DODGE RAM 2003 Service Repair Manual
Manufacturer: DODGE, Model Year: 2003, Model line: RAM, Model: DODGE RAM 2003Pages: 2895, PDF Size: 83.15 MB
Page 191 of 2895
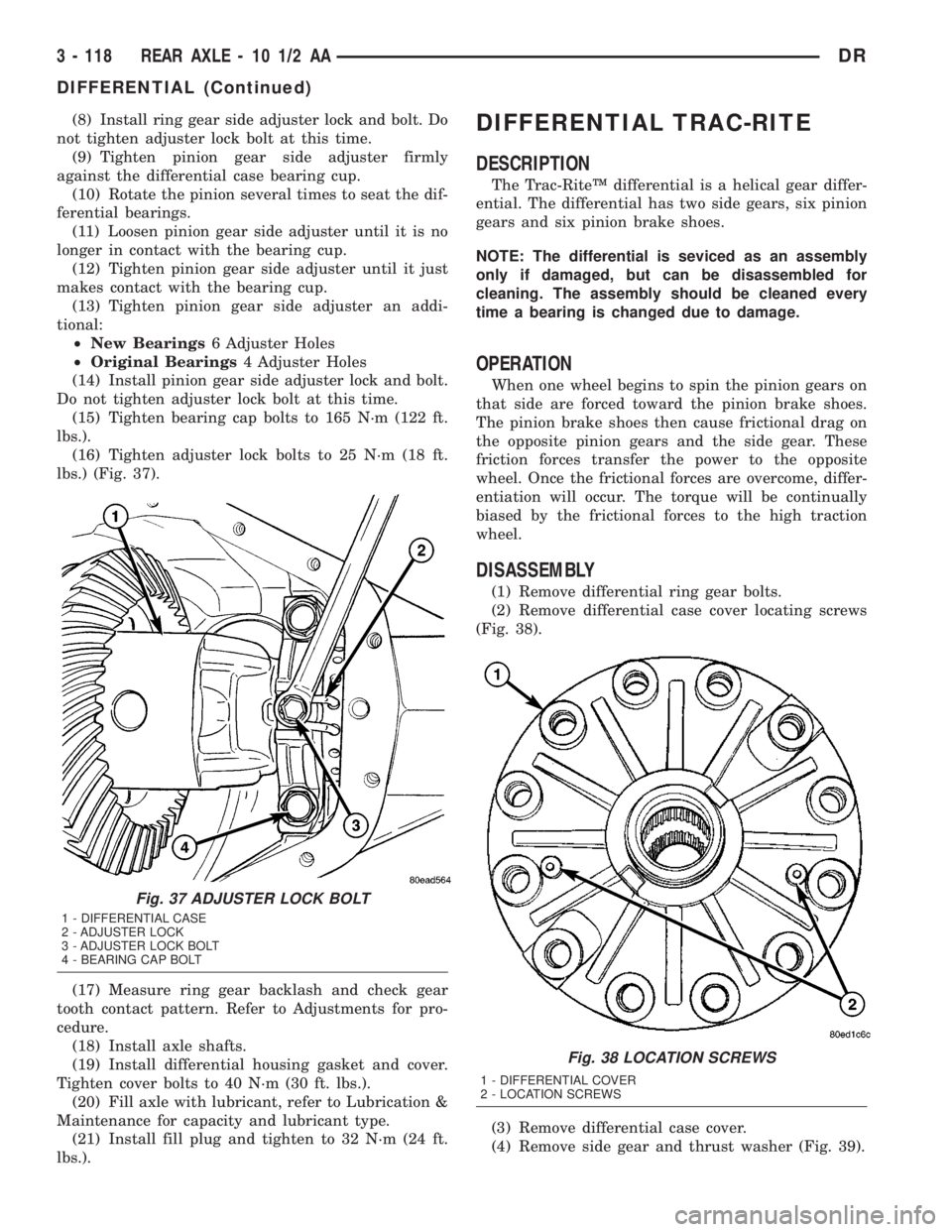
(8) Install ring gear side adjuster lock and bolt. Do
not tighten adjuster lock bolt at this time.
(9) Tighten pinion gear side adjuster firmly
against the differential case bearing cup.
(10) Rotate the pinion several times to seat the dif-
ferential bearings.
(11) Loosen pinion gear side adjuster until it is no
longer in contact with the bearing cup.
(12) Tighten pinion gear side adjuster until it just
makes contact with the bearing cup.
(13) Tighten pinion gear side adjuster an addi-
tional:
²New Bearings6 Adjuster Holes
²Original Bearings4 Adjuster Holes
(14) Install pinion gear side adjuster lock and bolt.
Do not tighten adjuster lock bolt at this time.
(15) Tighten bearing cap bolts to 165 N´m (122 ft.
lbs.).
(16) Tighten adjuster lock bolts to 25 N´m (18 ft.
lbs.) (Fig. 37).
(17) Measure ring gear backlash and check gear
tooth contact pattern. Refer to Adjustments for pro-
cedure.
(18) Install axle shafts.
(19) Install differential housing gasket and cover.
Tighten cover bolts to 40 N´m (30 ft. lbs.).
(20) Fill axle with lubricant, refer to Lubrication &
Maintenance for capacity and lubricant type.
(21) Install fill plug and tighten to 32 N´m (24 ft.
lbs.).DIFFERENTIAL TRAC-RITE
DESCRIPTION
The Trac-RiteŸ differential is a helical gear differ-
ential. The differential has two side gears, six pinion
gears and six pinion brake shoes.
NOTE: The differential is seviced as an assembly
only if damaged, but can be disassembled for
cleaning. The assembly should be cleaned every
time a bearing is changed due to damage.
OPERATION
When one wheel begins to spin the pinion gears on
that side are forced toward the pinion brake shoes.
The pinion brake shoes then cause frictional drag on
the opposite pinion gears and the side gear. These
friction forces transfer the power to the opposite
wheel. Once the frictional forces are overcome, differ-
entiation will occur. The torque will be continually
biased by the frictional forces to the high traction
wheel.
DISASSEMBLY
(1) Remove differential ring gear bolts.
(2) Remove differential case cover locating screws
(Fig. 38).
(3) Remove differential case cover.
(4) Remove side gear and thrust washer (Fig. 39).
