DODGE TRUCK 1993 Service Repair Manual
Manufacturer: DODGE, Model Year: 1993, Model line: TRUCK, Model: DODGE TRUCK 1993Pages: 1502, PDF Size: 80.97 MB
Page 1251 of 1502
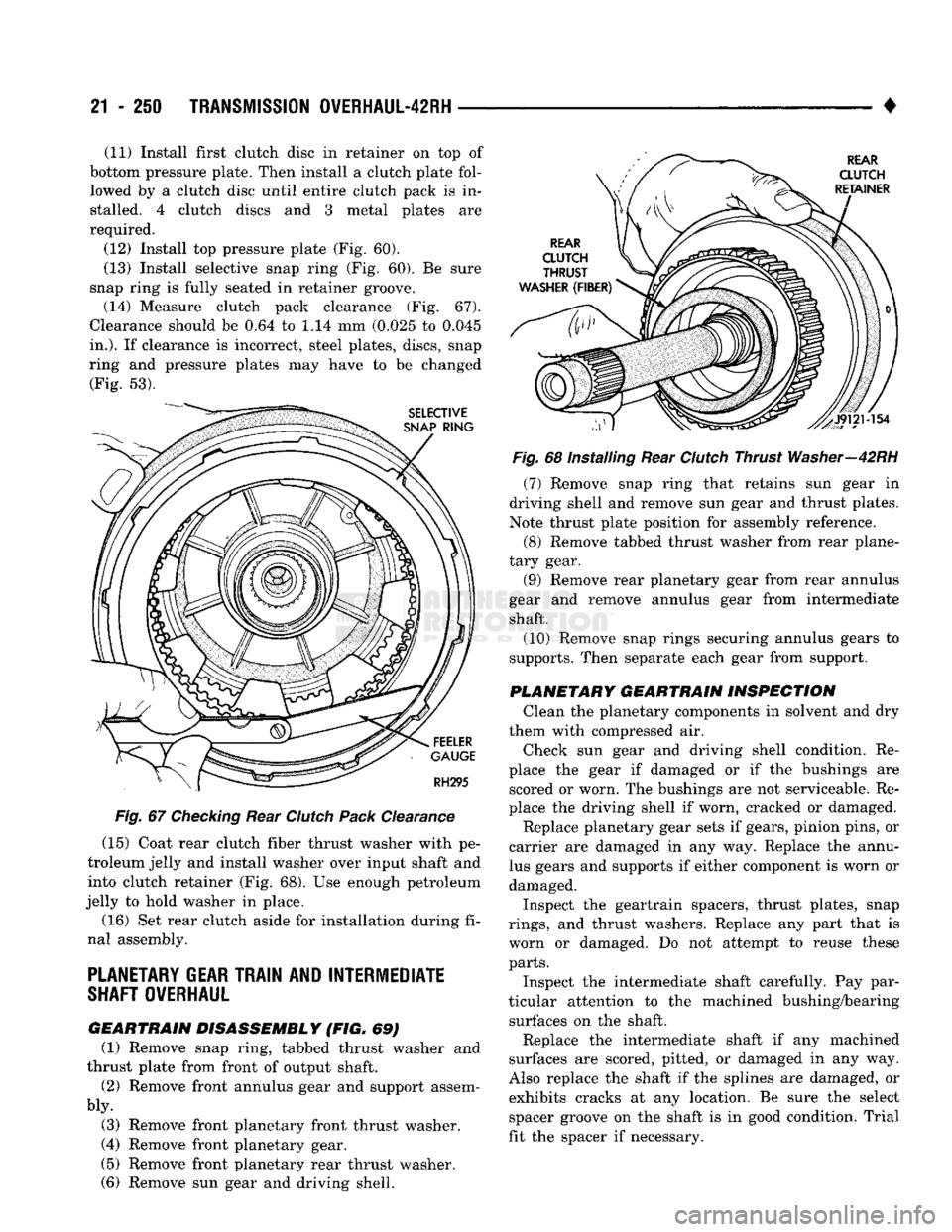
21
- 250
TRANSMISSION 0VERHAUL-42RH
—
Fig.
67
Checking
Rear
Clutch
Pack
Clearance
(15) Coat rear clutch fiber thrust washer with pe
troleum jelly and install washer over input shaft and into clutch retainer (Fig. 68). Use enough petroleum
jelly to hold washer in place.
(16) Set rear clutch aside for installation during fi
nal assembly.
PLANETARY GEAR TRAIN AND INTERMEDIATE
SHAFT OVERHAUL
GEARTRAIN DISASSEMBLY (FIG* 69) (1) Remove snap ring, tabbed thrust washer and
thrust plate from front of output shaft. (2) Remove front annulus gear and support assem
bly. (3) Remove front planetary front thrust washer.
(4) Remove front planetary gear.
(5) Remove front planetary rear thrust washer.
(6) Remove sun gear and driving shell. •
Fig.
68 Installing Rear
Clutch
Thrust Washer—42RH (7) Remove snap ring that retains sun gear in
driving shell and remove sun gear and thrust plates.
Note thrust plate position for assembly reference. (8) Remove tabbed thrust washer from rear plane
tary gear.
(9) Remove rear planetary gear from rear annulus
gear and remove annulus gear from intermediate
shaft.
(10) Remove snap rings securing annulus gears to
supports. Then separate each gear from support.
PLANETARY GEARTRAIN INSPECTION Clean the planetary components in solvent and dry
them with compressed air. Check sun gear and driving shell condition. Re
place the gear if damaged or if the bushings are scored or worn. The bushings are not serviceable. Re
place the driving shell if worn, cracked or damaged.
Replace planetary gear sets if gears, pinion pins, or
carrier are damaged in any way. Replace the annu
lus gears and supports if either component is worn or
damaged.
Inspect the geartrain spacers, thrust plates, snap
rings,
and thrust washers. Replace any part that is worn or damaged. Do not attempt to reuse these
parts.
Inspect the intermediate shaft carefully. Pay par
ticular attention to the machined bushing/bearing surfaces on the shaft.
Replace the intermediate shaft if any machined
surfaces are scored, pitted, or damaged in any way.
Also replace the shaft if the splines are damaged, or exhibits cracks at any location. Be sure the select spacer groove on the shaft is in good condition. Trial
fit the spacer if necessary.
(11) Install first clutch disc in retainer on top of
bottom pressure plate. Then install a clutch plate fol lowed by a clutch disc until entire clutch pack is in
stalled. 4 clutch discs and 3 metal plates are
required.
(12) Install top pressure plate (Fig. 60).
(13) Install selective snap ring (Fig. 60). Be sure
snap ring is fully seated in retainer groove. (14) Measure clutch pack clearance (Fig. 67).
Clearance should be 0.64 to 1.14 mm (0.025 to 0.045
in.).
If clearance is incorrect, steel plates, discs, snap
ring and pressure plates may have to be changed (Fig. 53).
