stop start CHEVROLET CAMARO 1967 1.G Chassis Workshop Manual
[x] Cancel search | Manufacturer: CHEVROLET, Model Year: 1967, Model line: CAMARO, Model: CHEVROLET CAMARO 1967 1.GPages: 659, PDF Size: 114.24 MB
Page 16 of 659
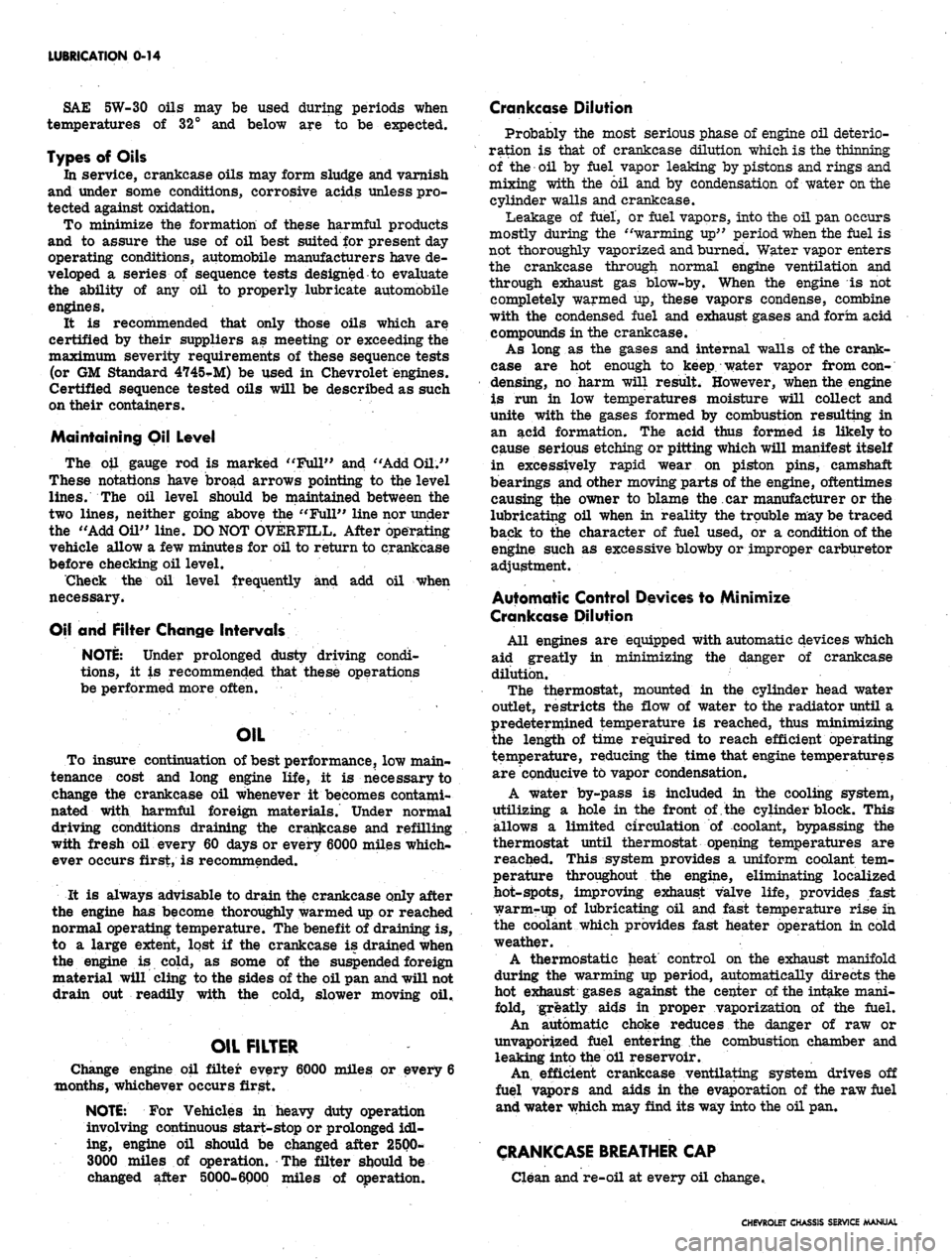
LUBRICATION 0-14
SAE 5W-30 oils may be used during periods when
temperatures of 32° and below are to be expected.
Types of Oils
In service, crankcase oils may form sludge and varnish
and under some conditions, corrosive acids unless pro-
tected against oxidation.
To minimize the formation of these harmful products
and to assure the use of oil best suited for present day
operating conditions, automobile manufacturers have de-
veloped a series of sequence tests designed to evaluate
the ability of any oil to properly lubricate automobile
engines.
It is recommended that only those oils which are
certified by their suppliers as meeting or exceeding the
maximum severity requirements of these sequence tests
(or GM Standard 4745-M) be used in Chevrolet engines.
Certified sequence tested oils will be described as such
on their containers.
Maintaining Oil Level
The oil gauge rod is marked "Full" and "Add Oil."
These notations have broad arrows pointing to the level
lines.
The oil level should be maintained between the
two lines, neither going above the "Full" line nor under
the "Add Oil" line. DO NOT OVERFILL. After operating
vehicle allow a few minutes for oil to return to crankcase
before checking oil level.
Check the oil level frequently and add oil when
necessary.
Oil and Filter Change Intervals
NOTE:
Under prolonged dusty driving condi-
tions,
it is recommended that these operations
be performed more often.
OIL
To insure continuation of best performance, low main-
tenance cost and long engine life, it is necessary to
change the crankcase oil whenever it becomes contami-
nated with harmful foreign materials. Under normal
driving conditions draining the crankcase and refilling
with fresh oil every 60 days or every 6000 miles which-
ever occurs first, is recommended.
It is always advisable to drain the crankcase only after
the engine has become thoroughly warmed up or reached
normal operating temperature. The benefit of draining is,
to a large extent, lost if the crankcase is drained when
the engine is cold, as some of the suspended foreign
material will cling to the sides of the oil pan and will not
drain out readily with the cold, slower moving oil.
OIL FILTER
Change engine oil filter every 6000 miles or every 6
months, whichever occurs first.
NOTE:
For Vehicles in heavy duty operation
involving continuous start-stop or prolonged idl-
ing, engine oil should be changed after 2500-
3000 miles of operation. The filter should be
changed after 5000-6000 miles of operation.
Crankcase Dilution
Probably the most serious phase of engine oil deterio-
ration is that of crankcase dilution which is the thinning
of the oil by fuel vapor leaking by pistons and rings and
mixing with the oil and by condensation of water on the
cylinder walls and crankcase.
Leakage of fuel, or fuel vapors, into the oil pan occurs
mostly during the "warming up" period when the fuel is
not thoroughly vaporized and burned. Water vapor enters
the crankcase through normal engine ventilation and
through exhaust gas blow-by. When the engine is not
completely warmed up, these vapors condense, combine
with the condensed fuel and exhaust gases and form acid
compounds in the crankcase.
As long as the gases and internal walls of the crank-
case are hot enough to keep water vapor from con-
densing, no harm will result. However, when the engine
is run in low temperatures moisture will collect and
unite with the gases formed by combustion resulting in
an acid formation. The acid thus formed is likely to
cause serious etching or pitting which will manifest itself
in excessively rapid wear on piston pins, camshaft
bearings and other moving parts of the engine, oftentimes
causing the owner to blame the car manufacturer or the
lubricating oil when in reality the trouble may be traced
back to the character of fuel used, or a condition of the
engine such as excessive blowby or improper carburetor
adjustment.
Automatic Control Devices to Minimize
Crankcase Dilution
All engines are equipped with automatic devices which
aid greatly in minimizing the danger of crankcase
dUution.
The thermostat, mounted in the cylinder head water
outlet, restricts the flow of water to the radiator until a
predetermined temperature is reached, thus minimizing
the length of time required to reach efficient operating
temperature, reducing the time that engine temperatures
are conducive to vapor condensation.
A water by-pass is included in the cooling system,
utilizing a hole in the front of, the cylinder block. This
allows a limited circulation of coolant, bypassing the
thermostat until thermostat opening temperatures are
reached. This system provides a uniform coolant tem-
perature throughout the engine, eliminating localized
hot-spots, improving exhaust valve life, provides fast
warmrup of lubricating oil and fast temperature rise in
the coolant which provides fast heater operation in cold
weather.
A thermostatic heat control on the exhaust manifold
during the warming up period, automatically directs the
hot exhaust gases against the center of the intake mani-
fold, greatly aids in proper vaporization of the fuel.
An automatic choke reduces the danger of raw or
unvaporized fuel entering the combustion chamber and
leaking into the oil reservoir.
An.
efficient crankcase ventilating system drives off
fuel vapors and aids in the evaporation of the raw fuel
and water which may find its way into the oil pan.
CRANKCASE BREATHER CAP
Clean and re-oil at every oil change..
