FIAT UNO 1983 Service Owner's Manual
Manufacturer: FIAT, Model Year: 1983, Model line: UNO, Model: FIAT UNO 1983Pages: 303, PDF Size: 10.36 MB
Page 21 of 303
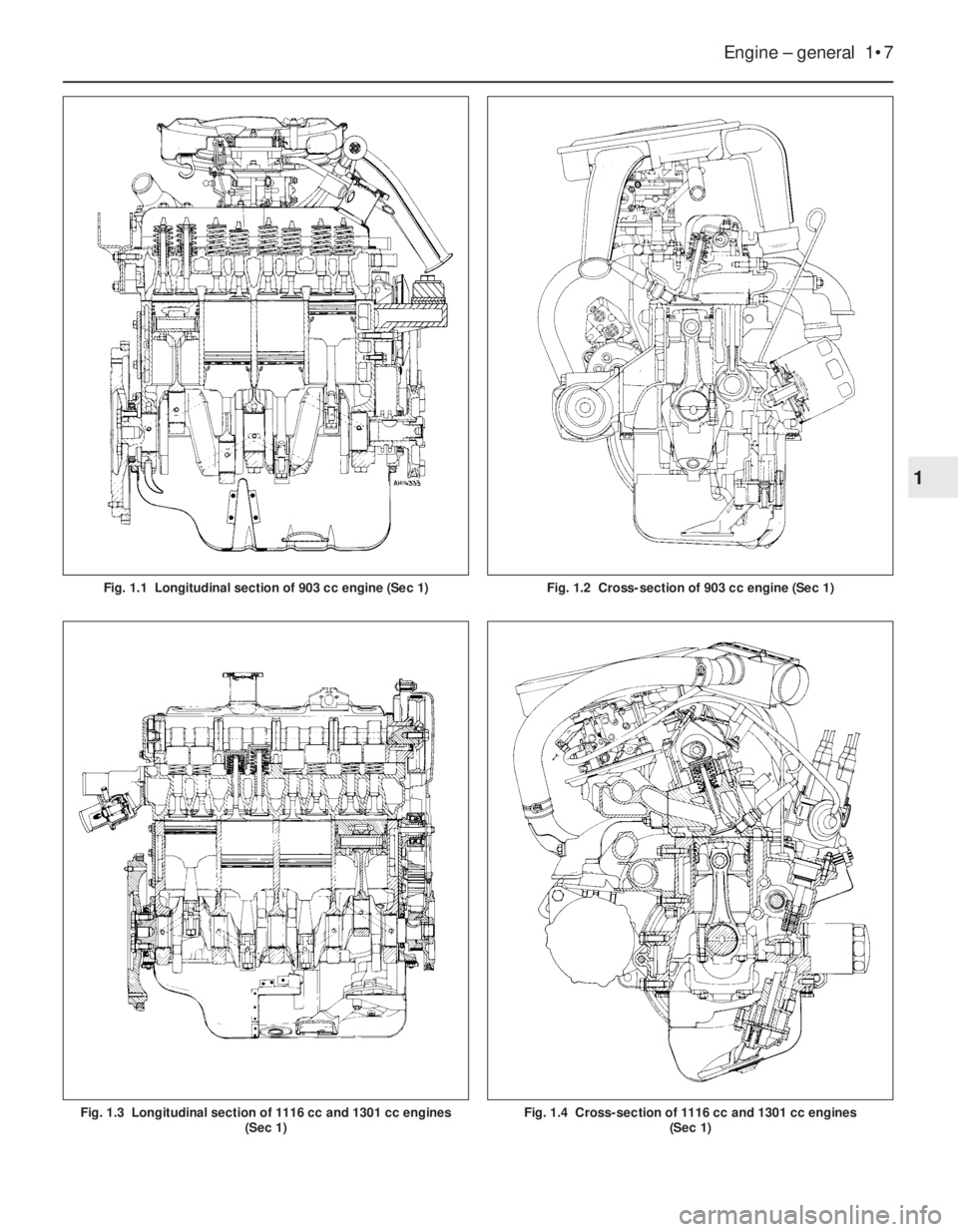
Engine – general 1•7
Fig. 1.1 Longitudinal section of 903 cc engine (Sec 1)
Fig. 1.3 Longitudinal section of 1116 cc and 1301 cc engines
(Sec 1)
Fig. 1.2 Cross-section of 903 cc engine (Sec 1)
Fig. 1.4 Cross-section of 1116 cc and 1301 cc engines
(Sec 1)
1
Page 22 of 303
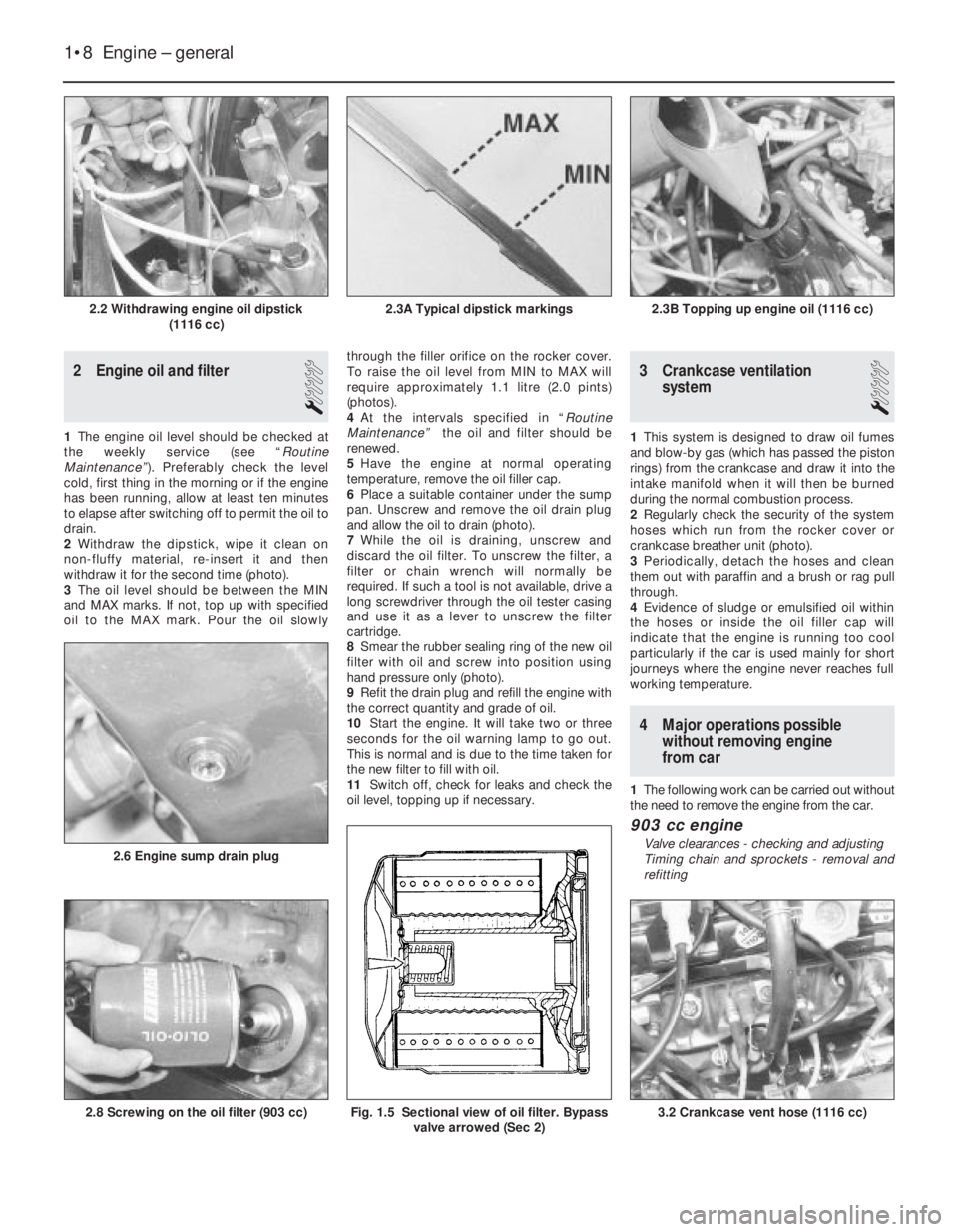
2 Engine oil and filter
1
1The engine oil level should be checked at
the weekly service (see “Routine
Maintenance”). Preferably check the level
cold, first thing in the morning or if the engine
has been running, allow at least ten minutes
to elapse after switching off to permit the oil to
drain.
2Withdraw the dipstick, wipe it clean on
non-fluffy material, re-insert it and then
withdraw it for the second time (photo).
