DODGE RAM 2003 Service Repair Manual
Manufacturer: DODGE, Model Year: 2003, Model line: RAM, Model: DODGE RAM 2003Pages: 2895, PDF Size: 83.15 MB
Page 2501 of 2895
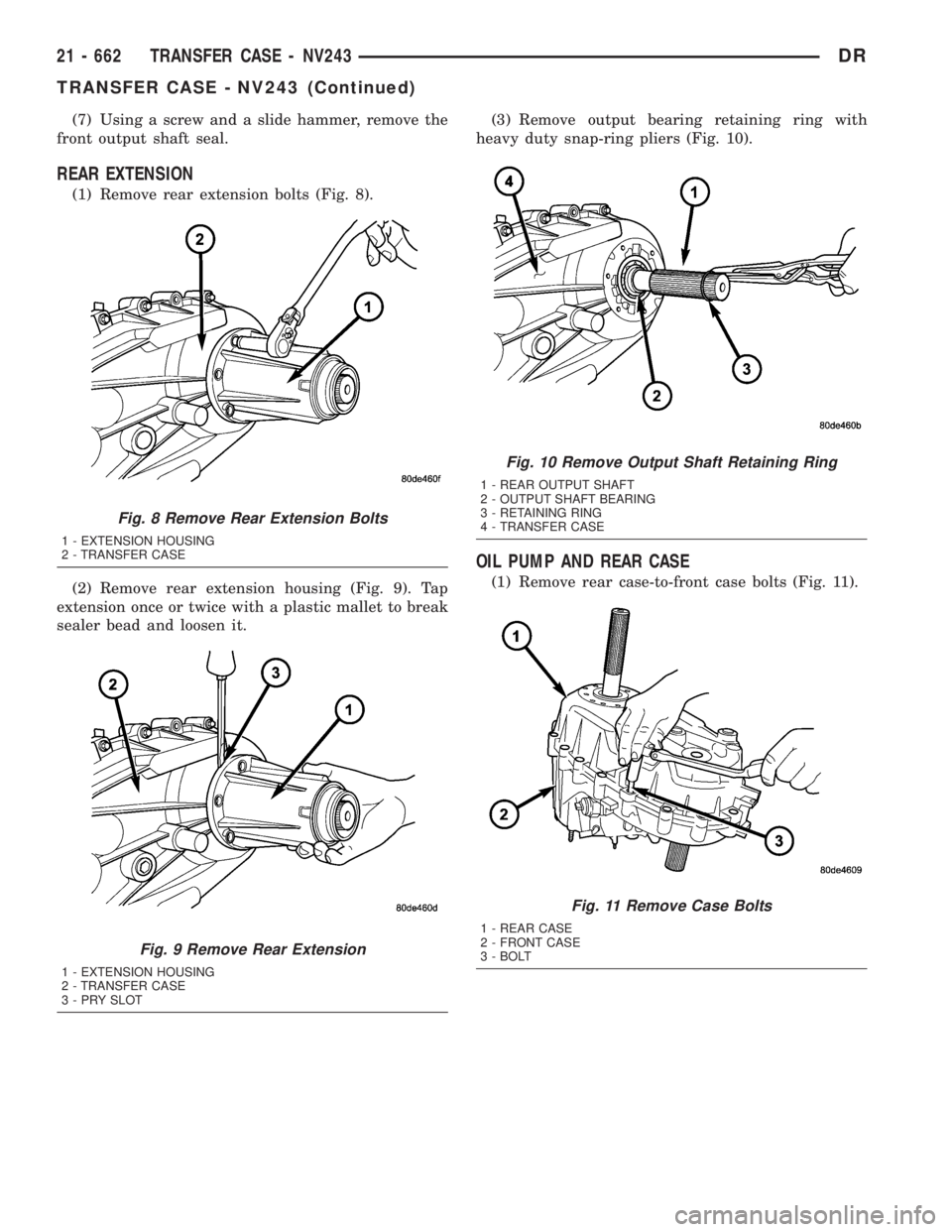
(7) Using a screw and a slide hammer, remove the
front output shaft seal.
REAR EXTENSION
(1) Remove rear extension bolts (Fig. 8).
(2) Remove rear extension housing (Fig. 9). Tap
extension once or twice with a plastic mallet to break
sealer bead and loosen it.(3) Remove output bearing retaining ring with
heavy duty snap-ring pliers (Fig. 10).
OIL PUMP AND REAR CASE
(1) Remove rear case-to-front case bolts (Fig. 11).
Fig. 8 Remove Rear Extension Bolts
1 - EXTENSION HOUSING
2 - TRANSFER CASE
Fig. 9 Remove Rear Extension
1 - EXTENSION HOUSING
2 - TRANSFER CASE
3 - PRY SLOT
Fig. 10 Remove Output Shaft Retaining Ring
1 - REAR OUTPUT SHAFT
2 - OUTPUT SHAFT BEARING
3 - RETAINING RING
4 - TRANSFER CASE
Fig. 11 Remove Case Bolts
1 - REAR CASE
2 - FRONT CASE
3 - BOLT
21 - 662 TRANSFER CASE - NV243DR
TRANSFER CASE - NV243 (Continued)
Page 2502 of 2895
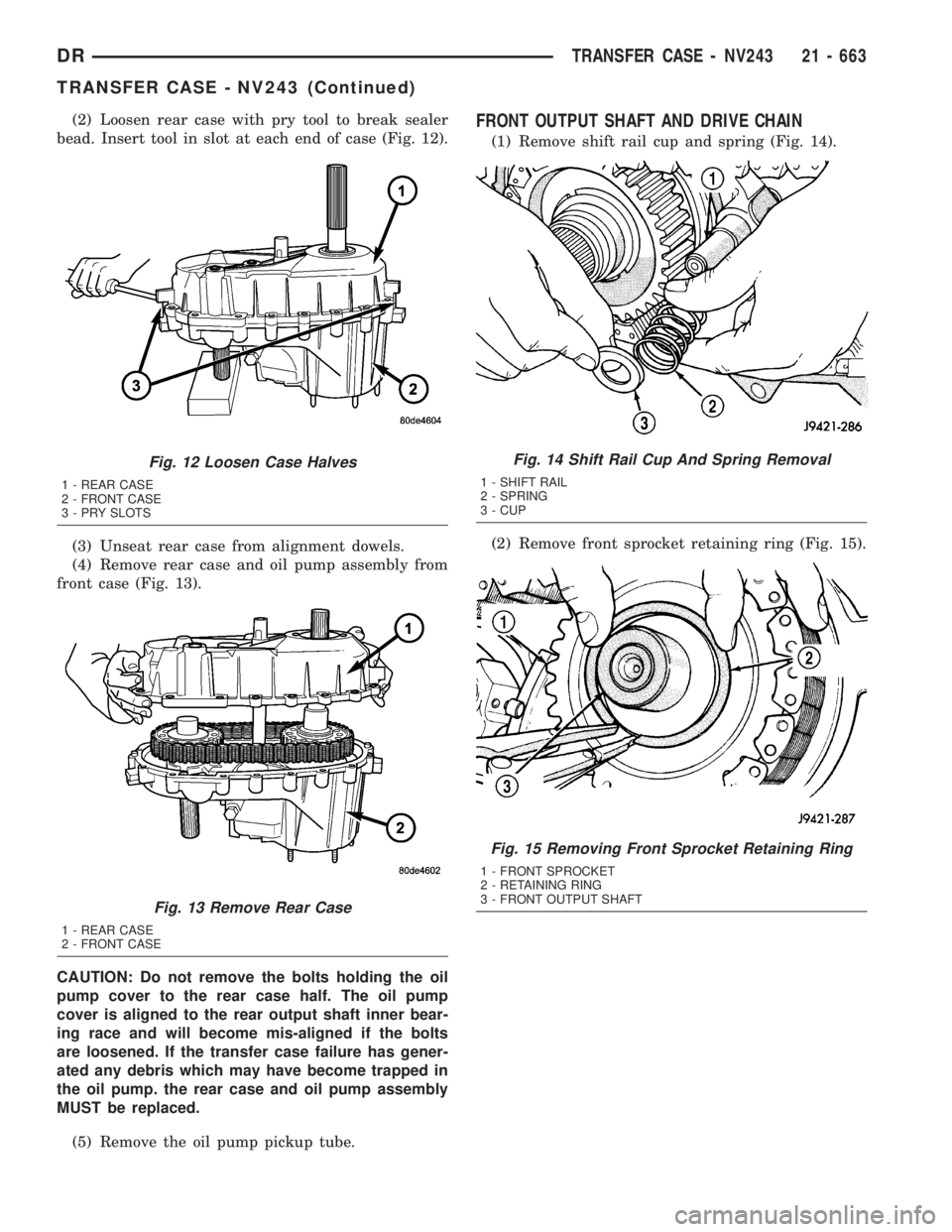
(2) Loosen rear case with pry tool to break sealer
bead. Insert tool in slot at each end of case (Fig. 12).
