DODGE RAM 2003 Service Repair Manual
Manufacturer: DODGE, Model Year: 2003, Model line: RAM, Model: DODGE RAM 2003Pages: 2895, PDF Size: 83.15 MB
Page 221 of 2895
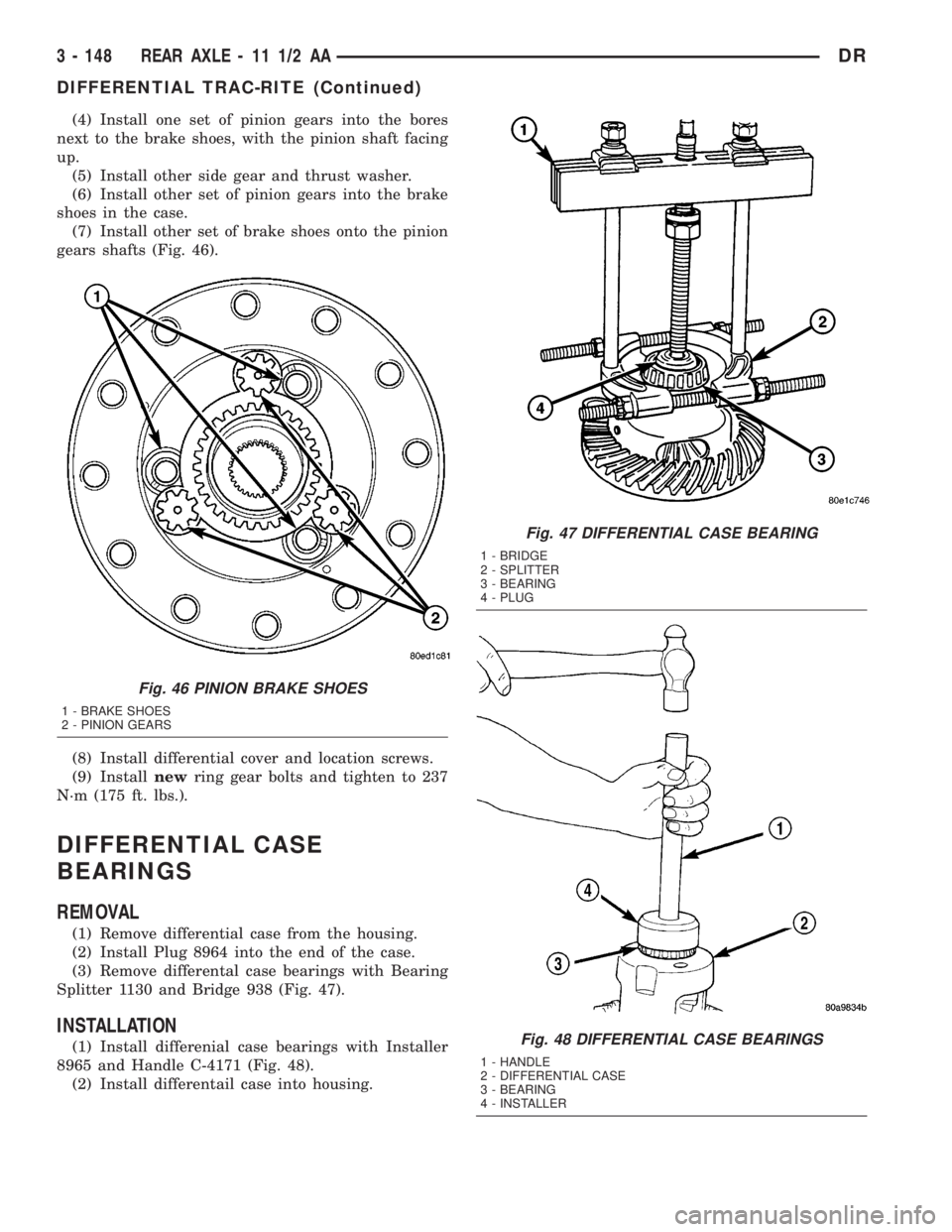
(4) Install one set of pinion gears into the bores
next to the brake shoes, with the pinion shaft facing
up.
(5) Install other side gear and thrust washer.
(6) Install other set of pinion gears into the brake
shoes in the case.
(7) Install other set of brake shoes onto the pinion
gears shafts (Fig. 46).
(8) Install differential cover and location screws.
(9) Installnewring gear bolts and tighten to 237
N´m (175 ft. lbs.).
DIFFERENTIAL CASE
BEARINGS
REMOVAL
(1) Remove differential case from the housing.
(2) Install Plug 8964 into the end of the case.
(3) Remove differental case bearings with Bearing
Splitter 1130 and Bridge 938 (Fig. 47).
INSTALLATION
(1) Install differenial case bearings with Installer
8965 and Handle C-4171 (Fig. 48).
(2) Install differentail case into housing.
Fig. 46 PINION BRAKE SHOES
1 - BRAKE SHOES
2 - PINION GEARS
Fig. 47 DIFFERENTIAL CASE BEARING
1 - BRIDGE
2 - SPLITTER
3 - BEARING
4 - PLUG
Fig. 48 DIFFERENTIAL CASE BEARINGS
1 - HANDLE
2 - DIFFERENTIAL CASE
3 - BEARING
4 - INSTALLER
3 - 148 REAR AXLE - 11 1/2 AADR
DIFFERENTIAL TRAC-RITE (Continued)
Page 222 of 2895
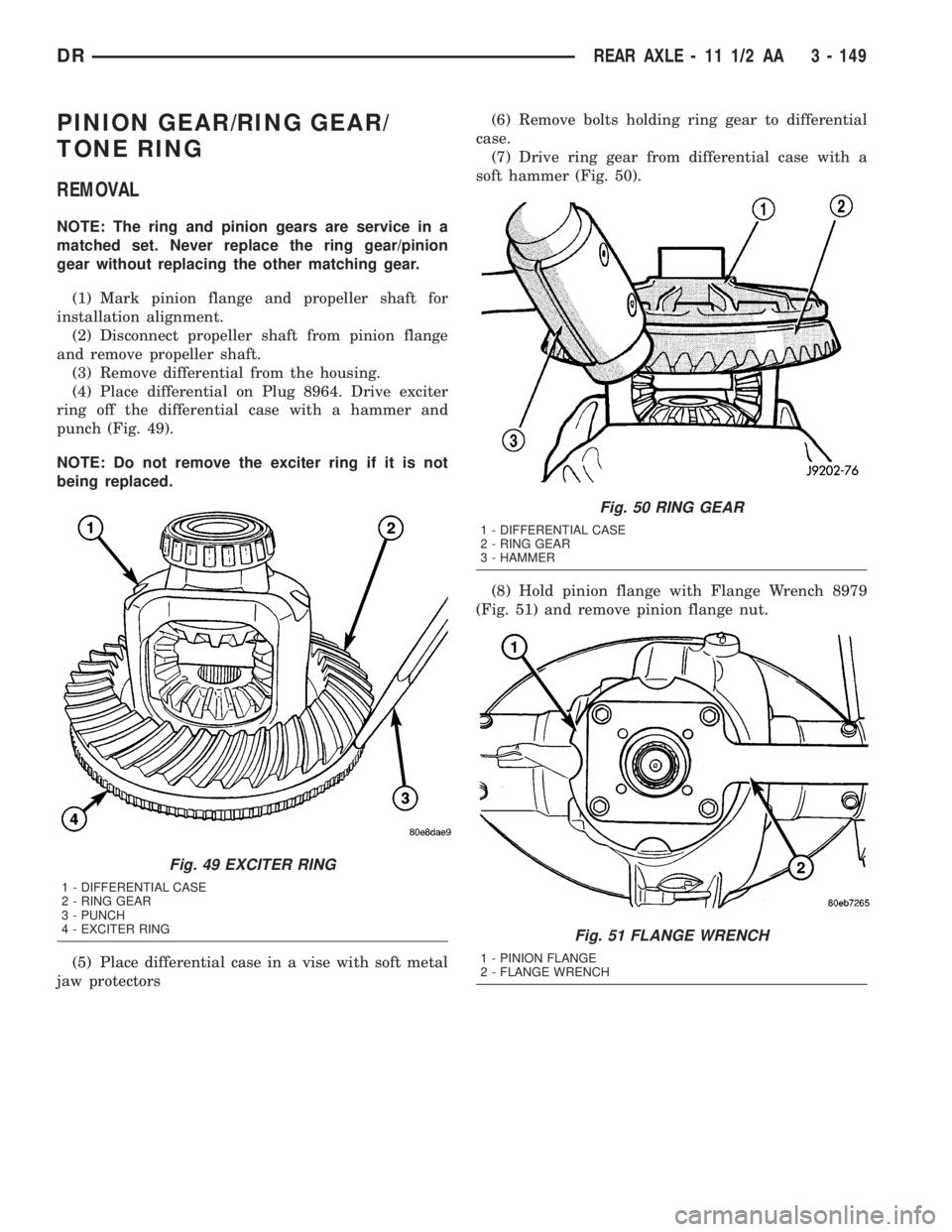
PINION GEAR/RING GEAR/
TONE RING
REMOVAL
NOTE: The ring and pinion gears are service in a
matched set. Never replace the ring gear/pinion
gear without replacing the other matching gear.
