DODGE RAM 2001 Service Repair Manual
Manufacturer: DODGE, Model Year: 2001, Model line: RAM, Model: DODGE RAM 2001Pages: 2889, PDF Size: 68.07 MB
Page 2551 of 2889
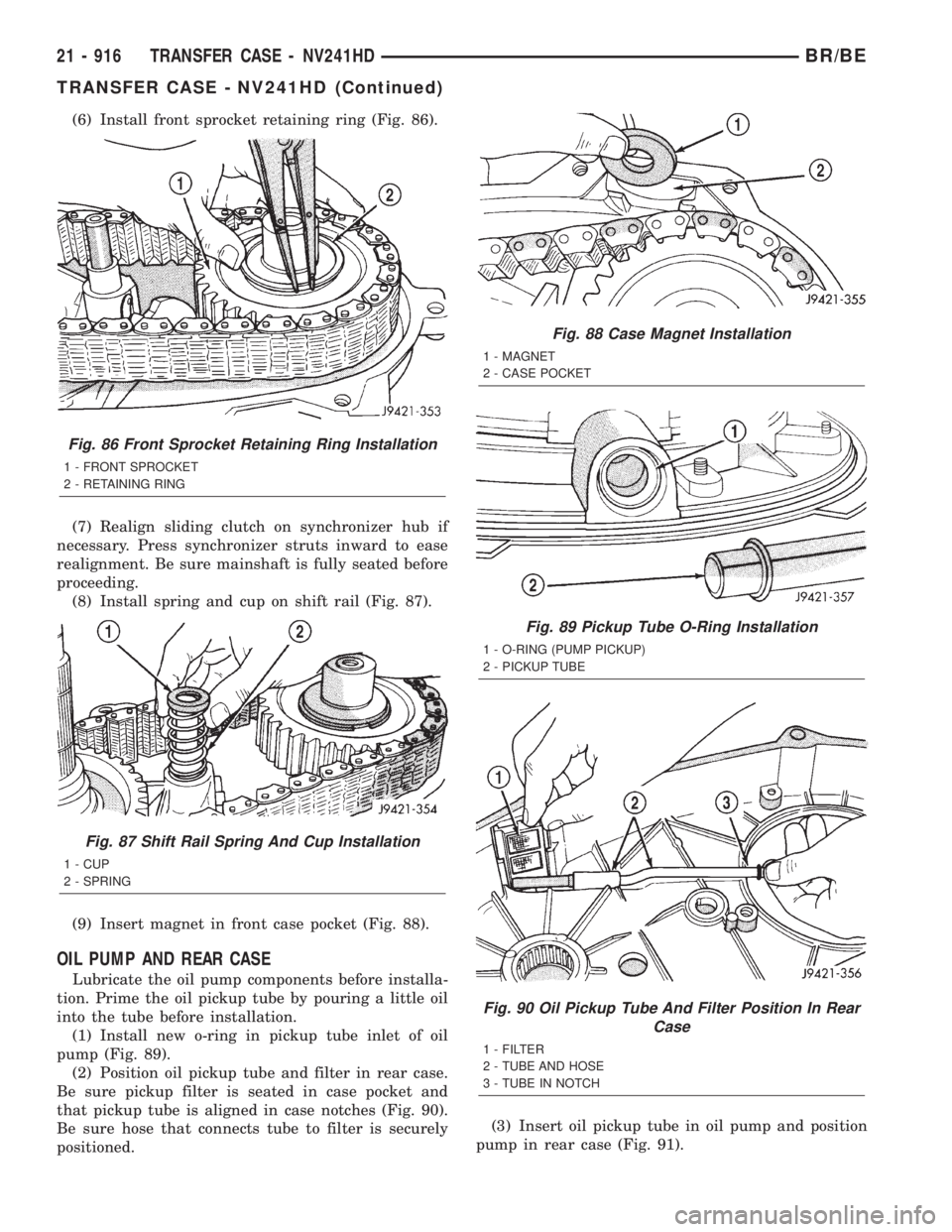
(6) Install front sprocket retaining ring (Fig. 86).
(7) Realign sliding clutch on synchronizer hub if
necessary. Press synchronizer struts inward to ease
realignment. Be sure mainshaft is fully seated before
proceeding.
(8) Install spring and cup on shift rail (Fig. 87).
(9) Insert magnet in front case pocket (Fig. 88).
OIL PUMP AND REAR CASE
Lubricate the oil pump components before installa-
tion. Prime the oil pickup tube by pouring a little oil
into the tube before installation.
(1) Install new o-ring in pickup tube inlet of oil
pump (Fig. 89).
(2) Position oil pickup tube and filter in rear case.
Be sure pickup filter is seated in case pocket and
that pickup tube is aligned in case notches (Fig. 90).
Be sure hose that connects tube to filter is securely
positioned.(3) Insert oil pickup tube in oil pump and position
pump in rear case (Fig. 91).
Fig. 86 Front Sprocket Retaining Ring Installation
1 - FRONT SPROCKET
2 - RETAINING RING
Fig. 87 Shift Rail Spring And Cup Installation
1 - CUP
2 - SPRING
Fig. 88 Case Magnet Installation
1 - MAGNET
2 - CASE POCKET
Fig. 89 Pickup Tube O-Ring Installation
1 - O-RING (PUMP PICKUP)
2 - PICKUP TUBE
Fig. 90 Oil Pickup Tube And Filter Position In Rear
Case
1 - FILTER
2 - TUBE AND HOSE
3 - TUBE IN NOTCH
21 - 916 TRANSFER CASE - NV241HDBR/BE
TRANSFER CASE - NV241HD (Continued)
Page 2552 of 2889

(4) Apply bead of MopartGasket Maker, or equiv-
alent, to mating surface of front case. Keep sealer
bead width to maximum of 3/16 inch. Do not use
excessive amount of sealer as excess will be displaced
into case interior.
(5) Align oil pump with mainshaft and align shift
rail with bore in rear case. Then install rear case and
oil pump assembly (Fig. 92). Be sure oil pump and
pickup tube remain in position during case installa-
tion.
(6) Install 4-5 rear case-to front case bolts to hold
rear case in position. Tighten bolts snug but not to
specified torque at this time.
CAUTION: Verify that shift rail (Fig. 93), and case
alignment dowels are seated before installing any
bolts. Case could be cracked if shaft rail or dowels
are misaligned.