3The oil level should be between the MIN
and MAX marks. If not, top up with specified
oil to the MAX mark. Pour the oil slowlythrough the filler orifice on the rocker cover.
To raise the oil level from MIN to MAX will
require approximately 1.1 litre (2.0 pints)
(photos).
4At the intervals specified in “Routine
Maintenance” the oil and filter should be
renewed.
5Have the engine at normal operating
temperature, remove the oil filler cap.
6Place a suitable container under the sump
pan. Unscrew and remove the oil drain plug
and allow the oil to drain (photo).
7While the oil is draining, unscrew and
discard the oil filter. To unscrew the filter, a
filter or chain wrench will normally be
required. If such a tool is not available, drive a
long screwdriver through the oil tester casing
and use it as a lever to unscrew the filter
cartridge.
8Smear the rubber sealing ring of the new oil
filter with oil and screw into position using
hand pressure only (photo).
9Refit the drain plug and refill the engine with
the correct quantity and grade of oil.
10Start the engine. It will take two or three
seconds for the oil warning lamp to go out.
This is normal and is due to the time taken for
the new filter to fill with oil.
11Switch off, check for leaks and check the
oil level, topping up if necessary.
3 Crankcase ventilation
system
1
1This system is designed to draw oil fumes
and blow-by gas (which has passed the piston
rings) from the crankcase and draw it into the
intake manifold when it will then be burned
during the normal combustion process.
2Regularly check the security of the system
hoses which run from the rocker cover or
crankcase breather unit (photo).
3Periodically, detach the hoses and clean
them out with paraffin and a brush or rag pull
through.
4Evidence of sludge or emulsified oil within
the hoses or inside the oil filler cap will
indicate that the engine is running too cool
particularly if the car is used mainly for short
journeys where the engine never reaches full
working temperature.
4 Major operations possible
without removing engine
from car
1The following work can be carried out without
the need to remove the engine from the car.
903 cc engine
Valve clearances - checking and adjusting
Timing chain and sprockets - removal and
refitting
1•8 Engine – general
3.2 Crankcase vent hose (1116 cc)Fig. 1.5 Sectional view of oil filter. Bypass
valve arrowed (Sec 2)2.8 Screwing on the oil filter (903 cc)
2.6 Engine sump drain plug
2.3B Topping up engine oil (1116 cc)2.3A Typical dipstick markings2.2 Withdrawing engine oil dipstick
(1116 cc)
Page 23 of 303
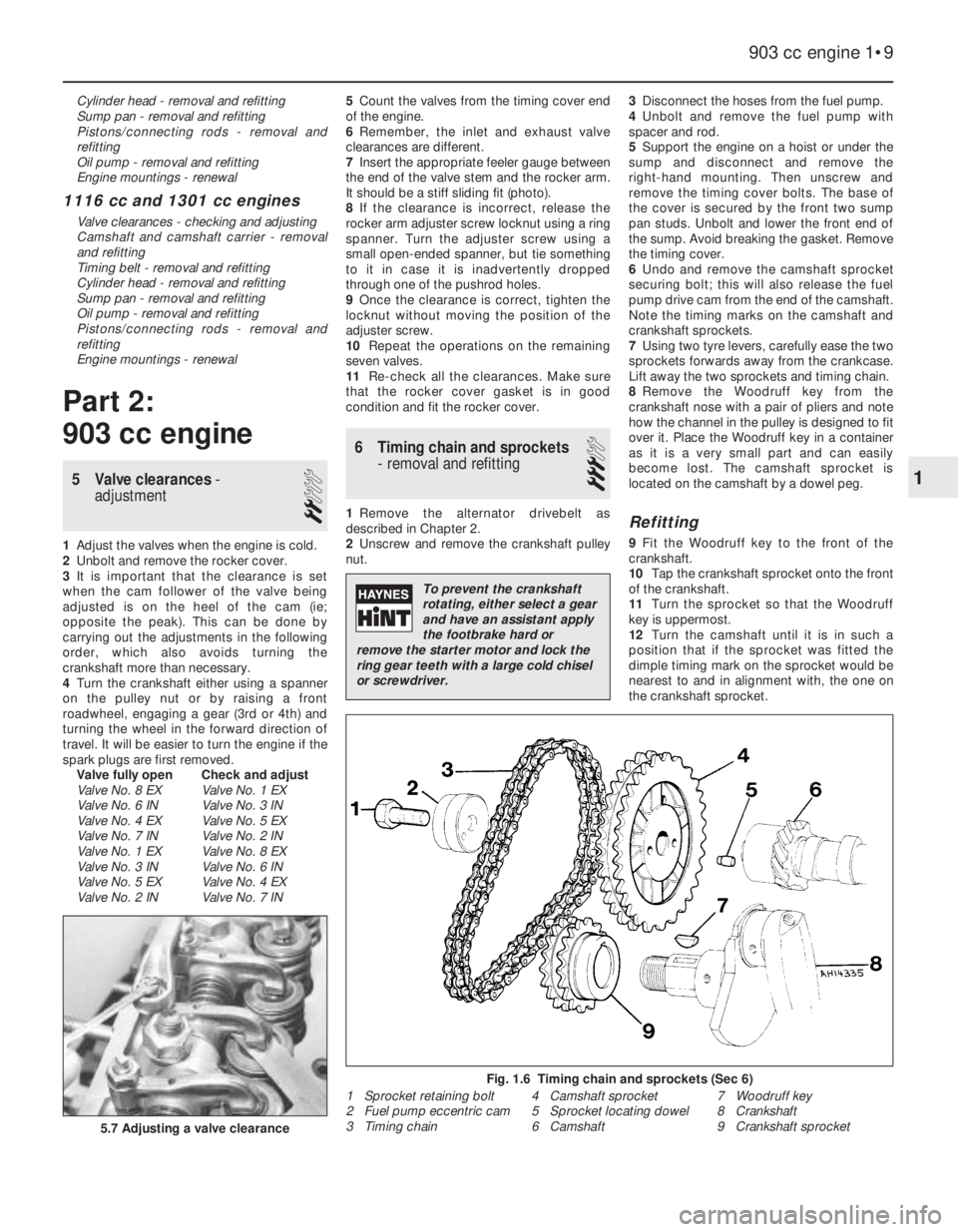
Cylinder head - removal and refitting
Sump pan - removal and refitting
Pistons/connecting rods - removal and
refitting
Oil pump - removal and refitting
Engine mountings - renewal
1116 cc and 1301 cc engines
Valve clearances - checking and adjusting
Camshaft and camshaft carrier - removal
and refitting
Timing belt - removal and refitting
Cylinder head - removal and refitting
Sump pan - removal and refitting
Oil pump - removal and refitting
Pistons/connecting rods - removal and
refitting
Engine mountings - renewal
Part 2:
903 cc engine
5 Valve clearances-
adjustment
2
1Adjust the valves when the engine is cold.
2Unbolt and remove the rocker cover.
3It is important that the clearance is set
when the cam follower of the valve being
adjusted is on the heel of the cam (ie;
opposite the peak). This can be done by
carrying out the adjustments in the following
order, which also avoids turning the
crankshaft more than necessary.
4Turn the crankshaft either using a spanner
on the pulley nut or by raising a front
roadwheel, engaging a gear (3rd or 4th) and
turning the wheel in the forward direction of
travel. It will be easier to turn the engine if the
spark plugs are first removed.
Valve fully open Check and adjust
Valve No. 8 EX Valve No. 1 EX
Valve No. 6 IN Valve No. 3 IN
Valve No. 4 EX Valve No. 5 EX
Valve No. 7 IN Valve No. 2 IN
Valve No. 1 EX Valve No. 8 EX
Valve No. 3 IN Valve No. 6 IN
Valve No. 5 EX Valve No. 4 EX
Valve No. 2 IN Valve No. 7 IN5Count the valves from the timing cover end
of the engine.
6Remember, the inlet and exhaust valve
clearances are different.
7Insert the appropriate feeler gauge between
the end of the valve stem and the rocker arm.
It should be a stiff sliding fit (photo).
8If the clearance is incorrect, release the
rocker arm adjuster screw locknut using a ring
spanner. Turn the adjuster screw using a
small open-ended spanner, but tie something
to it in case it is inadvertently dropped
through one of the pushrod holes.
9Once the clearance is correct, tighten the
locknut without moving the position of the
adjuster screw.
10Repeat the operations on the remaining
seven valves.
11Re-check all the clearances. Make sure
that the rocker cover gasket is in good
condition and fit the rocker cover.
6 Timing chain and sprockets
- removal and refitting
3
1Remove the alternator drivebelt as
described in Chapter 2.
2Unscrew and remove the crankshaft pulley
nut.3Disconnect the hoses from the fuel pump.
