warning light ASTON MARTIN V8 VANTAGE 2010 Workshop Manual
[x] Cancel search | Manufacturer: ASTON MARTIN, Model Year: 2010, Model line: V8 VANTAGE, Model: ASTON MARTIN V8 VANTAGE 2010Pages: 947, PDF Size: 43.21 MB
Page 3 of 947
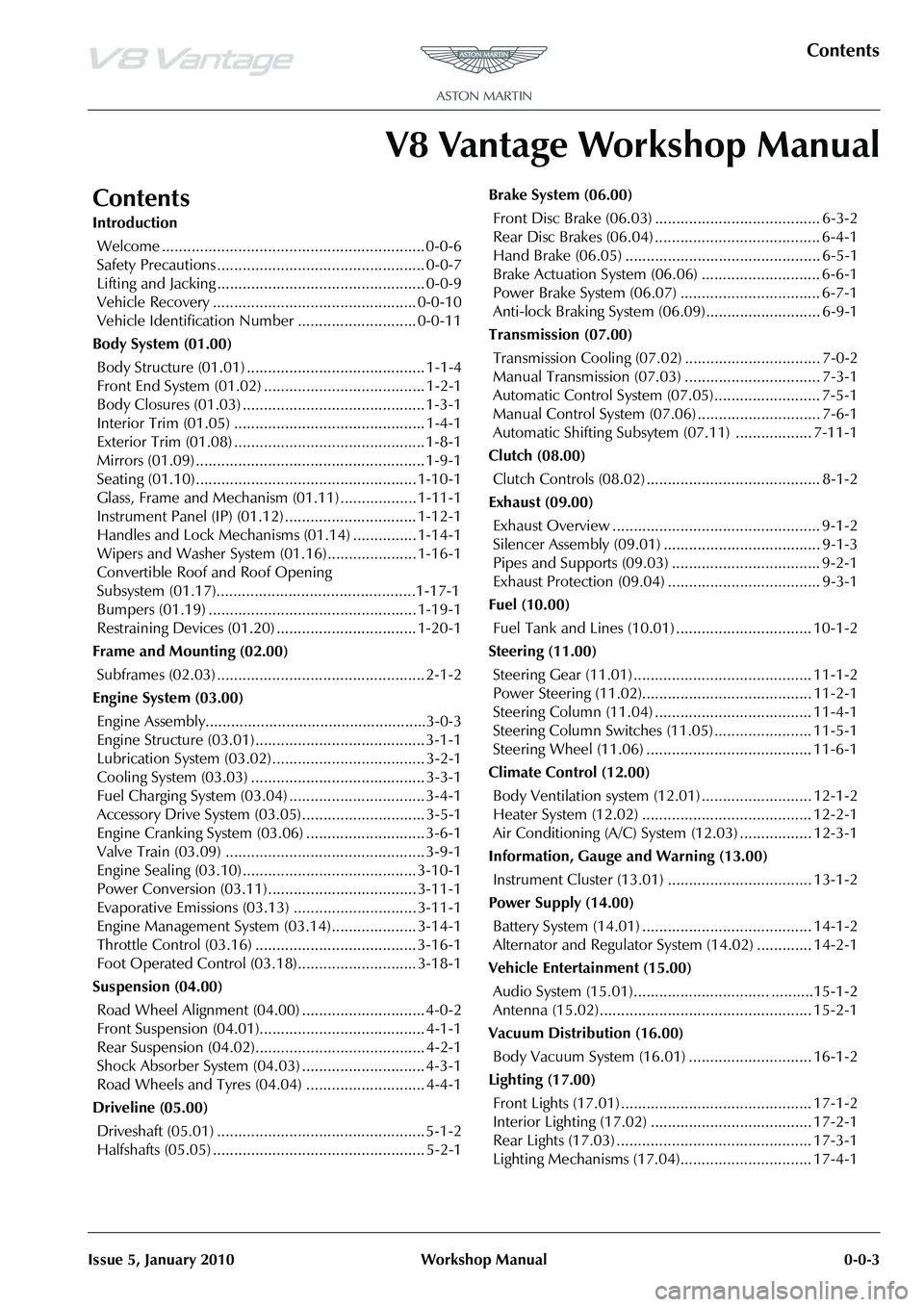
Contents
Issue 5, January 2010 Workshop Manual 0-0-3
V8 Vantage Workshop Manual
Contents
IntroductionWelcome .............................................................. 0-0-6
Safety Precautions ................................................. 0-0-7
Lifting and Jacking ................................................. 0-0-9
Vehicle Recovery ................................................ 0-0-10
Vehicle Identification Number ............................ 0-0-11
Body System (01.00) Body Structure (01.01) .......................................... 1-1-4
Front End System (01.02) ...................................... 1-2-1
Body Closures (01.03) ........................................... 1-3-1
Interior Trim (01.05) ............................................. 1-4-1
Exterior Trim (01.08) ............................................. 1-8-1
Mirrors (01.09) ...................................................... 1-9-1
Seating (01.10).................................................... 1-10-1
Glass, Frame and Mechanism (01.11) .................. 1-11-1
Instrument Panel (IP) (01.12) . .............................. 1-12-1
Handles and Lock Mechanisms (01.14) ............... 1-14-1
Wipers and Washer System (01.16)..................... 1-16-1
Convertible Roof and Roof Opening
Subsystem (01.17)................ ...............................1-17-1
Bumpers (01.19) ................................................. 1-19-1
Restraining Devices (01.20) .... ............................. 1-20-1
Frame and Mounting (02.00) Subframes (02.03) ................................................. 2-1-2
Engine System (03.00) Engine Assembly....................................................3-0-3
Engine Structure (03.01)........................................ 3-1-1
Lubrication System (03.02).................................... 3-2-1
Cooling System (03.03) ......................................... 3-3-1
Fuel Charging System (03.04) ................................ 3-4-1
Accessory Drive System (03.05)............................. 3-5-1
Engine Cranking System (03. 06) ............................ 3-6-1
Valve Train (03.09) ............................................... 3-9-1
Engine Sealing (03.10)......................................... 3-10-1
Power Conversion (03.11)................................... 3-11-1
Evaporative Emissions (03.13) ............................. 3-11-1
Engine Management System (0 3.14).................... 3-14-1
Throttle Control (03.16) ...... ................................ 3-16-1
Foot Operated Control (03.18)............................ 3-18-1
Suspension (04.00) Road Wheel Alignment (04.00) ............................. 4-0-2
Front Suspension (04.01)....................................... 4-1-1
Rear Suspension (04.02)........................................ 4-2-1
Shock Absorber System (04.03) ............................. 4-3-1