(7) Verify that oil pump is aligned and seated on
rear case. Reposition pump if necessary.
Fig. 91 Positioning Oil Pump In Rear Case
1 - OIL PUMP
2 - REAR CASE
3 - FILTER
4 - PICKUP TUBE
Fig. 92 Rear Case And Oil Pump Installation
1 - MAINSHAFT
2 - OIL PUMP
3 - REAR CASE
Fig. 93 Shift Rail Seated In Rear Case Bore
1 - REAR CASE
2 - SHIFT RAIL
BR/BETRANSFER CASE - NV241HD 21 - 917
TRANSFER CASE - NV241HD (Continued)
Page 2553 of 2889
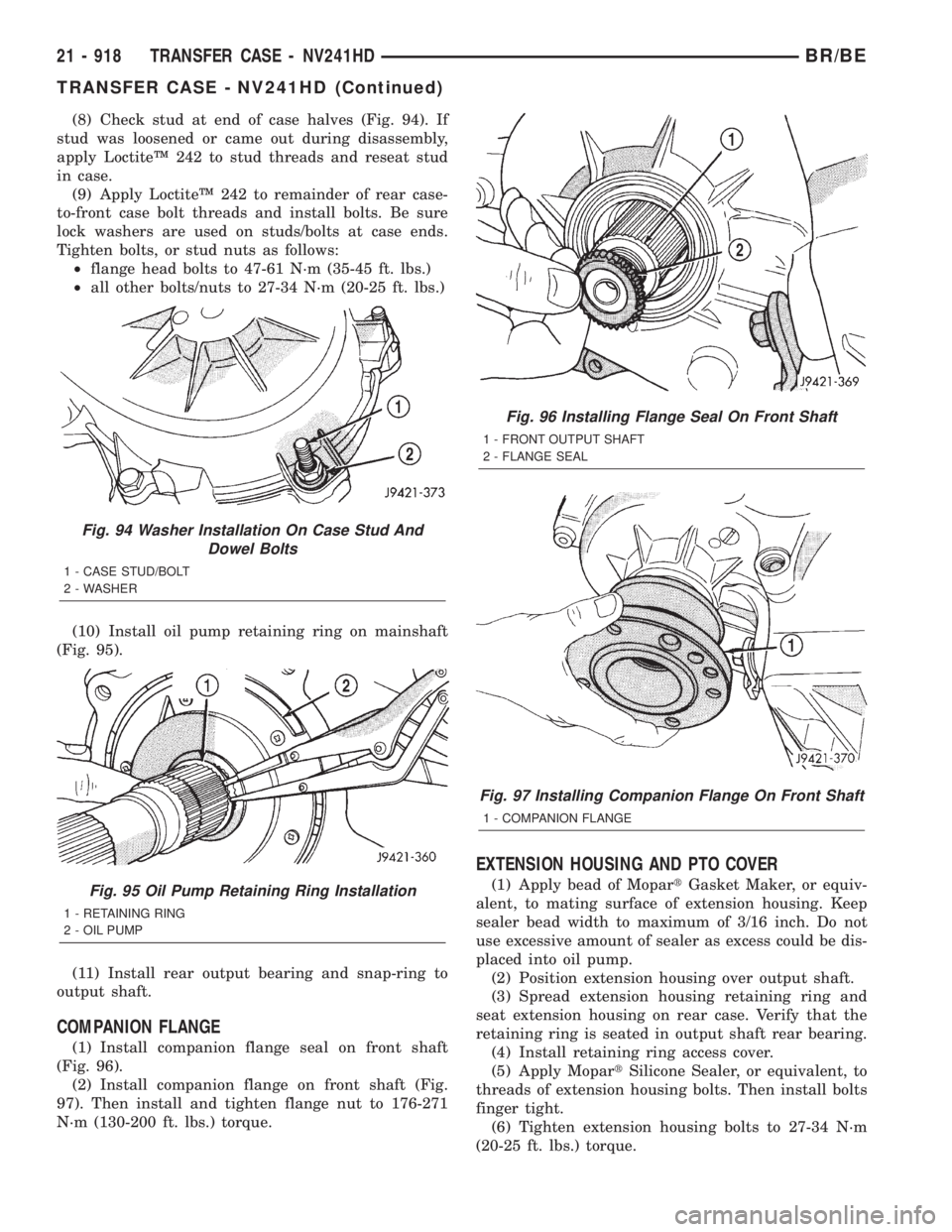
(8) Check stud at end of case halves (Fig. 94). If
stud was loosened or came out during disassembly,
apply LoctiteŸ 242 to stud threads and reseat stud
in case.
(9) Apply LoctiteŸ 242 to remainder of rear case-
to-front case bolt threads and install bolts. Be sure
lock washers are used on studs/bolts at case ends.
Tighten bolts, or stud nuts as follows:
²flange head bolts to 47-61 N´m (35-45 ft. lbs.)
²all other bolts/nuts to 27-34 N´m (20-25 ft. lbs.)
(10) Install oil pump retaining ring on mainshaft
(Fig. 95).
(11) Install rear output bearing and snap-ring to
output shaft.
COMPANION FLANGE
(1) Install companion flange seal on front shaft
(Fig. 96).
(2) Install companion flange on front shaft (Fig.
97). Then install and tighten flange nut to 176-271
N´m (130-200 ft. lbs.) torque.
EXTENSION HOUSING AND PTO COVER
(1) Apply bead of MopartGasket Maker, or equiv-
alent, to mating surface of extension housing. Keep
sealer bead width to maximum of 3/16 inch. Do not
use excessive amount of sealer as excess could be dis-
placed into oil pump.
(2) Position extension housing over output shaft.
(3) Spread extension housing retaining ring and
seat extension housing on rear case. Verify that the
retaining ring is seated in output shaft rear bearing.
(4) Install retaining ring access cover.
(5) Apply MopartSilicone Sealer, or equivalent, to
threads of extension housing bolts. Then install bolts
finger tight.
(6) Tighten extension housing bolts to 27-34 N´m
(20-25 ft. lbs.) torque.
