FORD SIERRA 1992 2.G SOHC Engines User Guide
Manufacturer: FORD, Model Year: 1992, Model line: SIERRA, Model: FORD SIERRA 1992 2.GPages: 24, PDF Size: 1.03 MB
Page 11 of 24
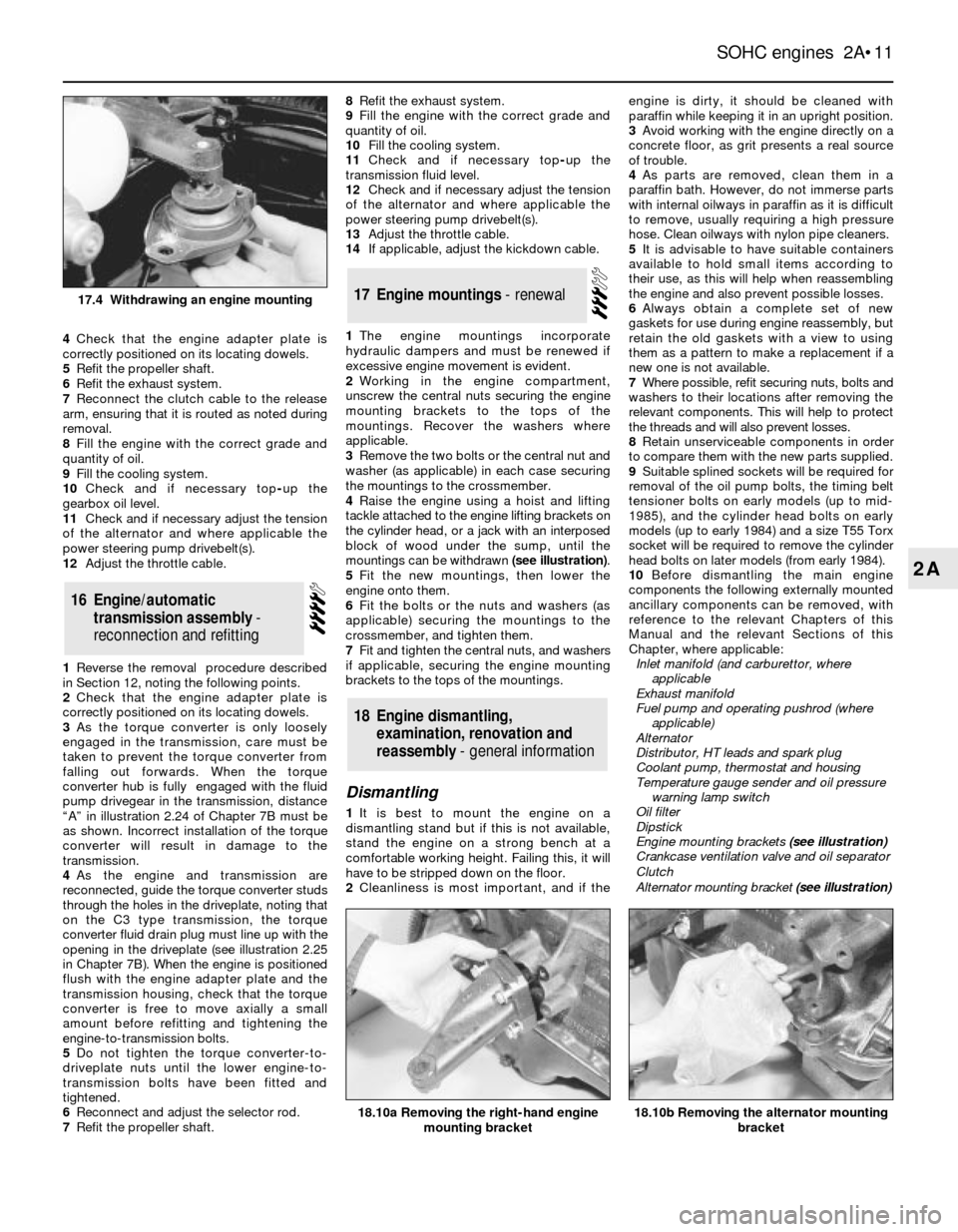
4Check that the engine adapter plate is
correctly positioned on its locating dowels.
5Refit the propeller shaft.
6Refit the exhaust system.
7Reconnect the clutch cable to the release
arm, ensuring that it is routed as noted during
removal.
8Fill the engine with the correct grade and
quantity of oil.
9Fill the cooling system.
10Check and if necessary top-up the
gearbox oil level.
11Check and if necessary adjust the tension
of the alternator and where applicable the
power steering pump drivebelt(s).
12Adjust the throttle cable.
1Reverse the removal procedure described
in Section 12, noting the following points.
2Check that the engine adapter plate is
correctly positioned on its locating dowels.
3As the torque converter is only loosely
engaged in the transmission, care must be
taken to prevent the torque converter from
falling out forwards. When the torque
converter hub is fully engaged with the fluid
pump drivegear in the transmission, distance
ÒAÓ in illustration 2.24 of Chapter 7B must be
as shown. Incorrect installation of the torque
converter will result in damage to the
transmission.
4As the engine and transmission are
reconnected, guide the torque converter studs
through the holes in the driveplate, noting that
on the C3 type transmission, the torque
converter fluid drain plug must line up with the
opening in the driveplate (see illustration 2.25
in Chapter 7B). When the engine is positioned
flush with the engine adapter plate and the
transmission housing, check that the torque
converter is free to move axially a small
amount before refitting and tightening the
engine-to-transmission bolts.
5Do not tighten the torque converter-to-
driveplate nuts until the lower engine-to-
transmission bolts have been fitted and
tightened.
6Reconnect and adjust the selector rod.
7Refit the propeller shaft.8Refit the exhaust system.
9Fill the engine with the correct grade and
quantity of oil.
10Fill the cooling system.
11Check and if necessary top-up the
transmission fluid level.
12Check and if necessary adjust the tension
of the alternator and where applicable the
power steering pump drivebelt(s).
13Adjust the throttle cable.
14If applicable, adjust the kickdown cable.
1The engine mountings incorporate
hydraulic dampers and must be renewed if
excessive engine movement is evident.
2Working in the engine compartment,
unscrew the central nuts securing the engine
mounting brackets to the tops of the
mountings. Recover the washers where
applicable.
3Remove the two bolts or the central nut and
washer (as applicable) in each case securing
the mountings to the crossmember.
4Raise the engine using a hoist and lifting
tackle attached to the engine lifting brackets on
the cylinder head, or a jack with an interposed
block of wood under the sump, until the
mountings can be withdrawn (see illustration).
5Fit the new mountings, then lower the
engine onto them.
6Fit the bolts or the nuts and washers (as
applicable) securing the mountings to the
crossmember, and tighten them.
7Fit and tighten the central nuts, and washers
if applicable, securing the engine mounting
brackets to the tops of the mountings.
Dismantling
1It is best to mount the engine on a
dismantling stand but if this is not available,
stand the engine on a strong bench at a
comfortable working height. Failing this, it will
have to be stripped down on the floor.
2Cleanliness is most important, and if theengine is dirty, it should be cleaned with
paraffin while keeping it in an upright position.
3Avoid working with the engine directly on a
concrete floor, as grit presents a real source
of trouble.
4As parts are removed, clean them in a
paraffin bath. However, do not immerse parts
with internal oilways in paraffin as it is difficult
to remove, usually requiring a high pressure
hose. Clean oilways with nylon pipe cleaners.
5It is advisable to have suitable containers
available to hold small items according to
their use, as this will help when reassembling
the engine and also prevent possible losses.
6Always obtain a complete set of new
gaskets for use during engine reassembly, but
retain the old gaskets with a view to using
them as a pattern to make a replacement if a
new one is not available.
7Where possible, refit securing nuts, bolts and
washers to their locations after removing the
relevant components. This will help to protect
the threads and will also prevent losses.
8Retain unserviceable components in order
to compare them with the new parts supplied.
9Suitable splined sockets will be required for
removal of the oil pump bolts, the timing belt
tensioner bolts on early models (up to mid-
1985), and the cylinder head bolts on early
models (up to early 1984) and a size T55 Torx
socket will be required to remove the cylinder
head bolts on later models (from early 1984).
