light ASTON MARTIN V8 VANTAGE 2010 User Guide
[x] Cancel search | Manufacturer: ASTON MARTIN, Model Year: 2010, Model line: V8 VANTAGE, Model: ASTON MARTIN V8 VANTAGE 2010Pages: 947, PDF Size: 43.21 MB
Page 85 of 947
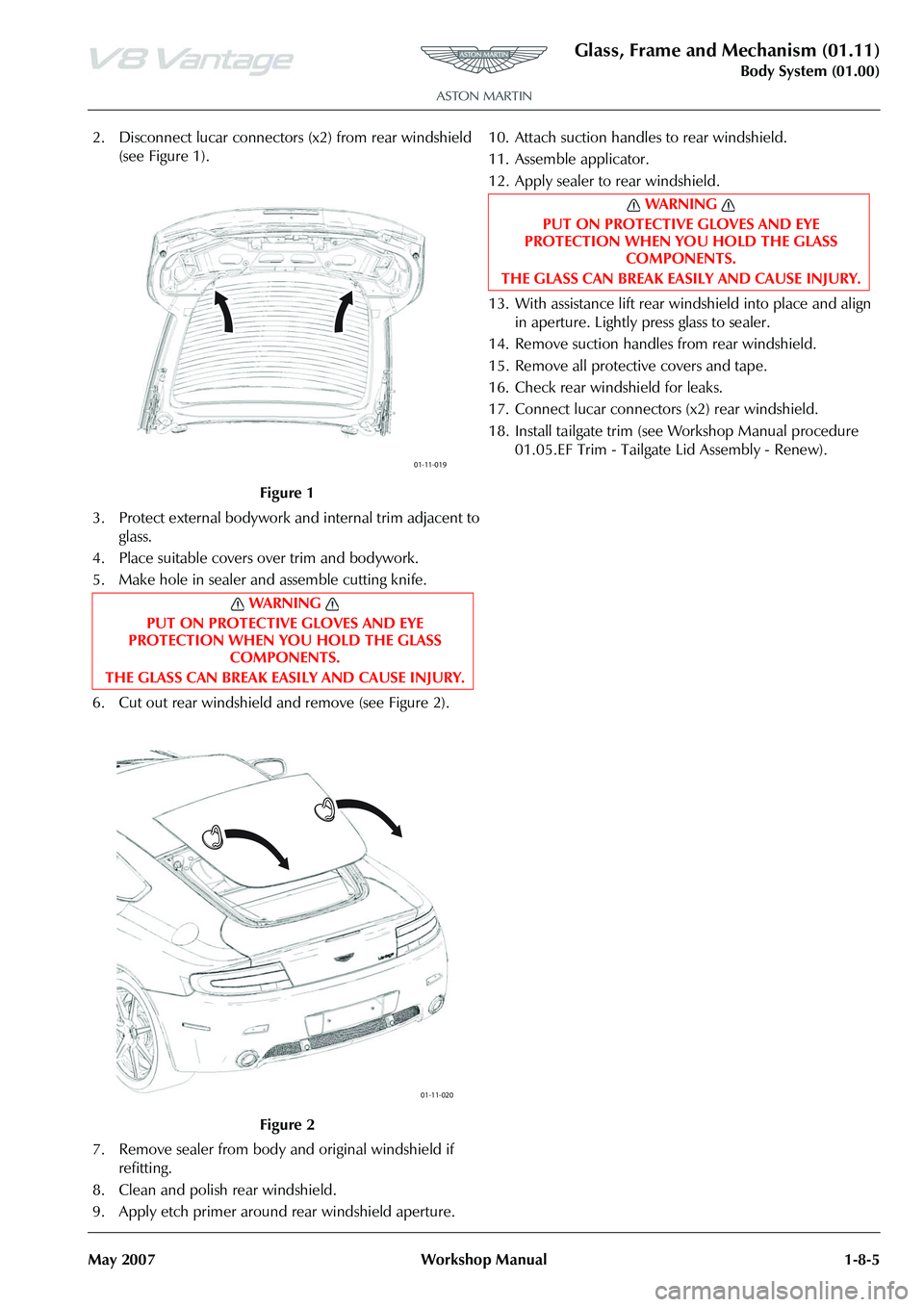
Glass, Frame and Mechanism (01.11)
Body System (01.00)
May 2007 Workshop Manual 1-8-5
2. Disconnect lucar connectors (x2) from rear windshield
(see Figure 1).
3. Protect external bodywork and internal trim adjacent to glass.
4. Place suitable covers over trim and bodywork.
5. Make hole in sealer and assemble cutting knife.
6. Cut out rear windshield and remove (see Figure 2).
7. Remove sealer from body and original windshield if refitting.
8. Clean and polish rear windshield.
9. Apply etch primer around rear windshield aperture. 10. Attach suction handles to rear windshield.
11. Assemble applicator.
12. Apply sealer to rear windshield.
13. With assistance lift rear windshield into place and align
in aperture. Lightly press glass to sealer.
14. Remove suction handles from rear windshield.
15. Remove all protective covers and tape.
16. Check rear windshield for leaks.
17. Connect lucar connectors (x2) rear windshield.
18. Install tailgate trim (see Workshop Manual procedure 01.05.EF Trim - Tailgate Lid Assembly - Renew).
Figure 1
WAR NI N G
PUT ON PROTECTIVE GLOVES AND EYE
PROTECTION WHEN YOU HOLD THE GLASS COMPONENTS.
THE GLASS CAN BREAK EASILY AND CAUSE INJURY.
Figure 2
WA R N I N G
PUT ON PROTECTIVE GLOVES AND EYE
PROTECTION WHEN YO U HOLD THE GLASS
COMPONENTS.
THE GLASS CAN BREAK EASILY AND CAUSE INJURY.