(1) Mark pinion flange and propeller shaft for
installation alignment.
(2) Disconnect propeller shaft from pinion flange
and remove propeller shaft.
(3) Remove differential from the housing.
(4) Place differential on Plug 8964. Drive exciter
ring off the differential case with a hammer and
punch (Fig. 49).
NOTE: Do not remove the exciter ring if it is not
being replaced.
(5) Place differential case in a vise with soft metal
jaw protectors(6) Remove bolts holding ring gear to differential
case.
(7) Drive ring gear from differential case with a
soft hammer (Fig. 50).
(8) Hold pinion flange with Flange Wrench 8979
(Fig. 51) and remove pinion flange nut.
Fig. 49 EXCITER RING
1 - DIFFERENTIAL CASE
2 - RING GEAR
3 - PUNCH
4 - EXCITER RING
Fig. 50 RING GEAR
1 - DIFFERENTIAL CASE
2 - RING GEAR
3 - HAMMER
Fig. 51 FLANGE WRENCH
1 - PINION FLANGE
2 - FLANGE WRENCH
DRREAR AXLE - 11 1/2 AA 3 - 149
Page 223 of 2895
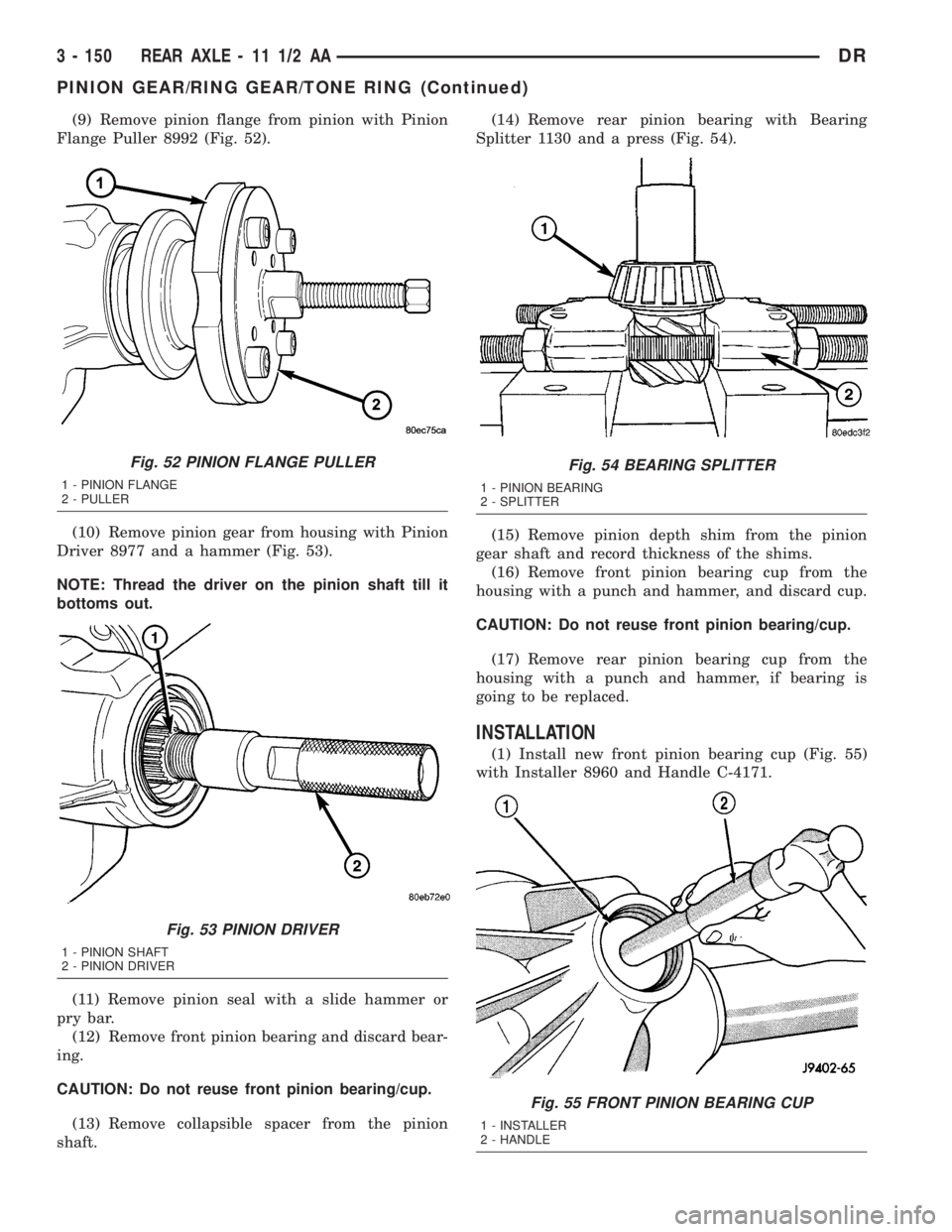
(9) Remove pinion flange from pinion with Pinion
Flange Puller 8992 (Fig. 52).
(10) Remove pinion gear from housing with Pinion
Driver 8977 and a hammer (Fig. 53).