CHEVROLET CHASSIS SERVICE MANUAL
Page 42 of 659
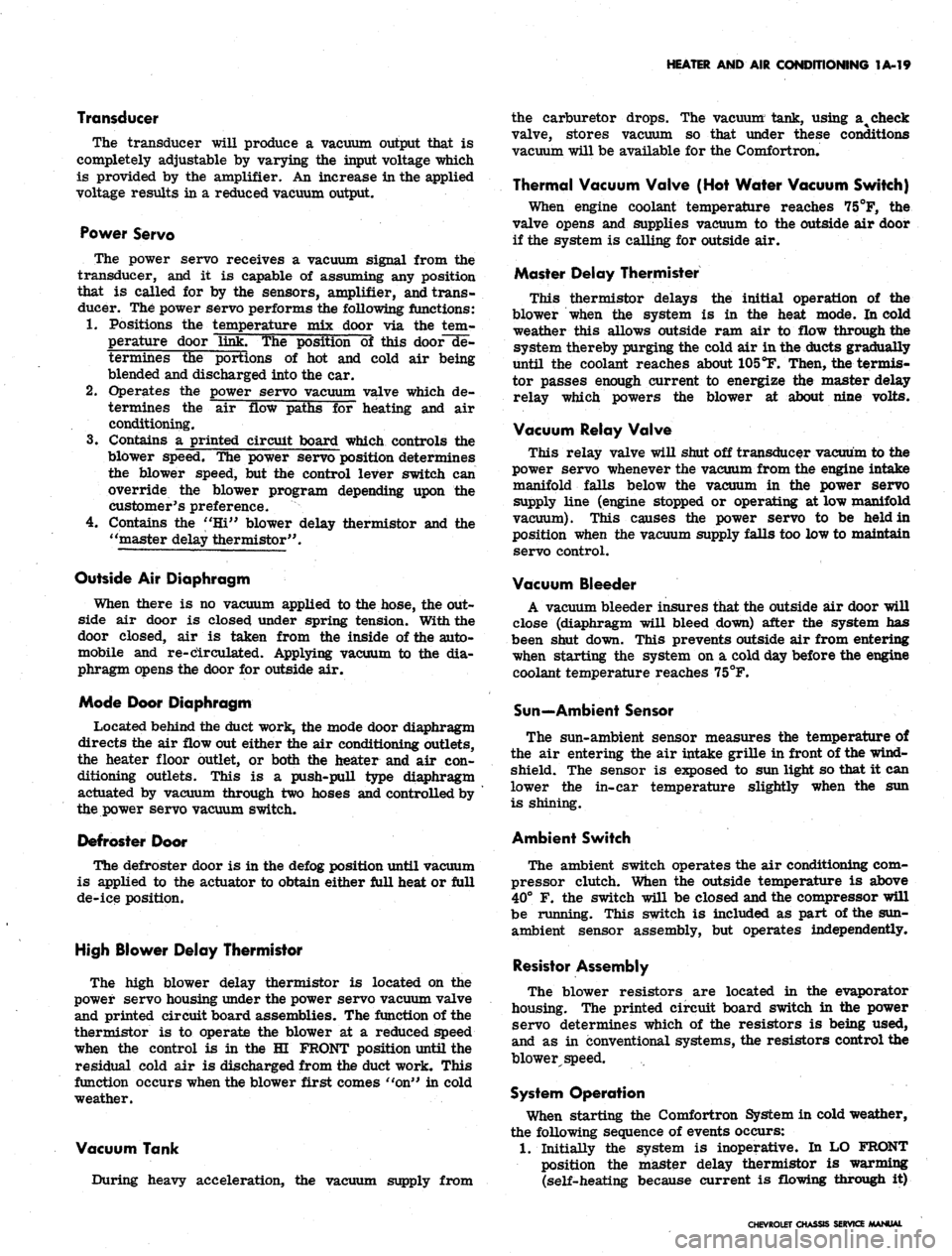
HEATER AND AIR CONDITIONING 1A-19
Transducer
The transducer will produce a vacuum output that is
completely adjustable by varying the input voltage which
is provided by the amplifier. An increase in the applied
voltage results in a reduced vacuum output.
Power Servo
The power servo receives a vacuum signal from the
transducer, and it is capable of assuming any position
that is called for by the sensors, amplifier, and trans-
ducer. The power servo performs the following functions:
1.
Positions the temperature mix door via the tern-
perature door link. The position of this door~"de-
termihes the portions of hot and cold air being
blended and discharged into the car.
2.
Operates the power servo vacuum valve which de-
termines the air flow paths for heating and air
conditioning.
3.
Contains a printed circuit board which controls the
blower speed. The power servo position determines
the blower speed, but the control lever switch can
override the blower program depending upon the
customer's preference.
4.
Contains the "Hi" blower delay thermistor and the
"master delay thermistor".
Outside Air Diaphragm
When there is no vacuum applied to the hose, the out-
side air door is closed under spring tension. With the
door closed, air is taken from the inside of the auto-
mobile and re-circulated. Applying vacuum to the dia-
phragm opens the door for outside air.
Mode Door Diaphragm
Located behind the duct work, the mode door diaphragm
directs the air flow out either the air conditioning outlets,
the heater floor outlet, or both the heater and air con-
ditioning outlets. This is a push-pull type diaphragm
actuated by vacuum through two hoses and controlled by
the power servo vacuum switch.
Defroster Door
The defroster door is in the defog position until vacuum
is applied to the actuator to obtain either full heat or full
de-ice position.
High Blower Delay Thermistor
The high blower delay thermistor is located on the
power servo housing under the power servo vacuum valve
and printed circuit board assemblies. The function of the
thermistor is to operate the blower at a reduced speed
when the control is in the HI FRONT position until the
residual cold air is discharged from the duct work. This
function occurs when the blower first comes "on" in cold
weather.
Vacuum Tank
During heavy acceleration, the vacuum supply from
the carburetor drops. The vacuum tank, using a^ check
valve, stores vacuum so that under these conditions
vacuum will be available for the Comfortron.
Thermal Vacuum Valve (Hot Water Vacuum Switch)
When engine coolant temperature reaches 75°F, the
valve opens and supplies vacuum to the outside air door
if the system is calling for outside air.
Master Delay Thermister
This thermistor delays the initial operation of the
blower when the system is in the heat mode. In cold
weather this allows outside ram air to flow through the
system thereby purging the cold air in the ducts gradually
until the coolant reaches about 105°F. Then, the termis-
tor passes enough current to energize the master delay
relay which powers the blower at about nine volts.
Vacuum Relay Valve
This relay valve will shut off transducer vacuum to the
power servo whenever the vacuum from the engine intake
manifold falls below the vacuum in the power servo
supply line (engine stopped or operating at low manifold
vacuum). This causes the power servo to be held in
position when the vacuum supply falls too low to maintain
servo control.
Vacuum Bleeder
A vacuum bleeder insures that the outside air door will
close (diaphragm will bleed down) after the system has
been shut down. This prevents outside air from entering
when starting the system on a cold day before the engine
coolant temperature reaches 75°F.
Sun—Ambient Sensor
The sun-ambient sensor measures the temperature of
the air entering the air intake grille in front of the wind-
shield. The sensor is exposed to sun light so that it can
lower the in-car temperature slightly when the sun
is shining.
Ambient Switch
The ambient switch operates the air conditioning com-
pressor clutch. When the outside temperature is above
40° F. the switch will be closed and the compressor will
be running. This switch is included as| part of the sun-
ambient sensor assembly, but operates independently.
Resistor Assembly
The blower resistors are located in the evaporator
housing. The printed circuit board switch in the power
servo determines which of the resistors is being used,
and as in conventional systems, the resistors control the
blower speed.
System Operation
When starting the Comfortron System in cold weather,
the following sequence of events occurs:
1.
Initially the system is inoperative. In LO FRONT
position the master delay thermistor is warming
(self-heating because current is flowing through it)
CHEVROLET CHASSIS SERVICE MANUAL
Page 66 of 659
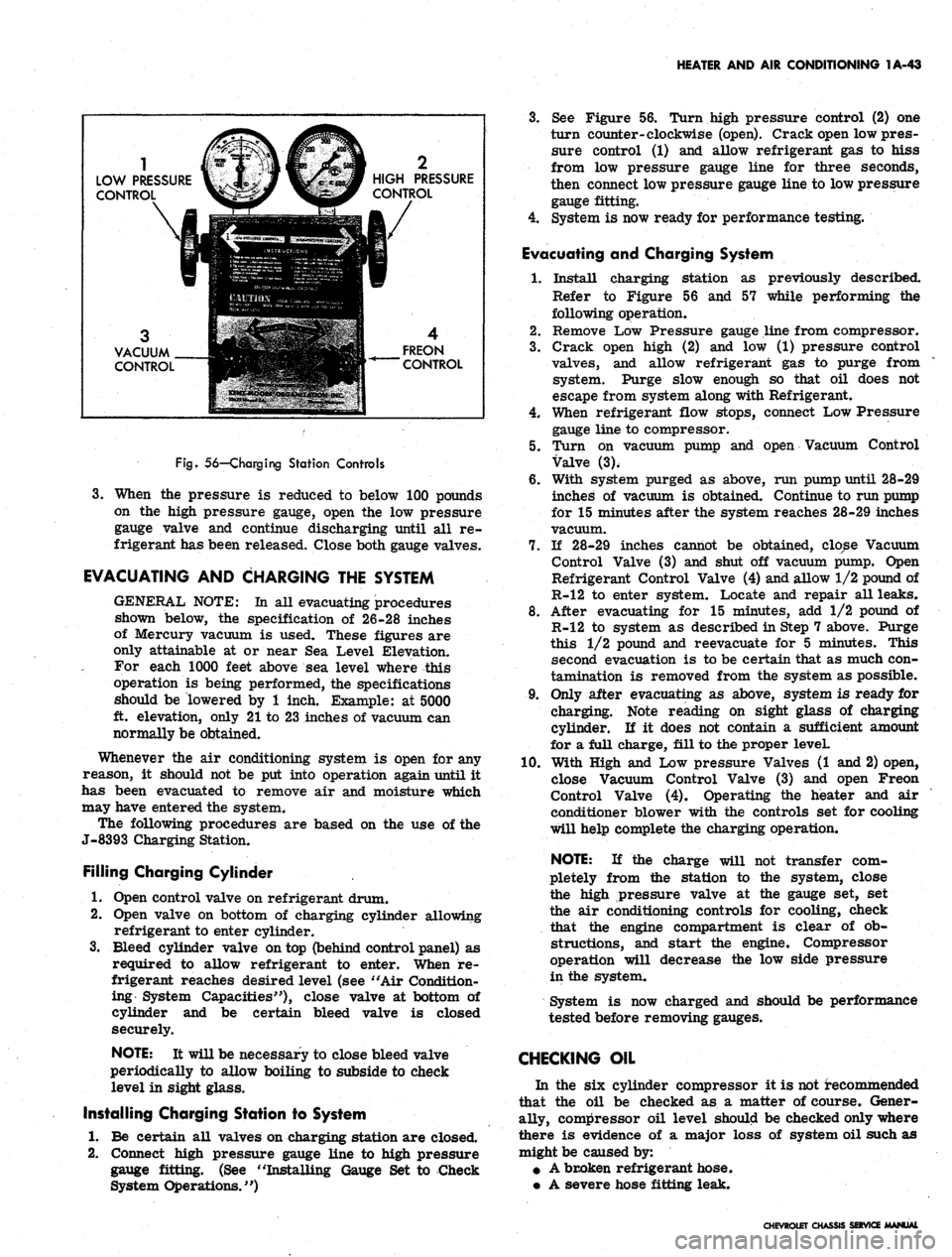
HEATER AND AIR CONDITIONING 1A-43
LOW PRESSURE
CONTROL
HIGH PRESSURE
CONTROL
3
VACUUM
CONTROL
4
FREON
CONTROL
Fig,
56—Charging Station Controls
3.
