DODGE RAM 1500 1998 2.G Workshop Manual
Manufacturer: DODGE, Model Year: 1998, Model line: RAM 1500, Model: DODGE RAM 1500 1998 2.GPages: 2627
Page 2091 of 2627
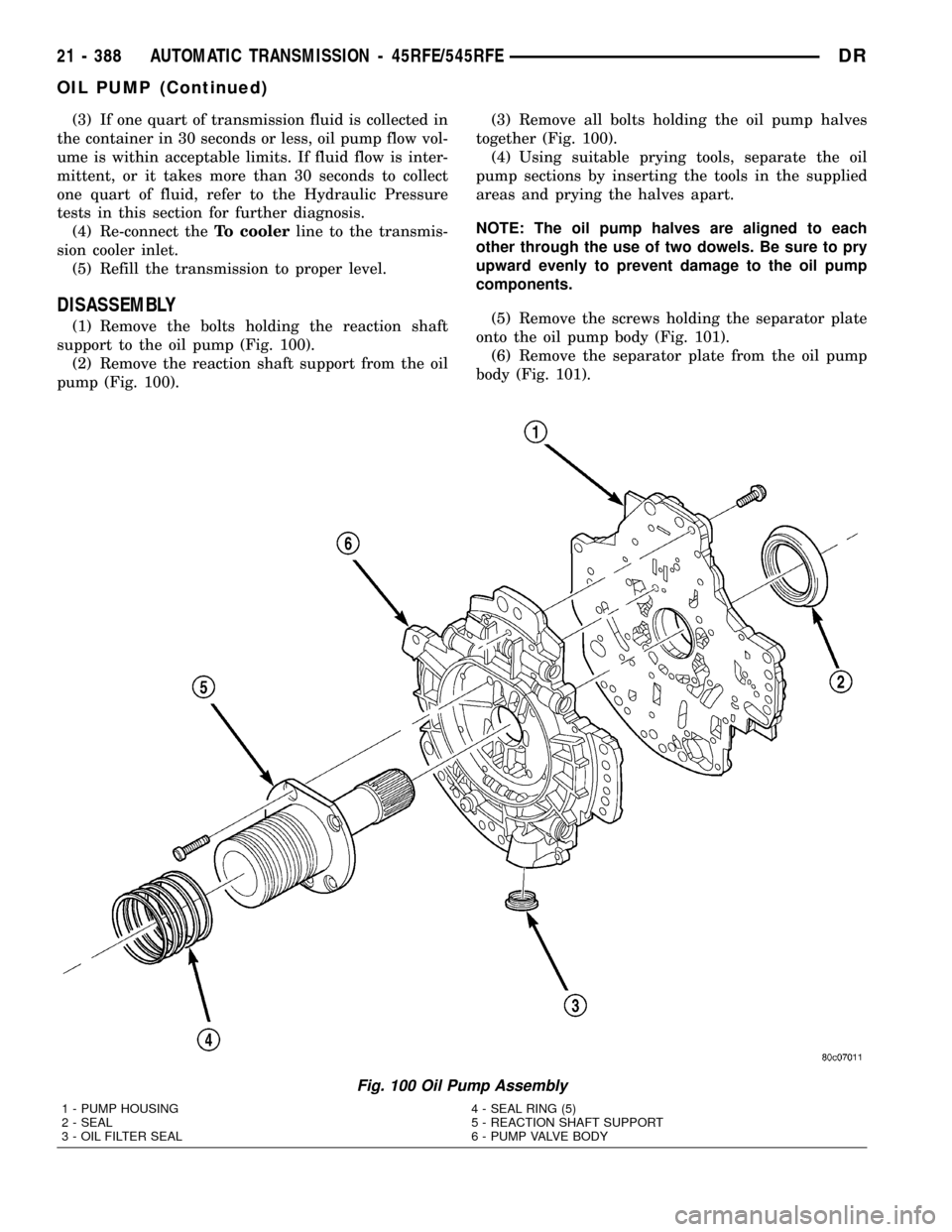
(3) If one quart of transmission fluid is collected in
the container in 30 seconds or less, oil pump flow vol-
ume is within acceptable limits. If fluid flow is inter-
mittent, or it takes more than 30 seconds to collect
one quart of fluid, refer to the Hydraulic Pressure
tests in this section for further diagnosis.
(4) Re-connect theTo coolerline to the transmis-
sion cooler inlet.
(5) Refill the transmission to proper level.
DISASSEMBLY
(1) Remove the bolts holding the reaction shaft
support to the oil pump (Fig. 100).
(2) Remove the reaction shaft support from the oil
pump (Fig. 100).(3) Remove all bolts holding the oil pump halves
together (Fig. 100).
(4) Using suitable prying tools, separate the oil
pump sections by inserting the tools in the supplied
areas and prying the halves apart.
NOTE: The oil pump halves are aligned to each
other through the use of two dowels. Be sure to pry
upward evenly to prevent damage to the oil pump
components.
(5) Remove the screws holding the separator plate
onto the oil pump body (Fig. 101).
(6) Remove the separator plate from the oil pump
body (Fig. 101).
