steering wheel ASTON MARTIN V8 VANTAGE 2010 Workshop Manual
[x] Cancel search | Manufacturer: ASTON MARTIN, Model Year: 2010, Model line: V8 VANTAGE, Model: ASTON MARTIN V8 VANTAGE 2010Pages: 947, PDF Size: 43.21 MB
Page 3 of 947
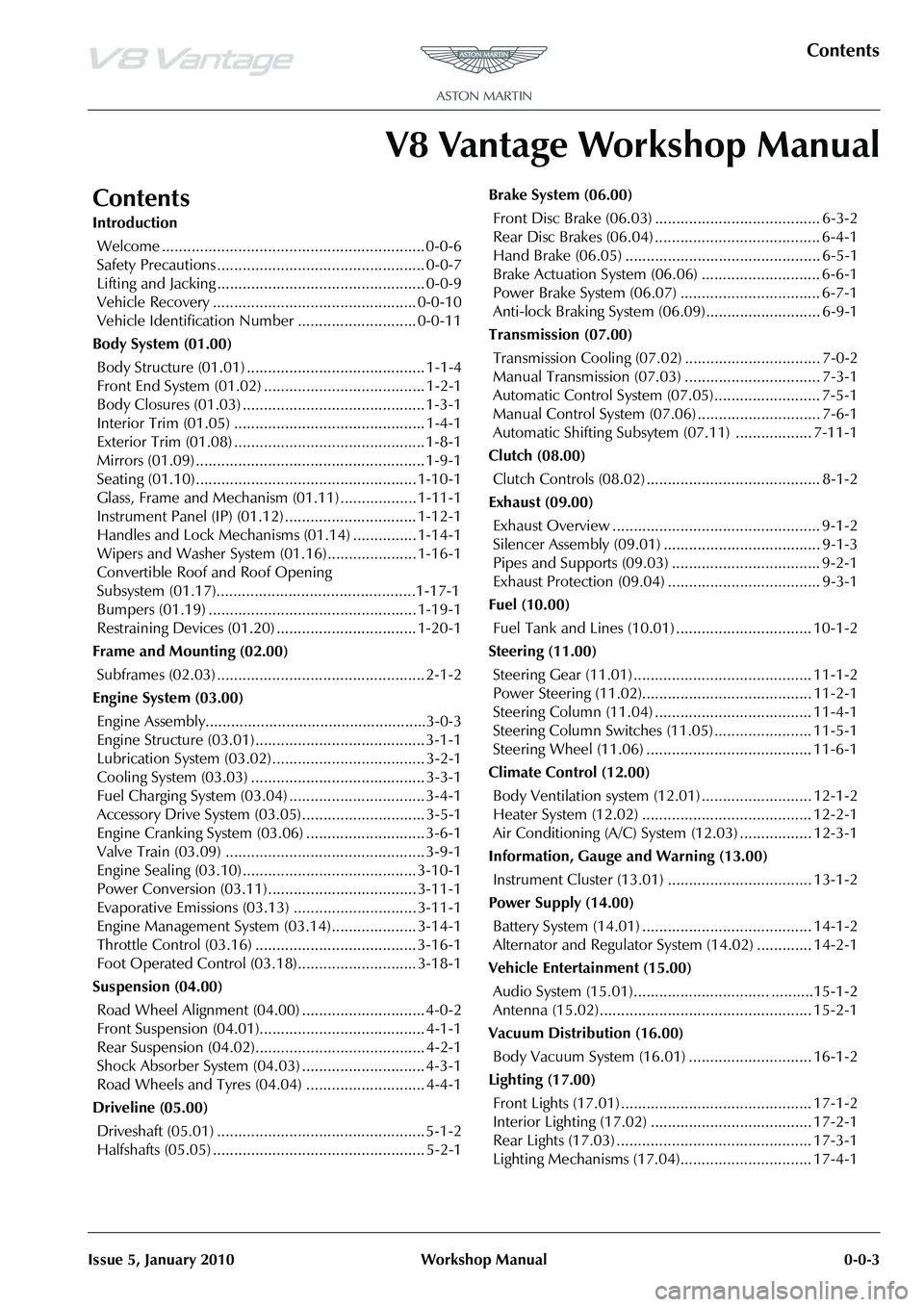
Contents
Issue 5, January 2010 Workshop Manual 0-0-3
V8 Vantage Workshop Manual
Contents
IntroductionWelcome .............................................................. 0-0-6
Safety Precautions ................................................. 0-0-7
Lifting and Jacking ................................................. 0-0-9
Vehicle Recovery ................................................ 0-0-10
Vehicle Identification Number ............................ 0-0-11
Body System (01.00) Body Structure (01.01) .......................................... 1-1-4
Front End System (01.02) ...................................... 1-2-1
Body Closures (01.03) ........................................... 1-3-1
Interior Trim (01.05) ............................................. 1-4-1
Exterior Trim (01.08) ............................................. 1-8-1
Mirrors (01.09) ...................................................... 1-9-1
Seating (01.10).................................................... 1-10-1
Glass, Frame and Mechanism (01.11) .................. 1-11-1
Instrument Panel (IP) (01.12) . .............................. 1-12-1
Handles and Lock Mechanisms (01.14) ............... 1-14-1
Wipers and Washer System (01.16)..................... 1-16-1
Convertible Roof and Roof Opening
Subsystem (01.17)................ ...............................1-17-1
Bumpers (01.19) ................................................. 1-19-1
Restraining Devices (01.20) .... ............................. 1-20-1
Frame and Mounting (02.00) Subframes (02.03) ................................................. 2-1-2
Engine System (03.00) Engine Assembly....................................................3-0-3
Engine Structure (03.01)........................................ 3-1-1
Lubrication System (03.02).................................... 3-2-1
Cooling System (03.03) ......................................... 3-3-1
Fuel Charging System (03.04) ................................ 3-4-1
Accessory Drive System (03.05)............................. 3-5-1
Engine Cranking System (03. 06) ............................ 3-6-1
Valve Train (03.09) ............................................... 3-9-1
Engine Sealing (03.10)......................................... 3-10-1
Power Conversion (03.11)................................... 3-11-1
Evaporative Emissions (03.13) ............................. 3-11-1
Engine Management System (0 3.14).................... 3-14-1
Throttle Control (03.16) ...... ................................ 3-16-1
Foot Operated Control (03.18)............................ 3-18-1
Suspension (04.00) Road Wheel Alignment (04.00) ............................. 4-0-2
Front Suspension (04.01)....................................... 4-1-1
Rear Suspension (04.02)........................................ 4-2-1
Shock Absorber System (04.03) ............................. 4-3-1
Road Wheels and Tyres (04.04) ............................ 4-4-1
Driveline (05.00) Driveshaft (05.01) ................................................. 5-1-2
Halfshafts (05.05) .................................................. 5-2-1 Brake System (06.00)
Front Disc Brake (06.03) ....................................... 6-3-2
Rear Disc Brakes (06.04) ....................................... 6-4-1
Hand Brake (06.05) .............................................. 6-5-1
Brake Actuation System (06.06 ) ............................ 6-6-1
Power Brake System (06.07) ................................. 6-7-1
Anti-lock Braking System (06.09)........................... 6-9-1
Transmission (07.00) Transmission Cooling (07.02) ................................ 7-0-2
Manual Transmission (07.03) ................................ 7-3-1
Automatic Control System (07.05)......................... 7-5-1
Manual Control System (07.06) ............................. 7-6-1
Automatic Shifting Subsytem (07.11) .................. 7-11-1
Clutch (08.00) Clutch Controls (08.02) ......................................... 8-1-2
