DODGE RAM 1500 1998 2.G Workshop Manual
Manufacturer: DODGE, Model Year: 1998, Model line: RAM 1500, Model: DODGE RAM 1500 1998 2.GPages: 2627
Page 2161 of 2627
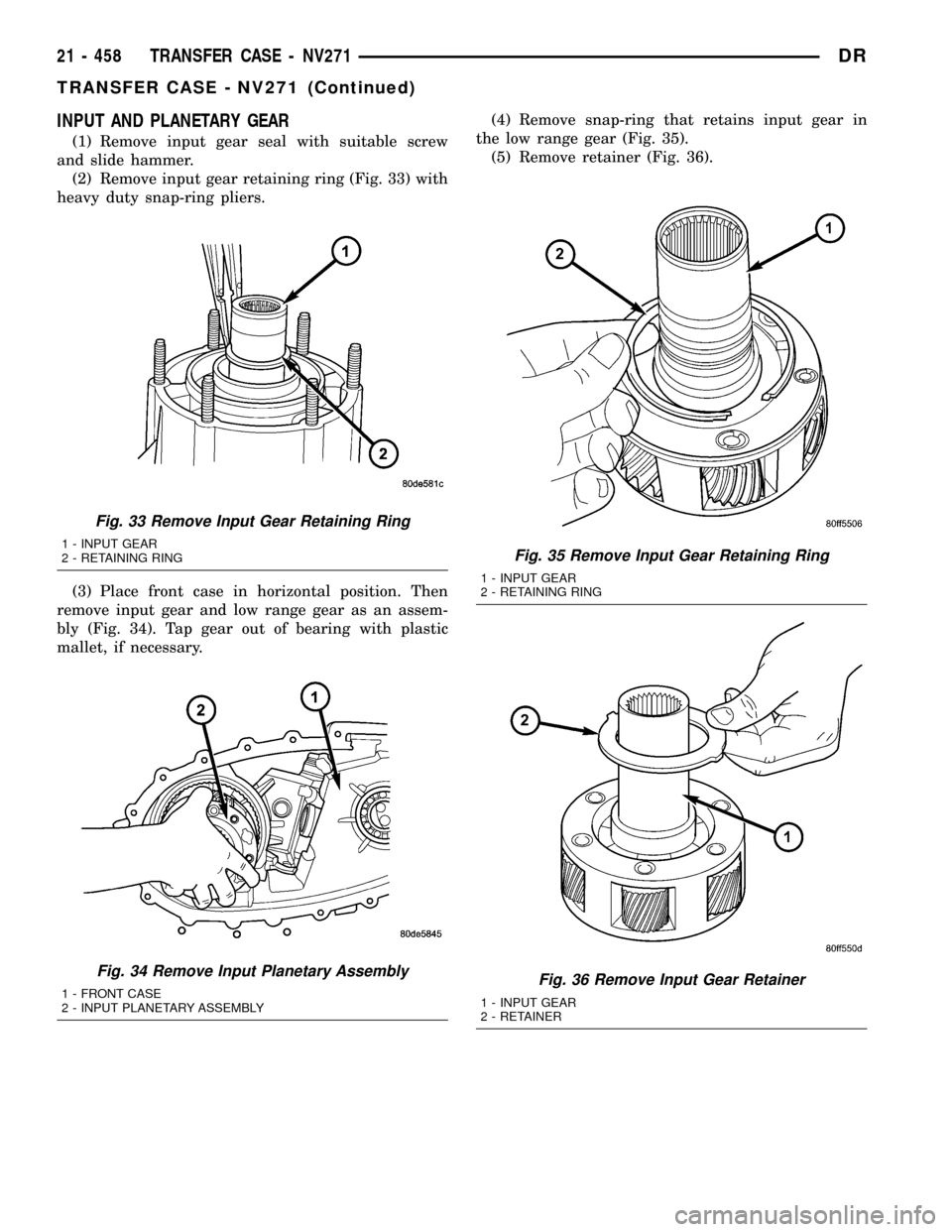
INPUT AND PLANETARY GEAR
(1) Remove input gear seal with suitable screw
and slide hammer.
(2) Remove input gear retaining ring (Fig. 33) with
heavy duty snap-ring pliers.
(3) Place front case in horizontal position. Then
remove input gear and low range gear as an assem-
bly (Fig. 34). Tap gear out of bearing with plastic
mallet, if necessary.(4) Remove snap-ring that retains input gear in
the low range gear (Fig. 35).
(5) Remove retainer (Fig. 36).
Fig. 35 Remove Input Gear Retaining Ring
1 - INPUT GEAR
2 - RETAINING RING
Fig. 36 Remove Input Gear Retainer
1 - INPUT GEAR
2 - RETAINER
Fig. 33 Remove Input Gear Retaining Ring
1 - INPUT GEAR
2 - RETAINING RING
Fig. 34 Remove Input Planetary Assembly
1 - FRONT CASE
2 - INPUT PLANETARY ASSEMBLY
21 - 458 TRANSFER CASE - NV271DR
TRANSFER CASE - NV271 (Continued)
Page 2162 of 2627
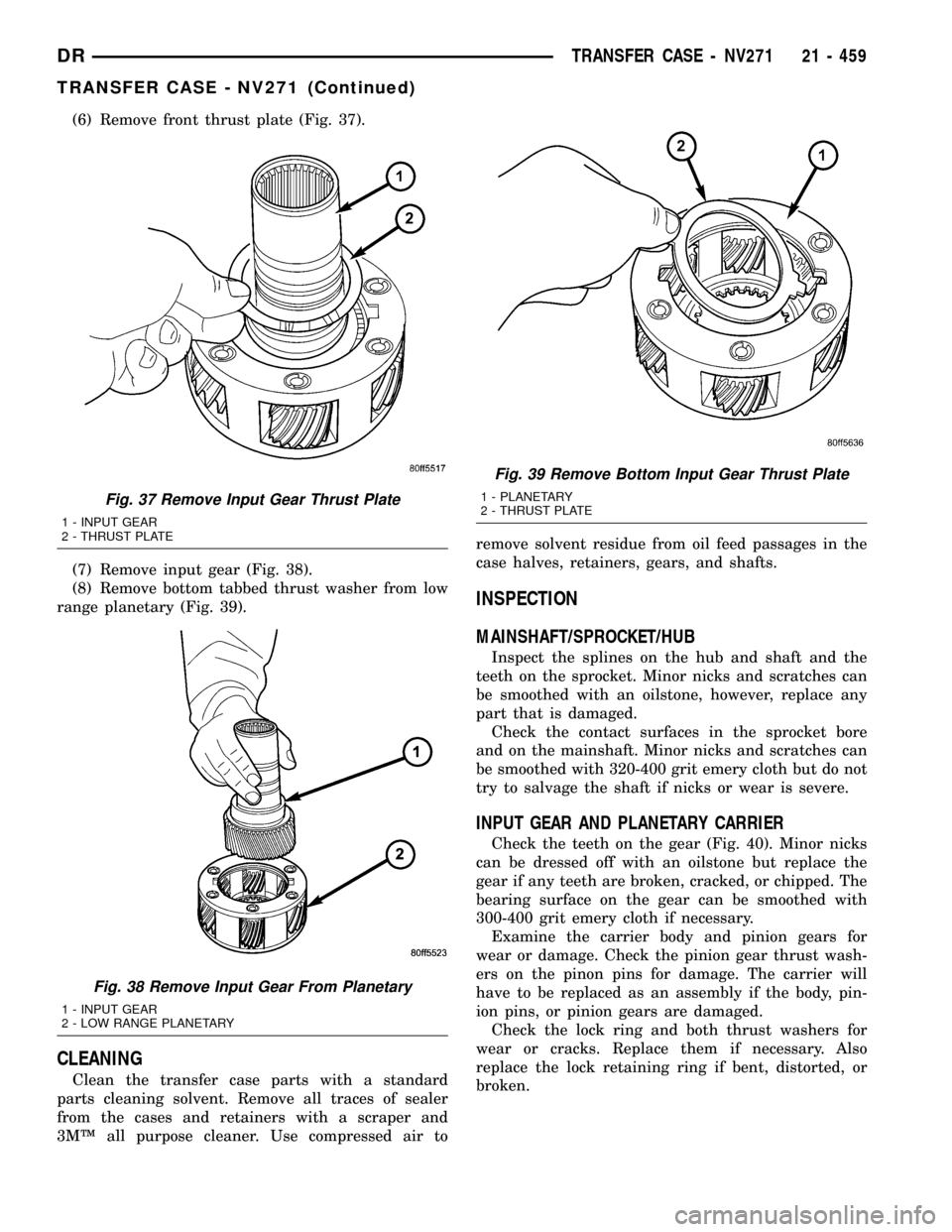
(6) Remove front thrust plate (Fig. 37).
(7) Remove input gear (Fig. 38).
(8) Remove bottom tabbed thrust washer from low
range planetary (Fig. 39).
CLEANING
Clean the transfer case parts with a standard
parts cleaning solvent. Remove all traces of sealer
from the cases and retainers with a scraper and
3MŸ all purpose cleaner. Use compressed air toremove solvent residue from oil feed passages in the
case halves, retainers, gears, and shafts.
INSPECTION
MAINSHAFT/SPROCKET/HUB
Inspect the splines on the hub and shaft and the