Fig. 37 ADJUSTER LOCK BOLT
1 - DIFFERENTIAL CASE
2 - ADJUSTER LOCK
3 - ADJUSTER LOCK BOLT
4 - BEARING CAP BOLT
Fig. 38 LOCATION SCREWS
1 - DIFFERENTIAL COVER
2 - LOCATION SCREWS
3 - 118 REAR AXLE - 10 1/2 AADR
DIFFERENTIAL (Continued)
Page 192 of 2895
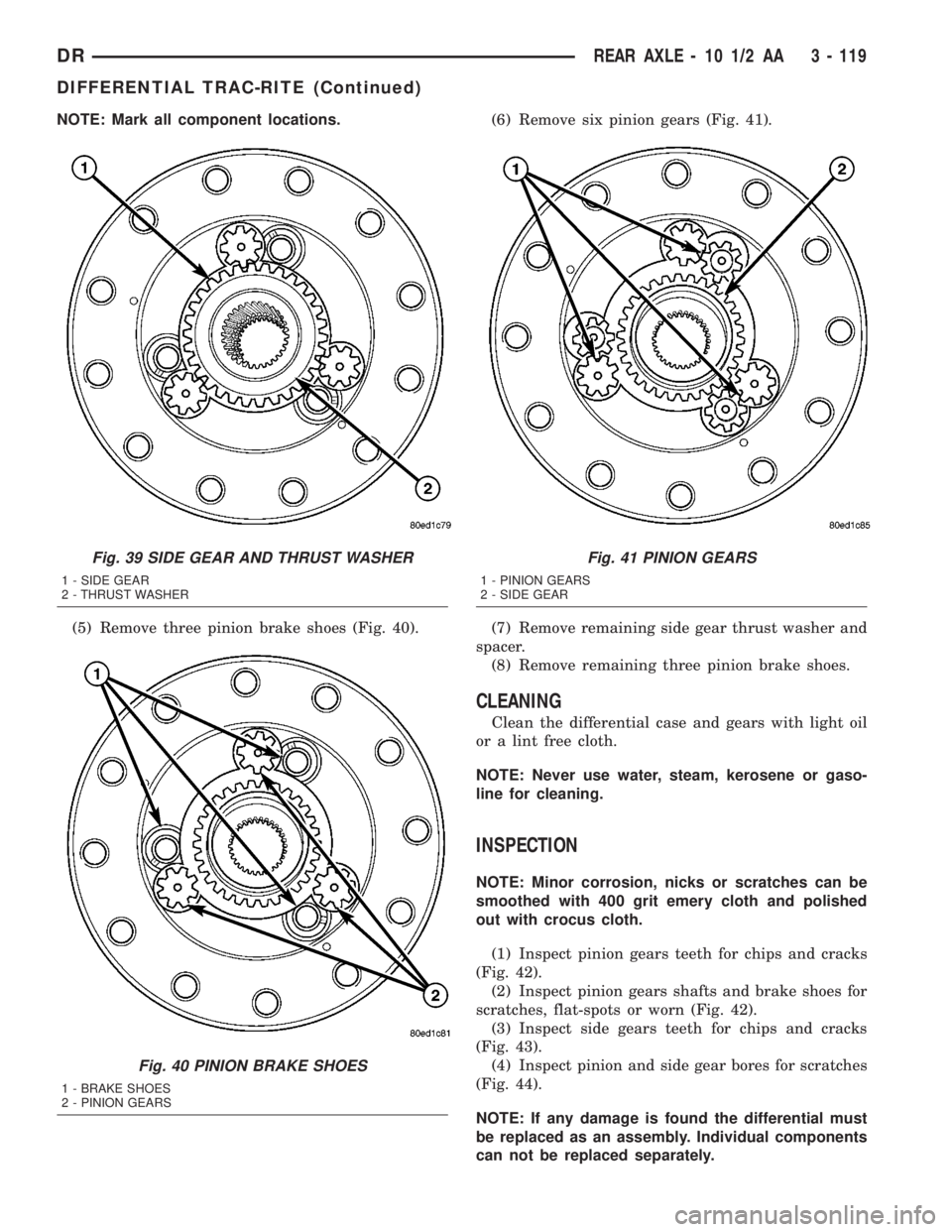
NOTE: Mark all component locations.
(5) Remove three pinion brake shoes (Fig. 40).(6) Remove six pinion gears (Fig. 41).
(7) Remove remaining side gear thrust washer and
spacer.
(8) Remove remaining three pinion brake shoes.
CLEANING
Clean the differential case and gears with light oil
or a lint free cloth.
NOTE: Never use water, steam, kerosene or gaso-
line for cleaning.
INSPECTION
NOTE: Minor corrosion, nicks or scratches can be
smoothed with 400 grit emery cloth and polished
out with crocus cloth.
(1) Inspect pinion gears teeth for chips and cracks
(Fig. 42).
(2) Inspect pinion gears shafts and brake shoes for
scratches, flat-spots or worn (Fig. 42).
(3) Inspect side gears teeth for chips and cracks
(Fig. 43).
(4) Inspect pinion and side gear bores for scratches
(Fig. 44).
NOTE: If any damage is found the differential must
be replaced as an assembly. Individual components
can not be replaced separately.
Fig. 39 SIDE GEAR AND THRUST WASHER
1 - SIDE GEAR
2 - THRUST WASHER
Fig. 40 PINION BRAKE SHOES
1 - BRAKE SHOES
2 - PINION GEARS
Fig. 41 PINION GEARS
1 - PINION GEARS
2 - SIDE GEAR
DRREAR AXLE - 10 1/2 AA 3 - 119
DIFFERENTIAL TRAC-RITE (Continued)
Page 193 of 2895
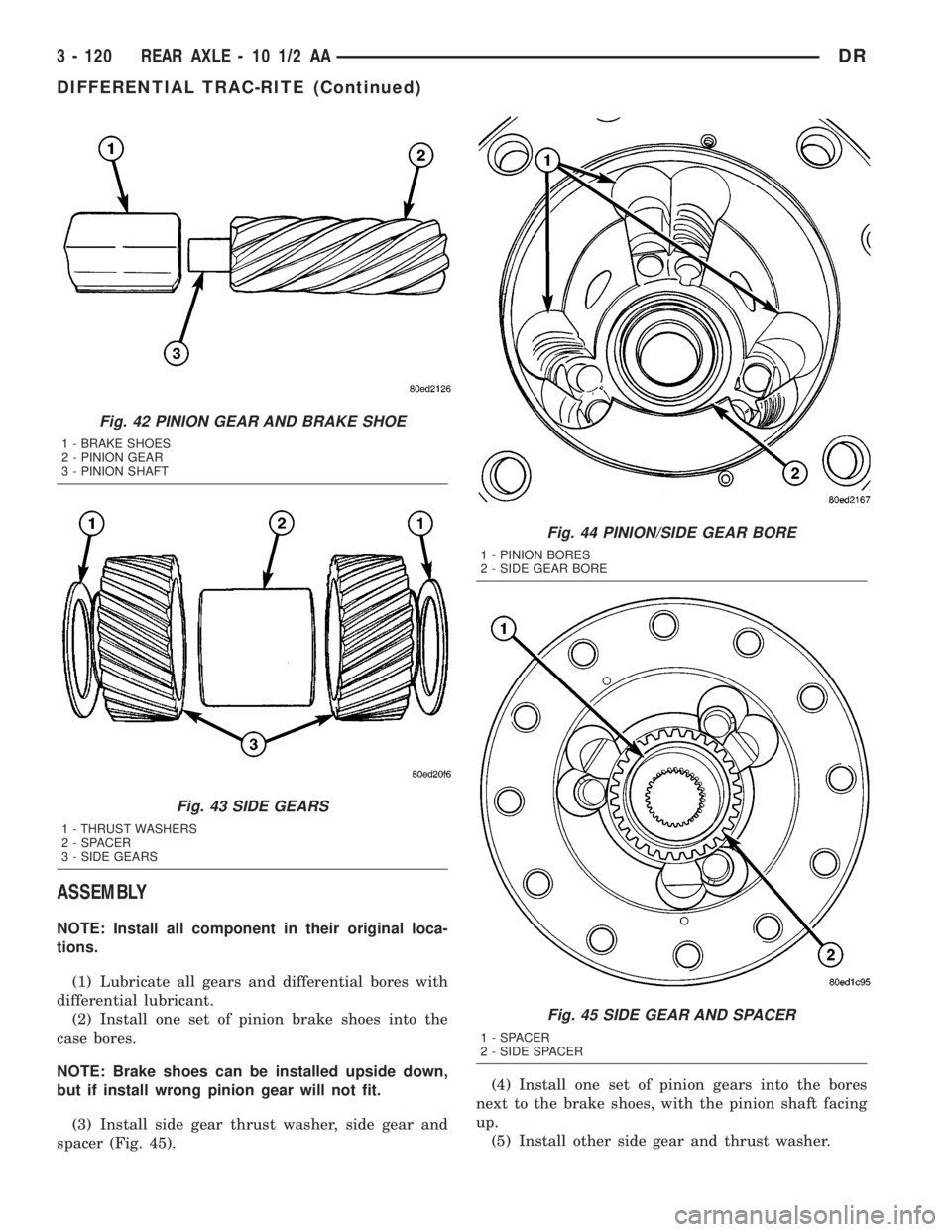
ASSEMBLY
NOTE: Install all component in their original loca-
tions.
