Connectors DODGE RAM 1500 1998 2.G Owners Manual
[x] Cancel search | Manufacturer: DODGE, Model Year: 1998, Model line: RAM 1500, Model: DODGE RAM 1500 1998 2.GPages: 2627
Page 1904 of 2627
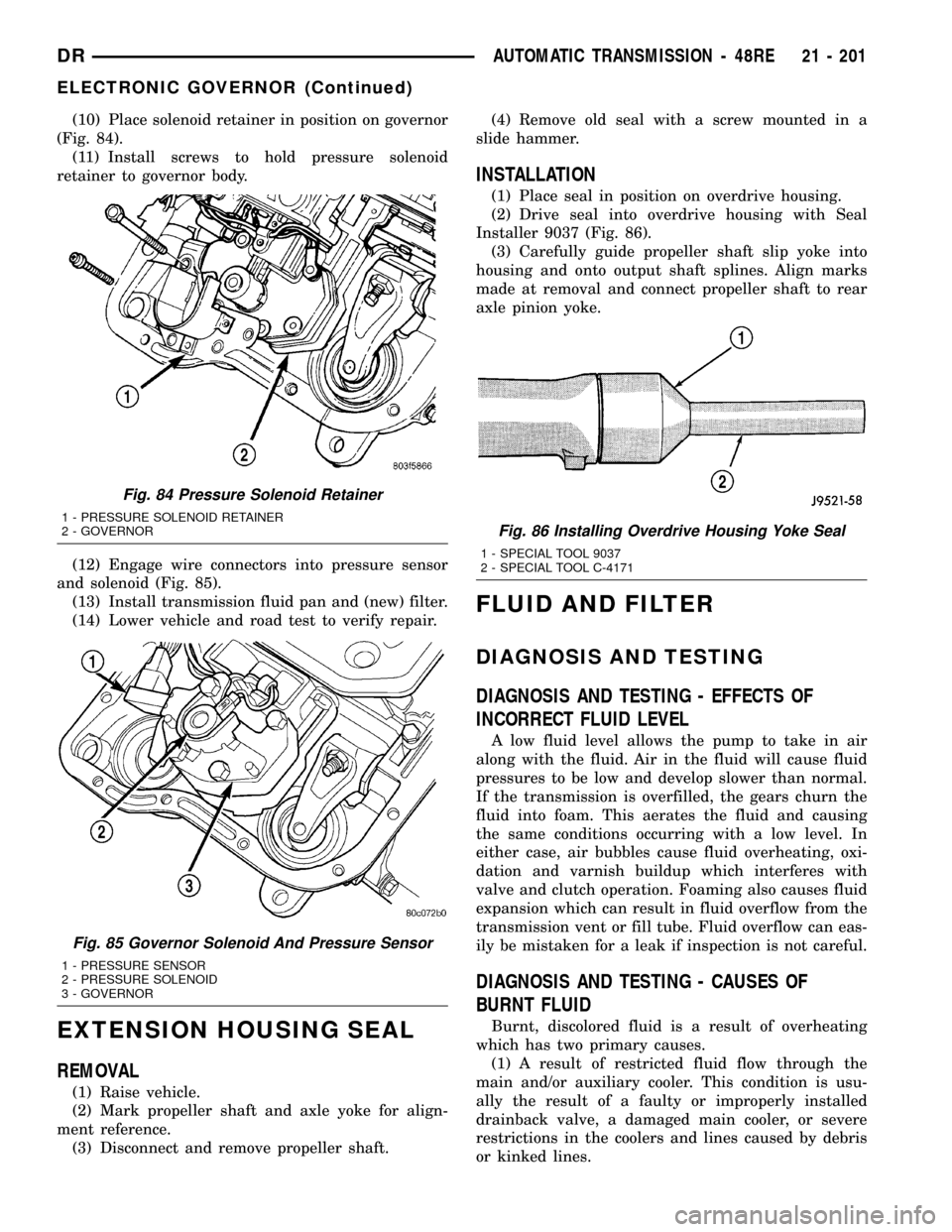
(10) Place solenoid retainer in position on governor
(Fig. 84).
(11) Install screws to hold pressure solenoid
retainer to governor body.
(12) Engage wire connectors into pressure sensor
and solenoid (Fig. 85).
(13) Install transmission fluid pan and (new) filter.
(14) Lower vehicle and road test to verify repair.
EXTENSION HOUSING SEAL
REMOVAL
(1) Raise vehicle.
(2) Mark propeller shaft and axle yoke for align-
ment reference.
(3) Disconnect and remove propeller shaft.(4) Remove old seal with a screw mounted in a
slide hammer.
INSTALLATION
(1) Place seal in position on overdrive housing.
(2) Drive seal into overdrive housing with Seal
Installer 9037 (Fig. 86).
(3) Carefully guide propeller shaft slip yoke into
housing and onto output shaft splines. Align marks
made at removal and connect propeller shaft to rear
axle pinion yoke.
FLUID AND FILTER
DIAGNOSIS AND TESTING
DIAGNOSIS AND TESTING - EFFECTS OF
INCORRECT FLUID LEVEL
A low fluid level allows the pump to take in air
along with the fluid. Air in the fluid will cause fluid
pressures to be low and develop slower than normal.
If the transmission is overfilled, the gears churn the
fluid into foam. This aerates the fluid and causing
the same conditions occurring with a low level. In
either case, air bubbles cause fluid overheating, oxi-
dation and varnish buildup which interferes with
valve and clutch operation. Foaming also causes fluid
expansion which can result in fluid overflow from the
transmission vent or fill tube. Fluid overflow can eas-
ily be mistaken for a leak if inspection is not careful.
DIAGNOSIS AND TESTING - CAUSES OF
BURNT FLUID
Burnt, discolored fluid is a result of overheating
which has two primary causes.
(1) A result of restricted fluid flow through the
main and/or auxiliary cooler. This condition is usu-
ally the result of a faulty or improperly installed
drainback valve, a damaged main cooler, or severe
restrictions in the coolers and lines caused by debris
or kinked lines.