Exhaust (09.00) Exhaust Overview ................................................. 9-1-2
Silencer Assembly (09.01) ..................................... 9-1-3
Pipes and Supports (09.03) ................................... 9-2-1
Exhaust Protection (09.04) .................................... 9-3-1
Fuel (10.00) Fuel Tank and Lines (10.01) ................................ 10-1-2
Steering (11.00) Steering Gear (11.01) .......................................... 11-1-2
Power Steering (11.02)........................................ 11-2-1
Steering Column (11.04) ..................................... 11-4-1
Steering Column Switches (1 1.05) ....................... 11-5-1
Steering Wheel (11.06) ....................................... 11-6-1
Climate Control (12.00) Body Ventilation system (12.01) .......................... 12-1-2
Heater System (12.02) ........................................ 12-2-1
Air Conditioning (A/C) System (12.03) ................. 12-3-1
Information, Gauge and Warning (13.00) Instrument Cluster (13.01) .................................. 13-1-2
Power Supply (14.00) Battery System (14.01) ........................................ 14-1-2
Alternator and Regulator System (14.02) ............. 14-2-1
Vehicle Entertainment (15.00) Audio System (15.01)................................ ..........15-1-2
Antenna (15.02).................................................. 15-2-1
Vacuum Distribution (16.00) Body Vacuum System (16.01) ............................. 16-1-2
Lighting (17.00) Front Lights (17.01) ............................................. 17-1-2
Interior Lighting (17.02) ...................................... 17-2-1
Rear Lights (17.03) .............................................. 17-3-1
Lighting Mechanisms (17.04). .............................. 17-4-1
Page 10 of 947
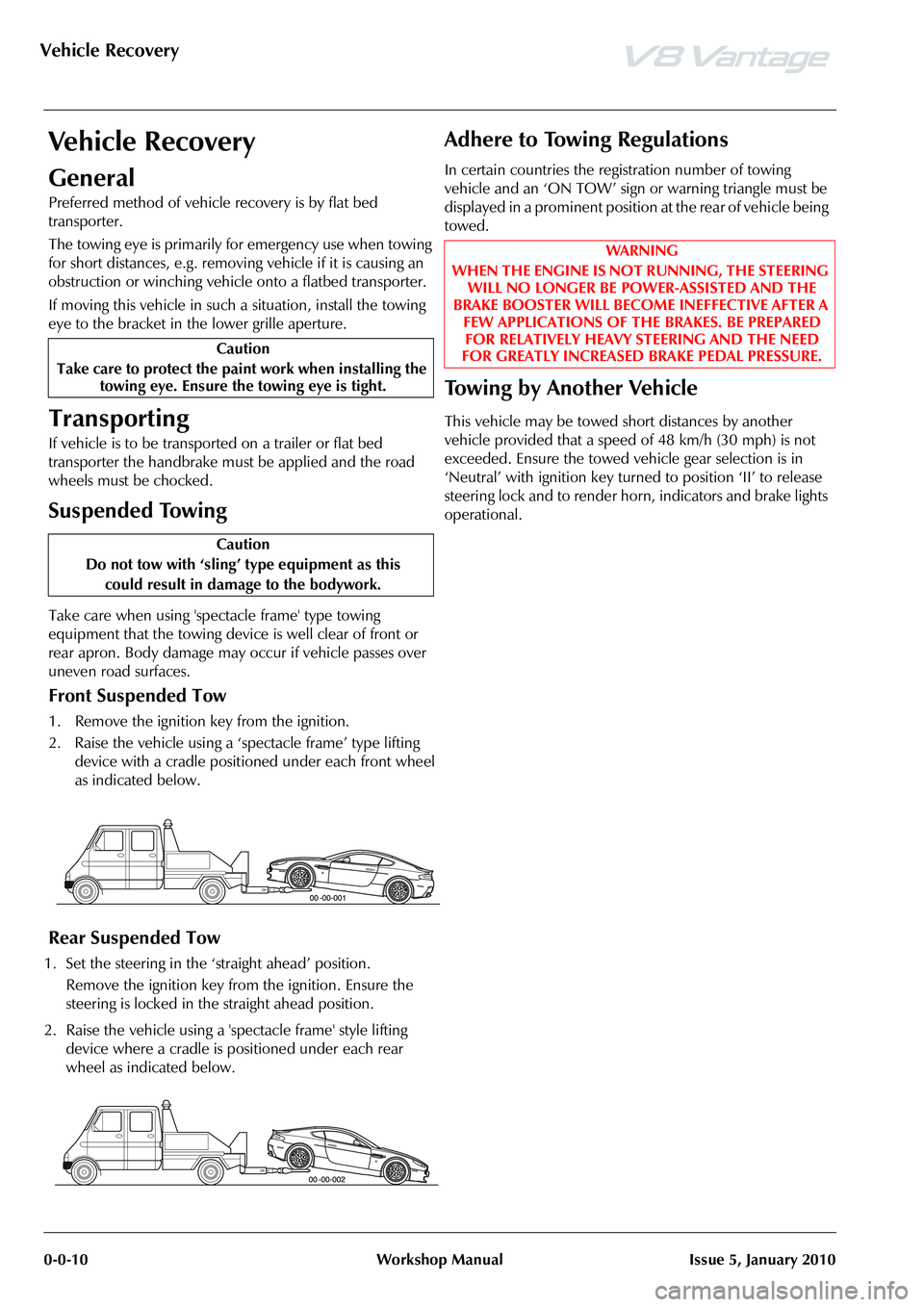
Vehicle Recovery
0-0-10 Workshop Manual Issue 5, January 2010
Vehicle Recovery
General
Preferred method of vehicle recovery is by flat bed
transporter.
The towing eye is primarily for emergency use when towing
for short distances, e.g. removing vehicle if it is causing an
obstruction or winching vehicl e onto a flatbed transporter.
If moving this vehicle in such a situation, install the towing
eye to the bracket in the lower grille aperture.
Transporting
If vehicle is to be transported on a trailer or flat bed
transporter the handbrake must be applied and the road
wheels must be chocked.
Suspended Towing
Take care when using 'spectacle frame' type towing
equipment that the towing device is well clear of front or
rear apron. Body damage may occur if vehicle passes over
uneven road surfaces.
Front Suspended Tow
1. Remove the ignition key from the ignition.
2. Raise the vehicle using a ‘spectacle frame’ type lifting device with a cradle positioned under each front wheel
as indicated below.
Rear Suspended Tow
1. Set the steering in the ‘straight ahead’ position.
Remove the ignition key from the ignition. Ensure the
steering is locked in the straight ahead position.
2. Raise the vehicle using a 'spectacle frame' style lifting device where a cradle is positioned under each rear
wheel as indicated below.
Adhere to Towing Regulations
In certain countries the regi stration number of towing
vehicle and an ‘ON TOW’ sign or warning triangle must be
displayed in a prominent position at the rear of vehicle being
towed.
To w i n g b y A n o t h e r V e h i c l e
This vehicle may be towed short distances by another
vehicle provided that a speed of 48 km/h (30 mph) is not
exceeded. Ensure the towed vehicle gear selection is in
‘Neutral’ with ignition key turned to position ‘II’ to release
steering lock and to render hor n, indicators and brake lights
operational.
Caution
Take care to protect the paint work when installing the towing eye. Ensure the towing eye is tight.
Caution
Do not tow with ‘sling’ type equipment as this
could result in damage to the bodywork.
WAR NI NG
WHEN THE ENGINE IS NOT RUNNING, THE STEERING WILL NO LONGER BE POWER-ASSISTED AND THE
BRAKE BOOSTER WILL BECOME INEFFECTIVE AFTER A FEW APPLICATIONS OF TH E BRAKES. BE PREPARED
FOR RELATIVELY HEAVY STEERING AND THE NEED
FOR GREATLY INCREASED BRAKE PEDAL PRESSURE.
