CHEVROLET PLYMOUTH ACCLAIM 1993 Service Manual
Manufacturer: CHEVROLET, Model Year: 1993, Model line: PLYMOUTH ACCLAIM, Model: CHEVROLET PLYMOUTH ACCLAIM 1993Pages: 2438, PDF Size: 74.98 MB
Page 2101 of 2438
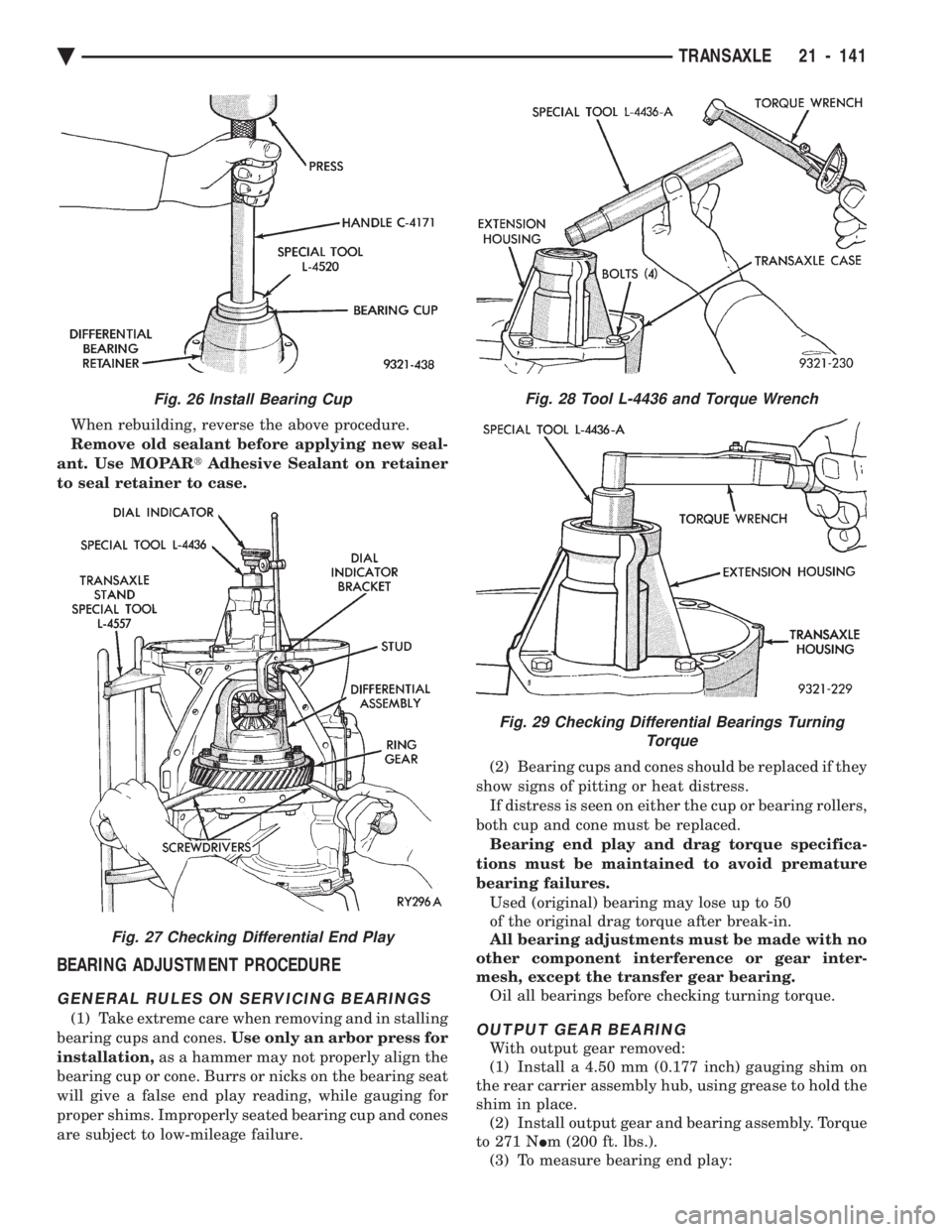
When rebuilding, reverse the above procedure.
Remove old sealant before applying new seal-
ant. Use MOPAR tAdhesive Sealant on retainer
to seal retainer to case.
BEARING ADJUSTMENT PROCEDURE
GENERAL RULES ON SERVICING BEARINGS
(1) Take extreme care when removing and in stalling
bearing cups and cones. Use only an arbor press for
installation, as a hammer may not properly align the
bearing cup or cone. Burrs or nicks on the bearing seat
will give a false end play reading, while gauging for
proper shims. Improperly seated bearing cup and cones
are subject to low-mileage failure. (2) Bearing cups and cones should be replaced if they
show signs of pitting or heat distress. If distress is seen on either the cup or bearing rollers,
both cup and cone must be replaced. Bearing end play and drag torque specifica-
tions must be maintained to avoid premature
bearing failures. Used (original) bearing may lose up to 50
of the original drag torque after break-in.
All bearing adjustments must be made with no
other component interference or gear inter-
mesh, except the transfer gear bearing. Oil all bearings before checking turning torque.OUTPUT GEAR BEARING
With output gear removed:
(1) Install a 4.50 mm (0.177 inch) gauging shim on
the rear carrier assembly hub, using grease to hold the
shim in place. (2) Install output gear and bearing assembly. Torque
to 271 N Im (200 ft. lbs.).