Road Wheels and Tyres (04.04) ............................ 4-4-1
Driveline (05.00) Driveshaft (05.01) ................................................. 5-1-2
Halfshafts (05.05) .................................................. 5-2-1 Brake System (06.00)
Front Disc Brake (06.03) ....................................... 6-3-2
Rear Disc Brakes (06.04) ....................................... 6-4-1
Hand Brake (06.05) .............................................. 6-5-1
Brake Actuation System (06.06 ) ............................ 6-6-1
Power Brake System (06.07) ................................. 6-7-1
Anti-lock Braking System (06.09)........................... 6-9-1
Transmission (07.00) Transmission Cooling (07.02) ................................ 7-0-2
Manual Transmission (07.03) ................................ 7-3-1
Automatic Control System (07.05)......................... 7-5-1
Manual Control System (07.06) ............................. 7-6-1
Automatic Shifting Subsytem (07.11) .................. 7-11-1
Clutch (08.00) Clutch Controls (08.02) ......................................... 8-1-2
Exhaust (09.00) Exhaust Overview ................................................. 9-1-2
Silencer Assembly (09.01) ..................................... 9-1-3
Pipes and Supports (09.03) ................................... 9-2-1
Exhaust Protection (09.04) .................................... 9-3-1
Fuel (10.00) Fuel Tank and Lines (10.01) ................................ 10-1-2
Steering (11.00) Steering Gear (11.01) .......................................... 11-1-2
Power Steering (11.02)........................................ 11-2-1
Steering Column (11.04) ..................................... 11-4-1
Steering Column Switches (1 1.05) ....................... 11-5-1
Steering Wheel (11.06) ....................................... 11-6-1
Climate Control (12.00) Body Ventilation system (12.01) .......................... 12-1-2
Heater System (12.02) ........................................ 12-2-1
Air Conditioning (A/C) System (12.03) ................. 12-3-1
Information, Gauge and Warning (13.00) Instrument Cluster (13.01) .................................. 13-1-2
Power Supply (14.00) Battery System (14.01) ........................................ 14-1-2
Alternator and Regulator System (14.02) ............. 14-2-1
Vehicle Entertainment (15.00) Audio System (15.01)................................ ..........15-1-2
Antenna (15.02).................................................. 15-2-1
Vacuum Distribution (16.00) Body Vacuum System (16.01) ............................. 16-1-2
Lighting (17.00) Front Lights (17.01) ............................................. 17-1-2
Interior Lighting (17.02) ...................................... 17-2-1
Rear Lights (17.03) .............................................. 17-3-1
Lighting Mechanisms (17.04). .............................. 17-4-1
Page 10 of 947
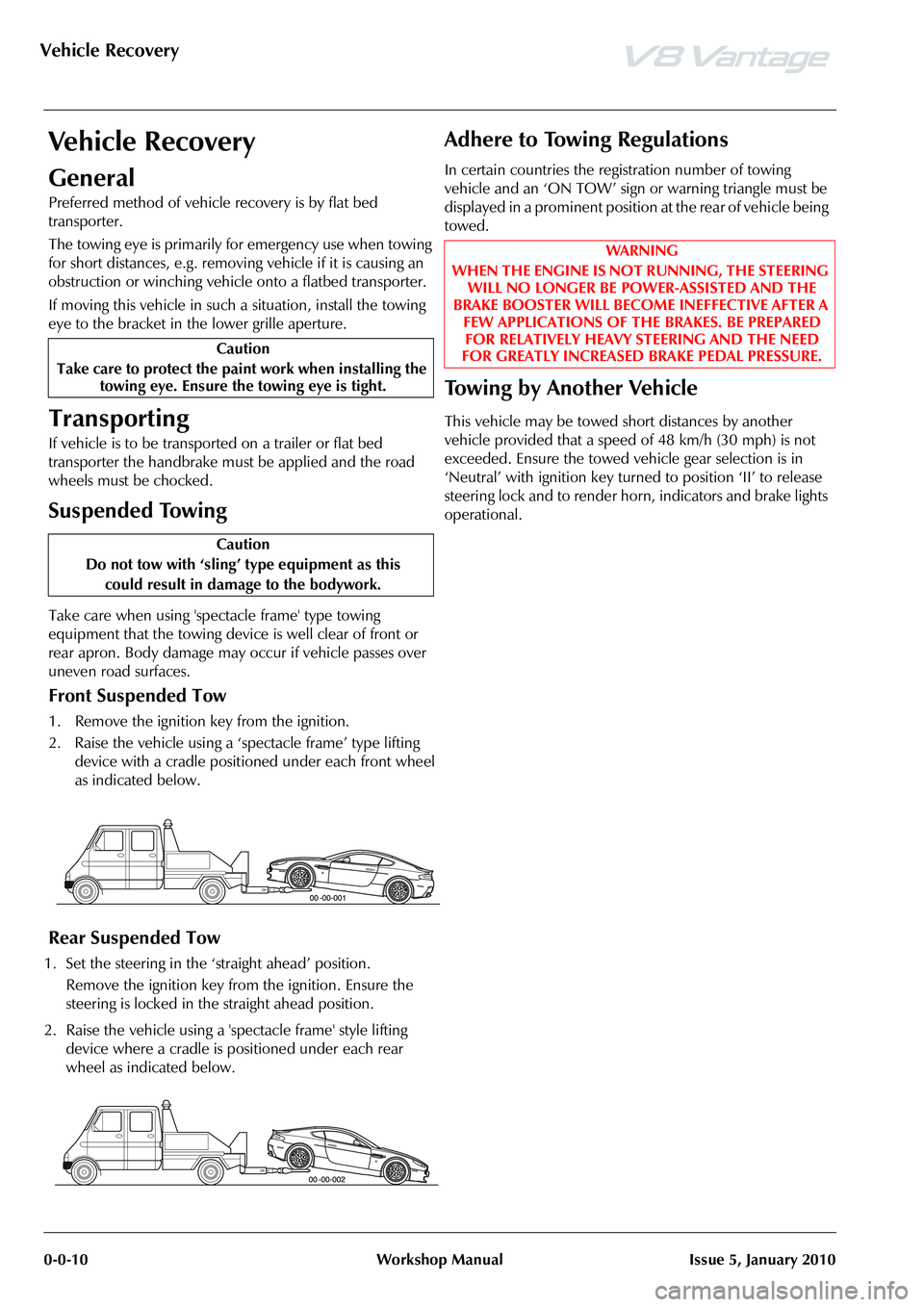
Vehicle Recovery
0-0-10 Workshop Manual Issue 5, January 2010
Vehicle Recovery
General
Preferred method of vehicle recovery is by flat bed
transporter.
