lock DATSUN PICK-UP 1977 Service Manual
[x] Cancel search | Manufacturer: DATSUN, Model Year: 1977, Model line: PICK-UP, Model: DATSUN PICK-UP 1977Pages: 537, PDF Size: 35.48 MB
Page 304 of 537
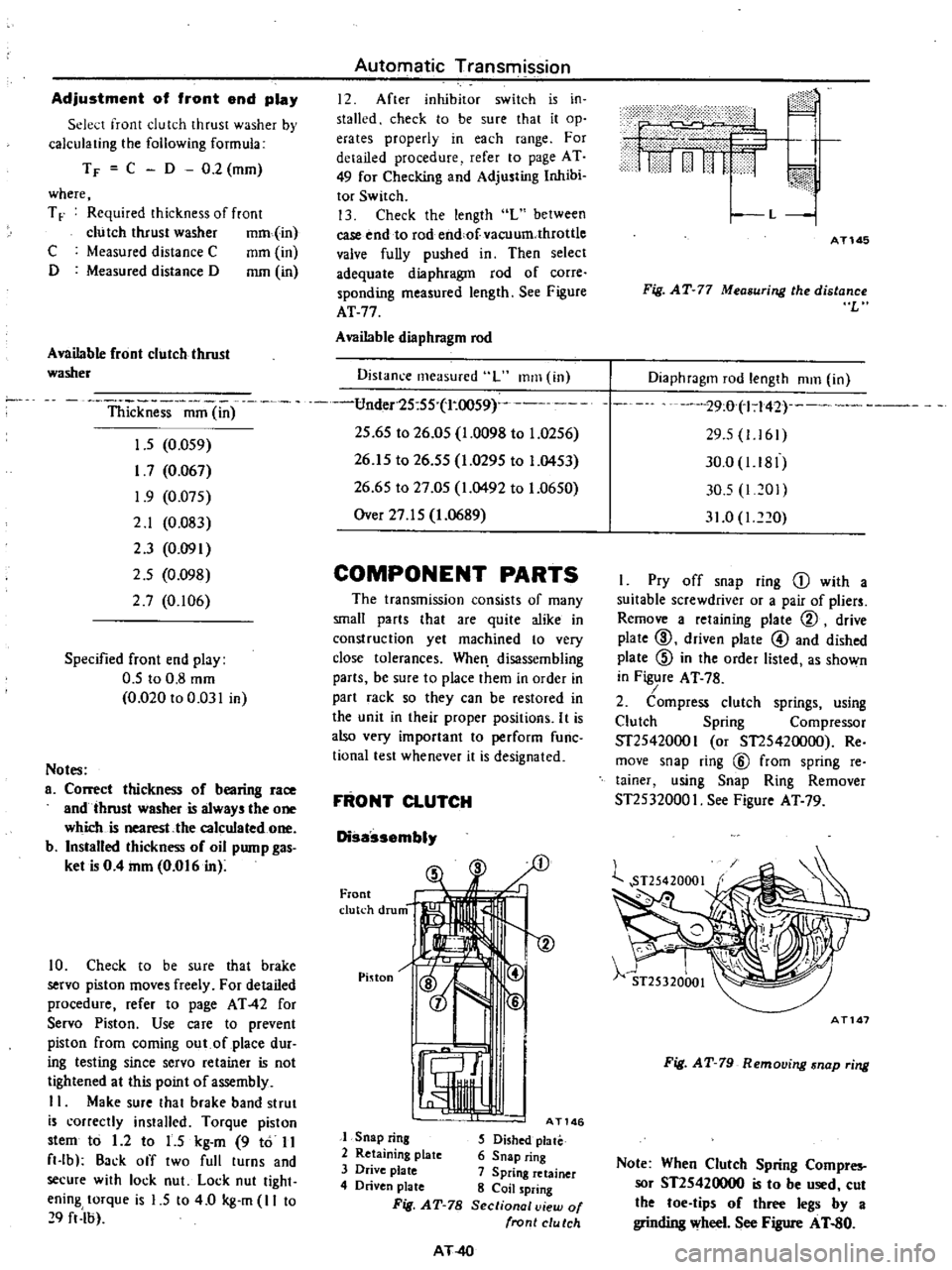
Adjustment
of
front
end
play
Sele
t
front
dutch
thrust
washer
by
calculating
the
following
formula
T
F
C
D
0
2
mm
where
T
F
Required
thickness
of
front
clutch
thrust
washer
mm
in
C
Measured
distance
C
mm
in
D
Measured
distance
D
mm
in
Available
front
clutch
thrust
washer
Thickness
mm
in
1
5
0
059
I
7
0
067
1
9
0
075
2
1
0
083
2
3
0
091
2
5
0
098
27
0
106
Specified
front
end
play
0
5
to
0
8
mm
0
020
to
0
031
in
Notes
a
Correct
thickness
of
bearing
race
and
thrust
washer
is
always
the
one
which
is
nearest
the
calculated
one
b
Installed
thickness
of
oil
pump
gas
ket
is
0
4
mm
0
016
in
10
Check
to
be
sure
that
brake
servo
piston
moves
freely
For
detailed
ptocedure
refer
to
page
AT
42
for
Servo
Piston
Use
care
to
prevent
piston
from
coming
out
of
place
dUI
ing
testing
since
servo
retainer
is
not
tightened
at
this
point
of
assembly
II
Make
sure
that
brake
band
strut
is
correctly
installcd
Torque
piston
stem
to
1
2
to
1
5
kg
m
9
to
11
f1
lb
Back
off
two
full
lurns
and
secure
with
lock
nut
Lock
nut
tight
ening
torque
is
1
5
to
4
0
kg
m
II
to
9
f1
lb
Automatic
Transmission
12
After
inhibitor
switch
is
in
stalled
check
to
be
sure
that
it
op
erates
properly
in
each
range
For
detailed
procedure
refer
to
page
AT
49
for
Checl
ing
and
Adjusting
Inhibi
tor
Switch
13
Check
the
length
L
between
case
end
to
rod
end
ofvacuum
throllle
valve
fully
pushed
in
Then
select
adequate
diaphragm
rod
of
corre
sponding
measured
length
See
Figure
AT
77
Available
diaphragm
rod
Distanl
e
measured
L
ITIm
in
Under25
55
l
OO59
25
65
to
26
05
1
0098
to
1
0256
26
15
to
26
55
1
0295
to
1
0453
26
65
to
27
05
1
0492
to
1
0650
Over
27
15
1
0689
COMPONENT
PARTS
The
transmission
cons
sts
of
many
small
parts
that
are
quite
alike
in
construction
yet
machined
to
very
close
tolerances
When
disassembling
parts
be
sure
to
place
them
in
order
in
part
rack
so
they
can
be
restored
in
the
unit
in
their
proper
positions
It
is
also
very
important
to
perform
func
tianal
test
whenever
it
is
designated
FRONT
CLUTCH
Disassembly
Front
clutch
drum
I
Pinon
lcz
t
AT146
1
Snap
ring
2
Retaining
plate
3
Drive
plate
4
Driven
plate
Fit
AT
78
S
Dished
plate
6
Snap
ring
7
Spring
retainer
8
Coil
spring
Sectional
view
of
front
clu
tch
AT
40
i
i
n
H
I
I
ni
c
A
i
iif
L
1
AT145
Fig
AT
77
Measuring
the
distance
L
Diaphragm
rod
length