Fig. 94 Washer Installation On Case Stud And
Dowel Bolts
1 - CASE STUD/BOLT
2 - WASHER
Fig. 95 Oil Pump Retaining Ring Installation
1 - RETAINING RING
2 - OIL PUMP
Fig. 96 Installing Flange Seal On Front Shaft
1 - FRONT OUTPUT SHAFT
2 - FLANGE SEAL
Fig. 97 Installing Companion Flange On Front Shaft
1 - COMPANION FLANGE
21 - 918 TRANSFER CASE - NV241HDBR/BE
TRANSFER CASE - NV241HD (Continued)
Page 2554 of 2889
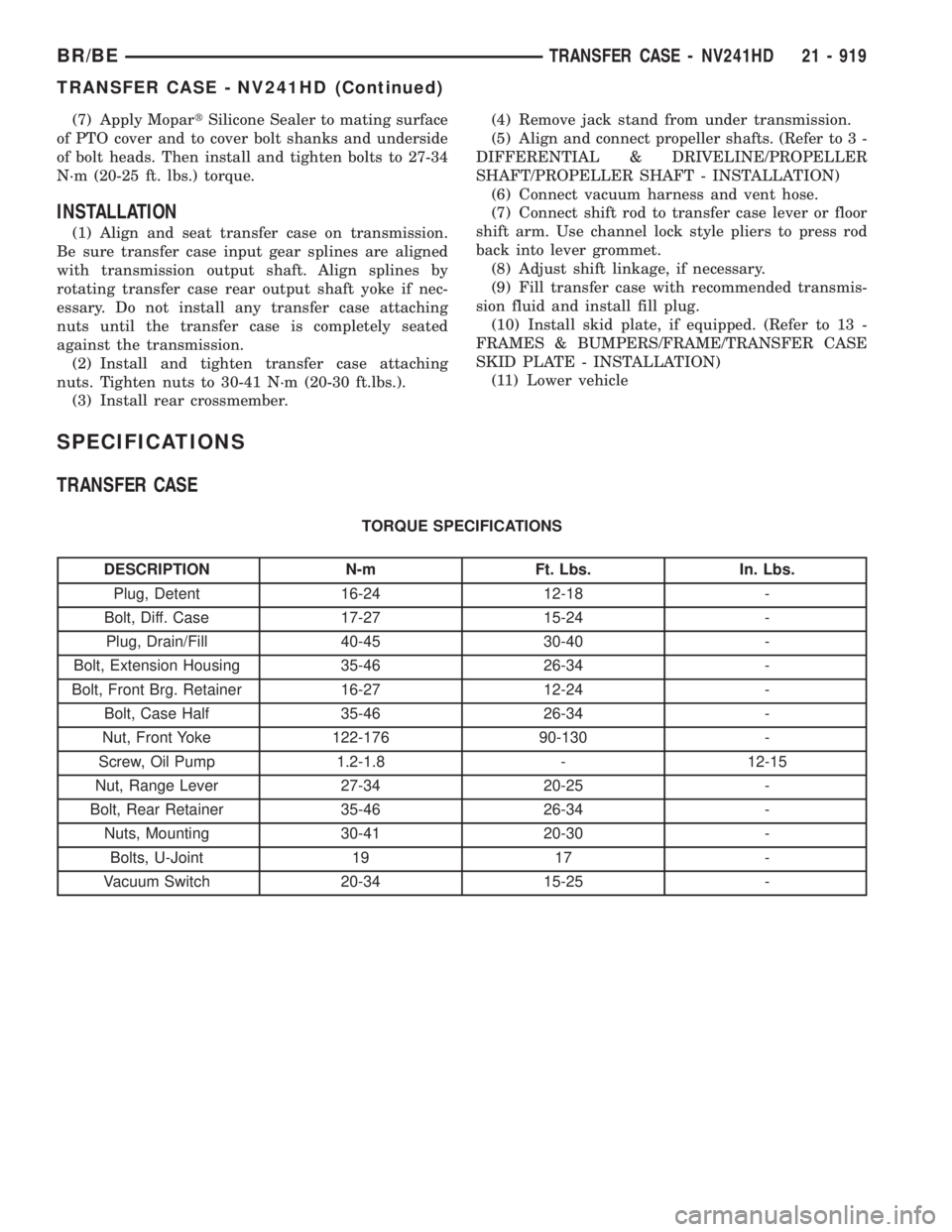
(7) Apply MopartSilicone Sealer to mating surface
of PTO cover and to cover bolt shanks and underside
of bolt heads. Then install and tighten bolts to 27-34
N´m (20-25 ft. lbs.) torque.
INSTALLATION
(1) Align and seat transfer case on transmission.
Be sure transfer case input gear splines are aligned
with transmission output shaft. Align splines by
rotating transfer case rear output shaft yoke if nec-
essary. Do not install any transfer case attaching
nuts until the transfer case is completely seated
against the transmission.
(2) Install and tighten transfer case attaching
nuts. Tighten nuts to 30-41 N´m (20-30 ft.lbs.).
(3) Install rear crossmember.(4) Remove jack stand from under transmission.
(5) Align and connect propeller shafts. (Refer to 3 -
DIFFERENTIAL & DRIVELINE/PROPELLER
SHAFT/PROPELLER SHAFT - INSTALLATION)
(6) Connect vacuum harness and vent hose.
(7) Connect shift rod to transfer case lever or floor
shift arm. Use channel lock style pliers to press rod
back into lever grommet.
(8) Adjust shift linkage, if necessary.
(9) Fill transfer case with recommended transmis-
sion fluid and install fill plug.
(10) Install skid plate, if equipped. (Refer to 13 -
FRAMES & BUMPERS/FRAME/TRANSFER CASE
SKID PLATE - INSTALLATION)
(11) Lower vehicle
SPECIFICATIONS
TRANSFER CASE
TORQUE SPECIFICATIONS
DESCRIPTION N-m Ft. Lbs. In. Lbs.
