DODGE RAM 2003 Service Repair Manual
Manufacturer: DODGE, Model Year: 2003, Model line: RAM, Model: DODGE RAM 2003Pages: 2895, PDF Size: 83.15 MB
Page 151 of 2895

²Ring gear too close to pinion gear (Fig. 11).
Increase backlash, by moving the ring away from the
pinion gear using the adjusters.
²Ring gear too far away from pinion gear (Fig.
12). Decrease backlash, by moving the ring closer to
the pinion gear using the adjusters.
²Ring gear too close to pinion gear (Fig. 13).
Increase backlash, by moving the ring away from the
pinion gear using the adjusters.
²Pinion gear set too low (Fig. 14). Increase pinion
gear height, by increasing the pinion depth shim
thickness.
²Pinion gear set too high (Fig. 15). Decrease pin-
ion depth, by decreasing the pinion depth shim thick-
ness.
SIDE GEAR CLEARANCE
When measuring side gear clearance, check each
gear independently. If it necessary to replace a side
gear, replace both gears as a matched set.
(1) Install the axle shafts and C-locks and pinion
mate shaft.(2) Measure each side gear clearance. Insert a
matched pair of feeler gauge blades between the gear
and differential housing on opposite sides of the hub
(Fig. 16).
(3) If side gear clearances is no more than 0.005
inch. Determine if the axle shaft is contacting the
pinion mate shaft.Do not remove the feeler
gauges, inspect the axle shaft with the feeler
gauge inserted behind the side gear.If the end of
Fig. 11 INCORRECT BACKLASH
1 - DRIVE SIDE TOE
2 - COAST SIDE HEEL
Fig. 12 INCORRECT BACKLASH
1 - DRIVE SIDE HEEL
2 - COAST SIDE HEEL
Fig. 13 INCORRECT BACKLASH
1 - DRIVE SIDE TOE
2 - COAST SIDE TOE
Fig. 14 LOW PINION HEIGHT
Fig. 15 HIGH PINION HEIGHT
3 - 78 REAR AXLE-91/4DR
REAR AXLE - 9 1/4 (Continued)
Page 152 of 2895

the axle shaft is not contacting the pinion mate
shaft, the side gear clearance is acceptable.
(4) If clearance is more than 0.005 inch (axle shaft
not contacting mate shaft), record the side gear clear-
ance. Remove the thrust washer and measure its
thickness with a micrometer. Add the washer thick-
ness to the recorded side gear clearance. The sum of
gear clearance and washer thickness will determine
required thickness of replacement thrust washer
(Fig. 17).In some cases, the end of the axle shaft will move
and contact the mate shaft when the feeler gauge is
inserted. The C-lock is preventing the side gear from
sliding on the axle shaft.
(5) If there is no side gear clearance, remove the
C-lock from the axle shaft. Use a micrometer to mea-
sure the thrust washer thickness. Record the thick-
ness and re-install the thrust washer. Assemble the
differential case without the C-lock installed and re-
measure the side gear clearance.
(6) Compare both clearance measurements. If the
difference is less than 0.012 inch (0.305 mm), add
clearance recorded when the C-lock was installed to
thrust washer thickness measured. The sum will
determine the required thickness of the replacement
thrust washer.
(7) If clearance is 0.012 inch (0.305 mm) or
greater, both side gears must be replaced (matched
set) and the clearance measurements repeated.
(8) If clearance (above) continues to be 0.012 inch
(0.305 mm) or greater, the case must be replaced.
SPECIFICATIONS
AXLE SPECIFICATIONS
DESCRIPTION SPECIFICATION
Axle Ratio 3.21, 3.55, 3.92
Differential Case Flange Runout 0.076 mm (0.003 in.)
Differential Case Clearance 0.12 mm (0.005 in.)
Ring Gear Diameter 235 mm (9.25 in.)
Ring Gear Backlash 0.12-0.20 mm (0.005-0.008 in.)
Ring Gear Runout 0.12 mm (0.005 in.)
Pinion Bearing Preload - New Bearings 1.7-4 N´m (15-35 in. lbs.)
Pinion Bearing Preload - Original Bearings 1-2 N´m (10-20 in. lbs.)
Fig. 16 SIDE GEAR CLEARANCE
1 - FEELER GAUGE
2 - SIDE GEAR
Fig. 17 SIDE GEAR CALCULATIONS
DRREAR AXLE - 9 1/4 3 - 79
REAR AXLE - 9 1/4 (Continued)
Page 153 of 2895