(1) Lubricate all gears and differential bores with
differential lubricant.
(2) Install one set of pinion brake shoes into the
case bores.
NOTE: Brake shoes can be installed upside down,
but if install wrong pinion gear will not fit.
(3) Install side gear thrust washer, side gear and
spacer (Fig. 45).(4) Install one set of pinion gears into the bores
next to the brake shoes, with the pinion shaft facing
up.
(5) Install other side gear and thrust washer.
Fig. 42 PINION GEAR AND BRAKE SHOE
1 - BRAKE SHOES
2 - PINION GEAR
3 - PINION SHAFT
Fig. 43 SIDE GEARS
1 - THRUST WASHERS
2 - SPACER
3 - SIDE GEARS
Fig. 44 PINION/SIDE GEAR BORE
1 - PINION BORES
2 - SIDE GEAR BORE
Fig. 45 SIDE GEAR AND SPACER
1 - SPACER
2 - SIDE SPACER
3 - 120 REAR AXLE - 10 1/2 AADR
DIFFERENTIAL TRAC-RITE (Continued)
Page 194 of 2895
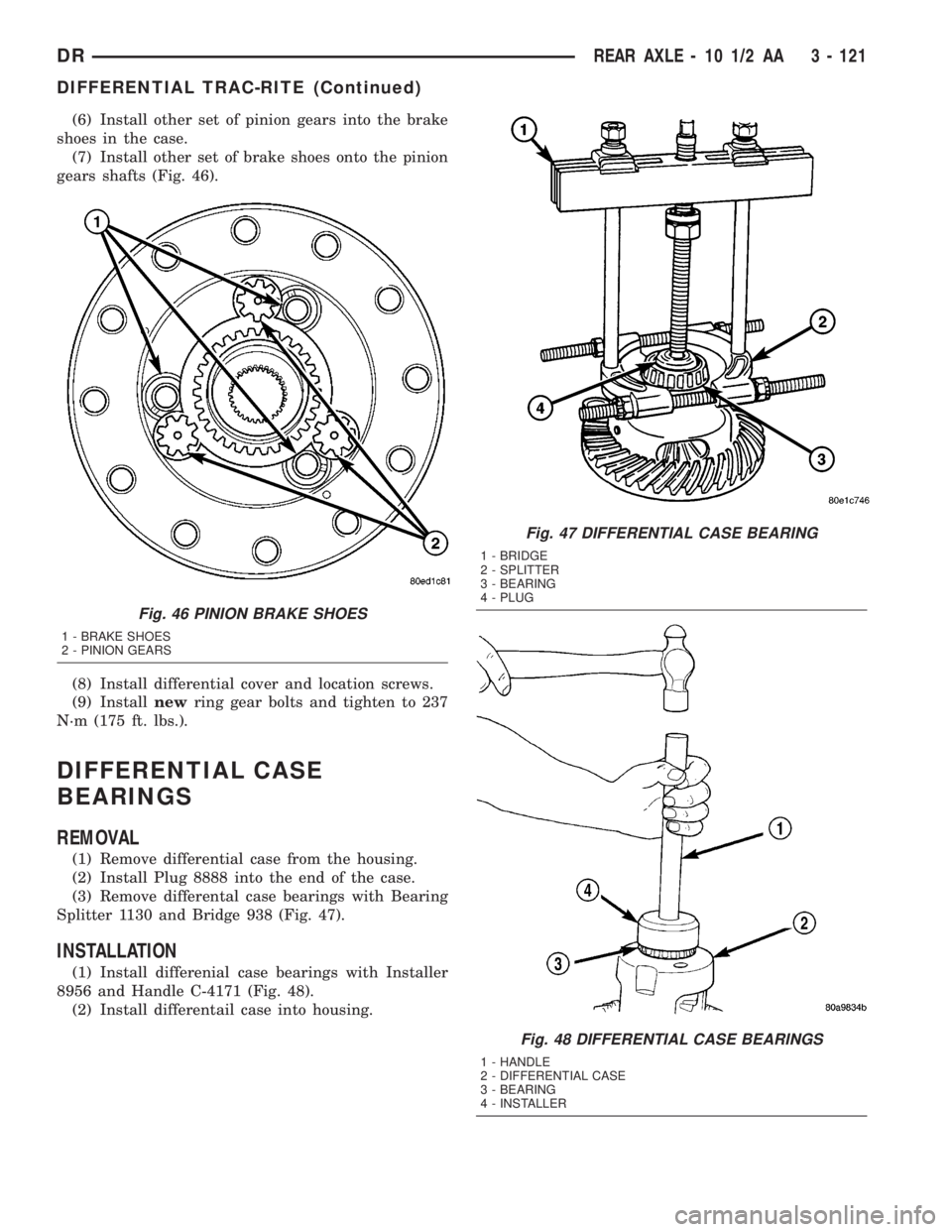
(6) Install other set of pinion gears into the brake
shoes in the case.