The towing eye is primarily for emergency use when towing
for short distances, e.g. removing vehicle if it is causing an
obstruction or winching vehicl e onto a flatbed transporter.
If moving this vehicle in such a situation, install the towing
eye to the bracket in the lower grille aperture.
Transporting
If vehicle is to be transported on a trailer or flat bed
transporter the handbrake must be applied and the road
wheels must be chocked.
Suspended Towing
Take care when using 'spectacle frame' type towing
equipment that the towing device is well clear of front or
rear apron. Body damage may occur if vehicle passes over
uneven road surfaces.
Front Suspended Tow
1. Remove the ignition key from the ignition.
2. Raise the vehicle using a ‘spectacle frame’ type lifting device with a cradle positioned under each front wheel
as indicated below.
Rear Suspended Tow
1. Set the steering in the ‘straight ahead’ position.
Remove the ignition key from the ignition. Ensure the
steering is locked in the straight ahead position.
2. Raise the vehicle using a 'spectacle frame' style lifting device where a cradle is positioned under each rear
wheel as indicated below.
Adhere to Towing Regulations
In certain countries the regi stration number of towing
vehicle and an ‘ON TOW’ sign or warning triangle must be
displayed in a prominent position at the rear of vehicle being
towed.
To w i n g b y A n o t h e r V e h i c l e
This vehicle may be towed short distances by another
vehicle provided that a speed of 48 km/h (30 mph) is not
exceeded. Ensure the towed vehicle gear selection is in
‘Neutral’ with ignition key turned to position ‘II’ to release
steering lock and to render hor n, indicators and brake lights
operational.
Caution
Take care to protect the paint work when installing the towing eye. Ensure the towing eye is tight.
Caution
Do not tow with ‘sling’ type equipment as this
could result in damage to the bodywork.
WAR NI NG
WHEN THE ENGINE IS NOT RUNNING, THE STEERING WILL NO LONGER BE POWER-ASSISTED AND THE
BRAKE BOOSTER WILL BECOME INEFFECTIVE AFTER A FEW APPLICATIONS OF TH E BRAKES. BE PREPARED
FOR RELATIVELY HEAVY STEERING AND THE NEED
FOR GREATLY INCREASED BRAKE PEDAL PRESSURE.
Page 460 of 947
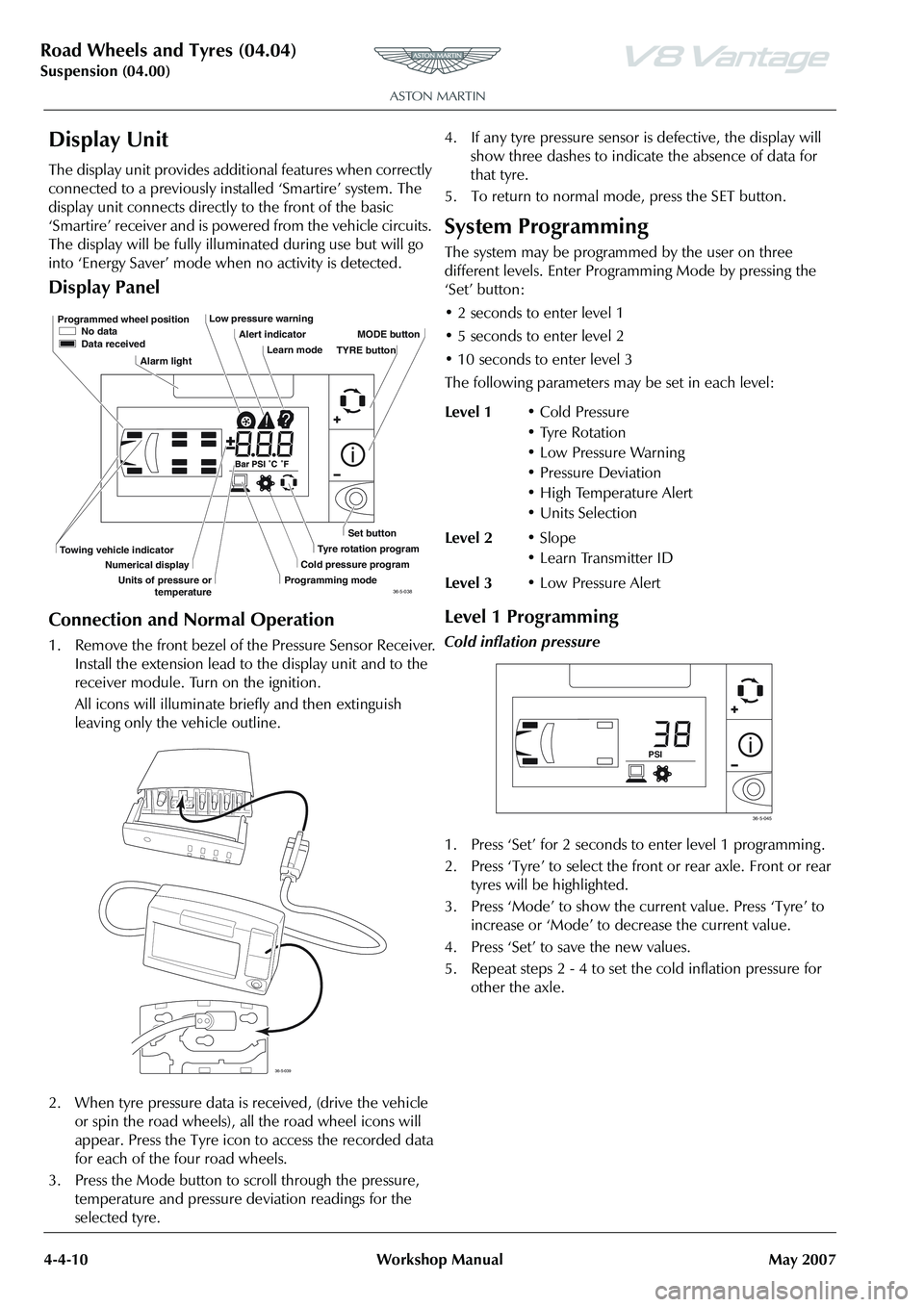
Road Wheels and Tyres (04.04)
Suspension (04.00)4-4-10 Workshop Manual May 2007
Display Unit
The display unit provides additional features when correctly
