light ASTON MARTIN V8 VANTAGE 2010 Owner's Manual
[x] Cancel search | Manufacturer: ASTON MARTIN, Model Year: 2010, Model line: V8 VANTAGE, Model: ASTON MARTIN V8 VANTAGE 2010Pages: 947, PDF Size: 43.21 MB
Page 157 of 947
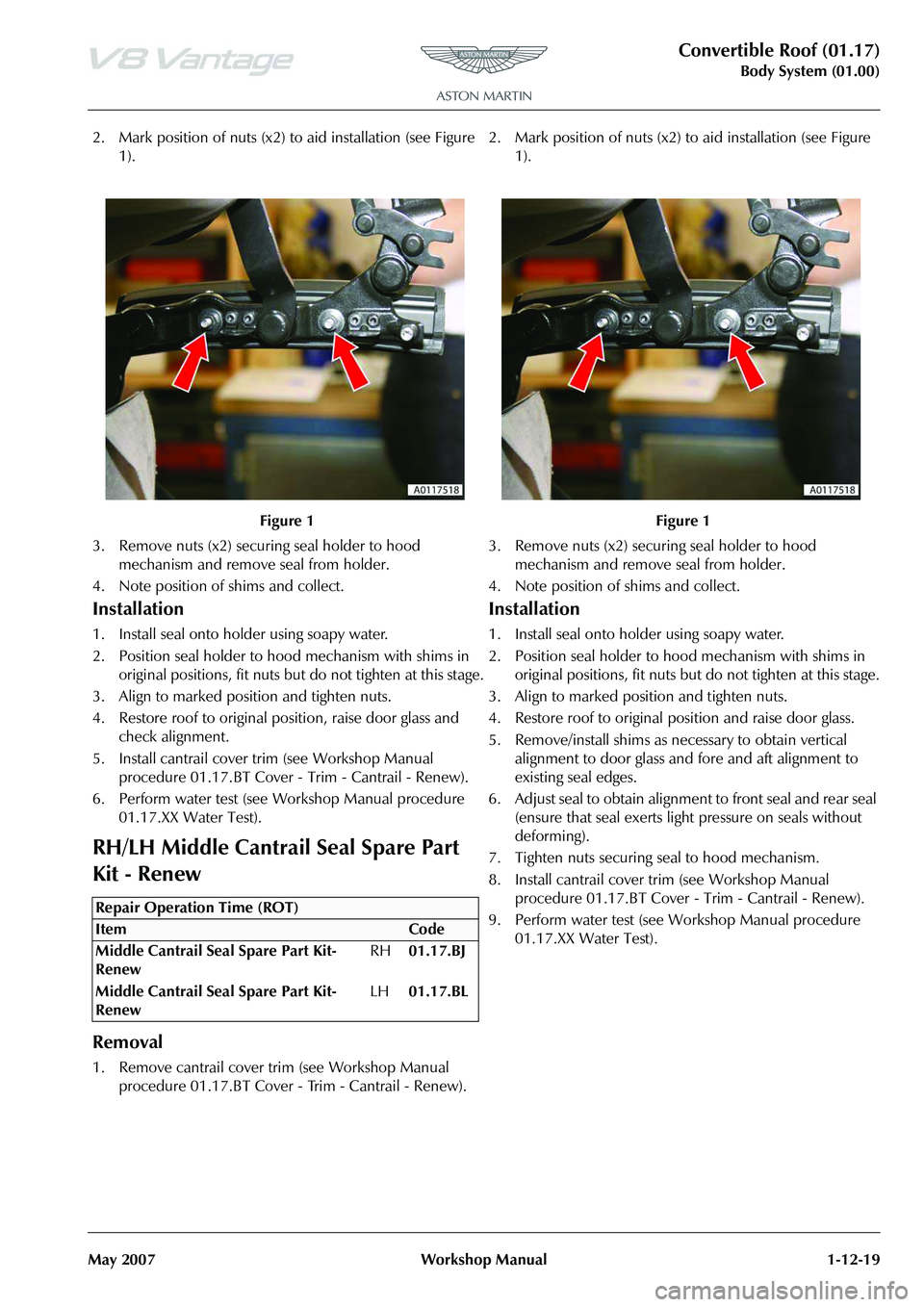
Convertible Roof (01.17)
Body System (01.00)
May 2007 Workshop Manual 1-12-19
2. Mark position of nuts (x2) to aid installation (see Figure
1).
3. Remove nuts (x2) securing seal holder to hood mechanism and remove seal from holder.
4. Note position of shims and collect.
Installation
1. Install seal onto holder using soapy water.
2. Position seal holder to hood mechanism with shims in original positions, fit nuts but do not tighten at this stage.
3. Align to marked position and tighten nuts.
4. Restore roof to original position, raise door glass and check alignment.
5. Install cantrail cover tr im (see Workshop Manual
procedure 01.17.BT Cover - Trim - Cantrail - Renew).
6. Perform water test (see Workshop Manual procedure 01.17.XX Water Test).
RH/LH Middle Cantrail Seal Spare Part
Kit - Renew
Removal
1. Remove cantrail cover trim (see Workshop Manual procedure 01.17.BT Cover - Trim - Cantrail - Renew). 2. Mark position of nuts (x2) to aid installation (see Figure
1).
3. Remove nuts (x2) securing seal holder to hood mechanism and remove seal from holder.
4. Note position of shims and collect.
Installation
1. Install seal onto holder using soapy water.
2. Position seal holder to hood mechanism with shims in original positions, fit nuts bu t do not tighten at this stage.
3. Align to marked position and tighten nuts.
4. Restore roof to original position and raise door glass.
5. Remove/install shims as nece ssary to obtain vertical
alignment to door glass and fore and aft alignment to
existing seal edges.
6. Adjust seal to obtain alignment to front seal and rear seal (ensure that seal exerts light pressure on seals without
deforming).