(3) Unseat rear case from alignment dowels.
(4) Remove rear case and oil pump assembly from
front case (Fig. 13).
CAUTION: Do not remove the bolts holding the oil
pump cover to the rear case half. The oil pump
cover is aligned to the rear output shaft inner bear-
ing race and will become mis-aligned if the bolts
are loosened. If the transfer case failure has gener-
ated any debris which may have become trapped in
the oil pump. the rear case and oil pump assembly
MUST be replaced.
(5) Remove the oil pump pickup tube.FRONT OUTPUT SHAFT AND DRIVE CHAIN
(1) Remove shift rail cup and spring (Fig. 14).
(2) Remove front sprocket retaining ring (Fig. 15).
Fig. 12 Loosen Case Halves
1 - REAR CASE
2 - FRONT CASE
3 - PRY SLOTS
Fig. 13 Remove Rear Case
1 - REAR CASE
2 - FRONT CASE
Fig. 14 Shift Rail Cup And Spring Removal
1 - SHIFT RAIL
2 - SPRING
3 - CUP
Fig. 15 Removing Front Sprocket Retaining Ring
1 - FRONT SPROCKET
2 - RETAINING RING
3 - FRONT OUTPUT SHAFT
DRTRANSFER CASE - NV243 21 - 663
TRANSFER CASE - NV243 (Continued)
Page 2503 of 2895
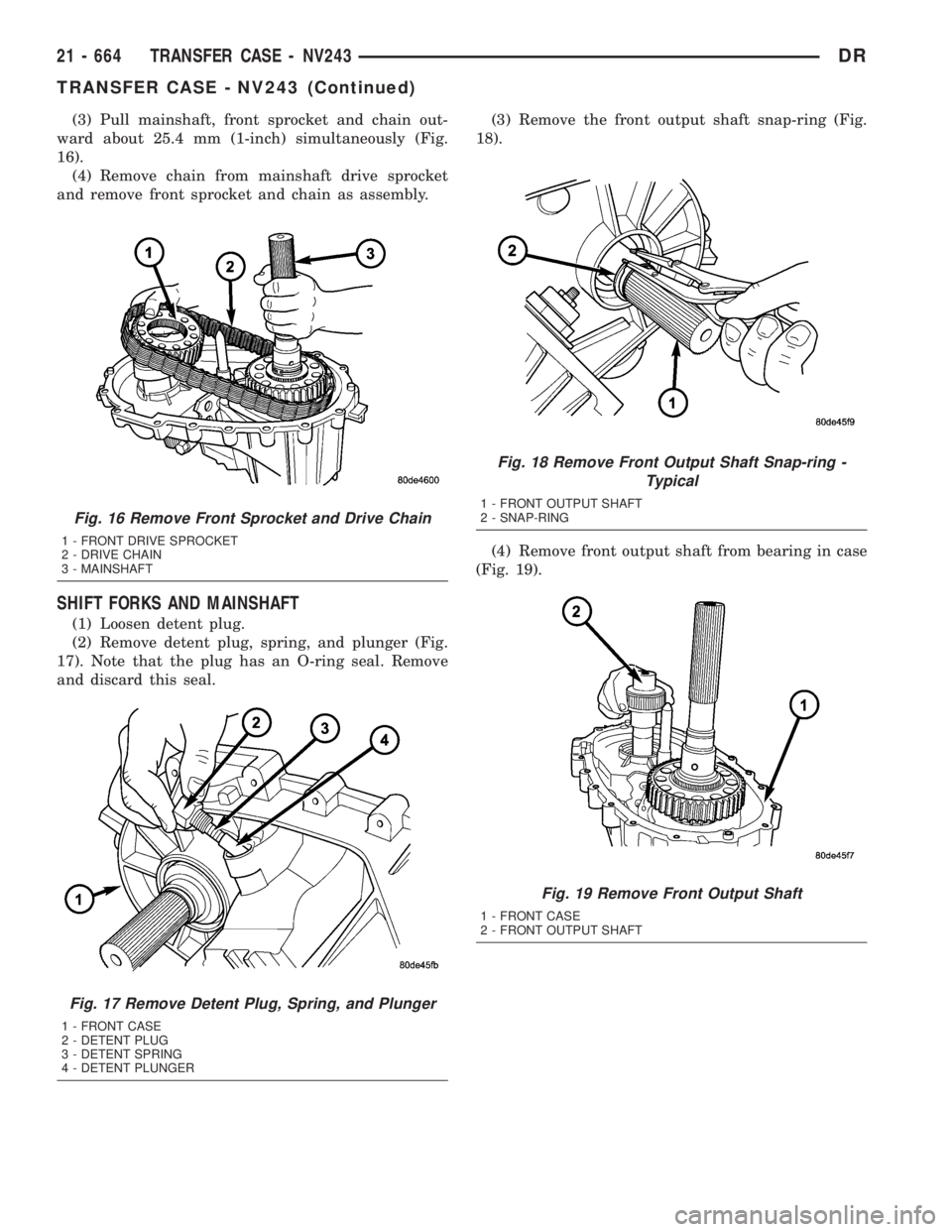
(3) Pull mainshaft, front sprocket and chain out-
ward about 25.4 mm (1-inch) simultaneously (Fig.