teeth on the sprocket. Minor nicks and scratches can
be smoothed with an oilstone, however, replace any
part that is damaged.
Check the contact surfaces in the sprocket bore
and on the mainshaft. Minor nicks and scratches can
be smoothed with 320-400 grit emery cloth but do not
try to salvage the shaft if nicks or wear is severe.
INPUT GEAR AND PLANETARY CARRIER
Check the teeth on the gear (Fig. 40). Minor nicks
can be dressed off with an oilstone but replace the
gear if any teeth are broken, cracked, or chipped. The
bearing surface on the gear can be smoothed with
300-400 grit emery cloth if necessary.
Examine the carrier body and pinion gears for
wear or damage. Check the pinion gear thrust wash-
ers on the pinon pins for damage. The carrier will
have to be replaced as an assembly if the body, pin-
ion pins, or pinion gears are damaged.
Check the lock ring and both thrust washers for
wear or cracks. Replace them if necessary. Also
replace the lock retaining ring if bent, distorted, or
broken.
Fig. 37 Remove Input Gear Thrust Plate
1 - INPUT GEAR
2 - THRUST PLATE
Fig. 38 Remove Input Gear From Planetary
1 - INPUT GEAR
2 - LOW RANGE PLANETARY
Fig. 39 Remove Bottom Input Gear Thrust Plate
1 - PLANETARY
2 - THRUST PLATE
DRTRANSFER CASE - NV271 21 - 459
TRANSFER CASE - NV271 (Continued)
Page 2163 of 2627
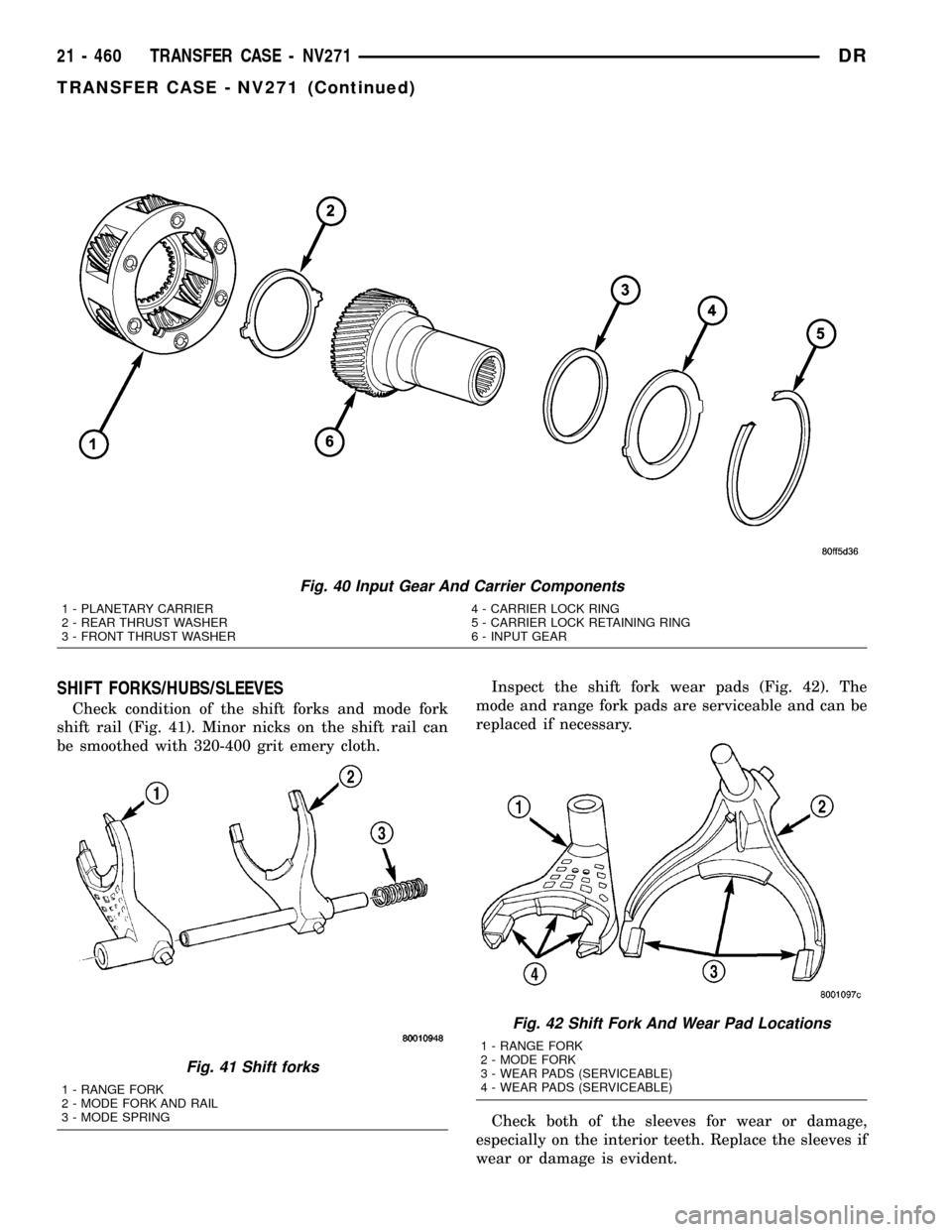
SHIFT FORKS/HUBS/SLEEVES
Check condition of the shift forks and mode fork
shift rail (Fig. 41). Minor nicks on the shift rail can
be smoothed with 320-400 grit emery cloth.Inspect the shift fork wear pads (Fig. 42). The
mode and range fork pads are serviceable and can be
replaced if necessary.