Page 86 of 947
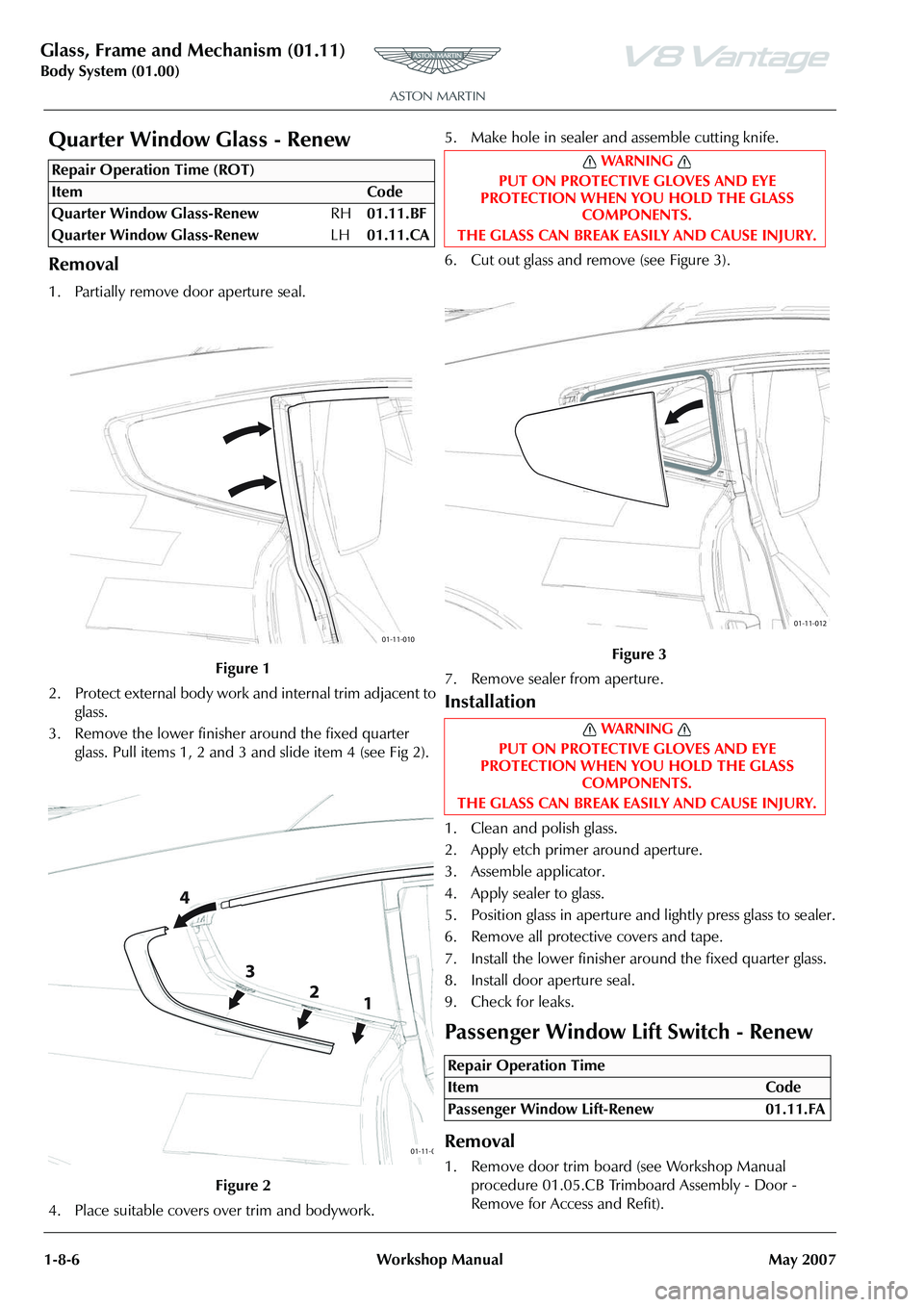
Glass, Frame and Mechanism (01.11)
Body System (01.00)1-8-6 Workshop Manual May 2007
Quarter Window Glass - Renew
Removal
1. Partially remove door aperture seal.
2. Protect external body work and internal trim adjacent to glass.
3. Remove the lower finisher around the fixed quarter
glass. Pull items 1, 2 and 3 and slide item 4 (see Fig 2).
4. Place suitable covers over trim and bodywork. 5. Make hole in sealer and assemble cutting knife.
6. Cut out glass and remove (see Figure 3).
7. Remove sealer from aperture.
Installation
1. Clean and polish glass.
2. Apply etch primer around aperture.
3. Assemble applicator.
4. Apply sealer to glass.
5. Position glass in aperture and lightly press glass to sealer.
6. Remove all protective covers and tape.
7. Install the lower finisher around the fixed quarter glass.
8. Install door aperture seal.
9. Check for leaks.
Passenger Window Lift Switch - Renew
Removal
1. Remove door trim board (see Workshop Manual
procedure 01.05.CB Trimboard Assembly - Door -
Remove for Access and Refit).
Repair Operation Time (ROT)
WAR NI NG
PUT ON PROTECTIVE GLOVES AND EYE
PROTECTION WHEN YOU HOLD THE GLASS COMPONENTS.
THE GLASS CAN BREAK EASILY AND CAUSE INJURY.
Figure 3
WAR NI NG
PUT ON PROTECTIVE GLOVES AND EYE
PROTECTION WHEN YOU HOLD THE GLASS COMPONENTS.
THE GLASS CAN BREAK EASILY AND CAUSE INJURY.
Repair Operation Time
ItemCode
Passenger Window Lift-Renew 01.11.FA
Page 95 of 947

Instrument Panel (IP) (01.12)
Body System (01.00)
Issue 5, January 2010 Workshop Manual 1-9-7
Instrument Centre Panel Assembly -
Renew
1. Remove instrument panel bezel assembly (see Workshop Manual procedure 01.12.AV Bezel Assembly
- Instrument Panel - Remove for Access and Refit).
2. Remove console panel assembly (see Workshop Manual procedure 01.12.DB Panel Assembly Console - Renew).
3. Remove instrument cluster hood (6 clips)
4. Remove passenger upper ou ter panel assembly (see
Workshop Manual procedure 01.12.AE Panel Assembly
- IP - Upper - Passenger - Renew).