Page 1252 of 1502
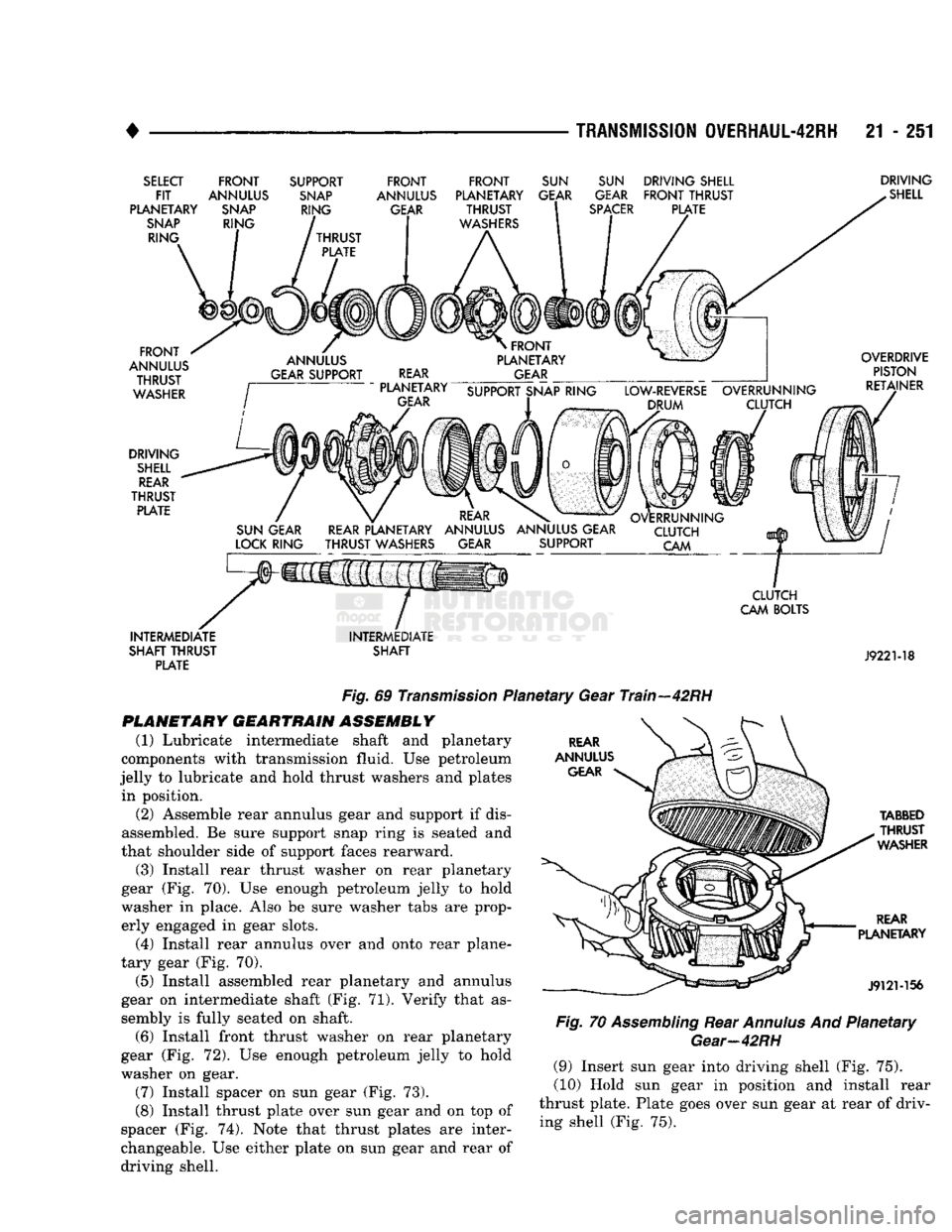
#
, , . , _
TRANSMISSION 0VERHAUL-42RH
21 - 251
SELECT
FRONT
FIT ANNULUS
PLANETARY SNAP
SNAP
RING RING SUPPORT
SNAP
RING
FRONT
ANNULUS
GEAR
FRONT
PLANETARY THRUST
WASHERS
SUN
GEAR
SUN
GEAR
SPACER
DRIVING SHELL
FRONT
THRUST
PLATE
FRONT
ANNULUS
THRUST
WASHER
DRIVING
SHELL
REAR
THRUST PLATE OVERDRIVE
PISTON
RETAINER INTERMEDIATE
SHAFT THRUST PLATE DRIVING
,
SHELL
CLUTCH
CAM BOLTS
INTERMEDIATE SHAFT
Fig.
69
Transmission
Planetary Gear Train—42RH
J9221-18
PLANETARY
GEARTRAIN
ASSEMBLY
(1) Lubricate intermediate shaft and planetary
components with transmission fluid. Use petroleum
jelly to lubricate and hold thrust washers and plates in position. (2) Assemble rear annulus gear and support if dis
assembled. Be sure support snap ring is seated and
that shoulder side of support faces rearward.
(3) Install rear thrust washer on rear planetary
gear (Fig. 70). Use enough petroleum jelly to hold
washer in place. Also be sure washer tabs are prop erly engaged in gear slots.
(4) Install rear annulus over and onto rear plane
tary gear (Fig. 70).
(5) Install assembled rear planetary and annulus
gear on intermediate shaft (Fig. 71). Verify that as
sembly is fully seated on shaft.
(6) Install front thrust washer on rear planetary
gear (Fig. 72). Use enough petroleum jelly to hold
washer on gear.
(7) Install spacer on sun gear (Fig. 73).
(8) Install thrust plate over sun gear and on top of
spacer (Fig. 74). Note that thrust plates are inter
changeable. Use either plate on sun gear and rear of
driving shell.
REAR
ANNULUS
GEAR
TABBED
THRUST
WASHER
REAR
PLANETARY
J9121-156
Fig.
70
Assembling
Rear
Annulus
And Planetary
Gear-42RH
(9) Insert sun gear into driving shell (Fig. 75).
(10) Hold sun gear in position and install rear
thrust plate. Plate goes over sun gear at rear of driv ing shell (Fig. 75).