Plug, Detent 16-24 12-18 -
Bolt, Diff. Case 17-27 15-24 -
Plug, Drain/Fill 40-45 30-40 -
Bolt, Extension Housing 35-46 26-34 -
Bolt, Front Brg. Retainer 16-27 12-24 -
Bolt, Case Half 35-46 26-34 -
Nut, Front Yoke 122-176 90-130 -
Screw, Oil Pump 1.2-1.8 - 12-15
Nut, Range Lever 27-34 20-25 -
Bolt, Rear Retainer 35-46 26-34 -
Nuts, Mounting 30-41 20-30 -
Bolts, U-Joint 19 17 -
Vacuum Switch 20-34 15-25 -
BR/BETRANSFER CASE - NV241HD 21 - 919
TRANSFER CASE - NV241HD (Continued)
Page 2555 of 2889
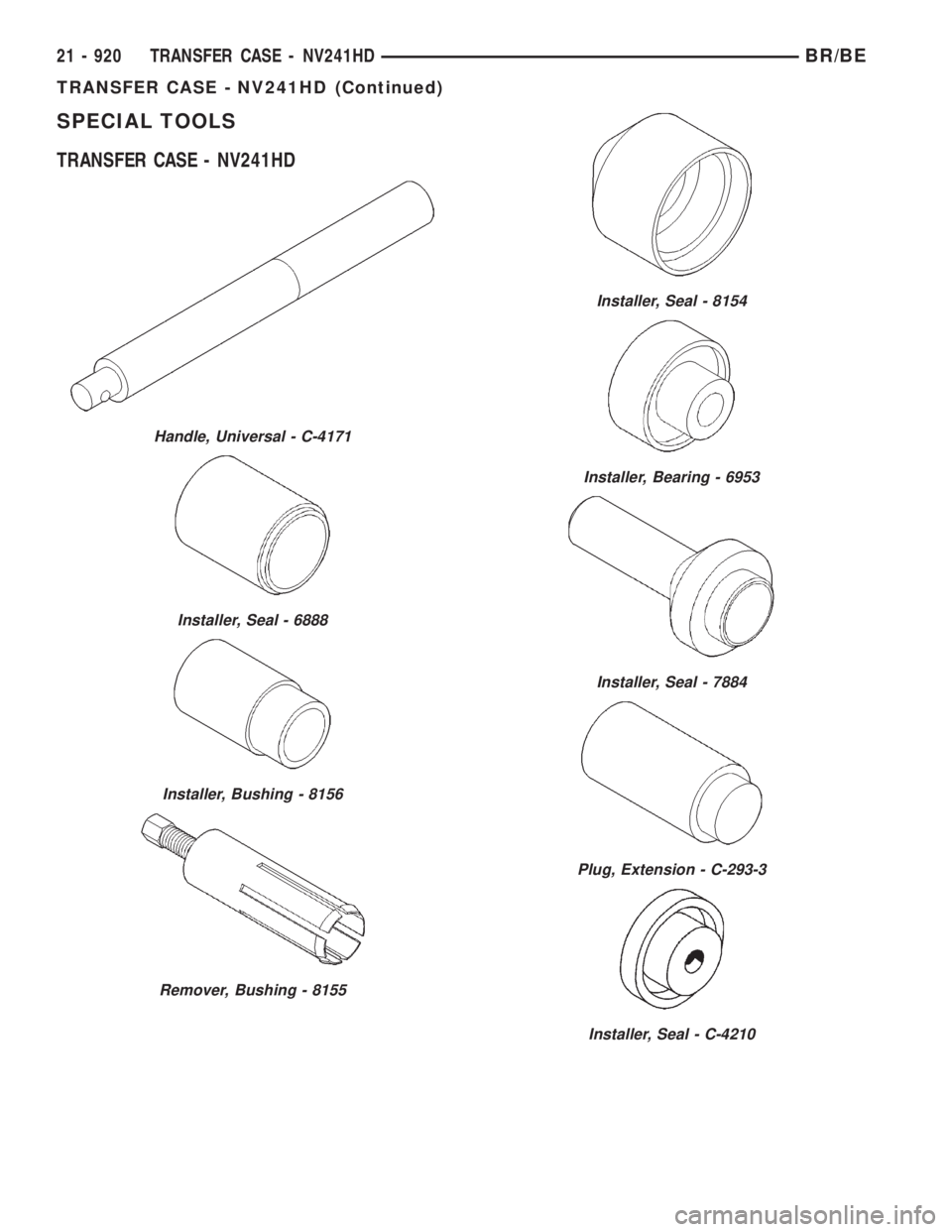
SPECIAL TOOLS
TRANSFER CASE - NV241HD
Handle, Universal - C-4171
Installer, Seal - 6888
Installer, Bushing - 8156
Remover, Bushing - 8155
Installer, Seal - 8154
Installer, Bearing - 6953
Installer, Seal - 7884
Plug, Extension - C-293-3
Installer, Seal - C-4210
21 - 920 TRANSFER CASE - NV241HDBR/BE
TRANSFER CASE - NV241HD (Continued)
Page 2556 of 2889
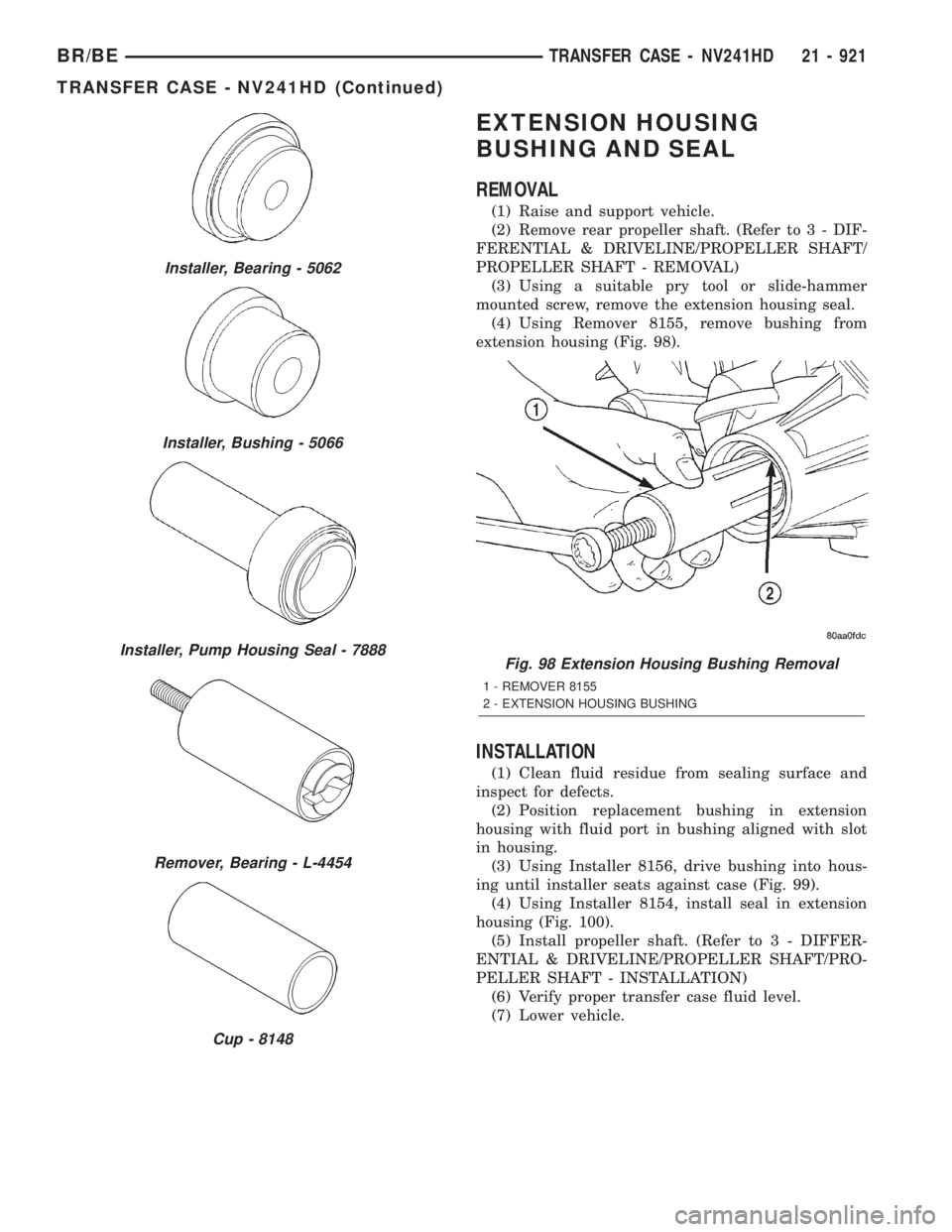
EXTENSION HOUSING
BUSHING AND SEAL
REMOVAL
(1) Raise and support vehicle.
