CHEVROLET PLYMOUTH ACCLAIM 1993 Service Manual
Manufacturer: CHEVROLET, Model Year: 1993, Model line: PLYMOUTH ACCLAIM, Model: CHEVROLET PLYMOUTH ACCLAIM 1993Pages: 2438, PDF Size: 74.98 MB
Page 1681 of 2438

CYLINDER BORE INSPECTION
The cylinder walls should be checked for out- of-
round and taper with Tool C-119 (Fig. 4). If the cylinder
walls are badly scuffed or scored, the cylinder block
should be replaced. Measure the cylinder bore at three levels in direc-
tions A and B (Fig. 4). Top measurement should be
12mm (.50 inch) down and bottom measurement
should be 12mm (.50 inch.) up from bottom of bore.
Refer to (Fig. 5) for specifications.
FINISHED PISTONS
All pistons are machined to the same weight in
grams, to maintain piston balance. For cylinder bores
which have been honed, new pistons and connecting
rod assemblies are available for service.
FITTING PISTONS
Piston and cylinder wall must be clean and dry.
Piston diameter should be measured 90 degrees to
piston pin at size location shown in (Fig. 6). Cylinder
bores should be measured halfway down the cylinder
bore and transverse to the engine crankshaft center
line shown in (Fig. 4). Refer to (Fig. 5) for specifica-
tions. Pistons and cylinder bores should be measured
at normal room temperature, 70ÉF (21ÉC)
PISTON PINS
The piston pin rotates in the piston only, and is
retained by the press interference fit of the piston pin
in the connecting rod. The piston pin is not to be
removed damage to the piston may result.
FITTING RINGS
(1) Wipe cylinder bore clean. Insert ring and push
down with piston to ensure it is square in bore. The
ring gap measurement must be made with the ring
positioning at least 12mm (.50 inch) from bottom of
cylinder bore. Check gap with feeler gauge (Fig. 7).
Fig. 5 Cylinder Bore and Piston Specifications
Fig. 6 Piston Measurements
Fig. 7 Check Gap on Piston Rings
Fig. 4 Checking Cylinder Bore Size
Ä 3.3/3.8L ENGINE 9 - 115
Page 1682 of 2438
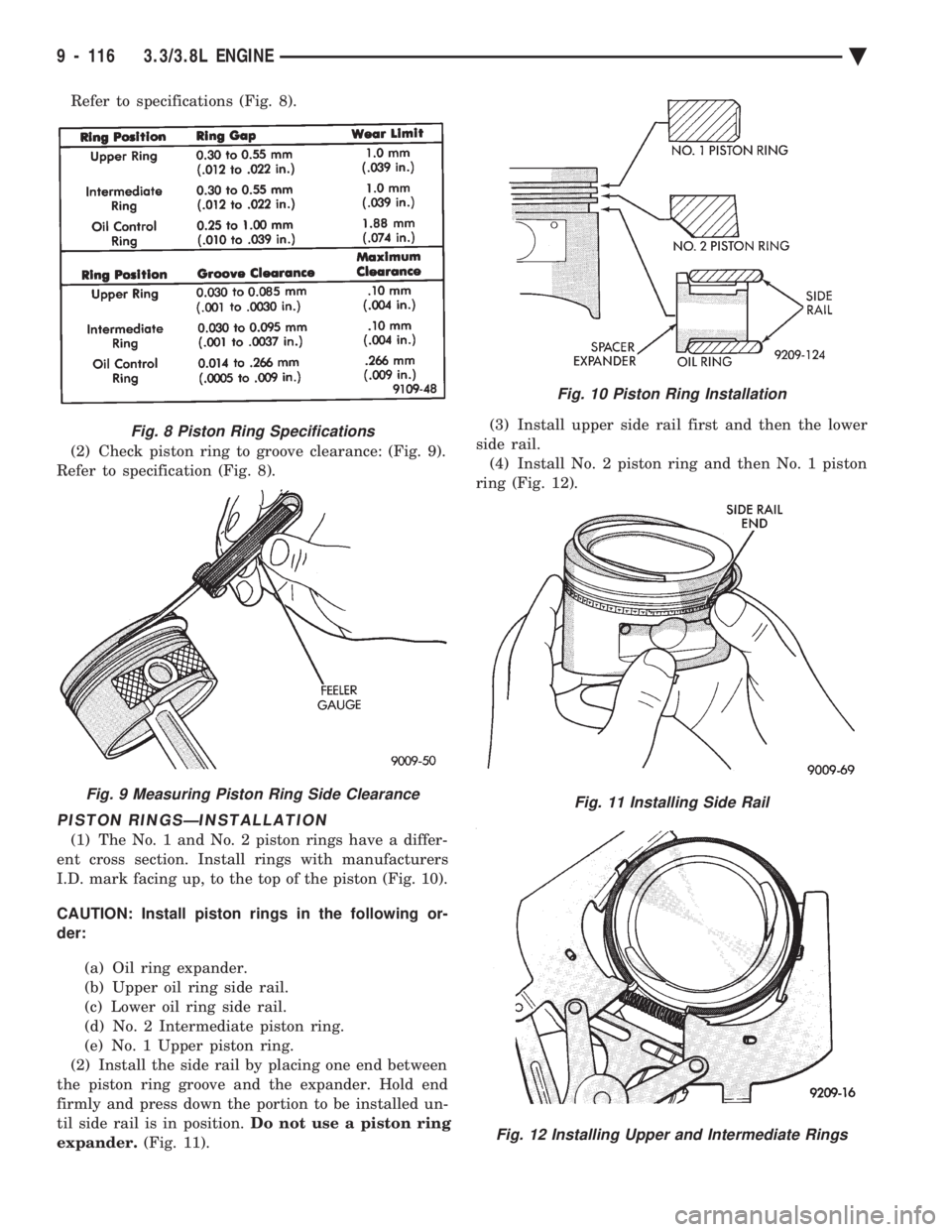
Refer to specifications (Fig. 8).
(2) Check piston ring to groove clearance: (Fig. 9).
Refer to specification (Fig. 8).
PISTON RINGSÐINSTALLATION
(1) The No. 1 and No. 2 piston rings have a differ-
ent cross section. Install rings with manufacturers
I.D. mark facing up, to the top of the piston (Fig. 10).
CAUTION: Install piston rings in the following or-
der:
(a) Oil ring expander.
(b) Upper oil ring side rail.
(c) Lower oil ring side rail.
(d) No. 2 Intermediate piston ring.
(e) No. 1 Upper piston ring.