Page 1253 of 1502
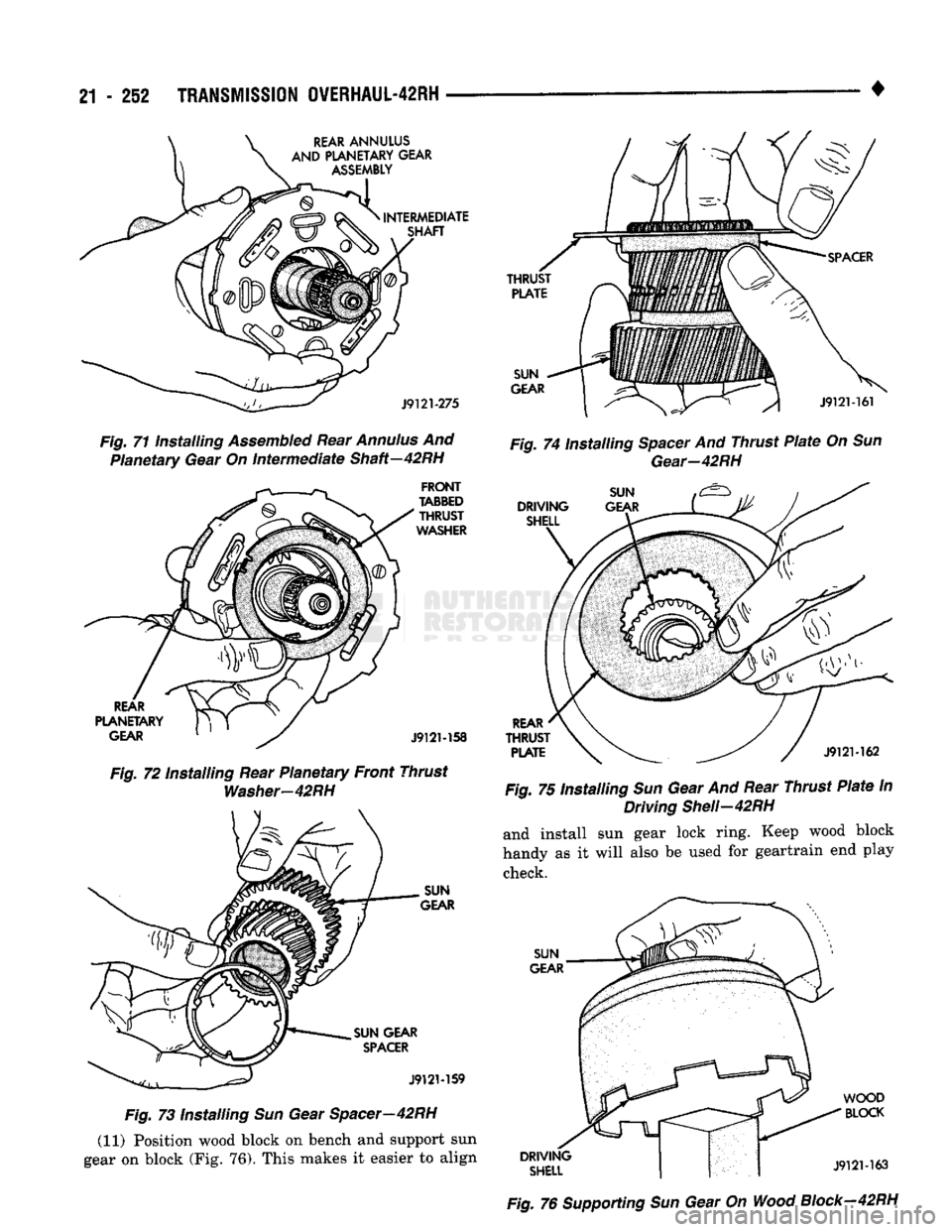
21
- 252 TRANSMISSION OVERHAUL-42RH
•
REAR
ANNULUS
AND
PLANETARY
GEAR
ASSEMBLY
INTERMEDIATE
SHAFT
J9121-275
Fig.
71 installing
Assembled
Rear
Annulus
And Planetary Gear On
Intermediate
Shaft—42RH
FRONT
TABBED
THRUST
WASHER
REAR
PLANETARY
GEAR
J9121-158
Fig.
72 Installing Rear Planetary Front Thrust
Washer-42RH
SUN
GEAR SUN GEAR
SPACER
J912M59
Fig.
73 Installing Sun Gear Spacer—42RH
(11) Position wood block on bench and support sun
gear on block (Fig. 76). This makes it easier to align
THRUST
PLATE
Fig.
74 Installing
Spacer
And Thrust
Plate
On Sun
Gear-42RH
SUN
DRIVING
GEAR SHELL
REAR
THRUST
PLATE
J9121-162
Fig.
75 Installing Sun Gear And Rear Thrust
Plate
In
Driving
Shell-42RH
and install sun gear lock ring. Keep wood block
handy as it will also be used for geartrain end play check.
SUN
GEAR
DRIVING
SHELL
WOOD
BLOCK
J912M63
Fig.
76 Supporting Sun Gear On
Wood
Block-42RH
Page 1254 of 1502
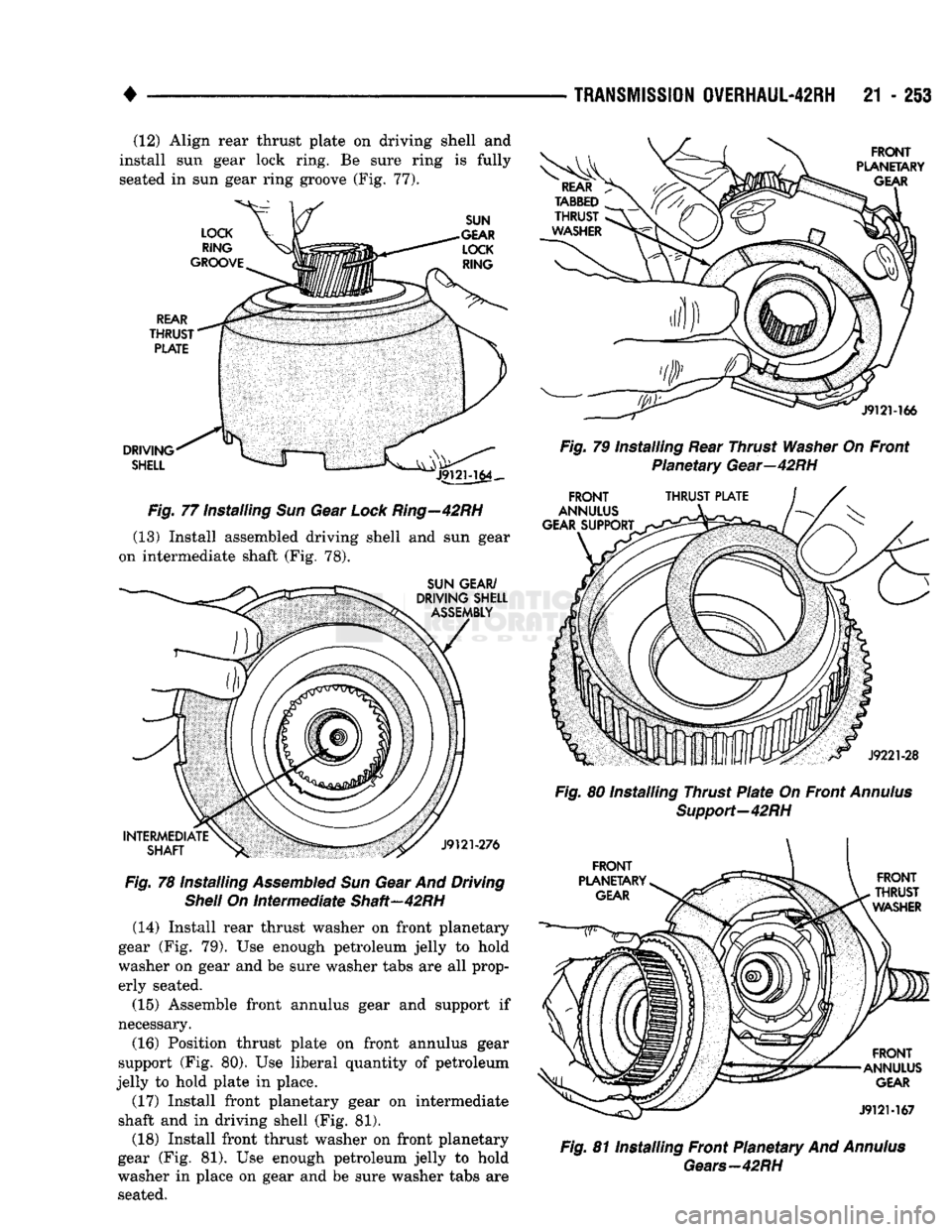
•
TRANSMISSION
OVERHAUL-42RH
21 - 253 (12) Align rear thrust plate on driving shell and
install sun gear lock ring. Be sure ring is fully seated in sun gear ring groove (Fig. 77).