mm
in
29
00
142
u
29
5
1161
30
0
1
81
30
5
1201
31
0
I
O
I
Pry
off
snap
ring
D
with
a
suitable
screwdriver
or
a
pair
of
pliers
Remove
a
retaining
plate
@
drive
plate
CID
driven
plate
@
and
dished
plate
@
in
the
order
listed
as
shown
in
Figure
AT
78
I
2
Compress
clutch
springs
using
Clutch
Spring
Compressor
ST25420001
or
51
25420000
Re
move
snap
ring
@
from
spring
re
tainer
using
Snap
Ring
Remover
ST2532000
I
See
Figure
AT
79
AT147
Fig
AT
79
Removing
snap
ring
Note
When
Clutch
Spring
Compres
sor
ST25420000
is
to
be
used
cut
the
toe
tips
of
three
legs
by
a
grinding
wheel
See
Figure
AT
80
Page 309 of 537
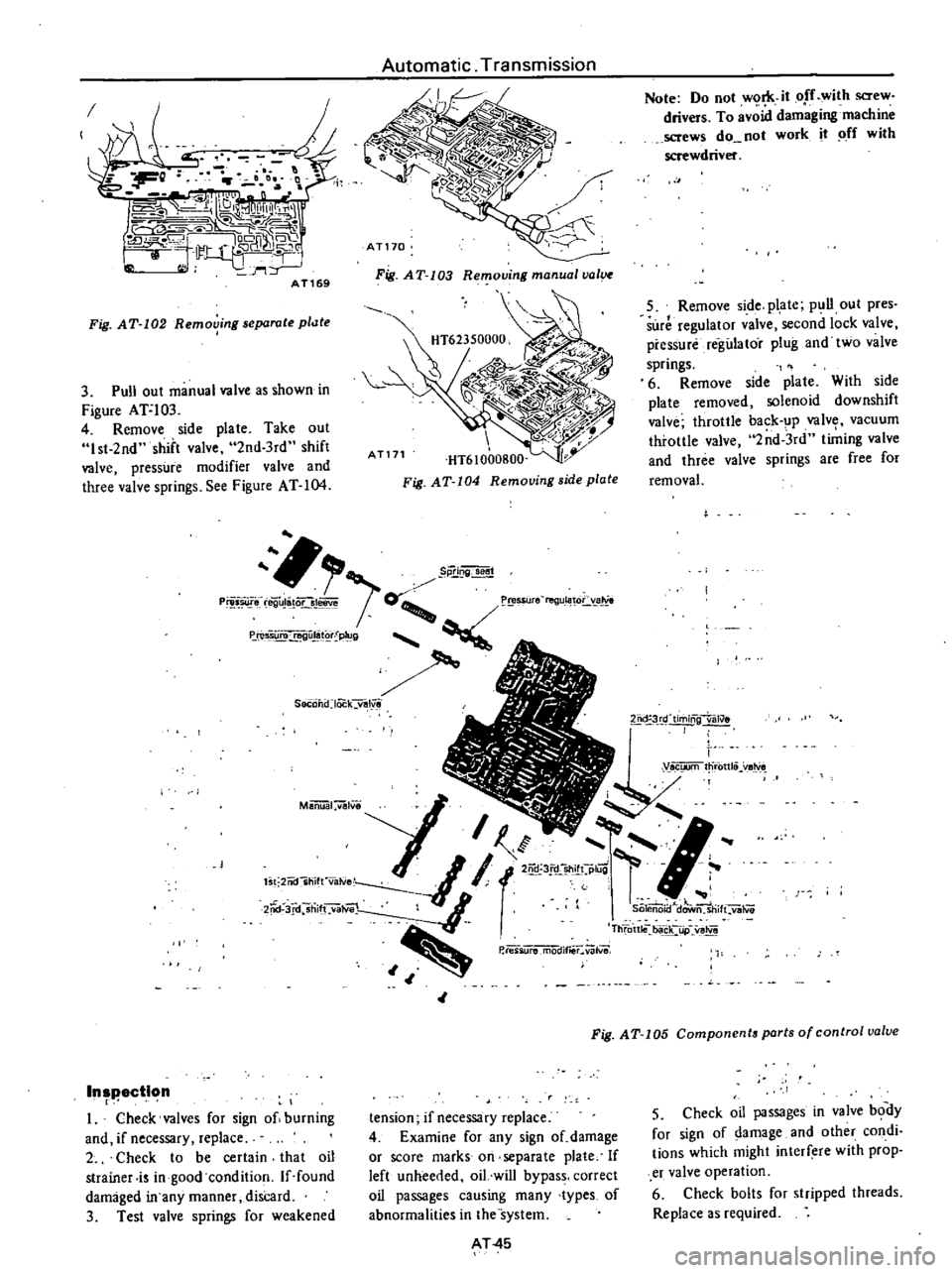
I
F
1
D
t
l
a
J
n
f
19l1
Ull
IU
P
C
o
J
CJ
IODrR
CC
t
LL6
SJQIl2J
lhl
fB
rt
AT169
Fig
AT
102
Removing
separate
pllJte
3
Pull
out
manual
valve
as
shown
in
Figure
Ar103
4
Remove
side
plate
Take
out
1st
2nd
shift
valve
2nd
3rd
shift
valve
pressure
modifier
valve
and
three
valve
springs
See
Figure
AT
104
Automatic
Transmission
Fig
AT
103
Removing
manual
val
AT1
1
HT61000800
Fig
AT
104
Removing
side
plate
g
p
e
eguJa
Of
le6Ve
or
r
essure
reguJl
oL
@iO
I
f
g
SecOni
J
lOCltvalYi
y
h
l
l
2I
r
JI
Io
J
l
j
t
1
i
S
r
0
x
t
i
3
1
Note
Do
not
w
it
off
with
screw
drivers
To
avoid
darnagingmachine
screws
do
not
work
it
ff
with
screwdriver
5
Remove
side
plate
pull
out
pres
sure
regulator
valve
second
lock
valve
pressure
regi1lator
plug
and
two
valve
springs
6
Remove
side
plate
With
side
plate
removed
solenoid
downshift
valve
throttle
back
up
valve
vacuum
throttle
valve
2
d
3rd
t
ing
valve
and
three
valve
springs
are
free
for
removal
2nd
3rd
timing
talve
r
en
i
C1iJrilth
rottle
lI
lY
e
M
a
alVSY
I
j1
f
I
1
f
Iv
I
f
2i
3
CP
g
f
st
2nd
S
t
a
el
2i1d
3
d
St1itLvalv
so
iit
a
stiift
V81v
i
hrottle
f
iicnjp
VB
y
i
P
ie
mo
i
Inspection
r
I
Check
valves
for
sign
of
burning
and
if
necessary
replace
2
Check
to
be
certain
that
oil
strainer
is
in
good
condition
If
found
damaged
in
any
manner
disCard
3
Test
valve
springs
for
weakened
Fig
AT
105
Components
ports
of
control
uolue
tension
if
necessary
replace
4
Examine
for
any
sign
oLdamage
or
score
marks
on
separate
plate
If
left
unheedcd
oiL
will
bypass
correct
oil
passages
causing
many
types
of
abnormalities
in
thesystem
AT45
5
Check
oil
passages
in
valve
b
dy
for
sign
of
damage
and
other
condi
tions
which
might
interfere
with
prop
er
valve
operation
6
Check
bolts
for
stripped
threads
Replace
as
required
Page 310 of 537
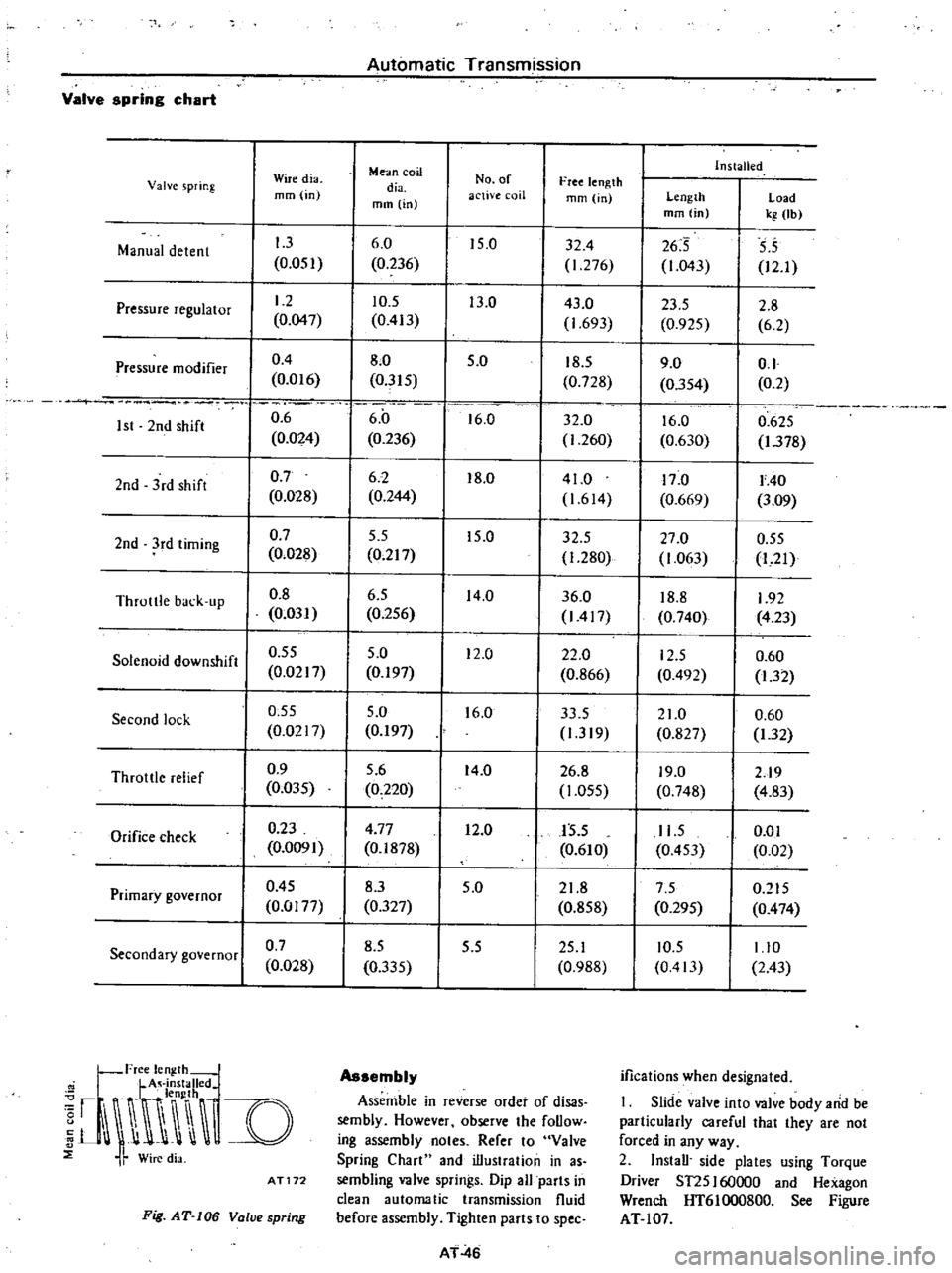
Automatic
Transmission
Valve
spring
chart
Mean
coil
Installed
Valve