16).
(4) Remove chain from mainshaft drive sprocket
and remove front sprocket and chain as assembly.
SHIFT FORKS AND MAINSHAFT
(1) Loosen detent plug.
(2) Remove detent plug, spring, and plunger (Fig.
17). Note that the plug has an O-ring seal. Remove
and discard this seal.(3) Remove the front output shaft snap-ring (Fig.
18).
(4) Remove front output shaft from bearing in case
(Fig. 19).
Fig. 16 Remove Front Sprocket and Drive Chain
1 - FRONT DRIVE SPROCKET
2 - DRIVE CHAIN
3 - MAINSHAFT
Fig. 17 Remove Detent Plug, Spring, and Plunger
1 - FRONT CASE
2 - DETENT PLUG
3 - DETENT SPRING
4 - DETENT PLUNGER
Fig. 18 Remove Front Output Shaft Snap-ring -
Typical
1 - FRONT OUTPUT SHAFT
2 - SNAP-RING
Fig. 19 Remove Front Output Shaft
1 - FRONT CASE
2 - FRONT OUTPUT SHAFT
21 - 664 TRANSFER CASE - NV243DR
TRANSFER CASE - NV243 (Continued)
Page 2504 of 2895
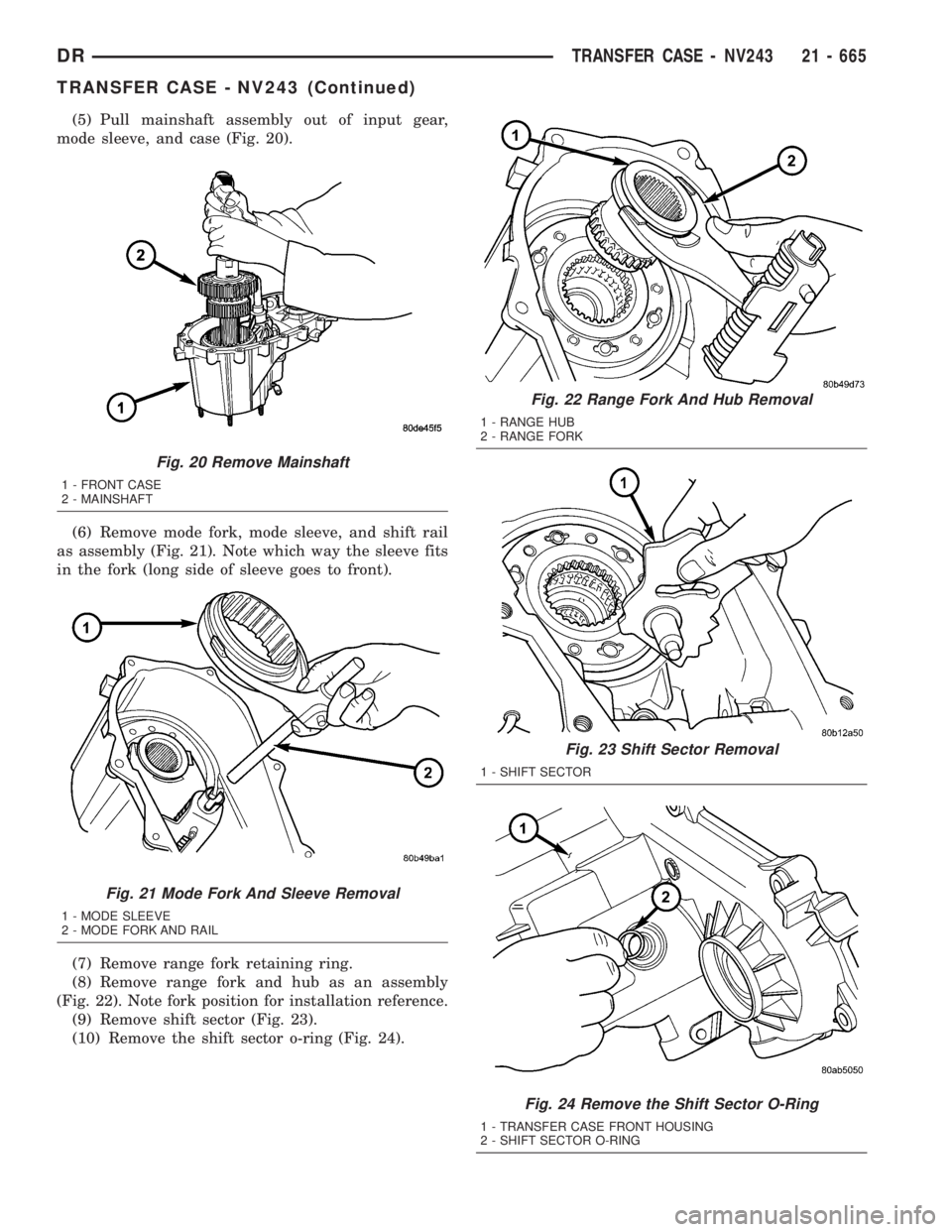
(5) Pull mainshaft assembly out of input gear,
mode sleeve, and case (Fig. 20).
(6) Remove mode fork, mode sleeve, and shift rail
as assembly (Fig. 21). Note which way the sleeve fits
in the fork (long side of sleeve goes to front).
(7) Remove range fork retaining ring.
(8) Remove range fork and hub as an assembly
(Fig. 22). Note fork position for installation reference.
(9) Remove shift sector (Fig. 23).
(10) Remove the shift sector o-ring (Fig. 24).
