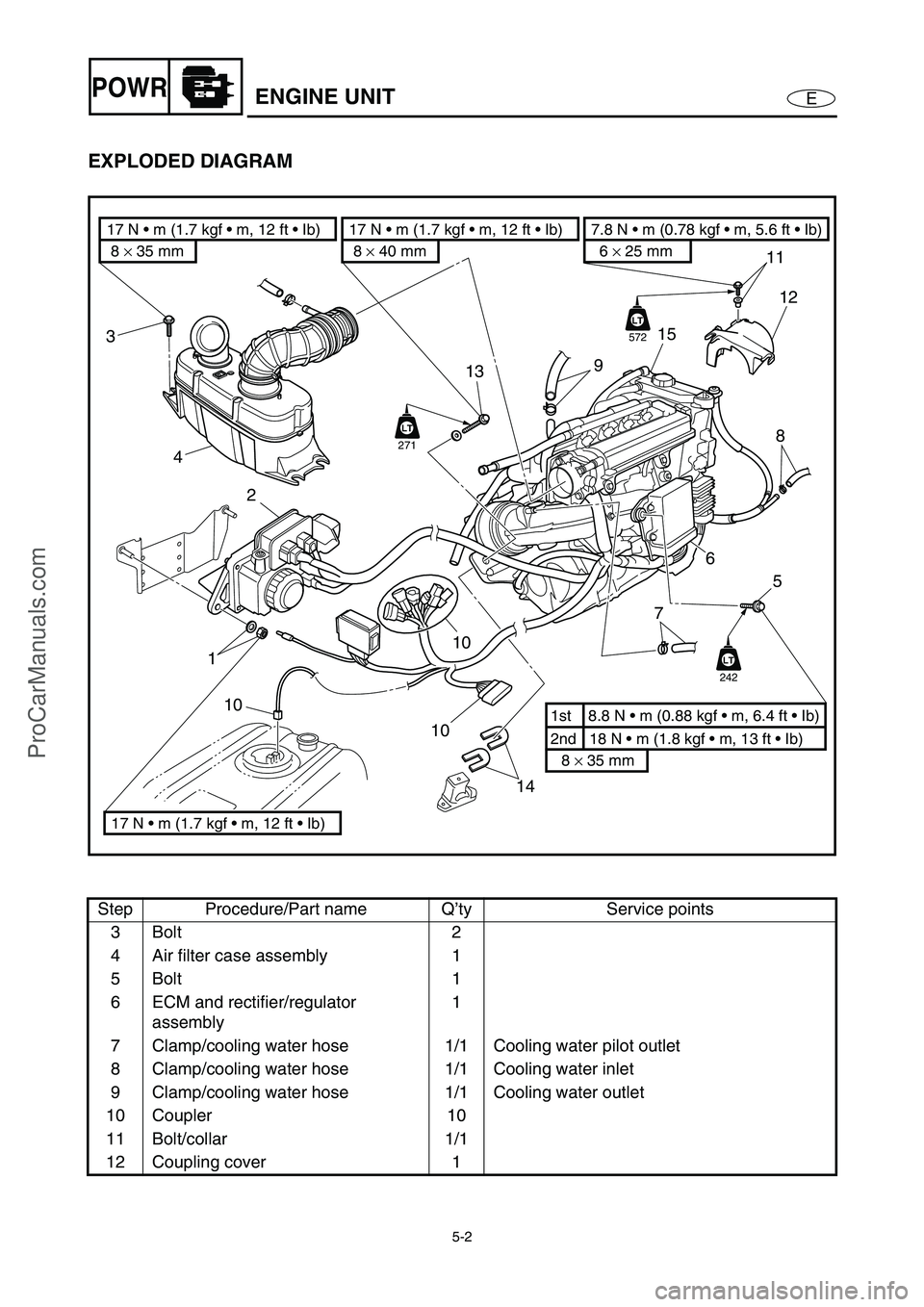
5-2
EPOWRENGINE UNIT
EXPLODED DIAGRAM
Step Procedure/Part name Q’ty Service points
3Bolt 2
4 Air filter case assembly 1
5Bolt 1
6 ECM and rectifier/regulator
assembly1
7 Clamp/cooling water hose 1/1 Cooling water pilot outlet
8 Clamp/cooling water hose 1/1 Cooling water inlet
9 Clamp/cooling water hose 1/1 Cooling water outlet
10 Coupler 10
11 Bolt/collar 1/1
12 Coupling cover 1
14 10
10
2
113
3
4
11
15
12
8
7
9
6
5
