fuel ASTON MARTIN V8 VANTAGE 2010 Service Manual
[x] Cancel search | Manufacturer: ASTON MARTIN, Model Year: 2010, Model line: V8 VANTAGE, Model: ASTON MARTIN V8 VANTAGE 2010Pages: 947, PDF Size: 43.21 MB
Page 450 of 947
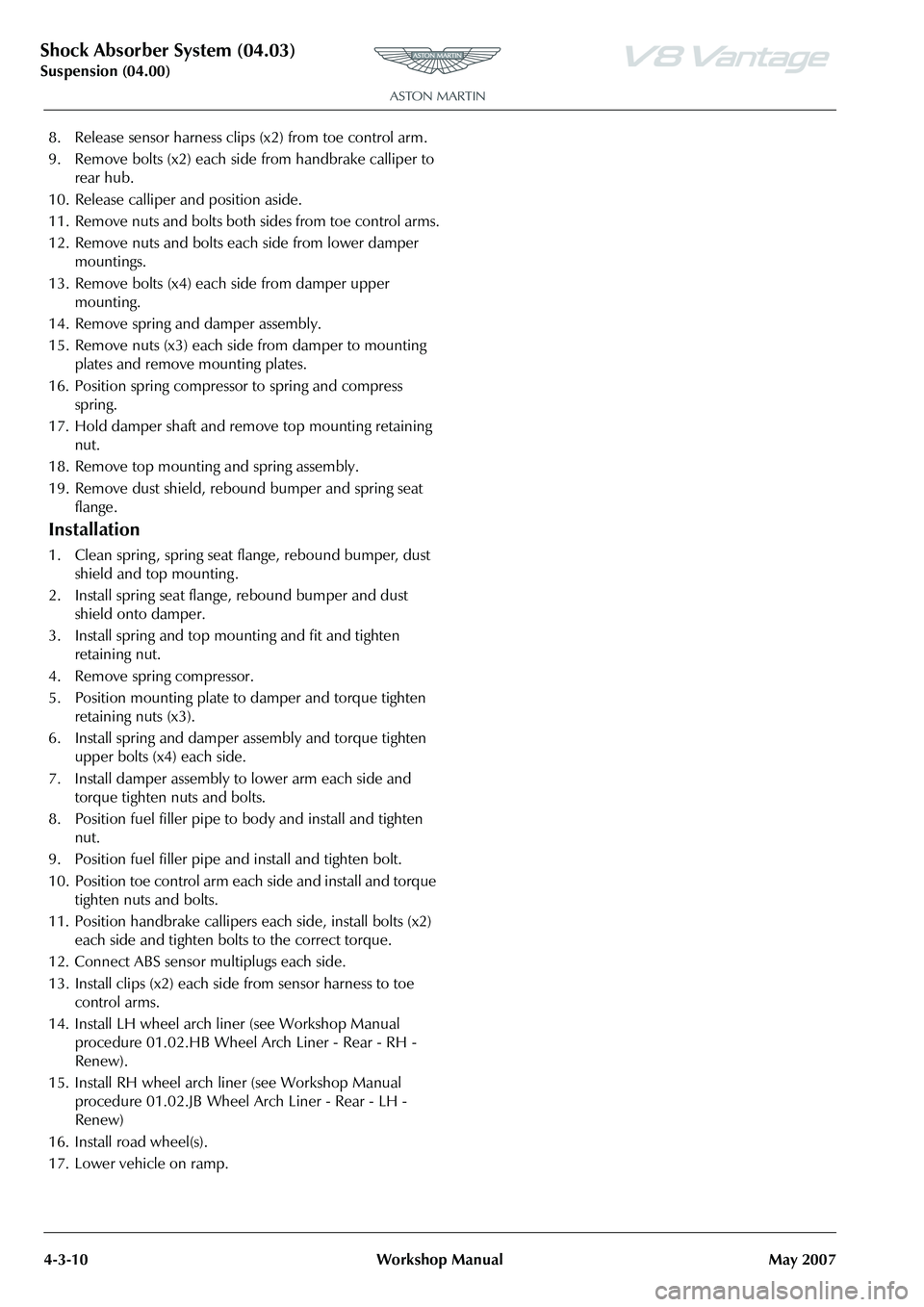
Shock Absorber System (04.03)