Fig. 20 Remove Mainshaft
1 - FRONT CASE
2 - MAINSHAFT
Fig. 21 Mode Fork And Sleeve Removal
1 - MODE SLEEVE
2 - MODE FORK AND RAIL
Fig. 22 Range Fork And Hub Removal
1 - RANGE HUB
2 - RANGE FORK
Fig. 23 Shift Sector Removal
1 - SHIFT SECTOR
Fig. 24 Remove the Shift Sector O-Ring
1 - TRANSFER CASE FRONT HOUSING
2 - SHIFT SECTOR O-RING
DRTRANSFER CASE - NV243 21 - 665
TRANSFER CASE - NV243 (Continued)
Page 2505 of 2895
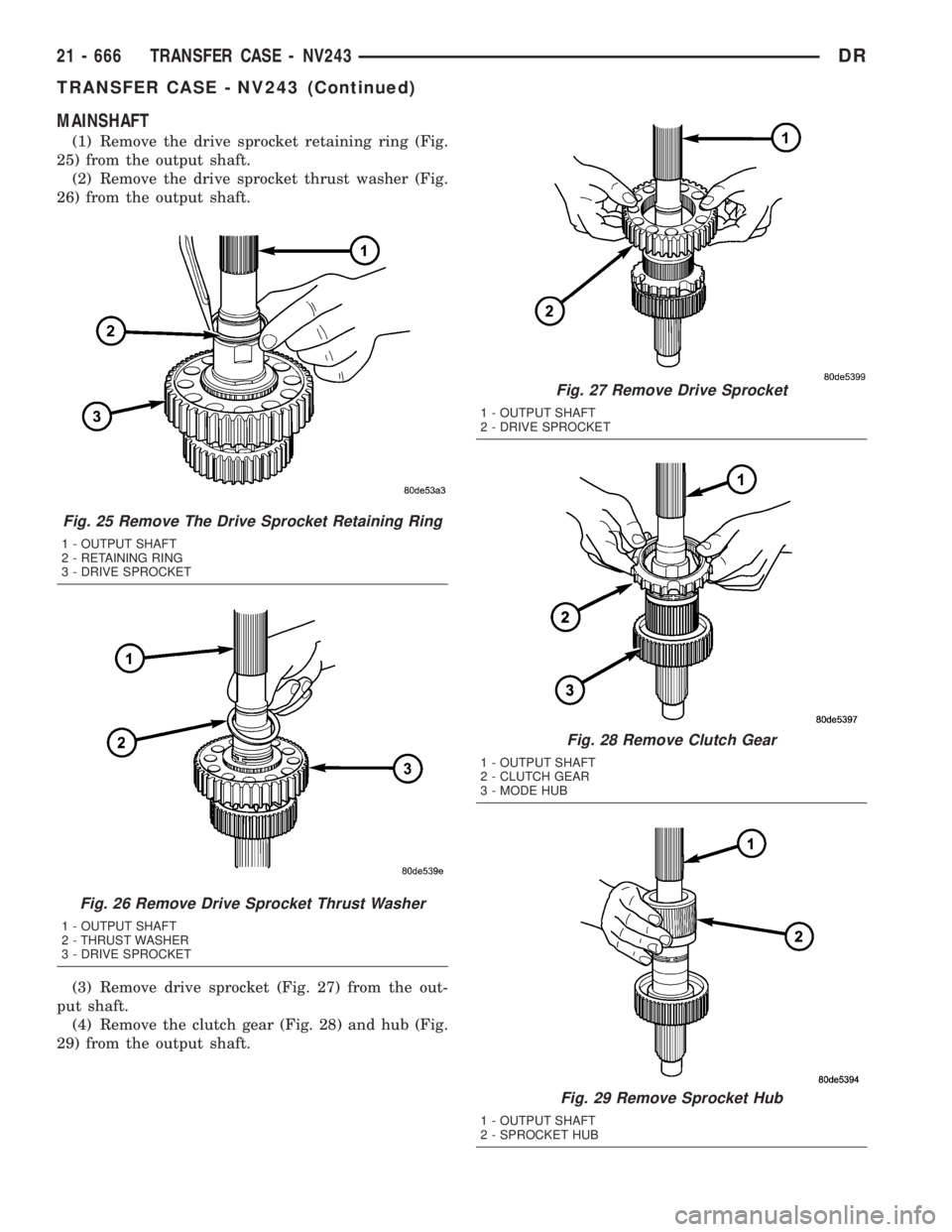
MAINSHAFT
(1) Remove the drive sprocket retaining ring (Fig.
25) from the output shaft.
(2) Remove the drive sprocket thrust washer (Fig.
26) from the output shaft.
(3) Remove drive sprocket (Fig. 27) from the out-
put shaft.
(4) Remove the clutch gear (Fig. 28) and hub (Fig.
29) from the output shaft.