(2) Install the side rail by placing one end between
the piston ring groove and the expander. Hold end
firmly and press down the portion to be installed un-
til side rail is in position. Do not use a piston ring
expander. (Fig. 11). (3) Install upper side rail first and then the lower
side rail. (4) Install No. 2 piston ring and then No. 1 piston
ring (Fig. 12).
Fig. 8 Piston Ring Specifications
Fig. 9 Measuring Piston Ring Side Clearance
Fig. 10 Piston Ring Installation
Fig. 11 Installing Side Rail
Fig. 12 Installing Upper and Intermediate Rings
9 - 116 3.3/3.8L ENGINE Ä
Page 1683 of 2438
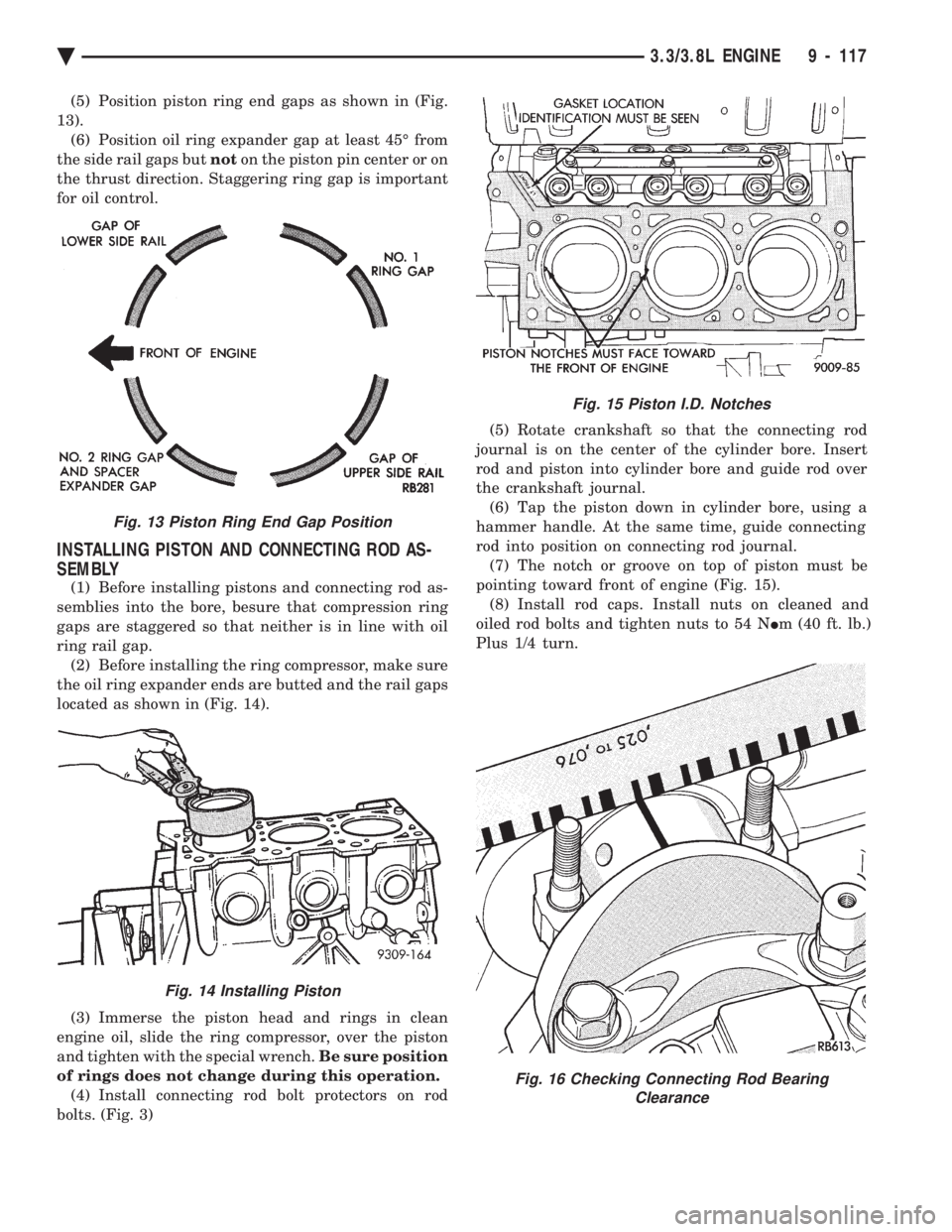
(5) Position piston ring end gaps as shown in (Fig.
13). (6) Position oil ring expander gap at least 45É from
the side rail gaps but noton the piston pin center or on
the thrust direction. Staggering ring gap is important
for oil control.
INSTALLING PISTON AND CONNECTING ROD AS-
SEMBLY
(1) Before installing pistons and connecting rod as-
semblies into the bore, besure that compression ring
gaps are staggered so that neither is in line with oil
ring rail gap. (2) Before installing the ring compressor, make sure
the oil ring expander ends are butted and the rail gaps
located as shown in (Fig. 14).
(3) Immerse the piston head and rings in clean
engine oil, slide the ring compressor, over the piston
and tighten with the special wrench. Be sure position
of rings does not change during this operation. (4) Install connecting rod bolt protectors on rod
bolts. (Fig. 3) (5) Rotate crankshaft so that the connecting rod
journal is on the center of the cylinder bore. Insert
rod and piston into cylinder bore and guide rod over
the crankshaft journal. (6) Tap the piston down in cylinder bore, using a
hammer handle. At the same time, guide connecting
rod into position on connecting rod journal. (7) The notch or groove on top of piston must be
pointing toward front of engine (Fig. 15). (8) Install rod caps. Install nuts on cleaned and
oiled rod bolts and tighten nuts to 54 N Im (40 ft. lb.)
Plus 1/4 turn.