(7) Install other set of brake shoes onto the pinion
gears shafts (Fig. 46).
(8) Install differential cover and location screws.
(9) Installnewring gear bolts and tighten to 237
N´m (175 ft. lbs.).
DIFFERENTIAL CASE
BEARINGS
REMOVAL
(1) Remove differential case from the housing.
(2) Install Plug 8888 into the end of the case.
(3) Remove differental case bearings with Bearing
Splitter 1130 and Bridge 938 (Fig. 47).
INSTALLATION
(1) Install differenial case bearings with Installer
8956 and Handle C-4171 (Fig. 48).
(2) Install differentail case into housing.
Fig. 46 PINION BRAKE SHOES
1 - BRAKE SHOES
2 - PINION GEARS
Fig. 47 DIFFERENTIAL CASE BEARING
1 - BRIDGE
2 - SPLITTER
3 - BEARING
4 - PLUG
Fig. 48 DIFFERENTIAL CASE BEARINGS
1 - HANDLE
2 - DIFFERENTIAL CASE
3 - BEARING
4 - INSTALLER
DRREAR AXLE - 10 1/2 AA 3 - 121
DIFFERENTIAL TRAC-RITE (Continued)
Page 195 of 2895
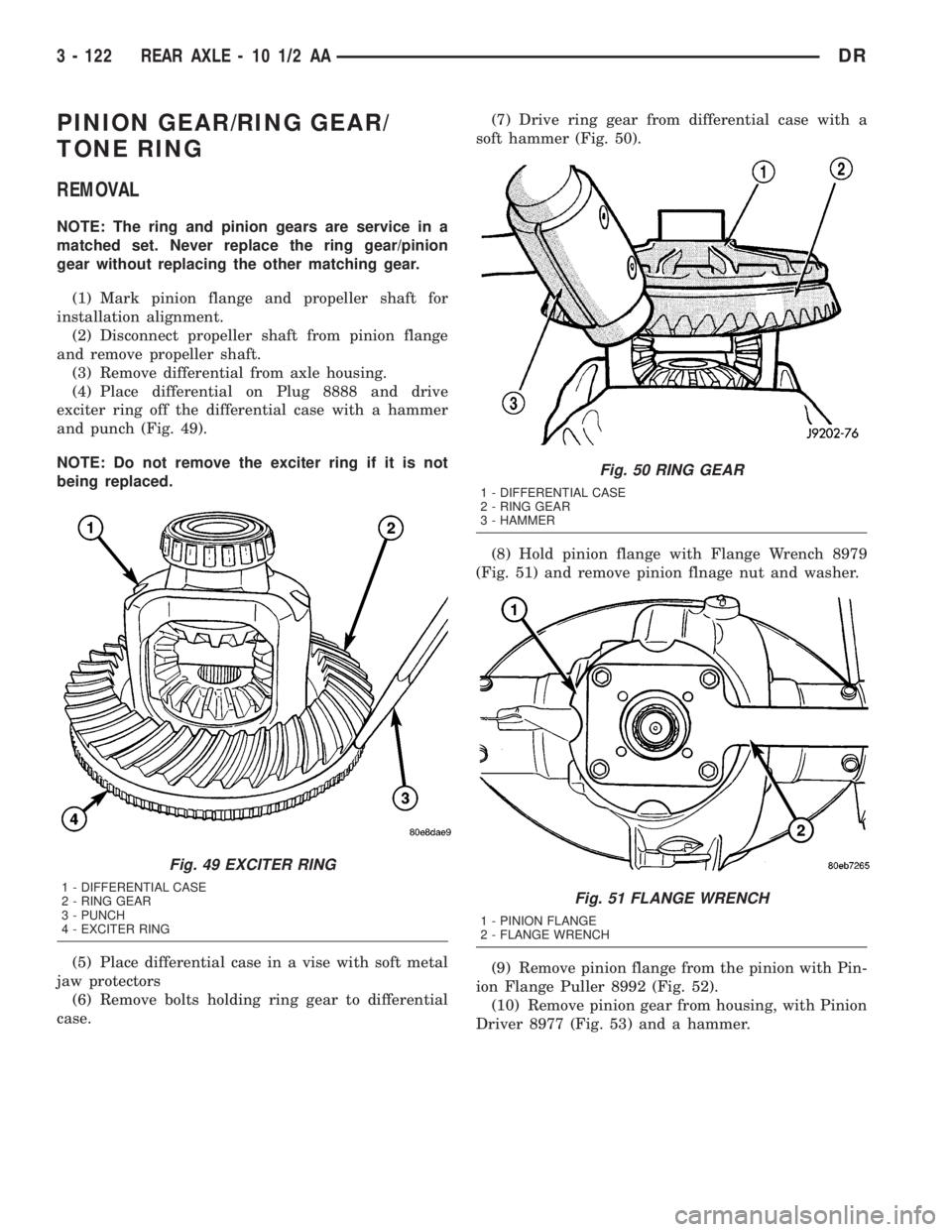
PINION GEAR/RING GEAR/
TONE RING
REMOVAL
NOTE: The ring and pinion gears are service in a
matched set. Never replace the ring gear/pinion
gear without replacing the other matching gear.
(1) Mark pinion flange and propeller shaft for
installation alignment.
(2) Disconnect propeller shaft from pinion flange
and remove propeller shaft.
(3) Remove differential from axle housing.
(4) Place differential on Plug 8888 and drive
exciter ring off the differential case with a hammer
and punch (Fig. 49).
NOTE: Do not remove the exciter ring if it is not
being replaced.
(5) Place differential case in a vise with soft metal
jaw protectors
(6) Remove bolts holding ring gear to differential
case.(7) Drive ring gear from differential case with a
soft hammer (Fig. 50).
(8) Hold pinion flange with Flange Wrench 8979
(Fig. 51) and remove pinion flnage nut and washer.
(9) Remove pinion flange from the pinion with Pin-
ion Flange Puller 8992 (Fig. 52).
(10) Remove pinion gear from housing, with Pinion
Driver 8977 (Fig. 53) and a hammer.