(3) To measure bearing end play:
Fig. 26 Install Bearing Cup
Fig. 27 Checking Differential End Play
Fig. 28 Tool L-4436 and Torque Wrench
Fig. 29 Checking Differential Bearings Turning Torque
Ä TRANSAXLE 21 - 141
Page 2102 of 2438
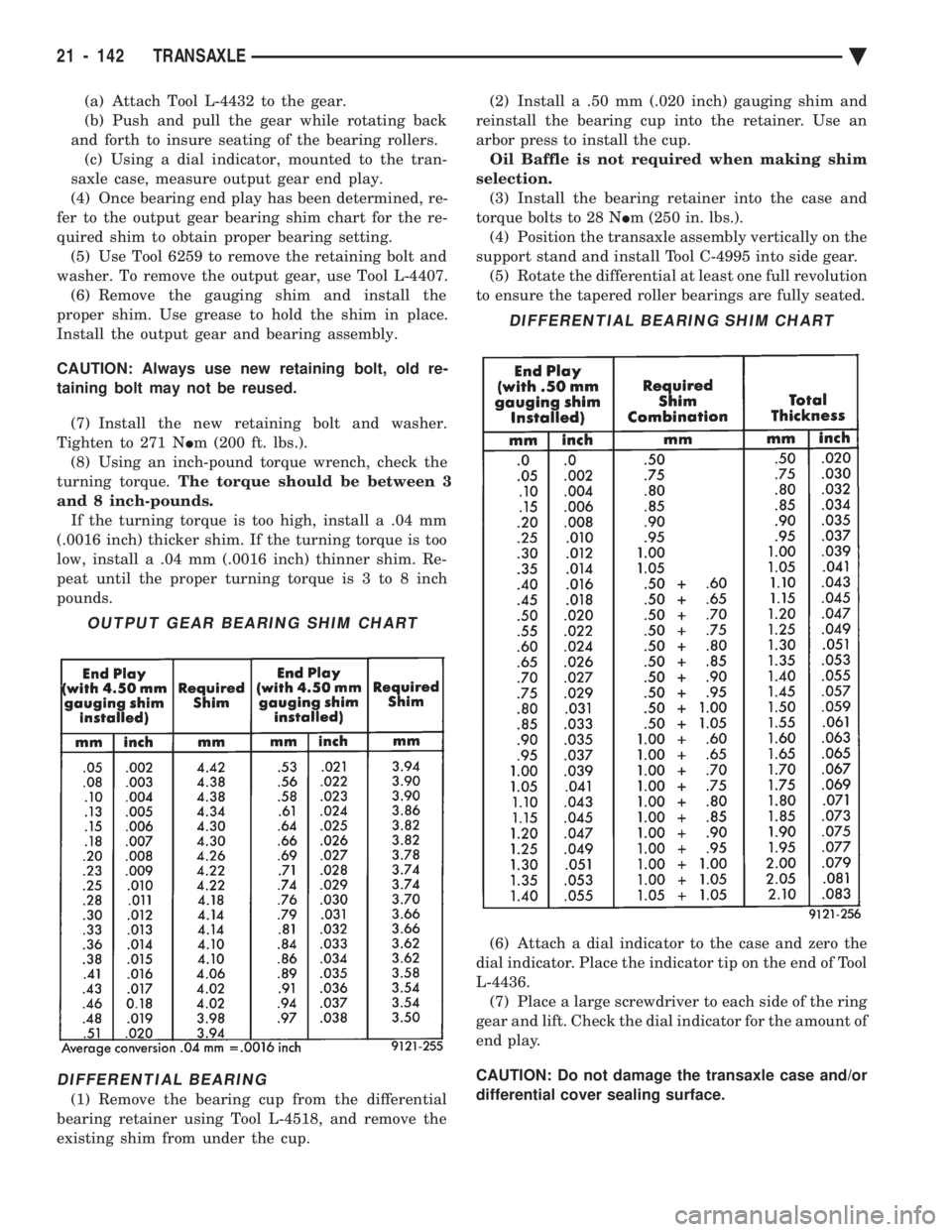
(a) Attach Tool L-4432 to the gear.
(b) Push and pull the gear while rotating back
and forth to insure seating of the bearing rollers. (c) Using a dial indicator, mounted to the tran-
saxle case, measure output gear end play.
(4) Once bearing end play has been determined, re-
fer to the output gear bearing shim chart for the re-
quired shim to obtain proper bearing setting. (5) Use Tool 6259 to remove the retaining bolt and
washer. To remove the output gear, use Tool L-4407. (6) Remove the gauging shim and install the
proper shim. Use grease to hold the shim in place.
Install the output gear and bearing assembly.
CAUTION: Always use new retaining bolt, old re-
taining bolt may not be reused.
(7) Install the new retaining bolt and washer.
Tighten to 271 N Im (200 ft. lbs.).
(8) Using an inch-pound torque wrench, check the
turning torque. The torque should be between 3
and 8 inch-pounds. If the turning torque is too high, install a .04 mm
(.0016 inch) thicker shim. If the turning torque is too
low, install a .04 mm (.0016 inch) thinner shim. Re-
peat until the proper turning torque is 3 to 8 inch
pounds.
DIFFERENTIAL BEARING
(1) Remove the bearing cup from the differential
bearing retainer using Tool L-4518, and remove the
existing shim from under the cup. (2) Install a .50 mm (.020 inch) gauging shim and
reinstall the bearing cup into the retainer. Use an
arbor press to install the cup. Oil Baffle is not required when making shim
selection. (3) Install the bearing retainer into the case and
torque bolts to 28 N Im (250 in. lbs.).
(4) Position the transaxle assembly vertically on the
support stand and install Tool C-4995 into side gear. (5) Rotate the differential at least one full revolution
to ensure the tapered roller bearings are fully seated.
(6) Attach a dial indicator to the case and zero the
dial indicator. Place the indicator tip on the end of Tool
L-4436. (7) Place a large screwdriver to each side of the ring
gear and lift. Check the dial indicator for the amount of
end play.
CAUTION: Do not damage the transaxle case and/or
differential cover sealing surface.