Fig. 84 Pressure Solenoid Retainer
1 - PRESSURE SOLENOID RETAINER
2 - GOVERNOR
Fig. 85 Governor Solenoid And Pressure Sensor
1 - PRESSURE SENSOR
2 - PRESSURE SOLENOID
3 - GOVERNOR
Fig. 86 Installing Overdrive Housing Yoke Seal
1 - SPECIAL TOOL 9037
2 - SPECIAL TOOL C-4171
DRAUTOMATIC TRANSMISSION - 48RE 21 - 201
ELECTRONIC GOVERNOR (Continued)
Page 1938 of 2627
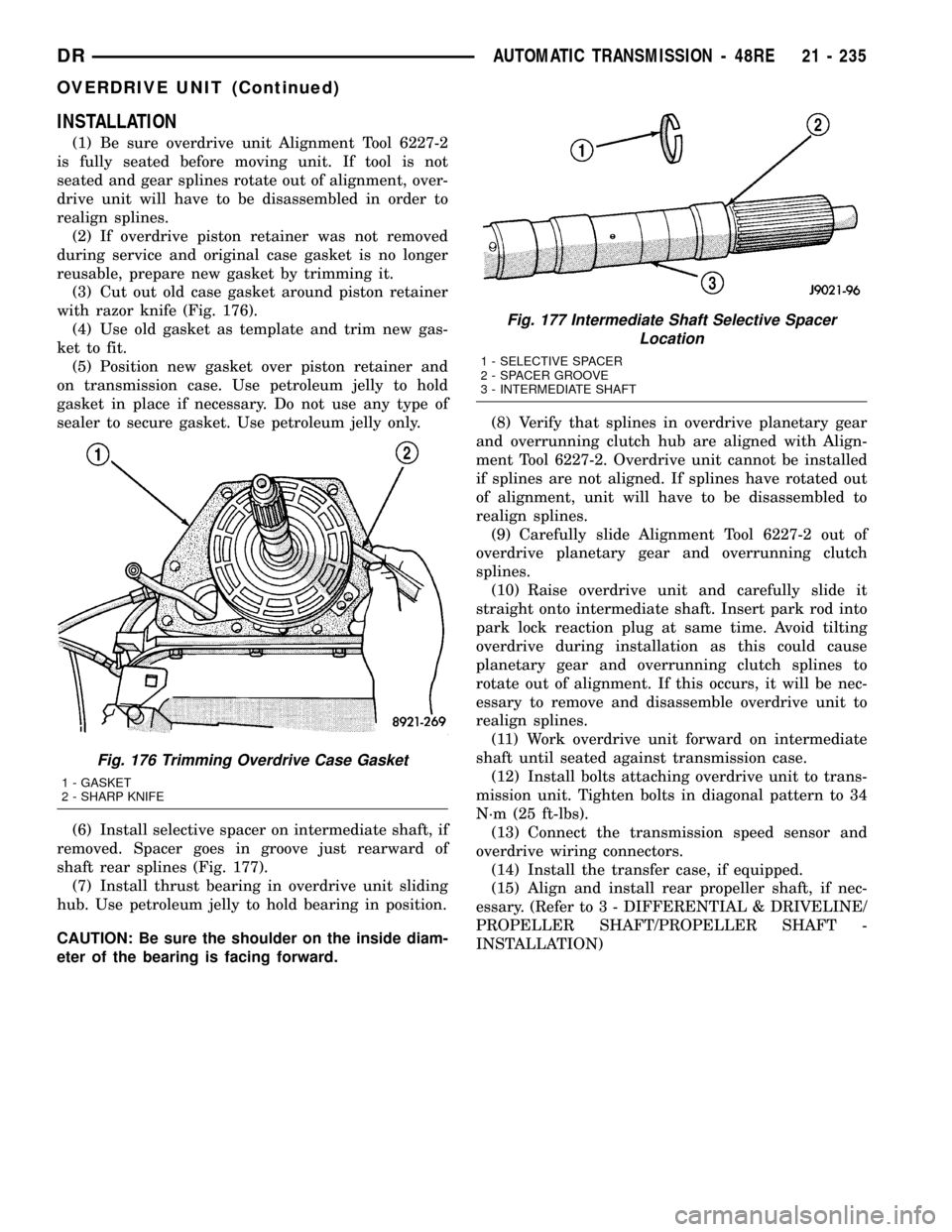
INSTALLATION
(1) Be sure overdrive unit Alignment Tool 6227-2
is fully seated before moving unit. If tool is not
seated and gear splines rotate out of alignment, over-
drive unit will have to be disassembled in order to
realign splines.
(2) If overdrive piston retainer was not removed
during service and original case gasket is no longer
reusable, prepare new gasket by trimming it.
(3) Cut out old case gasket around piston retainer
with razor knife (Fig. 176).
(4) Use old gasket as template and trim new gas-
ket to fit.
(5) Position new gasket over piston retainer and
on transmission case. Use petroleum jelly to hold
gasket in place if necessary. Do not use any type of
sealer to secure gasket. Use petroleum jelly only.
(6) Install selective spacer on intermediate shaft, if
removed. Spacer goes in groove just rearward of
shaft rear splines (Fig. 177).
(7) Install thrust bearing in overdrive unit sliding
hub. Use petroleum jelly to hold bearing in position.
CAUTION: Be sure the shoulder on the inside diam-
eter of the bearing is facing forward.(8) Verify that splines in overdrive planetary gear
and overrunning clutch hub are aligned with Align-
ment Tool 6227-2. Overdrive unit cannot be installed
if splines are not aligned. If splines have rotated out
of alignment, unit will have to be disassembled to
realign splines.
(9) Carefully slide Alignment Tool 6227-2 out of
overdrive planetary gear and overrunning clutch
splines.
(10) Raise overdrive unit and carefully slide it
straight onto intermediate shaft. Insert park rod into
park lock reaction plug at same time. Avoid tilting
overdrive during installation as this could cause
planetary gear and overrunning clutch splines to
rotate out of alignment. If this occurs, it will be nec-
essary to remove and disassemble overdrive unit to
realign splines.
(11) Work overdrive unit forward on intermediate
shaft until seated against transmission case.
(12) Install bolts attaching overdrive unit to trans-
mission unit. Tighten bolts in diagonal pattern to 34
N´m (25 ft-lbs).
(13) Connect the transmission speed sensor and
overdrive wiring connectors.
(14) Install the transfer case, if equipped.
(15) Align and install rear propeller shaft, if nec-
essary. (Refer to 3 - DIFFERENTIAL & DRIVELINE/
PROPELLER SHAFT/PROPELLER SHAFT -
INSTALLATION)
Fig. 176 Trimming Overdrive Case Gasket
1 - GASKET
2 - SHARP KNIFE
Fig. 177 Intermediate Shaft Selective Spacer
Location
1 - SELECTIVE SPACER
2 - SPACER GROOVE
3 - INTERMEDIATE SHAFT
DRAUTOMATIC TRANSMISSION - 48RE 21 - 235
OVERDRIVE UNIT (Continued)
Page 1957 of 2627
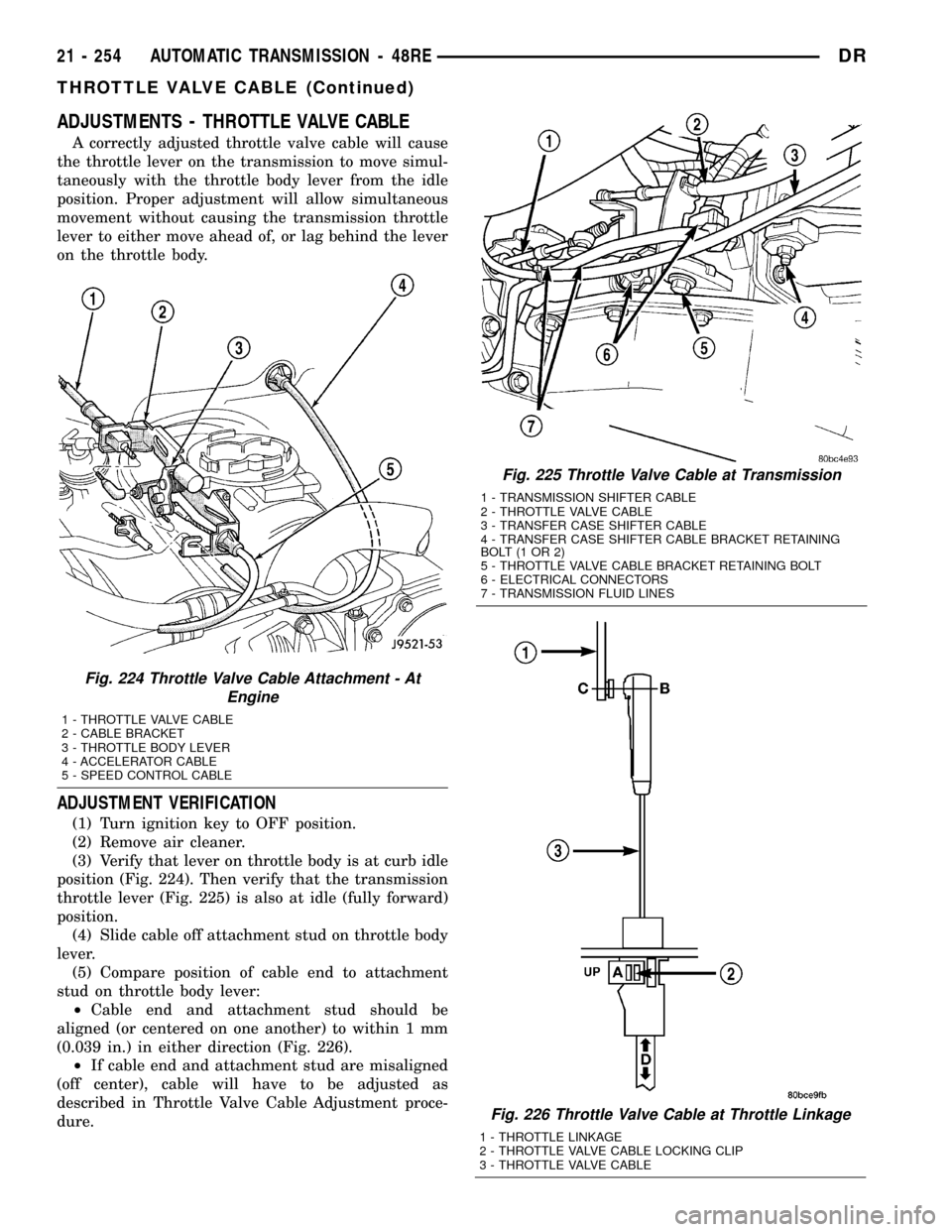
ADJUSTMENTS - THROTTLE VALVE CABLE
A correctly adjusted throttle valve cable will cause
the throttle lever on the transmission to move simul-
taneously with the throttle body lever from the idle
position. Proper adjustment will allow simultaneous
movement without causing the transmission throttle
lever to either move ahead of, or lag behind the lever
on the throttle body.