2nd 18 N m (1.8 kgf m, 13 ft Ib) 1st 8.8 N m (0.88 kgf m, 6.4 ft Ib)
8 × 35 mm
6 × 25 mm
7.8 N m (0.78 kgf m, 5.6 ft Ib)
8 × 35 mm 17 N m (1.7 kgf m, 12 ft Ib)
17 N m (1.7 kgf m, 12 ft Ib)8 × 40 mm
17 N m (1.7 kgf m, 12 ft Ib)
10LT
242
LT
LT
572
LT
LT
271
ProCarManuals.com
Page 102 of 347
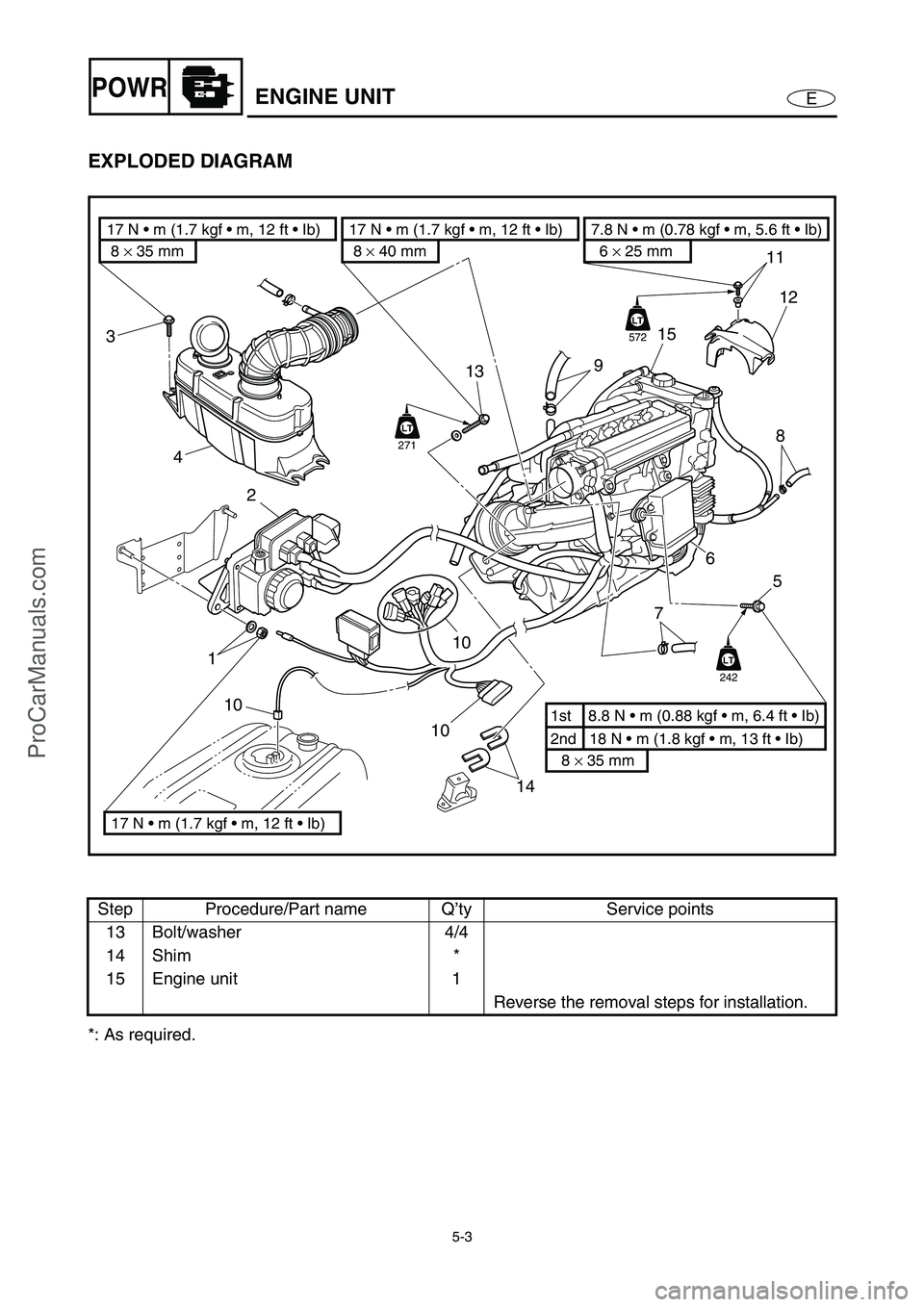
5-3
EPOWRENGINE UNIT
EXPLODED DIAGRAM
*: As required.Step Procedure/Part name Q’ty Service points
13 Bolt/washer 4/4
14 Shim *
15 Engine unit 1
Reverse the removal steps for installation.