Fig. 100 Oil Pump Assembly
1 - PUMP HOUSING 4 - SEAL RING (5)
2 - SEAL 5 - REACTION SHAFT SUPPORT
3 - OIL FILTER SEAL 6 - PUMP VALVE BODY
21 - 388 AUTOMATIC TRANSMISSION - 45RFE/545RFEDR
OIL PUMP (Continued)
Page 2092 of 2627
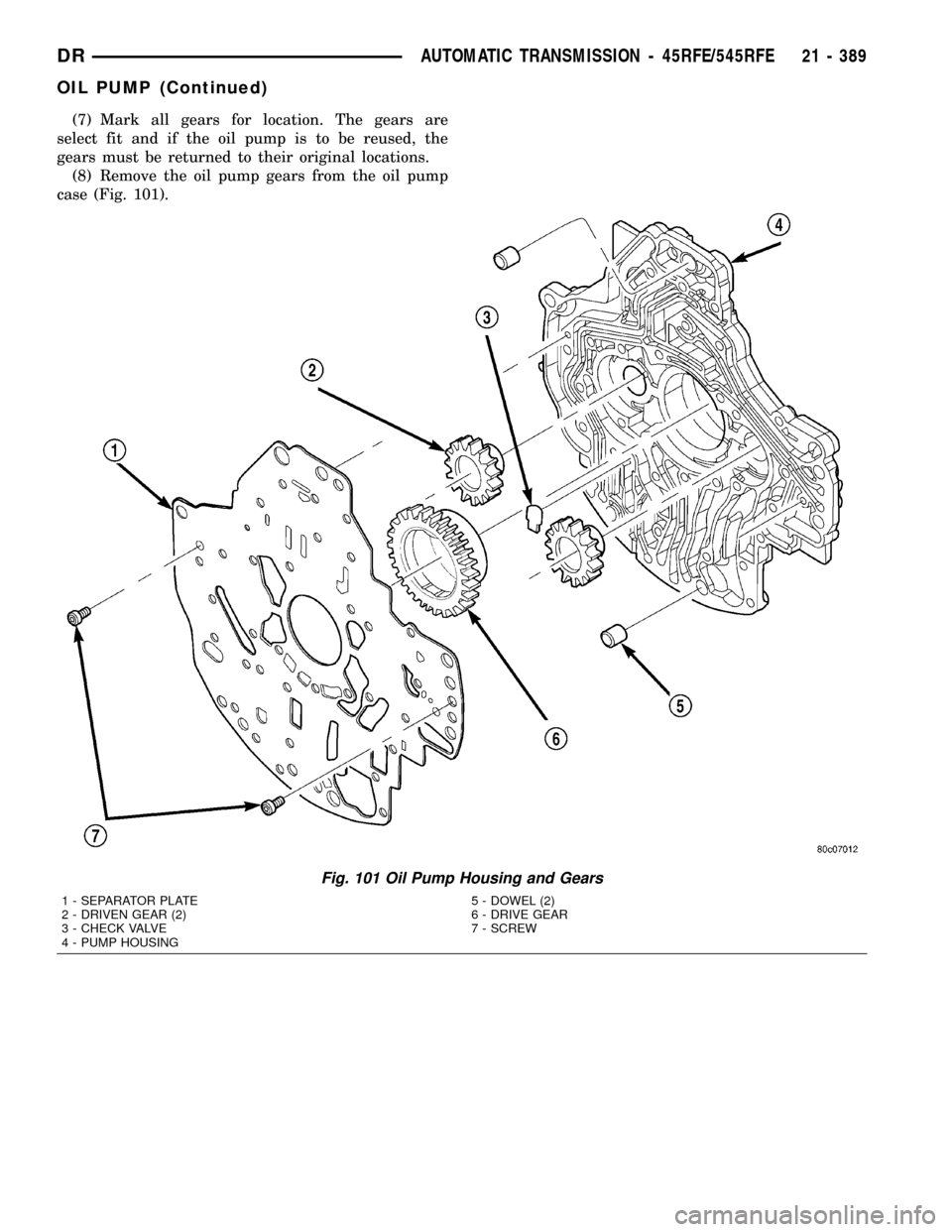
(7) Mark all gears for location. The gears are
select fit and if the oil pump is to be reused, the
gears must be returned to their original locations.
(8) Remove the oil pump gears from the oil pump
case (Fig. 101).
Fig. 101 Oil Pump Housing and Gears
1 - SEPARATOR PLATE 5 - DOWEL (2)
2 - DRIVEN GEAR (2) 6 - DRIVE GEAR
3 - CHECK VALVE 7 - SCREW
4 - PUMP HOUSING
DRAUTOMATIC TRANSMISSION - 45RFE/545RFE 21 - 389
OIL PUMP (Continued)
Page 2093 of 2627
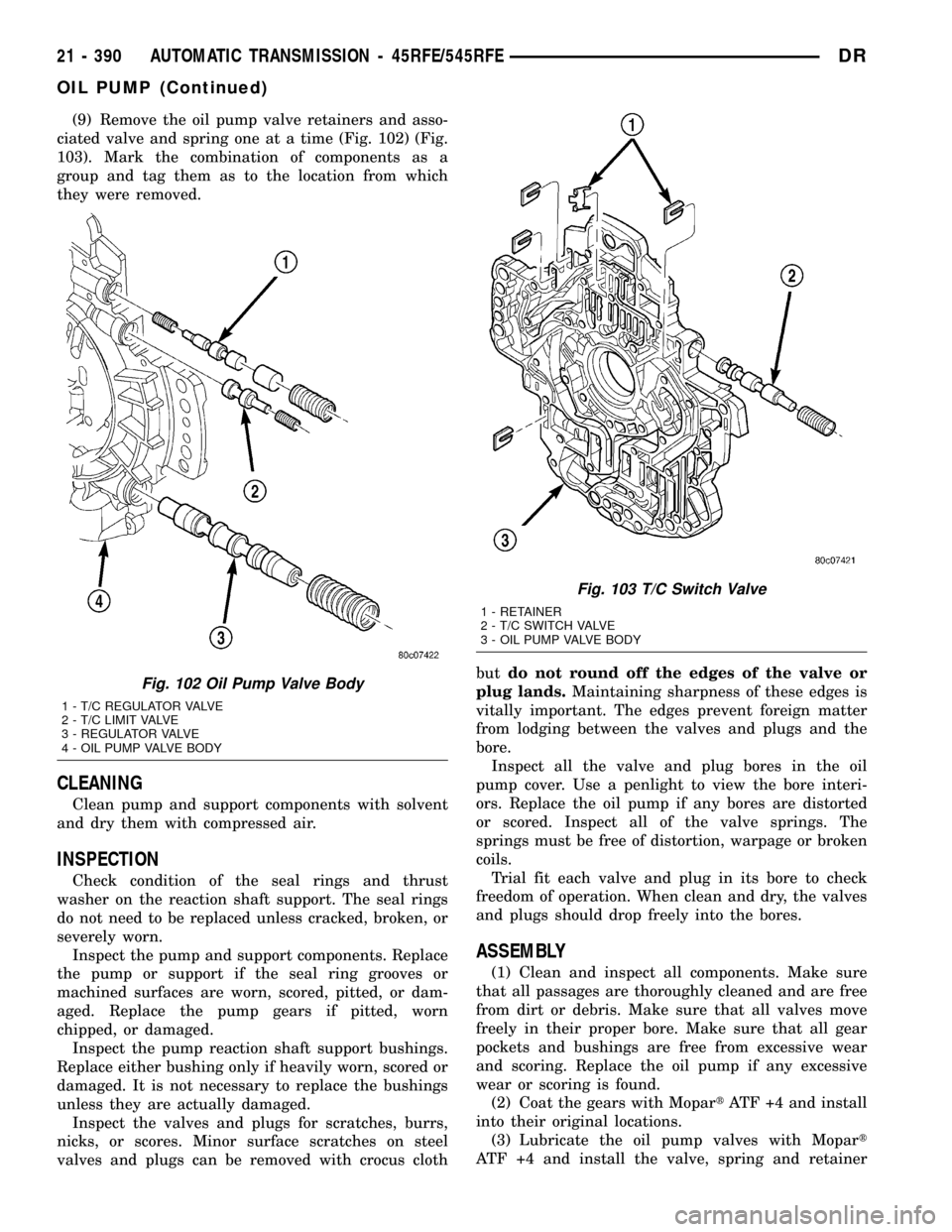
(9) Remove the oil pump valve retainers and asso-
ciated valve and spring one at a time (Fig. 102) (Fig.
103). Mark the combination of components as a
group and tag them as to the location from which
they were removed.
CLEANING
Clean pump and support components with solvent
and dry them with compressed air.
INSPECTION
Check condition of the seal rings and thrust
washer on the reaction shaft support. The seal rings
do not need to be replaced unless cracked, broken, or
severely worn.
Inspect the pump and support components. Replace
the pump or support if the seal ring grooves or
machined surfaces are worn, scored, pitted, or dam-
aged. Replace the pump gears if pitted, worn
chipped, or damaged.