Fig.
77 Installing Sun Gear
Lock
Ring—42RH
(13) Install assembled driving shell and sun gear
on intermediate shaft (Fig. 78).
Fig.
78 Installing
Assembled
Sun Gear And Driving
Shell
On
Intermediate
Shaft—42RH
(14) Install rear thrust washer on front planetary
gear (Fig. 79). Use enough petroleum jelly to hold
washer on gear and be sure washer tabs are all prop erly seated.
(15) Assemble front annulus gear and support if
necessary.
(16) Position thrust plate on front annulus gear
support (Fig. 80). Use liberal quantity of petroleum
jelly to hold plate in place.
(17) Install front planetary gear on intermediate
shaft and in driving shell (Fig. 81).
(18) Install front thrust washer on front planetary
gear (Fig. 81). Use enough petroleum jelly to hold
washer in place on gear and be sure washer tabs are seated.
Fig.
79 Installing Rear Thrust
Washer
On Front
Planetary Gear—42RH
Fig.
80 Installing Thrust
Plate
On Front
Annulus
Support—42RH
Fig.
81 Installing Front Planetary And
Annulus
Gears—42RH
Page 1255 of 1502
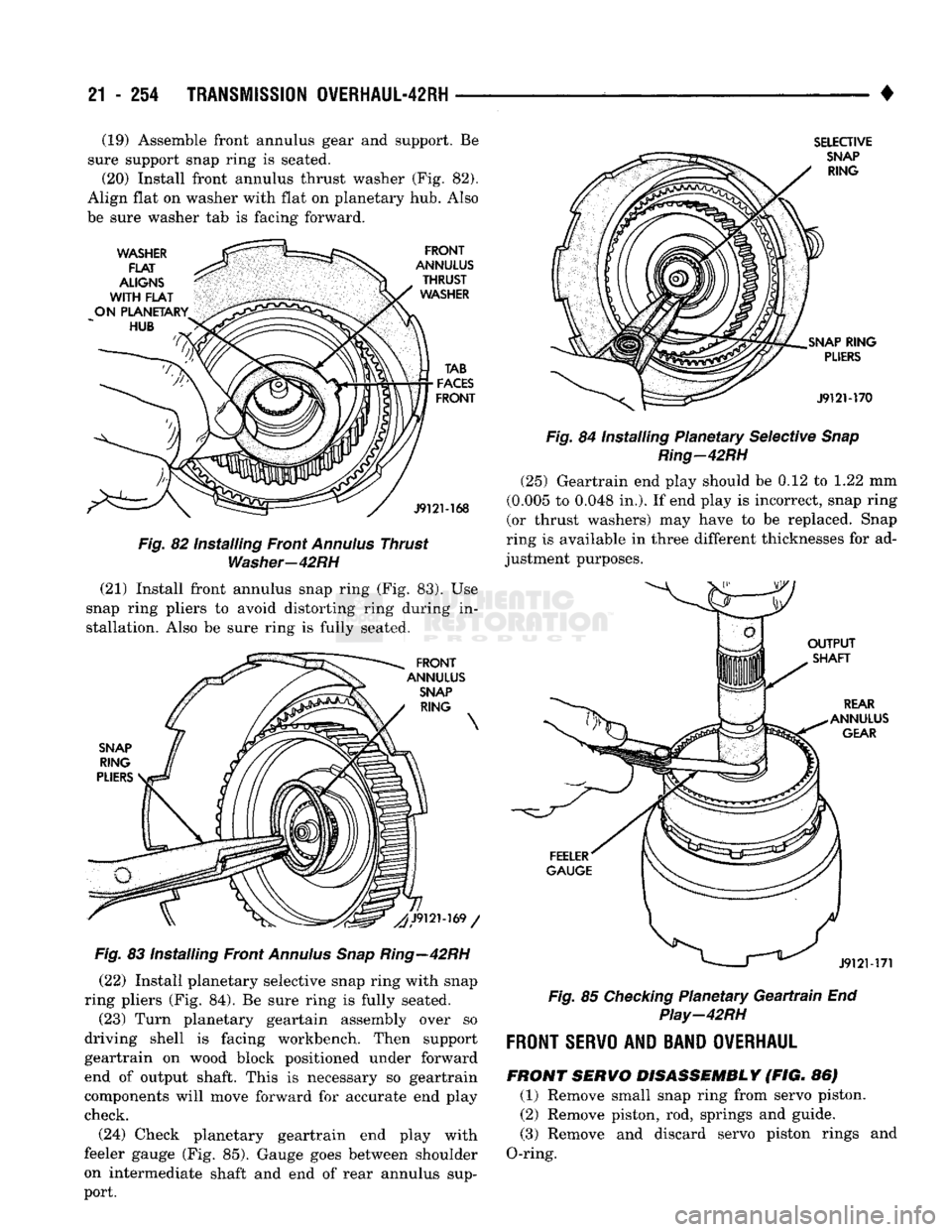
21
- 254
TRANSMISSION OVERHAUL-42RH
• (19) Assemble front annulus gear and support. Be
sure support snap ring is seated. (20) Install front annulus thrust washer (Fig. 82).
Align flat on washer with flat on planetary hub. Also
be sure washer tab is facing forward.
Fig.
82 Installing Front
Annulus
Thrust
Washer-42RH
(21) Install front annulus snap ring (Fig. 83). Use
snap ring pliers to avoid distorting ring during in
stallation. Also be sure ring is fully seated.
Fig.
83 Installing Front
Annulus Snap Ring—42RH
(22) Install planetary selective snap ring with snap
ring pliers (Fig. 84). Be sure ring is fully seated.
(23) Turn planetary geartain assembly over so
driving shell is facing workbench. Then support
geartrain on wood block positioned under forward
end of output shaft. This is necessary so geartrain
components will move forward for accurate end play check.
(24) Check planetary geartrain end play with
feeler gauge (Fig. 85). Gauge goes between shoulder
on intermediate shaft and end of rear annulus sup
port.
SELECTIVE
Fig.
84 Installing Planetary Selective
Snap Ring-42RH
(25) Geartrain end play should be 0.12 to 1.22 mm
(0.005 to 0.048 in.). If end play is incorrect, snap ring
(or thrust washers) may have to be replaced. Snap
ring is available in three different thicknesses for ad
justment purposes.
Fig.
85
Checking
Planetary
Geartrain
End
Play-42RH
FRONT
SERVO
AND
BAND OVERHAUL
FRONT
SERVO DISASSEMBLY
(FIG. 86) (1) Remove small snap ring from servo piston. (2) Remove piston, rod, springs and guide.
(3) Remove and discard servo piston rings and
O-ring.