Suspension (04.00)4-3-10 Workshop Manual May 2007
8. Release sensor harness clips (x2) from toe control arm.
9. Remove bolts (x2) each side from handbrake calliper to rear hub.
10. Release calliper and position aside.
11. Remove nuts and bolts both sides from toe control arms.
12. Remove nuts and bolts each side from lower damper mountings.
13. Remove bolts (x4) each side from damper upper mounting.
14. Remove spring and damper assembly.
15. Remove nuts (x3) each side from damper to mounting plates and remove mounting plates.
16. Position spring compressor to spring and compress spring.
17. Hold damper shaft and remove top mounting retaining nut.
18. Remove top mounting and spring assembly.
19. Remove dust shield, rebound bumper and spring seat flange.
Installation
1. Clean spring, spring seat flange, rebound bumper, dust
shield and top mounting .
2. Install spring seat flange, rebound bumper and dust shield onto damper.
3. Install spring and top mounting and fit and tighten retaining nut.
4. Remove spring compressor.
5. Position mounting plate to damper and torque tighten retaining nuts (x3).
6. Install spring and damper assembly and torque tighten upper bolts (x4) each side.
7. Install damper assembly to lower arm each side and torque tighten nuts and bolts.
8. Position fuel filler pipe to body and install and tighten nut.
9. Position fuel filler pipe and install and tighten bolt.
10. Position toe control arm each side and install and torque tighten nuts and bolts.
11. Position handbrake callipers each side, install bolts (x2) each side and tighten bolts to the correct torque.
12. Connect ABS sensor multiplugs each side.
13. Install clips (x2) each side from sensor harness to toe control arms.
14. Install LH wheel arch liner (see Workshop Manual procedure 01.02.HB Wheel Arch Liner - Rear - RH -
Renew).
15. Install RH wheel arch liner (see Workshop Manual procedure 01.02.JB Wheel Arch Liner - Rear - LH -
Renew)
16. Install road wheel(s).
17. Lower vehicle on ramp.
Page 508 of 947
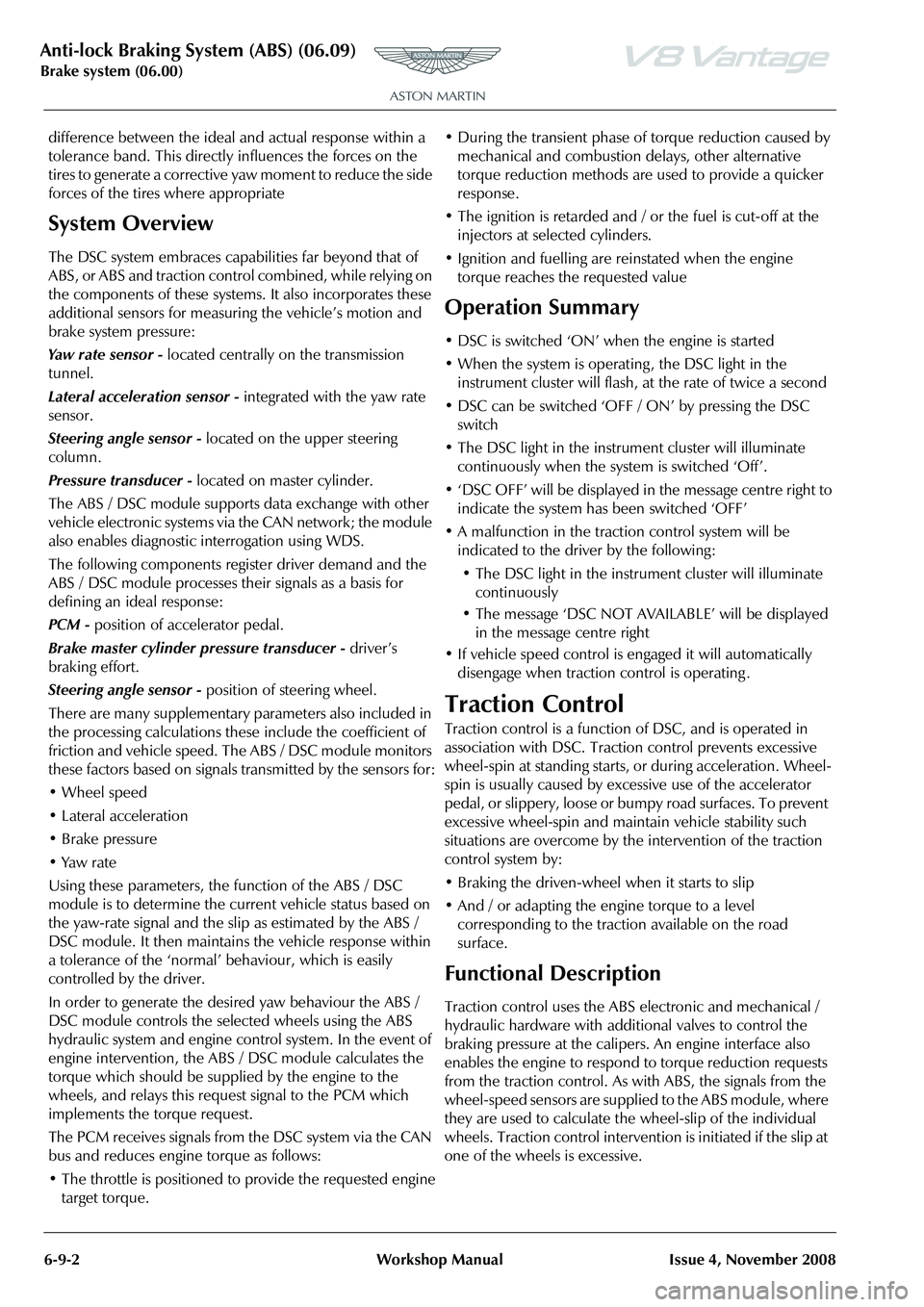
Anti-lock Braking System (ABS) (06.09)
Brake system (06.00)
6-9-2 Workshop Manual Issue 4, November 2008
difference between the ideal and actual response within a
tolerance band. This directly influences the forces on the
tires to generate a corrective yaw moment to reduce the side