Fig. 49 EXCITER RING
1 - DIFFERENTIAL CASE
2 - RING GEAR
3 - PUNCH
4 - EXCITER RING
Fig. 50 RING GEAR
1 - DIFFERENTIAL CASE
2 - RING GEAR
3 - HAMMER
Fig. 51 FLANGE WRENCH
1 - PINION FLANGE
2 - FLANGE WRENCH
3 - 122 REAR AXLE - 10 1/2 AADR
Page 196 of 2895
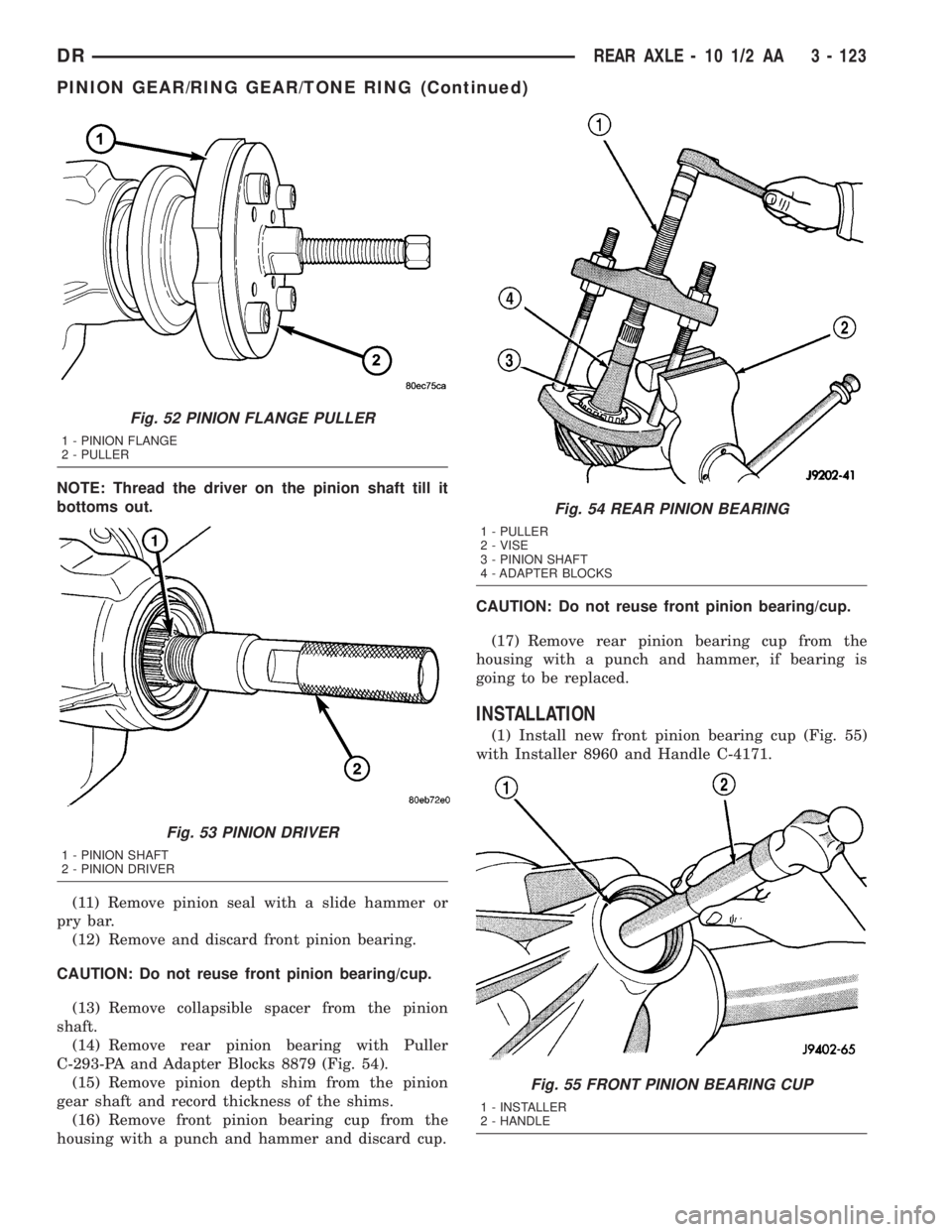
NOTE: Thread the driver on the pinion shaft till it
bottoms out.
(11) Remove pinion seal with a slide hammer or
pry bar.
(12) Remove and discard front pinion bearing.
CAUTION: Do not reuse front pinion bearing/cup.
(13) Remove collapsible spacer from the pinion
shaft.
(14) Remove rear pinion bearing with Puller
C-293-PA and Adapter Blocks 8879 (Fig. 54).
(15) Remove pinion depth shim from the pinion
gear shaft and record thickness of the shims.
(16) Remove front pinion bearing cup from the
housing with a punch and hammer and discard cup.CAUTION: Do not reuse front pinion bearing/cup.
(17) Remove rear pinion bearing cup from the
housing with a punch and hammer, if bearing is
going to be replaced.
INSTALLATION
(1) Install new front pinion bearing cup (Fig. 55)
with Installer 8960 and Handle C-4171.
Fig. 52 PINION FLANGE PULLER
1 - PINION FLANGE
2 - PULLER
Fig. 53 PINION DRIVER
1 - PINION SHAFT
2 - PINION DRIVER
Fig. 54 REAR PINION BEARING
1 - PULLER
2 - VISE
3 - PINION SHAFT
4 - ADAPTER BLOCKS
Fig. 55 FRONT PINION BEARING CUP
1 - INSTALLER
2 - HANDLE
DRREAR AXLE - 10 1/2 AA 3 - 123
PINION GEAR/RING GEAR/TONE RING (Continued)
Page 197 of 2895
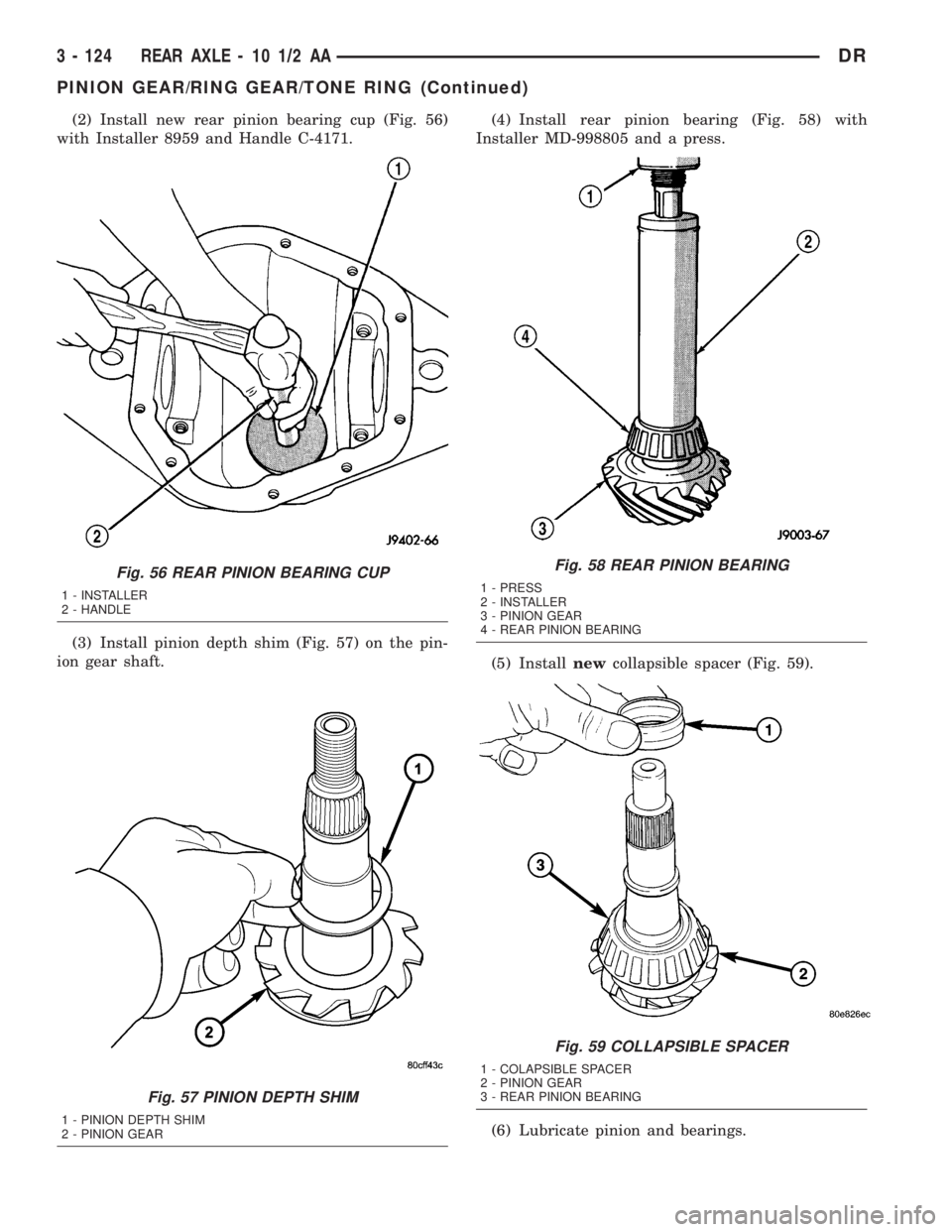
(2) Install new rear pinion bearing cup (Fig. 56)
with Installer 8959 and Handle C-4171.
