CHEVROLET PLYMOUTH ACCLAIM 1993 Service Manual
Manufacturer: CHEVROLET, Model Year: 1993, Model line: PLYMOUTH ACCLAIM, Model: CHEVROLET PLYMOUTH ACCLAIM 1993Pages: 2438, PDF Size: 74.98 MB
Page 1611 of 2438
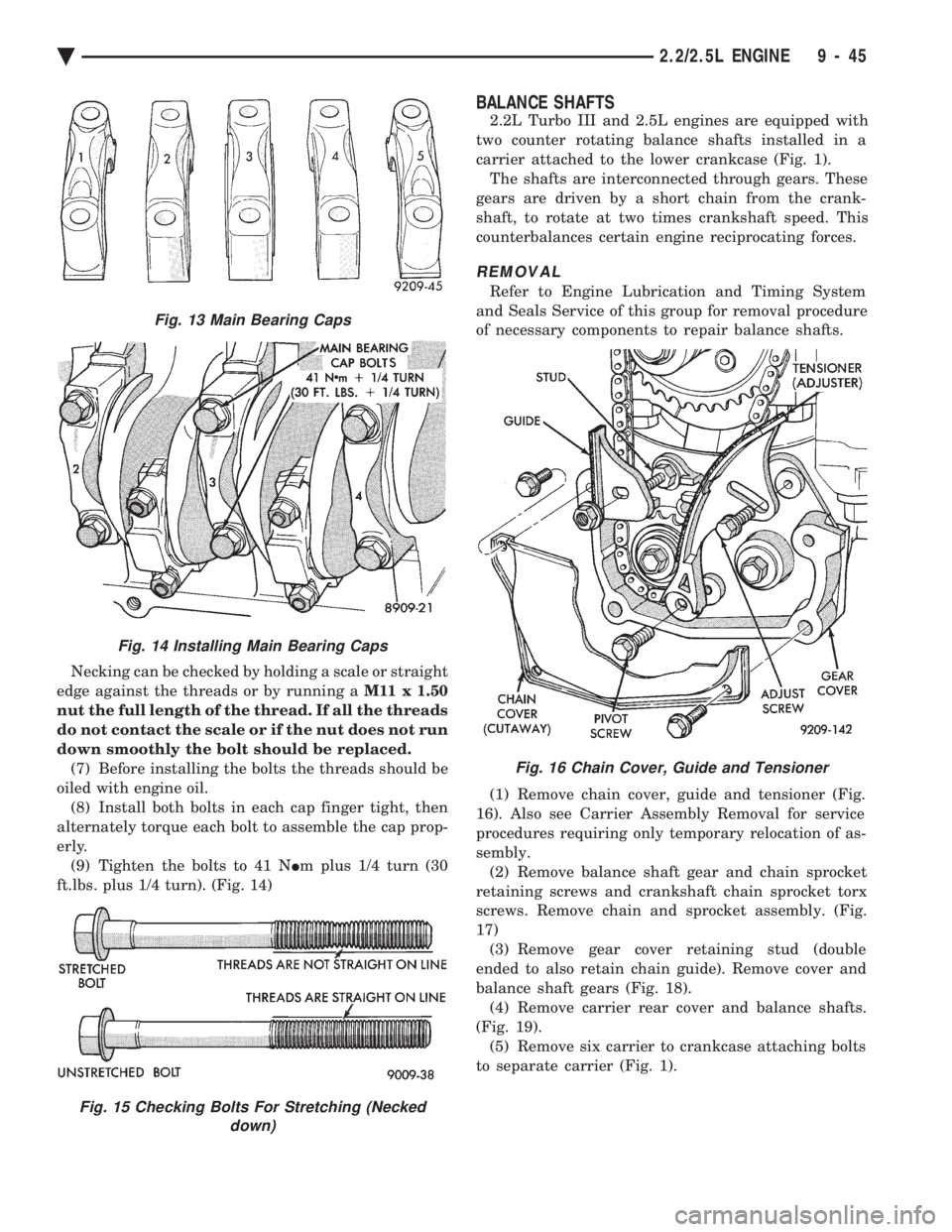
Necking can be checked by holding a scale or straight
edge against the threads or by running a M11 x 1.50
nut the full length of the thread. If all the threads
do not contact the scale or if the nut does not run
down smoothly the bolt should be replaced. (7) Before installing the bolts the threads should be
oiled with engine oil. (8) Install both bolts in each cap finger tight, then
alternately torque each bolt to assemble the cap prop-
erly. (9) Tighten the bolts to 41 N Im plus 1/4 turn (30
ft.lbs. plus 1/4 turn). (Fig. 14)
BALANCE SHAFTS
2.2L Turbo III and 2.5L engines are equipped with
two counter rotating balance shafts installed in a
carrier attached to the lower crankcase (Fig. 1). The shafts are interconnected through gears. These
gears are driven by a short chain from the crank-
shaft, to rotate at two times crankshaft speed. This
counterbalances certain engine reciprocating forces.
REMOVAL
Refer to Engine Lubrication and Timing System
and Seals Service of this group for removal procedure
of necessary components to repair balance shafts.
(1) Remove chain cover, guide and tensioner (Fig.
16). Also see Carrier Assembly Removal for service
procedures requiring only temporary relocation of as-
sembly. (2) Remove balance shaft gear and chain sprocket
retaining screws and crankshaft chain sprocket torx
screws. Remove chain and sprocket assembly. (Fig.
17) (3) Remove gear cover retaining stud (double
ended to also retain chain guide). Remove cover and
balance shaft gears (Fig. 18). (4) Remove carrier rear cover and balance shafts.
(Fig. 19). (5) Remove six carrier to crankcase attaching bolts
to separate carrier (Fig. 1).