5. Remove passenger panel assembly (4 clips and 4 screws)
6. Remove driver's upper inner panel assembly (5 clips)
7. Remove driver's upper outer panel assembly (4 clips)
8. Remove driver's panel assembly (4 clips and 3 screws)
9. Remove receiver and audio media system panel screws (x4), disconnect multiplugs (x12).
10. Pull back carpet and disconnect seat adjust switch multiplugs (x6), release harness clip (x2)
11. Remove instrument centre panel assembly
12. Remove seat adjust switches (screws x8).
Installation
1. Install seat adjust switches (screws x8).
2. Install instrument centre panel assembly
3. Connect seat adjust switch multiplugs (x6), install harness clip (x2) and carpet.
4. Install receiver and audio media systems panel (12 multiplugs and 4 screws)
5. Install driver's panel assembly (4 clips and 3 screws)
6. Install driver's upper oute r panel assembly (4 clips)
7. Install driver's upper inne r panel assembly (5 clips)
8. Install passenger's panel assembly (4 clips and 4 screws)
9. Install passenger's upper outer panel assembly (see Workshop Manual procedure 01.12.AE Panel Assembly
- IP - Upper - Passenger - Renew).
10. Install instrument cl uster hood (6 clips)
11. Install console panel asse mbly (see Workshop Manual
procedure 01.12.DB Panel Assembly Console - Renew).
12. Install instrument panel be zel assembly (see Workshop
Manual procedure 01.12.AV Bezel Assembly -
Instrument Panel - Remove for Access and Refit).
Knee Protector - Renew
Removal
1. Remove driver's lower panel assembly (7 clips) and disconnect air temperature pipe.
2. Disconnect footwell light and remove unit from panel.
3. Mark one socket for relocation and remove diagnostic sockets (x2) from panel.
4. Remove pop-rivets (x5), sc rews (x4) and remove panel.
Installation
1. Align knee protector panel in position and secure with
screws (x4).
2. Install pop-rivets (x5).
3. Install diagnostic sockets (x2) (ensure marked socket is in correct location).
4. Install footwell light and reconnect multiplug.
5. Install driver's lower panel assembly (7 clips) and connect air temperature pipe.
Instrument Panel Assembly - Renew
Removal
1. Remove Instrument pane l assembly (see Workshop
Manual procedure 01.12.AB Instrument Panel - Facia
Assembly - Remo ve for Access and Refit).
2. Remove steering column (bolts x4, multiplugs x5).
3. Remove passenger air bag module (screws x4).
4. Remove centre speaker (screws x2) and unclip harness (see Figure 1).
Repair Operation Time (ROT)
Repair Operation Time (ROT)
Repair Operation Time (ROT)
A0112220
Page 96 of 947

Instrument Panel (IP) (01.12)
Body System (01.00)1-9-8 Workshop Manual Issue 5, January 2010
5. Remove lighting switch (screws x3) (see Figure 2).
6. Disconnect Passenger airbag inhibit switch (see Figure
3). 7. Disconnect interior guard switch (see Figure 4).
8. Remove RKE module (screws x2).
9. Remove side demist ducts (see Figure 5).
10. Remove RH footwell lamp (see Figure 6).
Figure 2
Figure 3
A0112221
A0112222
Figure 4
Figure 5
Figure 6
A0112223
A0112225
A0112226A
Page 97 of 947
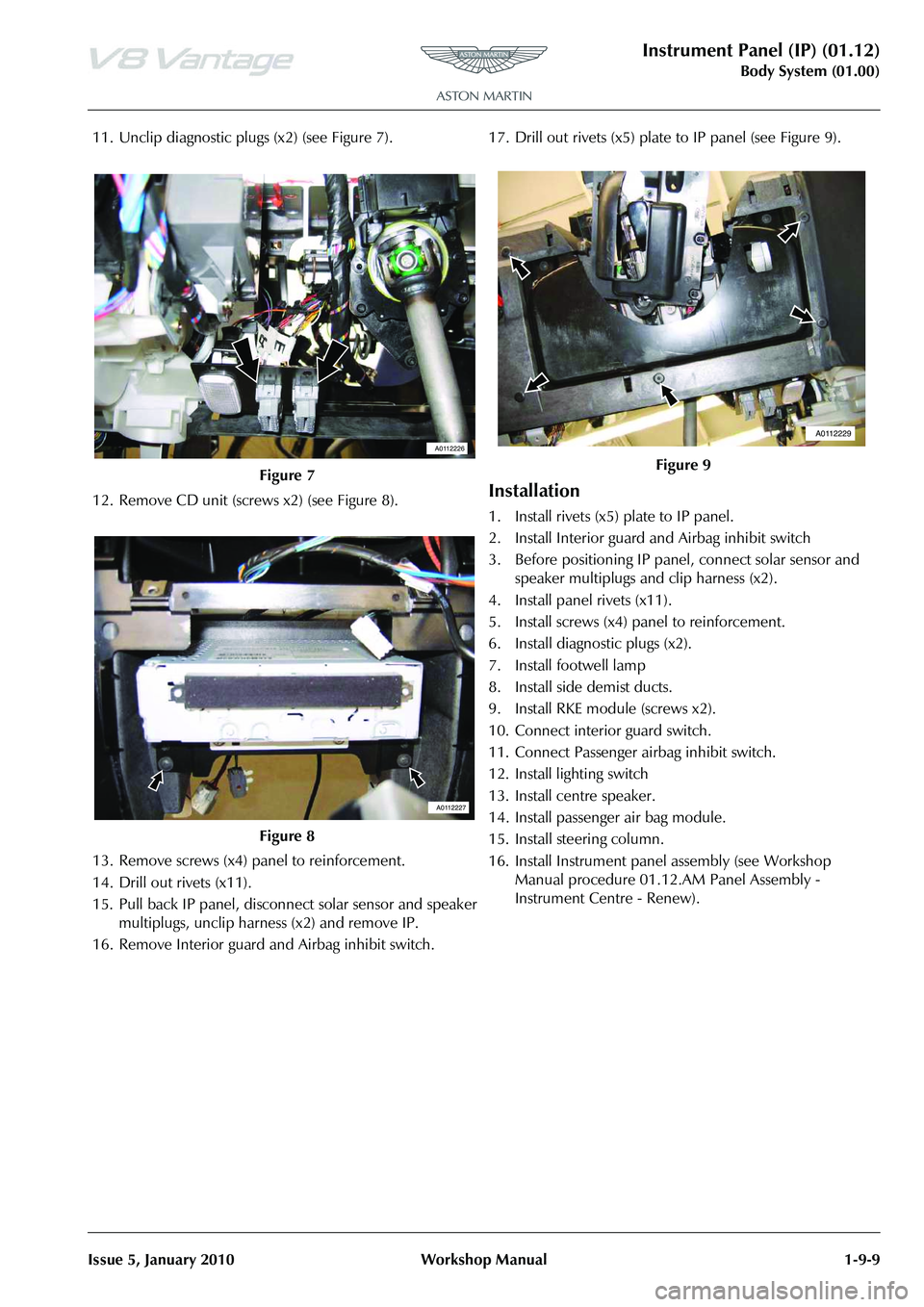
Instrument Panel (IP) (01.12)
Body System (01.00)