forces of the tires where appropriate
System Overview
The DSC system embraces capabilities far beyond that of
ABS, or ABS and traction control combined, while relying on
the components of these systems. It also incorporates these
additional sensors for measur ing the vehicle’s motion and
brake system pressure:
Ya w r a t e s e n s o r - located centrally on the transmission
tunnel.
Lateral acceleration sensor - integrated with the yaw rate
sensor.
Steering angle sensor - located on the upper steering
column.
Pressure transducer - located on master cylinder.
The ABS / DSC module supports data exchange with other
vehicle electronic systems via the CAN network; the module
also enables diagnostic interrogation using WDS.
The following components register driver demand and the
ABS / DSC module processes their signals as a basis for
defining an ideal response:
PCM - position of accelerator pedal.
Brake master cylinder pressure transducer - driver’s
braking effort.
Steering angle sensor - position of steering wheel.
There are many supplementary parameters also included in
the processing calculations these include the coefficient of
friction and vehicle speed. The ABS / DSC module monitors
these factors based on signals transmitted by the sensors for:
• Wheel speed
• Lateral acceleration
• Brake pressure
• Yaw rate
Using these parameters, the function of the ABS / DSC
module is to determine the current vehicle status based on
the yaw-rate signal and the slip as estimated by the ABS /
DSC module. It then maintains the vehicle response within
a tolerance of the ‘normal’ behaviour, which is easily
controlled by the driver.
In order to generate the desired yaw behaviour the ABS /
DSC module controls the selected wheels using the ABS
hydraulic system and engine control system. In the event of
engine intervention, the ABS / DSC module calculates the
torque which should be supplied by the engine to the
wheels, and relays this request signal to the PCM which
implements the torque request.
The PCM receives signals from the DSC system via the CAN
bus and reduces engine torque as follows:
• The throttle is positioned to provide the requested engine target torque. • During the transient phase of torque reduction caused by
mechanical and combustion delays, other alternative
torque reduction methods are used to provide a quicker
response.