Fig. 16 Chain Cover, Guide and Tensioner
Fig. 13 Main Bearing Caps
Fig. 14 Installing Main Bearing Caps
Fig. 15 Checking Bolts For Stretching (Necked down)
Ä 2.2/2.5L ENGINE 9 - 45
Page 1612 of 2438
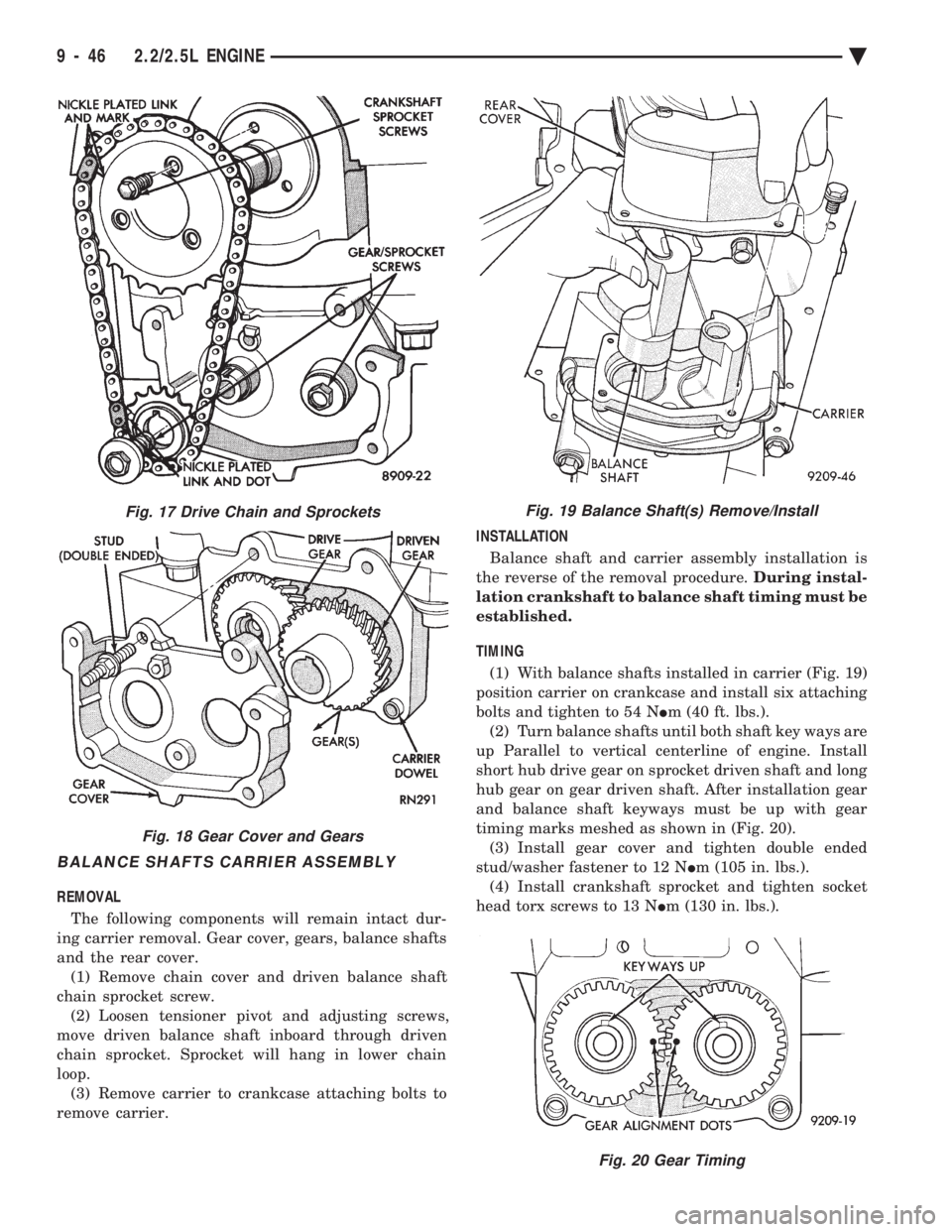
BALANCE SHAFTS CARRIER ASSEMBLY
REMOVAL The following components will remain intact dur-
ing carrier removal. Gear cover, gears, balance shafts
and the rear cover. (1) Remove chain cover and driven balance shaft
chain sprocket screw. (2) Loosen tensioner pivot and adjusting screws,
move driven balance shaft inboard through driven
chain sprocket. Sprocket will hang in lower chain
loop. (3) Remove carrier to crankcase attaching bolts to
remove carrier. INSTALLATION
Balance shaft and carrier assembly installation is
the reverse of the removal procedure. During instal-
lation crankshaft to balance shaft timing must be
established.
TIMING
(1) With balance shafts installed in carrier (Fig. 19)
position carrier on crankcase and install six attaching
bolts and tighten to 54 N Im (40 ft. lbs.).
(2) Turn balance shafts until both shaft key ways are
up Parallel to vertical centerline of engine. Install
short hub drive gear on sprocket driven shaft and long
hub gear on gear driven shaft. After installation gear
and balance shaft keyways must be up with gear
timing marks meshed as shown in (Fig. 20). (3) Install gear cover and tighten double ended
stud/washer fastener to 12 N Im (105 in. lbs.).
(4) Install crankshaft sprocket and tighten socket
head torx screws to 13 N Im (130 in. lbs.).
Fig. 20 Gear Timing
Fig. 17 Drive Chain and Sprockets
Fig. 18 Gear Cover and Gears
Fig. 19 Balance Shaft(s) Remove/Install
9 - 46 2.2/2.5L ENGINE Ä
Page 1613 of 2438
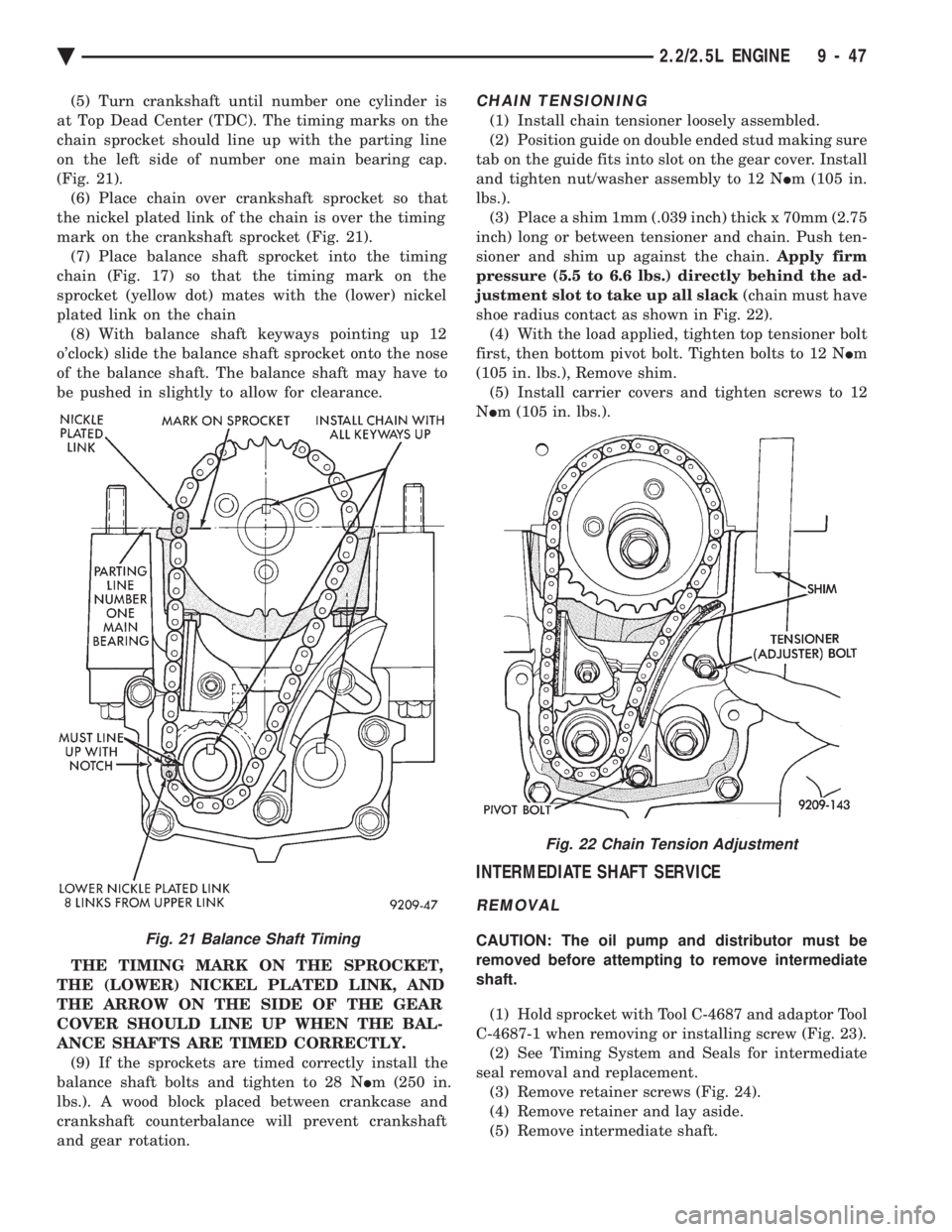
(5) Turn crankshaft until number one cylinder is
at Top Dead Center (TDC). The timing marks on the
chain sprocket should line up with the parting line
on the left side of number one main bearing cap.