4Unbolt and remove the fuel pump with
spacer and rod.
5Support the engine on a hoist or under the
sump and disconnect and remove the
right-hand mounting. Then unscrew and
remove the timing cover bolts. The base of
the cover is secured by the front two sump
pan studs. Unbolt and lower the front end of
the sump. Avoid breaking the gasket. Remove
the timing cover.
6Undo and remove the camshaft sprocket
securing bolt; this will also release the fuel
pump drive cam from the end of the camshaft.
Note the timing marks on the camshaft and
crankshaft sprockets.
7Using two tyre levers, carefully ease the two
sprockets forwards away from the crankcase.
Lift away the two sprockets and timing chain.
8Remove the Woodruff key from the
crankshaft nose with a pair of pliers and note
how the channel in the pulley is designed to fit
over it. Place the Woodruff key in a container
as it is a very small part and can easily
become lost. The camshaft sprocket is
located on the camshaft by a dowel peg.Refitting
9Fit the Woodruff key to the front of the
crankshaft.
10Tap the crankshaft sprocket onto the front
of the crankshaft.
11Turn the sprocket so that the Woodruff
key is uppermost.
12Turn the camshaft until it is in such a
position that if the sprocket was fitted the
dimple timing mark on the sprocket would be
nearest to and in alignment with, the one on
the crankshaft sprocket.
903 cc engine 1•9
5.7 Adjusting a valve clearance
1 Sprocket retaining bolt
2 Fuel pump eccentric cam
3 Timing chain4 Camshaft sprocket
5 Sprocket locating dowel
6 Camshaft7 Woodruff key
8 Crankshaft
9 Crankshaft sprocket
Fig. 1.6 Timing chain and sprockets (Sec 6)
1
To prevent the crankshaft
rotating, either select a gear
and have an assistant apply
the footbrake hard or
remove the starter motor and lock the
ring gear teeth with a large cold chisel
or screwdriver.
Page 24 of 303
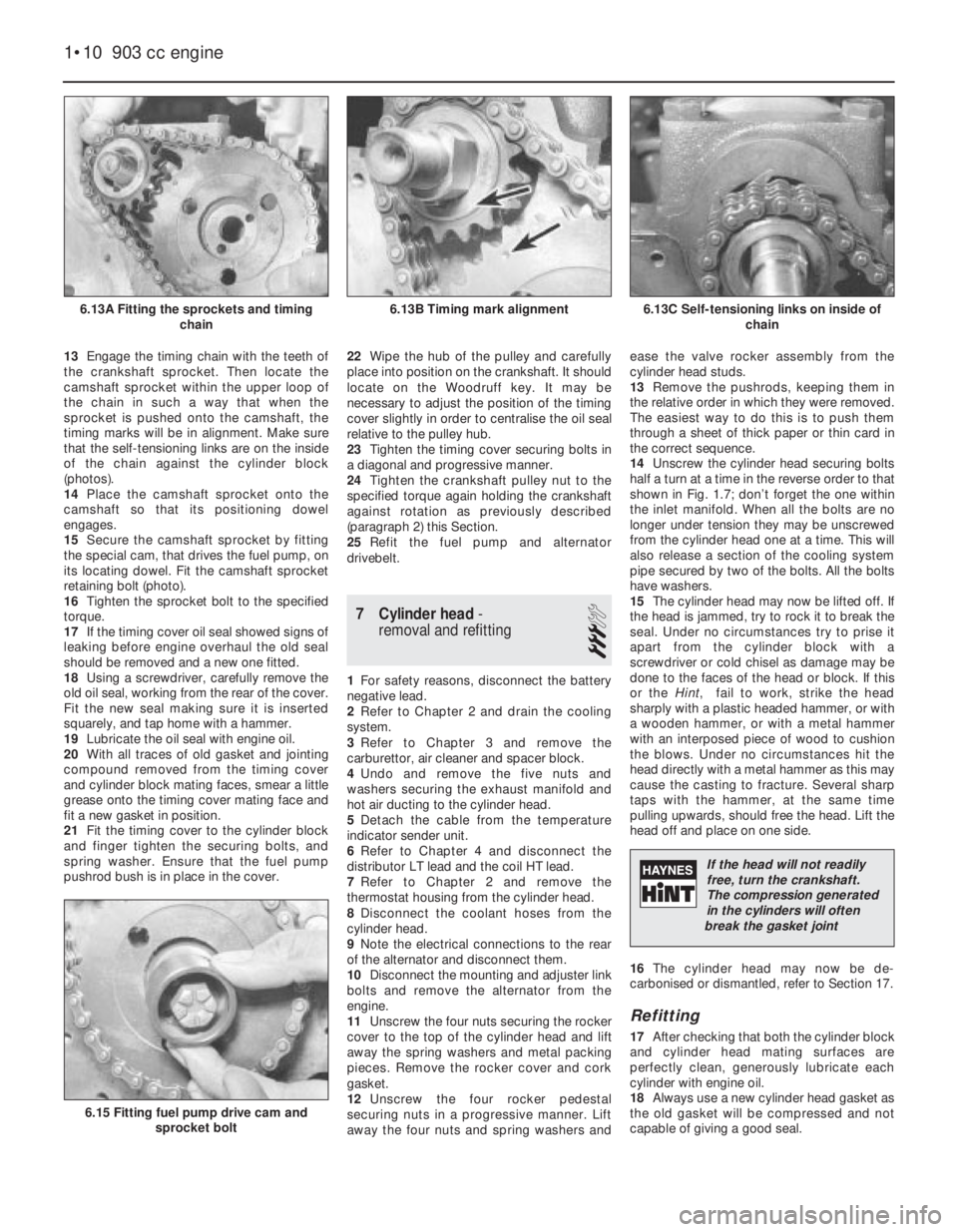
13Engage the timing chain with the teeth of
the crankshaft sprocket. Then locate the
camshaft sprocket within the upper loop of
the chain in such a way that when the
sprocket is pushed onto the camshaft, the
timing marks will be in alignment. Make sure
that the self-tensioning links are on the inside
of the chain against the cylinder block
(photos).
14Place the camshaft sprocket onto the
camshaft so that its positioning dowel
engages.
15Secure the camshaft sprocket by fitting
the special cam, that drives the fuel pump, on
its locating dowel. Fit the camshaft sprocket
retaining bolt (photo).
16Tighten the sprocket bolt to the specified
torque.
17If the timing cover oil seal showed signs of
leaking before engine overhaul the old seal
should be removed and a new one fitted.
18Using a screwdriver, carefully remove the
old oil seal, working from the rear of the cover.
Fit the new seal making sure it is inserted
squarely, and tap home with a hammer.
19Lubricate the oil seal with engine oil.
20With all traces of old gasket and jointing
compound removed from the timing cover
and cylinder block mating faces, smear a little
grease onto the timing cover mating face and
fit a new gasket in position.
21Fit the timing cover to the cylinder block
and finger tighten the securing bolts, and
spring washer. Ensure that the fuel pump
pushrod bush is in place in the cover.22Wipe the hub of the pulley and carefully
place into position on the crankshaft. It should
locate on the Woodruff key. It may be
necessary to adjust the position of the timing
cover slightly in order to centralise the oil seal
relative to the pulley hub.
23Tighten the timing cover securing bolts in
a diagonal and progressive manner.
24Tighten the crankshaft pulley nut to the
specified torque again holding the crankshaft
against rotation as previously described
(paragraph 2) this Section.
25Refit the fuel pump and alternator
drivebelt.
7 Cylinder head-
removal and refitting
3
1For safety reasons, disconnect the battery
negative lead.
2Refer to Chapter 2 and drain the cooling
system.
3Refer to Chapter 3 and remove the
carburettor, air cleaner and spacer block.
4Undo and remove the five nuts and
washers securing the exhaust manifold and
hot air ducting to the cylinder head.
5Detach the cable from the temperature
indicator sender unit.
6Refer to Chapter 4 and disconnect the
distributor LT lead and the coil HT lead.
7Refer to Chapter 2 and remove the
thermostat housing from the cylinder head.
8Disconnect the coolant hoses from the
cylinder head.
9Note the electrical connections to the rear
of the alternator and disconnect them.
10Disconnect the mounting and adjuster link
bolts and remove the alternator from the
engine.
11Unscrew the four nuts securing the rocker
cover to the top of the cylinder head and lift
away the spring washers and metal packing
pieces. Remove the rocker cover and cork
gasket.
12Unscrew the four rocker pedestal
securing nuts in a progressive manner. Lift
away the four nuts and spring washers andease the valve rocker assembly from the
cylinder head studs.
13Remove the pushrods, keeping them in
the relative order in which they were removed.