• The ignition is retarded and / or the fuel is cut-off at the injectors at selected cylinders.
• Ignition and fuelling are reinstated when the engine torque reaches the requested value
Operation Summary
• DSC is switched ‘ON’ when the engine is started
• When the system is operating , the DSC light in the instrument cluster will flash, at the rate of twice a second
• DSC can be switched ‘OFF / ON’ by pressing the DSC switch
• The DSC light in the instru ment cluster will illuminate
continuously when the system is switched ‘Off’.
• ‘DSC OFF’ will be displayed in the message centre right to indicate the system has been switched ‘OFF’
• A malfunction in the traction control system will be indicated to the driver by the following:
• The DSC light in the instru ment cluster will illuminate
continuously
• The message ‘DSC NOT AVAILABLE’ will be displayed in the message centre right
• If vehicle speed control is engaged it will automatically disengage when traction control is operating .
Traction Control
Traction control is a function of DSC, and is operated in
association with DSC. Traction control prevents excessive
wheel-spin at standing starts, or during acceleration. Wheel-
spin is usually caused by ex cessive use of the accelerator
pedal, or slippery, loose or bumpy road surfaces. To prevent
excessive wheel-spin and mainta in vehicle stability such
situations are overcome by the intervention of the traction
control system by:
• Braking the driven-wheel when it starts to slip