10Before dismantling the main engine
components the following externally mounted
ancillary components can be removed, with
reference to the relevant Chapters of this
Manual and the relevant Sections of this
Chapter, where applicable:
Inlet manifold (and carburettor, where
applicable
Exhaust manifold
Fuel pump and operating pushrod (where
applicable)
Alternator
Distributor, HT leads and spark plug
Coolant pump, thermostat and housing
Temperature gauge sender and oil pressure
warning lamp switch
Oil filter
Dipstick
Engine mounting brackets (see illustration)
Crankcase ventilation valve and oil separator
Clutch
Alternator mounting bracket (see illustration)
18Engine dismantling,
examination, renovation and
reassembly - general information
17Engine mountings - renewal
16Engine/automatic
transmission assembly -
reconnection and refitting
SOHC engines 2A¥11
2A
18.10b Removing the alternator mounting
bracket18.10a Removing the right-hand engine
mounting bracket
17.4 Withdrawing an engine mounting
Page 12 of 24
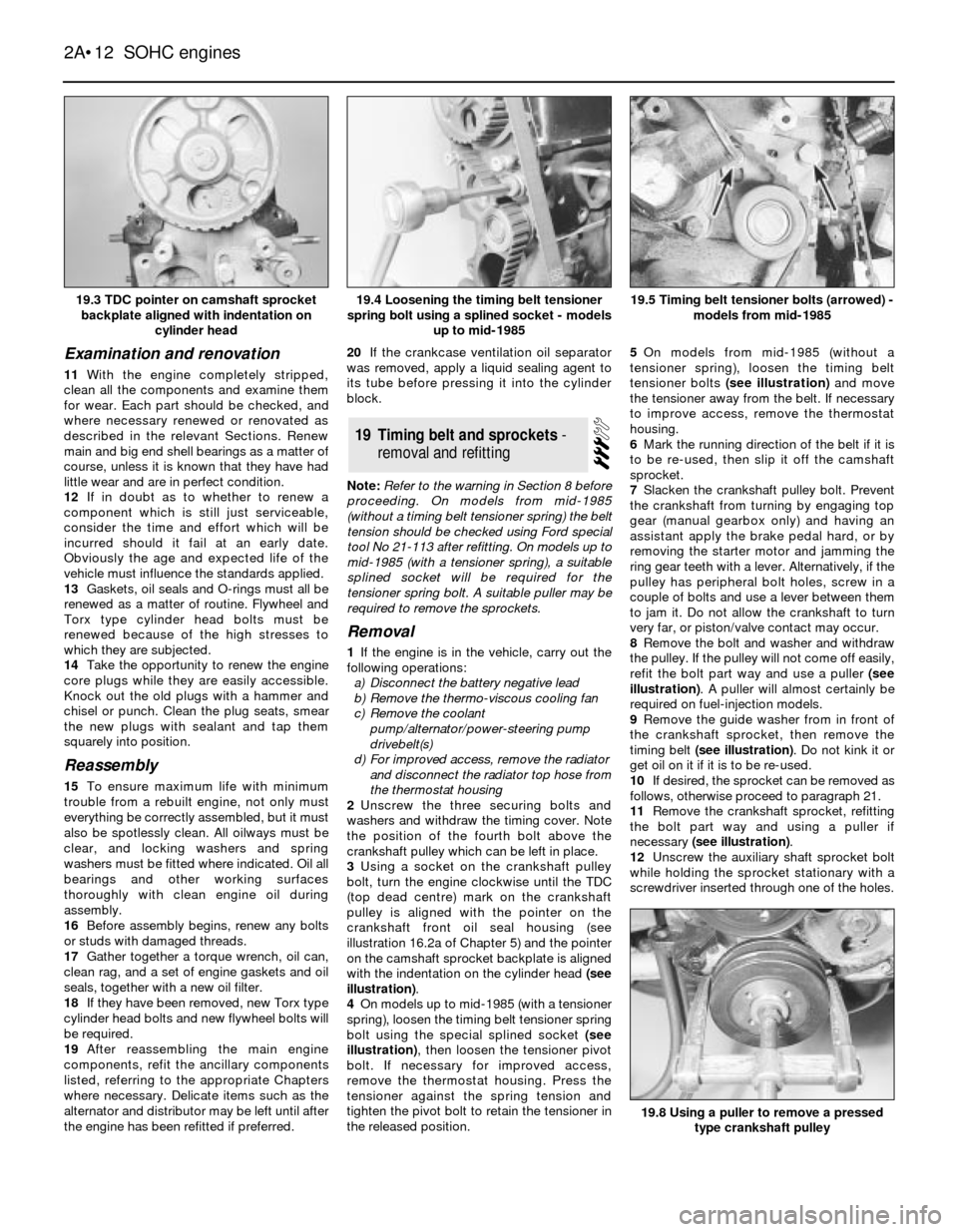
Examination and renovation
11With the engine completely stripped,
clean all the components and examine them
for wear. Each part should be checked, and
where necessary renewed or renovated as
described in the relevant Sections. Renew
main and big end shell bearings as a matter of
course, unless it is known that they have had
little wear and are in perfect condition.
12If in doubt as to whether to renew a
component which is still just serviceable,
consider the time and effort which will be
incurred should it fail at an early date.
Obviously the age and expected life of the
vehicle must influence the standards applied.
13Gaskets, oil seals and O-rings must all be
renewed as a matter of routine. Flywheel and
Torx type cylinder head bolts must be
renewed because of the high stresses to
which they are subjected.
14Take the opportunity to renew the engine
core plugs while they are easily accessible.
Knock out the old plugs with a hammer and
chisel or punch. Clean the plug seats, smear
the new plugs with sealant and tap them
squarely into position.
Reassembly
15To ensure maximum life with minimum
trouble from a rebuilt engine, not only must
everything be correctly assembled, but it must
also be spotlessly clean. All oilways must be
clear, and locking washers and spring
washers must be fitted where indicated. Oil all
bearings and other working surfaces
thoroughly with clean engine oil during
assembly.
16Before assembly begins, renew any bolts
or studs with damaged threads.
17Gather together a torque wrench, oil can,
clean rag, and a set of engine gaskets and oil
seals, together with a new oil filter.
18If they have been removed, new Torx type
cylinder head bolts and new flywheel bolts will
be required.
19After reassembling the main engine
components, refit the ancillary components
listed, referring to the appropriate Chapters
where necessary. Delicate items such as the
alternator and distributor may be left until after
the engine has been refitted if preferred.20If the crankcase ventilation oil separator
was removed, apply a liquid sealing agent to
its tube before pressing it into the cylinder
block.
Note: Refer to the warning in Section 8 before
proceeding. On models from mid-1985
(without a timing belt tensioner spring) the belt
tension should be checked using Ford special
tool No 21-113 after refitting. On models up to
mid-1985 (with a tensioner spring), a suitable
splined socket will be required for the
tensioner spring bolt. A suitable puller may be
required to remove the sprockets.
Removal
1If the engine is in the vehicle, carry out the
following operations:
a)Disconnect the battery negative lead
b)Remove the thermo-viscous cooling fan
c)Remove the coolant
pump/alternator/power-steering pump
drivebelt(s)
d)For improved access, remove the radiator
and disconnect the radiator top hose from
the thermostat housing
2Unscrew the three securing bolts and
washers and withdraw the timing cover. Note
the position of the fourth bolt above the
crankshaft pulley which can be left in place.
3Using a socket on the crankshaft pulley
bolt, turn the engine clockwise until the TDC
(top dead centre) mark on the crankshaft
pulley is aligned with the pointer on the
crankshaft front oil seal housing (see
illustration 16.2a of Chapter 5) and the pointer
on the camshaft sprocket backplate is aligned
with the indentation on the cylinder head (see
illustration).
4On models up to mid-1985 (with a tensioner
spring), loosen the timing belt tensioner spring
bolt using the special splined socket (see
illustration), then loosen the tensioner pivot
bolt. If necessary for improved access,
remove the thermostat housing. Press the
tensioner against the spring tension and
tighten the pivot bolt to retain the tensioner in
the released position.5On models from mid-1985 (without a
tensioner spring), loosen the timing belt
tensioner bolts (see illustration)and move
the tensioner away from the belt. If necessary
to improve access, remove the thermostat
housing.
6Mark the running direction of the belt if it is
to be re-used, then slip it off the camshaft
sprocket.
7Slacken the crankshaft pulley bolt. Prevent
the crankshaft from turning by engaging top
gear (manual gearbox only) and having an
assistant apply the brake pedal hard, or by
removing the starter motor and jamming the
ring gear teeth with a lever. Alternatively, if the
pulley has peripheral bolt holes, screw in a
couple of bolts and use a lever between them
to jam it. Do not allow the crankshaft to turn
very far, or piston/valve contact may occur.
8Remove the bolt and washer and withdraw
the pulley. If the pulley will not come off easily,
refit the bolt part way and use a puller (see
illustration). A puller will almost certainly be
required on fuel-injection models.
9Remove the guide washer from in front of
the crankshaft sprocket, then remove the
timing belt (see illustration). Do not kink it or
get oil on it if it is to be re-used.
10If desired, the sprocket can be removed as
follows, otherwise proceed to paragraph 21.
11Remove the crankshaft sprocket, refitting
the bolt part way and using a puller if
necessary (see illustration).
12Unscrew the auxiliary shaft sprocket bolt
while holding the sprocket stationary with a
screwdriver inserted through one of the holes.