spring
Wiredia
dia
No
of
free
length
mm
in
mm
in
active
coil
mm
in
Length
Load
mm
in
kg
lb
Manual
detent
1
3
6
0
15
0
32
4
26
5
5
5
0
051
0
236
1
276
1
043
12
1
Pressure
regulator
1
2
10
5
13
0
43
0
23
5
2
8
0
047
0
413
1
693
0
925
6
2
Pressure
modifier
0
4
8
0
5
0
18
5
9
0
0
1
0
016
0
315
0
728
0
354
0
2
1st
2nd
shift
0
6
6
0
6
0
32
0
16
0
0
625
0
024
0
236
1
260
0
630
1
378
2nd
3rd
shifl
0
7
6
2
8
0
41
0
17
0
1
40
0
028
0
244
1
614
0
669
3
09
2nd
3rd
timing
0
7
5
5
15
0
32
5
27
0
0
55
0
028
0
217
1
280
1
063
1
21
Throule
back
lIP
0
8
6
5
14
0
36
0
18
8
1
92
0
031
0
256
1417
0
740
4
23
Solenoid
downshift
0
55
5
0
12
0
22
0
12
5
0
60
0
0217
0
197
0
866
0
492
1
32
Second
lock
0
55
5
0
16
0
33
5
21
0
0
60
0
0217
0
197
1
319
0
827
1
32
Throule
relief
0
9
5
6
14
0
26
8
19
0
2
9
0
035
0
220
1
055
0
748
4
83
Orifice
check
0
23
4
77
12
0
J5
5
11
5
0
01
0
0091
0
1878
0
610
0
453
0
02
Primary
governor
0
45
8
3
5
0
21
8
7
5
0
215
0
0177
0
327
0
858
0
295
0
474
Secondary
governor
0
7
8
5
5
5
25
1
10
5
I
10
0
028
0
335
0
988
0
413
2
43
Free
lenglhm
A
installed
f
n
ri
DO
n
i
Wire
dia
AT172
Assembly
Assemble
in
reverse
order
of
disas
sembly
However
observe
the
follow
ing
assembly
noles
Refer
to
Valve
Spring
Chart
and
illustralion
in
as
sembling
valve
springs
Dip
all
parts
in
clean
automatic
transmission
fluid
before
assembly
Tighten
parts
to
spec
ifications
when
designated
I
Slide
valve
into
valve
body
arid
be
particularly
careful
that
they
are
not
forced
in
any
way
2
Install
side
plates
using
Torque
Driver
ST25160000
and
Hexagon
Wrench
HT6
I
000800
See
Figure
AT
l
07
Fig
AT
106
Value
spring
AT
46
Page 322 of 537
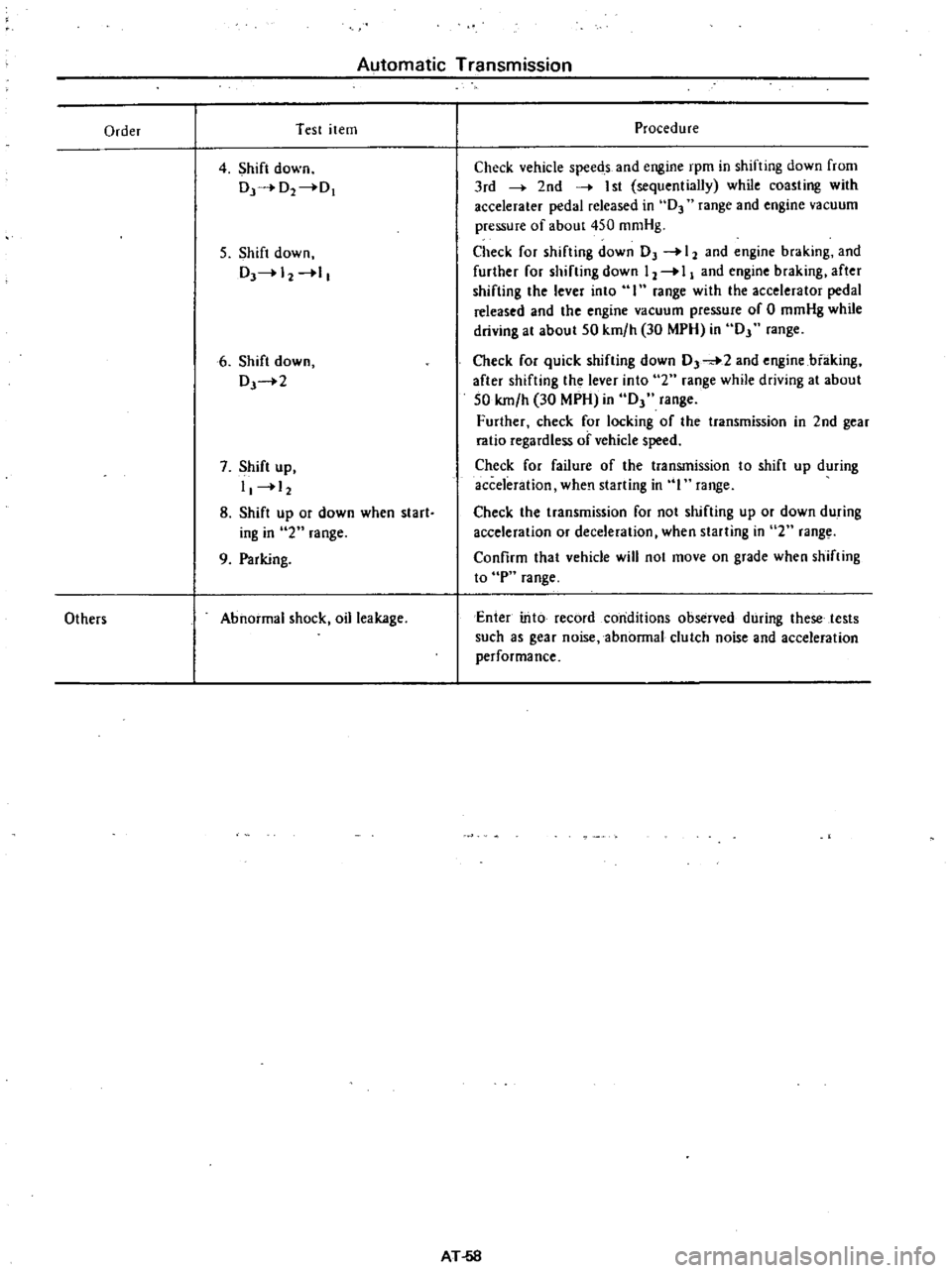
Automatic
Transmission
Order
Test
item
4
Shift
down
Dr
O2
0
5
Shift
down
DJ
12
1
6
Shift
down
DJ
2
7
Shift
up
I
12
8
Shift
up
or
down
when
start
iog
in
2
range
9
Parking
Others
Abnormal
shock
oil
leakage
Procedure
Check
vehicle
speeds
and
engine
rpm
in
shifting
down
from
3rd
2nd
I
st
sequentially
while
coasting
with
accelerater
pedal
released
in
D3
range
and
engine
vacuum
pressure
of
about
450
mmHg
Check
for
shifting
down
OJ
12
and
engine
braking
and
further
for
shifting
down
12
I
and
engine
braking
after
shifting
the
lever
into
I
range
with
the
accelerator
pedal
released
and
the
engine
vacuum
pressure
of
0
mmHg
while
driving
at
about
50
km
h
30
MPH
in
OJ
range
Check
for
quick
shifting
down
0
2
and
engine
biaking
after
shifting
the
lever
into
2
range
while
driving
at
about
50
km
h
30
MPH
in
OJ
range
Further
check
for
locking
of
the
transmission
in