NOTE: Thread the driver on the pinion shaft till it
bottoms out.
(11) Remove pinion seal with a slide hammer or
pry bar.
(12) Remove front pinion bearing and discard bear-
ing.
CAUTION: Do not reuse front pinion bearing/cup.
(13) Remove collapsible spacer from the pinion
shaft.(14) Remove rear pinion bearing with Bearing
Splitter 1130 and a press (Fig. 54).
(15) Remove pinion depth shim from the pinion
gear shaft and record thickness of the shims.
(16) Remove front pinion bearing cup from the
housing with a punch and hammer, and discard cup.
CAUTION: Do not reuse front pinion bearing/cup.
(17) Remove rear pinion bearing cup from the
housing with a punch and hammer, if bearing is
going to be replaced.
INSTALLATION
(1) Install new front pinion bearing cup (Fig. 55)
with Installer 8960 and Handle C-4171.
Fig. 52 PINION FLANGE PULLER
1 - PINION FLANGE
2 - PULLER
Fig. 53 PINION DRIVER
1 - PINION SHAFT
2 - PINION DRIVER
Fig. 54 BEARING SPLITTER
1 - PINION BEARING
2 - SPLITTER
Fig. 55 FRONT PINION BEARING CUP
1 - INSTALLER
2 - HANDLE
3 - 150 REAR AXLE - 11 1/2 AADR
PINION GEAR/RING GEAR/TONE RING (Continued)
Page 224 of 2895
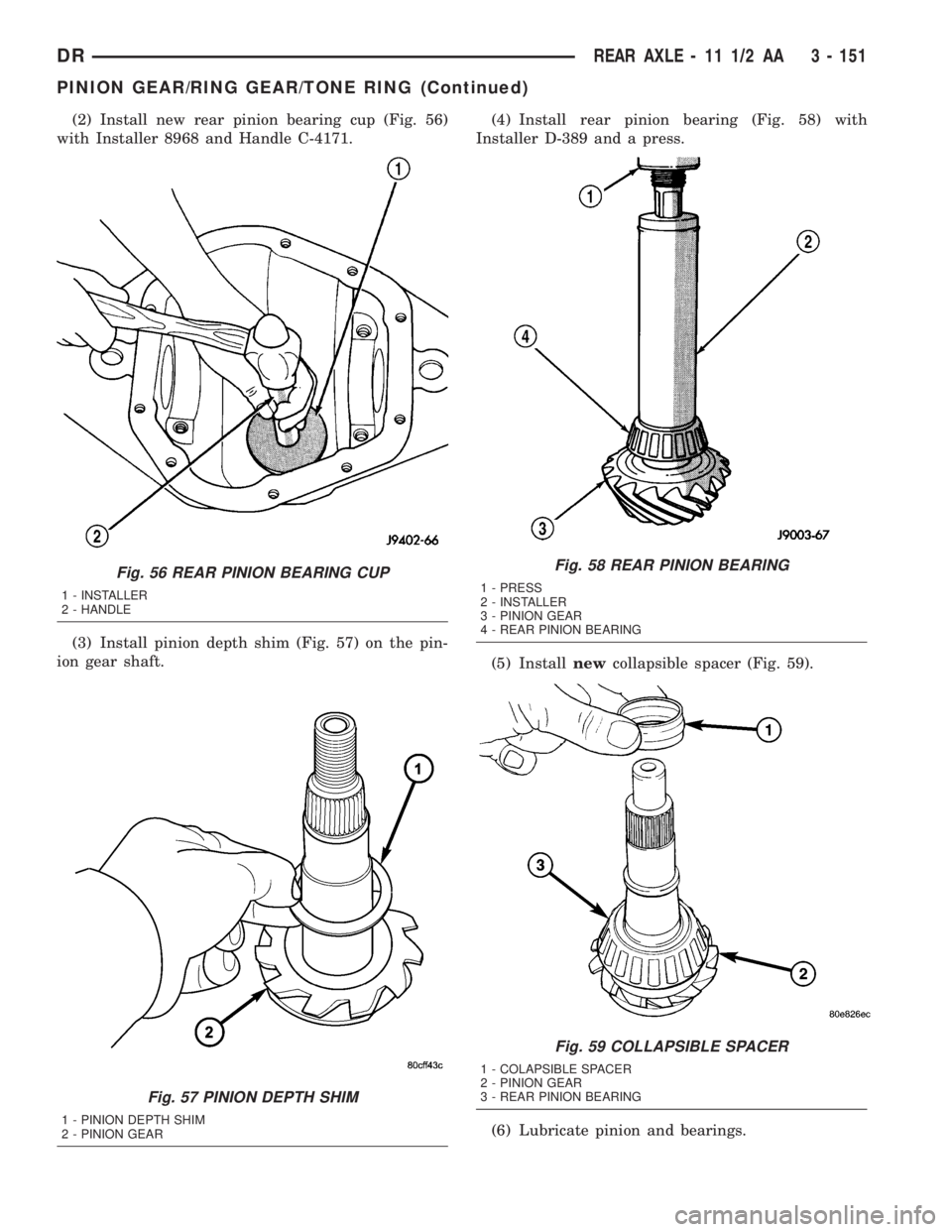
(2) Install new rear pinion bearing cup (Fig. 56)
with Installer 8968 and Handle C-4171.
(3) Install pinion depth shim (Fig. 57) on the pin-
ion gear shaft.(4) Install rear pinion bearing (Fig. 58) with
Installer D-389 and a press.
(5) Installnewcollapsible spacer (Fig. 59).
(6) Lubricate pinion and bearings.