connected to a previously installed ‘Smartire’ system. The
display unit connects directly to the front of the basic
‘Smartire’ receiver and is powered from the vehicle circuits.
The display will be fully illu minated during use but will go
into ‘Energy Saver’ mode when no activity is detected.
Display Panel
Connection and Normal Operation
1. Remove the front bezel of the Pressure Sensor Receiver. Install the extension lead to the display unit and to the
receiver module. Turn on the ignition.
All icons will illuminate briefly and then extinguish
leaving only the vehicle outline.
2. When tyre pressure data is received, (drive the vehicle
or spin the road wheels), all the road wheel icons will
appear. Press the Tyre icon to access the recorded data
for each of the four road wheels.
3. Press the Mode button to scroll through the pressure, temperature and pressure deviation readings for the
selected tyre. 4. If any tyre pressure sensor is defective, the display will
show three dashes to indicate the absence of data for
that tyre.
5. To return to normal mode, press the SET button.
System Programming
The system may be programmed by the user on three
different levels. Enter Progra mming Mode by pressing the
‘Set’ button:
• 2 seconds to enter level 1
• 5 seconds to enter level 2
• 10 seconds to enter level 3
The following parameters ma y be set in each level:
Level 1 Programming
Cold inflation pressure
1. Press ‘Set’ for 2 seconds to enter level 1 programming .
2. Press ‘Tyre’ to select the front or rear axle. Front or rear
tyres will be highlighted.
3. Press ‘Mode’ to show the current value. Press ‘Tyre’ to increase or ‘Mode’ to decrease the current value.
4. Press ‘Set’ to save the new values.
5. Repeat steps 2 - 4 to set the cold inflation pressure for other the axle.
Programmed wheel position No data
Data received
Alarm light Low pressure warning
Alert indicatorLearn mode MODE button
Set button
Tyre rotation program
Cold pressure program
Programming mode
Towing vehicle indicator
Numerical display
Units of pressure or temperature TYRE button
36-5-038
36-5-039
Level 1
• Cold Pressure
• Tyre Rotation
• Low Pressure Warning
• Pressure Deviation
• High Temperature Alert
•Units Selection
Level 2 •Slope
• Learn Transmitter ID
Level 3 • Low Pressure Alert
PSI
36-5-045
Page 484 of 947
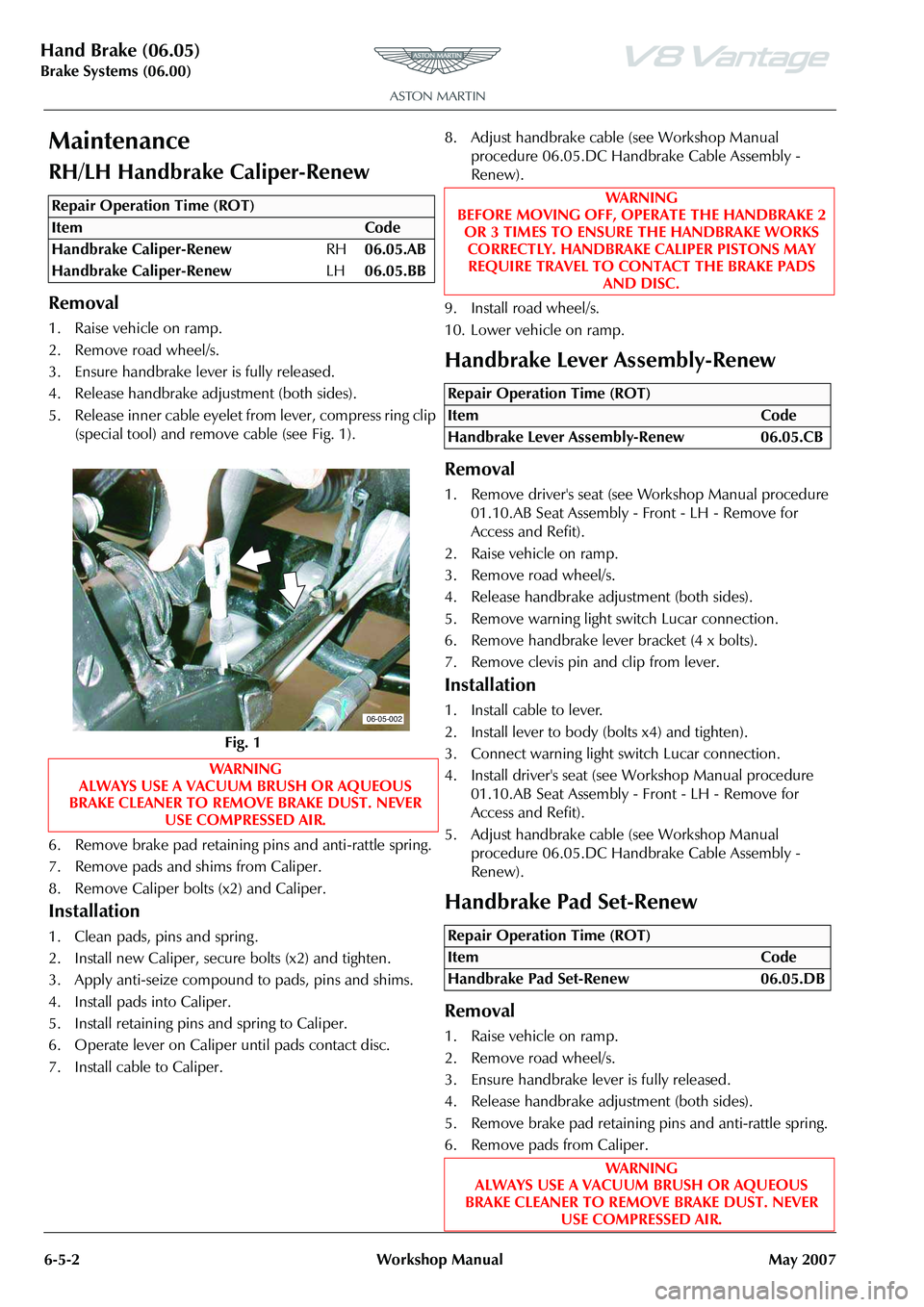
Hand Brake (06.05)
Brake Systems (06.00)6-5-2 Workshop Manual May 2007