2nd
gear
ratio
regardless
of
vehicle
speed
Check
for
failure
of
the
transmission
to
shift
up
during
acceleration
when
starting
in
I
range
Check
the
transmission
for
not
shifting
up
or
down
during
acceleration
or
deceleration
when
starting
in
2
rang
Confirm
that
vehicle
will
not
move
on
grade
when
shifting
to
P
range
Enter
into
record
conditions
observed
during
these
tests
such
as
gear
noise
abnormal
clutch
noise
and
acceleration
performance
AT
58
Page 323 of 537
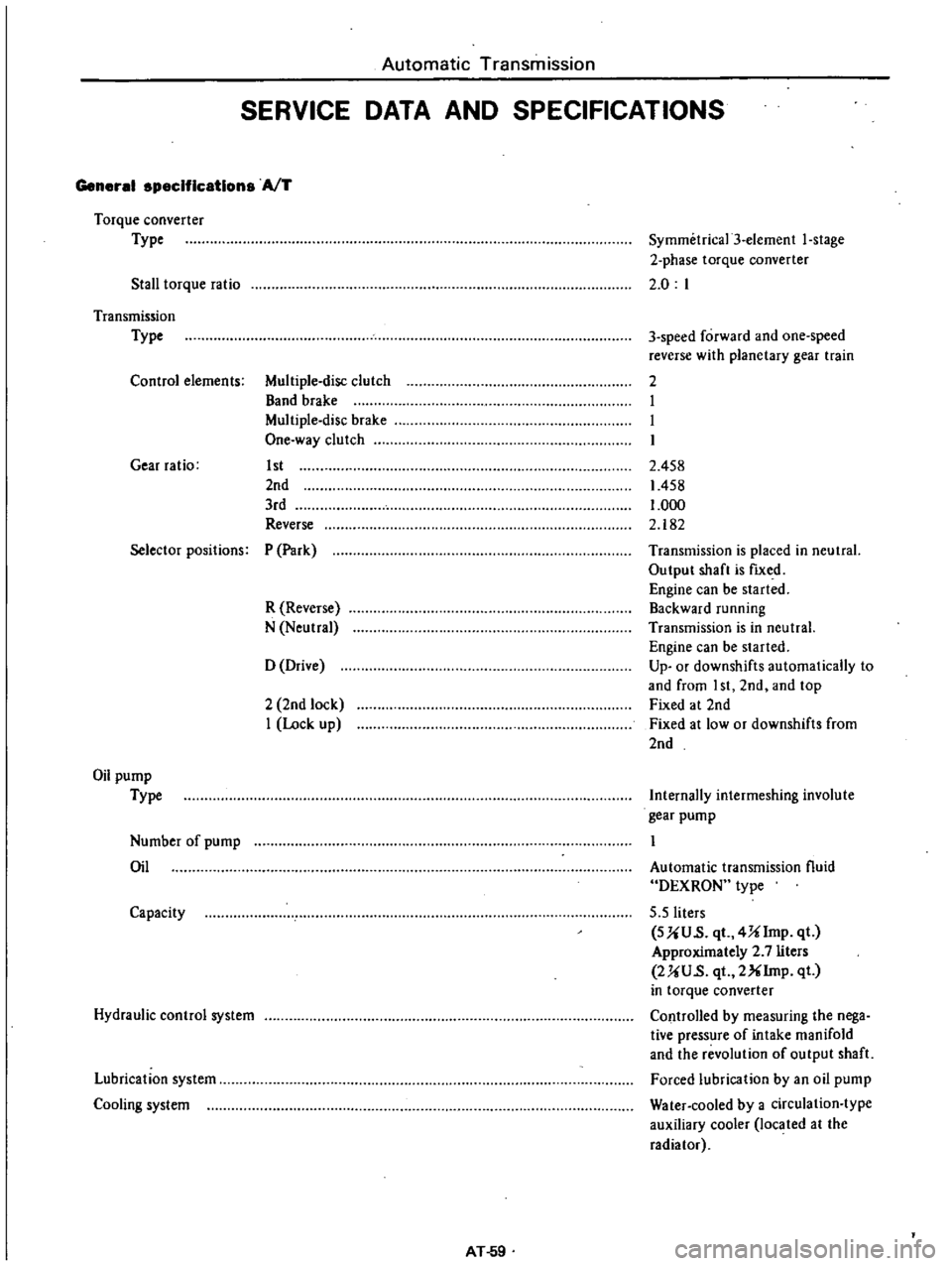
Automatic
Transmission
SERVICE
DATA
AND
SPECIFICATIONS
General
specifications
AfT
Torque
converter
Type
Stall
torque
ratio
Symmetrica13
element
I
stage
2
phase
torque
converter
2
0
I
Transmission
Type
Control
elements
Multiple
disc
clutch
Band
brake
Multiple
disc
brake
One
way
clutch
Gear
ratio
1st
2nd
3rd
Reverse
3
speed
forward
and
one
speed
reverse
with
planetary
gear
train
2
I
I
I
2
458
1458
1
000
2
182
Selector
positions
P
Park
R
Reverse
N
Neutral
Transmission
is
placed
in
neutral
Output
shaft
is
fIXed
Engine
can
be
started
Backward
running
Transmission
is
in
neutral
Engine
can
be
started
Up
or
downshifts
automatically
to
and
from
I
st
2nd
and
top
Fixed
at
2nd
Fixed
at
low
or
downshifts
from
2nd
o
Drive
2
2nd
lock
I
Lock
up
Oil
pump
Type
Internally
intermeshing
involute
gear
pump
Number
of
pump
Oil
Automatic
transmission
fluid
DEXRON
type
5
5
liters
SUU
s
qt
4Ulmp
qt
Approximately
2
7
liters
2UU
s
qt
2XIrnp
qt
in
torque
converter
Controlled
by
measuring
the
nega
tive
pressure
of
intake
manifold
and
the
revolution
of
output
shaft
Forced
lubrication
by
an
oil
pump
Water
cooled
by
a
circulation
type
auxiliary
cooler
located
at
the
radiator
Capacity
Hydraulic
control
system
Lubrication
system
Cooling
system
AT
59
Page 325 of 537
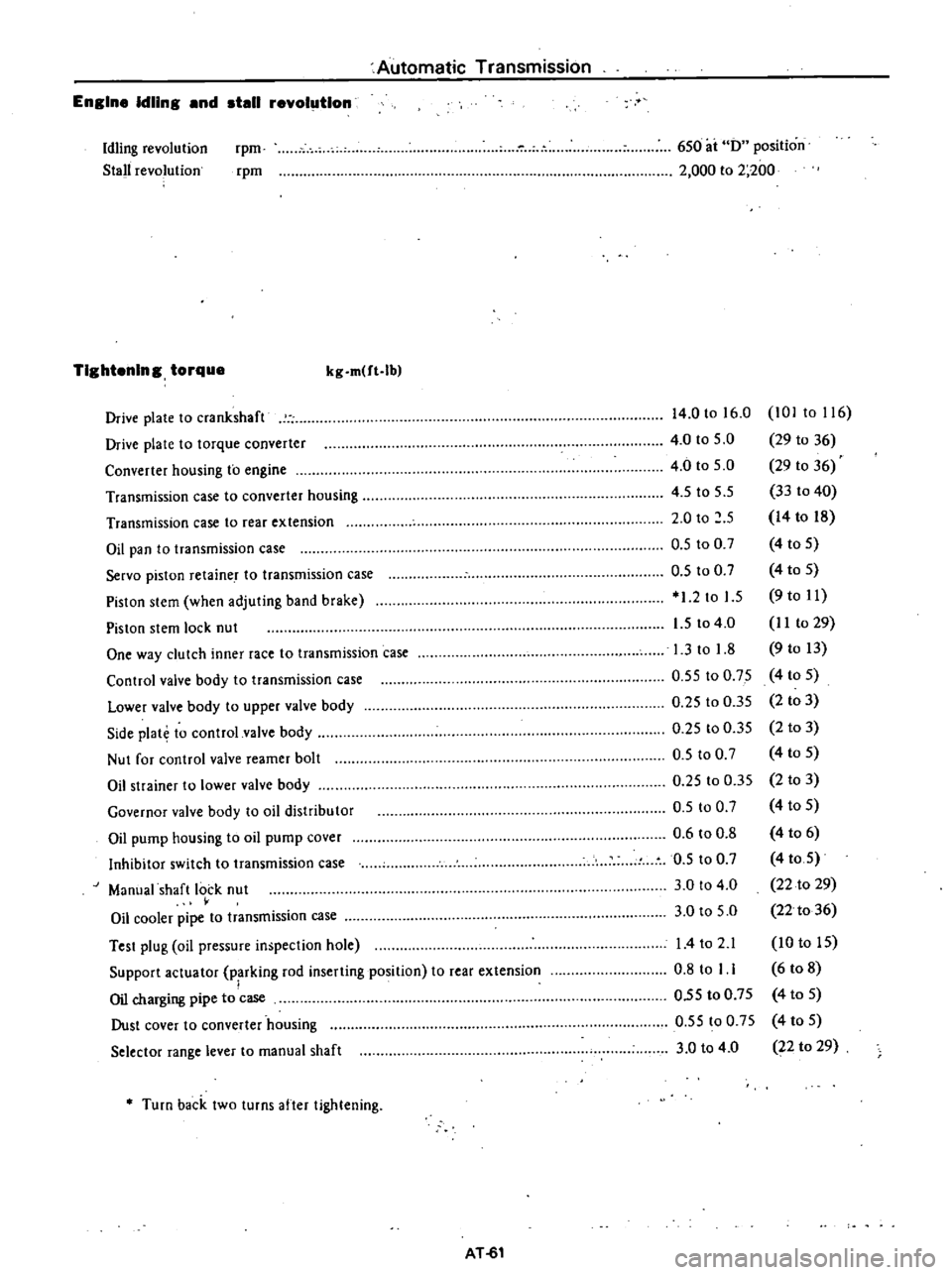
Automatic
Transmission
Engine
Idling
and
stall
revolution
Idling
revolution
Stall
revolution
rpm
rpm
6S0
ai
0
position
2
000
to
2
200
TIghtening
torque
kg
m
ft
lb
Drive
plate
to
crankshaft
Drive
plate
to
torque
converter
Converter
housing
to
engine
Transmission
case
to
converter
housing
Transmission
case
to
rear
extension
Oil
pan
to
transmission
case
Servo
piston
retaine
T
to
transmission
case
Pislon
slem
when
adjuting
band
brake
Piston
stem
lock
nut
One
way
clutch
inner
race
to
transmission
case
Control
valve
body
to
transmission
case
Lower
valve
body
to
upper
valve
body
Side
plat
to
control
valve
body
Nut
for
control
valve
reamer
bolt
Oil
strainer
to
lower
valve
body
Governor
valve
body
to
oil
distribu
tor
Oil
pump
housing