Check both of the sleeves for wear or damage,
especially on the interior teeth. Replace the sleeves if
wear or damage is evident.
Fig. 40 Input Gear And Carrier Components
1 - PLANETARY CARRIER 4 - CARRIER LOCK RING
2 - REAR THRUST WASHER 5 - CARRIER LOCK RETAINING RING
3 - FRONT THRUST WASHER 6 - INPUT GEAR
Fig. 41 Shift forks
1 - RANGE FORK
2 - MODE FORK AND RAIL
3 - MODE SPRING
Fig. 42 Shift Fork And Wear Pad Locations
1 - RANGE FORK
2 - MODE FORK
3 - WEAR PADS (SERVICEABLE)
4 - WEAR PADS (SERVICEABLE)
21 - 460 TRANSFER CASE - NV271DR
TRANSFER CASE - NV271 (Continued)
Page 2164 of 2627
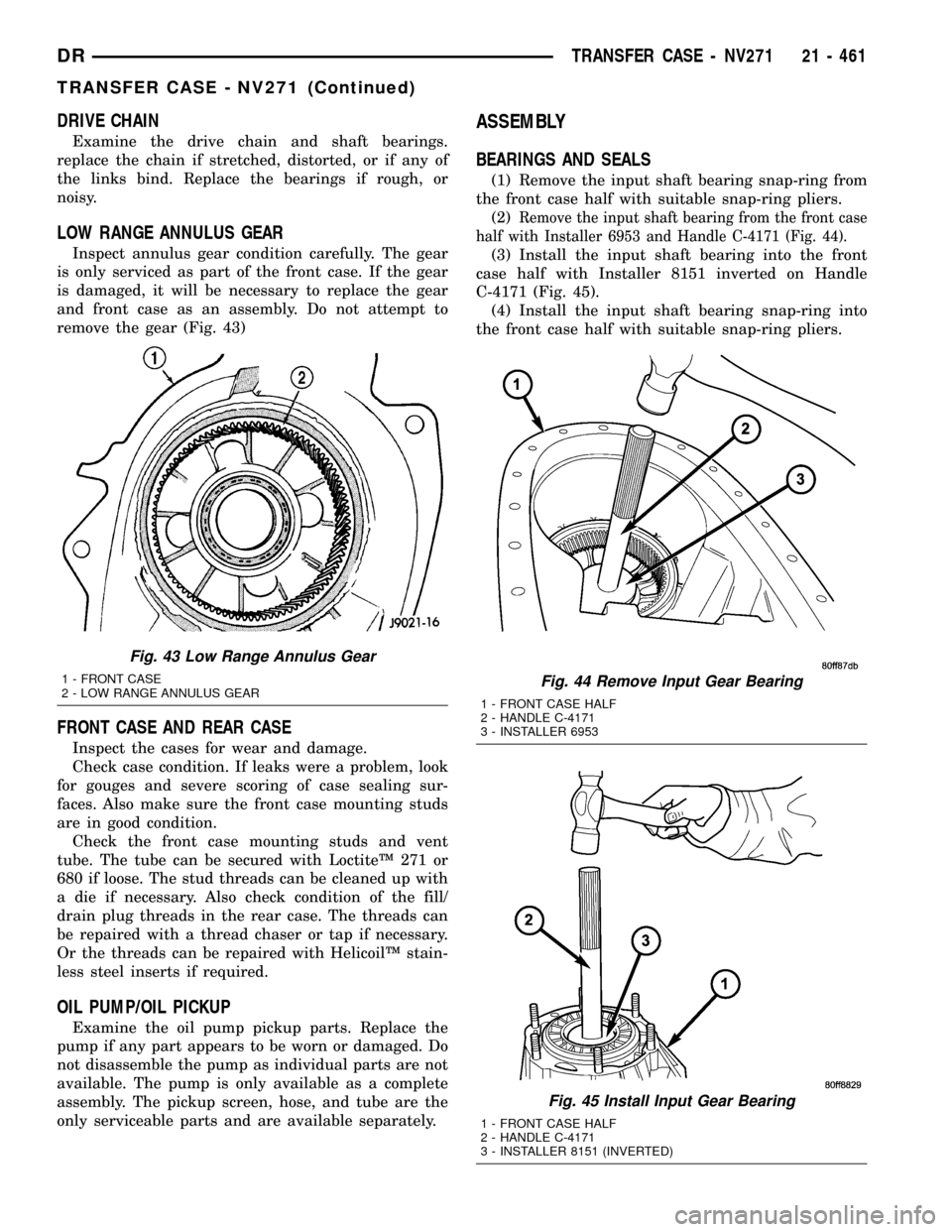
DRIVE CHAIN
Examine the drive chain and shaft bearings.
replace the chain if stretched, distorted, or if any of
the links bind. Replace the bearings if rough, or
noisy.