Fig. 25 Remove The Drive Sprocket Retaining Ring
1 - OUTPUT SHAFT
2 - RETAINING RING
3 - DRIVE SPROCKET
Fig. 26 Remove Drive Sprocket Thrust Washer
1 - OUTPUT SHAFT
2 - THRUST WASHER
3 - DRIVE SPROCKET
Fig. 27 Remove Drive Sprocket
1 - OUTPUT SHAFT
2 - DRIVE SPROCKET
Fig. 28 Remove Clutch Gear
1 - OUTPUT SHAFT
2 - CLUTCH GEAR
3 - MODE HUB
Fig. 29 Remove Sprocket Hub
1 - OUTPUT SHAFT
2 - SPROCKET HUB
21 - 666 TRANSFER CASE - NV243DR
TRANSFER CASE - NV243 (Continued)
Page 2506 of 2895
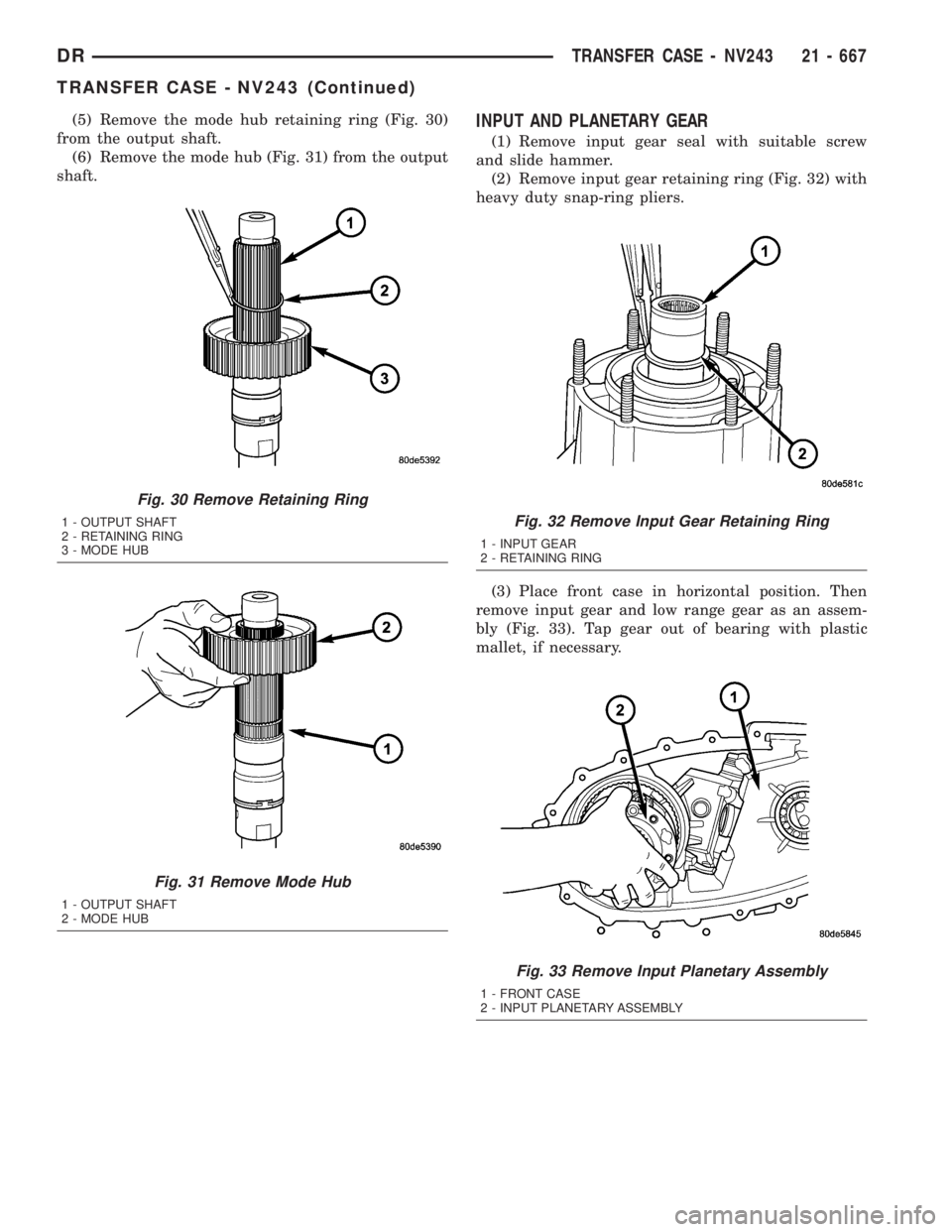
(5) Remove the mode hub retaining ring (Fig. 30)
from the output shaft.
(6) Remove the mode hub (Fig. 31) from the output
shaft.INPUT AND PLANETARY GEAR
(1) Remove input gear seal with suitable screw
and slide hammer.
(2) Remove input gear retaining ring (Fig. 32) with
heavy duty snap-ring pliers.
(3) Place front case in horizontal position. Then
remove input gear and low range gear as an assem-
bly (Fig. 33). Tap gear out of bearing with plastic
mallet, if necessary.
Fig. 30 Remove Retaining Ring
1 - OUTPUT SHAFT
2 - RETAINING RING
3 - MODE HUB
Fig. 31 Remove Mode Hub
1 - OUTPUT SHAFT
2 - MODE HUB
Fig. 32 Remove Input Gear Retaining Ring
1 - INPUT GEAR
2 - RETAINING RING
Fig. 33 Remove Input Planetary Assembly
1 - FRONT CASE
2 - INPUT PLANETARY ASSEMBLY
DRTRANSFER CASE - NV243 21 - 667
TRANSFER CASE - NV243 (Continued)
Page 2507 of 2895
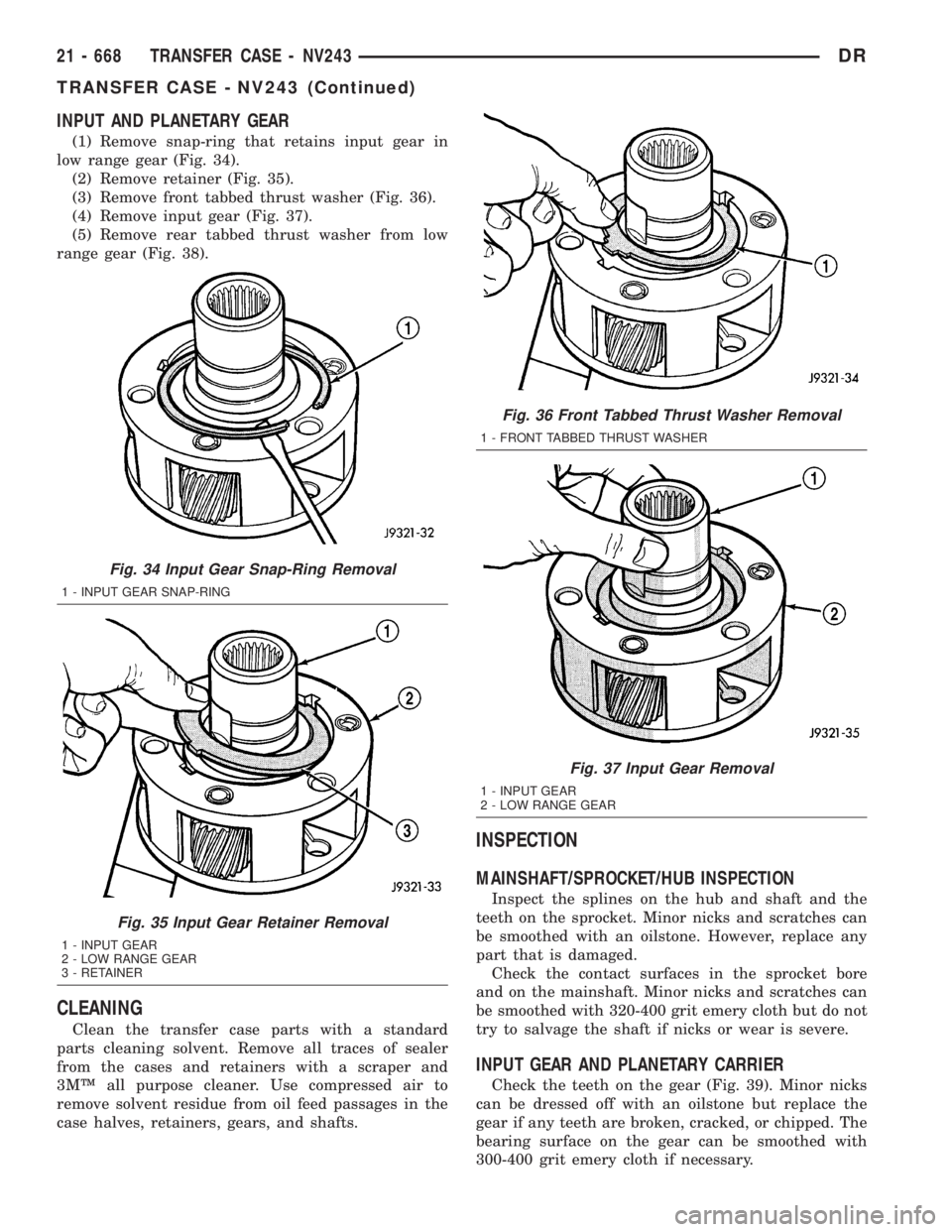
INPUT AND PLANETARY GEAR
(1) Remove snap-ring that retains input gear in
low range gear (Fig. 34).