(Fig. 21). (6) Place chain over crankshaft sprocket so that
the nickel plated link of the chain is over the timing
mark on the crankshaft sprocket (Fig. 21). (7) Place balance shaft sprocket into the timing
chain (Fig. 17) so that the timing mark on the
sprocket (yellow dot) mates with the (lower) nickel
plated link on the chain (8) With balance shaft keyways pointing up 12
o'clock) slide the balance shaft sprocket onto the nose
of the balance shaft. The balance shaft may have to
be pushed in slightly to allow for clearance.
THE TIMING MARK ON THE SPROCKET,
THE (LOWER) NICKEL PLATED LINK, AND
THE ARROW ON THE SIDE OF THE GEAR
COVER SHOULD LINE UP WHEN THE BAL-
ANCE SHAFTS ARE TIMED CORRECTLY. (9) If the sprockets are timed correctly install the
balance shaft bolts and tighten to 28 N Im (250 in.
lbs.). A wood block placed between crankcase and
crankshaft counterbalance will prevent crankshaft
and gear rotation.CHAIN TENSIONING
(1) Install chain tensioner loosely assembled.
(2) Position guide on double ended stud making sure
tab on the guide fits into slot on the gear cover. Install
and tighten nut/washer assembly to 12 N Im (105 in.
lbs.). (3) Place a shim 1mm (.039 inch) thick x 70mm (2.75
inch) long or between tensioner and chain. Push ten-
sioner and shim up against the chain. Apply firm
pressure (5.5 to 6.6 lbs.) directly behind the ad-
justment slot to take up all slack (chain must have
shoe radius contact as shown in Fig. 22). (4) With the load applied, tighten top tensioner bolt
first, then bottom pivot bolt. Tighten bolts to 12 N Im
(105 in. lbs.), Remove shim. (5) Install carrier covers and tighten screws to 12
N Im (105 in. lbs.).
INTERMEDIATE SHAFT SERVICE
REMOVAL
CAUTION: The oil pump and distributor must be
removed before attempting to remove intermediate
shaft.
(1) Hold sprocket with Tool C-4687 and adaptor Tool
C-4687-1 when removing or installing screw (Fig. 23). (2) See Timing System and Seals for intermediate
seal removal and replacement. (3) Remove retainer screws (Fig. 24).
(4) Remove retainer and lay aside.
(5) Remove intermediate shaft.Fig. 21 Balance Shaft Timing
Fig. 22 Chain Tension Adjustment
Ä 2.2/2.5L ENGINE 9 - 47
Page 1614 of 2438
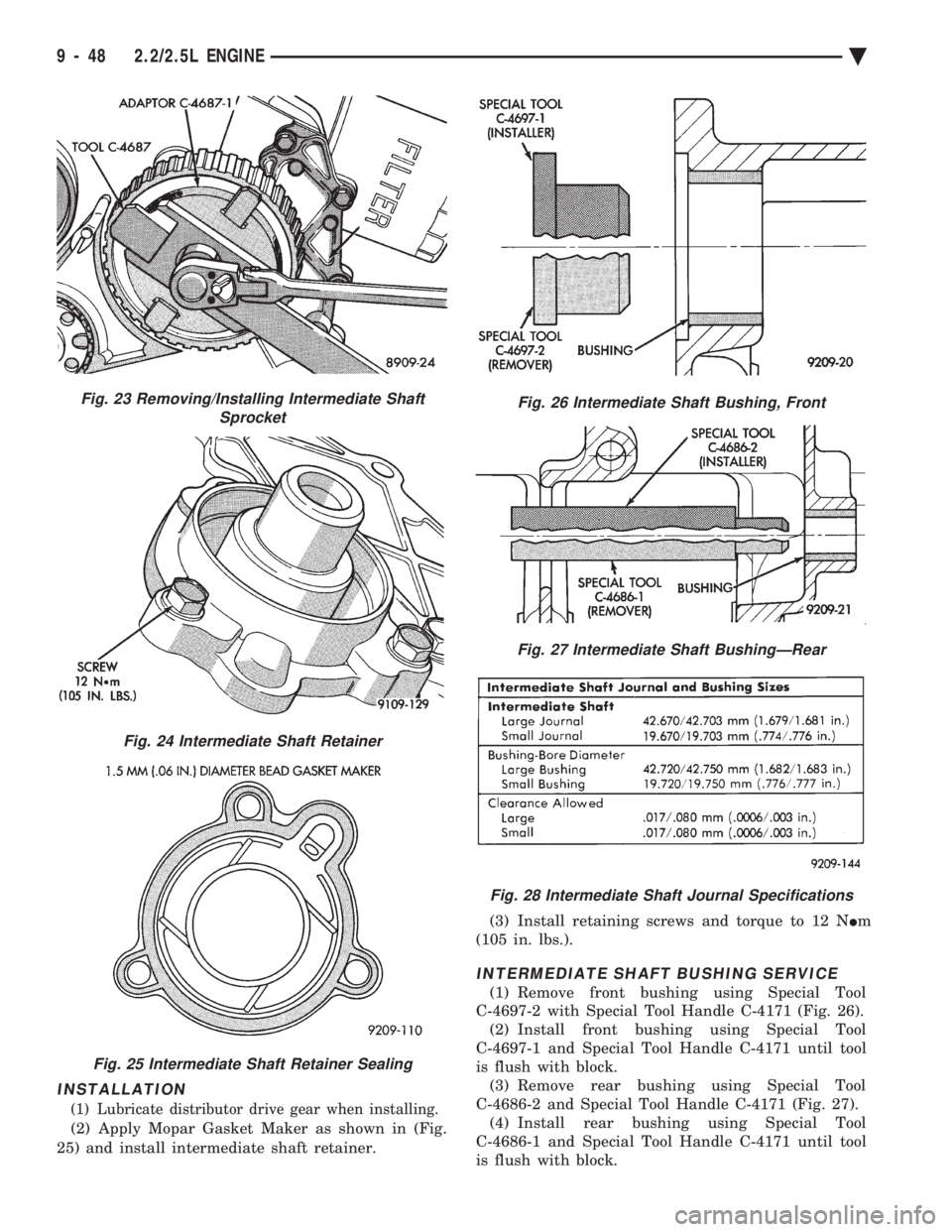
INSTALLATION
(1) Lubricate distributor drive gear when installing.