19Timing belt and sprockets -
removal and refitting
2A¥12SOHC engines
19.3 TDC pointer on camshaft sprocket
backplate aligned with indentation on
cylinder head19.5 Timing belt tensioner bolts (arrowed) -
models from mid-1985
19.8 Using a puller to remove a pressed
type crankshaft pulley
19.4 Loosening the timing belt tensioner
spring bolt using a splined socket - models
up to mid-1985
Page 13 of 24
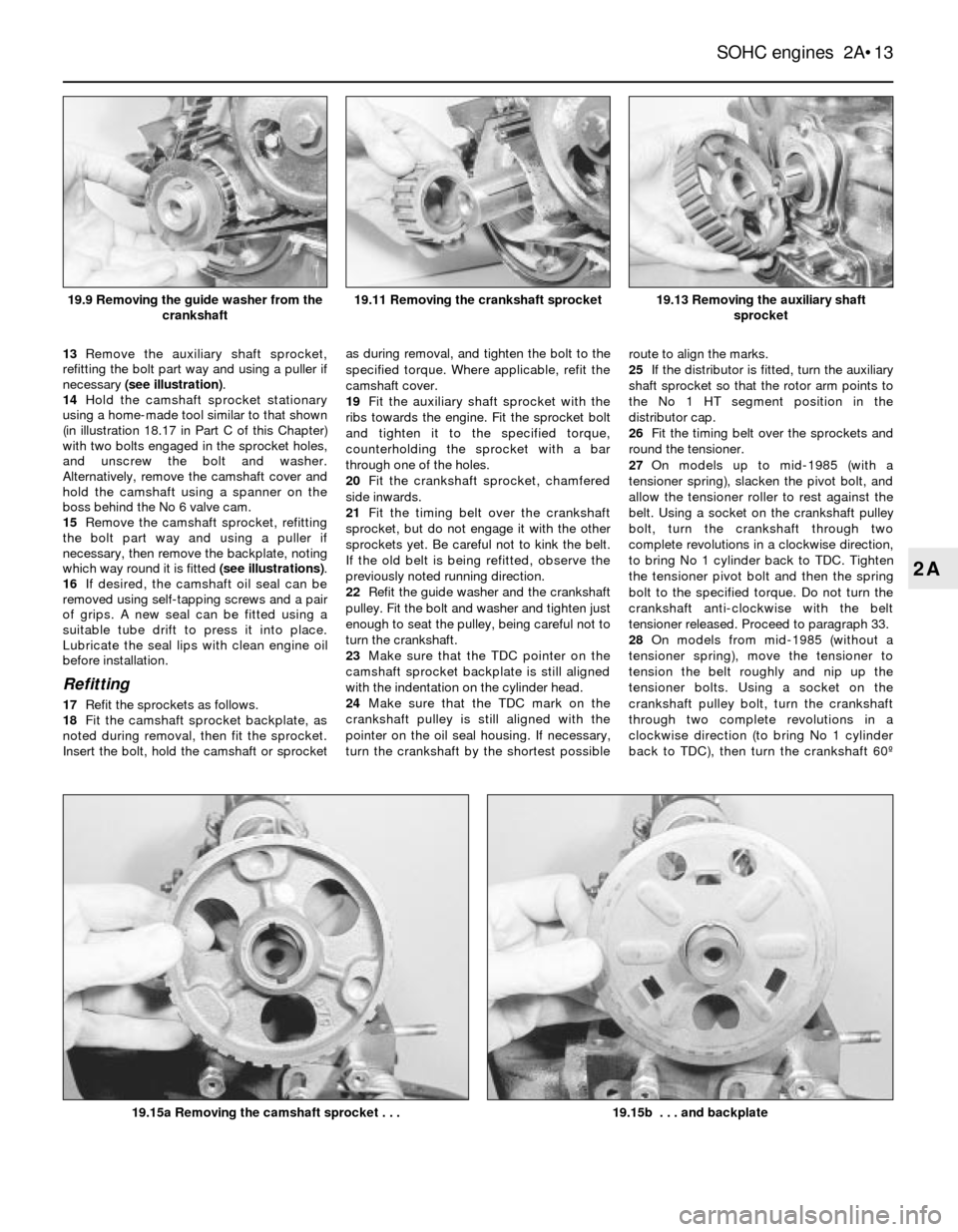
13Remove the auxiliary shaft sprocket,
refitting the bolt part way and using a puller if
necessary (see illustration).
14Hold the camshaft sprocket stationary
using a home-made tool similar to that shown
(in illustration 18.17 in Part C of this Chapter)
with two bolts engaged in the sprocket holes,
and unscrew the bolt and washer.
Alternatively, remove the camshaft cover and
hold the camshaft using a spanner on the
boss behind the No 6 valve cam.
15Remove the camshaft sprocket, refitting
the bolt part way and using a puller if
necessary, then remove the backplate, noting
which way round it is fitted (see illustrations).
16If desired, the camshaft oil seal can be
removed using self-tapping screws and a pair
of grips. A new seal can be fitted using a
suitable tube drift to press it into place.
Lubricate the seal lips with clean engine oil
before installation.
Refitting
17Refit the sprockets as follows.
18Fit the camshaft sprocket backplate, as
noted during removal, then fit the sprocket.
Insert the bolt, hold the camshaft or sprocketas during removal, and tighten the bolt to the
specified torque. Where applicable, refit the
camshaft cover.
19Fit the auxiliary shaft sprocket with the
ribs towards the engine. Fit the sprocket bolt
and tighten it to the specified torque,
counterholding the sprocket with a bar
through one of the holes.
20Fit the crankshaft sprocket, chamfered
side inwards.
21Fit the timing belt over the crankshaft
sprocket, but do not engage it with the other
sprockets yet. Be careful not to kink the belt.
If the old belt is being refitted, observe the
previously noted running direction.
22Refit the guide washer and the crankshaft
pulley. Fit the bolt and washer and tighten just
enough to seat the pulley, being careful not to
turn the crankshaft.
23Make sure that the TDC pointer on the
camshaft sprocket backplate is still aligned
with the indentation on the cylinder head.
24Make sure that the TDC mark on the
crankshaft pulley is still aligned with the
pointer on the oil seal housing. If necessary,
turn the crankshaft by the shortest possibleroute to align the marks.
25If the distributor is fitted, turn the auxiliary
shaft sprocket so that the rotor arm points to
the No 1 HT segment position in the
distributor cap.
26Fit the timing belt over the sprockets and
round the tensioner.
27On models up to mid-1985 (with a
tensioner spring), slacken the pivot bolt, and
allow the tensioner roller to rest against the
belt. Using a socket on the crankshaft pulley
bolt, turn the crankshaft through two
complete revolutions in a clockwise direction,
to bring No 1 cylinder back to TDC. Tighten
the tensioner pivot bolt and then the spring
bolt to the specified torque. Do not turn the
crankshaft anti-clockwise with the belt
tensioner released. Proceed to paragraph 33.
28On models from mid-1985 (without a
tensioner spring), move the tensioner to
tension the belt roughly and nip up the
tensioner bolts. Using a socket on the
crankshaft pulley bolt, turn the crankshaft
through two complete revolutions in a
clockwise direction (to bring No 1 cylinder
back to TDC), then turn the crankshaft 60¼
SOHC engines 2A¥13
2A
19.13 Removing the auxiliary shaft
sprocket
19.15b . . . and backplate19.15a Removing the camshaft sprocket . . .
19.11 Removing the crankshaft sprocket19.9 Removing the guide washer from the
crankshaft
Page 14 of 24
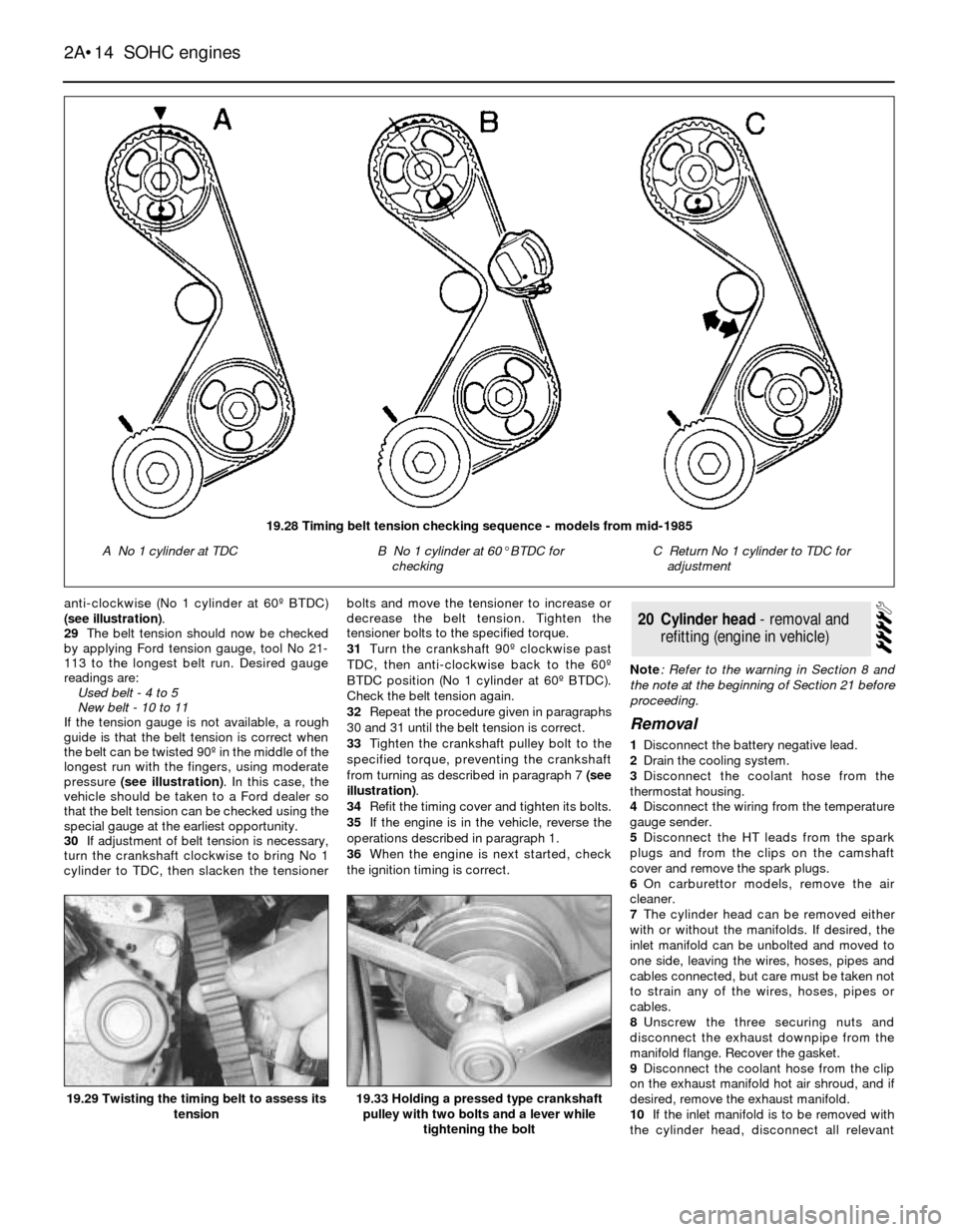
anti-clockwise (No 1 cylinder at 60¼ BTDC)
(see illustration).
