DODGE RAM 2003 Service Repair Manual
Manufacturer: DODGE, Model Year: 2003, Model line: RAM, Model: DODGE RAM 2003Pages: 2895, PDF Size: 83.15 MB
Page 131 of 2895

ASSEMBLY
(1) Pack the bearing caps 1/3 full of wheel bearing
lubricant. Apply extreme pressure (EP), lithium-base
lubricant to aid in installation.
(2) Position the spider in the yoke. Insert the seals
and bearings. Tap the bearing caps into the yoke
bores far enough to hold the spider in position.
(3) Place the socket (driver) against one bearing
cap. Position the yoke with the socket in a vise.
(4) Tighten the vise to force the bearing caps into
the yoke. Force the caps enough to install the retain-
ing clips.
(5) Install the bearing cap retaining clips.
(6) Install axle shaft.
INSTALLATION
(1) Clean axle shaft and apply a thin film of
Mopar Wheel Bearing Grease to the shaft splines
and hub bore.
(2) Install axle shaft through the steering knuckle
and into the differential side gears (Fig. 19).
CAUTION: Do not damage axle shaft seal during
axle installtion.
(3) Install hub bearing in the knuckle.
(4) Install hub bearing bolts and tighten to 202
N´m (149 ft. lbs.).
(5) Install ABS wheel speed sensor, brake rotor
and caliper.
(6) Install axle washer and nut. Tighten axle nut
to 179 N´m (132 ft. lbs.).(7) Rotate axle several 5 to 10 times to seat the
wheel bearing.
(8) Tighten axle nut to final torque of 356 N´m
(263 ft. lbs.).
(9) Align nut to next cotter pin hole and install
new cotter pin.
(10) Install wheel and tire assembly.
AXLE SHAFT SEALS
REMOVAL
(1) Remove hub bearings and axle shafts.
(2) Remove differential from differential housing.
(3) Remove differential bearing adjusters (Fig. 20).
(4) Remove axle seals (Fig. 21) located behind
adjusters with Receiver 8498 and Extractor 6310.
(5) Install Receiver 8498 into the adjuster bore.
(6) Install Extractor Rod 6310 with Extractor Foot
6310-9 through the receiver and the axle seal (Fig.
22).
(7) Install Extractor Plate 6310-2 and Nut 6310-7
on the extractor rod.
(8) Tighten nut on the extractor rod (Fig. 23) and
pull the seal out and into the receiver.
INSTALLATION
(1) Install axle seal on Installer Cups 8885-2 and
position cups with seals into the housing.
NOTE: Seal are installed with the axle guide facing
outward.
Fig. 19 AXLE SHAFT
1 - AXLE YOKE
2 - AXLE SHAFT
3 - KNUCKLE
Fig. 20 ADJUSTERS
1 - DIFFERENTIAL CASE BEARING ADJUSTERS
2 - DIFFERENTIAL HOUSING
3 - 58 FRONT AXLE - 9 1/4 AADR
AXLE SHAFTS (Continued)
Page 132 of 2895

(2) Install Turnbuckle 8885-1 (Fig. 24) into the
installer cups and expand the turnbuckle until the
seal bottom out in the housing.
(3) Install differential into the axle housing.
(4) Install axle shaft and hub bearings
Fig. 21 AXLE SHAFT SEAL
1 - ADJUSTER THREADS
2 - SEAL
Fig. 22 SEAL RECEIVER
1 - RECEIVER
2 - EXTRACTOR FOOT
Fig. 23 SEAL EXTRACTOR
1 - EXTRACTOR ROD
2 - EXTRACTOR NUT
Fig. 24 AXLE SEAL INSTALLER
1 - INSTALLER CUP
2 - INSTALLER TURNBUCKLE
3 - INSTALLER CUP
DRFRONT AXLE - 9 1/4 AA 3 - 59
AXLE SHAFT SEALS (Continued)
Page 133 of 2895

PINION SEAL
REMOVAL
(1) Mark the propeller shaft and pinion flange for
installation reference.
(2) Remove propeller shaft.
(3) Remove hub bearings and axle shafts.
(4) Rotate pinion gear three or four times.
(5) Measure and record the torque necessary to
rotate (Fig. 25) the pinion gear with an inch pound
torque wrench.
