check engine light DATSUN 210 1979 Service Manual
[x] Cancel search | Manufacturer: DATSUN, Model Year: 1979, Model line: 210, Model: DATSUN 210 1979Pages: 548, PDF Size: 28.66 MB
Page 19 of 548
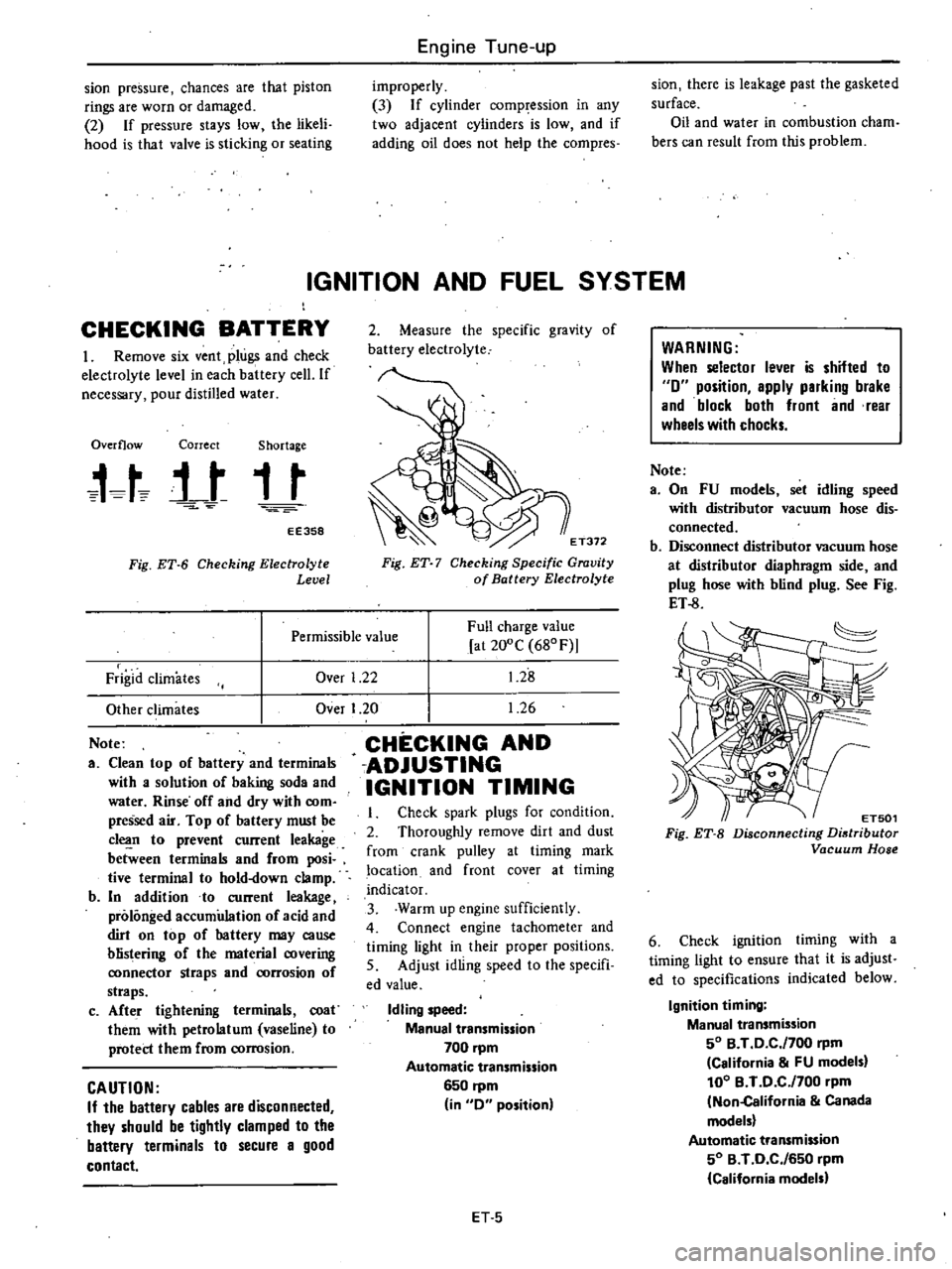
sion
pressure
chances
are
that
piston
rings
are
worn
or
damaged
2
If
pressure
stays
low
the
likeli
hood
is
that
valve
is
sticking
or
seating
Engine
Tune
up
improperly
3
If
cylinder
compression
in
any
two
adjacent
cylinders
is
low
and
if
adding
oil
does
not
help
the
compres
sion
there
is
leakage
past
the
gasketed
surface
Oil
and
water
in
combustion
cham
bers
can
result
from
this
problem
IGNITION
AND
FUEL
SYSTEM
CHECKING
BATTERY
I
Remove
six
vent
plugs
and
check
electrolyte
level
in
each
battery
cell
If
necessary
pour
distilled
water
Overflow
Correct
Shortage
t
t
j
t
t
t
EE358
Fig
ET
6
Checking
Electrolyte
Level
2
Measure
the
specific
gravity
of
battery
electrolyte
E
T372
Fig
ET
7
Checking
Specific
Gravity
of
Battery
Electrolyte
Over
1
22
Full
charge
value
at
200C
680F
1
28
1
26
Permissible
value
Frigid
climates
Other
climates
Note
a
Clean
top
of
battery
and
terminals
with
a
solution
of
baking
soda
and
water
Rinse
off
and
dry
with
com
pressed
air
Top
of
battery
must
be
c1
n
to
prevent
current
leakage
between
terminals
and
from
posi
tive
terminal
to
hold
down
clamp
b
In
addition
to
current
leakage
prolonged
accumulation
of
acid
and
dirt
on
top
of
hattery
may
cause
blistering
of
the
material
covering
ronnector
straps
and
rorrosion
of
straps
c
Afte
r
tightening
terminals
coat
them
with
petrolatum
vaseline
to
protect
them
from
corrosion
CAUTION
If
the
battery
cables
are
disconnected
they
should
be
tightly
clamped
to
the
battery
terminals
to
secure
a
good
contact
Over
I
20
CHECKING
AND
ADJUSTING
IGNITION
TIMING
Check
spark
plugs
for
condition
2
Thoroughly
remove
dirt
and
dust
from
crank
pulley
at
timing
mark
location
and
front
cover
at
timing
indicator
3
Warm
up
engine
sufficiently
4
Connect
engine
tachometer
and
timing
light
in
their
proper
positions
5
Adjust
idling
speed
to
the
specifi
ed
value
Idling
speed
Manual
transmission
700
pm
Automatic
transmission
6S0
rpm
in
0
position
ET
S
WARNING
When
selector
lever
is
shifted
to
0
position
apply
parking
brake
and
block
both
front
and
rear
wheels
with
chocks
Note
a
On
FU
models
set
idling
speed
with
distributor
vacuum
hose
dis
connected
b
Disconnect
distributor
vacuum
hose
at
distributor
diaphragm
side
and
plug
hose
with
blind
plug
See
Fig
ET
8
ET501
Fig
ET
B
Disconnecting
Distributor
Vacuum
Hose
6
Check
ignition
timing
with
a
timing
light
to
ensure
that
it
is
adjust
ed
to
specifications
indicated
below
Ignition
timing
Manual
transmission
SO
B
T
0
C
f700
rpm
California
FU
models
100
B
T
0
C
f700
pm
Non
California
Canada
models
Automatic
