FIAT UNO 1983 Service Repair Manual
Manufacturer: FIAT, Model Year: 1983, Model line: UNO, Model: FIAT UNO 1983Pages: 303, PDF Size: 10.36 MB
Page 221 of 303
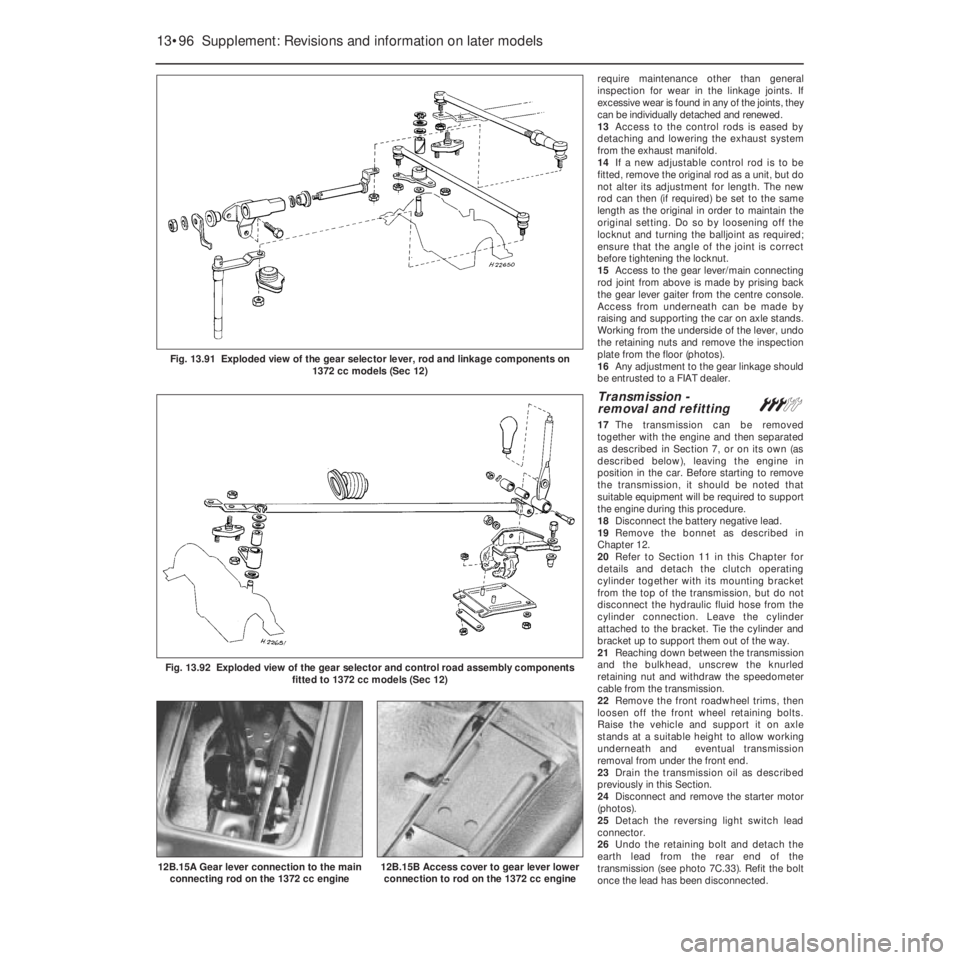
require maintenance other than general
inspection for wear in the linkage joints. If
excessive wear is found in any of the joints, they
can be individually detached and renewed.
13Access to the control rods is eased by
detaching and lowering the exhaust system
from the exhaust manifold.
14If a new adjustable control rod is to be
fitted, remove the original rod as a unit, but do
not alter its adjustment for length. The new
rod can then (if required) be set to the same
length as the original in order to maintain the
original setting. Do so by loosening off the
locknut and turning the balljoint as required;
ensure that the angle of the joint is correct
before tightening the locknut.
15Access to the gear lever/main connecting
rod joint from above is made by prising back
the gear lever gaiter from the centre console.
Access from underneath can be made by
raising and supporting the car on axle stands.
Working from the underside of the lever, undo
the retaining nuts and remove the inspection
plate from the floor (photos).
16Any adjustment to the gear linkage should
be entrusted to a FIAT dealer.
Transmission -
removal and refitting#
17The transmission can be removed
together with the engine and then separated
as described in Section 7, or on its own (as
described below), leaving the engine in
position in the car. Before starting to remove
the transmission, it should be noted that
suitable equipment will be required to support
the engine during this procedure.
18Disconnect the battery negative lead.
19Remove the bonnet as described in
Chapter 12.
20Refer to Section 11 in this Chapter for
details and detach the clutch operating
cylinder together with its mounting bracket
from the top of the transmission, but do not
disconnect the hydraulic fluid hose from the
cylinder connection. Leave the cylinder
attached to the bracket. Tie the cylinder and
bracket up to support them out of the way.
21Reaching down between the transmission
and the bulkhead, unscrew the knurled
retaining nut and withdraw the speedometer
cable from the transmission.
22Remove the front roadwheel trims, then
loosen off the front wheel retaining bolts.
Raise the vehicle and support it on axle
stands at a suitable height to allow working
underneath and eventual transmission
removal from under the front end.
23Drain the transmission oil as described
previously in this Section.
24Disconnect and remove the starter motor
(photos).
25Detach the reversing light switch lead
connector.
26Undo the retaining bolt and detach the
earth lead from the rear end of the
transmission (see photo 7C.33). Refit the bolt
once the lead has been disconnected.
13•96 Supplement: Revisions and information on later models
12B.15B Access cover to gear lever lower
connection to rod on the 1372 cc engine
Fig. 13.92 Exploded view of the gear selector and control road assembly components
fitted to 1372 cc models (Sec 12)
12B.15A Gear lever connection to the main
connecting rod on the 1372 cc engine
Fig. 13.91 Exploded view of the gear selector lever, rod and linkage components on
1372 cc models (Sec 12)
Page 222 of 303
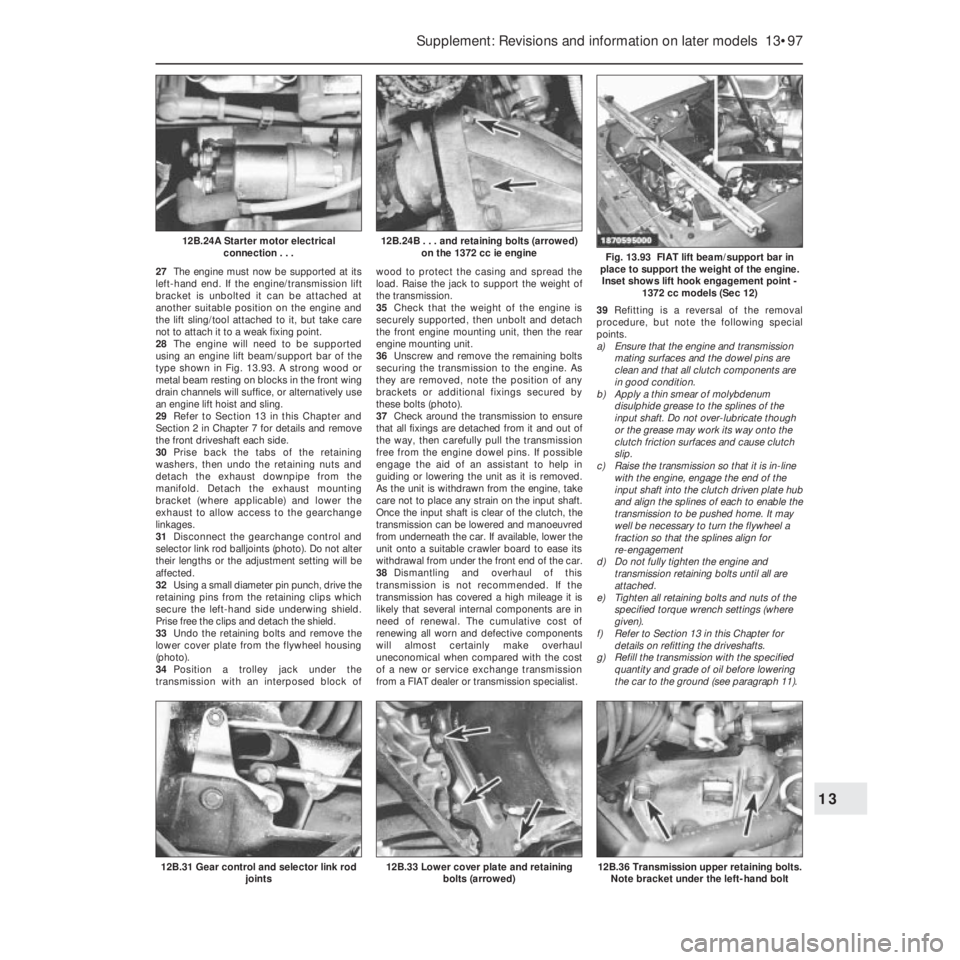
27The engine must now be supported at its
left-hand end. If the engine/transmission lift
bracket is unbolted it can be attached at
another suitable position on the engine and
the lift sling/tool attached to it, but take care
not to attach it to a weak fixing point.
