DODGE RAM 2003 Service Repair Manual
Manufacturer: DODGE, Model Year: 2003, Model line: RAM, Model: DODGE RAM 2003Pages: 2895, PDF Size: 83.15 MB
Page 2491 of 2895
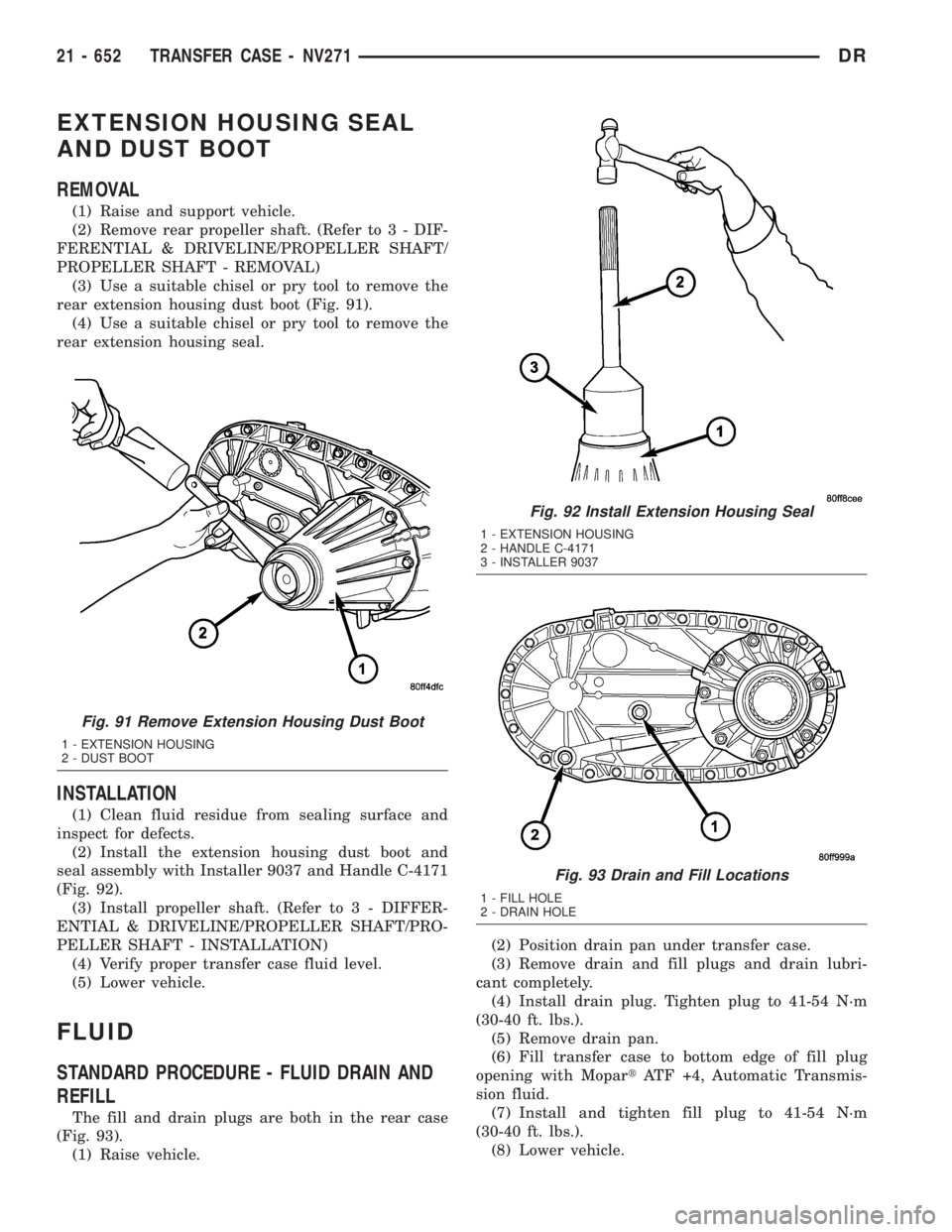
EXTENSION HOUSING SEAL
AND DUST BOOT
REMOVAL
(1) Raise and support vehicle.
(2) Remove rear propeller shaft. (Refer to 3 - DIF-
FERENTIAL & DRIVELINE/PROPELLER SHAFT/
PROPELLER SHAFT - REMOVAL)
(3) Use a suitable chisel or pry tool to remove the
rear extension housing dust boot (Fig. 91).
(4) Use a suitable chisel or pry tool to remove the
rear extension housing seal.
INSTALLATION
(1) Clean fluid residue from sealing surface and
inspect for defects.
(2) Install the extension housing dust boot and
seal assembly with Installer 9037 and Handle C-4171
(Fig. 92).
(3) Install propeller shaft. (Refer to 3 - DIFFER-
ENTIAL & DRIVELINE/PROPELLER SHAFT/PRO-
PELLER SHAFT - INSTALLATION)
(4) Verify proper transfer case fluid level.
(5) Lower vehicle.
FLUID
STANDARD PROCEDURE - FLUID DRAIN AND
REFILL
The fill and drain plugs are both in the rear case
(Fig. 93).
(1) Raise vehicle.(2) Position drain pan under transfer case.
(3) Remove drain and fill plugs and drain lubri-
cant completely.
(4) Install drain plug. Tighten plug to 41-54 N´m
(30-40 ft. lbs.).
(5) Remove drain pan.
(6) Fill transfer case to bottom edge of fill plug
opening with MopartATF +4, Automatic Transmis-
sion fluid.
(7) Install and tighten fill plug to 41-54 N´m
(30-40 ft. lbs.).
(8) Lower vehicle.