(2) Apply Mopar Gasket Maker as shown in (Fig.
25) and install intermediate shaft retainer. (3) Install retaining screws and torque to 12 N
Im
(105 in. lbs.).
INTERMEDIATE SHAFT BUSHING SERVICE
(1) Remove front bushing using Special Tool
C-4697-2 with Special Tool Handle C-4171 (Fig. 26). (2) Install front bushing using Special Tool
C-4697-1 and Special Tool Handle C-4171 until tool
is flush with block. (3) Remove rear bushing using Special Tool
C-4686-2 and Special Tool Handle C-4171 (Fig. 27). (4) Install rear bushing using Special Tool
C-4686-1 and Special Tool Handle C-4171 until tool
is flush with block.
Fig. 23 Removing/Installing Intermediate Shaft Sprocket
Fig. 24 Intermediate Shaft Retainer
Fig. 25 Intermediate Shaft Retainer Sealing
Fig. 26 Intermediate Shaft Bushing, Front
Fig. 27 Intermediate Shaft BushingÐRear
Fig. 28 Intermediate Shaft Journal Specifications
9 - 48 2.2/2.5L ENGINE Ä
Page 1615 of 2438
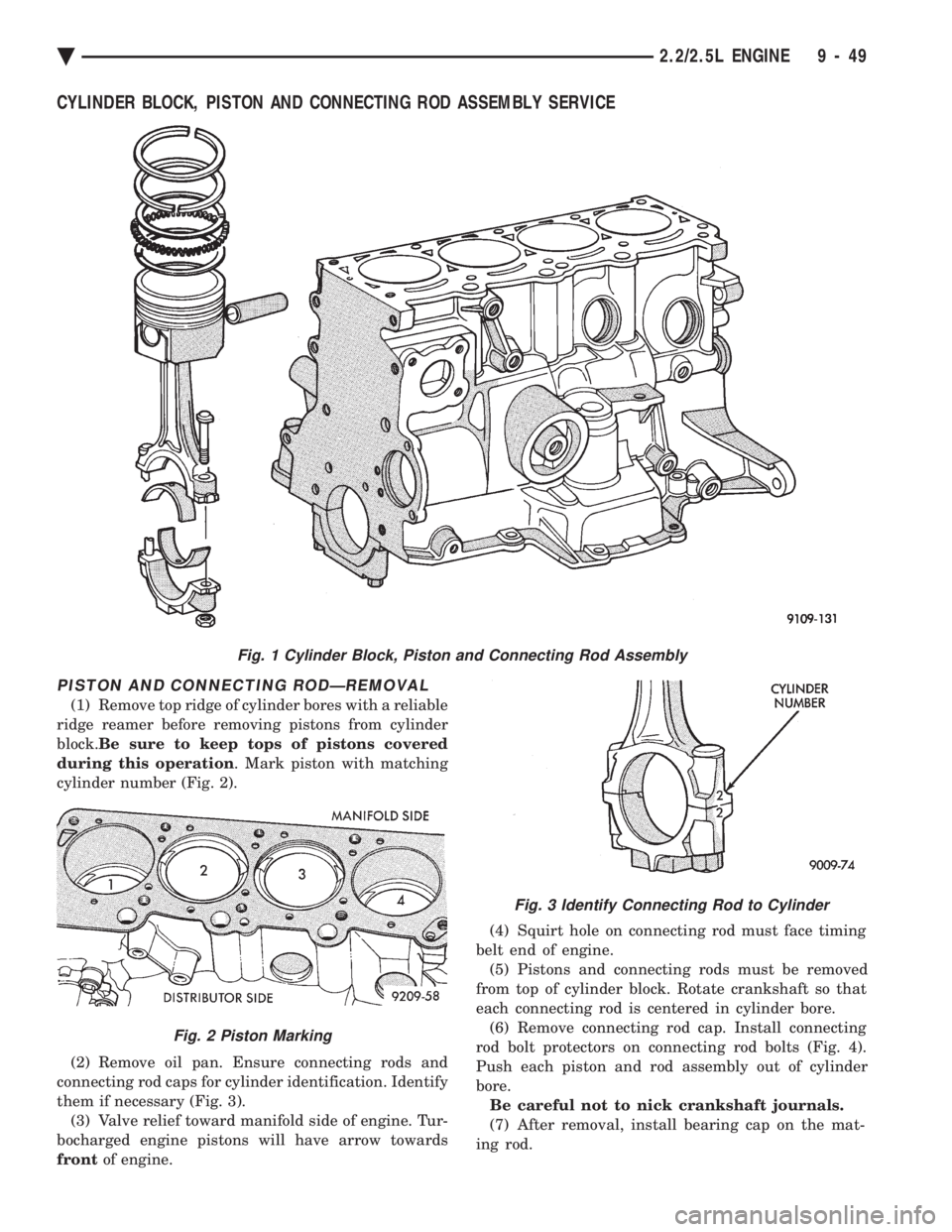
CYLINDER BLOCK, PISTON AND CONNECTING ROD ASSEMBLY SERVICE
PISTON AND CONNECTING RODÐREMOVAL
(1) Remove top ridge of cylinder bores with a reliable
ridge reamer before removing pistons from cylinder
block. Be sure to keep tops of pistons covered
during this operation . Mark piston with matching
cylinder number (Fig. 2).
(2) Remove oil pan. Ensure connecting rods and
connecting rod caps for cylinder identification. Identify
them if necessary (Fig. 3). (3) Valve relief toward manifold side of engine. Tur-
bocharged engine pistons will have arrow towards
front of engine. (4) Squirt hole on connecting rod must face timing
belt end of engine. (5) Pistons and connecting rods must be removed
from top of cylinder block. Rotate crankshaft so that
each connecting rod is centered in cylinder bore. (6) Remove connecting rod cap. Install connecting
rod bolt protectors on connecting rod bolts (Fig. 4).