Fig. 15 Piston I.D. Notches
Fig. 16 Checking Connecting Rod Bearing Clearance
Fig. 13 Piston Ring End Gap Position
Fig. 14 Installing Piston
Ä 3.3/3.8L ENGINE 9 - 117
Page 1684 of 2438
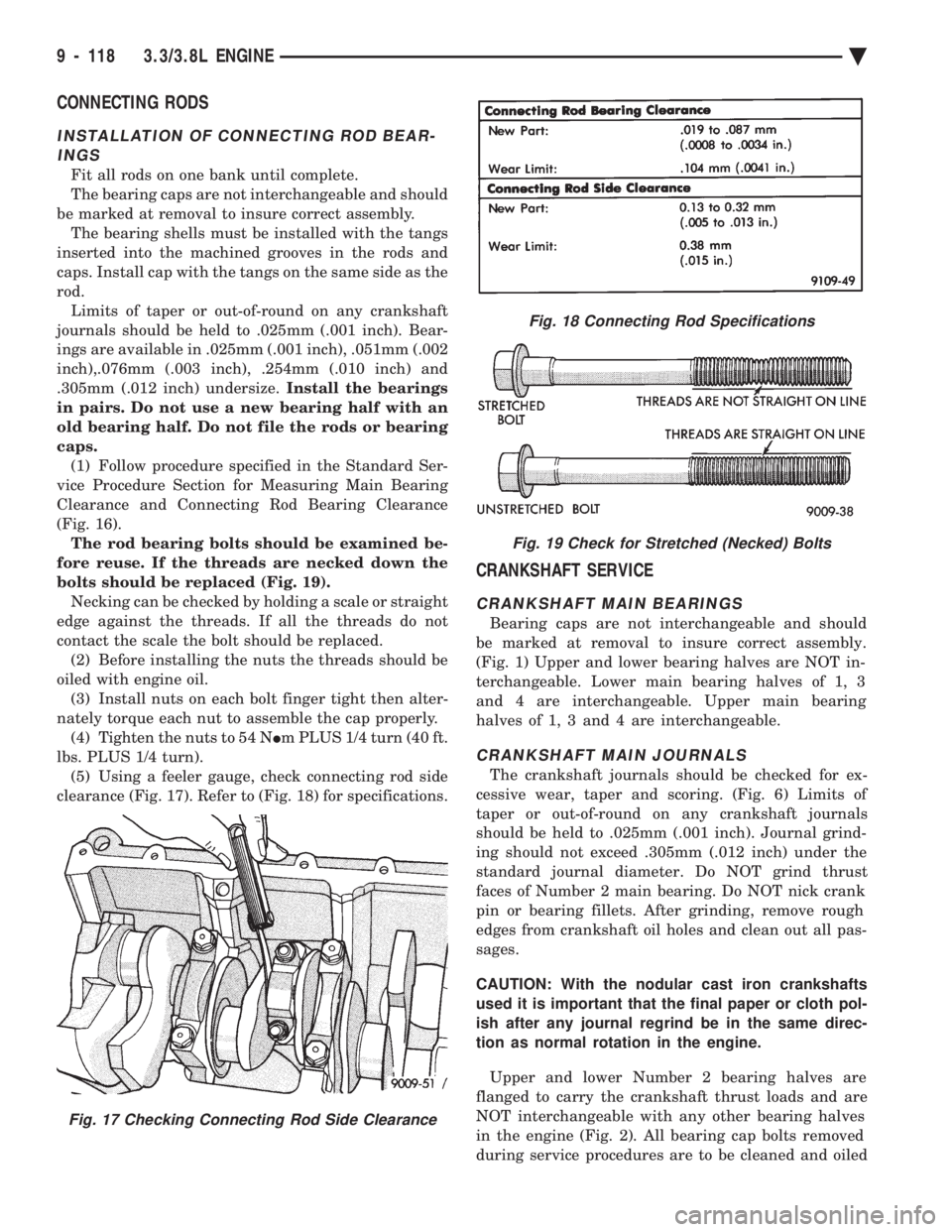
CONNECTING RODS
INSTALLATION OF CONNECTING ROD BEAR- INGS
Fit all rods on one bank until complete.
The bearing caps are not interchangeable and should
be marked at removal to insure correct assembly. The bearing shells must be installed with the tangs
inserted into the machined grooves in the rods and
caps. Install cap with the tangs on the same side as the
rod. Limits of taper or out-of-round on any crankshaft
journals should be held to .025mm (.001 inch). Bear-
ings are available in .025mm (.001 inch), .051mm (.002
inch),.076mm (.003 inch), .254mm (.010 inch) and
.305mm (.012 inch) undersize. Install the bearings
in pairs. Do not use a new bearing half with an
old bearing half. Do not file the rods or bearing
caps. (1) Follow procedure specified in the Standard Ser-
vice Procedure Section for Measuring Main Bearing
Clearance and Connecting Rod Bearing Clearance
(Fig. 16). The rod bearing bolts should be examined be-
fore reuse. If the threads are necked down the
bolts should be replaced (Fig. 19). Necking can be checked by holding a scale or straight
edge against the threads. If all the threads do not
contact the scale the bolt should be replaced. (2) Before installing the nuts the threads should be
oiled with engine oil. (3) Install nuts on each bolt finger tight then alter-
nately torque each nut to assemble the cap properly. (4) Tighten the nuts to 54 N Im PLUS 1/4 turn (40 ft.
lbs. PLUS 1/4 turn). (5) Using a feeler gauge, check connecting rod side
clearance (Fig. 17). Refer to (Fig. 18) for specifications.
CRANKSHAFT SERVICE
CRANKSHAFT MAIN BEARINGS
Bearing caps are not interchangeable and should
be marked at removal to insure correct assembly.
(Fig. 1) Upper and lower bearing halves are NOT in-
terchangeable. Lower main bearing halves of 1, 3
and 4 are interchangeable. Upper main bearing
halves of 1, 3 and 4 are interchangeable.
CRANKSHAFT MAIN JOURNALS
The crankshaft journals should be checked for ex-
cessive wear, taper and scoring. (Fig. 6) Limits of
taper or out-of-round on any crankshaft journals
should be held to .025mm (.001 inch). Journal grind-
ing should not exceed .305mm (.012 inch) under the
standard journal diameter. Do NOT grind thrust
faces of Number 2 main bearing. Do NOT nick crank
pin or bearing fillets. After grinding, remove rough
edges from crankshaft oil holes and clean out all pas-
sages.
CAUTION: With the nodular cast iron crankshafts
used it is important that the final paper or cloth pol-
ish after any journal regrind be in the same direc-
tion as normal rotation in the engine.