to
oil
pump
cover
Inhibitor
switch
to
transmission
case
Manual
shaft
lock
nut
Oil
cooler
pipe
to
transmission
case
Test
plug
oil
pressure
inspection
hole
Support
actuator
parking
rod
inserting
position
to
rear
extension
I
Oil
charging
pipe
to
case
Dust
cover
to
converter
housing
Selector
range
lever
to
manual
shaft
14
0
to
16
0
101
to
116
4
0
to
5
0
29
to
36
4
0
to
S
O
29
10
36
4
S
to
5
5
33
to
40
2
0
to
S
14
to
18
O
S
to
0
7
4
to
S
O
S
to
0
7
4
to
S
1
2
to
1
5
9
to
11
1
5
to
4
0
I
I
to
29
1
3
to
1
8
9
to
13
0
5S
to
0
75
4
to
S
0
25
to
O
3S
2
to
3
0
25
to
0
35
2
to
3
O
S
to
0
7
4
to
S
0
25
to
0
35
2
to
3
D
S
100
7
4
to
5
0
6
to
0
8
4
to
6
0
5
to
0
7
4
toS
3
0
to
4
0
22
to
29
3
0
to
S
O
22
to
36
I
4to
2
1
10
to
IS
0
8
to
I
1
6
to
8
O
5S
to
0
7S
4
to
S
O
5S
to
0
75
4
to
S
3
0
to
4
0
22
to
29
Turn
back
two
turns
after
tightening
AT
61
Page 330 of 537
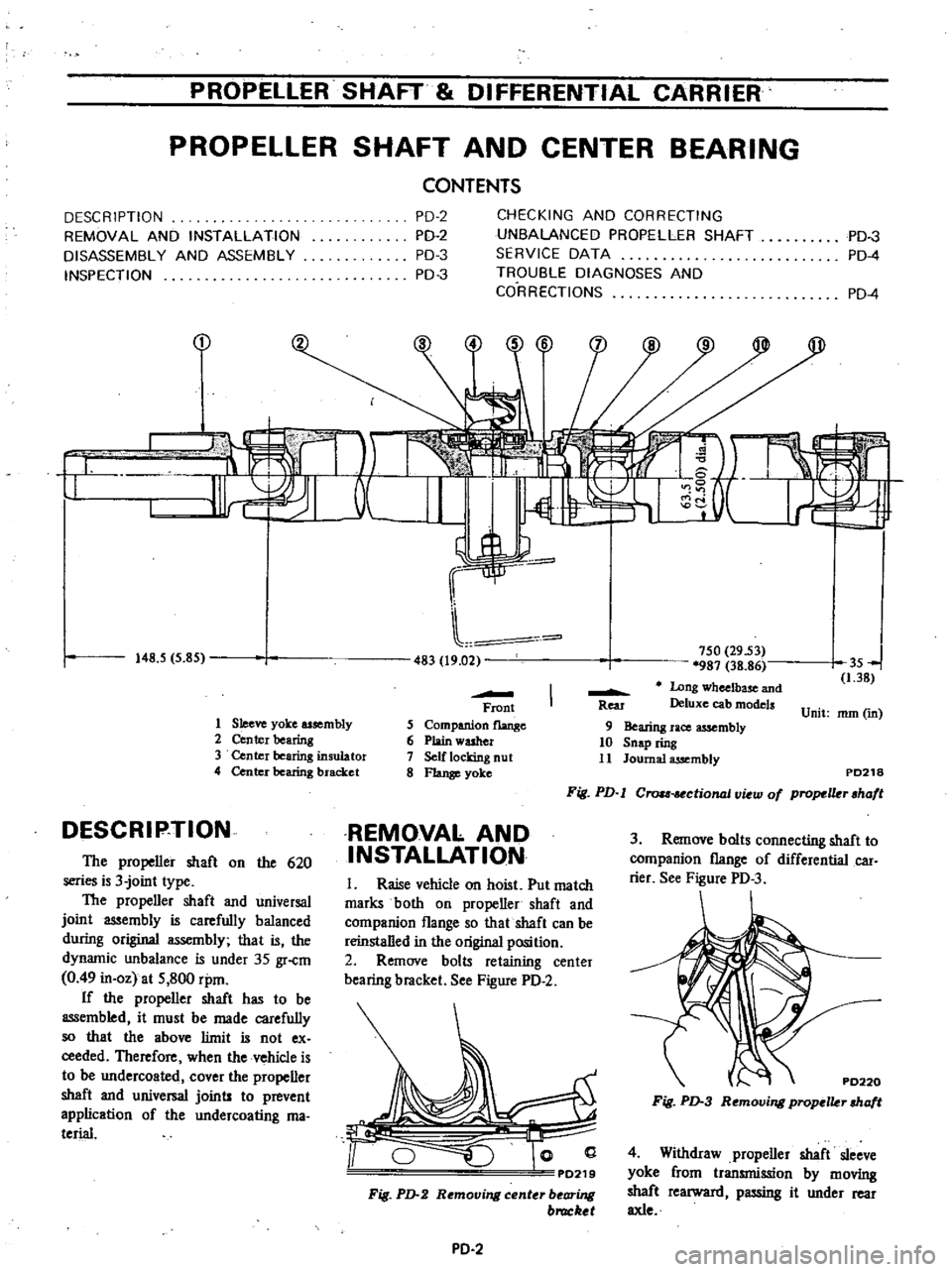
PROPElLER
SHAFT
DIFFERENTIAL
CARRIER
PROPELLER
SHAFT
AND
CENTER
BEARING
CONTENTS
DESCRIPTION
REMOVAL
AND
INSTALLATION
DISASSEMBLY
AND
ASSEMBLY
INSPECTION
i
t
I
tl
J
I
O
148
5
5
85
PD
2
PD
2
PD
3
PD
3
CHECKING
AND
CORRECTING
UNBALANCED
PROPELLER
SHAFT
SERVICE
DATA
TROUBLE
DIAGNOSES
AND
CORRECTIONS
PD
4
PD
3
PD
4
2
483
19
02
750
29
53
987
38
86
Long
wheelbase
and
Deluxe
cab
models
Unit
mm
in
35
1
38
Front
5
Companion
flange
6
Plain
washer
7
Self
locking
nut
8
Flange
yoke
Rea
1
Sleeve
yoke
assembly
2
Center
bearing
3
Center
bearing
insulator
4
Center
bearing
bracket
DESCRIP
TION
The
propeller
shaft
on
the
620
series
is
3
joint
type
The
propeller
shaft
and
universal
joint
assembly
is
carefully
balanced
during
original
assembly
that
is
the
dynamic
unbalance
is
under
35
gr
cm
0
49
in
oz
at
S
800
rpm
If
the
propeller
shaft
has
to
be
assembled
it
must
be
made
carefully
so
that
the
above
limit
is
not
ex
ceeded
Therefore
when
the
vehicle
is
to
be
undercoated
cover
the
propeller
shaft
and
universal
joints
to
prevent
application
of
the
undercoating
ma
terial
9
Bearing
race
assembly
10
Snap
ring
11
Journal
assembly
PD218
Fig
PD
l
Crou
ctional
v
w
of
propelkr
hafl
REMOVAL
AND
INSTALLATION
3
Remove
bolts
connecting
shaft
to
companion
flange
of
differential
car
rier
See
Figure
PD
3
I
Raise
vehicle
on
hoist
Put
match
marks
both
on
propeller
shaft
and
companion
flange
so
that
shaft
can
be
reinstalled
in
the
original
position
2
Remove
bolts
retaining
center
bearing
bracket
See
Figure
PD
2
PD220
Fig
PD
3
Removing
propclkr
cha
t
PD219
Fig
PD
2
Removing
center
bearing
bruckel
4
Withdraw
propeller
shaft
sleeve
yoke
from