When the pressure is reduced to below 100 pounds
on the high pressure gauge, open the low pressure
gauge valve and continue discharging until all re-
frigerant has been released. Close both gauge valves.
EVACUATING AND CHARGING THE SYSTEM
GENERAL NOTE: La all evacuating procedures
shown below, the specification of 26-28 inches
of Mercury vacuum is used. These figures are
only attainable at or near Sea Level Elevation.
For each 1000 feet above sea level where this
operation is being performed, the specifications
should be lowered by 1 inch. Example: at 5000
ft. elevation, only 21 to 23 inches of vacuum can
normally be obtained.
Whenever the air conditioning system is open for any
reason, it should not be put into operation again until it
has been evacuated to remove air and moisture which
may have entered the system.
The following procedures are based on the use of the
J-8393 Charging Station.
Filling Charging Cylinder
1.
Open control valve on refrigerant drum.
2.
Open valve on bottom of charging cylinder allowing
refrigerant to enter cylinder.
3.
Bleed cylinder valve on top (behind control panel) as
required to allow refrigerant to enter. When re-
frigerant reaches desired level (see "Air Condition-
ing System Capacities"), close valve at bottom of
cylinder and be certain bleed valve is closed
securely.
NOTE: It will be necessary to close bleed valve
periodically to allow boiling to subside to check
level in sight glass.
Installing Charging Station to System
1.
Be certain all valves on charging station are closed.
2.
Connect high pressure gauge line to high pressure
gauge fitting. (See "Installing Gauge Set to Check
System Operations.")
3.
See Figure 56. Turn high pressure control (2) one
turn counter-clockwise (open). Crack open low pres-
sure control (1) and allow refrigerant gas to hiss
from low pressure gauge line for three seconds,
then connect low pressure gauge line to low pressure
gauge fitting.
4.
System is now ready for performance testing.
Evacuating and Charging System
1.
Install charging station as previously described.
Refer to Figure 56 and 57 while performing the
following operation.
2.
Remove Low Pressure gauge line from compressor.
3.
Crack open high (2) and low (1) pressure control
valves, and allow refrigerant gas to purge from
system. Purge slow enough so that oil does not
escape from system along with Refrigerant.
4.
When refrigerant flow stops, connect Low Pressure
gauge line to compressor.
5.
Turn on vacuum pump and open Vacuum Control
Valve (3).
6. With system purged as above, run pump until 28-29
inched of vacuum is obtained. Continue to run pump
for 15 minutes after the system reaches 28-29 inches
vacuum.
7.
If 28-29 inches cannot be obtained, close Vacuum
Control Valve (3) and shut off vacuum pump. Open
Refrigerant Control Valve (4) and allow 1/2 pound of
R-12 to enter system. Locate and repair all leaks.
8. After evacuating for 15 minutes, add 1/2 pound of
R-12 to system as described in Step 7 above. Purge
this 1/2 pound and reevacuate for 5 minutes. This
second evacuation is to be certain that as much con-
tamination is removed from the system as possible.
9. Only after evacuating as above, system is ready for
charging. Note reading on sight glass of charging
cylinder. If it does not contain a sufficient amount
for a full charge, fill to the proper leveL
10.
With High and Low pressure Valves (1 and 2) open,
close Vacuum Control Valve (3) and open Freon
Control Valve (4). Operating the heater and air
conditioner blower with the controls set for cooling
will help complete the charging operation.
NOTE: If the charge will not transfer com-
pletely from the station to the system, close
the high pressure valve at the gauge set, set
the air conditioning controls for cooling, check
that the engine compartment is clear of ob-
structions, and start the engine. Compressor
operation will decrease the low side pressure
in the system.
System is now charged and should be performance
tested before removing gauges.
CHECKING OIL
In the six cylinder compressor it is not recommended
that the oil be checked as a matter of course. Gener-
ally, compressor oil level should be checked only where
there is evidence of a major loss of system oil such as
might be caused by:
• A broken refrigerant hose.
• A severe hose fitting leak.
CHEVROLET CHASSIS SERVICE MANUAL
Page 179 of 659
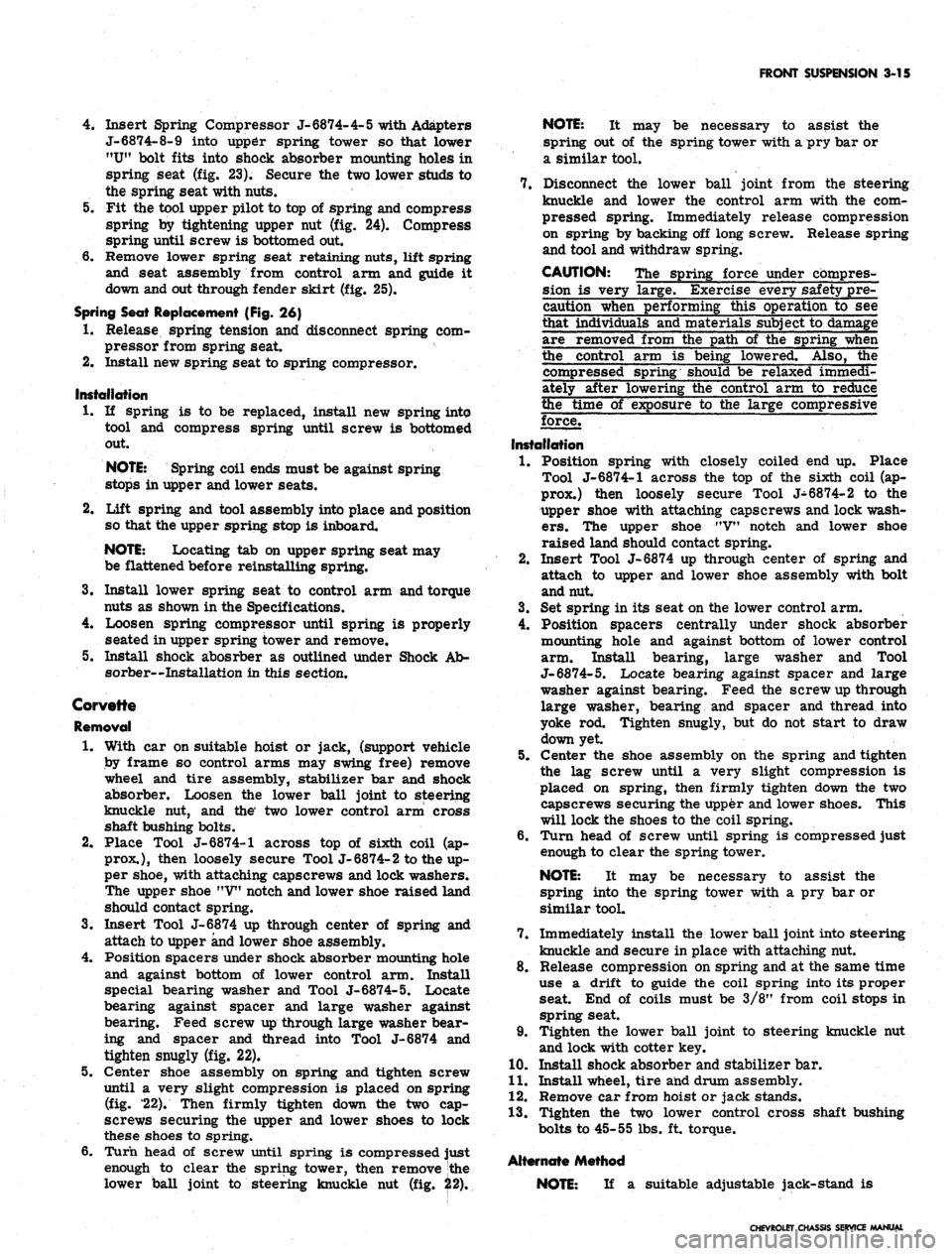
FRONT SUSPENSION 3-15
4.
Insert Spring Compressor J-
6874-
4-
5 with Adapters
J-6874-8-9 into upp^r spring tower so that lower
MU"
bolt fits into shock absorber mounting holes in
spring seat (fig. 23). Secure the two lower studs to
the spring seat with nuts.
5.
Fit the tool upper pilot to top of spring and compress
spring by tightening upper nut (fig. 24). Compress
spring until screw is bottomed out.
6. Remove lower spring seat retaining nuts, lift spring
and seat assembly from control arm and guide it
down and out through fender skirt (fig. 25).
Spring Seat Replacement (Fig. 26)
1.
Release spring tension and disconnect spring com-
pressor from spring seat.
2.
Install new spring seat to spring compressor.