28The engine will need to be supported
using an engine lift beam/support bar of the
type shown in Fig. 13.93. A strong wood or
metal beam resting on blocks in the front wing
drain channels will suffice, or alternatively use
an engine lift hoist and sling.
29Refer to Section 13 in this Chapter and
Section 2 in Chapter 7 for details and remove
the front driveshaft each side.
30Prise back the tabs of the retaining
washers, then undo the retaining nuts and
detach the exhaust downpipe from the
manifold. Detach the exhaust mounting
bracket (where applicable) and lower the
exhaust to allow access to the gearchange
linkages.
31Disconnect the gearchange control and
selector link rod balljoints (photo). Do not alter
their lengths or the adjustment setting will be
affected.
32Using a small diameter pin punch, drive the
retaining pins from the retaining clips which
secure the left-hand side underwing shield.
Prise free the clips and detach the shield.
33Undo the retaining bolts and remove the
lower cover plate from the flywheel housing
(photo).
34Position a trolley jack under the
transmission with an interposed block ofwood to protect the casing and spread the
load. Raise the jack to support the weight of
the transmission.
35Check that the weight of the engine is
securely supported, then unbolt and detach
the front engine mounting unit, then the rear
engine mounting unit.
36Unscrew and remove the remaining bolts
securing the transmission to the engine. As
they are removed, note the position of any
brackets or additional fixings secured by
these bolts (photo).
37Check around the transmission to ensure
that all fixings are detached from it and out of
the way, then carefully pull the transmission
free from the engine dowel pins. If possible
engage the aid of an assistant to help in
guiding or lowering the unit as it is removed.
As the unit is withdrawn from the engine, take
care not to place any strain on the input shaft.
Once the input shaft is clear of the clutch, the
transmission can be lowered and manoeuvred
from underneath the car. If available, lower the
unit onto a suitable crawler board to ease its
withdrawal from under the front end of the car.
38Dismantling and overhaul of this
transmission is not recommended. If the
transmission has covered a high mileage it is
likely that several internal components are in
need of renewal. The cumulative cost of
renewing all worn and defective components
will almost certainly make overhaul
uneconomical when compared with the cost
of a new or service exchange transmission
from a FIAT dealer or transmission specialist.39Refitting is a reversal of the removal
procedure, but note the following special
points.
a) Ensure that the engine and transmission
mating surfaces and the dowel pins are
clean and that all clutch components are
in good condition.
b) Apply a thin smear of molybdenum
disulphide grease to the splines of the
input shaft. Do not over-lubricate though
or the grease may work its way onto the
clutch friction surfaces and cause clutch
slip.
c) Raise the transmission so that it is in-line
with the engine, engage the end of the
input shaft into the clutch driven plate hub
and align the splines of each to enable the
transmission to be pushed home. It may
well be necessary to turn the flywheel a
fraction so that the splines align for
re-engagement
d) Do not fully tighten the engine and
transmission retaining bolts until all are
attached.
e) Tighten all retaining bolts and nuts of the
specified torque wrench settings (where
given).
f) Refer to Section 13 in this Chapter for
details on refitting the driveshafts.
g) Refill the transmission with the specified
quantity and grade of oil before lowering
the car to the ground (see paragraph 11).
Supplement: Revisions and information on later models 13•97
Fig. 13.93 FIAT lift beam/support bar in
place to support the weight of the engine.
Inset shows lift hook engagement point -
1372 cc models (Sec 12)
12B.24B . . . and retaining bolts (arrowed)
on the 1372 cc ie engine12B.24A Starter motor electrical
connection . . .
12B.36 Transmission upper retaining bolts.
Note bracket under the left-hand bolt12B.33 Lower cover plate and retaining
bolts (arrowed)12B.31 Gear control and selector link rod
joints
13
Page 223 of 303
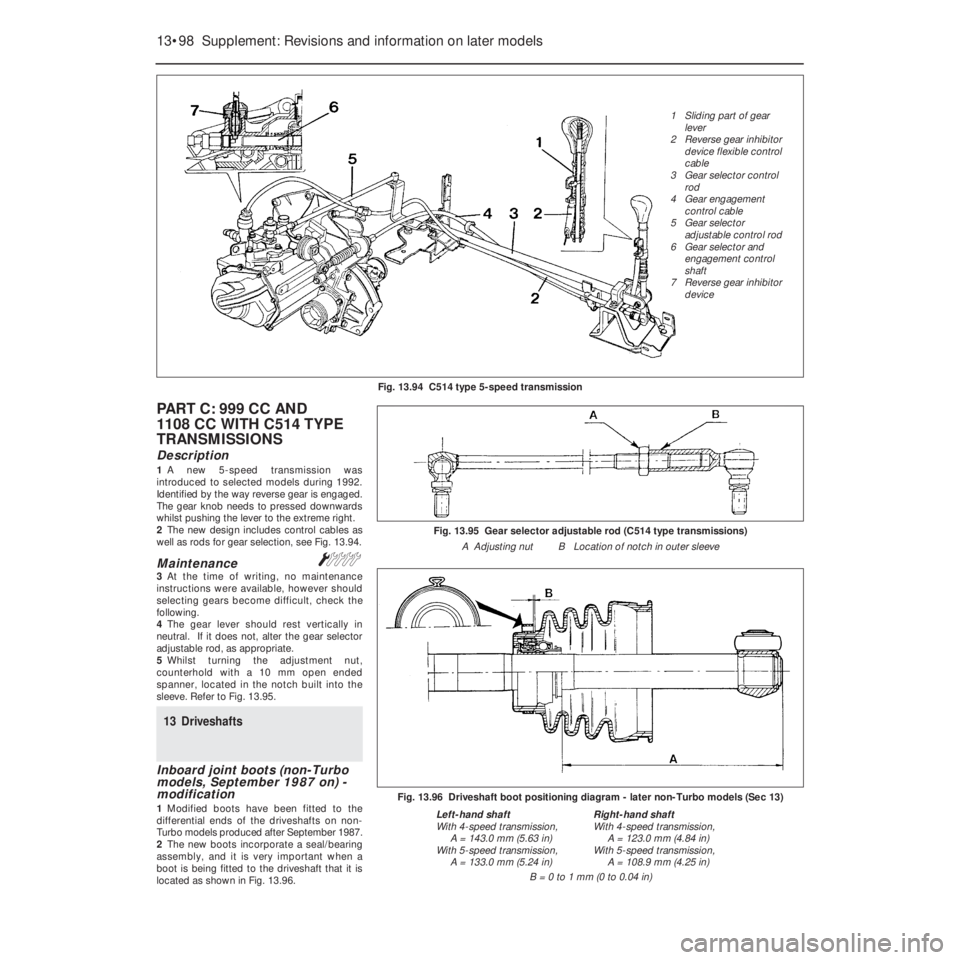
PART C: 999 CC AND
1108 CC WITH C514 TYPE
TRANSMISSIONS
Description
1A new 5-speed transmission was
introduced to selected models during 1992.