Issue 5, January 2010 Workshop Manual 1-9-9
11. Unclip diagnostic plugs (x2) (see Figure 7).
12. Remove CD unit (screws x2) (see Figure 8).
13. Remove screws (x4) panel to reinforcement.
14. Drill out rivets (x11).
15. Pull back IP panel, disconnect solar sensor and speaker multiplugs, unclip harness (x2) and remove IP.
16. Remove Interior guard and Airbag inhibit switch. 17. Drill out rivets (x5) plate
to IP panel (see Figure 9).
Installation
1. Install rivets (x5) plate to IP panel.
2. Install Interior guard and Airbag inhibit switch
3. Before positioning IP panel, connect solar sensor and
speaker multiplugs and clip harness (x2).
4. Install panel rivets (x11).
5. Install screws (x4) panel to reinforcement.
6. Install diagnostic plugs (x2).
7. Install footwell lamp
8. Install side demist ducts.
9. Install RKE module (screws x2).
10. Connect interior guard switch.
11. Connect Passenger airbag inhibit switch.
12. Install lighting switch
13. Install centre speaker.
14. Install passenger air bag module.
15. Install steering column.
16. Install Instrument panel assembly (see Workshop Manual procedure 01.12. AM Panel Assembly -
Instrument Centre - Renew).
Figure 7
Figure 8
A0112226
A0112227
Figure 9
A0112229
Page 121 of 947
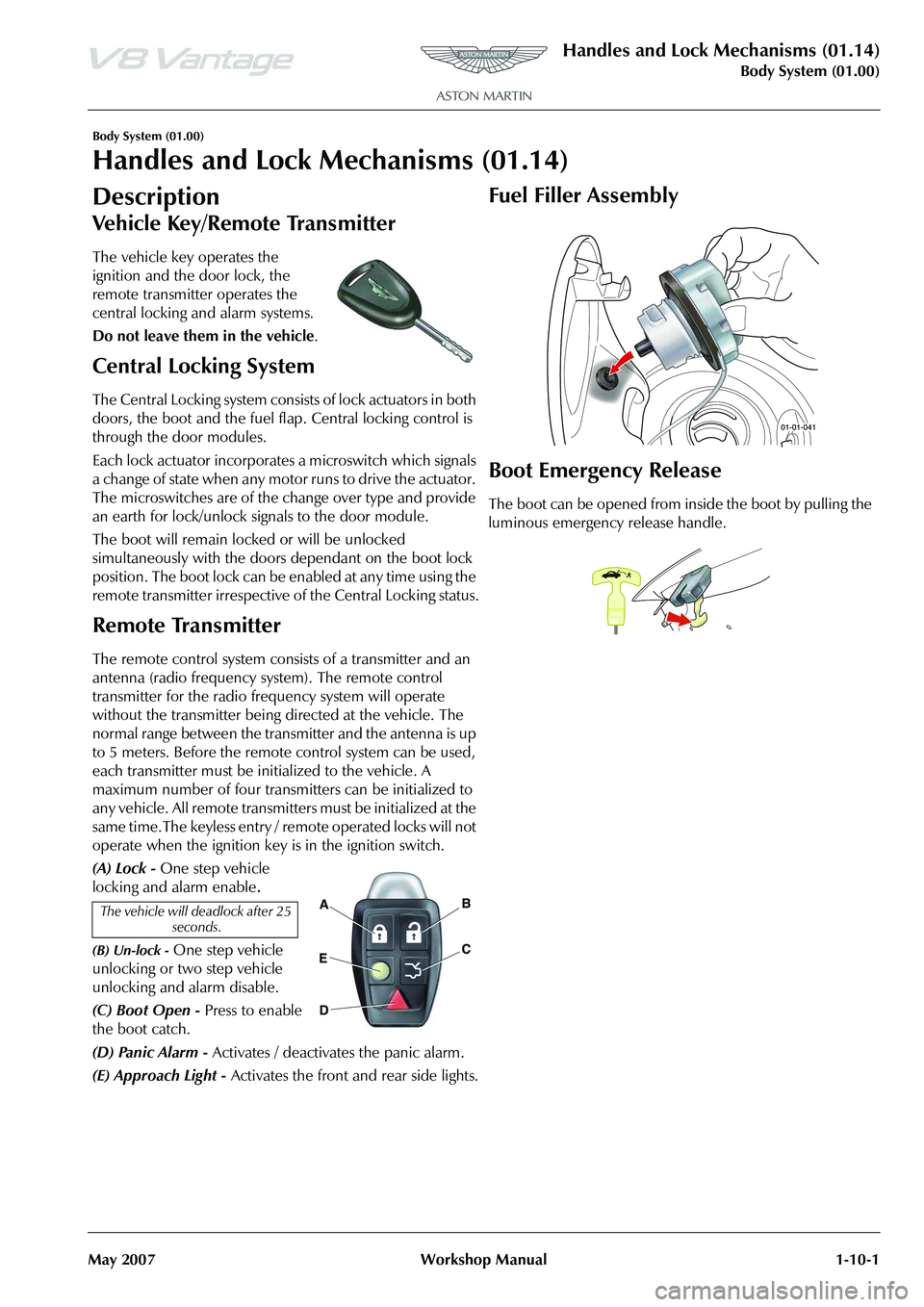
Handles and Lock Mechanisms (01.14)
Body System (01.00)
May 2007 Workshop Manual 1-10-1
Body System (01.00)
Handles and Lock Mechanisms (01.14)
Description
The vehicle key operates the
ignition and the door lock, the
remote transmitter operates the
central locking and alarm systems.