Page 91 of 947
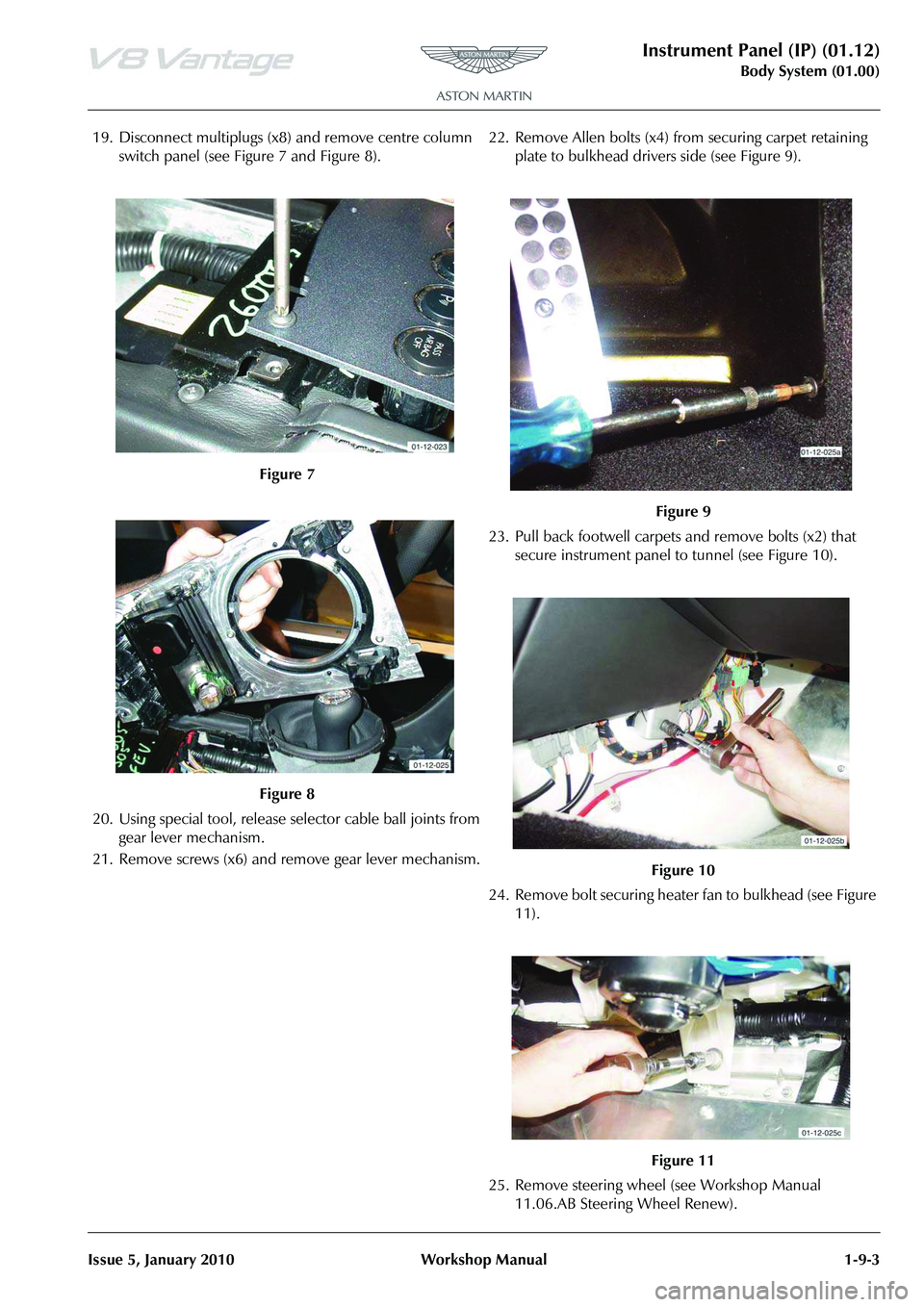
Instrument Panel (IP) (01.12)
Body System (01.00)
Issue 5, January 2010 Workshop Manual 1-9-3
19. Disconnect multiplugs (x8) and remove centre column
switch panel (see Figure 7 and Figure 8).
20. Using special tool, release se lector cable ball joints from
gear lever mechanism.
21. Remove screws (x6) and remove gear lever mechanism. 22. Remove Allen bolts (x4) from securing carpet retaining
plate to bulkhead drivers side (see Figure 9).
23. Pull back footwell carpets and remove bolts (x2) that secure instrument panel to tunnel (see Figure 10).
24. Remove bolt securing heater fan to bulkhead (see Figure 11).
25. Remove steering wheel (see Workshop Manual 11.06.AB Steering Wheel Renew).
Figure 7
Figure 8
Figure 9
Figure 10
Figure 11
Page 93 of 947
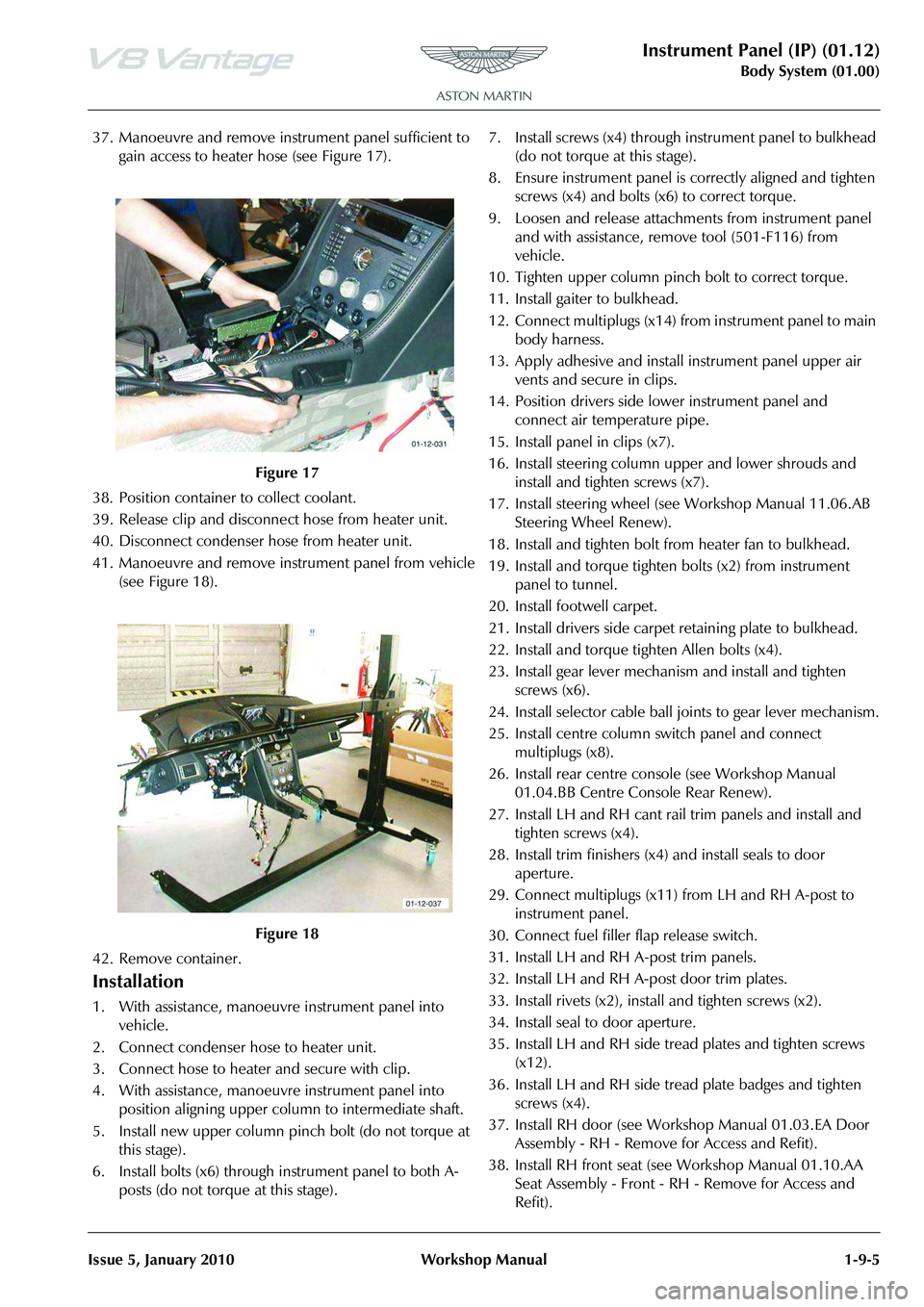
Instrument Panel (IP) (01.12)
Body System (01.00)
Issue 5, January 2010 Workshop Manual 1-9-5
37. Manoeuvre and remove inst rument panel sufficient to
gain access to heater hose (see Figure 17).
38. Position container to collect coolant.
39. Release clip and disconne ct hose from heater unit.
40. Disconnect condenser hose from heater unit.
41. Manoeuvre and remove inst rument panel from vehicle
(see Figure 18).
42. Remove container.
Installation
1. With assistance, manoeuvre instrument panel into vehicle.
2. Connect condenser hose to heater unit.
3. Connect hose to heater and secure with clip.
4. With assistance, manoeuvre instrument panel into position aligning upper column to intermediate shaft.
5. Install new upper column pinch bolt (do not torque at this stage).
6. Install bolts (x6) through instrument panel to both A- posts (do not torque at this stage). 7. Install screws (x4) through
instrument panel to bulkhead
(do not torque at this stage).
8. Ensure instrument panel is correctly aligned and tighten screws (x4) and bolts (x6) to correct torque.
9. Loosen and release attachme nts from instrument panel
and with assistance, remove tool (501-F116) from
vehicle.
10. Tighten upper column pinch bolt to correct torque.
11. Install gaiter to bulkhead.
12. Connect multiplugs (x14) fr om instrument panel to main
body harness.
13. Apply adhesive and install instrument panel upper air
vents and secure in clips.