Inspect the pump reaction shaft support bushings.
Replace either bushing only if heavily worn, scored or
damaged. It is not necessary to replace the bushings
unless they are actually damaged.
Inspect the valves and plugs for scratches, burrs,
nicks, or scores. Minor surface scratches on steel
valves and plugs can be removed with crocus clothbutdo not round off the edges of the valve or
plug lands.Maintaining sharpness of these edges is
vitally important. The edges prevent foreign matter
from lodging between the valves and plugs and the
bore.
Inspect all the valve and plug bores in the oil
pump cover. Use a penlight to view the bore interi-
ors. Replace the oil pump if any bores are distorted
or scored. Inspect all of the valve springs. The
springs must be free of distortion, warpage or broken
coils.
Trial fit each valve and plug in its bore to check
freedom of operation. When clean and dry, the valves
and plugs should drop freely into the bores.
ASSEMBLY
(1) Clean and inspect all components. Make sure
that all passages are thoroughly cleaned and are free
from dirt or debris. Make sure that all valves move
freely in their proper bore. Make sure that all gear
pockets and bushings are free from excessive wear
and scoring. Replace the oil pump if any excessive
wear or scoring is found.
(2) Coat the gears with MopartATF +4 and install
into their original locations.
(3) Lubricate the oil pump valves with Mopart
ATF +4 and install the valve, spring and retainer
Fig. 102 Oil Pump Valve Body
1 - T/C REGULATOR VALVE
2 - T/C LIMIT VALVE
3 - REGULATOR VALVE
4 - OIL PUMP VALVE BODY
Fig. 103 T/C Switch Valve
1 - RETAINER
2 - T/C SWITCH VALVE
3 - OIL PUMP VALVE BODY
21 - 390 AUTOMATIC TRANSMISSION - 45RFE/545RFEDR
OIL PUMP (Continued)
Page 2094 of 2627
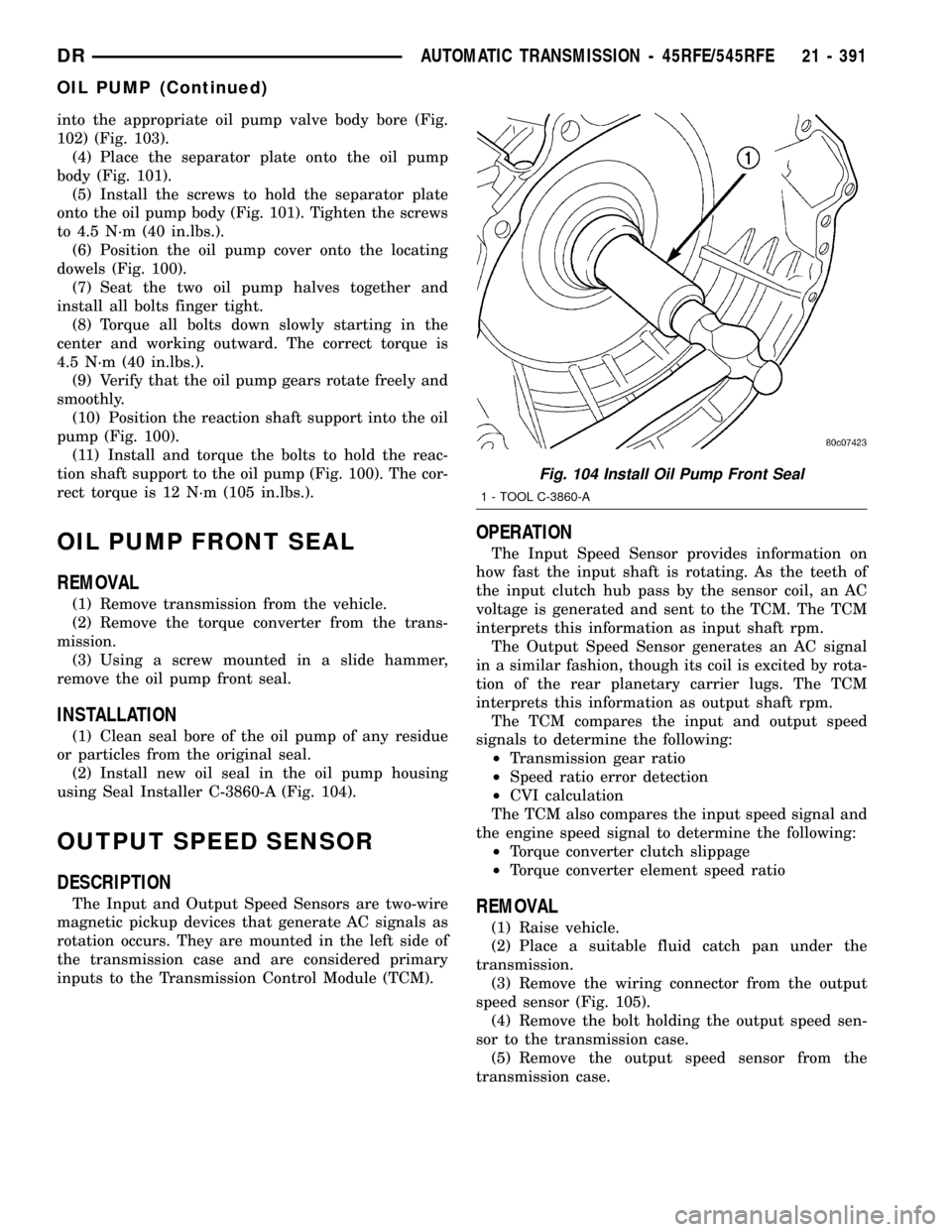
into the appropriate oil pump valve body bore (Fig.
102) (Fig. 103).
(4) Place the separator plate onto the oil pump
body (Fig. 101).
(5) Install the screws to hold the separator plate
onto the oil pump body (Fig. 101). Tighten the screws
to 4.5 N´m (40 in.lbs.).
(6) Position the oil pump cover onto the locating
dowels (Fig. 100).
(7) Seat the two oil pump halves together and
install all bolts finger tight.
(8) Torque all bolts down slowly starting in the
center and working outward. The correct torque is
4.5 N´m (40 in.lbs.).
(9) Verify that the oil pump gears rotate freely and
smoothly.
(10) Position the reaction shaft support into the oil
pump (Fig. 100).
(11) Install and torque the bolts to hold the reac-
tion shaft support to the oil pump (Fig. 100). The cor-
rect torque is 12 N´m (105 in.lbs.).
OIL PUMP FRONT SEAL
REMOVAL
(1) Remove transmission from the vehicle.
(2) Remove the torque converter from the trans-
mission.
(3) Using a screw mounted in a slide hammer,
remove the oil pump front seal.
INSTALLATION
(1) Clean seal bore of the oil pump of any residue
or particles from the original seal.
(2) Install new oil seal in the oil pump housing
using Seal Installer C-3860-A (Fig. 104).