transmission
by
moving
shaft
rearward
passing
it
under
rear
axle
PD
2
Page 331 of 537
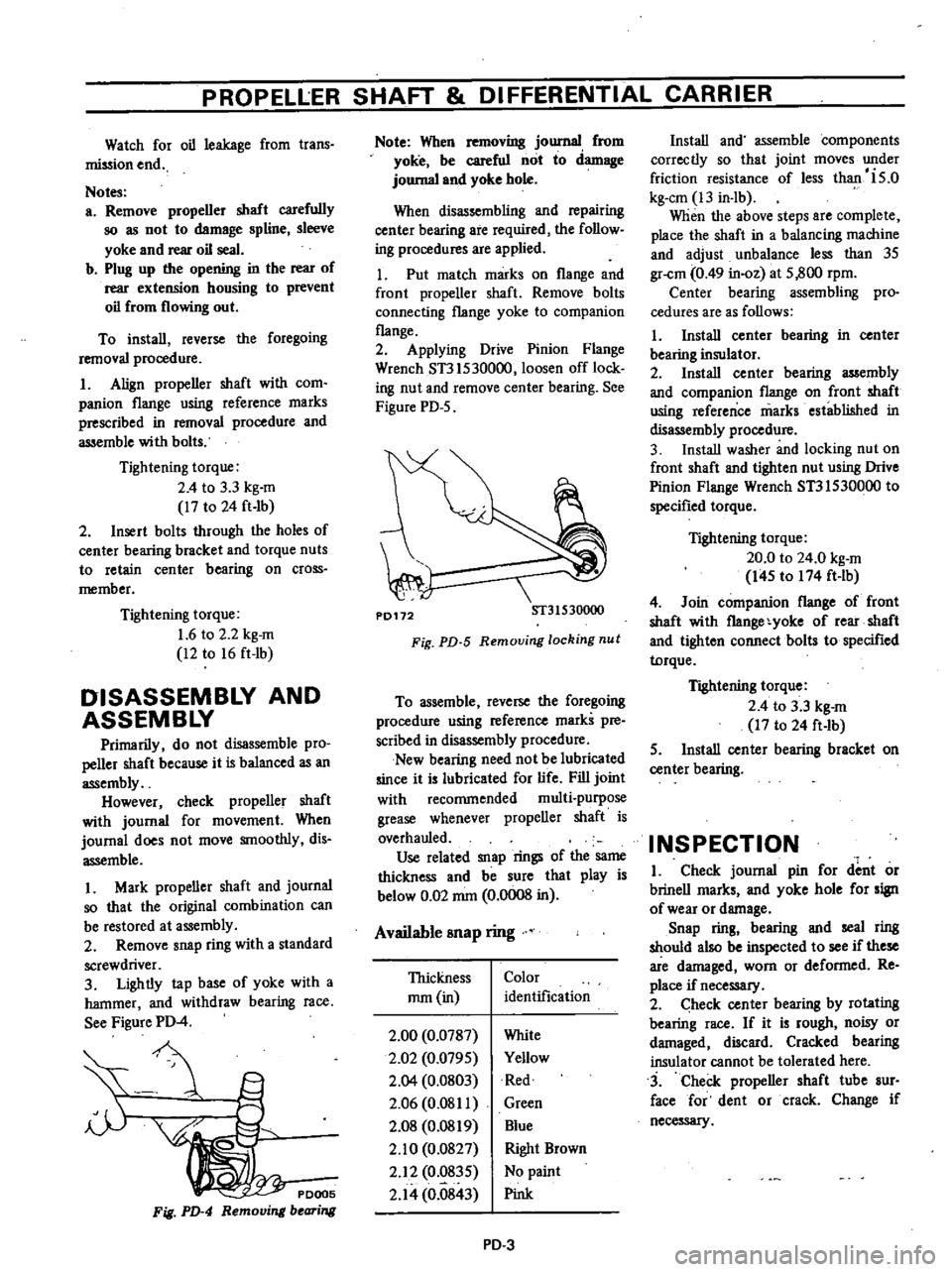
PROPELLER
SHAFT
DIFFERENTIAL
CARRIER
Watch
for
oil
leakage
from
trans
mission
end
Notes
a
Remove
propeller
shaft
carefully
so
as
not
to
damage
spline
sleeve
yoke
and
rear
oil
seal
b
Plug
up
the
opening
in
the
rear
of
rear
extension
housing
to
prevent
oil
from
flowing
out
To
install
reverse
the
foregoing
removal
procedure
1
Align
propeller
shaft
with
com
panion
flange
using
reference
marks
prescribed
in
removal
procedure
and
assemble
with
bolts
Tightening
torque
2
4
to
3
3
kg
m
17
to
24
ft
Ib
2
Insert
bolts
through
the
holes
of
center
beariug
bracket
and
torque
nuts
to
retain
center
bearing
on
cross
member
Tightening
torque
1
6
to
2
2
kg
m
12
to
16
ft
Ib
DISASSEMBLY
AND
ASSEMBLY
Primarily
do
not
disassemble
pro
peller
shaft
because
it
is
balanced
as
an
assembly
However
check
propeller
shaft
with
journal
for
movement
When
journal
does
not
move
smoothly
dis
assemble
1
Mark
propeller
shaft
and
journal
so
that
the
original
combination
can
be
restored
at
assembly
2
Remove
snap
ring
with
a
standard
screwdriver
3
Lightly
tap
base
of
yoke
with
a
hammer
and
withdraw
bearing
race
See
Figure
PD
4
PDOO5
Fig
PD
4
Remo
i
bearing
Note
When
removing
journal
from
yoke
be
careful
not
to
damage
journal
and
yoke
bole
When
disassembling
and
repairing
center
bearing
are
required
the
follow
ing
procedures
are
applied
1
Put
match
marks
on
flange
and
front
propeller
shaft
Remove
bolts
connecting
flange
yoke
to
companion
flange
2
Applying
Drive
Pinion
Flange
Wrench
ST3lS30000
loosen
off
lock
ing
nut
and
remove
center
bearing
See
Figure
PD
5
P0172
ST31530000
Fig
PD
5
Remouing
locking
nut
To
assemble
reverse
the
foregoing
procedure
using
reference
marks
pre
scribed
in
disassembly
procedure
New
bearing
need
not
be
lubricated
since
it
is
lubricated
for
life
Fill
joint
with
recommended
multi
purpose
grease
whenever
propeller
shaft
is
overhauled
Use
related
snap
rings
of
the
same
thickness
and
be
sure
that
play
is
below
0
02
mm
0
0008
in
Available
snap
ring
Thickness
mm
in
Color
identification
2
00
0
0787
2
02
0
079S
2
Q4
0
0803
2
06
0
08
II
2
08
0
0819
2
10
0
0827
2
12
0
83S
2
14
0
0843
White
Yellow
Red
Green
Blue
Right
Brown
No
paint
Pink
PD
3
Install
and
assemble
components
correctly
so
that
joint
moves
under
friction
resistance
of
less
than
is
o
kg
em
13
in
lb
When
the
above
steps
are
complete
place
the
shaft
in
a
balancing
machine
and
adjust
unbalance
less
than
3S
gr
cm
0
49
in
oz
at
S
800