transmission
SO
B
T
0
C
f6S0
rpm
California
models
Page 27 of 548
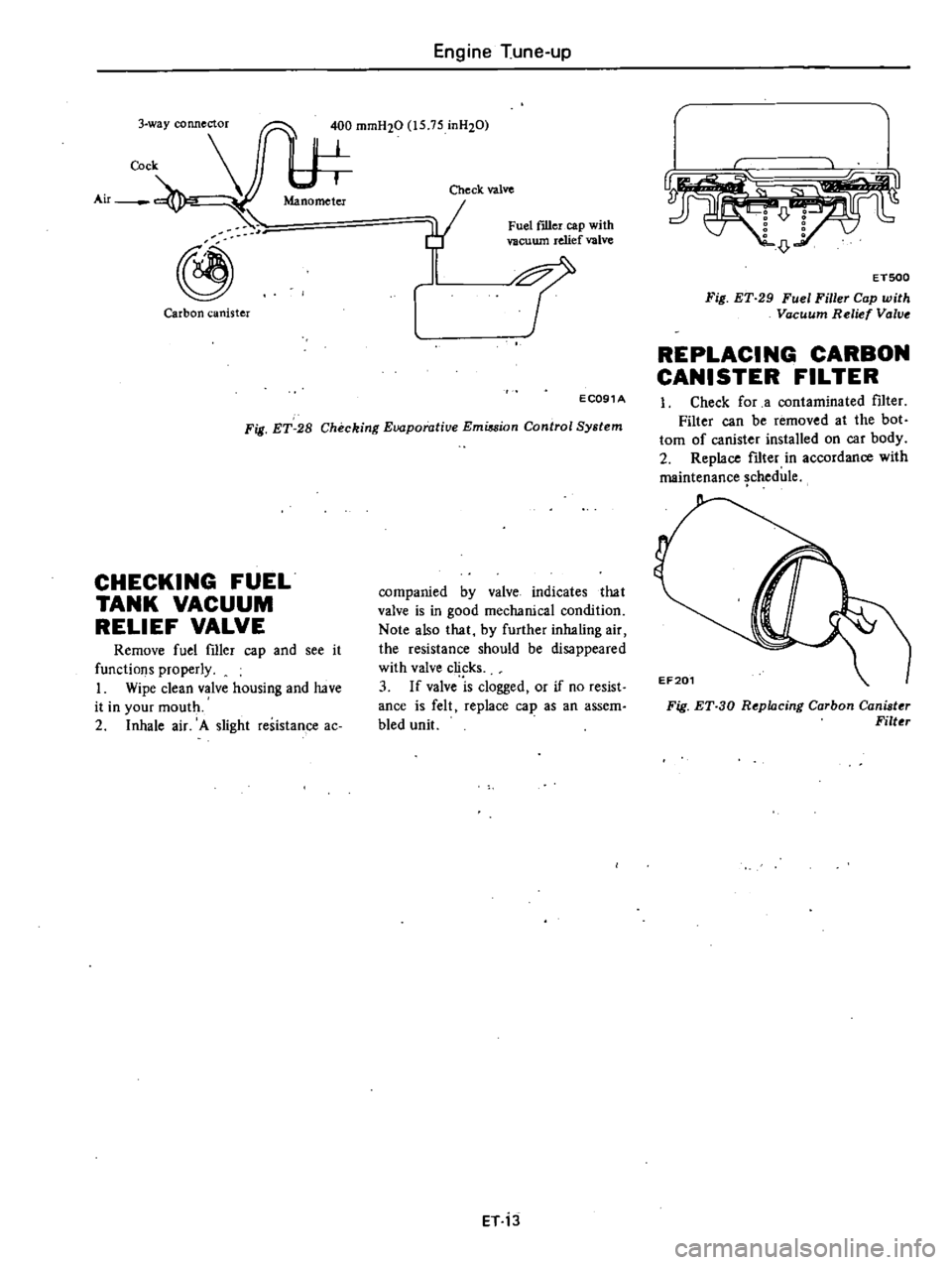
3
way
connector
ck
Air
Manometer
@
Carbon
canister
Engine
Tune
up
400
mmH20
15
75
in
H20
Check
valve
r
F
uel
filler
cap
with
vacuum
relief
valve
1
Fig
ET
28
Checking
Evaporatiue
Emiuion
Control
System
EC091A
CHECKING
FUEL
TANK
VACUUM
RELIEF
VALVE
Remove
fuel
filler
cap
and
see
it
functions
properly
I
Wipe
clean
valve
housing
and
have
it
in
your
mouth
2
Inhale
air
A
slight
resistance
ac
companied
by
valve
indicates
that
valve
is
in
good
mechanical
condition
Note
also
that
by
further
inhaling
air
the
resistance
should
be
disappeared
with
valve
c
ks
3
If
valve
is
clogged
or
if
no
resist
ance
is
felt
replace
cap
as
an
assem
bled
unit
ET
j3
D
o
0
o
0
o
0
ET500
Fig
ET
29
Fuel
Filler
Cap
with
Vacuum
Relief
Value
REPLACING
CARBON
CANISTER
FILTER
Check
for
a
contaminated
fJlter
Filter
can
be
removed
at
the
bot
tom
of
canister
installed
on
car
body
2
Replace
fJlter
in
accordance
with
maintenance
chedule
EF201
Fig
ET
30
Repfucing
Carbon
Canister
Filter
Page 30 of 548
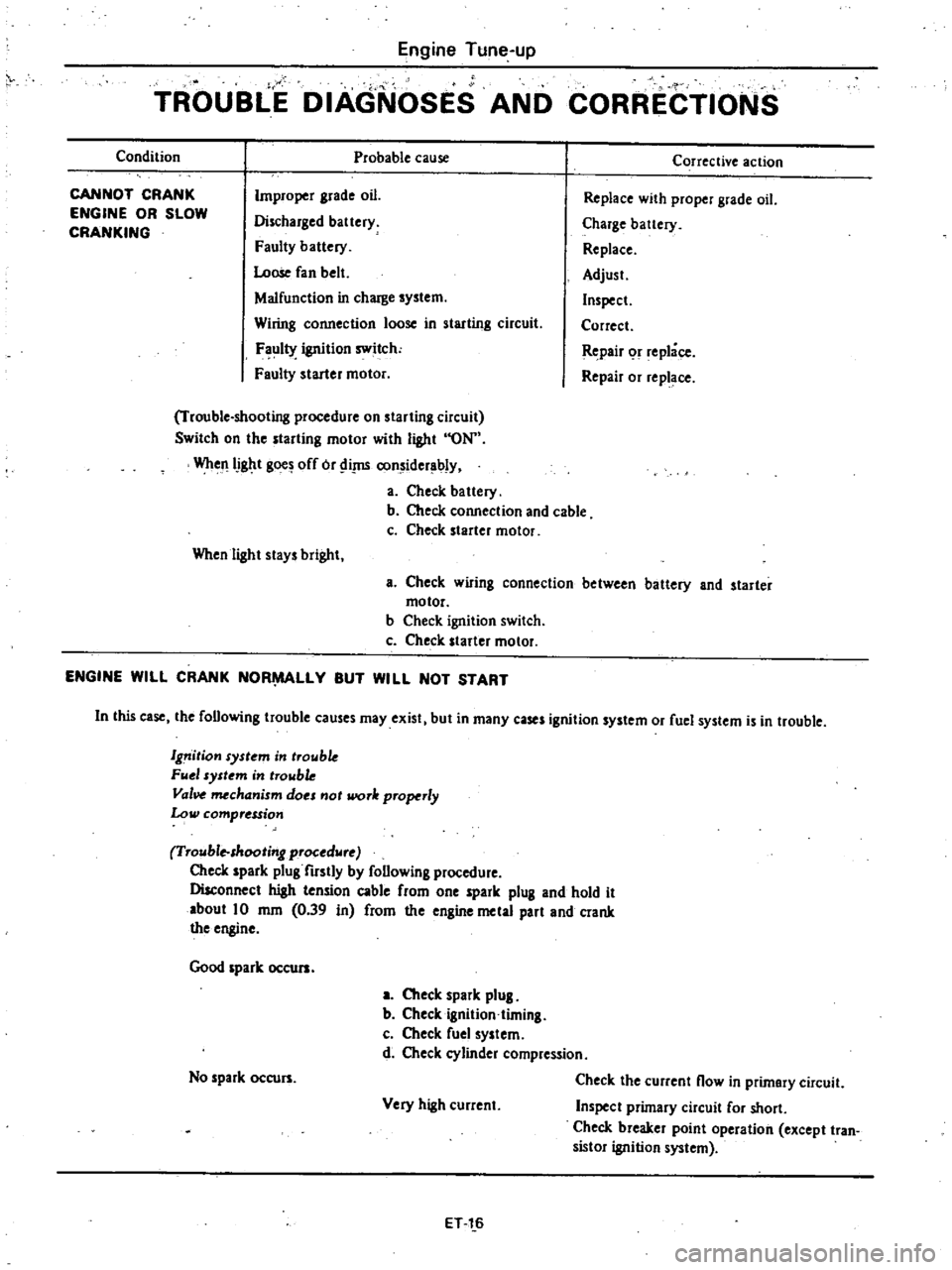
Engine
Tune
up
TROUBLE
DIAGNOSES
AND
CORRECTIONS
Condition
Probable
cause
CANNOT
CRANK
ENGINE
OR
SLOW
CRANKING
Improper
grade
oil
Discharged
battery
Faulty
battery
Loose
fan
belt
Malfunction
in
charge
system
Wiring
connection
loose
in
starting
circuit
F
ul1Y
ignition
switch
Faulty
starter
motor
Trouble
shooting
procedure
on
starting
circuit
Switch
on
the
starting
motor
with
light
ON
WheJlIJght
gOO
off
or
Ii
J1S
considerably
a
Check
battery
b
Check
connection
and
cable
c
Check
starter
motor
When
light
stays
bright
Corrective
action
Replace
with
proper
grade
oil
Charge
battery
Replace
Adjust
Inspect
Correct
Repair
or
replace
Repair
or
replace
a
Check
wlflng
connection
between
battery
and
starter
motor
b
Check
ignition
switch
c
Check
starter
motor
ENGINE
WILL
CRANK
NOR
LLY
BUT
WILL
NOT
START
In
this
case
the
following
trouble
causes
may
exist
but
in
many
cases
ignition
system
or
fuel
system
is
in
trouble
19
ition
syst
m
in
trouble
FII
1
system
in
trowb
Val
mechanism
do
not
work
properly
Low
compression
Trouble
shooting
procedure
Check
spark
plug
firstly
by
following
procedure
Disconnect
high
tension
cable
from
one
spark
plug
and
hold
it
about
10
mm
0
39
in
from
the
engine
metal
part
and
crank
the
engine
Good
spark
occurs
a
Check
spark
plug
b
Checkignition
timing
c
Check
fuel
system
d
Check
cylinder
compression
Check
the
current
now
in
primary
circuit
Very
high
current
Inspect
primary
circuit
for
short
Check
breaker
point
operation
except
tran
sistor
ignition
system
No
spark
occurs
ET
l
6
Page 35 of 548
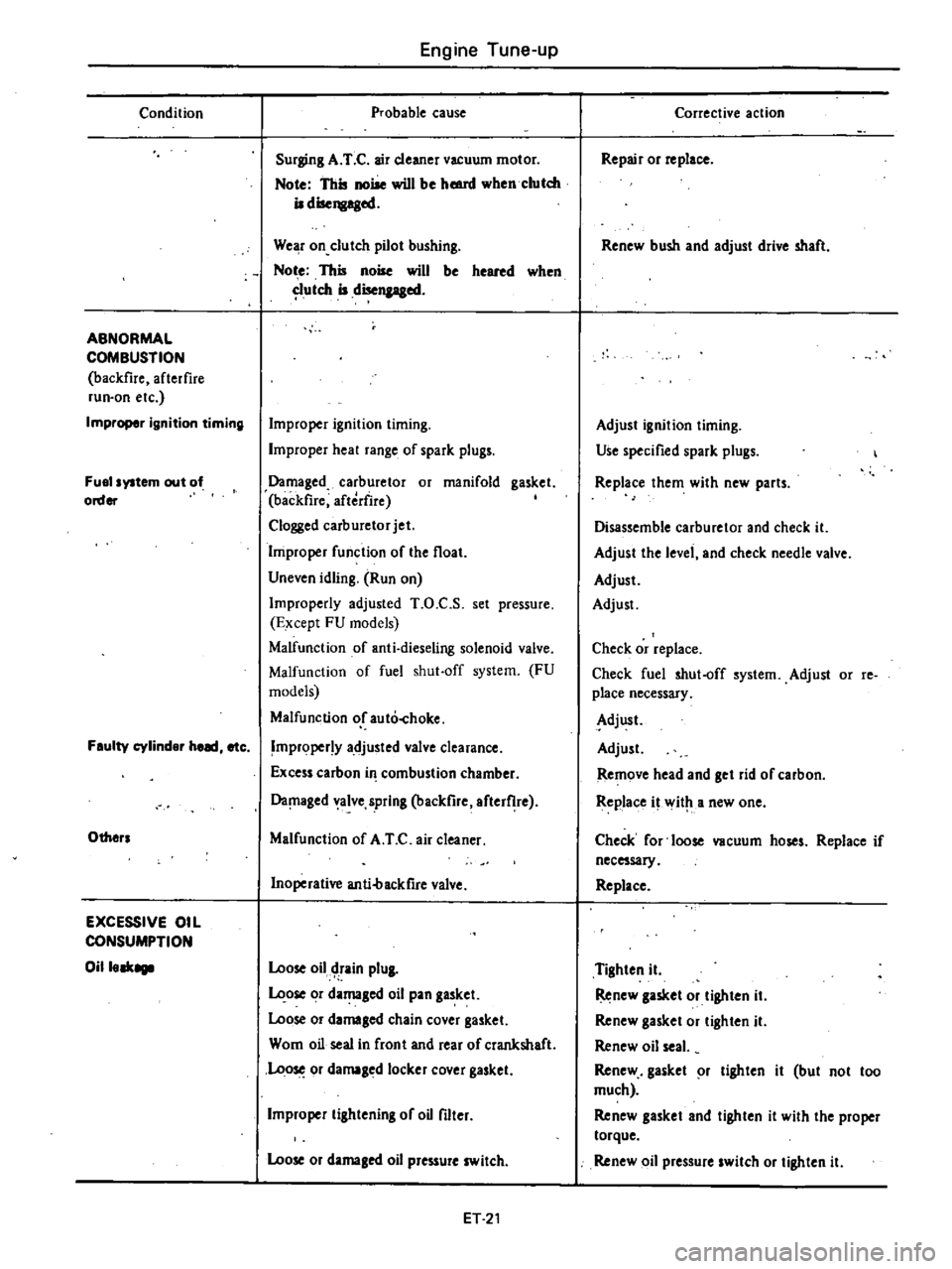
Condition
ABNORMAL
COMBUSTION
backfire
afterfire
run
on
etc
Improper