14. Position drivers side lower instrument panel and connect air temperature pipe.
15. Install panel in clips (x7).
16. Install steering column upper and lower shrouds and install and tighten screws (x7).
17. Install steering wheel (see Workshop Manual 11.06.AB Steering Wheel Renew).
18. Install and tighten bolt from heater fan to bulkhead.
19. Install and torque tighten bolts (x2) from instrument panel to tunnel.
20. Install footwell carpet.
21. Install drivers side carpet retaining plate to bulkhead.
22. Install and torque tighten Allen bolts (x4).
23. Install gear lever mechanism and install and tighten screws (x6).
24. Install selector cable ball joints to gear lever mechanism.
25. Install centre column switch panel and connect multiplugs (x8).
26. Install rear centre cons ole (see Workshop Manual
01.04.BB Centre Console Rear Renew).
27. Install LH and RH cant rail trim panels and install and tighten screws (x4).
28. Install trim finishers (x4) and install seals to door aperture.
29. Connect multiplugs (x11) from LH and RH A-post to
instrument panel.
30. Connect fuel filler flap release switch.
31. Install LH and RH A-post trim panels.
32. Install LH and RH A-post door trim plates.
33. Install rivets (x2), insta ll and tighten screws (x2).
34. Install seal to door aperture.
35. Install LH and RH side tread plates and tighten screws (x12).
36. Install LH and RH side tread plate badges and tighten screws (x4).
37. Install RH door (see Workshop Manual 01.03.EA Door Assembly - RH - Remove for Access and Refit).
38. Install RH front seat (see Workshop Manual 01.10.AA Seat Assembly - Front - RH - Remove for Access and
Refit).
Figure 17
Figure 18
Page 133 of 947
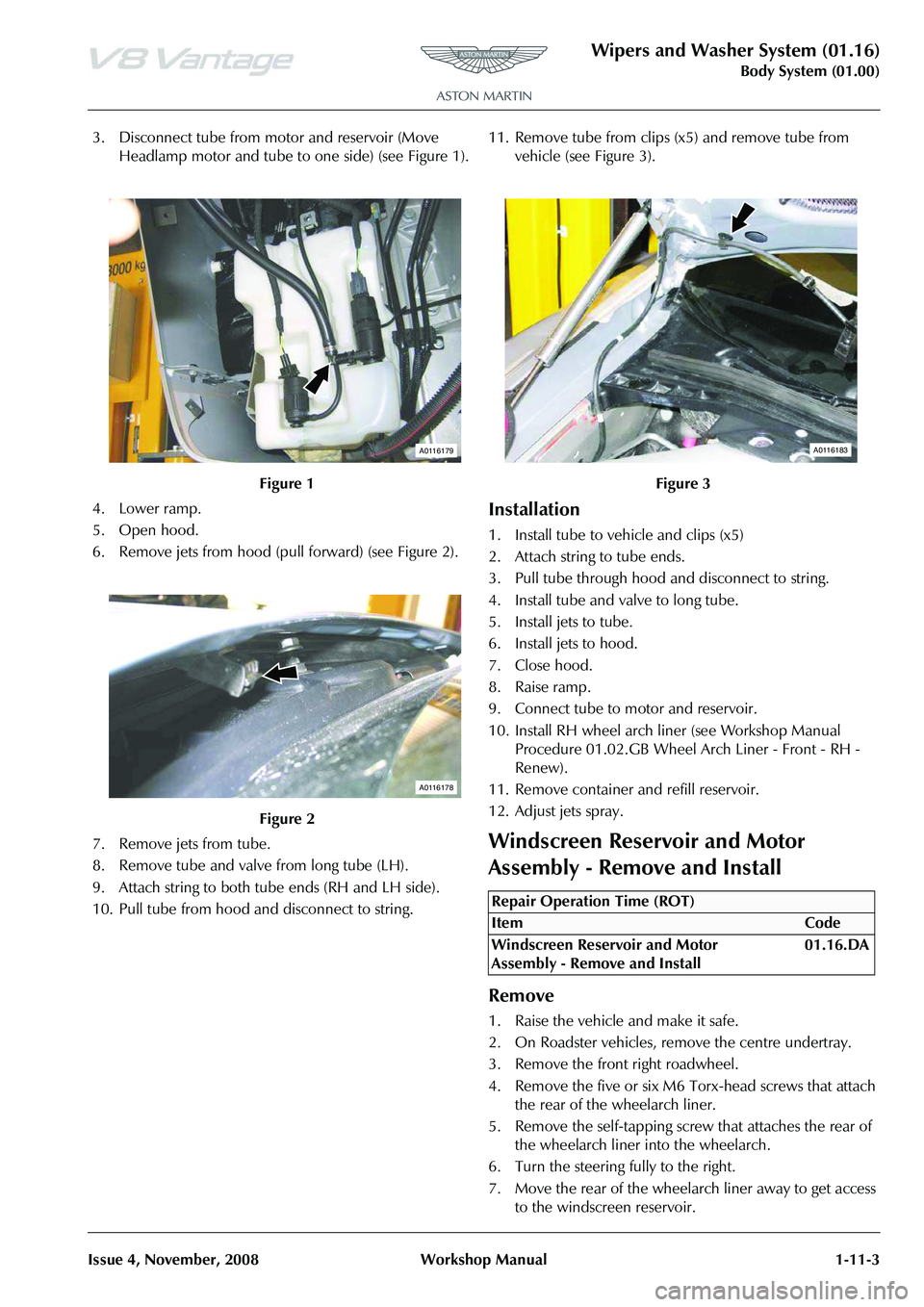
Wipers and Washer System (01.16)
Body System (01.00)
Issue 4, November, 2008 Workshop Manual 1-11-3
3. Disconnect tube from motor and reservoir (Move Headlamp motor and tube to one side) (see Figure 1).
4. Lower ramp.
5. Open hood.
6. Remove jets from hood (pull forward) (see Figure 2).
7. Remove jets from tube.
8. Remove tube and valve from long tube (LH).
9. Attach string to both tube ends (RH and LH side).
10. Pull tube from hood and disconnect to string. 11. Remove tube from clips (x5) and remove tube from
vehicle (see Figure 3).
Installation
1. Install tube to vehicle and clips (x5)
2. Attach string to tube ends.
3. Pull tube through hood and disconnect to string.
4. Install tube and valve to long tube.
5. Install jets to tube.
6. Install jets to hood.
7. Close hood.
8. Raise ramp.
9. Connect tube to motor and reservoir.
10. Install RH wheel arch liner (see Workshop Manual Procedure 01.02.GB Wheel Arch Liner - Front - RH -
Renew).
