service oil ASTON MARTIN V8 VANTAGE 2010 Workshop Manual
[x] Cancel search | Manufacturer: ASTON MARTIN, Model Year: 2010, Model line: V8 VANTAGE, Model: ASTON MARTIN V8 VANTAGE 2010Pages: 947, PDF Size: 43.21 MB
Page 7 of 947

Safety Precautions
Issue 5, January 2010 Workshop Manual 0-0-7
Safety Precautions
All service workshops are a source of potential danger and
repair work should only be performed by technically trained
staff following procedures detailed in this manual. A safety
conscious approach to the performance of all service
procedures must be observed at all times. Statutory
requirements governing all aspects of health and safety at
work including directives for the proper use of materials and
equipment must be implemented.
The following contains a list of particular safety precautions
which should be observed; it is not intended to be
exhaustive.
Battery Disconnection
When a service manual procedure requires the vehicle
battery to be disconnected - always physically disconnect
the vehicle battery earth (Negative) lead.
Do not use the ‘Battery Disconnect Switch’.
After reconnecting the vehicle battery the following items
will have to be reset or re-learnt:
•Radio pre-sets
•Windows
• DTCs will be lost
Air Conditioning (A/C) System
Do not break into the A/C refrigeration system until the
refrigerant has been evacuated using the procedure detailed
in this manual. Do not disconne ct any A/C refrigerant system
pipes unless trained and instructed to do so. The refrigerant
used can cause blindness if allowed to contact your eyes.
Chemical Handling and Storage
Chemicals used in the servicing of motor vehicles include
acids, adhesives, antifreeze, brake fluids, coolants, grease,
oil, paint, resin and solvents. Exposure to certain chemicals
through direct contact or inhalation can be fatal.
Potential hazards may also be present through the incorrect
use, storage and handling of chemicals causing a fire risk.
The following precaution s should be observed.
• Strictly adhere to handling and safety information found on containers and labels.
• Do not store chemicals in unlabelled or incorrectly labelled containers.
• Containers used for storing chemicals should not be left open; there is a risk of spilling , or evaporation of fumes
which may be inflammable or toxic.
• Do not mix chemicals unless instructed to do so following manufacturers guidelines.
• Do not inhale chemical materials to determine identity, they may be toxic.
• Do not use petrol, kerosene, diesel fuel, gas oil, thinners or solvents for washing skin.
• Containers whose capacity is over 25 litres (5 gallons) require a bund wall in order to contain spillages. • Chemicals based on solvents such as paint should not be
sprayed in a confined space; work areas used for such
operations should be well ve ntilated and fume extraction
equipment should be utilised.
• Ensure that adequate ventilation is provided when volatile de-greasing agents are being used.
• Avoid splashing the skin, eyes and clothing .
• Clean chemicals from the skin and clothing as soon as
possible after soiling .
• Wear protective clothing such as goggles, non porous gloves and apron when handling battery acid and other
corrosive and toxic substances.
Electrical Equipment
• Ensure that electrical equipment is in safe working order before use.
• Inspect power leads of all mains electrical equipment for damage and security, and check that it is properly earthed.
• Ensure that electrical equipment is protected by a fuse of the correct current rating .
• Disconnect the battery before commencing repair operations to the electrical sy stem, fuel system and engine
or when working beneath the vehicle.
Exhaust Fumes
Engines should not be run in confined spaces as exhaust
fumes contain harmful and to xic substances including
carbon monoxide which can prove fatal if inhaled. Engines
must only be run where there is fume extraction equipment
in operation or where there is adequate ventilation.
Fire Precautions
• Ensure that a suitable form of fire extinguisher is conveniently located near the work area.
• Keep oils, solvents and combustible materials away from naked flames and other sources of ignition.
• Ensure that NO SMOKING signs are posted around areas where combustible materials and vapour may be present
and ensure that the warnings are strictly observed.
• Ensure that dry sand is availabl e to soak up any spillage of
fuel or other flammable solutions.
• Fume extraction equipment must be available and in full working order to remove combustible and toxic vapours.
• All personnel should be aware of the fire drill procedures and precautions. WAR NI NG
DO NOT SMOKE IN THE VICINITY OF VOLATILE DE- GREASING AGENTS.
WAR NI NG
FUME EXTRACTION EQUIPMENT MUST BE IN
OPERATION WHEN SOLVENTS ARE USED E.G. TRICHLOROETHANE, WHITE SPIRIT, SBP3,
METHYLENE CHLORIDE, PERCHLORETHYLENE.
Page 8 of 947
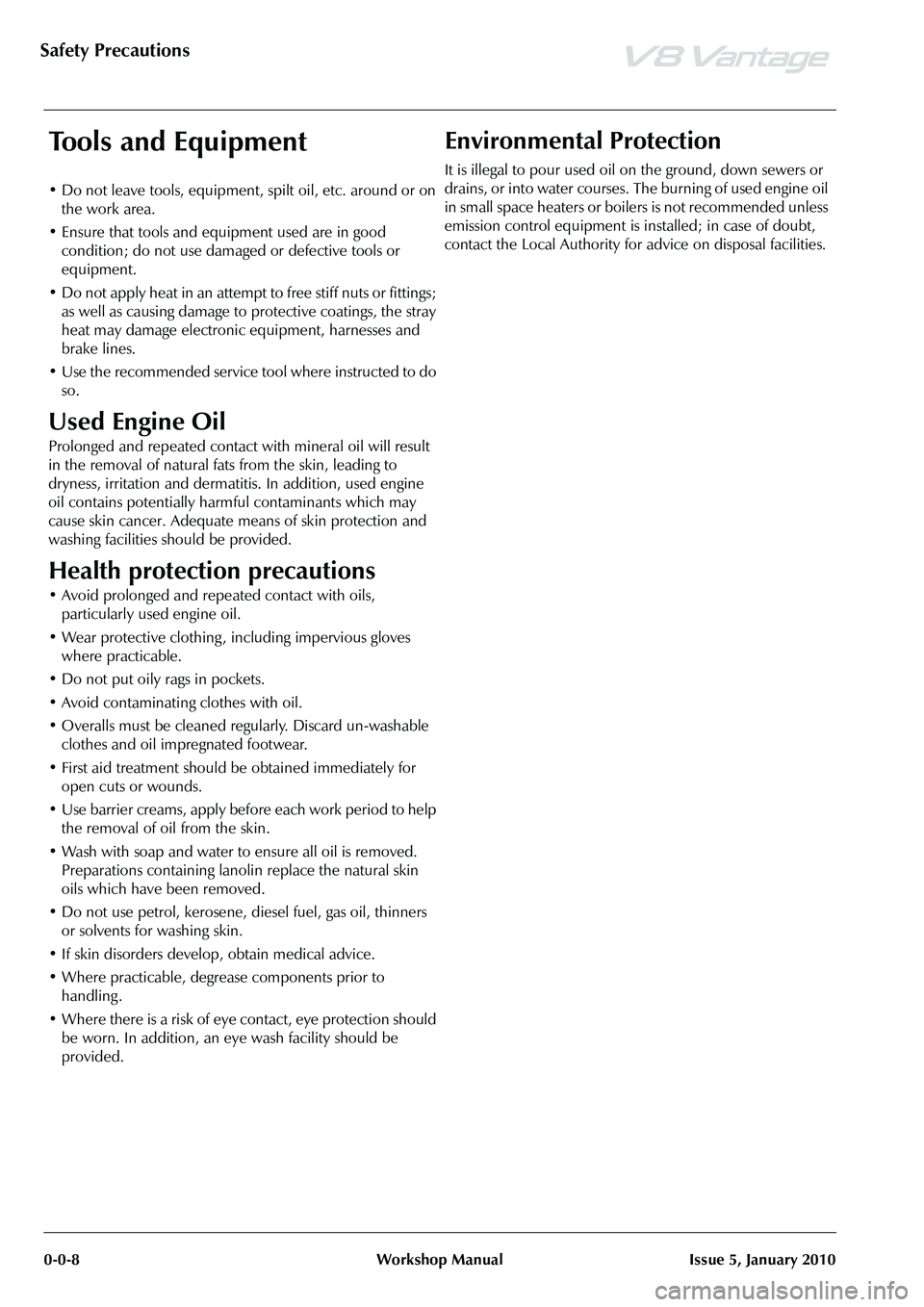
Safety Precautions
0-0-8 Workshop Manual Issue 5, January 2010
Tools and Equipment
• Do not leave tools, equipment, spilt oil, etc. around or on the work area.
