lock DATSUN PICK-UP 1977 Service Manual
[x] Cancel search | Manufacturer: DATSUN, Model Year: 1977, Model line: PICK-UP, Model: DATSUN PICK-UP 1977Pages: 537, PDF Size: 35.48 MB
Page 411 of 537
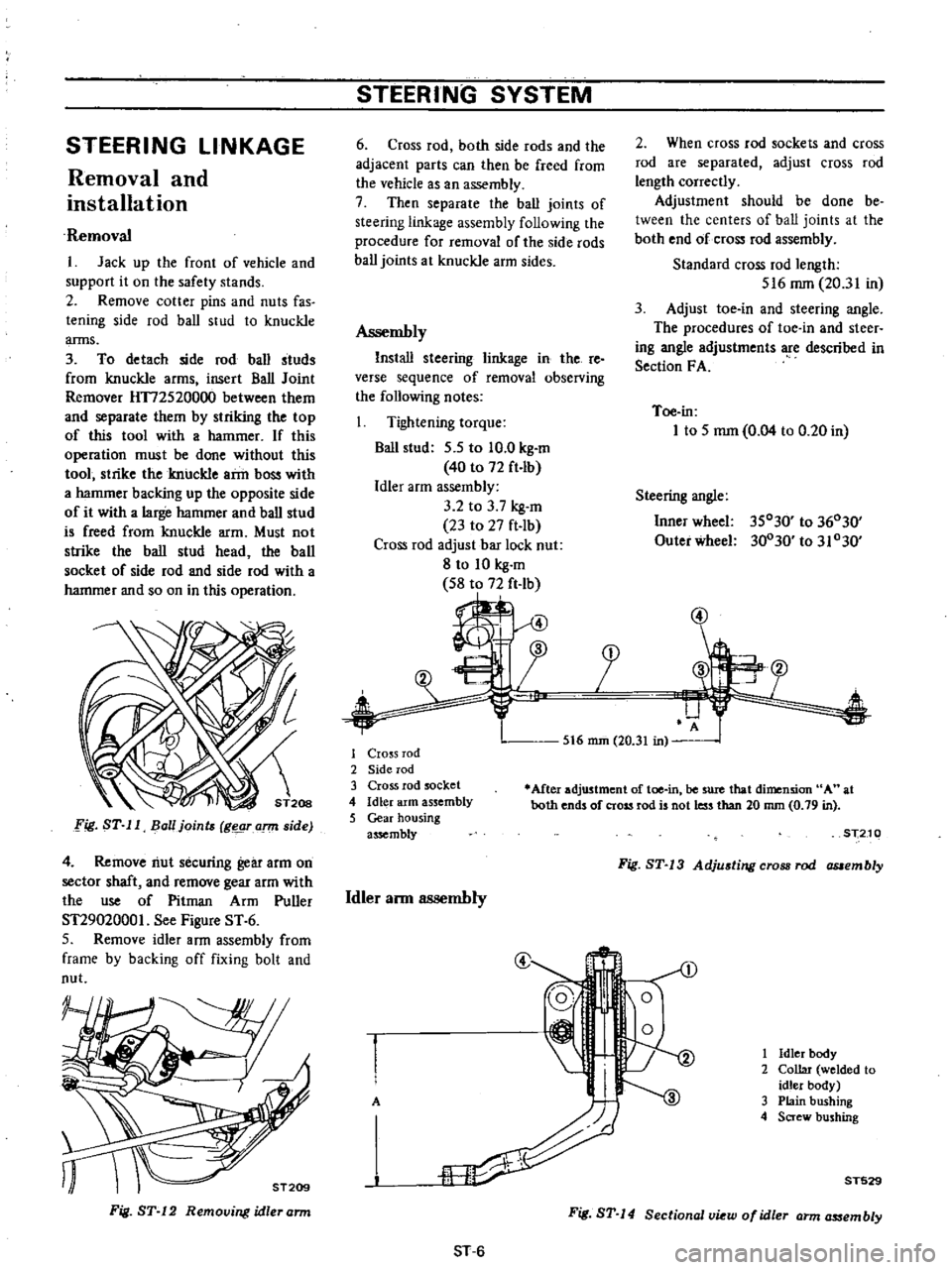
STEERING
LINKAGE
Removal
and
installation
Removal
I
Jack
up
the
front
of
vehicle
and
support
it
on
the
safety
stands
2
Remove
cotter
pins
and
nuts
fas
tening
side
rod
ball
stud
to
knuckle
arms
3
To
detach
side
rod
ball
studs
from
knuckle
arms
insert
Ball
Joint
Remover
HT72520000
between
them
and
separate
them
by
striking
the
top
of
this
tool
with
a
hammer
If
this
operation
must
be
done
without
this
tool
strike
the
knuckle
arm
boss
with
a
hammer
backing
up
the
opposite
side
of
it
with
a
large
hammer
and
bail
stud
is
freed
from
knuckle
arm
Must
not
strike
the
baIl
stud
head
the
ball
socket
of
side
rod
and
side
rod
with
a
hammer
and
so
on
in
this
operation
Fig
ST
11
Ball
joints
Ic
ann
side
4
Remove
riut
securing
gear
armOD
sector
shaft
and
remove
gear
arm
with
the
use
of
Pitman
Arm
Puller
ST29020001
See
Figure
ST
6
S
Remove
idler
arm
assembly
from
frame
by
backing
off
fixing
bolt
and
nut
Ffa
ST
12
Removing
idler
ann
STEERING
SYSTEM
6
Cross
rod
both
side
rods
and
the
adjacent
parts
can
then
be
freed
from
the
vehicle
as
an
assembly
7
Then
separate
the
ball
joints
of
steering
linkage
assembly
following
the
procedure
for
removal
of
the
side
rods
ball
joints
at
knuckle
arm
sides
Assembly
Install
steering
linkage
in
the
reo
verse
sequence
of
removal
observing
the
following
notes
Tightening
torque
Ball
stud
S
S
to
10
0
kg
m
40
to
72
ft
lb
Idler
arm
assembly
3
2
to
3
7
kg
m
23
to
27
ft
lb
Cross
rod
adjust
bar
lock
nut
8
to
10
kg
m
72
fL
2
f
2
When
cross
rod
sockets
and
cross
rod
are
separated
adjust
cross
rod
length
correctly
Adjustment
should
be
done
be
tween
the
centers
of
ball
joints
at
the
both
end
of
cross
rod
assembly
Standard
cross
rod
length
516
rom
20
31
in
3
Adjust
toe
in
and
steering
angle
The
procedures
of
toe
in
and
steer
ing
angle
adjustments
Ie
described
in
Section
F
A
Toe
in
1
to
5
mm
0
04
to
0
20
in
Steering
angle
Inner
wheel
3S030
to
36030
Outer
wheel
30030
to
31030
5t6
mm
20
31
in
1
Cro
s
rod
2
Side
rod
3
Cross
rod
socket
4
Idler
arm
assembly
5
Gear
housing
assembly
Mter
adjustment
of
toe
in
be
sure
that
dimension
A
at
both
ends
of
cross
rod
is
not
less
than
20
nun
0
79
in
Idler
ann
assembly
ST210
Fig
ST
13
Adjusting
cross
rod
assembly
@
1
Idler
body
2
Collar
welded
to
idler
body
A
3
Plain
bushing
4
Screw
bushing
T529
ST
6
Fig
ST
14
Sectional
W