OUTPUT SPEED SENSOR
DESCRIPTION
The Input and Output Speed Sensors are two-wire
magnetic pickup devices that generate AC signals as
rotation occurs. They are mounted in the left side of
the transmission case and are considered primary
inputs to the Transmission Control Module (TCM).
OPERATION
The Input Speed Sensor provides information on
how fast the input shaft is rotating. As the teeth of
the input clutch hub pass by the sensor coil, an AC
voltage is generated and sent to the TCM. The TCM
interprets this information as input shaft rpm.
The Output Speed Sensor generates an AC signal
in a similar fashion, though its coil is excited by rota-
tion of the rear planetary carrier lugs. The TCM
interprets this information as output shaft rpm.
The TCM compares the input and output speed
signals to determine the following:
²Transmission gear ratio
²Speed ratio error detection
²CVI calculation
The TCM also compares the input speed signal and
the engine speed signal to determine the following:
²Torque converter clutch slippage
²Torque converter element speed ratio
REMOVAL
(1) Raise vehicle.
(2) Place a suitable fluid catch pan under the
transmission.
(3) Remove the wiring connector from the output
speed sensor (Fig. 105).
(4) Remove the bolt holding the output speed sen-
sor to the transmission case.
(5) Remove the output speed sensor from the
transmission case.
Fig. 104 Install Oil Pump Front Seal
1 - TOOL C-3860-A
DRAUTOMATIC TRANSMISSION - 45RFE/545RFE 21 - 391
OIL PUMP (Continued)
Page 2095 of 2627
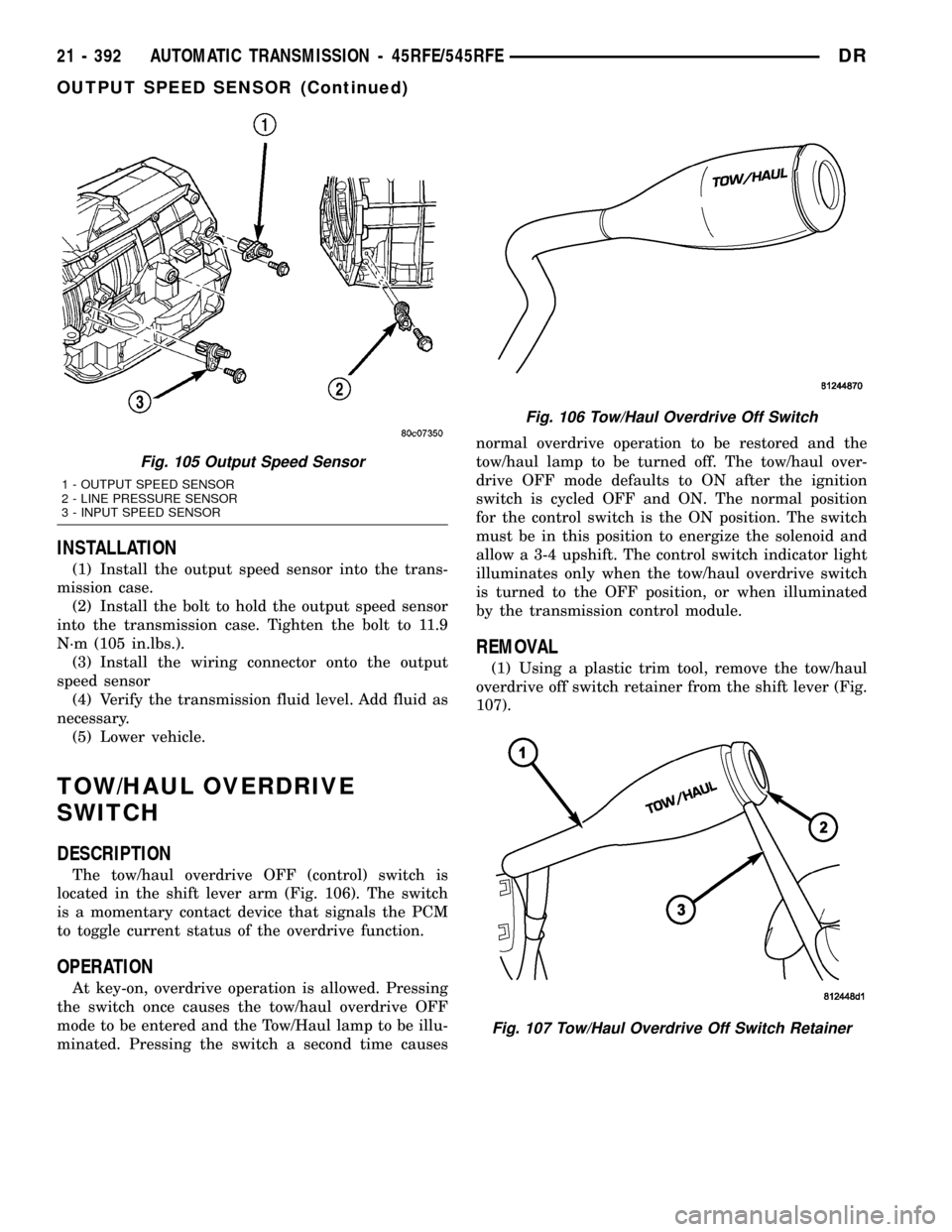
INSTALLATION
(1) Install the output speed sensor into the trans-
mission case.
(2) Install the bolt to hold the output speed sensor
into the transmission case. Tighten the bolt to 11.9
N´m (105 in.lbs.).
(3) Install the wiring connector onto the output
speed sensor
(4) Verify the transmission fluid level. Add fluid as
necessary.
(5) Lower vehicle.
TOW/HAUL OVERDRIVE
SWITCH
DESCRIPTION
The tow/haul overdrive OFF (control) switch is
located in the shift lever arm (Fig. 106). The switch
is a momentary contact device that signals the PCM
to toggle current status of the overdrive function.
OPERATION
At key-on, overdrive operation is allowed. Pressing
the switch once causes the tow/haul overdrive OFF
mode to be entered and the Tow/Haul lamp to be illu-
minated. Pressing the switch a second time causesnormal overdrive operation to be restored and the
tow/haul lamp to be turned off. The tow/haul over-
drive OFF mode defaults to ON after the ignition
switch is cycled OFF and ON. The normal position
for the control switch is the ON position. The switch
must be in this position to energize the solenoid and
allow a 3-4 upshift. The control switch indicator light
illuminates only when the tow/haul overdrive switch
is turned to the OFF position, or when illuminated
by the transmission control module.
REMOVAL
(1) Using a plastic trim tool, remove the tow/haul
overdrive off switch retainer from the shift lever (Fig.
107).