• Ensure that tools and equipment used are in good condition; do not use damaged or defective tools or
equipment.
• Do not apply heat in an attempt to free stiff nuts or fittings; as well as causing damage to protective coatings, the stray
heat may damage electronic equipment, harnesses and
brake lines.
• Use the recommended service tool where instructed to do so.
Used Engine Oil
Prolonged and repeated contact with mineral oil will result
in the removal of natural fats from the skin, leading to
dryness, irritation and dermatitis. In addition, used engine
oil contains potentially harmful contaminants which may
cause skin cancer. Adequate means of skin protection and
washing facilities should be provided.
Health protection precautions
• Avoid prolonged and repeated contact with oils, particularly used engine oil.
• Wear protective clothing , including impervious gloves where practicable.
• Do not put oily rags in pockets.
• Avoid contaminating clothes with oil.
• Overalls must be cleaned regularly. Discard un-washable clothes and oil impregnated footwear.
• First aid treatment should be obtained immediately for open cuts or wounds.
• Use barrier creams, apply before each work period to help the removal of oil from the skin.
• Wash with soap and water to ensure all oil is removed. Preparations containing lanolin replace the natural skin
oils which have been removed.
• Do not use petrol, kerosene, diesel fuel, gas oil, thinners or solvents for washing skin.
• If skin disorders develop, obtain medical advice.
• Where practicable, degrease components prior to handling .
• Where there is a risk of eye contact, eye protection should
be worn. In addition, an ey e wash facility should be
provided.
Environmental Protection
It is illegal to pour used oil on the ground, down sewers or
drains, or into water courses. The burning of used engine oil
in small space heaters or boilers is not recommended unless
emission control equipment is in stalled; in case of doubt,
contact the Local Authority for ad vice on disposal facilities.
Page 276 of 947
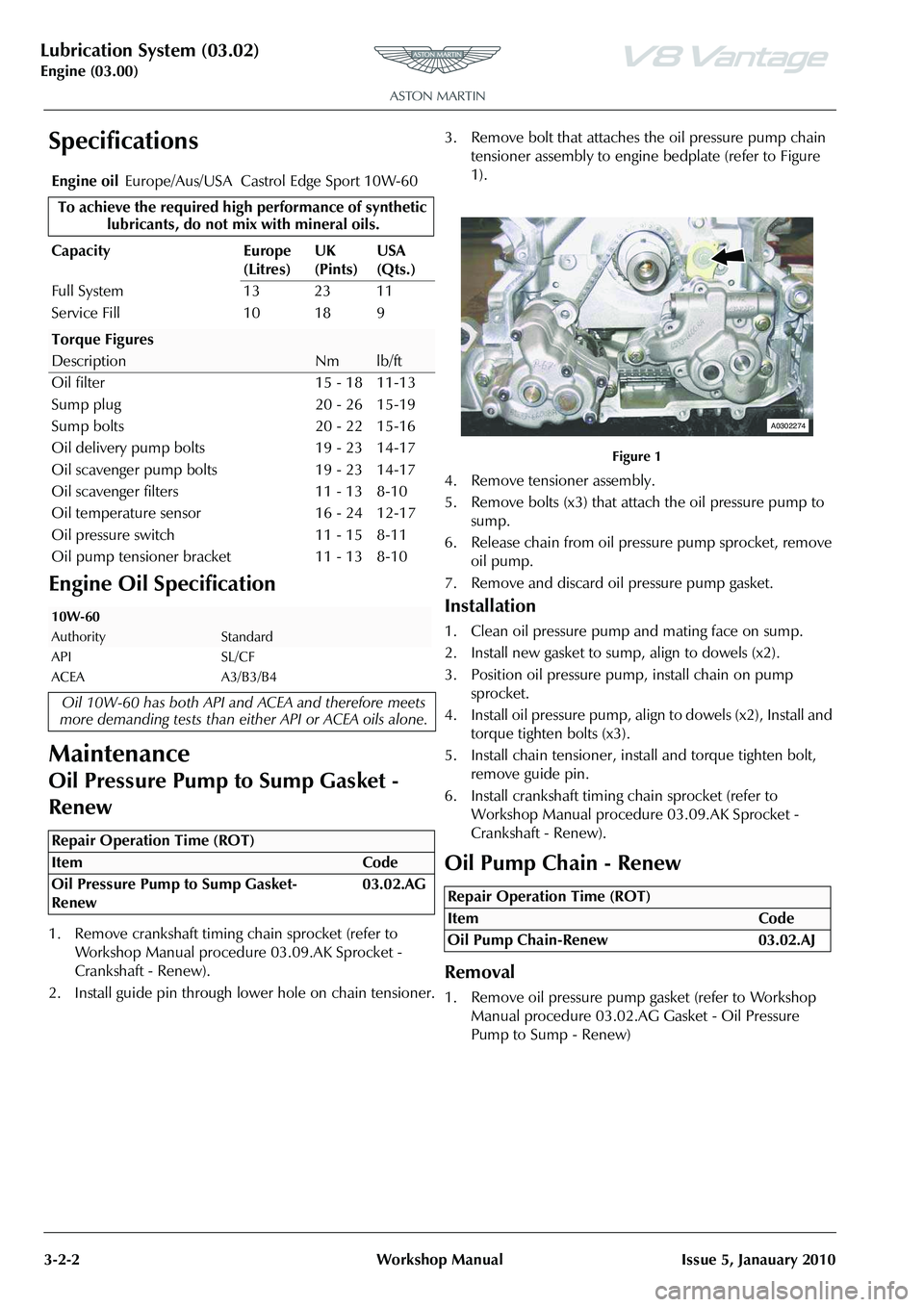
Lubrication System (03.02)
Engine (03.00)3-2-2 Workshop Manual Issue 5, Janauary 2010
Specifications
Engine Oil Specification
Maintenance
Oil Pressure Pump to Sump Gasket -
Renew
1. Remove crankshaft timing chain sprocket (refer to Workshop Manual procedure 03.09.AK Sprocket -
Crankshaft - Renew).