rpm
Center
bearing
assembling
pro
cedures
are
as
follows
I
Install
center
bearing
in
center
bearing
insulator
2
Install
center
bearing
assembly
and
companion
flange
on
front
shaft
usiug
reference
marks
established
in
disassembly
procedure
3
Install
washer
and
locking
nut
on
front
shaft
and
tighten
nut
using
Drive
Pinion
Flange
Wrench
ST3IS30000
to
specified
torque
Tightening
torque
20
0
to
24
0
kg
m
I4S
to
174
ft
lb
4
Join
companion
flange
of
front
shaft
with
f1ange
yoke
of
rear
shaft
and
tighten
connect
bolts
to
specified
torque
Tightening
torque
2
4
to
3
3
kg
m
17
to
24
ft
Ib
S
Install
center
bearing
bracket
on
center
bearing
INSPECTION
I
Check
journal
pin
for
dent
or
brinell
marks
and
yoke
hole
for
sign
of
wear
or
damage
Snap
ring
bearing
and
seal
ring
should
also
be
inspected
to
see
if
these
are
damaged
worn
or
deformed
Re
place
if
necessary
2
heck
center
bearing
by
rotating
bearing
race
If
it
is
rough
noisy
or
damaged
discard
Cracked
bearing
insulator
cannot
be
tolerated
here
3
Check
propeller
shaft
tube
sur
face
for
dent
or
crack
Change
if
necessary
Page 332 of 537
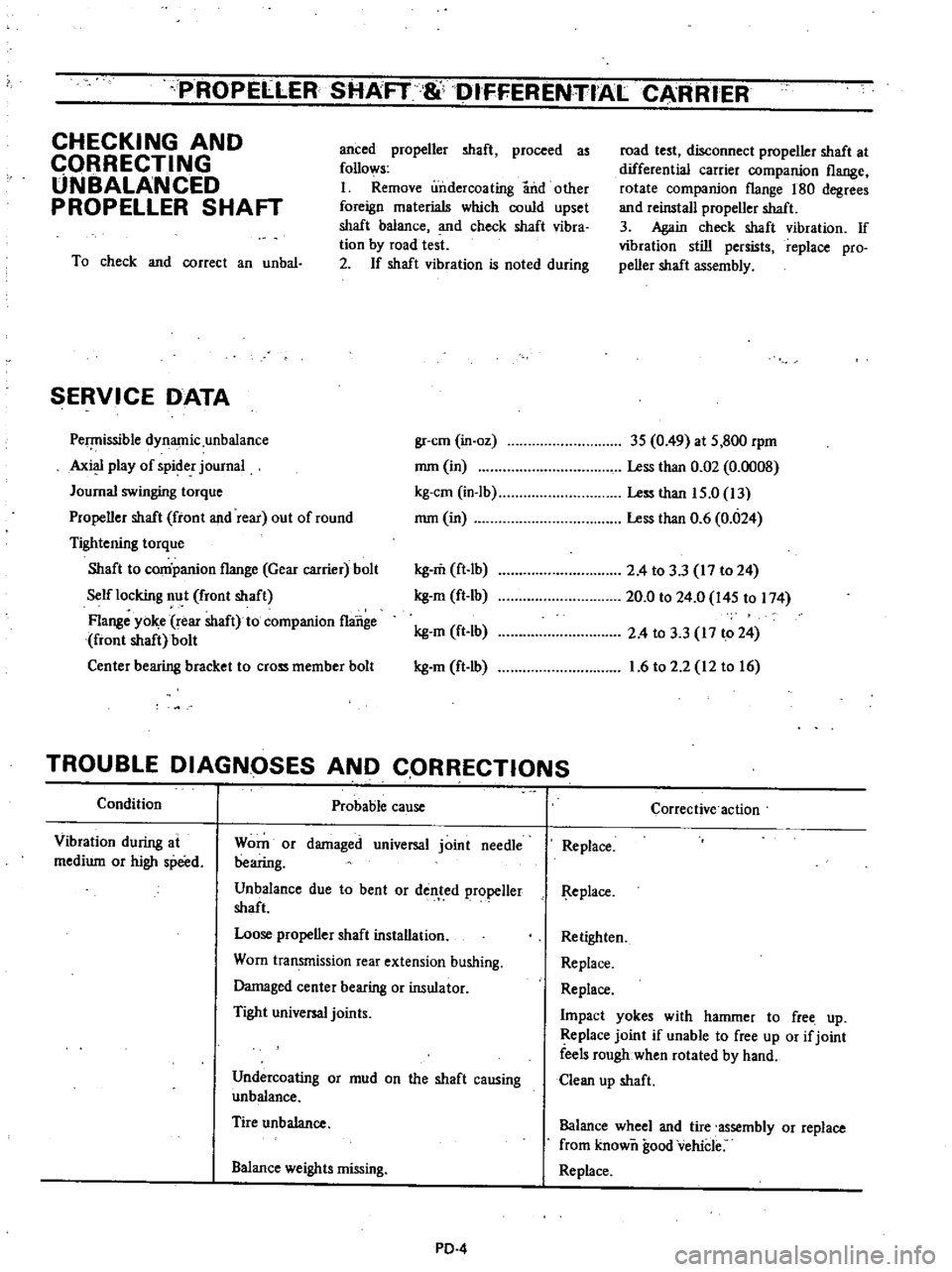
PROPELLER
SHAFT
8l
DIFFERENTIALCAAR
ER
CHECKING
AND
CQRRECTING
UNBALANCED
PROPELLER
SHAFT
anced
propeller
shaft
proceed
as
follows
I
Remove
undercoating
and
other
foreign
materials
which
could
upset
shaft
balance
and
check
shaft
vibra
tion
by
road
test
2
If
shaft
vibration
is
noted
during
To
check
and
correct
an
unbal
SERVICE
DATA
Pe
issible
dynamic
unbalance
Axi
play
of
spider
journal
Journal
swinging
torque
Propeller
shaft
front
and
rear
out
of
round
Tightening
torque
Shaft
to
conipanion
flange
Gear
carrier
bolt
Self
locking
nut
front
shaft
Flange
yo
e
rear
shaft
to
companion
flange
front
shaft
bolt
Center
bearing
bracket
to
cross
member
bolt
road
test
disconnect
propeller
shaft
at
differential
carrier
companion
flange
rotate
companion
flange
180
degrees
and
reinstall
propeller
shaft
3
Again
check
shaft
vibration
If
vibration
still
persists
replace
pro
peller
shaft
assembly
gr
cm
in
oz
3S
0
49
at
S
800
rpm
mm
in
Less
than
0
02
0
0008
kg
em
in
Ib
Less
than
IS
O
13
mm
in
Less
than
0
6
0
024
kg
m
ft
lb
kg
m
ft
Ib
kg
m
ft
lb
kg
m
ft
lb
2
4
to
3
3
17
to
24
20
0
to
24
0
l4S
to
174
2
4
to
3
3
17
to
24
1
6
to
2
2
12
to
16
TROUBLE
DIAGNOSES
AND
CQRRECTIONS
Condition
Probable
cause
Vibration
during
at
medium
or
high
speed
Worn
or
damaged
universal
joint
needle
bearing
Unbalance
due
to
bent
or
dented
propeller
shaft
Loose
propeller
shaft
installation
Worn
transmission
rear
extension