14 10
10
2
113
3
4
11
15
12
8
7
9
6
5
2nd 18 N m (1.8 kgf m, 13 ft Ib) 1st 8.8 N m (0.88 kgf m, 6.4 ft Ib)
8 × 35 mm
6 × 25 mm
7.8 N m (0.78 kgf m, 5.6 ft Ib)
8 × 35 mm 17 N m (1.7 kgf m, 12 ft Ib)
17 N m (1.7 kgf m, 12 ft Ib)8 × 40 mm
17 N m (1.7 kgf m, 12 ft Ib)
10LT
242
LT
LT
572
LT
LT
271
ProCarManuals.com
Page 103 of 347
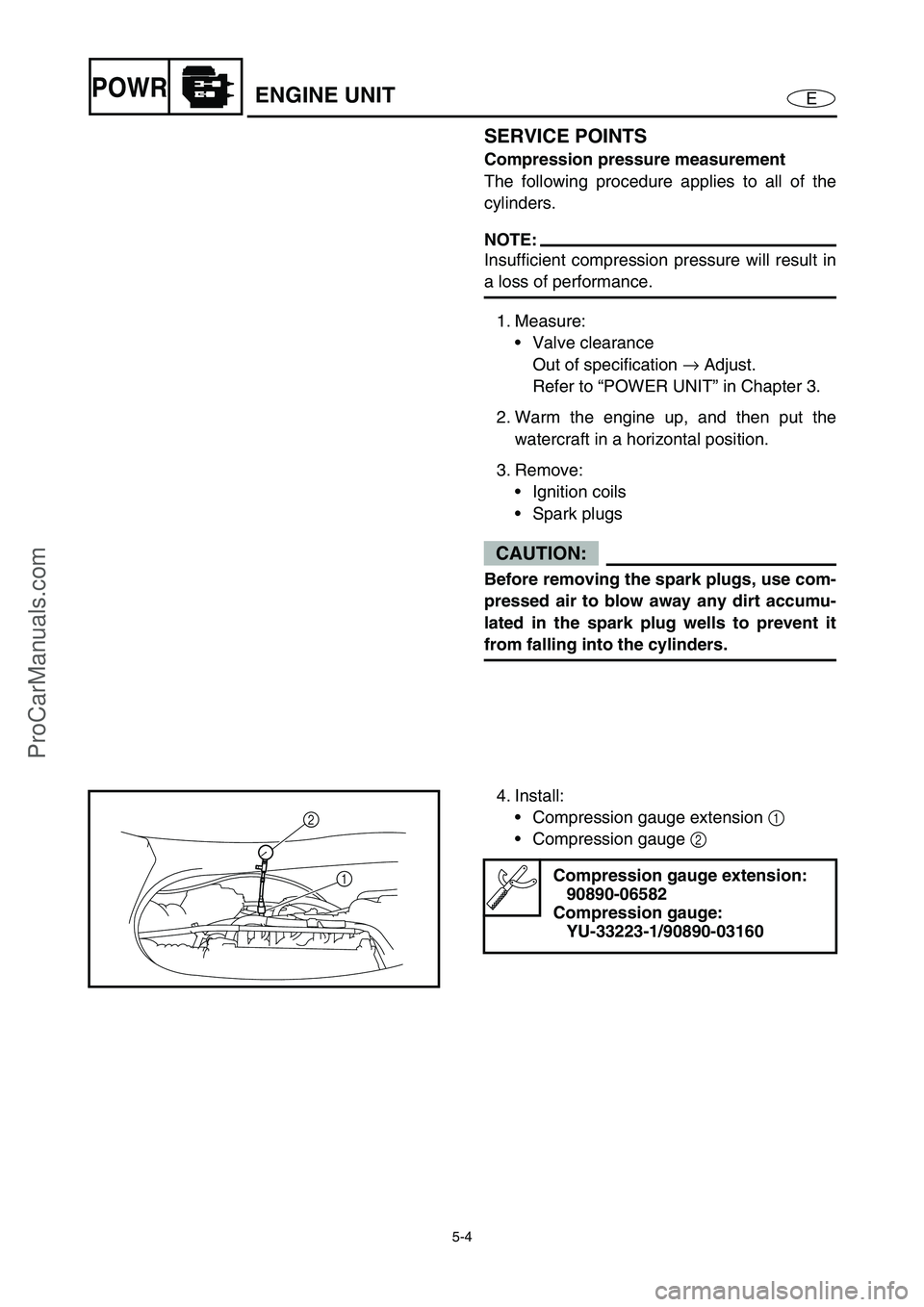
5-4
EPOWRENGINE UNIT
SERVICE POINTS
Compression pressure measurement
The following procedure applies to all of the
cylinders.
NOTE:
Insufficient compression pressure will result in
a loss of performance.
1. Measure:
Valve clearance
Out of specification →
Adjust.
Refer to “POWER UNIT” in Chapter 3.
2. Warm the engine up, and then put the
watercraft in a horizontal position.