2. Install guide pin through lower hole on chain tensioner. 3. Remove bolt that attaches
the oil pressure pump chain
tensioner assembly to engine bedplate (refer to Figure
1).
4. Remove tensioner assembly.
5. Remove bolts (x3) that attach the oil pressure pump to sump.
6. Release chain from oil pres sure pump sprocket, remove
oil pump.
7. Remove and discard oil pressure pump gasket.
Installation
1. Clean oil pressure pump and mating face on sump.
2. Install new gasket to sump, align to dowels (x2).
3. Position oil pressure pump, install chain on pump sprocket.
4. Install oil pressure pump, align to dowels (x2), Install and torque tighten bolts (x3).
5. Install chain tensioner, install and torque tighten bolt, remove guide pin.
6. Install crankshaft timing chain sprocket (refer to Workshop Manual procedure 03.09.AK Sprocket -
Crankshaft - Renew).
Oil Pump Chain - Renew
Removal
1. Remove oil pressure pump gasket (refer to Workshop Manual procedure 03.02.AG Gasket - Oil Pressure
Pump to Sump - Renew)
Engine oil
Europe/Aus/USA Castrol Edge Sport 10W-60
To achieve the required high performance of synthetic
lubricants, do not mi x with mineral oils.
Capacity Europe (Litres)UK
(Pints)USA
(Qts.)
Full System 13 23 11
Service Fill 10 18 9
Torque Figures
DescriptionNmlb/ft
Oil filter 15 - 18 11-13
Sump plug 20 - 26 15-19
Sump bolts 20 - 22 15-16
Oil delivery pump bolts 19 - 23 14-17
Oil scavenger pump bolts 19 - 23 14-17
Oil scavenger filters 11 - 13 8-10
Oil temperature sensor 16 - 24 12-17
Oil pressure switch 11 - 15 8-11
Oil pump tensioner bracket 11 - 13 8-10
10W-60
AuthorityStandard
API SL/CF
ACEA A3/B3/B4
Oil 10W-60 has both API and ACEA and therefore meets
more demanding tests than eith er API or ACEA oils alone.
Repair Operation Time (ROT)
Figure 1
Repair Operation Time (ROT)
ItemCode
Oil Pump Chain-Renew 03.02.AJ
A0302274
Page 479 of 947
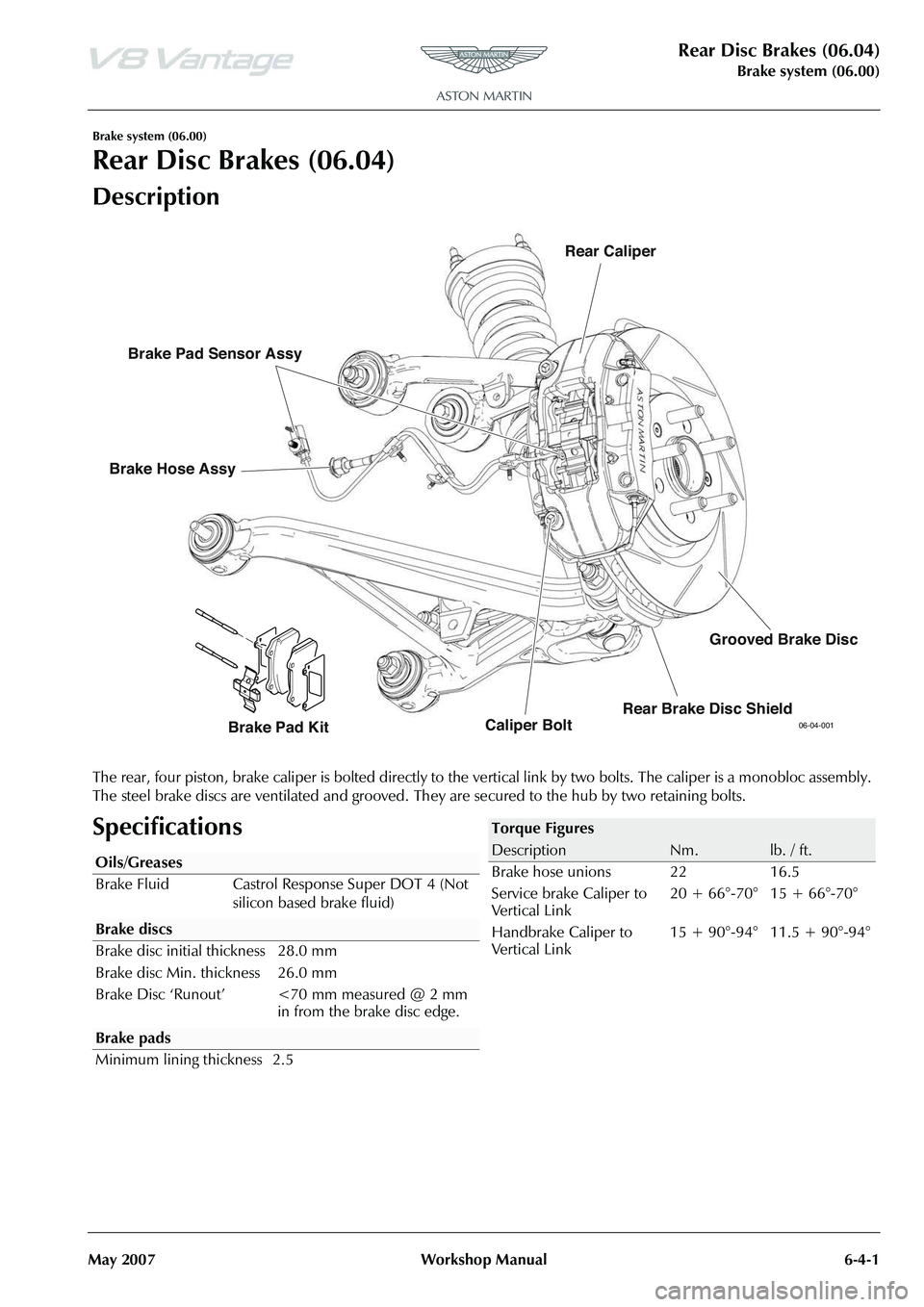
Rear Disc Brakes (06.04)
Brake system (06.00)
May 2007 Workshop Manual 6-4-1
Brake system (06.00)
Rear Disc Brakes (06.04)
Description
The rear, four piston, brake caliper is bolted directly to the ve rtical link by two bolts. The caliper is a monobloc assembly.
The steel brake discs are ventilated and grooved. Th ey are secured to the hub by two retaining bolts.
Specifications
06-04-001Caliper BoltRear Caliper
Brake Hose Assy
Brake Pad Kit
Brake Pad Sensor Assy
Rear Brake Disc ShieldGrooved Brake Disc
Oils/Greases
Brake Fluid Castrol Response Super DOT 4 (Not
silicon based brake fluid)
Brake pads
Minimum lining thickness 2.5
Torque Figures
DescriptionNm.lb. / ft.