11. Remove container and refill reservoir.
12. Adjust jets spray.
Windscreen Reservoir and Motor
Assembly - Remove and Install
Remove
1. Raise the vehicle and make it safe.
2. On Roadster vehicles, re move the centre undertray.
3. Remove the front right roadwheel.
4. Remove the five or six M6 Torx-head screws that attach the rear of the wheelarch liner.
5. Remove the self-tapping screw that attaches the rear of the wheelarch liner into the wheelarch.
6. Turn the steering fully to the right.
7. Move the rear of the wheelarch liner away to get access to the windscreen reservoir.
Figure 1
Figure 2
A0116179
A0116178
Figure 3
Repair Operation Time (ROT)
A0116183
Page 134 of 947
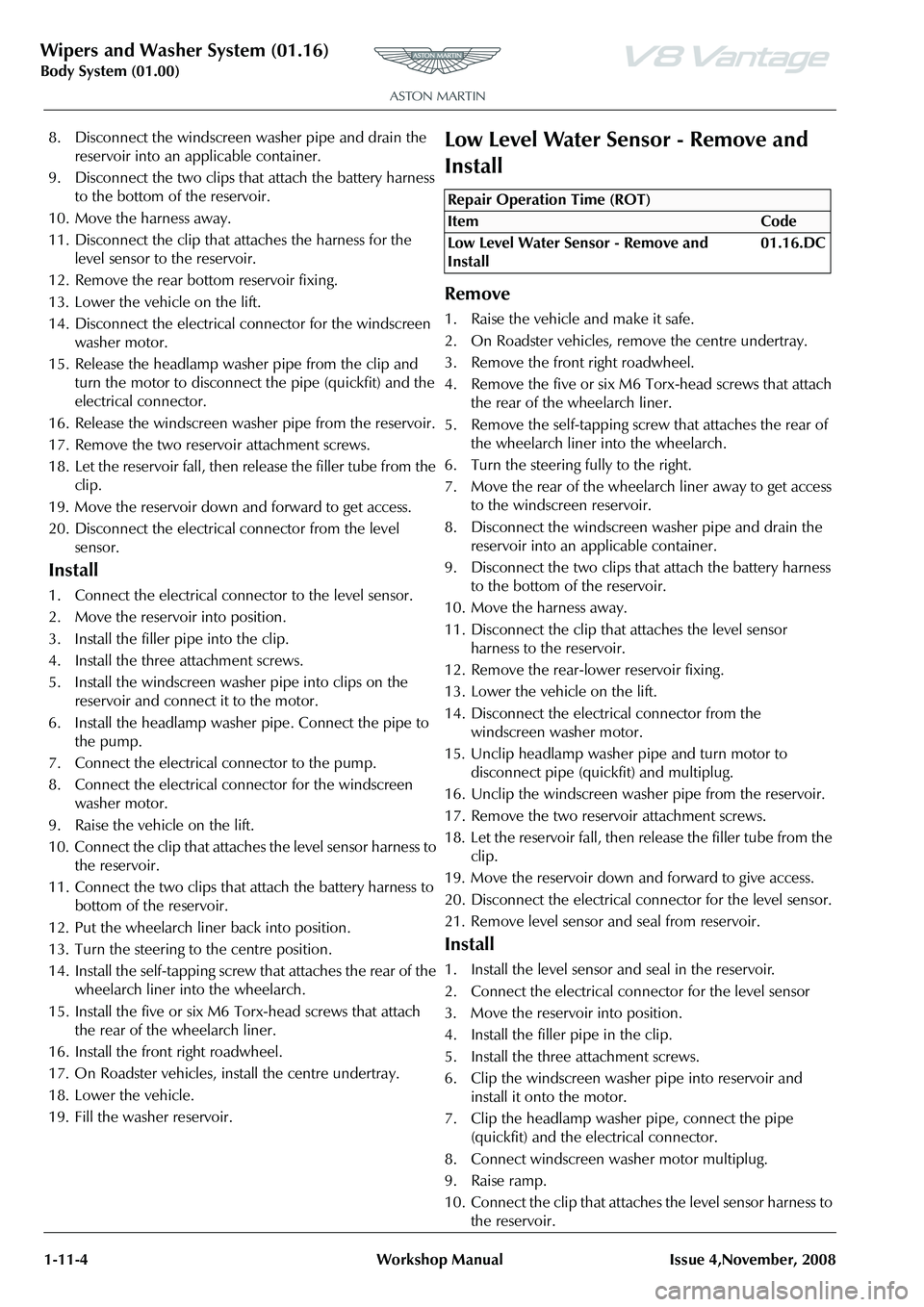
Wipers and Washer System (01.16)
Body System (01.00)1-11-4 Workshop Manual Issue 4,November, 2008
8. Disconnect the windscreen washer pipe and drain the reservoir into an applicable container.
9. Disconnect the two clips that attach the battery harness to the bottom of the reservoir.
10. Move the harness away.
11. Disconnect the clip that attaches the harness for the level sensor to the reservoir.
12. Remove the rear bottom reservoir fixing.
13. Lower the vehicle on the lift.
14. Disconnect the electrical connector for the windscreen washer motor.
15. Release the headlamp washer pipe from the clip and turn the motor to disconnect the pipe (quickfit) and the
electrical connector.
16. Release the windscreen washer pipe from the reservoir.
17. Remove the two reservoir attachment screws.
18. Let the reservoir fall, then release the filler tube from the clip.
19. Move the reservoir down and forward to get access.
20. Disconnect the electrical connector from the level sensor.
Install
1. Connect the electrical connector to the level sensor.
2. Move the reservoir into position.
3. Install the filler pipe into the clip.
4. Install the three attachment screws.
5. Install the windscreen washer pipe into clips on the reservoir and connect it to the motor.
6. Install the headlamp washer pipe. Connect the pipe to the pump.
7. Connect the electrical connector to the pump.
8. Connect the electrical co nnector for the windscreen
washer motor.
9. Raise the vehicle on the lift.
10. Connect the clip that attach es the level sensor harness to
the reservoir.
11. Connect the two clips that attach the battery harness to bottom of the reservoir.
12. Put the wheelarch liner back into position.
13. Turn the steering to the centre position.
14. Install the self-tapping screw that attaches the rear of the wheelarch liner into the wheelarch.
15. Install the five or six M6 Torx-head screws that attach the rear of the wheelarch liner.
16. Install the front right roadwheel.
17. On Roadster vehicles, in stall the centre undertray.
18. Lower the vehicle.
19. Fill the washer reservoir.
Low Level Water Sensor - Remove and
Install
Remove
1. Raise the vehicle and make it safe.
2. On Roadster vehicles, remove the centre undertray.
3. Remove the front right roadwheel.
4. Remove the five or six M6 Torx-head screws that attach the rear of the wheelarch liner.
5. Remove the self-tapping screw that attaches the rear of the wheelarch liner into the wheelarch.
6. Turn the steering fully to the right.
7. Move the rear of the wheelarch liner away to get access to the windscreen reservoir.
8. Disconnect the windscreen washer pipe and drain the reservoir into an applicable container.
9. Disconnect the two clips that attach the battery harness to the bottom of the reservoir.
10. Move the harness away.
11. Disconnect the clip that attaches the level sensor harness to the reservoir.
12. Remove the rear-lower reservoir fixing.
13. Lower the vehicle on the lift.
14. Disconnect the electrical connector from the windscreen washer motor.
15. Unclip headlamp washer pipe and turn motor to disconnect pipe (quickfit) and multiplug.
16. Unclip the windscreen washer pipe from the reservoir.
17. Remove the two reservoir attachment screws.
18. Let the reservoir fall, then release the filler tube from the
clip.
19. Move the reservoir down and forward to give access.
20. Disconnect the electrical connector for the level sensor.
21. Remove level sensor and seal from reservoir.
Install
1. Install the level sensor and seal in the reservoir.
2. Connect the electrical connector for the level sensor
3. Move the reservoir into position.
4. Install the filler pipe in the clip.
5. Install the three attachment screws.
6. Clip the windscreen washer pipe into reservoir and install it onto the motor.
7. Clip the headlamp washer pipe, connect the pipe
(quickfit) and the electrical connector.