Push each piston and rod assembly out of cylinder
bore. Be careful not to nick crankshaft journals.
(7) After removal, install bearing cap on the mat-
ing rod.
Fig. 1 Cylinder Block, Piston and Connecting Rod Assembly
Fig. 3 Identify Connecting Rod to Cylinder
Fig. 2 Piston Marking
Ä 2.2/2.5L ENGINE 9 - 49
Page 1616 of 2438
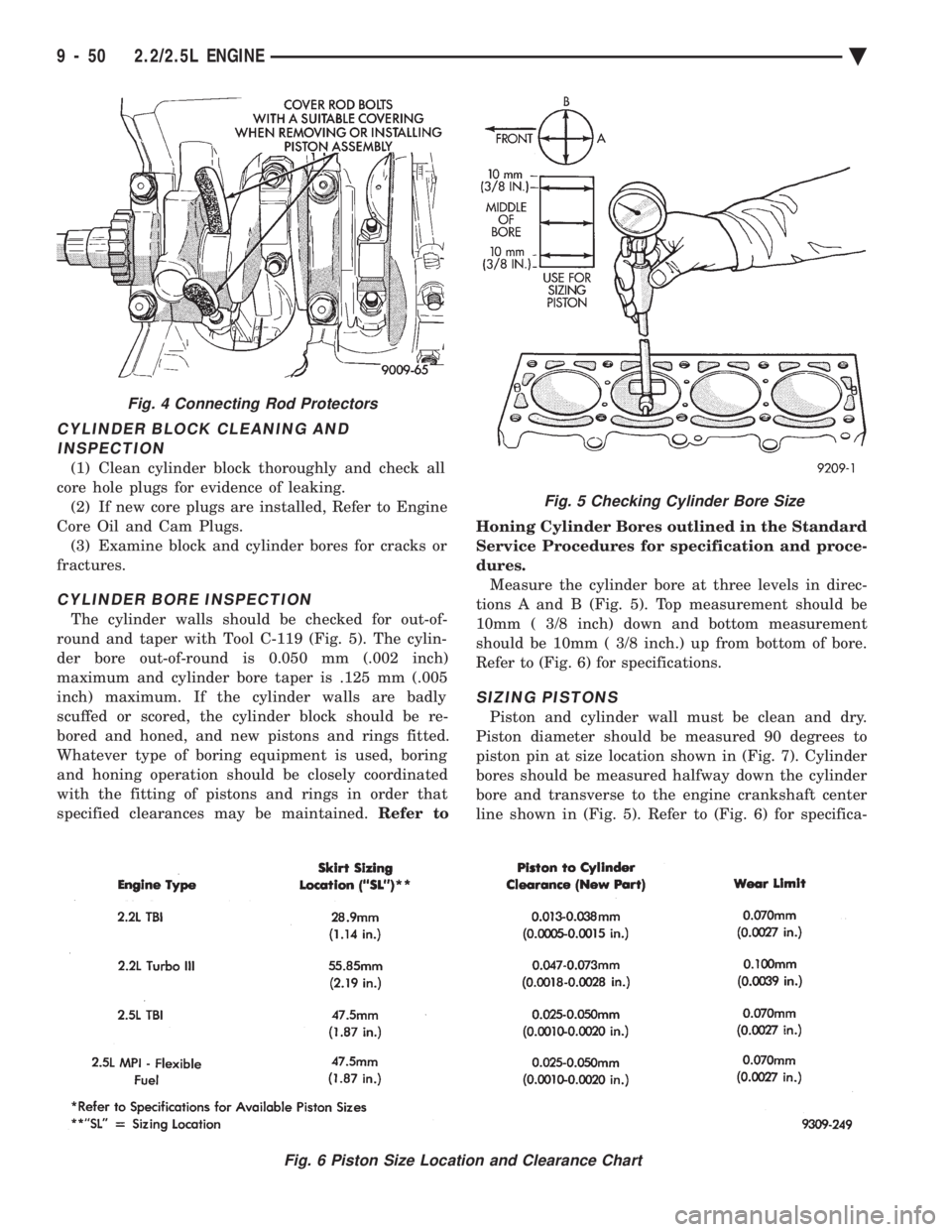
CYLINDER BLOCK CLEANING AND INSPECTION
(1) Clean cylinder block thoroughly and check all
core hole plugs for evidence of leaking. (2) If new core plugs are installed, Refer to Engine
Core Oil and Cam Plugs. (3) Examine block and cylinder bores for cracks or
fractures.
CYLINDER BORE INSPECTION
The cylinder walls should be checked for out-of-
round and taper with Tool C-119 (Fig. 5). The cylin-
der bore out-of-round is 0.050 mm (.002 inch)
maximum and cylinder bore taper is .125 mm (.005
inch) maximum. If the cylinder walls are badly
scuffed or scored, the cylinder block should be re-
bored and honed, and new pistons and rings fitted.
Whatever type of boring equipment is used, boring
and honing operation should be closely coordinated
with the fitting of pistons and rings in order that
specified clearances may be maintained. Refer to Honing Cylinder Bores outlined in the Standard
Service Procedures for specification and proce-
dures.
Measure the cylinder bore at three levels in direc-
tions A and B (Fig. 5). Top measurement should be
10mm ( 3/8 inch) down and bottom measurement
should be 10mm ( 3/8 inch.) up from bottom of bore.
Refer to (Fig. 6) for specifications.
SIZING PISTONS
Piston and cylinder wall must be clean and dry.