Brake hose unions 22 16.5
Service brake Caliper to
Vertical Link 20 + 66°-70° 15 + 66°-70°
Handbrake Caliper to
Vertical Link 15 + 90°-94° 11.5 + 90°-94°
Page 518 of 947
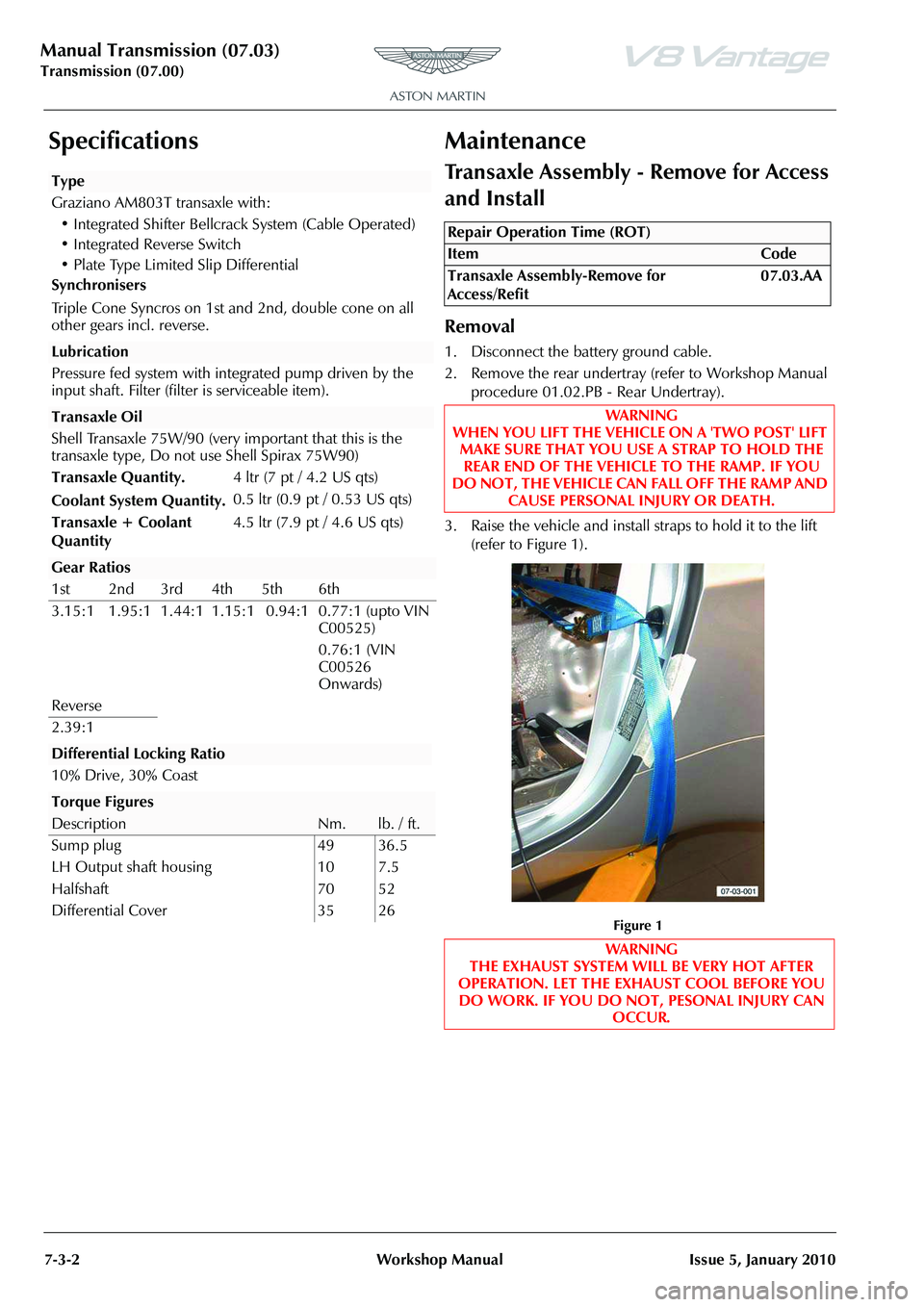
Manual Transmission (07.03)
Transmission (07.00)7-3-2 Workshop Manual Issue 5, January 2010
Specifications Maintenance
Transaxle Assembly - Remove for Access
and Install
Removal
1. Disconnect the battery ground cable.
2. Remove the rear undertray (refer to Workshop Manual procedure 01.02.PB - Rear Undertray).
3. Raise the vehicle and install straps to hold it to the lift (refer to Figure 1).
Figure 1
Type
Graziano AM803T transaxle with:
• Integrated Shifter Bellcrack System (Cable Operated)
• Integrated Reverse Switch
• Plate Type Limited Slip Differential
Synchronisers
Triple Cone Syncros on 1st and 2nd, double cone on all
other gears incl. reverse.
Lubrication
Pressure fed system with integrated pump driven by the
input shaft. Filter (filter is serviceable item).
Transaxle Oil
Shell Transaxle 75W/90 (very important that this is the
transaxle type, Do not use Shell Spirax 75W90)
Transaxle Quantity.
Coolant System Quantity. 4 ltr (7 pt / 4.2 US qts)
0.5 ltr (0.9 pt / 0.53 US qts)
Transaxle + Coolant
Quantity 4.5 ltr (7.9 pt / 4.6 US qts)
Gear Ratios
1st 2nd 3rd 4th 5th 6th
3.15:1 1.95:1 1.44:1 1.15:1 0.94:1 0.77:1 (upto VIN
C00525)
0.76:1 (VIN
C00526
Onwards)
Reverse
2.39:1
Differential Locking Ratio
10% Drive, 30% Coast
Torque Figures
DescriptionNm.lb. / ft.
Sump plug 49 36.5
LH Output shaft housing 10 7.5
Halfshaft 70 52
Differential Cover 35 26
Repair Operation Time (ROT)
ItemCode
Transaxle Assembly-Remove for
Access/Refit 07.03.AA
WAR NI NG
WHEN YOU LIFT THE VEHICLE ON A 'TWO POST' LIFT MAKE SURE THAT YOU USE A STRAP TO HOLD THE REAR END OF THE VEHICLE TO THE RAMP. IF YOU
DO NOT, THE VEHICLE CAN FALL OFF THE RAMP AND CAUSE PERSONAL INJURY OR DEATH.
WAR NI NG
THE EXHAUST SYSTEM WILL BE VERY HOT AFTER
OPERATION. LET THE EXHA UST COOL BEFORE YOU
DO WORK. IF YOU DO NO T, PESONAL INJURY CAN
OCCUR.