Page 1256 of 1502
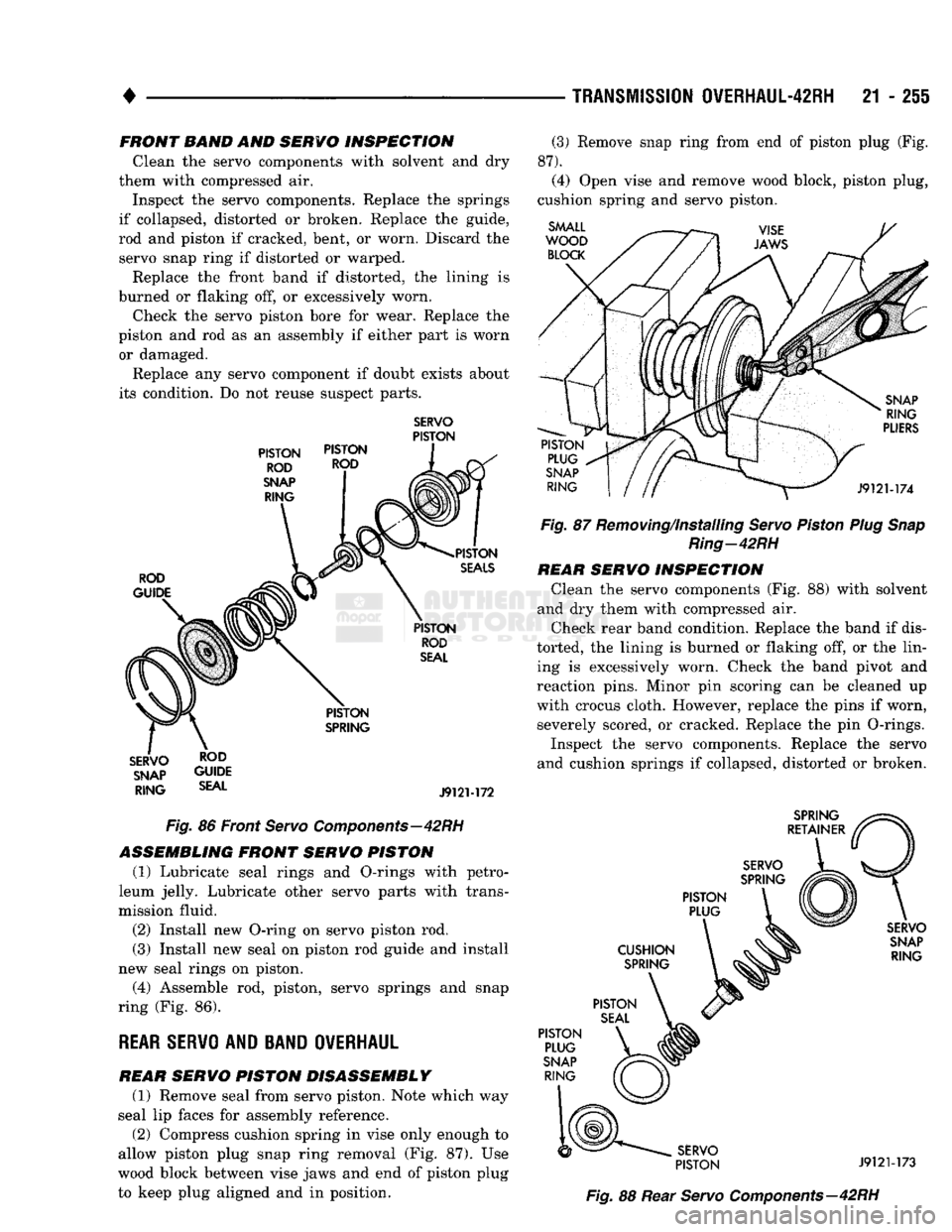
TRANSMISSION
OVERHAUL-42RH
21 - 255
FRONT BAND AND SERVO INSPECTION
Clean the servo components with solvent and dry
them with compressed air.
Inspect the servo components. Replace the springs
if collapsed, distorted or broken. Replace the guide,
rod and piston if cracked, bent, or worn. Discard the servo snap ring if distorted or warped.
Replace the front band if distorted, the lining is
burned or flaking off, or excessively worn.
Check the servo piston bore for wear. Replace the
piston and rod as an assembly if either part is worn or damaged.
Replace any servo component if doubt exists about
its condition. Do not reuse suspect parts.
PISTON PISTON
ROD
ROD
SNAP
RING
SERVO
PISTON
ROD
GUIDE
PISTON
SEALS
PISTON
ROD
SEAL
PISTON
SPRING
SERVO
ROD
SNAP
GUIDE RING
SEAL J912M72
Fig.
86 Front
Servo
Components—42RH
ASSEMBLING FRONT SERVO PISTON
(1) Lubricate seal rings and O-rings with petro
leum jelly. Lubricate other servo parts with trans
mission fluid.
(2) Install new O-ring on servo piston rod.
(3) Install new seal on piston rod guide and install
new seal rings on piston. (4) Assemble rod, piston, servo springs and snap
ring (Fig. 86).
REAR
SER¥0 AND BAND OVERHAUL
REAR SERVO PISTON DISASSEMBLY (1) Remove seal from servo piston. Note which way
seal lip faces for assembly reference.
(2) Compress cushion spring in vise only enough to
allow piston plug snap ring removal (Fig. 87). Use
wood block between vise jaws and end of piston plug
to keep plug aligned and in position. (3) Remove snap ring from end of piston plug (Fig.
87).
(4) Open vise and remove wood block, piston plug,
cushion spring and servo piston.
SMALL
WOOD BLOCK
PISTON PLUG
SNAP
RING
SNAP
RING
PLIERS
J9121-174
Fig.
87 Removing/lnstailing
Servo
Piston
Piug
Snap
Ring—42RH
REAR SERVO INSPECTION Clean the servo components (Fig. 88) with solvent
and dry them with compressed air.
Check rear band condition. Replace the band if dis
torted, the lining is burned or flaking off, or the lin ing is excessively worn. Check the band pivot and
reaction pins. Minor pin scoring can be cleaned up
with crocus cloth. However, replace the pins if worn, severely scored, or cracked. Replace the pin O-rings.
Inspect the servo components. Replace the servo
and cushion springs if collapsed, distorted or broken.
SPRING
RETAINER
SERVO
SPRING
PISTON PLUG
CUSHION
SPRING SERVO
SNAP
RING
PISTON PLUG
SNAP
RING
SERVO
PISTON
J9121-173
Fig.