Fig. 56 REAR PINION BEARING CUP
1 - INSTALLER
2 - HANDLE
Fig. 57 PINION DEPTH SHIM
1 - PINION DEPTH SHIM
2 - PINION GEAR
Fig. 58 REAR PINION BEARING
1 - PRESS
2 - INSTALLER
3 - PINION GEAR
4 - REAR PINION BEARING
Fig. 59 COLLAPSIBLE SPACER
1 - COLAPSIBLE SPACER
2 - PINION GEAR
3 - REAR PINION BEARING
DRREAR AXLE - 11 1/2 AA 3 - 151
PINION GEAR/RING GEAR/TONE RING (Continued)
Page 225 of 2895
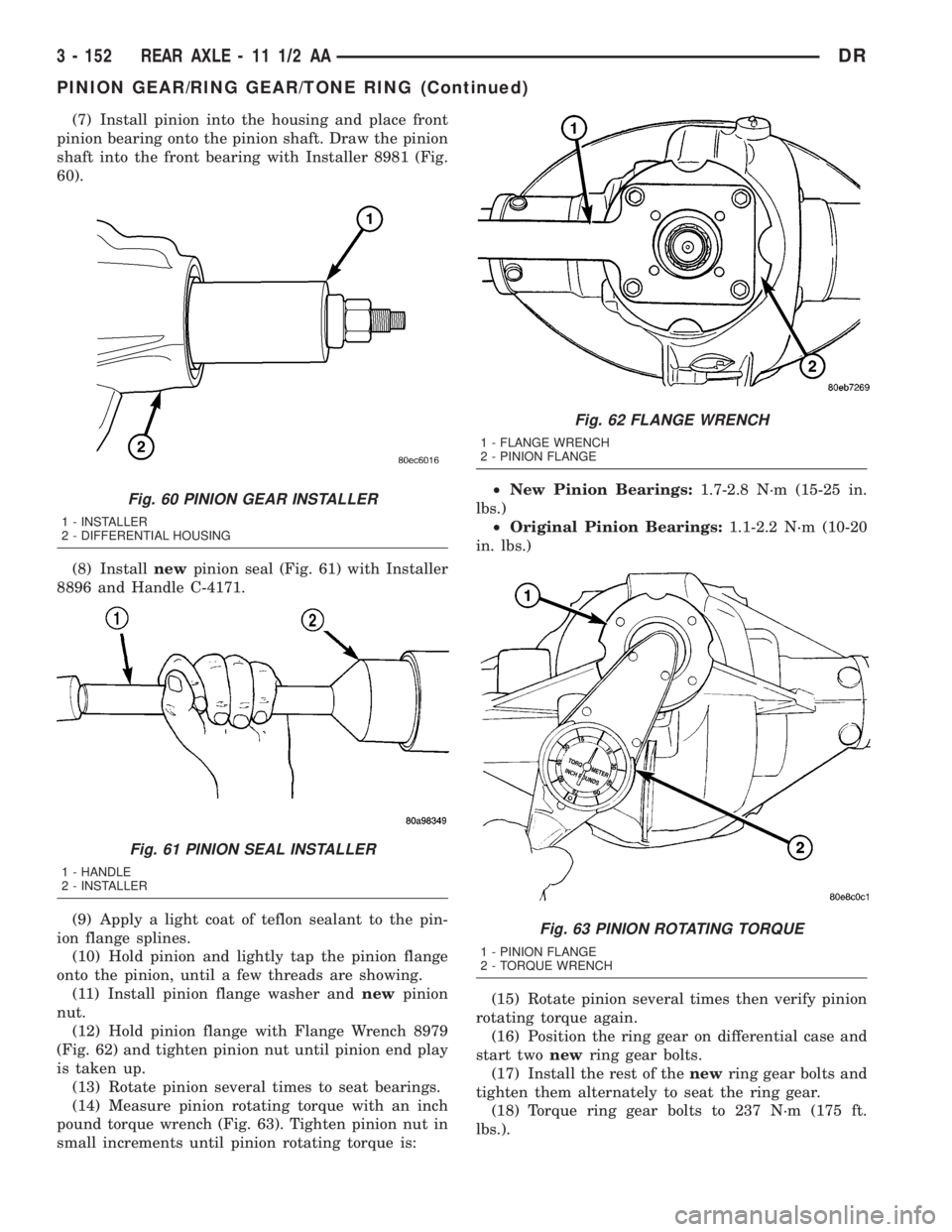
(7) Install pinion into the housing and place front
pinion bearing onto the pinion shaft. Draw the pinion
shaft into the front bearing with Installer 8981 (Fig.
60).
(8) Installnewpinion seal (Fig. 61) with Installer
8896 and Handle C-4171.
(9) Apply a light coat of teflon sealant to the pin-
ion flange splines.
(10) Hold pinion and lightly tap the pinion flange
onto the pinion, until a few threads are showing.
(11) Install pinion flange washer andnewpinion
nut.
(12) Hold pinion flange with Flange Wrench 8979
(Fig. 62) and tighten pinion nut until pinion end play
is taken up.
(13) Rotate pinion several times to seat bearings.
(14) Measure pinion rotating torque with an inch
pound torque wrench (Fig. 63). Tighten pinion nut in
small increments until pinion rotating torque is:²New Pinion Bearings:1.7-2.8 N´m (15-25 in.
lbs.)
²Original Pinion Bearings:1.1-2.2 N´m (10-20
in. lbs.)
(15) Rotate pinion several times then verify pinion
rotating torque again.
(16) Position the ring gear on differential case and
start twonewring gear bolts.
(17) Install the rest of thenewring gear bolts and
tighten them alternately to seat the ring gear.
(18) Torque ring gear bolts to 237 N´m (175 ft.
lbs.).
Fig. 60 PINION GEAR INSTALLER
1 - INSTALLER
2 - DIFFERENTIAL HOUSING
Fig. 61 PINION SEAL INSTALLER
1 - HANDLE
2 - INSTALLER
Fig. 62 FLANGE WRENCH
1 - FLANGE WRENCH
2 - PINION FLANGE
Fig. 63 PINION ROTATING TORQUE
1 - PINION FLANGE
2 - TORQUE WRENCH
3 - 152 REAR AXLE - 11 1/2 AADR
PINION GEAR/RING GEAR/TONE RING (Continued)
Page 226 of 2895
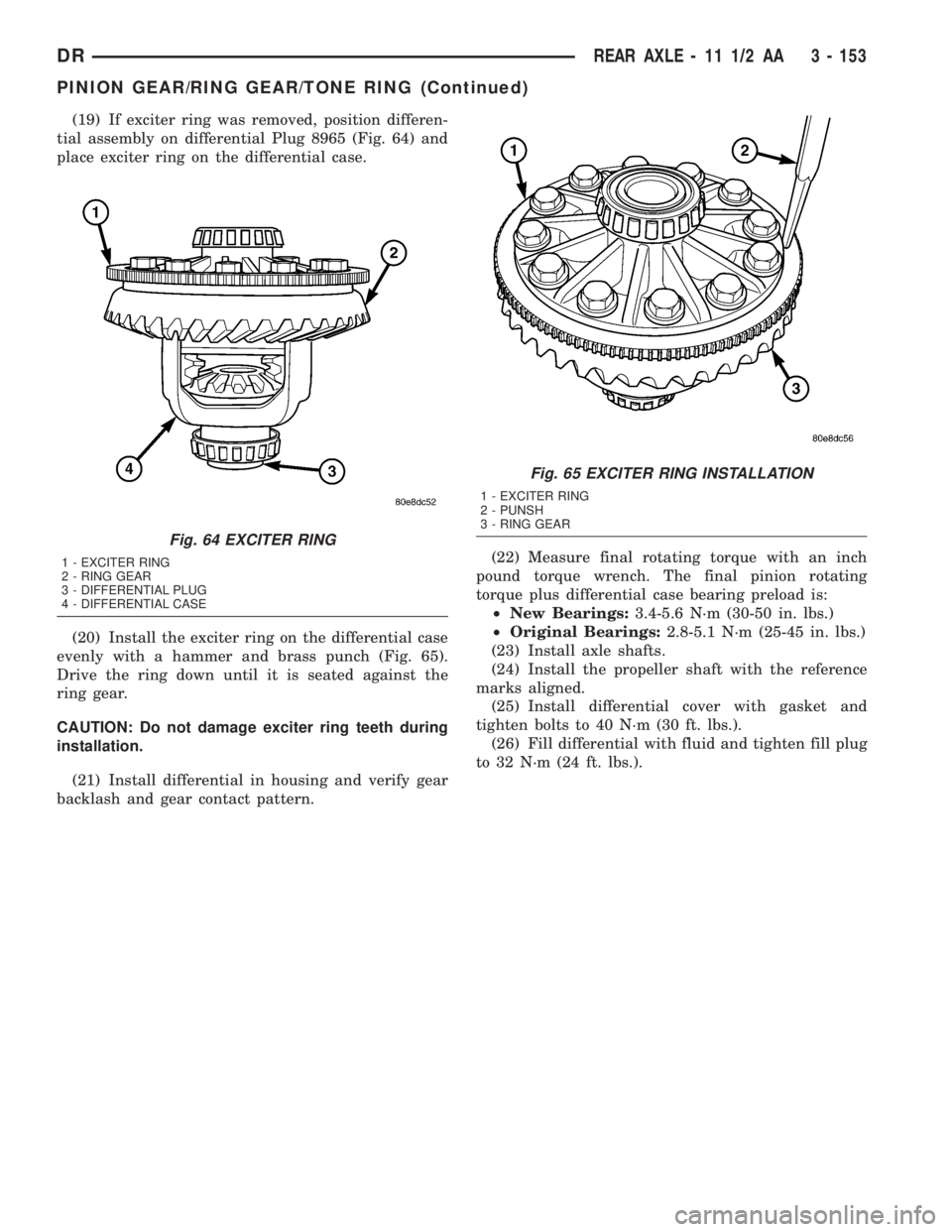
(19) If exciter ring was removed, position differen-
tial assembly on differential Plug 8965 (Fig. 64) and
place exciter ring on the differential case.