OUTPUT GEAR BEARING SHIM CHART
DIFFERENTIAL BEARING SHIM CHART
21 - 142 TRANSAXLE Ä
Page 2103 of 2438
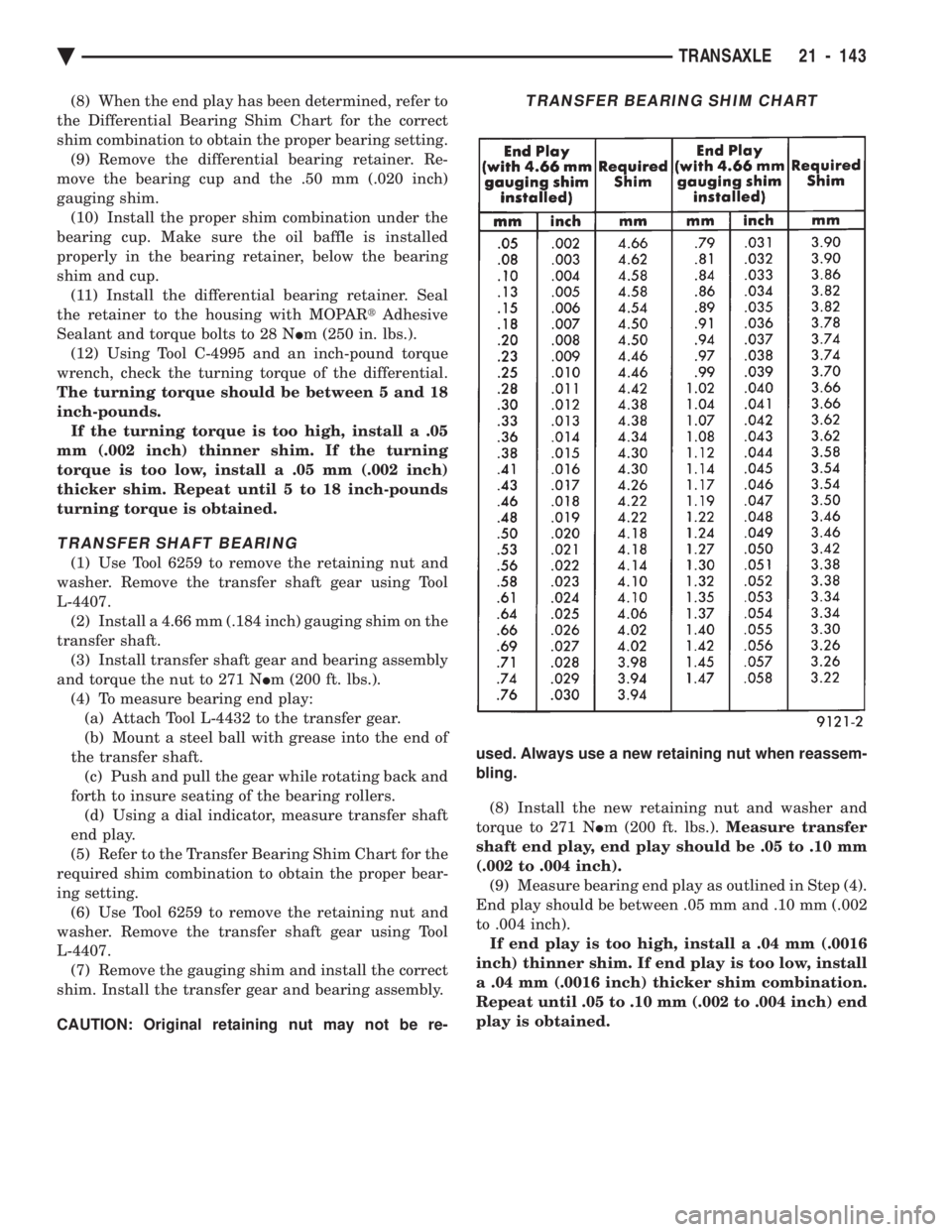
(8) When the end play has been determined, refer to
the Differential Bearing Shim Chart for the correct
shim combination to obtain the proper bearing setting. (9) Remove the differential bearing retainer. Re-
move the bearing cup and the .50 mm (.020 inch)
gauging shim. (10) Install the proper shim combination under the
bearing cup. Make sure the oil baffle is installed
properly in the bearing retainer, below the bearing
shim and cup. (11) Install the differential bearing retainer. Seal
the retainer to the housing with MOPAR tAdhesive
Sealant and torque bolts to 28 N Im (250 in. lbs.).
(12) Using Tool C-4995 and an inch-pound torque
wrench, check the turning torque of the differential.
The turning torque should be between 5 and 18
inch-pounds. If the turning torque is too high, install a .05
mm (.002 inch) thinner shim. If the turning
torque is too low, install a .05 mm (.002 inch)
thicker shim. Repeat until 5 to 18 inch-pounds
turning torque is obtained.
TRANSFER SHAFT BEARING
(1) Use Tool 6259 to remove the retaining nut and
washer. Remove the transfer shaft gear using Tool
L-4407. (2) Install a 4.66 mm (.184 inch) gauging shim on the
transfer shaft. (3) Install transfer shaft gear and bearing assembly
and torque the nut to 271 N Im (200 ft. lbs.).
(4) To measure bearing end play: (a) Attach Tool L-4432 to the transfer gear.
(b) Mount a steel ball with grease into the end of
the transfer shaft. (c) Push and pull the gear while rotating back and
forth to insure seating of the bearing rollers. (d) Using a dial indicator, measure transfer shaft
end play.
(5) Refer to the Transfer Bearing Shim Chart for the
required shim combination to obtain the proper bear-
ing setting. (6) Use Tool 6259 to remove the retaining nut and
washer. Remove the transfer shaft gear using Tool
L-4407. (7) Remove the gauging shim and install the correct
shim. Install the transfer gear and bearing assembly.
CAUTION: Original retaining nut may not be re- used. Always use a new retaining nut when reassem-
bling.
(8) Install the new retaining nut and washer and
torque to 271 N Im (200 ft. lbs.). Measure transfer
shaft end play, end play should be .05 to .10 mm
(.002 to .004 inch). (9) Measure bearing end play as outlined in Step (4).
End play should be between .05 mm and .10 mm (.002
to .004 inch). If end play is too high, install a .04 mm (.0016
inch) thinner shim. If end play is too low, install
a .04 mm (.0016 inch) thicker shim combination.
Repeat until .05 to .10 mm (.002 to .004 inch) end
play is obtained.