Page 557 of 947
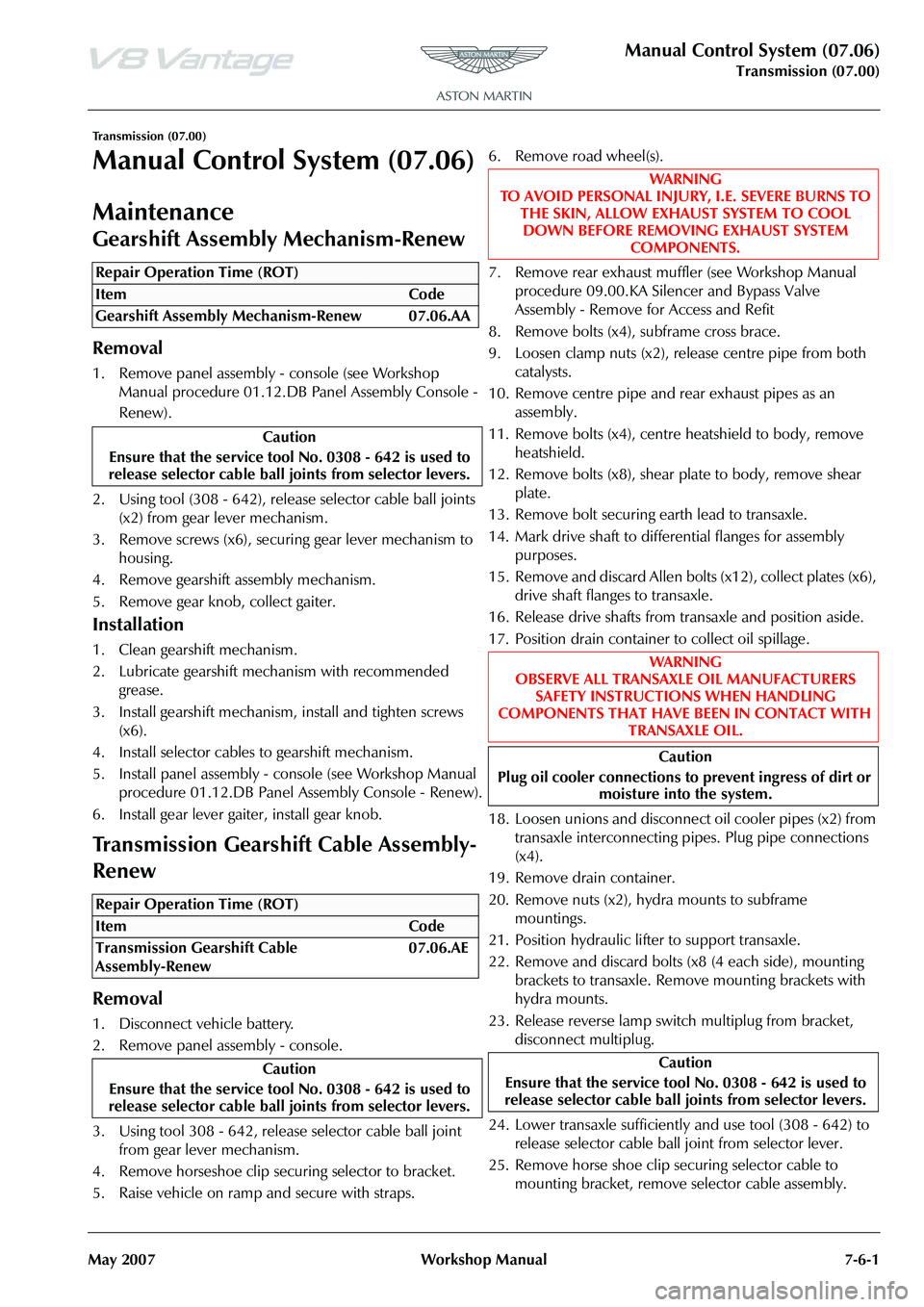
Manual Control System (07.06)
Transmission (07.00)
May 2007 Workshop Manual 7-6-1
Transmission (07.00)
Manual Control System (07.06)
Maintenance
Gearshift Assembly Mechanism-Renew
Removal
1. Remove panel assembly - console (see Workshop Manual procedure 01.12.DB Panel Assembly Console -
Renew).
2. Using tool (308 - 642), release selector cable ball joints (x2) from gear lever mechanism.
3. Remove screws (x6), securi ng gear lever mechanism to
housing.
4. Remove gearshift assembly mechanism.
5. Remove gear knob, collect gaiter.
Installation
1. Clean gearshift mechanism.
2. Lubricate gearshift mechanism with recommended grease.
3. Install gearshift mechanism, install and tighten screws
(x6).
4. Install selector cables to gearshift mechanism.
5. Install panel assembly - console (see Workshop Manual procedure 01.12.DB Panel Assembly Console - Renew).
6. Install gear lever gaiter, install gear knob.
Transmission Gearshift Cable Assembly-
Renew
Removal
1. Disconnect vehicle battery.
2. Remove panel assembly - console.
3. Using tool 308 - 642, release selector cable ball joint from gear lever mechanism.
4. Remove horseshoe clip secu ring selector to bracket.
5. Raise vehicle on ramp and secure with straps. 6. Remove road wheel(s).
7. Remove rear exhaust muffl
er (see Workshop Manual
procedure 09.00.KA Silencer and Bypass Valve
Assembly - Re move for Access and Refit
8. Remove bolts (x4), subframe cross brace.
9. Loosen clamp nuts (x2), release centre pipe from both catalysts.
10. Remove centre pipe and rear exhaust pipes as an
assembly.
11. Remove bolts (x4), centre heatshield to body, remove heatshield.
12. Remove bolts (x8), shear plate to body, remove shear plate.
13. Remove bolt securing earth lead to transaxle.
14. Mark drive shaft to differential flanges for assembly purposes.
15. Remove and discard Allen bolts (x12), collect plates (x6), drive shaft flanges to transaxle.
16. Release drive shafts from transaxle and position aside.
17. Position drain container to collect oil spillage.
18. Loosen unions and disconnect oil cooler pipes (x2) from
transaxle interconnecting pipes. Plug pipe connections
(x4).
19. Remove drain container.
20. Remove nuts (x2), hydra mounts to subframe mountings.
21. Position hydraulic lifter to support transaxle.
22. Remove and discard bolts (x8 (4 each side), mounting brackets to transaxle. Remove mounting brackets with
hydra mounts.
23. Release reverse lamp switch multiplug from bracket, disconnect multiplug.
24. Lower transaxle sufficiently and use tool (308 - 642) to release selector cable ball joint from selector lever.
25. Remove horse shoe clip securing selector cable to mounting bracket, remove selector cable assembly.
Repair Operation Time (ROT)
Repair Operation Time (ROT)
WA R N I N G
TO AVOID PERSONAL INJURY, I.E. SEVERE BURNS TO
THE SKIN, ALLOW EXHAUST SYSTEM TO COOL DOWN BEFORE REMOVING EXHAUST SYSTEM COMPONENTS.
WA R N I N G
OBSERVE ALL TRANSAXLE OIL MANUFACTURERS SAFETY INSTRUCTIONS WHEN HANDLING
COMPONENTS THAT HAVE BEEN IN CONTACT WITH
TRANSAXLE OIL.
Caution
Plug oil cooler connections to prevent ingress of dirt or moisture into the system.
Caution
Ensure that the service tool No. 0308 - 642 is used to
release selector cable ball joints from selector levers.