Upper and lower Number 2 bearing halves are
flanged to carry the crankshaft thrust loads and are
NOT interchangeable with any other bearing halves
in the engine (Fig. 2). All bearing cap bolts removed
during service procedures are to be cleaned and oiled
Fig. 18 Connecting Rod Specifications
Fig. 19 Check for Stretched (Necked) Bolts
Fig. 17 Checking Connecting Rod Side Clearance
9 - 118 3.3/3.8L ENGINE Ä
Page 1685 of 2438
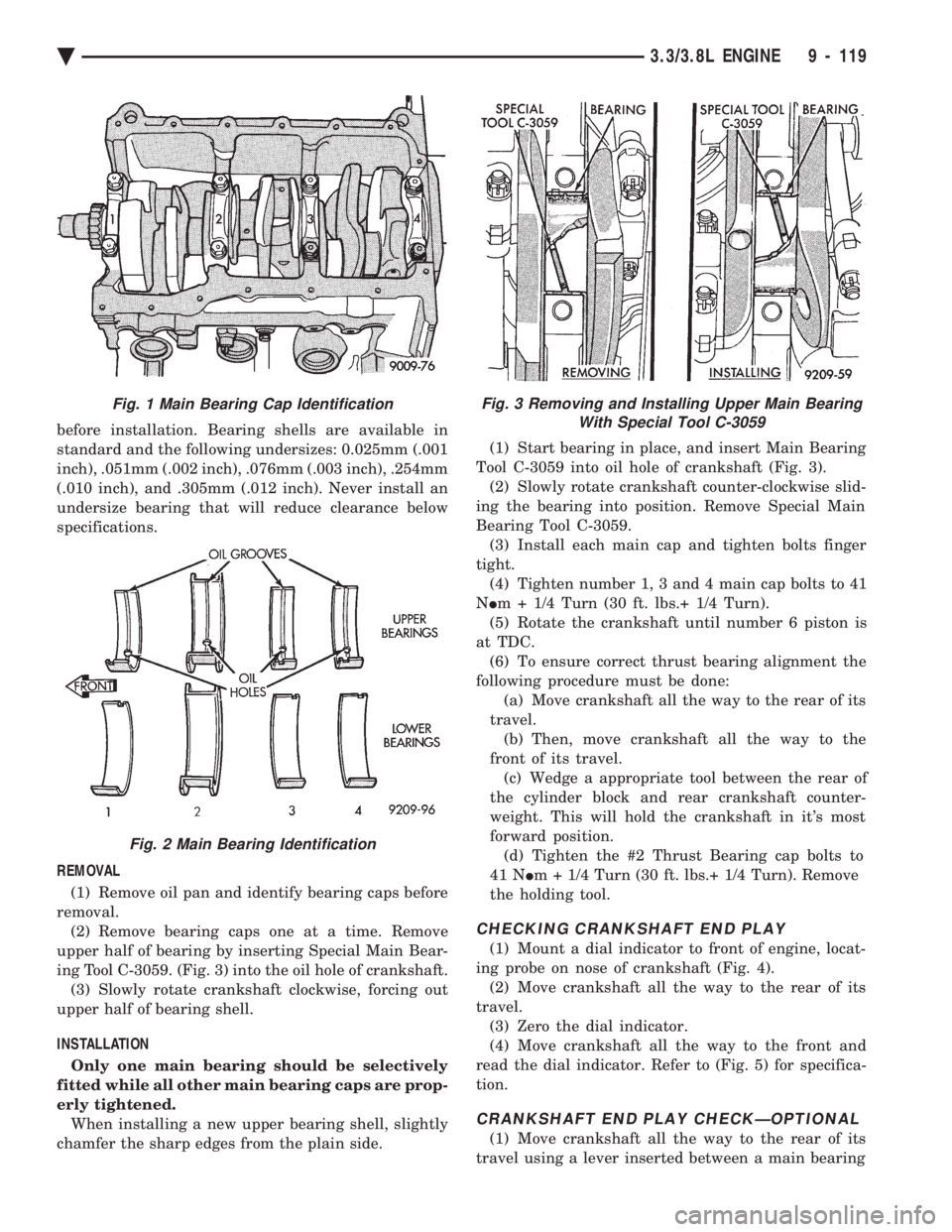
before installation. Bearing shells are available in
standard and the following undersizes: 0.025mm (.001
inch), .051mm (.002 inch), .076mm (.003 inch), .254mm
(.010 inch), and .305mm (.012 inch). Never install an
undersize bearing that will reduce clearance below
specifications.
REMOVAL (1) Remove oil pan and identify bearing caps before
removal. (2) Remove bearing caps one at a time. Remove
upper half of bearing by inserting Special Main Bear-
ing Tool C-3059. (Fig. 3) into the oil hole of crankshaft. (3) Slowly rotate crankshaft clockwise, forcing out
upper half of bearing shell.
INSTALLATION Only one main bearing should be selectively
fitted while all other main bearing caps are prop-
erly tightened. When installing a new upper bearing shell, slightly
chamfer the sharp edges from the plain side. (1) Start bearing in place, and insert Main Bearing
Tool C-3059 into oil hole of crankshaft (Fig. 3). (2) Slowly rotate crankshaft counter-clockwise slid-
ing the bearing into position. Remove Special Main
Bearing Tool C-3059. (3) Install each main cap and tighten bolts finger
tight. (4) Tighten number 1, 3 and 4 main cap bolts to 41
N Im + 1/4 Turn (30 ft. lbs.+ 1/4 Turn).
(5) Rotate the crankshaft until number 6 piston is
at TDC. (6) To ensure correct thrust bearing alignment the
following procedure must be done: (a) Move crankshaft all the way to the rear of its
travel. (b) Then, move crankshaft all the way to the
front of its travel. (c) Wedge a appropriate tool between the rear of
the cylinder block and rear crankshaft counter-
weight. This will hold the crankshaft in it's most
forward position. (d) Tighten the #2 Thrust Bearing cap bolts to
41 N Im + 1/4 Turn (30 ft. lbs.+ 1/4 Turn). Remove
the holding tool.
CHECKING CRANKSHAFT END PLAY
(1) Mount a dial indicator to front of engine, locat-
ing probe on nose of crankshaft (Fig. 4). (2) Move crankshaft all the way to the rear of its
travel. (3) Zero the dial indicator.
(4) Move crankshaft all the way to the front and
read the dial indicator. Refer to (Fig. 5) for specifica-
tion.