(20) Install the exciter ring on the differential case
evenly with a hammer and brass punch (Fig. 65).
Drive the ring down until it is seated against the
ring gear.
CAUTION: Do not damage exciter ring teeth during
installation.
(21) Install differential in housing and verify gear
backlash and gear contact pattern.(22) Measure final rotating torque with an inch
pound torque wrench. The final pinion rotating
torque plus differential case bearing preload is:
²New Bearings:3.4-5.6 N´m (30-50 in. lbs.)
²Original Bearings:2.8-5.1 N´m (25-45 in. lbs.)
(23) Install axle shafts.
(24) Install the propeller shaft with the reference
marks aligned.
(25) Install differential cover with gasket and
tighten bolts to 40 N´m (30 ft. lbs.).
(26) Fill differential with fluid and tighten fill plug
to 32 N´m (24 ft. lbs.).
Fig. 64 EXCITER RING
1 - EXCITER RING
2 - RING GEAR
3 - DIFFERENTIAL PLUG
4 - DIFFERENTIAL CASE
Fig. 65 EXCITER RING INSTALLATION
1 - EXCITER RING
2 - PUNSH
3 - RING GEAR
DRREAR AXLE - 11 1/2 AA 3 - 153
PINION GEAR/RING GEAR/TONE RING (Continued)
Page 227 of 2895
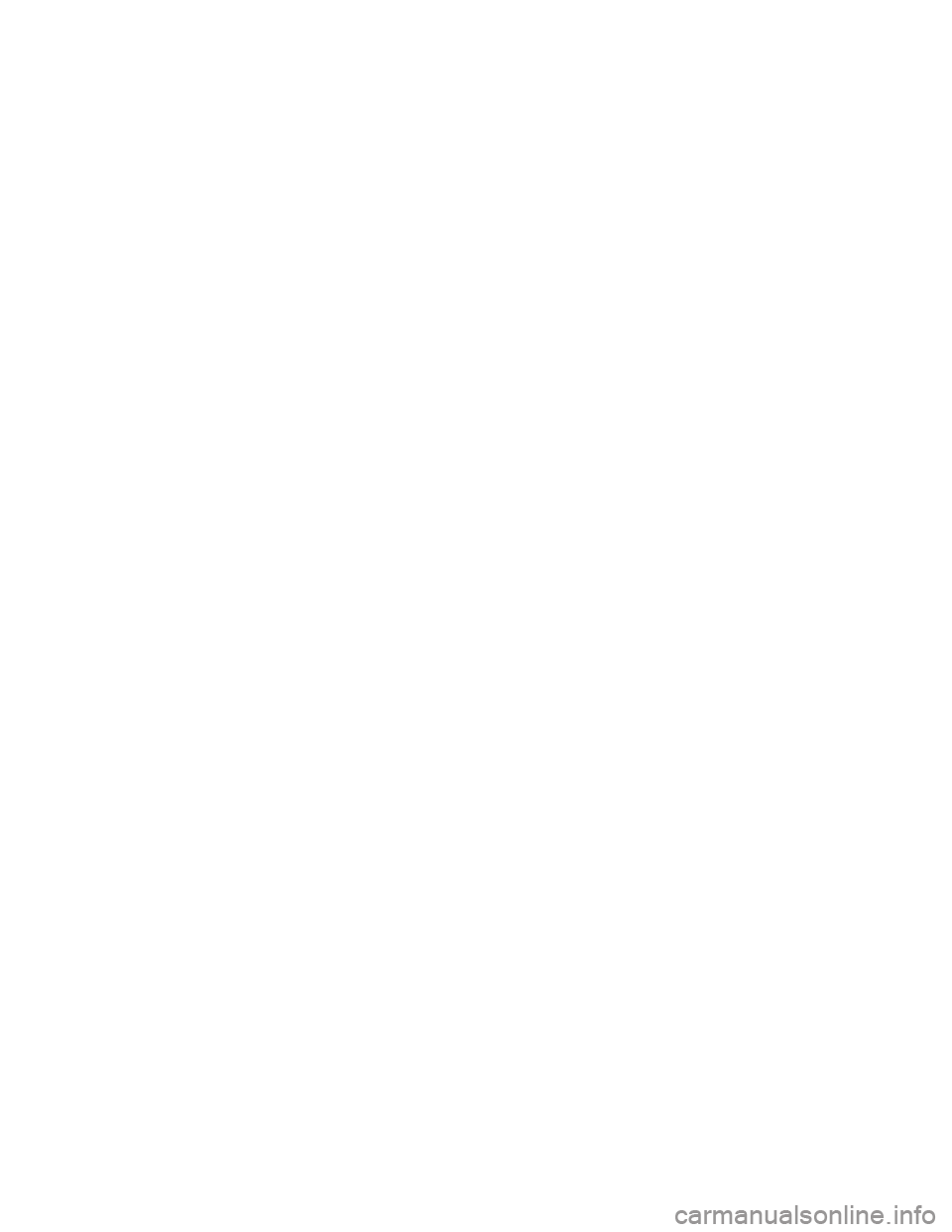
Page 228 of 2895
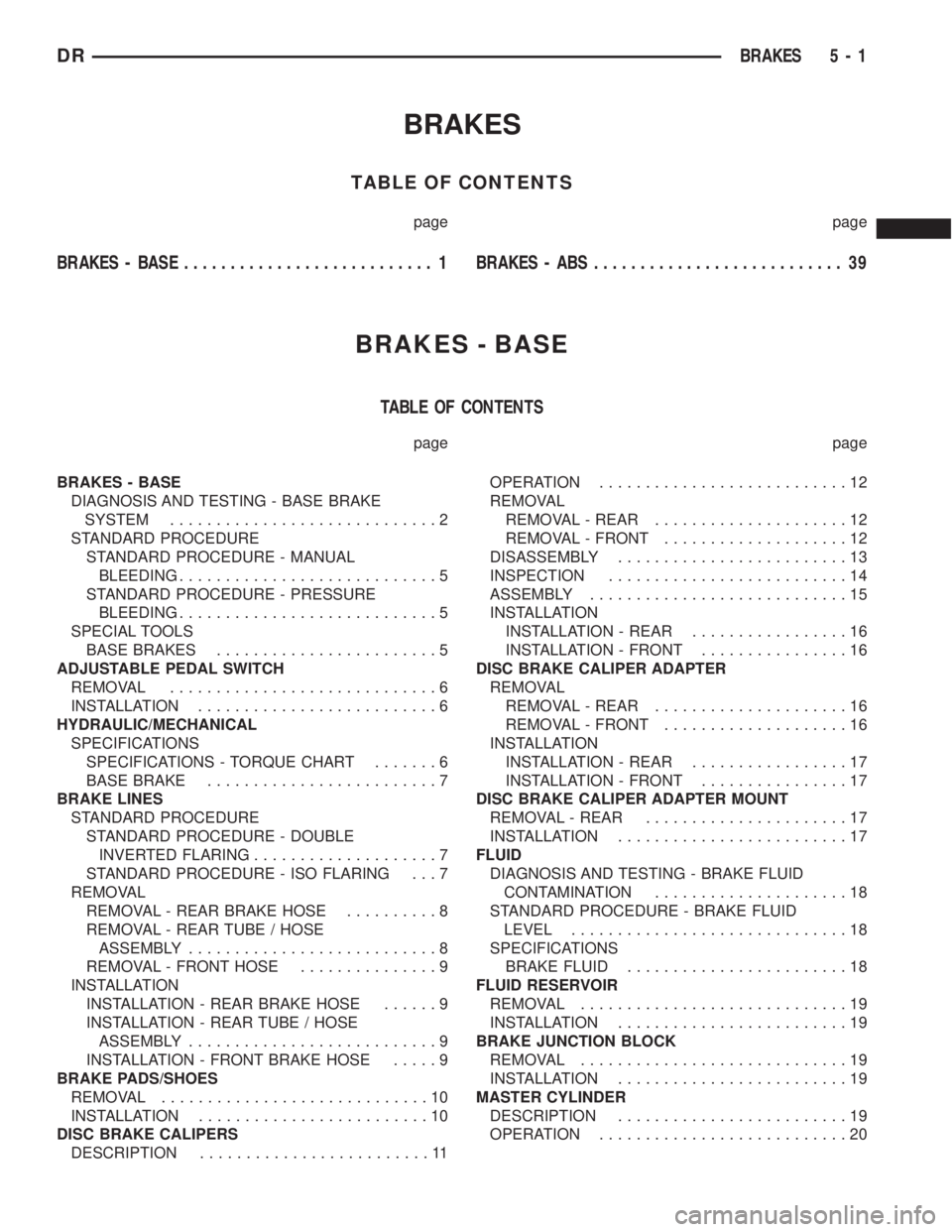
BRAKES
TABLE OF CONTENTS
page page
BRAKES - BASE........................... 1BRAKES - ABS........................... 39
BRAKES - BASE
TABLE OF CONTENTS
page page
BRAKES - BASE
DIAGNOSIS AND TESTING - BASE BRAKE
SYSTEM.............................2
STANDARD PROCEDURE
STANDARD PROCEDURE - MANUAL
BLEEDING............................5
STANDARD PROCEDURE - PRESSURE
BLEEDING............................5
SPECIAL TOOLS
BASE BRAKES........................5
ADJUSTABLE PEDAL SWITCH
REMOVAL.............................6
INSTALLATION..........................6
HYDRAULIC/MECHANICAL
SPECIFICATIONS
SPECIFICATIONS - TORQUE CHART.......6
BASE BRAKE.........................7
BRAKE LINES
STANDARD PROCEDURE
STANDARD PROCEDURE - DOUBLE
INVERTED FLARING....................7
STANDARD PROCEDURE - ISO FLARING . . . 7
REMOVAL
REMOVAL - REAR BRAKE HOSE..........8
REMOVAL - REAR TUBE / HOSE
ASSEMBLY...........................8
REMOVAL - FRONT HOSE...............9
INSTALLATION
INSTALLATION - REAR BRAKE HOSE......9
INSTALLATION - REAR TUBE / HOSE
ASSEMBLY...........................9
INSTALLATION - FRONT BRAKE HOSE.....9
BRAKE PADS/SHOES
REMOVAL.............................10
INSTALLATION.........................10