LOW RANGE ANNULUS GEAR
Inspect annulus gear condition carefully. The gear
is only serviced as part of the front case. If the gear
is damaged, it will be necessary to replace the gear
and front case as an assembly. Do not attempt to
remove the gear (Fig. 43)
FRONT CASE AND REAR CASE
Inspect the cases for wear and damage.
Check case condition. If leaks were a problem, look
for gouges and severe scoring of case sealing sur-
faces. Also make sure the front case mounting studs
are in good condition.
Check the front case mounting studs and vent
tube. The tube can be secured with LoctiteŸ 271 or
680 if loose. The stud threads can be cleaned up with
a die if necessary. Also check condition of the fill/
drain plug threads in the rear case. The threads can
be repaired with a thread chaser or tap if necessary.
Or the threads can be repaired with HelicoilŸ stain-
less steel inserts if required.
OIL PUMP/OIL PICKUP
Examine the oil pump pickup parts. Replace the
pump if any part appears to be worn or damaged. Do
not disassemble the pump as individual parts are not
available. The pump is only available as a complete
assembly. The pickup screen, hose, and tube are the
only serviceable parts and are available separately.
ASSEMBLY
BEARINGS AND SEALS
(1) Remove the input shaft bearing snap-ring from
the front case half with suitable snap-ring pliers.
(2)
Remove the input shaft bearing from the front case
half with Installer 6953 and Handle C-4171 (Fig. 44).
(3) Install the input shaft bearing into the front
case half with Installer 8151 inverted on Handle
C-4171 (Fig. 45).
(4) Install the input shaft bearing snap-ring into
the front case half with suitable snap-ring pliers.
Fig. 43 Low Range Annulus Gear
1 - FRONT CASE
2 - LOW RANGE ANNULUS GEARFig. 44 Remove Input Gear Bearing
1 - FRONT CASE HALF
2 - HANDLE C-4171
3 - INSTALLER 6953
Fig. 45 Install Input Gear Bearing
1 - FRONT CASE HALF
2 - HANDLE C-4171
3 - INSTALLER 8151 (INVERTED)
DRTRANSFER CASE - NV271 21 - 461
TRANSFER CASE - NV271 (Continued)
Page 2165 of 2627
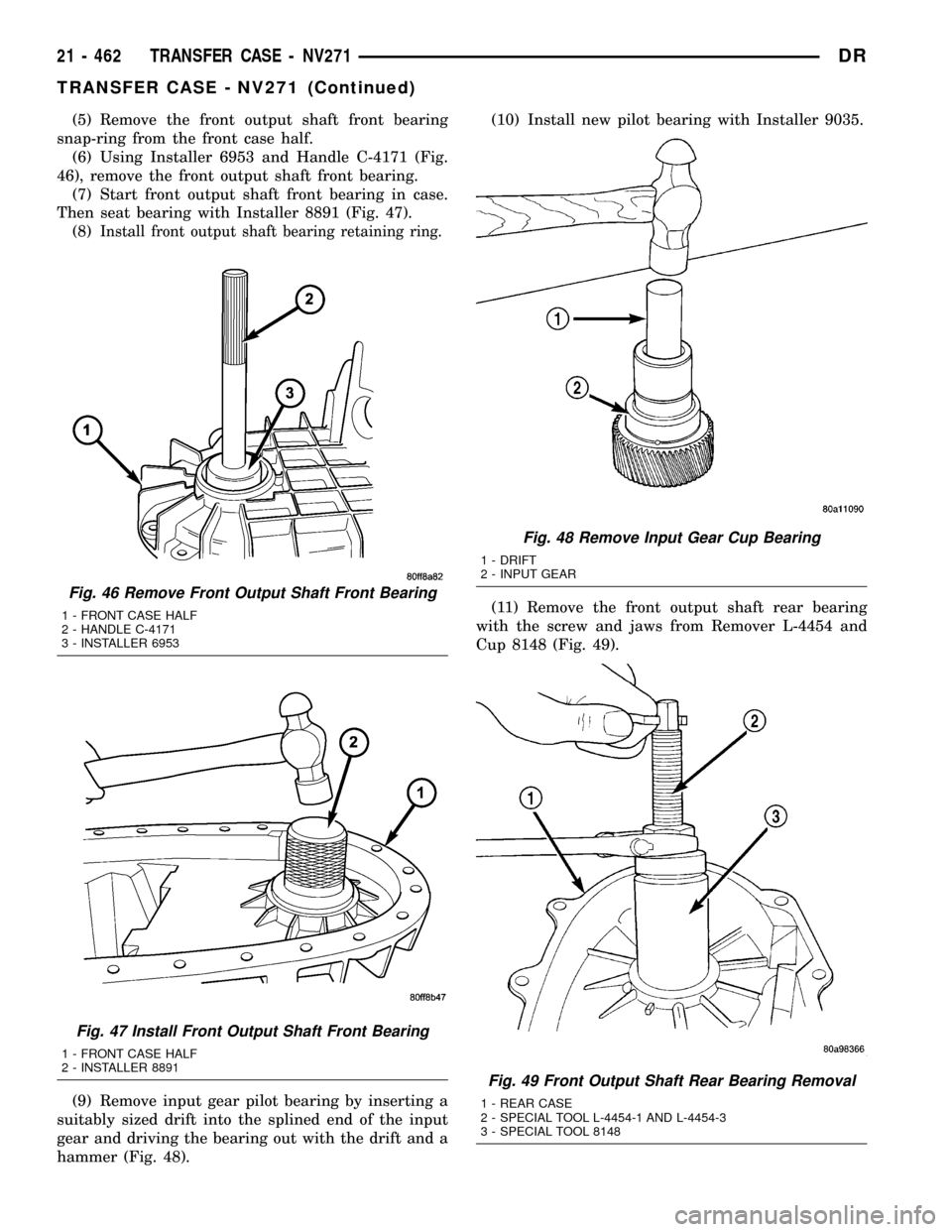
(5) Remove the front output shaft front bearing
snap-ring from the front case half.
(6) Using Installer 6953 and Handle C-4171 (Fig.
46), remove the front output shaft front bearing.
(7) Start front output shaft front bearing in case.
Then seat bearing with Installer 8891 (Fig. 47).
(8)
Install front output shaft bearing retaining ring.