Identified by the way reverse gear is engaged.
The gear knob needs to pressed downwards
whilst pushing the lever to the extreme right.
2The new design includes control cables as
well as rods for gear selection, see Fig. 13.94.
MaintenanceÁ3At the time of writing, no maintenance
instructions were available, however should
selecting gears become difficult, check the
following.
4The gear lever should rest vertically in
neutral. If it does not, alter the gear selector
adjustable rod, as appropriate.
5Whilst turning the adjustment nut,
counterhold with a 10 mm open ended
spanner, located in the notch built into the
sleeve. Refer to Fig. 13.95.
13 Driveshafts
Inboard joint boots (non-Turbo
models, September 1987 on) -
modification
1Modified boots have been fitted to the
differential ends of the driveshafts on non-
Turbo models produced after September 1987.
2The new boots incorporate a seal/bearing
assembly, and it is very important when a
boot is being fitted to the driveshaft that it is
located as shown in Fig. 13.96.
13•98 Supplement: Revisions and information on later models
Fig. 13.96 Driveshaft boot positioning diagram - later non-Turbo models (Sec 13)
Left-hand shaft
With 4-speed transmission,
A = 143.0 mm (5.63 in)
With 5-speed transmission,
A = 133.0 mm (5.24 in)Right-hand shaft
With 4-speed transmission,
A = 123.0 mm (4.84 in)
With 5-speed transmission,
A = 108.9 mm (4.25 in)
Fig. 13.94 C514 type 5-speed transmission
1 Sliding part of gear
lever
2 Reverse gear inhibitor
device flexible control
cable
3 Gear selector control
rod
4 Gear engagement
control cable
5 Gear selector
adjustable control rod
6 Gear selector and
engagement control
shaft
7 Reverse gear inhibitor
device
B = 0 to 1 mm (0 to 0.04 in)
Fig. 13.95 Gear selector adjustable rod (C514 type transmissions)
A Adjusting nut B Location of notch in outer sleeve
Page 224 of 303
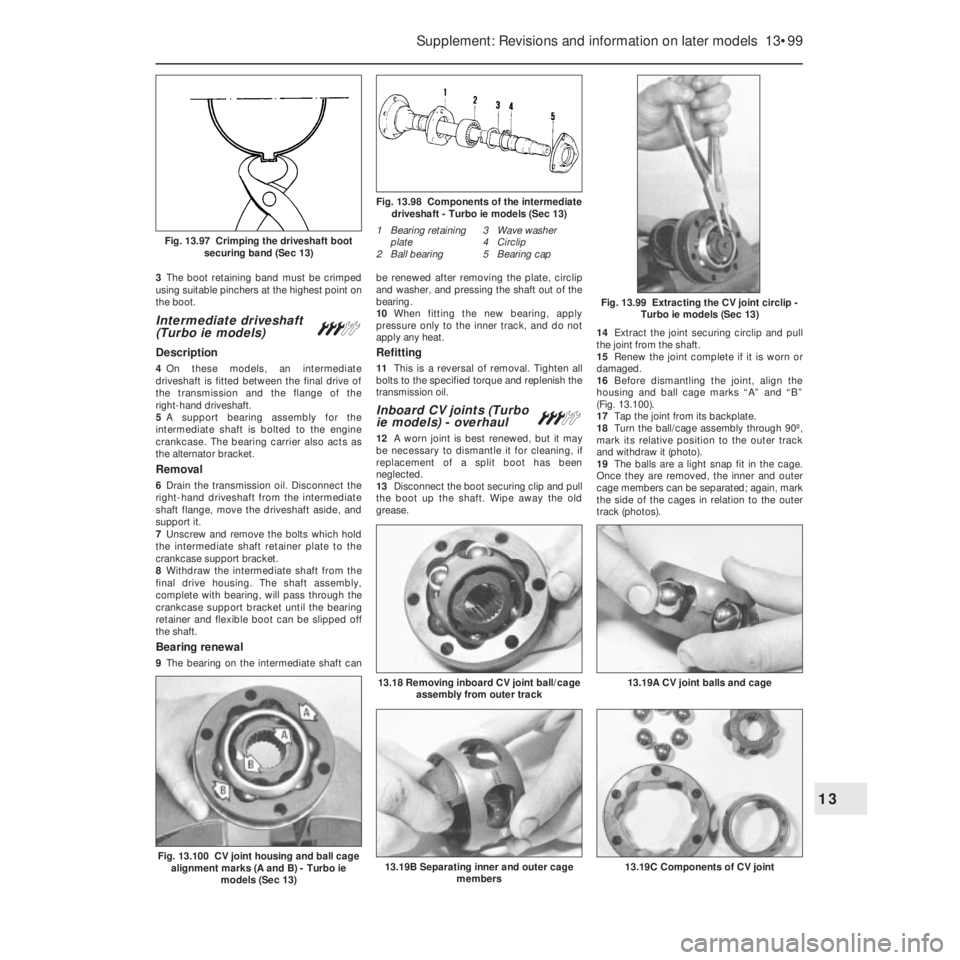
3The boot retaining band must be crimped
using suitable pinchers at the highest point on
the boot.
Intermediate driveshaft
(Turbo ie models) #
Description
4On these models, an intermediate
driveshaft is fitted between the final drive of
the transmission and the flange of the
right-hand driveshaft.
5A support bearing assembly for the
intermediate shaft is bolted to the engine
crankcase. The bearing carrier also acts as
the alternator bracket.
Removal
6Drain the transmission oil. Disconnect the
right-hand driveshaft from the intermediate
shaft flange, move the driveshaft aside, and
support it.
7Unscrew and remove the bolts which hold
the intermediate shaft retainer plate to the
crankcase support bracket.
8Withdraw the intermediate shaft from the
final drive housing. The shaft assembly,
complete with bearing, will pass through the
crankcase support bracket until the bearing
retainer and flexible boot can be slipped off
the shaft.
Bearing renewal
9The bearing on the intermediate shaft canbe renewed after removing the plate, circlip
and washer, and pressing the shaft out of the
bearing.
10When fitting the new bearing, apply
pressure only to the inner track, and do not
apply any heat.
Refitting
11This is a reversal of removal. Tighten all
bolts to the specified torque and replenish the
transmission oil.
Inboard CV joints (Turbo
ie models) - overhaul #
12A worn joint is best renewed, but it may
be necessary to dismantle it for cleaning, if
replacement of a split boot has been
neglected.