29The belt tension should now be checked
by applying Ford tension gauge, tool No 21-
113 to the longest belt run. Desired gauge
readings are:
Used belt - 4 to 5
New belt - 10 to 11
If the tension gauge is not available, a rough
guide is that the belt tension is correct when
the belt can be twisted 90¼ in the middle of the
longest run with the fingers, using moderate
pressure (see illustration). In this case, the
vehicle should be taken to a Ford dealer so
that the belt tension can be checked using the
special gauge at the earliest opportunity.
30If adjustment of belt tension is necessary,
turn the crankshaft clockwise to bring No 1
cylinder to TDC, then slacken the tensionerbolts and move the tensioner to increase or
decrease the belt tension. Tighten the
tensioner bolts to the specified torque.
31Turn the crankshaft 90¼ clockwise past
TDC, then anti-clockwise back to the 60¼
BTDC position (No 1 cylinder at 60¼ BTDC).
Check the belt tension again.
32Repeat the procedure given in paragraphs
30 and 31 until the belt tension is correct.
33Tighten the crankshaft pulley bolt to the
specified torque, preventing the crankshaft
from turning as described in paragraph 7 (see
illustration).
34Refit the timing cover and tighten its bolts.
35If the engine is in the vehicle, reverse the
operations described in paragraph 1.
36When the engine is next started, check
the ignition timing is correct.Note: Refer to the warning in Section 8 and
the note at the beginning of Section 21 before
proceeding.
Removal
1Disconnect the battery negative lead.
2Drain the cooling system.
3Disconnect the coolant hose from the
thermostat housing.
4Disconnect the wiring from the temperature
gauge sender.
5Disconnect the HT leads from the spark
plugs and from the clips on the camshaft
cover and remove the spark plugs.
6On carburettor models, remove the air
cleaner.
7The cylinder head can be removed either
with or without the manifolds. If desired, the
inlet manifold can be unbolted and moved to
one side, leaving the wires, hoses, pipes and
cables connected, but care must be taken not
to strain any of the wires, hoses, pipes or
cables.
8Unscrew the three securing nuts and
disconnect the exhaust downpipe from the
manifold flange. Recover the gasket.
9Disconnect the coolant hose from the clip
on the exhaust manifold hot air shroud, and if
desired, remove the exhaust manifold.
10If the inlet manifold is to be removed with
the cylinder head, disconnect all relevant
20Cylinder head - removal and
refitting (engine in vehicle)
2A¥14SOHC engines
19.33 Holding a pressed type crankshaft
pulley with two bolts and a lever while
tightening the bolt19.29 Twisting the timing belt to assess its
tension
19.28 Timing belt tension checking sequence - models from mid-1985
A No 1 cylinder at TDCB No 1 cylinder at 60¡BTDC for
checkingC Return No 1 cylinder to TDC for
adjustment
Page 15 of 24
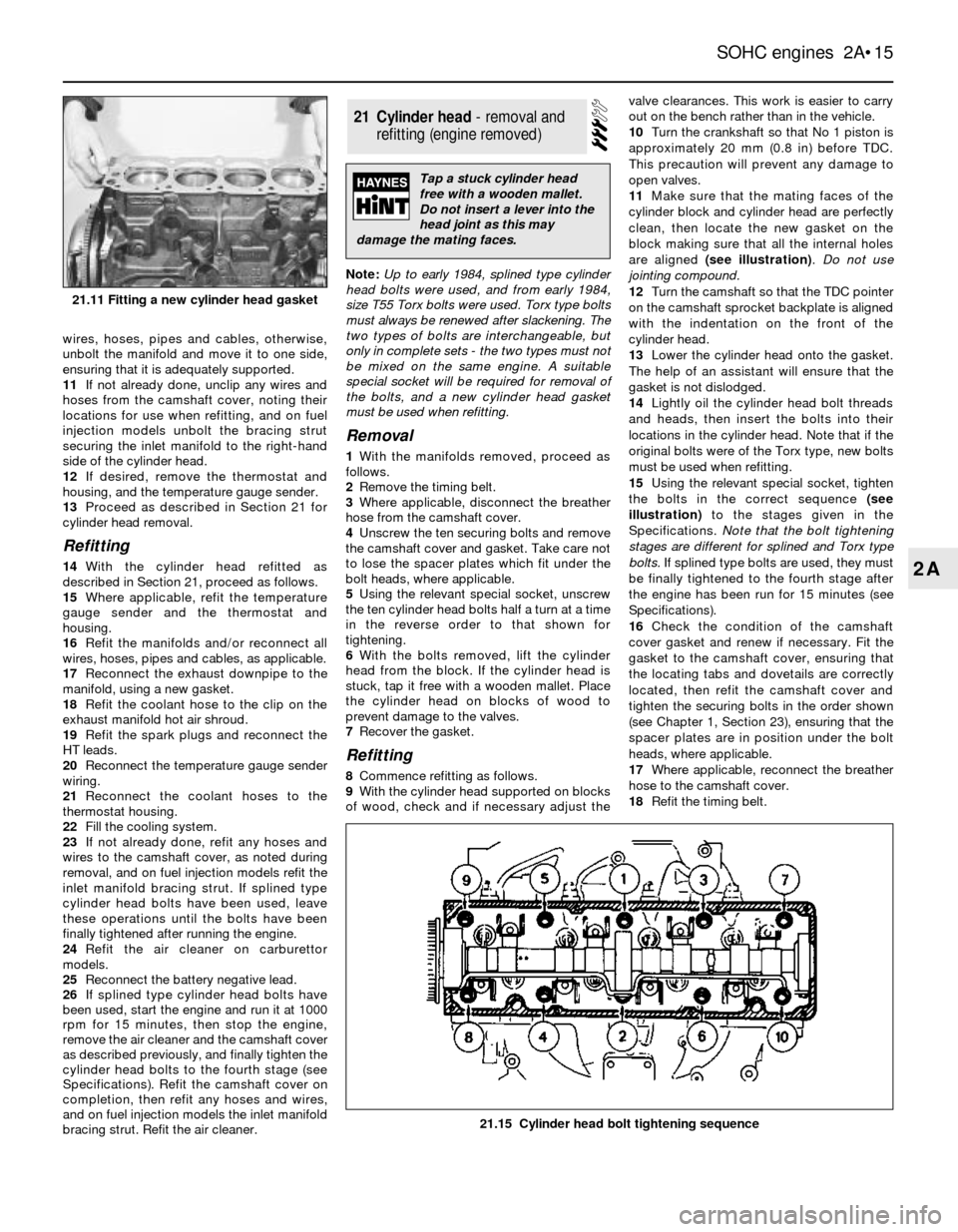
wires, hoses, pipes and cables, otherwise,
unbolt the manifold and move it to one side,
ensuring that it is adequately supported.
11If not already done, unclip any wires and
hoses from the camshaft cover, noting their
locations for use when refitting, and on fuel
injection models unbolt the bracing strut
securing the inlet manifold to the right-hand
side of the cylinder head.
12If desired, remove the thermostat and
housing, and the temperature gauge sender.
13Proceed as described in Section 21 for
cylinder head removal.
Refitting
14With the cylinder head refitted as
described in Section 21, proceed as follows.
15Where applicable, refit the temperature
gauge sender and the thermostat and
housing.
16Refit the manifolds and/or reconnect all
wires, hoses, pipes and cables, as applicable.
17Reconnect the exhaust downpipe to the
manifold, using a new gasket.
18Refit the coolant hose to the clip on the
exhaust manifold hot air shroud.
19Refit the spark plugs and reconnect the
HT leads.
20Reconnect the temperature gauge sender
wiring.
21Reconnect the coolant hoses to the
thermostat housing.
22Fill the cooling system.
23If not already done, refit any hoses and
wires to the camshaft cover, as noted during
removal, and on fuel injection models refit the
inlet manifold bracing strut. If splined type
cylinder head bolts have been used, leave
these operations until the bolts have been
finally tightened after running the engine.
24Refit the air cleaner on carburettor
models.
25Reconnect the battery negative lead.
26If splined type cylinder head bolts have
been used, start the engine and run it at 1000
rpm for 15 minutes, then stop the engine,
remove the air cleaner and the camshaft cover
as described previously, and finally tighten the
cylinder head bolts to the fourth stage (see
Specifications). Refit the camshaft cover on
completion, then refit any hoses and wires,
and on fuel injection models the inlet manifold
bracing strut. Refit the air cleaner.Note: Up to early 1984, splined type cylinder
head bolts were used, and from early 1984,
size T55 Torx bolts were used. Torx type bolts
must always be renewed after slackening. The
two types of bolts are interchangeable, but
only in complete sets - the two types must not
be mixed on the same engine. A suitable
special socket will be required for removal of
the bolts, and a new cylinder head gasket
must be used when refitting.
Removal
1With the manifolds removed, proceed as
follows.
2Remove the timing belt.
3Where applicable, disconnect the breather
hose from the camshaft cover.
4Unscrew the ten securing bolts and remove
the camshaft cover and gasket. Take care not
to lose the spacer plates which fit under the
bolt heads, where applicable.
5Using the relevant special socket, unscrew
the ten cylinder head bolts half a turn at a time
in the reverse order to that shown for
tightening.
6With the bolts removed, lift the cylinder
head from the block. If the cylinder head is
stuck, tap it free with a wooden mallet. Place
the cylinder head on blocks of wood to
prevent damage to the valves.
7Recover the gasket.
Refitting
8Commence refitting as follows.
9With the cylinder head supported on blocks
of wood, check and if necessary adjust thevalve clearances. This work is easier to carry
out on the bench rather than in the vehicle.