(2) Remove rear propeller shaft. (Refer to 3 - DIF-
FERENTIAL & DRIVELINE/PROPELLER SHAFT/
PROPELLER SHAFT - REMOVAL)
(3) Using a suitable pry tool or slide-hammer
mounted screw, remove the extension housing seal.
(4) Using Remover 8155, remove bushing from
extension housing (Fig. 98).
INSTALLATION
(1) Clean fluid residue from sealing surface and
inspect for defects.
(2) Position replacement bushing in extension
housing with fluid port in bushing aligned with slot
in housing.
(3) Using Installer 8156, drive bushing into hous-
ing until installer seats against case (Fig. 99).
(4) Using Installer 8154, install seal in extension
housing (Fig. 100).
(5) Install propeller shaft. (Refer to 3 - DIFFER-
ENTIAL & DRIVELINE/PROPELLER SHAFT/PRO-
PELLER SHAFT - INSTALLATION)
(6) Verify proper transfer case fluid level.
(7) Lower vehicle.
Installer, Bearing - 5062
Installer, Bushing - 5066
Installer, Pump Housing Seal - 7888
Remover, Bearing - L-4454
Cup - 8148
Fig. 98 Extension Housing Bushing Removal
1 - REMOVER 8155
2 - EXTENSION HOUSING BUSHING
BR/BETRANSFER CASE - NV241HD 21 - 921
TRANSFER CASE - NV241HD (Continued)
Page 2557 of 2889
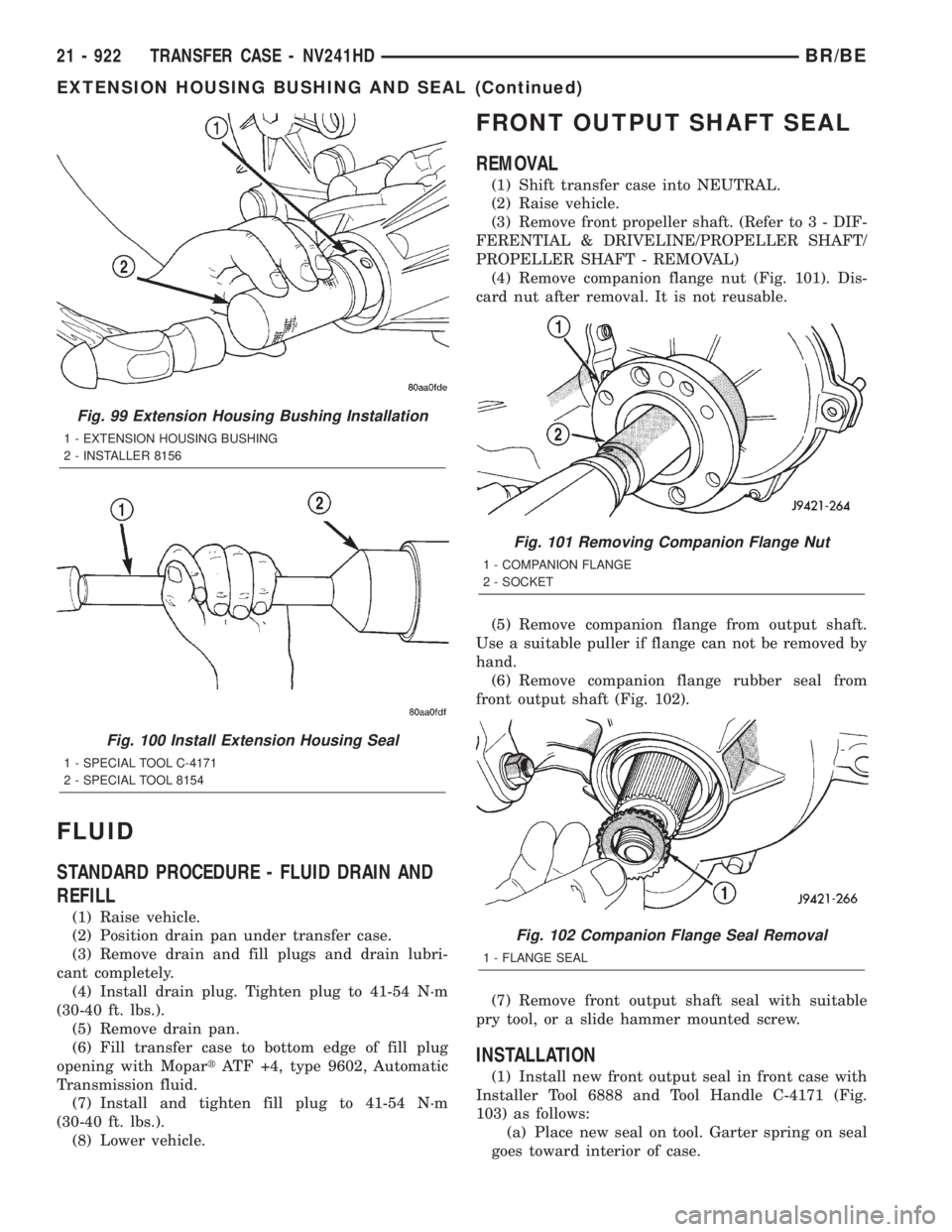
FLUID
STANDARD PROCEDURE - FLUID DRAIN AND
REFILL
(1) Raise vehicle.