(2) Remove retainer (Fig. 35).
(3) Remove front tabbed thrust washer (Fig. 36).
(4) Remove input gear (Fig. 37).
(5) Remove rear tabbed thrust washer from low
range gear (Fig. 38).
CLEANING
Clean the transfer case parts with a standard
parts cleaning solvent. Remove all traces of sealer
from the cases and retainers with a scraper and
3MŸ all purpose cleaner. Use compressed air to
remove solvent residue from oil feed passages in the
case halves, retainers, gears, and shafts.
INSPECTION
MAINSHAFT/SPROCKET/HUB INSPECTION
Inspect the splines on the hub and shaft and the
teeth on the sprocket. Minor nicks and scratches can
be smoothed with an oilstone. However, replace any
part that is damaged.
Check the contact surfaces in the sprocket bore
and on the mainshaft. Minor nicks and scratches can
be smoothed with 320-400 grit emery cloth but do not
try to salvage the shaft if nicks or wear is severe.
INPUT GEAR AND PLANETARY CARRIER
Check the teeth on the gear (Fig. 39). Minor nicks
can be dressed off with an oilstone but replace the
gear if any teeth are broken, cracked, or chipped. The
bearing surface on the gear can be smoothed with
300-400 grit emery cloth if necessary.
Fig. 34 Input Gear Snap-Ring Removal
1 - INPUT GEAR SNAP-RING
Fig. 35 Input Gear Retainer Removal
1 - INPUT GEAR
2 - LOW RANGE GEAR
3 - RETAINER
Fig. 36 Front Tabbed Thrust Washer Removal
1 - FRONT TABBED THRUST WASHER
Fig. 37 Input Gear Removal
1 - INPUT GEAR
2 - LOW RANGE GEAR
21 - 668 TRANSFER CASE - NV243DR
TRANSFER CASE - NV243 (Continued)
Page 2508 of 2895
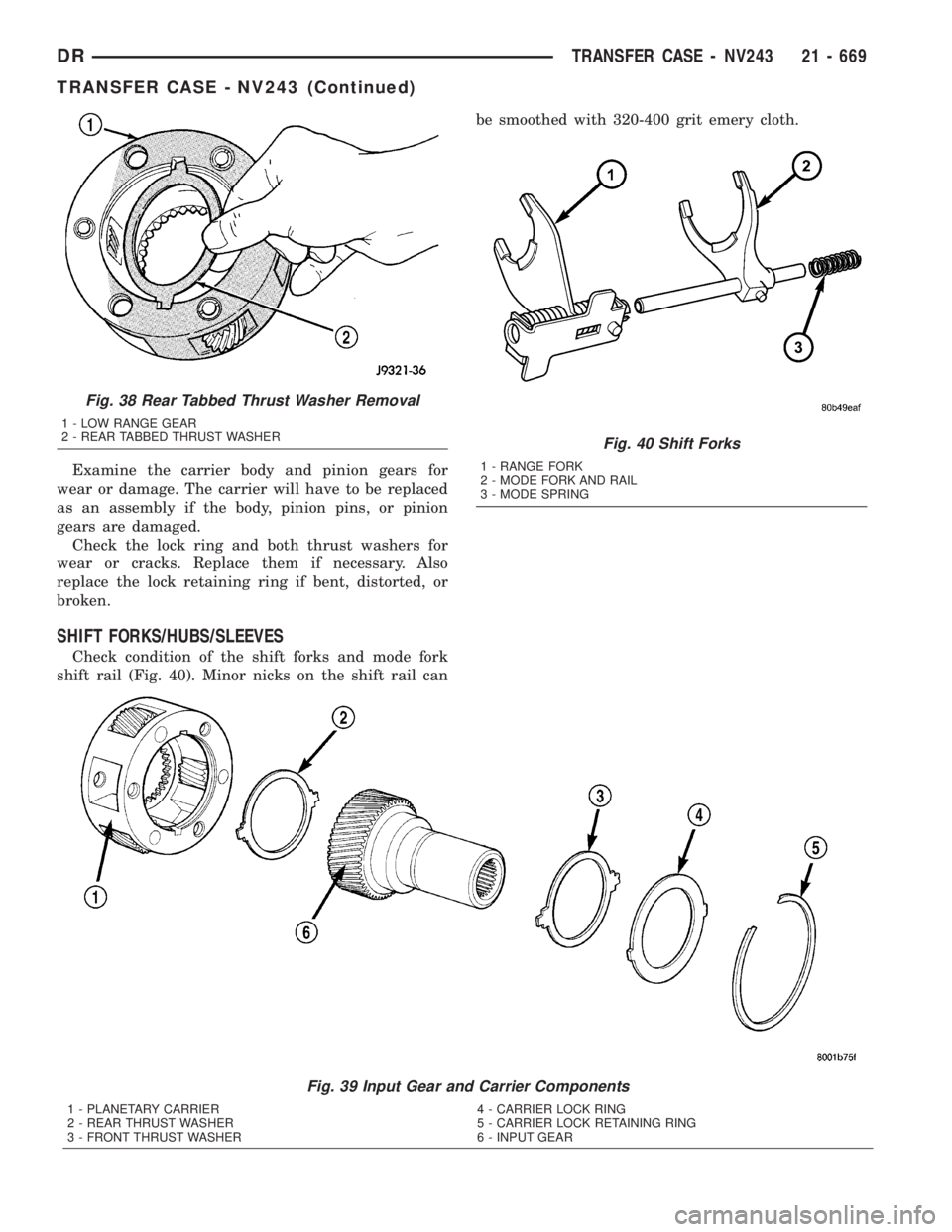
Examine the carrier body and pinion gears for
wear or damage. The carrier will have to be replaced
as an assembly if the body, pinion pins, or pinion
gears are damaged.