CRANKSHAFT END PLAY CHECKÐOPTIONAL
(1) Move crankshaft all the way to the rear of its
travel using a lever inserted between a main bearing
Fig. 3 Removing and Installing Upper Main Bearing With Special Tool C-3059Fig. 1 Main Bearing Cap Identification
Fig. 2 Main Bearing Identification
Ä 3.3/3.8L ENGINE 9 - 119
Page 1686 of 2438
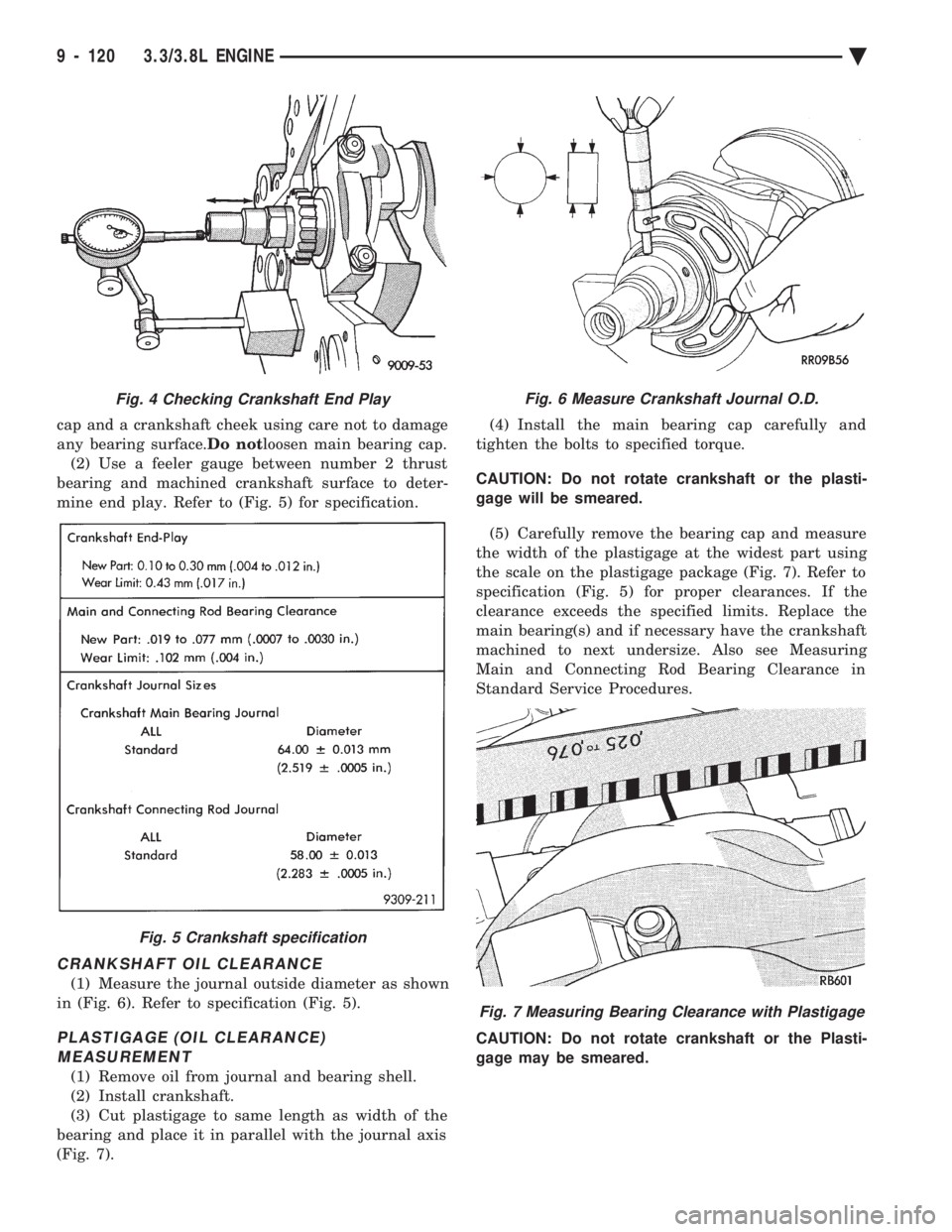
cap and a crankshaft cheek using care not to damage
any bearing surface. Do notloosen main bearing cap.
(2) Use a feeler gauge between number 2 thrust
bearing and machined crankshaft surface to deter-
mine end play. Refer to (Fig. 5) for specification.
CRANKSHAFT OIL CLEARANCE
(1) Measure the journal outside diameter as shown
in (Fig. 6). Refer to specification (Fig. 5).
PLASTIGAGE (OIL CLEARANCE) MEASUREMENT
(1) Remove oil from journal and bearing shell.
(2) Install crankshaft.
(3) Cut plastigage to same length as width of the
bearing and place it in parallel with the journal axis
(Fig. 7). (4) Install the main bearing cap carefully and
tighten the bolts to specified torque.
CAUTION: Do not rotate crankshaft or the plasti-
gage will be smeared.
(5) Carefully remove the bearing cap and measure
the width of the plastigage at the widest part using
the scale on the plastigage package (Fig. 7). Refer to
specification (Fig. 5) for proper clearances. If the
clearance exceeds the specified limits. Replace the
main bearing(s) and if necessary have the crankshaft
machined to next undersize. Also see Measuring
Main and Connecting Rod Bearing Clearance in
Standard Service Procedures.
CAUTION: Do not rotate crankshaft or the Plasti-
gage may be smeared.