Page 596 of 947
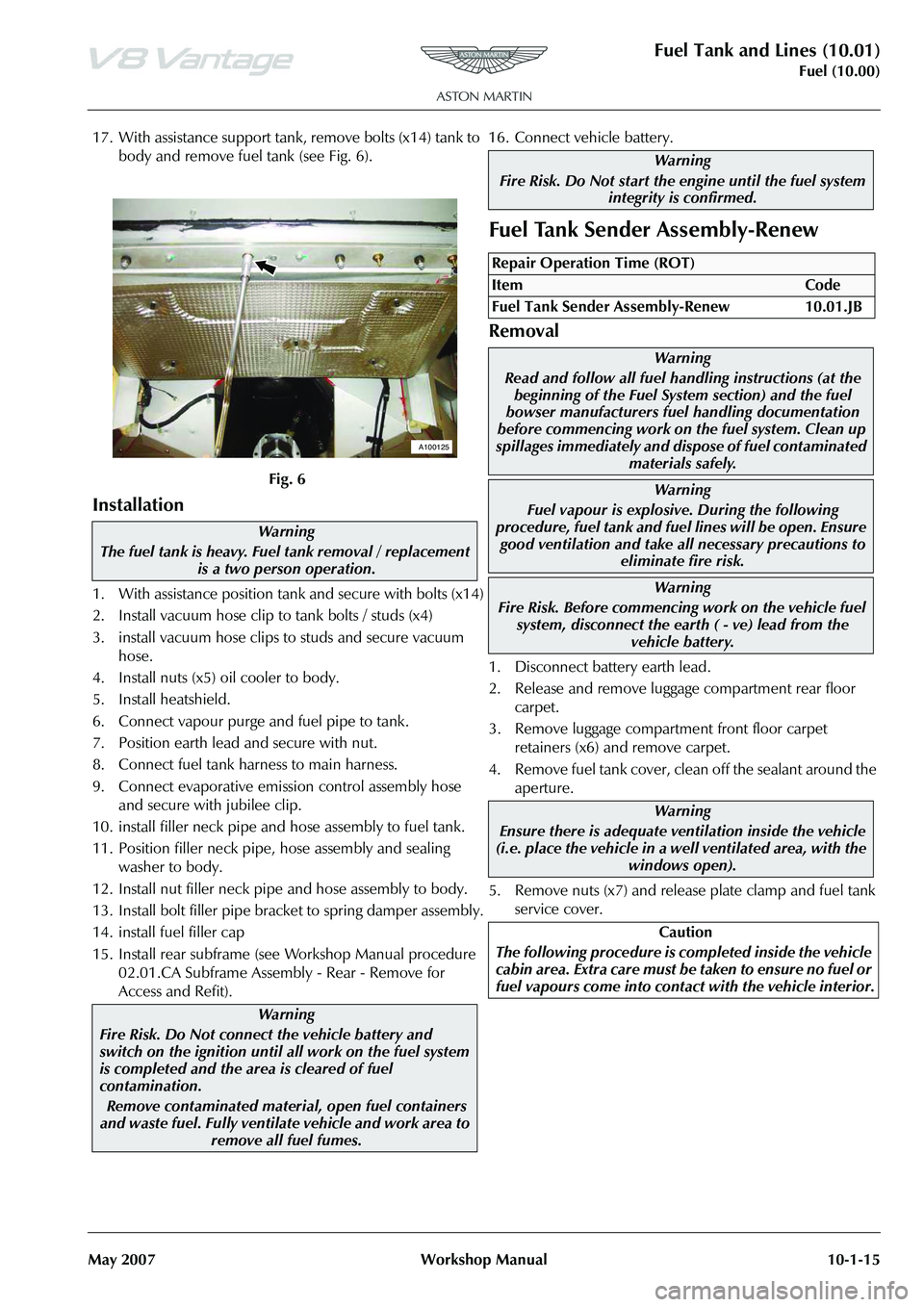
Fuel Tank and Lines (10.01)
Fuel (10.00)
May 2007 Workshop Manual 10-1-15
17. With assistance support tank, remove bolts (x14) tank to body and remove fuel tank (see Fig. 6).
Installation
1. With assistance position tank and secure with bolts (x14)
2. Install vacuum hose clip to tank bolts / studs (x4)
3. install vacuum hose clips to studs and secure vacuum hose.
4. Install nuts (x5) oil cooler to body.
5. Install heatshield.
6. Connect vapour purge and fuel pipe to tank.
7. Position earth lead and secure with nut.
8. Connect fuel tank harness to main harness.
9. Connect evaporative emission control assembly hose and secure with jubilee clip.
10. install filler neck pipe and hose assembly to fuel tank.
11. Position filler neck pipe, hose assembly and sealing washer to body.
12. Install nut filler neck pipe and hose assembly to body.
13. Install bolt filler pipe bracket to spring damper assembly.
14. install fuel filler cap
15. Install rear subframe (see Workshop Manual procedure 02.01.CA Subframe Assembly - Rear - Remove for
Access and Refit). 16. Connect vehicle battery.
Fuel Tank Sender Assembly-Renew
Removal
1. Disconnect battery earth lead.
2. Release and remove luggage compartment rear floor
carpet.
3. Remove luggage compartment front floor carpet retainers (x6) and remove carpet.
4. Remove fuel tank cover, clean off the sealant around the aperture.
5. Remove nuts (x7) and release plate clamp and fuel tank service cover.
Fig. 6
Warning
The fuel tank is heavy. Fuel tank removal / replacement
is a two person operation.
Warning
Fire Risk. Do Not connect the vehicle battery and
switch on the ignition until all work on the fuel system
is completed and the area is cleared of fuel
contamination. Remove contaminated material, open fuel containers
and waste fuel. Fully ventilate vehicle and work area to remove all fuel fumes.
$
Warning
Fire Risk. Do Not start the en gine until the fuel system
integrity is confirmed.
Repair Operation Time (ROT)
Warning
Read and follow all fuel hand ling instructions (at the
beginning of the Fuel System section) and the fuel
bowser manufacturers fuel handling documentation
before commencing work on the fuel system. Clean up
spillages immediately and dispose of fuel contaminated materials safely.
Warning
Fuel vapour is explosiv e. During the following
procedure, fuel tank and fuel lines will be open. Ensure
good ventilation and take all necessary precautions to eliminate fire risk.
Warning
Fire Risk. Before commencing work on the vehicle fuel system, disconnect the earth ( - ve) lead from the vehicle battery.
Warning
Ensure there is adequate ventilation inside the vehicle
(i.e. place the vehicle in a well ventilated area, with the windows open).
Caution
The following procedure is completed inside the vehicle
cabin area. Extra care must be taken to ensure no fuel or
fuel vapours come into contac t with the vehicle interior.