Piston diameter should be measured 90 degrees to
piston pin at size location shown in (Fig. 7). Cylinder
bores should be measured halfway down the cylinder
bore and transverse to the engine crankshaft center
line shown in (Fig. 5). Refer to (Fig. 6) for specifica-
Fig. 5 Checking Cylinder Bore Size
Fig. 6 Piston Size Location and Clearance Chart
Fig. 4 Connecting Rod Protectors
9 - 50 2.2/2.5L ENGINE Ä
Page 1617 of 2438
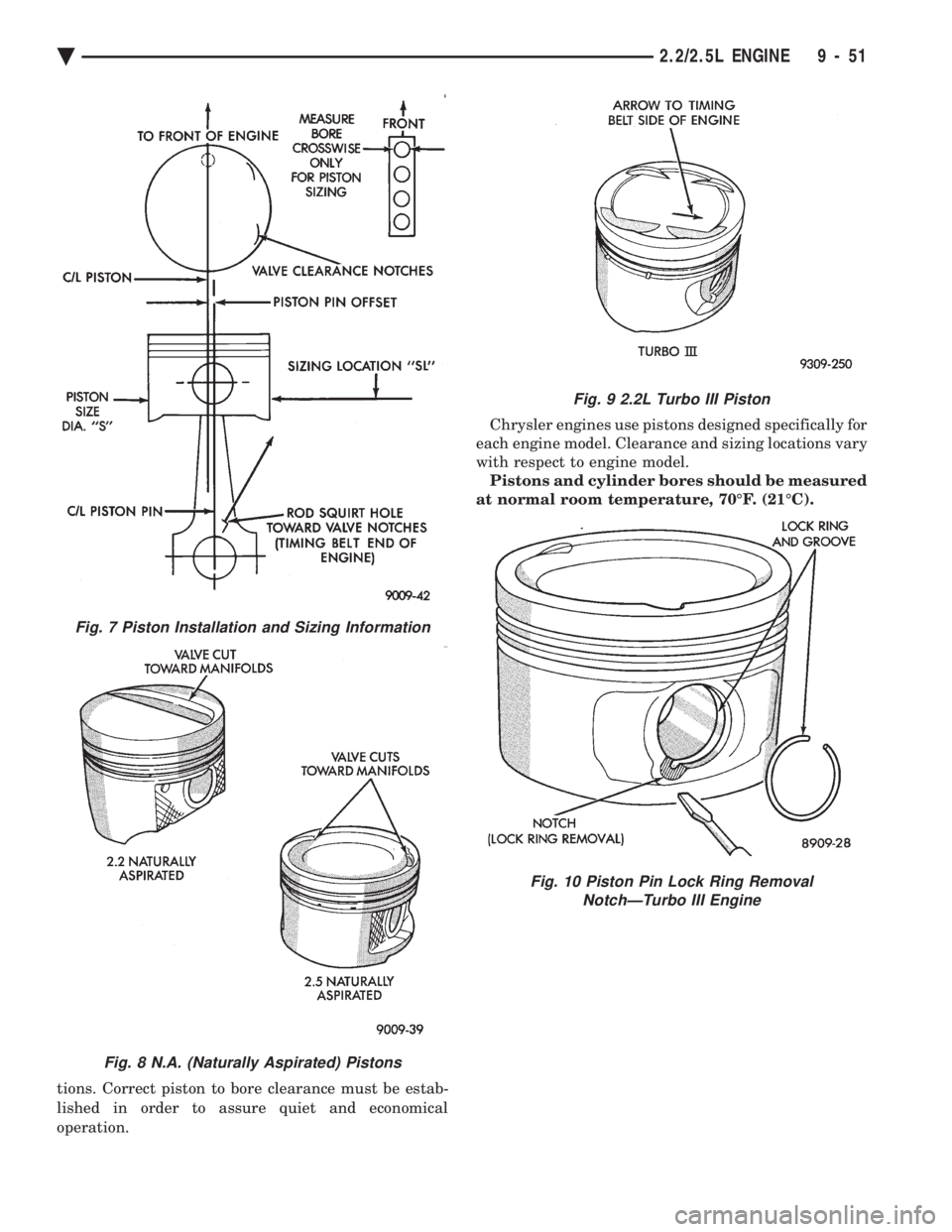
tions. Correct piston to bore clearance must be estab-
lished in order to assure quiet and economical
operation. Chrysler engines use pistons designed specifically for
each engine model. Clearance and sizing locations vary
with respect to engine model. Pistons and cylinder bores should be measured
at normal room temperature, 70ÉF. (21ÉC).
Fig. 7 Piston Installation and Sizing Information
Fig. 8 N.A. (Naturally Aspirated) Pistons
Fig. 9 2.2L Turbo III Piston
Fig. 10 Piston Pin Lock Ring Removal NotchÐTurbo III Engine
Ä 2.2/2.5L ENGINE 9 - 51
Page 1618 of 2438
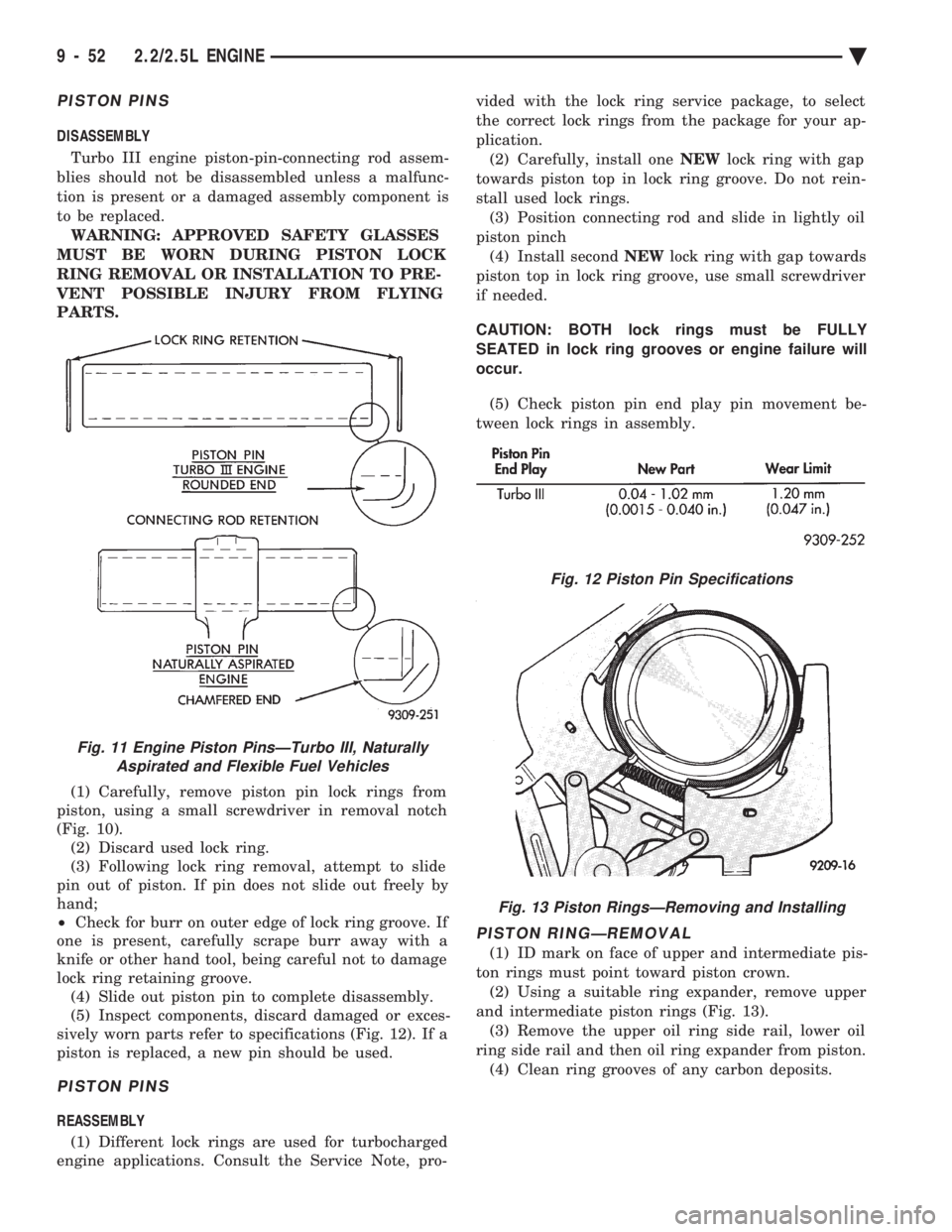
PISTON PINS
DISASSEMBLY Turbo III engine piston-pin-connecting rod assem-
blies should not be disassembled unless a malfunc-
tion is present or a damaged assembly component is
to be replaced. WARNING: APPROVED SAFETY GLASSES
MUST BE WORN DURING PISTON LOCK
RING REMOVAL OR INSTALLATION TO PRE-
VENT POSSIBLE INJURY FROM FLYING
PARTS.