The easiest way to do this is to push them
through a sheet of thick paper or thin card in
the correct sequence.
14Unscrew the cylinder head securing bolts
half a turn at a time in the reverse order to that
shown in Fig. 1.7; don’t forget the one within
the inlet manifold. When all the bolts are no
longer under tension they may be unscrewed
from the cylinder head one at a time. This will
also release a section of the cooling system
pipe secured by two of the bolts. All the bolts
have washers.
15The cylinder head may now be lifted off. If
the head is jammed, try to rock it to break the
seal. Under no circumstances try to prise it
apart from the cylinder block with a
screwdriver or cold chisel as damage may be
done to the faces of the head or block. If this
or the Hint, fail to work, strike the head
sharply with a plastic headed hammer, or with
a wooden hammer, or with a metal hammer
with an interposed piece of wood to cushion
the blows. Under no circumstances hit the
head directly with a metal hammer as this may
cause the casting to fracture. Several sharp
taps with the hammer, at the same time
pulling upwards, should free the head. Lift the
head off and place on one side.
16The cylinder head may now be de-
carbonised or dismantled, refer to Section 17.
Refitting
17After checking that both the cylinder block
and cylinder head mating surfaces are
perfectly clean, generously lubricate each
cylinder with engine oil.
18Always use a new cylinder head gasket as
the old gasket will be compressed and not
capable of giving a good seal.
1•10 903 cc engine
6.15 Fitting fuel pump drive cam and
sprocket bolt
6.13C Self-tensioning links on inside of
chain6.13B Timing mark alignment6.13A Fitting the sprockets and timing
chain
If the head will not readily
free, turn the crankshaft.
The compression generated
in the cylinders will often
break the gasket joint
Page 25 of 303
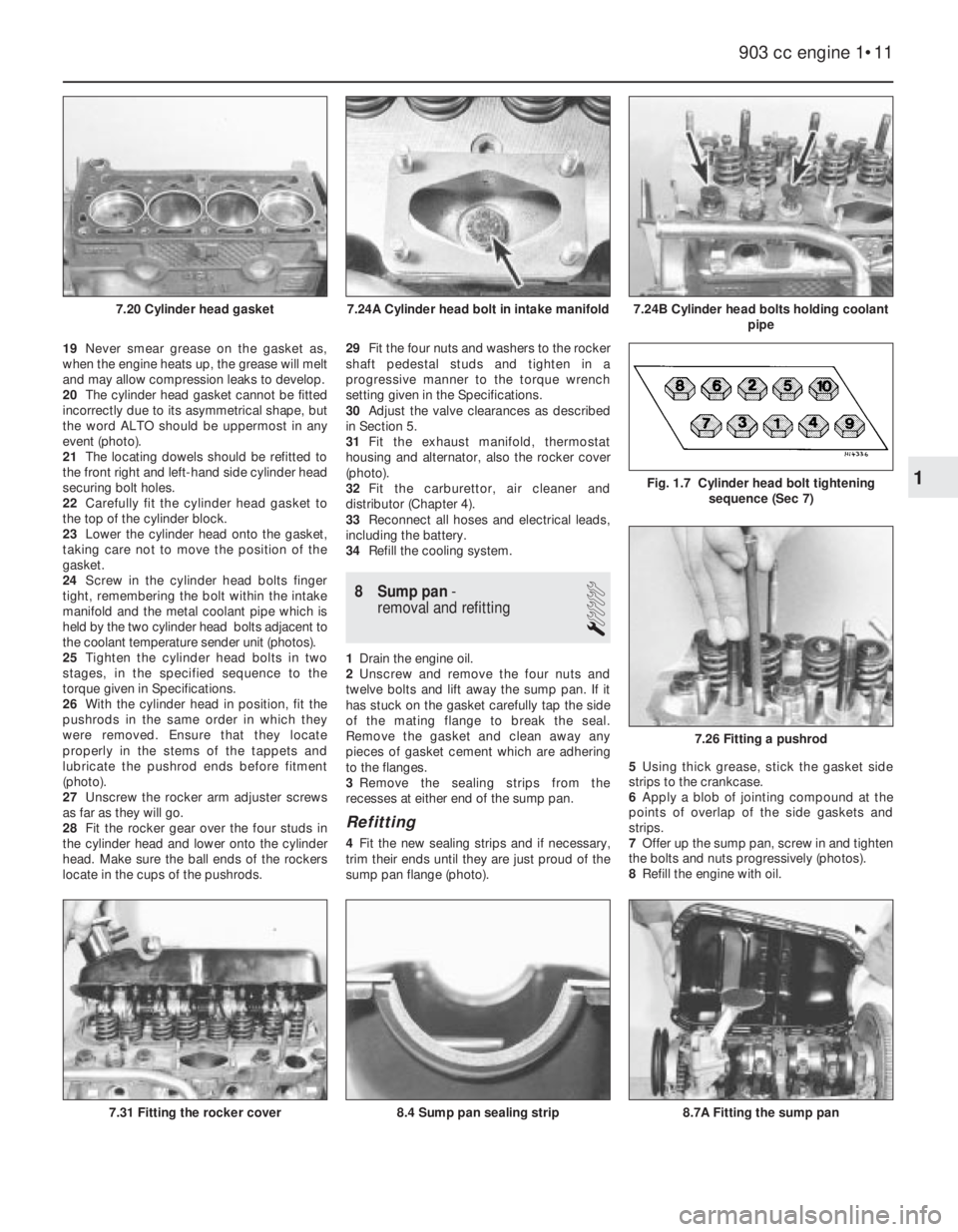
19Never smear grease on the gasket as,
when the engine heats up, the grease will melt
and may allow compression leaks to develop.
20The cylinder head gasket cannot be fitted
incorrectly due to its asymmetrical shape, but
the word ALTO should be uppermost in any
event (photo).
21The locating dowels should be refitted to
the front right and left-hand side cylinder head
securing bolt holes.
22Carefully fit the cylinder head gasket to
the top of the cylinder block.
23Lower the cylinder head onto the gasket,
taking care not to move the position of the
gasket.
24Screw in the cylinder head bolts finger
tight, remembering the bolt within the intake
manifold and the metal coolant pipe which is
held by the two cylinder head bolts adjacent to
the coolant temperature sender unit (photos).
25Tighten the cylinder head bolts in two
stages, in the specified sequence to the
torque given in Specifications.
26With the cylinder head in position, fit the
pushrods in the same order in which they
were removed. Ensure that they locate
properly in the stems of the tappets and
lubricate the pushrod ends before fitment
(photo).
27Unscrew the rocker arm adjuster screws
as far as they will go.
28Fit the rocker gear over the four studs in
the cylinder head and lower onto the cylinder
head. Make sure the ball ends of the rockers
locate in the cups of the pushrods.29Fit the four nuts and washers to the rocker
shaft pedestal studs and tighten in a
progressive manner to the torque wrench
setting given in the Specifications.
30Adjust the valve clearances as described
in Section 5.
31Fit the exhaust manifold, thermostat
housing and alternator, also the rocker cover
(photo).
32Fit the carburettor, air cleaner and
distributor (Chapter 4).
33Reconnect all hoses and electrical leads,
including the battery.
34Refill the cooling system.
8 Sump pan-
removal and refitting
1
1Drain the engine oil.
2Unscrew and remove the four nuts and
twelve bolts and lift away the sump pan. If it
has stuck on the gasket carefully tap the side
of the mating flange to break the seal.
Remove the gasket and clean away any
pieces of gasket cement which are adhering
to the flanges.
3Remove the sealing strips from the
recesses at either end of the sump pan.
Refitting
4Fit the new sealing strips and if necessary,
trim their ends until they are just proud of the
sump pan flange (photo).5Using thick grease, stick the gasket side
strips to the crankcase.
6Apply a blob of jointing compound at the
points of overlap of the side gaskets and
strips.
7Offer up the sump pan, screw in and tighten
the bolts and nuts progressively (photos).
8Refill the engine with oil.