TORQUE SPECIFICATIONS
DESCRIPTION N´m Ft. Lbs. In. Lbs.
Differential Cover Bolts 41 30 -
Bearing Cap Bolts 136 100 -
Ring Gear Bolts 157 115 -
Pinion Nut Minimum 285 210 -
Adjuster Lock Screw 10 7.5 90
Backing Plate Bolts 65 48 -
Pinion Mate Shaft Lock
Screw11 8 -
Axle U-Bolt Nuts 149 110 -
SPECIAL TOOLS
PULLER 6790
REMOVER 6310
INSTALLER C-4198
HANDLE C-4171
INSTALLER C-4076-B
HANDLE C-4735-1
3 - 80 REAR AXLE-91/4DR
REAR AXLE - 9 1/4 (Continued)
Page 154 of 2895

HOLDER 6719
PULLER C-452
INSTALLER C-3718
WRENCH C-4164
PULLER C-293-PA
ADAPTERS C-293-37
PLUG SP-3289
ADAPTERS C-293-47
INSTALLER C-4340
FIXTURE 8138
DRREAR AXLE - 9 1/4 3 - 81
REAR AXLE - 9 1/4 (Continued)
Page 155 of 2895

INSTALLER C-4345
REMOVER C-4307
INSTALLER C-4308
INSTALLER D-130
INSTALLER C-3095-A
TRAC-LOK TOOLS 8140
TRAC-LOK TOOLS 6960
PINION BLOCK 8540
ARBOR DISCS 8541
PINION GAUGE SET 6775
3 - 82 REAR AXLE-91/4DR
REAR AXLE - 9 1/4 (Continued)
Page 156 of 2895

AXLE SHAFTS
REMOVAL
(1) Place transmission in neutral.
(2) Raise and support the vehicle.
(3) Remove wheel and tire assembly.
(4) Remove brake caliper, adapter and rotor (Fig.
18).
(5) Remove differential housing cover and drain
lubricant.
(6) Rotate differential case so pinion mate shaft
lock screw is accessible. Remove lock screw and pin-
ion mate shaft from differential case (Fig. 19).
(7) Push axle shaft inward and remove axle shaft
C-lock from the axle shaft (Fig. 20).(8) Remove axle shaft (Fig. 21) carefully to prevent
damage to the shaft bearing and seal in the axle
tube.
INSTALLATION
(1) Lubricate bearing bore and seal lip with gear
lubricant.
(2) Insall axle shaft and engage into side gear
splines.
NOTE: Use care to prevent shaft splines from dam-
aging axle shaft seal.
(3) Insert C-lock in end of axle shaft then push
axle shaft outward to seat C-lock in side gear.
Fig. 18 REAR ROTOR
1 - ROTOR
2 - CALIPER ADAPTER
3 - CALIPER
Fig. 19 PINION MATE SHAFT LOCK SCREW
1 - LOCK SCREW
2 - PINION MATE SHAFT
Fig. 20 AXLE SHAFT C-LOCK
1 - C-LOCK
2 - AXLE SHAFT
3 - SIDE GEAR
Fig. 21 AXLE SHAFT
1 - AXLE SHAFT
2 - SUPPORT PLATE
3 - CALIPER
4 - PARK BRAKE SHOE ASSEMBLY
DRREAR AXLE - 9 1/4 3 - 83
Page 157 of 2895