Fig. 91 Remove Extension Housing Dust Boot
1 - EXTENSION HOUSING
2 - DUST BOOT
Fig. 92 Install Extension Housing Seal
1 - EXTENSION HOUSING
2 - HANDLE C-4171
3 - INSTALLER 9037
Fig. 93 Drain and Fill Locations
1 - FILL HOLE
2 - DRAIN HOLE
21 - 652 TRANSFER CASE - NV271DR
Page 2492 of 2895
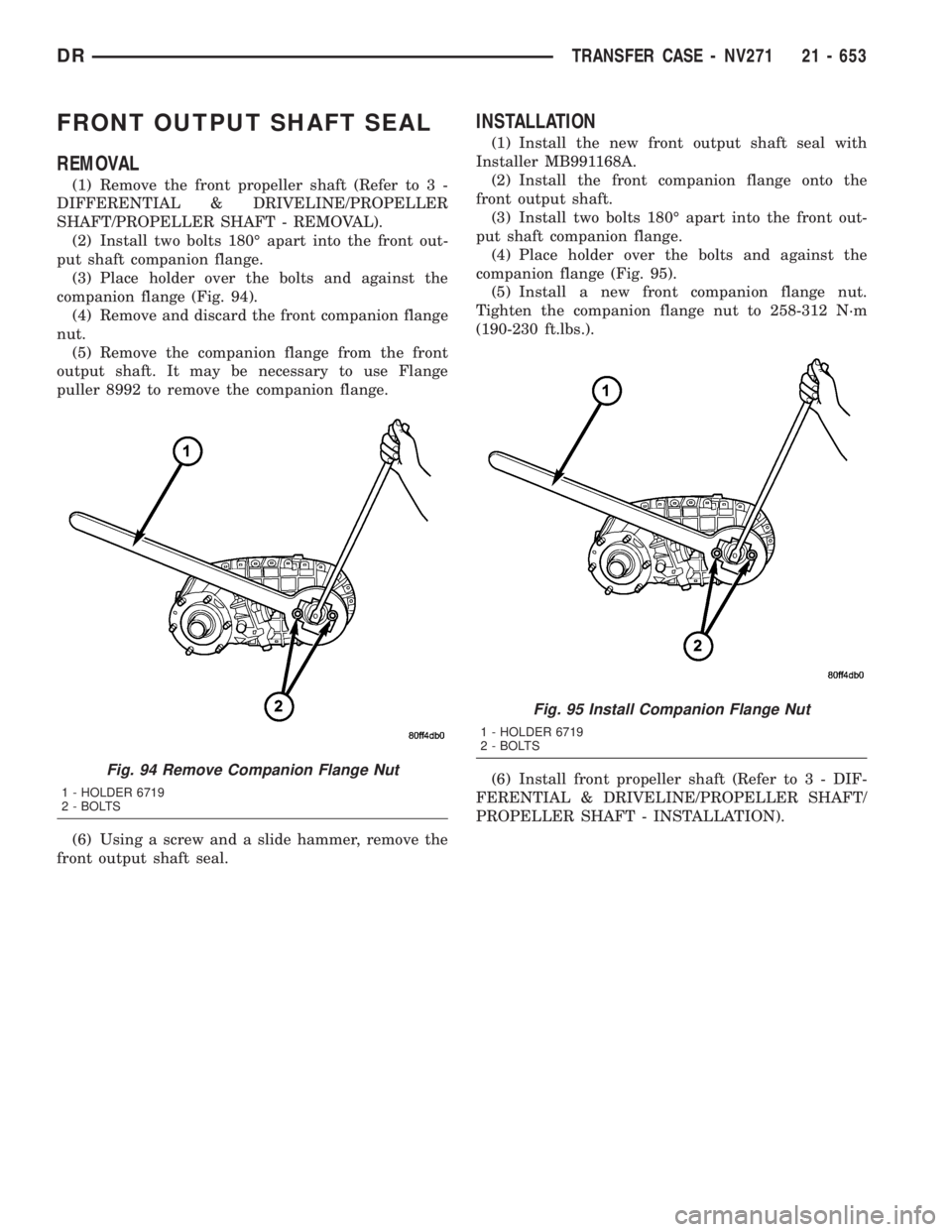
FRONT OUTPUT SHAFT SEAL
REMOVAL
(1) Remove the front propeller shaft (Refer to 3 -
DIFFERENTIAL & DRIVELINE/PROPELLER
SHAFT/PROPELLER SHAFT - REMOVAL).
(2) Install two bolts 180É apart into the front out-
put shaft companion flange.
(3) Place holder over the bolts and against the
companion flange (Fig. 94).
(4) Remove and discard the front companion flange
nut.
(5) Remove the companion flange from the front
output shaft. It may be necessary to use Flange
puller 8992 to remove the companion flange.
(6) Using a screw and a slide hammer, remove the
front output shaft seal.
INSTALLATION
(1) Install the new front output shaft seal with
Installer MB991168A.
(2) Install the front companion flange onto the
front output shaft.
(3) Install two bolts 180É apart into the front out-
put shaft companion flange.
(4) Place holder over the bolts and against the
companion flange (Fig. 95).
(5) Install a new front companion flange nut.
Tighten the companion flange nut to 258-312 N´m
(190-230 ft.lbs.).
(6) Install front propeller shaft (Refer to 3 - DIF-
FERENTIAL & DRIVELINE/PROPELLER SHAFT/
PROPELLER SHAFT - INSTALLATION).
Fig. 94 Remove Companion Flange Nut
1 - HOLDER 6719
2 - BOLTS
Fig. 95 Install Companion Flange Nut
1 - HOLDER 6719
2 - BOLTS
DRTRANSFER CASE - NV271 21 - 653
Page 2493 of 2895
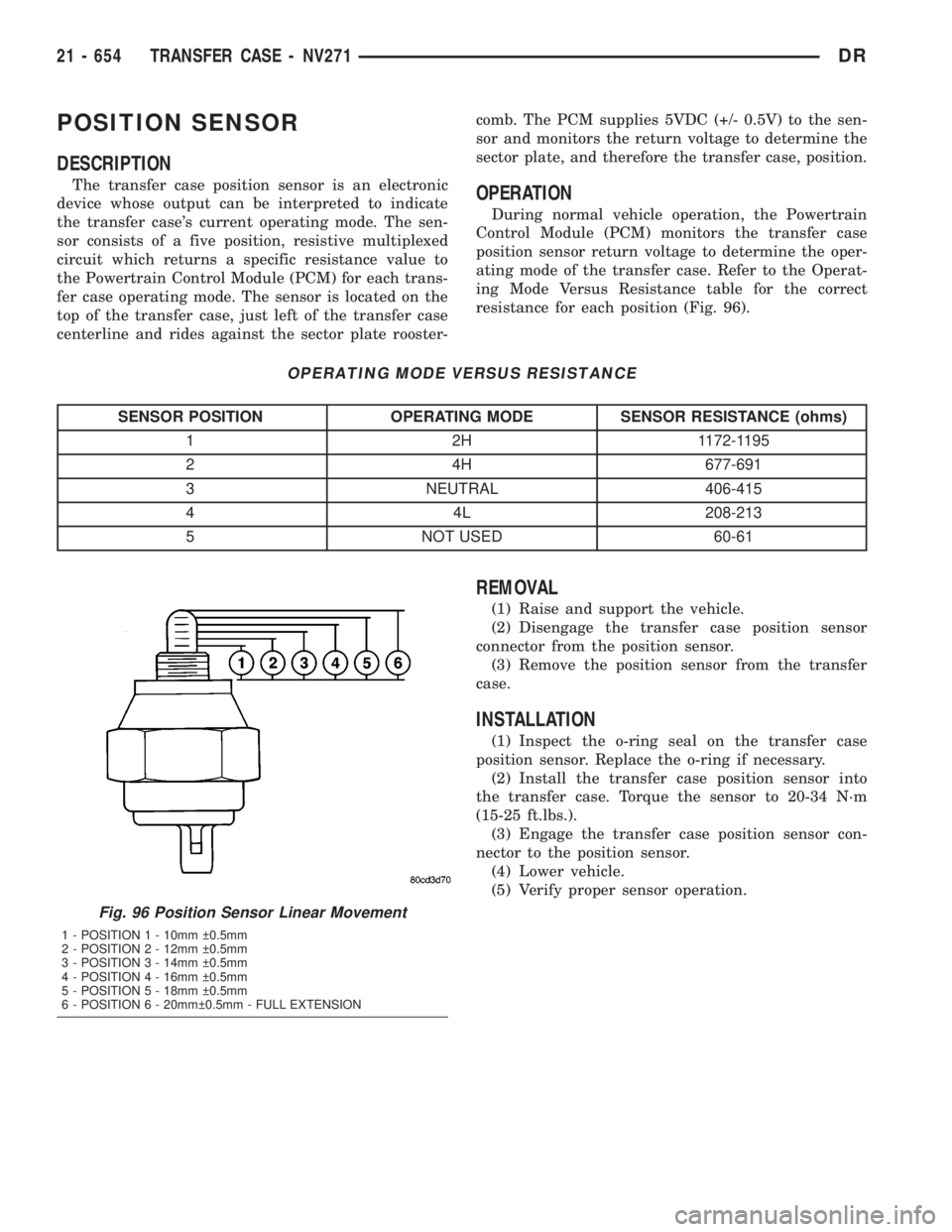
POSITION SENSOR
DESCRIPTION
The transfer case position sensor is an electronic
device whose output can be interpreted to indicate
the transfer case's current operating mode. The sen-
sor consists of a five position, resistive multiplexed
circuit which returns a specific resistance value to
the Powertrain Control Module (PCM) for each trans-
fer case operating mode. The sensor is located on the
top of the transfer case, just left of the transfer case
centerline and rides against the sector plate rooster-comb. The PCM supplies 5VDC (+/- 0.5V) to the sen-
sor and monitors the return voltage to determine the
sector plate, and therefore the transfer case, position.OPERATION
During normal vehicle operation, the Powertrain
Control Module (PCM) monitors the transfer case
position sensor return voltage to determine the oper-
ating mode of the transfer case. Refer to the Operat-
ing Mode Versus Resistance table for the correct
resistance for each position (Fig. 96).