Do not leave them in the vehicle .
Central Locking System
The Central Locking system consists of lock actuators in both
doors, the boot and the fuel flap. Central locking control is
through the door modules.
Each lock actuator incorporates a microswitch which signals
a change of state when any motor runs to drive the actuator.
The microswitches are of the change over type and provide
an earth for lock/unlock signals to the door module.
The boot will remain locked or will be unlocked
simultaneously with the doors dependant on the boot lock
position. The boot lock can be enabled at any time using the
remote transmitter irrespective of the Central Locking status.
Remote Transmitter
The remote control system consists of a transmitter and an
antenna (radio frequency system). The remote control
transmitter for the radio frequency system will operate
without the transmitter being directed at the vehicle. The
normal range between the transmitter and the antenna is up
to 5 meters. Before the remote control system can be used,
each transmitter must be initialized to the vehicle. A
maximum number of four transmitters can be initialized to
any vehicle. All remote transmitters must be initialized at the
same time.The keyless entry / remote operated locks will not
operate when the ignition key is in the ignition switch.
(A) Lock - One step vehicle
locking and alarm enable
.
(B) Un-lock - One step vehicle
unlocking or two step vehicle
unlocking and alarm disable.
(C) Boot Open - Press to enable
the boot catch.
(D) Panic Alarm - Activates / deactivates the panic alarm.
(E) Approach Light - Activates the front and rear side lights.
Fuel Filler Assembly
Boot Emergency Release
The boot can be opened from in side the boot by pulling the
luminous emergency release handle.
The vehicle will deadlock after 25 seconds.
Page 131 of 947
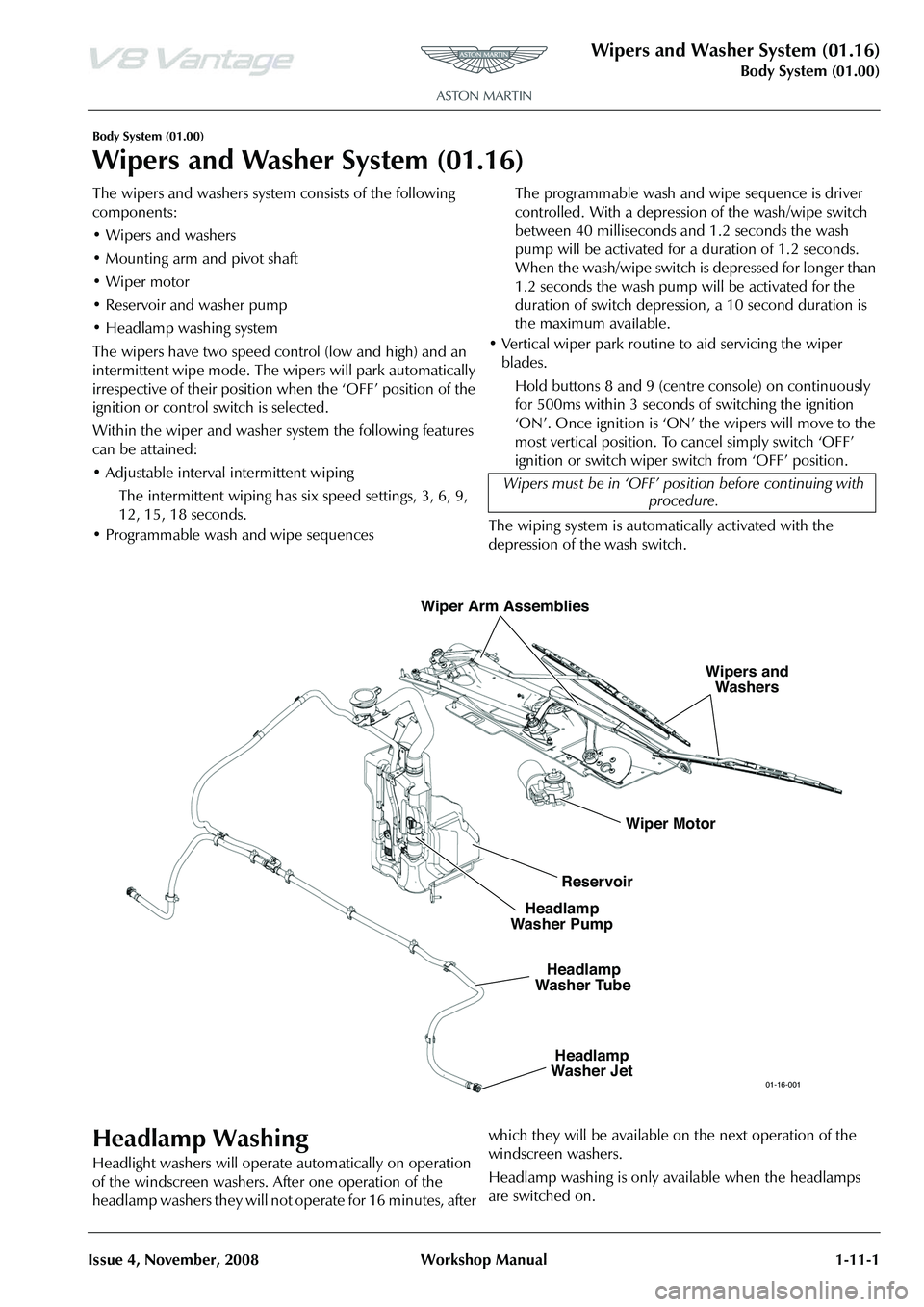
Wipers and Washer System (01.16)
Body System (01.00)
Issue 4, November, 2008 Workshop Manual 1-11-1
Body System (01.00)
Wipers and Washer System (01.16)
The wipers and washers system consists of the following
components:
• Wipers and washers
• Mounting arm and pivot shaft
•Wiper motor
• Reservoir and washer pump
• Headlamp washing system
The wipers have two speed control (low and high) and an
intermittent wipe mode. The wi pers will park automatically
irrespective of their position when the ‘OFF’ position of the
ignition or control switch is selected.