7. Tighten nuts securing seal to hood mechanism.
8. Install cantrail cover trim (see Workshop Manual procedure 01.17.BT Cover - Trim - Cantrail - Renew).
9. Perform water test (see Workshop Manual procedure 01.17.XX Water Test).
Figure 1
Repair Operation Time (ROT)
Figure 1
Page 183 of 947
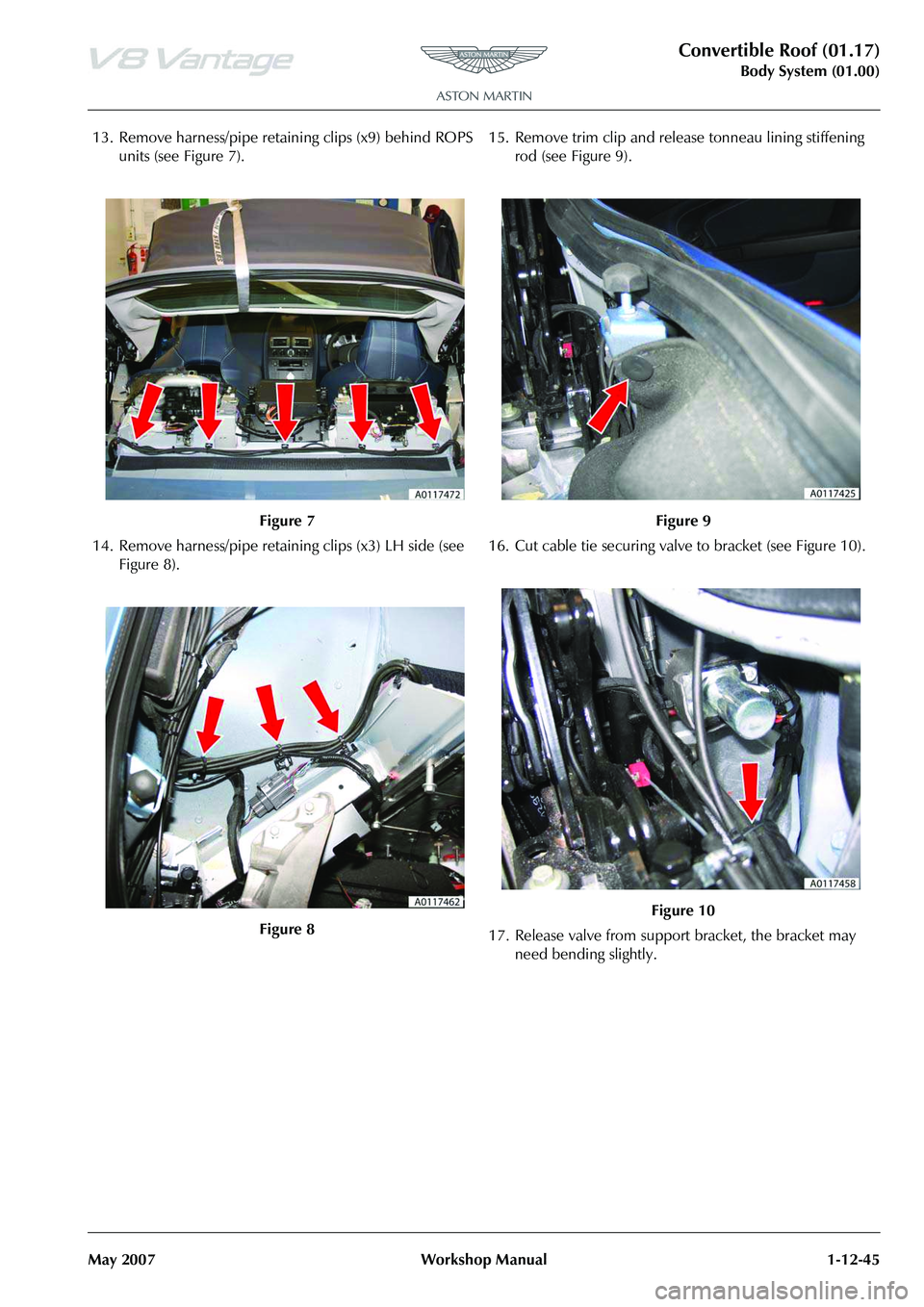
Convertible Roof (01.17)
Body System (01.00)
May 2007 Workshop Manual 1-12-45
13. Remove harness/pipe retain ing clips (x9) behind ROPS
units (see Figure 7).
14. Remove harness/pipe retaining clips (x3) LH side (see Figure 8). 15. Remove trim clip and releas
e tonneau lining stiffening
rod (see Figure 9).
16. Cut cable tie securing valv e to bracket (see Figure 10).
17. Release valve from support bracket, the bracket may need bending slightly.
Figure 7
Figure 8
Figure 9
Figure 10
Page 190 of 947
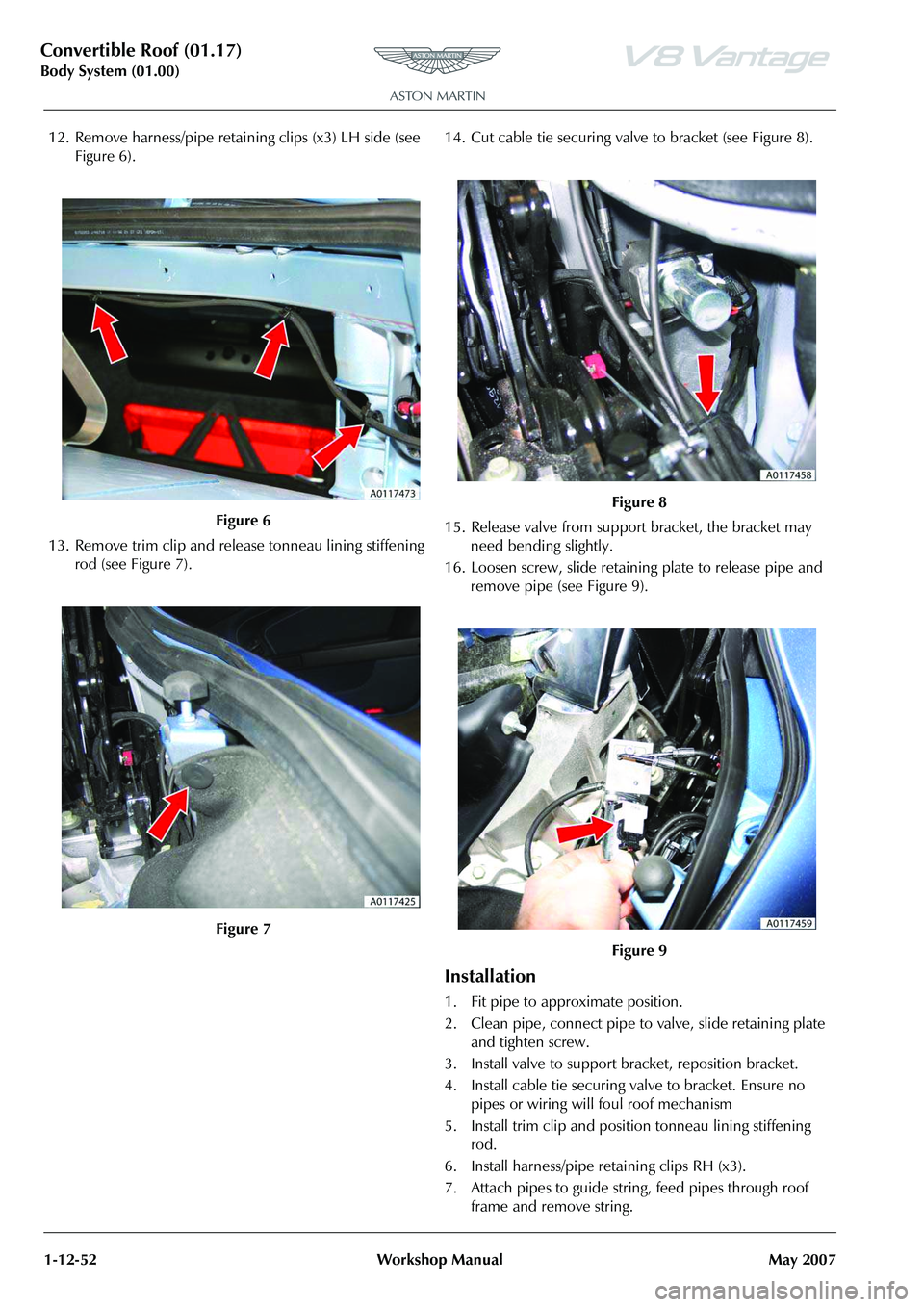
Convertible Roof (01.17)