of
idler
arm
as
sembly
Page 412 of 537
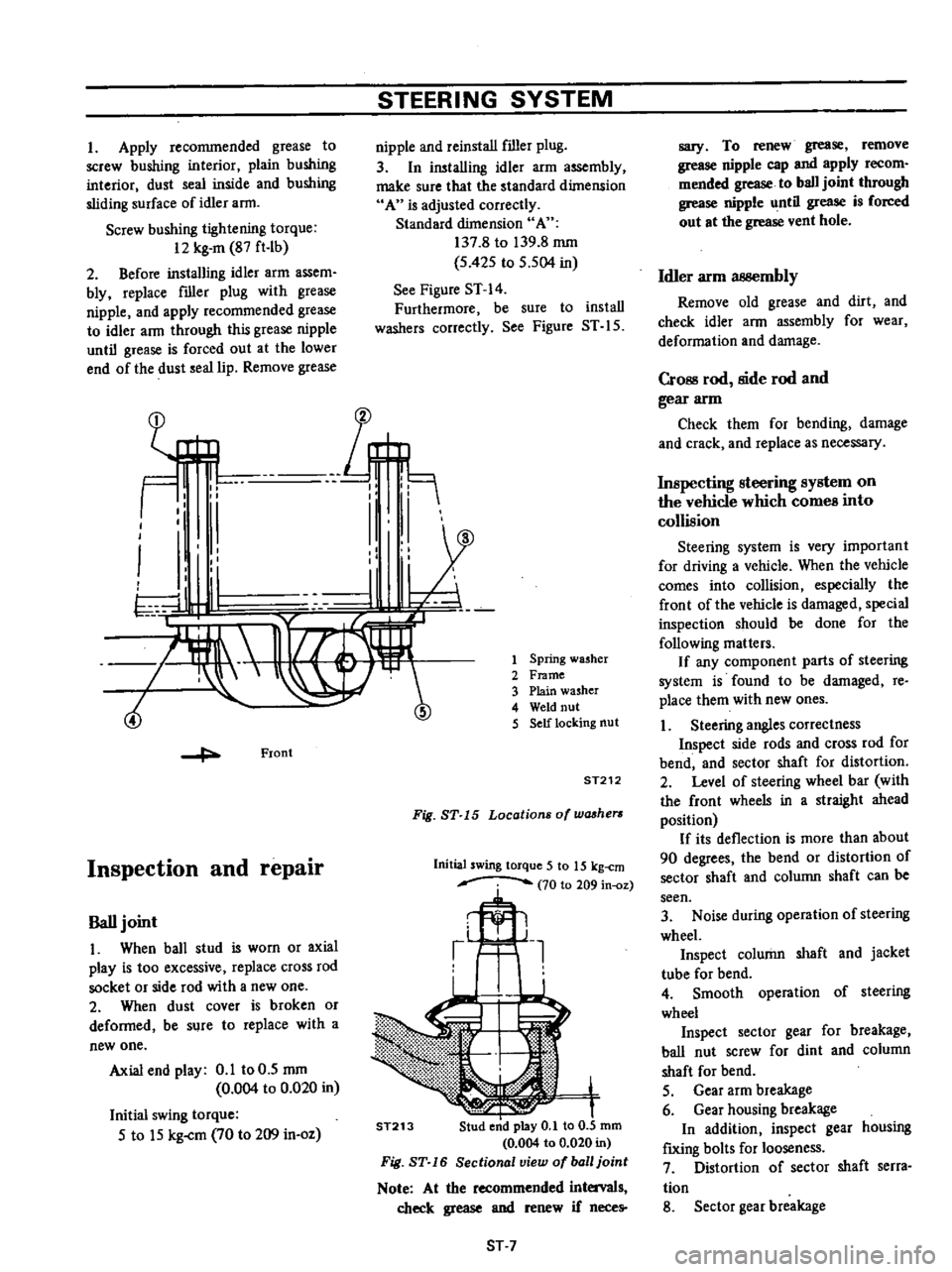
I
J
L6
3
4
5
1
Apply
recommended
grease
to
screw
bushing
interior
plain
bushing
interior
dust
seal
inside
and
bushing
sliding
surface
of
idler
ann
Screw
bushing
tightening
torque
12
kg
m
87
ft
lb
2
Before
installing
idler
arm
assem
bly
replace
f
iller
plug
with
grease
nipple
and
apply
recommended
grease
to
idler
ann
through
this
grease
nipple
until
grease
is
forced
out
at
the
lower
end
of
the
dust
seal
lip
Remove
grease
I
8
I
II
I
I
FIODt
Inspection
and
repair
Ball
joint
1
When
ball
stud
is
worn
or
axial
play
is
too
excessive
replace
cross
rod
socket
or
side
rod
with
a
new
one
2
When
dust
cover
is
broken
or
defonned
be
sure
to
replace
with
a
new
one
Axial
end
play
0
1
to
0
5
mm
0
004
to
0
020
in
Initial
swing
torque
S
to
15
kg
cm
70
to
209
in
oz
STEERING
SYSTEM
nipple
and
reinstall
filler
plug
3
In
installing
idler
arm
assembly
make
sure
that
the
standard
dimension
A
is
adjusted
correctly
Standard
dimension
A
137
8
to
139
8
mm
S
42S
to
S
504
in
See
Figure
ST
14
Furthermore
be
sure
to
install
washers
correctly
See
Figure
ST
IS
Spring
washer
Frame
Plain
washer
Weld
nut
Self
locking
nut
ST212
Fig
ST
15
Locations
of
washers
Initial
swing
torque
5
to
15
kg
cm
70
to
209
in
oz
ST213
ST
7
sary
To
renew
grease
remove
grease
nipple
cap
and
apply
recom
mended
grease
to
ball
joint
through
grease
nipple
until
grease
is
forced
out
at
the
grease
vent
hole
Idler
arm
3B8embly
Remove
old
grease
and
dirt
and
check
idler
ann
assembly
for
wear
deformation
and
damage
CrOBS
rod
side
rod
and
gear
arm
Check
them
for
bending
damage
and
crack
and
replace
as
necessary
Inspecting
steering
system
on
the
vehicle
which
comes
into
collision
Steering
system
is
very
important
for
driving
a
vehicle
When
the
vehicle
comes
into
collision
especially
the
front
of
the
vehicle
is
damaged
special
inspection
should
be
done
for
the
following
matters
If
any
component
parts
of
steering
system
is
found
to
be
damaged
re
place
them
with
new
ones
1
Steering
angles
correctness
Inspect
side
rods
and
cross
rod
for
bend
and
sector
shaft
for
distortion
2
Level
of
steering
wheel
bar
with
the
front
wheels
in
a
straight
ahead
position
If
its
deflection
is
more
than
about
90
degrees
the
bend
or
distortion
of
sector
shaft
and
column
shaft
can
be
seen
3
Noise
during
operation
of
steering
wheel
Inspect
column
shaft
and
jacket
tube
for
bend
4
Smooth
operation
of
steering
wheel
Inspect
sector
gear
for
breakage
ball
nut
screw
for
dint
and
column
shaft
for
bend
S
Gear