Within the wiper and washer sy stem the following features
can be attained:
• Adjustable interval intermittent wiping
The intermittent wiping has six speed settings, 3, 6, 9,
12, 15, 18 seconds.
• Programmable wash and wipe sequences The programmable wash and wipe sequence is driver
controlled. With a depression of the wash/wipe switch
between 40 milliseconds and 1.2 seconds the wash
pump will be activated for a duration of 1.2 seconds.
When the wash/wipe switch is depressed for longer than
1.2 seconds the wash pump will be activated for the
duration of switch depression
, a 10 second duration is
the maximum available.
• Vertical wiper park routine to aid servicing the wiper blades.
Hold buttons 8 and 9 (centre console) on continuously
for 500ms within 3 seconds of switching the ignition
‘ON’. Once ignition is ‘ON’ the wipers will move to the
most vertical position. To cancel simply switch ‘OFF’
ignition or switch wiper switch from ‘OFF’ position.
The wiping system is automatically activated with the
depression of the wash switch.
Headlamp Washing
Headlight washers will operate automatically on operation
of the windscreen washers. After one operation of the
headlamp washers they will not operate for 16 minutes, after which they will be available on the next operation of the
windscreen washers.
Headlamp washing is only available when the headlamps
are switched on.Wipers must be in ‘OFF’ pos
ition before continuing with
procedure.
Wiper Motor Wipers and
Washers
Wiper Arm Assemblies
Reservoir
Headlamp
Washer Pump
Headlamp
Washer Jet
Headlamp
Washer Tube
01-16-001
Page 141 of 947
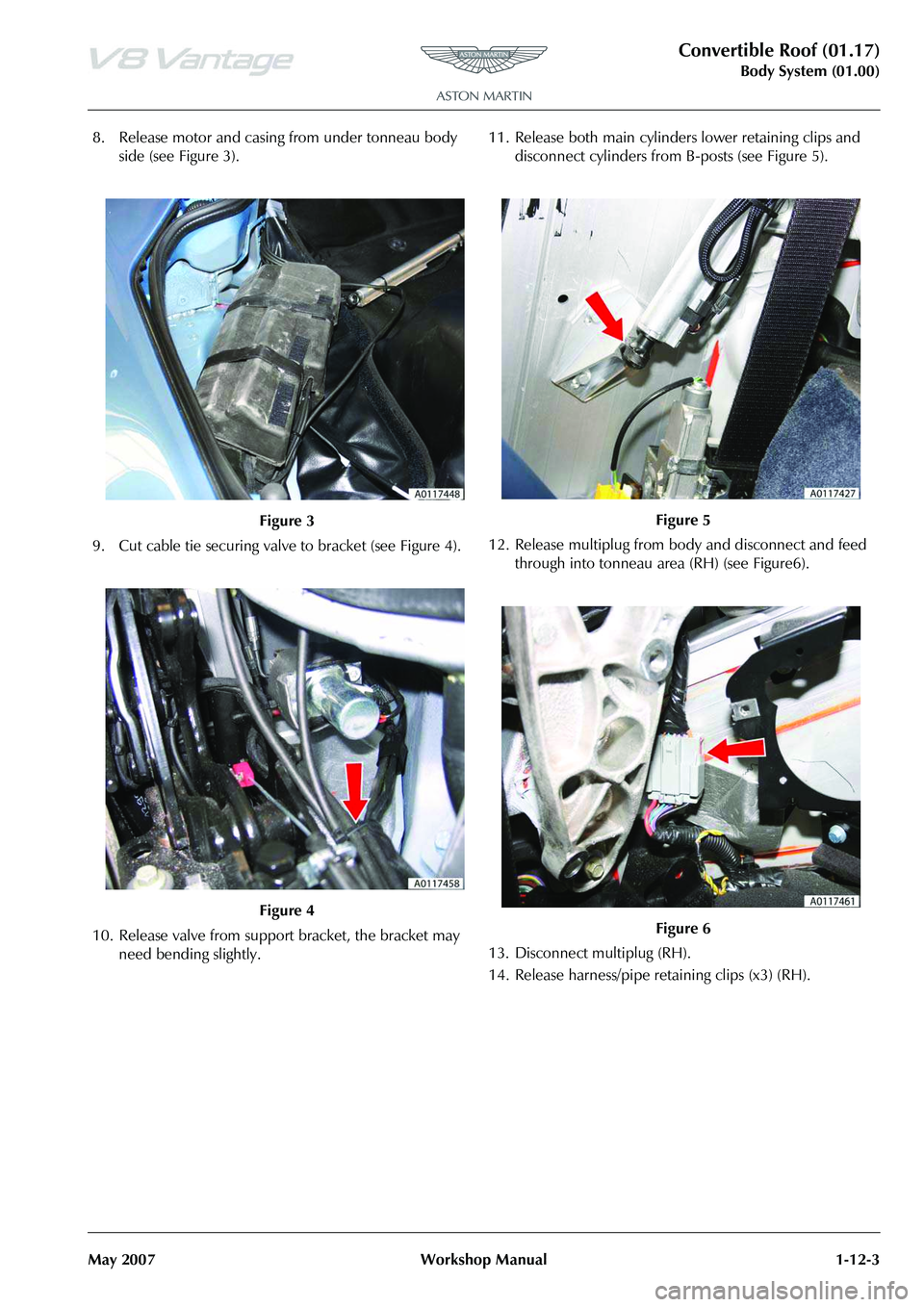
Convertible Roof (01.17)
Body System (01.00)
May 2007 Workshop Manual 1-12-3
8. Release motor and casing from under tonneau body side (see Figure 3).
9. Cut cable tie securing valve to bracket (see Figure 4).
10. Release valve from support bracket, the bracket may need bending slightly. 11. Release both main cylinders lower retaining clips and
disconnect cylinders from B-posts (see Figure 5).