ADJUSTMENT VERIFICATION
(1) Turn ignition key to OFF position.
(2) Remove air cleaner.
(3) Verify that lever on throttle body is at curb idle
position (Fig. 224). Then verify that the transmission
throttle lever (Fig. 225) is also at idle (fully forward)
position.
(4) Slide cable off attachment stud on throttle body
lever.
(5) Compare position of cable end to attachment
stud on throttle body lever:
²Cable end and attachment stud should be
aligned (or centered on one another) to within 1 mm
(0.039 in.) in either direction (Fig. 226).
²If cable end and attachment stud are misaligned
(off center), cable will have to be adjusted as
described in Throttle Valve Cable Adjustment proce-
dure.
Fig. 225 Throttle Valve Cable at Transmission
1 - TRANSMISSION SHIFTER CABLE
2 - THROTTLE VALVE CABLE
3 - TRANSFER CASE SHIFTER CABLE
4 - TRANSFER CASE SHIFTER CABLE BRACKET RETAINING
BOLT(1OR2)
5 - THROTTLE VALVE CABLE BRACKET RETAINING BOLT
6 - ELECTRICAL CONNECTORS
7 - TRANSMISSION FLUID LINES
Fig. 226 Throttle Valve Cable at Throttle Linkage
1 - THROTTLE LINKAGE
2 - THROTTLE VALVE CABLE LOCKING CLIP
3 - THROTTLE VALVE CABLE
Fig. 224 Throttle Valve Cable Attachment - At
Engine
1 - THROTTLE VALVE CABLE
2 - CABLE BRACKET
3 - THROTTLE BODY LEVER
4 - ACCELERATOR CABLE
5 - SPEED CONTROL CABLE
21 - 254 AUTOMATIC TRANSMISSION - 48REDR
THROTTLE VALVE CABLE (Continued)
Page 1965 of 2627
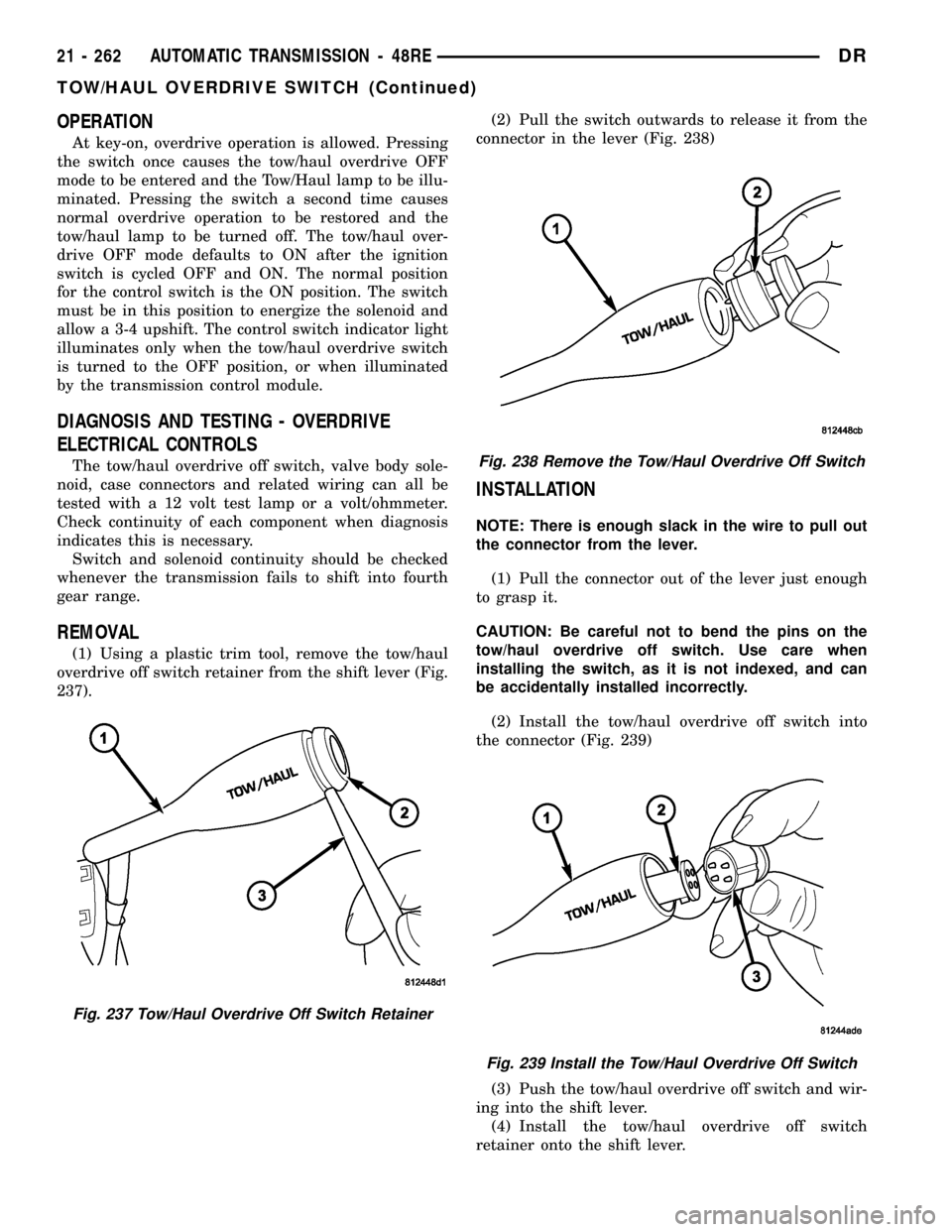
OPERATION
At key-on, overdrive operation is allowed. Pressing
the switch once causes the tow/haul overdrive OFF
mode to be entered and the Tow/Haul lamp to be illu-
minated. Pressing the switch a second time causes
normal overdrive operation to be restored and the
tow/haul lamp to be turned off. The tow/haul over-
drive OFF mode defaults to ON after the ignition
switch is cycled OFF and ON. The normal position
for the control switch is the ON position. The switch
must be in this position to energize the solenoid and
allow a 3-4 upshift. The control switch indicator light
illuminates only when the tow/haul overdrive switch
is turned to the OFF position, or when illuminated
by the transmission control module.
DIAGNOSIS AND TESTING - OVERDRIVE
ELECTRICAL CONTROLS
The tow/haul overdrive off switch, valve body sole-
noid, case connectors and related wiring can all be
tested with a 12 volt test lamp or a volt/ohmmeter.