Maintenance
RH/LH Handbrake Caliper-Renew
Removal
1. Raise vehicle on ramp.
2. Remove road wheel/s.
3. Ensure handbrake leve r is fully released.
4. Release handbrake adjustment (both sides).
5. Release inner cable eyelet from lever, compress ring clip (special tool) and remove cable (see Fig. 1).
6. Remove brake pad retaining pins and anti-rattle spring.
7. Remove pads and shims from Caliper.
8. Remove Caliper bolts (x2) and Caliper.
Installation
1. Clean pads, pins and spring .
2. Install new Caliper, secu re bolts (x2) and tighten.
3. Apply anti-seize compound to pads, pins and shims.
4. Install pads into Caliper.
5. Install retaining pins and spring to Caliper.
6. Operate lever on Caliper until pads contact disc.
7. Install cable to Caliper. 8. Adjust handbrake cable (see Workshop Manual
procedure 06.05.DC Handbrake Cable Assembly -
Renew).
9. Install road wheel/s.
10. Lower vehicle on ramp.
Handbrake Lever Assembly-Renew
Removal
1. Remove driver's seat (see Workshop Manual procedure 01.10.AB Seat Assembly - Front - LH - Remove for
Access and Refit).
2. Raise vehicle on ramp.
3. Remove road wheel/s.
4. Release handbrake adjustment (both sides).
5. Remove warning light switch Lucar connection.
6. Remove handbrake lever bracket (4 x bolts).
7. Remove clevis pin and clip from lever.
Installation
1. Install cable to lever.
2. Install lever to body (bolts x4) and tighten).
3. Connect warning light switch Lucar connection.
4. Install driver's seat (see Workshop Manual procedure 01.10.AB Seat Assembly - Front - LH - Remove for
Access and Refit).
5. Adjust handbrake cable (see Workshop Manual procedure 06.05.DC Handbrake Cable Assembly -
Renew).
Handbrake Pad Set-Renew
Removal
1. Raise vehicle on ramp.
2. Remove road wheel/s.
3. Ensure handbrake lever is fully released.
4. Release handbrake adjustment (both sides).
5. Remove brake pad retaining pins and anti-rattle spring.
6. Remove pads from Caliper.
Repair Operation Time (ROT)
06-05-002
WAR NI NG
BEFORE MOVING OFF, OPERATE THE HANDBRAKE 2
OR 3 TIMES TO ENSURE THE HANDBRAKE WORKS CORRECTLY. HANDBRAKE CALIPER PISTONS MAY REQUIRE TRAVEL TO CONTACT THE BRAKE PADS
AND DISC.
Repair Operation Time (ROT)
ItemCode
Handbrake Lever Assembly-Renew 06.05.CB
Repair Operation Time (ROT)
ItemCode
Handbrake Pad Set-Renew 06.05.DB
WAR NI NG
ALWAYS USE A VACUUM BRUSH OR AQUEOUS
BRAKE CLEANER TO REMOVE BRAKE DUST. NEVER USE COMPRESSED AIR.