arm
breakage
6
Gear
housing
breakage
In
addition
inspect
gear
housing
f
IXing
bolts
for
looseness
7
Distortion
of
sector
shaft
serra
tion
8
Sector
gear
breakage
Page 413 of 537
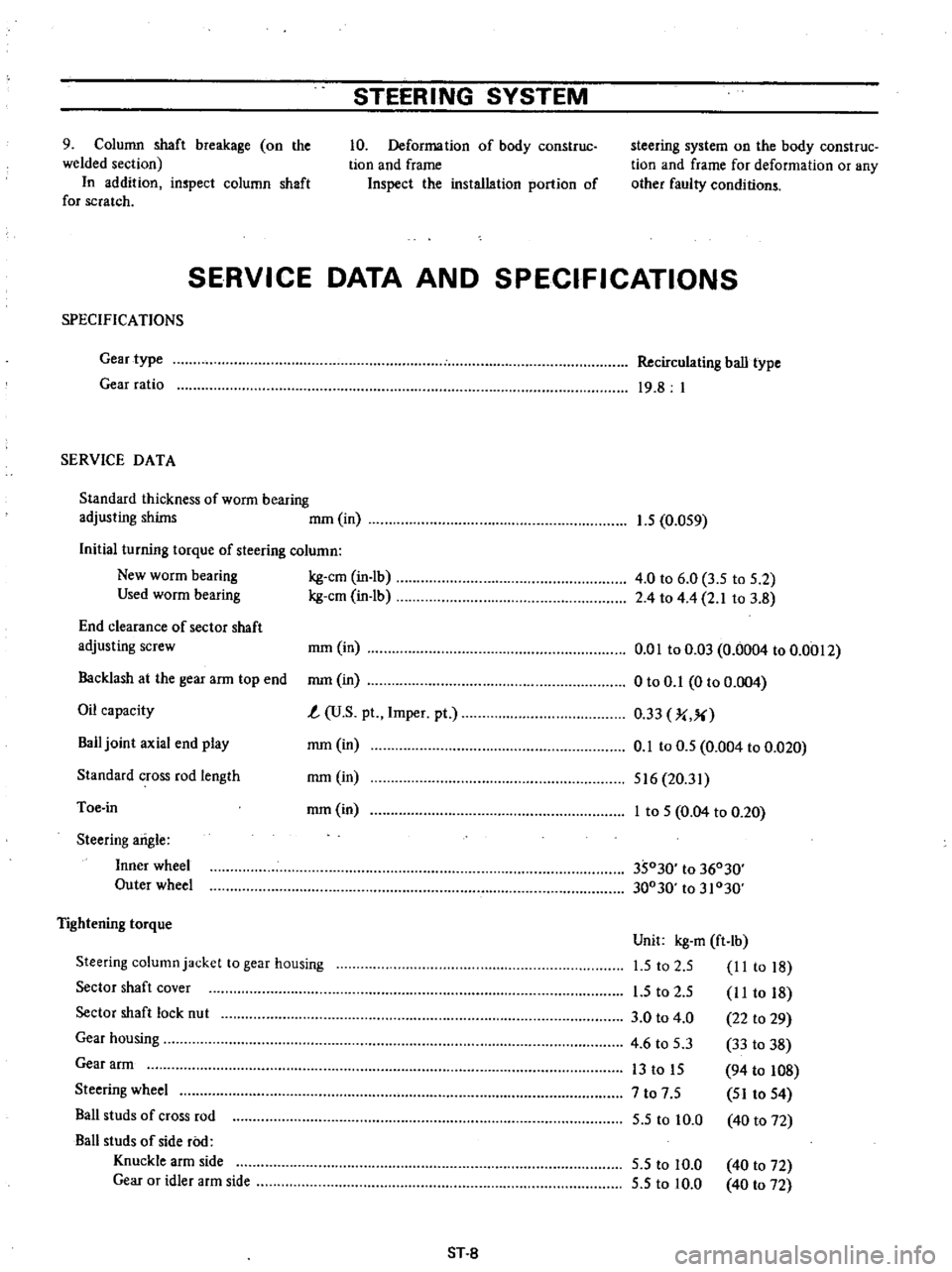
STEERING
SYSTEM
9
Column
shaft
breakage
on
the
welded
section
In
addition
inspect
column
shaft
for
scratch
10
Deformation
of
body
construc
tion
and
frame
Inspect
the
installation
portion
of
steering
system
on
the
body
construe
tion
and
frame
for
deformation
or
any
other
faulty
conditions
SERVICE
DATA
AND
SPECIFICATIONS
SPECIFICA
nONS
Gear
type
Gear
ratio
SERVICE
DATA
Standard
thickness
of
worm
bearing
adjusting
shims
mOl
in
Initial
turning
torque
of
steering
column
New
worm
bearing
kg
em
in
lb
Used
worm
bearing
kg
em
in
lb
End
clearance
of
sector
shaft
adjusting
screw
rom
in
Backlash
at
the
gear
arm
top
end
rom
in
Oil
capacity
t
U
S
pt
Impel
pt
Bail
joint
axial
end
play
rom
in
Standard
cross
rod
length
rom
in
Toe
in
rom
in
Steering
arigle
Inner
wheel
Outer
wheel
Tightening
torque
Steering
column
jacket
to
gear
housing
Sector
shaft
cover
Sector
shaft
lock
nut
Gear
housing
Gear
arm
Steering
wheel
Bail
studs
of
cross
rod
Ball
studs
of
side
roo
Knuckle
arm
side
Gear
or
idler
arm
side
ST
8
Recirculating
ball
type
19
8
I
1
5
0
OS9
4
0
to
6
0
3
5
to
S
2
2
4
to
4
4
2
1
to
3
8
om
to
0
03
0
0004
to
0
0012
o
to
0
1
0
to
0
004
0
33
J
X
0
1
to
0
5
0
004
to
0
020
516
20
31
I
to
S
0
04
to
0
20
35030
to
36030
30030
to
31030
Unit
kg
m
ft
lb
1
5
to
2
S
II
to
18
I
S
to
2
S
I
I
to
18
3
0
to
4
0
22
to
29
4
6
to
5
3
33
to
38
13
to
IS
94
to
108
7
to
7
S
SI
to
S4
S
S
to
10
0
40
to
72
S
S
to
10
0
S
5
to
10
0
40
to
72
40
to
72
Page 417 of 537
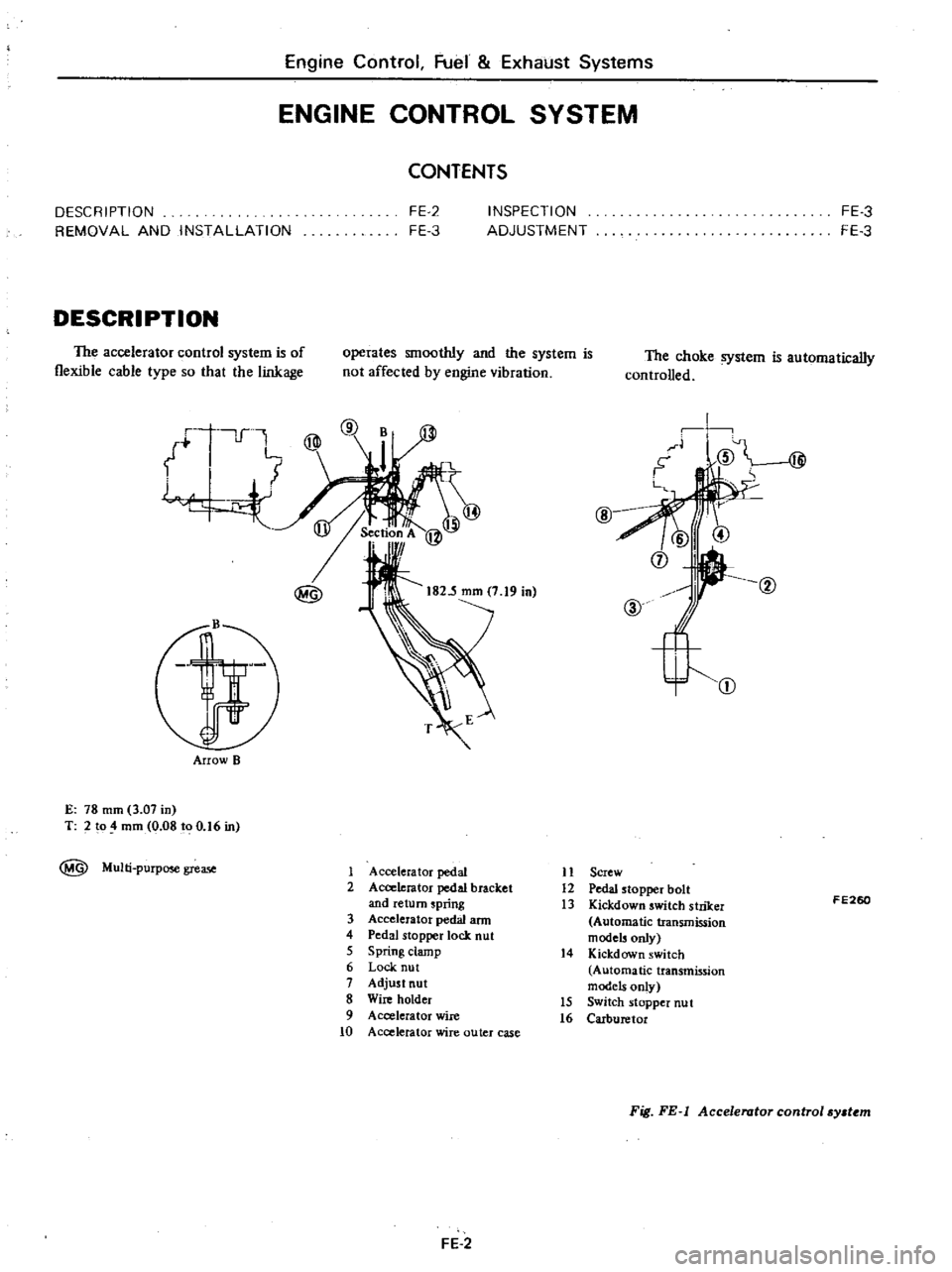
Engine
Control
Fuel
Exhaust
Systems
ENGINE
CONTROL
SYSTEM
CONTENTS
DESCRIPTION
REMOVAL
AND
INSTAllATION
INSPECTION
ADJUSTMENT
FE
2
FE
3
DESCRIPTION
The
accelerator
control
system
is
of
flexible
cable
type
so
that
the
linkage
operates
smoothly
and
the
system
is
not
affected
by
engine
vibration
u
l
f
L
4
@
Arrow
B
E
78
mm
3
07
in
T
2
to
4
mm
0
08
to
0
16
in
MUlti
purpose
grease
FE
3
FE
3
The
choke
system
is
automatically
controlled
i
p
@
I
@
@
CV
j
I
Accelerator
pedal
II
Screw
2
Accelerator
pedal
bracket
12
Pedal
stopper
bolt
and
return
spring
13
Kickdown
switch
striker
3
Accelerator
pedal
arm
Automatic
transmission
4
Pedal
stopper
lock
nut
models
only
5
S
pring
clamp
14
Kickdown
switch
6
Lock
nut
Automatic
transmission
7
Adjust
nut
models
only
8
Wire
holder
15
Switch
stopper
nu
t
9
Accelerator
wire
16
Carburetor
10