8. Connect windscreen washer motor multiplug.
9. Raise ramp.
10. Connect the clip that attaches the level sensor harness to the reservoir.
Repair Operation Time (ROT)
ItemCode
Low Level Water Sensor - Remove and
Install 01.16.DC
Page 135 of 947
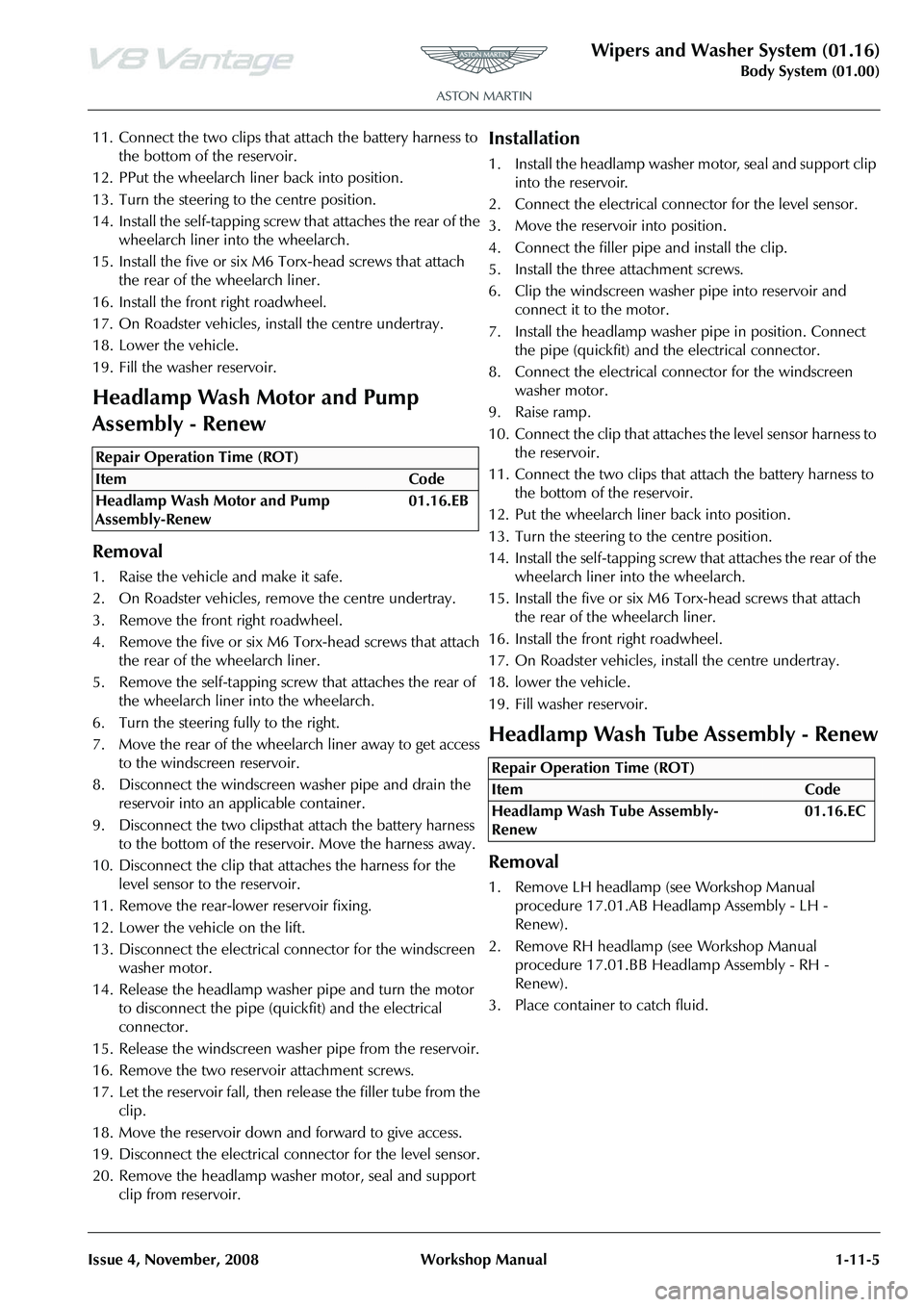
Wipers and Washer System (01.16)
Body System (01.00)
Issue 4, November, 2008 Workshop Manual 1-11-5
11. Connect the two clips that attach the battery harness to the bottom of the reservoir.
12. PPut the wheelarch liner back into position.
13. Turn the steering to the centre position.
14. Install the self-tapping screw that attaches the rear of the wheelarch liner into the wheelarch.
15. Install the five or six M6 Torx-head screws that attach
the rear of the wheelarch liner.
16. Install the front right roadwheel.
17. On Roadster vehicles, in stall the centre undertray.
18. Lower the vehicle.
19. Fill the washer reservoir.
Headlamp Wash Motor and Pump
Assembly - Renew
Removal
1. Raise the vehicle and make it safe.
2. On Roadster vehicles, re move the centre undertray.
3. Remove the front right roadwheel.
4. Remove the five or six M6 Torx-head screws that attach the rear of the wheelarch liner.
5. Remove the self-tapping screw that attaches the rear of the wheelarch liner into the wheelarch.
6. Turn the steering fully to the right.
7. Move the rear of the wheela rch liner away to get access
to the windscreen reservoir.
8. Disconnect the windscreen washer pipe and drain the reservoir into an applicable container.
9. Disconnect the two clipsthat attach the battery harness to the bottom of the reservoir. Move the harness away.
10. Disconnect the clip that attaches the harness for the
level sensor to the reservoir.
11. Remove the rear-lower reservoir fixing.
12. Lower the vehicle on the lift.
13. Disconnect the electrical connector for the windscreen
washer motor.
14. Release the headlamp washer pipe and turn the motor to disconnect the pipe (quickfit) and the electrical
connector.
15. Release the windscreen washer pipe from the reservoir.
16. Remove the two reservoir attachment screws.
17. Let the reservoir fall, then release the filler tube from the clip.
18. Move the reservoir down and forward to give access.
19. Disconnect the electrical co nnector for the level sensor.
20. Remove the headlamp washer motor, seal and support clip from reservoir.
Installation
1. Install the headlamp washer motor, seal and support clip into the reservoir.
2. Connect the electrical connector for the level sensor.
3. Move the reservoir into position.
4. Connect the filler pipe and install the clip.
5. Install the three attachment screws.
6. Clip the windscreen washer pipe into reservoir and connect it to the motor.
7. Install the headlamp washer pipe in position. Connect
the pipe (quickfit) and the electrical connector.
8. Connect the electrical connector for the windscreen washer motor.
9. Raise ramp.
10. Connect the clip that attaches the level sensor harness to the reservoir.
11. Connect the two clips that attach the battery harness to the bottom of the reservoir.
12. Put the wheelarch liner back into position.
13. Turn the steering to the centre position.
14. Install the self-tapping screw that attaches the rear of the wheelarch liner into the wheelarch.
15. Install the five or six M6 Torx-head screws that attach the rear of the wheelarch liner.
16. Install the front right roadwheel.
17. On Roadster vehicles, install the centre undertray.
18. lower the vehicle.
19. Fill washer reservoir.
Headlamp Wash Tube Assembly - Renew
Removal
1. Remove LH headlamp (see Workshop Manual procedure 17.01.AB Headlamp Assembly - LH -
Renew).
2. Remove RH headlamp (see Workshop Manual procedure 17.01.BB Headlamp Assembly - RH -
Renew).
3. Place container to catch fluid.
Repair Operation Time (ROT)
Repair Operation Time (ROT)
Page 215 of 947
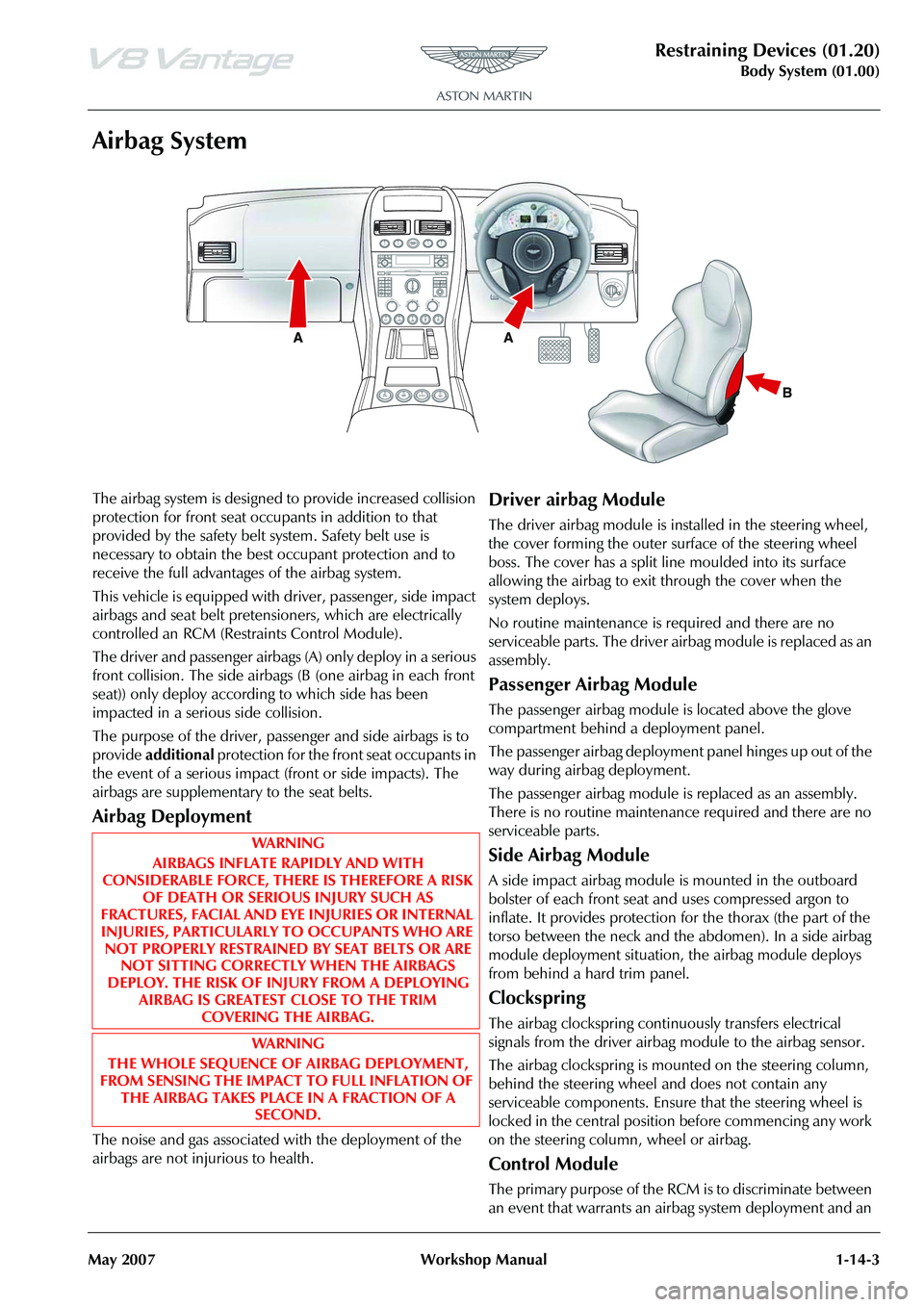
Restraining Devices (01.20)
Body System (01.00)
May 2007 Workshop Manual 1-14-3
Airbag System
The airbag system is designed to provide increased collision
protection for front seat occu pants in addition to that
provided by the safety belt system. Safety belt use is
necessary to obtain the best occupant protection and to
receive the full advantages of the airbag system.