Fig. 105 Output Speed Sensor
1 - OUTPUT SPEED SENSOR
2 - LINE PRESSURE SENSOR
3 - INPUT SPEED SENSOR
Fig. 106 Tow/Haul Overdrive Off Switch
Fig. 107 Tow/Haul Overdrive Off Switch Retainer
21 - 392 AUTOMATIC TRANSMISSION - 45RFE/545RFEDR
OUTPUT SPEED SENSOR (Continued)
Page 2096 of 2627
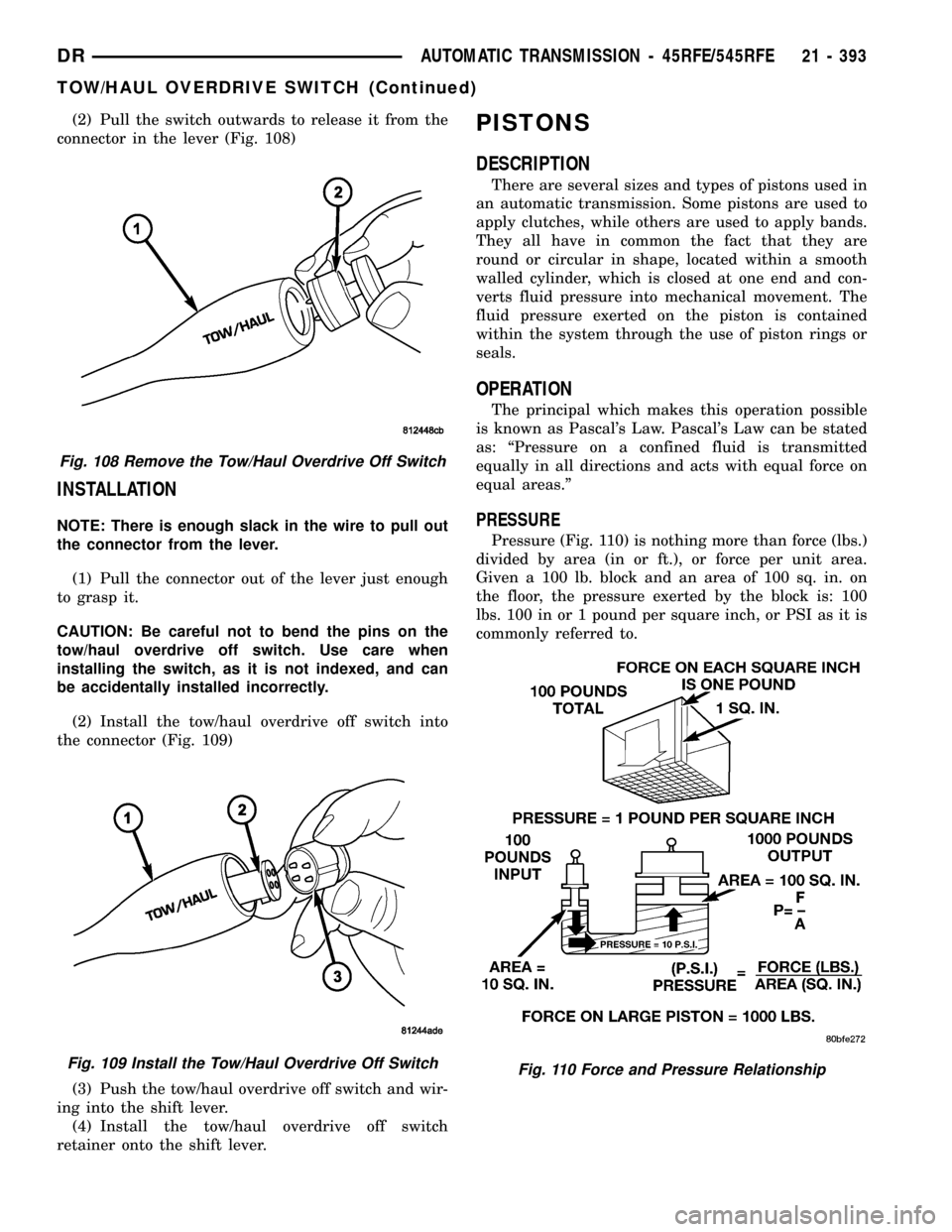
(2) Pull the switch outwards to release it from the
connector in the lever (Fig. 108)
INSTALLATION
NOTE: There is enough slack in the wire to pull out
the connector from the lever.
(1) Pull the connector out of the lever just enough
to grasp it.
CAUTION: Be careful not to bend the pins on the
tow/haul overdrive off switch. Use care when
installing the switch, as it is not indexed, and can
be accidentally installed incorrectly.
(2) Install the tow/haul overdrive off switch into
the connector (Fig. 109)
(3) Push the tow/haul overdrive off switch and wir-
ing into the shift lever.
(4) Install the tow/haul overdrive off switch
retainer onto the shift lever.
PISTONS
DESCRIPTION
There are several sizes and types of pistons used in
an automatic transmission. Some pistons are used to
apply clutches, while others are used to apply bands.
They all have in common the fact that they are
round or circular in shape, located within a smooth
walled cylinder, which is closed at one end and con-
verts fluid pressure into mechanical movement. The
fluid pressure exerted on the piston is contained
within the system through the use of piston rings or
seals.
OPERATION
The principal which makes this operation possible
is known as Pascal's Law. Pascal's Law can be stated
as: ªPressure on a confined fluid is transmitted
equally in all directions and acts with equal force on
equal areas.º
PRESSURE
Pressure (Fig. 110) is nothing more than force (lbs.)
divided by area (in or ft.), or force per unit area.
Given a 100 lb. block and an area of 100 sq. in. on
the floor, the pressure exerted by the block is: 100
lbs. 100 in or 1 pound per square inch, or PSI as it is
commonly referred to.