88 Rear
Servo
Components—42RH
Page 1257 of 1502
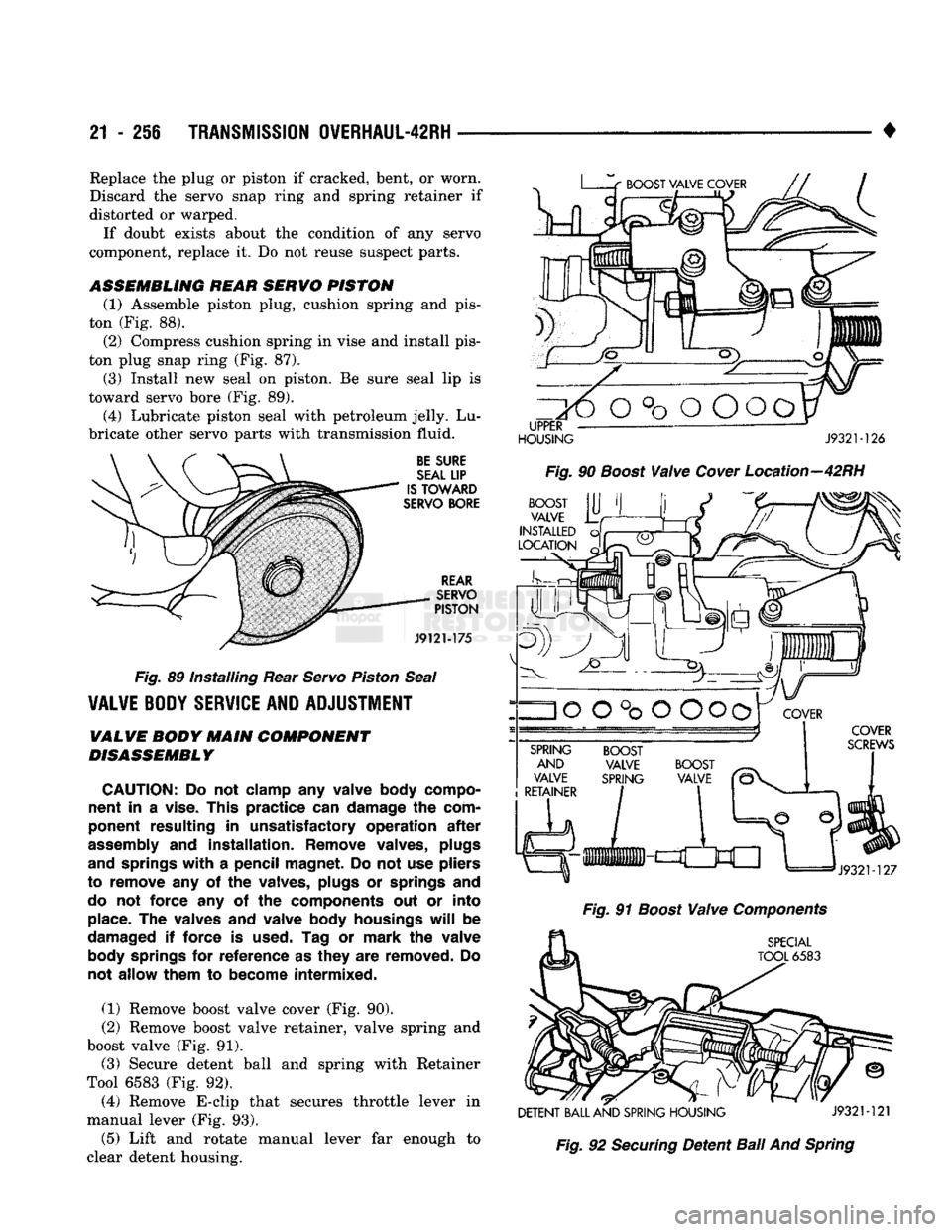
21
- 256
TRANSMISSION OVERHAUL-42RH
Replace the plug or piston if cracked, bent, or worn.
Discard the servo snap ring and spring retainer if
distorted or warped. If doubt exists about the condition of any servo
component, replace it. Do not reuse suspect parts.
ASSEMBLING REAR SERWO PISTON (1) Assemble piston plug, cushion spring and pis
ton (Fig. 88). (2) Compress cushion spring in vise and install pis
ton plug snap ring (Fig. 87).
(3) Install new seal on piston. Be sure seal lip is
toward servo bore (Fig. 89). (4) Lubricate piston seal with petroleum jelly. Lu
bricate other servo parts with transmission fluid.
BE
SURE
SEAL
LIP
IS
TOWARD
SERVO
BORE
REAR
SERVO
PISTON
J9121-175
Fig.
89 installing Rear
Servo
Piston
Seal
VALVE
BODY
SERVICE
AND ADJUSTMENT
WALWE
BODY MAIN COMPONENT
DISASSEMBLY
CAUTION:
Do not
clamp
any
valve body compo
nent
in a
vise. This
practice
can
damage
the
com
ponent
resulting
in
unsatisfactory operation
after
assembly
and
installation. Remove valves,
plugs
and
springs
with
a
pencil magnet.
Do not use
pliers
to remove
any of the
valves, plugs
or
springs
and
do
not
force
any of the
components
out or into
place.
The
valves
and
valve body
housings
will
be
damaged
if
force
is
used.
Tag or
mark
the
valve body springs
for
reference
as
they
are
removed.
Do
not allow
them
to
become intermixed.
(1) Remove boost valve cover (Fig. 90).
(2) Remove boost valve retainer, valve spring and
boost valve (Fig. 91). (3) Secure detent ball and spring with Retainer
Tool 6583 (Fig. 92).
(4) Remove E-clip that secures throttle lever in
manual lever (Fig. 93). (5) Lift and rotate manual lever far enough to
clear detent housing.
IK)
O °o O OOO
UPPER
HOUSING
J9321-126
Fig.
90
Boost
Valve
Cover
Location—42RH
BOOST VALVE
INSTALLED
LOCATION
SPRING BOOST AND VALVE BOOST
VALVE SPRING VALVE
RETAINER COVER
SCREWS
J9321-127
Fig.
91
Boost
Valve
Components
SPECIAL
TOOL
6583
DETENT BALL AND SPRING HOUSING
J9321
-121
Fig.
92
Securing
Detent
Ball
And
Spring
Page 1258 of 1502
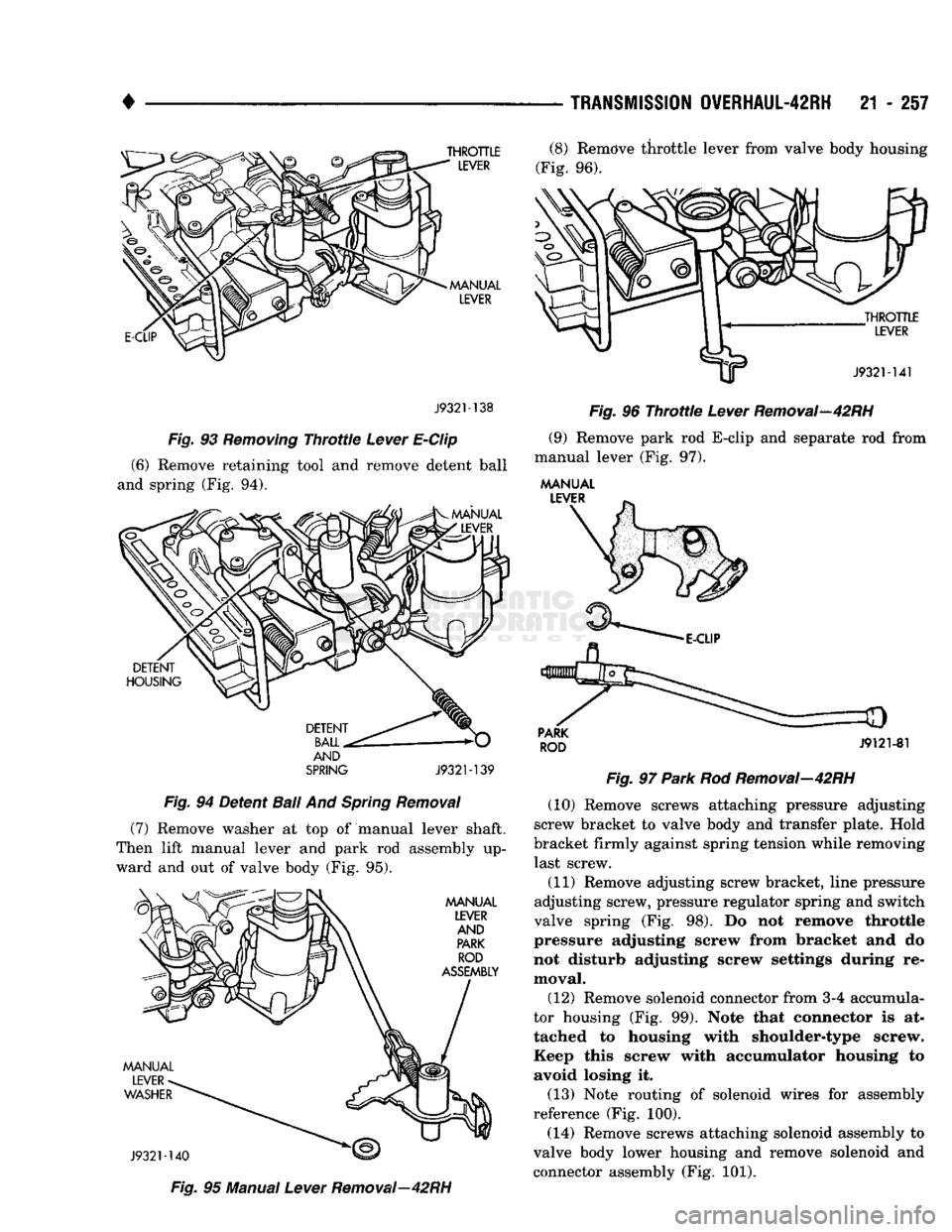
•
TRANSMISSION
0VERHAUL-42RH
21 - 257
THROTTLE
LEVER
AAANUAL
LEVER
E-CLIP
J9321-138
Fig. 93 Removing Throttle Lever
E-Clip
(6) Remove retaining tool and remove detent ball
and spring (Fig. 94). AAANUAL
LEVER
DETENT
HOUSING
DETENT
BALL.