Installation
1.
If spring is to be replaced, install new spring into
tool and compress spring until screw is bottomed
out.
NOTE: Spring coil ends must be against spring
stops in upper and lower seats.
2.
Lift spring and tool assembly into place and position
so that the upper spring stop is inboard.
NOTE: Locating tab on upper spring seat may
be flattened before reinstalling spring.
3.
Install lower spring seat to control arm and torque
nuts as shown in the Specifications.
4.
Loosen spring compressor until spring is properly
seated in upper spring tower and remove.
5.
Install shock abosrber as outlined under Shock Ab-
sorber—Installation in this section.
Corvette
Removal
1.
With car on suitable hoist or jack, (support vehicle
by frame so control arms may swing free) remove
wheel and tire assembly, stabilizer bar and shock
absorber. Loosen the lower ball joint to steering
knuckle nut, and the' two lower control arm cross
shaft bushing bolts.
2.
Place Tool J-6874-1 across top of sixth coil (ap-
prox.),
then loosely secure Tool J-6874-2 to the up-
per shoe, with attaching capscrews and lock washers.
The upper shoe "V" notch and lower shoe raised land
should contact spring.
3.
Insert Tool J-6874 up through center of spring and
attach to upper and lower shoe assembly.
4.
Position spacers under shock absorber mounting hole
and against bottom of lower control arm. Install
special bearing washer and Tool J-6874-5. Locate
bearing against spacer and large washer against
bearing. Feed screw up through large washer bear-
ing and spacer and thread into Tool J-6874 and
tighten snugly (fig. 22).
5.
Center shoe assembly on spring and tighten screw
until a very slight compression is placed on spring
(fig. '22). Then firmly tighten down the two cap-
screws securing the upper and lower shoes to lock
these shoes to spring.
6. Turn head of screw until spring is compressed just
enough to clear the spring tower, then remove the
lower ball joint to steering knuckle nut (fig. 22).
NOTE: It may be necessary to assist the
spring out of the spring tower with a pry bar or
a similar tool.
7.
Disconnect the lower ball joint from the steering
knuckle and lower the control arm with the com-
pressed spring. Immediately release compression
on spring by backing off long screw. Release spring
and tool and withdraw spring.
CAUTION: The spring force under compres-
sion is very large. Exercise every safety pre-
caution when performing this operation to see
that individuals and materials subject to damage
are removed from the path of the spring when
the control arm is being lowered. Also, the
compressed spring
be relaxed immedi-
ately after lowering the control arm to reduce
the time of exposure to the large compressive
force.
Installation
1.
Position spring with closely coiled end up. Place
Tool J-6874-1 across the top of the sixth coil (ap-
prox.) then loosely secure Tool J-6874-2 to the
upper shoe with attaching capscrews and lock wash-
ers.
The upper shoe MV" notch and lower shoe
raised land should contact spring.
2.
Insert Tool J-6874 up through center of spring and
attach to upper and lower shoe assembly with bolt
and nut.
3.
Set spring in its seat on the lower control arm.
4.
Position spacers centrally under shock absorber
mounting hole and against bottom of lower control
arm. Install bearing, large washer and Tool
J-6874-5.
Locate bearing against spacer and large
washer against bearing. Feed the screw up through
large washer, bearing and spacer and thread into
yoke rod. Tighten snugly, but do not start to draw
down yet
5.
Center the shoe assembly on the spring and tighten
the lag screw until a very slight compression is
placed on spring, then firmly tighten down the two
capscrews securing the upper and lower shoes. This
will lock the shoes to the coil spring.
6. Turn head of screw until spring is compressed just
enough to clear the spring tower.
NOTE: It may be necessary to assist the
spring into the spring tower with a pry bar or
similar tool.
7.
Immediately install the lower ball joint into steering
knuckle and secure in place with attaching nut.
8. Release compression on spring and at the same time
use a drift to guide the coil spring into its proper
seat. End of coils must be 3/8" from coil stops in
spring seat.
9. Tighten the lower ball joint to steering knuckle nut
and lock with cotter key.
10.
Install shock absorber and stabilizer bar.
11.
Install wheel, tire and drum assembly.
12.
Remove car from hoist or jack stands.
13.
Tighten the two lower control cross shaft bushing
bolts to 45-55 lbs. ft. torque.
NOTE: If a suitable adjustable jack-stand is
CHEVROLET CHASSIS SERVICE MANUAL
Page 197 of 659
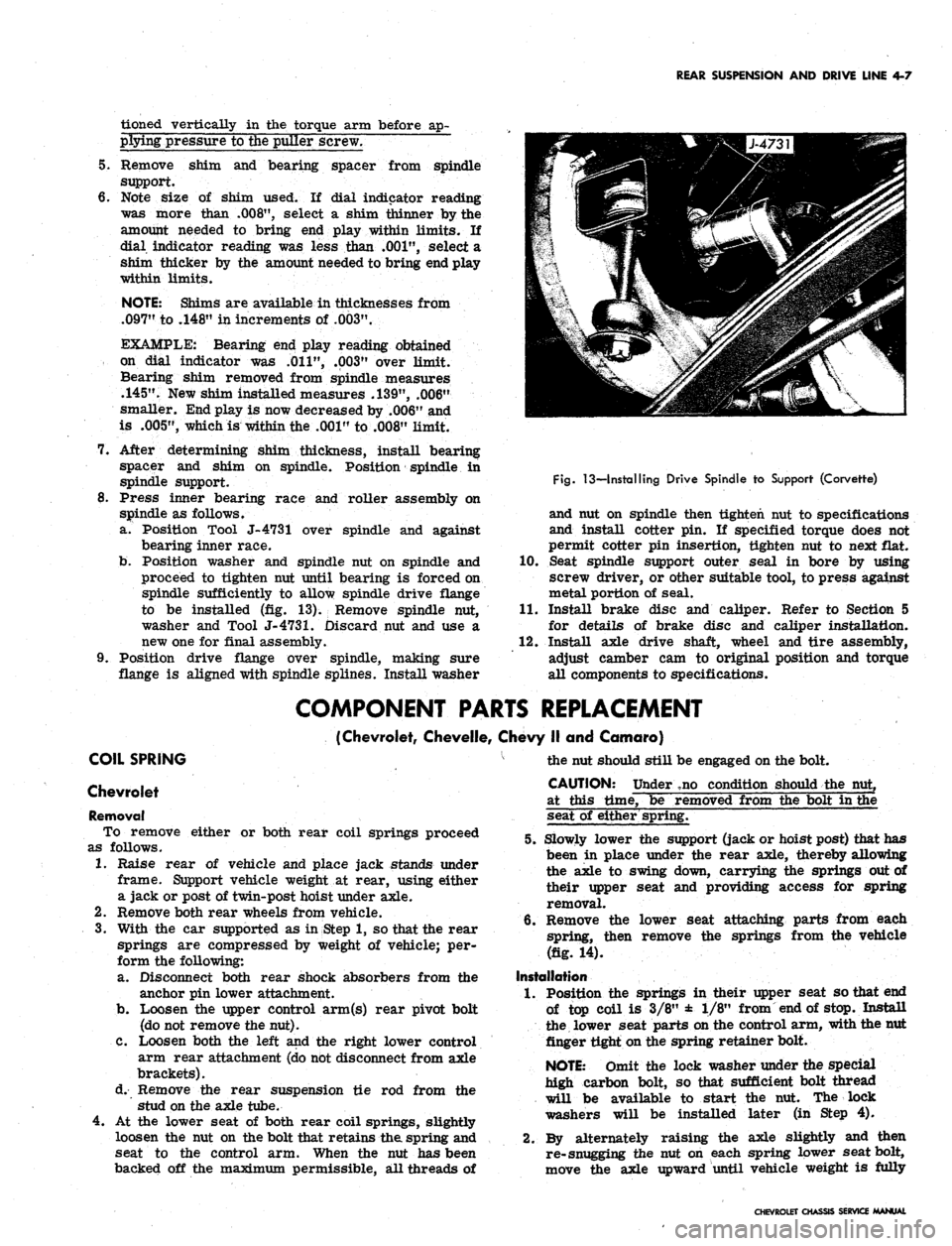
REAR SUSPENSION AND DRIVE LINE 4-7
tioned vertically in the torque arm before ap-
plying pressure to the puller screw.
5.
Remove shim and bearing spacer from spindle
support.
6. Note size of shim used. If dial indicator reading
was more than
.008",
select a shim thinner by the
amount needed to bring end play within limits. If
dial indicator reading was less than
.001",
select a
shim thicker by the amount needed to bring end play
within limits.
NOTE: Shims are available in thicknesses from
.097"
to .148" in increments of
.003".
EXAMPLE: Bearing end play reading obtained
on dial indicator was
.011",
.003" over limit.
Bearing shim removed from spindle measures
.145".
New shim installed measures .139", .006"
smaller. End play is now decreased by .006" and
is
.005",
which is within the .001" to .008" limit.
7.
After determining shim thickness, install bearing
spacer and shim on spindle. Position spindle in
spindle support.
8. Press inner bearing race and roller assembly on
spindle as follows.
a. Position Tool J-4731 over spindle and against
bearing inner race.
b.
Position washer and spindle nut on spindle and
proceed to tighten nut until bearing is forced on
spindle sufficiently to allow spindle drive flange
to be installed (fig. 13). Remove spindle nut,
washer and Tool
J-4731.
Discard nut and use a
new one for final assembly.
9. Position drive flange over spindle, making sure
flange is aligned with spindle splines. Install washer
Fig.
13—Installing Drive Spindle to Support (Corvette)
and nut on spindle then tighten nut to specifications
and install cotter pin. If specified torque does not
permit cotter pin insertion, tighten nut to next flat.
10.
Seat spindle support outer seal in bore by using
screw driver, or other suitable tool, to press against
metal portion of seal.