(3) Install pinion depth shim (Fig. 57) on the pin-
ion gear shaft.(4) Install rear pinion bearing (Fig. 58) with
Installer MD-998805 and a press.
(5) Installnewcollapsible spacer (Fig. 59).
(6) Lubricate pinion and bearings.
Fig. 56 REAR PINION BEARING CUP
1 - INSTALLER
2 - HANDLE
Fig. 57 PINION DEPTH SHIM
1 - PINION DEPTH SHIM
2 - PINION GEAR
Fig. 58 REAR PINION BEARING
1 - PRESS
2 - INSTALLER
3 - PINION GEAR
4 - REAR PINION BEARING
Fig. 59 COLLAPSIBLE SPACER
1 - COLAPSIBLE SPACER
2 - PINION GEAR
3 - REAR PINION BEARING
3 - 124 REAR AXLE - 10 1/2 AADR
PINION GEAR/RING GEAR/TONE RING (Continued)
Page 198 of 2895
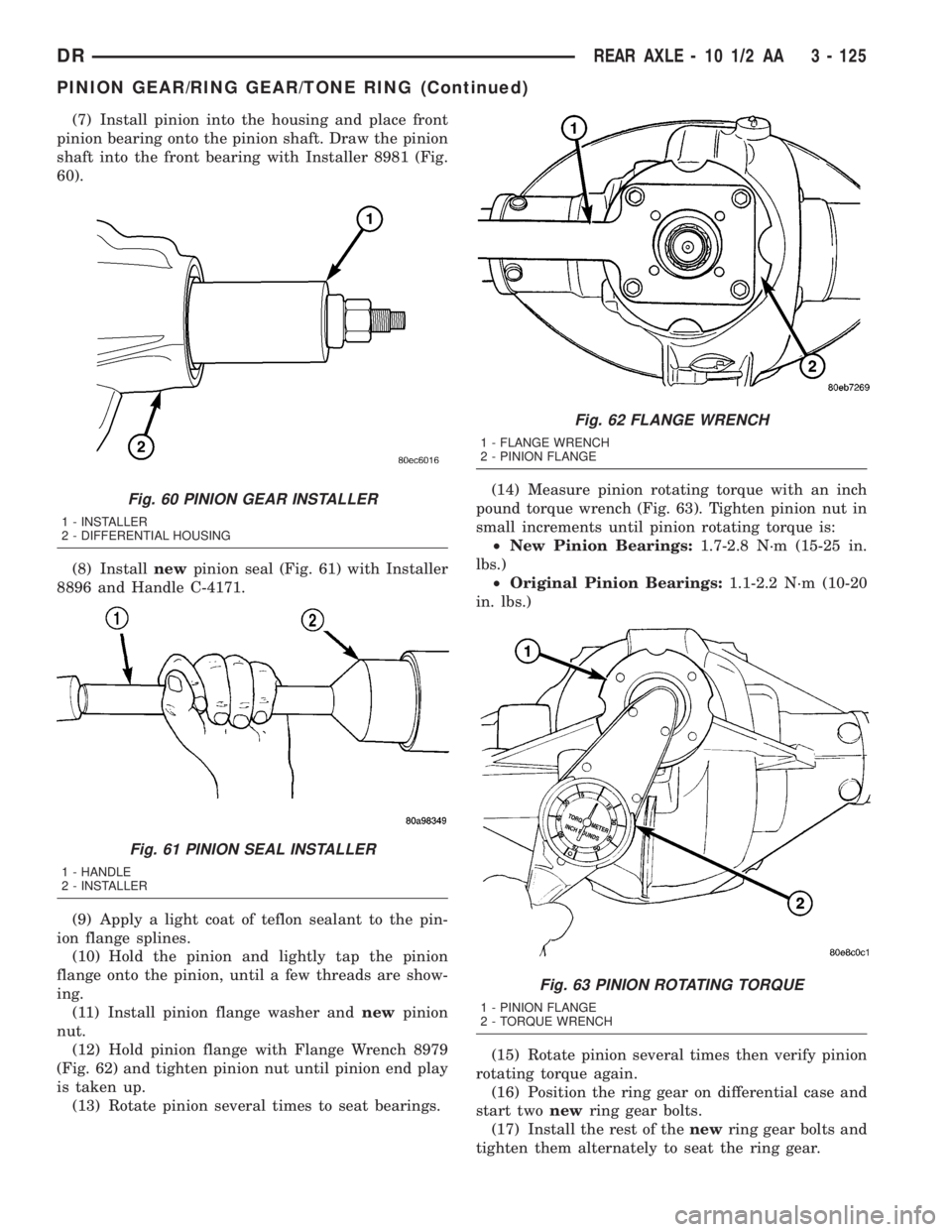
(7) Install pinion into the housing and place front
pinion bearing onto the pinion shaft. Draw the pinion
shaft into the front bearing with Installer 8981 (Fig.
60).
(8) Installnewpinion seal (Fig. 61) with Installer
8896 and Handle C-4171.