Check continuity of each component when diagnosis
indicates this is necessary.
Switch and solenoid continuity should be checked
whenever the transmission fails to shift into fourth
gear range.
REMOVAL
(1) Using a plastic trim tool, remove the tow/haul
overdrive off switch retainer from the shift lever (Fig.
237).(2) Pull the switch outwards to release it from the
connector in the lever (Fig. 238)
INSTALLATION
NOTE: There is enough slack in the wire to pull out
the connector from the lever.
(1) Pull the connector out of the lever just enough
to grasp it.
CAUTION: Be careful not to bend the pins on the
tow/haul overdrive off switch. Use care when
installing the switch, as it is not indexed, and can
be accidentally installed incorrectly.
(2) Install the tow/haul overdrive off switch into
the connector (Fig. 239)
(3) Push the tow/haul overdrive off switch and wir-
ing into the shift lever.
(4) Install the tow/haul overdrive off switch
retainer onto the shift lever.
Fig. 237 Tow/Haul Overdrive Off Switch Retainer
Fig. 238 Remove the Tow/Haul Overdrive Off Switch
Fig. 239 Install the Tow/Haul Overdrive Off Switch
21 - 262 AUTOMATIC TRANSMISSION - 48REDR
TOW/HAUL OVERDRIVE SWITCH (Continued)
Page 2187 of 2627
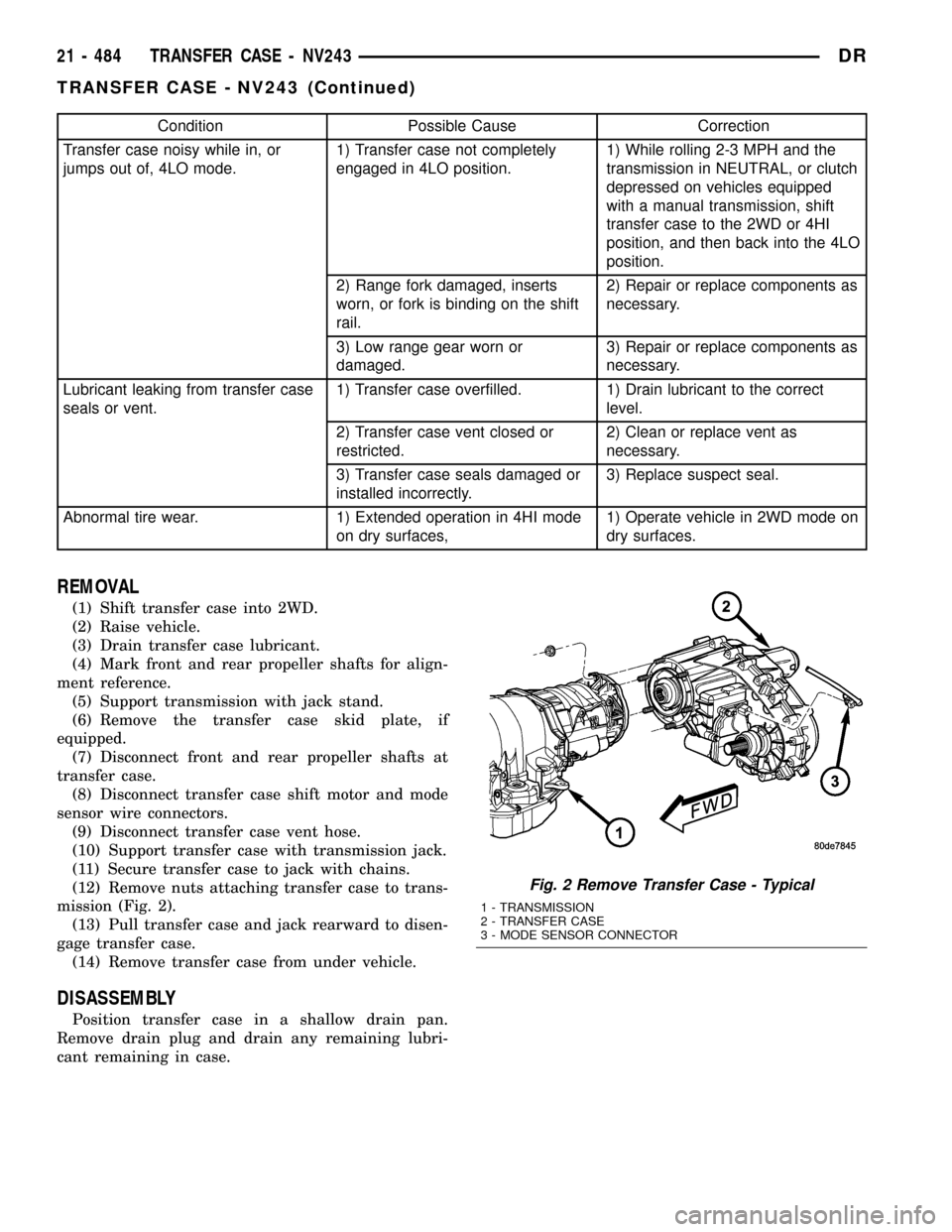
Condition Possible Cause Correction
Transfer case noisy while in, or
jumps out of, 4LO mode.1) Transfer case not completely
engaged in 4LO position.1) While rolling 2-3 MPH and the
transmission in NEUTRAL, or clutch
depressed on vehicles equipped
with a manual transmission, shift
transfer case to the 2WD or 4HI
position, and then back into the 4LO
position.
2) Range fork damaged, inserts
worn, or fork is binding on the shift
rail.2) Repair or replace components as
necessary.
3) Low range gear worn or
damaged.3) Repair or replace components as
necessary.
Lubricant leaking from transfer case
seals or vent.1) Transfer case overfilled. 1) Drain lubricant to the correct
level.
2) Transfer case vent closed or
restricted.2) Clean or replace vent as
necessary.
3) Transfer case seals damaged or
installed incorrectly.3) Replace suspect seal.
Abnormal tire wear. 1) Extended operation in 4HI mode
on dry surfaces,1) Operate vehicle in 2WD mode on
dry surfaces.
REMOVAL
(1) Shift transfer case into 2WD.
(2) Raise vehicle.
(3) Drain transfer case lubricant.
(4) Mark front and rear propeller shafts for align-
ment reference.
(5) Support transmission with jack stand.
(6) Remove the transfer case skid plate, if
equipped.
(7) Disconnect front and rear propeller shafts at
transfer case.
(8) Disconnect transfer case shift motor and mode
sensor wire connectors.
(9) Disconnect transfer case vent hose.
(10) Support transfer case with transmission jack.
(11) Secure transfer case to jack with chains.
(12) Remove nuts attaching transfer case to trans-
mission (Fig. 2).
(13) Pull transfer case and jack rearward to disen-
gage transfer case.
(14) Remove transfer case from under vehicle.
DISASSEMBLY
Position transfer case in a shallow drain pan.
Remove drain plug and drain any remaining lubri-
cant remaining in case.