• And / or adapting the engine torque to a level corresponding to the traction available on the road
surface.
Functional Description
Traction control uses the ABS electronic and mechanical /
hydraulic hardware with additional valves to control the
braking pressure at the calipe rs. An engine interface also
enables the engine to respond to torque reduction requests
from the traction control. As with ABS, the signals from the
wheel-speed sensors are supplied to the ABS module, where
they are used to calculate the wheel-slip of the individual
wheels. Traction control intervention is initiated if the slip at
one of the wheels is excessive.
Page 509 of 947
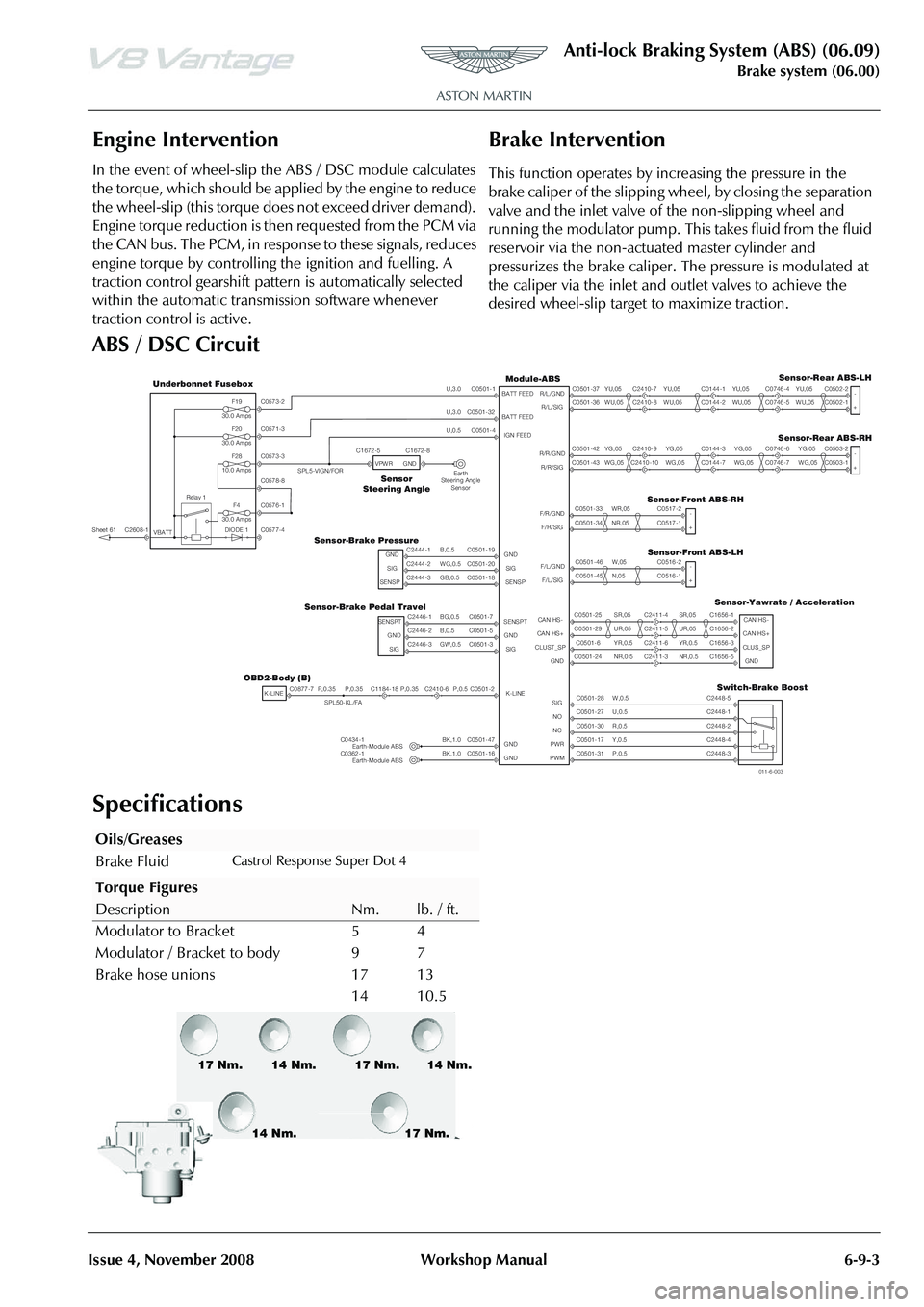
Anti-lock Braking System (ABS) (06.09)
Brake system (06.00)
Issue 4, November 2008 Workshop Manual 6-9-3
Engine Intervention
In the event of wheel-slip the ABS / DSC module calculates
the torque, which should be applied by the engine to reduce
the wheel-slip (this torque does not exceed driver demand).
Engine torque reduction is then requested from the PCM via
the CAN bus. The PCM, in response to these signals, reduces
engine torque by controlling the ignition and fuelling. A
traction control gearshift pattern is automatically selected
within the automatic transmission software whenever
traction control is active.
Brake Intervention
This function operates by increasing the pressure in the
brake caliper of the slipping wheel, by closing the separation
valve and the inlet valve of the non-slipping wheel and
running the modulator pump. This takes fluid from the fluid