13Disconnect the boot securing clip and pull
the boot up the shaft. Wipe away the old
grease. 14Extract the joint securing circlip and pull
the joint from the shaft.
15Renew the joint complete if it is worn or
damaged.
16Before dismantling the joint, align the
housing and ball cage marks “A” and “B”
(Fig. 13.100).
17Tap the joint from its backplate.
18Turn the ball/cage assembly through 90º,
mark its relative position to the outer track
and withdraw it (photo).
19The balls are a light snap fit in the cage.
Once they are removed, the inner and outer
cage members can be separated; again, mark
the side of the cages in relation to the outer
track (photos).
Supplement: Revisions and information on later models 13•99
Fig. 13.99 Extracting the CV joint circlip -
Turbo ie models (Sec 13)
Fig. 13.98 Components of the intermediate
driveshaft - Turbo ie models (Sec 13)
1 Bearing retaining
plate
2 Ball bearing3 Wave washer
4 Circlip
5 Bearing cap
Fig. 13.97 Crimping the driveshaft boot
securing band (Sec 13)
13.19C Components of CV joint13.19B Separating inner and outer cage
members
13.19A CV joint balls and cage13.18 Removing inboard CV joint ball/cage
assembly from outer track
Fig. 13.100 CV joint housing and ball cage
alignment marks (A and B) - Turbo ie
models (Sec 13)
13
Page 225 of 303
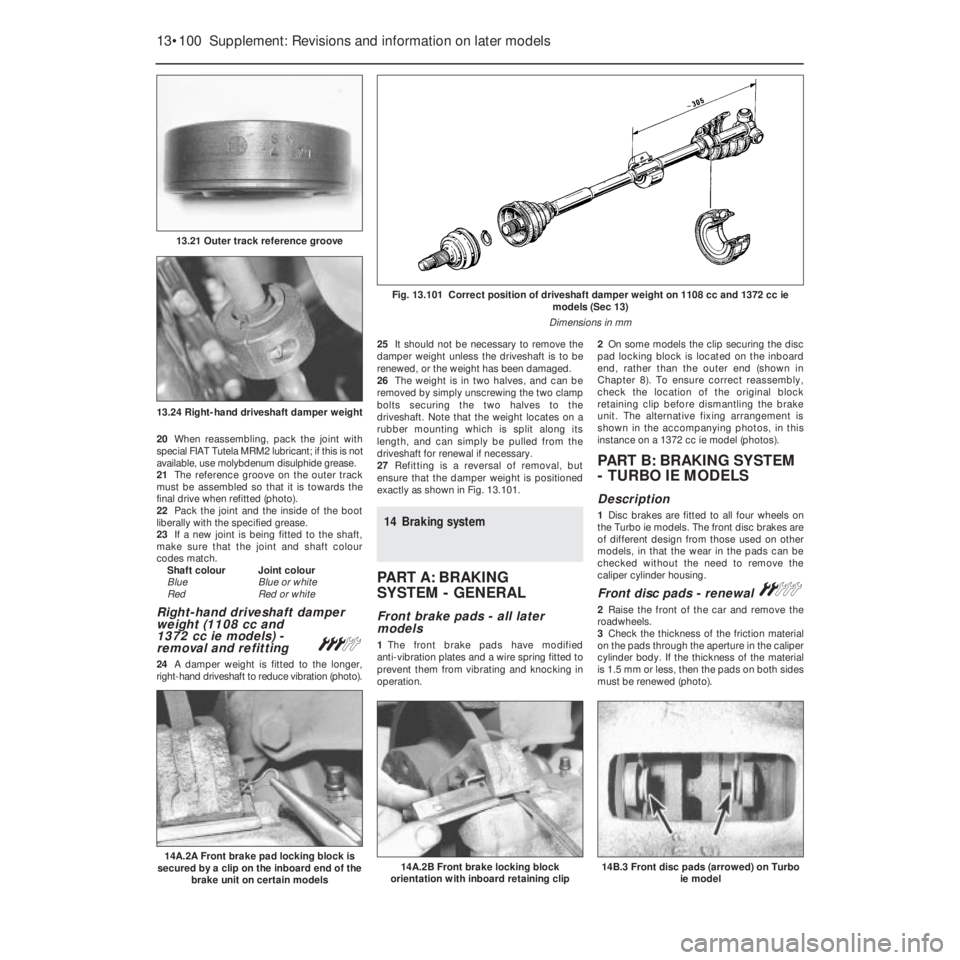
20When reassembling, pack the joint with
special FIAT Tutela MRM2 lubricant; if this is not
available, use molybdenum disulphide grease.
21The reference groove on the outer track
must be assembled so that it is towards the
final drive when refitted (photo).
22Pack the joint and the inside of the boot
liberally with the specified grease.
23If a new joint is being fitted to the shaft,
make sure that the joint and shaft colour
codes match.
Shaft colour Joint colour
Blue Blue or white
Red Red or white
Right-hand driveshaft damper
weight (1108 cc and
1372 cc ie models) -
removal and refitting
#
24A damper weight is fitted to the longer,
right-hand driveshaft to reduce vibration (photo).25It should not be necessary to remove the
damper weight unless the driveshaft is to be
renewed, or the weight has been damaged.
26The weight is in two halves, and can be
removed by simply unscrewing the two clamp
bolts securing the two halves to the
driveshaft. Note that the weight locates on a
rubber mounting which is split along its
length, and can simply be pulled from the
driveshaft for renewal if necessary.
27Refitting is a reversal of removal, but
ensure that the damper weight is positioned
exactly as shown in Fig. 13.101.
14 Braking system
PART A: BRAKING
SYSTEM - GENERAL
Front brake pads - all later
models
1The front brake pads have modified
anti-vibration plates and a wire spring fitted to
prevent them from vibrating and knocking in
operation. 2On some models the clip securing the disc
pad locking block is located on the inboard
end, rather than the outer end (shown in
Chapter 8). To ensure correct reassembly,
check the location of the original block
retaining clip before dismantling the brake
unit. The alternative fixing arrangement is
shown in the accompanying photos, in this
instance on a 1372 cc ie model (photos).
PART B: BRAKING SYSTEM
- TURBO IE MODELS
Description
1Disc brakes are fitted to all four wheels on
the Turbo ie models. The front disc brakes are
of different design from those used on other
models, in that the wear in the pads can be
checked without the need to remove the
caliper cylinder housing.
Front disc pads - renewalª
2Raise the front of the car and remove the
roadwheels.
3Check the thickness of the friction material
on the pads through the aperture in the caliper
cylinder body. If the thickness of the material
is 1.5 mm or less, then the pads on both sides
must be renewed (photo).