OPERATING MODE VERSUS RESISTANCE
SENSOR POSITION OPERATING MODE SENSOR RESISTANCE (ohms)
1 2H 1172-1195
2 4H 677-691
3 NEUTRAL 406-415
4 4L 208-213
5 NOT USED 60-61
REMOVAL
(1) Raise and support the vehicle.
(2) Disengage the transfer case position sensor
connector from the position sensor.
(3) Remove the position sensor from the transfer
case.
INSTALLATION
(1) Inspect the o-ring seal on the transfer case
position sensor. Replace the o-ring if necessary.
(2) Install the transfer case position sensor into
the transfer case. Torque the sensor to 20-34 N´m
(15-25 ft.lbs.).
(3) Engage the transfer case position sensor con-
nector to the position sensor.
(4) Lower vehicle.
(5) Verify proper sensor operation.
Fig. 96 Position Sensor Linear Movement
1 - POSITION 1 - 10mm 0.5mm
2 - POSITION 2 - 12mm 0.5mm
3 - POSITION 3 - 14mm 0.5mm
4 - POSITION 4 - 16mm 0.5mm
5 - POSITION 5 - 18mm 0.5mm
6 - POSITION 6 - 20mm 0.5mm - FULL EXTENSION
21 - 654 TRANSFER CASE - NV271DR
Page 2494 of 2895
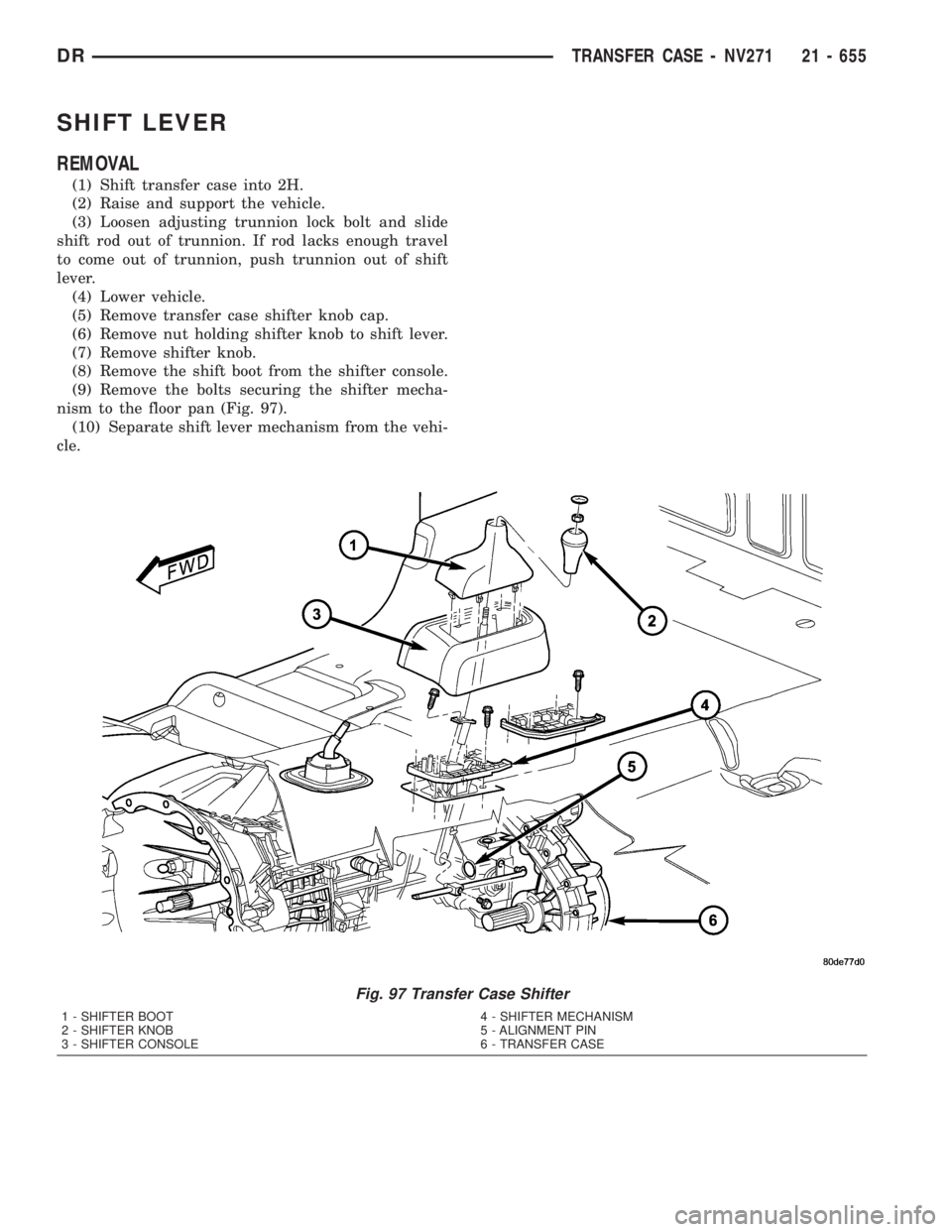
SHIFT LEVER
REMOVAL
(1) Shift transfer case into 2H.