Fig. 2 Remove Transfer Case - Typical
1 - TRANSMISSION
2 - TRANSFER CASE
3 - MODE SENSOR CONNECTOR
21 - 484 TRANSFER CASE - NV243DR
TRANSFER CASE - NV243 (Continued)
Page 2208 of 2627
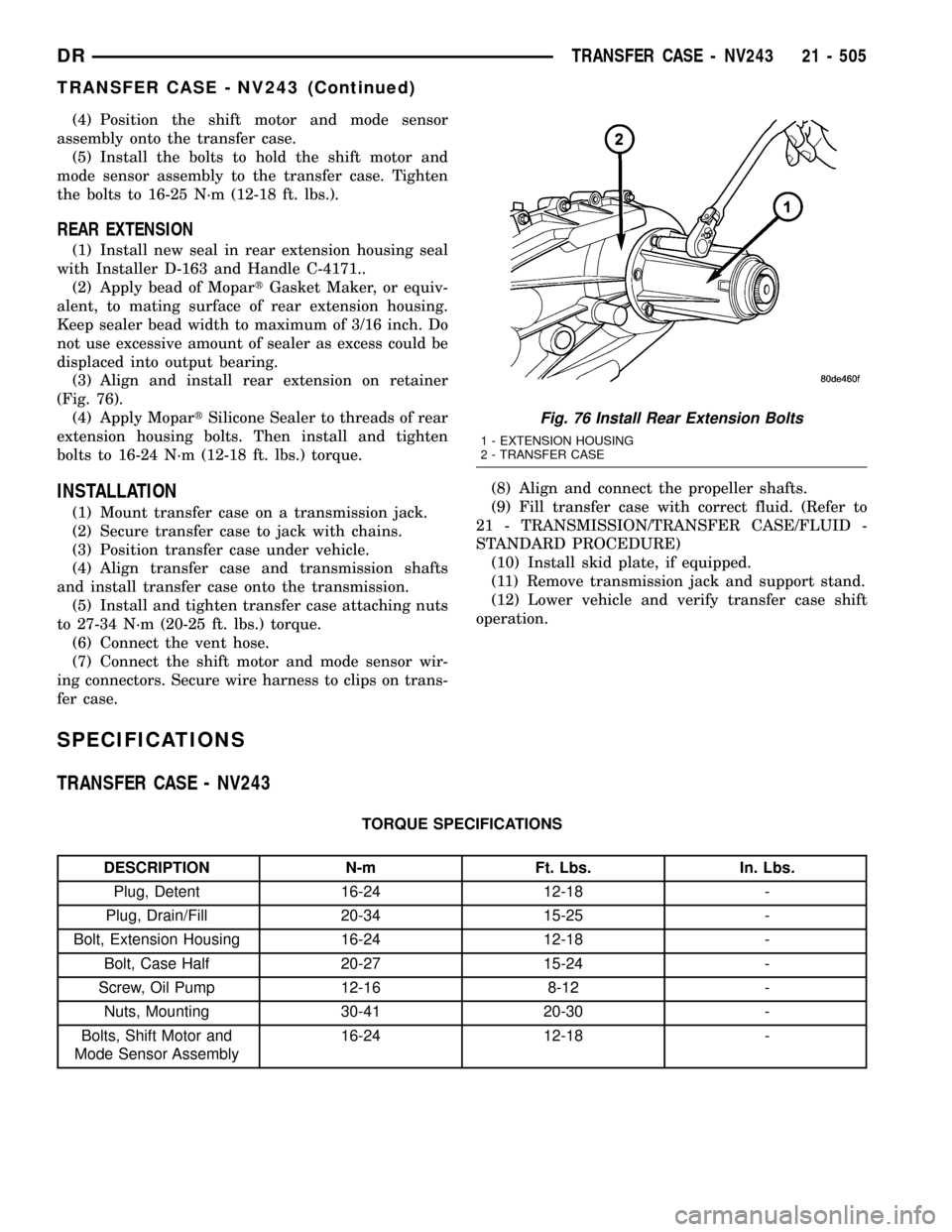
(4) Position the shift motor and mode sensor
assembly onto the transfer case.
(5) Install the bolts to hold the shift motor and
mode sensor assembly to the transfer case. Tighten
the bolts to 16-25 N´m (12-18 ft. lbs.).
REAR EXTENSION
(1) Install new seal in rear extension housing seal
with Installer D-163 and Handle C-4171..
(2) Apply bead of MopartGasket Maker, or equiv-
alent, to mating surface of rear extension housing.
Keep sealer bead width to maximum of 3/16 inch. Do
not use excessive amount of sealer as excess could be
displaced into output bearing.
(3) Align and install rear extension on retainer
(Fig. 76).
(4) Apply MopartSilicone Sealer to threads of rear
extension housing bolts. Then install and tighten
bolts to 16-24 N´m (12-18 ft. lbs.) torque.
INSTALLATION
(1) Mount transfer case on a transmission jack.
(2) Secure transfer case to jack with chains.
(3) Position transfer case under vehicle.
(4) Align transfer case and transmission shafts
and install transfer case onto the transmission.
(5) Install and tighten transfer case attaching nuts
to 27-34 N´m (20-25 ft. lbs.) torque.
(6) Connect the vent hose.
(7) Connect the shift motor and mode sensor wir-
ing connectors. Secure wire harness to clips on trans-
fer case.(8) Align and connect the propeller shafts.
(9) Fill transfer case with correct fluid. (Refer to
21 - TRANSMISSION/TRANSFER CASE/FLUID -
STANDARD PROCEDURE)
(10) Install skid plate, if equipped.
(11) Remove transmission jack and support stand.
(12) Lower vehicle and verify transfer case shift
operation.
SPECIFICATIONS
TRANSFER CASE - NV243
TORQUE SPECIFICATIONS
DESCRIPTION N-m Ft. Lbs. In. Lbs.
Plug, Detent 16-24 12-18 -
Plug, Drain/Fill 20-34 15-25 -
Bolt, Extension Housing 16-24 12-18 -
Bolt, Case Half 20-27 15-24 -
Screw, Oil Pump 12-16 8-12 -
Nuts, Mounting 30-41 20-30 -
Bolts, Shift Motor and
Mode Sensor Assembly16-24 12-18 -
Fig. 76 Install Rear Extension Bolts
1 - EXTENSION HOUSING
2 - TRANSFER CASE
DRTRANSFER CASE - NV243 21 - 505
TRANSFER CASE - NV243 (Continued)
Page 2214 of 2627
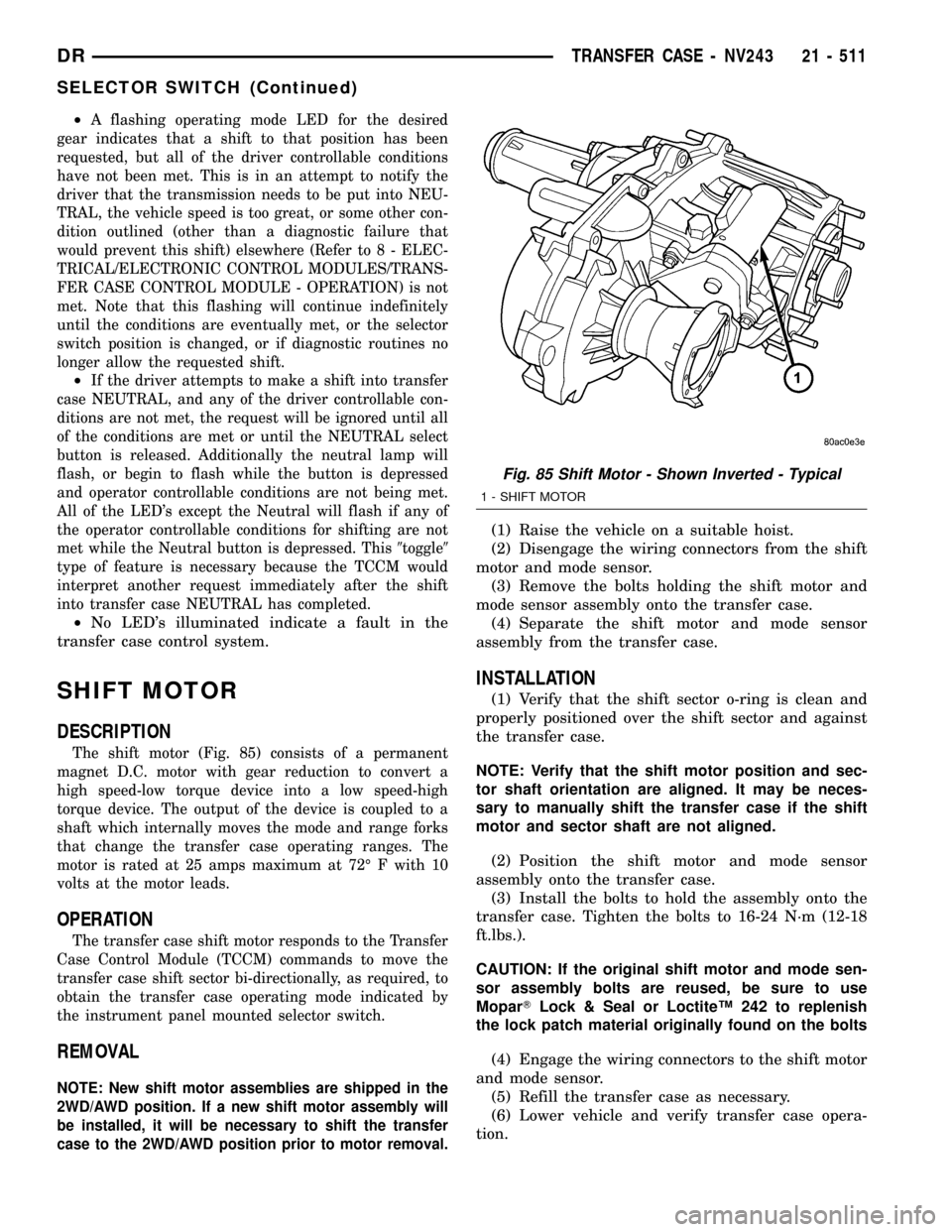
²A flashing operating mode LED for the desired
gear indicates that a shift to that position has been
requested, but all of the driver controllable conditions
have not been met. This is in an attempt to notify the
driver that the transmission needs to be put into NEU-
TRAL, the vehicle speed is too great, or some other con-
dition outlined (other than a diagnostic failure that
would prevent this shift) elsewhere (Refer to 8 - ELEC-
TRICAL/ELECTRONIC CONTROL MODULES/TRANS-
FER CASE CONTROL MODULE - OPERATION) is not
met. Note that this flashing will continue indefinitely
until the conditions are eventually met, or the selector
switch position is changed, or if diagnostic routines no
longer allow the requested shift.