13•100 Supplement: Revisions and information on later models
14B.3 Front disc pads (arrowed) on Turbo
ie model14A.2B Front brake locking block
orientation with inboard retaining clip14A.2A Front brake pad locking block is
secured by a clip on the inboard end of the
brake unit on certain models
Fig. 13.101 Correct position of driveshaft damper weight on 1108 cc and 1372 cc ie
models (Sec 13)
Dimensions in mm
13.24 Right-hand driveshaft damper weight
13.21 Outer track reference groove
Page 226 of 303
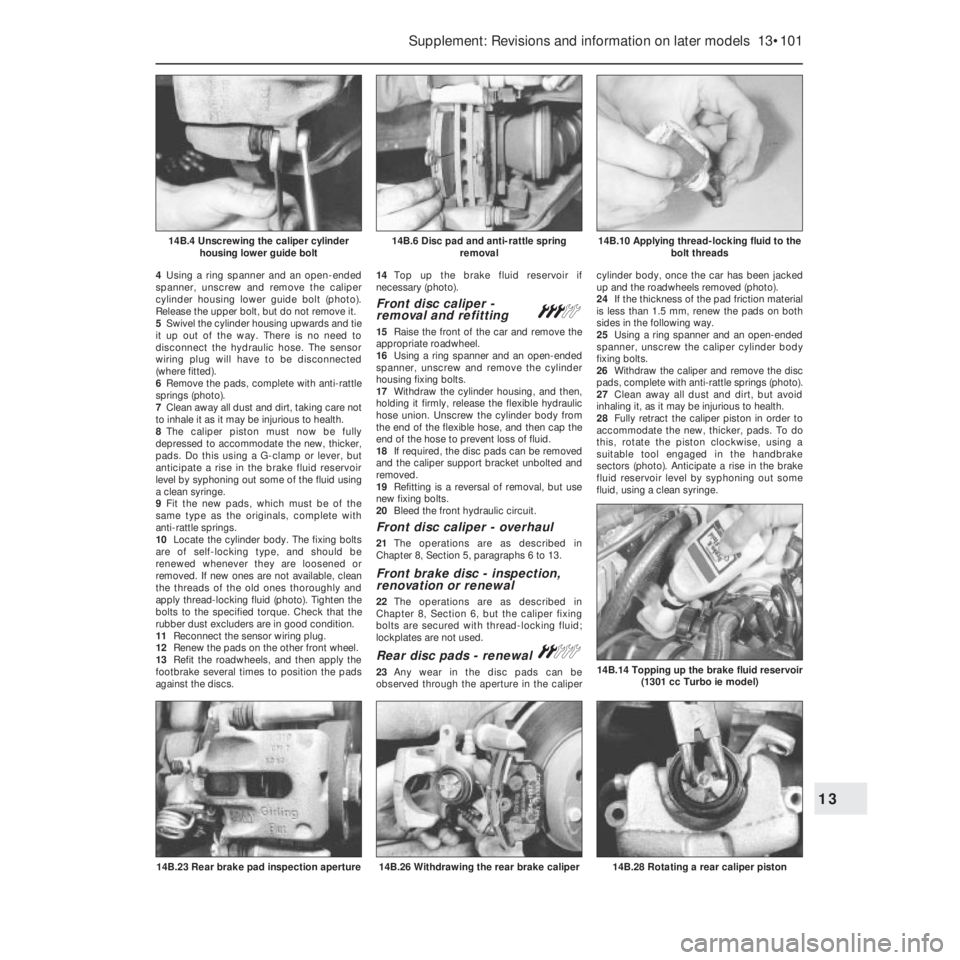
4Using a ring spanner and an open-ended
spanner, unscrew and remove the caliper
cylinder housing lower guide bolt (photo).
Release the upper bolt, but do not remove it.
5Swivel the cylinder housing upwards and tie
it up out of the way. There is no need to
disconnect the hydraulic hose. The sensor
wiring plug will have to be disconnected
(where fitted).
6Remove the pads, complete with anti-rattle
springs (photo).
7Clean away all dust and dirt, taking care not
to inhale it as it may be injurious to health.
8The caliper piston must now be fully
depressed to accommodate the new, thicker,
pads. Do this using a G-clamp or lever, but
anticipate a rise in the brake fluid reservoir
level by syphoning out some of the fluid using
a clean syringe.
9Fit the new pads, which must be of the
same type as the originals, complete with
anti-rattle springs.
10Locate the cylinder body. The fixing bolts
are of self-locking type, and should be
renewed whenever they are loosened or
removed. If new ones are not available, clean
the threads of the old ones thoroughly and
apply thread-locking fluid (photo). Tighten the
bolts to the specified torque. Check that the
rubber dust excluders are in good condition.
11Reconnect the sensor wiring plug.
12Renew the pads on the other front wheel.
13Refit the roadwheels, and then apply the
footbrake several times to position the pads
against the discs.14Top up the brake fluid reservoir if
necessary (photo).
Front disc caliper -
removal and refitting#
15Raise the front of the car and remove the
appropriate roadwheel.
16Using a ring spanner and an open-ended
spanner, unscrew and remove the cylinder
housing fixing bolts.
17Withdraw the cylinder housing, and then,
holding it firmly, release the flexible hydraulic
hose union. Unscrew the cylinder body from
the end of the flexible hose, and then cap the
end of the hose to prevent loss of fluid.
18If required, the disc pads can be removed
and the caliper support bracket unbolted and
removed.
19Refitting is a reversal of removal, but use
new fixing bolts.
20Bleed the front hydraulic circuit.
Front disc caliper - overhaul
21The operations are as described in
Chapter 8, Section 5, paragraphs 6 to 13.
Front brake disc - inspection,
renovation or renewal
22The operations are as described in
Chapter 8, Section 6, but the caliper fixing
bolts are secured with thread-locking fluid;
lockplates are not used.
Rear disc pads - renewal ª
23Any wear in the disc pads can be
observed through the aperture in the calipercylinder body, once the car has been jacked
up and the roadwheels removed (photo).
24If the thickness of the pad friction material
is less than 1.5 mm, renew the pads on both
sides in the following way.
25Using a ring spanner and an open-ended
spanner, unscrew the caliper cylinder body
fixing bolts.
26Withdraw the caliper and remove the disc
pads, complete with anti-rattle springs (photo).
27Clean away all dust and dirt, but avoid
inhaling it, as it may be injurious to health.
28Fully retract the caliper piston in order to
accommodate the new, thicker, pads. To do
this, rotate the piston clockwise, using a
suitable tool engaged in the handbrake
sectors (photo). Anticipate a rise in the brake
fluid reservoir level by syphoning out some
fluid, using a clean syringe.