reservoir via the non-actuated master cylinder and
pressurizes the brake caliper. The pressure is modulated at
the caliper via the inlet and outlet valves to achieve the
desired wheel-slip target to maximize traction.
ABS / DSC Circuit
Specifications
SR,05UR,05YR,0.5NR,0.5
WR,05NR,05
YG,05WG,05
YU,05WU,05
W,05N,05
W,0.5U,0.5R,0.5
P,0.5Y,0.5
B,0.5WG,0.5GB,0.5
B,0.5BG,0.5
GW,0.5
P,0.5
U,0.5
U,3.0
BK,1.0BK,1.0
P,0.35P,0.35P,0.35 U,3.0
WG,05YG,05
WU,05
SR,05UR,05YR,0.5NR,0.5
WG,05YG,05
WU,05
WG,05YG,05
WU,05YU,05YU,05YU,05Module-ABS
OBD2-Body (B)
Earth-Module ABSEarth-Module ABS
C1184-18C2410-6
Sensor-Brake Pressure
Sensor-Brake Pedal Travel
Sensor-Rear ABS-LH
C0746-7C0746-6
C0746-5
Switch-Brake Boost
Sensor-Yawrate / Acceleration
C2411-6C2411-5C2411-4
C2411-3
C0144-7C0144-3
C0144-2
Sensor-Front ABS-LH
Sensor-Front ABS-RH
C2410-10C2410-9
C2410-8
Sensor-Rear ABS-RH
C0746-4C0144-1C2410-7
C0877-7
K-LINESPL50-KL/FA
C0362-1C0434-1
C2444-2
SIGC2444-1
GND
C2444-3
SENSP
C2446-2
GNDC2446-1
SENSPT
C2446-3
SIG
C0501-47
GNDC0501-16
GND
C0501-2K-LINE
C0501-24
GND
C0501-31
PWM
C0501-30
NC
C0501-25
CAN HS-
C0501-28
SIGC0501-27
NO
C0501-29
CAN HS+C0501-6
CLUST_SP
C0501-17
PWR
C0501-5
GND
C0501-32BATT FEED
C0501-7
SENSPT
C0501-3 SIG
C0501-20 SIGC0501-19
GND
C0501-18 SENSP
C0501-4IGN FEED
C0501-46
F/L/GNDC0501-45
F/L/SIG
C0501-42
R/R/GNDC0501-43
R/R/SIG
C0501-36
R/L/SIG
C0501-34
F/R/SIGC0501-33
F/R/GND
C0501-1
BATT FEEDC0501-37
R/L/GND
C2448-5
C2448-3
C2448-2C2448-1
C2448-4
C1656-3 CLUS_SPC1656-2
CAN HS+C1656-1 CAN HS-
C1656-5
GND
C0516-2-C0516-1+
C0517-2
-C0517-1+