(9) Remove input gear pilot bearing by inserting a
suitably sized drift into the splined end of the input
gear and driving the bearing out with the drift and a
hammer (Fig. 48).(10) Install new pilot bearing with Installer 9035.
(11) Remove the front output shaft rear bearing
with the screw and jaws from Remover L-4454 and
Cup 8148 (Fig. 49).
Fig. 46 Remove Front Output Shaft Front Bearing
1 - FRONT CASE HALF
2 - HANDLE C-4171
3 - INSTALLER 6953
Fig. 47 Install Front Output Shaft Front Bearing
1 - FRONT CASE HALF
2 - INSTALLER 8891
Fig. 48 Remove Input Gear Cup Bearing
1 - DRIFT
2 - INPUT GEAR
Fig. 49 Front Output Shaft Rear Bearing Removal
1 - REAR CASE
2 - SPECIAL TOOL L-4454-1 AND L-4454-3
3 - SPECIAL TOOL 8148
21 - 462 TRANSFER CASE - NV271DR
TRANSFER CASE - NV271 (Continued)
Page 2166 of 2627
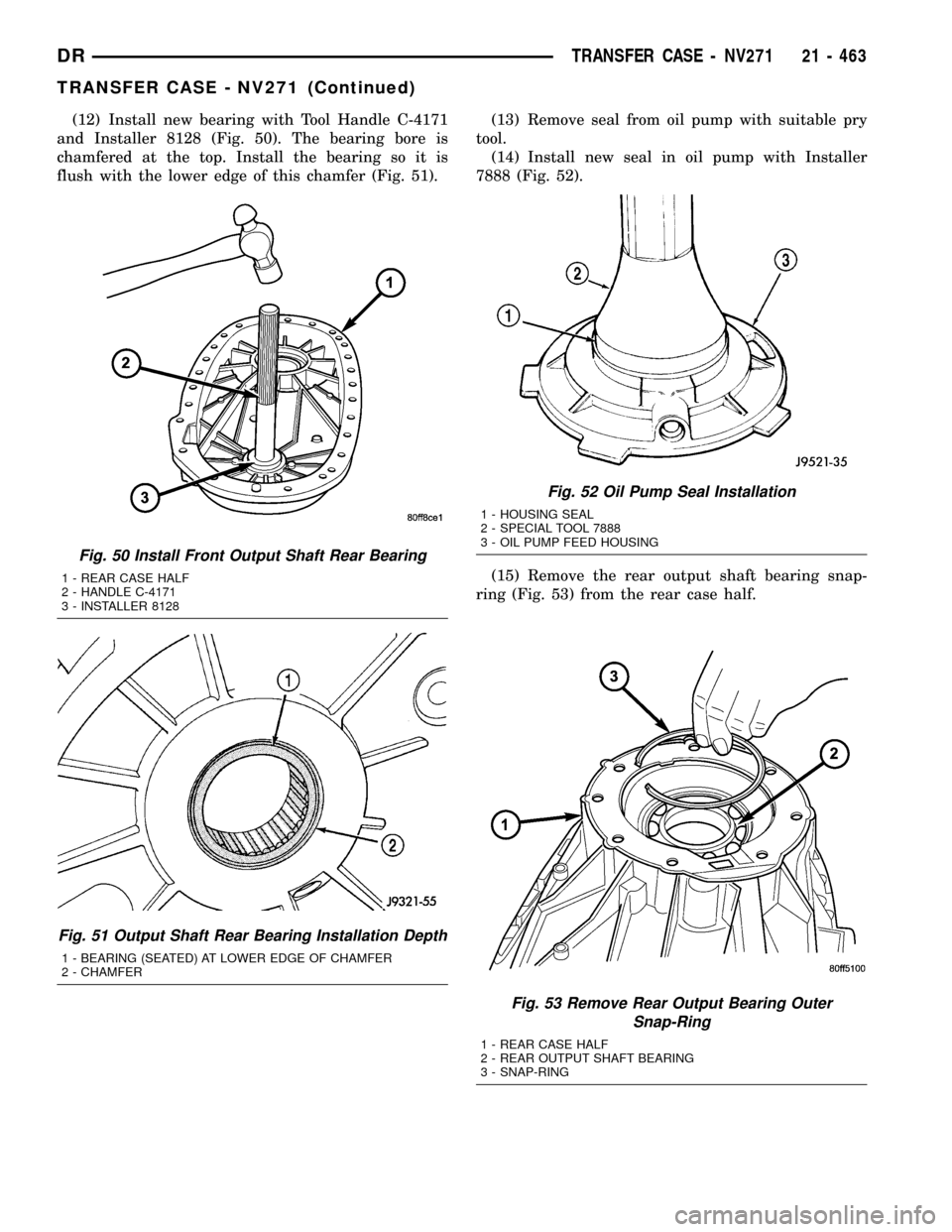
(12) Install new bearing with Tool Handle C-4171
and Installer 8128 (Fig. 50). The bearing bore is
chamfered at the top. Install the bearing so it is
flush with the lower edge of this chamfer (Fig. 51).(13) Remove seal from oil pump with suitable pry
tool.
(14) Install new seal in oil pump with Installer
7888 (Fig. 52).
(15) Remove the rear output shaft bearing snap-
ring (Fig. 53) from the rear case half.