Supplement: Revisions and information on later models 13•101
14B.10 Applying thread-locking fluid to the
bolt threads14B.6 Disc pad and anti-rattle spring
removal14B.4 Unscrewing the caliper cylinder
housing lower guide bolt
14B.28 Rotating a rear caliper piston14B.26 Withdrawing the rear brake caliper14B.23 Rear brake pad inspection aperture
14B.14 Topping up the brake fluid reservoir
(1301 cc Turbo ie model)
13
Page 227 of 303
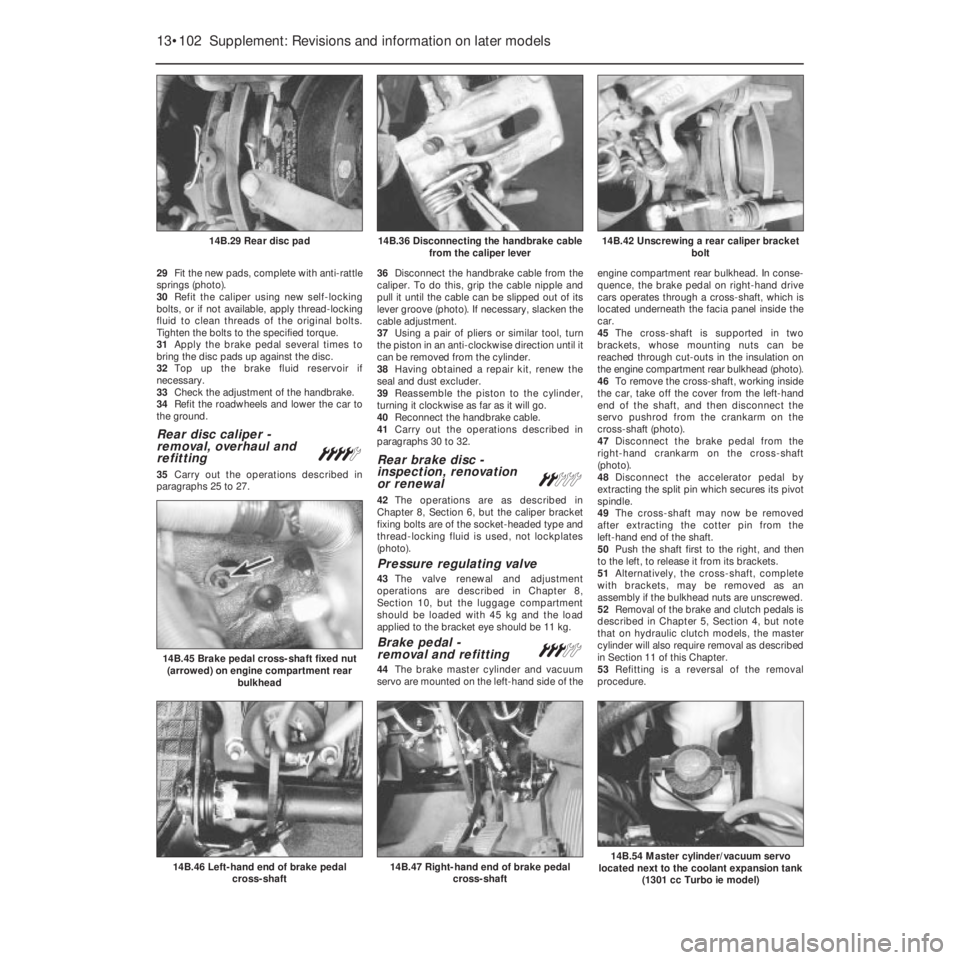
14B.54 Master cylinder/vacuum servo
located next to the coolant expansion tank
(1301 cc Turbo ie model)
29Fit the new pads, complete with anti-rattle
springs (photo).
30Refit the caliper using new self-locking
bolts, or if not available, apply thread-locking
fluid to clean threads of the original bolts.
Tighten the bolts to the specified torque.
31Apply the brake pedal several times to
bring the disc pads up against the disc.
32Top up the brake fluid reservoir if
necessary.
33Check the adjustment of the handbrake.
34Refit the roadwheels and lower the car to
the ground.
Rear disc caliper -
removal, overhaul and
refitting
¢
35Carry out the operations described in
paragraphs 25 to 27.36Disconnect the handbrake cable from the
caliper. To do this, grip the cable nipple and
pull it until the cable can be slipped out of its
lever groove (photo). If necessary, slacken the
cable adjustment.
37Using a pair of pliers or similar tool, turn
the piston in an anti-clockwise direction until it
can be removed from the cylinder.
38Having obtained a repair kit, renew the
seal and dust excluder.
39Reassemble the piston to the cylinder,
turning it clockwise as far as it will go.
40Reconnect the handbrake cable.
41Carry out the operations described in
paragraphs 30 to 32.
Rear brake disc -
inspection, renovation
or renewal
ª
42The operations are as described in
Chapter 8, Section 6, but the caliper bracket
fixing bolts are of the socket-headed type and
thread-locking fluid is used, not lockplates
(photo).
Pressure regulating valve
43The valve renewal and adjustment
operations are described in Chapter 8,
Section 10, but the luggage compartment
should be loaded with 45 kg and the load
applied to the bracket eye should be 11 kg.
Brake pedal -
removal and refitting#
44The brake master cylinder and vacuum
servo are mounted on the left-hand side of theengine compartment rear bulkhead. In conse-
quence, the brake pedal on right-hand drive
cars operates through a cross-shaft, which is
located underneath the facia panel inside the
car.
45The cross-shaft is supported in two
brackets, whose mounting nuts can be
reached through cut-outs in the insulation on
the engine compartment rear bulkhead (photo).
46To remove the cross-shaft, working inside
the car, take off the cover from the left-hand
end of the shaft, and then disconnect the
servo pushrod from the crankarm on the
cross-shaft (photo).
47Disconnect the brake pedal from the
right-hand crankarm on the cross-shaft
(photo).
48Disconnect the accelerator pedal by
extracting the split pin which secures its pivot
spindle.
49The cross-shaft may now be removed
after extracting the cotter pin from the
left-hand end of the shaft.
50Push the shaft first to the right, and then
to the left, to release it from its brackets.
51Alternatively, the cross-shaft, complete
with brackets, may be removed as an
assembly if the bulkhead nuts are unscrewed.
52Removal of the brake and clutch pedals is
described in Chapter 5, Section 4, but note
that on hydraulic clutch models, the master
cylinder will also require removal as described
in Section 11 of this Chapter.
53Refitting is a reversal of the removal
procedure.
13•102 Supplement: Revisions and information on later models
14B.47 Right-hand end of brake pedal
cross-shaft14B.46 Left-hand end of brake pedal
cross-shaft
14B.45 Brake pedal cross-shaft fixed nut
(arrowed) on engine compartment rear
bulkhead
14B.42 Unscrewing a rear caliper bracket
bolt14B.36 Disconnecting the handbrake cable
from the caliper lever14B.29 Rear disc pad
Page 228 of 303
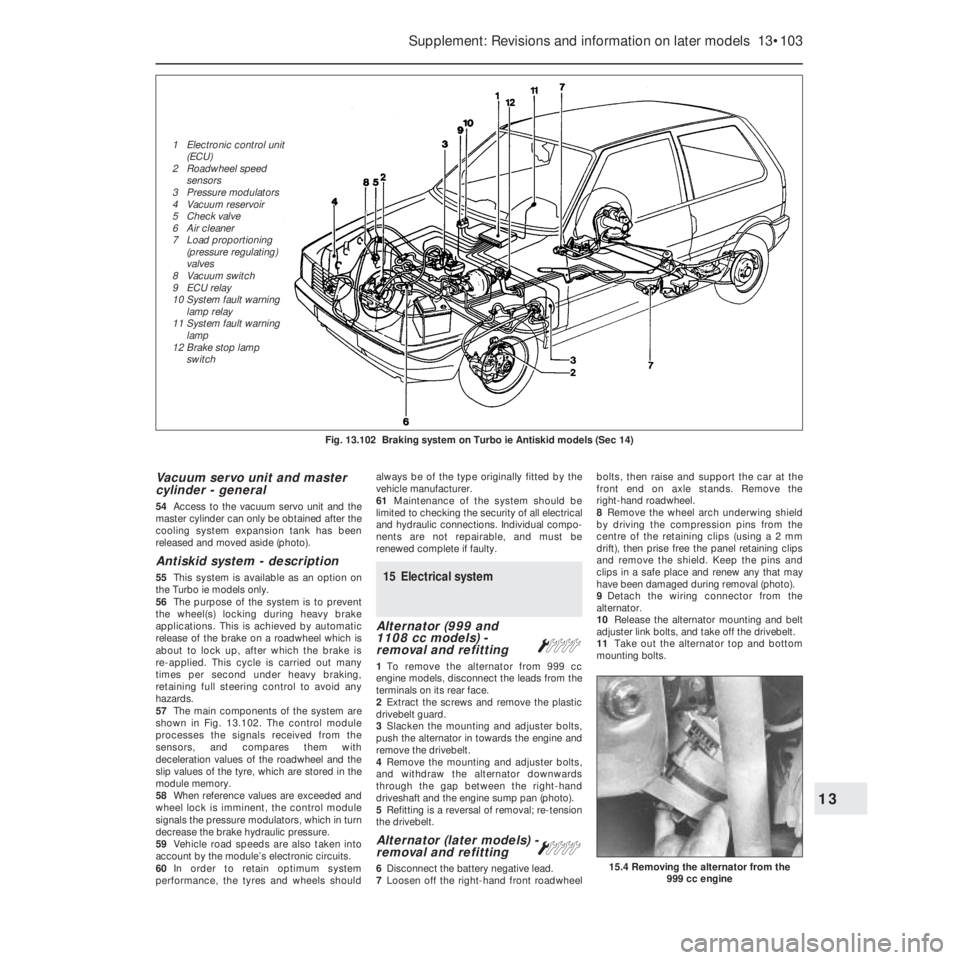
Vacuum servo unit and master
cylinder - general
54Access to the vacuum servo unit and the
master cylinder can only be obtained after the
cooling system expansion tank has been
released and moved aside (photo).