Body System (01.00)1-12-52 Workshop Manual May 2007
12. Remove harness/pipe retaining clips (x3) LH side (see Figure 6).
13. Remove trim clip and releas e tonneau lining stiffening
rod (see Figure 7). 14. Cut cable tie securing valve to bracket (see Figure 8).
15. Release valve from support bracket, the bracket may
need bending slightly.
16. Loosen screw, slide retaining plate to release pipe and remove pipe (see Figure 9).
Installation
1. Fit pipe to approximate position.
2. Clean pipe, connect pipe to valve, slide retaining plate
and tighten screw.
3. Install valve to support bracket, reposition bracket.
4. Install cable tie securing valve to bracket. Ensure no pipes or wiring will foul roof mechanism
5. Install trim clip and position tonneau lining stiffening rod.
6. Install harness/pipe retaining clips RH (x3).
7. Attach pipes to guide string, feed pipes through roof frame and remove string.
Figure 6
Figure 7
Figure 8
Figure 9
Page 202 of 947
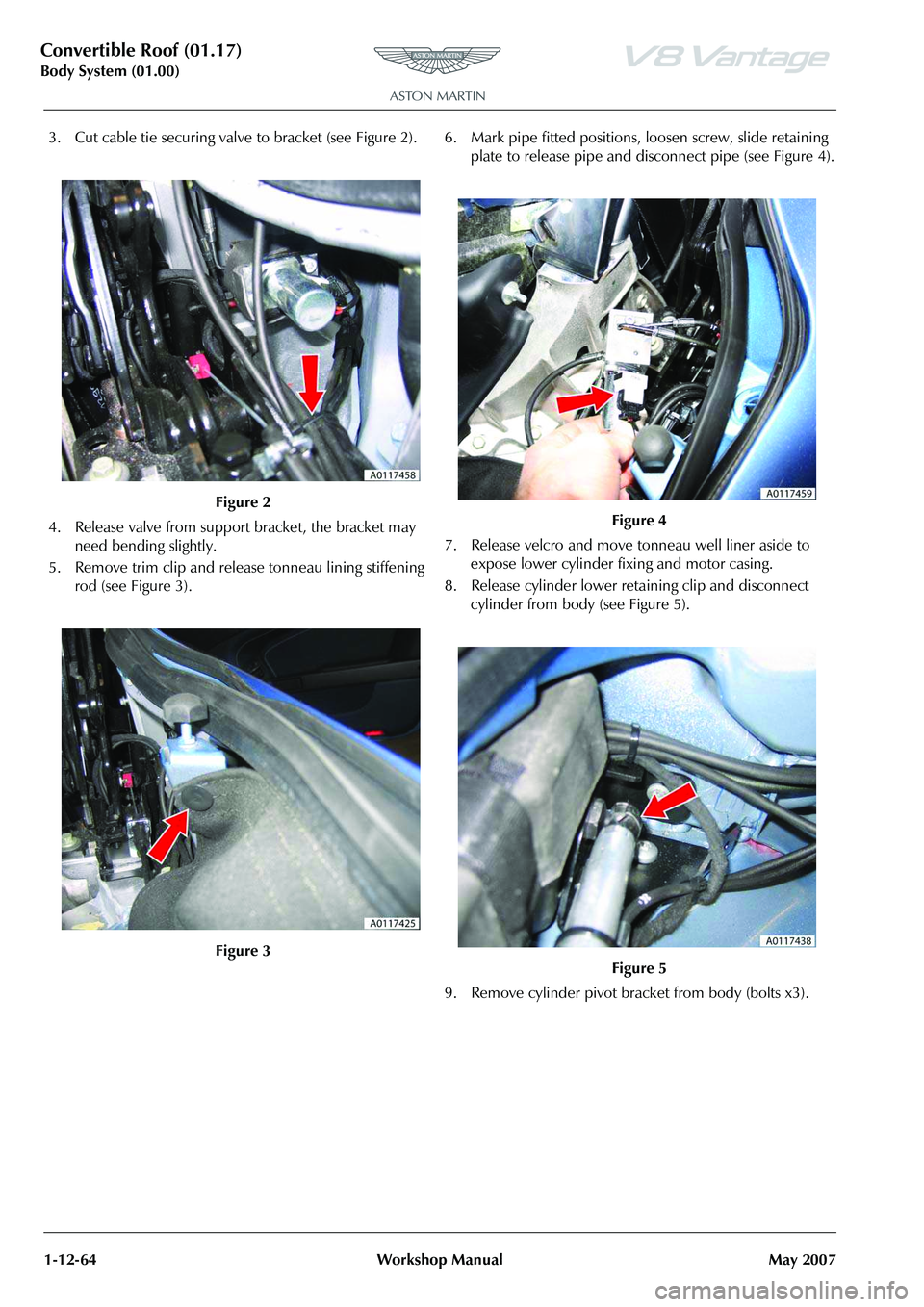
Convertible Roof (01.17)
Body System (01.00)1-12-64 Workshop Manual May 2007
3. Cut cable tie securing valve to bracket (see Figure 2).
4. Release valve from support bracket, the bracket may need bending slightly.
5. Remove trim clip and releas e tonneau lining stiffening
rod (see Figure 3). 6. Mark pipe fitted positions, loosen screw, slide retaining
plate to release pipe and disc onnect pipe (see Figure 4).