(1) Carefully, remove piston pin lock rings from
piston, using a small screwdriver in removal notch
(Fig. 10). (2) Discard used lock ring.
(3) Following lock ring removal, attempt to slide
pin out of piston. If pin does not slide out freely by
hand;
² Check for burr on outer edge of lock ring groove. If
one is present, carefully scrape burr away with a
knife or other hand tool, being careful not to damage
lock ring retaining groove. (4) Slide out piston pin to complete disassembly.
(5) Inspect components, discard damaged or exces-
sively worn parts refer to specifications (Fig. 12). If a
piston is replaced, a new pin should be used.
PISTON PINS
REASSEMBLY
(1) Different lock rings are used for turbocharged
engine applications. Consult the Service Note, pro- vided with the lock ring service package, to select
the correct lock rings from the package for your ap-
plication.
(2) Carefully, install one NEWlock ring with gap
towards piston top in lock ring groove. Do not rein-
stall used lock rings. (3) Position connecting rod and slide in lightly oil
piston pinch (4) Install second NEWlock ring with gap towards
piston top in lock ring groove, use small screwdriver
if needed.
CAUTION: BOTH lock rings must be FULLY
SEATED in lock ring grooves or engine failure will
occur.
(5) Check piston pin end play pin movement be-
tween lock rings in assembly.
PISTON RINGÐREMOVAL
(1) ID mark on face of upper and intermediate pis-
ton rings must point toward piston crown. (2) Using a suitable ring expander, remove upper
and intermediate piston rings (Fig. 13). (3) Remove the upper oil ring side rail, lower oil
ring side rail and then oil ring expander from piston. (4) Clean ring grooves of any carbon deposits.
Fig. 11 Engine Piston PinsÐTurbo III, Naturally Aspirated and Flexible Fuel Vehicles
Fig. 12 Piston Pin Specifications
Fig. 13 Piston RingsÐRemoving and Installing
9 - 52 2.2/2.5L ENGINE Ä
Page 1619 of 2438
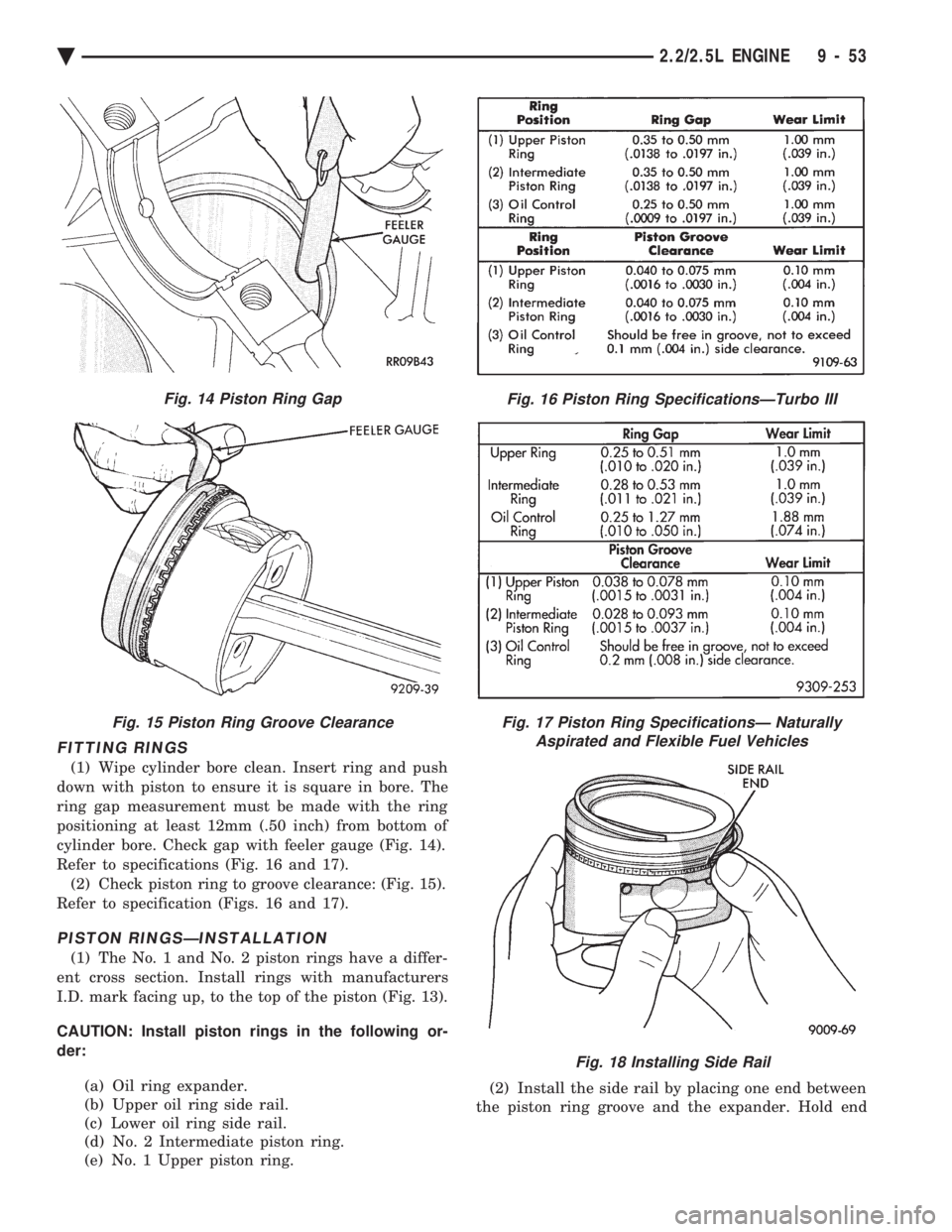
FITTING RINGS
(1) Wipe cylinder bore clean. Insert ring and push
down with piston to ensure it is square in bore. The
ring gap measurement must be made with the ring
positioning at least 12mm (.50 inch) from bottom of
cylinder bore. Check gap with feeler gauge (Fig. 14).