903 cc engine 1•11
7.24B Cylinder head bolts holding coolant
pipe7.24A Cylinder head bolt in intake manifold7.20 Cylinder head gasket
7.31 Fitting the rocker cover
7.26 Fitting a pushrod
Fig. 1.7 Cylinder head bolt tightening
sequence (Sec 7)1
8.4 Sump pan sealing strip8.7A Fitting the sump pan
Page 26 of 303
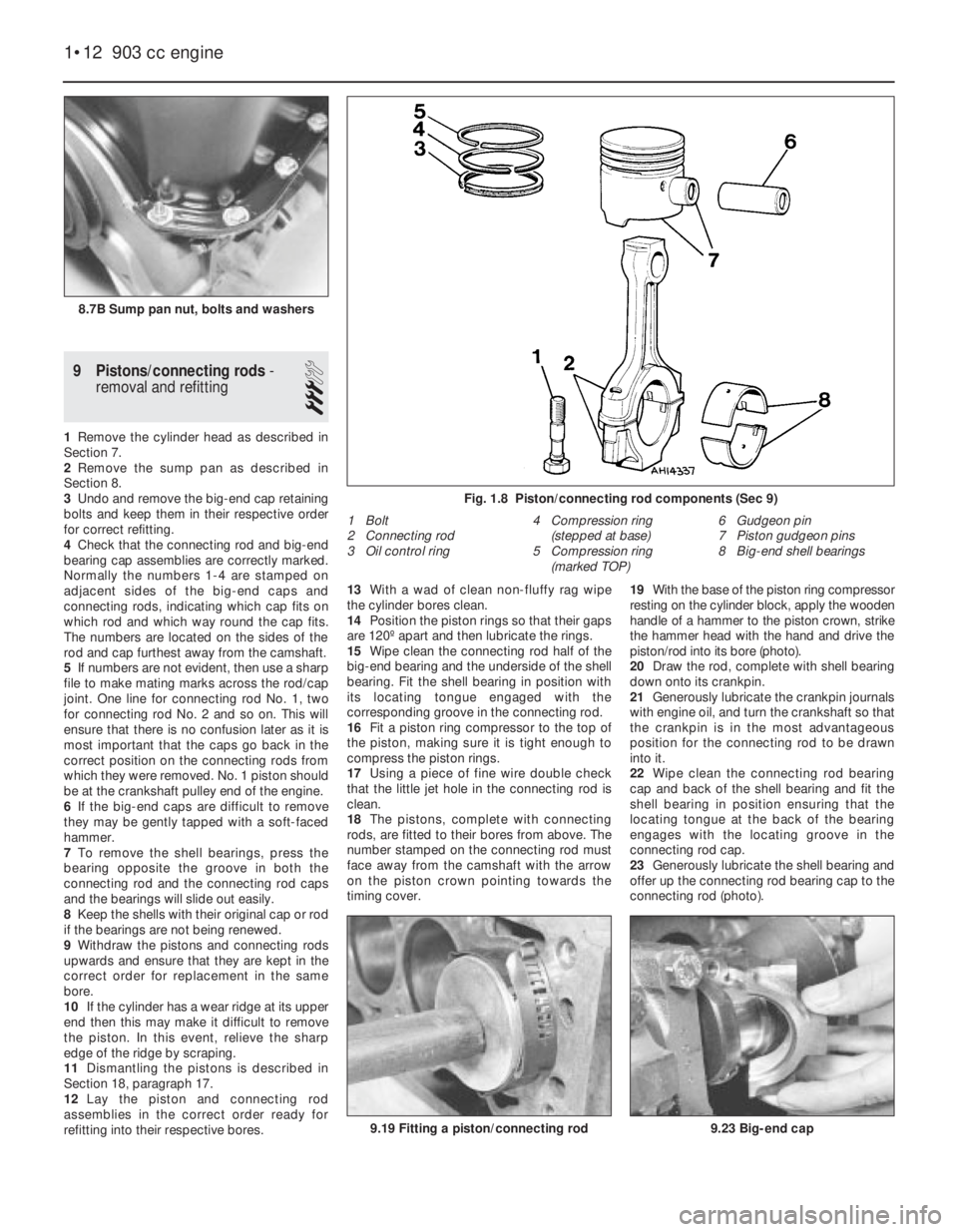
9 Pistons/connecting rods-
removal and refitting
3
1Remove the cylinder head as described in
Section 7.
2Remove the sump pan as described in
Section 8.
3Undo and remove the big-end cap retaining
bolts and keep them in their respective order
for correct refitting.
4Check that the connecting rod and big-end
bearing cap assemblies are correctly marked.
Normally the numbers 1-4 are stamped on
adjacent sides of the big-end caps and
connecting rods, indicating which cap fits on
which rod and which way round the cap fits.
The numbers are located on the sides of the
rod and cap furthest away from the camshaft.
5If numbers are not evident, then use a sharp
file to make mating marks across the rod/cap
joint. One line for connecting rod No. 1, two
for connecting rod No. 2 and so on. This will
ensure that there is no confusion later as it is
most important that the caps go back in the
correct position on the connecting rods from
which they were removed. No. 1 piston should
be at the crankshaft pulley end of the engine.
6If the big-end caps are difficult to remove
they may be gently tapped with a soft-faced
hammer.
7To remove the shell bearings, press the
bearing opposite the groove in both the
connecting rod and the connecting rod caps
and the bearings will slide out easily.
8Keep the shells with their original cap or rod
if the bearings are not being renewed.
9Withdraw the pistons and connecting rods
upwards and ensure that they are kept in the
correct order for replacement in the same
bore.
10If the cylinder has a wear ridge at its upper
end then this may make it difficult to remove
the piston. In this event, relieve the sharp
edge of the ridge by scraping.
11Dismantling the pistons is described in
Section 18, paragraph 17.
12Lay the piston and connecting rod
assemblies in the correct order ready for
refitting into their respective bores.13With a wad of clean non-fluffy rag wipe
the cylinder bores clean.
14Position the piston rings so that their gaps
are 120º apart and then lubricate the rings.
15Wipe clean the connecting rod half of the
big-end bearing and the underside of the shell
bearing. Fit the shell bearing in position with
its locating tongue engaged with the
corresponding groove in the connecting rod.
16Fit a piston ring compressor to the top of
the piston, making sure it is tight enough to
compress the piston rings.
17Using a piece of fine wire double check
that the little jet hole in the connecting rod is
clean.
18The pistons, complete with connecting
rods, are fitted to their bores from above. The
number stamped on the connecting rod must
face away from the camshaft with the arrow
on the piston crown pointing towards the
timing cover.19With the base of the piston ring compressor
resting on the cylinder block, apply the wooden
handle of a hammer to the piston crown, strike
the hammer head with the hand and drive the
piston/rod into its bore (photo).
20Draw the rod, complete with shell bearing
down onto its crankpin.
21Generously lubricate the crankpin journals
with engine oil, and turn the crankshaft so that
the crankpin is in the most advantageous
position for the connecting rod to be drawn
into it.
22Wipe clean the connecting rod bearing
cap and back of the shell bearing and fit the
shell bearing in position ensuring that the
locating tongue at the back of the bearing
engages with the locating groove in the
connecting rod cap.
23Generously lubricate the shell bearing and
offer up the connecting rod bearing cap to the
connecting rod (photo).