DISC BRAKE CALIPERS
DESCRIPTION.........................11OPERATION...........................12
REMOVAL
REMOVAL - REAR.....................12
REMOVAL - FRONT....................12
DISASSEMBLY.........................13
INSPECTION..........................14
ASSEMBLY............................15
INSTALLATION
INSTALLATION - REAR.................16
INSTALLATION - FRONT................16
DISC BRAKE CALIPER ADAPTER
REMOVAL
REMOVAL - REAR.....................16
REMOVAL - FRONT....................16
INSTALLATION
INSTALLATION - REAR.................17
INSTALLATION - FRONT................17
DISC BRAKE CALIPER ADAPTER MOUNT
REMOVAL - REAR......................17
INSTALLATION.........................17
FLUID
DIAGNOSIS AND TESTING - BRAKE FLUID
CONTAMINATION.....................18
STANDARD PROCEDURE - BRAKE FLUID
LEVEL..............................18
SPECIFICATIONS
BRAKE FLUID........................18
FLUID RESERVOIR
REMOVAL.............................19
INSTALLATION.........................19
BRAKE JUNCTION BLOCK
REMOVAL.............................19
INSTALLATION.........................19
MASTER CYLINDER
DESCRIPTION.........................19
OPERATION...........................20
DRBRAKES 5 - 1
Page 229 of 2895
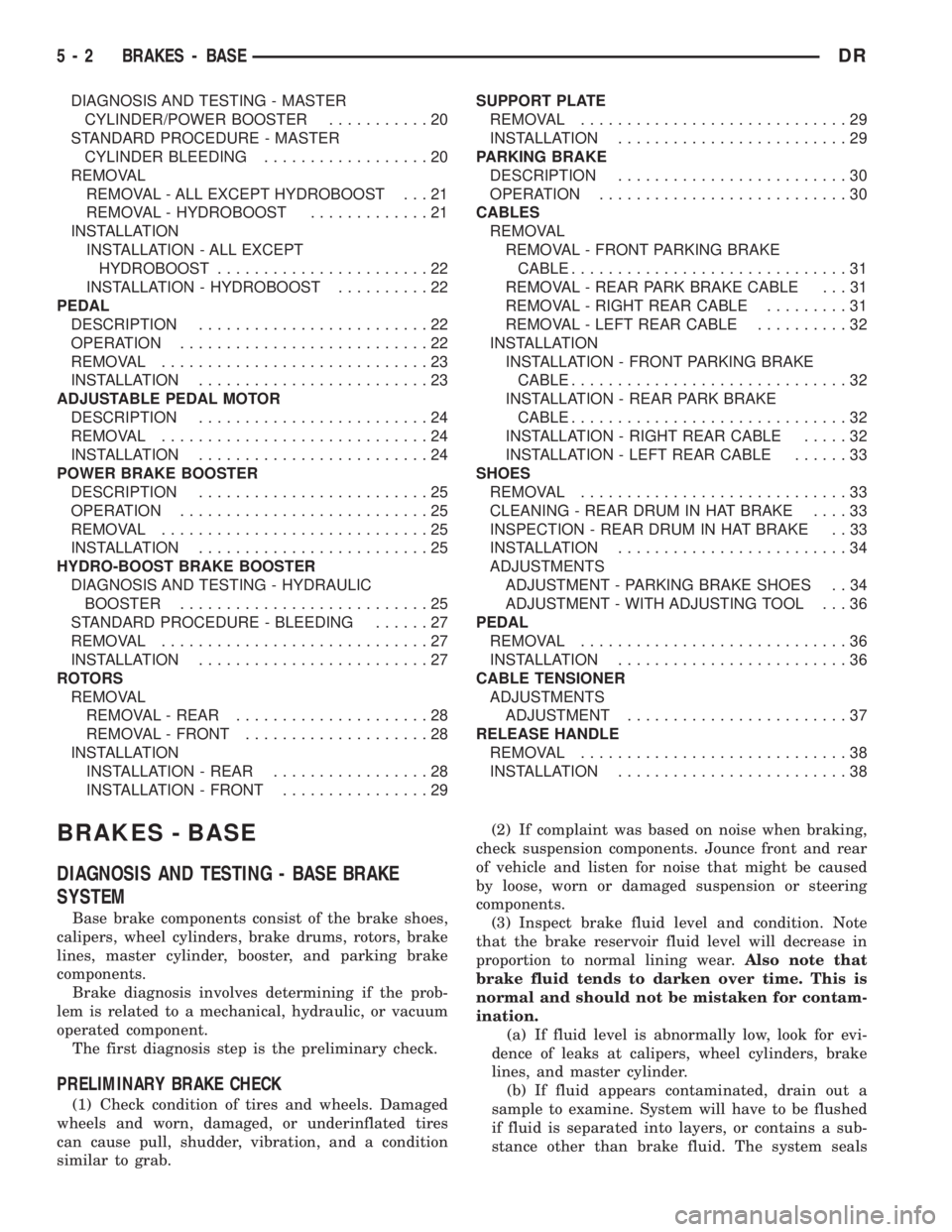
DIAGNOSIS AND TESTING - MASTER
CYLINDER/POWER BOOSTER...........20
STANDARD PROCEDURE - MASTER
CYLINDER BLEEDING..................20
REMOVAL
REMOVAL - ALL EXCEPT HYDROBOOST . . . 21
REMOVAL - HYDROBOOST.............21
INSTALLATION
INSTALLATION - ALL EXCEPT
HYDROBOOST.......................22
INSTALLATION - HYDROBOOST..........22
PEDAL
DESCRIPTION.........................22
OPERATION...........................22
REMOVAL.............................23
INSTALLATION.........................23
ADJUSTABLE PEDAL MOTOR
DESCRIPTION.........................24
REMOVAL.............................24
INSTALLATION.........................24
POWER BRAKE BOOSTER
DESCRIPTION.........................25
OPERATION...........................25
REMOVAL.............................25
INSTALLATION.........................25
HYDRO-BOOST BRAKE BOOSTER
DIAGNOSIS AND TESTING - HYDRAULIC
BOOSTER...........................25
STANDARD PROCEDURE - BLEEDING......27
REMOVAL.............................27
INSTALLATION.........................27
ROTORS
REMOVAL
REMOVAL - REAR.....................28
REMOVAL - FRONT....................28
INSTALLATION