C0502-1
+
C0503-2 -C0503-1+
C0502-2 -
Sensor
Steering Angle
Sheet 61
F4
30.0 AmpsRelay 1
Underbonnet Fusebox
DIODE 1
F28
10.0 Amps
F20
30.0 Amps
F19
30.0 Amps
Earth
Steering Angle
Sensor
C0576-1
C0577-4C2608-1 VBATT
C0573-2
C0571-3
C0573-3
C0578-8SPL5-VIGN/FOR
C1672-5
VPWRC1672-8
GND
011-6-003
Oils/Greases
Brake FluidCastrol Response Super Dot 4
Torque Figures
DescriptionNm.lb. / ft.
Modulator to Bracket 5 4
Modulator / Bracket to body 9 7
Brake hose unions 17 1413
10.5
17 Nm. 17 Nm.
17 Nm.
14 Nm.
14 Nm. 14 Nm.
Page 582 of 947
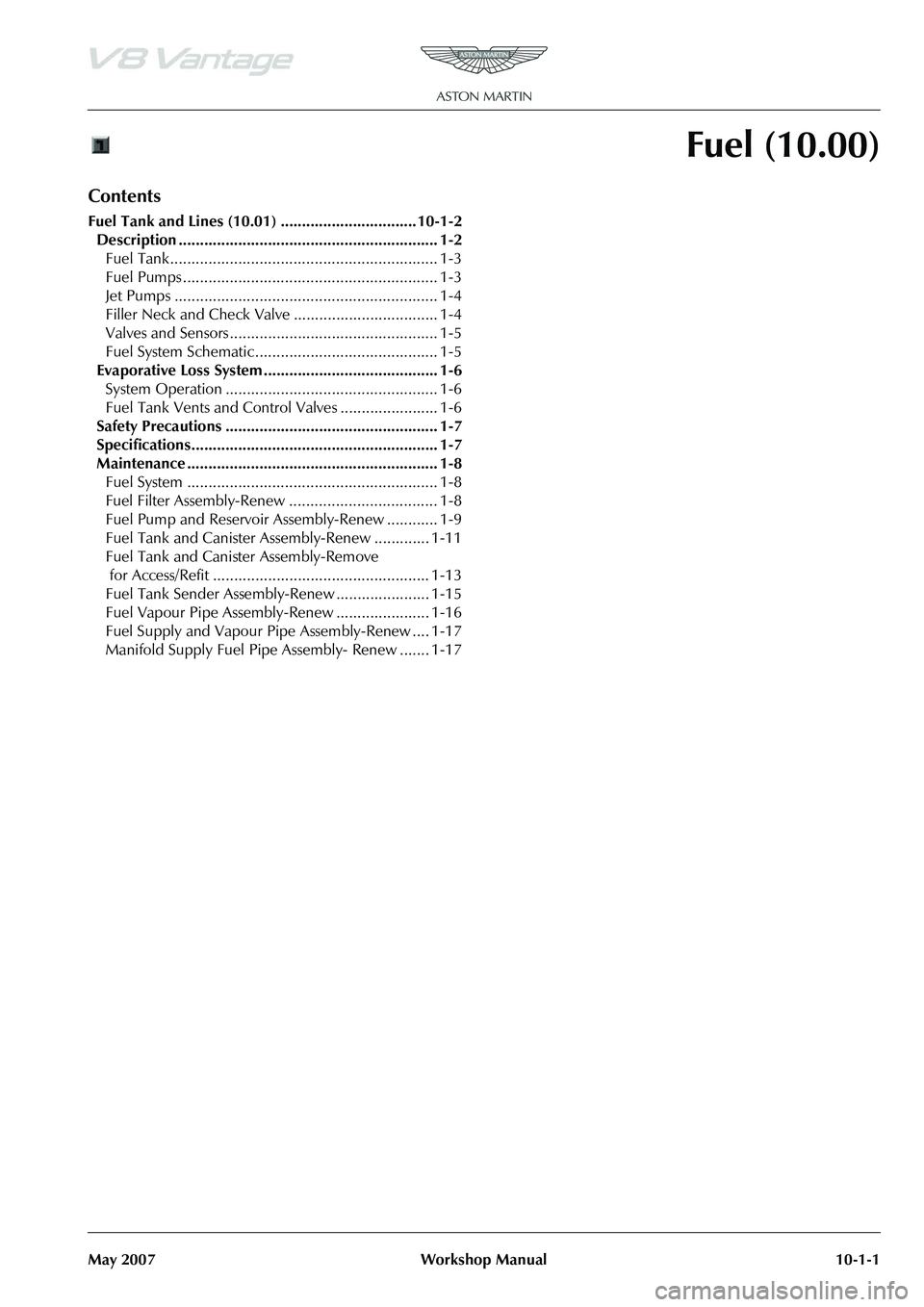
May 2007 Workshop Manual 10-1-1
Fuel (10.00)
Contents
Fuel Tank and Lines (10.01) ................................ 10-1-2Description ............................................................. 1-2 Fuel Tank............................................................... 1-3
Fuel Pumps ............................................................ 1-3
Jet Pumps .............................................................. 1-4
Filler Neck and Check Valve .................................. 1-4
Valves and Sensors ................................................. 1-5
Fuel System Schematic ........................................... 1-5
Evaporative Loss System ......................................... 1-6 System Operation .................................................. 1-6
Fuel Tank Vents and Control Valves ....................... 1-6
Safety Precautions .................................................. 1-7
Specifications.......................................................... 1-7