1•12 903 cc engine
9.23 Big-end cap9.19 Fitting a piston/connecting rod
Fig. 1.8 Piston/connecting rod components (Sec 9)
1 Bolt
2 Connecting rod
3 Oil control ring4 Compression ring
(stepped at base)
5 Compression ring
(marked TOP)6 Gudgeon pin
7 Piston gudgeon pins
8 Big-end shell bearings
8.7B Sump pan nut, bolts and washers
Page 27 of 303
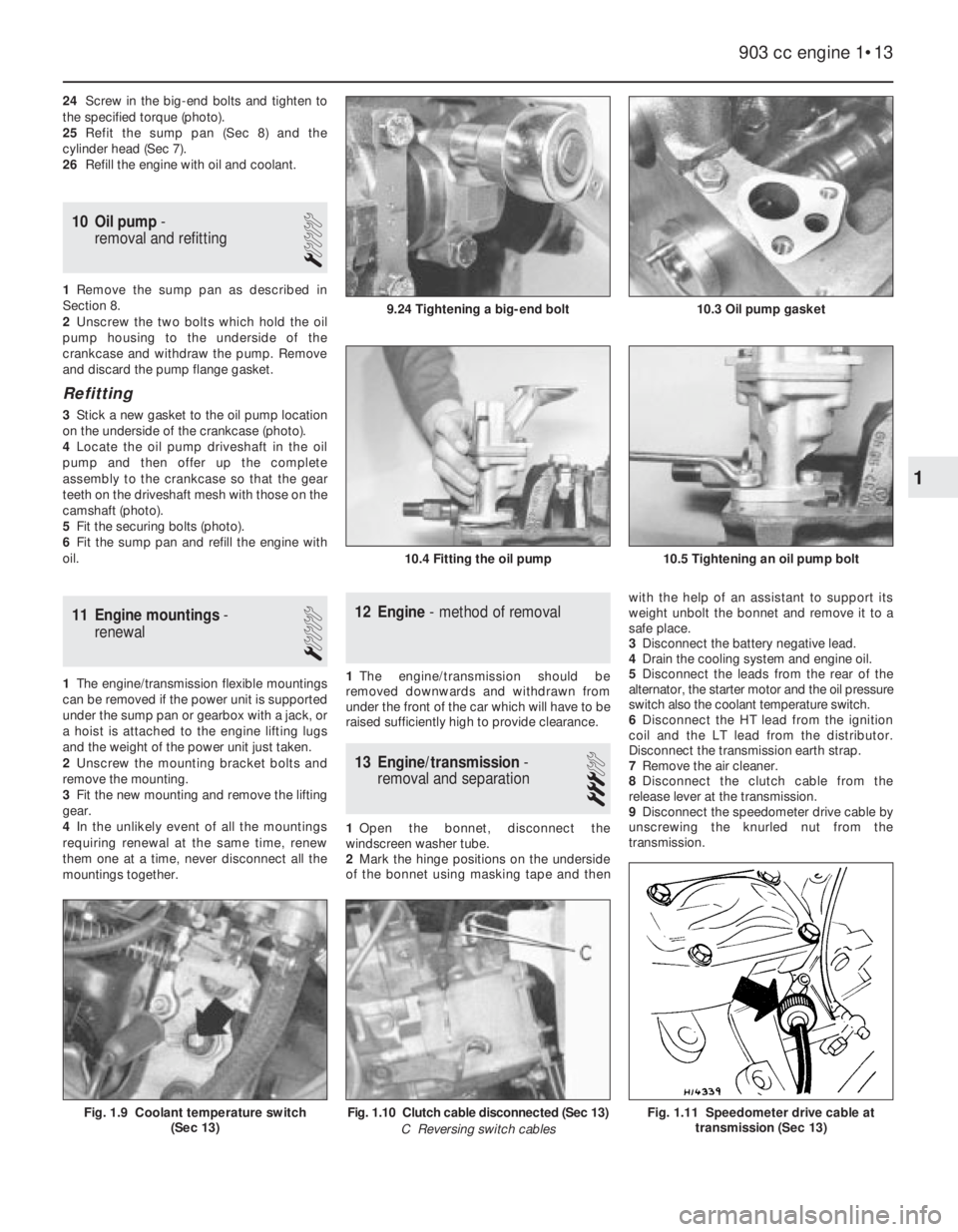
24Screw in the big-end bolts and tighten to
the specified torque (photo).
25Refit the sump pan (Sec 8) and the
cylinder head (Sec 7).
26Refill the engine with oil and coolant.
10 Oil pump-
removal and refitting
1
1Remove the sump pan as described in
Section 8.
2Unscrew the two bolts which hold the oil
pump housing to the underside of the
crankcase and withdraw the pump. Remove
and discard the pump flange gasket.
Refitting
3Stick a new gasket to the oil pump location
on the underside of the crankcase (photo).
4Locate the oil pump driveshaft in the oil
pump and then offer up the complete
assembly to the crankcase so that the gear
teeth on the driveshaft mesh with those on the
camshaft (photo).
5Fit the securing bolts (photo).
6Fit the sump pan and refill the engine with
oil.
11 Engine mountings-
renewal
1
1The engine/transmission flexible mountings
can be removed if the power unit is supported
under the sump pan or gearbox with a jack, or
a hoist is attached to the engine lifting lugs
and the weight of the power unit just taken.
2Unscrew the mounting bracket bolts and
remove the mounting.
3Fit the new mounting and remove the lifting
gear.
4In the unlikely event of all the mountings
requiring renewal at the same time, renew
them one at a time, never disconnect all the
mountings together.
12 Engine- method of removal
1The engine/transmission should be
removed downwards and withdrawn from
under the front of the car which will have to be
raised sufficiently high to provide clearance.
13 Engine/transmission-
removal and separation
3
1Open the bonnet, disconnect the
windscreen washer tube.
2Mark the hinge positions on the underside
of the bonnet using masking tape and thenwith the help of an assistant to support its
weight unbolt the bonnet and remove it to a
safe place.
3Disconnect the battery negative lead.
4Drain the cooling system and engine oil.
5Disconnect the leads from the rear of the
alternator, the starter motor and the oil pressure
switch also the coolant temperature switch.
6Disconnect the HT lead from the ignition
coil and the LT lead from the distributor.
Disconnect the transmission earth strap.
7Remove the air cleaner.
8Disconnect the clutch cable from the
release lever at the transmission.
9Disconnect the speedometer drive cable by
unscrewing the knurled nut from the
transmission.
903 cc engine 1•13
10.3 Oil pump gasket
10.4 Fitting the oil pump10.5 Tightening an oil pump bolt
9.24 Tightening a big-end bolt
Fig. 1.11 Speedometer drive cable at
transmission (Sec 13)Fig. 1.10 Clutch cable disconnected (Sec 13)
C Reversing switch cablesFig. 1.9 Coolant temperature switch
(Sec 13)
1
Page 28 of 303
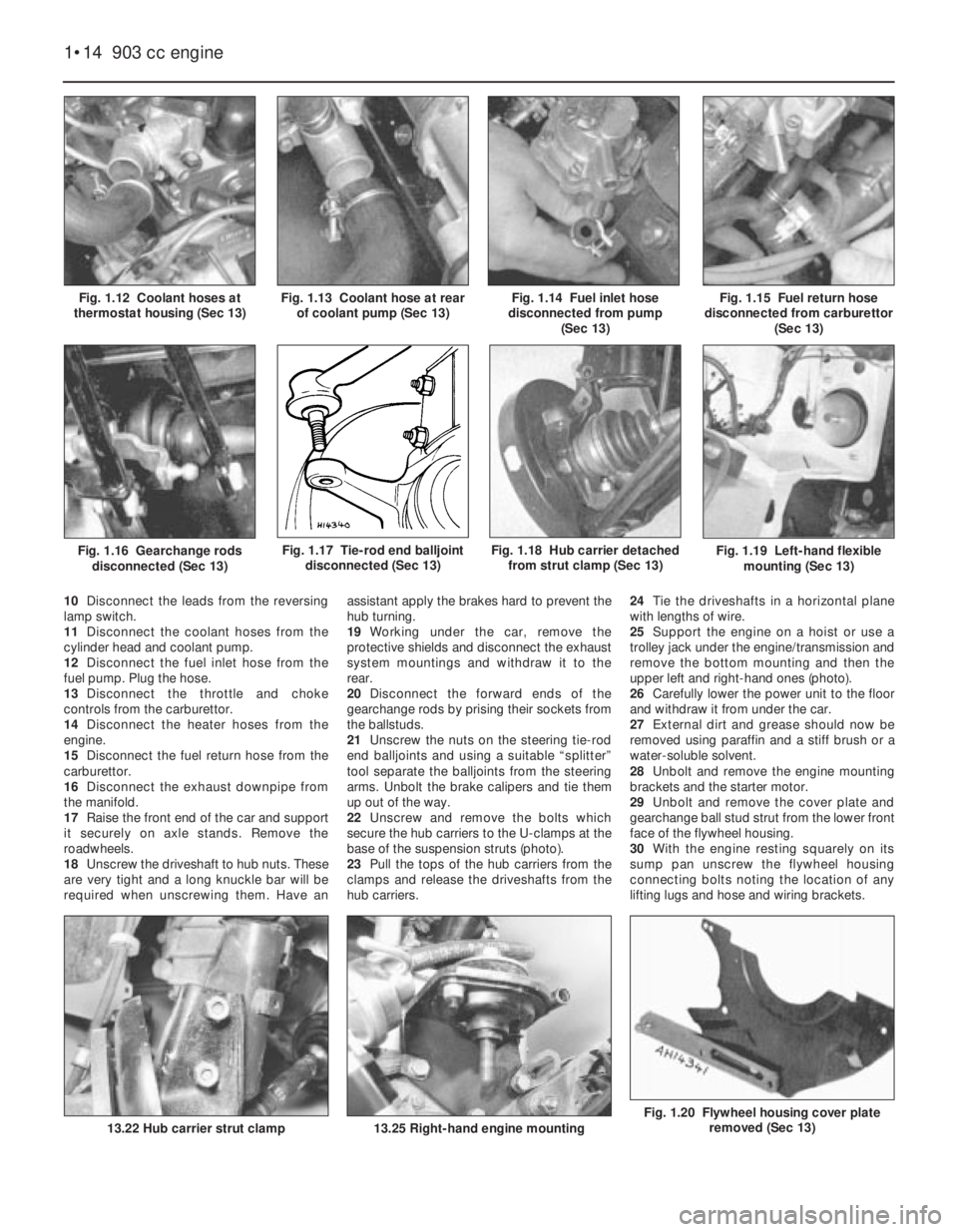
Fig. 1.20 Flywheel housing cover plate
removed (Sec 13)
Fig. 1.19 Left-hand flexible
mounting (Sec 13)
10Disconnect the leads from the reversing
lamp switch.