7. Release velcro and move to nneau well liner aside to
expose lower cylinder fixing and motor casing.
8. Release cylinder lower retaining clip and disconnect cylinder from body (see Figure 5).
9. Remove cylinder pivot bracket from body (bolts x3).
Figure 2
Figure 3
Figure 4
Figure 5
Page 211 of 947
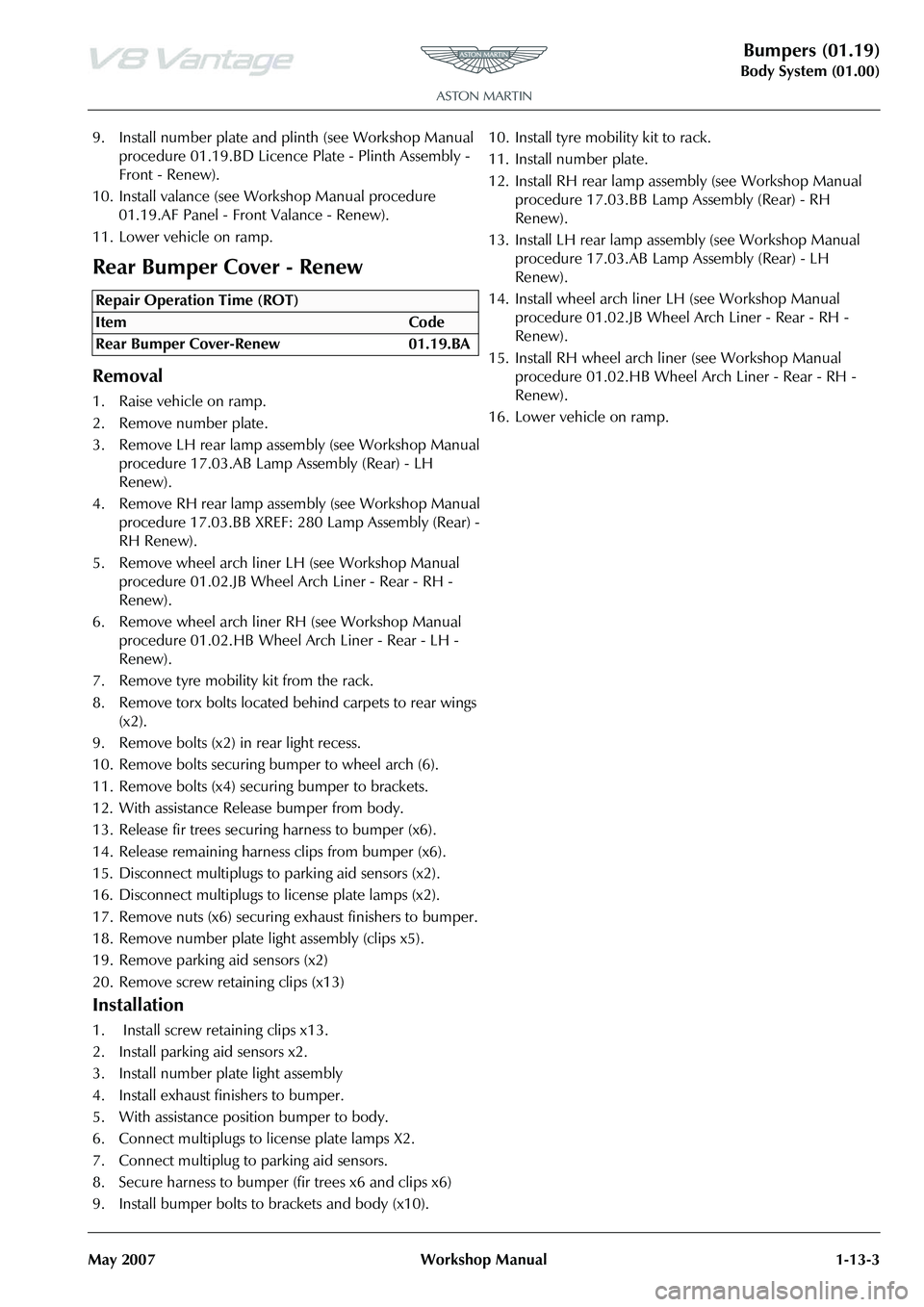
Bumpers (01.19)
Body System (01.00)
May 2007 Workshop Manual 1-13-3
9. Install number plate and plinth (see Workshop Manual procedure 01.19.BD Licence Plate - Plinth Assembly -
Front - Renew).
10. Install valance (see Workshop Manual procedure 01.19.AF Panel - Front Valance - Renew).
11. Lower vehicle on ramp.
Rear Bumper Cover - Renew
Removal
1. Raise vehicle on ramp.
2. Remove number plate.
3. Remove LH rear lamp assembly (see Workshop Manual procedure 17.03.AB Lamp Assembly (Rear) - LH
Renew).
4. Remove RH rear lamp assembly (see Workshop Manual procedure 17.03.BB XREF: 280 Lamp Assembly (Rear) -
RH Renew).
5. Remove wheel arch liner LH (see Workshop Manual procedure 01.02.JB Wheel Arch Liner - Rear - RH -
Renew).
6. Remove wheel arch liner RH (see Workshop Manual procedure 01.02.HB Wheel Arch Liner - Rear - LH -
Renew).
7. Remove tyre mobility kit from the rack.
8. Remove torx bolts located behind carpets to rear wings (x2).
9. Remove bolts (x2) in rear light recess.
10. Remove bolts securing bumper to wheel arch (6).
11. Remove bolts (x4) securing bumper to brackets.
12. With assistance Release bumper from body.
13. Release fir trees securing harness to bumper (x6).
14. Release remaining harness clips from bumper (x6).
15. Disconnect multiplugs to parking aid sensors (x2).
16. Disconnect multiplugs to license plate lamps (x2).
17. Remove nuts (x6) securing exhaust finishers to bumper.
18. Remove number plate light assembly (clips x5).
19. Remove parking aid sensors (x2)
20. Remove screw retaining clips (x13)
Installation
1. Install screw retaining clips x13.
2. Install parking aid sensors x2.
3. Install number pl ate light assembly
4. Install exhaust finishers to bumper.
5. With assistance position bumper to body.
6. Connect multiplugs to license plate lamps X2.
7. Connect multiplug to parking aid sensors.
8. Secure harness to bumper (f ir trees x6 and clips x6)
9. Install bumper bolts to brackets and body (x10). 10. Install tyre mobility kit to rack.
11. Install number plate.
12. Install RH rear lamp asse
mbly (see Workshop Manual
procedure 17.03.BB Lamp Assembly (Rear) - RH
Renew).