10Turn the crankshaft so that No 1 piston is
approximately 20 mm (0.8 in) before TDC.
This precaution will prevent any damage to
open valves.
11Make sure that the mating faces of the
cylinder block and cylinder head are perfectly
clean, then locate the new gasket on the
block making sure that all the internal holes
are aligned (see illustration). Do not use
jointing compound.
12Turn the camshaft so that the TDC pointer
on the camshaft sprocket backplate is aligned
with the indentation on the front of the
cylinder head.
13Lower the cylinder head onto the gasket.
The help of an assistant will ensure that the
gasket is not dislodged.
14Lightly oil the cylinder head bolt threads
and heads, then insert the bolts into their
locations in the cylinder head. Note that if the
original bolts were of the Torx type, new bolts
must be used when refitting.
15Using the relevant special socket, tighten
the bolts in the correct sequence (see
illustration)to the stages given in the
Specifications. Note that the bolt tightening
stages are different for splined and Torx type
bolts. If splined type bolts are used, they must
be finally tightened to the fourth stage after
the engine has been run for 15 minutes (see
Specifications).
16Check the condition of the camshaft
cover gasket and renew if necessary. Fit the
gasket to the camshaft cover, ensuring that
the locating tabs and dovetails are correctly
located, then refit the camshaft cover and
tighten the securing bolts in the order shown
(see Chapter 1, Section 23), ensuring that the
spacer plates are in position under the bolt
heads, where applicable.
17Where applicable, reconnect the breather
hose to the camshaft cover.
18Refit the timing belt.
21Cylinder head - removal and
refitting (engine removed)
SOHC engines 2A¥15
2A
21.15 Cylinder head bolt tightening sequence
21.11 Fitting a new cylinder head gasket
Tap a stuck cylinder head
free with a wooden mallet.
Do not insert a lever into the
head joint as this may
damage the mating faces.
Page 16 of 24
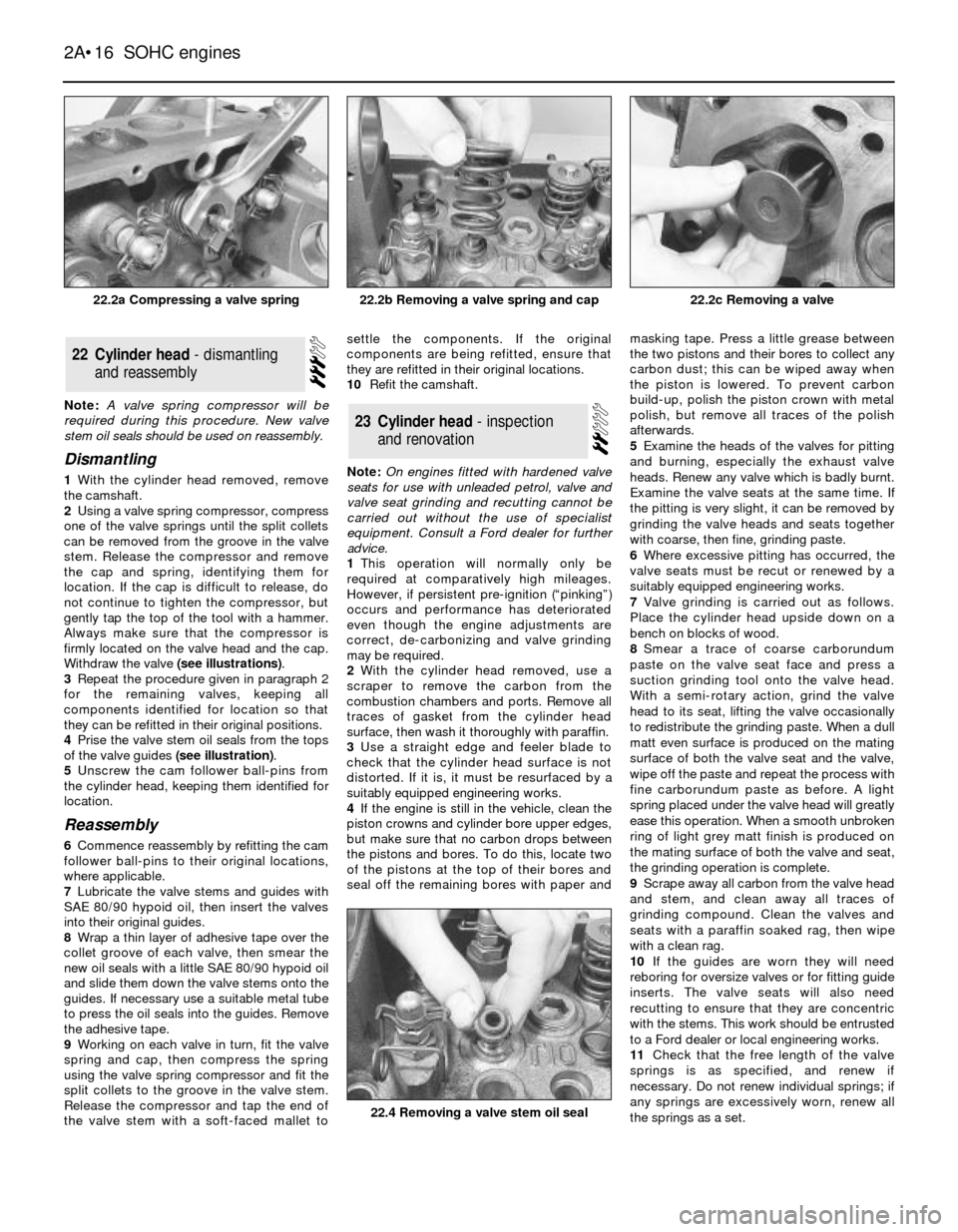
Note: A valve spring compressor will be
required during this procedure. New valve
stem oil seals should be used on reassembly.
Dismantling
1With the cylinder head removed, remove
the camshaft.
2Using a valve spring compressor, compress
one of the valve springs until the split collets
can be removed from the groove in the valve
stem. Release the compressor and remove
the cap and spring, identifying them for
location. If the cap is difficult to release, do
not continue to tighten the compressor, but
gently tap the top of the tool with a hammer.
Always make sure that the compressor is
firmly located on the valve head and the cap.
Withdraw the valve (see illustrations).
3Repeat the procedure given in paragraph 2
for the remaining valves, keeping all
components identified for location so that
they can be refitted in their original positions.
4Prise the valve stem oil seals from the tops
of the valve guides (see illustration).
5Unscrew the cam follower ball-pins from
the cylinder head, keeping them identified for
location.
Reassembly
6Commence reassembly by refitting the cam
follower ball-pins to their original locations,
where applicable.
7Lubricate the valve stems and guides with
SAE 80/90 hypoid oil, then insert the valves
into their original guides.
8Wrap a thin layer of adhesive tape over the
collet groove of each valve, then smear the
new oil seals with a little SAE 80/90 hypoid oil
and slide them down the valve stems onto the
guides. If necessary use a suitable metal tube
to press the oil seals into the guides. Remove
the adhesive tape.
9Working on each valve in turn, fit the valve
spring and cap, then compress the spring
using the valve spring compressor and fit the
split collets to the groove in the valve stem.
Release the compressor and tap the end of
the valve stem with a soft-faced mallet tosettle the components. If the original
components are being refitted, ensure that
they are refitted in their original locations.
10Refit the camshaft.
Note: On engines fitted with hardened valve
seats for use with unleaded petrol, valve and
valve seat grinding and recutting cannot be
carried out without the use of specialist
equipment. Consult a Ford dealer for further
advice.
1This operation will normally only be
required at comparatively high mileages.
However, if persistent pre-ignition (ÒpinkingÓ)
occurs and performance has deteriorated
even though the engine adjustments are
correct, de-carbonizing and valve grinding
may be required.
2With the cylinder head removed, use a
scraper to remove the carbon from the
combustion chambers and ports. Remove all
traces of gasket from the cylinder head
surface, then wash it thoroughly with paraffin.
3Use a straight edge and feeler blade to
check that the cylinder head surface is not
distorted. If it is, it must be resurfaced by a
suitably equipped engineering works.
4If the engine is still in the vehicle, clean the
piston crowns and cylinder bore upper edges,
but make sure that no carbon drops between
the pistons and bores. To do this, locate two
of the pistons at the top of their bores and
seal off the remaining bores with paper andmasking tape. Press a little grease between
the two pistons and their bores to collect any
carbon dust; this can be wiped away when
the piston is lowered. To prevent carbon
build-up, polish the piston crown with metal
polish, but remove all traces of the polish
afterwards.
5Examine the heads of the valves for pitting
and burning, especially the exhaust valve
heads. Renew any valve which is badly burnt.
Examine the valve seats at the same time. If
the pitting is very slight, it can be removed by
grinding the valve heads and seats together
with coarse, then fine, grinding paste.
6Where excessive pitting has occurred, the
valve seats must be recut or renewed by a
suitably equipped engineering works.
7Valve grinding is carried out as follows.
Place the cylinder head upside down on a
bench on blocks of wood.
8Smear a trace of coarse carborundum
paste on the valve seat face and press a
suction grinding tool onto the valve head.
With a semi-rotary action, grind the valve
head to its seat, lifting the valve occasionally
to redistribute the grinding paste. When a dull
matt even surface is produced on the mating
surface of both the valve seat and the valve,
wipe off the paste and repeat the process with
fine carborundum paste as before. A light
spring placed under the valve head will greatly
ease this operation. When a smooth unbroken
ring of light grey matt finish is produced on
the mating surface of both the valve and seat,
the grinding operation is complete.
9Scrape away all carbon from the valve head
and stem, and clean away all traces of
grinding compound. Clean the valves and
seats with a paraffin soaked rag, then wipe
with a clean rag.