(4) Insert pinion shaft into differential case and
through thrust washers and differential pinions.
(5) Align hole in shaft with hole in the differential
case and install lock screw with Loctiteton the
threads. Tighten lock screw to 11 N´m (8 ft. lbs.).
(6) Install differential cover and fill with gear
lubricant to the bottom of the fill plug hole.
(7) Install brake rotor, caliper adapter and caliper.
(8) Install wheel and tire.
(9) Remove support and lower vehicle.
AXLE SHAFT SEALS
REMOVAL
(1) Remove axle shaft.
(2) Remove axle shaft seal (Fig. 22) from the axle
tube with a small pry bar.
INSTALLATION
(1) Wipe the axle tube bore clean. Remove any old
sealer or burrs from the tube.
(2) Coat the lip of thenewseal with axle lubricant
and install a seal with Installer C-4076-B and Han-
dle C-4735-1.
NOTE: When tool contacts the axle tube, the seal is
installed to the correct depth.
(3) Install the axle shaft.(4) Install differential cover and fill with gear
lubricant to the bottom of the fill plug hole.
AXLE BEARINGS
REMOVAL
(1) Remove axle shaft.
(2) Remove axle shaft seal from axle tube with a
small pry bar.
NOTE: The seal and bearing can be removed at the
same time with the bearing removal tool.
(3) Remove axle shaft bearing with Bearing
Remover 6310 and Foot 6310-9 (Fig. 23).
INSTALLATION
(1) Wipe the axle tube bore clean. Remove any old
sealer or burrs from the tube.
(2) Install axle shaft bearing with Installer C-4198
and Handle C-4171. Drive bearing in until tool con-
tacts the axle tube.
NOTE: Bearing is installed with the bearing part
number against the installer.
Fig. 22 AXLE SHAFT SEAL
1 - AXLE SEAL
2 - AXLE BEARING
Fig. 23 AXLE SHAFT BEARING REMOVER
1 - AXLE SHAFT TUBE
2 - NUT
3 - GUIDE PLATE
4 - GUIDE
5 - THREADED ROD
6 - ADAPTER
7 - FOOT
3 - 84 REAR AXLE-91/4DR
AXLE SHAFTS (Continued)
Page 158 of 2895

(3) Coat the lip of thenewaxle seal with axle
lubricant and install with Installer C-4076-B and
Handle C-4735-1.
NOTE: When tool contacts the axle tube, the seal is
installed to the correct depth.
(4) Install the axle shaft.
(5) Install differential cover and fill with gear
lubricant to the bottom of the fill plug hole.
PINION SEAL
REMOVAL
(1) Mark universal joint, companion flange and
pinion shaft for installation reference.
(2) Remove propeller shaft from the companion
flange.
(3) Remove the brake rotors to prevent any drag.
(4) Rotate companion flange three or four times
and record pinion rotating torque with an inch pound
torque wrench.
(5) Install two bolts into the companion flange
threaded holes, 180É apart. Position Holder 6719A
against the companion flange and install and tighten
two bolts and washers into the remaining holes.
(6) Hold the companion flange with Holder 6719A
and remove pinion nut and washer.
(7) Remove companion flange with Remover C-452
(Fig. 24).(8) Remove pinion seal with pry tool or slide-ham-
mer mounted screw.
INSTALLATION
(1) Apply a light coating of gear lubricant on the
lip of pinion seal.
(2) Installnewpinion seal with Installer C-3860-A
and Handle C-4171 (Fig. 25)
(3) Install companion flange on the end of the
shaft with the reference marks aligned.
(4) Install two bolts into the threaded holes in the
companion flange, 180É apart.
(5) Position Holder 6719 against the companion
flange and install a bolt and washer into one of the
remaining threaded holes. Tighten the bolts so holder
is held to the flange.
(6) Install companion flange on pinion shaft with
Installer C-3718 and Holder 6719.
(7) Install pinion washer and anewpinion nut.
The convex side of the washer must face outward.
CAUTION: Never exceed the minimum tightening
torque 285 N´m (210 ft. lbs.) when installing the
companion flange retaining nut at this point. Dam-
age to collapsible spacer or bearings may result.
(8) Hold companion flange with Holder 6719 and
tighten the pinion nut with a torque set to 285 N´m
(210 ft. lbs.) (Fig. 26). Rotate pinion several revolu-
tions to ensure the bearing rollers are seated.
(9) Rotate pinion with an inch pound torque
wrench. Rotating torque should be equal to the read-
ing recorded during removal plus an additional 0.56
N´m (5 in. lbs.) (Fig. 27).
Fig. 24 COMPANION FLANGE
1 - COMPANION FLANGE
2 - PULLER
Fig. 25 PINION SEAL INSTALLER
1 - HANDLE
2 - INSTALLER
3 - HOUSING
DRREAR AXLE - 9 1/4 3 - 85
AXLE BEARINGS (Continued)
Page 159 of 2895