INSTALLATION - REAR.................28
INSTALLATION - FRONT................29SUPPORT PLATE
REMOVAL.............................29
INSTALLATION.........................29
PARKING BRAKE
DESCRIPTION.........................30
OPERATION...........................30
CABLES
REMOVAL
REMOVAL - FRONT PARKING BRAKE
CABLE..............................31
REMOVAL - REAR PARK BRAKE CABLE . . . 31
REMOVAL - RIGHT REAR CABLE.........31
REMOVAL - LEFT REAR CABLE..........32
INSTALLATION
INSTALLATION - FRONT PARKING BRAKE
CABLE..............................32
INSTALLATION - REAR PARK BRAKE
CABLE..............................32
INSTALLATION - RIGHT REAR CABLE.....32
INSTALLATION - LEFT REAR CABLE......33
SHOES
REMOVAL.............................33
CLEANING - REAR DRUM IN HAT BRAKE....33
INSPECTION - REAR DRUM IN HAT BRAKE . . 33
INSTALLATION.........................34
ADJUSTMENTS
ADJUSTMENT - PARKING BRAKE SHOES . . 34
ADJUSTMENT - WITH ADJUSTING TOOL . . . 36
PEDAL
REMOVAL.............................36
INSTALLATION.........................36
CABLE TENSIONER
ADJUSTMENTS
ADJUSTMENT........................37
RELEASE HANDLE
REMOVAL.............................38
INSTALLATION.........................38
BRAKES - BASE
DIAGNOSIS AND TESTING - BASE BRAKE
SYSTEM
Base brake components consist of the brake shoes,
calipers, wheel cylinders, brake drums, rotors, brake
lines, master cylinder, booster, and parking brake
components.
Brake diagnosis involves determining if the prob-
lem is related to a mechanical, hydraulic, or vacuum
operated component.
The first diagnosis step is the preliminary check.
PRELIMINARY BRAKE CHECK
(1) Check condition of tires and wheels. Damaged
wheels and worn, damaged, or underinflated tires
can cause pull, shudder, vibration, and a condition
similar to grab.(2) If complaint was based on noise when braking,
check suspension components. Jounce front and rear
of vehicle and listen for noise that might be caused
by loose, worn or damaged suspension or steering
components.
(3) Inspect brake fluid level and condition. Note
that the brake reservoir fluid level will decrease in
proportion to normal lining wear.Also note that
brake fluid tends to darken over time. This is
normal and should not be mistaken for contam-
ination.
(a) If fluid level is abnormally low, look for evi-
dence of leaks at calipers, wheel cylinders, brake
lines, and master cylinder.