10If the guides are worn they will need
reboring for oversize valves or for fitting guide
inserts. The valve seats will also need
recutting to ensure that they are concentric
with the stems. This work should be entrusted
to a Ford dealer or local engineering works.
11Check that the free length of the valve
springs is as specified, and renew if
necessary. Do not renew individual springs; if
any springs are excessively worn, renew all
the springs as a set.
23Cylinder head - inspection
and renovation
22Cylinder head - dismantling
and reassembly
2A¥16SOHC engines
22.2a Compressing a valve spring22.2c Removing a valve
22.4 Removing a valve stem oil seal
22.2b Removing a valve spring and cap
Page 17 of 24
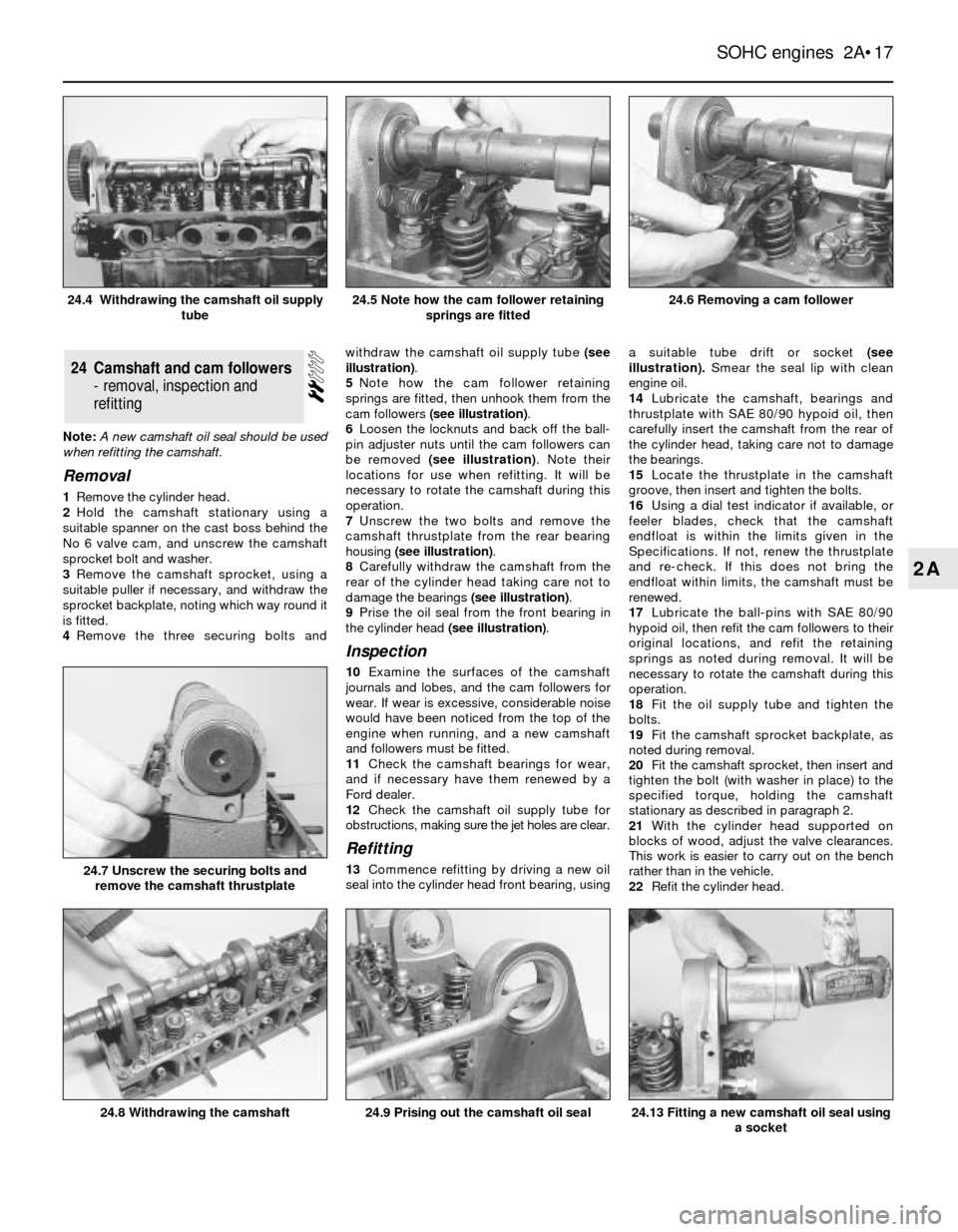
Note: A new camshaft oil seal should be used
when refitting the camshaft.
Removal
1Remove the cylinder head.
2Hold the camshaft stationary using a
suitable spanner on the cast boss behind the
No 6 valve cam, and unscrew the camshaft
sprocket bolt and washer.
3Remove the camshaft sprocket, using a
suitable puller if necessary, and withdraw the
sprocket backplate, noting which way round it
is fitted.
4Remove the three securing bolts andwithdraw the camshaft oil supply tube (see
illustration).
5Note how the cam follower retaining
springs are fitted, then unhook them from the
cam followers (see illustration).
6Loosen the locknuts and back off the ball-
pin adjuster nuts until the cam followers can
be removed (see illustration). Note their
locations for use when refitting. It will be
necessary to rotate the camshaft during this
operation.
7Unscrew the two bolts and remove the
camshaft thrustplate from the rear bearing
housing (see illustration).
8Carefully withdraw the camshaft from the
rear of the cylinder head taking care not to
damage the bearings (see illustration).
9Prise the oil seal from the front bearing in
the cylinder head (see illustration).
Inspection
10Examine the surfaces of the camshaft
journals and lobes, and the cam followers for
wear. If wear is excessive, considerable noise
would have been noticed from the top of the
engine when running, and a new camshaft
and followers must be fitted.
11Check the camshaft bearings for wear,
and if necessary have them renewed by a
Ford dealer.
12Check the camshaft oil supply tube for
obstructions, making sure the jet holes are clear.
Refitting
13Commence refitting by driving a new oil
seal into the cylinder head front bearing, usinga suitable tube drift or socket(see
illustration).Smear the seal lip with clean
engine oil.
14Lubricate the camshaft, bearings and
thrustplate with SAE 80/90 hypoid oil, then
carefully insert the camshaft from the rear of
the cylinder head, taking care not to damage
the bearings.
15Locate the thrustplate in the camshaft
groove, then insert and tighten the bolts.
16Using a dial test indicator if available, or
feelerblades, check that the camshaft
endfloat is within the limits given in the
Specifications. If not, renew the thrustplate
and re-check. If this does not bring the
endfloat within limits, the camshaft must be
renewed.
17Lubricate the ball-pins with SAE 80/90
hypoid oil, then refit the cam followers to their
original locations, and refit the retaining
springs as noted during removal. It will be
necessary to rotate the camshaft during this
operation.
18Fit the oil supply tube and tighten the
bolts.
19Fit the camshaft sprocket backplate, as
noted during removal.
20Fit the camshaft sprocket, then insert and
tighten the bolt (with washer in place) to the
specified torque, holding the camshaft
stationary as described in paragraph 2.
21With the cylinder head supported on
blocks of wood, adjust the valve clearances.
This work is easier to carry out on the bench
rather than in the vehicle.
22Refit the cylinder head.
24Camshaft and cam followers
- removal, inspection and
refitting
SOHC engines 2A¥17
2A
24.6 Removing a cam follower
24.13 Fitting a new camshaft oil seal using
a socket24.9 Prising out the camshaft oil seal24.8 Withdrawing the camshaft
24.7 Unscrew the securing bolts and
remove the camshaft thrustplate
24.5 Note how the cam follower retaining
springs are fitted24.4 Withdrawing the camshaft oil supply
tube
Page 18 of 24
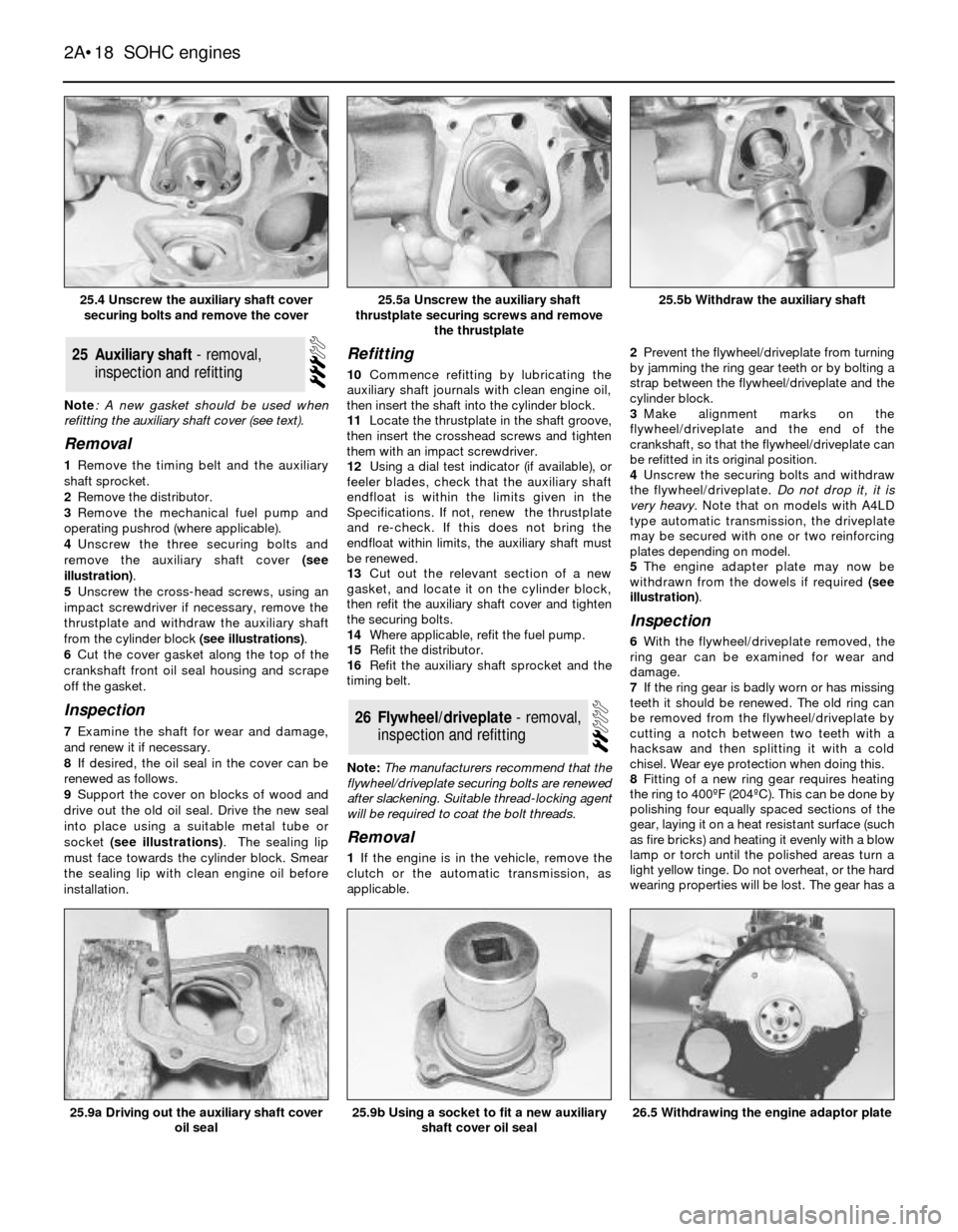
Note: A new gasket should be used when
refitting the auxiliary shaft cover (see text).