Maintenance ........................................................... 1-8 Fuel System ........................................................... 1-8
Fuel Filter Assembly-Renew .. ................................. 1-8
Fuel Pump and Reservoir Assembly-Renew ............ 1-9
Fuel Tank and Canister Assembly-Renew ............. 1-11
Fuel Tank and Canister Assembly-Remove
for Access/Refit ................................................... 1-13
Fuel Tank Sender Assembly-Renew ...................... 1-15
Fuel Vapour Pipe Assembly-Renew ...................... 1-16
Fuel Supply and Vapour Pipe Assembly-Renew .... 1-17
Manifold Supply Fuel Pipe Assembly- Renew ....... 1-17
Page 583 of 947
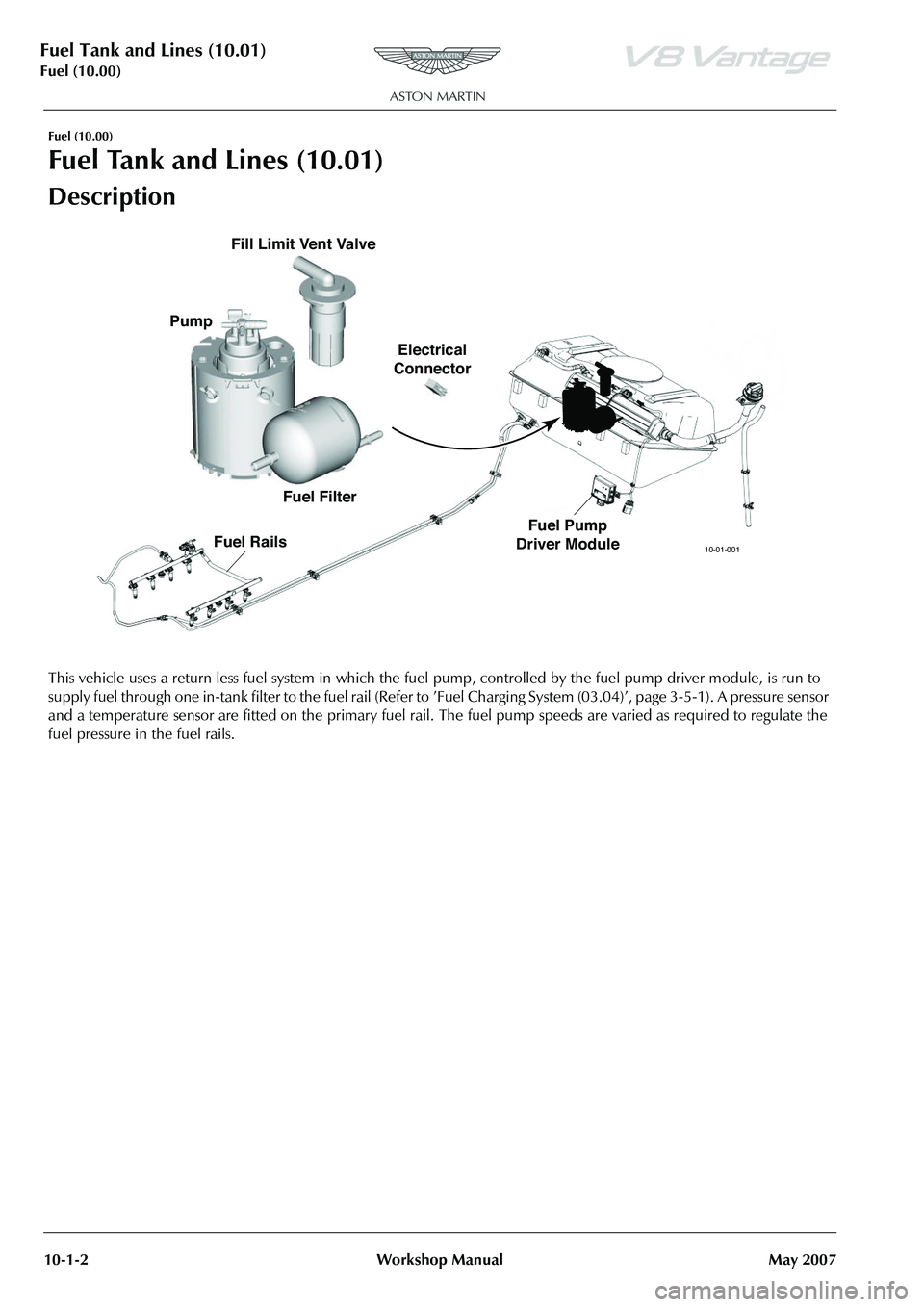
Fuel Tank and Lines (10.01)
Fuel (10.00)10-1-2 Workshop Manual May 2007
Fuel (10.00)
Fuel Tank and Lines (10.01)
Description
This vehicle uses a return less fuel system in which the fuel pump, controlled by the fuel pump driver module, is run to
supply fuel through one in-tank filter to the fuel rail (Refer to ’Fuel Charging System (03.04)’, page 3-5-1). A pressure senso r
and a temperature sensor are fitted on th e primary fuel rail. The fuel pump speeds are varied as required to regulate the
fuel pressure in the fuel rails.
$ G G Q R L Q L O O X V W U D W R U
6 D Y H D V S G I
5 H R S H Q L Q S K R W R V K R S D Q G V D Y H D V G S L S G I
3 X P S
) X H O ) L O W H U
) X H O 5 D L O V ) X H O 3 X P S
' U L Y H U 0 R G X O H
) L O O / L P L W 9 H Q W 9 D O Y H
( O H F W U L F D O
&