Fig. 108 Remove the Tow/Haul Overdrive Off Switch
Fig. 109 Install the Tow/Haul Overdrive Off SwitchFig. 110 Force and Pressure Relationship
DRAUTOMATIC TRANSMISSION - 45RFE/545RFE 21 - 393
TOW/HAUL OVERDRIVE SWITCH (Continued)
Page 2097 of 2627
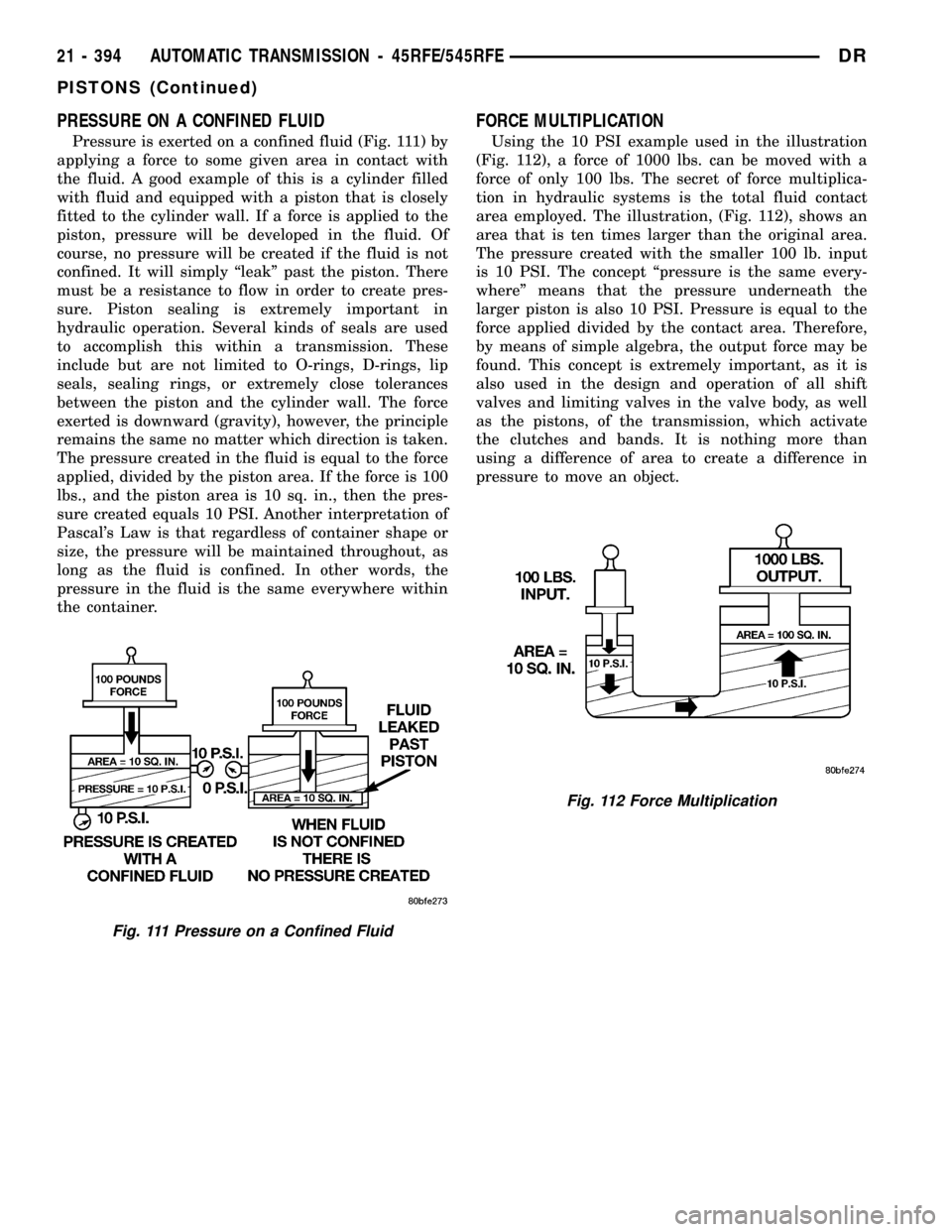
PRESSURE ON A CONFINED FLUID
Pressure is exerted on a confined fluid (Fig. 111) by
applying a force to some given area in contact with
the fluid. A good example of this is a cylinder filled
with fluid and equipped with a piston that is closely
fitted to the cylinder wall. If a force is applied to the
piston, pressure will be developed in the fluid. Of
course, no pressure will be created if the fluid is not
confined. It will simply ªleakº past the piston. There
must be a resistance to flow in order to create pres-
sure. Piston sealing is extremely important in
hydraulic operation. Several kinds of seals are used
to accomplish this within a transmission. These
include but are not limited to O-rings, D-rings, lip
seals, sealing rings, or extremely close tolerances
between the piston and the cylinder wall. The force
exerted is downward (gravity), however, the principle
remains the same no matter which direction is taken.
The pressure created in the fluid is equal to the force
applied, divided by the piston area. If the force is 100
lbs., and the piston area is 10 sq. in., then the pres-
sure created equals 10 PSI. Another interpretation of
Pascal's Law is that regardless of container shape or
size, the pressure will be maintained throughout, as
long as the fluid is confined. In other words, the
pressure in the fluid is the same everywhere within
the container.
FORCE MULTIPLICATION
Using the 10 PSI example used in the illustration
(Fig. 112), a force of 1000 lbs. can be moved with a
force of only 100 lbs. The secret of force multiplica-
tion in hydraulic systems is the total fluid contact
area employed. The illustration, (Fig. 112), shows an
area that is ten times larger than the original area.
The pressure created with the smaller 100 lb. input
is 10 PSI. The concept ªpressure is the same every-
whereº means that the pressure underneath the
larger piston is also 10 PSI. Pressure is equal to the
force applied divided by the contact area. Therefore,
by means of simple algebra, the output force may be
found. This concept is extremely important, as it is
also used in the design and operation of all shift
valves and limiting valves in the valve body, as well
as the pistons, of the transmission, which activate
the clutches and bands. It is nothing more than
using a difference of area to create a difference in
pressure to move an object.
Fig. 111 Pressure on a Confined Fluid
Fig. 112 Force Multiplication
21 - 394 AUTOMATIC TRANSMISSION - 45RFE/545RFEDR
PISTONS (Continued)
Page 2098 of 2627
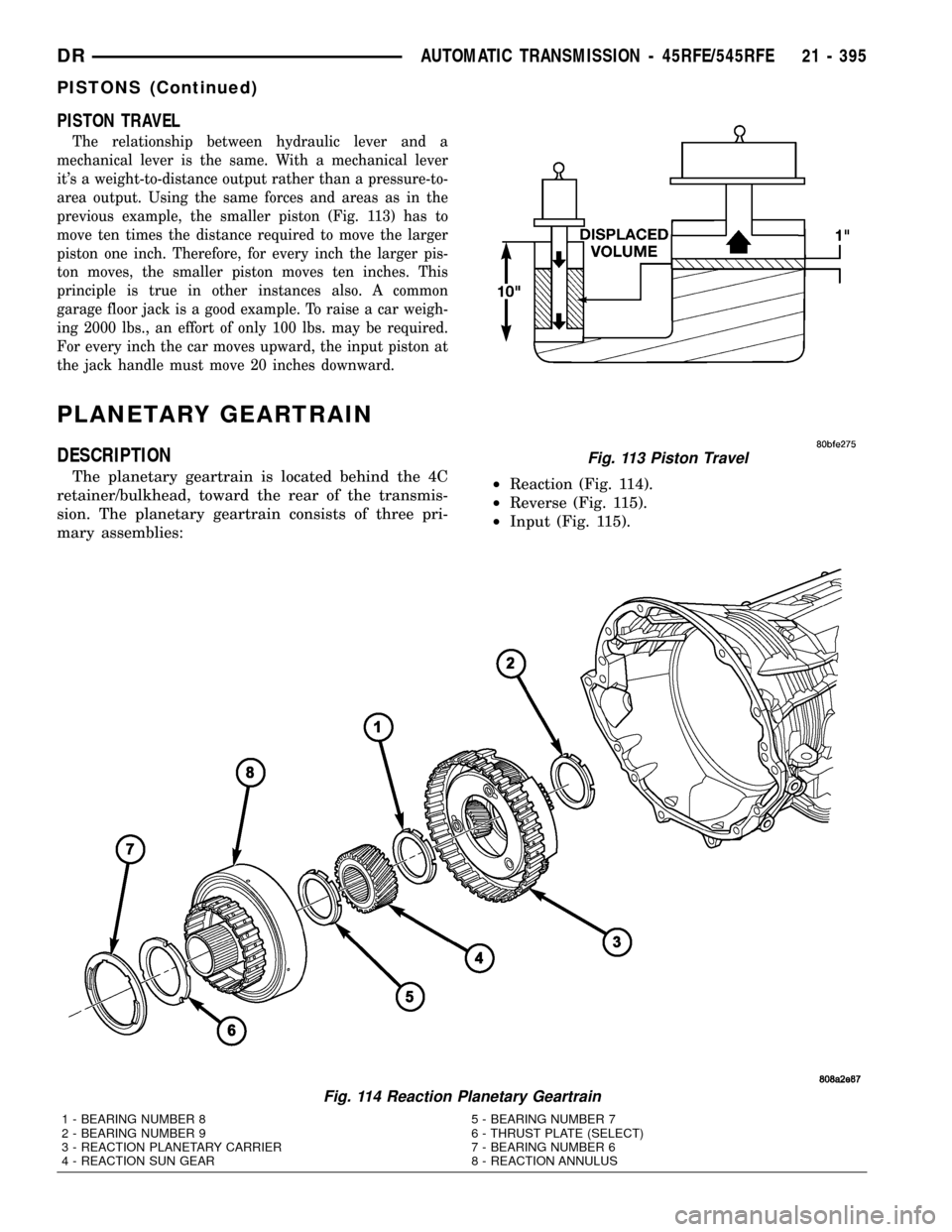
PISTON TRAVEL
The relationship between hydraulic lever and a
mechanical lever is the same. With a mechanical lever
it's a weight-to-distance output rather than a pressure-to-
area output. Using the same forces and areas as in the
previous example, the smaller piston (Fig. 113) has to
move ten times the distance required to move the larger
piston one inch. Therefore, for every inch the larger pis-
ton moves, the smaller piston moves ten inches. This
principle is true in other instances also. A common
garage floor jack is a good example. To raise a car weigh-
ing 2000 lbs., an effort of only 100 lbs. may be required.