Fig. 4 Checking Crankshaft End Play
Fig. 5 Crankshaft specification
Fig. 6 Measure Crankshaft Journal O.D.
Fig. 7 Measuring Bearing Clearance with Plastigage
9 - 120 3.3/3.8L ENGINE Ä
Page 1687 of 2438
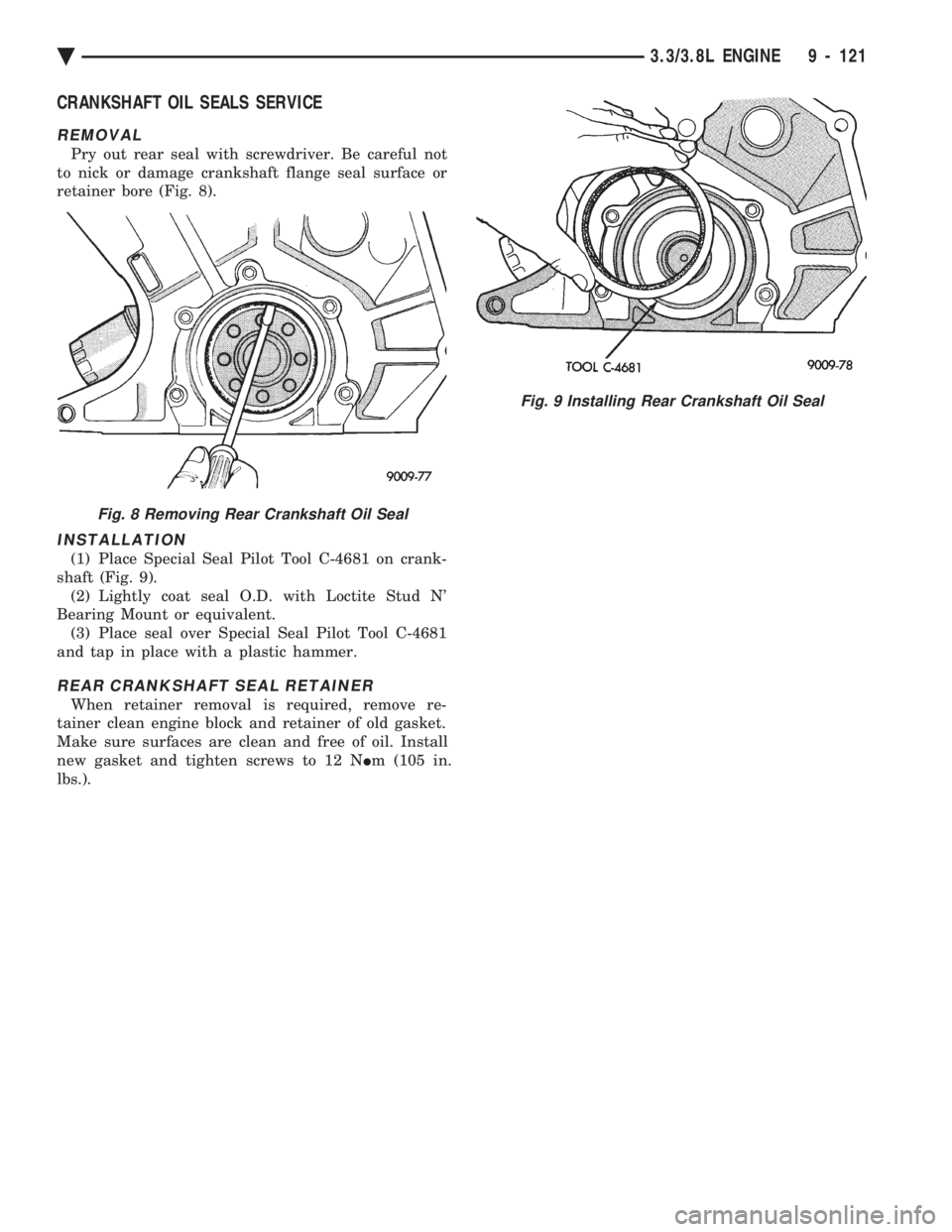
CRANKSHAFT OIL SEALS SERVICE
REMOVAL
Pry out rear seal with screwdriver. Be careful not
to nick or damage crankshaft flange seal surface or
retainer bore (Fig. 8).
INSTALLATION
(1) Place Special Seal Pilot Tool C-4681 on crank-
shaft (Fig. 9). (2) Lightly coat seal O.D. with Loctite Stud N'
Bearing Mount or equivalent. (3) Place seal over Special Seal Pilot Tool C-4681
and tap in place with a plastic hammer.
REAR CRANKSHAFT SEAL RETAINER
When retainer removal is required, remove re-
tainer clean engine block and retainer of old gasket.
Make sure surfaces are clean and free of oil. Install
new gasket and tighten screws to 12 N Im (105 in.
lbs.).
Fig. 9 Installing Rear Crankshaft Oil Seal
Fig. 8 Removing Rear Crankshaft Oil Seal
Ä 3.3/3.8L ENGINE 9 - 121
Page 1688 of 2438
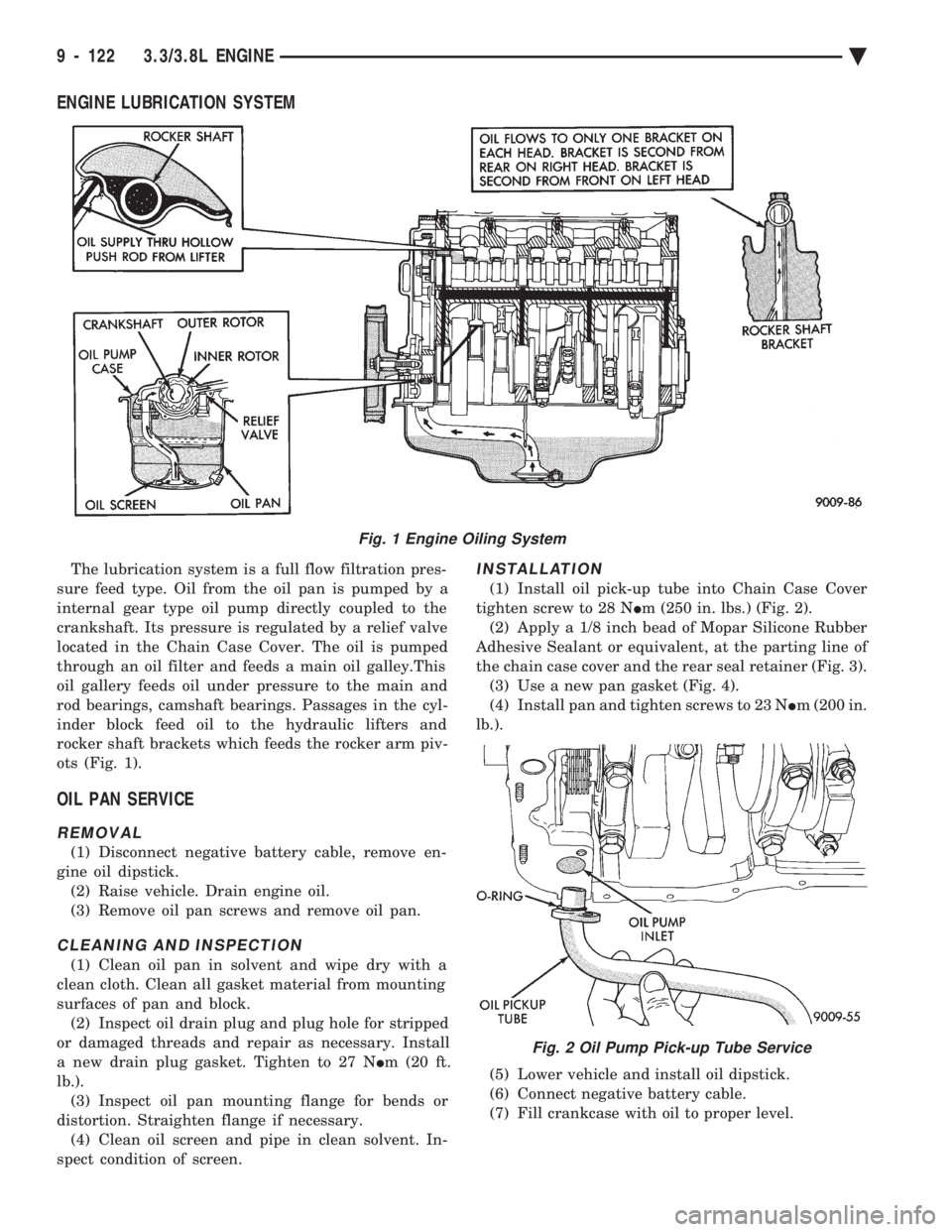
ENGINE LUBRICATION SYSTEM
The lubrication system is a full flow filtration pres-
sure feed type. Oil from the oil pan is pumped by a
internal gear type oil pump directly coupled to the
crankshaft. Its pressure is regulated by a relief valve
located in the Chain Case Cover. The oil is pumped
through an oil filter and feeds a main oil galley.This
oil gallery feeds oil under pressure to the main and
rod bearings, camshaft bearings. Passages in the cyl-
inder block feed oil to the hydraulic lifters and
rocker shaft brackets which feeds the rocker arm piv-
ots (Fig. 1).