CAUTION: Never loosen pinion nut to decrease pin-
ion bearing rotating torque and never exceed spec-
ified preload torque. If rotating torque is exceeded,
a new collapsible spacer must be installed.(10) If rotating torque is low, use Holder 6719 to
hold the companion flange and tighten pinion nut in
6.8 N´m (5 ft. lbs.) increments until proper rotating
torque is achieved.
NOTE: The bearing rotating torque should be con-
stant during a complete revolution of the pinion. If
the rotating torque varies, this indicates a binding
condition.
NOTE: The seal replacement is unacceptable if the
final pinion nut torque is less than 285 N´m (210 ft.
lbs.).
(11) Install propeller shaft with the installation
reference marks aligned.
(12) Tighten the companion flange bolts to 108
N´m (80 ft. lbs.).
(13) Install brake rotors.
(14) Check the differential lubricant level.
DIFFERENTIAL
DESCRIPTION
The differential case is a one-piece design. The dif-
ferential pinion mate shaft is retained with a
threaded pin. Differential bearing preload and ring
gear backlash are set and maintained by threaded
adjusters at the outside of the differential housing.
Pinion bearing preload is set and maintained by the
use of a collapsible spacer. The removable differential
cover provides a means for inspection and service.
OPERATION
During straight-ahead driving, the differential pin-
ion gears do not rotate on the pinion mate shaft. This
occurs because input torque applied to the gears is
divided and distributed equally between the two side
gears. As a result, the pinion gears revolve with the
pinion mate shaft but do not rotate around it (Fig.
28).
When turning corners, the outside wheel must
travel a greater distance than the inside wheel to
complete a turn. To accomplish this, the differential
allows the axle shafts to turn at unequal speeds (Fig.
29). In this instance, the input torque applied to the