12. Release multiplug from body and disconnect and feed through into tonneau area (RH) (see Figure6).
13. Disconnect multiplug (RH).
14. Release harness/pipe retaining clips (x3) (RH).
Figure 3
Figure 4
Figure 5
Figure 6
Page 155 of 947
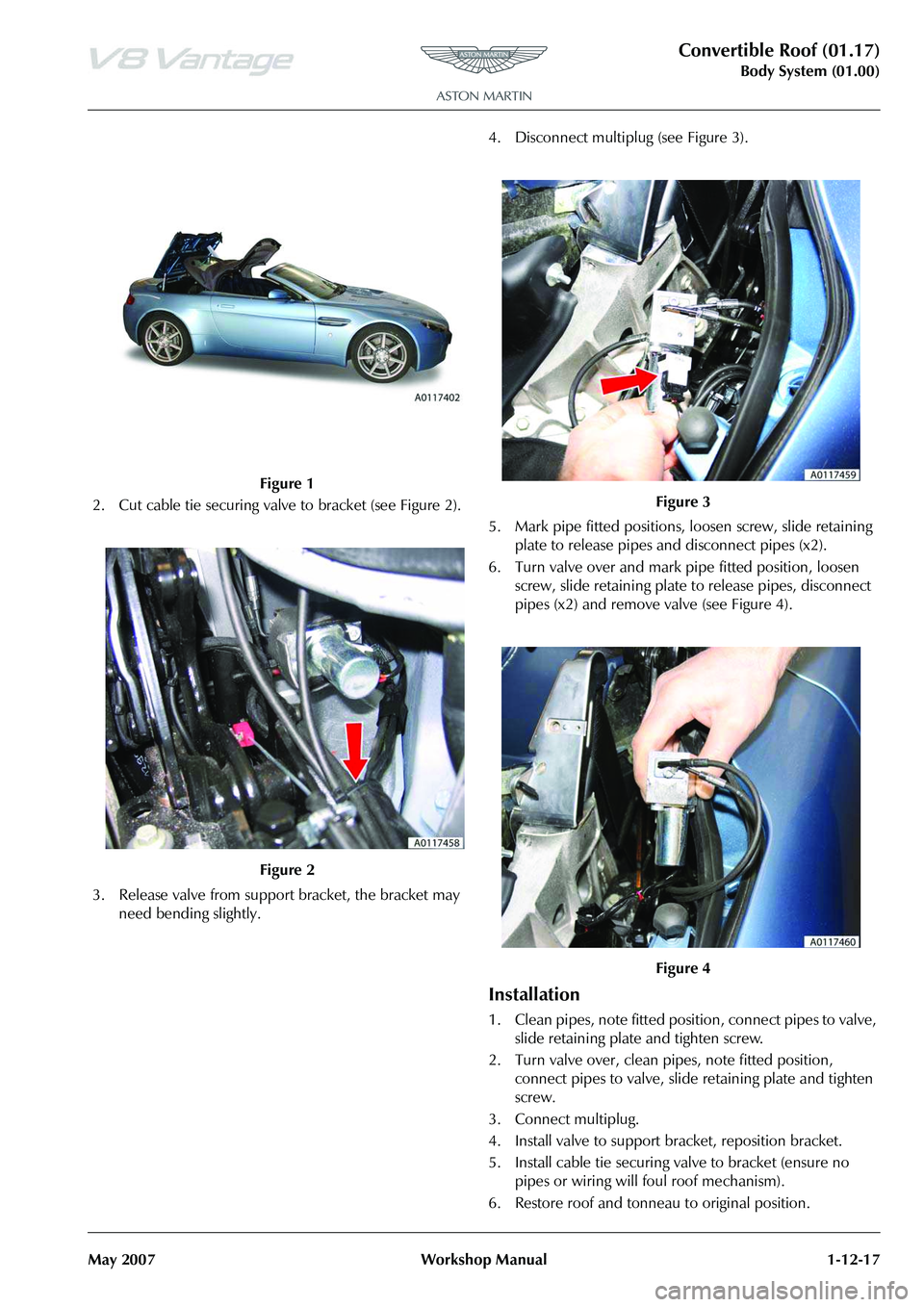
Convertible Roof (01.17)
Body System (01.00)
May 2007 Workshop Manual 1-12-17
2. Cut cable tie securing valve to bracket (see Figure 2).
3. Release valve from support bracket, the bracket may need bending slightly. 4. Disconnect multiplug (see Figure 3).
5. Mark pipe fitted positions, loosen screw, slide retaining
plate to release pipes and disconnect pipes (x2).
6. Turn valve over and mark pipe fitted position, loosen screw, slide retaining plate to release pipes, disconnect
pipes (x2) and remove valve (see Figure 4).
Installation
1. Clean pipes, note fitted posi tion, connect pipes to valve,
slide retaining plate and tighten screw.
2. Turn valve over, clean pipes, note fitted position, connect pipes to valve, slide retaining plate and tighten
screw.