ignition
timing
Fuel
system
out
of
order
Feulty
cylinder
heed
etc
Others
EXCESSIVE
OIL
CONSUMPTION
Oilleek8111
Engine
Tune
up
Probable
cause
Surging
A
T
C
air
cleaner
vacuum
motor
Note
This
noise
will
be
hmnl
when
clutch
iI
disengaged
We
r
on
clutch
pilot
bushing
Not
e
This
noise
will
be
heared
when
utch
iI
disengaged
Improper
ignition
timing
Improper
heal
range
of
spark
plugs
Damaged
carburetor
or
manifold
gasket
backfire
aftedire
Clogged
carburetor
jet
Improper
function
of
the
float
Uneven
idling
Run
on
Improperly
adjusted
T
O
C
S
set
pressure
Except
FU
models
Malfunction
of
anti
dieseling
solenoid
valve
Malfunction
of
fuel
shut
off
system
FU
models
Malfunction
or
auto
hoke
Improper
y
adjusted
valve
clearance
Excess
carbon
in
combustion
chamber
Da
laged
alve
spring
backfire
after
he
Malfunction
of
A
T
C
air
cleaner
Inoperative
anti4lackfire
valve
Loose
oil
tain
plUI
ose
or
damaged
oil
pan
gasket
Loose
or
damaled
chain
cover
gasket
Wom
oil
seal
in
front
and
rear
of
crankshaft
Loo
or
damaged
locker
cover
gasket
Improper
lilhtening
of
oU
filter
Loose
or
damaled
oil
pressure
switch
ET
21
Corrective
action
Repair
or
replace
Renew
bush
and
adjust
drive
shaft
Adjust
ignition
liming
Use
specified
spark
plugs
Replace
them
with
new
parts
Disassemble
carburetor
and
check
it
Adjust
the
level
and
check
needle
valve
Adjust
Adjust
Check
or
replace
Check
fuel
shut
off
system
Adjust
or
re
place
necessary
Adjust
Adjust
Remove
head
and
get
rid
of
carbon
Replace
it
wit
a
new
one
Check
for
loose
vacuum
hoses
Replace
if
necessary
Replace
Tighten
it
Renew
lasket
or
tighten
iI
Renew
gasket
or
lighten
it
Renew
oil
seal
Renew
gasket
r
lighten
it
but
not
too
much
Renew
gasket
and
tighten
it
with
the
proper
torque
Renew
oil
pressure
switch
or
tighten
it
Page 36 of 548
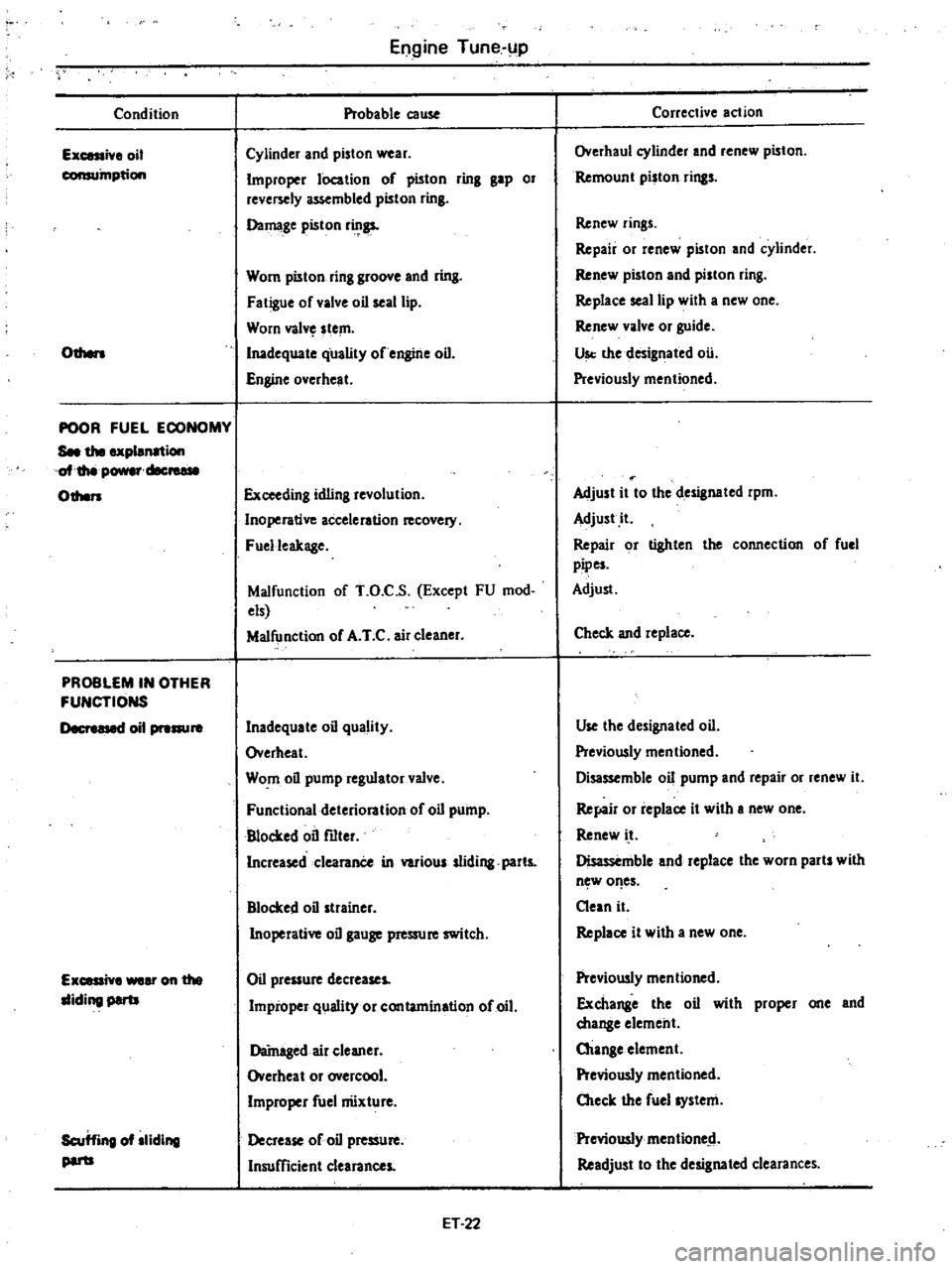
Condition
Ex
iv
oil
consumption
Odlen
POOR
FUEL
ECONOMY
See
the
explanation
oI
thtI
power
cIec
01hen
PROBLEM
IN
OTHER
FUNCTIONS
t
1
oil
pre
E
eronthe
lIiding
par1J
Scuffing
oIlliding
par1J
Engine
Tune
up
Probable
cause
Cylinder
and
piston
wear
Improper
lOcation
of
pi5ton
ring
gap
or
reversely
assembled
piston
ring
Damage
pi5ton
r
gs
Wom
pilton
ring
groove
and
ring
Fatigue
of
valve
oil
seal
lip
Worn
valv
stem
Inadequate
qUality
of
engine
oil
Engine
overheat
Exceeding
idling
revolution
Inoperative
acceleration
covel
Fuelleakage
Malfunction
of
T
O
C
S
Except
FU
mod
els
Malfunction
of
A
T
C
air
cleaner
Inadequate
oil
quality
Overheat
Worn
oil
pump
regulator
valve
Functional
deterioration
of
oil
pump
Blocked
oil
filter
Increased
clearanCe
in
various
sliding
parts
Blocked
oil
strainer
Inoperative
oil
gauge
pressure
switch
Oil
pressure
decreases
Improper
quality
or
contamination
of
oil
Damaged
air
cleaner
Overheat
or
overcool
Improper
fuel