pinion gears is not divided equally. The pinion gears
now rotate around the pinion mate shaft in opposite
directions. This allows the side gear and axle shaft
attached to the outside wheel to rotate at a faster
speed.
REMOVAL
(1) Remove filler plug from the differential cover.
Fig. 26 TIGHTENING PINION NUT
1 - DIFFERENTIAL HOUSING
2 - COMPANION FLANGE HOLDER
3 - TORQUE WRENCH
Fig. 27 PINION ROTATION TORQUE
1 - COMPANION FLANGE
2 - TORQUE WRENCH
3 - 86 REAR AXLE-91/4DR
PINION SEAL (Continued)
Page 160 of 2895
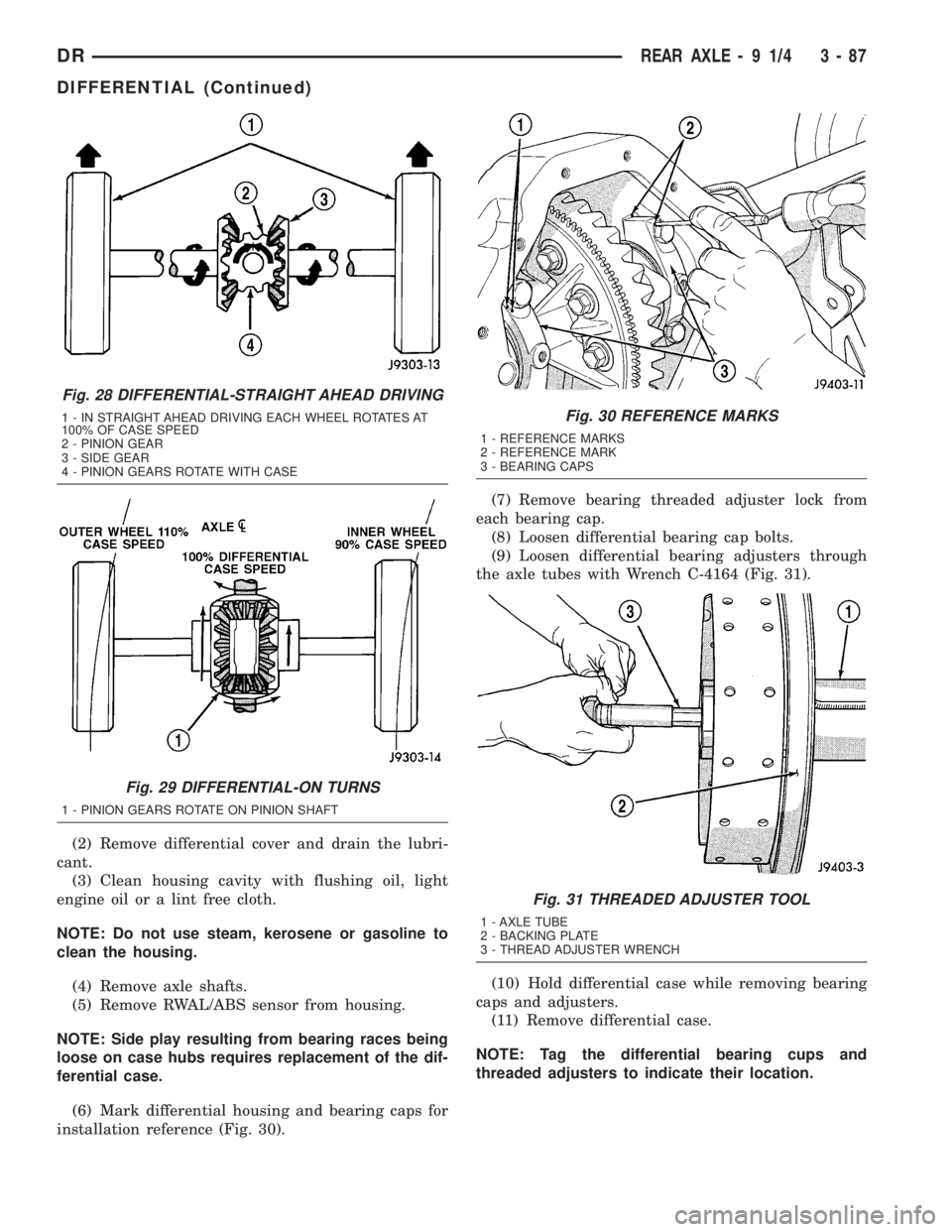
(2) Remove differential cover and drain the lubri-
cant.
(3) Clean housing cavity with flushing oil, light
engine oil or a lint free cloth.
NOTE: Do not use steam, kerosene or gasoline to
clean the housing.
(4) Remove axle shafts.
(5) Remove RWAL/ABS sensor from housing.
NOTE: Side play resulting from bearing races being
loose on case hubs requires replacement of the dif-
ferential case.
(6) Mark differential housing and bearing caps for
installation reference (Fig. 30).(7) Remove bearing threaded adjuster lock from
each bearing cap.
(8) Loosen differential bearing cap bolts.
(9) Loosen differential bearing adjusters through
the axle tubes with Wrench C-4164 (Fig. 31).
(10) Hold differential case while removing bearing
caps and adjusters.
(11) Remove differential case.
NOTE: Tag the differential bearing cups and
threaded adjusters to indicate their location.
Fig. 28 DIFFERENTIAL-STRAIGHT AHEAD DRIVING
1 - IN STRAIGHT AHEAD DRIVING EACH WHEEL ROTATES AT
100% OF CASE SPEED
2 - PINION GEAR
3 - SIDE GEAR
4 - PINION GEARS ROTATE WITH CASE
Fig. 29 DIFFERENTIAL-ON TURNS
1 - PINION GEARS ROTATE ON PINION SHAFT
Fig. 30 REFERENCE MARKS
1 - REFERENCE MARKS
2 - REFERENCE MARK
3 - BEARING CAPS
Fig. 31 THREADED ADJUSTER TOOL
1 - AXLE TUBE
2 - BACKING PLATE
3 - THREAD ADJUSTER WRENCH
DRREAR AXLE - 9 1/4 3 - 87
DIFFERENTIAL (Continued)