3. Remove:
Ignition coils
Spark plugs
CAUTION:
Before removing the spark plugs, use com-
pressed air to blow away any dirt accumu-
lated in the spark plug wells to prevent it
from falling into the cylinders.
4. Install:
Compression gauge extension 1
Compression gauge 2
Compression gauge extension:
90890-06582
Compression gauge:
YU-33223-1/90890-03160
2
1
ProCarManuals.com
Page 104 of 347
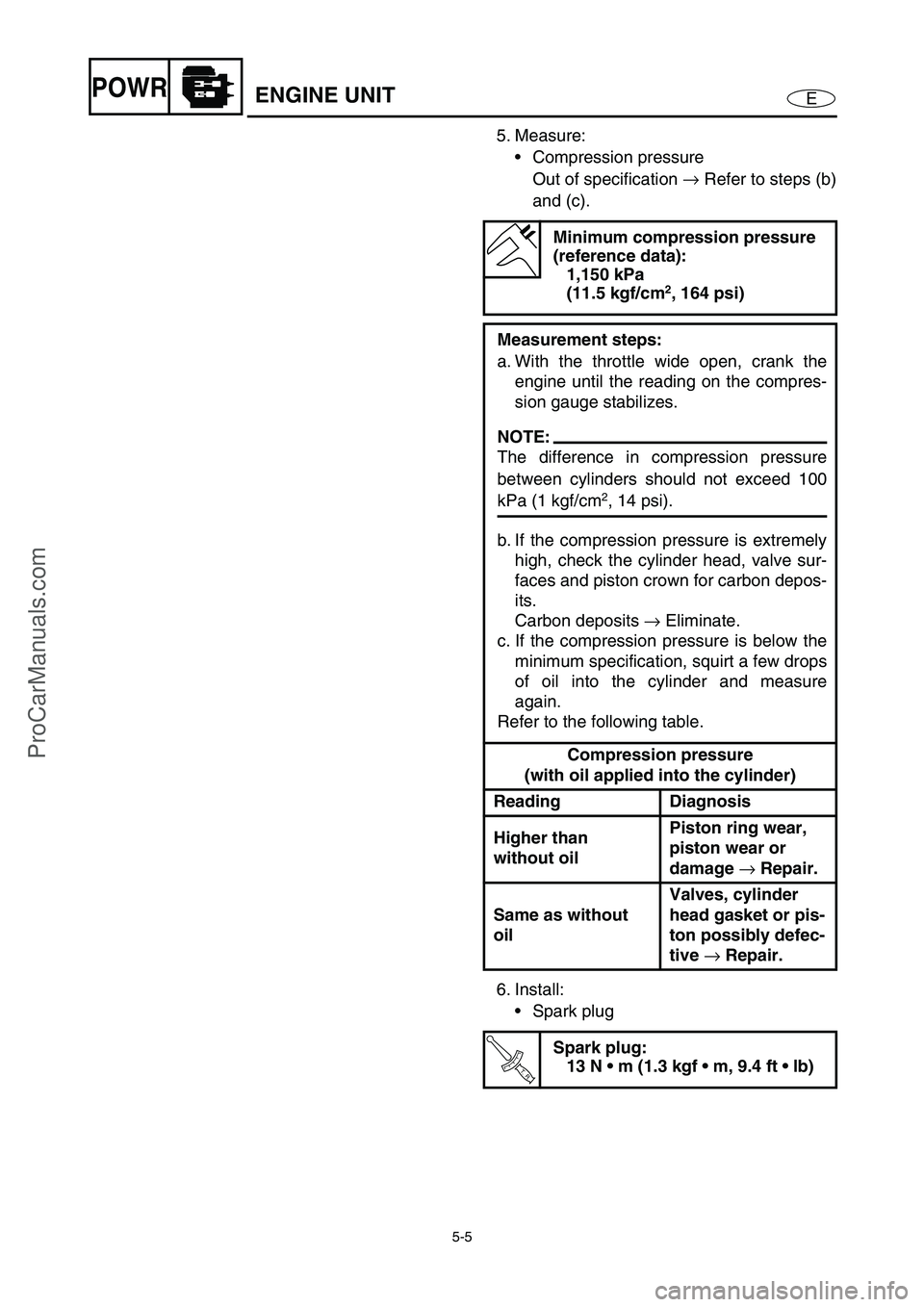
5-5
EPOWRENGINE UNIT
5. Measure:
Compression pressure
Out of specification →
Refer to steps (b)
and (c).
6. Install:
Spark plug
Minimum compression pressure
(reference data):
1,150 kPa
(11.5 kgf/cm
2, 164 psi)
Measurement steps:
a. With the throttle wide open, crank the
engine until the reading on the compres-
sion gauge stabilizes.
NOTE:
The difference in compression pressure
between cylinders should not exceed 100
kPa (1 kgf/cm2, 14 psi).
b. If the compression pressure is extremely
high, check the cylinder head, valve sur-
faces and piston crown for carbon depos-
its.
Carbon deposits →
Eliminate.
c. If the compression pressure is below the
minimum specification, squirt a few drops
of oil into the cylinder and measure
again.
Refer to the following table.
Compression pressure
(with oil applied into the cylinder)
Reading Diagnosis
Higher than
without oilPiston ring wear,
piston wear or
damage
→ Repair.
Same as without
oilValves, cylinder
head gasket or pis-
ton possibly defec-
tive
→ Repair.
T R..