²If the driver attempts to make a shift into transfer
case NEUTRAL, and any of the driver controllable con-
ditions are not met, the request will be ignored until all
of the conditions are met or until the NEUTRAL select
button is released. Additionally the neutral lamp will
flash, or begin to flash while the button is depressed
and operator controllable conditions are not being met.
All of the LED's except the Neutral will flash if any of
the operator controllable conditions for shifting are not
met while the Neutral button is depressed. This9toggle9
type of feature is necessary because the TCCM would
interpret another request immediately after the shift
into transfer case NEUTRAL has completed.
²No LED's illuminated indicate a fault in the
transfer case control system.
SHIFT MOTOR
DESCRIPTION
The shift motor (Fig. 85) consists of a permanent
magnet D.C. motor with gear reduction to convert a
high speed-low torque device into a low speed-high
torque device. The output of the device is coupled to a
shaft which internally moves the mode and range forks
that change the transfer case operating ranges. The
motor is rated at 25 amps maximum at 72É F with 10
volts at the motor leads.
OPERATION
The transfer case shift motor responds to the Transfer
Case Control Module (TCCM) commands to move the
transfer case shift sector bi-directionally, as required, to
obtain the transfer case operating mode indicated by
the instrument panel mounted selector switch.
REMOVAL
NOTE: New shift motor assemblies are shipped in the
2WD/AWD position. If a new shift motor assembly will
be installed, it will be necessary to shift the transfer
case to the 2WD/AWD position prior to motor removal.
(1) Raise the vehicle on a suitable hoist.
(2) Disengage the wiring connectors from the shift
motor and mode sensor.
(3) Remove the bolts holding the shift motor and
mode sensor assembly onto the transfer case.
(4) Separate the shift motor and mode sensor
assembly from the transfer case.
INSTALLATION
(1) Verify that the shift sector o-ring is clean and
properly positioned over the shift sector and against
the transfer case.
NOTE: Verify that the shift motor position and sec-
tor shaft orientation are aligned. It may be neces-
sary to manually shift the transfer case if the shift
motor and sector shaft are not aligned.
(2) Position the shift motor and mode sensor
assembly onto the transfer case.
(3) Install the bolts to hold the assembly onto the
transfer case. Tighten the bolts to 16-24 N´m (12-18
ft.lbs.).
CAUTION: If the original shift motor and mode sen-
sor assembly bolts are reused, be sure to use
MoparTLock & Seal or LoctiteŸ 242 to replenish
the lock patch material originally found on the bolts
(4) Engage the wiring connectors to the shift motor
and mode sensor.
(5) Refill the transfer case as necessary.
(6) Lower vehicle and verify transfer case opera-
tion.
Fig. 85 Shift Motor - Shown Inverted - Typical
1 - SHIFT MOTOR
DRTRANSFER CASE - NV243 21 - 511
SELECTOR SWITCH (Continued)
Page 2217 of 2627
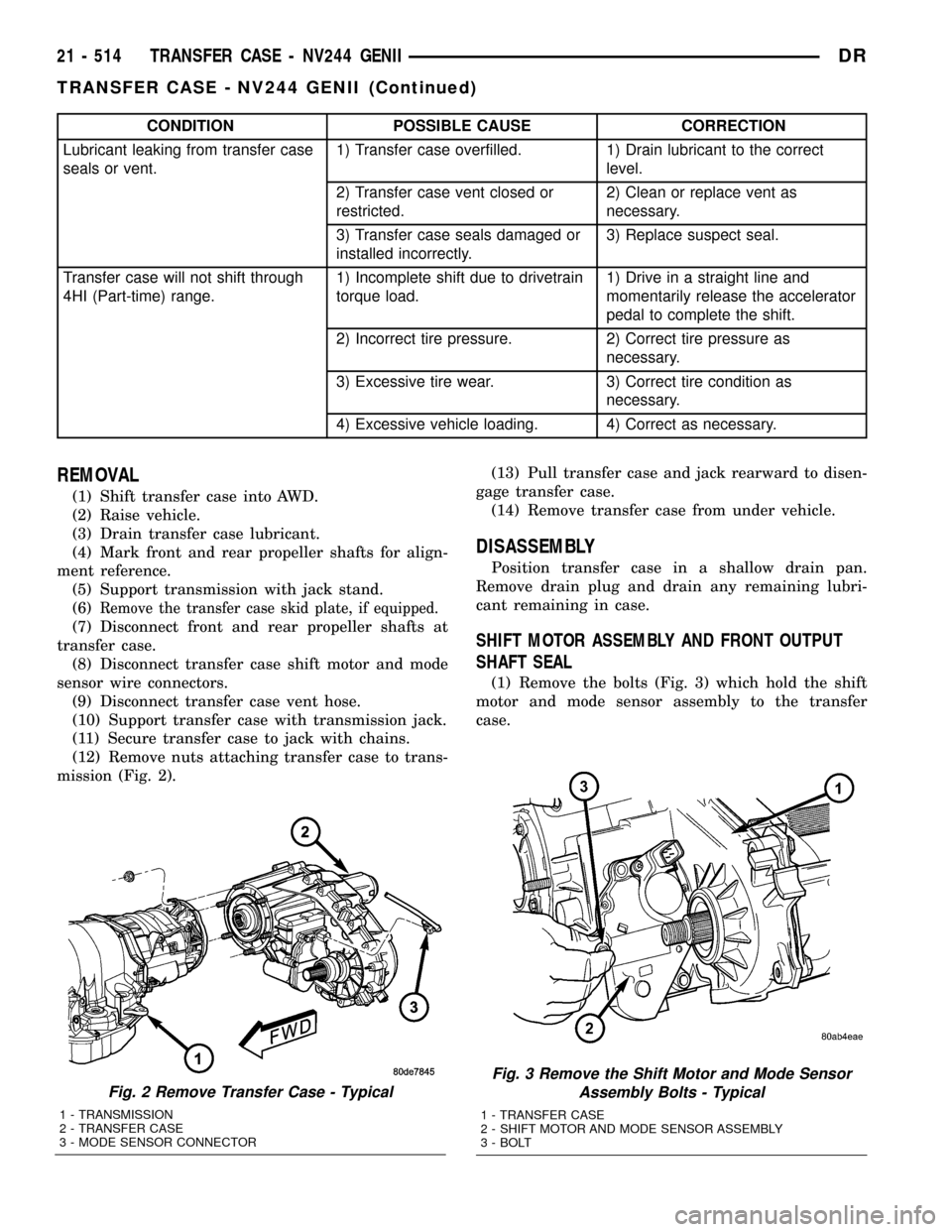
CONDITION POSSIBLE CAUSE CORRECTION
Lubricant leaking from transfer case
seals or vent.1) Transfer case overfilled. 1) Drain lubricant to the correct
level.