(2) Position drain pan under transfer case.
(3) Remove drain and fill plugs and drain lubri-
cant completely.
(4) Install drain plug. Tighten plug to 41-54 N´m
(30-40 ft. lbs.).
(5) Remove drain pan.
(6) Fill transfer case to bottom edge of fill plug
opening with MopartATF +4, type 9602, Automatic
Transmission fluid.
(7) Install and tighten fill plug to 41-54 N´m
(30-40 ft. lbs.).
(8) Lower vehicle.
FRONT OUTPUT SHAFT SEAL
REMOVAL
(1) Shift transfer case into NEUTRAL.
(2) Raise vehicle.
(3) Remove front propeller shaft. (Refer to 3 - DIF-
FERENTIAL & DRIVELINE/PROPELLER SHAFT/
PROPELLER SHAFT - REMOVAL)
(4) Remove companion flange nut (Fig. 101). Dis-
card nut after removal. It is not reusable.
(5) Remove companion flange from output shaft.
Use a suitable puller if flange can not be removed by
hand.
(6) Remove companion flange rubber seal from
front output shaft (Fig. 102).
(7) Remove front output shaft seal with suitable
pry tool, or a slide hammer mounted screw.
INSTALLATION
(1) Install new front output seal in front case with
Installer Tool 6888 and Tool Handle C-4171 (Fig.
103) as follows:
(a) Place new seal on tool. Garter spring on seal
goes toward interior of case.
Fig. 99 Extension Housing Bushing Installation
1 - EXTENSION HOUSING BUSHING
2 - INSTALLER 8156
Fig. 100 Install Extension Housing Seal
1 - SPECIAL TOOL C-4171
2 - SPECIAL TOOL 8154
Fig. 101 Removing Companion Flange Nut
1 - COMPANION FLANGE
2 - SOCKET
Fig. 102 Companion Flange Seal Removal
1 - FLANGE SEAL
21 - 922 TRANSFER CASE - NV241HDBR/BE
EXTENSION HOUSING BUSHING AND SEAL (Continued)
Page 2558 of 2889
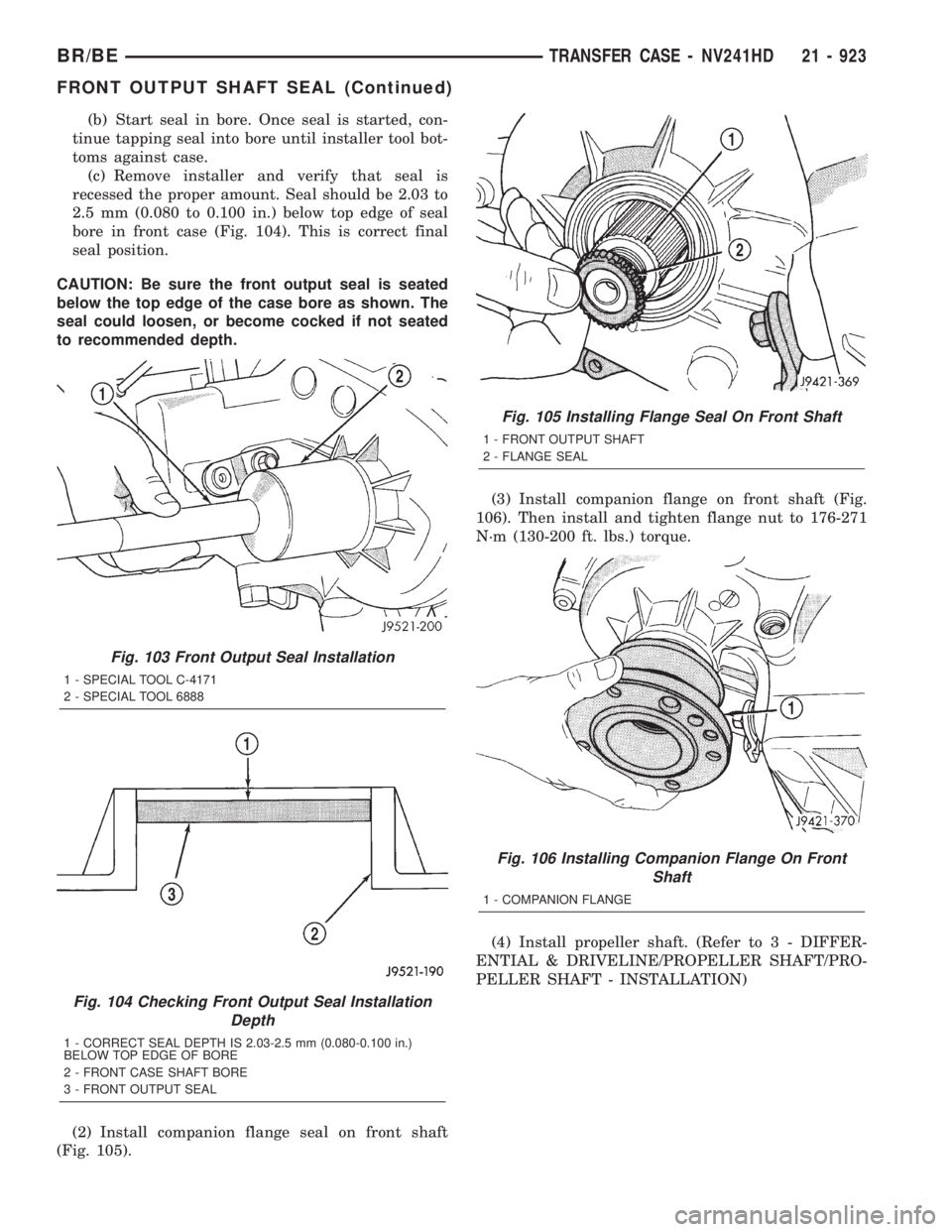
(b) Start seal in bore. Once seal is started, con-
tinue tapping seal into bore until installer tool bot-
toms against case.