TRANSFER BEARING SHIM CHART
Ä TRANSAXLE 21 - 143
Page 2104 of 2438
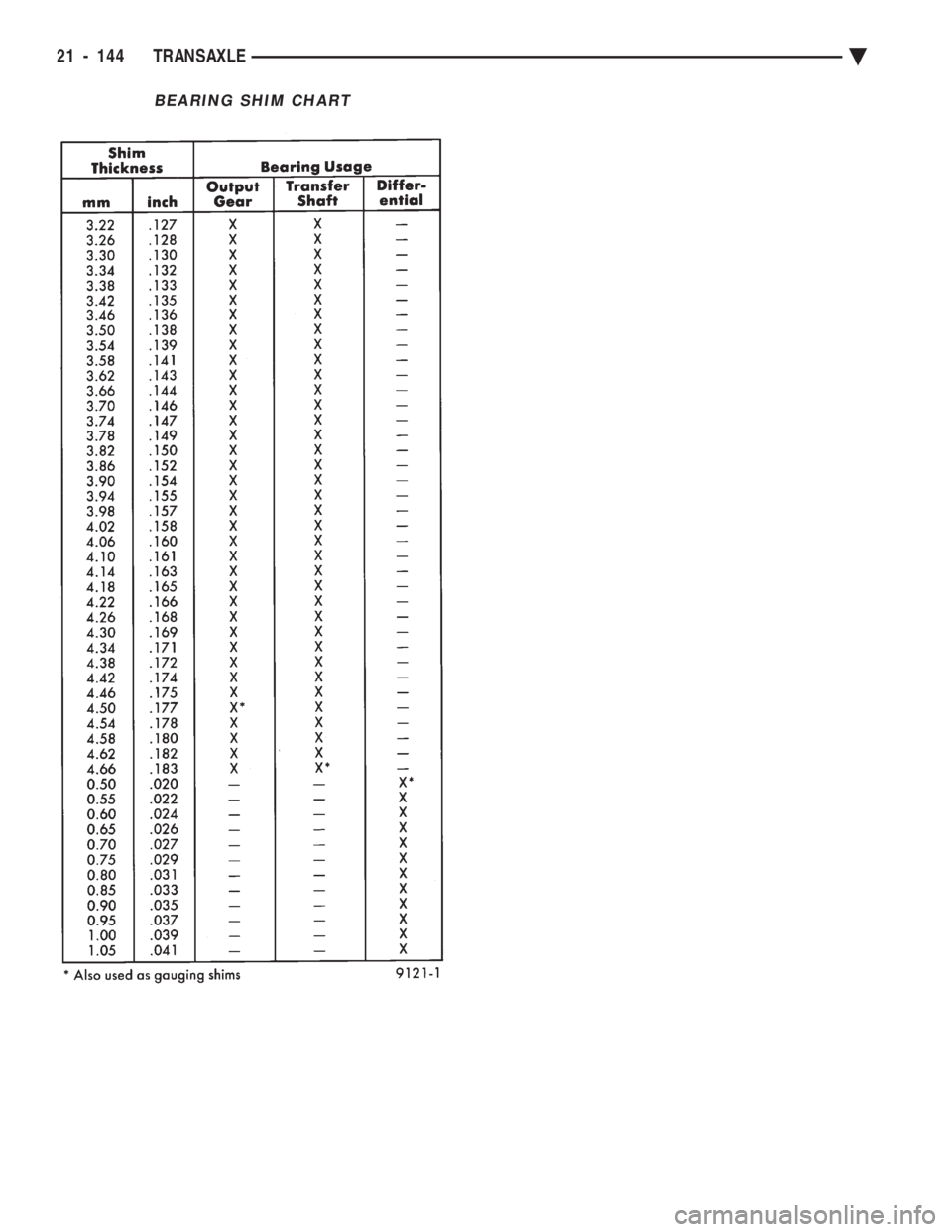
BEARING SHIM CHART
21 - 144 TRANSAXLE Ä
Page 2105 of 2438
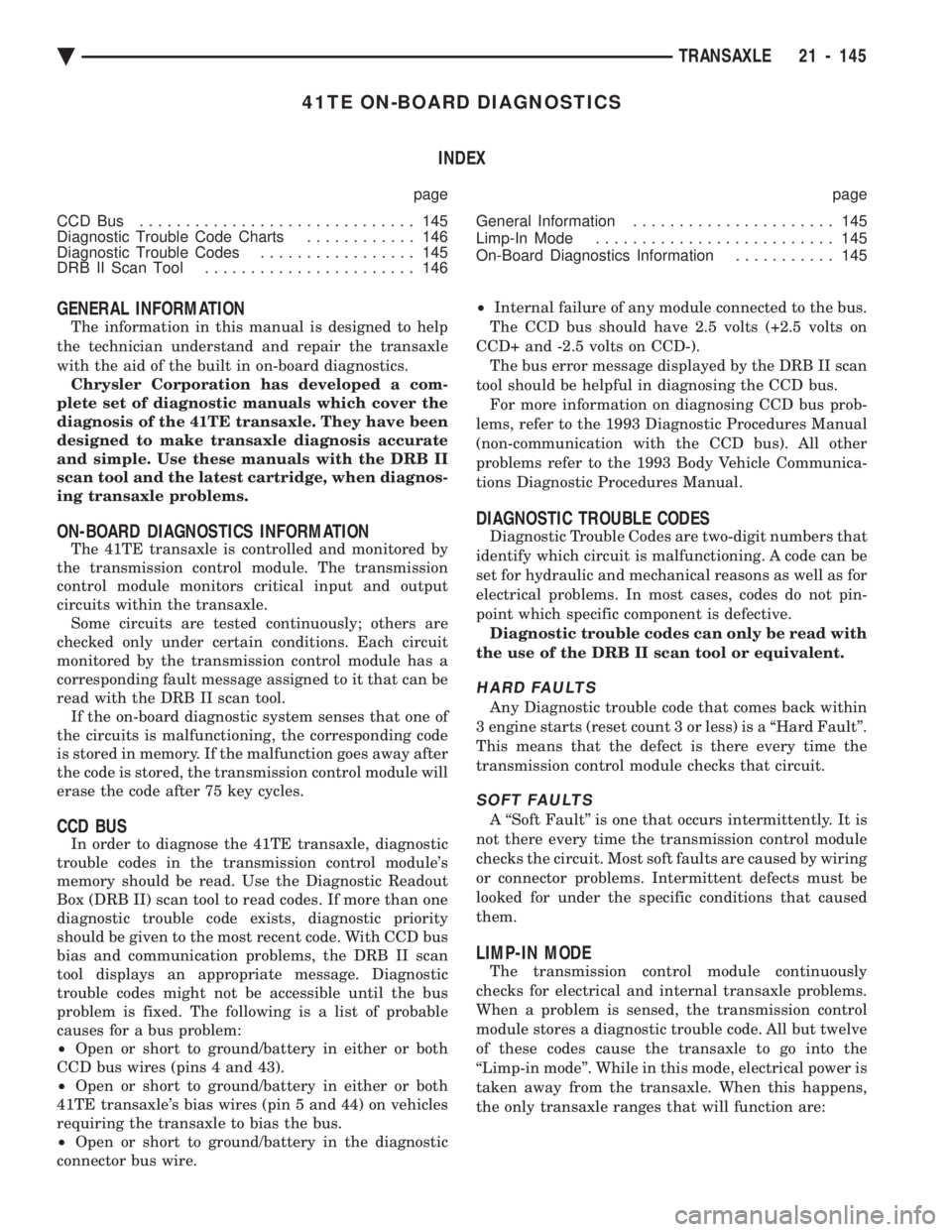
41TE ON-BOARD DIAGNOSTICS INDEX
page page
CCD Bus .............................. 145
Diagnostic Trouble Code Charts ............ 146
Diagnostic Trouble Codes ................. 145
DRB II Scan Tool ....................... 146 General Information
...................... 145
Limp-In Mode .......................... 145
On-Board Diagnostics Information ........... 145
GENERAL INFORMATION
The information in this manual is designed to help
the technician understand and repair the transaxle
with the aid of the built in on-board diagnostics. Chrysler Corporation has developed a com-
plete set of diagnostic manuals which cover the
diagnosis of the 41TE transaxle. They have been
designed to make transaxle diagnosis accurate
and simple. Use these manuals with the DRB II
scan tool and the latest cartridge, when diagnos-
ing transaxle problems.