(9) Apply a light coat of teflon sealant to the pin-
ion flange splines.
(10) Hold the pinion and lightly tap the pinion
flange onto the pinion, until a few threads are show-
ing.
(11) Install pinion flange washer andnewpinion
nut.
(12) Hold pinion flange with Flange Wrench 8979
(Fig. 62) and tighten pinion nut until pinion end play
is taken up.
(13) Rotate pinion several times to seat bearings.(14) Measure pinion rotating torque with an inch
pound torque wrench (Fig. 63). Tighten pinion nut in
small increments until pinion rotating torque is:
²New Pinion Bearings:1.7-2.8 N´m (15-25 in.
lbs.)
²Original Pinion Bearings:1.1-2.2 N´m (10-20
in. lbs.)
(15) Rotate pinion several times then verify pinion
rotating torque again.
(16) Position the ring gear on differential case and
start twonewring gear bolts.
(17) Install the rest of thenewring gear bolts and
tighten them alternately to seat the ring gear.
Fig. 60 PINION GEAR INSTALLER
1 - INSTALLER
2 - DIFFERENTIAL HOUSING
Fig. 61 PINION SEAL INSTALLER
1 - HANDLE
2 - INSTALLER
Fig. 62 FLANGE WRENCH
1 - FLANGE WRENCH
2 - PINION FLANGE
Fig. 63 PINION ROTATING TORQUE
1 - PINION FLANGE
2 - TORQUE WRENCH
DRREAR AXLE - 10 1/2 AA 3 - 125
PINION GEAR/RING GEAR/TONE RING (Continued)
Page 199 of 2895
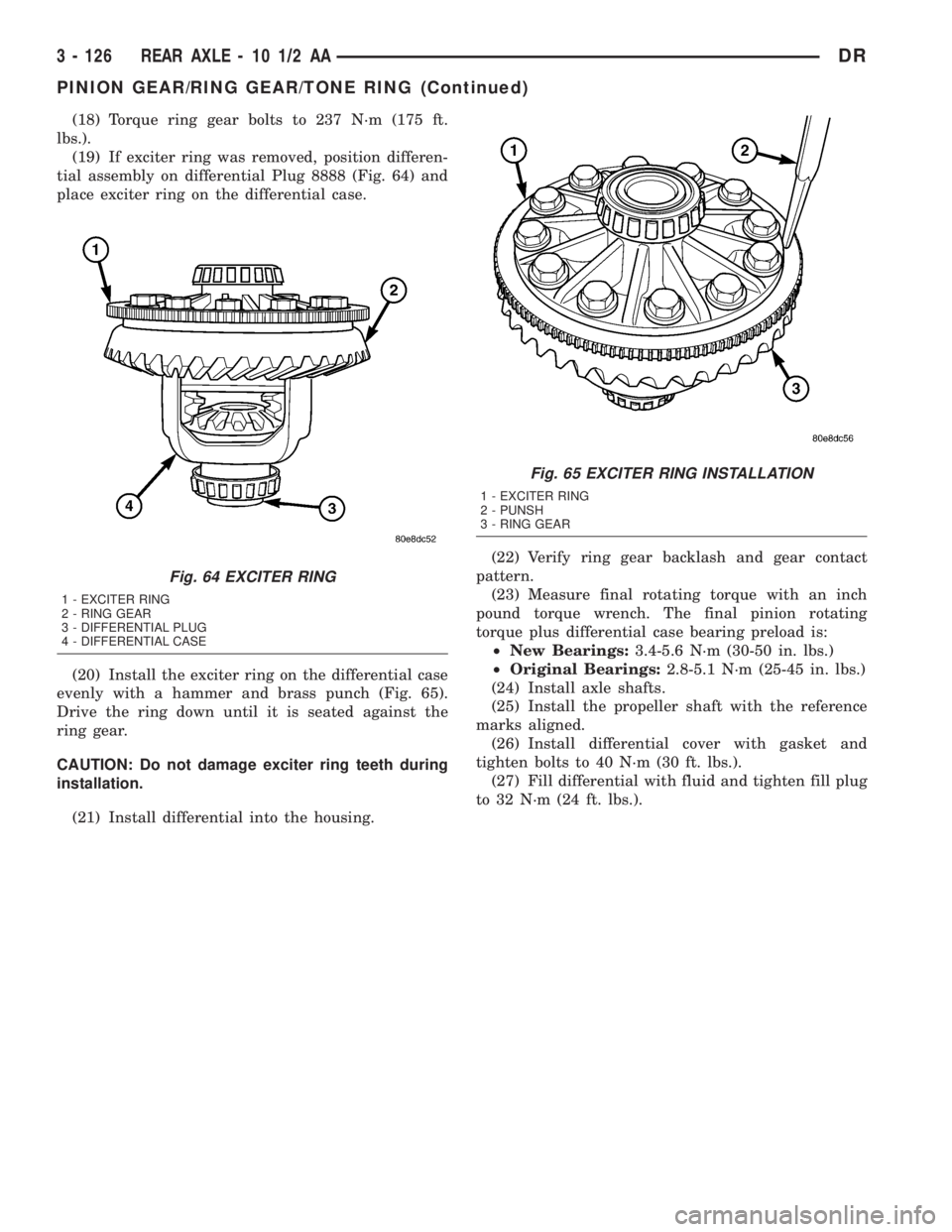
(18) Torque ring gear bolts to 237 N´m (175 ft.
lbs.).
(19) If exciter ring was removed, position differen-
tial assembly on differential Plug 8888 (Fig. 64) and
place exciter ring on the differential case.
(20) Install the exciter ring on the differential case
evenly with a hammer and brass punch (Fig. 65).
Drive the ring down until it is seated against the
ring gear.
CAUTION: Do not damage exciter ring teeth during
installation.
(21) Install differential into the housing.(22) Verify ring gear backlash and gear contact
pattern.
(23) Measure final rotating torque with an inch
pound torque wrench. The final pinion rotating
torque plus differential case bearing preload is:
²New Bearings:3.4-5.6 N´m (30-50 in. lbs.)
²Original Bearings:2.8-5.1 N´m (25-45 in. lbs.)
(24) Install axle shafts.
(25) Install the propeller shaft with the reference
marks aligned.
(26) Install differential cover with gasket and
tighten bolts to 40 N´m (30 ft. lbs.).
(27) Fill differential with fluid and tighten fill plug
to 32 N´m (24 ft. lbs.).