Accelerator
wire
outer
case
FE
2
FE260
Fig
FE
l
Accelerator
control
sy
t
m
Page 418 of 537
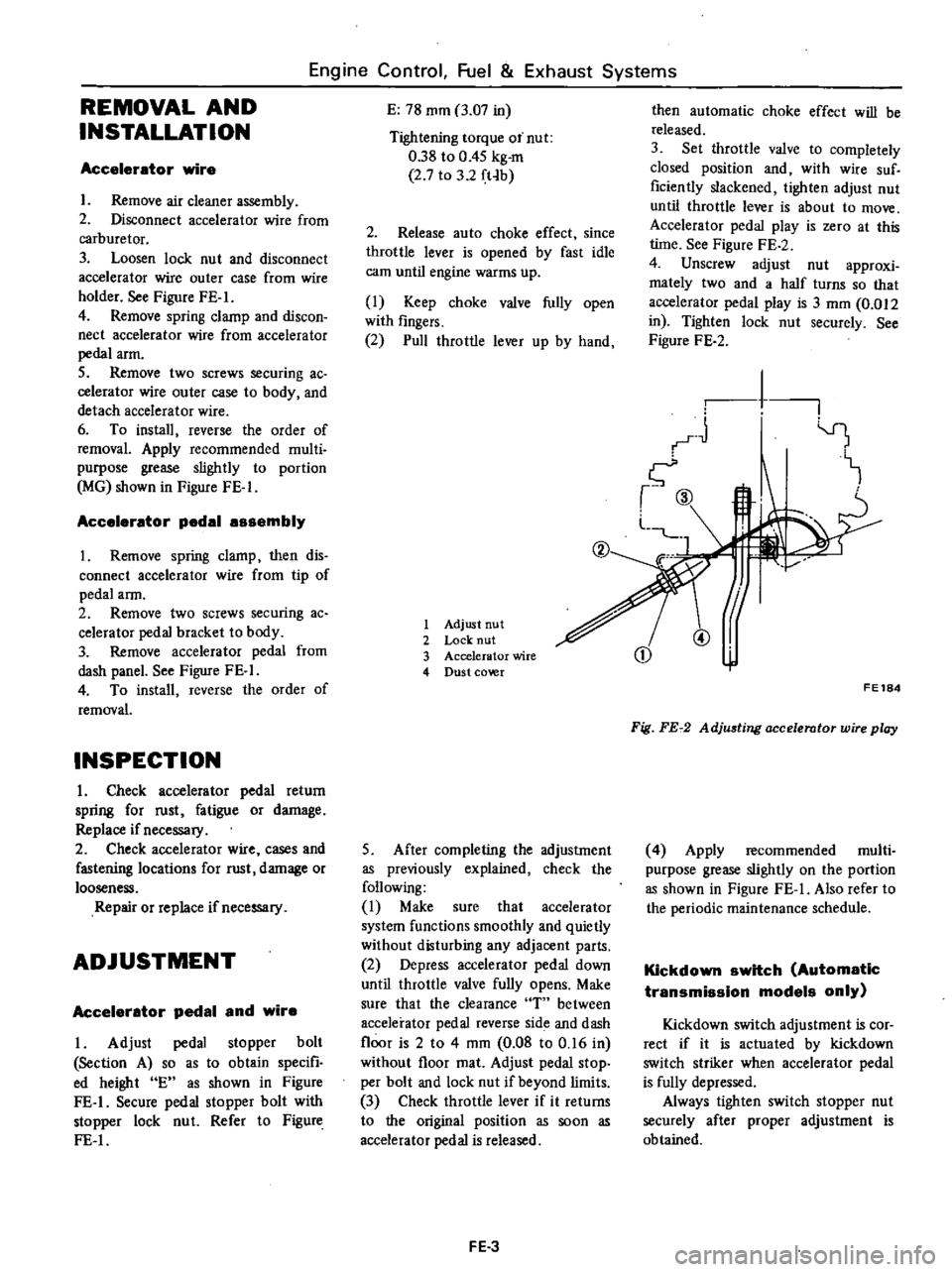
Engine
Control
Fuel
Exhaust
Systems
REMOVAL
AND
INSTALLATION
Accelerator
wire
I
Remove
air
cleaner
assembly
2
Disconnect
accelerator
wire
from
carburetor
3
Loosen
lock
nut
and
disconnect
accelerator
wire
outer
case
from
wire
holder
See
Figure
FE
I
4
Remove
spring
clamp
and
discon
nect
accelerator
wire
from
accelerator
pedal
arm
S
Remove
two
screws
securing
ac
celerator
wire
outer
case
to
body
and
detach
accelerator
wire
6
To
install
reverse
the
order
of
removal
Apply
recommended
multi
purpose
grease
slightly
to
portion
MG
shown
in
Figure
FE
I
Accelerator
pedal
assembly
I
Remove
spring
clamp
then
dis
connect
accelerator
wire
from
tip
of
pedal
ann
2
Remove
two
screws
securing
ac
celerator
pedal
bracket
to
body
3
Remove
accelerator
pedal
from
dash
panel
See
Figure
FE
I
4
To
install
reverse
the
order
of
removal
INSPECTION
I
Check
accelerator
pedal
return
spring
for
rust
fatigue
or
damage
Replace
if
necessary
2
Check
accelerator
wire
cases
and
fastening
locations
for
rust
damage
or
looseness
Repair
or
replace
if
necessary
ADJUSTMENT
Accelerstor
pedal
and
wire
Adjust
pedal
stopper
bolt
Section
A
so
as
to
obtain
specifi
ed
height
E
as
shown
in
Figure
FE
I
Secure
pedal
stopper
bolt
with
stopper
lock
nut
Refer
to
Figure
FE
I
E
78
mOl
3
07
in
Tightening
torque
01
nut
0
38
to
0
4S
kg
m
2
7
to
3
2
ft
b
2
Release
auto
choke
effect
since
throttle
lever
is
opened
by
fast
idle
earn
until
engine
warms
up
I
Keep
choke
valve
fully
open
with
fingers
2
Pull
throttle
lever
up
by
hand
1
Adjust
nut
2
Lock
nut
3
Accelerator
wire
4
Dust
co
r
5
After
completing
the
adjustment
as
previously
explained
check
the
following
I
Make
sure
that
accelerator
system
functions
smoothly
and
quietly
without
disturbing
any
adjacent
parts
2
Depress
accelerator
pedal
down
until
throttle
valve
fully
opens
Make
sure
that
the
clearance
T
between
accelerator
pedal
reverse
side
and
dash
floor
is
2
to
4
mm
0
08
to
0
16
in
without
floor
mat
Adjust
pedal
stop
per
bolt
and
lock
nut
if
beyond
limits
3
Check
throttle
lever
if
it
returns
to
the
original
position
as
soon
as
accelerator
pedal
is
released
FE
3
then
automatic
choke
effect
will
be
released
3
Set
throttle
valve
to
completely
closed
position
and
with
wire
suf
ficiently
slackened
lighten
adjust
nut
until
throttle
lever
is
about
to
move
Accelerator
pedal
play
is
zero
at
this
lime
See
Figure
FE
2
4
Unscrew
adjust
nut
approxi
mately
two
and
a
half
turns