Page 485 of 947
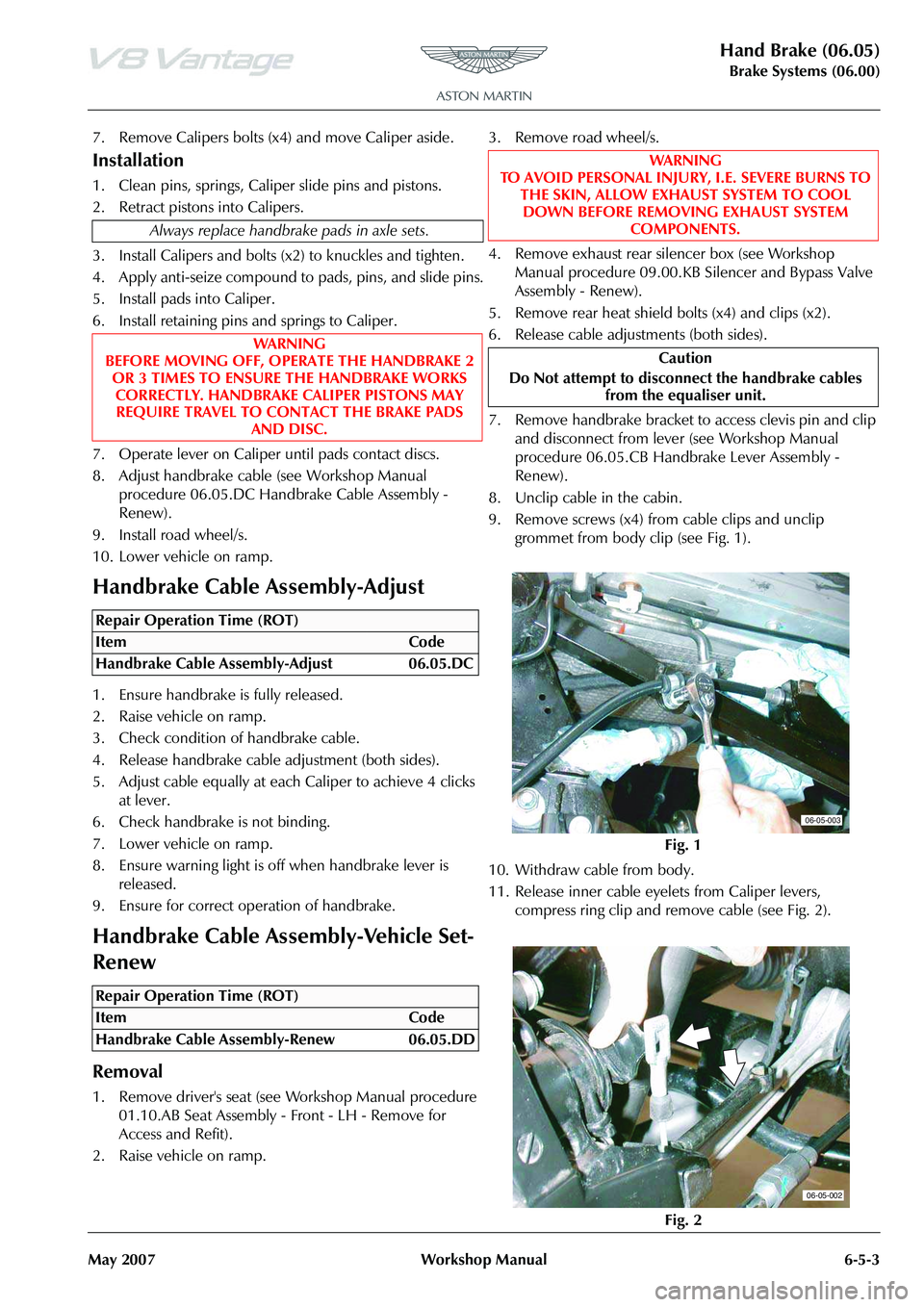
Hand Brake (06.05)
Brake Systems (06.00)
May 2007 Workshop Manual 6-5-3
7. Remove Calipers bolts (x 4) and move Caliper aside.
Installation
1. Clean pins, springs, Caliper slide pins and pistons.
2. Retract pistons into Calipers.
3. Install Calipers and bolts (x2) to knuckles and tighten.
4. Apply anti-seize compound to pads, pins, and slide pins.
5. Install pads into Caliper.
6. Install retaining pins and springs to Caliper.
7. Operate lever on Caliper until pads contact discs.
8. Adjust handbrake cable (see Workshop Manual
procedure 06.05.DC Handbrake Cable Assembly -
Renew).
9. Install road wheel/s.
10. Lower vehicle on ramp.
Handbrake Cable Assembly-Adjust
1. Ensure handbrake is fully released.
2. Raise vehicle on ramp.
3. Check condition of handbrake cable.
4. Release handbrake cable adjustment (both sides).
5. Adjust cable equally at each Caliper to achieve 4 clicks at lever.
6. Check handbrake is not binding.
7. Lower vehicle on ramp.
8. Ensure warning light is off when handbrake lever is released.
9. Ensure for correct operation of handbrake.
Handbrake Cable Assembly-Vehicle Set-
Renew
Removal
1. Remove driver's seat (see Workshop Manual procedure
01.10.AB Seat Assembly - Front - LH - Remove for
Access and Refit).
2. Raise vehicle on ramp. 3. Remove road wheel/s.
4. Remove exhaust rear sile
ncer box (see Workshop
Manual procedure 09.00.KB Silencer and Bypass Valve
Assembly - Renew).
5. Remove rear heat shield bolts (x4) and clips (x2).
6. Release cable adjustments (both sides).
7. Remove handbrake bracket to access clevis pin and clip and disconnect from lever (see Workshop Manual
procedure 06.05.CB Handbrake Lever Assembly -
Renew).
8. Unclip cable in the cabin.
9. Remove screws (x4) from cable clips and unclip grommet from body clip (see Fig. 1).
10. Withdraw cable from body.
11. Release inner cable eyelets from Caliper levers, compress ring clip and remove cable (see Fig. 2).
Always replace handbrake pads in axle sets.