11.
Install brake disc and caliper. Refer to Section 5
for details of brake disc and caliper installation.
12.
Install axle drive shaft, wheel and tire assembly,
adjust camber cam to original position and torque
all components to specifications.
COMPONENT PARTS REPLACEMENT
(Chevrolet, Chevelle, Chevy II and Camaro)
COIL SPRING
Chevrolet
Removal
To remove either or both rear coil springs proceed
as follows.
1.
Raise rear of vehicle and place jack stands under
frame. Support vehicle weight at rear, using either
a jack or post of twin-post hoist under axle.
2.
Remove both rear wheels from vehicle.
3.
With the car supported as in Step 1, so that the rear
springs are compressed by weight of vehicle; per-
form the following:
a. Disconnect both rear shock absorbers from the
anchor pin lower attachment.
b.
Loosen the upper control arm(s) rear pivot bolt
(do not remove the nut).
C. Loosen both the left and the right lower control
arm rear attachment (do not disconnect from axle
brackets).
d. Remove the rear suspension tie rod from the
stud on the axle tube.
4.
At the lower seat of both rear coil springs, slightly
loosen the nut on the bolt that retains the spring and
seat to the control arm. When the nut has been
backed off the maximum permissible, all threads of
the nut should still be engaged on the bolt.
CAUTION: Under ,no condition should the nut,
at this time, be removed from the bolt in the
seat of either spring.
5.
Slowly lower the support (jack or hoist post) that has
been in place under the rear axle, thereby allowing
the axle to swing down, carrying the springs out of
their upper seat and providing access for spring
removal.
6. Remove the lower seat attaching parts from each
spring, then remove the springs from the vehicle
(fig. 14).
Installation
1.
Position the springs in their upper seat so that end
of top coil is 3/8" ± 1/8" from end of stop. Install
the lower seat parts on the control arm, with the nut
finger tight on the spring retainer bolt.
NOTE: Omit the lock washer under the special
high carbon bolt, so that sufficient bolt thread
will be available to start the nut. The lock
washers will be installed later (in Step 4).
2.
By alternately raising the axle slightly and then
re-snugging the nut on each spring lower seat bolt,
move the axle upward until vehicle weight is fully
CHEVROLET CHASSIS SERVICE MANUAL
Page 264 of 659
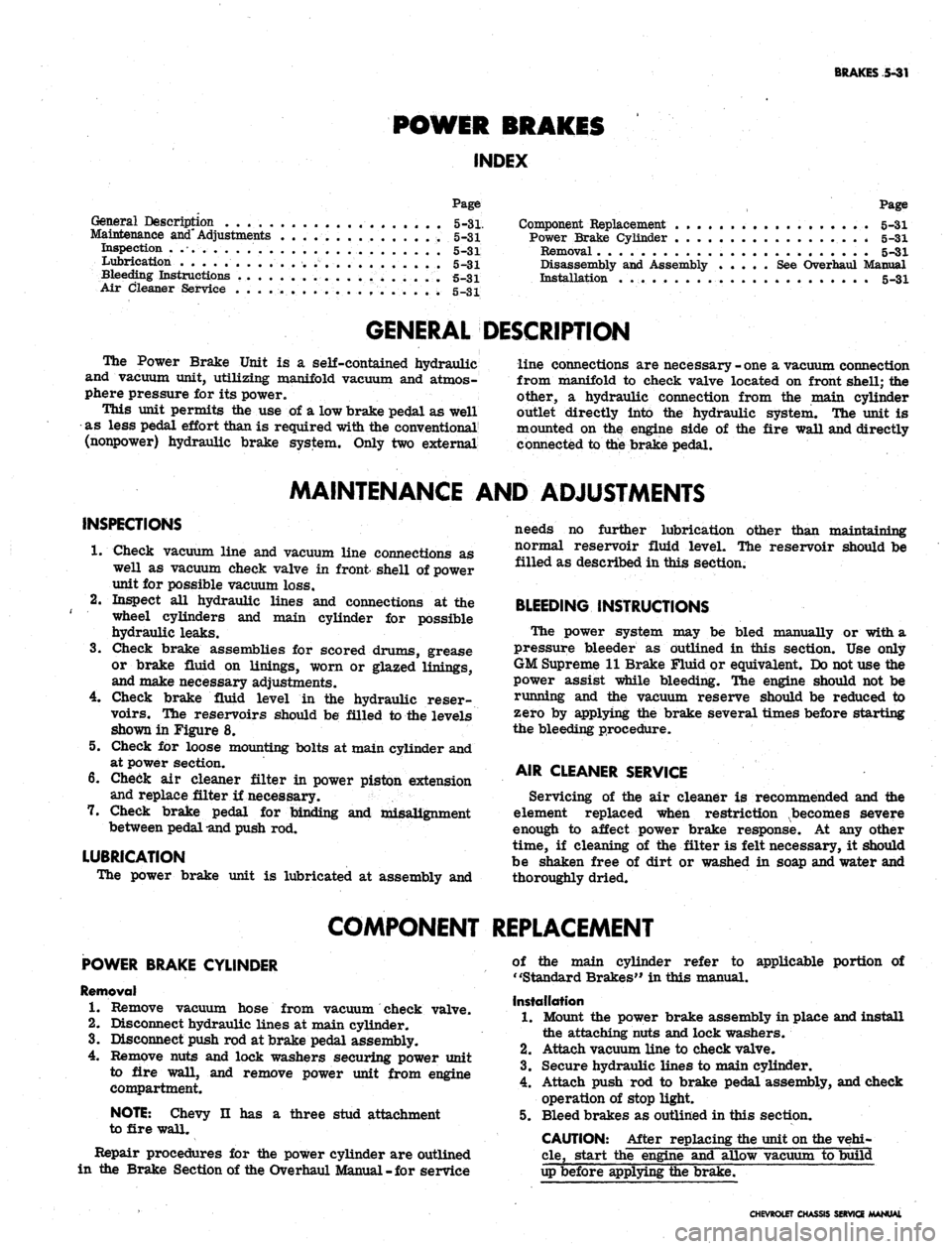
BRAKES
5-31
POWER BRAKES
INDEX
General Description 5-31
Maintenance
and"
Adjustments 5-31
Inspection . ... 5_31
Lubrication 5-31
Bleeding Instructions . . . 5.31
Air Cleaner Service . . . , 5.31
Page
Component Replacement 5-31
Power Brake Cylinder ......* 5-31
Removal . . 5-31
Disassembly and Assembly See Overhaul Manual
Installation . . . . 5-31
GENERAL DESCRIPTION
The Power Brake Unit is a self-contained hydraulic
and vacuum unit, utilizing manifold vacuum and atmos-
phere pressure for its power.
This unit permits the use of a low brake pedal as well
as less pedal effort than is required with the conventional
(nonpower) hydraulic brake system. Only two external
line connections are necessary -
one
a vacuum connection
from manifold to check valve located on front shell; the
other, a hydraulic connection from the main cylinder
outlet directly into the hydraulic system. The unit is
mounted on the engine side of the fire wall and directly
connected to the brake pedal.
MAINTENANCE AND ADJUSTMENTS
INSPECTIONS
1.
Check vacuum line and vacuum line connections as
well as vacuum check valve in front shell of power
unit for possible vacuum loss.
2.
Inspect all hydraulic lines and connections at the
wheel cylinders and main cylinder for possible
hydraulic leaks.
3.
Check brake assemblies for scored drums, grease
or brake fluid on linings, worn or glazed linings,
and make necessary adjustments.
4.
Check brake fluid level in the hydraulic reser-
voirs.
The reservoirs should be filled to the levels
shown in Figure 8.
5. Check for loose mounting bolts at main cylinder and
at power section.
6. Check air cleaner filter in power piston extension
and replace filter if necessary.
7. Check brake pedal for binding and misalignment
between pedal
-and
push rod.
LUBRICATION
The power brake unit is lubricated at assembly and
needs no further lubrication other than maintaining
normal reservoir fluid level. The reservoir should be
filled as described in this section.
BLEEDING INSTRUCTIONS
The power system may be bled manually or with a
pressure bleeder as outlined in this section. Use only
GM
Supreme 11 Brake Fluid or equivalent. Do not use the
power assist while bleeding. The engine should not be
running and the vacuum reserve should be reduced to
zero by applying the brake several times before starting
the bleeding procedure.
AIR CLEANER SERVICE
Servicing of the air cleaner is recommended and the
element replaced when restriction becomes severe
enough to affect power brake response. At any other
time, if cleaning of the filter is felt necessary, it should
be shaken free of dirt or washed in soap and water and
thoroughly dried.
COMPONENT REPLACEMENT
POWER BRAKE CYLINDER
Removal
1.
Remove vacuum hose from vacuum check valve.
2.
Disconnect hydraulic lines at main cylinder.
Disconnect push rod at brake pedal assembly.
Remove nuts and lock washers securing power unit
to fire wall, and remove power unit from engine
compartment.
3.
4.
NOTE:
Chevy
to fire wall.
has a three stud attachment
Repair procedures for the power cylinder are outlined
in the Brake Section of the Overhaul Manual-for service
of the main cylinder refer to applicable portion of
"Standard Brakes" in this manual.
Installation
1.
Mount the power brake assembly in place and install
the attaching nuts and lock washers.
2.
Attach vacuum line to check valve.
3.
Secure hydraulic lines to main cylinder.
4.
Attach push rod to brake pedal assembly, and check
operation of stop light.
5. Bleed brakes as outlined in this section.
CAUTION: After replacing the unit on the vehi-
cle,
start the engine and allow vacuum to build
up before applying the brake.