so
that
accelerator
pedal
play
is
3
mOl
0
012
in
Tighten
lock
nut
securely
See
Figure
FE
2
1
I
1
CD
@
FE184
Fig
FE72
AdjU6ting
accelerator
wire
play
4
Apply
recommended
multi
purpose
grease
slightly
on
the
portion
as
shown
in
Figure
FE
I
Also
refer
to
the
periodic
maintenance
schedule
Kickdown
switch
Automatic
transmission
models
only
Kickdown
switch
adjustment
is
cor
rect
if
it
is
actuated
by
kickdown
switch
striker
when
accelerator
pedal
is
fully
depressed
Always
tighten
switch
stopper
nut
securely
after
proper
adjustment
is
obtained
Page 420 of 537
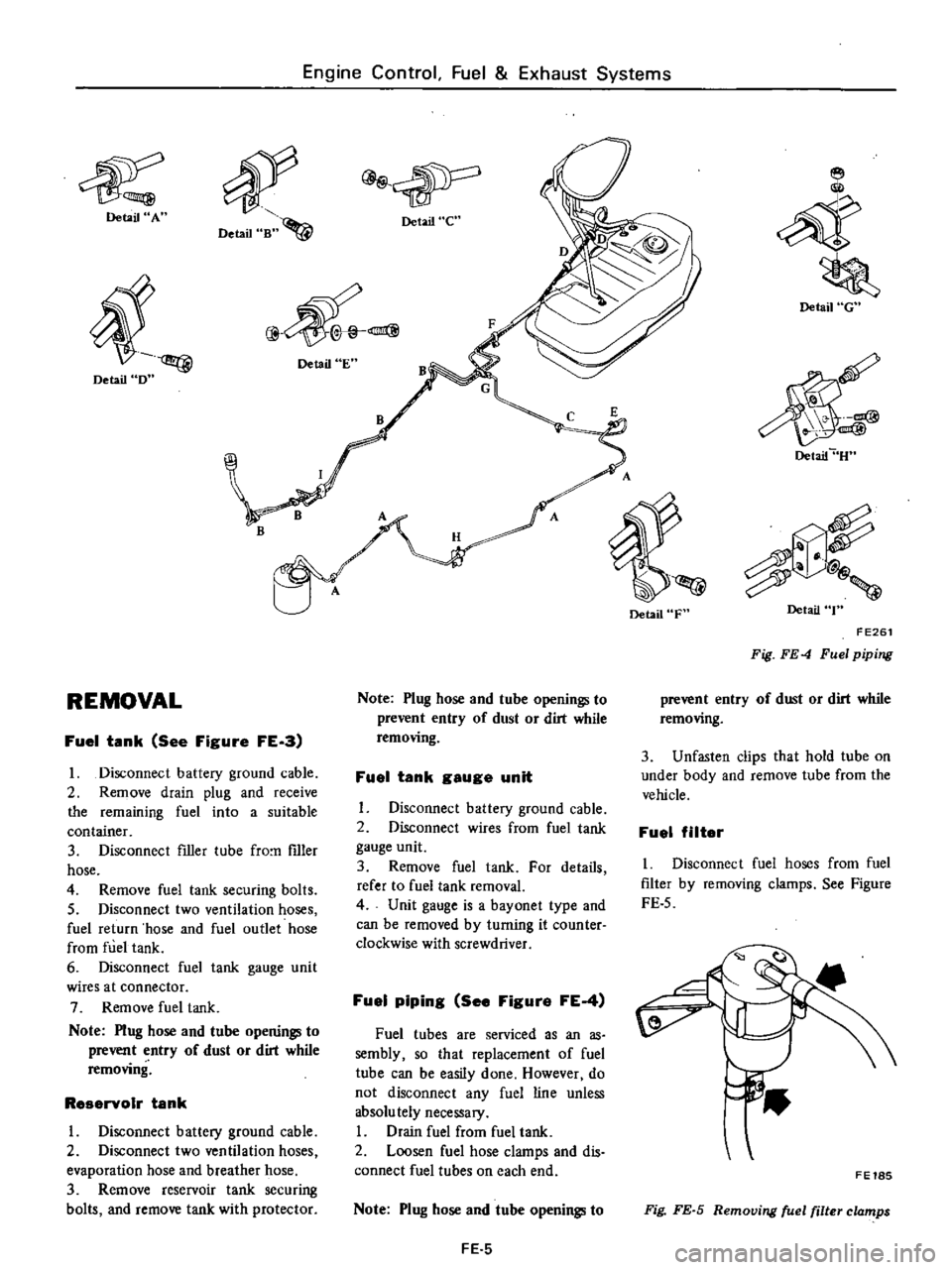
Detail
A
Detail
D
REMOVAL
Engine
Control
Fuel
Exhaust
Systems
Detail
Bn
4
Detail
e
@
Detail
E
B
Fuel
tank
See
Figure
FE
a
I
Disconnect
battery
ground
cable
2
Remove
drain
plug
and
receive
the
remaining
fuel
into
a
suitable
container
3
Disconnect
filler
tube
fro
filler
hose
4
Remove
fuel
tank
securing
bolts
5
Disconnect
two
ventilation
hoses
fuel
return
hose
and
fuel
outlet
hose
from
fuel
tank
6
Disconnect
fuel
tank
gauge
unit
wires
at
connector
7
Remove
fuel
tank
Note
Plug
hose
and
tube
opening
l
to
prevent
entry
of
dust
or
dirt
while
removing
ReservoIr
tank
1
Disconnect
battery
ground
cable
2
Disconnect
two
ventilation
hoses
evaporation
hose
and
breather
hose
3
Remove
reservoir
tank
securing
bolts
and
remove
tank
with
protector
Note
Plug
hose
and
tube
opening
l
to
prevent
entry
of
dust
or
dirt
while
removing
Fuel
tank
gauge
unit
Disconnect
battery
ground
cable
2
Disconnect
wires
from
fuel
tank
gauge
unit
3
Remove
fuel
tank
For
details
refer
to
fuel
tank
removal
4
Unit
gauge
is
a
bayonet
type
and
can
be
removed
by
turning
it
counter
clockwise
with
screwdriver
Fuel
piping
See
Figure
FE
4
Fuel
tubes
are
serviced
as
an
as
sembly
so
that
replacement
of
fuel
tube
can
be
easily
done
However
do
not
disconnect
any
fuel
line
unless
absolu
tely
necessary
I
Drain
fuel
from
fuel
tank
2
Loosen
fuel
hose
clamps
and
dis
connect
fuel
tubes
on
each
end
Note
Plug
hose
and
tube
openings
to
FE
5
Detail
F
Detail
G
Detail
U
Detail
T
FE261
Fig
FE
4
Fuel
piping
prevent
entry
of
dust
or
dirt
while
removing
3
Unfasten
clips
that
hold
tube
on
under
body
and
remove
tube
from
the
vehicle
Fuel
filter
I
Disconnect
fuel
hoses
from
fuel
filter
by
removing
clamps
See
Figure
FE
5
FE18S
Fig
FE
S
Removing
fuel
filter
clamps
Page 428 of 537
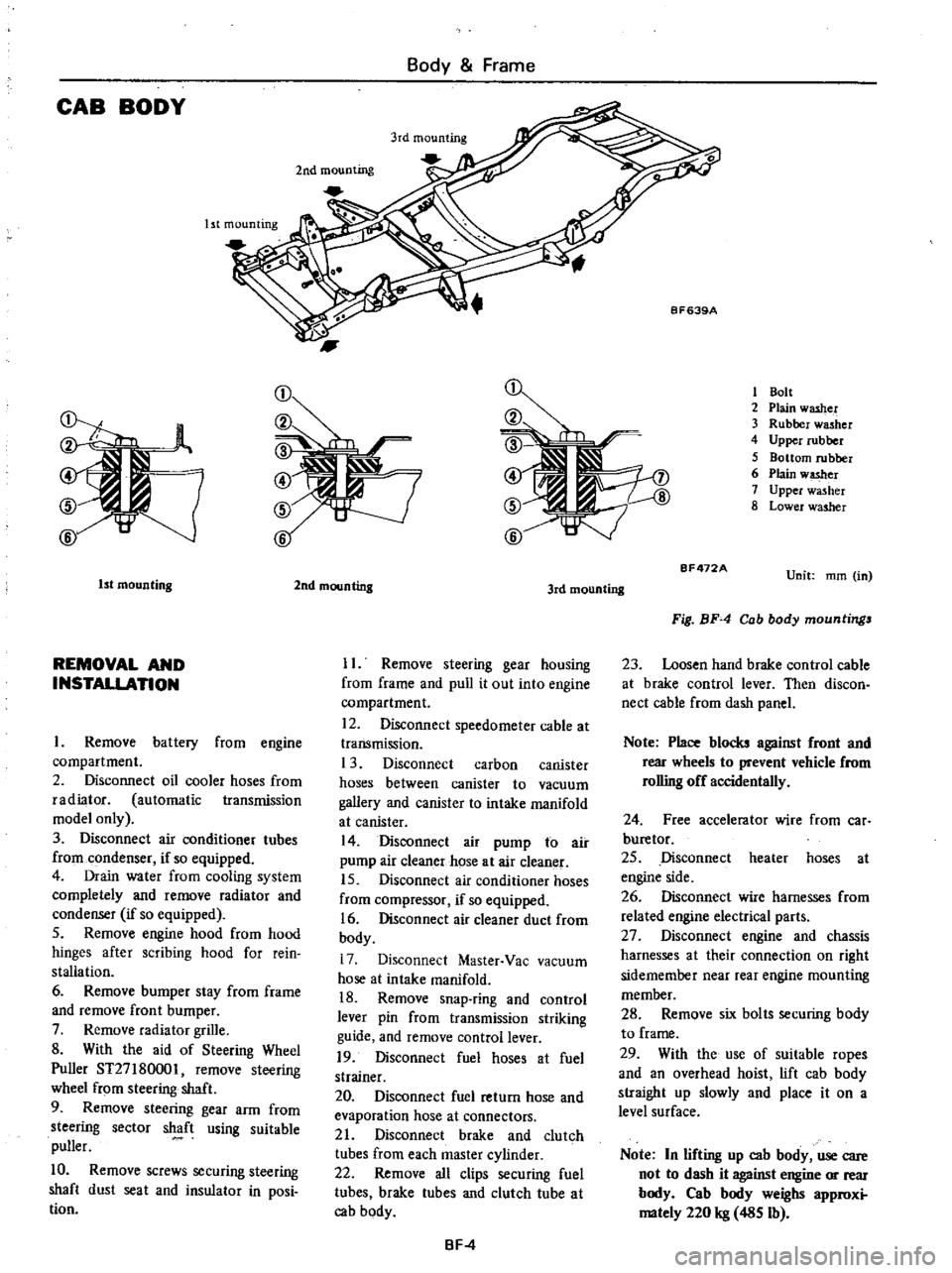
CAB
BODY
Body
Frame
Ist
mounting
2nd
mounting
1
Bolt
2
Plain
washer
3
Rubber
washer
4
Upper
rubber
5
Bottom
rubber
6
Plain
w
er
7
Upper
washer
8
Lower
washer