(6) Hold pinion flange with Flange Wrench 8979
(Fig. 26) and remove pinion flange nut and washer.(7) Remove pinion flange with Pinion Flange
Puller 8992 (Fig. 27).
(8) Remove pinion shaft seal with a pry tool or
slide hammer mounted screw.
INSTALLATION
(1) Installnewpinion seal with Installer 8882 and
Handle C-4171 (Fig. 28).
(2) Apply a light coat of teflon thread sealant to
the pinion flange splines.
(3) Lightly tap the pinion flange onto the pinion
until a few threads are showing.
(4) Install flange washer andnewpinion nut.
(5) Hold flange with Flange Wrench 8979 and
tighten pinion nut until pinion end play is taken up.
(6) Rotate pinion several times to seat bearings.
(7) Measure pinion rotating torque with an inch
pound torque wrench and compare it to recorded
measurement. Tighten pinion nut in small incre-
Fig. 25 PINION ROTATING TORQUE
1 - PINION FLANGE
2 - TORQUE WRENCH
Fig. 26 FLANGE WRENCH
1 - PINION FLANGE
2 - WRENCH
Fig. 27 PINION FLANGE PULLER
1 - PINION FLANGE
2 - PULLER
Fig. 28 PINION SEAL INSTALLER
1 - HANDLE
2 - INSTALLER
3 - 60 FRONT AXLE - 9 1/4 AADR
Page 134 of 2895
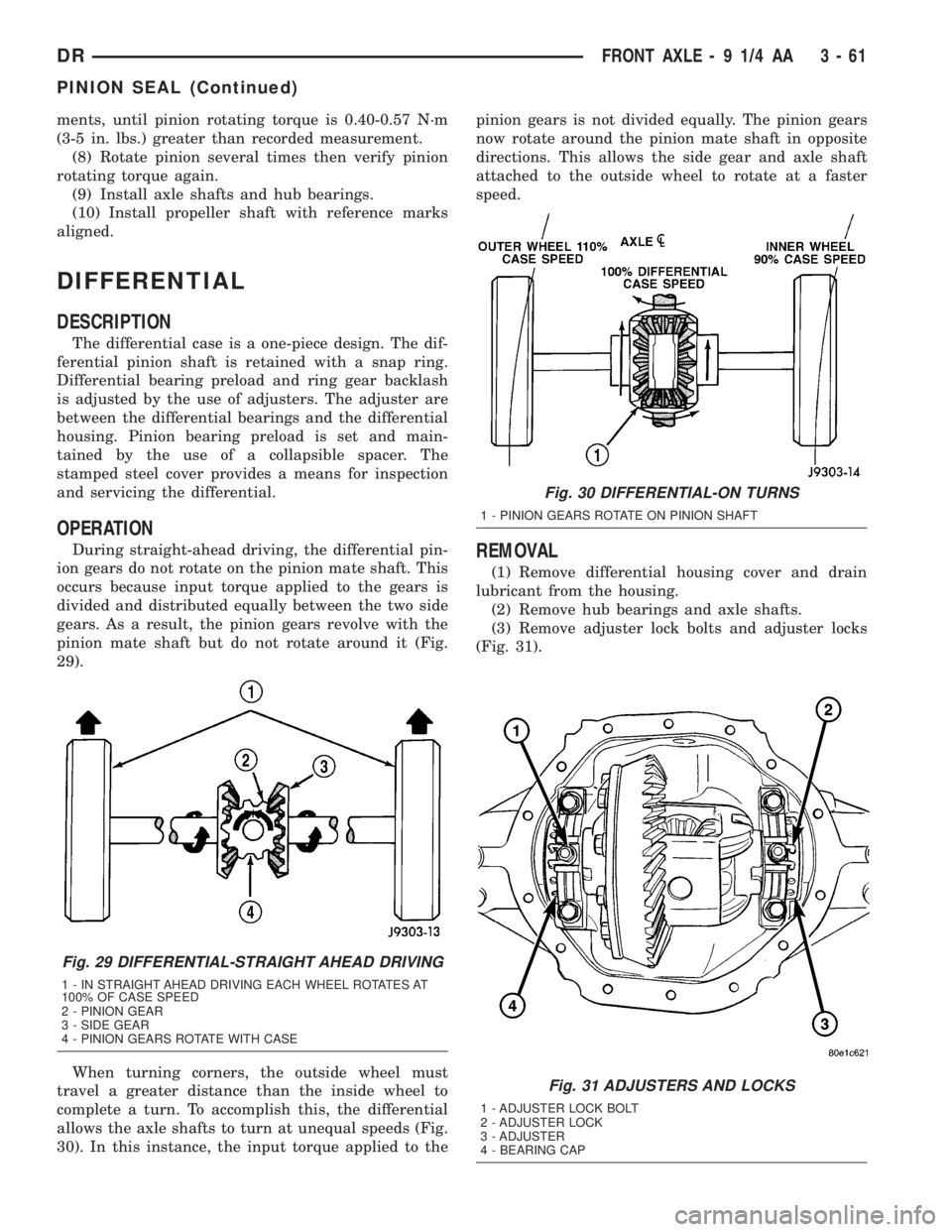
ments, until pinion rotating torque is 0.40-0.57 N´m
(3-5 in. lbs.) greater than recorded measurement.