CHEVROLET CHASSIS SERVICE
Page 272 of 659
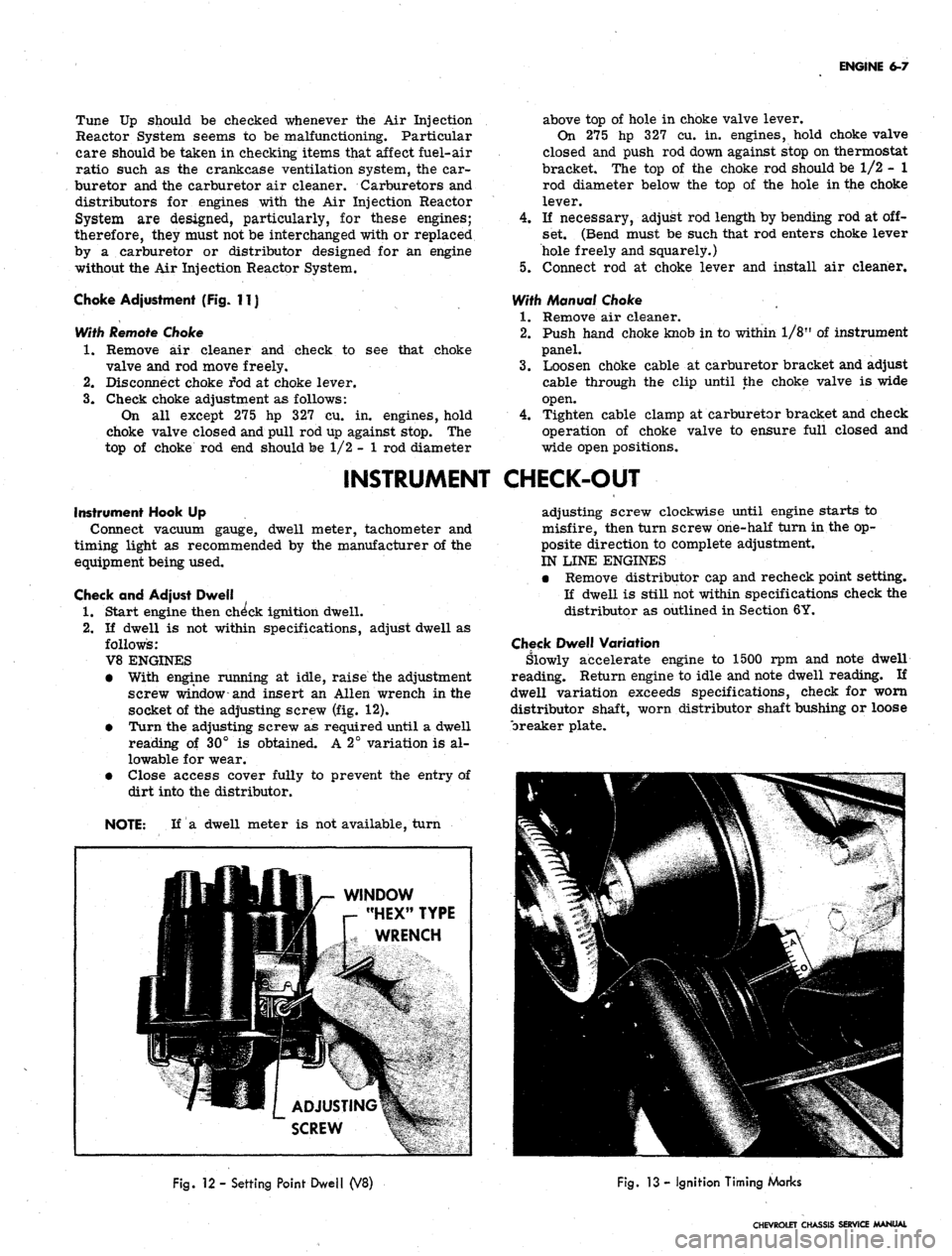
ENGINE 6-7
Tune Up should be checked whenever the Air Injection
Reactor System seems to be malfunctioning. Particular
care should be taken in checking items that affect fuel-air
ratio such as the crankcase ventilation system, the car-
buretor and the carburetor air cleaner. Carburetors and
distributors for engines with the Air Injection Reactor
System are designed, particularly, for these engines;
therefore, they must not be interchanged with or replaced
by a carburetor or distributor designed for an engine
without the Air Injection Reactor System.
Choke Adjustment (Fig. 11)
With Remote Choke
1.
Remove air cleaner and check to see that choke
valve and rod move freely.
2.
Disconnect choke r*od at choke lever.
Check choke adjustment as follows:
On all except 275 hp 327 cu. in. engines, hold
choke valve closed and pull rod up against stop. The
top of choke rod end should be 1/2 - 1 rod diameter
4.
5.
above top of hole in choke valve lever.
On 275 hp 327 cu. in. engines, hold choke valve
closed and push rod down against stop on thermostat
bracket. The top of the choke rod should be 1/2 - 1
rod diameter below the top of the hole in the choke
lever.
If necessary, adjust rod length by bending rod at off-
set. (Bend must be such that rod enters choke lever
hole freely and squarely.)
Connect rod at choke lever and install air cleaner.
3.
With Manual
Choke
1.
Remove air cleaner.
2.
Push hand choke knob in to within 1/8" of instrument
panel.
3.
Loosen choke cable at carburetor bracket and adjust
cable through the clip until the choke valve is wide
open.
4.
Tighten cable clamp at carburetor bracket and check
operation of choke valve to ensure full closed and
wide open positions.
INSTRUMENT CHECK-OUT
Instrument Hook Up
Connect vacuum gauge, dwell meter, tachometer and
timing light as recommended by the manufacturer of the
equipment being used.
Check and Adjust Dwell
1.
Start engine then ch^ck ignition dwell.
.2.
If dwell is not within specifications, adjust dwell as
follows:
V8 ENGINES
• With engine running at idle, raise the adjustment
screw window-and insert an Allen wrench in the
socket of the adjusting screw (fig. 12).
• Turn the adjusting screw as required until a dwell
reading of 30° is obtained. A 2° variation is al-
lowable for wear.
• Close access cover fully to prevent the entry of
dirt into the distributor.
NOTE: If a dwell meter is not available, turn
adjusting screw clockwise until engine starts to
misfire, then turn screw one-half turn in the op-
posite direction to complete adjustment.
IN LINE ENGINES
• Remove distributor cap and recheck point setting.
If dwell is still not within specifications check the
distributor as outlined in Section 6Y.
Check Dwell Variation
Slowly accelerate engine to 1500 rpm and note dwell
reading. Return engine to idle and note dwell reading. If
dwell variation exceeds specifications, check for worn
distributor shaft, worn distributor shaft bushing or loose
breaker plate.
WINDOW
"HEX" TYPE
WRENCH
Fig.
12 - Setting Point Dwell (V8)
Fig.
13 - Ignition Timing Marks
CHEVROLET CHASSIS SERVICE MANUAL
Page 273 of 659
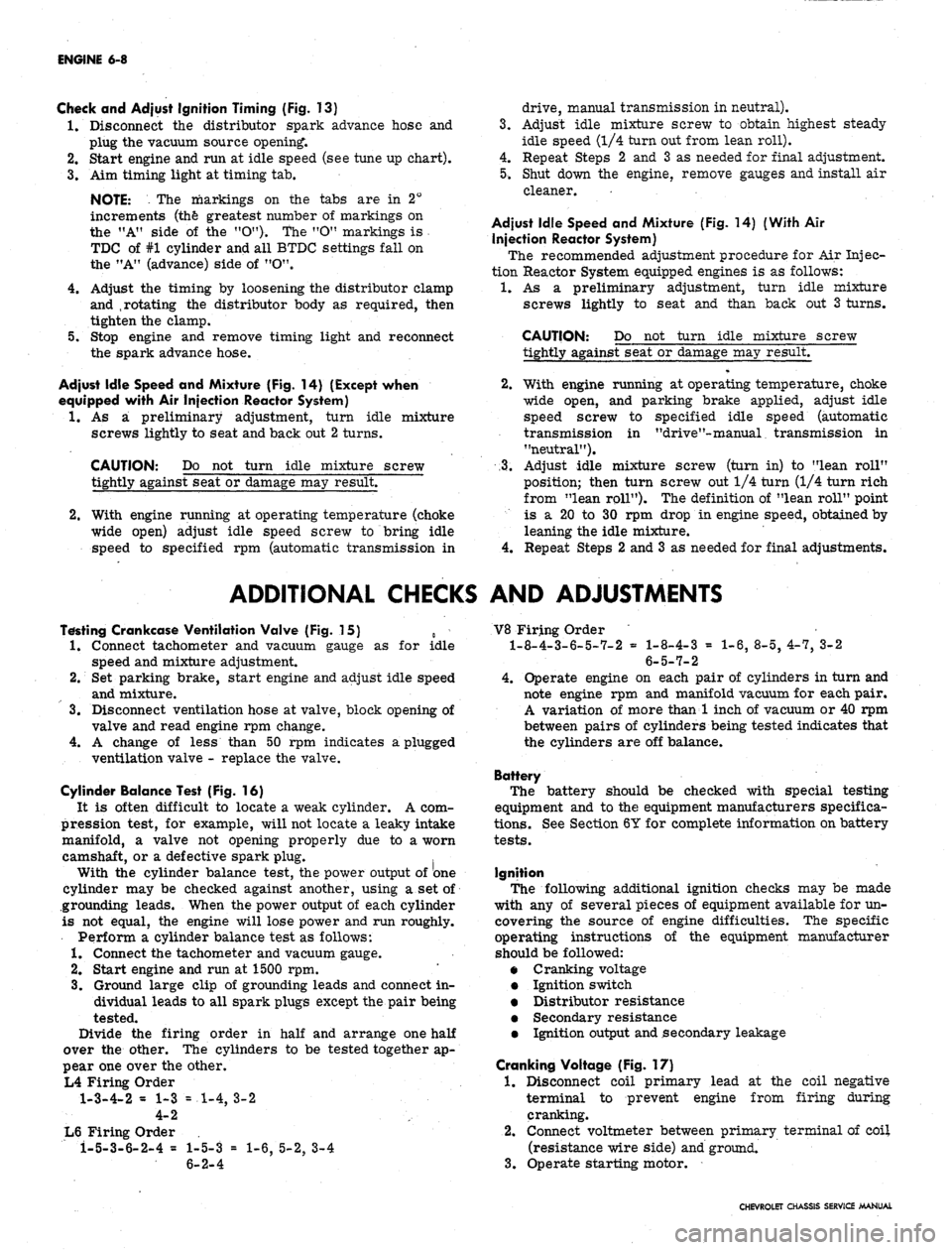
ENGINE
6-8
Check
and
Adjust Ignition Timing
(Fig. 13)
1.