ON-BOARD DIAGNOSTICS INFORMATION
The 41TE transaxle is controlled and monitored by
the transmission control module. The transmission
control module monitors critical input and output
circuits within the transaxle. Some circuits are tested continuously; others are
checked only under certain conditions. Each circuit
monitored by the transmission control module has a
corresponding fault message assigned to it that can be
read with the DRB II scan tool. If the on-board diagnostic system senses that one of
the circuits is malfunctioning, the corresponding code
is stored in memory. If the malfunction goes away after
the code is stored, the transmission control module will
erase the code after 75 key cycles.
CCD BUS
In order to diagnose the 41TE transaxle, diagnostic
trouble codes in the transmission control module's
memory should be read. Use the Diagnostic Readout
Box (DRB II) scan tool to read codes. If more than one
diagnostic trouble code exists, diagnostic priority
should be given to the most recent code. With CCD bus
bias and communication problems, the DRB II scan
tool displays an appropriate message. Diagnostic
trouble codes might not be accessible until the bus
problem is fixed. The following is a list of probable
causes for a bus problem:
² Open or short to ground/battery in either or both
CCD bus wires (pins 4 and 43).
² Open or short to ground/battery in either or both
41TE transaxle's bias wires (pin 5 and 44) on vehicles
requiring the transaxle to bias the bus.
² Open or short to ground/battery in the diagnostic
connector bus wire. ²
Internal failure of any module connected to the bus.
The CCD bus should have 2.5 volts (+2.5 volts on
CCD+ and -2.5 volts on CCD-). The bus error message displayed by the DRB II scan
tool should be helpful in diagnosing the CCD bus. For more information on diagnosing CCD bus prob-
lems, refer to the 1993 Diagnostic Procedures Manual
(non-communication with the CCD bus). All other
problems refer to the 1993 Body Vehicle Communica-
tions Diagnostic Procedures Manual.
DIAGNOSTIC TROUBLE CODES
Diagnostic Trouble Codes are two-digit numbers that
identify which circuit is malfunctioning. A code can be
set for hydraulic and mechanical reasons as well as for
electrical problems. In most cases, codes do not pin-
point which specific component is defective. Diagnostic trouble codes can only be read with
the use of the DRB II scan tool or equivalent.
HARD FAULTS
Any Diagnostic trouble code that comes back within
3 engine starts (reset count 3 or less) is a ``Hard Fault''.
This means that the defect is there every time the
transmission control module checks that circuit.
SOFT FAULTS
A ``Soft Fault'' is one that occurs intermittently. It is
not there every time the transmission control module
checks the circuit. Most soft faults are caused by wiring
or connector problems. Intermittent defects must be
looked for under the specific conditions that caused
them.
LIMP-IN MODE
The transmission control module continuously
checks for electrical and internal transaxle problems.
When a problem is sensed, the transmission control
module stores a diagnostic trouble code. All but twelve
of these codes cause the transaxle to go into the
``Limp-in mode''. While in this mode, electrical power is
taken away from the transaxle. When this happens,
the only transaxle ranges that will function are:
Ä TRANSAXLE 21 - 145
Page 2106 of 2438
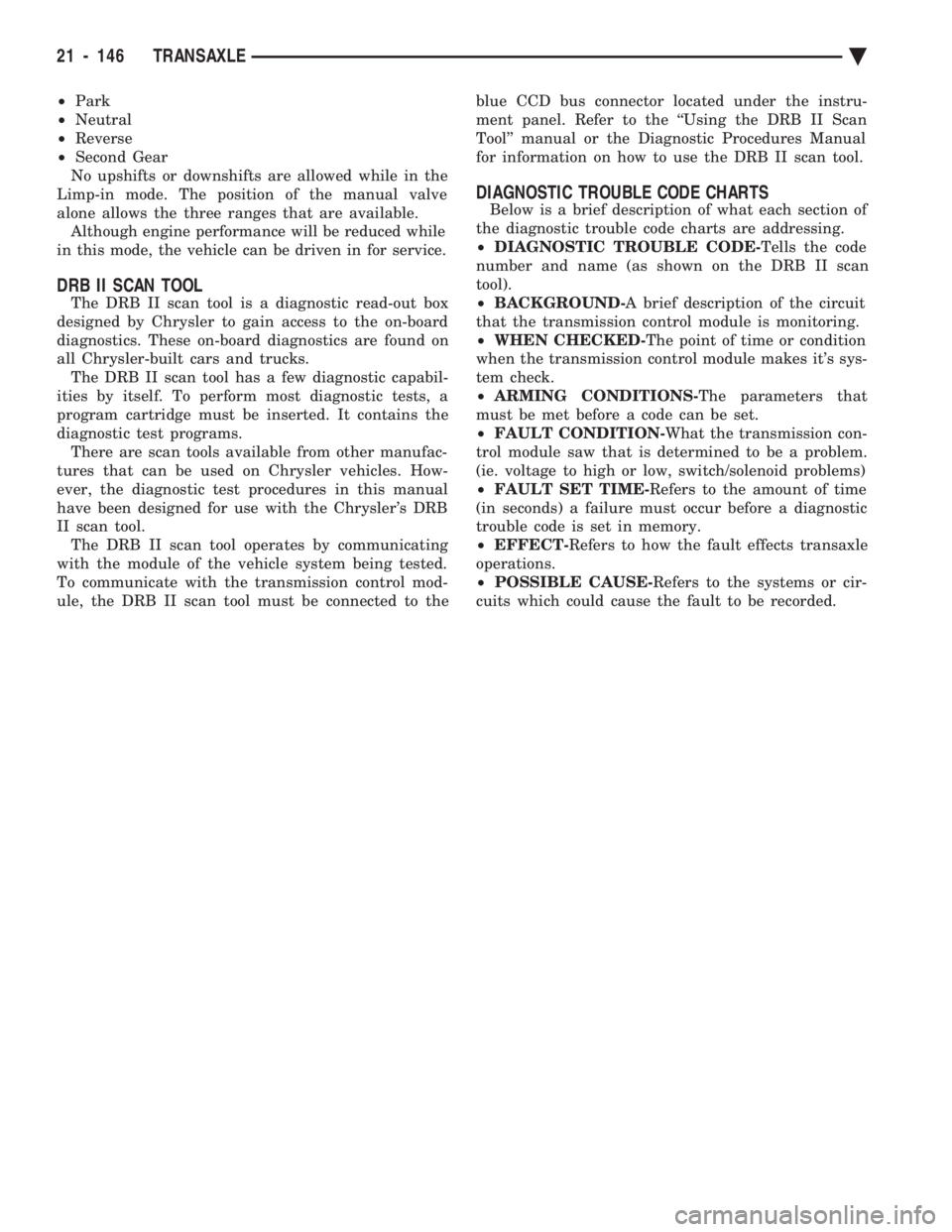
² Park
² Neutral
² Reverse
² Second Gear
No upshifts or downshifts are allowed while in the
Limp-in mode. The position of the manual valve
alone allows the three ranges that are available. Although engine performance will be reduced while
in this mode, the vehicle can be driven in for service.