11Disconnect the coolant hoses from the
cylinder head and coolant pump.
12Disconnect the fuel inlet hose from the
fuel pump. Plug the hose.
13Disconnect the throttle and choke
controls from the carburettor.
14Disconnect the heater hoses from the
engine.
15Disconnect the fuel return hose from the
carburettor.
16Disconnect the exhaust downpipe from
the manifold.
17Raise the front end of the car and support
it securely on axle stands. Remove the
roadwheels.
18Unscrew the driveshaft to hub nuts. These
are very tight and a long knuckle bar will be
required when unscrewing them. Have anassistant apply the brakes hard to prevent the
hub turning.
19Working under the car, remove the
protective shields and disconnect the exhaust
system mountings and withdraw it to the
rear.
20Disconnect the forward ends of the
gearchange rods by prising their sockets from
the ballstuds.
21Unscrew the nuts on the steering tie-rod
end balljoints and using a suitable “splitter”
tool separate the balljoints from the steering
arms. Unbolt the brake calipers and tie them
up out of the way.
22Unscrew and remove the bolts which
secure the hub carriers to the U-clamps at the
base of the suspension struts (photo).
23Pull the tops of the hub carriers from the
clamps and release the driveshafts from the
hub carriers.24Tie the driveshafts in a horizontal plane
with lengths of wire.
25Support the engine on a hoist or use a
trolley jack under the engine/transmission and
remove the bottom mounting and then the
upper left and right-hand ones (photo).
26Carefully lower the power unit to the floor
and withdraw it from under the car.
27External dirt and grease should now be
removed using paraffin and a stiff brush or a
water-soluble solvent.
28Unbolt and remove the engine mounting
brackets and the starter motor.
29Unbolt and remove the cover plate and
gearchange ball stud strut from the lower front
face of the flywheel housing.
30With the engine resting squarely on its
sump pan unscrew the flywheel housing
connecting bolts noting the location of any
lifting lugs and hose and wiring brackets.
1•14 903 cc engine
13.25 Right-hand engine mounting
Fig. 1.18 Hub carrier detached
from strut clamp (Sec 13)
13.22 Hub carrier strut clamp
Fig. 1.17 Tie-rod end balljoint
disconnected (Sec 13)Fig. 1.16 Gearchange rods
disconnected (Sec 13)
Fig. 1.15 Fuel return hose
disconnected from carburettor
(Sec 13)Fig. 1.14 Fuel inlet hose
disconnected from pump
(Sec 13)Fig. 1.13 Coolant hose at rear
of coolant pump (Sec 13)Fig. 1.12 Coolant hoses at
thermostat housing (Sec 13)
Page 29 of 303
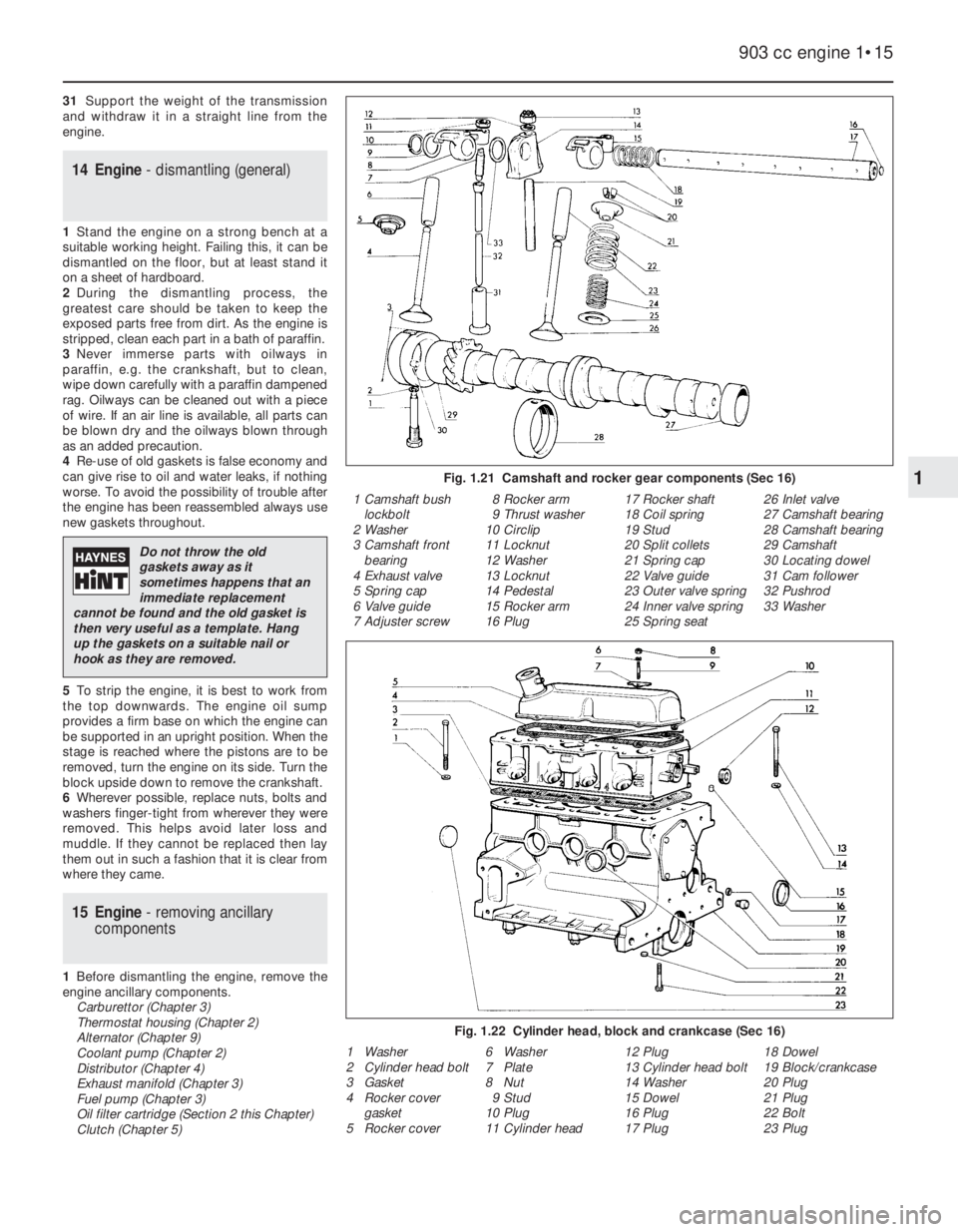
31Support the weight of the transmission
and withdraw it in a straight line from the
engine.
14 Engine- dismantling (general)
1Stand the engine on a strong bench at a
suitable working height. Failing this, it can be
dismantled on the floor, but at least stand it
on a sheet of hardboard.
2During the dismantling process, the
greatest care should be taken to keep the
exposed parts free from dirt. As the engine is
stripped, clean each part in a bath of paraffin.
3Never immerse parts with oilways in
paraffin, e.g. the crankshaft, but to clean,
wipe down carefully with a paraffin dampened
rag. Oilways can be cleaned out with a piece
of wire. If an air line is available, all parts can
be blown dry and the oilways blown through
as an added precaution.
4Re-use of old gaskets is false economy and
can give rise to oil and water leaks, if nothing
worse. To avoid the possibility of trouble after
the engine has been reassembled always use
new gaskets throughout.
5To strip the engine, it is best to work from
the top downwards. The engine oil sump
provides a firm base on which the engine can
be supported in an upright position. When the
stage is reached where the pistons are to be
removed, turn the engine on its side. Turn the
block upside down to remove the crankshaft.
6Wherever possible, replace nuts, bolts and
washers finger-tight from wherever they were
removed. This helps avoid later loss and
muddle. If they cannot be replaced then lay
them out in such a fashion that it is clear from
where they came.
15 Engine- removing ancillary
components
1Before dismantling the engine, remove the
engine ancillary components.