(2) Raise and support the vehicle.
(3) Loosen adjusting trunnion lock bolt and slide
shift rod out of trunnion. If rod lacks enough travel
to come out of trunnion, push trunnion out of shift
lever.
(4) Lower vehicle.
(5) Remove transfer case shifter knob cap.
(6) Remove nut holding shifter knob to shift lever.
(7) Remove shifter knob.
(8) Remove the shift boot from the shifter console.
(9) Remove the bolts securing the shifter mecha-
nism to the floor pan (Fig. 97).
(10) Separate shift lever mechanism from the vehi-
cle.
Fig. 97 Transfer Case Shifter
1 - SHIFTER BOOT
2 - SHIFTER KNOB
3 - SHIFTER CONSOLE4 - SHIFTER MECHANISM
5 - ALIGNMENT PIN
6 - TRANSFER CASE
DRTRANSFER CASE - NV271 21 - 655
Page 2495 of 2895
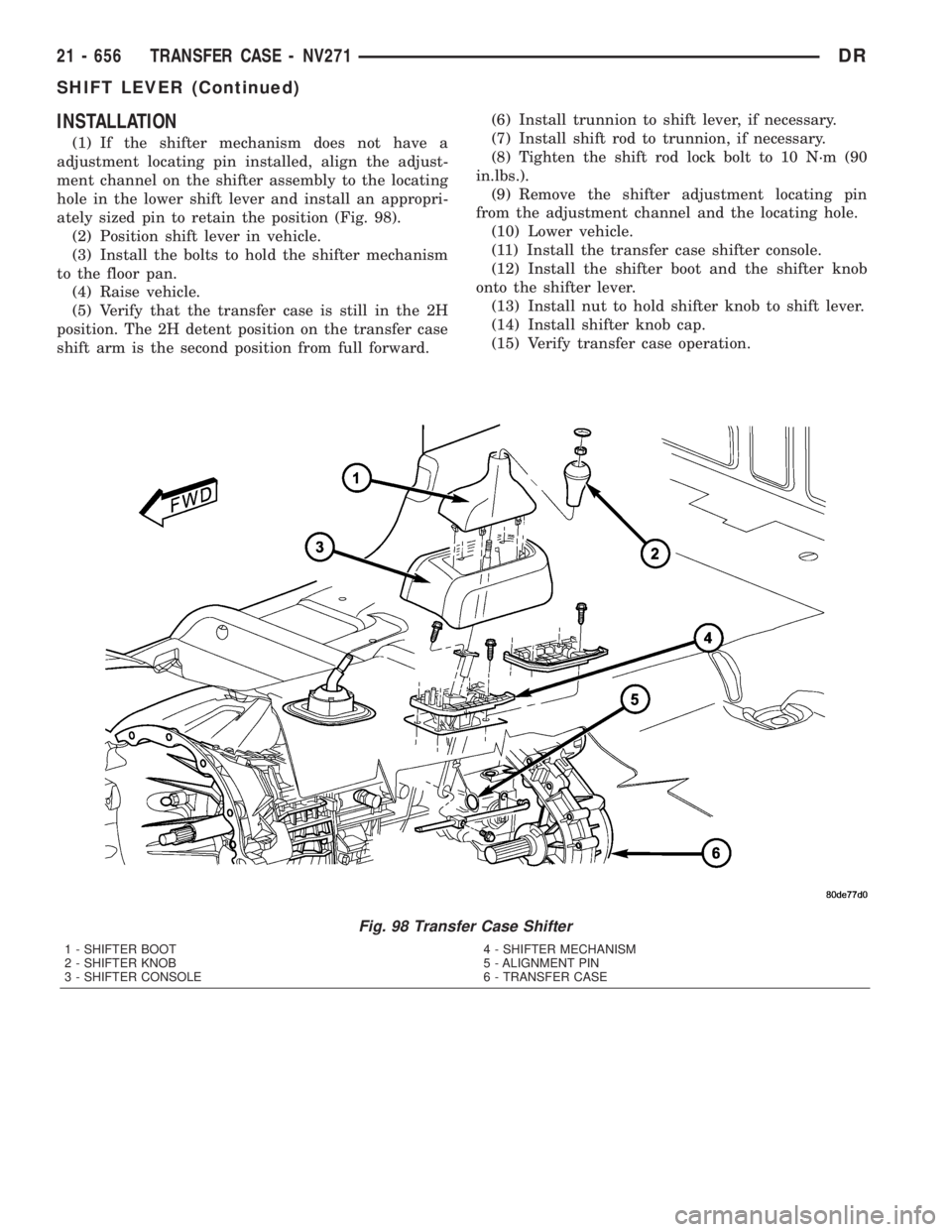
INSTALLATION
(1) If the shifter mechanism does not have a
adjustment locating pin installed, align the adjust-
ment channel on the shifter assembly to the locating
hole in the lower shift lever and install an appropri-
ately sized pin to retain the position (Fig. 98).
(2) Position shift lever in vehicle.
(3) Install the bolts to hold the shifter mechanism
to the floor pan.
(4) Raise vehicle.
(5) Verify that the transfer case is still in the 2H
position. The 2H detent position on the transfer case
shift arm is the second position from full forward.(6) Install trunnion to shift lever, if necessary.
(7) Install shift rod to trunnion, if necessary.
(8) Tighten the shift rod lock bolt to 10 N´m (90
in.lbs.).
(9) Remove the shifter adjustment locating pin
from the adjustment channel and the locating hole.
(10) Lower vehicle.
(11) Install the transfer case shifter console.
(12) Install the shifter boot and the shifter knob
onto the shifter lever.
(13) Install nut to hold shifter knob to shift lever.
(14) Install shifter knob cap.
(15) Verify transfer case operation.