1st
mounting
REMOVAL
AND
INSTALLATION
Remove
battery
from
engine
compartment
2
Disconnect
oil
cooler
hoses
from
radiator
automatic
transmission
model
only
3
Disconnect
air
conditioner
tubes
from
condenser
if
so
equipped
4
Drain
water
from
cooling
system
completely
and
remove
radiator
and
condenser
if
so
equipped
5
Remove
engine
hood
from
hood
hinges
after
scribing
hood
for
rein
stallation
6
Remove
bumper
stay
from
frame
and
remove
front
bumper
7
Remove
radiator
grille
8
With
the
aid
of
Steering
Wheel
Puller
ST27
180001
remove
steering
wheel
from
steering
shaft
9
Remove
steering
gear
arm
from
steering
sector
shaft
using
suitable
puller
10
Remove
screws
securing
steering
shaft
dust
seat
and
insulator
in
posi
tion
2nd
mounting
3rd
mounting
II
Remove
steering
gear
housing
from
frame
and
pull
it
out
into
engine
compartment
12
Disconnect
speedometer
cable
at
transmission
1
3
Disconnect
carbon
canister
hoses
between
canister
to
vacuum
gallery
and
canister
to
intake
manifold
at
canister
14
Disconnect
air
pump
to
air
pump
air
cleaner
hose
at
air
cleaner
15
Disconnect
air
conditioner
hoses
from
compressor
if
so
equipped
16
Disconnect
air
cleaner
duct
from
body
17
Disconnect
Master
Vac
vacuum
hose
at
intake
manifold
18
Remove
snap
ring
and
control
lever
pin
from
transmission
striking
guide
and
remove
control
lever
19
Disconnect
fuel
hoses
at
fuel
strainer
20
Disconnect
fuel
return
hose
and
evaporation
hose
at
connectors
21
Disconnect
brake
and
clutch
tubes
from
each
master
cylinder
22
Remove
all
clips
securing
fuel
tubes
brake
tubes
and
clutch
tube
at
cab
body
BF
4
BF472A
Unit
mm
in
Fig
BF
4
Cab
body
mountings
23
Loosen
hand
brake
control
cable
at
brake
control
lever
Then
discon
nect
cable
from
dash
panel
Note
Place
blocks
against
front
and
rear
wheels
to
prevent
vehicle
from
rolling
off
accidentally
24
Free
accelerator
wire
from
car
buretor
25
Disconnect
heater
hoses
at
engine
side
26
Disconnect
wire
harnesses
from
related
engine
electrical
parts
27
Disconnect
engine
and
chassis
harnesses
at
their
connection
on
right
sidemember
near
rear
engine
mounting
member
28
Remove
six
bolts
securing
body
to
frame
29
With
the
use
of
suitable
ropes
and
an
overhead
hoist
lift
cab
body
straight
up
slowly
and
place
it
on
a
level
surface
Note
In
lifting
up
cab
body
use
care
not
to
dash
it
against
engine
or
rear
body
Cab
body
weighs
approxi
mately
220
kg
485
Ib
Page 432 of 537
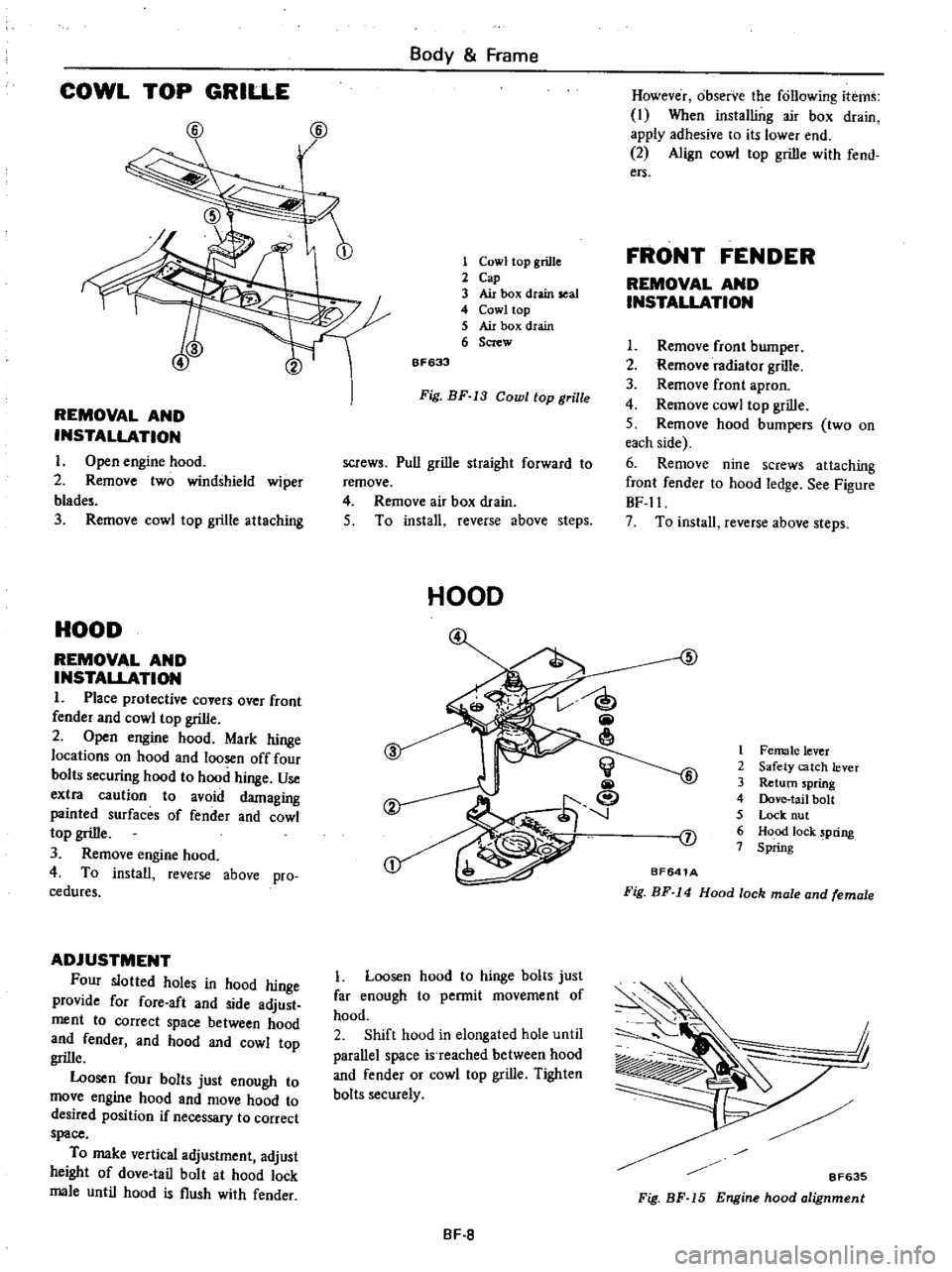
COWL
TOP
GRILLE
@
@
REMOVAL
AND
INSTALLATION
I
Open
engine
hood
2
Remove
two
windshield
wiper