Fig. 64 EXCITER RING
1 - EXCITER RING
2 - RING GEAR
3 - DIFFERENTIAL PLUG
4 - DIFFERENTIAL CASE
Fig. 65 EXCITER RING INSTALLATION
1 - EXCITER RING
2 - PUNSH
3 - RING GEAR
3 - 126 REAR AXLE - 10 1/2 AADR
PINION GEAR/RING GEAR/TONE RING (Continued)
Page 200 of 2895
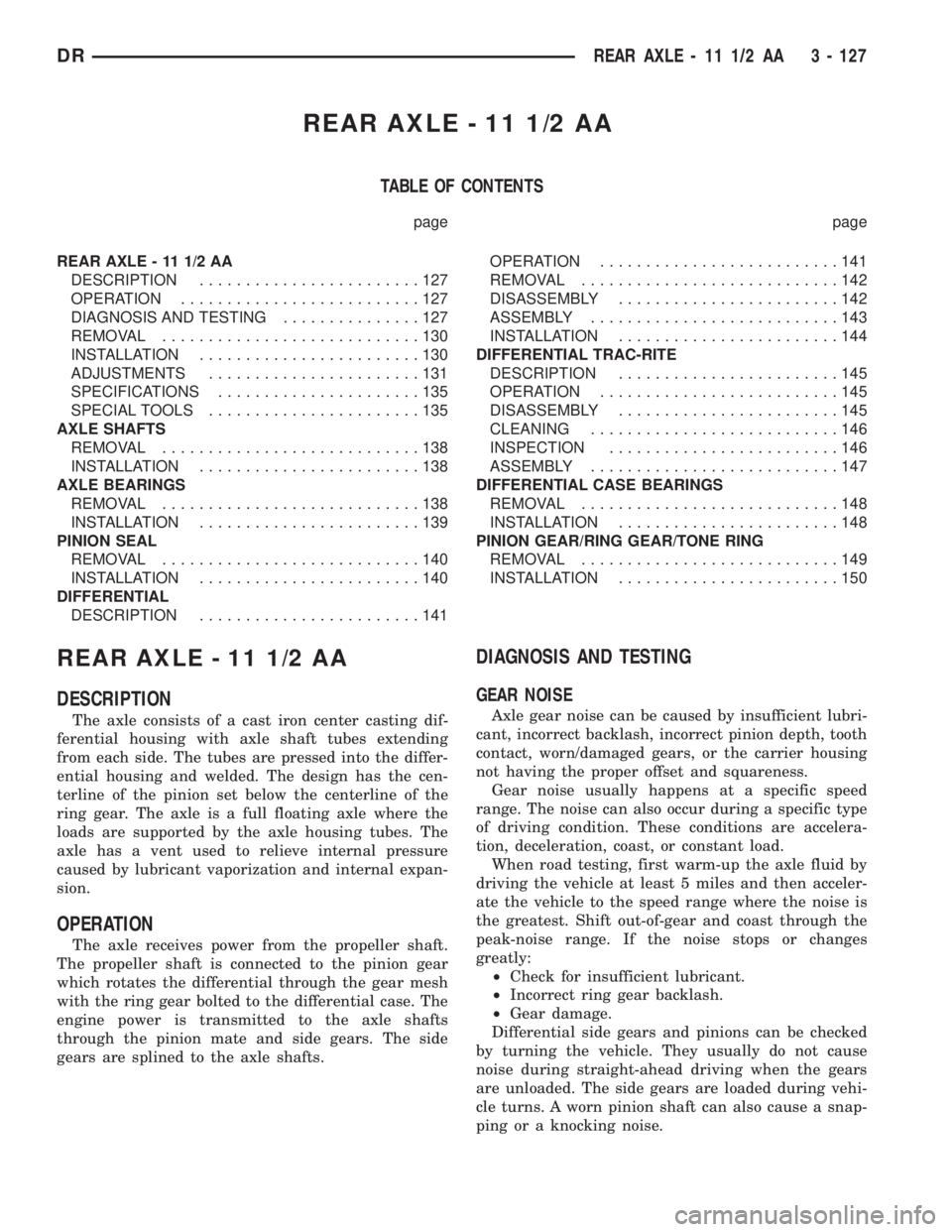
REAR AXLE - 11 1/2 AA
TABLE OF CONTENTS
page page
REAR AXLE - 11 1/2 AA
DESCRIPTION........................127
OPERATION..........................127
DIAGNOSIS AND TESTING...............127
REMOVAL............................130
INSTALLATION........................130
ADJUSTMENTS.......................131
SPECIFICATIONS......................135
SPECIAL TOOLS.......................135
AXLE SHAFTS
REMOVAL............................138
INSTALLATION........................138
AXLE BEARINGS
REMOVAL............................138
INSTALLATION........................139
PINION SEAL
REMOVAL............................140
INSTALLATION........................140
DIFFERENTIAL
DESCRIPTION........................141OPERATION..........................141
REMOVAL............................142
DISASSEMBLY........................142
ASSEMBLY...........................143
INSTALLATION........................144
DIFFERENTIAL TRAC-RITE
DESCRIPTION........................145
OPERATION..........................145
DISASSEMBLY........................145
CLEANING...........................146
INSPECTION.........................146
ASSEMBLY...........................147
DIFFERENTIAL CASE BEARINGS
REMOVAL............................148
INSTALLATION........................148
PINION GEAR/RING GEAR/TONE RING
REMOVAL............................149
INSTALLATION........................150
REAR AXLE - 11 1/2 AA
DESCRIPTION
The axle consists of a cast iron center casting dif-
ferential housing with axle shaft tubes extending
from each side. The tubes are pressed into the differ-
ential housing and welded. The design has the cen-
terline of the pinion set below the centerline of the
ring gear. The axle is a full floating axle where the
loads are supported by the axle housing tubes. The
axle has a vent used to relieve internal pressure
caused by lubricant vaporization and internal expan-
sion.
OPERATION
The axle receives power from the propeller shaft.
The propeller shaft is connected to the pinion gear
which rotates the differential through the gear mesh
with the ring gear bolted to the differential case. The
engine power is transmitted to the axle shafts
through the pinion mate and side gears. The side
gears are splined to the axle shafts.
DIAGNOSIS AND TESTING
GEAR NOISE
Axle gear noise can be caused by insufficient lubri-
cant, incorrect backlash, incorrect pinion depth, tooth
contact, worn/damaged gears, or the carrier housing
not having the proper offset and squareness.
Gear noise usually happens at a specific speed
range. The noise can also occur during a specific type
of driving condition. These conditions are accelera-
tion, deceleration, coast, or constant load.
When road testing, first warm-up the axle fluid by
driving the vehicle at least 5 miles and then acceler-
ate the vehicle to the speed range where the noise is
the greatest. Shift out-of-gear and coast through the
peak-noise range. If the noise stops or changes
greatly:
²Check for insufficient lubricant.
²Incorrect ring gear backlash.
²Gear damage.
Differential side gears and pinions can be checked
by turning the vehicle. They usually do not cause
noise during straight-ahead driving when the gears
are unloaded. The side gears are loaded during vehi-
cle turns. A worn pinion shaft can also cause a snap-
ping or a knocking noise.
DRREAR AXLE - 11 1/2 AA 3 - 127