Check the lock ring and both thrust washers for
wear or cracks. Replace them if necessary. Also
replace the lock retaining ring if bent, distorted, or
broken.
SHIFT FORKS/HUBS/SLEEVES
Check condition of the shift forks and mode fork
shift rail (Fig. 40). Minor nicks on the shift rail canbe smoothed with 320-400 grit emery cloth.
Fig. 39 Input Gear and Carrier Components
1 - PLANETARY CARRIER 4 - CARRIER LOCK RING
2 - REAR THRUST WASHER 5 - CARRIER LOCK RETAINING RING
3 - FRONT THRUST WASHER 6 - INPUT GEAR
Fig. 38 Rear Tabbed Thrust Washer Removal
1 - LOW RANGE GEAR
2 - REAR TABBED THRUST WASHER
Fig. 40 Shift Forks
1 - RANGE FORK
2 - MODE FORK AND RAIL
3 - MODE SPRING
DRTRANSFER CASE - NV243 21 - 669
TRANSFER CASE - NV243 (Continued)
Page 2509 of 2895
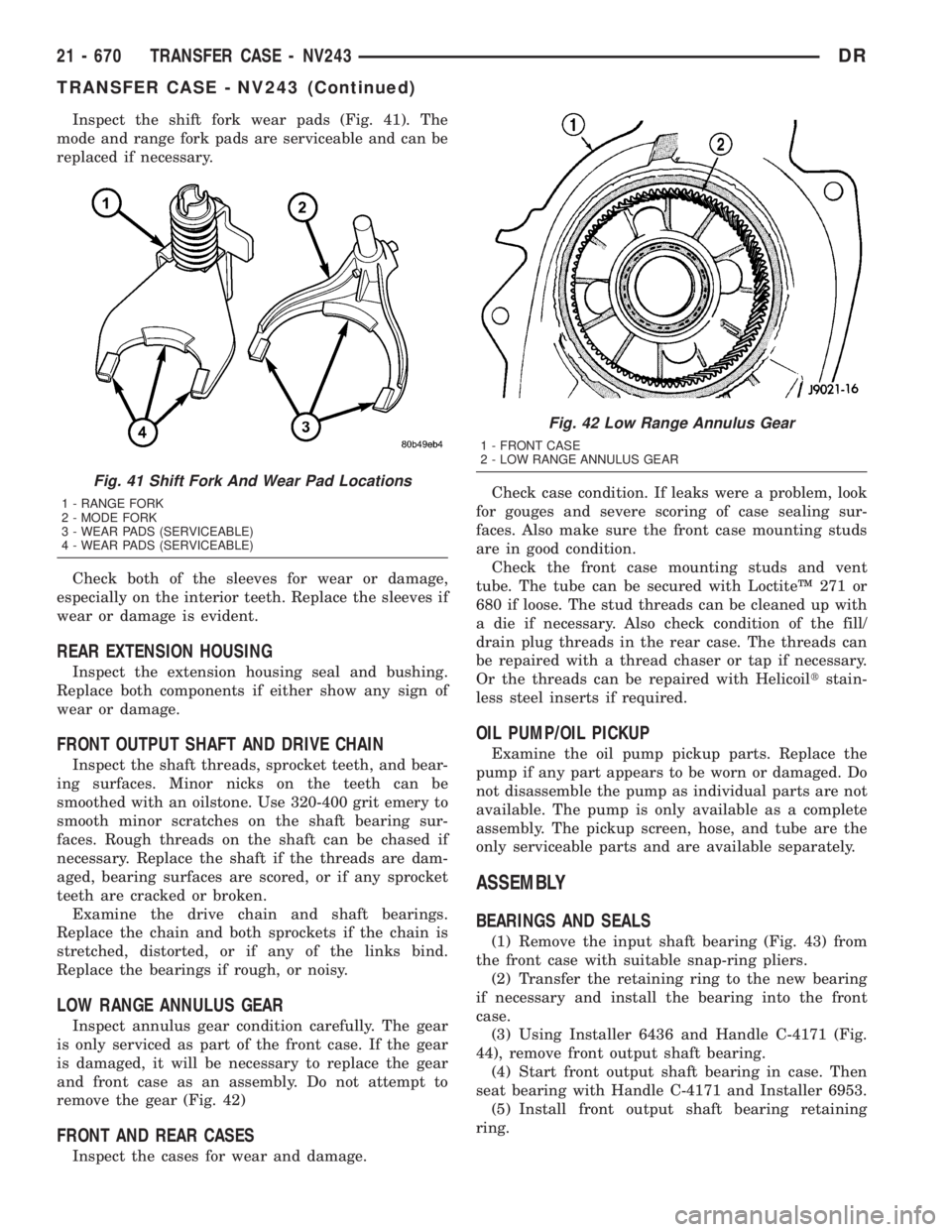
Inspect the shift fork wear pads (Fig. 41). The
mode and range fork pads are serviceable and can be
replaced if necessary.
Check both of the sleeves for wear or damage,
especially on the interior teeth. Replace the sleeves if
wear or damage is evident.
REAR EXTENSION HOUSING
Inspect the extension housing seal and bushing.
Replace both components if either show any sign of
wear or damage.
FRONT OUTPUT SHAFT AND DRIVE CHAIN
Inspect the shaft threads, sprocket teeth, and bear-
ing surfaces. Minor nicks on the teeth can be
smoothed with an oilstone. Use 320-400 grit emery to
smooth minor scratches on the shaft bearing sur-
faces. Rough threads on the shaft can be chased if
necessary. Replace the shaft if the threads are dam-
aged, bearing surfaces are scored, or if any sprocket
teeth are cracked or broken.
Examine the drive chain and shaft bearings.
Replace the chain and both sprockets if the chain is
stretched, distorted, or if any of the links bind.
Replace the bearings if rough, or noisy.
LOW RANGE ANNULUS GEAR
Inspect annulus gear condition carefully. The gear
is only serviced as part of the front case. If the gear
is damaged, it will be necessary to replace the gear
and front case as an assembly. Do not attempt to
remove the gear (Fig. 42)
FRONT AND REAR CASES
Inspect the cases for wear and damage.Check case condition. If leaks were a problem, look
for gouges and severe scoring of case sealing sur-
faces. Also make sure the front case mounting studs
are in good condition.