Page 751 of 947
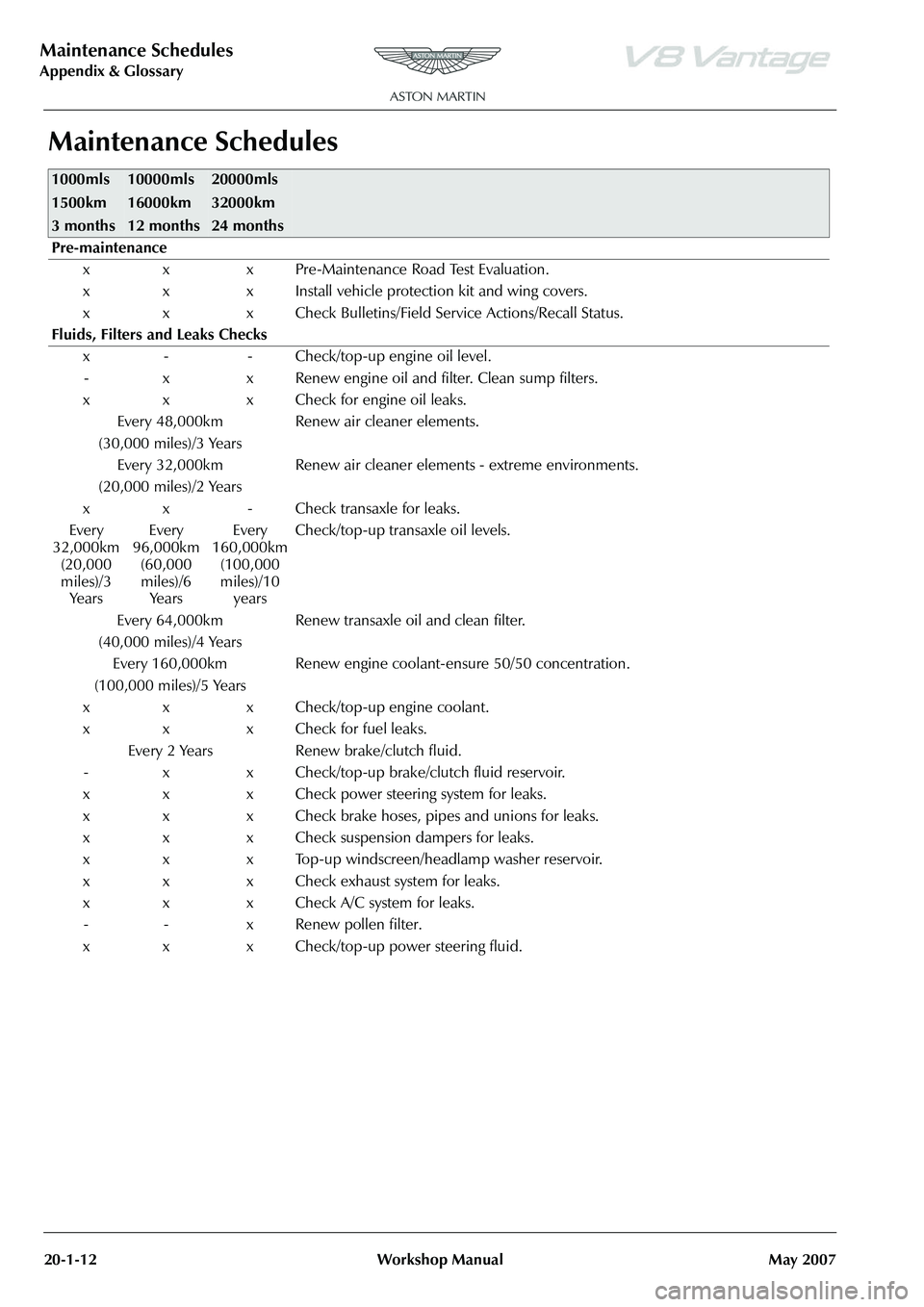
Maintenance Schedules
Appendix & Glossary20-1-12 Workshop Manual May 2007
Maintenance Schedules
1000mls
1500km
3 months10000mls
16000km
12 months20000mls
32000km
24 months
Pre-maintenance
x x x Pre-Maintenance Road Test Evaluation.
x x x Install vehicle protection kit and wing covers.
x x x Check Bulletins/Field Service Actions/Recall Status.
Fluids, Filters and Leaks Checks x - - Check/top-up engine oil level.- x x Renew engine oil and filter. Clean sump filters.
x x x Check for engine oil leaks. Every 48,000km
(30,000 miles)/3 Years Renew air cleaner elements.
Every 32,000km
(20,000 miles)/2 Years Renew air cleaner elements - extreme environments.
x x - Check transaxle for leaks.
Every
32,000km (20,000
miles)/3 Ye a r s Every
96,000km (60,000
miles)/6 Ye a r s Every
160,000km (100,000
miles)/10 years Check/top-up transaxle oil levels.
Every 64,000km
(40,000 miles)/4 Years Renew transaxle oil and clean filter.
Every 160,000km
(100,000 miles)/5 Years Renew engine coolant-ensure 50/50 concentration.
x x x Check/top-up engine coolant.
x x x Check for fuel leaks. Every 2 Years Renew brake/clutch fluid.
- x x Check/top-up brake/clutch fluid reservoir.
x x x Check power steering system for leaks.
x x x Check brake hoses, pipes and unions for leaks.
x x x Check suspension dampers for leaks.
x x x Top-up windscreen/headlamp washer reservoir.
x x x Check exhaust system for leaks.
x x x Check A/C system for leaks. - - x Renew pollen filter.
x x x Check/top-up power steering fluid.
Page 939 of 947
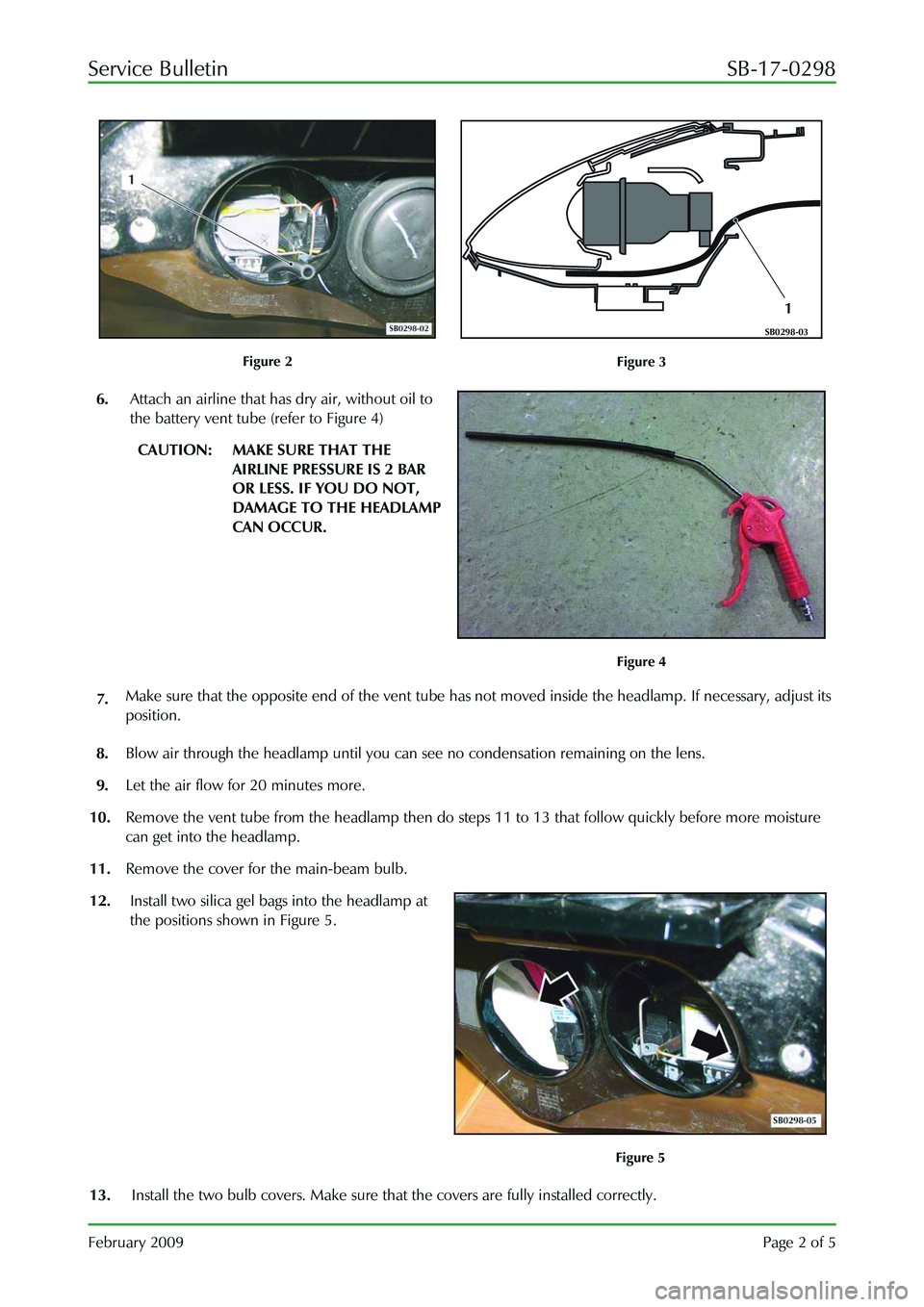
Service Bulletin SB-17-0298
February 2009 Page 2 of 5
Figure 2
1
SB0298-03
Figure 3
6. Attach an airline that has dry air, without oil to
the battery vent tube (refer to Figure 4)
CAUTION: MAKE SURE THAT THE
AIRLINE PRESSURE IS 2 BAR
OR LESS. IF YOU DO NOT,
DAMAGE TO THE HEADLAMP
CAN OCCUR.