OIL PAN SERVICE
REMOVAL
(1) Disconnect negative battery cable, remove en-
gine oil dipstick. (2) Raise vehicle. Drain engine oil.
(3) Remove oil pan screws and remove oil pan.
CLEANING AND INSPECTION
(1) Clean oil pan in solvent and wipe dry with a
clean cloth. Clean all gasket material from mounting
surfaces of pan and block. (2) Inspect oil drain plug and plug hole for stripped
or damaged threads and repair as necessary. Install
a new drain plug gasket. Tighten to 27 N Im (20 ft.
lb.). (3) Inspect oil pan mounting flange for bends or
distortion. Straighten flange if necessary. (4) Clean oil screen and pipe in clean solvent. In-
spect condition of screen.
INSTALLATION
(1) Install oil pick-up tube into Chain Case Cover
tighten screw to 28 N Im (250 in. lbs.) (Fig. 2).
(2) Apply a 1/8 inch bead of Mopar Silicone Rubber
Adhesive Sealant or equivalent, at the parting line of
the chain case cover and the rear seal retainer (Fig. 3). (3) Use a new pan gasket (Fig. 4).
(4) Install pan and tighten screws to 23 N Im (200 in.
lb.).
(5) Lower vehicle and install oil dipstick.
(6) Connect negative battery cable.
(7) Fill crankcase with oil to proper level.
Fig. 1 Engine Oiling System
Fig. 2 Oil Pump Pick-up Tube Service
9 - 122 3.3/3.8L ENGINE Ä
Page 1689 of 2438
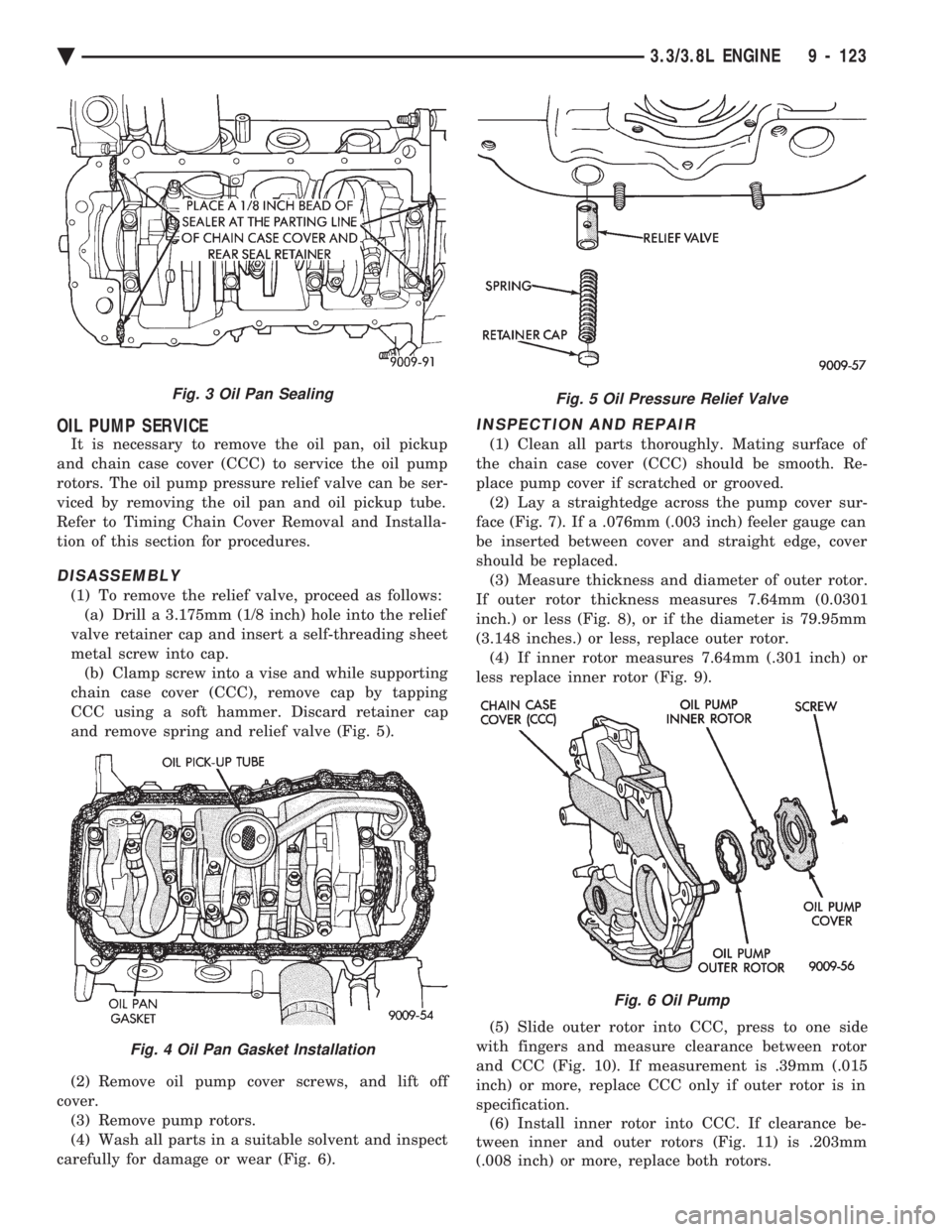
OIL PUMP SERVICE
It is necessary to remove the oil pan, oil pickup
and chain case cover (CCC) to service the oil pump
rotors. The oil pump pressure relief valve can be ser-
viced by removing the oil pan and oil pickup tube.
Refer to Timing Chain Cover Removal and Installa-
tion of this section for procedures.
DISASSEMBLY
(1) To remove the relief valve, proceed as follows: (a) Drill a 3.175mm (1/8 inch) hole into the relief
valve retainer cap and insert a self-threading sheet
metal screw into cap. (b) Clamp screw into a vise and while supporting
chain case cover (CCC), remove cap by tapping
CCC using a soft hammer. Discard retainer cap
and remove spring and relief valve (Fig. 5).
(2) Remove oil pump cover screws, and lift off
cover. (3) Remove pump rotors.
(4) Wash all parts in a suitable solvent and inspect
carefully for damage or wear (Fig. 6).