13. Install LH rear lamp assembly (see Workshop Manual procedure 17.03.AB Lamp Assembly (Rear) - LH
Renew).
14. Install wheel arch liner LH (see Workshop Manual procedure 01.02.JB Wheel Arch Liner - Rear - RH -
Renew).
15. Install RH wheel arch li ner (see Workshop Manual
procedure 01.02.HB Wheel Arch Liner - Rear - RH -
Renew).
16. Lower vehicle on ramp.
Repair Operation Time (ROT)
Page 240 of 947
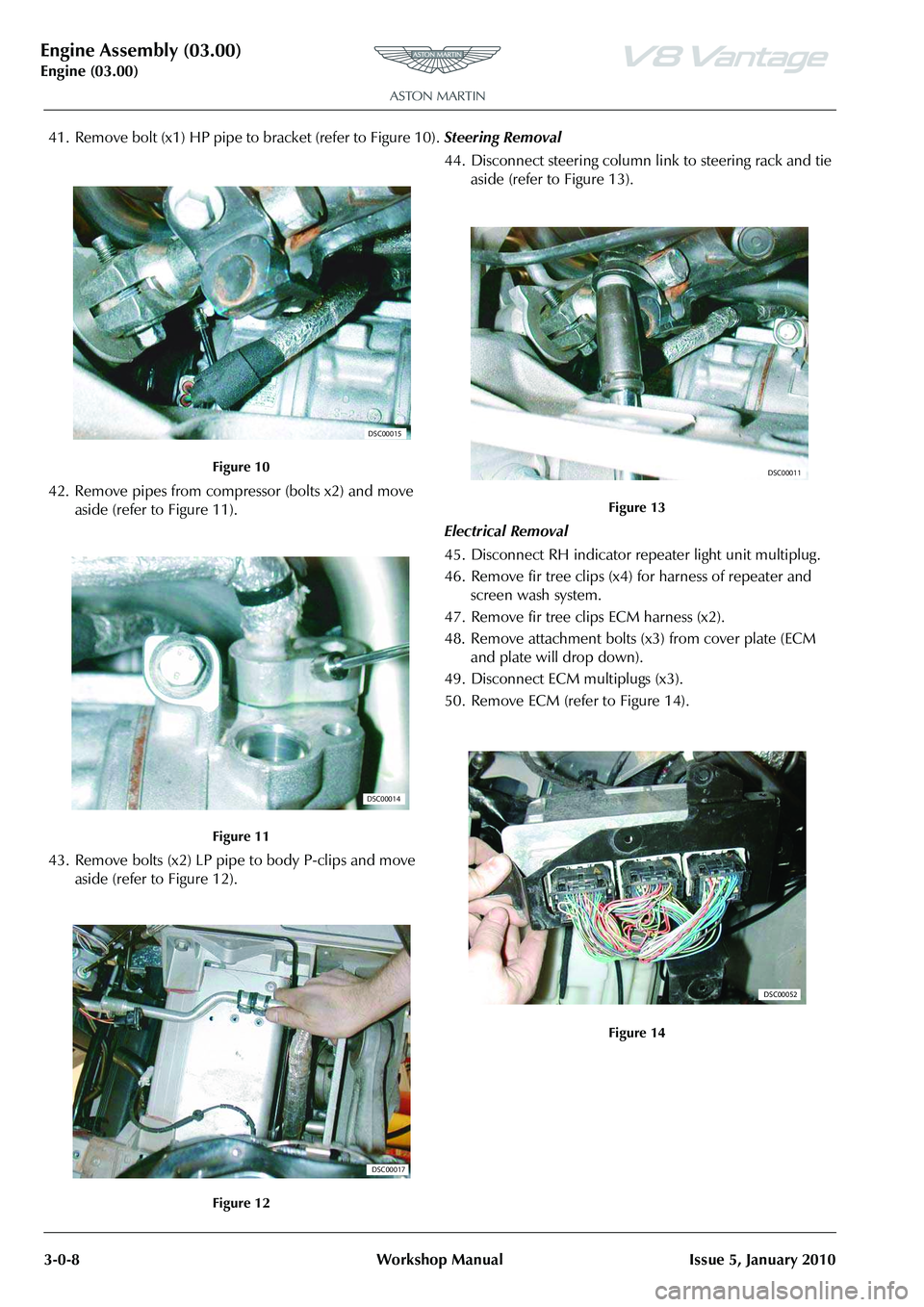
Engine Assembly (03.00)
Engine (03.00)3-0-8 Workshop Manual Issue 5, January 2010
41. Remove bolt (x1) HP pipe to bracket (refer to Figure 10).
42. Remove pipes from compressor (bolts x2) and move aside (refer to Figure 11).
43. Remove bolts (x2) LP pipe to body P-clips and move
aside (refer to Figure 12). Steering Removal
44. Disconnect steering column link to steering rack and tie
aside (refer to Figure 13).