nUxture
Decrease
of
oil
presSure
Insufficient
clearances
ET
22
Corrective
action
Overhaul
cylinder
and
renew
piston
Remount
piston
rings
Renew
rings
Repair
or
renew
piston
and
cylinder
Renew
piston
and
piston
ring
Replace
seal
lip
with
a
new
one
Renew
valve
or
guide
Us
the
designated
ou
Previously
mentioned
Adjust
it
to
the
designated
rpm
Adjust
it
Repair
or
lighten
the
connection
of
fuel
pipes
Adjust
Check
and
replace
Use
the
designated
oil
Previously
mentioned
Disassemble
oil
pump
and
repair
or
renew
it
Ref4ir
or
replace
it
with
I
new
one
Renew
i
t
Disassemble
and
replace
the
worn
parts
with
n
w
of
es
Clean
it
Replace
it
with
a
new
one
Previously
mentioned
Exchange
the
oil
with
proper
one
and
change
element
Otange
element
Previously
mentioned
Oteck
the
fuel
system
Previously
mentione
d
Readjust
to
the
designated
clearances
Page 44 of 548
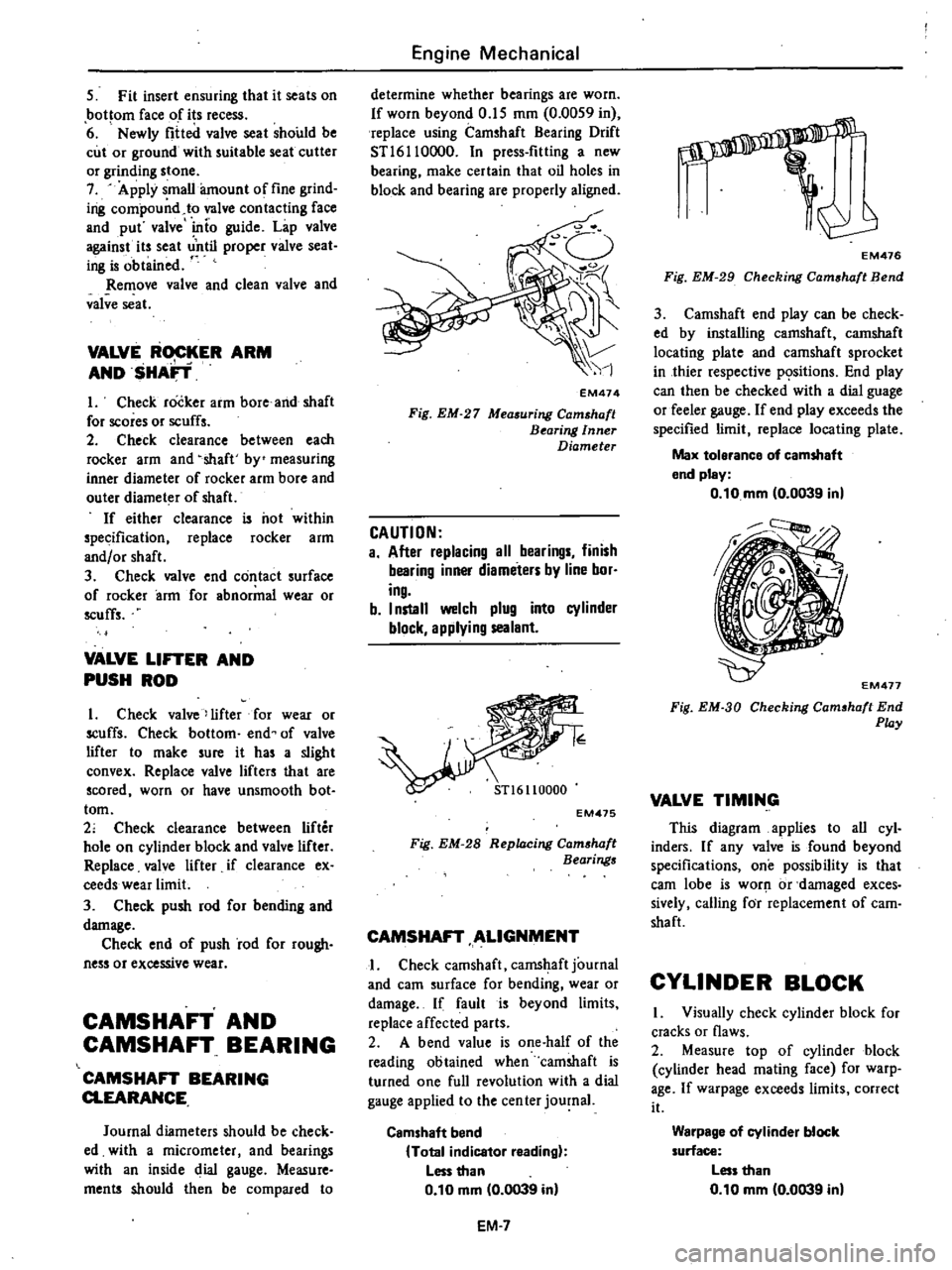
5
Fit
insert
ensuring
that
it
seats
on
bottom
face
of
its
recess
6
Newly
fitted
valve
seat
should
be
cut
or
ground
with
suitable
seat
cutter
or
grinding
stone
7
Apply
smalliunount
of
fine
grind
ing
compound
to
valve
contacting
face
and
put
valve
into
guide
Lap
valve
against
its
seat
ntil
proper
valve
seat
ing
is
obtained
Remove
valve
and
clean
valve
and
valve
seat
VALVE
ROCKER
ARM
1
AND
SHAFT
I
Check
rocker
arm
bore
and
shaft
for
scores
or
scuffs
2
Check
clearance
between
each
rocker
arm
and
shaft
by
measuring
inner
diameter
of
rocker
arm
bore
and
outer
diameter
of
shaft
If
either
clearance
is
not
within
spec
ification
replace
rocker
arm
and
or
shaft
3
Check
valve
end
contact
surface
of
rocker
arm
for
abnormal
wear
or
scuffs
VALVE
LIFTER
AND
PUSH
ROD
I
Check
valve
lifter
for
wear
or
scuffs
Check
bottom
end
of
valve
lifter
to
make
sure
it
has
a
slight
convex
Replace
valve
lifters
that
are
scored
worn
or
have
unsmooth
bot
tom
2
Check
clearance
between
lifter
hole
on
cylinder
block
and
valve
lifter
Replace
valve
lifter
if
clearance
ex
ceeds
wear
limit
3
Check
push
rod
for
bending
and
damage
Check
end
of
push
rod
for
rough
ness
or
excessive
wear
CAMSHAFT
AND
CAMSHAFT
BEARING
CAMSHAFT
BEARING
CLEARANCE
Journal
diameters
should
be
check
ed
with
a
micrometer
and
bearings
with
an
inside
dial
gauge
Measure
ments
should
then
be
compared
to
Engine
Mechanical
determine
whether
bearings
are
worn
If
worn
beyond
0
15
mm
0
0059
in
replace
using
Camshaft
Bearing
Drift
STl6Il0000
In
press
fitting
a
new
bearing
make
certain
that
oil
holes
in
block
and
bearing
are
properly
aligned
EM474
Fig
EM
27
Measuring
Camshaft
Bearing
Inner
Diameter
CAUTION
a
After
replacing
all
bearings
finish
bearing
inner
diameters
by
line
bor
ing
b
I
nstall
welch
plug
into
cylinder
block
applying
sealant
EM475
Fig
EM
28
Replacing
Cam
haft
Bearings
CAMSHAFT
ALIGNMENT
I
Check