DRB II SCAN TOOL
The DRB II scan tool is a diagnostic read-out box
designed by Chrysler to gain access to the on-board
diagnostics. These on-board diagnostics are found on
all Chrysler-built cars and trucks. The DRB II scan tool has a few diagnostic capabil-
ities by itself. To perform most diagnostic tests, a
program cartridge must be inserted. It contains the
diagnostic test programs. There are scan tools available from other manufac-
tures that can be used on Chrysler vehicles. How-
ever, the diagnostic test procedures in this manual
have been designed for use with the Chrysler's DRB
II scan tool. The DRB II scan tool operates by communicating
with the module of the vehicle system being tested.
To communicate with the transmission control mod-
ule, the DRB II scan tool must be connected to the blue CCD bus connector located under the instru-
ment panel. Refer to the ``Using the DRB II Scan
Tool'' manual or the Diagnostic Procedures Manual
for information on how to use the DRB II scan tool.
DIAGNOSTIC TROUBLE CODE CHARTS
Below is a brief description of what each section of
the diagnostic trouble code charts are addressing.
² DIAGNOSTIC TROUBLE CODE- Tells the code
number and name (as shown on the DRB II scan
tool).
² BACKGROUND- A brief description of the circuit
that the transmission control module is monitoring.
² WHEN CHECKED- The point of time or condition
when the transmission control module makes it's sys-
tem check.
² ARMING CONDITIONS- The parameters that
must be met before a code can be set.
² FAULT CONDITION- What the transmission con-
trol module saw that is determined to be a problem.
(ie. voltage to high or low, switch/solenoid problems)