(b) If fluid appears contaminated, drain out a
sample to examine. System will have to be flushed
if fluid is separated into layers, or contains a sub-
stance other than brake fluid. The system seals
5 - 2 BRAKES - BASEDR
Page 230 of 2895
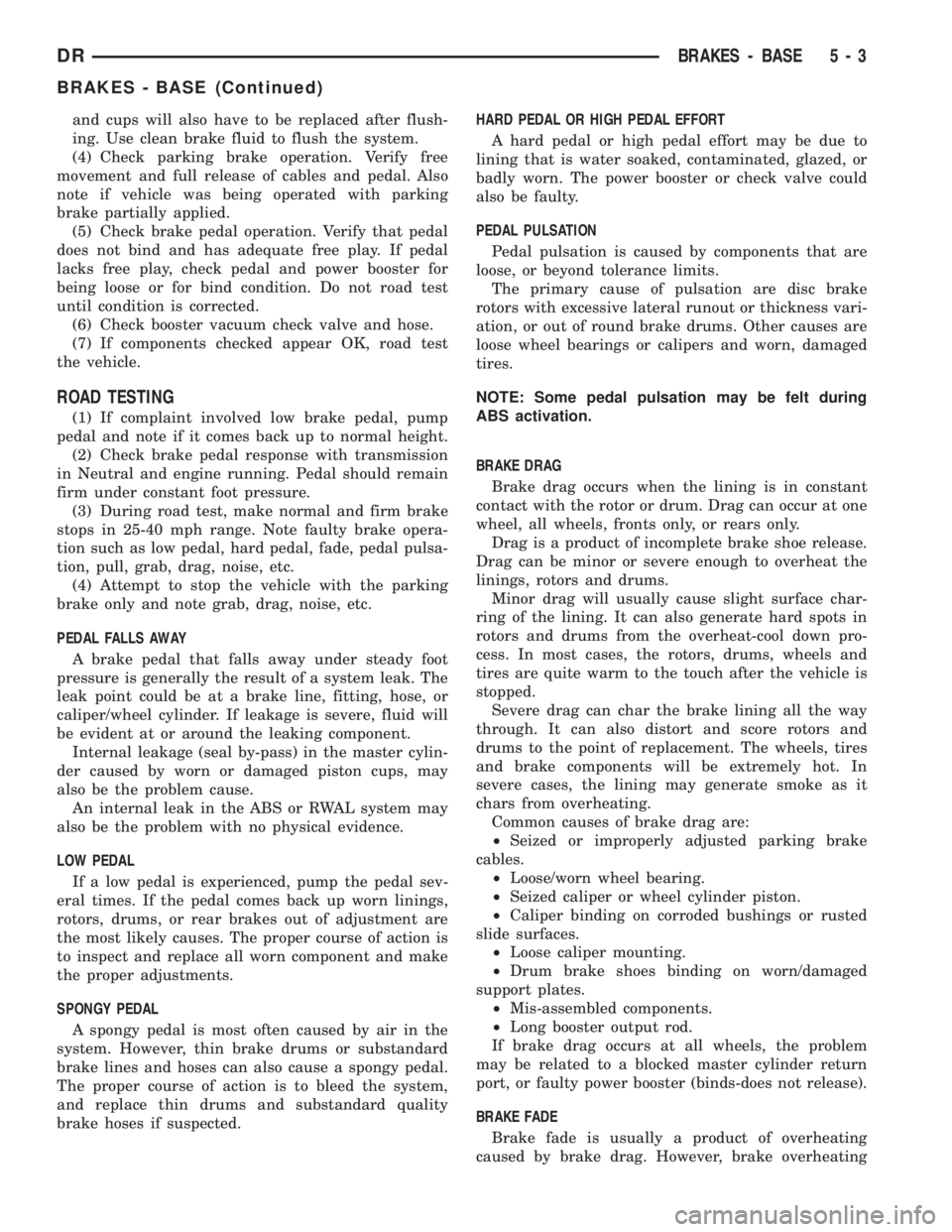
and cups will also have to be replaced after flush-
ing. Use clean brake fluid to flush the system.
(4) Check parking brake operation. Verify free
movement and full release of cables and pedal. Also
note if vehicle was being operated with parking
brake partially applied.
(5) Check brake pedal operation. Verify that pedal
does not bind and has adequate free play. If pedal
lacks free play, check pedal and power booster for
being loose or for bind condition. Do not road test
until condition is corrected.
(6) Check booster vacuum check valve and hose.
(7) If components checked appear OK, road test
the vehicle.
ROAD TESTING
(1) If complaint involved low brake pedal, pump
pedal and note if it comes back up to normal height.
(2) Check brake pedal response with transmission
in Neutral and engine running. Pedal should remain
firm under constant foot pressure.
(3) During road test, make normal and firm brake
stops in 25-40 mph range. Note faulty brake opera-
tion such as low pedal, hard pedal, fade, pedal pulsa-
tion, pull, grab, drag, noise, etc.
(4) Attempt to stop the vehicle with the parking
brake only and note grab, drag, noise, etc.
PEDAL FALLS AWAY
A brake pedal that falls away under steady foot
pressure is generally the result of a system leak. The
leak point could be at a brake line, fitting, hose, or
caliper/wheel cylinder. If leakage is severe, fluid will
be evident at or around the leaking component.
Internal leakage (seal by-pass) in the master cylin-
der caused by worn or damaged piston cups, may
also be the problem cause.
An internal leak in the ABS or RWAL system may
also be the problem with no physical evidence.
LOW PEDAL
If a low pedal is experienced, pump the pedal sev-
eral times. If the pedal comes back up worn linings,
rotors, drums, or rear brakes out of adjustment are
the most likely causes. The proper course of action is
to inspect and replace all worn component and make
the proper adjustments.
SPONGY PEDAL
A spongy pedal is most often caused by air in the
system. However, thin brake drums or substandard
brake lines and hoses can also cause a spongy pedal.
The proper course of action is to bleed the system,
and replace thin drums and substandard quality
brake hoses if suspected.HARD PEDAL OR HIGH PEDAL EFFORT
A hard pedal or high pedal effort may be due to
lining that is water soaked, contaminated, glazed, or
badly worn. The power booster or check valve could
also be faulty.
PEDAL PULSATION
Pedal pulsation is caused by components that are
loose, or beyond tolerance limits.
The primary cause of pulsation are disc brake
rotors with excessive lateral runout or thickness vari-
ation, or out of round brake drums. Other causes are
loose wheel bearings or calipers and worn, damaged
tires.
NOTE: Some pedal pulsation may be felt during
ABS activation.
BRAKE DRAG
Brake drag occurs when the lining is in constant
contact with the rotor or drum. Drag can occur at one
wheel, all wheels, fronts only, or rears only.
Drag is a product of incomplete brake shoe release.
Drag can be minor or severe enough to overheat the
linings, rotors and drums.
Minor drag will usually cause slight surface char-
ring of the lining. It can also generate hard spots in
rotors and drums from the overheat-cool down pro-
cess. In most cases, the rotors, drums, wheels and
tires are quite warm to the touch after the vehicle is
stopped.
Severe drag can char the brake lining all the way
through. It can also distort and score rotors and
drums to the point of replacement. The wheels, tires
and brake components will be extremely hot. In
severe cases, the lining may generate smoke as it
chars from overheating.
Common causes of brake drag are:
²Seized or improperly adjusted parking brake
cables.
²Loose/worn wheel bearing.
²Seized caliper or wheel cylinder piston.
²Caliper binding on corroded bushings or rusted
slide surfaces.
²Loose caliper mounting.
²Drum brake shoes binding on worn/damaged
support plates.
²Mis-assembled components.
²Long booster output rod.
If brake drag occurs at all wheels, the problem
may be related to a blocked master cylinder return
port, or faulty power booster (binds-does not release).
BRAKE FADE
Brake fade is usually a product of overheating
caused by brake drag. However, brake overheating
DRBRAKES - BASE 5 - 3
BRAKES - BASE (Continued)