Removal
1Remove the timing belt and the auxiliary
shaft sprocket.
2Remove the distributor.
3Remove the mechanical fuel pump and
operating pushrod (where applicable).
4Unscrew the three securing bolts and
remove the auxiliary shaft cover (see
illustration).
5Unscrew the cross-head screws, using an
impact screwdriver if necessary, remove the
thrustplate and withdraw the auxiliary shaft
from the cylinder block (see illustrations).
6Cut the cover gasket along the top of the
crankshaft front oil seal housing and scrape
off the gasket.
Inspection
7Examine the shaft for wear and damage,
and renew it if necessary.
8If desired, the oil seal in the cover can be
renewed as follows.
9Support the cover on blocks of wood and
drive out the old oil seal. Drive the new seal
into place using a suitable metal tube or
socket (see illustrations). The sealing lip
must face towards the cylinder block. Smear
the sealing lip with clean engine oil before
installation.
Refitting
10Commence refitting by lubricating the
auxiliary shaft journals with clean engine oil,
then insert the shaft into the cylinder block.
11Locate the thrustplate in the shaft groove,
then insert the crosshead screws and tighten
them with an impact screwdriver.
12Using a dial test indicator (if available), or
feelerblades, check that the auxiliary shaft
endfloat is within the limits given in the
Specifications. If not, renew the thrustplate
and re-check. If this does not bring the
endfloat within limits, the auxiliary shaft must
be renewed.
13Cut out the relevant section of a new
gasket, and locate it on the cylinder block,
then refit the auxiliary shaft cover and tighten
the securing bolts.
14Where applicable, refit the fuel pump.
15Refit the distributor.
16Refit the auxiliary shaft sprocket and the
timing belt.
Note: The manufacturers recommend that the
flywheel/driveplate securing bolts are renewed
after slackening. Suitable thread-locking agent
will be required to coat the bolt threads.
Removal
1If the engine is in the vehicle, remove the
clutch or the automatic transmission, as
applicable.2Prevent the flywheel/driveplate from turning
by jamming the ring gear teeth or by bolting a
strap between the flywheel/driveplate and the
cylinder block.
3Make alignment marks on the
flywheel/driveplate and the end of the
crankshaft, so that the flywheel/driveplate can
be refitted in its original position.
4Unscrew the securing bolts and withdraw
the flywheel/driveplate. Do not drop it, it is
very heavy. Note that on models with A4LD
type automatic transmission, the driveplate
may be secured with one or two reinforcing
plates depending on model.
5The engine adapter plate may now be
withdrawn from the dowels if required (see
illustration).
Inspection
6With the flywheel/driveplate removed, the
ring gear can be examined for wear and
damage.
7If the ring gear is badly worn or has missing
teeth it should be renewed. The old ring can
be removed from the flywheel/driveplate by
cutting a notch between two teeth with a
hacksaw and then splitting it with a cold
chisel. Wear eye protection when doing this.
8Fitting of a new ring gear requires heating
the ring to 400¼F (204¼C). This can be done by
polishing four equally spaced sections of the
gear, laying it on a heat resistant surface (such
as fire bricks) and heating it evenly with a blow
lamp or torch until the polished areas turn a
light yellow tinge. Do not overheat, or the hard
wearing properties will be lost. The gear has a
26Flywheel/driveplate - removal,
inspection and refitting
25Auxiliary shaft - removal,
inspection and refitting
2A¥18SOHC engines
25.4 Unscrew the auxiliary shaft cover
securing bolts and remove the cover25.5b Withdraw the auxiliary shaft
26.5 Withdrawing the engine adaptor plate25.9b Using a socket to fit a new auxiliary
shaft cover oil seal25.9a Driving out the auxiliary shaft cover
oil seal
25.5a Unscrew the auxiliary shaft
thrustplate securing screws and remove
the thrustplate
Page 19 of 24
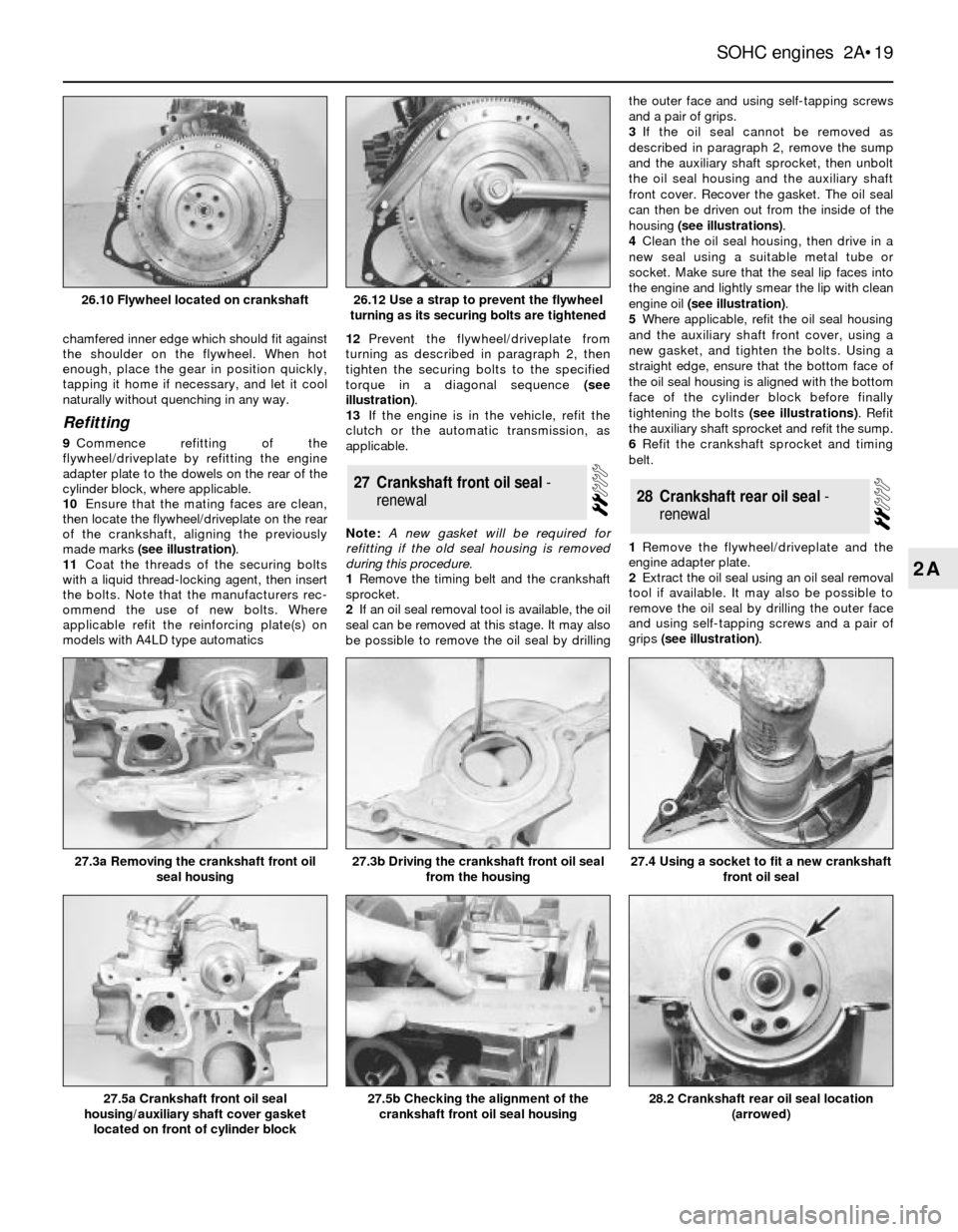
chamfered inner edge which should fit against
the shoulder on the flywheel. When hot
enough, place the gear in position quickly,
tapping it home if necessary, and let it cool
naturally without quenching in any way.