2) Transfer case vent closed or
restricted.2) Clean or replace vent as
necessary.
3) Transfer case seals damaged or
installed incorrectly.3) Replace suspect seal.
Transfer case will not shift through
4HI (Part-time) range.1) Incomplete shift due to drivetrain
torque load.1) Drive in a straight line and
momentarily release the accelerator
pedal to complete the shift.
2) Incorrect tire pressure. 2) Correct tire pressure as
necessary.
3) Excessive tire wear. 3) Correct tire condition as
necessary.
4) Excessive vehicle loading. 4) Correct as necessary.
REMOVAL
(1) Shift transfer case into AWD.
(2) Raise vehicle.
(3) Drain transfer case lubricant.
(4) Mark front and rear propeller shafts for align-
ment reference.
(5) Support transmission with jack stand.
(6)
Remove the transfer case skid plate, if equipped.
(7) Disconnect front and rear propeller shafts at
transfer case.
(8) Disconnect transfer case shift motor and mode
sensor wire connectors.
(9) Disconnect transfer case vent hose.
(10) Support transfer case with transmission jack.
(11) Secure transfer case to jack with chains.
(12) Remove nuts attaching transfer case to trans-
mission (Fig. 2).(13) Pull transfer case and jack rearward to disen-
gage transfer case.
(14) Remove transfer case from under vehicle.
DISASSEMBLY
Position transfer case in a shallow drain pan.
Remove drain plug and drain any remaining lubri-
cant remaining in case.
SHIFT MOTOR ASSEMBLY AND FRONT OUTPUT
SHAFT SEAL
(1) Remove the bolts (Fig. 3) which hold the shift
motor and mode sensor assembly to the transfer
case.
Fig. 2 Remove Transfer Case - Typical
1 - TRANSMISSION
2 - TRANSFER CASE
3 - MODE SENSOR CONNECTOR
Fig. 3 Remove the Shift Motor and Mode Sensor
Assembly Bolts - Typical
1 - TRANSFER CASE
2 - SHIFT MOTOR AND MODE SENSOR ASSEMBLY
3 - BOLT
21 - 514 TRANSFER CASE - NV244 GENIIDR
TRANSFER CASE - NV244 GENII (Continued)
Page 2237 of 2627
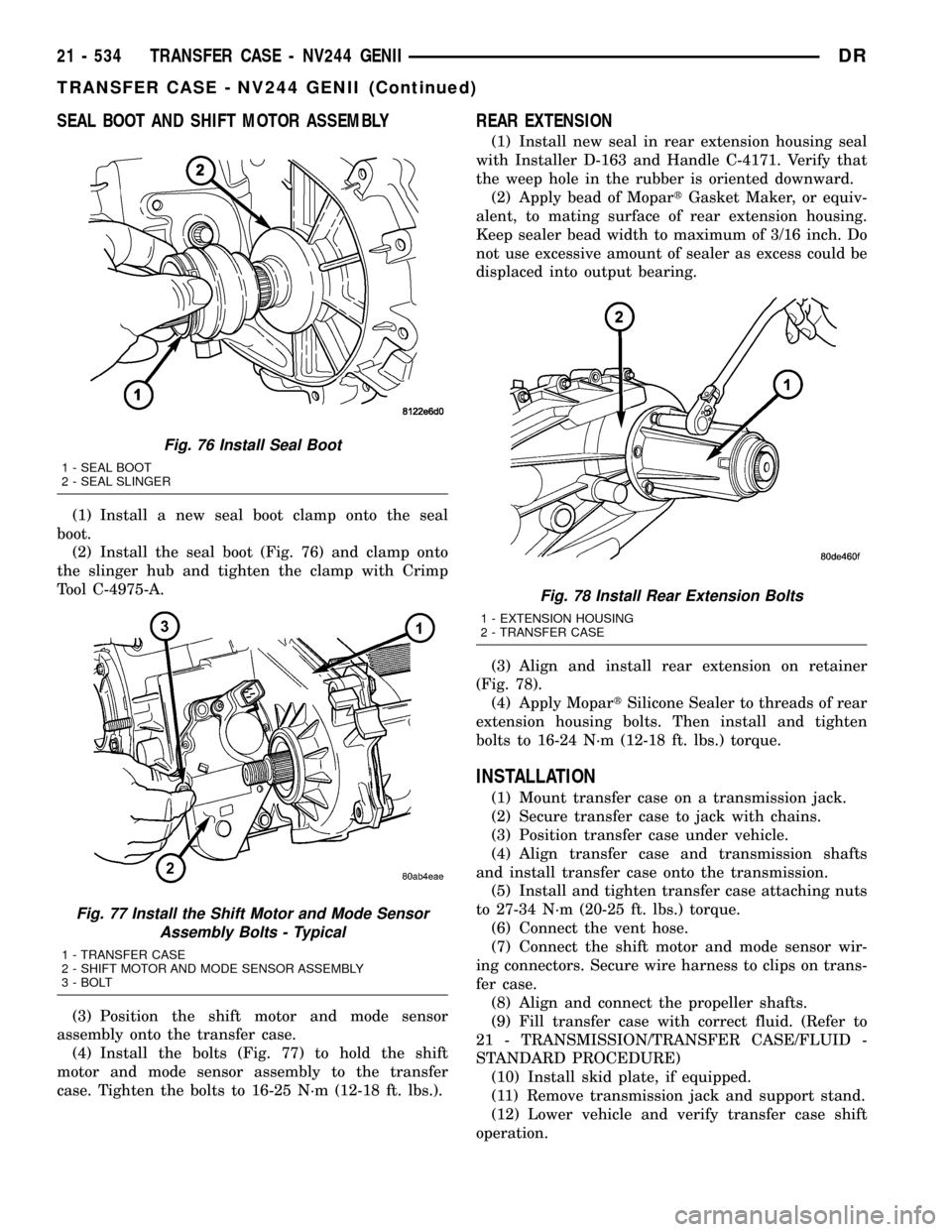
SEAL BOOT AND SHIFT MOTOR ASSEMBLY
(1) Install a new seal boot clamp onto the seal
boot.
(2) Install the seal boot (Fig. 76) and clamp onto
the slinger hub and tighten the clamp with Crimp
Tool C-4975-A.
(3) Position the shift motor and mode sensor
assembly onto the transfer case.
(4) Install the bolts (Fig. 77) to hold the shift
motor and mode sensor assembly to the transfer
case. Tighten the bolts to 16-25 N´m (12-18 ft. lbs.).
REAR EXTENSION
(1) Install new seal in rear extension housing seal
with Installer D-163 and Handle C-4171. Verify that
the weep hole in the rubber is oriented downward.