Antiskid system - description
55This system is available as an option on
the Turbo ie models only.
56The purpose of the system is to prevent
the wheel(s) locking during heavy brake
applications. This is achieved by automatic
release of the brake on a roadwheel which is
about to lock up, after which the brake is
re-applied. This cycle is carried out many
times per second under heavy braking,
retaining full steering control to avoid any
hazards.
57The main components of the system are
shown in Fig. 13.102. The control module
processes the signals received from the
sensors, and compares them with
deceleration values of the roadwheel and the
slip values of the tyre, which are stored in the
module memory.
58When reference values are exceeded and
wheel lock is imminent, the control module
signals the pressure modulators, which in turn
decrease the brake hydraulic pressure.
59Vehicle road speeds are also taken into
account by the module’s electronic circuits.
60In order to retain optimum system
performance, the tyres and wheels shouldalways be of the type originally fitted by the
vehicle manufacturer.
61Maintenance of the system should be
limited to checking the security of all electrical
and hydraulic connections. Individual compo-
nents are not repairable, and must be
renewed complete if faulty.15 Electrical system
Alternator (999 and
1108 cc models) -
removal and refitting
Á
1To remove the alternator from 999 cc
engine models, disconnect the leads from the
terminals on its rear face.
2Extract the screws and remove the plastic
drivebelt guard.
3Slacken the mounting and adjuster bolts,
push the alternator in towards the engine and
remove the drivebelt.
4Remove the mounting and adjuster bolts,
and withdraw the alternator downwards
through the gap between the right-hand
driveshaft and the engine sump pan (photo).
5Refitting is a reversal of removal; re-tension
the drivebelt.
Alternator (later models) -
removal and refitting Á
6Disconnect the battery negative lead.
7Loosen off the right-hand front roadwheelbolts, then raise and support the car at the
front end on axle stands. Remove the
right-hand roadwheel.
8Remove the wheel arch underwing shield
by driving the compression pins from the
centre of the retaining clips (using a 2 mm
drift), then prise free the panel retaining clips
and remove the shield. Keep the pins and
clips in a safe place and renew any that may
have been damaged during removal (photo).
9Detach the wiring connector from the
alternator.
10Release the alternator mounting and belt
adjuster link bolts, and take off the drivebelt.
11Take out the alternator top and bottom
mounting bolts.
Supplement: Revisions and information on later models 13•103
15.4 Removing the alternator from the
999 cc engine
Fig. 13.102 Braking system on Turbo ie Antiskid models (Sec 14)
13
1 Electronic control unit
(ECU)
2 Roadwheel speed
sensors
3 Pressure modulators
4 Vacuum reservoir
5 Check valve
6 Air cleaner
7 Load proportioning
(pressure regulating)
valves
8 Vacuum switch
9 ECU relay
10 System fault warning
lamp relay
11 System fault warning
lamp
12 Brake stop lamp
switch
Page 229 of 303
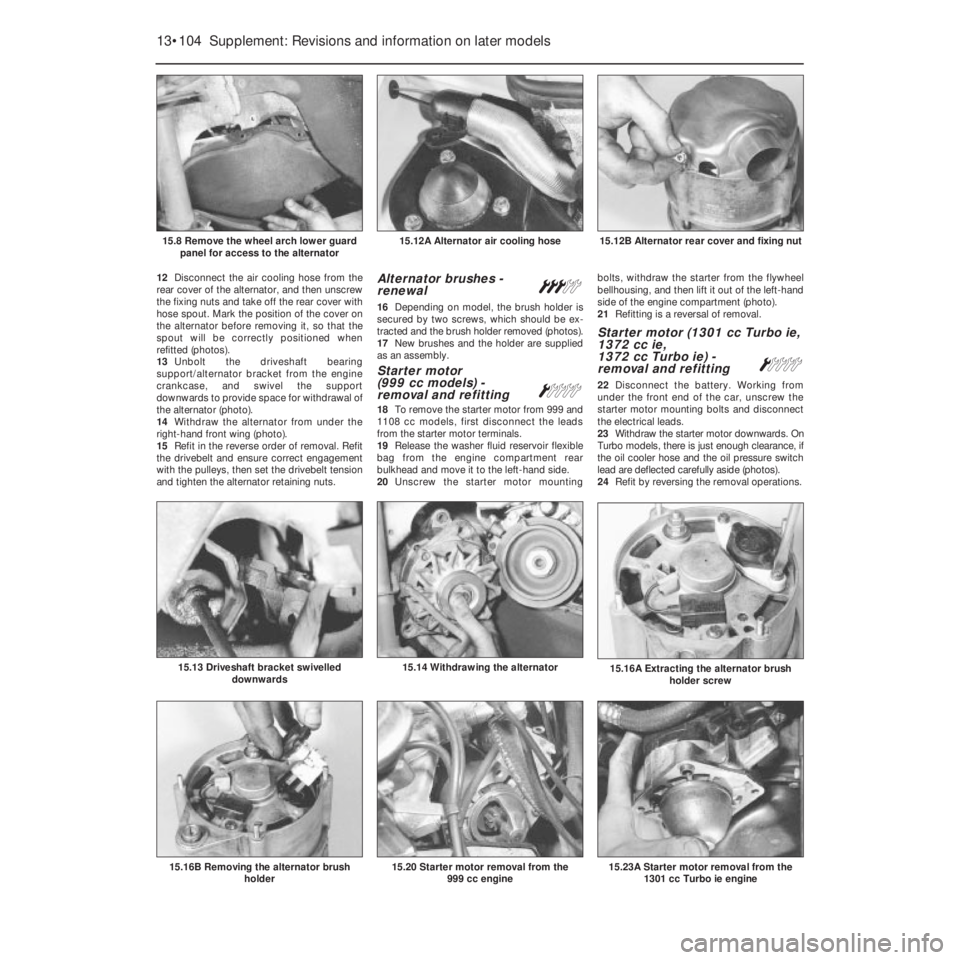
15.23A Starter motor removal from the
1301 cc Turbo ie engine15.20 Starter motor removal from the
999 cc engine
12Disconnect the air cooling hose from the
rear cover of the alternator, and then unscrew
the fixing nuts and take off the rear cover with
hose spout. Mark the position of the cover on
the alternator before removing it, so that the
spout will be correctly positioned when
refitted (photos).
13Unbolt the driveshaft bearing
support/alternator bracket from the engine
crankcase, and swivel the support
downwards to provide space for withdrawal of
the alternator (photo).
14Withdraw the alternator from under the
right-hand front wing (photo).