(8) Rotate pinion several times then verify pinion
rotating torque again.
(9) Install axle shafts and hub bearings.
(10) Install propeller shaft with reference marks
aligned.
DIFFERENTIAL
DESCRIPTION
The differential case is a one-piece design. The dif-
ferential pinion shaft is retained with a snap ring.
Differential bearing preload and ring gear backlash
is adjusted by the use of adjusters. The adjuster are
between the differential bearings and the differential
housing. Pinion bearing preload is set and main-
tained by the use of a collapsible spacer. The
stamped steel cover provides a means for inspection
and servicing the differential.
OPERATION
During straight-ahead driving, the differential pin-
ion gears do not rotate on the pinion mate shaft. This
occurs because input torque applied to the gears is
divided and distributed equally between the two side
gears. As a result, the pinion gears revolve with the
pinion mate shaft but do not rotate around it (Fig.
29).
When turning corners, the outside wheel must
travel a greater distance than the inside wheel to
complete a turn. To accomplish this, the differential
allows the axle shafts to turn at unequal speeds (Fig.
30). In this instance, the input torque applied to thepinion gears is not divided equally. The pinion gears
now rotate around the pinion mate shaft in opposite
directions. This allows the side gear and axle shaft
attached to the outside wheel to rotate at a faster
speed.REMOVAL
(1) Remove differential housing cover and drain
lubricant from the housing.
(2) Remove hub bearings and axle shafts.
(3) Remove adjuster lock bolts and adjuster locks
(Fig. 31).
Fig. 29 DIFFERENTIAL-STRAIGHT AHEAD DRIVING
1 - IN STRAIGHT AHEAD DRIVING EACH WHEEL ROTATES AT
100% OF CASE SPEED
2 - PINION GEAR
3 - SIDE GEAR
4 - PINION GEARS ROTATE WITH CASE
Fig. 30 DIFFERENTIAL-ON TURNS
1 - PINION GEARS ROTATE ON PINION SHAFT
Fig. 31 ADJUSTERS AND LOCKS
1 - ADJUSTER LOCK BOLT
2 - ADJUSTER LOCK
3 - ADJUSTER
4 - BEARING CAP
DRFRONT AXLE - 9 1/4 AA 3 - 61
PINION SEAL (Continued)
Page 135 of 2895

(4) Mark bearing caps left and right for installa-
tion reference.
(5) Remove bearing cap bolts and remove bearing
caps.
(6) Loosen differential bearing adjusters (Fig. 32)
with Spanner Wrench 8883.
(7) Remove differential case from the housing.
(8) Remove bearing cups and tag them left and
right for installation reference.
DISASSEMBLY
(1) Remove pinion shaft lock bolt.
(2) Remove pinion shaft (Fig. 33).(3) Rotate differential pinion gears to differential
window and remove pinion gears and thrust washers
(Fig. 34).
(4) Remove differential side gears and thrust
washers (Fig. 35).