Figure 4
7. Make sure that the opposite end of the vent tube has
not moved inside the headlamp. If necessary, adjust its
position.
8. Blow air through the headlamp until you can see no condensation remaining on the lens.
9. Let the air flow for 20 minutes more.
10. Remove the vent tube from the headlamp then do st eps 11 to 13 that follow quickly before more moisture
can get into the headlamp.
11. Remove the cover for the main-beam bulb.
12. Install two silica gel bags into the headlamp at
the positions shown in Figure 5.
Figure 5
13. Install the two bulb covers. Make sure that the covers are fully installed correctly.
Page 941 of 947
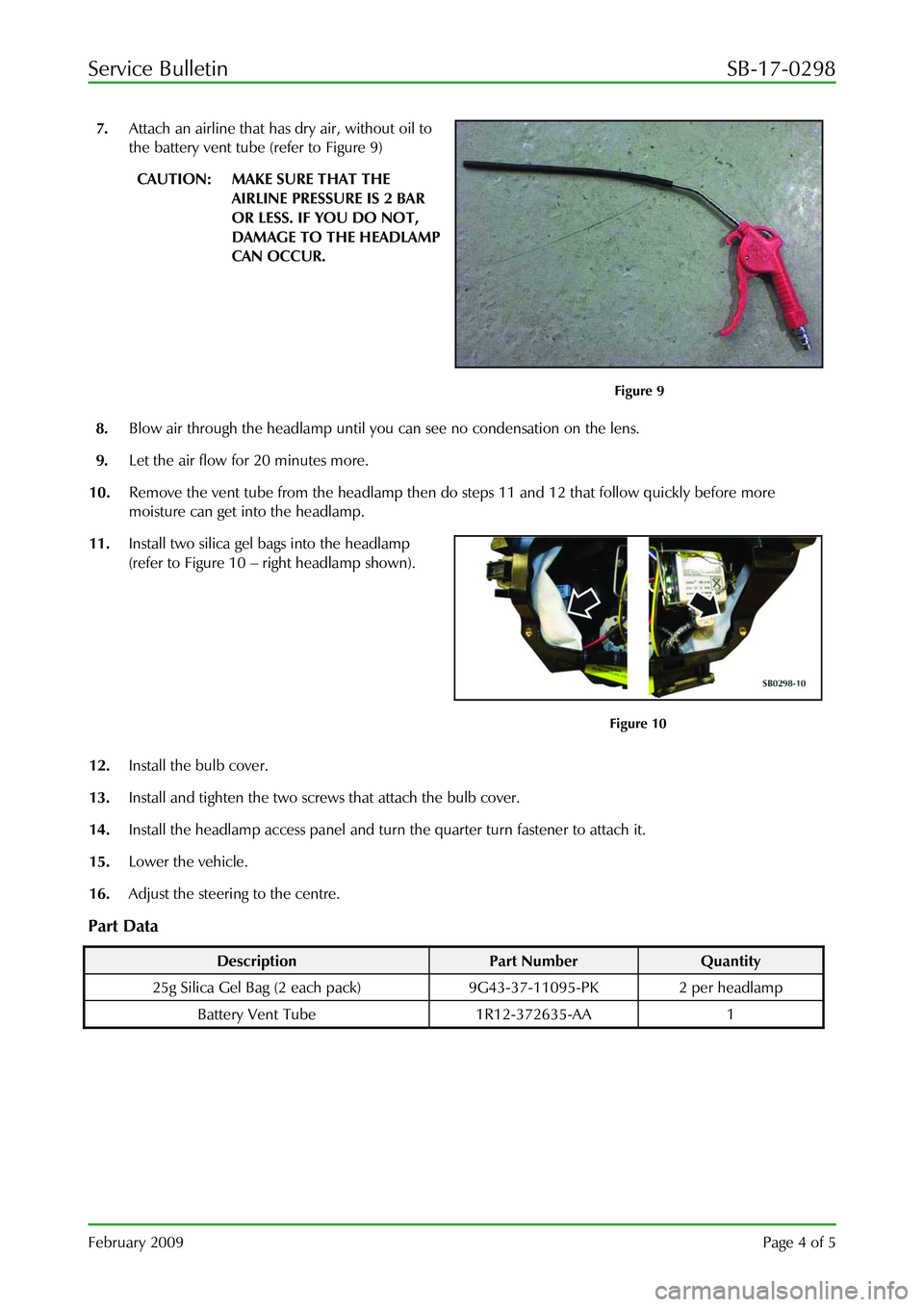
Service Bulletin SB-17-0298
February 2009 Page 4 of 5
7. Attach an airline that has dry air, without oil to
the battery vent tube (refer to Figure 9)
CAUTION: MAKE SURE THAT THE
AIRLINE PRESSURE IS 2 BAR
OR LESS. IF YOU DO NOT,
DAMAGE TO THE HEADLAMP
CAN OCCUR.
Figure 9
8. Blow air through the headlamp until you can see no condensation on the lens.
9. Let the air flow for 20 minutes more.
10. Remove the vent tube from the headlamp then do steps 11 and 12 that follow quickly before more
moisture can get into the headlamp.
11. Install two silica gel bags into the headlamp
(refer to Figure 10 – right headlamp shown).
Figure 10
12. Install the bulb cover.
13. Install and tighten the two screws that attach the bulb cover.
14. Install the headlamp access panel and turn the quarter turn fastener to attach it.
15. Lower the vehicle.
16. Adjust the steering to the centre.
Part Data
Description Part Number Quantity
25g Silica Gel Bag (2 each pa ck) 9G43-37-11095-PK 2 per headlamp
Battery Vent Tube 1R12-372635-AA 1