15Refit in the reverse order of removal. Refit
the drivebelt and ensure correct engagement
with the pulleys, then set the drivebelt tension
and tighten the alternator retaining nuts.Alternator brushes -
renewal#
16Depending on model, the brush holder is
secured by two screws, which should be ex-
tracted and the brush holder removed (photos).
17New brushes and the holder are supplied
as an assembly.
Starter motor
(999 cc models) -
removal and refitting
Á
18To remove the starter motor from 999 and
1108 cc models, first disconnect the leads
from the starter motor terminals.
19Release the washer fluid reservoir flexible
bag from the engine compartment rear
bulkhead and move it to the left-hand side.
20Unscrew the starter motor mountingbolts, withdraw the starter from the flywheel
bellhousing, and then lift it out of the left-hand
side of the engine compartment (photo).
21Refitting is a reversal of removal.
Starter motor (1301 cc Turbo ie,
1372 cc ie,
1372 cc Turbo ie) -
removal and refitting
Á
22Disconnect the battery. Working from
under the front end of the car, unscrew the
starter motor mounting bolts and disconnect
the electrical leads.
23Withdraw the starter motor downwards. On
Turbo models, there is just enough clearance, if
the oil cooler hose and the oil pressure switch
lead are deflected carefully aside (photos).
24Refit by reversing the removal operations.
13•104 Supplement: Revisions and information on later models
15.16B Removing the alternator brush
holder
15.16A Extracting the alternator brush
holder screw15.14 Withdrawing the alternator15.13 Driveshaft bracket swivelled
downwards
15.12B Alternator rear cover and fixing nut15.12A Alternator air cooling hose15.8 Remove the wheel arch lower guard
panel for access to the alternator
Page 230 of 303
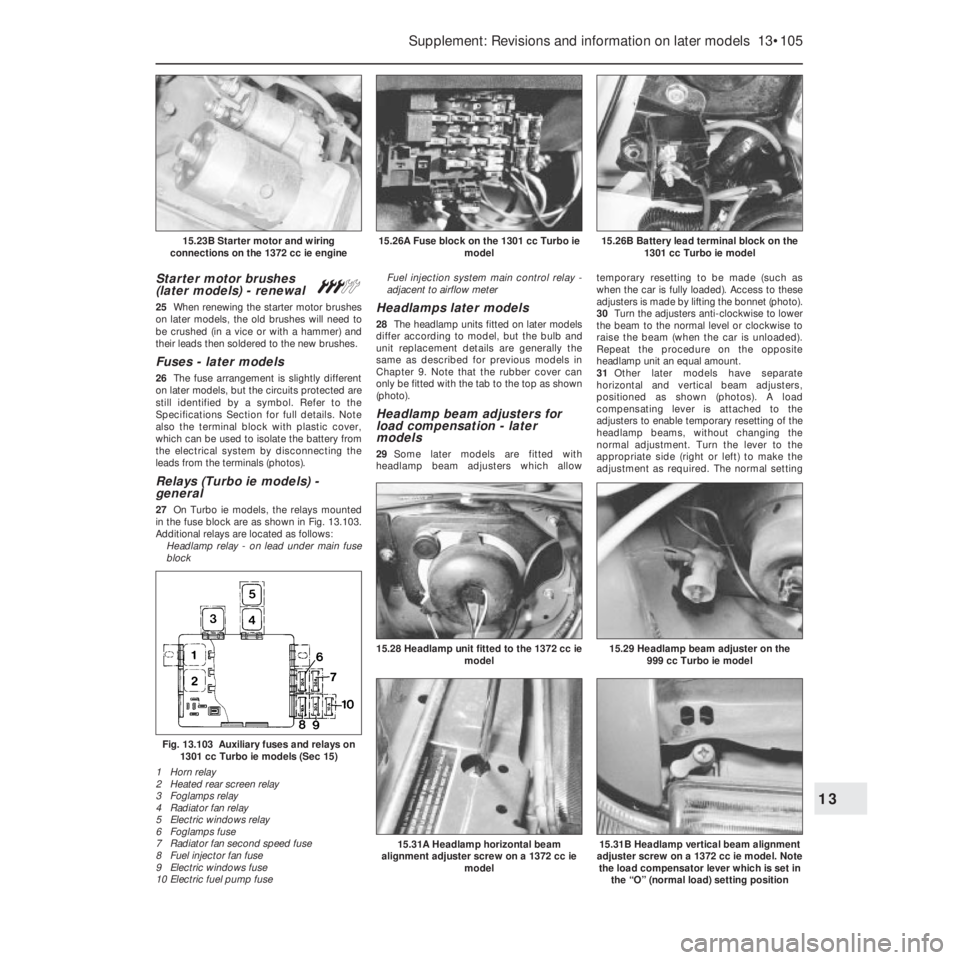
Starter motor brushes
(later models) - renewal#
25When renewing the starter motor brushes
on later models, the old brushes will need to
be crushed (in a vice or with a hammer) and
their leads then soldered to the new brushes.
Fuses - later models
26The fuse arrangement is slightly different
on later models, but the circuits protected are
still identified by a symbol. Refer to the
Specifications Section for full details. Note
also the terminal block with plastic cover,
which can be used to isolate the battery from
the electrical system by disconnecting the
leads from the terminals (photos).
Relays (Turbo ie models) -
general
27On Turbo ie models, the relays mounted
in the fuse block are as shown in Fig. 13.103.
Additional relays are located as follows:
Headlamp relay - on lead under main fuse
blockFuel injection system main control relay -
adjacent to airflow meter
Headlamps later models
28The headlamp units fitted on later models
differ according to model, but the bulb and
unit replacement details are generally the
same as described for previous models in
Chapter 9. Note that the rubber cover can
only be fitted with the tab to the top as shown
(photo).
Headlamp beam adjusters for
load compensation - later
models
29Some later models are fitted with
headlamp beam adjusters which allowtemporary resetting to be made (such as
when the car is fully loaded). Access to these
adjusters is made by lifting the bonnet (photo).
30Turn the adjusters anti-clockwise to lower
the beam to the normal level or clockwise to
raise the beam (when the car is unloaded).
Repeat the procedure on the opposite
headlamp unit an equal amount.
31Other later models have separate
horizontal and vertical beam adjusters,
positioned as shown (photos). A load
compensating lever is attached to the
adjusters to enable temporary resetting of the
headlamp beams, without changing the
normal adjustment. Turn the lever to the
appropriate side (right or left) to make the
adjustment as required. The normal setting
Supplement: Revisions and information on later models 13•105
15.26B Battery lead terminal block on the
1301 cc Turbo ie model15.23B Starter motor and wiring
connections on the 1372 cc ie engine
15.31B Headlamp vertical beam alignment
adjuster screw on a 1372 cc ie model. Note
the load compensator lever which is set in
the “O” (normal load) setting position15.31A Headlamp horizontal beam
alignment adjuster screw on a 1372 cc ie
model
15.29 Headlamp beam adjuster on the
999 cc Turbo ie model15.28 Headlamp unit fitted to the 1372 cc ie
model
15.26A Fuse block on the 1301 cc Turbo ie
model
13
Fig. 13.103 Auxiliary fuses and relays on
1301 cc Turbo ie models (Sec 15)
1 Horn relay
2 Heated rear screen relay
3 Foglamps relay
4 Radiator fan relay
5 Electric windows relay
6 Foglamps fuse
7 Radiator fan second speed fuse
8 Fuel injector fan fuse
9 Electric windows fuse
10 Electric fuel pump fuse