blad
3
Remove
cowl
top
grille
attaching
HOOD
REMOVAL
AND
INSTALLATION
1
Place
protective
covers
over
front
fender
and
cowl
top
grille
2
Open
engine
hood
Mark
hinge
locations
on
hood
and
loosen
off
four
bolts
securing
hood
to
hood
hinge
Use
extra
caution
to
avoid
damaging
painted
surfaces
of
fender
and
cowl
top
grille
3
Remove
engine
hood
4
To
install
reverse
above
pro
cedures
ADJUSTMENT
Four
slotted
holes
in
hood
hinge
provide
for
fore
aft
and
side
adjust
ment
to
correct
space
between
hood
and
fender
and
hood
and
cowl
top
grille
Loosen
four
bolts
just
enough
to
move
engine
hood
and
move
hood
to
desired
position
if
necessary
to
correct
space
To
make
vertical
adjustment
adjust
height
of
dove
tail
bolt
at
hood
lock
male
until
hood
is
flush
with
fender
Body
Frame
1
Cowl
top
grille
2
Cap
3
Air
box
dtain
seal
4
Cowl
top
5
Air
box
drain
6
Screw
6F633
Fig
BF
13
Cowl
top
grille
screws
Pull
grille
straight
forward
to
remove
4
Remove
air
box
drain
5
To
install
reverse
above
steps
HOOD
Loosen
hood
to
hinge
bolts
just
far
enough
to
permit
movement
of
hood
2
Shift
hood
in
elongated
hole
until
parallel
space
is
reached
between
hood
and
fender
or
cowl
top
grille
Tighten
bolts
securely
BF
8
However
observe
the
following
items
I
When
installing
air
box
drain
apply
adhesive
to
its
lower
end
2
Align
cowl
top
grille
with
fend
ers
FRONT
FENDER
REMOVAL
AND
INSTALLATION
I
Remove
front
bumper
2
Remove
radiator
grille
3
Remove
front
apron
4
Remove
cowl
top
grille
S
Remove
hood
bumpers
two
on
each
side
6
Remove
nine
screws
attaching
front
fender
to
hood
ledge
See
Figure
BF
ll
7
To
install
reverse
above
steps
5
1
Female
lever
2
Safety
catch
lever
3
Return
spring
4
Dove
tail
bolt
S
Lock
nut
6
Hood
lock
pring
7
Spring
J
BF641A
Fig
BF
14
Hood
lock
male
and
female
j
I
8F635
Fig
BF
15
Engine
hood
alignment
Page 433 of 537
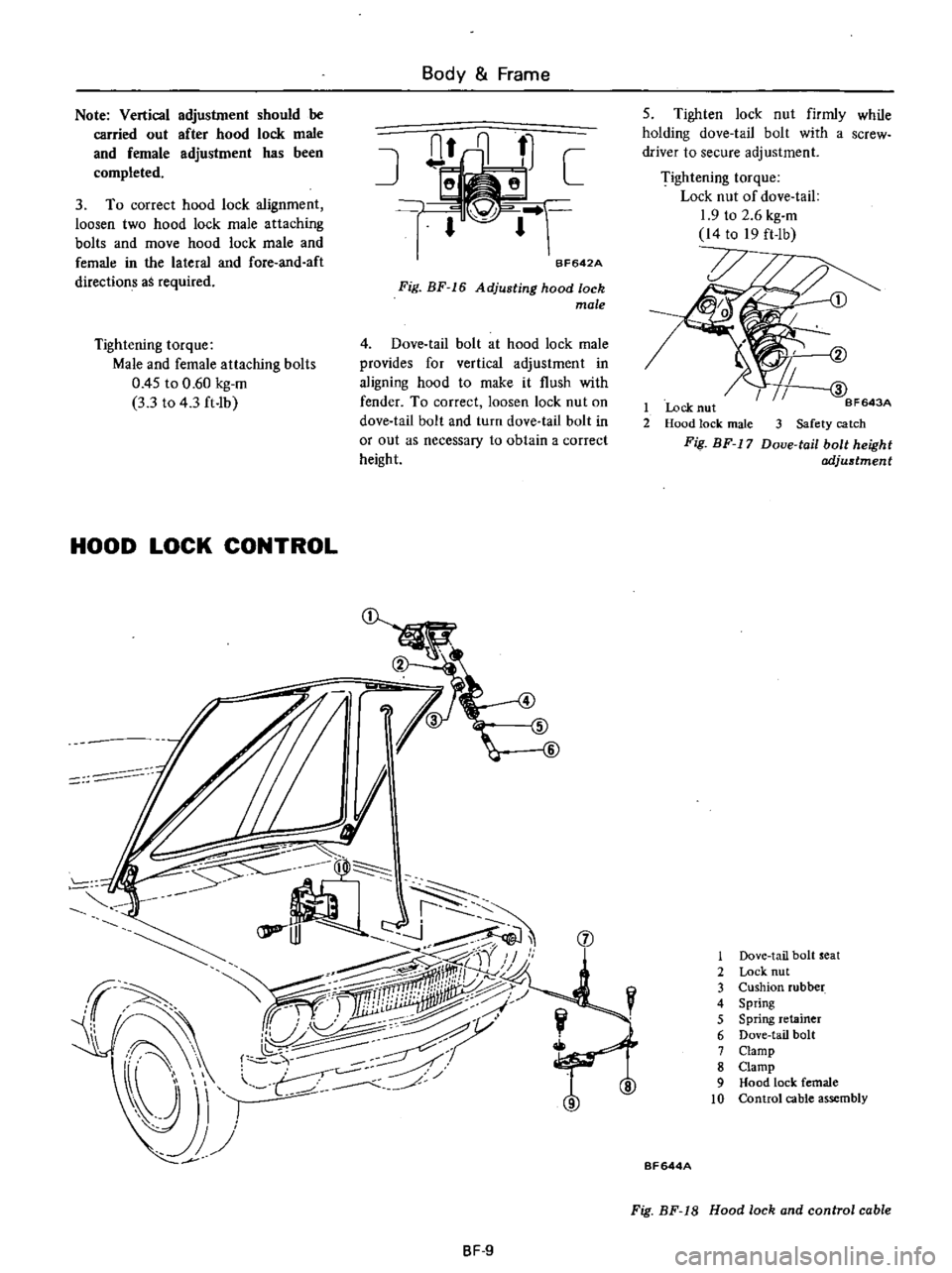
Body
Frame
Note
Vertical
adjustment
should
be
carried
out
after
hood
lock
male
and
female
adjustment
has
been
completed
3
To
correct
hood
lock
alignment
loosen
two
hood
lock
male
attaching
bolts
and
move
hood
lock
male
and
female
in
the
lateral
and
fore
and
aft
directions
as
required
D
1r
r
BF642A
Fig
BF
16
Adjusting
hood
lock
male
Tightening
torque
Male
and
female
attaching
bolts
0
45
to
0
60
kg
m
3
3
to
4
3
ft
Ib
4
Dove
tail
bolt
at
hood
lock
male
provides
for
vertical
adjustment
in
aligning
hood
to
make
it
flush
with
fender
To
correct
loosen
lock
nut
on
dove
tail
bolt
and
turn
dove
tail
bolt
in
or
out
as
necessary
to
obtain
a
correct
height
HOOD
LOCK