WA R N I N G
BEFORE MOVING OFF, OPERATE THE HANDBRAKE 2 OR 3 TIMES TO ENSURE THE HANDBRAKE WORKS
CORRECTLY. HANDBRAKE CALIPER PISTONS MAY REQUIRE TRAVEL TO CONTACT THE BRAKE PADS AND DISC.
Repair Operation Time (ROT)
Repair Operation Time (ROT)
WA R N I N G
TO AVOID PERSONAL INJURY, I.E. SEVERE BURNS TO
THE SKIN, ALLOW EXHAUST SYSTEM TO COOL DOWN BEFORE REMOVING EXHAUST SYSTEM COMPONENTS.
Caution
Do Not attempt to disconne ct the handbrake cables
from the equaliser unit.
Fig. 1
Fig. 2
06-05-003
06-05-002
Page 507 of 947
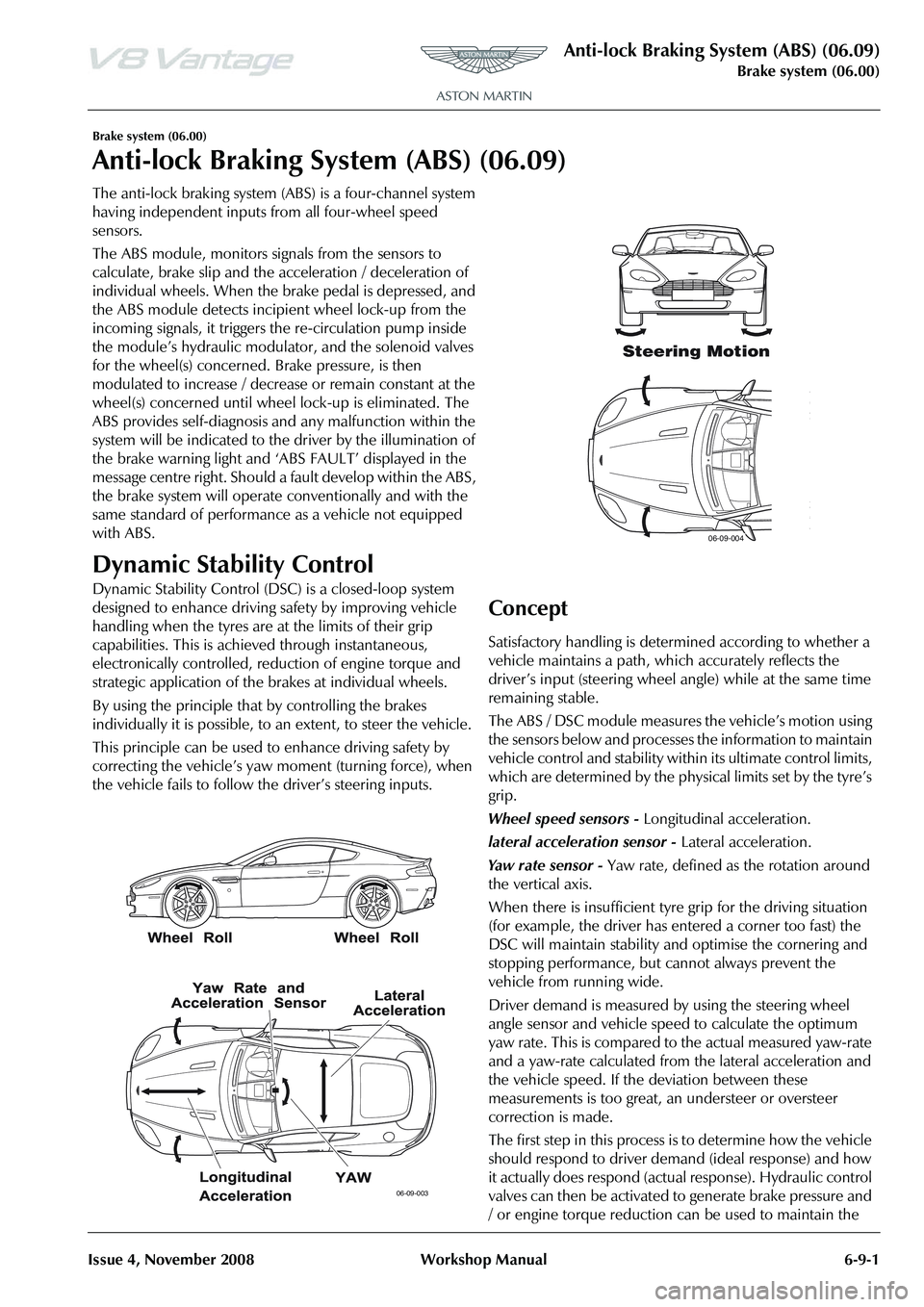
Anti-lock Braking System (ABS) (06.09)
Brake system (06.00)
Issue 4, November 2008 Workshop Manual 6-9-1
Brake system (06.00)
Anti-lock Braking System (ABS) (06.09)
The anti-lock braking system (ABS) is a four-channel system
having independent inputs from all four-wheel speed
sensors.
The ABS module, monitors signals from the sensors to
calculate, brake slip and the acceleration / deceleration of
individual wheels. When the brake pedal is depressed, and
the ABS module detects incipient wheel lock-up from the
incoming signals, it triggers the re-circulation pump inside
the module’s hydraulic modulator, and the solenoid valves
for the wheel(s) concerned. Brake pressure, is then
modulated to increase / decrease or remain constant at the
wheel(s) concerned until whee l lock-up is eliminated. The
ABS provides self-diagnosis and any malfunction within the
system will be indicated to the dr iver by the illumination of
the brake warning light and ‘ABS FAULT’ displayed in the
message centre right. Should a fault develop within the ABS,
the brake system will operate conventionally and with the
same standard of performanc e as a vehicle not equipped
with ABS.