Spark plug:
13 N m (1.3 kgf m, 9.4 ft lb)
ProCarManuals.com
Page 105 of 347
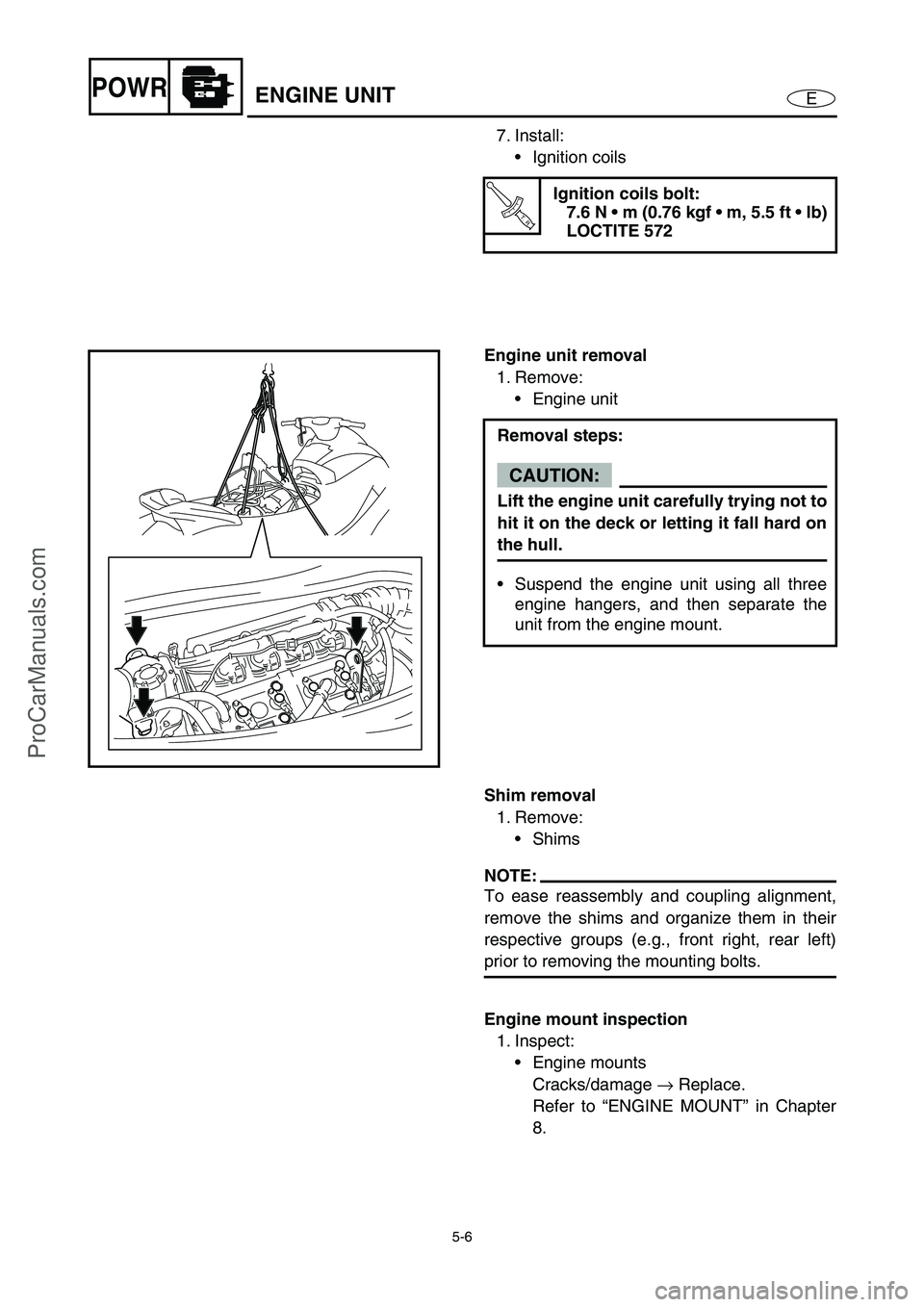
5-6
EPOWRENGINE UNIT
7. Install:
Ignition coils
T R..
Ignition coils bolt:
7.6 N m (0.76 kgf m, 5.5 ft lb)
LOCTITE 572
Engine unit removal
1. Remove:
Engine unit
Removal steps:
CAUTION:
Lift the engine unit carefully trying not to
hit it on the deck or letting it fall hard on
the hull.
Suspend the engine unit using all three
engine hangers, and then separate the
unit from the engine mount.
Shim removal
1. Remove:
Shims
NOTE:
To ease reassembly and coupling alignment,
remove the shims and organize them in their
respective groups (e.g., front right, rear left)
prior to removing the mounting bolts.
Engine mount inspection
1. Inspect:
Engine mounts
Cracks/damage →
Replace.
Refer to “ENGINE MOUNT” in Chapter
8.