camshaft
camshaft
journal
and
earn
surface
for
bending
wear
or
damage
If
fault
is
beyond
limits
replace
affected
parts
2
A
bend
value
is
one
half
of
the
reading
obtained
when
camshaft
is
turned
one
full
revolution
with
a
dial
gauge
applied
to
the
cen
ter
journal
Camshaft
bend
Total
indicator
reading
Less
than
0
10
mm
0
0039
in
EM
7
s
EM476
Fig
EM
29
Checking
Cam
haft
Bend
3
Camshaft
end
play
can
be
check
ed
by
installing
camshaft
camshaft
locating
plate
and
camshaft
sprocket
in
thier
respective
p
sitions
End
play
can
then
be
checked
with
a
dial
guage
or
feeler
gauge
If
end
play
exceeds
the
specified
limit
replace
locating
plate
Max
tolerance
of
camshaft
end
pley
0
10
mm
0
0039
in
EM477
Fig
EM
3D
Checking
Cam
haft
End
Play
VALVE
TIMING
This
diagram
applies
to
all
cyl
inders
If
any
valve
is
found
beyond
specifications
one
possibility
is
that
earn
lobe
is
worJ
1
or
damaged
exces
sively
calling
for
replacement
of
cam
shaft
CYLINDER
BLOCK
I
Visually
check
cylinder
block
for
cracks
or
flaws
2
Measure
top
of
cylinder
block
cylinder
head
mating
face
for
warp
age
If
warpage
exceeds
limits
correct
it
Warpage
of
cylinder
block
surface
Less
than
0
10
mm
0
0039
in
Page 49 of 548
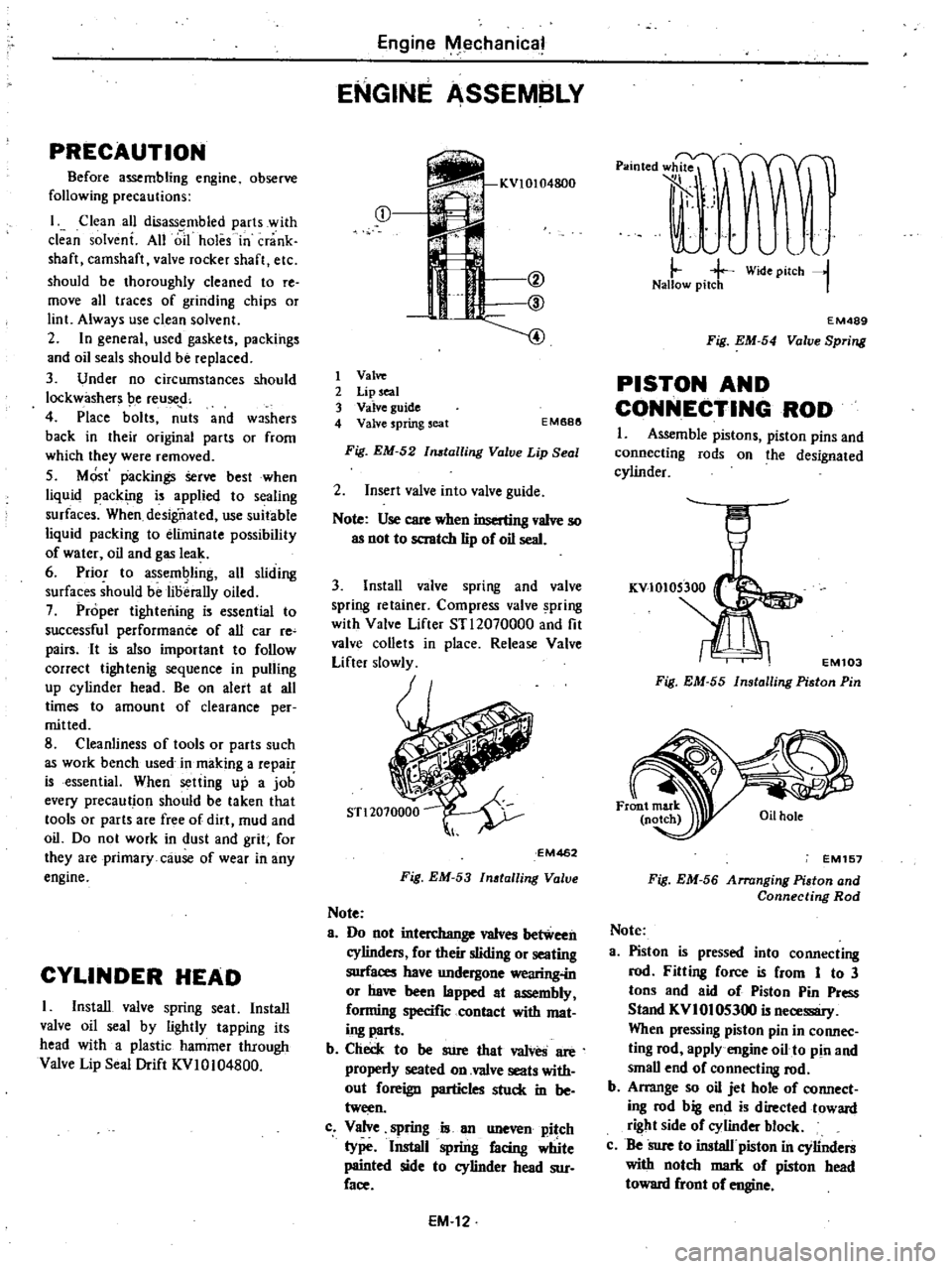
PRECAUTION
Before
assembling
engine
observe
following
precautions
I
Clean
all
disass
mbled
parts
with
clean
solvent
All
611
holes
in
crank
shaft
camshaft
valve
rocker
shaft
etc
should
be
thoroughly
cleaned
to
re
move
all
traces
of
grinding
chips
or
lint
Always
use
clean
solvent
2
In
general
used
gaskets
packings
and
oil
seals
should
be
replaced
3
Under
no
circumstances
should
lockwashers
be
reuse
d
4
Place
bolts
nuts
and
woshers
back
in
their
original
parts
or
from
which
they
were
removed
5
MOst
packing
Serve
best
when
liquid
packing
is
applied
to
sealing
surfaces
When
desigiiated
use
suitable
liquid
packing
to
eliminate
possibility
of
water
oil
and
gas
leak
6
Prior
to
assemQling
all
sliding
surfaces
should
be
lioerally
oiled
7
Proper
tightening
is
essential
to
successful
performanCe
of
all
car
re
pairs
It
is
also
important
to
follow
correct
tightenig
sequence
in
pulling
up
cylinder
head
Be
on
alert
at
all
times
to
amount
of
clearance
per
mitted
8
Cleanliness
of
tools
or
parts
such
as
work
bench
used
jn
making
a
repai
is
essential
When
setting
up
a
job
every
precaution
should
be
taken
that
tools
or
parts
are
free
of
dirt
mud
and
oil
Do
not
work
in
dust
and
grit
for
they
are
primary
cause
of
wear
in
any
engine
CYLINDER
HEAD
I
Install
valve
spring
seat
Install
valve
oil
seal
by
lightly
tapping
its
head
with
a
plastic
hammer
through
Valve
Lip
Seal
Drift
KVI0104800
Engine
Mechanical
ENGINE
ASSEMBLY
m
f
if
@
@
4
1
Valve
2
Lip
seal
3
Valve
guide
4
Valve
spring
seat
EM688
Fig
EM
52
tailing
Valve
Lip
Seal
2
Insert