Carburettor (Chapter 3)
Thermostat housing (Chapter 2)
Alternator (Chapter 9)
Coolant pump (Chapter 2)
Distributor (Chapter 4)
Exhaust manifold (Chapter 3)
Fuel pump (Chapter 3)
Oil filter cartridge (Section 2 this Chapter)
Clutch (Chapter 5)
903 cc engine 1•15
Fig. 1.21 Camshaft and rocker gear components (Sec 16)
Fig. 1.22 Cylinder head, block and crankcase (Sec 16)
1 Camshaft bush
lockbolt
2 Washer
3 Camshaft front
bearing
4 Exhaust valve
5 Spring cap
6 Valve guide
7 Adjuster screw8 Rocker arm
9 Thrust washer
10 Circlip
11 Locknut
12 Washer
13 Locknut
14 Pedestal
15 Rocker arm
16 Plug17 Rocker shaft
18 Coil spring
19 Stud
20 Split collets
21 Spring cap
22 Valve guide
23 Outer valve spring
24 Inner valve spring
25 Spring seat26 Inlet valve
27 Camshaft bearing
28 Camshaft bearing
29 Camshaft
30 Locating dowel
31 Cam follower
32 Pushrod
33 Washer
1 Washer
2 Cylinder head bolt
3 Gasket
4 Rocker cover
gasket
5 Rocker cover6 Washer
7 Plate
8 Nut
9 Stud
10 Plug
11 Cylinder head12 Plug
13 Cylinder head bolt
14 Washer
15 Dowel
16 Plug
17 Plug18 Dowel
19 Block/crankcase
20 Plug
21 Plug
22 Bolt
23 Plug
1
Do not throw the old
gaskets away as it
sometimes happens that an
immediate replacement
cannot be found and the old gasket is
then very useful as a template. Hang
up the gaskets on a suitable nail or
hook as they are removed.
Page 30 of 303
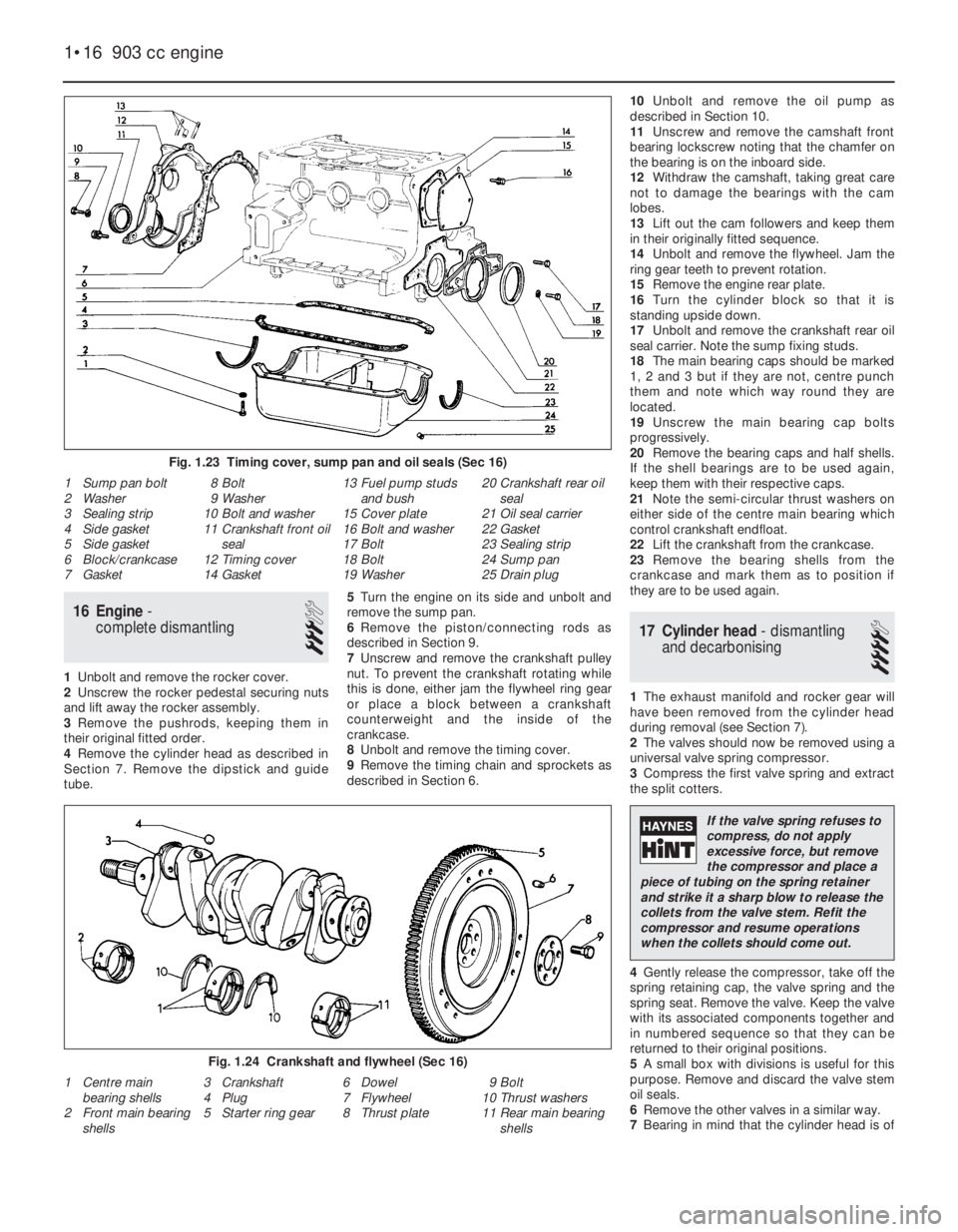
16 Engine-
complete dismantling
3
1Unbolt and remove the rocker cover.
2Unscrew the rocker pedestal securing nuts
and lift away the rocker assembly.
3Remove the pushrods, keeping them in
their original fitted order.
4Remove the cylinder head as described in
Section 7. Remove the dipstick and guide
tube.5Turn the engine on its side and unbolt and
remove the sump pan.
6Remove the piston/connecting rods as
described in Section 9.
7Unscrew and remove the crankshaft pulley
nut. To prevent the crankshaft rotating while
this is done, either jam the flywheel ring gear
or place a block between a crankshaft
counterweight and the inside of the
crankcase.
8Unbolt and remove the timing cover.
9Remove the timing chain and sprockets as
described in Section 6. 10Unbolt and remove the oil pump as
described in Section 10.
11Unscrew and remove the camshaft front
bearing lockscrew noting that the chamfer on
the bearing is on the inboard side.
12Withdraw the camshaft, taking great care
not to damage the bearings with the cam
lobes.
13Lift out the cam followers and keep them
in their originally fitted sequence.
14Unbolt and remove the flywheel. Jam the
ring gear teeth to prevent rotation.
15Remove the engine rear plate.
16Turn the cylinder block so that it is
standing upside down.
17Unbolt and remove the crankshaft rear oil
seal carrier. Note the sump fixing studs.
18The main bearing caps should be marked
1, 2 and 3 but if they are not, centre punch
them and note which way round they are
located.
19Unscrew the main bearing cap bolts
progressively.
20Remove the bearing caps and half shells.
If the shell bearings are to be used again,
keep them with their respective caps.
21Note the semi-circular thrust washers on
either side of the centre main bearing which
control crankshaft endfloat.
22Lift the crankshaft from the crankcase.
23Remove the bearing shells from the
crankcase and mark them as to position if
they are to be used again.
17 Cylinder head- dismantling
and decarbonising
4
1The exhaust manifold and rocker gear will
have been removed from the cylinder head
during removal (see Section 7).
2The valves should now be removed using a
universal valve spring compressor.
3Compress the first valve spring and extract
the split cotters.
4Gently release the compressor, take off the
spring retaining cap, the valve spring and the
spring seat. Remove the valve. Keep the valve
with its associated components together and
in numbered sequence so that they can be
returned to their original positions.
5A small box with divisions is useful for this
purpose. Remove and discard the valve stem
oil seals.
6Remove the other valves in a similar way.
7Bearing in mind that the cylinder head is of
1•16 903 cc engine
Fig. 1.23 Timing cover, sump pan and oil seals (Sec 16)
Fig. 1.24 Crankshaft and flywheel (Sec 16)
1 Sump pan bolt
2 Washer
3 Sealing strip
4 Side gasket
5 Side gasket
6 Block/crankcase
7 Gasket8 Bolt
9 Washer
10 Bolt and washer
11 Crankshaft front oil
seal
12 Timing cover
14 Gasket13 Fuel pump studs
and bush
15 Cover plate
16 Bolt and washer
17 Bolt
18 Bolt
19 Washer20 Crankshaft rear oil
seal
21 Oil seal carrier
22 Gasket
23 Sealing strip
24 Sump pan
25 Drain plug
1 Centre main
bearing shells
2 Front main bearing
shells3 Crankshaft
4 Plug
5 Starter ring gear6 Dowel
7 Flywheel
8 Thrust plate9 Bolt
10 Thrust washers
11 Rear main bearing
shells
If the valve spring refuses to
compress, do not apply
excessive force, but remove
the compressor and place a
piece of tubing on the spring retainer
and strike it a sharp blow to release the
collets from the valve stem. Refit the
compressor and resume operations
when the collets should come out.