Fig. 53 Remove Rear Output Bearing Outer
Snap-Ring
1 - REAR CASE HALF
2 - REAR OUTPUT SHAFT BEARING
3 - SNAP-RING
Fig. 50 Install Front Output Shaft Rear Bearing
1 - REAR CASE HALF
2 - HANDLE C-4171
3 - INSTALLER 8128
Fig. 51 Output Shaft Rear Bearing Installation Depth
1 - BEARING (SEATED) AT LOWER EDGE OF CHAMFER
2 - CHAMFER
Fig. 52 Oil Pump Seal Installation
1 - HOUSING SEAL
2 - SPECIAL TOOL 7888
3 - OIL PUMP FEED HOUSING
DRTRANSFER CASE - NV271 21 - 463
TRANSFER CASE - NV271 (Continued)
Page 2167 of 2627
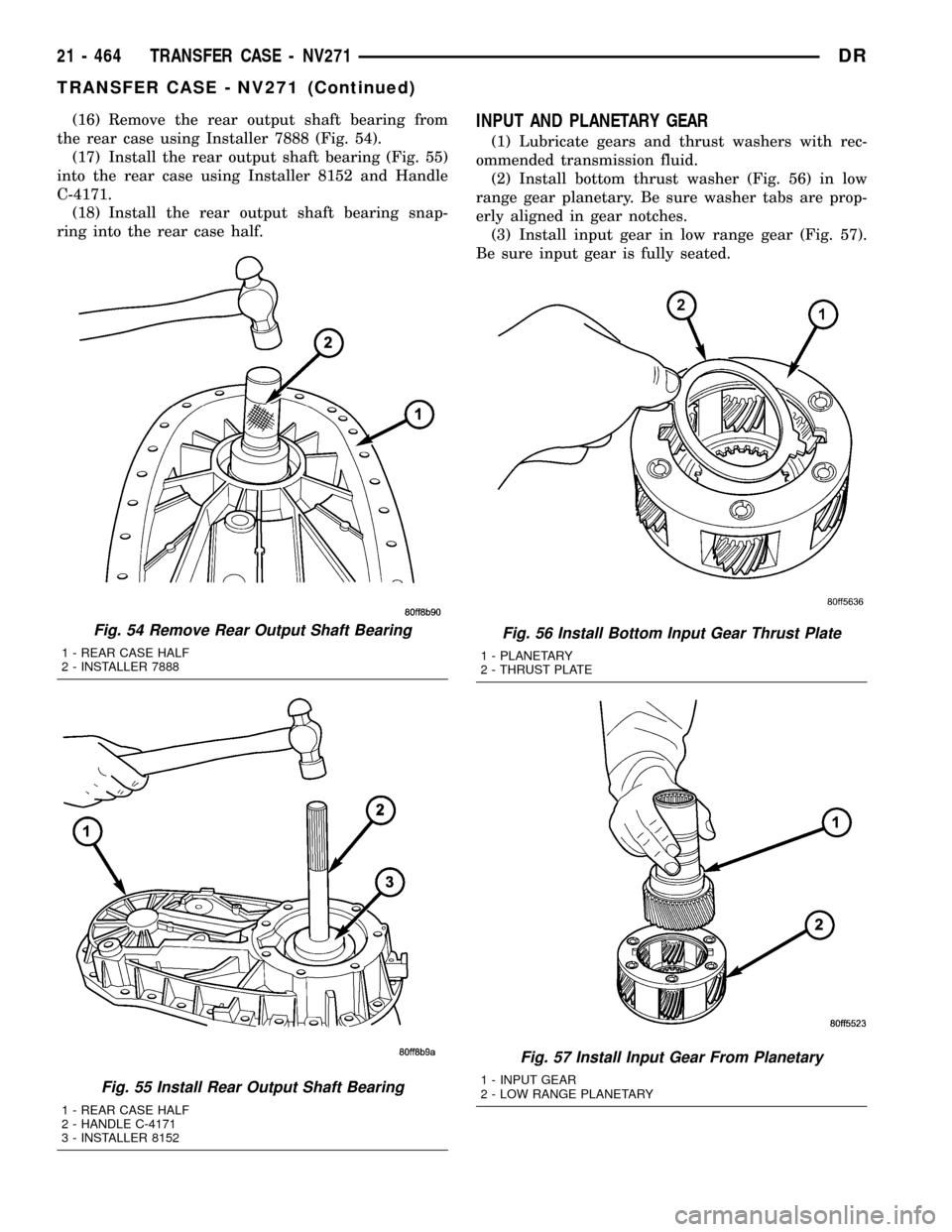
(16) Remove the rear output shaft bearing from
the rear case using Installer 7888 (Fig. 54).
(17) Install the rear output shaft bearing (Fig. 55)
into the rear case using Installer 8152 and Handle
C-4171.
(18) Install the rear output shaft bearing snap-
ring into the rear case half.INPUT AND PLANETARY GEAR
(1) Lubricate gears and thrust washers with rec-
ommended transmission fluid.
(2) Install bottom thrust washer (Fig. 56) in low
range gear planetary. Be sure washer tabs are prop-
erly aligned in gear notches.
(3) Install input gear in low range gear (Fig. 57).
Be sure input gear is fully seated.
Fig. 54 Remove Rear Output Shaft Bearing
1 - REAR CASE HALF
2 - INSTALLER 7888
Fig. 55 Install Rear Output Shaft Bearing
1 - REAR CASE HALF
2 - HANDLE C-4171
3 - INSTALLER 8152
Fig. 56 Install Bottom Input Gear Thrust Plate
1 - PLANETARY
2 - THRUST PLATE
Fig. 57 Install Input Gear From Planetary
1 - INPUT GEAR
2 - LOW RANGE PLANETARY
21 - 464 TRANSFER CASE - NV271DR
TRANSFER CASE - NV271 (Continued)
Page 2168 of 2627
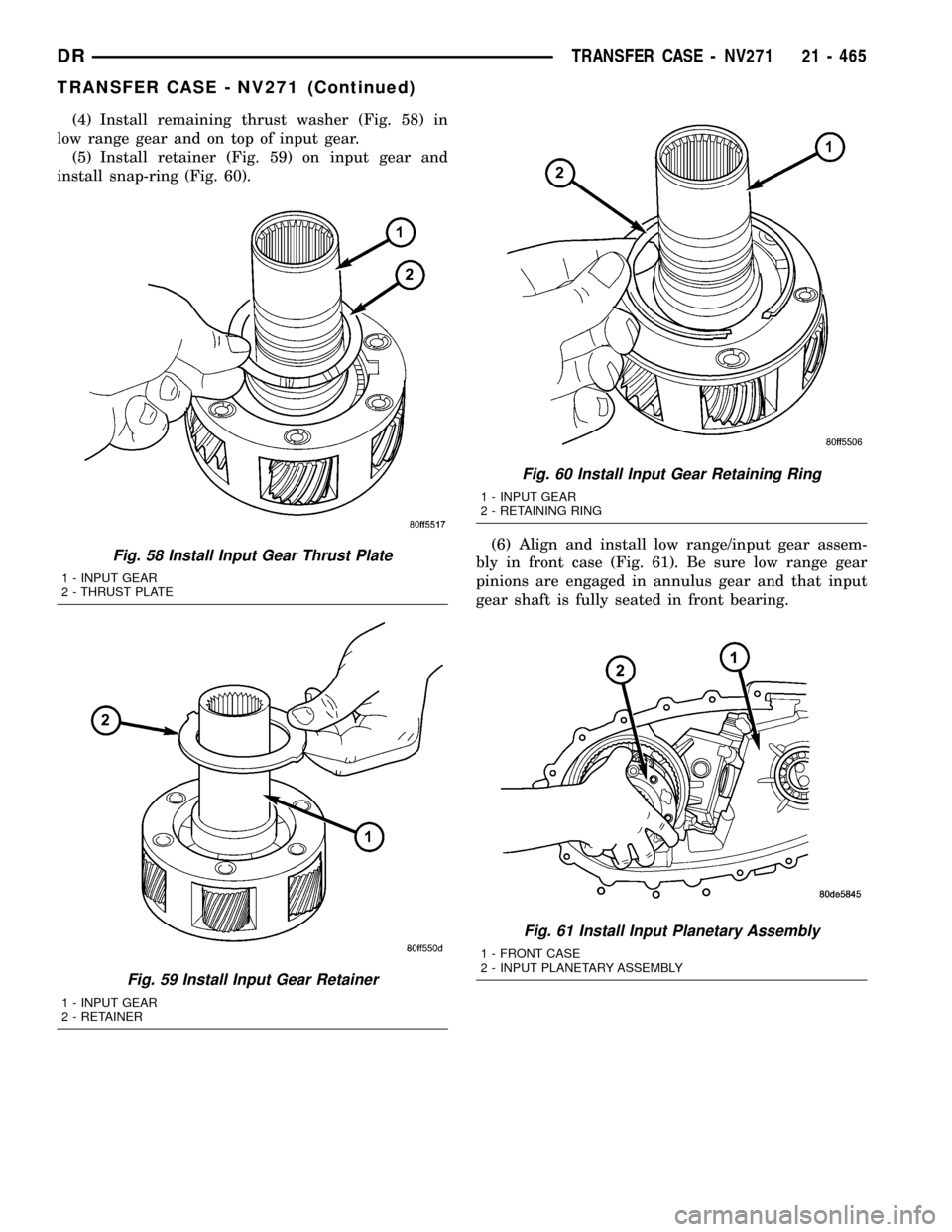
(4) Install remaining thrust washer (Fig. 58) in
low range gear and on top of input gear.