This vehicle is equipped with dr iver, passenger, side impact
airbags and seat belt pretensioners, which are electrically
controlled an RCM (Restraints Control Module).
The driver and passenger airbags (A) only deploy in a serious
front collision. The side airbags (B (one airbag in each front
seat)) only deploy according to which side has been
impacted in a serious side collision.
The purpose of the driver, passenger and side airbags is to
provide additional protection for the front seat occupants in
the event of a serious impact (front or side impacts). The
airbags are supplementary to the seat belts.
Airbag Deployment
The noise and gas associated with the deployment of the
airbags are not injurious to health.
Driver airbag Module
The driver airbag module is installed in the steering wheel,
the cover forming the outer surface of the steering wheel
boss. The cover has a split line moulded into its surface
allowing the airbag to exit through the cover when the
system deploys.
No routine maintenance is required and there are no
serviceable parts. The driver airbag module is replaced as an
assembly.
Passenger Airbag Module
The passenger airbag module is located above the glove
compartment behind a deployment panel.
The passenger airbag deployment panel hinges up out of the
way during airbag deployment.
The passenger airbag module is replaced as an assembly.
There is no routine maintenance required and there are no
serviceable parts.
Side Airbag Module
A side impact airbag module is mounted in the outboard
bolster of each front seat and uses compressed argon to
inflate. It provides protection for the thorax (the part of the
torso between the neck and the abdomen). In a side airbag
module deployment situation, the airbag module deploys
from behind a hard trim panel.
Clockspring
The airbag clockspring continuously transfers electrical
signals from the driver airbag module to the airbag sensor.
The airbag clockspring is mounted on the steering column,
behind the steering wheel and does not contain any
serviceable components. Ensure that the steering wheel is
locked in the central position before commencing any work
on the steering column, wheel or airbag.
Control Module
The primary purpose of the RCM is to discriminate between
an event that warrants an airbag system deployment and an
R P
N
D
WAR NI N G
AIRBAGS INFLATE RAPIDLY AND WITH
CONSIDERABLE FORCE, THERE IS THEREFORE A RISK OF DEATH OR SERIOUS INJURY SUCH AS
FRACTURES, FACIAL AND EY E INJURIES OR INTERNAL
INJURIES, PARTICULARLY TO OCCUPANTS WHO ARE NOT PROPERLY RESTRAINED BY SEAT BELTS OR ARE NOT SITTING CORRECTLY WHEN THE AIRBAGS
DEPLOY. THE RISK OF IN JURY FROM A DEPLOYING
AIRBAG IS GREATEST CLOSE TO THE TRIM COVERING THE AIRBAG.
WAR NI N G
THE WHOLE SEQUENCE OF AIRBAG DEPLOYMENT,
FROM SENSING THE IMPACT TO FULL INFLATION OF THE AIRBAG TAKES PLACE IN A FRACTION OF A SECOND.
Page 216 of 947
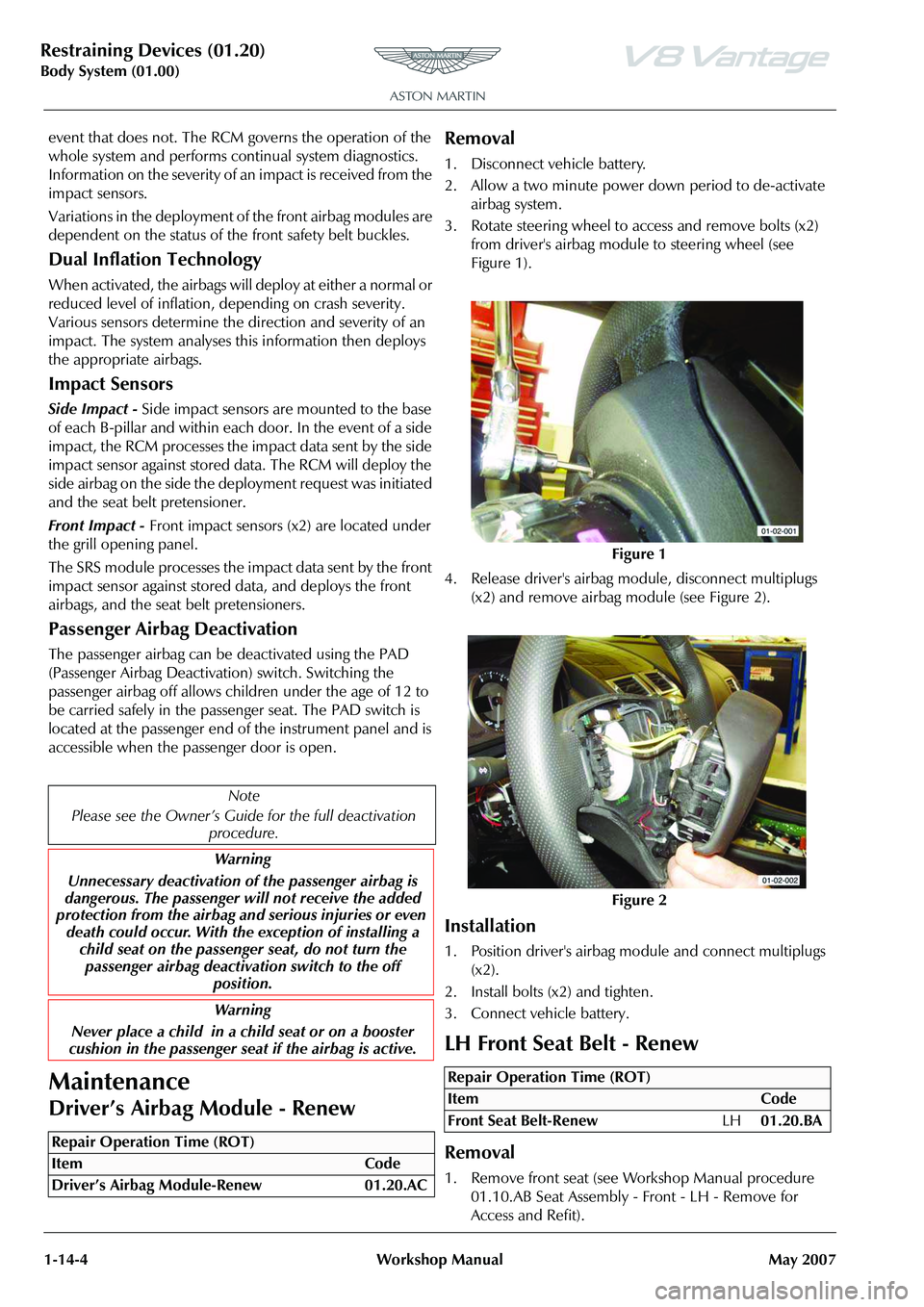
Restraining Devices (01.20)
Body System (01.00)1-14-4 Workshop Manual May 2007
event that does not. The RCM governs the operation of the
whole system and performs continual system diagnostics.
Information on the severity of an impact is received from the
impact sensors.
Variations in the deployment of the front airbag modules are
dependent on the status of the front safety belt buckles.
Dual Inflation Technology
When activated, the airbags will deploy at either a normal or
reduced level of inflation, depending on crash severity.
Various sensors determine the direction and severity of an
impact. The system analyses this information then deploys
the appropriate airbags.
Impact Sensors
Side Impact - Side impact sensors are mounted to the base
of each B-pillar and within each door. In the event of a side
impact, the RCM processes the impact data sent by the side
impact sensor against stored data. The RCM will deploy the
side airbag on the side the deployment request was initiated
and the seat belt pretensioner.