valve
into
valve
guide
Note
Use
care
when
inserting
valve
so
as
not
to
scratch
lip
of
oil
seal
3
Install
valve
spring
and
valve
spring
retainer
Compress
valve
pring
with
Valve
Lifter
STl2070000
and
fit
valve
collets
in
place
Release
Valve
Lifter
slowly
EM462
Fig
EM
53
Inatalling
Valve
Note
8
Do
not
interchange
valves
between
cylinders
for
their
sliding
or
seating
surfaces
have
undergone
wearing
in
or
have
been
lapped
at
assembly
forming
specific
contact
with
mat
ing
parts
b
Check
to
be
sure
that
valves
are
properly
seated
on
valve
seats
with
out
foreign
particles
stuck
in
be
tween
c
Valve
spring
is
an
uneven
pitch
type
Install
spring
facing
Wte
painted
side
to
cylinder
head
sur
face
EM
12
p
lOted
l
rJF
t
A
J
il
j
j
Wide
pilCh
l
Nallow
pitch
I
EM489
Fig
EM
54
Valve
Spring
PISTON
AND
CONNECTING
ROD
I
Assemble
pistons
piston
pins
and
connecting
rods
on
the
designated
cylinder
EM103
Fig
EM
55
Installing
Piston
Pin
EM157
Fig
EM
56
Arranging
Piaton
and
Connecting
Rod
Note
3
Piston
is
pressed
into
connecting
rod
Fitting
force
is
from
1
to
3
tons
and
aid
of
Piston
Pin
Press
Stand
KVI
01
05300
is
necessary
When
pressing
piston
pin
in
connec
ting
rod
apply
engine
oil
to
pin
and
small
end
of
connecti
8
rod
b
Arrange
so
oil
jet
hole
of
connect
ing
rod
big
end
is
directed
toward
right
side
of
cylinder
block
c
Be
Sure
to
install
piston
in
cylinders
with
notch
mark
of
piston
head
toward
front
of
engine
Page 75 of 548
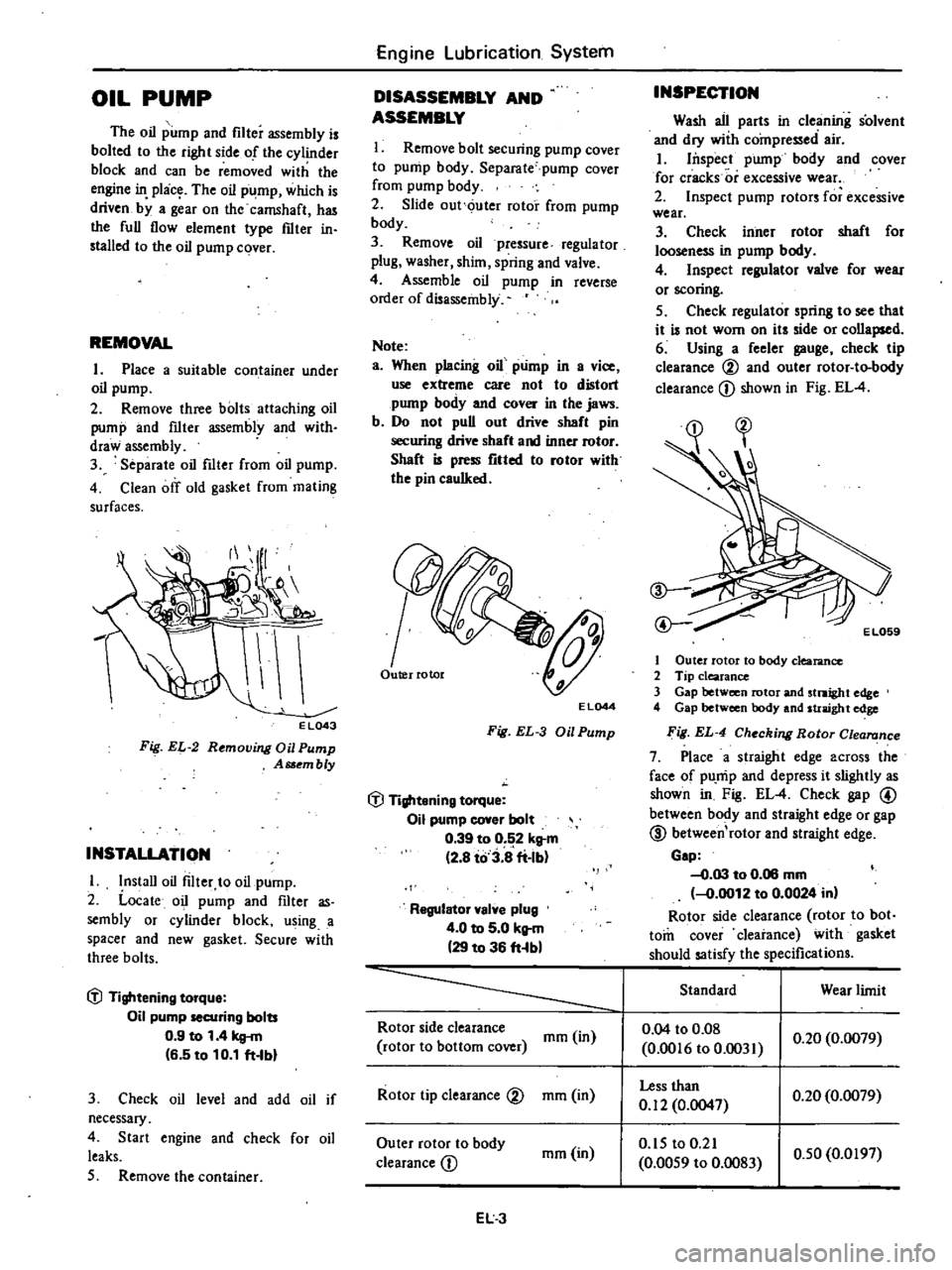
OIL
PUMP
The
oil
pump
and
filter
assembly
is
bolted
to
the
right
side
of
the
cylinder
block
and
can
be
removed
with
the
engine
in
pl
c
The
oil
pump
which
is
driven
by
a
gear
on
the
camshaft
has
the
full
flow
element
type
filter
in
stalled
to
the
oil
pump
cover
REMOVAL
I
Place
a
suitable
container
under
oil
pump
2
Remove
three
bolts
attaching
oil
pump
and
filter
assembly
and
with
draw
assembly
3
Separate
oil
filter
from
oil
pump
4
Ciean
off
old
gasket
from
mating
surfaces
i
E
L043
F
EL
2
R
moving
Oil
Pump
Asso
mbly
INSTALLATION
I
Install
oil
filter
to
oil
pump
2
Locate
oil
pump
and
filter
as
sembly
or
cylinder
block
using
a
spacer
and
new
gasket
Secure
with
three
bolts
l
l
Tightening
torque
Oil
pump
securing
bolts
0
9
to
1
4
kg
m
6
5
to
10
1
ft
lbl
3
Check
oil
level
and
add
oil
if
necessary
4
Start
engine
and
check
for
oil
leaks
5
Remove
the
container
Engine
Lubrication
System
DISASSEMBLY
AND
ASSEMBLY
I
Remove
bolt
securing
pump
cover
to
pump
body
Separate
pump
cover
from
pump
body
2
Slide
out
outer
rotor
from
pump
body
3
Remove
oil
pressure
regulator
plug
washer
shim
spring
and
valve
4
Assemble
oil
pump
in
reverse
order
of
disassembly
Note
a
When
placing
oil
pump
in
a
vice
use
extreme
care
not
to
distort
pump
body
and
cover
in
the
jaws
b
Do
not
pull
out
drive
shaft
pin