(2) Apply bead of MopartGasket Maker, or equiv-
alent, to mating surface of rear extension housing.
Keep sealer bead width to maximum of 3/16 inch. Do
not use excessive amount of sealer as excess could be
displaced into output bearing.
(3) Align and install rear extension on retainer
(Fig. 78).
(4) Apply MopartSilicone Sealer to threads of rear
extension housing bolts. Then install and tighten
bolts to 16-24 N´m (12-18 ft. lbs.) torque.
INSTALLATION
(1) Mount transfer case on a transmission jack.
(2) Secure transfer case to jack with chains.
(3) Position transfer case under vehicle.
(4) Align transfer case and transmission shafts
and install transfer case onto the transmission.
(5) Install and tighten transfer case attaching nuts
to 27-34 N´m (20-25 ft. lbs.) torque.
(6) Connect the vent hose.
(7) Connect the shift motor and mode sensor wir-
ing connectors. Secure wire harness to clips on trans-
fer case.
(8) Align and connect the propeller shafts.
(9) Fill transfer case with correct fluid. (Refer to
21 - TRANSMISSION/TRANSFER CASE/FLUID -
STANDARD PROCEDURE)
(10) Install skid plate, if equipped.
(11) Remove transmission jack and support stand.
(12) Lower vehicle and verify transfer case shift
operation.
Fig. 76 Install Seal Boot
1 - SEAL BOOT
2 - SEAL SLINGER
Fig. 77 Install the Shift Motor and Mode Sensor
Assembly Bolts - Typical
1 - TRANSFER CASE
2 - SHIFT MOTOR AND MODE SENSOR ASSEMBLY
3 - BOLT
Fig. 78 Install Rear Extension Bolts
1 - EXTENSION HOUSING
2 - TRANSFER CASE
21 - 534 TRANSFER CASE - NV244 GENIIDR
TRANSFER CASE - NV244 GENII (Continued)
Page 2244 of 2627
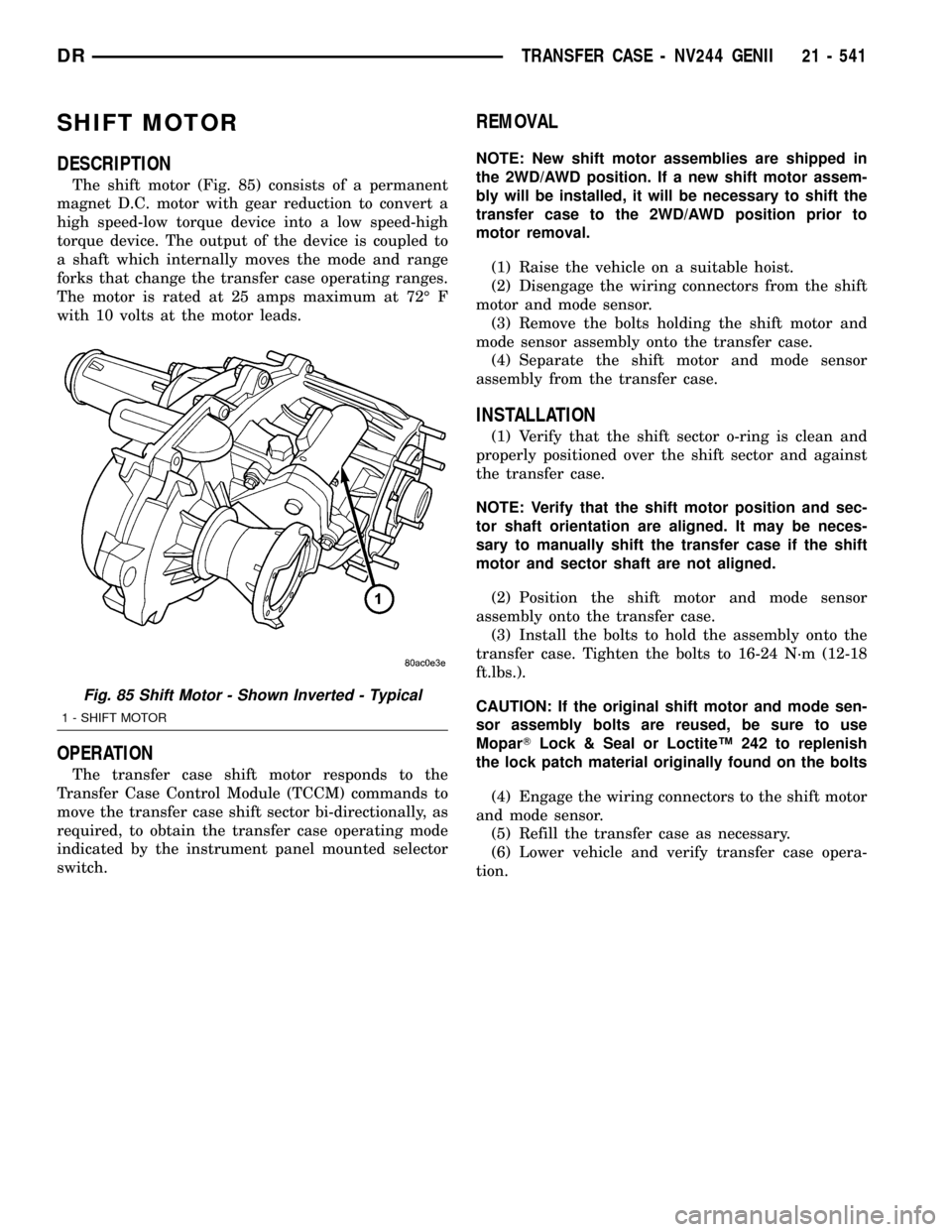
SHIFT MOTOR
DESCRIPTION
The shift motor (Fig. 85) consists of a permanent
magnet D.C. motor with gear reduction to convert a
high speed-low torque device into a low speed-high
torque device. The output of the device is coupled to
a shaft which internally moves the mode and range
forks that change the transfer case operating ranges.
The motor is rated at 25 amps maximum at 72É F
with 10 volts at the motor leads.
OPERATION
The transfer case shift motor responds to the
Transfer Case Control Module (TCCM) commands to
move the transfer case shift sector bi-directionally, as
required, to obtain the transfer case operating mode
indicated by the instrument panel mounted selector
switch.
REMOVAL
NOTE: New shift motor assemblies are shipped in
the 2WD/AWD position. If a new shift motor assem-
bly will be installed, it will be necessary to shift the
transfer case to the 2WD/AWD position prior to
motor removal.
(1) Raise the vehicle on a suitable hoist.
(2) Disengage the wiring connectors from the shift
motor and mode sensor.
(3) Remove the bolts holding the shift motor and
mode sensor assembly onto the transfer case.
(4) Separate the shift motor and mode sensor
assembly from the transfer case.
INSTALLATION
(1) Verify that the shift sector o-ring is clean and
properly positioned over the shift sector and against
the transfer case.
NOTE: Verify that the shift motor position and sec-
tor shaft orientation are aligned. It may be neces-
sary to manually shift the transfer case if the shift
motor and sector shaft are not aligned.
(2) Position the shift motor and mode sensor
assembly onto the transfer case.
(3) Install the bolts to hold the assembly onto the
transfer case. Tighten the bolts to 16-24 N´m (12-18
ft.lbs.).
CAUTION: If the original shift motor and mode sen-
sor assembly bolts are reused, be sure to use
MoparTLock & Seal or LoctiteŸ 242 to replenish
the lock patch material originally found on the bolts
(4) Engage the wiring connectors to the shift motor
and mode sensor.
(5) Refill the transfer case as necessary.
(6) Lower vehicle and verify transfer case opera-
tion.
Fig. 85 Shift Motor - Shown Inverted - Typical
1 - SHIFT MOTOR
DRTRANSFER CASE - NV244 GENII 21 - 541