Refitting
9Commence refitting of the
flywheel/driveplate by refitting the engine
adapter plate to the dowels on the rear of the
cylinder block, where applicable.
10Ensure that the mating faces are clean,
then locate the flywheel/driveplate on the rear
of the crankshaft, aligning the previously
made marks (see illustration).
11Coat the threads of the securing bolts
with a liquid thread-locking agent, then insert
the bolts. Note that the manufacturers rec-
ommend the use of new bolts. Where
applicable refit the reinforcing plate(s) on
models with A4LD type automatics12Prevent the flywheel/driveplate from
turning as described in paragraph 2, then
tighten the securing bolts to the specified
torque in a diagonal sequence (see
illustration).
13If the engine is in the vehicle, refit the
clutch or the automatic transmission, as
applicable.
Note: A new gasket will be required for
refitting if the old seal housing is removed
during this procedure.
1Remove the timing belt and the crankshaft
sprocket.
2If an oil seal removal tool is available, the oil
seal can be removed at this stage. It may also
be possible to remove the oil seal by drillingthe outer face and using self-tapping screws
and a pair of grips.
3If the oil seal cannot be removed as
described in paragraph 2, remove the sump
and the auxiliary shaft sprocket, then unbolt
the oil seal housing and the auxiliary shaft
front cover. Recover the gasket. The oil seal
can then be driven out from the inside of the
housing (see illustrations).
4Clean the oil seal housing, then drive in a
new seal using a suitable metal tube or
socket. Make sure that the seal lip faces into
the engine and lightly smear the lip with clean
engine oil (see illustration).
5Where applicable, refit the oil seal housing
and the auxiliary shaft front cover, using a
new gasket, and tighten the bolts. Using a
straight edge, ensure that the bottom face of
the oil seal housing is aligned with the bottom
face of the cylinder block before finally
tightening the bolts (see illustrations). Refit
the auxiliary shaft sprocket and refit the sump.
6Refit the crankshaft sprocket and timing
belt.
1Remove the flywheel/driveplate and the
engine adapter plate.
2Extract the oil seal using an oil seal removal
tool if available. It may also be possible to
remove the oil seal by drilling the outer face
and using self-tapping screws and a pair of
grips (see illustration).
28Crankshaft rear oil seal -
renewal27Crankshaft front oil seal -
renewal
SOHC engines 2A¥19
2A
27.3a Removing the crankshaft front oil
seal housing27.3b Driving the crankshaft front oil seal
from the housing
28.2 Crankshaft rear oil seal location
(arrowed)27.5b Checking the alignment of the
crankshaft front oil seal housing27.5a Crankshaft front oil seal
housing/auxiliary shaft cover gasket
located on front of cylinder block
27.4 Using a socket to fit a new crankshaft
front oil seal
26.12 Use a strap to prevent the flywheel
turning as its securing bolts are tightened26.10 Flywheel located on crankshaft
Page 20 of 24
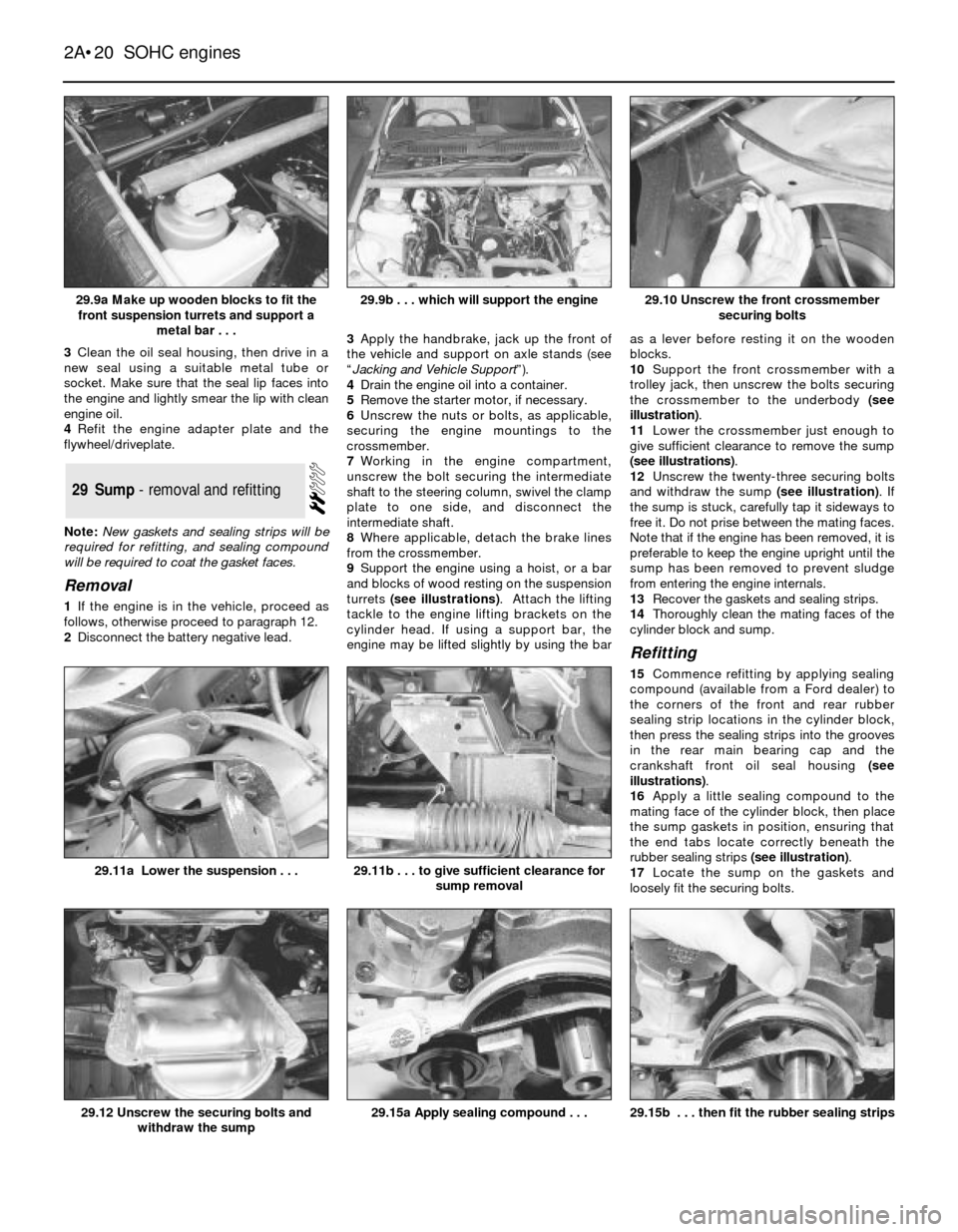
3Clean the oil seal housing, then drive in a
new seal using a suitable metal tube or
socket. Make sure that the seal lip faces into
the engine and lightly smear the lip with clean
engine oil.
4Refit the engine adapter plate and the
flywheel/driveplate.
Note: New gaskets and sealing strips will be
required for refitting, and sealing compound
will be required to coat the gasket faces.
Removal
1If the engine is in the vehicle, proceed as
follows, otherwise proceed to paragraph 12.
2Disconnect the battery negative lead.3Apply the handbrake, jack up the front of
the vehicle and support on axle stands (see
ÒJacking and Vehicle SupportÓ).
4Drain the engine oil into a container.
5Remove the starter motor, if necessary.
6Unscrew the nuts or bolts, as applicable,
securing the engine mountings to the
crossmember.
7Working in the engine compartment,
unscrew the bolt securing the intermediate
shaft to the steering column, swivel the clamp
plate to one side, and disconnect the
intermediate shaft.
8Where applicable, detach the brake lines
from the crossmember.
9Support the engine using a hoist, or a bar
and blocks of wood resting on the suspension
turrets (see illustrations). Attach the lifting
tackle to the engine lifting brackets on the
cylinder head. If using a support bar, the
engine may be lifted slightly by using the baras a lever before resting it on the wooden
blocks.
10Support the front crossmember with a
trolley jack, then unscrew the bolts securing
the crossmember to the underbody (see
illustration).
11Lower the crossmember just enough to
give sufficient clearance to remove the sump
(see illustrations).
12Unscrew the twenty-three securing bolts
and withdraw the sump (see illustration). If
the sump is stuck, carefully tap it sideways to
free it. Do not prise between the mating faces.
Note that if the engine has been removed, it is
preferable to keep the engine upright until the
sump has been removed to prevent sludge
from entering the engine internals.
13Recover the gaskets and sealing strips.
14Thoroughly clean the mating faces of the
cylinder block and sump.
Refitting
15Commence refitting by applying sealing
compound (available from a Ford dealer) to
the corners of the front and rear rubber
sealing strip locations in the cylinder block,
then press the sealing strips into the grooves
in the rear main bearing cap and the
crankshaft front oil seal housing (see
illustrations).
16Apply a little sealing compound to the
mating face of the cylinder block, then place
the sump gaskets in position, ensuring that
the end tabs locate correctly beneath the
rubber sealing strips (see illustration).
17Locate the sump on the gaskets and
loosely fit the securing bolts.
29Sump - removal and refitting
2A¥20SOHC engines
29.9a Make up wooden blocks to fit the
front suspension turrets and support a
metal bar . . .29.10 Unscrew the front crossmember
securing bolts
29.15b . . . then fit the rubber sealing strips29.15a Apply sealing compound . . .29.12 Unscrew the securing bolts and
withdraw the sump
29.11b . . . to give sufficient clearance for
sump removal29.11a Lower the suspension . . .
29.9b . . . which will support the engine