Disconnect
the
distributor spark advance hose
and
plug
the
vacuum source opening.
2.
Start engine
and run at
idle speed
(see
tune
up
chart).
3.
Aim
timing light
at
timing
tab.
NOTE:
- The
markings
on the
tabs
are in 2°
increments
(the
greatest number
of
markings
on
the
"A"
side
of the "O"). the "O"
markings
is
TDC
of
#1 cylinder
and all
BTDC settings fall
on
the
"A"
(advance) side
of "O".
4.
Adjust
the
timing
by
loosening
the
distributor clamp
and
,
rotating
the
distributor body
as
required, then
tighten
the
clamp.
5.
Stop engine
and
remove timing light
and
reconnect
the spark advance hose.
Adjust Idle Speed
and
Mixture
(Fig. 14)
(Except when
equipped with
Air
Injection Reactor System)
1.
As a
preliminary adjustment, turn idle mixture
screws lightly
to
seat
and
back
out 2
turns.
CAUTION:
Do not
turn idle mixture screw
tightly against seat
or
damage
may
result.
2.
With engine running
at
operating temperature (choke
wide open) adjust idle speed screw
to
bring idle
speed
to
specified
rpm
(automatic transmission
in
drive, manual transmission
in
neutral).
3.
Adjust idle mixture screw
to
obtain highest steady
idle speed
(1/4
turn
out
from lean roll).
4.
Repeat Steps
2 and 3 as
needed
for
final adjustment.
5.
Shut down
the
engine, remove gauges
and
install
air
cleaner.
Adjust Idle Speed
and
Mixture
(Fig. 14)
(With
Air
Injection Reactor System)
The recommended adjustment procedure
for Air
Injec-
tion Reactor System equipped engines
is as
follows:
1.
As a
preliminary adjustment, turn idle mixture
screws lightly
to
seat
and
than back
out 3
turns.
CAUTION:
Do not
turn idle mixture screw
tightly against seat
or
damage
may
result.
2.
With engine running
at
operating temperature, choke
wide open,
and
parking brake applied, adjust idle
specified idle speed (automatic
"drive"-manual transmission
in
to
in
screw
transmission
"neutral").
;3.
Adjust idle mixture screw (turn
in) to
"lean roll"
position; then turn screw
out 1/4
turn
(1/4
turn rich
from "lean roll").
The
definition
of
"lean roll" point
is
a 20 to 30 rpm
drop
in
engine speed, obtained
by
leaning
the
idle mixture.
4.
Repeat Steps
2 and 3 as
needed
for
final adjustments.
ADDITIONAL CHECKS
AND
ADJUSTMENTS
Testing Crankcase Ventilation Valve
(Fig. 15) 0
1.
Connect tachometer
and
vacuum gauge
as for
idle
speed
and
mixture adjustment.
2.
Set
parking brake, start engine
and
adjust idle speed
and mixture.
3.
Disconnect ventilation hose
at
valve, block opening
of
valve
and
read engine
rpm
change.
4.
A
change
of
less than
50 rpm
indicates
a
plugged
ventilation valve
-
replace
the
valve.
Cylinder Balance Test
(Fig. 16)
It
is
often difficult
to
locate
a
weak cylinder.
A com-
pression test,
for
example, will
not
locate
a
leaky intake
manifold,
a
valve
not
opening properly
due to a
worn
camshaft,
or a
defective spark plug.
With
the
cylinder balance test,
the
power output
of one
cylinder
may be
checked against another, using
a set of
grounding leads. When
the
power output
of
each cylinder
is
not
equal,
the
engine will lose power
and run
roughly.
Perform
a
cylinder balance test
as
follows:
1.
Connect
the
tachometer
and
vacuum gauge.
2.
Start engine
and run at 1500 rpm.
3.
Ground large clip
of
grounding leads
and
connect
in-
dividual leads
to all
spark plugs except
the
pair being
tested.
Divide
the
firing order
in
half
and
arrange
one
half
over
the
other.
The
cylinders
to be
tested together
ap-
pear
one
over
the
other.
L4 Firing Order
V8 Firing Order
1-8-4-3-6-5-7-2
1-6, 8-5, 4-7, 3-2
1-3-4-2
= 1-3
4-2
L6 Firing Order
1-5-3-6-2-4
=
=
1-4. 3-2
1-5-3
6-2-4
1-6, 5-2, 3-4
1-8-4-3
6-5-7-2
4.
Operate engine
on
each pair
of
cylinders
in
turn
and
note engine
rpm and
manifold vacuum
for
each pair.
A variation
of
more than
1
inch
of
vacuum
or 40 rpm
between pairs
of
cylinders being tested indicates that
the cylinders
are off
balance.
Battery
The battery should
be
checked with special testing
equipment
and to the
equipment manufacturers specifica-
tions.
See
Section 6Y
for
complete information
on
battery
tests.
Ignition
The following additional ignition checks
may be
made
with
any of
several pieces
of
equipment available
for un-
covering
the
source
of
engine difficulties.
The
specific
operating instructions
of the
equipment manufacturer
should
be
followed:
Cranking voltage
Ignition switch
Distributor resistance
Secondary resistance
Ignition output
and
secondary leakage
Cranking Voltage
(Fig. 17)
1.
Disconnect coil primary lead
at the
coil negative
terminal
to
prevent engine from firing during
cranking.
2.
Connect voltmeter between primary terminal
of coi|
(resistance wire side)
and
ground.
3.
Operate starting motor.
CHEVROLET CHASSIS SERVICE MANUAL
Page 276 of 659
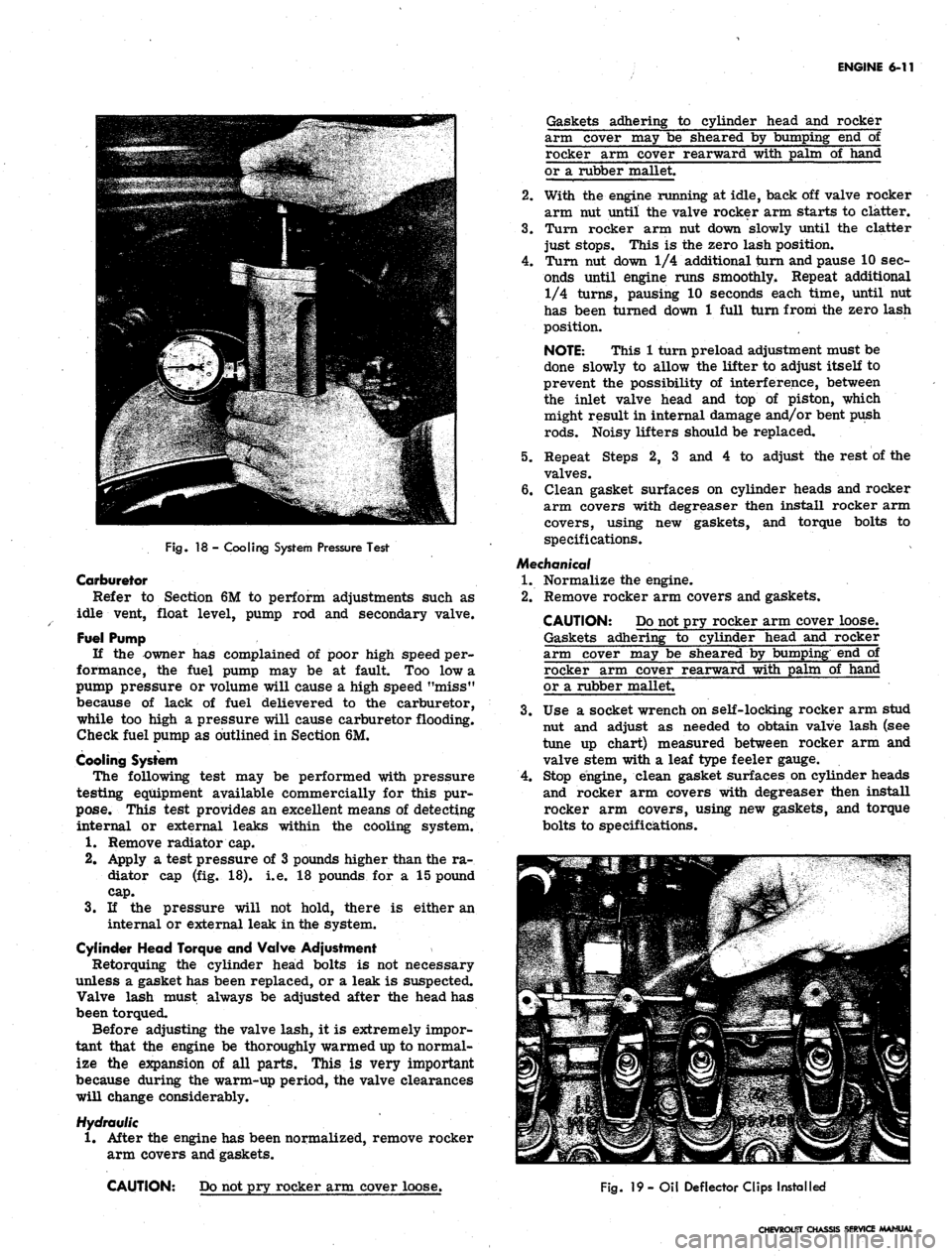
ENGINE 6-11
Fig.