Electrical Removal
45. Disconnect RH indicator repeater light unit multiplug.
46. Remove fir tree clips (x4) for harness of repeater and screen wash system.
47. Remove fir tree clips ECM harness (x2).
48. Remove attachment bolts (x3) from cover plate (ECM and plate will drop down).
49. Disconnect ECM multiplugs (x3).
50. Remove ECM (refer to Figure 14).
Figure 10
Figure 11
Figure 12
$ 3 #
$ 3 #
$ 3 #
Figure 13
Figure 14
$ 3 #
$ 3 #
Page 246 of 947
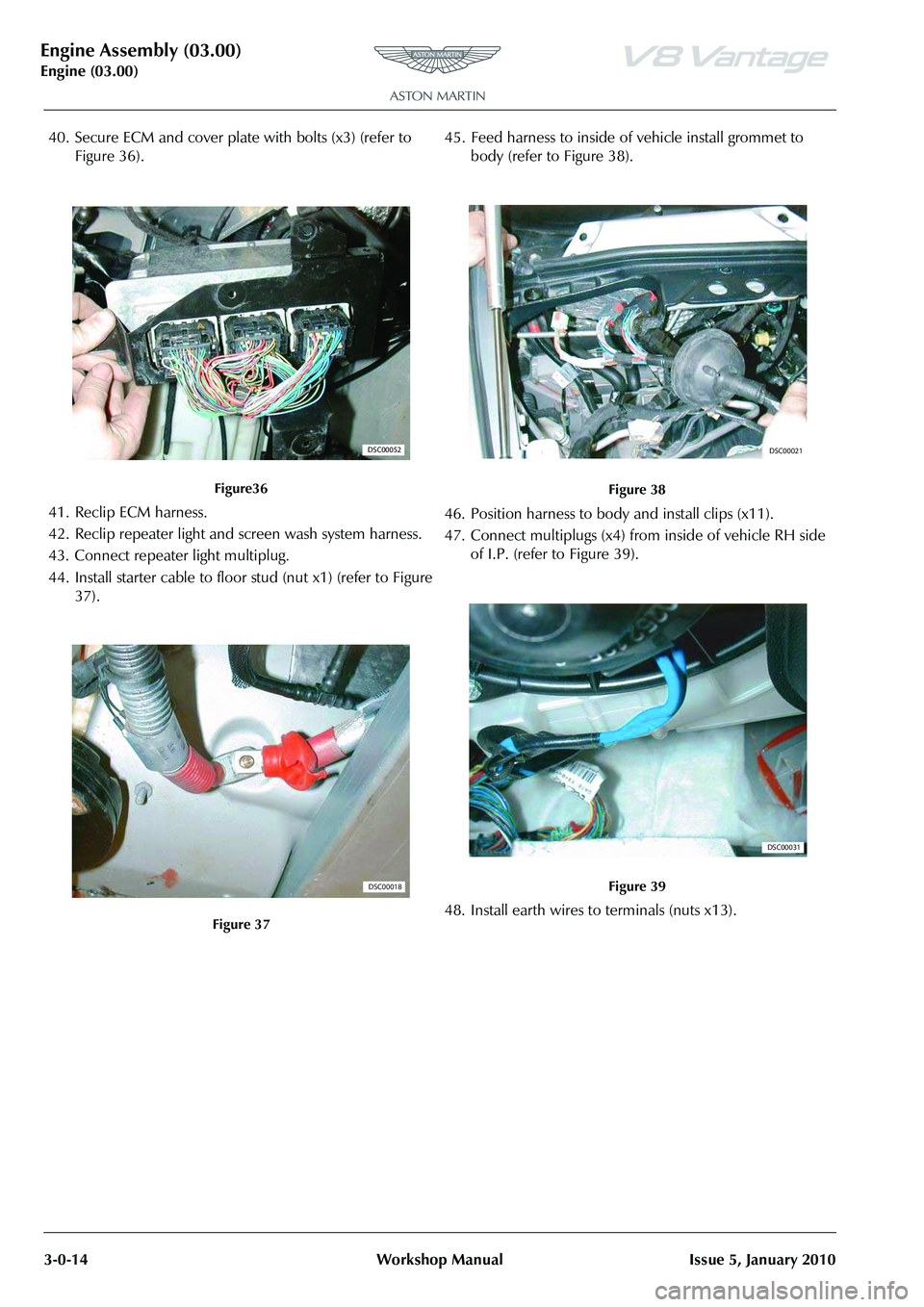
Engine Assembly (03.00)
Engine (03.00)3-0-14 Workshop Manual Issue 5, January 2010
40. Secure ECM and cover plate with bolts (x3) (refer to Figure 36).
41. Reclip ECM harness.
42. Reclip repeater light and screen wash system harness.
43. Connect repeater light multiplug.
44. Install starter cable to floor st ud (nut x1) (refer to Figure
37). 45. Feed harness to inside of vehicle install grommet to
body (refer to Figure 38).
46. Position harness to body and install clips (x11).
47. Connect multiplugs (x4) from inside of vehicle RH side of I.P. (refer to Figure 39).
48. Install earth wires to terminals (nuts x13).
Figure36
Figure 37
$ 3 #
$ 3 #
Figure 38
Figure 39
$ 3 #
$ 3 #
Page 282 of 947
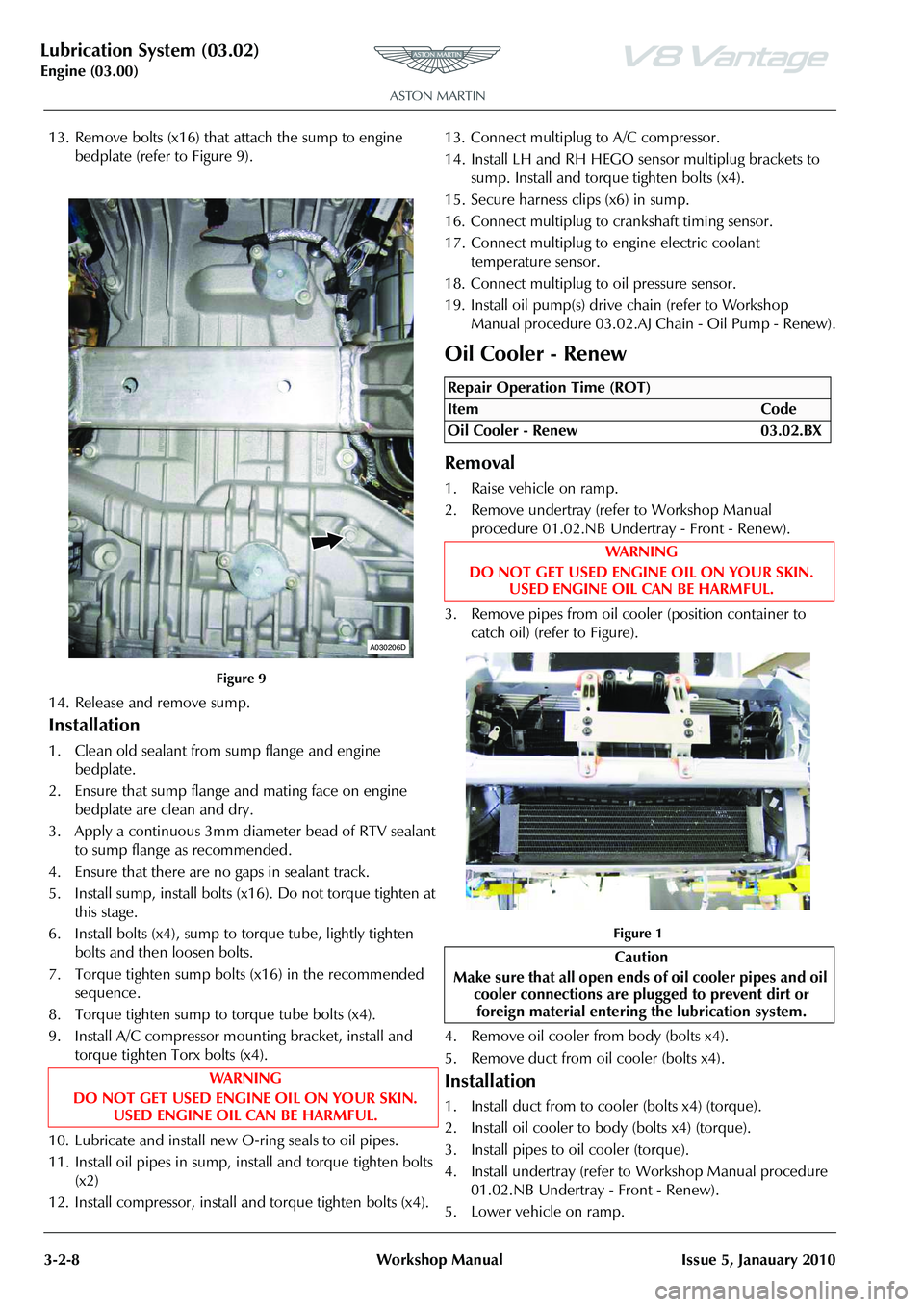
Lubrication System (03.02)