Fig. 98 Transfer Case Shifter
1 - SHIFTER BOOT
2 - SHIFTER KNOB
3 - SHIFTER CONSOLE4 - SHIFTER MECHANISM
5 - ALIGNMENT PIN
6 - TRANSFER CASE
21 - 656 TRANSFER CASE - NV271DR
SHIFT LEVER (Continued)
Page 2496 of 2895
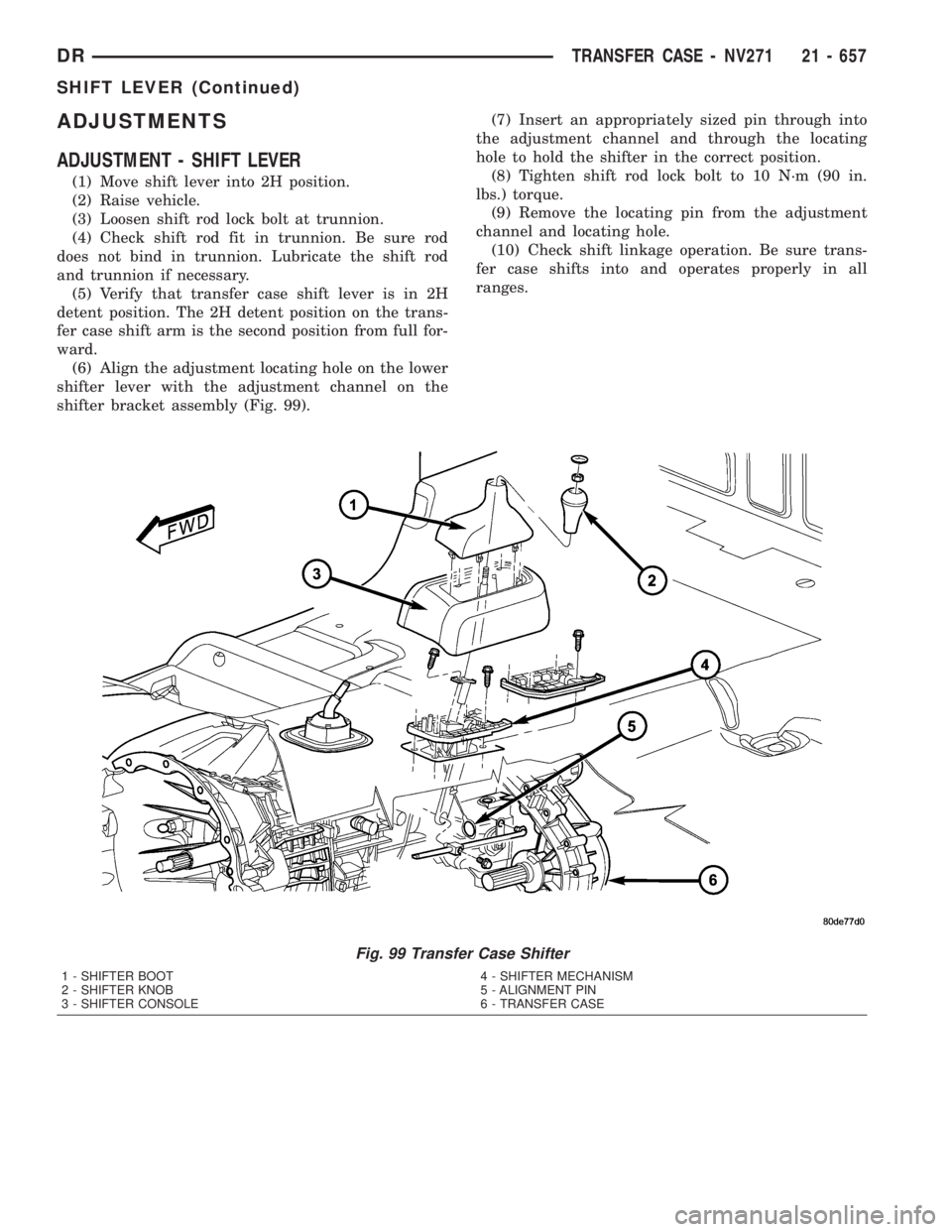
ADJUSTMENTS
ADJUSTMENT - SHIFT LEVER
(1) Move shift lever into 2H position.
(2) Raise vehicle.
(3) Loosen shift rod lock bolt at trunnion.
(4) Check shift rod fit in trunnion. Be sure rod
does not bind in trunnion. Lubricate the shift rod
and trunnion if necessary.
(5) Verify that transfer case shift lever is in 2H
detent position. The 2H detent position on the trans-
fer case shift arm is the second position from full for-
ward.
(6) Align the adjustment locating hole on the lower
shifter lever with the adjustment channel on the
shifter bracket assembly (Fig. 99).(7) Insert an appropriately sized pin through into
the adjustment channel and through the locating
hole to hold the shifter in the correct position.
(8) Tighten shift rod lock bolt to 10 N´m (90 in.
lbs.) torque.
(9) Remove the locating pin from the adjustment
channel and locating hole.
(10) Check shift linkage operation. Be sure trans-
fer case shifts into and operates properly in all
ranges.
Fig. 99 Transfer Case Shifter
1 - SHIFTER BOOT
2 - SHIFTER KNOB
3 - SHIFTER CONSOLE4 - SHIFTER MECHANISM
5 - ALIGNMENT PIN
6 - TRANSFER CASE
DRTRANSFER CASE - NV271 21 - 657
SHIFT LEVER (Continued)
Page 2497 of 2895
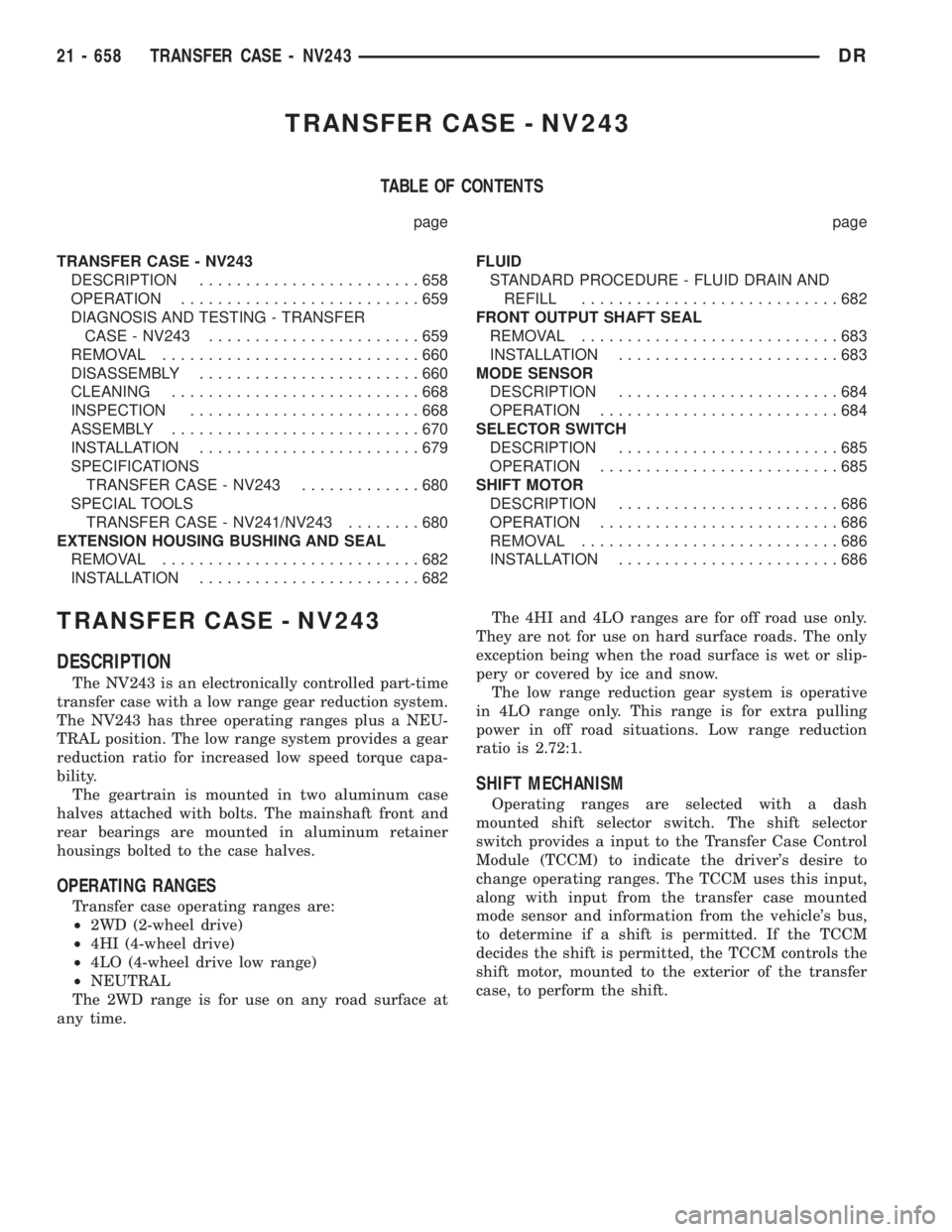
TRANSFER CASE - NV243
TABLE OF CONTENTS
page page
TRANSFER CASE - NV243
DESCRIPTION........................658
OPERATION..........................659
DIAGNOSIS AND TESTING - TRANSFER
CASE - NV243.......................659
REMOVAL............................660
DISASSEMBLY........................660
CLEANING...........................668
INSPECTION.........................668
ASSEMBLY...........................670
INSTALLATION........................679
SPECIFICATIONS
TRANSFER CASE - NV243.............680
SPECIAL TOOLS
TRANSFER CASE - NV241/NV243........680
EXTENSION HOUSING BUSHING AND SEAL
REMOVAL............................682
INSTALLATION........................682FLUID
STANDARD PROCEDURE - FLUID DRAIN AND
REFILL............................682
FRONT OUTPUT SHAFT SEAL