securing
drive
shaft
and
inner
rotor
Shaft
is
press
fitted
to
rotor
with
the
pin
caulked
EL044
Fig
EL
3
Oil
Pump
l
l
Tightening
torque
Oil
pump
cove
bolt
0
39
to
0
5
2
kltm
2
8
to
3
8
ti
Ib
Regulator
valve
plug
4
0
to
5
0
kltm
29
to
36
ft
bl
INSPECTION
Wash
all
parts
in
cleaning
solvent
and
dry
wiih
compressed
air
I
hispect
pump
body
and
cover
for
cracks
or
excessive
wear
2
Inspect
pump
rotors
for
excessive
wear
3
Check
inner
rotor
shaft
for
looseness
in
pump
body
4
Inspect
regulator
valve
for
wear
or
scoring
5
Check
regulator
spring
to
see
that
it
is
not
worn
on
its
side
or
collapsed
6
Using
a
feeler
gauge
check
tip
clearance
00
and
outer
rotor
to
body
clearance
CD
shown
in
Fig
EL
4
EL059
1
Outer
rotor
to
body
clearance
2
Tip
clearance
3
Gap
between
rotor
and
stnight
edge
4
Gap
between
body
and
straight
edge
ig
EL
4
Checking
Rotor
Clea
nce
7
Place
a
straight
edge
across
the
face
of
pU
mp
and
depress
it
slightly
as
shown
in
Fig
EL
4
Check
gap
@
between
body
and
straight
edge
or
gap
@
between
rotor
and
straight
edge
Gap
0
03
to
0
06
mm
0
0012
to
0
0024
in
Rotor
side
clearance
rotor
to
bot
tom
cover
clearance
with
gasket
should
satisfy
the
specifications
Standard
Wear
limit
Rotor
side
clearance
mm
in
0
04
to
0
08
rotor
to
bottom
cover
0
0016
to
0
031
0
20
0
0079
Rotor
tip
clearance
V
mm
in
Less
than
0
20
0
0079
0
12
0
0047
Outer
rotor
to
body
mm
in
0
15
to
0
21
0
50
0
0197
clearance
CD
0
0059
to
0
083
EL3
Page 76 of 548
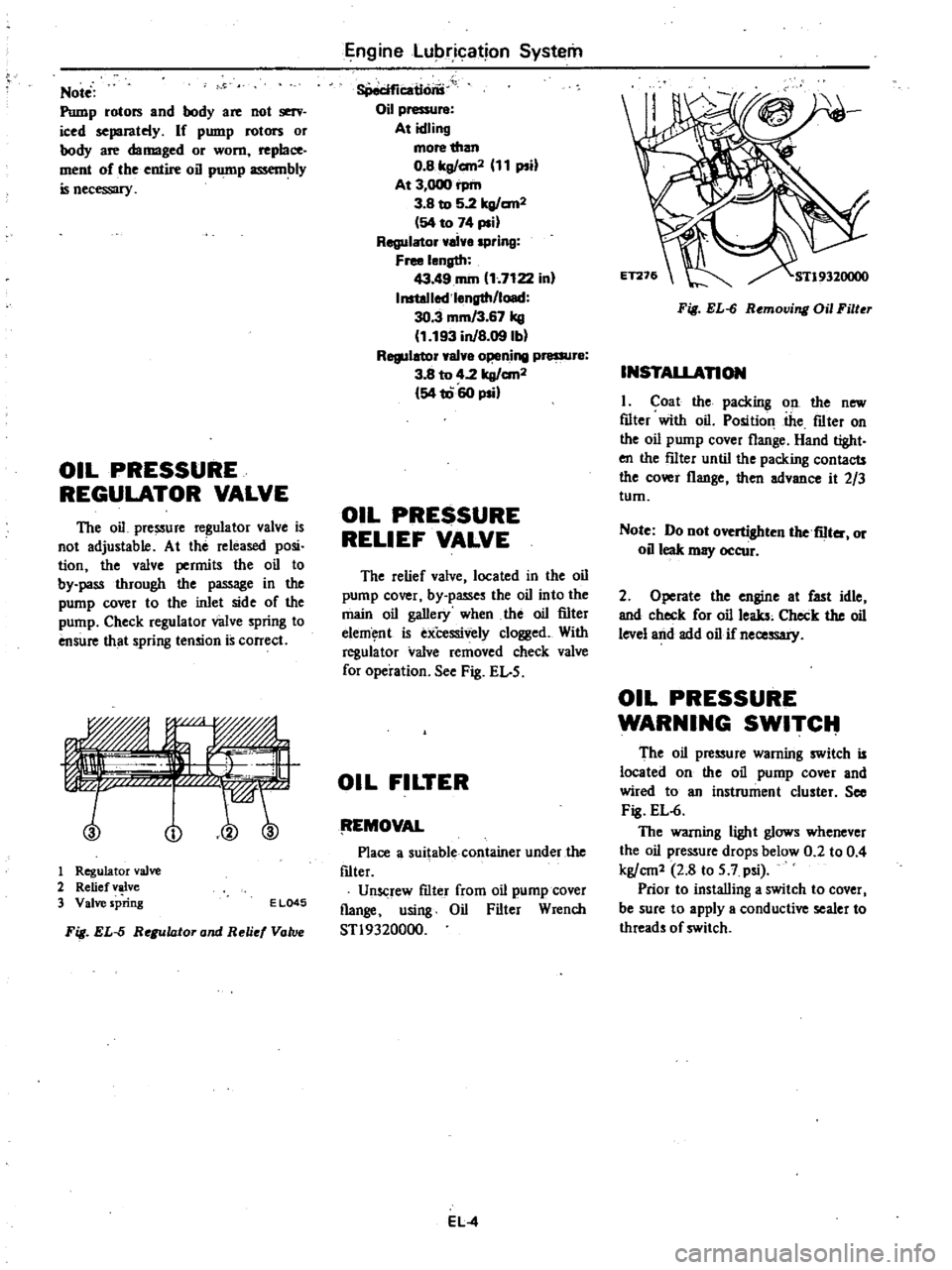
Not
Pump
rotors
and
body
are
not
serv
iced
separatdy
If
pump
rotors
or
body
are
damaged
or
worn
replace
ment
of
the
entire
oil
pump
assembly
isnecessary
OIL
PRESSURE
REGULATOR
VALVE
The
oil
pressure
regulator
valve
is
not
adjustable
At
the
released
posi
tion
the
valve
permits
the
oil
to
by
pass
through
the
passage
in
the
pump
cover
to
the
inlet
side
of
the
pump
Check
regulator
valve
spring
to
ensure
that
spring
tension
is
correct
no
1
Regulator
valve
2
Relief
valve
3
Valve
spring
E
L045
Fig
EL
5
Regulator
and
Reli
Vatv
Engine
Lubrication
System
8Peciflcatlons
Oil
pressure
At
idling
more
than
O
Blrg
an2
11
psi
At
3
000
rpm
3
B
to
5
2lrg
an2
54
to
74
psi
Regulator
ai
spring
Free
length
43
49
rom
1
7122
in
InstoJlod
l
ngth
load
30
3
mm
3
67
kg
1
193
inJB
09lbl
Regulator
val
o
ning
pressur
3
8
to
4
2
lrg
an2
54
1060
psi
OIL
PRESSURE
RELIEF
VALVE
The
relief
valve
located
in
the
oil
pump
cover
by
passes
the
oil
into
the
main
oil
gallery
when
the
oil
filter
elem
nt
is
exCessively
clogged
With
regula
tor
valve
removed
check
valve
for
operation
See
Fig
EL
5
OIL
FILTER
tEMOVAL
Place
a
suitable
container
under
the
f1lter
Unscrew
f1lter
from
oil
pump
cover
flange
using
Oil
Filter
Wrench
STl9320000
EL
4
Fig
EL
6
Removing
Oil
Filter
INSTALLAnON
I
Coat
the
packing
on