bushing
Damaged
center
bearing
or
insulator
Tight
universal
joints
Undercoating
or
mud
on
the
shaft
causing
unbalance
Tire
unbalance
Balance
weights
missing
PD
4
Corrective
action
Replace
I
l
eplace
Retighten
Replace
Replace
Impact
yokes
with
hammer
to
free
up
Replace
joint
if
unable
to
free
up
or
if
joint
feels
rough
when
rotated
by
hand
Clean
up
shaft
Balance
wheel
and
tire
assembly
or
replace
from
known
good
vehicle
Replace
Page 333 of 537
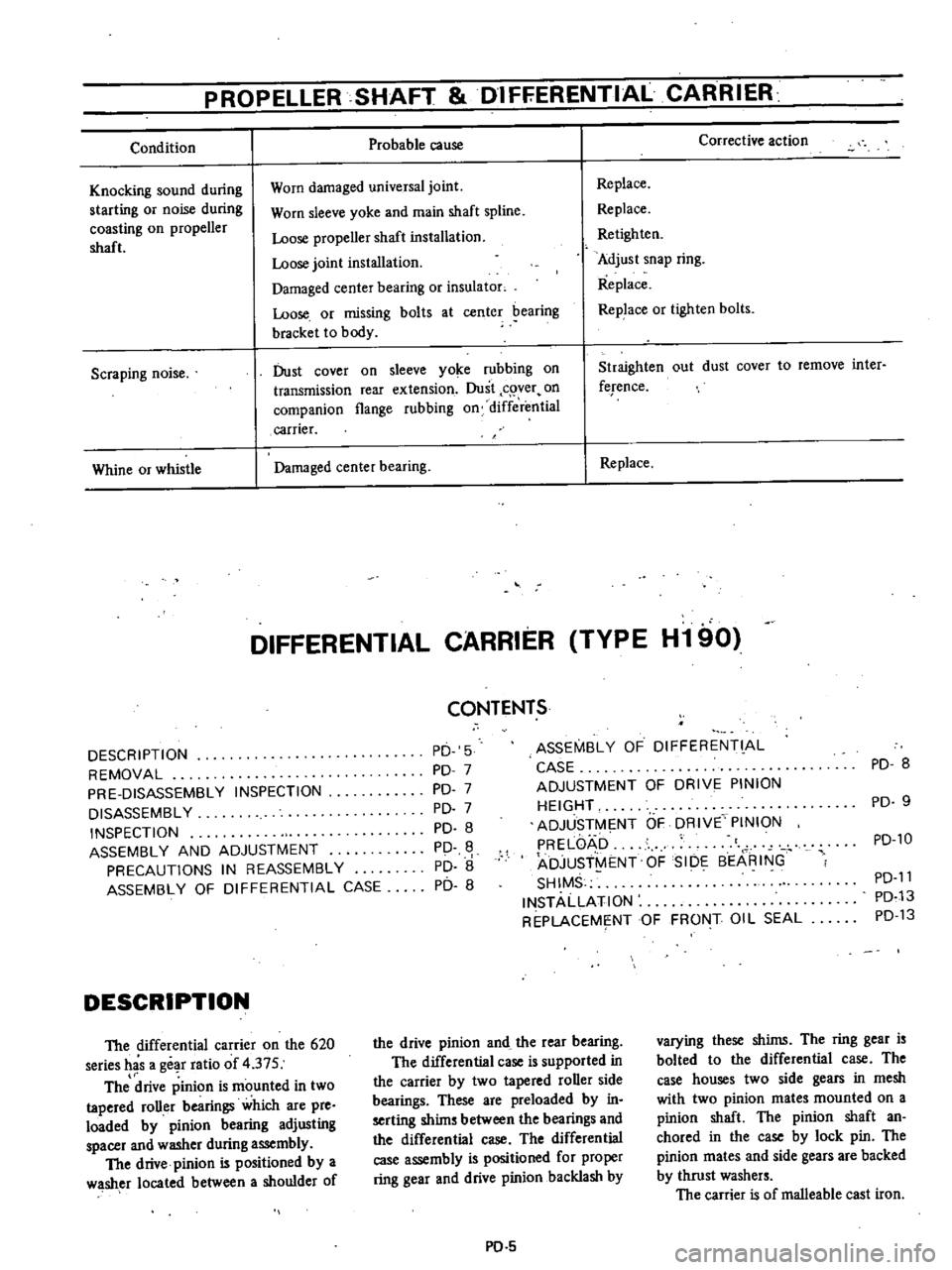
PROPELLER
SHAFT
DIFFERENTIAL
CARRIER
Condition
Probable
cause
Knocking
sound
during
starting
or
noise
during
coasting
on
propeller
shaft
Worn
damaged
universal
joint
Worn
sleeve
yoke
and
main
shaft
spline
Loose
propeller
shaft
installation
Loose
joint
installation
Damaged
center
bearing
or
insulator
Loose
or
missing
bolts
at
center
bearing
bracket
to
body
Scraping
noise
Dust
cover
on
sleeve
yoke
rubbing
on
transmission
rear
extension
Dust
c
ver
on
companion
flange
rubbing
on
differ
mtial
carrier
Whine
or
whistle
Damaged
center
bearing
Corrective
action
Replace
Replace
Retighten
Adjust
snap
ring
Replace
Replace
or
tighten
bolts
Straighten
out
dust
cover
to
remove
inter
ference
Replace
DIFFERENTIAL
CARRIER
TYPE
H190
CONTENTS
DESCRIPTION
REMOVAL
PRE
DISASSEMBLY
INSPECTION
DISASSEMBLY
INSPECTION
ASSEMBLY
AND
ADJUSTMENT
PRECAUTIONS
IN
REASSEMBLY
ASSEMBLY
OF
DIFFERENTIAL
CASE
PD
5
PD
7
PD
7
PD
7
PD
8
PD
PD
8
PD
8
DESCRIPTION
The
differential
carrier
on
the
620
series
has
a
gear
ratio
of
4
37S
The
drive
pinion
is
rnounted
in
two
tapered
roUer
bearings
which
are
pre
loaded
by
pinion
bearing
adjusting
spacer
and
washer
during
assembly
The
drive
pinion
is
positioned
by
a
washer
located
between
a
shoulder
of
ASSEMBl
Y
OF
DIFFERENT
Al
CASE
ADJUSTMENT
OF
DRIVE
PINION
HEIGHT
ADJUSTME
NT
OF
DRIVE
PINION
PRELOAD
t
ADJUST
ENT
OF
SIDE
8EARING
SHIMS
INSTAllATION
REPLACEME
NTOF
FRONT
Oil
SEAL
the
drive
pinion
and
the
rear
bearing
The
differential
case
is
supported
in
the
carrier
by
two
tapered
roller
side
bearings
These
are
preloaded
by
in
serting
shims
between
the
bearings
and
the
differential
case
The
differential
case
assembly
is
positioned
for
proper
ring
gear
and
drive
pinion
backlash
by
PO
5
PD
8
PD
9
PD
lO
PD
11
PD
13
PD
13
varying
these
shims
The
ring
gear
is
bolted
to
the
differential
case
The
case
houses
two
side
gears
in
mesh
with
two
pinion
mates
mounted
on
a
pinion
shaft
The
pinion
shaft
an
chored
in
the
case
by
lock
pin
The
pinion
mates
and
side
gears
are
backed
by
thrust
washers
The
carrier
is
of
malleable
cast
iron