² FAULT SET TIME- Refers to the amount of time
(in seconds) a failure must occur before a diagnostic
trouble code is set in memory.
² EFFECT- Refers to how the fault effects transaxle
operations.
² POSSIBLE CAUSE- Refers to the systems or cir-
cuits which could cause the fault to be recorded.
21 - 146 TRANSAXLE Ä
Page 2107 of 2438
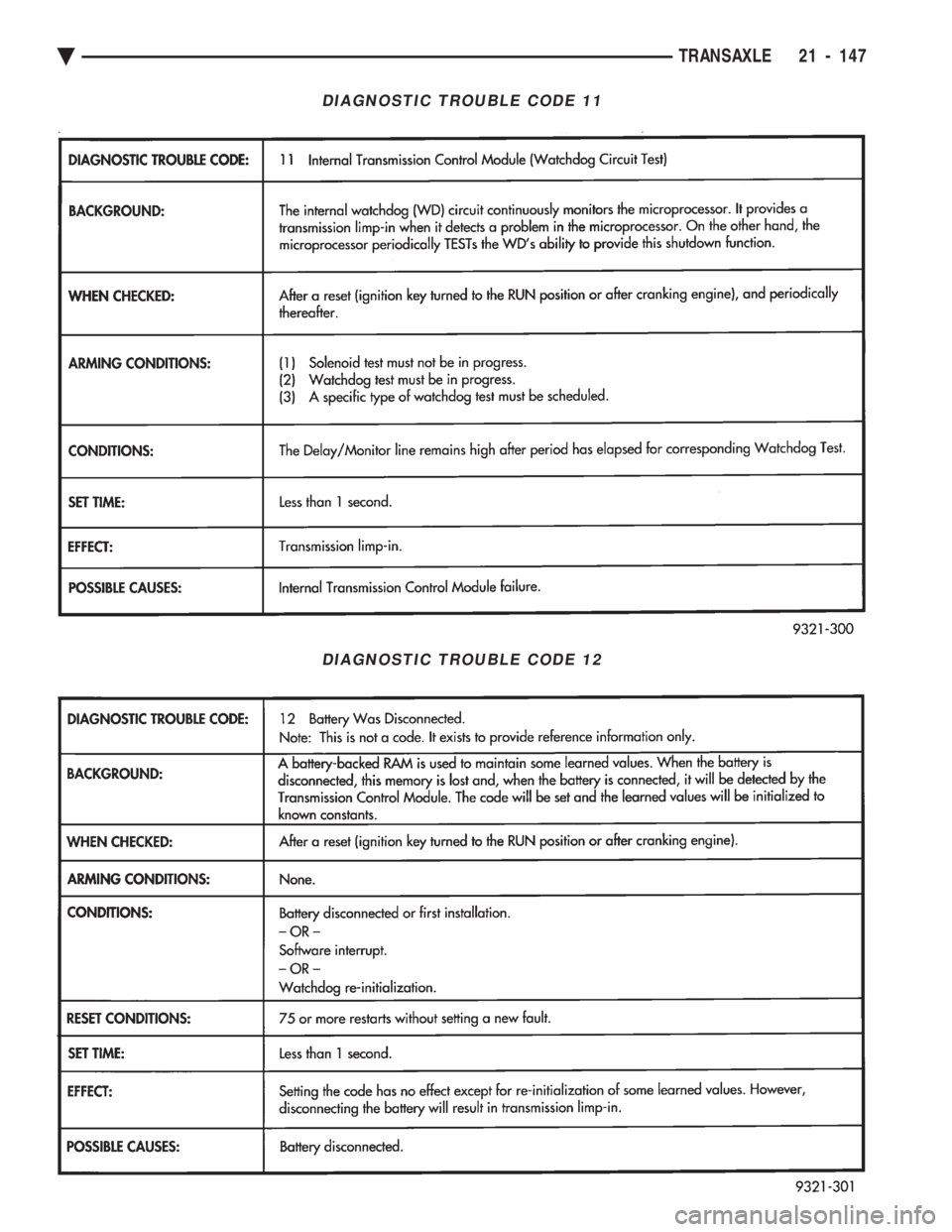
DIAGNOSTIC TROUBLE CODE 11
DIAGNOSTIC TROUBLE CODE 12
Ä TRANSAXLE 21 - 147
Page 2108 of 2438
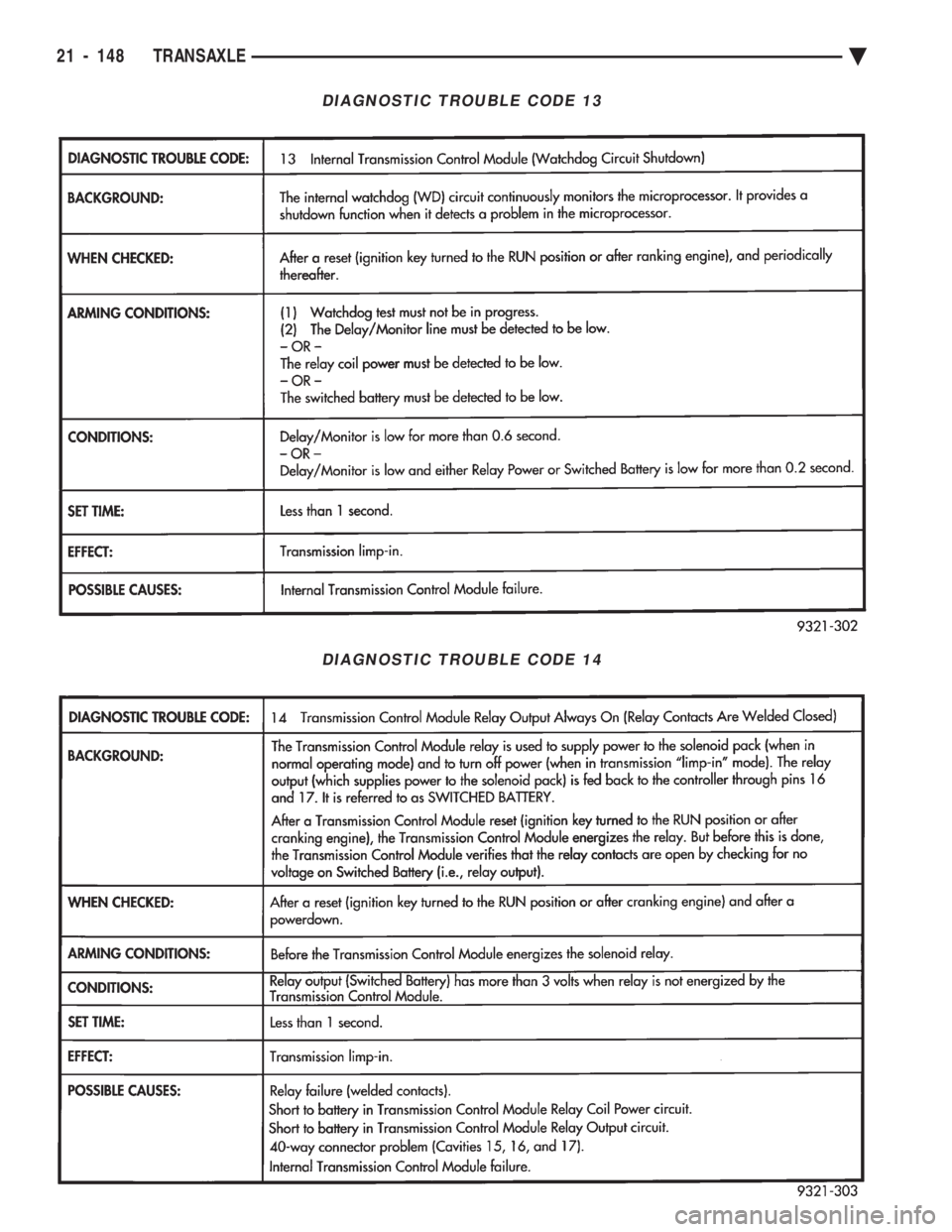
DIAGNOSTIC TROUBLE CODE 13
DIAGNOSTIC TROUBLE CODE 14
21 - 148 TRANSAXLE Ä
Page 2109 of 2438
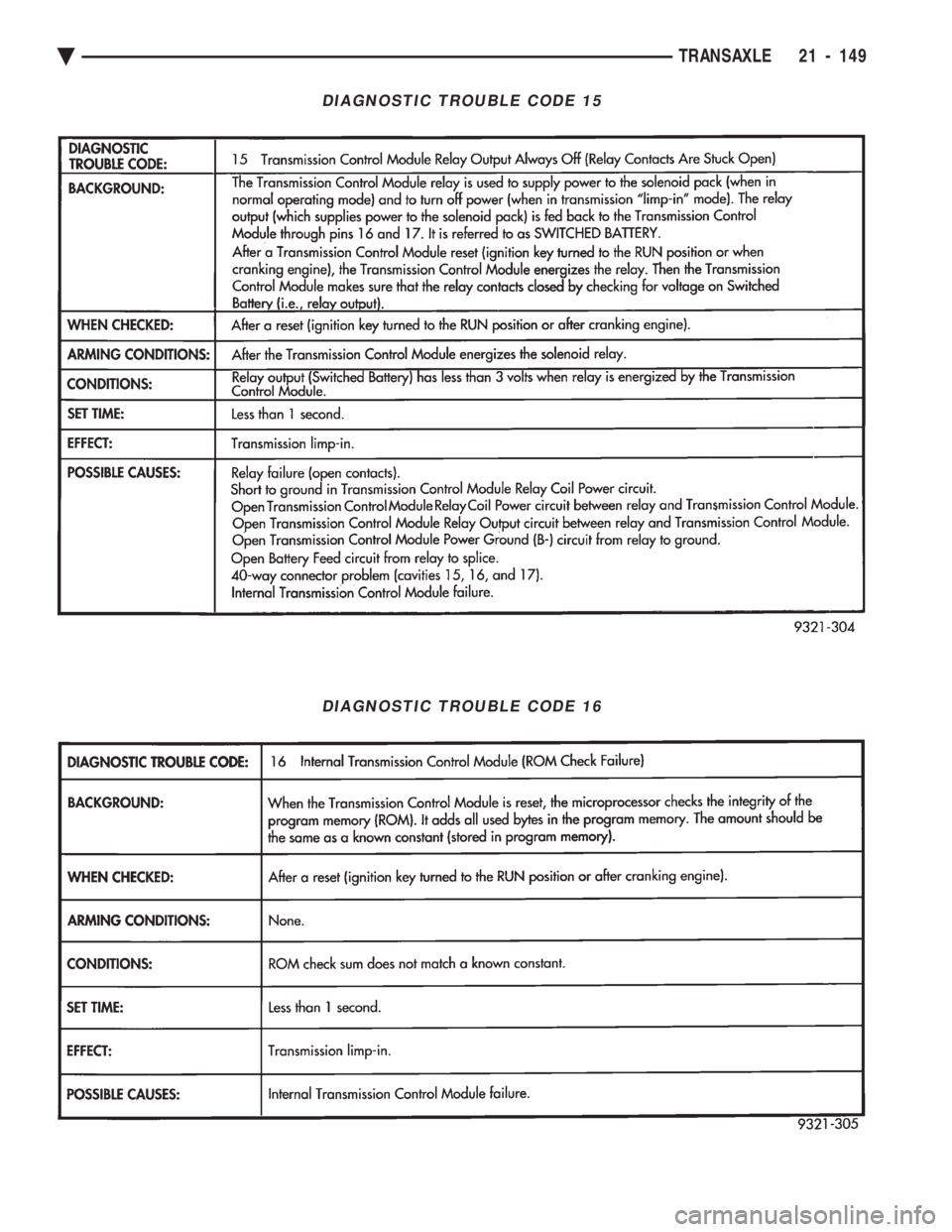
DIAGNOSTIC TROUBLE CODE 15
DIAGNOSTIC TROUBLE CODE 16
Ä TRANSAXLE 21 - 149
Page 2110 of 2438
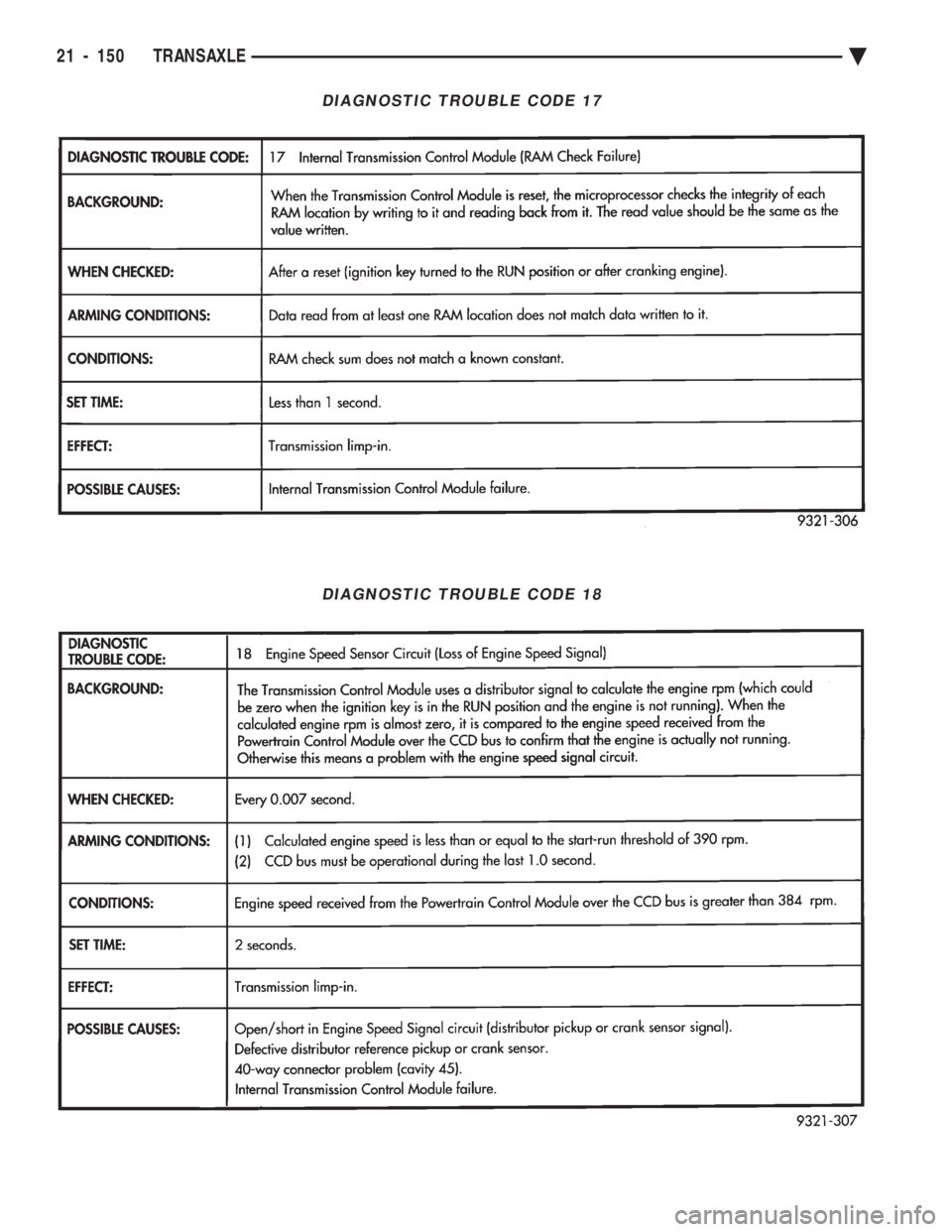
DIAGNOSTIC TROUBLE CODE 17
DIAGNOSTIC TROUBLE CODE 18
21 - 150 TRANSAXLE Ä