the
new
f1lter
with
oil
Position
the
f1lter
on
the
oil
pump
cover
flange
Hand
tight
en
the
f11ter
until
the
packing
contacts
the
cover
flange
then
advance
it
2
3
tum
Note
Do
not
overtighten
the
fiIter
or
oil
leak
may
occur
2
Operate
the
engine
at
fast
idle
and
check
for
oil
leaks
Check
the
oil
level
and
add
oil
if
necessary
OIL
PRESSURE
WARNING
SWITCIt
The
oil
pressure
warning
switch
is
located
on
the
oil
pump
cover
and
wired
to
an
instrument
cluster
See
Fig
EL
6
The
warning
light
glows
whenever
the
oil
pressure
drops
below
0
2
to
0
4
kg
cm1
2
8
to
5
7
psi
Prior
to
installing
a
switch
to
cover
I
be
sure
to
apply
a
conductive
sealer
to
threads
of
switch
Page 99 of 548
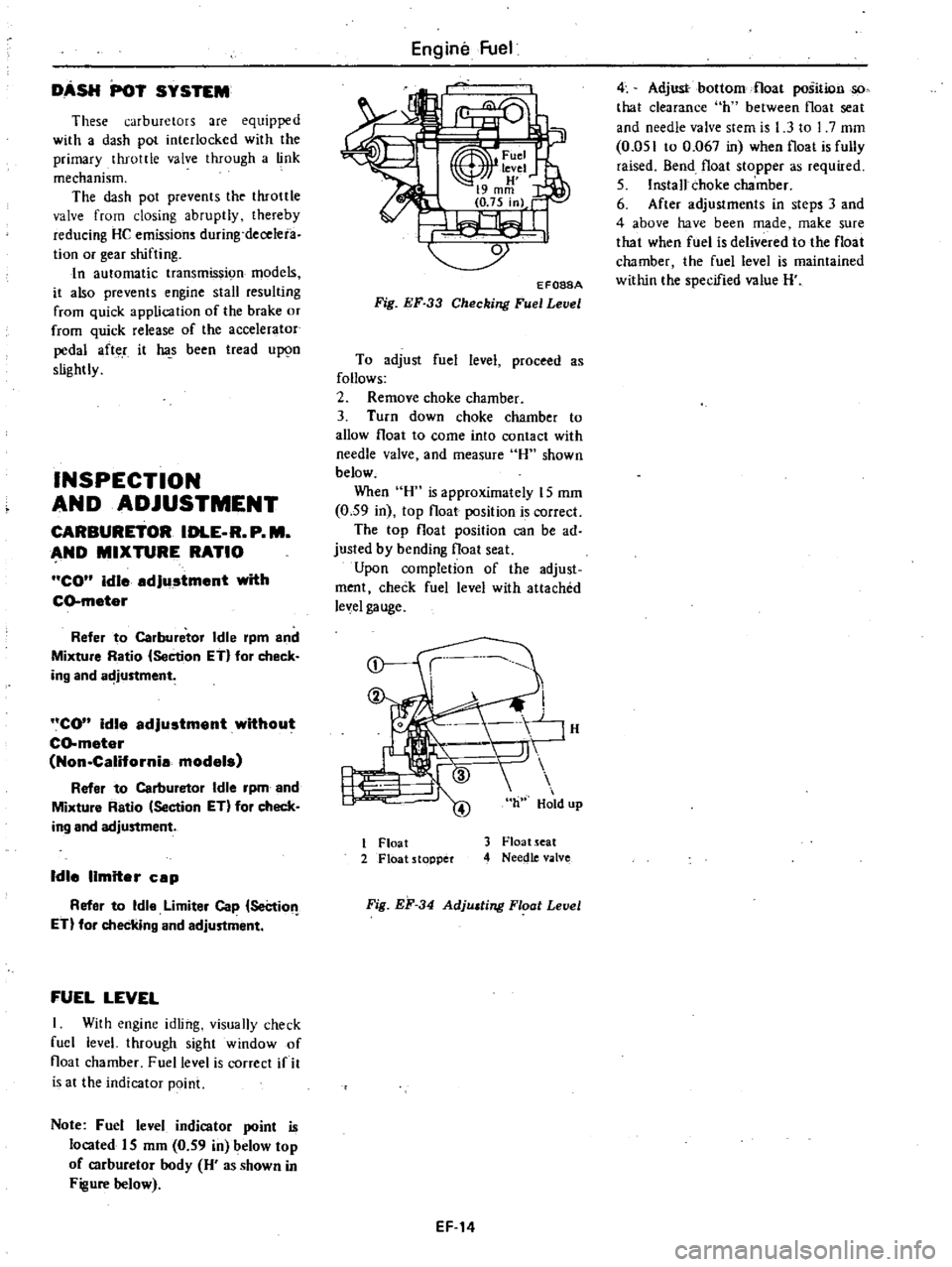
DASH
POT
SYSTEM
These
carburetors
are
equipped
with
a
dash
pot
interlocked
with
the
primary
thrott
Ie
valve
through
a
link
mechanism
The
dash
pot
prevents
the
throttle
valve
from
closing
abruptly
thereby
reducing
He
emissions
during
deceleia
tion
or
gear
shifting
In
automatic
transmissi9fi
models
it
also
prevents
engine
stall
resulting
from
quick
application
of
the
brake
or
from
quick
release
of
the
accelerator
pedal
after
it
s
been
tread
upon
slightly
INSPECTION
AND
ADJUSTMENT
CARBURETOR
IDLE
R
P
M
AND
MIXTURE
RATIO
CO
idle
adjustment
with
CO
meter
Refer
to
Carburetor
Idle
rpm
and
Mixture
Ratio
Section
ET
for
check
ing
and
a
justment
CO
idle
adjustment
without
CO
meter
Non
California
models
Refer
to
Carburetor
Idle
rpm
and
Mixture
Ratio
Section
ETl
fot
check
ing
and
adjustment
Idle
limiter
cap
Refer
to
Idle
Limiter
Cap
SeCtio
ET
for
checking
and
adjustment
FUEL
LEVEL
I
With
engine
idling
visually
check
fuel
level
through
sight
window
of
float
chamber
Fuel
level
is
correct
if
it
is
at
the
indicator
point
Note
Fuel
level
indicator
point
is
located
IS
mm
0
59
in
below
top
of
carburetor
body
H
as
shown
in
Figure
below
Engine
Fuel
EF088A
Fig
EF
33
Checking
Fuel
Level
To
adjust
fuel
level
proceed
as
follows
2
Remove
choke
chamber
3
Turn
down
choke
chamber
to
allow
float
to
come
into
contact
with
needle
valve
and
measure
H
shown
below
When
H
is
approximately
15
mm
0
59
in
top
float
position
is
correct
The
top
float
position
can
be
ad
justed
by
bending
float
seat
Upon
completion
of
the
adjust
ment
check
fuel
level
with
attached
level
gauge
nhH
J
1
Float
2
Float
stopper
3
Float
seat
4
Needle
valve
Fig
EF
34
Adjusting
Floot
Level
EF
14
4
Adjust
bottom
float
position
so
that
clearance
hl
between
float
seat
and
needle
valve
stem
is
1
3
to
I
7
mm
0
051
to
0
067
in
when
float
is
fully
raised
Bend
float
stopper
as
required
5
Install
choke
chamber
6
After
adjustments
in
steps
3
and
4
above
have
been
made
make
sure
that
when
fuel
is
delivered
to
the
float
chamber
the
fuel
level
is
maintained
within
the
specified
value
H