AND
SPRING
J9321-139
Fig.
94 Detent Bali And Spring Removal (7) Remove washer at top of manual lever shaft.
Then lift manual lever and park rod assembly up
ward and out of valve body (Fig. 95).
AAANUAL
LEVER AND
PARK ROD
ASSEMBLY
MANUAL LEVER
WASHER
J932M40
Fig.
95 Manual
Lever
Removal—42RH (8) Remove throttle lever from valve body housing
(Fig. 96).
THROTTLE
LEVER
J932M41
Fig.
96
Throttle
Lever
Removal—42RH (9) Remove park rod E-clip and separate rod from
manual lever (Fig. 97).
MANUAL
LEVER
PARK ROD
J9121-81
Fig.
97
Park
Rod Removal—42RH
(10) Remove screws attaching pressure adjusting
screw bracket to valve body and transfer plate. Hold
bracket firmly against spring tension while removing last screw.
(11) Remove adjusting screw bracket, line pressure
adjusting screw, pressure regulator spring and switch
valve spring (Fig. 98). Do not remove throttle
pressure adjusting screw from bracket and do
not disturb adjusting screw settings during re
moval.
(12) Remove solenoid connector from 3-4 accumula
tor housing (Fig. 99). Note that connector is at
tached to housing with shoulder-type screw.
Keep this screw with accumulator housing to avoid losing it.
(13) Note routing of solenoid wires for assembly
reference (Fig. 100).
(14) Remove screws attaching solenoid assembly to
valve body lower housing and remove solenoid and connector assembly (Fig. 101).
Page 1259 of 1502
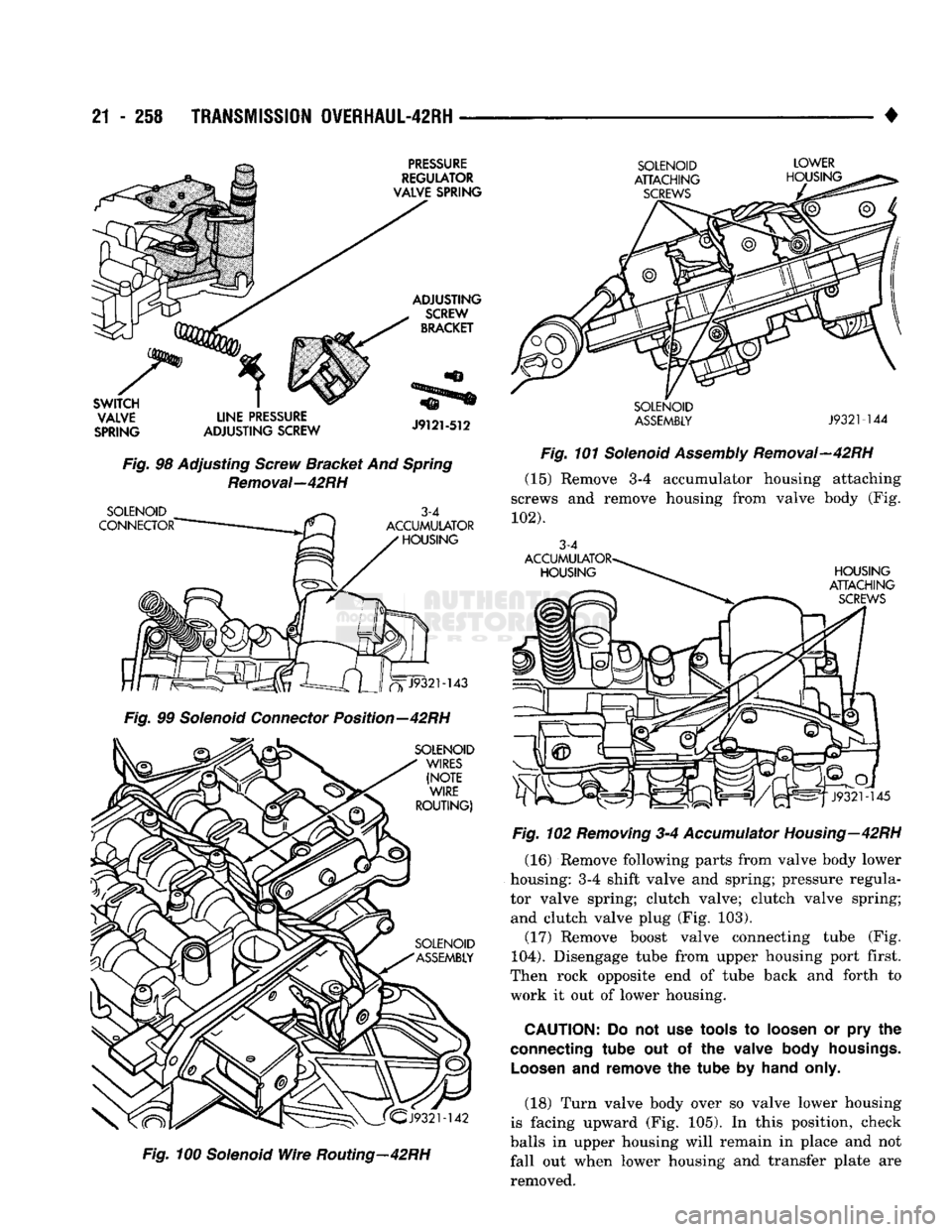
21
- 258
TRANSMISSION 0VERHAUL-42RH
•
PRESSURE
REGULATOR
VALVE SPRING
ADJUSTING
SCREW
BRACKET
SWITCH VALVE
SPRING
LINE PRESSURE
ADJUSTING SCREW
J9121-512
Fig.