Engine (03.00)3-2-8 Workshop Manual Issue 5, Janauary 2010
13. Remove bolts (x16) that attach the sump to engine bedplate (refer to Figure 9).
14. Release and remove sump.
Installation
1. Clean old sealant from sump flange and engine bedplate.
2. Ensure that sump flange and mating face on engine bedplate are clean and dry.
3. Apply a continuous 3mm diameter bead of RTV sealant to sump flange as recommended.
4. Ensure that there are no gaps in sealant track.
5. Install sump, install bolts (x16). Do not torque tighten at this stage.
6. Install bolts (x4), sump to torque tube, lightly tighten bolts and then loosen bolts.
7. Torque tighten sump bolts (x16) in the recommended sequence.
8. Torque tighten sump to torque tube bolts (x4).
9. Install A/C compressor mounting bracket, install and torque tighten Torx bolts (x4).
10. Lubricate and install new O-ring seals to oil pipes.
11. Install oil pipes in sump, install and torque tighten bolts (x2)
12. Install compressor, install and torque tighten bolts (x4). 13. Connect multiplug to A/C compressor.
14. Install LH and RH HEGO
sensor multiplug brackets to
sump. Install and torque tighten bolts (x4).
15. Secure harness clips (x6) in sump.
16. Connect multiplug to crankshaft timing sensor.
17. Connect multiplug to engine electric coolant temperature sensor.
18. Connect multiplug to oil pressure sensor.
19. Install oil pump(s) drive chain (refer to Workshop
Manual procedure 03.02.AJ Chain - Oil Pump - Renew).
Oil Cooler - Renew
Removal
1. Raise vehicle on ramp.
2. Remove undertray (refer to Workshop Manual procedure 01.02.NB Undertray - Front - Renew).
3. Remove pipes from oil cooler (position container to catch oil) (refer to Figure).
Figure 1
4. Remove oil cooler from body (bolts x4).
5. Remove duct from oil cooler (bolts x4).
Installation
1. Install duct from to cooler (bolts x4) (torque).
2. Install oil cooler to body (bolts x4) (torque).
3. Install pipes to oil cooler (torque).
4. Install undertray (refer to Workshop Manual procedure 01.02.NB Undertray - Front - Renew).
5. Lower vehicle on ramp.
Figure 9
WAR NI NG
DO NOT GET USED ENGINE OIL ON YOUR SKIN. USED ENGINE OIL CAN BE HARMFUL.
A030206D
Repair Operation Time (ROT)
ItemCode
Oil Cooler - Renew 03.02.BX
WAR NI NG
DO NOT GET USED ENGINE OIL ON YOUR SKIN. USED ENGINE OIL CAN BE HARMFUL.
Caution
Make sure that all open ends of oil cooler pipes and oil cooler connections are plugged to prevent dirt or
foreign material entering the lubrication system.
Page 307 of 947
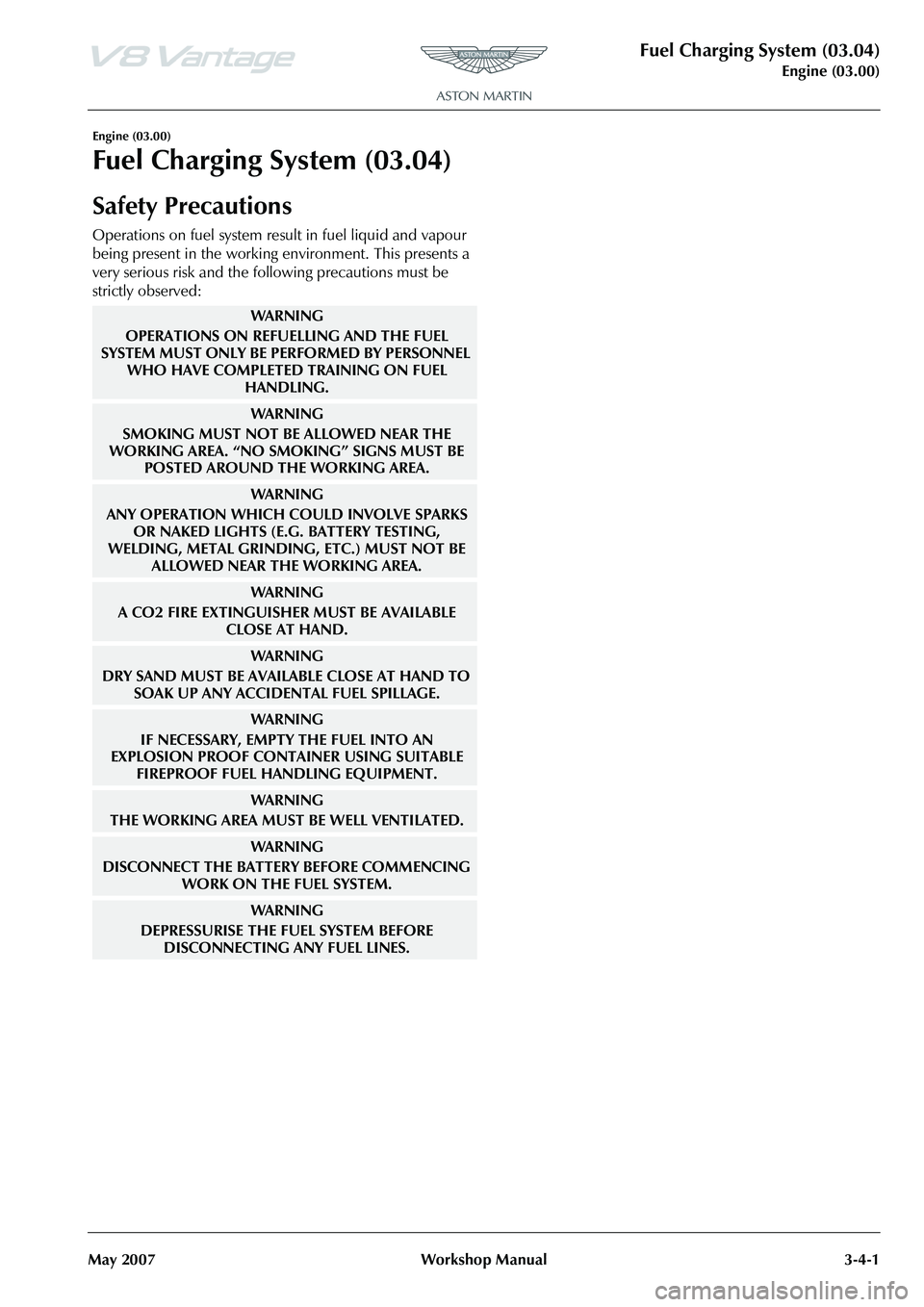
Fuel Charging System (03.04)
Engine (03.00)
May 2007 Workshop Manual 3-4-1
Engine (03.00)
Fuel Charging System (03.04)
Safety Precautions
Operations on fuel system result in fuel liquid and vapour
being present in the working environment. This presents a
very serious risk and the following precautions must be
strictly observed:
WAR NI NG
OPERATIONS ON REFUELLING AND THE FUEL
SYSTEM MUST ONLY BE PERFORMED BY PERSONNEL WHO HAVE COMPLETED TRAINING ON FUEL HANDLING.