18 - Cooling System Pressure Test
Carburetor
Refer to Section 6M to perform adjustments such as
idle vent, float level, pump rod and secondary valve.
Fuel Pump
If the owner has complained of poor high speed per-
formance, the fuel pump may be at fault. Too low a
pump pressure or volume will cause a high speed "miss"
because of lack of fuel delievered to the carburetor,
while too high a pressure will cause carburetor flooding.
Check fuel pump as outlined in Section 6M.
Cooling System
The following test may be performed with pressure
testing equipment available commercially for this pur-
pose.
This test provides an excellent means of detecting
internal or external leaks within the cooling system.
1.
Remove radiator cap.
2.
Apply a test pressure of 3 pounds higher than the ra-
diator cap (fig. 18). i.e. 18 pounds for a 15 pound
cap.
3.
If the pressure will not hold, there is either an
internal or external leak in the system.
Cylinder Head Torque and Valve Adjustment
Retorquing the cylinder head bolts is not necessary
unless a gasket has been replaced, or a leak is suspected.
Valve lash must always be adjusted after the head has
been torqued.
Before adjusting the valve lash, it is extremely impor-
tant that the engine be thoroughly warmed up to normal-
ize the expansion of all parts. This is very important
because during the warm-up period, the valve clearances
will change considerably.
Hydraulic
1.
After the engine has been normalized, remove rocker
arm covers and gaskets.
CAUTION: Do not pry rocker arm cover loose.
Gaskets adhering to cylinder head and rocker
arm cover may be sheared by bumping end of
rocker arm cover rearward with palm of hand
or a rubber mallet.
2.
With the engine running at idle, back off valve rocker
arm nut until the valve rocker arm starts to clatter.
3.
Turn rocker arm nut down slowly until the clatter
just stops. This is the zero lash position.
4.
Turn nut down 1/4 additional turn and pause 10 sec-
onds until engine runs smoothly* Repeat additional
1/4 turns, pausing 10 seconds each time, until nut
has been turned down 1 full turn from the zero lash
position.
NOTE: This 1 turn preload adjustment must be
done slowly to allow the lifter to adjust itself to
prevent the possibility of interference, between
the inlet valve head and top of piston, which
might result in internal damage and/or bent push
rods.
Noisy lifters should be replaced.
5.
Repeat Steps 2, 3 and 4 to adjust the rest of the
valves.
6. Clean gasket surfaces on cylinder heads and rocker
arm covers with degreaser then install rocker arm
covers, using new gaskets, and torque bolts to
specifications.
Mechanical
1.
Normalize the engine.
2.
Remove rocker arm covers and gaskets.
CAUTION: Do not pry rocker arm cover loose.
Gaskets adhering to cylinder head and rocker
arm cover may be sheared by bumping end of
rocker arm cover rearward with palm of hand
or a rubber mallet.
3.
Use a socket wrench on self-locking rocker arm stud
nut and adjust as needed to obtain valve lash (see
tune up chart) measured between rocker arm and
valve stem with a leaf type feeler gauge.
4.
Stop engine, clean gasket surfaces on cylinder heads
and rocker arm covers with degreaser then install
rocker arm covers, using new gaskets, and torque
bolts to specifications.
Fig.
19
- Oil Deflector Clips Installed
CHEVROLET CHASSIS SERVICE MANUAL
Page 288 of 659
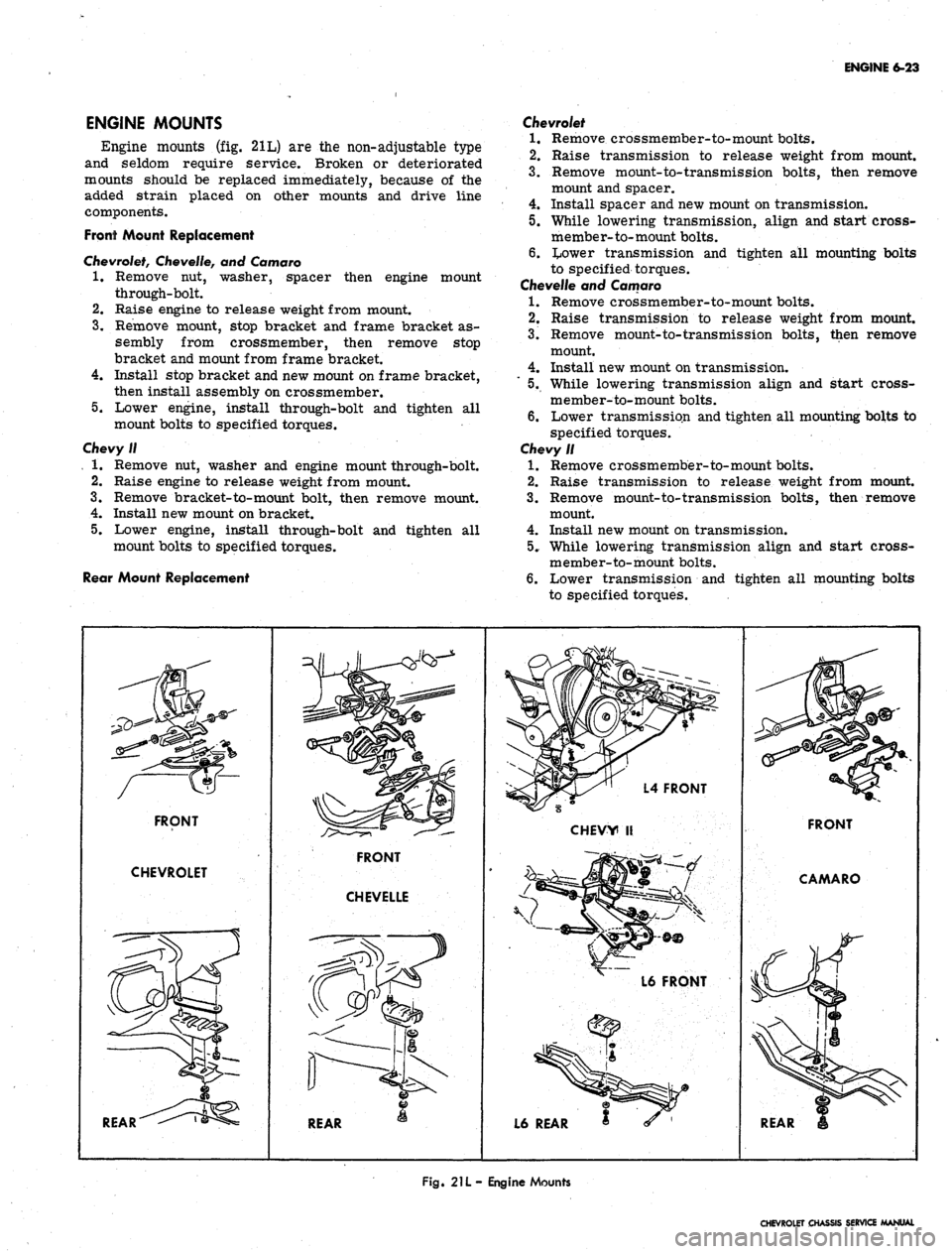
ENGINE 6-23
ENGINE MOUNTS
Engine mounts (fig. 21L) are the non-adjustable type
and seldom require service. Broken or deteriorated
mounts should be replaced immediately, because of the
added strain placed on other mounts and drive line
components.
Front Mount Replacement
Chevrolet,
Chevelle, and Comoro
1.
Remove nut, washer, spacer then engine mount
through-bolt.
2.
Raise engine to release weight from mount.
3.
Remove mount, stop bracket and frame bracket as-
sembly from crossmember, then remove stop
bracket and mount from frame bracket.
4.
Install stop bracket and new mount on frame bracket,
then install assembly on crossmember.
5.
Lower engine, install through-bolt and tighten all
mount bolts to specified torques.
Chevy II
, 1. Remove nut, washer and engine mount through-bolt.
2.
Raise engine to release weight from mount.
3.
Remove bracket-to-mount bolt, then remove mount.
4.
Install new mount on bracket.
5.
Lower engine, install through-bolt and tighten all
mount bolts to specified torques.
Rear Mount Replacement
Chevrolet
1.
Remove crossmember-to-mount bolts.
2.
Raise transmission to release weight from mount.
3.
Remove mount-to-trans mission bolts, then remove
mount and spacer.
4.
Install spacer and new mount on transmission.
5.
While lowering transmission, align and start cross-
member-to-mount bolts.
6. tower transmission and tighten all mounting bolts
to specified torques.
Chevelle and Camaro
1.
Remove crossmember-to-mount bolts.
2.
Raise transmission to release weight from mount.
3.
Remove mount-to-transmission bolts, then remove
mount.
4.
Install new mount on transmission.
5.
While lowering transmission align and start cross-
member-to-mount bolts.
6. Lower transmission and tighten all mounting bolts to
specified torques.
Chevy II
1.
Remove crossmember-to-mount bolts.
2.
Raise transmission to release weight from mount.
3.
Remove mount-to-transmission bolts, then remove
mount.
4.
Install new mount on transmission.
5.
While lowering transmission align and start cross-
member-to-mount bolts.
6. Lower transmission and tighten all mounting bolts
to specified torques.
FRONT
CHEVROLET
REAR
REAR
L4 FRONT
CHEVY II
L6 FRONT
L6 REAR
FRONT
CAMARO
REAR
Fig.
21L- Engine Mounts
CHEVROLET CHASSIS SERVICE MANUAL