98 Adjusting
Screw
Bracket And
Spring
Removal—42RH
SOLENOID
CONNECTOR
3-4
ACCUMULATOR HOUSING
a=J932M43
Fig.
99
Solenoid
Connector
Position—42RH
SOLENOID
WIRES
(NOTE
WIRE
ROUTING)
s\^t%U^r
^^^^
Fig.
100
Solenoid
Wire
Routing—42RH
SOLENOID
ATTACHING
SCREWS
LOWER
HOUSING
SOLENOID
ASSEMBLY
J932M44
Fig.
101
Solenoid
Assembly
Removal—42RH (15) Remove 3-4 accumulator housing attaching
screws and remove housing from valve body (Fig.
102).
3-4
ACCUMULATOR- HOUSING HOUSING
ATTACHING
SCREWS
Fig.
102
Removing
3-4
Accumulator
Housing—42RH
(16) Remove following parts from valve body lower
housing: 3-4 shift valve and spring; pressure regula
tor valve spring; clutch valve; clutch valve spring; and clutch valve plug (Fig. 103).
(17) Remove boost valve connecting tube (Fig.
104).
Disengage tube from upper housing port first.
Then rock opposite end of tube back and forth to
work it out of lower housing.
CAUTION:
Do not use
tools
to
loosen
or pry the
connecting
tube
out of the
valve body
housings.
Loosen
and
remove
the
tube
by
hand only.
(18) Turn valve body over so valve lower housing
is facing upward (Fig. 105). In this position, check
balls in upper housing will remain in place and not fall out when lower housing and transfer plate are
removed.
Page 1260 of 1502
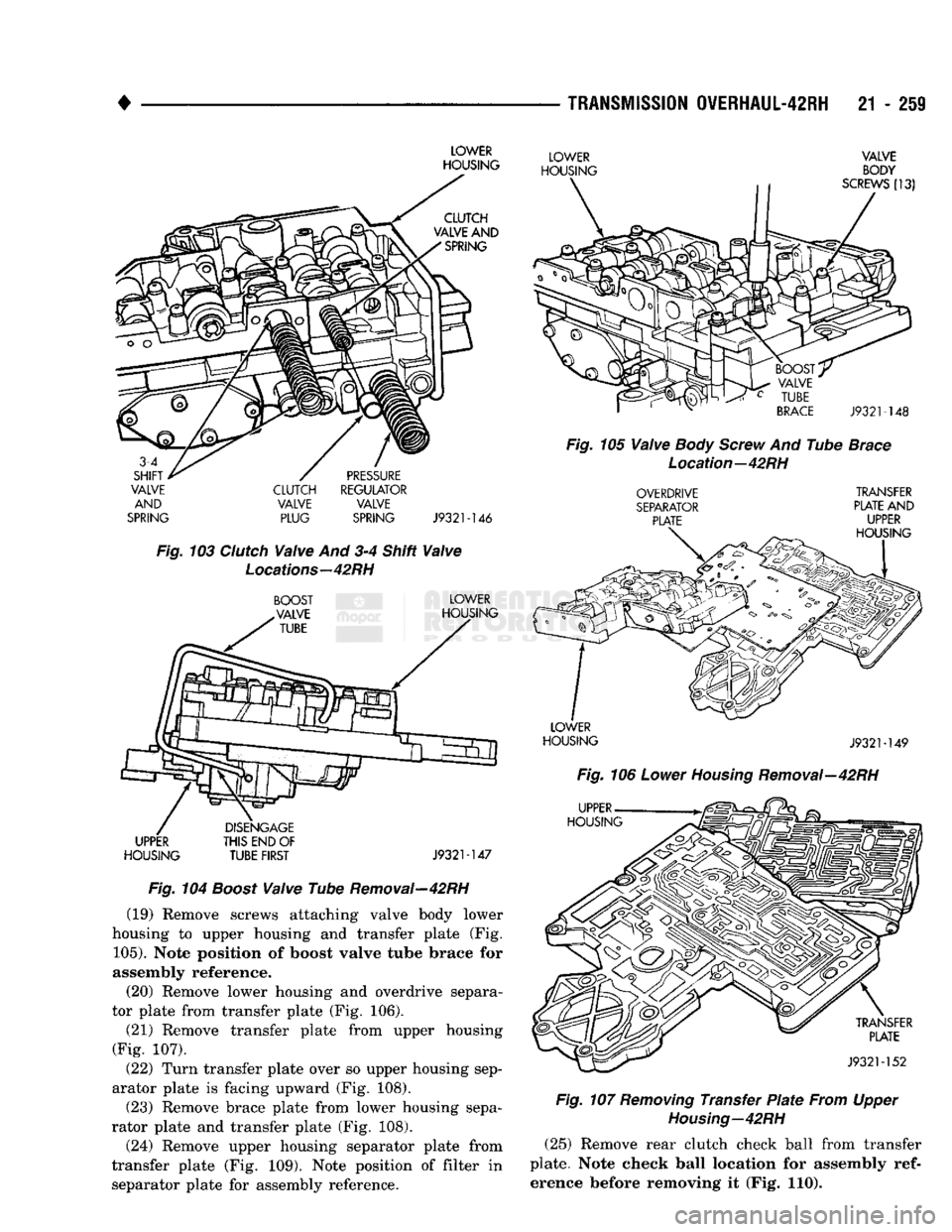
TRANSMISSION
0VERHAUL-42RH
21 - 259
LOWER
HOUSING
CLUTCH
VALVE
AND
SPRING
3-4
SHIFT
VALVE
AND
SPRING
PRESSURE
CLUTCH
REGULATOR
VALVE VALVE
PLUG
SPRING
J9321-146
Fig.
103
Clutch
Valve And 3-4 Shift Vaive
Locations—42
RH
BOOST
.VALVE
TUBE
LOWER
HOUSING
UPPER
HOUSING
DISENGAGE
THIS
END OF
TUBE
FIRST
J9321-147
Fig.
104
Boost
Valve Tube Removal—42RH (19) Remove screws attaching valve body lower
housing to upper housing and transfer plate (Fig.
105).
Note position of boost valve tube brace for
assembly reference.
(20) Remove lower housing and overdrive separa
tor plate from transfer plate (Fig. 106).
(21) Remove transfer plate from upper housing
(Fig. 107). (22) Turn transfer plate over so upper housing sep
arator plate is facing upward (Fig. 108).
(23) Remove brace plate from lower housing sepa
rator plate and transfer plate (Fig. 108).
(24) Remove upper housing separator plate from
transfer plate (Fig. 109). Note position of filter in separator plate for assembly reference.
LOWER
HOUSING
VALVE
BODY
SCREWS
(13)
S
^ c
TUBE
BRACE
J9321-148
Fig.
105 Valve
Body
Screw
And Tube
Brace
Location—42RH
OVERDRIVE
SEPARATOR
PLATE
TRANSFER
PLATE
AND
UPPER
HOUSING
LOWER
HOUSING
J9321-149
Fig.
106
Lower
Housing
Removal—42RH
UPPER
HOUSING
TRANSFER
PLATE
J932M52
Fig.
107
Removing
Transfer
Plate
From Upper
Housing—42RH
(25) Remove rear clutch check ball from transfer
plate. Note check ball location for assembly
ref
erence before removing it (Fig. 110).