Fig. 32 ADJUSTERS
1 - BEARING CUP
2 - ADJUSTER
3 - BEARING CUP
4 - ADJUSTER
Fig. 33 PINION SHAFT
1 - PINION SHAFT
2 - PUNCH
3 - PINION GEAR
4 - SIDE GEAR
Fig. 34 PINION GEAR
1 - DIFFERENTIAL WINDOW
2 - PINION GEAR
3 - THRUST GEAR
Fig. 35 SIDE GEARS
1 - SIDE GEAR
2 - SIDE GEAR
3 - PINION GEARS
3 - 62 FRONT AXLE - 9 1/4 AADR
DIFFERENTIAL (Continued)
Page 136 of 2895
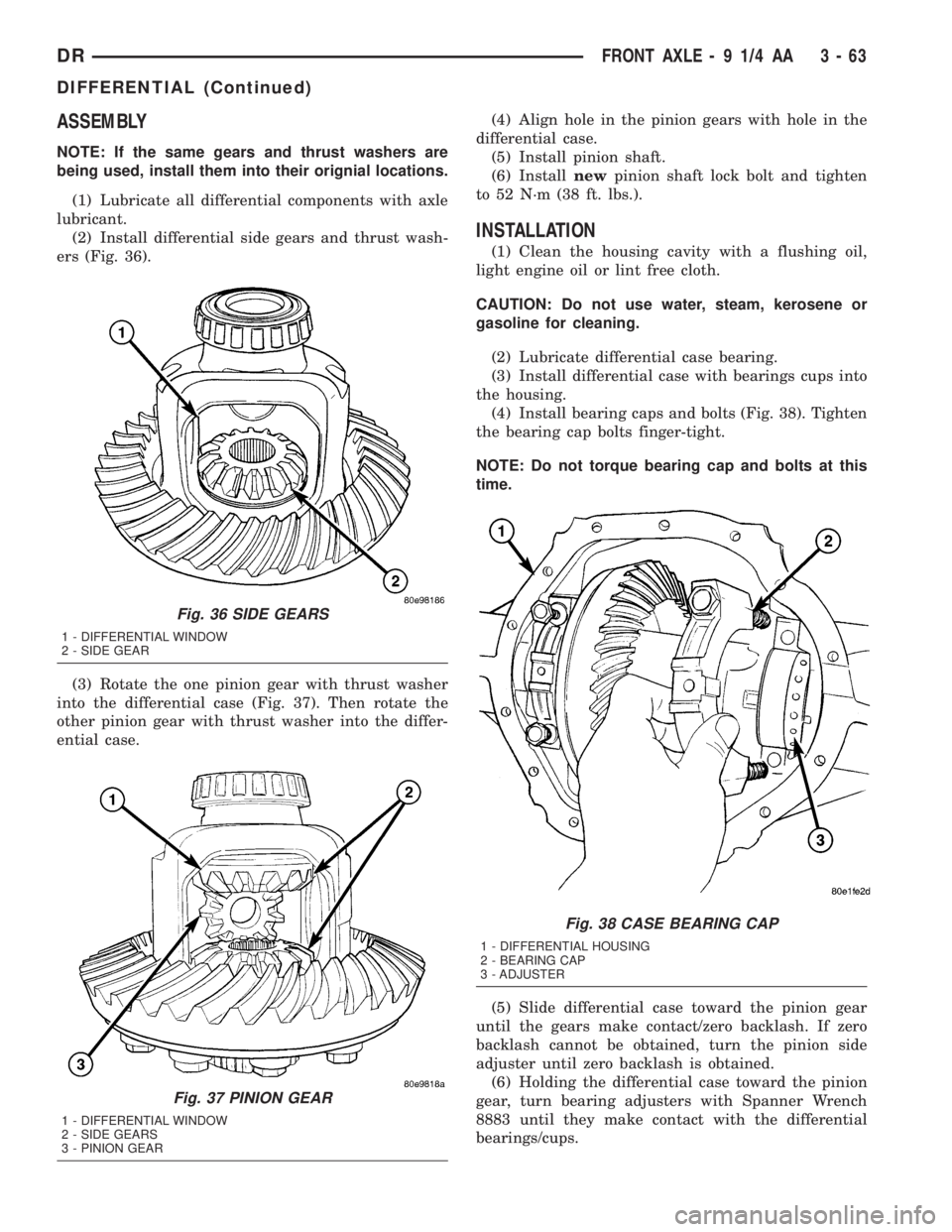
ASSEMBLY
NOTE: If the same gears and thrust washers are
being used, install them into their orignial locations.