For every inch the car moves upward, the input piston at
the jack handle must move 20 inches downward.
PLANETARY GEARTRAIN
DESCRIPTION
The planetary geartrain is located behind the 4C
retainer/bulkhead, toward the rear of the transmis-
sion. The planetary geartrain consists of three pri-
mary assemblies:²Reaction (Fig. 114).
²Reverse (Fig. 115).
²Input (Fig. 115).
Fig. 113 Piston Travel
Fig. 114 Reaction Planetary Geartrain
1 - BEARING NUMBER 8 5 - BEARING NUMBER 7
2 - BEARING NUMBER 9 6 - THRUST PLATE (SELECT)
3 - REACTION PLANETARY CARRIER 7 - BEARING NUMBER 6
4 - REACTION SUN GEAR 8 - REACTION ANNULUS
DRAUTOMATIC TRANSMISSION - 45RFE/545RFE 21 - 395
PISTONS (Continued)
Page 2099 of 2627
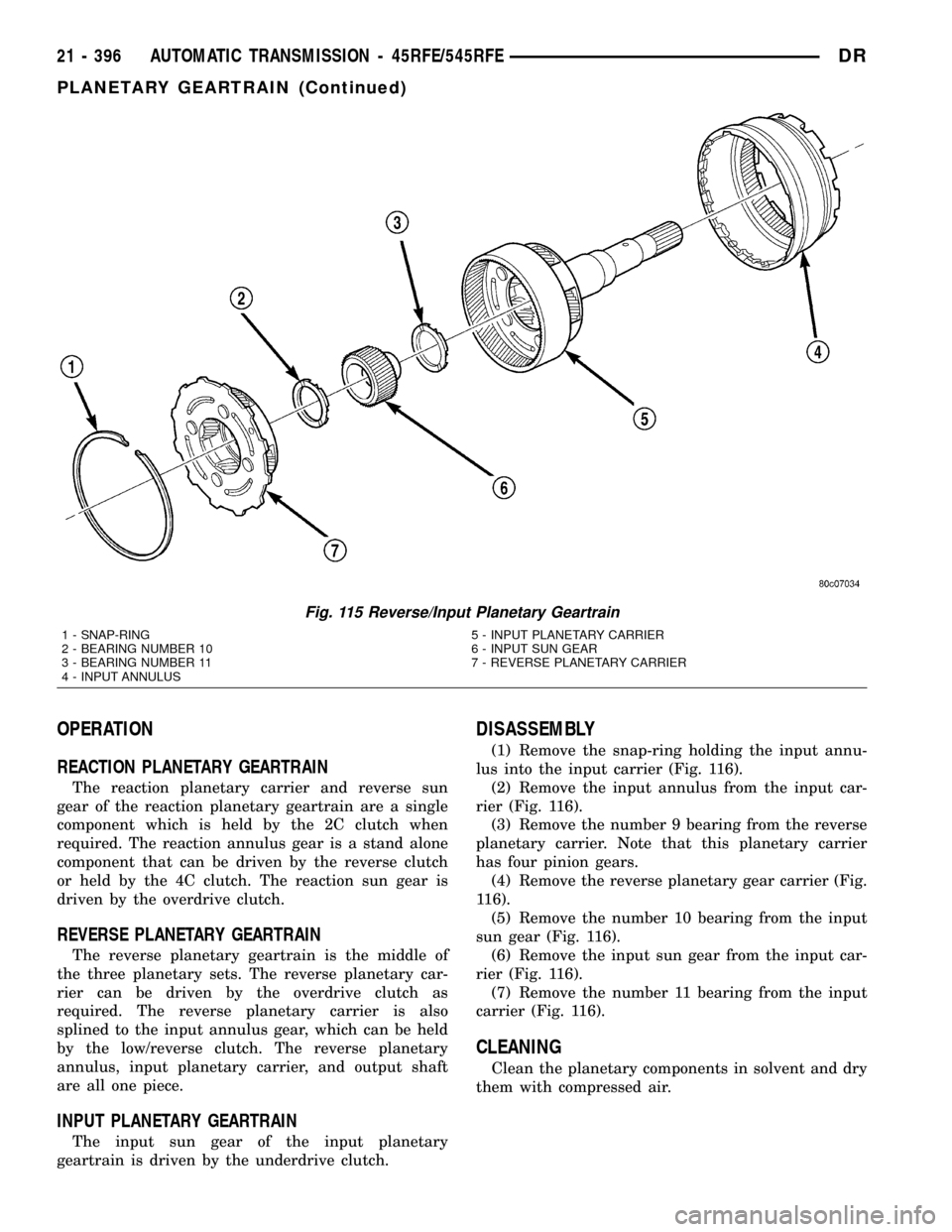
OPERATION
REACTION PLANETARY GEARTRAIN
The reaction planetary carrier and reverse sun
gear of the reaction planetary geartrain are a single
component which is held by the 2C clutch when
required. The reaction annulus gear is a stand alone
component that can be driven by the reverse clutch
or held by the 4C clutch. The reaction sun gear is
driven by the overdrive clutch.