ProCarManuals.com
Page 106 of 347
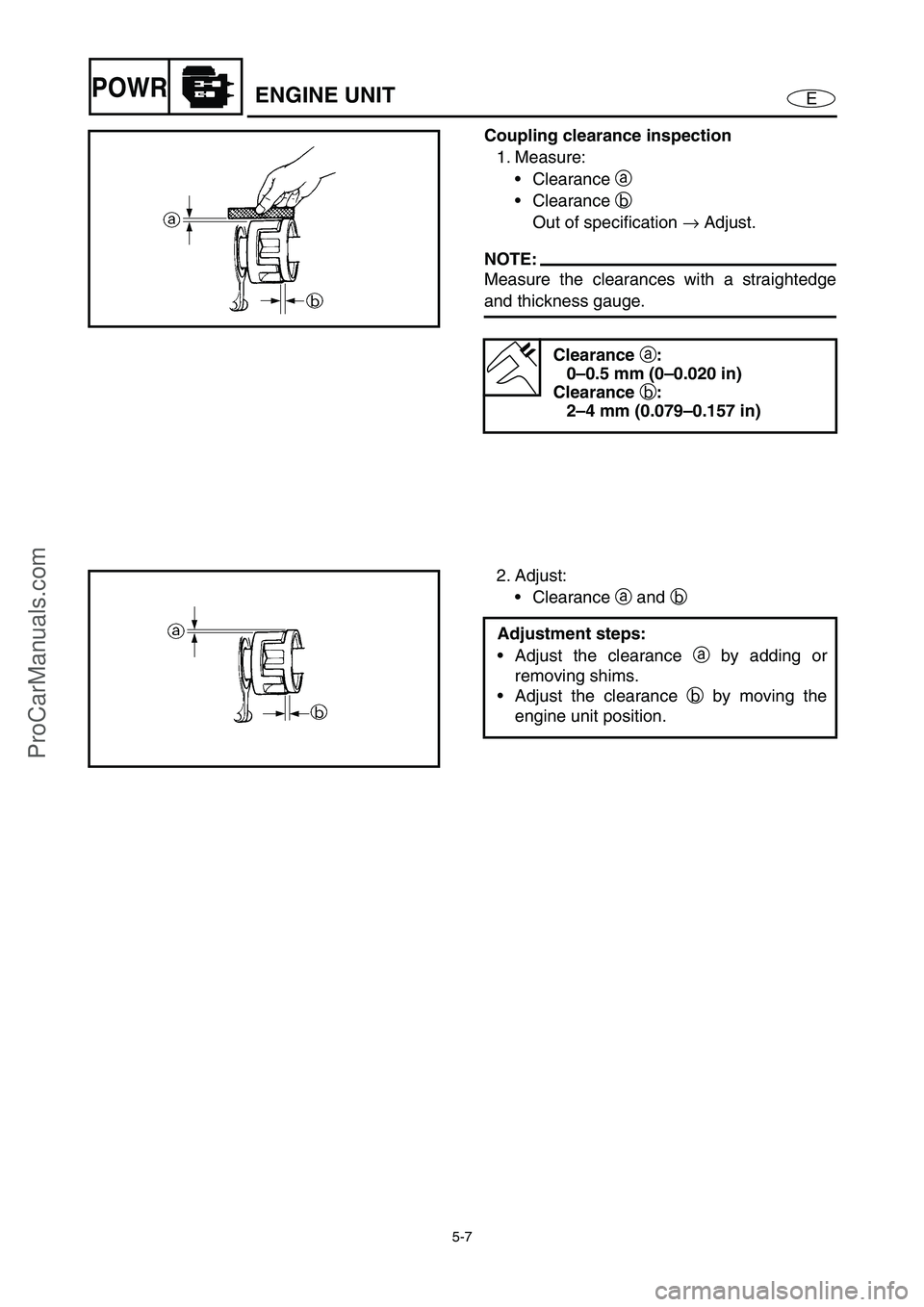
5-7
EPOWRENGINE UNIT
Coupling clearance inspection
1. Measure:
Clearance a
Clearance b
Out of specification →
Adjust.
NOTE:
Measure the clearances with a straightedge
and thickness gauge.
Clearance
a:
0–0.5 mm (0–0.020 in)
Clearance
b:
2–4 mm (0.079–0.157 in)
2. Adjust:
Clearance a
and b
Adjustment steps:
Adjust the clearance a
by adding or
removing shims.
Adjust the clearance b
by moving the
engine unit position.
ProCarManuals.com