(1) Lubricate all differential components with axle
lubricant.
(2) Install differential side gears and thrust wash-
ers (Fig. 36).
(3) Rotate the one pinion gear with thrust washer
into the differential case (Fig. 37). Then rotate the
other pinion gear with thrust washer into the differ-
ential case.(4) Align hole in the pinion gears with hole in the
differential case.
(5) Install pinion shaft.
(6) Installnewpinion shaft lock bolt and tighten
to 52 N´m (38 ft. lbs.).
INSTALLATION
(1) Clean the housing cavity with a flushing oil,
light engine oil or lint free cloth.
CAUTION: Do not use water, steam, kerosene or
gasoline for cleaning.
(2) Lubricate differential case bearing.
(3) Install differential case with bearings cups into
the housing.
(4) Install bearing caps and bolts (Fig. 38). Tighten
the bearing cap bolts finger-tight.
NOTE: Do not torque bearing cap and bolts at this
time.
(5) Slide differential case toward the pinion gear
until the gears make contact/zero backlash. If zero
backlash cannot be obtained, turn the pinion side
adjuster until zero backlash is obtained.
(6) Holding the differential case toward the pinion
gear, turn bearing adjusters with Spanner Wrench
8883 until they make contact with the differential
bearings/cups.
Fig. 36 SIDE GEARS
1 - DIFFERENTIAL WINDOW
2 - SIDE GEAR
Fig. 37 PINION GEAR
1 - DIFFERENTIAL WINDOW
2 - SIDE GEARS
3 - PINION GEAR
Fig. 38 CASE BEARING CAP
1 - DIFFERENTIAL HOUSING
2 - BEARING CAP
3 - ADJUSTER
DRFRONT AXLE - 9 1/4 AA 3 - 63
DIFFERENTIAL (Continued)
Page 137 of 2895

(7) Back off the ring gear side adjuster 4 holes, to
obtain initial ring gear backlash.
(8) Install ring gear side adjuster lock and bolt. Do
not tighten adjuster lock bolt at this time.
(9) Tighten pinion gear side adjuster firmly
against the differential case bearing cup.
(10) Rotate the pinion several times to seat the dif-
ferential bearings.
(11) Loosen pinion gear side adjuster until it is no
longer in contact with the bearing cup.
(12) Tighten pinion gear side adjuster until it just
makes contact with the bearing cup.
(13) Tighten pinion gear side adjuster an addi-
tional:
²New Bearings:6 Adjuster Holes
²Original Bearings:4 Adjuster Holes
(14) Install pinion gear side adjuster lock and bolt.
Do not tighten adjuster lock bolt at this time.
(15) Tighten bearing cap bolts to 85 N´m (63 ft.
lbs.).
(16) Tighten adjuster lock bolts to 25 N´m (18 ft.
lbs.) (Fig. 39).(17) Measure ring gear backlash and check gear
tooth contact pattern. Refer to Adjustments for pro-
cedure.
(18) Install axle shafts and hub bearings.
(19) Install differential housing gasket and cover.
Tighten cover bolts to 40 N´m (30 ft. lbs.).
(20) Fill differential with lubricant, refer to Lubri-
cation & Maintenance for capacity and lubricant
type.
(21) Install fill plug and tighten to 32 N´m (24 ft.
lbs.).
DIFFERENTIAL CASE
BEARINGS
REMOVAL
(1) Remove the differential case from the housing.
(2) Install Plug 8888 into the end of the case.
(3) Remove differental case bearings with Bearing
Splitter 1130 and Bridge 938 (Fig. 40).
Fig. 39 ADJUSTER LOCK BOLT
1 - DIFFERENTIAL CASE
2 - ADJUSTER LOCK
3 - ADJUSTER LOCK BOLT
4 - BEARING CAP BOLT
Fig. 40 DIFFERENTIAL CASE BEARING
1 - BRIDGE
2 - SPLITTER
3 - BEARING
4 - PLUG
3 - 64 FRONT AXLE - 9 1/4 AADR
DIFFERENTIAL (Continued)
Page 138 of 2895

INSTALLATION
(1) Set differential case on Plug 8888.