WAR NI NG
SMOKING MUST NOT BE ALLOWED NEAR THE
WORKING AREA. “NO SMOKING” SIGNS MUST BE POSTED AROUND THE WORKING AREA.
WAR NI NG
ANY OPERATION WHICH COULD INVOLVE SPARKS OR NAKED LIGHTS (E.G. BATTERY TESTING,
WELDING, METAL GRINDING, ETC.) MUST NOT BE ALLOWED NEAR THE WORKING AREA.
WAR NI NG
A CO2 FIRE EXTINGUISHER MUST BE AVAILABLE CLOSE AT HAND.
WAR NI NG
DRY SAND MUST BE AVAILABLE CLOSE AT HAND TO SOAK UP ANY ACCIDENTAL FUEL SPILLAGE.
WAR NI NG
IF NECESSARY, EMPTY THE FUEL INTO AN
EXPLOSION PROOF CONTAINER USING SUITABLE
FIREPROOF FUEL HANDLING EQUIPMENT.
WAR NI NG
THE WORKING AREA MUST BE WELL VENTILATED.
WAR NI NG
DISCONNECT THE BATTERY BEFORE COMMENCING WORK ON THE FUEL SYSTEM.
WAR NI NG
DEPRESSURISE THE FUEL SYSTEM BEFORE DISCONNECTING ANY FUEL LINES.
Page 376 of 947

Power Conversion (03.11)
Engine (03.00)3-11-4 Workshop Manual May 2007
10. Install crankshaft retaining caps (303-534), install and
lightly tighten bolts (x10) (see Figure 8).
Figure 8
11. Install connecting rod bearing caps (x8), install and torque tighten retaining bolts.
12. Remove bolts securing crankshaft retaining caps (303- 534), remove retaining caps (see Figure 9).
Figure 9
13. Apply a 2mm diameter continuous bead of sealant to cylinder block flange ensuring that there are no gaps in
the sealant.
14. Install engine bedplate to cylinder block, install and torque tighten bolts (x34) in the correct sequence.
15. Remove excess sealant from crankshaft rear oil seal
aperture and front face of cylinder block.
16. Clean windage tray.
17. Install windage tray, install and torque tighten bolts (x8). 18. Ensure that oil seal protector is positioned correctly and
install oil seal onto crankshaft flange.
19. Install tool (303-1189) to crankshaft, position nuts on tool against oil seal.
20. Ensure that oil seal and special are parallel to rear of engine.
21. To install oil seal, tighten nuts alternately on tool (303- 1189) until oil seal correctly seated.
22. Remove special tool from crankshaft.
23. Check that the oil se al is located correctly.
24. Clean flywheel and mating face on crankshaft.
25. Install flywheel, align to dowel on crankshaft flange.
26. Install new bolts (x8), install tool (303-1185) to restrain flywheel. Torque tighten bolts (x8) in the correct
sequence.
27. Clean clutch cover and drive plate.
28. Install clutch assembly on flywheel, align to dowels (x3).
29. Install bolts (x6), install clutch alignment tool, evenly torque tighten bolts (x6) in a diagonal sequence.
Remove clutch alignment tool.
30. Remove bolts (x2), collect tool (303-1185).
31. Install inspection cover, install and torque tighten bolts (x2).
32. Install engine sump (see Workshop Manual procedure 03.02.CN Pan - Oil Sump - Remove and Reseal With
Engine Removed).
Crankshaft Assembly-Renew
Removal
1. Remove bolts (x2), inspection cover to lower crankcase, remove cover.
2. Install tool (303-1185) to restrain flywheel, install and tighten bolts (x2).
3. Remove bolts (x6), clutch cover to flywheel.
4. Release clutch cover from dowels (x3), remove clutch cover, collect drive plate.
5. Remove and discard bolts (x8), flywheel to crankshaft flange.
6. Remove bolts (x2), collect tool (303-1185).
7. Release flywheel from dowel, remove flywheel.
8 . R e m o v e e n g i n e s u mp ( s e e Wo r k s h o p M a n u a l p ro c e d u re 03.02.CN Pan - Oil Sump - Remove and Reseal With
Engine Removed).
Caution
Do not lubricate engine bedplate retaining bolts.
Caution
Tighten engine bedplate retaining bolts in the sequence shown.
Caution
Do not rotate crankshaft until all engine bedplate
retaining bolts are tightened to specification.
Caution
Engine bedplate retaining bolts must be tightened
within twenty minutes of applying sealant.
A0311328
A0311328
Caution
Do not use any lubricant on cr ankshaft oil seals or seal
protectors. Make sure all co mponents are clean and dry.
Repair Operation Time (ROT)
ItemCode
Crankshaft Assembly-Renew 03.11.CF
WAR NI NG
DO NOT GET USED ENGINE OIL ON YOUR SKIN.
USED ENGINE OIL CAN BE HARMFUL.