(5) Install retainer (Fig. 59) on input gear and
install snap-ring (Fig. 60).
(6) Align and install low range/input gear assem-
bly in front case (Fig. 61). Be sure low range gear
pinions are engaged in annulus gear and that input
gear shaft is fully seated in front bearing.
Fig. 61 Install Input Planetary Assembly
1 - FRONT CASE
2 - INPUT PLANETARY ASSEMBLY
Fig. 58 Install Input Gear Thrust Plate
1 - INPUT GEAR
2 - THRUST PLATE
Fig. 59 Install Input Gear Retainer
1 - INPUT GEAR
2 - RETAINER
Fig. 60 Install Input Gear Retaining Ring
1 - INPUT GEAR
2 - RETAINING RING
DRTRANSFER CASE - NV271 21 - 465
TRANSFER CASE - NV271 (Continued)
Page 2169 of 2627
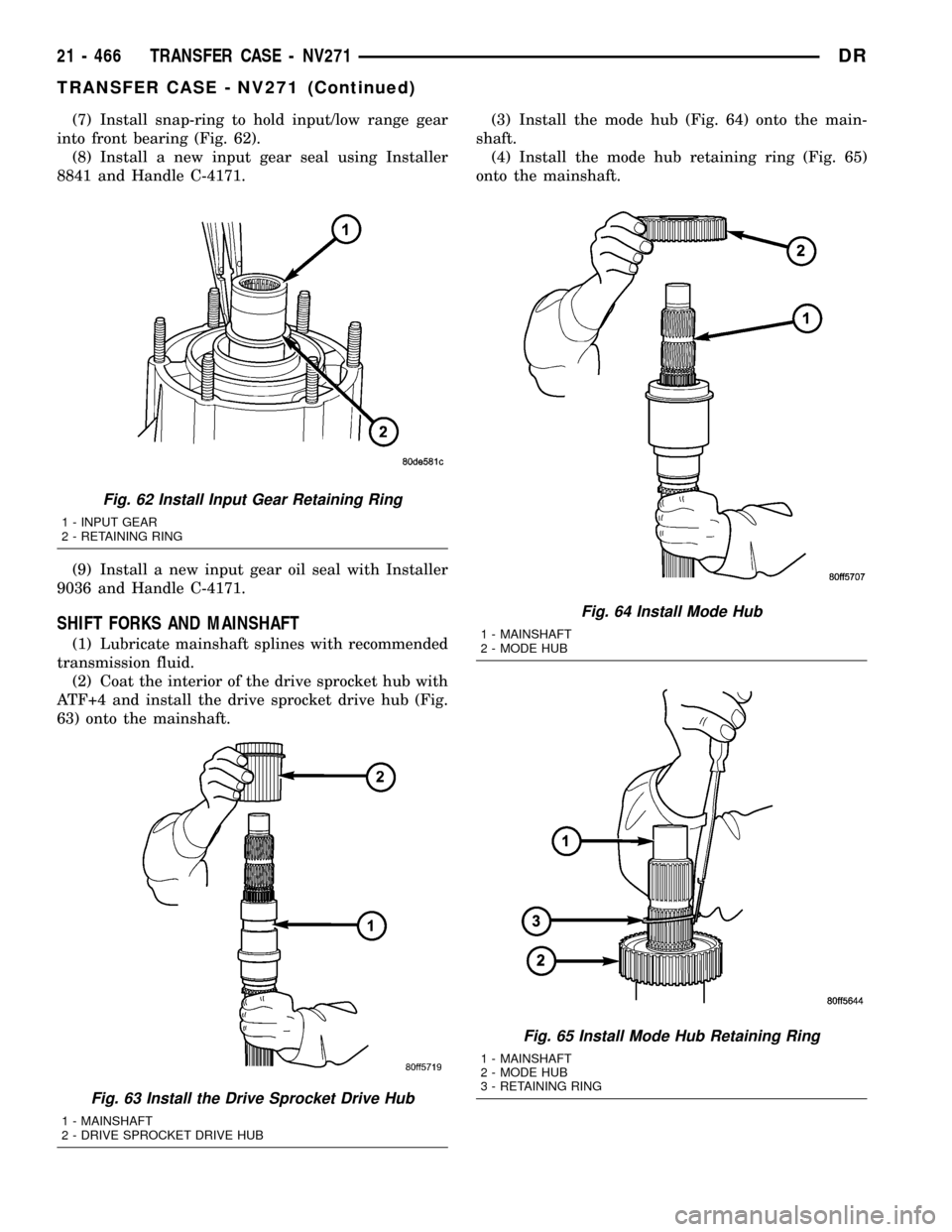
(7) Install snap-ring to hold input/low range gear
into front bearing (Fig. 62).