(2) Install differenial case bearings with Installer
8881 and Handle C-4171 (Fig. 41).
(3) Install differentail case into housing.
PINION GEAR/RING GEAR
REMOVAL
NOTE: The ring and pinion gears are service in a
matched set. Never replace the ring gear/pinion
gear without replacing the other matching gear.
(1) Mark pinion flange and propeller shaft for
installation alignment.
(2) Disconnect propeller shaft from pinion flange
and remove propeller shaft.
(3) Remove axle shafts.
(4) Remove differential from housing.
(5) Place differential case in a vise with soft metal
jaw protectors
(6) Remove bolts holding ring gear to differential
case.
(7) Drive ring gear from differential case with a
soft hammer (Fig. 42).
(8) Hold pinion flange with Flange Wrench 8979
(Fig. 43) and remove pinion flange nut and washer.(9) Remove pinion flange from pinion with Pinion
Flange Puller 8992 (Fig. 44).
(10) Remove pinion gear from housing with Pinion
Driver 8976 and a hammer (Fig. 45).
NOTE: Thread drive on shaft until it bottoms out.
(11) Remove pinion seal with a slide hammer or
pry bar.
(12) Remove and discard front pinion bearing
CAUTION: Do not reuse front pinion bearing/cup.
(13) Remove collapsible spacer from the pinion
shaft.
Fig. 41 DIFFERENTIAL CASE BEARINGS
1 - HANDLE
2 - DIFFERENTIAL CASE
3 - BEARING
4 - INSTALLER
Fig. 42 RING GEAR
1 - DIFFERENTIAL CASE
2 - RING GEAR
3 - HAMMER
Fig. 43 FLANGE WRENCH
1 - PINION FLANGE
2 - WRENCH
DRFRONT AXLE - 9 1/4 AA 3 - 65
DIFFERENTIAL CASE BEARINGS (Continued)
Page 139 of 2895

(14) Remove rear pinion bearing with Puller
C-293-PA and Adapters 8879 (Fig. 46).
(15) Remove pinion depth shim from the pinion
gear shaft and record thickness of the shims.
(16) Remove front pinion bearing cup from the
housing with a punch and hammer and discard.
CAUTION: Do not reuse front pinion bearing/cup.
(17) Remove rear pinion bearing cup from the
housing with a punch and hammer, if bearing is
replaced.
INSTALLATION
(1) Install front pinion bearing cup (Fig. 47) with
Installer D-146 and Handle C-4171.
Fig. 44 PINION FLANGE PULLER
1 - PINION FLANGE
2 - PULLER
Fig. 45 PINION DRIVER
1 - PINION SHAFT
2 - PINION DRIVER
Fig. 46 REAR PINION BEARING
1 - PULLER
2 - VISE
3 - PINION SHAFT
4 - ADAPTER BLOCKS
Fig. 47 FRONT PINION BEARING CUP
1 - INSTALLER
2 - HANDLE
3 - 66 FRONT AXLE - 9 1/4 AADR
PINION GEAR/RING GEAR (Continued)
Page 140 of 2895

(2) Install rear pinion bearing cup (Fig. 48) with
Installer 8886 and Handle C-4171, if bearing is
replaced.
(3) Install pinion depth shim (Fig. 49) on the pin-
ion gear shaft.(4) Install rear pinion bearing (Fig. 50) with
Installer C-3095-A and a press.
(5) Installnewcollapsible spacer (Fig. 51).
(6) Lubricate pinion and bearings.
Fig. 48 REAR PINION BEARING CUP
1 - INSTALLER
2 - HANDLE
Fig. 49 PINION DEPTH SHIM
1 - PINION DEPTH SHIM
2 - PINION GEAR
Fig. 50 REAR PINION BEARING
1 - PRESS
2 - INSTALLER
3 - PINION GEAR
4 - REAR PINION BEARING
Fig. 51 COLAPSIBLE SPACER
1 - COLAPSIBLE SPACER
2 - PINION GEAR
3 - REAR PINION BEARING
DRFRONT AXLE - 9 1/4 AA 3 - 67
PINION GEAR/RING GEAR (Continued)