INSPECTION AND REPAIR
(1) Clean all parts thoroughly. Mating surface of
the chain case cover (CCC) should be smooth. Re-
place pump cover if scratched or grooved. (2) Lay a straightedge across the pump cover sur-
face (Fig. 7). If a .076mm (.003 inch) feeler gauge can
be inserted between cover and straight edge, cover
should be replaced. (3) Measure thickness and diameter of outer rotor.
If outer rotor thickness measures 7.64mm (0.0301
inch.) or less (Fig. 8), or if the diameter is 79.95mm
(3.148 inches.) or less, replace outer rotor. (4) If inner rotor measures 7.64mm (.301 inch) or
less replace inner rotor (Fig. 9).
(5) Slide outer rotor into CCC, press to one side
with fingers and measure clearance between rotor
and CCC (Fig. 10). If measurement is .39mm (.015
inch) or more, replace CCC only if outer rotor is in
specification. (6) Install inner rotor into CCC. If clearance be-
tween inner and outer rotors (Fig. 11) is .203mm
(.008 inch) or more, replace both rotors.
Fig. 3 Oil Pan Sealing
Fig. 4 Oil Pan Gasket Installation
Fig. 5 Oil Pressure Relief Valve
Fig. 6 Oil Pump
Ä 3.3/3.8L ENGINE 9 - 123
Page 1690 of 2438
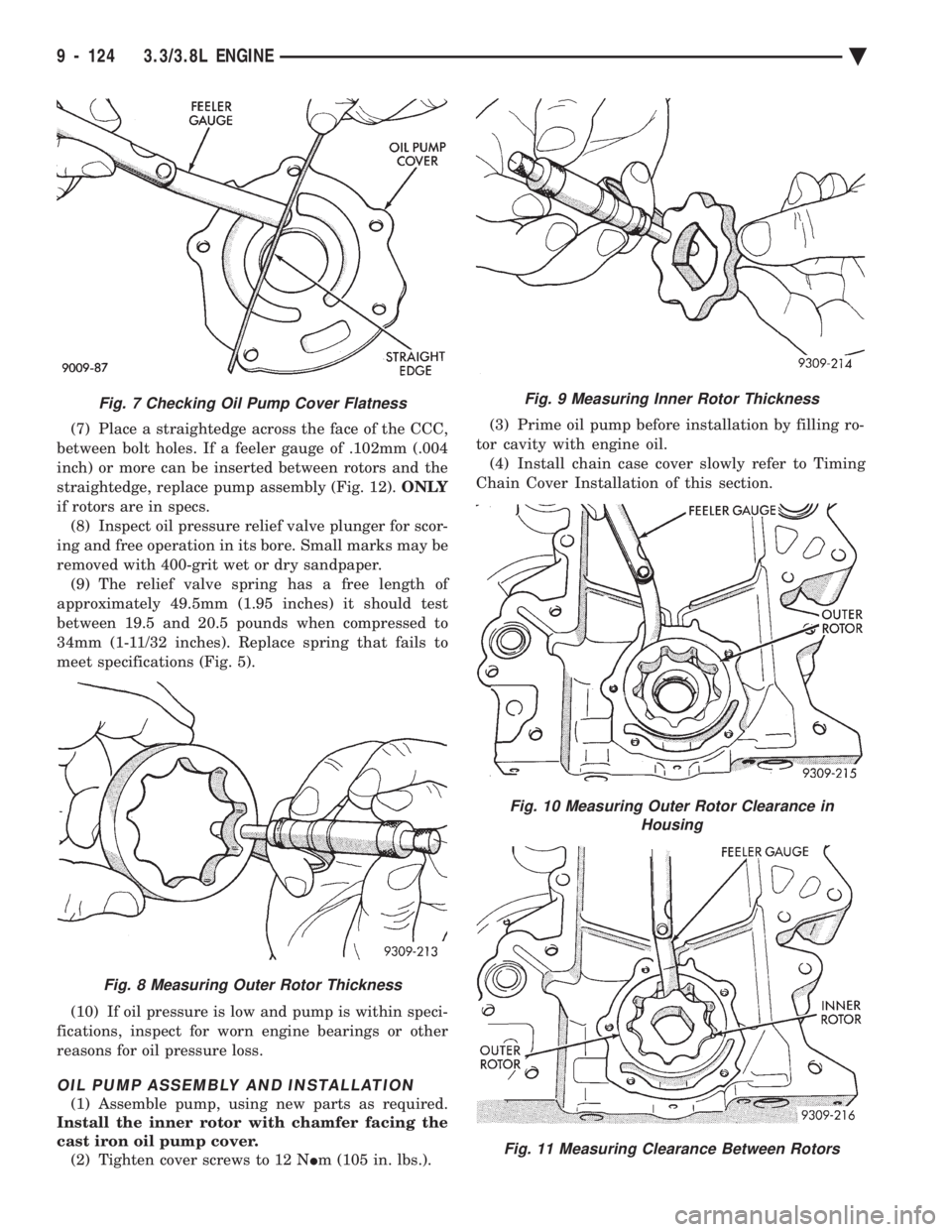
(7) Place a straightedge across the face of the CCC,
between bolt holes. If a feeler gauge of .102mm (.004
inch) or more can be inserted between rotors and the
straightedge, replace pump assembly (Fig. 12). ONLY
if rotors are in specs. (8) Inspect oil pressure relief valve plunger for scor-
ing and free operation in its bore. Small marks may be
removed with 400-grit wet or dry sandpaper. (9) The relief valve spring has a free length of
approximately 49.5mm (1.95 inches) it should test
between 19.5 and 20.5 pounds when compressed to
34mm (1-11/32 inches). Replace spring that fails to
meet specifications (Fig. 5).
(10) If oil pressure is low and pump is within speci-
fications, inspect for worn engine bearings or other
reasons for oil pressure loss.
OIL PUMP ASSEMBLY AND INSTALLATION
(1) Assemble pump, using new parts as required.
Install the inner rotor with chamfer facing the
cast iron oil pump cover. (2) Tighten cover screws to 12 N Im (105 in. lbs.). (3) Prime oil pump before installation by filling ro-
tor cavity with engine oil. (4) Install chain case cover slowly refer to Timing
Chain Cover Installation of this section.
Fig. 9 Measuring Inner Rotor Thickness
Fig. 10 Measuring Outer Rotor Clearance in Housing
Fig. 11 Measuring Clearance Between Rotors
Fig. 7 Checking Oil Pump Cover Flatness
Fig. 8 Measuring Outer Rotor Thickness
9 - 124 3.3/3.8L ENGINE Ä