(8) Install a new input gear seal using Installer
8841 and Handle C-4171.
(9) Install a new input gear oil seal with Installer
9036 and Handle C-4171.
SHIFT FORKS AND MAINSHAFT
(1) Lubricate mainshaft splines with recommended
transmission fluid.
(2) Coat the interior of the drive sprocket hub with
ATF+4 and install the drive sprocket drive hub (Fig.
63) onto the mainshaft.(3) Install the mode hub (Fig. 64) onto the main-
shaft.
(4) Install the mode hub retaining ring (Fig. 65)
onto the mainshaft.
Fig. 62 Install Input Gear Retaining Ring
1 - INPUT GEAR
2 - RETAINING RING
Fig. 63 Install the Drive Sprocket Drive Hub
1 - MAINSHAFT
2 - DRIVE SPROCKET DRIVE HUB
Fig. 64 Install Mode Hub
1 - MAINSHAFT
2 - MODE HUB
Fig. 65 Install Mode Hub Retaining Ring
1 - MAINSHAFT
2 - MODE HUB
3 - RETAINING RING
21 - 466 TRANSFER CASE - NV271DR
TRANSFER CASE - NV271 (Continued)
Page 2170 of 2627
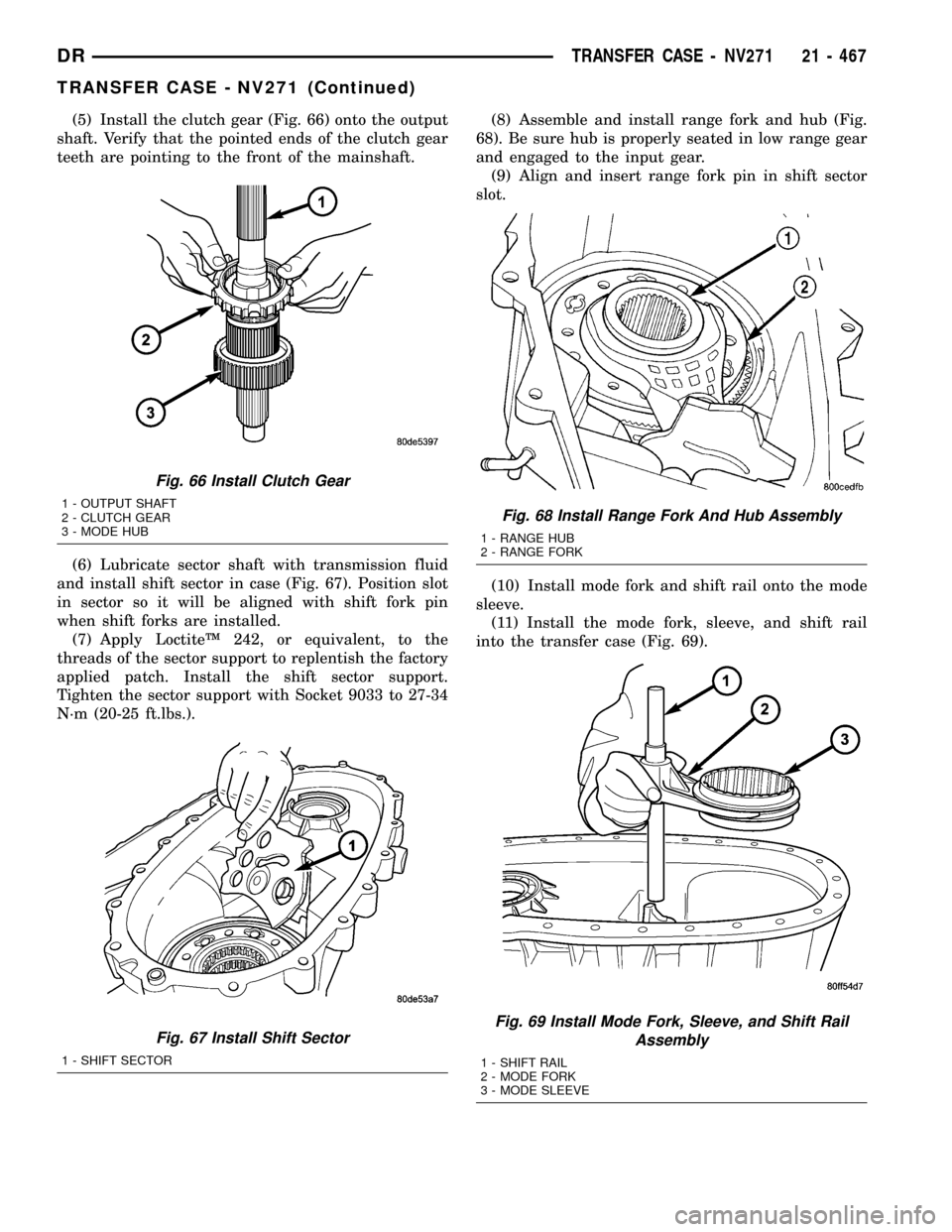
(5) Install the clutch gear (Fig. 66) onto the output
shaft. Verify that the pointed ends of the clutch gear
teeth are pointing to the front of the mainshaft.
(6) Lubricate sector shaft with transmission fluid
and install shift sector in case (Fig. 67). Position slot
in sector so it will be aligned with shift fork pin
when shift forks are installed.
(7) Apply LoctiteŸ 242, or equivalent, to the
threads of the sector support to replentish the factory
applied patch. Install the shift sector support.
Tighten the sector support with Socket 9033 to 27-34
N´m (20-25 ft.lbs.).(8) Assemble and install range fork and hub (Fig.
68). Be sure hub is properly seated in low range gear
and engaged to the input gear.
(9) Align and insert range fork pin in shift sector
slot.
(10) Install mode fork and shift rail onto the mode
sleeve.
(11) Install the mode fork, sleeve, and shift rail
into the transfer case (Fig. 69).
Fig. 66 Install Clutch Gear
1 - OUTPUT SHAFT
2 - CLUTCH GEAR
3 - MODE HUB
Fig. 67 Install Shift Sector
1 - SHIFT SECTOR
Fig. 68 Install Range Fork And Hub Assembly
1 - RANGE HUB
2 - RANGE FORK
Fig. 69 Install Mode Fork, Sleeve, and Shift Rail
Assembly
1 - SHIFT RAIL
2 - MODE FORK
3 - MODE SLEEVE
DRTRANSFER CASE - NV271 21 - 467
TRANSFER CASE - NV271 (Continued)