(c) Remove installer and verify that seal is
recessed the proper amount. Seal should be 2.03 to
2.5 mm (0.080 to 0.100 in.) below top edge of seal
bore in front case (Fig. 104). This is correct final
seal position.
CAUTION: Be sure the front output seal is seated
below the top edge of the case bore as shown. The
seal could loosen, or become cocked if not seated
to recommended depth.
(2) Install companion flange seal on front shaft
(Fig. 105).(3) Install companion flange on front shaft (Fig.
106). Then install and tighten flange nut to 176-271
N´m (130-200 ft. lbs.) torque.
(4) Install propeller shaft. (Refer to 3 - DIFFER-
ENTIAL & DRIVELINE/PROPELLER SHAFT/PRO-
PELLER SHAFT - INSTALLATION)
Fig. 103 Front Output Seal Installation
1 - SPECIAL TOOL C-4171
2 - SPECIAL TOOL 6888
Fig. 104 Checking Front Output Seal Installation
Depth
1 - CORRECT SEAL DEPTH IS 2.03-2.5 mm (0.080-0.100 in.)
BELOW TOP EDGE OF BORE
2 - FRONT CASE SHAFT BORE
3 - FRONT OUTPUT SEAL
Fig. 105 Installing Flange Seal On Front Shaft
1 - FRONT OUTPUT SHAFT
2 - FLANGE SEAL
Fig. 106 Installing Companion Flange On Front
Shaft
1 - COMPANION FLANGE
BR/BETRANSFER CASE - NV241HD 21 - 923
FRONT OUTPUT SHAFT SEAL (Continued)
Page 2559 of 2889
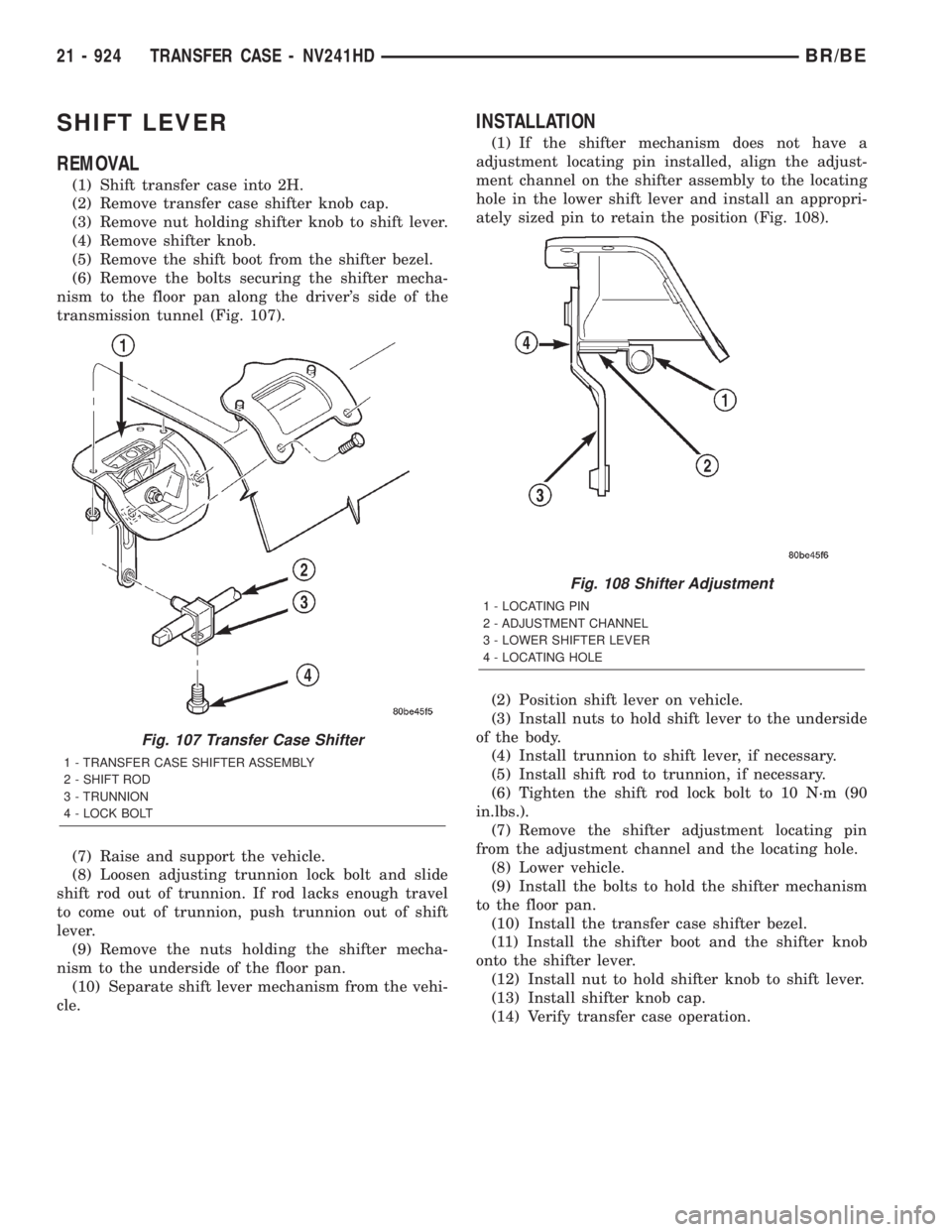
SHIFT LEVER
REMOVAL
(1) Shift transfer case into 2H.
(2) Remove transfer case shifter knob cap.
(3) Remove nut holding shifter knob to shift lever.
(4) Remove shifter knob.
(5) Remove the shift boot from the shifter bezel.
(6) Remove the bolts securing the shifter mecha-
nism to the floor pan along the driver's side of the
transmission tunnel (Fig. 107).
(7) Raise and support the vehicle.
(8) Loosen adjusting trunnion lock bolt and slide
shift rod out of trunnion. If rod lacks enough travel
to come out of trunnion, push trunnion out of shift
lever.
(9) Remove the nuts holding the shifter mecha-
nism to the underside of the floor pan.
(10) Separate shift lever mechanism from the vehi-
cle.
INSTALLATION
(1) If the shifter mechanism does not have a
adjustment locating pin installed, align the adjust-
ment channel on the shifter assembly to the locating
hole in the lower shift lever and install an appropri-
ately sized pin to retain the position (Fig. 108).
(2) Position shift lever on vehicle.