Refer to specifications (Fig. 16 and 17). (2) Check piston ring to groove clearance: (Fig. 15).
Refer to specification (Figs. 16 and 17).
PISTON RINGSÐINSTALLATION
(1) The No. 1 and No. 2 piston rings have a differ-
ent cross section. Install rings with manufacturers
I.D. mark facing up, to the top of the piston (Fig. 13).
CAUTION: Install piston rings in the following or-
der:
(a) Oil ring expander.
(b) Upper oil ring side rail.
(c) Lower oil ring side rail.
(d) No. 2 Intermediate piston ring.
(e) No. 1 Upper piston ring. (2) Install the side rail by placing one end between
the piston ring groove and the expander. Hold end
Fig. 16 Piston Ring SpecificationsÐTurbo III
Fig. 17 Piston Ring SpecificationsÐ Naturally Aspirated and Flexible Fuel Vehicles
Fig. 18 Installing Side Rail
Fig. 14 Piston Ring Gap
Fig. 15 Piston Ring Groove Clearance
Ä 2.2/2.5L ENGINE 9 - 53
Page 1620 of 2438
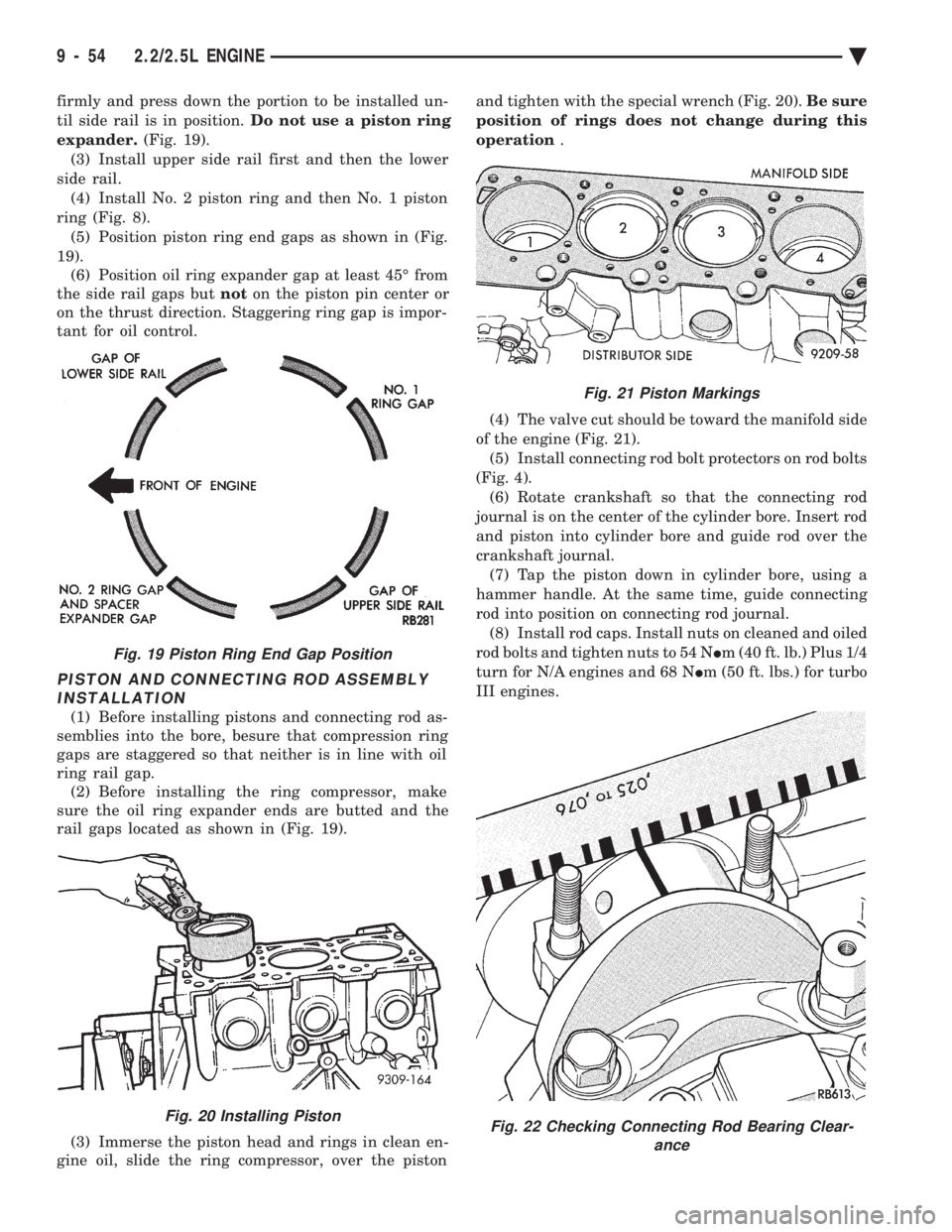
firmly and press down the portion to be installed un-
til side rail is in position. Do not use a piston ring
expander. (Fig. 19).
(3) Install upper side rail first and then the lower
side rail. (4) Install No. 2 piston ring and then No. 1 piston
ring (Fig. 8). (5) Position piston ring end gaps as shown in (Fig.
19). (6) Position oil ring expander gap at least 45É from
the side rail gaps but noton the piston pin center or
on the thrust direction. Staggering ring gap is impor-
tant for oil control.
PISTON AND CONNECTING ROD ASSEMBLY INSTALLATION
(1) Before installing pistons and connecting rod as-
semblies into the bore, besure that compression ring
gaps are staggered so that neither is in line with oil
ring rail gap. (2) Before installing the ring compressor, make
sure the oil ring expander ends are butted and the
rail gaps located as shown in (Fig. 19).
(3) Immerse the piston head and rings in clean en-
gine oil, slide the ring compressor, over the piston and tighten with the special wrench (Fig. 20).
Be sure
position of rings does not change during this
operation .
(4) The valve cut should be toward the manifold side
of the engine (Fig. 21). (5) Install connecting rod bolt protectors on rod bolts
(Fig. 4). (6) Rotate crankshaft so that the connecting rod
journal is on the center of the cylinder bore. Insert rod
and piston into cylinder bore and guide rod over the
crankshaft journal. (7) Tap the piston down in cylinder bore, using a
hammer handle. At the same time, guide connecting
rod into position on connecting rod journal. (8) Install rod caps. Install nuts on cleaned and oiled
rod bolts and tighten nuts to 54 N Im (40 ft. lb.) Plus 1/4
turn for N/A engines and 68 N Im (50 ft. lbs.) for turbo
III engines.
Fig. 19 Piston Ring End Gap Position
Fig. 20 Installing Piston
Fig. 21 Piston Markings
Fig. 22 Checking Connecting Rod Bearing Clear- ance
9 - 54 2.2/2.5L ENGINE Ä