REMOVAL............................683
INSTALLATION........................683
MODE SENSOR
DESCRIPTION........................684
OPERATION..........................684
SELECTOR SWITCH
DESCRIPTION........................685
OPERATION..........................685
SHIFT MOTOR
DESCRIPTION........................686
OPERATION..........................686
REMOVAL............................686
INSTALLATION........................686
TRANSFER CASE - NV243
DESCRIPTION
The NV243 is an electronically controlled part-time
transfer case with a low range gear reduction system.
The NV243 has three operating ranges plus a NEU-
TRAL position. The low range system provides a gear
reduction ratio for increased low speed torque capa-
bility.
The geartrain is mounted in two aluminum case
halves attached with bolts. The mainshaft front and
rear bearings are mounted in aluminum retainer
housings bolted to the case halves.
OPERATING RANGES
Transfer case operating ranges are:
²2WD (2-wheel drive)
²4HI (4-wheel drive)
²4LO (4-wheel drive low range)
²NEUTRAL
The 2WD range is for use on any road surface at
any time.The 4HI and 4LO ranges are for off road use only.
They are not for use on hard surface roads. The only
exception being when the road surface is wet or slip-
pery or covered by ice and snow.
The low range reduction gear system is operative
in 4LO range only. This range is for extra pulling
power in off road situations. Low range reduction
ratio is 2.72:1.
SHIFT MECHANISM
Operating ranges are selected with a dash
mounted shift selector switch. The shift selector
switch provides a input to the Transfer Case Control
Module (TCCM) to indicate the driver's desire to
change operating ranges. The TCCM uses this input,
along with input from the transfer case mounted
mode sensor and information from the vehicle's bus,
to determine if a shift is permitted. If the TCCM
decides the shift is permitted, the TCCM controls the
shift motor, mounted to the exterior of the transfer
case, to perform the shift.
21 - 658 TRANSFER CASE - NV243DR
Page 2498 of 2895
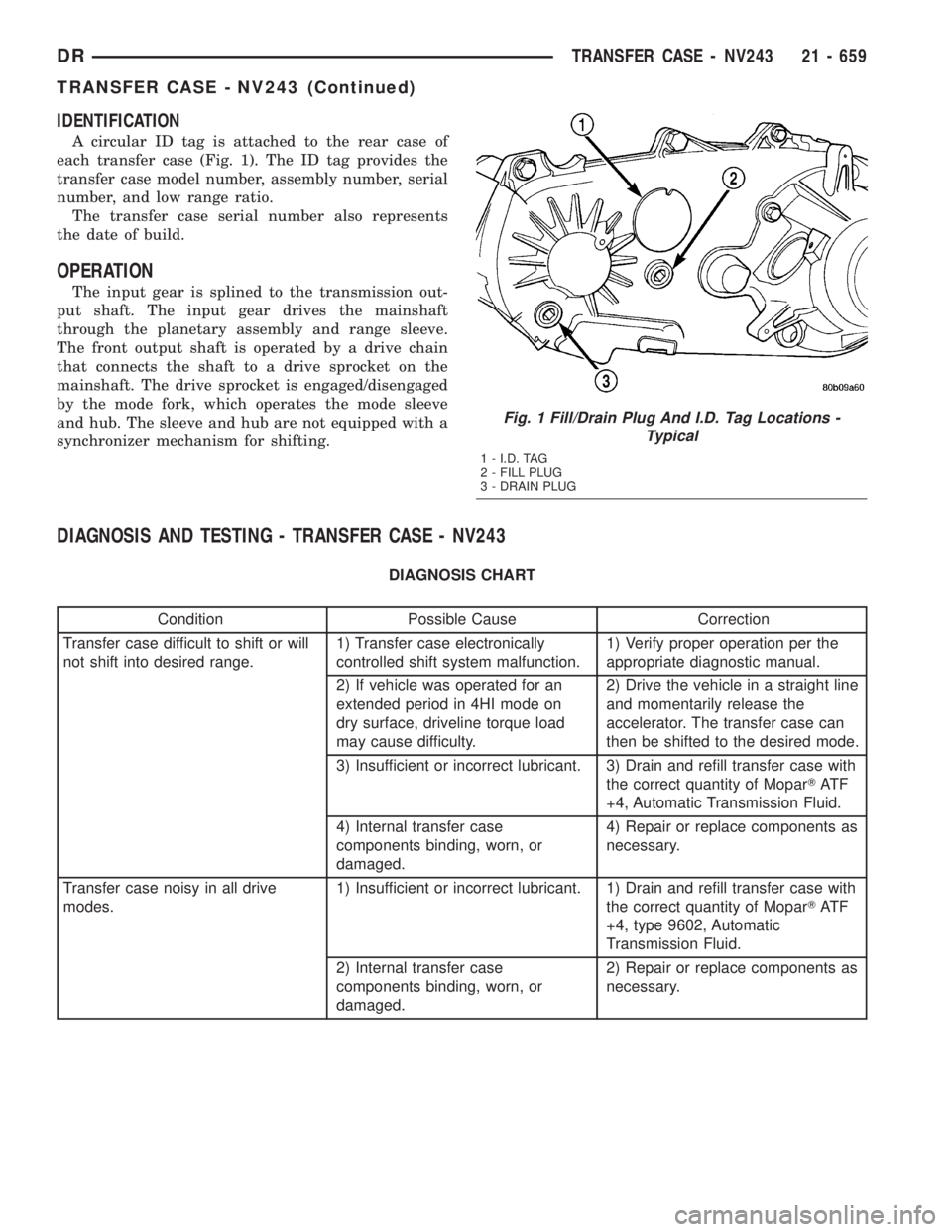
IDENTIFICATION
A circular ID tag is attached to the rear case of
each transfer case (Fig. 1). The ID tag provides the
transfer case model number, assembly number, serial
number, and low range ratio.