Front Impact - Front impact sensors (x2) are located under
the grill opening panel.
The SRS module processes the impact data sent by the front
impact sensor against stored data, and deploys the front
airbags, and the seat belt pretensioners.
Passenger Airbag Deactivation
The passenger airbag can be deactivated using the PAD
(Passenger Airbag Deactivation) switch. Switching the
passenger airbag off allows children under the age of 12 to
be carried safely in the passenger seat. The PAD switch is
located at the passenger end of the instrument panel and is
accessible when the pa ssenger door is open.
Maintenance
Driver’s Airbag Module - Renew
Removal
1. Disconnect vehicle battery.
2. Allow a two minute power down period to de-activate
airbag system.
3. Rotate steering wheel to access and remove bolts (x2) from driver's airbag module to steering wheel (see
Figure 1).
4. Release driver's airbag mo dule, disconnect multiplugs
(x2) and remove airbag module (see Figure 2).
Installation
1. Position driver's airbag mo dule and connect multiplugs
(x2).
2. Install bolts (x2) and tighten.
3. Connect vehicle battery.
LH Front Seat Belt - Renew
Removal
1. Remove front seat (see Workshop Manual procedure 01.10.AB Seat Assembly - Front - LH - Remove for
Access and Refit).
Note
Please see the Owner’s Guid e for the full deactivation
procedure.
Warning
Unnecessary deactivation of the passenger airbag is
dangerous. The passenger will not receive the added
protection from the airbag and serious injuries or even
death could occur. With the exception of installing a child seat on the passenge r seat, do not turn the
passenger airbag deactiva tion switch to the off
position.
Warning
Never place a child in a child seat or on a booster
cushion in the passenger seat if the airbag is active.
Repair Operation Time (ROT)
Figure 1
Figure 2
Repair Operation Time (ROT)
ItemCode
Front Seat Belt-Renew LH01.20.BA
Page 224 of 947
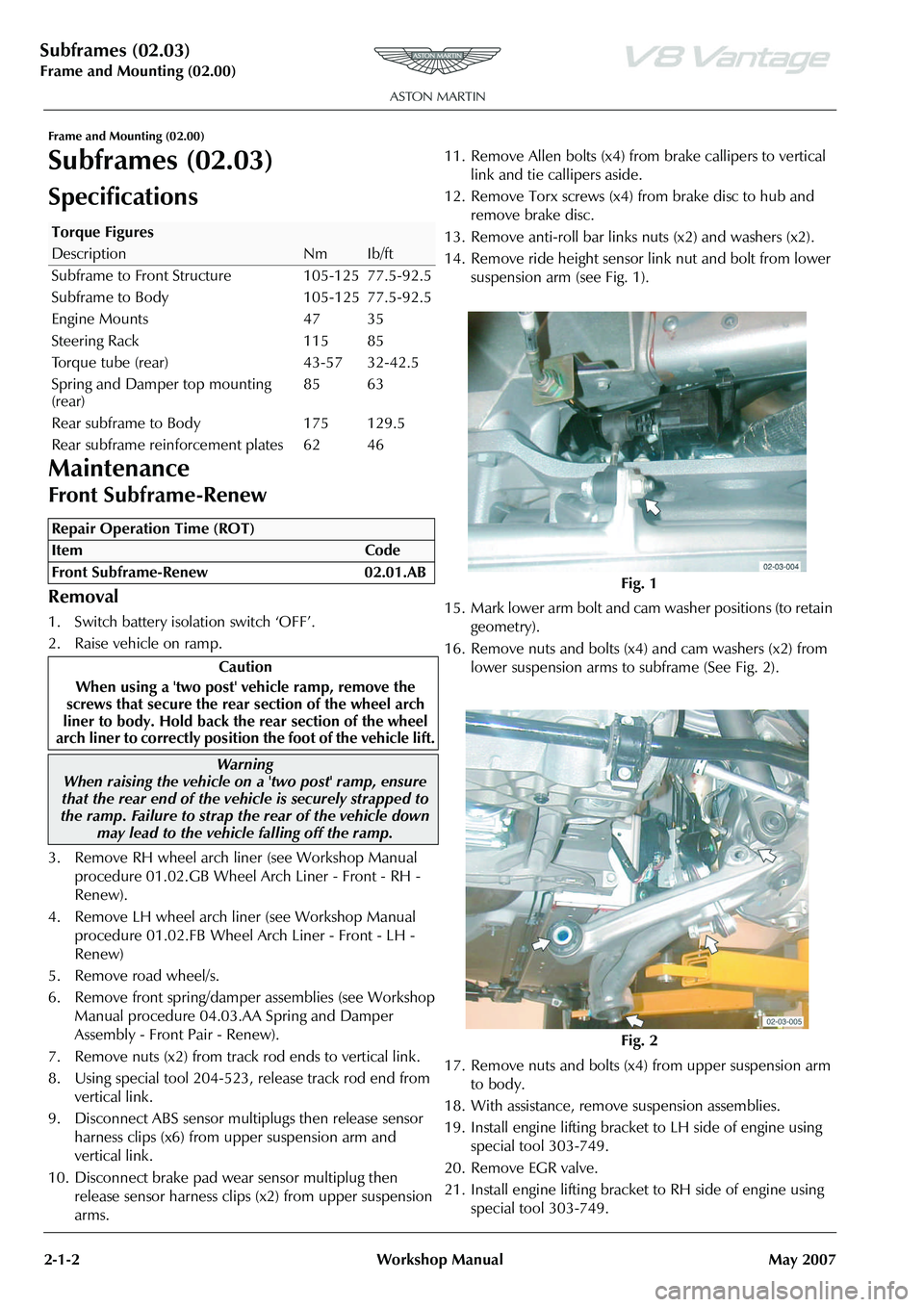
Subframes (02.03)
Frame and Mounting (02.00)
2-1-2 Workshop Manual May 2007
Frame and Mounting (02.00)
Subframes (02.03)
Specifications
Maintenance
Front Subframe-Renew
Removal
1. Switch battery isolation switch ‘OFF’.
2. Raise vehicle on ramp.
3. Remove RH wheel arch liner (see Workshop Manual procedure 01.02.GB Wheel Arch Liner - Front - RH -
Renew).
4. Remove LH wheel arch liner (see Workshop Manual procedure 01.02.FB Wheel Arch Liner - Front - LH -
Renew)
5. Remove road wheel/s.
6. Remove front spring/damper assemblies (see Workshop Manual procedure 04.03.AA Spring and Damper
Assembly - Front Pair - Renew).
7. Remove nuts (x2) from track rod ends to vertical link.
8. Using special tool 204-523, release track rod end from vertical link.
9. Disconnect ABS sensor multiplugs then release sensor harness clips (x6) from upper suspension arm and
vertical link.
10. Disconnect brake pad wear sensor multiplug then release sensor harness clips (x2) from upper suspension
arms. 11. Remove Allen bolts (x4) from brake callipers to vertical
link and tie callipers aside.
12. Remove Torx screws (x4) from brake disc to hub and remove brake disc.
13. Remove anti-roll bar links nuts (x2) and washers (x2).
14. Remove ride height sensor link nut and bolt from lower
suspension arm (see Fig. 1).
15. Mark lower arm bolt and cam washer positions (to retain
geometry).
16. Remove nuts and bolts (x4) and cam washers (x2) from lower suspension arms to subframe (See Fig. 2).
17. Remove nuts and bolts (x4) from upper suspension arm to body.
18. With assistance, remove suspension assemblies.
19. Install engine lifting bracket to LH side of engine using special tool 303-749.
20. Remove EGR valve.
21. Install engine lifting bracket to RH side of engine using special tool 303-749.
Torque Figures
DescriptionNmIb/ft
Subframe to Front Structure 105-125 77.5-92.5
Subframe to Body 105-125 77.5-92.5
Engine Mounts 47 35
Steering Rack 115 85
Torque tube (rear) 43-57 32-42.5
Spring and Damper top mounting
(rear) 85 63
Rear subframe to Body 175 129.5
Rear subframe reinforcement plates 62 46
Repair Operation Time (ROT)
Warning
When raising the vehicle on a 'two post' ramp, ensure
that the rear end of the vehi cle is securely strapped to
the ramp. Failure to strap th e rear of the vehicle down
may lead to the vehicl e falling off the ramp.
Fig. 1
Fig. 2