REVERSE PLANETARY GEARTRAIN
The reverse planetary geartrain is the middle of
the three planetary sets. The reverse planetary car-
rier can be driven by the overdrive clutch as
required. The reverse planetary carrier is also
splined to the input annulus gear, which can be held
by the low/reverse clutch. The reverse planetary
annulus, input planetary carrier, and output shaft
are all one piece.
INPUT PLANETARY GEARTRAIN
The input sun gear of the input planetary
geartrain is driven by the underdrive clutch.
DISASSEMBLY
(1) Remove the snap-ring holding the input annu-
lus into the input carrier (Fig. 116).
(2) Remove the input annulus from the input car-
rier (Fig. 116).
(3) Remove the number 9 bearing from the reverse
planetary carrier. Note that this planetary carrier
has four pinion gears.
(4) Remove the reverse planetary gear carrier (Fig.
116).
(5) Remove the number 10 bearing from the input
sun gear (Fig. 116).
(6) Remove the input sun gear from the input car-
rier (Fig. 116).
(7) Remove the number 11 bearing from the input
carrier (Fig. 116).
CLEANING
Clean the planetary components in solvent and dry
them with compressed air.
Fig. 115 Reverse/Input Planetary Geartrain
1 - SNAP-RING 5 - INPUT PLANETARY CARRIER
2 - BEARING NUMBER 10 6 - INPUT SUN GEAR
3 - BEARING NUMBER 11 7 - REVERSE PLANETARY CARRIER
4 - INPUT ANNULUS
21 - 396 AUTOMATIC TRANSMISSION - 45RFE/545RFEDR
PLANETARY GEARTRAIN (Continued)
Page 2100 of 2627
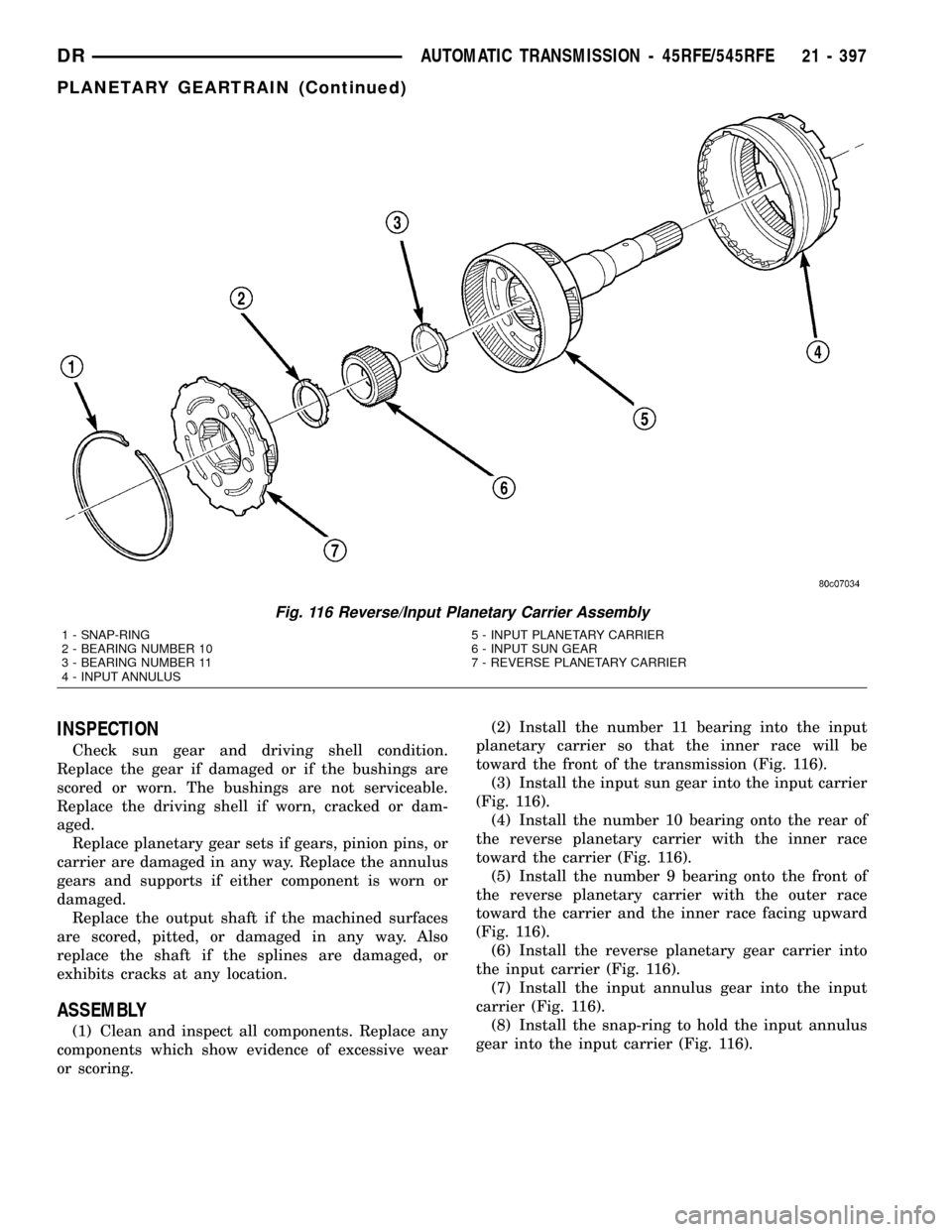
INSPECTION
Check sun gear and driving shell condition.
Replace the gear if damaged or if the bushings are
scored or worn. The bushings are not serviceable.
Replace the driving shell if worn, cracked or dam-
aged.
Replace planetary gear sets if gears, pinion pins, or
carrier are damaged in any way. Replace the annulus
gears and supports if either component is worn or
damaged.
Replace the output shaft if the machined surfaces
are scored, pitted, or damaged in any way. Also
replace the shaft if the splines are damaged, or
exhibits cracks at any location.
ASSEMBLY
(1) Clean and inspect all components. Replace any
components which show evidence of excessive wear
or scoring.(2) Install the number 11 bearing into the input
planetary carrier so that the inner race will be
toward the front of the transmission (Fig. 116).
(3) Install the input sun gear into the input carrier
(Fig. 116).
(4) Install the number 10 bearing onto the rear of
the reverse planetary carrier with the inner race
toward the carrier (Fig. 116).
(5) Install the number 9 bearing onto the front of
the reverse planetary carrier with the outer race
toward the carrier and the inner race facing upward
(Fig. 116).
(6) Install the reverse planetary gear carrier into
the input carrier (Fig. 116).
(7) Install the input annulus gear into the input
carrier (Fig. 116).
(8) Install the snap-ring to hold the input annulus
gear into the input carrier (Fig. 116).
Fig. 116 Reverse/Input Planetary Carrier Assembly
1 - SNAP-RING 5 - INPUT PLANETARY CARRIER
2 - BEARING NUMBER 10 6 - INPUT SUN GEAR
3 - BEARING NUMBER 11 7 - REVERSE PLANETARY CARRIER
4 - INPUT ANNULUS
DRAUTOMATIC TRANSMISSION - 45RFE/545RFE 21 - 397
PLANETARY GEARTRAIN (Continued)