(3) Install nuts to hold shift lever to the underside
of the body.
(4) Install trunnion to shift lever, if necessary.
(5) Install shift rod to trunnion, if necessary.
(6) Tighten the shift rod lock bolt to 10 N´m (90
in.lbs.).
(7) Remove the shifter adjustment locating pin
from the adjustment channel and the locating hole.
(8) Lower vehicle.
(9) Install the bolts to hold the shifter mechanism
to the floor pan.
(10) Install the transfer case shifter bezel.
(11) Install the shifter boot and the shifter knob
onto the shifter lever.
(12) Install nut to hold shifter knob to shift lever.
(13) Install shifter knob cap.
(14) Verify transfer case operation.
Fig. 107 Transfer Case Shifter
1 - TRANSFER CASE SHIFTER ASSEMBLY
2 - SHIFT ROD
3 - TRUNNION
4 - LOCK BOLT
Fig. 108 Shifter Adjustment
1 - LOCATING PIN
2 - ADJUSTMENT CHANNEL
3 - LOWER SHIFTER LEVER
4 - LOCATING HOLE
21 - 924 TRANSFER CASE - NV241HDBR/BE
Page 2560 of 2889
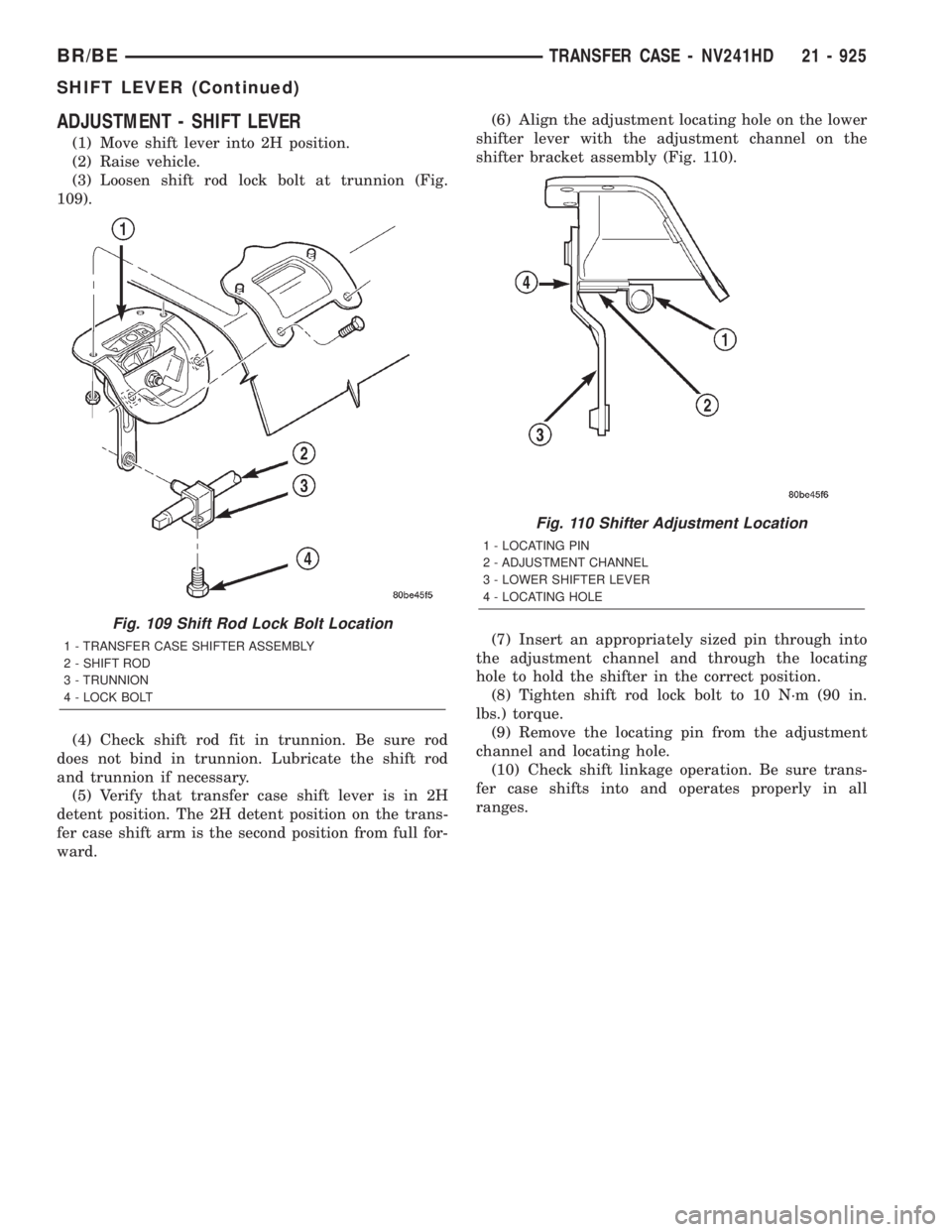
ADJUSTMENT - SHIFT LEVER
(1) Move shift lever into 2H position.
(2) Raise vehicle.
(3) Loosen shift rod lock bolt at trunnion (Fig.
109).
(4) Check shift rod fit in trunnion. Be sure rod
does not bind in trunnion. Lubricate the shift rod
and trunnion if necessary.
(5) Verify that transfer case shift lever is in 2H
detent position. The 2H detent position on the trans-
fer case shift arm is the second position from full for-
ward.(6) Align the adjustment locating hole on the lower
shifter lever with the adjustment channel on the
shifter bracket assembly (Fig. 110).
(7) Insert an appropriately sized pin through into
the adjustment channel and through the locating
hole to hold the shifter in the correct position.
(8) Tighten shift rod lock bolt to 10 N´m (90 in.
lbs.) torque.
(9) Remove the locating pin from the adjustment
channel and locating hole.
(10) Check shift linkage operation. Be sure trans-
fer case shifts into and operates properly in all
ranges.
Fig. 109 Shift Rod Lock Bolt Location
1 - TRANSFER CASE SHIFTER ASSEMBLY
2 - SHIFT ROD
3 - TRUNNION
4 - LOCK BOLT
Fig. 110 Shifter Adjustment Location
1 - LOCATING PIN
2 - ADJUSTMENT CHANNEL
3 - LOWER SHIFTER LEVER
4 - LOCATING HOLE
BR/BETRANSFER CASE - NV241HD 21 - 925
SHIFT LEVER (Continued)