CONTROL
JI
I
i
I
r
lPP
J
jJ
J
Sr
aj
I
I
I
J
f
ifry
ff
I
ii1iiilliii
j
iW
r
U
I
j
Y
f
7
j
1
JJ
J
8F
9
5
Tighten
lock
nut
firmly
while
holding
dove
tail
bolt
with
a
screw
driver
to
secure
adjustment
Tightening
torque
Lock
nut
of
dove
tail
1
9
to
2
6
kg
m
14
to
19
ft
lb
BF643A
1
Lock
nut
2
Hood
lock
male
3
Safety
catch
Fig
BF
17
Doue
tail
bolt
height
adjustment
1
Dove
tail
bolt
seat
2
Lock
nut
3
Cushion
rubber
4
Spring
5
Spring
retainer
6
Dove
tail
bolt
7
Clamp
8
Clamp
9
Hood
lock
female
10
Control
cable
assembly
BF644A
Fig
BF
18
Hood
lock
and
control
cable
Page 434 of 537
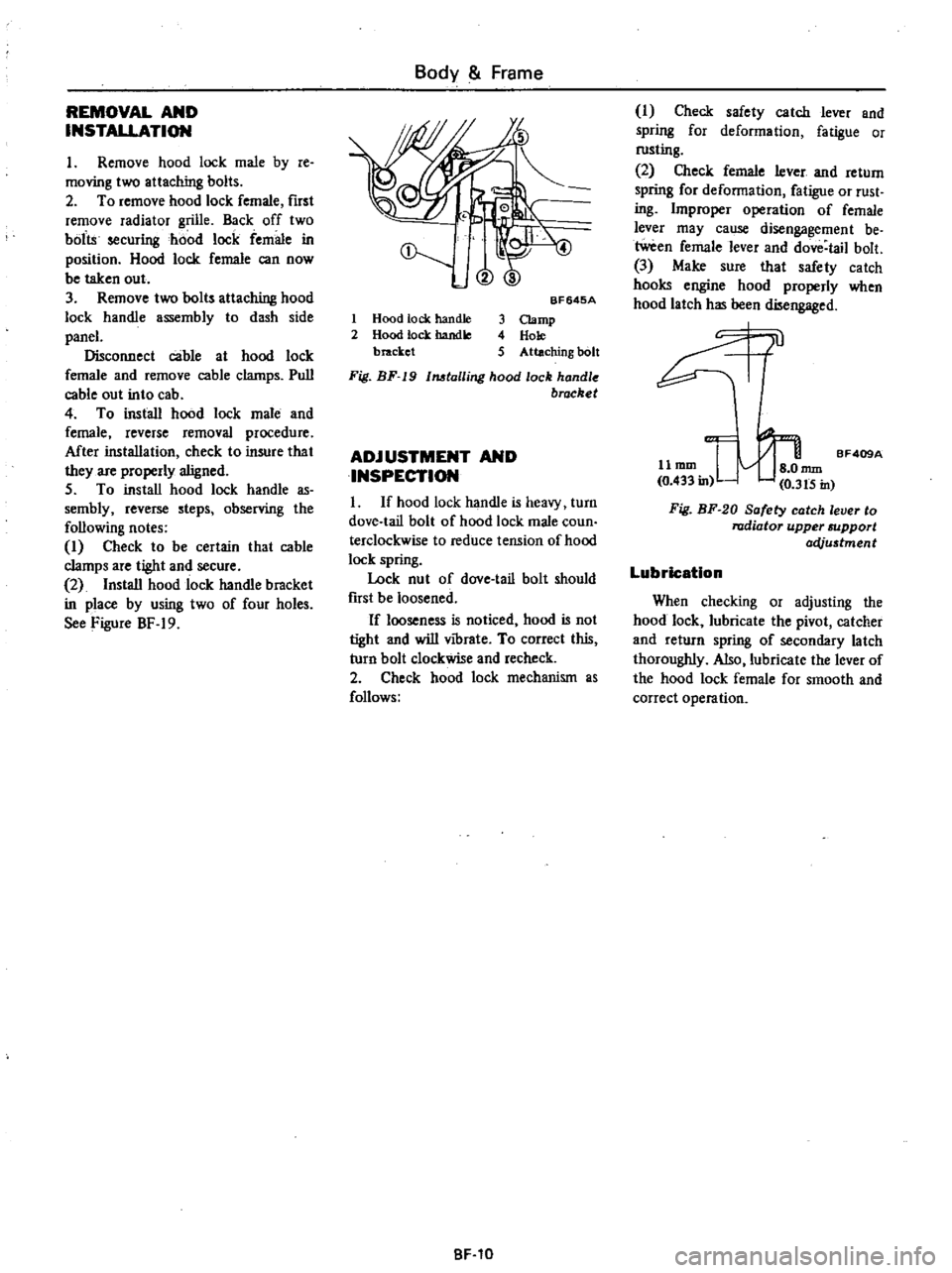
REMOVAL
AND
INSTALLATION
I
Remove
hood
lock
male
by
re
moving
two
attaching
bolts
2
To
remove
hood
lock
female
first
remove
radiator
grille
Back
off
two
bolts
securing
hood
lock
female
in
position
Hood
lock
female
can
now
be
taken
out
3
Remove
two
bolts
attaching
hood
lock
handle
assembly
to
dash
side
paneL
Disconnect
cable
at
hood
lock
female
and
remove
cable
clamps
Pull
cable
out
into
cab
4
To
install
hood
lock
male
and
female
reverse
removal
procedure
Mter
installation
check
to
insure
that
they
are
properly
aligned
5
To
install
hood
lock
handle
as
sembly
reverse
steps
observing
the
following
notes
I
Check
to
be
certain
that
cable
clamps
are
tight
and
secure
2
Install
hood
lock
handle
bracket
in
place
by
using
two
of
four
holes
See
Figure
BF
19
Body
Frame
@
1
Hood
tock
handle
2
Hood
lock
handle
bracket
BF645A
3
Clamp
4
Hole
5
Attaching
bolt
Fig
BF
19
1MtalIing
hood
lock
handle
brocket
ADJUSTMENT
AND
INSPECTION
I
If
hood
lock
handle
is
heavy
turn
dove
tail
bolt
of
hood
lock
male
coun
terclockwise
to
reduce
tension
of
hood
lock
spring
Lock
nut
of
dove
tail
bolt
should
fust
be
loosened
If
looseness
is
noticed
hood
is
not
tight
and
will
vibrate
To
correct
this
turn
bolt
clockwise
and
recheck
2
Check
hood
lock
mechanism
as
follows
BF
10
I
Check
safety
catch
lever
and
spring
for
deformation
fatigue
or
rusting
2
Check
female
lever
and
return
spring
for
deformation
fatigue
or
rust
ing
Improper
operation
of
female
lever
may
cause
disengagement
be
tween
female
lever
and
dove
tail
bolt
3
Make
sure
that
safety
catch
hooks
engine
hood
properly
when
hood
latch
has
been
disengaged
0l
11
mm
I
nun
BF409A
0
433
in
0
3t5
in
Fig
BF
20
Safety
catch
lever
to
radiator
upper
support
acVu5tment
Lubrication
When
checking
or
adjusting
the
hood
lock
lubricate
the
pivot
catcher
and
return
spring
of
secondary
latch
thoroughly
Also
lubricate
the
lever
of
the
hood
lock
female
for
smooth
and
correct
operation