3. Connect multiplug.
4. Install valve to support br acket, reposition bracket.
5. Install cable tie securing valve to bracket (ensure no pipes or wiring will foul roof mechanism).
6. Restore roof and tonneau to original position.
Figure 1
Figure 2
Figure 3
Figure 4
Page 156 of 947
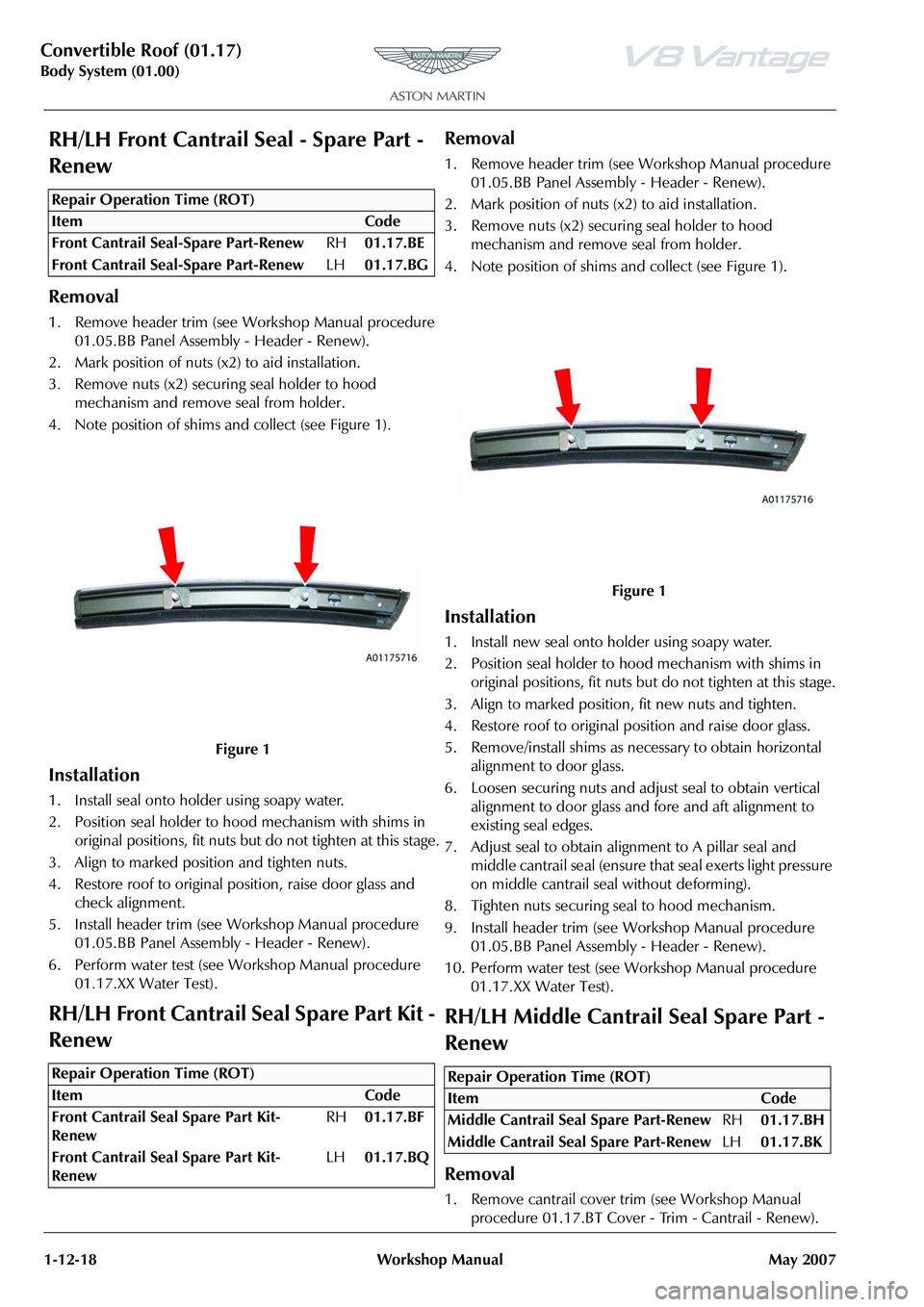
Convertible Roof (01.17)
Body System (01.00)1-12-18 Workshop Manual May 2007
RH/LH Front Cantrail Seal - Spare Part -
Renew
Removal
1. Remove header trim (see Workshop Manual procedure 01.05.BB Panel Assembly - Header - Renew).
2. Mark position of nuts (x2) to aid installation.
3. Remove nuts (x2) secu ring seal holder to hood
mechanism and remove seal from holder.
4. Note position of shims and collect (see Figure 1).
Installation
1. Install seal onto holder using soapy water.
2. Position seal holder to hood mechanism with shims in original positions, fit nuts but do not tighten at this stage.
3. Align to marked position and tighten nuts.
4. Restore roof to original position, raise door glass and check alignment.
5. Install header trim (see Workshop Manual procedure 01.05.BB Panel Assembly - Header - Renew).
6. Perform water test (see Workshop Manual procedure
01.17.XX Water Test).
RH/LH Front Cantrail Seal Spare Part Kit -
Renew
Removal
1. Remove header trim (see Workshop Manual procedure 01.05.BB Panel Assembly - Header - Renew).
2. Mark position of nuts (x2) to aid installation.
3. Remove nuts (x2) secu ring seal holder to hood
mechanism and remove seal from holder.
4. Note position of shims and collect (see Figure 1).
Installation
1. Install new seal onto holder using soapy water.
2. Position seal holder to hood mechanism with shims in
original positions, fit nuts but do not tighten at this stage.
3. Align to marked position, fit new nuts and tighten.
4. Restore roof to original position and raise door glass.
5. Remove/install shims as necessary to obtain horizontal alignment to door glass.
6. Loosen securing nuts and adju st seal to obtain vertical
alignment to door glass and fore and aft alignment to
existing seal edges.
7. Adjust seal to obtain alignment to A pillar seal and middle cantrail seal (ensure that seal exerts light pressure
on middle cantrail seal without deforming).
8. Tighten nuts securing seal to hood mechanism.
9. Install header trim (see Workshop Manual procedure 01.05.BB Panel Assembly - Header - Renew).
10. Perform water test (see Workshop Manual procedure 01.17.XX Water Test).
RH/LH Middle Cantrail Seal Spare Part -
Renew
Removal
1. Remove cantrail cover trim (see Workshop Manual procedure 01.17.BT Cover - Trim - Cantrail - Renew).
Repair Operation Time (ROT)
Repair Operation Time (ROT)
Figure 1
Repair Operation Time (ROT)
ItemCode
Middle Cantrail Se al Spare Part-Renew RH01.17.BH
Middle Cantrail Se al Spare Part-Renew LH01.17.BK