Check the front case mounting studs and vent
tube. The tube can be secured with LoctiteŸ 271 or
680 if loose. The stud threads can be cleaned up with
a die if necessary. Also check condition of the fill/
drain plug threads in the rear case. The threads can
be repaired with a thread chaser or tap if necessary.
Or the threads can be repaired with Helicoiltstain-
less steel inserts if required.
OIL PUMP/OIL PICKUP
Examine the oil pump pickup parts. Replace the
pump if any part appears to be worn or damaged. Do
not disassemble the pump as individual parts are not
available. The pump is only available as a complete
assembly. The pickup screen, hose, and tube are the
only serviceable parts and are available separately.
ASSEMBLY
BEARINGS AND SEALS
(1) Remove the input shaft bearing (Fig. 43) from
the front case with suitable snap-ring pliers.
(2) Transfer the retaining ring to the new bearing
if necessary and install the bearing into the front
case.
(3) Using Installer 6436 and Handle C-4171 (Fig.
44), remove front output shaft bearing.
(4) Start front output shaft bearing in case. Then
seat bearing with Handle C-4171 and Installer 6953.
(5) Install front output shaft bearing retaining
ring.
Fig. 41 Shift Fork And Wear Pad Locations
1 - RANGE FORK
2 - MODE FORK
3 - WEAR PADS (SERVICEABLE)
4 - WEAR PADS (SERVICEABLE)
Fig. 42 Low Range Annulus Gear
1 - FRONT CASE
2 - LOW RANGE ANNULUS GEAR
21 - 670 TRANSFER CASE - NV243DR
TRANSFER CASE - NV243 (Continued)
Page 2510 of 2895
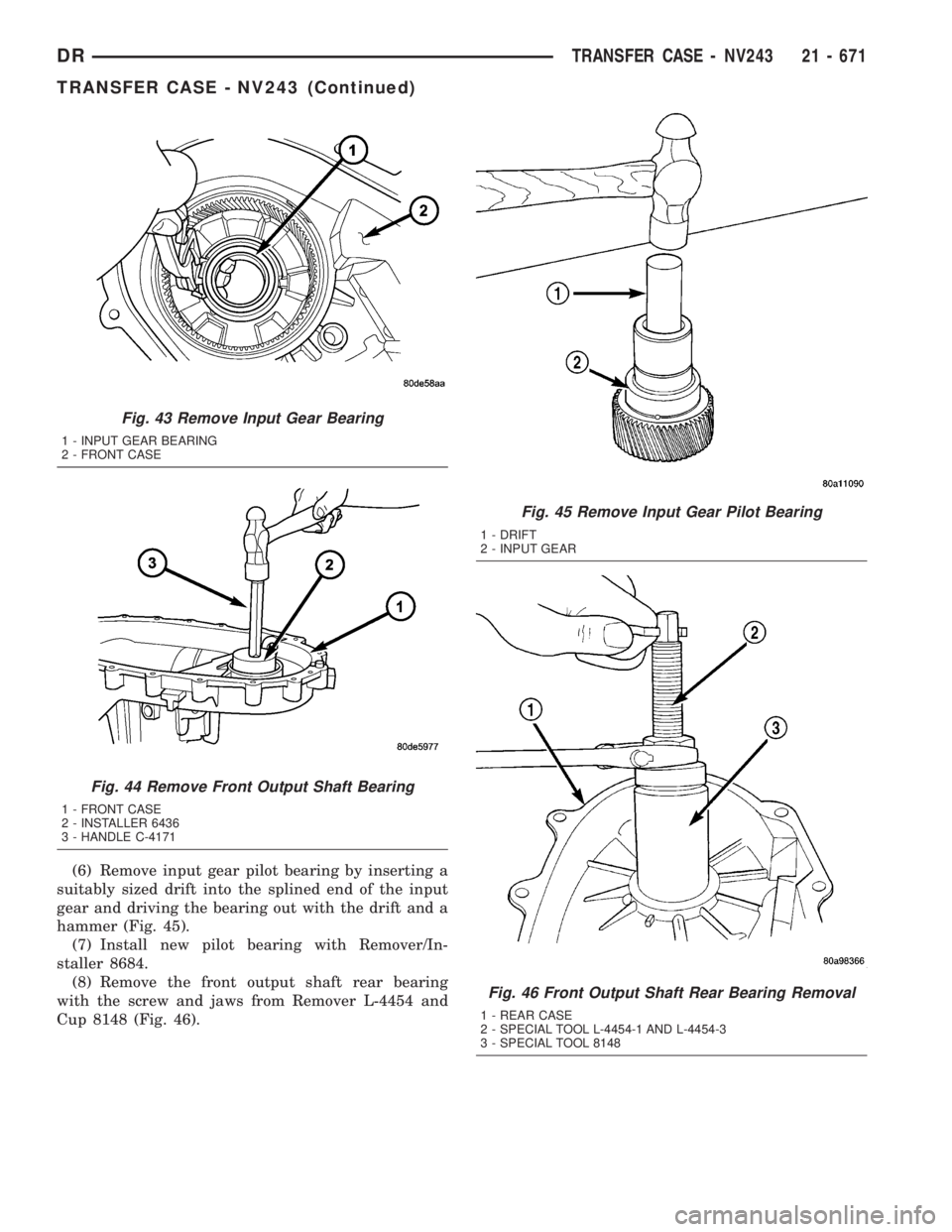
(6) Remove input gear pilot bearing by inserting a
suitably sized drift into the splined end of the input
gear and driving the bearing out with the drift and a
hammer (Fig. 45).
(7) Install new pilot bearing with Remover/In-
staller 8684.
(8) Remove the front output shaft rear bearing
with the screw and jaws from Remover L-4454 and
Cup 8148 (Fig. 46).
Fig. 46 Front Output Shaft Rear Bearing Removal
1 - REAR CASE
2 - SPECIAL TOOL L-4454-1 AND L-4454-3
3 - SPECIAL TOOL 8148
Fig. 43 Remove Input Gear Bearing
1 - INPUT GEAR BEARING
2 - FRONT CASE
Fig. 44 Remove Front Output Shaft Bearing
1 - FRONT CASE
2 - INSTALLER 6436
3 - HANDLE C-4171
Fig. 45 Remove Input Gear Pilot Bearing
1 - DRIFT
2 - INPUT GEAR
DRTRANSFER CASE - NV243 21 - 671
TRANSFER CASE - NV243 (Continued)