Dynamic Stability Control
Dynamic Stability Control (DSC ) is a closed-loop system
designed to enhance driving safety by improving vehicle
handling when the tyres are at the limits of their grip
capabilities. This is achieved through instantaneous,
electronically controlled, reduction of engine torque and
strategic application of the brakes at individual wheels.
By using the principle that by controlling the brakes
individually it is possible, to an extent, to steer the vehicle.
This principle can be used to enhance driving safety by
correcting the vehicle’s yaw moment (turning force), when
the vehicle fails to follow th e driver’s steering inputs.
Concept
Satisfactory handling is determined according to whether a
vehicle maintains a path, wh ich accurately reflects the
driver
Page 588 of 947
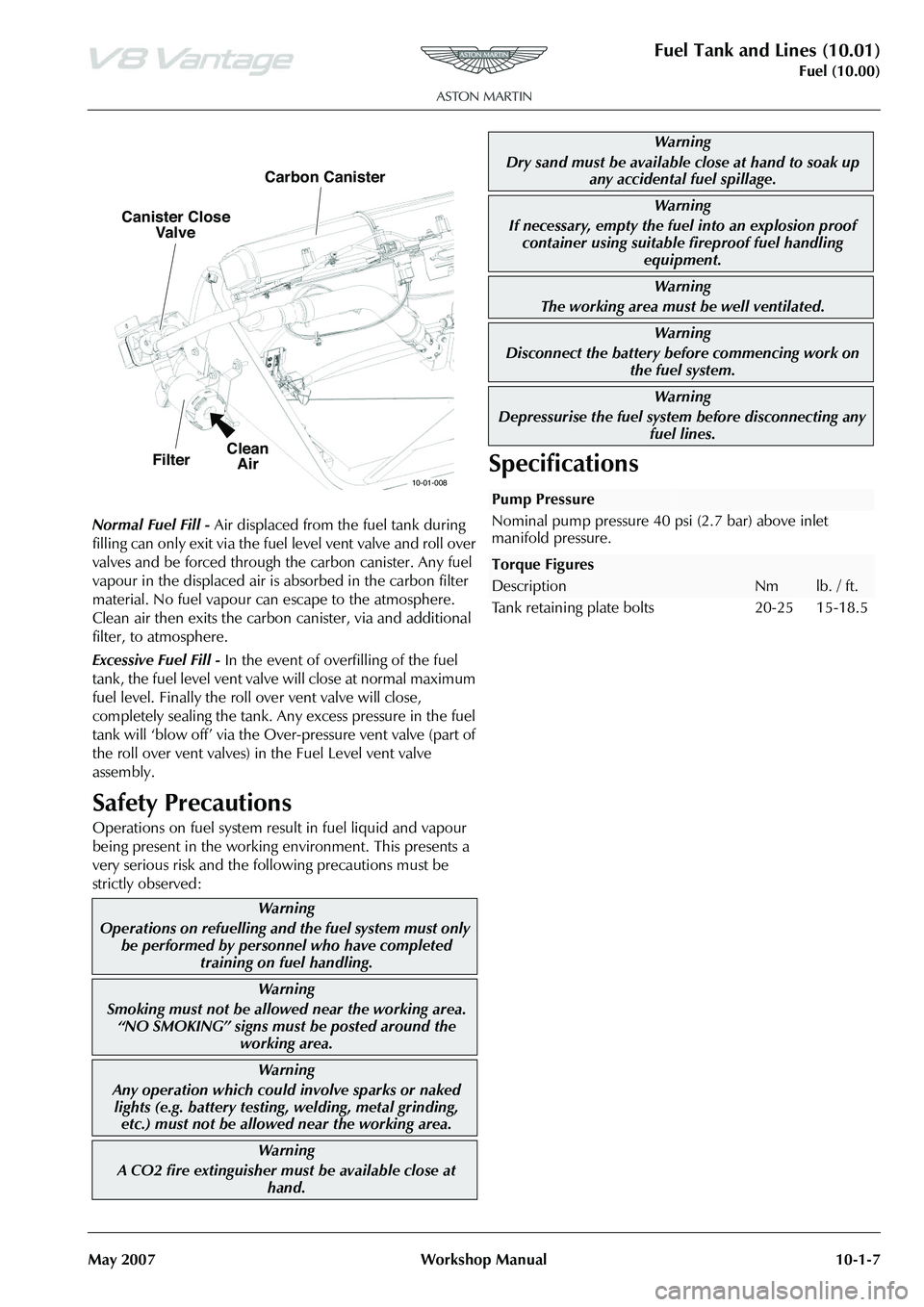
Fuel Tank and Lines (10.01)
Fuel (10.00)
May 2007 Workshop Manual 10-1-7
Normal Fuel Fill - Air displaced from the fuel tank during
filling can only exit via the fuel level vent valve and roll over
valves and be forced through the carbon canister. Any fuel
vapour in the displaced air is absorbed in the carbon filter
material. No fuel vapour can escape to the atmosphere.
Clean air then exits the carbon canister, via and additional
filter, to atmosphere.
Excessive Fuel Fill - In the event of overfilling of the fuel
tank, the fuel level vent valve will close at normal maximum
fuel level. Finally the roll over vent valve will close,
completely sealing the tank. Any excess pressure in the fuel
tank will ‘blow off’ via the Ov er-pressure vent valve (part of
the roll over vent valves) in the Fuel Level vent valve
assembly.
Safety Precautions
Operations on fuel system resu lt in fuel liquid and vapour
being present in the working environment. This presents a
very serious risk and the following precautions must be
strictly observed:
Specifications
Warning
Operations on refuelling and the fuel system must only
be performed by personnel who have completed training on fuel handling.
Warning
Smoking must not be allowed near the working area. “NO SMOKING” signs must be posted around the
working area.
Warning
Any operation which could involve sparks or naked lights (e.g. battery testing, welding, metal grinding,
etc.) must not be allowed near the working area.
Warning
A CO2 fire extinguisher must be available close at hand.
&