The transfer case serial number also represents
the date of build.
OPERATION
The input gear is splined to the transmission out-
put shaft. The input gear drives the mainshaft
through the planetary assembly and range sleeve.
The front output shaft is operated by a drive chain
that connects the shaft to a drive sprocket on the
mainshaft. The drive sprocket is engaged/disengaged
by the mode fork, which operates the mode sleeve
and hub. The sleeve and hub are not equipped with a
synchronizer mechanism for shifting.
DIAGNOSIS AND TESTING - TRANSFER CASE - NV243
DIAGNOSIS CHART
Condition Possible Cause Correction
Transfer case difficult to shift or will
not shift into desired range.1) Transfer case electronically
controlled shift system malfunction.1) Verify proper operation per the
appropriate diagnostic manual.
2) If vehicle was operated for an
extended period in 4HI mode on
dry surface, driveline torque load
may cause difficulty.2) Drive the vehicle in a straight line
and momentarily release the
accelerator. The transfer case can
then be shifted to the desired mode.
3) Insufficient or incorrect lubricant. 3) Drain and refill transfer case with
the correct quantity of MoparTAT F
+4, Automatic Transmission Fluid.
4) Internal transfer case
components binding, worn, or
damaged.4) Repair or replace components as
necessary.
Transfer case noisy in all drive
modes.1) Insufficient or incorrect lubricant. 1) Drain and refill transfer case with
the correct quantity of MoparTAT F
+4, type 9602, Automatic
Transmission Fluid.
2) Internal transfer case
components binding, worn, or
damaged.2) Repair or replace components as
necessary.
Fig. 1 Fill/Drain Plug And I.D. Tag Locations -
Typical
1 - I.D. TAG
2 - FILL PLUG
3 - DRAIN PLUG
DRTRANSFER CASE - NV243 21 - 659
TRANSFER CASE - NV243 (Continued)
Page 2499 of 2895
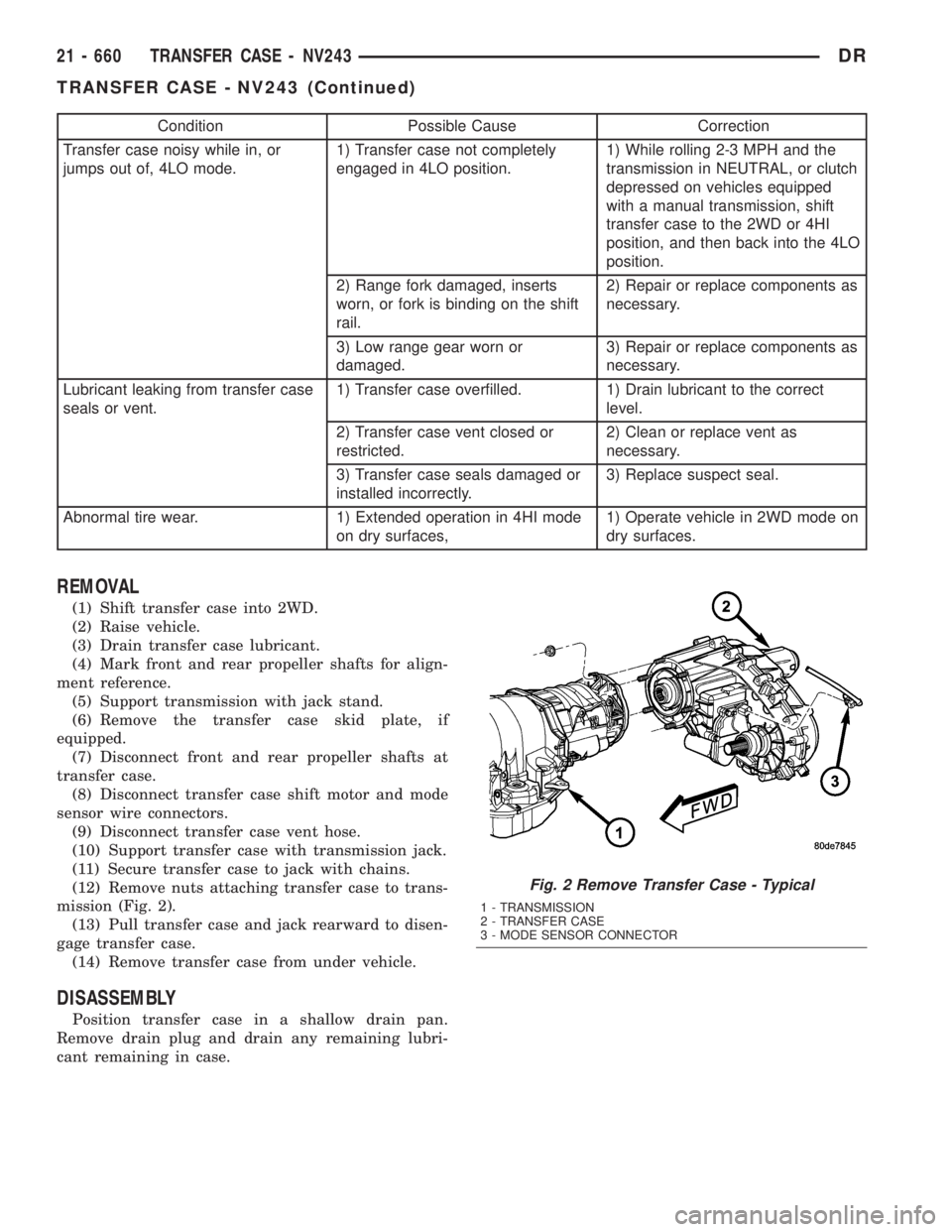
Condition Possible Cause Correction
Transfer case noisy while in, or
jumps out of, 4LO mode.1) Transfer case not completely
engaged in 4LO position.1) While rolling 2-3 MPH and the
transmission in NEUTRAL, or clutch
depressed on vehicles equipped
with a manual transmission, shift
transfer case to the 2WD or 4HI
position, and then back into the 4LO
position.
2) Range fork damaged, inserts
worn, or fork is binding on the shift
rail.2) Repair or replace components as
necessary.
3) Low range gear worn or
damaged.3) Repair or replace components as
necessary.
Lubricant leaking from transfer case
seals or vent.1) Transfer case overfilled. 1) Drain lubricant to the correct
level.
2) Transfer case vent closed or
restricted.2) Clean or replace vent as
necessary.
3) Transfer case seals damaged or
installed incorrectly.3) Replace suspect seal.
Abnormal tire wear. 1) Extended operation in 4HI mode
on dry surfaces,1) Operate vehicle in 2WD mode on
dry surfaces.
REMOVAL
(1) Shift transfer case into 2WD.
(2) Raise vehicle.
(3) Drain transfer case lubricant.
(4) Mark front and rear propeller shafts for align-
ment reference.
(5) Support transmission with jack stand.
(6) Remove the transfer case skid plate, if
equipped.
(7) Disconnect front and rear propeller shafts at
transfer case.
(8) Disconnect transfer case shift motor and mode
sensor wire connectors.
(9) Disconnect transfer case vent hose.
(10) Support transfer case with transmission jack.
(11) Secure transfer case to jack with chains.
(12) Remove nuts attaching transfer case to trans-
mission (Fig. 2).
(13) Pull transfer case and jack rearward to disen-
gage transfer case.
(14) Remove transfer case from under vehicle.
DISASSEMBLY
Position transfer case in a shallow drain pan.
Remove drain plug and drain any remaining lubri-
cant remaining in case.
Fig. 2 Remove Transfer Case - Typical
1 - TRANSMISSION
2 - TRANSFER CASE
3 - MODE SENSOR CONNECTOR
21 - 660 TRANSFER CASE - NV243DR
TRANSFER CASE - NV243 (Continued)
Page 2500 of 2895
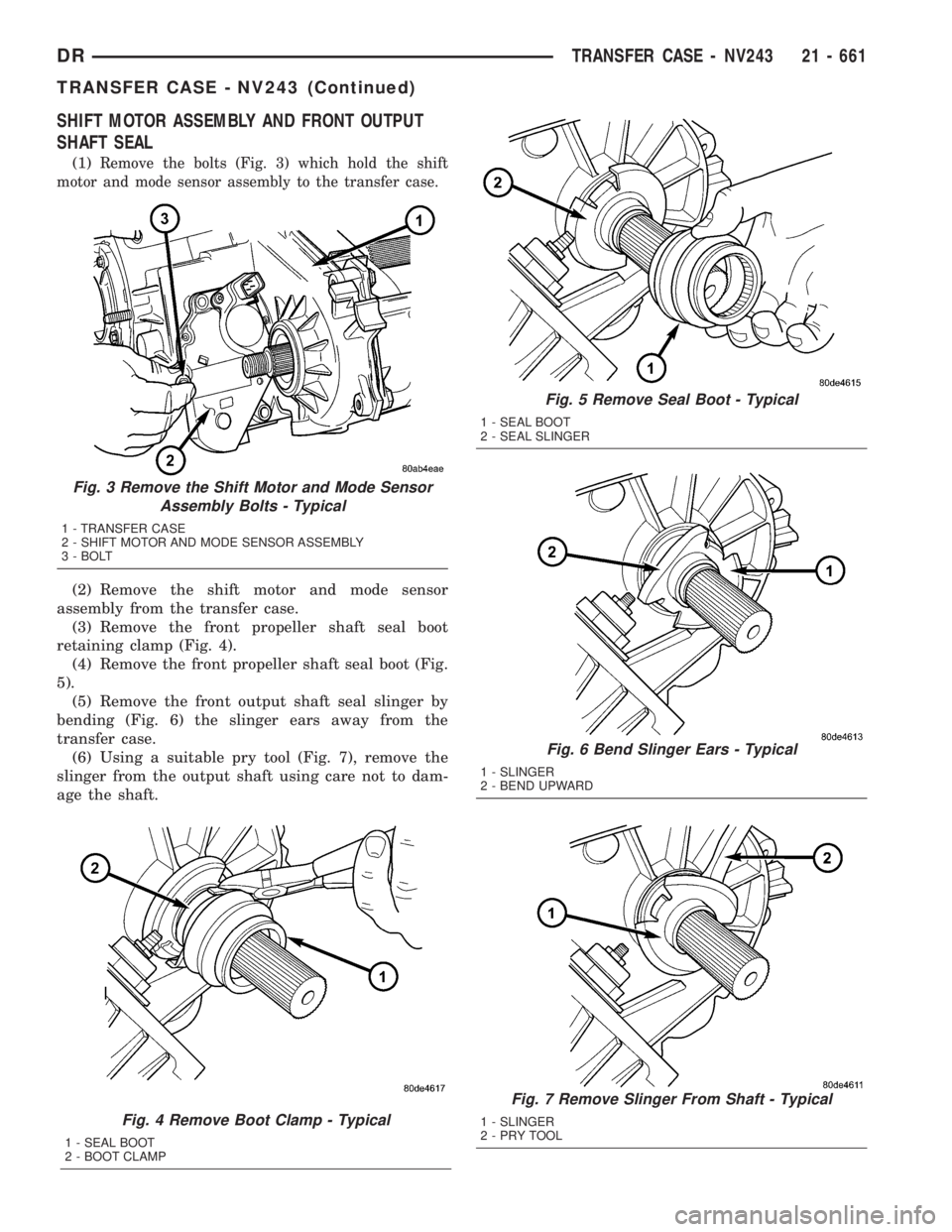
SHIFT MOTOR ASSEMBLY AND FRONT OUTPUT
SHAFT SEAL
(1)Remove the bolts (Fig. 3) which hold the shift
motor and mode sensor assembly to the transfer case.
(2) Remove the shift motor and mode sensor
assembly from the transfer case.
(3) Remove the front propeller shaft seal boot
retaining clamp (Fig. 4).
(4) Remove the front propeller shaft seal boot (Fig.
5).
(5) Remove the front output shaft seal slinger by
bending (Fig. 6) the slinger ears away from the
transfer case.
(6) Using a suitable pry tool (Fig. 7), remove the
slinger from the output shaft using care not to dam-
age the shaft.
Fig. 4 Remove Boot Clamp - Typical
1 - SEAL BOOT
2 - BOOT CLAMP
Fig. 3 Remove the Shift Motor and Mode Sensor
Assembly Bolts - Typical
1 - TRANSFER CASE
2 - SHIFT MOTOR AND MODE SENSOR ASSEMBLY
3 - BOLT
Fig. 5 Remove Seal Boot - Typical
1 - SEAL BOOT
2 - SEAL SLINGER
Fig. 6 Bend Slinger Ears - Typical
1 - SLINGER
2 - BEND UPWARD
Fig. 7 Remove Slinger From Shaft - Typical
1 - SLINGER
2-PRYTOOL
DRTRANSFER CASE - NV243 21 - 661
TRANSFER CASE - NV243 (Continued)